DOI:
10.1039/D0RA06639G
(Paper)
RSC Adv., 2020,
10, 40047-40054
Ce regulated surface properties of Mn/SAPO-34 for improved NH3-SCR at low temperature†
Received
31st July 2020
, Accepted 20th October 2020
First published on 4th November 2020
Abstract
Ce modified MnOx/SAPO-34 was prepared and investigated for low-temperature selective catalytic reduction of NOx with ammonia (NH3-SCR). The 0.3Ce–Mn/SAPO-34 catalyst had nearly 95% NO conversion at 200–350 °C at a space velocity of 10
000 h−1. Microporous SAPO-34 as the support provided the catalyst with increased hydrothermal stability. XPS and H2-TPR results proved that the Mn4+ and Oα content increased after incorporation of Ce, this promoted the conversion of NO at low temperature via a ‘fast SCR’ route. NH3-TPD measurements combined oxidation experiments of NO, NH3 indicated the reduction of both the surface acidity and the amount of acid sites, which effectively decreased the NH3 oxditaion to NO or N2O at elevated temperature and promoted the catalytic selectivity for nitrogen. A redox cycle between manganese oxide and Ce was assumed for the active oxygen transfer and facilitated the catalyst durability.
1 Introduction
Selective catalytic reduction by NH3 (NH3-SCR) is known as one of the most efficient ways to remove NOx from stationary sources.1 The involved major reaction is |
4NH3 + 4NO + O2 = 4N2 + 6H2O
| (1) |
The widely used commercial catalysts for NH3-SCR are V2O5–WO3/TiO2 and V2O5–MoO3/TiO2.2,3 As the catalyst works at a relative high temperature of 300–400 °C, it is usually located upstream of both the desulfurizer and the electrostatic precipitator, which causes the toxicity of vanadium species by sulfur and dust in the flue gas.4,5 Therefore, it is of great significance to develop low-temperature NH3-SCR catalysts so that the SCR reactor can be placed downstream of the desulfurizer and electrostatic precipitator to significantly improve the economics of NH3-SCR.
Transition metal including Fe, Mn, Cu and Ni supported on different commercial carriers have been investigated for the low-temperature NH3-SCR.6–8 Manganese based catalysts show good performances of low-temperature catalytic activity, for manganese oxides containing various types of labile oxygen and different oxidation states of Mn (Mn2+, Mn3+, and Mn4+), which are necessary to complete a catalytic cycle.9–12 But the selectivity for nitrogen was limited at elevated temperature, for the obvious oxidation of ammonia on manganese oxide surface, especially on the highly crystalline surface. Therefore, the remediation of redox properties of manganese oxide would be a viable route for inhibiting the ammonia oxidation. The doped manganese oxide has been investigated for NH3-SCR catalyst.13 As an inexpensive and a relatively nontoxic material, Ce has also been widely used as doping agent for its excellent redox properties and the great oxygen storages associated with plenty of oxygen vacancies.14–16 Ce modified Fe-ZSM-5 catalyst showed an improved NH3-SCR activity, which was ascribed to the enhanced oxidation of NO to NO2.17 Yang and Qi carried out systematically studies on Ce–Mn mixed oxide catalyst without supports. The results yielded nearly 100% conversion for NO at 120 °C at a high space velocity of 42
000 h−1, but N2O was observed as the temperature higher than 150 °C, indicated the complexity of the oxidation mechanism.18
Compared with the pure manganese oxide, supported one will provide highly spreading manganese oxide and would decrease the crystalline which are benefited for increase catalytic selectivity.19–23 So combined with the consideration of mechanical strength for engineering allocation, the conventional supported manganese oxide had been widely applied for this low-temperature SCR catalyst.20 It was reported that the molecular sieves (ZSM, beta) show high activities in NH3-SCR when used in supported Cu catalyst, but suffer from narrow activity window and hydrothermal deteriorations, which restrict its further commercial applications for NH3-SCR.24,25 As a chabazite type microporous molecular sieve with CHA structure, SAPO-34 can not only significantly improve the activity and selectivity of the composite catalyst,26,27 but also has excellent hydrothermal stability and resistance to SO2 poisoning, thereby prolonging the service life of the catalyst in the high-activity zone.28,29 Much of significant contributions had been made for Cu-based zeolite catalyst.30 The previous researches revealed the exact location of active sites and confirmed the isolated Cu2+ ions as active sites over Cu/SSZ-13 catalysts and Cu/CHA catalyst.31,32 Furthermore, Li Wei and co-work clarified the isolated Cu2+ ion located on the plane of the six-membered ring of SAPO-34, which appeared to be responsible for the excellent SCR activity and N2 selectivity.33 Based on the previous reorganization of Cu–zeolite based SCR catalysts, the position of the active species on molecular sieves reflected the interaction of active species with zeolite supports, and finally composed the surface acidity and redox cycle exist along with NH3-SCR route. Therefore, correlation the surface redoxity and acidity cycle of active species with the NH3-SCR activity and selectivity would provide a directly understanding for the zeolite-based SCR catalyst.
Therein, based on microporous zeolite materials as support and manganese oxides as active species aimed to the low temperature NH3-SCR process, we prepared the SCR catalyst of Ce modified manganese oxides supported on SAPO-34 zeolite. The as-prepared catalysts were characterized and the effects of Ce on the surface property such as redoxity and acidity of the Mn/SAPO-34 catalyst were analysed. The catalytic performances of Ce modified Mn/SAPO-34 catalyst as well as the hydrothermal stability of the catalyst were evaluated. The surface acidity and redox cycles of Ce modified Mn/SAPO-34 catalyst was discussed and correlated with NH3-SCR performances.
2 Experimental section
2.1 Catalyst preparation
The synthesis of SAPO-34 molecular sieve: with phosphoric acid, pseudo boehmite, tetraethyl orthosilicate and morpholine as sources, a gel with the molar ratio of 1.0 Al2O3
:
1.1 P2O5
:
0.6 SiO2
:
2.1 morpholine
:
66.0 H2O was prepared. After aging at room temperature for 12 hours, the temperature was increased to 200 °C at a heating rate of 3°C min−1 and kept at this temperature for 48 hours to crystallize. The obtained solid crystallized product was washed with deionized water to neutrality, dried and then calcined at 550 °C for 5 hours to obtain SAPO-34 molecular sieve. The synthesis of Mn/SAPO-34 or xCe–Mn/SAPO-34: the ultrasonic impregnation method was used to synthesized the Mn/SAPO-34 or xCe–Mn/SAPO-34. Typically, a certain amount of acetylacetone manganese(II) salt dehydrator, or cerium nitrate mixed with acetylacetone manganese(II) salt dehydrate (only changed the Ce/Mn ratio and kept the total amount of Ce (Ce(NO)3·6H2O) and Mn (Mn(CH3COO)2) precursors consistent (0.8922 g) for all samples) was dissolved in acetone (60 mL) at room temperature. Then the SAPO-34 powder (3.0 g) was added into the above solution with 1 h ultrasonic treatment to obtain catalyst precursors after evaporating the solvent, followed by calcined at 400 °C in air for 5 hs. The resulted catalysts were designated as Mn/SAPO-34 or xCe–Mn/SAPO-34, where x represented the mole ratio of the Ce/Mn, specifically from 0.1 to 0.4.
2.2 Catalytic activity measurements
The NH3-SCR activity was measured in a continuous flow fixed-bed stainless steel reactor using 1.57 mL 40–60 mesh catalyst at atmospheric pressure. The simulated flue gases consisted of 500 ppm NO, 500 ppm NH3, 5 vol% O2, and balanced with N2. The gas hourly space velocity (GHSV) was 10
000 h−1. The concentrations of NO, NO2, N2O and NH3 were determined using a flue gas analyser (Sensonic 4000, Sensonic). The reaction temperature was scheduled from 100 °C to 450 °C. The NO conversion (ηNO) and N2 selectivity were calculated by measuring the concentration of effluent gases according to the following equations: |
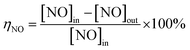 | (2) |
|
 | (3) |
2.3 Characterization of catalyst
The specific surface areas of the catalysts were measured by nitrogen adsorption and desorption method on 3H-2000PS1 (BeiShiDe instrument, China), using the Brunauer–Emmett–Teller (BET) model. The scanning electron microscopy (SEM) images were obtained using a field-emission scanning electron microscopy (JSM-7800F, JEOL, Japan), at the operation voltage of 5 kV. The X-ray diffraction (XRD) patterns of the samples were obtained with a Rigaku D/max-3C diffract meter with Cu Kα radiation (λ = 1.54056 Å) operating at 40 kV and 30 mA. The XRD patterns were collected in the 2θ range of 5–90° with a scanning step size of 0.02° and scanning rate of 10° min−1. The X-ray photoelectron spectroscopy (XPS) was performed on a PHI quant era II (Ulvac-Phi, Japan) under an ultra-high vacuum, using a monochromated Al Kα source (1486.6 eV) at 42.1 W. The measurements were performed at 20 eV pass energy, 0.1 eV step and 0.15 dwelling time. All the binding energies were corrected with reference to the C 1s peak at 284.8 eV.
The temperature programmed reduction with hydrogen (H2-TPR) were conducted on an automatic multifunction adsorption instrument (TP-5080, China) with 50 mg sample, the test ranged from 30 °C to 700 °C at a heating rate of 10 °C min−1 with a reducing gas consist of 10 vol% H2 and 90% N2 at the 30 mL min−1 flow rate. The NH3-temperature programmed desorption (NH3-TPD) measurements were carried out under the similar conditions with 100 mg sample after purged with He at 300 °C for half an hour. The inlet gas consisted of 5 vol% NH3 balanced with helium.
3 Results and discussion
3.1 NH3-SCR performances
The Ce modified Mn/SAPO-34 catalysts exhibited a superior catalytic activity, with the NO conversion exceeding 80% in the range of 200–350 °C, achieved the best performance at 300 °C. The addition of cerium obviously expanded the temperature windows towards the lower temperature range, accompanying with the improved NO conversion (>90%) at 200–350 °C. The active temperature window of the Ce modified catalyst was wider about 100 °C than the unmodified sample, whose diminished temperature windows was 250–300 °C and NO conversion below 85%.
The N2 selectivity of the catalysts was displayed in Fig. 1b. The Ce–Mn/SAPO-34 catalysts with different Ce/Mn ratios showed an increased N2 selectivity as cerium introduced, and the best performance of the catalysts for N2 selectivity (over 90% from 100–400 °C) was achieved at the Ce/Mn molar ratio of 0.3, illustrating that the presence of Ce enhanced the main reaction with the product of N2.
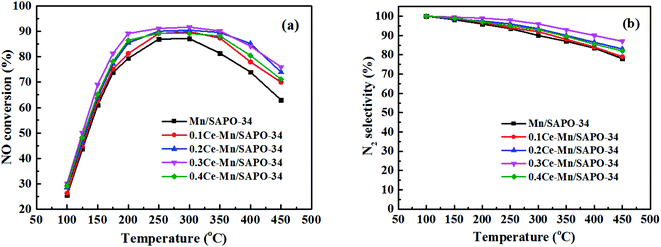 |
| Fig. 1 Catalytic performances of Mn/SAPO-34 and Ce–Mn/SAPO-34: (a) NO conversion, (b) the N2 selectivity in the NH3-SCR reaction. (The reaction condition: [NH3] = [NO] = 500 ppm, [O2] = 5 vol%, N2 balance and GHSV = 10 000 h−1). | |
3.2 Hydrothermal stability of catalysts
The catalyst resistance to H2O is one of the important indicators for the SCR catalyst. The hydrothermal stability of Mn/SAPO-34 and Ce–Mn/SAPO-34 catalysts were further studied by performing steaming treatments at 700 °C for 12 hours in flowing gas containing 10 vol% H2O and 90% air. The catalytic performances of the as-aged catalyst were presented in Fig. 2. It can be seen that the aged Mn/SAPO-34 catalyst showed poor activity, especially at low-temperatures (i.e., 150–200 °C); whereas the aged Ce modified Mn/SAPO-34 catalysts could maintain activity at low-temperatures range and show some declined NO conversion at the elevated temperature range. Among those, the aged 0.3Ce–Mn/SAPO-34 catalyst exhibited the optimal catalytic performance with the maximum value of NO conversion nearly 80% in the range of 200–300 °C.
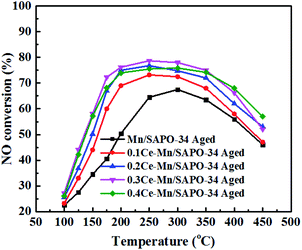 |
| Fig. 2 Catalytic performances of hydrothermally aged catalysts in the NH3-SCR process. (Hydrothermal aging conditions: 10 vol% H2O and 90% air, total flow rate = 200 mL min−1, aging time = 12 hours, aging temperature = 700 °C. The reaction condition: [NH3] = [NO] = 500 ppm, [O2] = 5 vol%, N2 balance and GHSV = 10 000 h−1). | |
3.3 Morphology and physical properties of the catalyst
3.3.1 Texture analysis. The texture structures of the Mn/SAPO-34 and Ce–Mn/SAPO-34catalysts were investigated by BET (Fig. S1a†). Type I isotherm curves for the catalysts were observed, typical for a microporous solid. The pores of the Mn/SAPO-34 and Ce–Mn/SAPO-34 catalysts are mostly distributed in the range of 3.3–3.7 nm (Fig. S1b†). Based on the BET specific surface area and pore volume of the Mn/SAPO-34 and Ce–Mn/SAPO-34 catalysts (Table S1†), it could be concluded that the modification of Ce significantly reduces the BET surface area, pore volume and pore diameter of the catalyst. For Mn/SAPO-34, the BET surface area and pore diameter were 416.57 m2 g−1 and 3.66 nm, as n(Ce/Mn) in Ce–Mn/SAPO-34 catalysts increased from 0.1 to 0.4, the BET surface area and pore diameter were decreased to 370.07 m2 g−1 and 3.32 nm, respectively, indicating that the part of the cerium oxide entered into the interior of the SAPO-34 molecular sieve carrier in addition to loading on the surface.The aged catalyst showed declined BET area and pore volumes. For aged 0.3Ce–Mn/SAPO-34 catalysts, the BET areas and pore volume decreased from 375.75 to 359.21 m2 g−1, and 0.169 to 0.0514 cm3 g−1 respectively (Fig. S2 and Table S2†). The observed decreased NO conversion over the aged-catalyst would be ascribed in certain degree to the diminish of BET area and pore volume.
3.3.2 SEM and XRD analysis. The SEM image (Fig. 3) depicts the surface morphology of the Mn/SAPO-34 and Ce–Mn/SAPO-34 catalysts, with a crystal size of about 3 μm and with a typical cubic structure of CHA,34 which is consistent with the following XRD results. The Mn/SAPO-34 catalyst exhibits a smooth surface, and there are some small particles between the cubic or on the surface. For the Ce modified catalysts, the surface is covered with randomly shaped material. As Ce content increased, the crystallinity of the Ce–Mn/SAPO-34 catalysts reduced significantly, this was consisted with XRD results (Fig. 4).
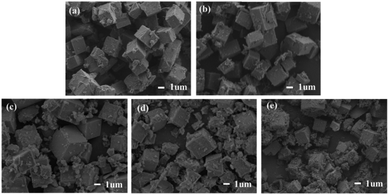 |
| Fig. 3 The SEM images of Mn/SAPO-34 and Ce–Mn/SAPO-34 catalysts: (a) Mn/SAPO-34, (b) 0.1Ce–Mn/SAPO-34, (c) 0.2Ce–Mn/SAPO-34, (d) 0.3Ce–Mn/SAPO-34, (e) 0.4Ce–Mn/SAPO-34. | |
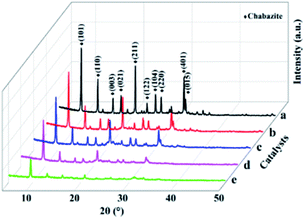 |
| Fig. 4 The XRD patterns of Mn/SAPO-34 and Ce–Mn/SAPO-34 catalysts. (a) Mn/SAPO-34, (b) 0.1Ce–Mn/SAPO-34, (c) 0.2Ce–Mn/SAPO-34, (d) 0.3Ce–Mn/SAPO-34, (e) 0.4Ce–Mn/SAPO-34. | |
For Mn/SAPO-34 and Ce–Mn/SAPO-34 catalyst, both have diffraction peaks of the chabazite phase, an indication of typical CHA structures (Fig. 4). In addition, no diffraction peaks associated with cerium oxides or manganese oxides were observed. This indicates that the Ce or Mn were predominantly present in amorphous combined with the SEM results. As compared with the Mn/SAPO-34 catalyst, the intensities of the main diffraction peak of Ce–Mn/SAPO-34 catalysts gradually diminished by increasing the Ce content, implying the modification of Ce reduced the crystallinity of Mn/SAPO-34 catalyst. In particular, the XRD pattern of the 0.4Ce–Mn/SAPO-34 catalyst with the largest Ce loading amount where the intensity of the reflection with maximum is much lower than the one in Mn/SAPO-34 catalyst.
3.3.3 NH3-TPD of the catalyst. The surface acidity of the catalysts was obtained based on NH3-TPD measurement (Fig. 5, Table S3†). The two NH3 desorption peaks were observed over a wide temperature range due to the variability of the adsorbed NH3 species with different thermal stabilities. The desorption peak around 170 °C, can be attributed to physical or weakly adsorbed NH3. The peak between 380 °C and 405 °C, can be attributed to stronger acid sites generated by the incorporation of silicon atoms into the framework of SAPO-34 molecular sieves during the formation process. After Ce doping, the weak acid sites of the catalysts showed little change, but the peaks related to the NH3 desorbing from strong acid sites were observed shifting to lower temperature, namely, from c.a. 400 °C on Mn/SAPO-34 to 374 °C over 0.3Ce–Mn/SAPO-34, accompanying with the weakening of the peak. This indicates the weak acidity and reduced amount of acid sites, which was responsible for the suppressed NH3 oxidation reaction and inverse the enhanced catalytic selectivity for nitrogen.
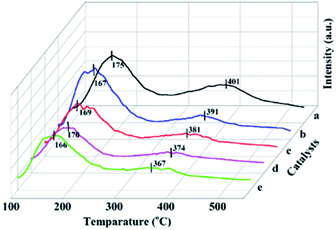 |
| Fig. 5 NH3-TPD profiles of Mn/SAPO-34 and Ce–Mn/SAPO-34 catalysts. (a) Mn/SAPO-34, (b) 0.1Ce–Mn/SAPO-34, (c) 0.2Ce–Mn/SAPO-34, (d) 0.3Ce–Mn/SAPO-34, (e) 0.4Ce–Mn/SAPO-34. | |
3.3.4 H2-TPR analysis. The redox ability over the catalysts containing Mn and Ce species is considered a key factor for the catalytic cycle of NH3-SCR reaction.35 which was demonstrated via H2-TPR measurement (Fig. 6). Three reduction peaks were observed in the range of 300–700 °C for the Mn/SAPO-34 catalyst, the low-temperature reduction peak at 384 °C could correlate to the reduction of MnO2 to Mn2O3, and the reduction peak near 494 °C, corresponding to the reduction of Mn2O3 to Mn3O4. Meanwhile, the high-temperature reduction peak at 630 °C was interpreted as a reduction of Mn3O4 to MnO.36 The following equation depicted the reduction process of MnOx in Mn/SAPO-34 catalyst.37 |
MnO2 → Mn2O3 → Mn3O4 → MnO
| (4) |
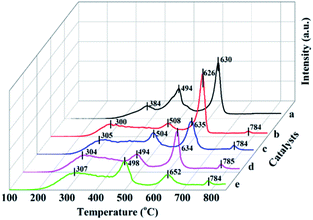 |
| Fig. 6 H2-TPR profiles of Mn/SAPO-34 and Ce–Mn/SAPO-34 catalysts. (a) Mn/SAPO-34, (b) 0.1Ce–Mn/SAPO-34, (c) 0.2Ce–Mn/SAPO-34, (d) 0.3Ce–Mn/SAPO-34, (e) 0.4Ce–Mn/SAPO-34. | |
For the Ce modified catalysts a broad peak is observed around 300 °C, which show much broader than that of Mn/SAPO-34 catalyst. The initial temperature of the peak over the Ce modified catalyst shifted to lower temperature, from 384 °C to 300 °C. This indicates the introduction of Ce not only alters the surface acidities, but also enhances the redox activity at low-temperature via the interaction between Mn and Ce species. This would be responsible for the increased low-temperature catalytic activity over Ce modified catalyst.
3.3.5 XPS analysis. The surface chemical composition and oxidation states of these synthesized catalysts were further investigated by XPS. High resolution spectra from Ce 3d, Mn 2p, and O 1 s are displayed in Fig. 7. For the Ce 3d spectrum (Fig. 7a), all samples exhibited eight characteristic peaks in the range of 920–875 eV, and are labelled as u′′′, u′′, u′, u, v′′′, v′′, v′, and v. The u′ and v′ peaks can be attributed to Ce3+ species, while the u′′′, u′′, u, v′′′, v′′, and v peaks can be assigned to Ce4+ species.38 From these peaks, we can learn that the Ce4+ oxidation state is predominant.
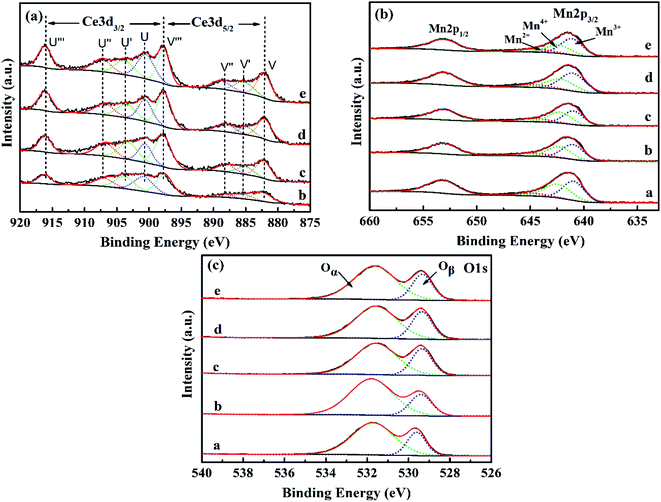 |
| Fig. 7 (a) Mn 2p, (b) Ce 3d and (c) O 1s XPS spectra of Mn/SAPO-34 and Ce–Mn/SAPO-34 catalysts. a: Mn/SAPO-34, b: 0.1Ce–Mn/SAPO-34, c: 0.2Ce–Mn/SAPO-34, d: 0.3Ce–Mn/SAPO-34, e: 0.4Ce–Mn/SAPO-34. | |
For the Mn 2p spectrum (Fig. 7b), two main peaks (643 eV and 654 eV) are apparently attributed to Mn 2p3/2 and Mn 2p1/2. By performing peak-fitting deconvolutions, the Mn 2p3/2 peaks can be divided into three characteristic peaks, which are assigned to Mn3+ (640.4 eV), Mn4+ (642.2 eV) and Mn2+ (644.5 eV), respectively. Previous studies have shown that Mn4+ species have favourable redox properties for NO conversion.16 Therefore, the relative content of surface Mn4+ (Mn4+/(Mn2+ + Mn3+ + Mn4+)) and Ce3+(Ce3+/(Ce3+ + Ce4+)) of these Ce–Mn/SAPO-34 catalysts were calculated, and listed in Table 1. The surface Mn4+ content of the 0.3Ce–Mn/SAPO-34 catalyst was higher than that over Mn/SAPO-34 catalyst. More specifically, at low loadings, the activity and selectivity increased with the increase of Ce loading (c.a. the atomic ratio of Ce/Mn gradually increase), and the best catalytic performance appeared at the Ce/Mn ratio of 49.05%, it gave 90.3% NO conversion and 98.5% selectivity for N2. However, the activity and selectivity would decrease significantly when the Ce/Mn ratio is higher than 49.05%. It furtherly confirmed that this catalytic system showed synergic effect between Ce and Mn and this subsequently improved the activity and selectivity of NH3-SCR. (Table S4†) This was attributed to the electronic interactions between manganese oxide and Ce, which consequently resulted in the redox equilibrium of Mn3+ + Ce4+ ↔ Mn4+ + Ce3+ shifting to the Mn4+ formation.
Table 1 The surface composition and states of the catalysts from XPS analysis
Samples |
Atomic concentration (%) |
Atomic ratio (%) |
Ce |
Mn |
O |
Ce/Mn |
Ce3+/(Ce3+ + Ce4+) |
Mn4+/(Mn2+ + Mn3+ + Mn4+) |
Oα/(Oα + Oβ) |
Mn/SAPO-34 |
0 |
18.24 |
47.88 |
0.00 |
0 |
46.22 |
71.84 |
0.1Ce–Mn/SAPO-34 |
1.52 |
16.31 |
45.63 |
9.32 |
11.54 |
48.35 |
74.38 |
0.2Ce–Mn/SAPO-34 |
4.19 |
15.35 |
43.35 |
27.30 |
12.32 |
47.61 |
75.65 |
0.3Ce–Mn/SAPO-34 |
6.95 |
14.17 |
42.58 |
49.05 |
13.92 |
51.27 |
76.98 |
0.4Ce–Mn/SAPO-34 |
9.24 |
12.63 |
40.65 |
73.16 |
13.28 |
43.58 |
76.36 |
The O 1 s spectrum (Fig. 7c) of these synthesized catalysts, which exhibited a strong peak at 529.1 eV, and a shoulder at a higher binding energy of 531.2 eV, attributable to lattice oxygen (labelled as Oβ) and adsorbed oxygen (labelled as Oα) on the surface of these samples, respectively.39 It has been widely reported that oxygen in the gas phase can be activated by oxygen vacancies on the surface of deNO catalysts to form surface adsorbed oxygen. This effect may also enhance catalytic performance in the NH3-SCR reaction.40 Furthermore, a process of oxygen storage/release betweenCe3+ and Ce4+ has been proposed in the following equations: (a) 2CeO2 → Ce2O3 + O* (adsorbed oxygen) and (b) Ce2O3 + 1/2O2 → 2CeO2. The increased Oα content can promote the oxidation of NO to NO2 and enhance the catalytic performance of the low-temperature deNO catalysts through a “fast NH3-SCR” route.
3.4 Redox performances of Ce–Mn/SAPO-34 catalyst
The oxidation of NH3 to NOx was examed (Fig. 8). Here, N2O and NO generated in the NH3 oxidation reaction were detected as temperature higher than 250 °C, and the amount of N2O and NO increased with the temperature. Compared with the Mn/SAPO-34 catalyst, the Ce–Mn/SAPO-34 catalyst exhibits lower N2O and NO concentration in the NH3 oxidation product. The results indicated the NH3 oxidation was suppressed on Ce modified catalyst at elevated temperature, by reducing acid amount and weak acidity on surface as expressed by NH3-TPD measurement, leading to the improved catalytic selectivity performance of NH3-SCR.
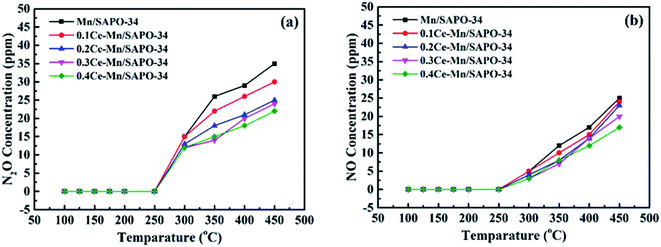 |
| Fig. 8 The concentration of N2O (a) and NO (b) generated in the NH3 oxidation. (The reactant condition: [NH3] = 500 ppm, [O2] = 5 vol%, N2 balance and GHSV = 10 000 h−1). | |
With Ce modified Mn/SAPO-34 catalyst, the NO oxidation activity increased significantly (Fig. 9), which suggested that the addition of Ce can increase the oxidation rate of NO to NO2. This was ascribed to the excellent redox properties associated with the existence of the Ce4+/Ce3+ redox couple and high oxygen storage/release capacity, which corresponding to the oxygen vacancies at interface between metal oxides. Therefore, the higher NO conversion was observed via promoted NO oxidation to NO2 at low-temperature, resulted from the ‘fast NH3-SCR’ route.28,29
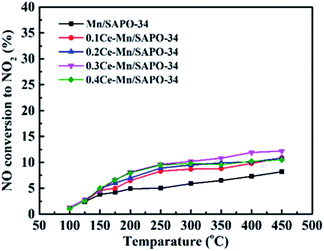 |
| Fig. 9 NO oxidation to NO2 experiment. (The reactant condition: [NO] = 500 ppm, [O2] = 5 vol%, N2 balance and GHSV = 10 000 h−1). | |
Therefore, the introducing of Ce regulated the following cycle by inducing the formation of Mn4+ at low temperature and reducing the acidity and the amount of acid sites on surface of Ce–Mn/SAPO-34 catalyst (Scheme 1), following Mn3+ + Ce4+ → Mn4+ + Ce4+. The enriched Mn4+ facilitated the NO oxidation to NO2, and improved the conversion of NO at low-temperatures following a fast NH3-SCR'route. Subsequently, the partially reduced Ce was oxidized to Ce4+ accompanying with the generation of active oxygen species. The weak acidity and reduced acid amount suppressed the reaction of NH3 oxidation to N2O or NO, which would improve the selectivity for nitrogen at elevated temperature.
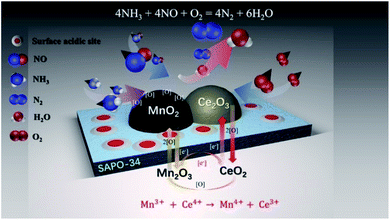 |
| Scheme 1 The catalytic mechanism schematic diagram for Ce–Mn/SAPO-34 in ‘NH3-SCR’ process. | |
4 Conclusions
In summary, Ce modified MnOx/SAPO-34 catalysts were prepared and evaluated for low-temperature NH3-SCR. The as-prepared catalysts showed high activity and selectivity for NO reduction with NH3 at low-temperature. Above 90% NO conversion was obtained on 0.3Ce–Mn/SAPO-34 catalyst at 200 °C with a GHSV of 10
000 h−1. Ce could substantially enhance the redox activity of Mn/SAPO-34 by formatting Mn4+ at low-temperature, resulting from the electronic interaction between manganese oxide and Ce. The redox cycle between manganese oxides and Ce of different valences accompanied with the generation and transition of active oxygen species. Subsequently, the introducing of Ce can improve the NO oxidation to NO2 and increase the conversion of NO at low-temperatures following a “fast NH3-SCR” route. Ce regulated Mn/SAPO-34 catalyst with weak acidity and reduced acid amount on surface were observed, which significantly suppressed the oxidation of NH3 at the elevated temperature, and facilitated the increase of catalytic selectivity.
Conflicts of interest
There are no conflicts to declare.
Acknowledgements
The authors would like to thank the financial support by Innovation and Development Project of Guangxi Science and Technology Department (Project Grants 809274011004).
References
- G. Busca, L. Lietti, G. Ramis and F. Berti, Appl. Catal., B, 1998, 18, 1 CrossRef CAS.
- C. Ciardelli, I. Nova, E. Tronconi, D. Chatterjee, B. Bandl-Konrad, M. Weibel and B. Krutzsch, Appl. Catal., B, 2007, 70, 80 CrossRef CAS.
- I. Nova, C. Ciardelli, E. Tronconi, D. Chatterjee and B. Bandl-Konrad, Catal. Today, 2006, 114, 3 CrossRef CAS.
- J. Li, H. Chang, L. Ma, J. Hao and R. Yang, Catal. Today, 2011, 175, 147 CrossRef CAS.
- W. S. Kijlstra, M. Biervliet, E. K. Poels and A. Bliek, Appl. Catal., B, 1998, 16, 327 CrossRef.
- Z. Qu, L. Miao, H. Wang and Q. Fu, Chem. Commun., 2015, 51, 956 RSC.
- C. Fang, D. Zhang, S. Cai and L. Zhang, Nanoscale, 2013, 5, 9199 RSC.
- Y. Wan, W. Zhao, Y. Tang and L. Li, Appl. Catal., B, 2014, 148, 114 CrossRef.
- B. Jiang, Y. Liu and Z. Wu, J. Hazard. Mater., 2009, 162, 1249 CrossRef CAS.
- W. S. Kijlstra, D. S. Brands and H. I. Smit. Preprints-American Chemical Society. Division of Petroleum Chemistry, 1997 Search PubMed.
- X. Lou, P. Liu and J. Li, Appl. Surf. Sci., 2014, 307, 382 CrossRef CAS.
- Z. Wu, B. Jiang and Y. Liu, J. Hazard. Mater., 2007, 145, 488 CrossRef CAS.
- Y. Xiong, C. Tang and X. Yao, Appl. Catal., A, 2015, 495, 206 CrossRef CAS.
- X. Yao, Y. Xiong and W. Zou, Appl. Catal., B, 2014, 144, 152 CrossRef CAS.
- Z. Liu, Y. Liu and B. Chen, Catal. Sci. Technol., 2016, 6, 6688–6696 RSC.
- D. Zhang, L. Zhang and L. Shi, Nanoscale, 2013, 5, 1127 RSC.
- G. Carja, G. Delahay and C. Signorile, Chem. Commun., 2004, 35, 1404 RSC.
- G. Qi and R. T. Yang, J. Catal., 2003, 217, 434 CrossRef CAS.
- J. Lia, J. Guoa and X. Shi, Appl. Surf. Sci., 2020, 534, 147592 CrossRef.
- P. G. Smirniotis, P. M. Sreekanth and D. A. Pena, Ind. Eng. Chem. Res., 2006, 45, 6436 CrossRef CAS.
- F. Cao, J. Xiang and S. Su, Fuel Process. Technol., 2015, 135, 66–72 CrossRef CAS.
- S. Ren, S. Li, Z. Su and J. Yang, Chem. Eng. J., 2018, 351, 540–547 CrossRef CAS.
- M. Chen, Q. Sun and X. Yang, Inorg. Chem. Commun., 2019, 105, 203–207 CrossRef CAS.
- J. H. Kwak, R. G. Tonkyn and D. H. Kim, J. Catal., 2010, 275, 187 CrossRef CAS.
- D. W. Fickel, E. D. Addio and J. A. Lauterbach, Appl. Catal., B, 2011, 102, 441–448 CrossRef CAS.
- R. Zhang, N. Liu and Z. Lei, Chem. Rev., 2016, 116, 3658 CrossRef CAS.
- H. I. Hamoud, V. Valtchev and M. Daturi, Appl. Catal., B, 2019, 250, 419–428 CrossRef CAS.
- A. M. Prakash and S. Unnikrishnan, J. Chem. Soc., Faraday Trans., 1994, 90, 2291–2296 RSC.
- P. Zhai, Z. M. Li, H. J. Liu and I. L. Li, Carbon, 2006, 44, 1151–1157 CrossRef.
- S. Mohan, P. Dinesha and S. Kumar, Chem. Eng. J., 2020, 384, 123253 CrossRef CAS.
- S. T. Korhonen, D. W. Fickel and R. F. Lobo, Chem. Commun., 2011, 47, 800 RSC.
- U. Deka, A. Juhin and E. A. Eilertsen, J. Phys. Chem. C, 2012, 116, 4809 CrossRef CAS.
- J. Xue, X. Wang and G. Qi, J. Catal., 2013, 297, 56 CrossRef CAS.
- L. Xu, A. Du and Y. Wei, Microporous Mesoporous Mater., 2008, 115, 332 CrossRef CAS.
- S. Wu, X. Yao and L. Zhang, Chem. Commun., 2015, 51, 3470 RSC.
- L. Wang, B. Huang and Y. Su, Chem. Eng. J., 2012, 192, 232 CrossRef CAS.
- F. Kapteijn, L. Singoredjo and A. Andreini, Appl. Catal., B, 1994, 3, 173 CrossRef CAS.
- M. Romeo, K. Bak and J. Elfallah, Surf. Interface Anal., 1993, 20, 508 CrossRef CAS.
- G. Carja, Y. Kameshima and K. Okada, Appl. Catal., B, 2007, 73, 60 CrossRef CAS.
- P. R. Ettireddy, N. Ettireddy and T. Boningari, J. Catal., 2012, 292, 53 CrossRef CAS.
Footnote |
† Electronic supplementary information (ESI) available. See DOI: 10.1039/d0ra06639g |
|
This journal is © The Royal Society of Chemistry 2020 |
Click here to see how this site uses Cookies. View our privacy policy here.