Yeast lipid-based biofuels and oleochemicals from lignocellulosic biomass: life cycle impact assessment†
Received
19th July 2019
, Accepted 23rd October 2019
First published on 25th October 2019
Abstract
Over the last few decades, much attention has been paid to various applications of microbial oil, including for transportation. Lignocellulosic biomass has been chosen to produce fuels and chemicals using different chemical/conversion pathways, although the excessive use of chemicals and solvents during the processes are issues of immediate environmental concern. Rhodotorula mucilaginosa IIPL32 (RMIIPL32) being an oleaginous yeast can accumulate triglycerides (lipid) through fermentation of xylose, extracted from pre-treatment of sugarcane bagasse. In this study, environmental impacts have been assessed for the generation of the lipid and its conversion into biodiesel, lube base oil and BTEX (benzene, toluene, ethyl benzene and xylene). Uncertainty analysis was carried out for all the emissions under the environmental impact categories for the processes. The emissions investigated for global warming potential (GWP) are found to be 260.03, 572.16, 27.83 and 85.19 kg CO2 equivalent for non-polar lipid, lube base oil, biodiesel and BTEX processes. The uncertainty is also found to be lower for GWP (i.e., <0.3) for all the processes. This is the first LCA report for yeast lipid production from sugarcane bagasse. Therefore, this study can be beneficial for the scale-up of yeast lipid fermentation and its conversion into high value products.
1. Introduction
The escalating energy demand has resulted in many challenges for India's economic growth as well as energy and environmental security.1–3 With the rise in fuel consumption at a brisk pace and domestic output remaining stagnant, India's oil import dependence has attained a new hike of 84% in 2018–19, as per a recent report of the Petroleum Planning and Analysis Cell (PPAC). Based on the current trend of growth, by 2030, India will have a fleet of nearly 600 million transport vehicles, which is almost three times the existing ∼210 million. With a target of downscaling oil imports by 10% by 2022 to save the country's precious foreign exchange, and at the same time a commitment to limit the anthropogenic CO2 emissions to reach the less than two-degree goal of the Intergovernmental Panel on Climate Change (IPCC) as the 4 per 1000 initiative during Conference of the Parties (COP)-21 at Paris in 2015, India has relaunched its New Biofuel Policy in 2019 to augment the biofuel share. Presently, India imports ∼350 MMT of carbon in the form of crude oil, coal, and natural gas (a total of ∼435 MMT) per annum. For a sustainable and resource efficient biofuel policy, with surplus agri-residue, forest residue, biogas, Municipal Solid Waste (MSW), and Used Cooking Oil (UCO), the country has ∼485 MMT of carbon excluding landfill and industrial emissions. Efficient use of resources is the key to sustainable development for any nation.4 Thus, with all the carbon available within the country's geographical scope, bio-based fuels as renewable alternatives can be envisaged as a substitute for fossil fuel to mitigate environmental pollution. Biofuels, generated from lignocellulosic biomass, can reduce the majority of concerns associated with fossil fuel.5–7 The use of biomass for the generation of fuels and chemicals is an efficient process as waste is transformed into a resource, reduces negative impacts of improper disposal of biomass in the environment and also aids in achieving a circular economy.8
India's indicative target of 10% blending of biofuels, whether bioethanol or biodiesel, by 2022, bioethanol from the lignocellulosic/vegetal feedstock and biodiesel from plant/algae based fatty oil, is nation-wide being brought into production scale reality. Apart from various oil seed-bearing plants, oleaginous microbes have recently been considered a cheap source of oil, which could be used either as a fuel precursor or oleochemical commodity through partial replacement of plant-borne oil. Oleaginous yeasts offer some potential advantages over plant-borne oil, or even algal oil due to their short generation time (80 h), can be cultivated under a roof in bioreactors, don't compete with food and feed and have similar lipid quality irrespective of regional differences.9–14 Yeast SCO stands out as a feedstock for the generation of value-added lipid derivatized fuels or oleochemicals.15
Life cycle assessment (LCA) is a way to evaluate the feasibility of any process for assessing the environmental impacts associated with the life cycle of any product, starting from raw material production to its disposal. LCA is a substantial and useful tool to showcase the ecological benefits of bioenergy processes, in terms of GHG balance. Scientific attempts at LCA studies are available for 2G bioethanol, as well as plant and algal fatty oil-based biodiesel processes. Also, substantial uncertainties in energy and environmental performance analysis have been noticed.16
In this study, an extensive life cycle assessment of the process of converting yeast lipid into biofuels and chemicals (biodiesel, BTEX, and lube base oil) was conducted to determine the environmental impact and process uncertainty17 and is being reported here for the first time to the best of our knowledge. All of the processes reported here begin with biomass, with a greener and eco-friendly route, but the use of solvents, chemicals, and electricity during the experimental run creates challenges for environmental safety. LCA can be carried out at a small scale in order to develop the strategy for improved sustainability in large scale processes,18 by scrutinizing almost every step from the beginning till the end of life of the product and recycling (in possible cases).19–23 A well-to-gate yeast-lipid derived biodiesel and oleochemicals model was established with the arrangement of data inventory, to calculate estimated advantages and shortcomings of the processes along with the uncertainties.
2. Methodology
Life cycle assessment (LCA) is an environmental assessment tool used for systematic quantification of the input–output inventory of reactant and product systems throughout all unit operations, thereby projecting the environmental performances based on a selected functional unit of the product.24–26 The ISO (International Organization for Standardization) 14040 and 14044 standards were adopted for this study.27 Most of the primary data used in this study have been generated through experimental work, and some secondary data were obtained from open literature specific to the Indian context. Sima Pro 9.0.0.29 was used as the modelling software tool.
2.1. Goal and scope definition
This cradle to gate study was aimed at assessing the environmental impacts of the laboratory scale conversion processes of yeast lipid-mediated biofuels and oleochemicals, to ensure an environmental impact. As per our earlier report,14 45 g of yeast lipid was generated from 240 g of xylose sugar (C5 from lignocellulosic biomass hydrolysate). This was considered as a functional unit for this LCA study. Emissions were calculated for the generation of 45 g of yeast lipid, starting from sugarcane cultivation (Fig. 1) to lipid extraction, where C6 rich biomass is kept outside of this boundary. However, for the conversion of lipid into different products, the input value of lipid varied as per the reaction setup, which should not be confused with the functional unit. Thus, the scope of the study was to evaluate the global warming potential (GWP), eutrophication, and ozone layer depletion (OLD), environmental indicators for the process chain.
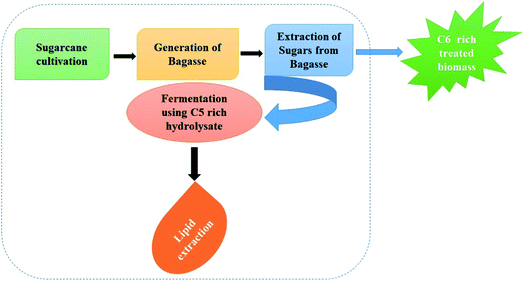 |
| Fig. 1 Image showing the process flow and system boundary from sugarcane cultivation to lipid extraction, where C6 rich biomass is kept outside of this boundary. | |
2.2. System boundaries
Based on current practices, the system boundary for this study included unit operations like (1) sugarcane cultivation, (2) generation of bagasse, (3) bagasse pre-treatment for pentose-rich fermentable sugar production, (4) yeast bioconversion (the biochemical pathway for yeast lipid synthesis is given in the ESI†), (5) lipid recovery, and solid catalytic conversion of lipid into (6) biodiesel, (7) BTEX, and (8) yeast lipid to lube base oil. During pre-treatment of sugarcane bagasse, the cellulosic fraction, rich in hexose sugars, remains as a by-product, and during post saccharification, the lignin-rich biomass remains as a by-product. In our study, we excluded these fractions from the system boundaries, considering their established production processes for 2G-ethanol and other value additions. Oleaginous yeast Rhodotorula mucilaginosa IIPL32 (MTCC 25056), considered for cultivation and lipid accumulation in this study, could produce lipid from lignocellulosic pentosans as well as hexosans. Since yeast is cultivated from pentose, the stream is not widely reported for the commercial endeavour; thus, we kept sugarcane bagasse derived pentosans within the system boundary. The overall system boundary, depicting the entire process is detailed in Fig. 2.
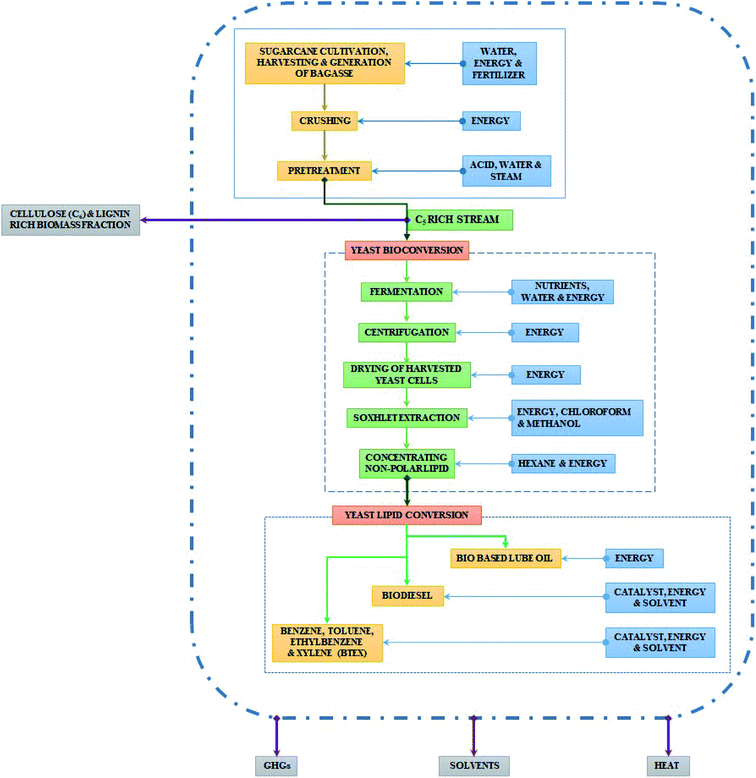 |
| Fig. 2 The overall system boundary, showing the entire process flow. | |
2.3. Life cycle inventory (LCI) and system description
A life cycle inventory was prepared for eight different unit processes, as input and output in terms of mass and energy for raw materials and products, and is given in Table 1. All the methods addressed in the life cycle inventory are summarized herein in the following subsections.
Table 1 Data inventory for unit processes: sugarcane bagasse to non-polar lipid, case A: lipid to biodiesel, case B: lipid to BTEX and case C: lipid to lube base oil
S. No |
Stages |
In/out |
Basic unit and hours |
Comments/references |
1 |
SCB cultivation |
Input |
28
|
P2O5 |
100 kg ha−1 |
K2O |
45 kg ha−1 |
N |
125 kg ha−1 |
Lime |
400 kg CaCO3 per ha |
Pesticides |
2.1 kg ha−1 |
Diesel |
223 MJ ha−1 |
Electricity |
17.6 kW h ha−1 |
Output |
Yield |
66 815 kg ha−1 |
Dry matter content |
0.30 kg kg−1 |
2 |
Generation of bagasse |
Input |
29
|
Sugarcane |
1000 kg |
Sulphur dioxide |
1.5 kg |
Limestone |
1.9 kg |
Sodium hydroxide |
0.5 kg |
Superphosphate |
0.1 kg |
Soda |
0.03 kg |
Organic chemicals |
0.01 kg |
Lubricating oil |
0.6 kg |
Phosphoric acid |
0.01 kg |
Water |
30 kg |
Transport, sugarcane |
12 tkm |
Transport, inputs |
0.6 tkm |
Output |
Sugar |
91.4 kg |
Molasses |
50.3 kg |
Bagasse |
6 kg |
Electricity |
54.2 kW h |
3 |
Extraction of sugars from SCB |
Input |
This study |
Electricity in the crusher |
3 kW h |
Biomass |
3 kg |
Electricity in the biomass digester |
28.75 kW h |
Steam |
5 kg |
Water |
24 L |
Acid |
0.11 kg |
Calcium oxide |
70 g |
Output |
C5 rich hydrolysate |
23 L |
C6 rich treated biomass |
2 kg |
4 |
Fermentation |
Input |
|
14
|
C5 rich hydrolysate sugar |
12 L/240 g |
Ammonium sulphate |
25.74 g |
KH2PO4 |
16.38 g |
Na2HPO4 |
9.71 g |
MgSO4 |
11.37 g |
Yeast extract |
13 g |
Steam |
2 kg |
Electricity in the fermenter |
54 kW h |
Electricity in the chiller |
26.6 kW h |
Electricity in the compressor |
26.6 kW h |
Output |
Lipid containing yeast cells |
184.2 g |
5 |
Lipid extraction |
Input |
This study |
Electricity for centrifugation |
4.85 kW h |
Electricity for cell drying |
18 kW h |
Electricity for grinding cells |
0.75 kW h |
Electricity for Soxhlet extraction |
144 kW h |
Electricity for the solvent concentrator |
2 kW h |
Chloroform |
0.3 kg |
Methanol |
0.08 kg |
Hexane |
0.06 kg |
Yeast cells |
184 g |
Output |
Non-polar lipid
|
45 g |
1 |
Case A: lipid to biodiesel |
Input |
30
|
Catalyst ZnO |
0.02 g |
MeOH |
20 g |
Yeast lipid |
2 g |
Electricity in the reactor |
17.25 kW h |
Output |
Biodiesel
|
0.8 g |
Glycerol
|
0.2 g |
2 |
Case B: lipid TO BTEX |
Input |
31
|
Ga |
0.05 g |
Alumina |
1 g |
Electricity (voltage/power) used in the |
1. PID controller |
10.8 kW h |
2. Temperature controller |
10.8 kW h |
3. Chiller |
20.7 kW h |
4. Liquid pump |
11.25 kW h |
Silicon carbide |
2–3 g |
Nitrogen |
20 mL min−1 |
Lipid |
6 mL |
Output |
Benzene |
0.32 mL |
Toluene |
3.84 mL |
Ethyl benzene |
0.24 mL |
Xylene |
0.042 mL |
3 |
Case C: lipid to lube base oil |
Input |
14
|
Lipid |
1 g |
Output |
Lube base oil |
1 g |
2.4. Sugarcane cultivation
Sugarcane is a perennial, kharif crop in northern India. The favourable temperatures of 21 °C to 27 °C and 75–150 cm rainfall are optimal for its cultivation and propagation. Since sugarcane is a water-intensive crop, irrigation is also required to minimize the effects of insufficient rain. Moisture-rich loamy soil is ideal for supporting better farming.32 The land is prepared before plantation by ploughing and levelling by tractors followed by soil enrichment by applying phosphorus, nitrogen and potassium. The common practice for tillage preparation involves ploughing of fields till the soil is soft. Usually fields are ploughed with tractors, 2 to 4 times with tractor drawn ploughs, generally at depths of 50–60 cm. After this, secondary tillage formation is performed as it grinds the soil and makes its texture uniform, which is essential for moisture retention by the soil. To crush the lumps and chunks, harrowing is done superficially at depths of 12–15 cm. Irrigation and excess water run off channels are preferred to be along and across the fields at 10–15 m intervals.33 The crop is regulated by the addition of fertilizers and herbicides and harvested after 9–10 months by cutting down the stems manually. During harvesting, the roots are left within the soil and allowed to grow for the next crop cycle with nutrient enrichment in soil.29
2.5. Generation of bagasse
In India, sugarcane is transported to sugar mills to generate sugar, molasses, surplus electricity, and surplus bagasse.34 During processing, sugarcane is cleaned by washing, torn, and pressed to extract the juice for sugar production, and the left-over bagasse is stored and used during the offseason. Bagasse serves two purposes, (1) for power co-generation to fulfil the primary energy requirements of the mill, and (2) to deliver spare electricity to the grid.35
2.6. Pre-treatment of bagasse for pentose sugar extraction
Sugarcane bagasse was procured from a local sugar mill (Doiwala Sugar Mill, Dehradun, India) situated within a distance of 3 km from the laboratory. In the laboratory, bagasse was stored in a cool, dry place and milled up to 3–5 mm particle size. Extraction of pentose sugars was carried out via a dilute acid pre-treatment method in a biomass digester, designed in-house. This pre-treatment process was performed as per the protocol.36 Pre-treatment was carried out at 140 °C for 90 min, with dilute sulphuric acid (3.76% w/w) and autogenous pressure; the solid-to-liquid ratio was 1
:
8.
2.7. Yeast bioconversion
The oleaginous yeast Rhodotorula mucilaginosa IIPL32 (MTCC 25056), an in-house soil isolate (oil dumping site of CSIR-Indian Institute of Petroleum, Dehradun, Uttarakhand, India), was reported in this study for lipid production. The yeast was cultivated in a fed-batch mode in a 15 L in situ sterilizable fermenter as per our earlier report.14 Briefly, yeast biomass was generated under carbon limiting and excess nitrogen conditions under high aeration. The xylose-rich fraction, hydrolysed from sugarcane bagasse (as mentioned in Section 2.3.3 above), was used as the sole carbon source. Carbon and nitrogen (C/N ∼ 20) were required for cell maintenance, growth, and division. Intracellular lipid accumulation was accentuated by shifting the reactor operation mode with applied nitrogen stress (purging concentrated xylose hydrolysate to attain C/N ∼ 40) and low aeration. During nitrogen stress, the cell division was limited, and carbon flux was directed towards intracellular lipid accumulation.36
2.8. Lipid recovery
After fermentation, lipid-rich cells were separated from the broth by centrifugation. The cells were oven-dried at 60 °C, milled, and further subjected to Soxhlet extraction using chloroform and methanol (2
:
1) as the solvent. The extracted total lipid was also treated with hexane, followed by water washing. Finally, the lipid was collected through vacuum evaporation of the solvent and quantified gravimetrically.14
2.9. Conversion of lipid to biodiesel
Oil trans-esterified into its corresponding ethyl or methyl esters is popularly known as biodiesel (FAEE or FAME). Transesterification catalysts are both homogeneous and heterogeneous with acidic or basic characteristics. As alkaline catalysts are not suitable for oils with high free fatty acid (FFA) content, due to soap formation and further separation of the ester and glycerol, a two-step transesterification process with acid catalysts is employed to first reduce the FFA value, followed by transesterification.37 This study involved the process of converting yeast lipid containing a high content of FFA (FFA ∼ 17%) to an alkyl ester in the presence of a solid catalyst, with esterification and transesterification happening in a single step (Fig. 3). The reaction was carried out in a Parr reactor (Parr, Germany) with yeast lipid and methanol (in 1
:
10 ratio), in the presence of a CSIR-IIP proprietary catalyst. The reaction conditions were optimized at a temperature and cooking time of 175 °C and 5 h under autogenous pressure (10–12 kg). Excess methanol favoured the conversion stoichiometry and was recovered using a rotavapor, after the termination of the reaction. The layers of biodiesel and glycerine were separated in a separating funnel, followed by water washing, drying, and distillation. The produced biodiesel met the ASTM D 6751, EN 14214, and BIS 15607 specifications.30
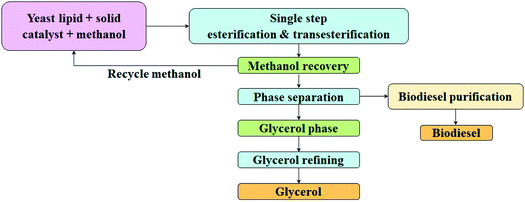 |
| Fig. 3 Schematic diagram for biodiesel production. | |
2.10. Conversion of lipid to lube-base oil
RMIIPL32 lipid was assessed as an alternative and sustainable source for bio-lubricant application, in comparison to mineral lube base oil. The fatty acid profile was analysed by NMR, FTIR, and GC × GC. Tribo-testing of RMIIPL32 lipid as a lube base oil resulted in the protection of the engine surfaces and reduced friction. In comparison with SN 150 (conventional mineral lube base oil), RMIIPL32 lipid reduced the coefficient of friction by 72% and the wear 24%.14
2.11. Conversion of lipid to BTEX
Benzene, toluene, ethyl benzene, and xylene (BTEX) are conventionally produced from fossil crude by catalytic hydrocracking. BTEX aromatics have been synthesized from renewable feedstocks like yeast single cell oil so as to give a new outlook for the green and sustainable route of production. Herein, RMIIPL32 lipid was selectively dehydrogenated in a fixed bed down-flow reactor with alumina-based catalysts at a reaction temperature of 450 °C and an atmosphere helium pressure of 20 h−1 space velocity (GHSV). A BTEX yield of 77% with 89% lipid conversion has been achieved.31
2.12. Impact assessment
The impact assessment was performed using a CML baseline method with normalization factor EU25, which included eight impact categories, viz, acidification, climate change, depletion of abiotic resources, ecotoxicity, eutrophication, human toxicity, ozone layer depletion, and photochemical oxidation.
2.13. Interpretation for impact assessment
From the life cycle inventories of impact assessment for the four main processes, GHG emissions for climate change or global warming potential (kg CO2 equivalent) for 100 years, and methane, tetrafluoro-, and CFC-14 (kg CFC-11 equivalent) emissions responsible for ozone layer depletion and nitrogen oxide emissions (kg P equivalent) were selected to report impact of emissions. Emissions were multiplied by the IPCC equivalency factors or characterization factors38,39 to calculate the impact.
2.14. Uncertainty analysis
Uncertainty analysis assists analysts and technology developers to estimate how close the predicted results are to the actual value. Generally, three steps are considered while evaluating uncertainty: (1) detecting possible sources of uncertainty; (2) enumerating various bases of uncertainty, whenever feasible; and (3) calculating total uncertainty by summing the different uncertainties lying in the process. Generally, Monte Carlo simulations are preferred over the basic uncertainty analysis. Monte Carlo simulations are software-based functions which use sampling of data to provide a probability-based estimation to the answer of mathematical equations. It is a complex process, as it generates random values repetitively based on the activity (input) data.17 The uncertainties in the LCA of the defined processes were assessed through Monte-Carlo analysis using SimaPro 9.0.0.29 software. A thousand runs were performed to obtain the curve at a 95% confidence interval using the CML-IA baseline V3.05/EU25 method.
3. Results
The main objective of this paper was to calculate GHG emissions from each defined process (1–4 in the LCI). The LCA results were also subjected to Monte-Carlo uncertainty analysis.
3.1. Life cycle assessment
Since this LCA was assessed to find emissions from laboratory scale processes used to produce lipid and other application products from it, the input value for each product was different (as given in the LCI). The results are shown in normalized values for each category in per year basis and emissions are also calculated for GWP/climate change, ozone layer depletion and eutrophication, for 45 g of lipid; the normalized emissions for eight impact categories (as per the CML baseline method) are given in Table 2. The maximum emissions are seen for marine aquatic ecotoxicity, followed by abiotic depletion (fossil fuel), global warming, acidification and eutrophication, for the processes given in Fig. 4. All the emissions for the defined processes are given in Tables S5–S8 (ESI†).
Table 2 Normalized emission results for the defined unit processes
Impact categories |
Units |
Lipid |
Biodiesel |
BTEX |
Lube base oil |
Abiotic depletion |
Year |
1.04 × 10−12 |
1.09 × 10−13 |
3.34 × 10−13 |
2.31 × 10−12 |
Abiotic depletion (fossil fuel) |
Year |
1.40 × 10−10 |
1.50 × 10−11 |
4.58 × 10−11 |
3.11 × 10−10 |
Global warming |
Year |
7.43 × 10−11 |
7.95 × 10−12 |
2.43 × 10−11 |
1.65 × 10−10 |
Ozone layer depletion OD |
Year |
2.50 × 10−12 |
1.14 × 10−13 |
3.43 × 10−13 |
5.56 × 10−12 |
Human toxicity |
Year |
8.45 × 10−12 |
2.04 × 10−12 |
6.25 × 10−12 |
4.24 × 10−11 |
Freshwater aquatic ecotoxicity |
Year |
3.08 × 10−12 |
3.06 × 10−11 |
9.37 × 10−11 |
6.36 × 10−10 |
Marine aquatic ecotoxicity |
Year |
3.29 × 10−9 |
6.23 × 10−10 |
1.91 × 10−9 |
1.29 × 10−8 |
Terrestrial ecotoxicity |
Year |
1.10 × 10−11 |
1.27 × 10−12 |
3.89 × 10−12 |
2.64 × 10−11 |
Photochemical oxidation |
Year |
6.79 × 10−12 |
7.26 × 10−13 |
2.22 × 10−12 |
1.51 × 10−11 |
Acidification |
Year |
5.45 × 10−11 |
5.83 × 10−12 |
1.78 × 10−11 |
1.21 × 10−10 |
Eutrophication |
Year |
1.48 × 10−11 |
5.94 × 10−12 |
1.82 × 10−11 |
1.23 × 10−10 |
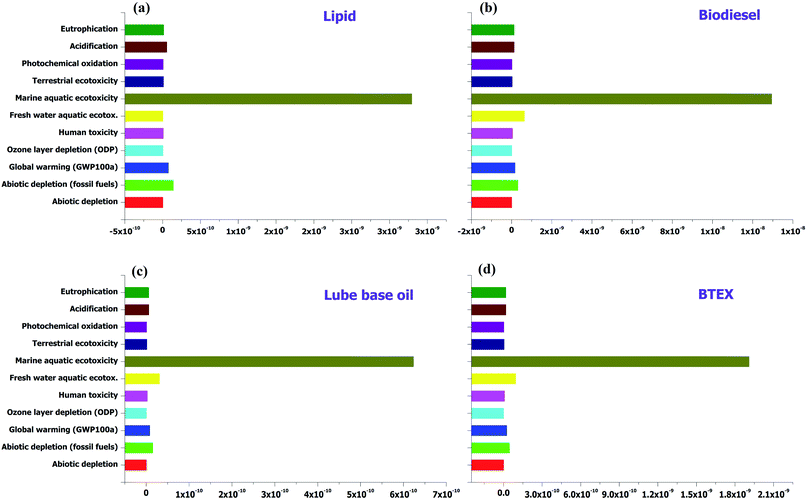 |
| Fig. 4 Impact assessment for conversion processes of (a) sugarcane bagasse to lipid; (b) lipid to biodiesel; (c) lipid to BTEX; and (d) lipid to lube base oil. | |
Individual emissions were calculated for the processes in kg CO2 equivalent (GWP), kg CFC-11 equivalent (ozone layer depletion) and kg P equivalent (eutrophication), as these environmental indicators are the main concern for environmental safety, as given in Table 3. The emissions for GWP are found to be 260.03, 572.16, 27.83 and 85.19 kg CO2 equivalent for non-polar lipid, lube base oil, biodiesel and BTEX processes. The estimated emissions for ozone layer depletion, for non-polar lipid lube base oil, biodiesel and BTEX processes are 1.88 × 10−7, 4.18 × 10−7, 2.00 × 10−5 and 6.14 × 10−5 kg CFC-11 equivalent, while in the eutrophication impact category the estimated emissions are as follows: 0.48 (non-polar lipid), 1.08 (lube base oil), 0.05 (biodiesel) and 0.15 (BTEX) kg P equivalent.
Table 3 Calculated emissions for the impact categories
Impact categories |
Emissions |
Units |
Characterization factor |
Lipid |
Biodiesel |
BTEX |
Lube base oil |
Climate change |
Carbon dioxide, in air |
kg CO2 equivalent |
1 |
3.22 |
0.34 |
1.05 |
0.01 |
Nitrogen oxides |
kg CO2 equivalent |
298 |
0.86 |
0.09 |
0.28 |
1.92 |
Methane |
kg CO2 equivalent |
25 |
2.32 × 10−8 |
2.34 × 10−9 |
7.11 × 10−9 |
5.15 × 10−8 |
Methane, tetrafluoro-, CFC-14 |
kg CO2 equivalent |
2310 |
2.69 × 10−6 |
2.86 × 10−7 |
8.77 × 10−7 |
5.97 × 10−6 |
Total emissions |
kg CO2 equivalent |
— |
260.03 |
27.83 |
85.19 |
572.16 |
Ozone layer depletion |
Methane, tetrafluoro-, CFC-14 |
kg CFC-11 equivalent |
0.07 |
2.69 × 10−6 |
2.86 × 10−4 |
8.77 × 10−4 |
5.97 × 10−6 |
Total emissions |
kg CFC-11 equivalent |
— |
1.88 × 10−7 |
2.00 × 10−5 |
6.14 × 10−5 |
4.18 × 10−7 |
Eutrophication |
Nitrogen oxides |
kg P equivalent |
0.56 |
0.86 |
0.09 |
0.28 |
1.92 |
Total emissions |
kg P equivalent |
— |
0.48 |
0.05 |
0.15 |
1.08 |
3.2. Uncertainty analysis
Monte-Carlo uncertainty analysis was carried out for four main unit processes (ESI Tables S1–S4†). The uncertainty graphs for the GWP of these processes are shown in Fig. 5. Uncertainty was quantified for each impact category by dividing the standard deviation by the mean. According to the IPCC, if the result of the division is more significant than 0.3, uncertainty is considered as large.17 The results of uncertainty analysis for the processes are presented in Table 4. After quantification of uncertainty, it was found that the uncertainty lies within the range (i.e., <0.3) for abiotic depletion, abiotic depletion (fossil fuels), acidification, global warming (GWP100a), eutrophication, freshwater aquatic ecotoxicity, and terrestrial ecotoxicity. However, for the marine aquatic ecotoxicity, ozone layer depletion (ODP) and human toxicity categories, uncertainty is slightly higher (i.e.,> 0.3), while for photochemical oxidation, the values are at the margin (i.e., 0.3) for lipid, biodiesel and BTEX unit operation and 0.33 for lube base oil.
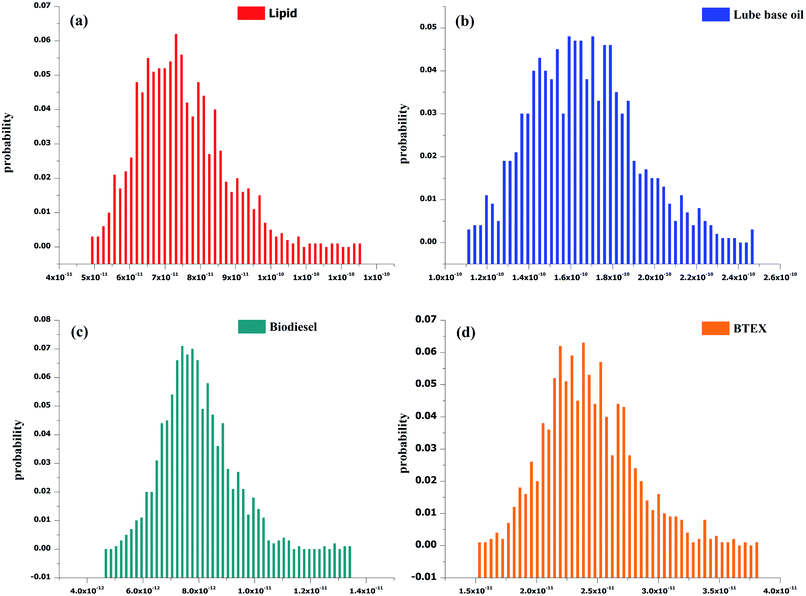 |
| Fig. 5 Uncertainty analysis for GWP (normalized values) of conversion processes of (a) sugarcane bagasse to lipid; (b) lipid to biodiesel; (c) lipid to BTEX; and (d) lipid to lube base oil; method: CML-IA baseline V3.05/EU 25, confidence interval 95%. | |
Table 4 Quantified uncertainties for all impact categories, for the defined processes
Impact category |
Lipid |
Biodiesel |
BTEX |
Lube base oil |
Abiotic depletion |
0.20 |
0.19 |
0.20 |
0.20 |
Abiotic depletion (fossil fuel) |
0.16 |
0.16 |
0.16 |
0.16 |
Global warming |
0.21 |
0.20 |
0.19 |
0.20 |
Ozone layer depletion (OLD) |
0.63 |
0.59 |
0.57 |
0.52 |
Human toxicity |
0.40 |
0.41 |
0.47 |
0.43 |
Freshwater aquatic ecotoxicity |
0.16 |
0.15 |
0.15 |
0.15 |
Marine aquatic ecotoxicity |
0.36 |
0.34 |
0.62 |
0.40 |
Terrestrial ecotoxicity |
0.28 |
0.26 |
0.29 |
0.27 |
Photochemical oxidation |
0.30 |
0.29 |
0.30 |
0.33 |
Acidification |
0.23 |
0.21 |
0.21 |
0.23 |
Eutrophication |
0.29 |
0.28 |
0.29 |
0.27 |
4. Discussion
Estimating emissions under any impact category is a prime necessity while performing any LCA. However, having a brief understanding of the potential sources for the emissions, their environmental effect, and strategies to mitigate the effects or of alternative ideas to adopt, adds significant value to the outcome of LCA. In this regard, the three main categories for which emissions have been calculated are concisely explained in this section.
4.1. Global warming potential
GWP can be defined as climate change due to the release of greenhouse gases (CO2, CH4, CFC-14b, NOx, etc.) by anthropogenic activities, resulting in an increase in global temperature. The noticeable effects of these gases on the environment include rising sea levels, disturbances in the immediate climate, forest fires, desertification and extinction of some plants and animal species, with the rising temperature.40–42 The primary cause for the release of these gases is by burning of fossil fuel during ploughing of fields by tractors at the time of sugarcane cultivation, transport of sugarcane from fields to mills, burning of leftover leafy traces on fields43 and during cogeneration of bagasse in mills. GWP is expressed over a time horizon of 100 years and has the reference unit kg CO2 equivalent.
4.2. Ozone layer depletion (OLD)
Damage to the ozone layer, present in the stratosphere, is caused by ozone-depleting gases, mainly chlorofluorocarbons (CFCs), hydrochlorofluorocarbons (HCFCs) and halons. There is no natural source of these gases; CFCs are used in insulation, refrigeration, and manufacture of polyurethane (plastic insulants), phenolics and firefighting equipment. CFCs have a significant impact on the ozone layer in comparison to HCFCs and other gases. The emission of these gases might result from the materials used in the packaging of chemicals and the equipment used for the manufacture of chemicals and materials used during the process, not directly but from the emissions taken into account from the reference database used by the software. It can be characterized as per the model given by the World Meteorological Organisation,44 and expressed in kg CFC-11 equivalent (chlorofluorocarbon-11 as the reference substance).
4.3. Eutrophication
Eutrophication refers to the enrichment of chemical nutrients in an ecosystem, which results in increased biomass production. Eutrophication occurs due to an increase in the concentration of nitrogen (N) and phosphorus (P) in ecosystems. This usually leads to increased algal growth (bloom) in water bodies at the expense of pre-existing species in that environment. It affects the biodiversity of the aquatic system, due to lack of oxygen by decomposition of algae. The potential sources of these nutrients are the fertilizers and manure used during sugarcane cultivation.45 Many case studies all over the world based on sugarcane utilizing processes have indicated that the major causes of eutrophication are the use of agrochemical and chemical fertilizers and emissions during their production.46,47 The N and P leach to underground water and contaminate nearby water bodies by field runoffs. It is estimated in kg P equivalent.
4.4. Uncertainty analysis
The data for sugarcane cultivation and generation of bagasse are highly variable in India.48 Therefore, it is one of the contributing factors for slightly higher uncertainties in the results, for some categories. The reported uncertainties, >0.3, for ozone layer depletion, human toxicity, and marine aquatic ecotoxicity have occurred mainly due to parameter uncertainty, temporal variability, spatial variability, and variability between objects or sources in the LCI.49 The higher estimated uncertainties for the ozone layer depletion category are due to the spatial (regional difference in inventories) and temporal (difference in yearly emission inventories) variability present for the responsible gases (as mentioned in Section 4.2).
The human toxicity potential refers to a unit of toxic chemical released into the environment. During the extraction of lipid and biodiesel production, considerable amounts of solvents (i.e., chloroform, methanol, and hexane) are used. These solvents are toxic, so they are used in closed loop systems to avoid their release into the environment. Also, 90% of the solvent is recovered for reuse. On the other hand, chemicals like arsenic, sodium dichromate, and hydrogen fluoride are used for electricity production from fossil resources. These chemicals are potentially toxic to human beings on direct and indirect exposure through the environment.44 Therefore, the higher uncertainty for human toxicity is mainly due to variation in data inventories for the use of toxic chemicals, in different electrical grids of different regions. Marine aquatic toxicity is usually due to the release of heavy metals into aquatic ecosystems. As none of the processes reported here involve any discharge of reaction waste into water bodies, the uncertainties might be solely due to variability in the database.
5. Conclusive remarks and recommendations
This paper reported an LCA for the first time for yeast lipid-based biofuels and chemicals from the Indian perspective. The emissions reported for each category after an assessment were found to be low and acceptable, at this scale. The uncertainty is also found to be lower for GWP, for all the processes. The yeast lipid generated by the fermentation of pentose sugar (extracted from sugarcane bagasse) is a high value and low volume product. This lipid has multiple applications, and can be converted into biodiesel, lube base oil and BTEX. The applications of these oleochemicals are well known in the chemical industry. However, the feedstock used during the process plays an essential role in making the process efficient in terms of better yield, low energy input, and higher substrate-to-product conversion with an acceptable range of environmental emissions. In this context, yeast lipid emerges as a potential alternative source for renewable energy. This study suggests the scope for the scale-up of this process up to 50 L fermentation (4.2 times, with respect to the mentioned volume, i.e., 12 L), as this work guarantees the quality of data used from experimental results. However, further scale-up of this process system to the industrial level cannot be proposed from this work, as the LCA results cannot necessarily be incremented in linear proportions with the lab scale results, due to mass production.18 However, the slightly higher uncertainties measured for ozone layer depletion, human toxicity, and marine aquatic ecotoxicity indicate the need for process development (to look for an alternative to toxic solvents and less energy consumption) or improving the LCI, to attain lower impact and range uncertainties for these categories.
Conflicts of interest
The authors declare that they have no conflicts of interest.
Funding sources
IUSSTF/DBT through GAP-3509 & DBT-PACE-BIRAC through GAP-3512.
Acknowledgements
The authors thankfully acknowledge Dr Anjan Ray, Director CSIR-IIP, for his constant motivation and support to this study, and for providing the necessary infrastructure.
References
- A. Singh and I. S. Olsen, Critical analysis of biochemical conversion, sustainability and life cycle assessment of algal biofuels, Appl. Energy, 2011, 88, 3548–3555 CrossRef CAS.
-
A. Singh and I. S. Olsen, Key issues in life cycle assessment of biofuels, in Sustainable Bioenergy and Bioproducts, Green Energy and Technology, ed. K. Gopalakrishnan, et al., 2012, Springer-Verlag London Limited, London, pp. 213–28 Search PubMed.
- D. Pant,
et al., Bioelectrochemical systems (BES) for sustainable energy production and product recovery from organic wastes and industrial wastewaters, RSC Adv., 2012, 2, 1248–1263 RSC.
- OECD-FAO Agricultural Outlook 2019-2028 © OECD/FAO 2019.
- S. Prasad, A. Singh and C. H. Joshi, Ethanol as an alternative fuel from agricultural, industrial and urban residues, Resour., Conserv. Recycl., 2007a, 50, 1–39 Search PubMed.
- S. Prasad,
et al., Ethanol production from sweet sorghum syrup for utilization as automotive fuel in India, Energy Fuels, 2007b, 21(4), 2415–2420 Search PubMed.
-
A. Singh, I. S. Olsen and D. Pant, Importance of life cycle assessment of renewable energy sources, in Life Cycle Assessment of Renewable Energy Sources, Green Energy and Technology, ed. A. Singh, et al., Springer-Verlag, London, 2013 Search PubMed.
-
Strategy Paper on Resource Efficiency, Niti Ayog, 2017 Search PubMed.
- Q. Li, W. Du and D. Liu, Perspectives of microbial oils for biodiesel production, Appl. Microbiol. Biotechnol., 2008, 80, 749–756 CrossRef CAS PubMed.
- J. M. Ageitos,
et al., Oily yeasts as oleaginous cell factories, Appl. Microbiol. Biotechnol., 2011, 90, 1219–1227 CrossRef CAS PubMed.
- P. Meeuwse,
et al., Lipids from yeast and fungi: tomorrow's source of biodiesel?, Biofuels, Bioprod. Biorefin., 2013, 7, 512–524 CrossRef CAS.
- R. I. Sitepu,
et al., Oleaginous yeasts for biodiesel: current and future trends in biology and production, Biotechnol. Adv., 2014, 32, 1336–1360 CrossRef PubMed.
- J. L. Adrio, Oleaginous yeasts: promising platforms for the production of oleochemicals and biofuels, Biotechnol. Bioeng., 2017, 114, 1915–1920 CrossRef CAS PubMed.
- S. Bandhu,
et al., Single cell oil from oleaginous yeast grown on sugarcane bagasse-derived xylose: an approach toward novel biolubricant for low friction and wear, ACS Sustainable Chem. Eng., 2018, 6(1), 275–283 CrossRef CAS.
- V. K. Probst,
et al., Oleaginous yeast: a value-added platform for renewable oils, Crit. Rev. Biotechnol., 2015, 36, 942–955 CrossRef PubMed.
- S. Dutta, F. Neto and C. M. Coelho, Microalgae biofuels: a comparative study on techno-economic analysis & life-cycle assessment, Algal Res., 2016, 20, 44–52 CrossRef.
-
A. McMurray, T. Pearson and F. Casarim, Guidance on Applying the Montecarlo Approach to Uncertainty Analyses in Forestry and Greenhouse Gas Accounting, 2017 Search PubMed.
-
M. Shibasaki, Upscaling Effect and Life Cycle Assessment, 13th CIRP International Conference on Life Cycle Engineering, Leuven, 2006 Search PubMed.
- S. Kamat,
et al., Coupled production of single cell oil as biodiesel feedstock, xylitol and xylanase from sugarcane bagasse in a biorefinery concept using fungi from the tropical mangrove wetlands, Bioresour. Technol., 2013, 135, 246–253 CrossRef CAS PubMed.
- A. A. Koutinas, A. Chatzifragkou and N. Kopsahelis, Design and techno-economic evaluation of microbial oil production as a renewable resource for biodiesel and oleochemical production, Fuel, 2014, 116, 566–577 CrossRef CAS.
- D. N. Orfield,
et al., Growing algae for biodiesel on direct sunlight or sugars: a comparative life cycle assessment, ACS Sustainable Chem. Eng., 2015, 3, 386–395 CrossRef.
- H. Karlsson,
et al., A systems analysis of biodiesel production from wheat straw using oleaginous yeast: process design, mass and energy balances, Biotechnol. Biofuels, 2016, 9, 229 CrossRef PubMed.
- S. Parsons,
et al., Techno-economic analysis (TEA) of microbial oil production from waste resources as part of a biorefinery concept: assessment at multiple scales under uncertainty, J. Chem. Technol. Biotechnol., 2019, 94(3), 701–711 CrossRef CAS.
- G. M. Varanda, G. Pinto and F. Martins, Life cycle analysis of biodiesel production, Fuel Process. Technol., 2011, 92, 1087–1094 CrossRef.
- C. Pieragostini, C. M. Mussati and P. Aguirre, On process optimization considering LCA methodology, J. Environ. Manage., 2012, 96, 43–54 CrossRef PubMed.
- P. Pawelzik,
et al., Critical aspects in the life cycle assessment (LCA) of bio-based materials – reviewing methodologies and deriving recommendations, Resour., Conserv. Recycl., 2013, 73, 211–228 CrossRef.
-
ISO, Environmental Management Life Cycle Assessment, European Standard EN ISO 14040 and 14044, International Standardization Organization, Switzerland, 2006 Search PubMed.
-
M. Marinussen, et al., LCI Data for the Calculation Tool Feedprint for Greenhouse Gas Emissions of Feed Production and Utilization, Background Data Report on Cultivation, 2012, version 2012, part 7/7: other plants Search PubMed.
- I. Tsiropoulos,
et al., Life cycle assessment of sugarcane ethanol production in India in comparison to Brazil, Int. J. Life Cycle Assess., 2014, 19(5), 1049–1067 CrossRef CAS.
-
S. Bandhu, et al., Heterocatalytic transesterification of single cell oil: lignocellulosic biomass to biodiesel, International Conference on Environment and Energy (ICEE), Hyderabad, 2014 Search PubMed.
- O. Singh,
et al., Converting lignocellulosic pentosan derived yeast lipid into aromatics: biomass to BTX, ACS Sustainable Chem. Eng., 2019, 7(15), 13437–13445 CrossRef CAS.
- C. M. Gopinathan and R. Sudhakaran, Biofuels: opportunities and challenges in India, In Vitro Cell. Dev. Biol.: Plant, 2009, 45(3), 350–371 CrossRef.
-
http://www.agritech.tnau.ac.in/expert_system/sugar/cultivationpractices.html, accessed October 2019.
-
S. Kumar, Bio-ethanol Production Inventories, Simapro Software Development India Pvt. Ltd, New Delhi, 2013 Search PubMed.
-
MoEF, Technical EIA Guidance Manual for Sugar Industry, Ministry of Environment and Forests, Government of India, Hyderabad, 2010 Search PubMed.
- D. Dasgupta,
et al., Cultivation of oleaginous yeast Rhodotorula mucilaginosa IIPL32 in split column airlift reactor and its influence on fuel properties, Biocatal. Agric. Biotechnol., 2017, 10, 308–316 CrossRef.
- P. Thliveros, E. Uckun Kiran and C. Webb, Microbial biodiesel production by direct methanolysis of oleaginous biomass, Bioresour. Technol., 2014, 157, 181–187 CrossRef CAS PubMed.
-
Intergovernmental Panel on Climate Change, IPCC Fourth Assessment Report, The Physical Science Basis, 2007, http://www.ipcc.ch/ipccreports/ar4-wg1.htm Search PubMed.
-
https://www.pre-sustainability.com/download/SimaPro8IntroductionToLCA.pdf, accessed October 2019.
-
https://www.thehindubusinessline.com/news/science/global-warming-impacts-on-india-will-be-huge-ipcc/article25157254.ece, accessed October 2019.
-
IPCC Working group III fourth assessment report, Summary for Policymakers, 2007, https://www.ipcc.ch/site/assets/uploads/2018/03/ar4_wg2_full_report.pdf, accessed October 2019 Search PubMed.
-
https://en.wikipedia.org/wiki/Climate_change_in_China, accessed October 2019.
-
https://economictimes.indiatimes.com/industry/energy/oil-gas/cabinet-okays-ethanol-projects-funding/articleshow/68208569.cms, accessed October 2019.
-
World Metrological Organization (WMO), Scientific Assessment of Ozone Depletion: Global Ozone Research and Monitoring Project, WHO, Geneva, Switzerland, 1991, vol. 2 Search PubMed.
-
A. P. Acero, C. Rodríguez and A. Ciroth, Impact Assessment Methods in Life Cycle Assessment and Their Impact Categories, LCIA Methods, 2017, Version: 1.5.6 Search PubMed.
- T. Silalertruksa, P. Pongpat and S. H. Gheewala, Life cycle assessment for enhancing environmental sustainability of sugarcane biorefinery in Thailand, J. Cleaner Prod., 2016, 140(2), 906–913 Search PubMed.
- C. C. S. Moore, A. R. Nogueira and L. Kulay, Environmental and energy assessment of the substitution of chemical fertilizers for industrial wastes of ethanol production in sugarcane cultivation in Brazil, Int. J. Life Cycle Assess., 2017, 22, 628–643 CrossRef CAS.
- S. Soam,
et al., Life cycle assessment of fuel ethanol from sugarcane molasses in northern and western India and its impact on Indian biofuel programme, Energy, 2015, 83, 307–315 CrossRef CAS.
- J. A. M. Huijbregts, Application of uncertainty and variability in LCA. Part I: a general framework for the analysis of uncertainty and variability in life cycle assessment, Int. J. Life Cycle Assess., 1998, 3(5), 273–280 CrossRef.
Footnote |
† Electronic supplementary information (ESI) available. See DOI: 10.1039/c9se00540d |
|
This journal is © The Royal Society of Chemistry 2020 |
Click here to see how this site uses Cookies. View our privacy policy here.