DOI:
10.1039/D0RA04093B
(Paper)
RSC Adv., 2020,
10, 24134-24144
Preparation, characterization, and thermal properties of novel fire-resistant microencapsulated phase change materials based on paraffin and a polystyrene shell
Received
7th May 2020
, Accepted 15th June 2020
First published on 24th June 2020
Abstract
Paraffin and paraffin mixtures that are preferred as phase change materials in many thermal energy storage applications are highly flammable. Microencapsulation of paraffin in a polymeric shell can decrease flammability, however, breaking of the shell under fire conditions can still cause a high risk. In the current paper, microencapsulated paraffin with a polystyrene shell is prepared and halogen-free flame retardants (ortho-phosphoric acid and pentaerythritol) were applied with the novel approach of direct incorporation during the microencapsulation process. Thermal energy storage and fire retardancy properties were characterized before and after fire-retardant addition. The fire behavior of samples in concrete blocks was determined with standardized methods in order to assess their suitability in building applications. ortho-Phosphoric acid as a flame retardant in microencapsulated phase change material was tested for the first time in this study. The results support that the improved flame retardancy and thermal energy storage properties were achieved with the incorporation of a flame retardant on microcapsules for energy storing concrete samples.
1. Introduction
Phase Change Materials (PCMs), used for storing thermal energy as latent heat with high storage density can provide flexible solutions in various applications such as heating, cooling, and thermal management. Different kinds of paraffin available at a wide range of temperatures (−125 to 100 °C) are preferred as PCM in many of these applications.1 Among the reasons behind the popularity of paraffin are its reliable phase change behavior, commercial availability, and low-cost. Little or no supercooling, no phase segregation, self-nucleating behavior, thermal and chemical stability, non-toxicity, and small volume change are the main features of paraffin that provide reproducible phase changes.2 On the other hand, the main drawback of paraffin is its high flammability, which makes it difficult to comply with safety standards and hinders further utilization. This should be taken into account in all PCM applications with the risk of fire hazards.3,4 In particular, in recent building codes more rigorous safety codes and flammability requirements are enforced.
In recent passive building applications, PCM is incorporated into concrete to increase energy density and efficiency.5–8 One problem of direct use of PCMs in building materials is leakage from the porous structure, which might result in spreading the fire much faster. Hence, the recent trend is microencapsulating PCMs to avoid leakage problems.9,10 In the review of PCMs in building applications by Cabeza et al.,11 it can be seen that paraffin is among the most preferred PCMs both in scientific reports and commercial products. There are some microencapsulated paraffin and gypsum wallboard incorporated with microencapsulated paraffin products on the market. Fire retardance methods applied to PCM incorporated wallboards are: adding an inflammable layer on the surface like aluminum foil or rigid polyvinyl chloride film, treating wallboard with liquid fire retardant like Fyrol CEF following incorporation of PCM, using brominated hexadecane and octadecane as PCM, using fire retardant surface coatings.12 Polymeric shells used in microencapsulated paraffin can decrease the flammability. However, it has been shown that polymeric shells of microencapsulated paraffin can crack and cause paraffin to leak out under fire conditions. Hence, microencapsulation cannot stop the fire hazard of paraffin used in the gypsum wallboard.13 The results of another study showed that using microencapsulated paraffin in mortar increased the flammability of mortar.14
The fire retardants that can be used for PCMs, as well as other products, generally can be categorized into three groups according to their effects as fire quenchers, heat absorbers, and intumescent fire retardants.15 Combinations of these can also be used to provide a synergistic effect. Further categorization based on chemical combinations such as halogen-containing, phosphorous-containing, silicon-containing, etc. is also possible.16 Halogen-based flame retardants are successfully utilized in many applications for suppressing the flammability of various materials. But, halogenated alkanes, widely used as fire quenchers in polymers, are known to produce corrosive hydrogen halide and release toxic gases during burning.17,18 Currently, halogen-free fire retardants are extensively being developed due to health and environmental problems caused by halogen-based fire retardants. Endothermic decomposition of heat absorber fire retardants such as magnesium hydroxide prevents the spreading of heat and limit combustion.15 Intumescent fire retardants are reported as more efficient and environmentally friendly.17 Some examples are pentaerythritol (PER), ammonium polyphosphate (APP), and expanded graphite. Upon burning, intumescent fire retardants create a char layer that protects the underlying material from oxygen and heat.15 Recent research shows that intumescent fire retardants can be microencapsulated to improve its properties and ease of applicability.19–21 Microencapsulation improves fire retardancy and thermal stability and increases water resistance.19
There are many studies on microencapsulated (mPCM) and form-stabilized (FS-PCM) products for thermal energy storage, but only a few addresses improvement of fire resistance properties of mPCMs (Table 1). Most of these studies are for FS-PCM and only three ref. 22–24 and one patent25 are on the application of fire retardant to mPCMs. There are a few recent studies on microencapsulated PCM that have fire retardant encapsulated together with the PCM as given in Table 1. Although researchers could reduce the flammability problem of the PCMs by different fire-retardant applications, the heat storage and recovery capacity of the final product was reduced during melting and solidification due to the addition of the high amount of fire retardants (∼40%) to maintain ideal fire retardancy performance. Therefore, it is still a big challenge to develop novel methods and fire retardants in order to minimize the amount of fire-retardant additive in microcapsules. In this way, not only a more economical solution will be achieved but also latent heat capacity of the PCM can be retained. On the basis of the above-mentioned perspective, this paper aims to design a paraffin-based microencapsulated phase change material with persistent fire retardancy and higher storage capacity by the addition of optimized novel fire retardant. Moreover, developed microcapsules are tested in real-concrete samples where the application field of mPCMs.
Table 1 Previous studies on fire-retardant applications to PCMs. mPCM: microencapsulated PCM, FS: form stabilized
PCM |
Type |
Form/shell |
Fire retardant |
Result |
Reference |
Paraffin |
mPCM |
Gelatin + Na-alginate |
Clay-nano particles applied in the shell material during microencapsulation |
Ignition time of treated textile increased by 25–50% |
22 |
Paraffin |
mPCM |
Polymetacrylic acid-co-ethyl methacrylate |
Diethyl ethylphosphonate (DEEP) applied with the PCM during microencapsulation |
Limiting oxygen index (LOI) value of treated foam increased by 6–9% |
23 |
Paraffin or fatty acid |
mPCM |
Melamine-formaldehyde resin, gelatin, polyurea, polyurethane, urea-formaldehyde resin, and combinations |
Boric acid, sodium carbonate, and sodium silicate applied on the surface of the microcapsule after microencapsulation |
NA |
25 |
Methyl ester |
mPCM |
NA |
Applied as a coating on the microcapsule during drying |
NA |
24 |
Palmitic acid |
FS-PCM |
SiO2 |
Melamine: in 24 g PCM (palmitic acid) 0.5 g or 2 g of melamine |
|
26 |
Paraffin |
FS |
High-density polyethylene (HDPE) |
9 different formulations of Mg(OH)2, Al(OH)3, APP, PER, EG, |
|
15 |
Paraffin |
FS-PCM |
HDPE |
APP + PER + melamine (2 : 1 : 1) 15–20–25% wt, EG |
|
27 |
Paraffin |
FS-PCM |
HDPE |
APP, PER, Fe |
Heat release rate (HRR) decreased by 40–56% |
28 |
Paraffin |
FS-PCM |
HDPE |
APP, expanded graphite (EG), zinc borate |
HRR decreased by 60% |
29 |
Paraffin |
FS-PCM |
HDPE |
APP, EG, zinc borate |
HRR decreased by 60–68% |
30 |
n-Octadecane |
Nano encapsulated |
Melamine-formaldehyde |
Phosphorus–nitrogen containing diamine (PNDA) |
pHRR decreased by 32.8% |
31 |
THR decreased by 30.3% |
TSR decreased by 18.6% |
n-Octadecane |
Nano encapsulated |
Poly(methylmethacrylate) |
Diethyl bis(2-hydroxyethyl acrylate)amino methylphosphonate |
pHRR decreased by 39.7% |
32 |
THR decreased by 18.4% |
TSR decreased by 12.2% |
LOI increased from 19.5% to 25.1% |
Micronal |
Polyurethane foam |
|
Melamine, APP or EG |
|
33 |
Hexadecanol |
Blended PCM |
— |
Phenylphosphonic dichloride (BPOD) and phosphorus oxychloride (POCl3) |
pHRR decreased by 56.2% |
34 |
Paraffin |
Shape stabilized |
|
Acrylic resin/expandable graphite (EG), alkyd resin/EG and epoxy resin/EG |
pHRR decreased by 62–84% |
35 |
1-Tetradecanol, 1-hexadecanol, 1-octadecanol, diethyl phosphite |
FS-PCM |
PHA and KH-560 |
Phosphorus and silicon |
Residual char. was increased up to 16.3% |
36 |
Polyethylene glycol (PEG) – 10 000 |
Shape stabilized composite |
Polyether |
TBBP-A and/or DBDPE |
LOI reached 21.3 |
37 |
PEG-4000 |
Shape stabilized |
Wood–plastic |
EG |
LOI increased to 30.5% |
38 |
Paraffin |
Shape stabilized |
High-density polyethylene (HDPE) and styrene–butadiene–styrene copolymer |
Organomontmorillonite, EG |
pHRR decreased by up to 72.7% |
39 |
Paraffin chlorinated paraffin |
FS-PCM |
HDPE |
EG, antimony trioxide |
pHRR decreased up to ∼50% |
40 |
Decanoic/palmitic acid eutectic mixture |
|
Plywood |
Silicon fume geopolymer-based coating |
Fire growth index (FGI) decreased from 1.97 to 0.71 kW m−2 s−1 |
41 |
Paraffin (70%) |
FS-composite |
Olefin block |
Acrylic resin/EG, glass fibers |
pHRR decreased by 58.8% |
42 |
Paraffin |
FS-PCM |
Epoxy resin |
PEPA–TMA |
pHRR decreased by 45%, LOI reached 29.8% |
43 |
In this study, we developed a microencapsulated phase change material (mPCM) based on paraffin and polystyrene shell. As a novel approach, we added fire retardants during the encapsulation process. In this way, it is expected that fire retardant will exist with PCM in core material as well as immobilized on the shell material of microcapsules. The aim is to develop a product that will not require further treatment of fire retardant of the mPCM, making it easier for the user to apply and achieve more effective use of fire-retardant material. The effects of fire retardant on thermal characteristics of mPCM and flammability properties of microcapsules and concrete structures are also discussed.
2. Experimental
2.1. Materials
Styrene monomer was purchased from Sigma-Aldrich and used for synthesizing shell material of the microcapsules. Paraffin 42–44 obtained from Merck was used as PCM core material. Ferrous sulfate heptahydrate (FeSO4·7H2O), ammonium persulphate ((NH4)2S2O8), sodium thiosulfate (Na2O3S2) and tert-butyl hydroperoxide purchased from Merck were used as initiators in the polymerization reaction. Triton X-100 (Merck) was used as a surfactant. Ethylene glycol di-methacrylate (EGDM, Merck) was used as a crosslinking agent.
ortho-Phosphoric acid (oPA) and pentaerythritol (PER) were supplied from Sigma-Aldrich Company and were used as fire retardants. The cement (CEM I 42,5 R) used in preparing concrete block samples was provided by Oyak Çimento, Adana. All the chemicals used in this study were analytical grade and used as received without any further purification step.
2.2. Microencapsulation of PCM
Emulsion polymerization adapted from previous studies in the literature44 was utilized to obtain microencapsulated PCM samples. The following synthesis routine was followed for paraffin–styrene microcapsules (Scheme 1). Styrene monomer, paraffin, ethylene glycol dimethacrylate, surfactant (Triton X-100), and deionized water were mixed for 60 min in a reaction flask using a mechanical stirrer at 3000 rpm and 50 °C to form an oil-in-water emulsion. 1 mL freshly prepared FeSO4·7H2O solution and 0.5 g ammonium persulphate were added as initiators. 0.25 g sodium thiosulfate (Na2S2O3) and 1 g t-butyl hydroperoxide (70%) were added and mixed at a constant speed of 500 rpm at 80 °C for 5 hours. Synthesized particles were filtered and washed with deionized water three times and dried in a fume hood at room temperature for 48 hours.
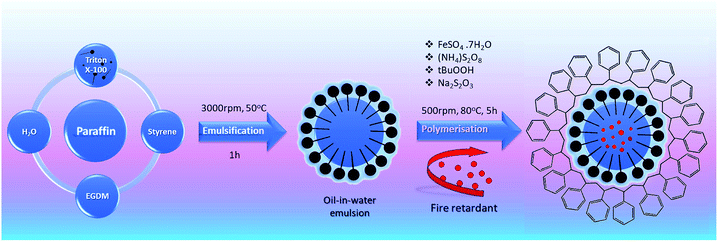 |
| Scheme 1 The fabrication process of paraffin-based microencapsulated PCM with fire-resistant additive. | |
2.3. Fire retardant application of PCM
Pentaerythritol (PER, C5H12O4) and o-phosphoric acid (oPA, H3PO4) were used for enhancing the fire-retardancy properties of microcapsules and added during the microencapsulation process. For this purpose, fire retardants were added with the initiator after the oil-in-water emulsion step in the polymerization reaction. Microcapsule fabrication temperature was modified depending on the fire retardant, in order to obtain efficient microencapsulation. For oPA two different temperatures of 90 °C and 85 °C (named as oPA-90 and oPA-85) and for PER 70 °C were tested.
2.4. Preparation of mPCM-concrete mixtures
In this study, a self-compacting concrete mixture with a water/cement ratio of 0.41 was used. mPCM dosage was selected as 10% and 0% for tested specimens and reference, respectively. Concrete mixtures prepared as instructed in by Turkish Standard TS 802 – Design of concrete mixes.45 The composition of 1 m3 concrete mixture is given in Table 2. Polycarboxylate ether was used as a superplasticizer. mPCM was replaced with the aggregates at a constant cement ratio. All the dry ingredients were mixed using a mechanical mixer. Then, water and superplasticizer added to the mixture and mixed for 5 min. mPCM was added in the last step to avoid breaking of microcapsules under mixing stress.
Table 2 Composition of standard cubic concrete samples
Materials |
Reference (0%) specimen (kg) |
10% PCM specimen (kg) |
Superplasticizer |
1.9 |
1.9 |
Paraffin |
0 |
5.4 |
0–3 crushed fine aggregates |
376.6 |
161.4 |
5–10 crushed fine aggregates |
258.4 |
221.4 |
Water |
65.8 |
64 |
Cement |
157.6 |
157.6 |
Total weight |
860.3 |
773.1 |
2.5. Characterization
2.5.1. Thermal analysis. The thermal characterization of the synthesized microcapsules was achieved by a simultaneous thermal analysis device (PerkinElmer STA-6000). Simultaneous thermal analysis (STA) provides thermogravimetric analysis (TGA) and differential thermal analysis (DTA) measurements of a sample at the same time. Analyses were carried out with 5 mg of sample, under inert nitrogen flowing, and also in an oxygen atmosphere for thermal stability and thermo-oxidative stability tests, at 20 mL min−1 flow rate. The temperature range was 30–600 °C at a heating rate of 20 °C min−1. All STA measurements were repeated three times. The accuracy of the method is ±0.5 °C and ±0.02% precision.
2.5.2. Chemical analysis. FTIR spectroscopy was employed to detect any possible changes in the chemical structure of microcapsules before and after fire-retardant treatment. FTIR spectra were obtained within a frequency range of 365–4000 cm−1 using a Thermo Scientific FTIR instrument.
2.5.3. Morphology. Structural characterization was determined by SEM, Zeiss Supra 55 scanning electron microscope (SEM). Prior to SEM analysis, samples were coated with Pt.
2.5.4. Fire retardancy tests. The reference and samples treated with fire retardants were tested according to methods described by ISO standards of TS EN ISO 1716 (determination of the gross heat of combustion, QPCS),46 TS EN ISO 1182 (non-combustibility test),47 and TS EN ISO 11925-2 (single-flame source test)48 as summarized in Table 3. The heat of combustion (calorific value) tests were carried out according to the method described in TS EN ISO 1716 using a bomb calorimeter (Parr 6200)46 for determination of gross heat of combustion. For this aim, 0.5 g of powdered sample and 0.5 g benzoic acid were placed into a pot. The pot was placed into the calorimeter and an ignition wire was placed in contact with the powdered sample. Then, the test was carried out with an oxygen bomb and heat of combustion value (MJ kg−1) was measured.
Table 3 The methods utilized for fire retardancy properties of the samples
Test name |
Measurement (unit) |
Fire resistance test standard |
Determination of the gross heat of combustion (QPCS) (calorific value) |
Heat of combustion (MJ kg−1) |
EN ISO 1716 (ref. 46) |
Non-combustibility test |
Weight change (mass loss%) |
EN ISO 1182 (ref. 47) |
Single-flame source test |
Ignition time (s) |
EN ISO 11925-2 (ref. 48) |
Fire classification |
|
EN 13501-1:2007+A1:2009 (ref. 49) |
The non-combustibility test was performed according to ISO 1182.47 This standard describes a test technique for determining the non-combustibility performance of homogeneous building products and important apparatuses of non-homogeneous building products. For the experiments, cylindrical concrete samples with a diameter of 45 mm and a height of 50 mm were prepared. Specimens were placed into an oven at 750 °C for 30 minutes. The samples were kept in a desiccator until reaching room temperature and weight changes were measured.
Single-flame source tests were conducted according to ISO 11925-2 “Ignitability of building products subjected to direct impingement of flame” using an oven with a flame source.48 The sample size was 250 mm × 90 mm × 60 mm. In this method, the specimen was vertically placed in a test chamber and subjected to a gas flame (20 ± 0.1 mm) with a 45-degree angle for 15 and 30 seconds.
The mPCM concrete samples were classified according to European standard EN 13501-1:+A1:2009 “Fire classification of construction products and building elements”. This standard gives information about the fire hazard classification method for all construction materials and building products. According to the standard, construction materials are classified as stated in the test methods in Euroclasses of A1, A2, B, C, D, E, and F. The non-combustible products are classified in A1 and A2 classes, and the combustible products are classified in ascending order from B to F.
3. Results and discussion
3.1. Thermal analysis
Thermal characteristics (phase-change temperatures, latent heat capacities, encapsulation ratio, and thermal stabilities) of microcapsules were studied by STA analysis giving DTA and TGA results. The thermograms corresponded to DTA were overlapped in Fig. 1 and summarized in Table 4. Melting temperatures (determined from the peak points of DTA curves) of paraffin, mPCM, oPA-85, oPA-90, and PER were determined as 45.1, 46.7, 46.9, 46.1, and 45.6 °C, respectively. The latent heats of paraffin, mPCM, oPA-85, oPA-90, and PER were measured as 82.3, 32.8, 45.1, 56.6, and 36.7 J g−1, respectively. The latent heat capacities of microcapsules varied by the amount of PCM core material which can be described by encapsulation ratio. Encapsulation ratios of microcapsules were calculated using the following eqn (1): |
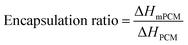 | (1) |
where, ΔHPCM is the latent heat capacity of core material (J g−1), ΔHmPCM is the latent heat capacity for microcapsules (J g−1).
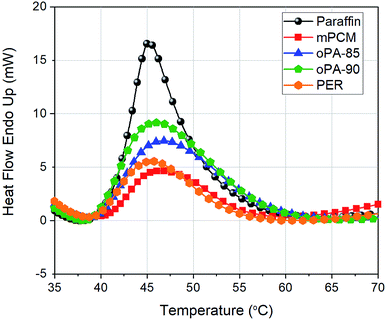 |
| Fig. 1 DTA curves of microcapsules. | |
Table 4 Comparison of thermal properties of microencapsulated samples
Sample |
DTA |
Onset (°C) |
Peak (°C) |
End (°C) |
Latent heat (J kg−1) |
Encapsulation ratio (%) |
Paraffin |
42 |
45.1 |
52 |
82.3 |
— |
mPCM |
41 |
46.7 |
56 |
32.8 |
40 |
oPA-85 |
40 |
46.9 |
58 |
45.1 |
55 |
oPA-90 |
39 |
46.1 |
56 |
56.6 |
68 |
PER |
40 |
45.6 |
54 |
36 |
44 |
Encapsulation ratios (from highest to low) were found to be oPA-90 > oPA-85 > PER > mPCM. Results indicated that fire retardant additives had a positive effect on the encapsulation ratio, this might be due to two reasons: (i) thinner shell thickness of microcapsules (ii) improved interactions between paraffin and polystyrene shell via fire retardant addition and temperature change. Also, in oPA samples, the encapsulation ratio is increased with the temperature increase from 85 °C to 90 °C. This might be due to the fact that during polymerization, the bonds between polymer chains become wider and increase the volume at higher temperatures which is close to polystyrene's glass transition temperature of 97 °C.
TGA analysis has importance to evaluate thermal stability, degradation steps, and determination of the operational temperature ranges. TGA analyses were conducted in two different gas combinations: inert N2 atmosphere, and N2/O2 gas switch mode. The thermal stability of the microcapsules under N2 gas atmosphere was shown in Fig. 2(a). According to results, paraffin subjected to one-step weight loss profile in a temperature range of 220–300 °C, corresponded to its evaporation. mPCM and fire retardant added microcapsules exhibited a two-step degradation profile, the first step starting at approximately 230 °C is related to the evaporation of paraffin core material and the differences between the amount of weight loss are due to the different encapsulation ratios as explained above. The second step that occurred at a temperature range of 310–450 °C corresponds to the deterioration of the polystyrene shell material. Also, in this step, it can be clearly seen that weight loss started and finished at higher temperatures in PER and oPA added samples. Among the tested samples, the best stability was achieved with oPA-90 sample which has the best encapsulation ratio and higher initial weight loss temperatures. The increase in the degradation temperatures indicates that fire retardants used in this study increased the thermal stability of the mPCM.
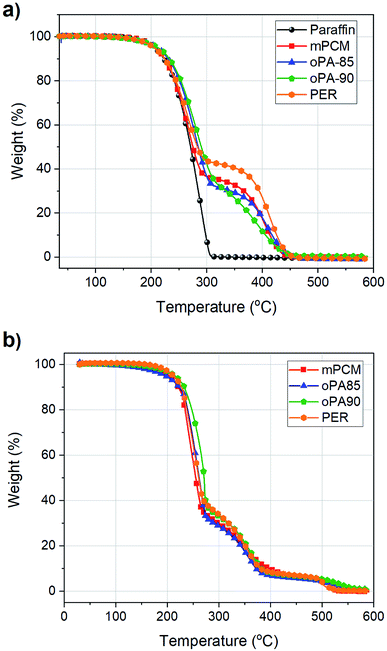 |
| Fig. 2 TGA curves obtained under (a) N2 gas flow (c) switch mode of N2/O2 gas flow. | |
In order to investigate the effect of the fire retardants on thermo-oxidative properties of polystyrene shell material of microcapsules, a switch gas analysis also carried out as shown in Fig. 2(b). For this aim, initially N2 gas was purged until a temperature of 275 °C at which paraffin completely evaporated and before the second weight loss step began. After that, the purge gas was switched to O2. Thermo-oxidative stabilities of microcapsules were found to be in the order of oPA-90 > PER > oPA-85 > mPCM. The TGA curves obtained with the switch gas purge exhibited similar trends as in the N2 gas purge. However, it should be noted that an extra residual carbonaceous char in the condensed phase around 500 °C was observed only in O2 atmosphere. This result indicates that the formation of a char layer can be successfully achieved with the use of fire retardants used in this study. Moreover, the degradation temperatures of microcapsules under O2 atmosphere were lower than those in N2 atmosphere. This indicates that oxygen promotes a faster degradation of polystyrene. In addition, when the char residue amounts were compared at 600 °C, the most stable microcapsule was found to be oPA-90 which supports the thermal stability of oPA-90 being higher than that of the other microcapsule samples. The TGA and DTA results revealed that there was a synergistic effect between the fire retardant (oPA) and shell structure which reduced the thermal degradation at higher temperatures, flame retardancy as well as encapsulation ratio.
Fig. 3 shows the FTIR spectra of the microcapsule samples. The C–H stretching and bending absorption bands related to aliphatic carbon-hydrogen bonds are at 2854–2900 cm−1 and 1400 cm−1, respectively. Moreover, CH2 rocking absorption band at around 725 cm−1 confirms the structure of the paraffin.
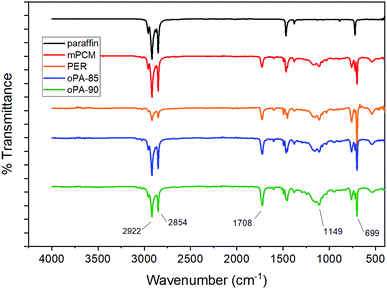 |
| Fig. 3 FT-IR analysis. | |
For the mPCM, in addition to peaks from paraffin, aromatic ring originated C
C and C–H peaks were observed at 1601 cm−1 and 699 cm−1, respectively. In oPA treated microcapsule samples, P
O and P–O peaks, related to phosphoric acid, were detected around 1400 cm−1 and 946 cm−1. FTIR results confirm that microencapsulation of paraffin along with the fire retardants was successfully achieved.
The SEM images of microcapsule samples were shown in Fig. 4(a–d). Microcapsules are mostly spherical and embedded in the polymer matrix. All the microcapsule samples have an average diameter of less than 1 μm. The surrounding polymer matrix thickens the shell structure and caused a lower encapsulation ratio. However, in Fig. 4(b), for oPA-85 samples, microcapsules were more separated with a cauliflower-like structure. This is due to the synergistic effect of oPA that provides a thinner shell structure and improved encapsulation efficiency.
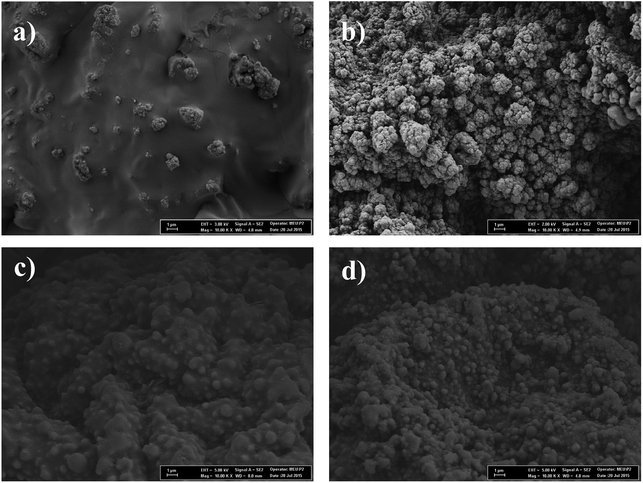 |
| Fig. 4 SEM pictures of (a) mPCM (b) oPA-85 (c) oPA-90 (d) PER. | |
3.2. Fire retardant properties of microcapsules
3.2.1. The heat of combustion (calorific value). The determination of the gross heat of combustion (QPCS) was achieved with reference concrete specimen and concrete with a microcapsule specimen, as shown in Fig. 5(a). The determination of the heat of combustion is crucial for comparing the flammability of the samples. In this method, the gross heat of combustion of specimens at constant volume was determined in an oxygen bomb calorimeter, which ensures the complete combustion of the specimens. QPCS values of reference specimen, mPCM, PER, oPA-85 and oPA-90 samples were found to be −0.39(∼0) MJ kg−1, 0.09 MJ kg−1, 0.32 MJ kg−1, 0.92 MJ kg−1, and 0.03 MJ kg−1, respectively. The results of the oxygen bomb tests showed that only the concrete sample containing oPA-90 has reduced the QPCS value compared to mPCM and exhibited very low flammability properties. All the concrete samples conform to the requirements of A1 class (≤2.0 MJ kg−1) according to EN 3501-1:2007+A1:2009.
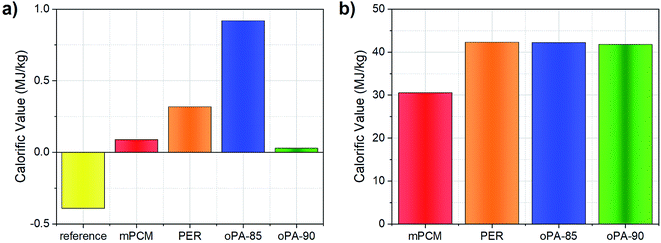 |
| Fig. 5 QPCS tests of (a) concrete samples, (b) bare-microcapsule samples. | |
The heat of combustion tests also repeated for bare-microcapsule samples as shown in Fig. 5(b). QPCS values of mPCM, PER, oPA-85, and oPA-90 samples were found to be 30.54 MJ kg−1, 42.31 MJ kg−1, 42.23 MJ kg−1, and 41.78 MJ kg−1, respectively. The calorific value of mPCM (without any flame retardant) is lower than those with fire retardants. This behavior can be explained with the higher microencapsulation ratio of the samples with fire retardants compared to mPCM that increases the paraffin in the microcapsules. As a result of this, more heat of combustion was supplied with an increasing amount of paraffin. However, oPA-90 sample, which has the highest paraffin content among them, gave similar results with the other fire retardant added samples which indicate that it showed more fire retardancy effect compared to the other microcapsules.
3.2.2. Non-combustibility test. The mass losses of the concrete materials due to combustion in the furnace were investigated according to the procedure described in ISO 1182 standard. For this aim, cylindrical concrete specimens with a diameter of 45 mm and 50 mm height were prepared. Mass losses for reference, mPCM, PER, oPA-85 and oPA-90 were found to be 6.2%, 10.5%, 10.0%, 7.7%, and 7.6%, respectively. No continuous flame was observed in specimens. According to the results, the mass loss percentage was increased by the microcapsule addition into concrete. However, this mass loss increase was limited by the addition of different fire-retardants and the best non-combustibility results were obtained with oPA added samples (Fig. 6).
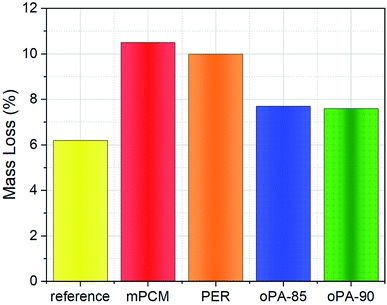 |
| Fig. 6 Noncombustibility tests of concrete samples. | |
3.2.3. Single-flame source test. Ignitability of concrete specimens was tested according to ISO 11925-2 test method. The concrete specimens with and without microcapsule were cast in 12.5 mm thickness and subjected to direct impingement of flame. Single-flame source tests carried out in a test chamber. The specimen is exposed to a gas flame. During the time of the ignition period, there were no burning droplets or flames of the test specimens. The single-flame source test complies with “d0” class according to EN 13501-1 standard.
4. Conclusions
In this study, oPA and PER, halogen-free flame retardants, were successfully encapsulated to improve the flame retardancy properties of paraffin-based microcapsules with polystyrene shell material. oPA, as a nontoxic and eco-friendly flame retardant in microencapsulated phase change materials, was tested for the first time in literature. Paraffin containing microcapsules were fabricated by emulsion polymerization technique and the reaction-to-fire's performance was evaluated and analyzed according to ISO standards (ISO 1716, ISO 1182, ISO 11925-2, and 13501-1). The variables including gross heat of combustion, mass loss, ignition time, and energy storage properties for concrete specimens and mPCM samples with and without flame retardants were taken into consideration. QPCS value of mPCM in concrete was reduced from 0.09 MJ kg−1 to 0.03 MJ kg−1 by the addition of oPA. Compared to unmodified-mPCM, the heat of combustion was reduced by 67%, and mass loss percentage was reduced from 10.5% to 7.6%, which indicates the non-combustibility properties of microcapsules were improved by the addition of fire-retardants. TGA results indicate that compared to raw paraffin, microencapsulation process and fire retardant addition was improved the thermal stability. Besides, one of the most interesting results, the encapsulation ratio of the microcapsules increased from 40% to 68% which increase the energy density of oPA added microcapsules as a result of synergetic interaction with polymeric shell material of microcapsules. Results showed that the introduction of fire retardants during microencapsulation of paraffin not only served enhanced fire retardancy properties but also provided improved thermal energy storage characteristics. The best results for the fire retardancy and thermal storage properties were obtained for the sample oPA-90. According to European classification of reaction to the fire EN 13501-1:2007+A1:2009, the PCM added concrete panels were classified as A2/B, d0 that makes them suitable to use in building envelopes for thermal regulation purposes.
Conflicts of interest
There are no conflicts to declare.
Acknowledgements
The authors would like to thank the financial support by Cukurova University Scientific Research Projects (BAP) Unit (Project No: FYL-2015-4447). B. K. was supported by Scientific and Technological Research Council of Turkey (TUBITAK 2210-C MSc Scholarship Programme). K. C. acknowledges support from the TUBITAK BIDEB-2218 National Postdoctoral Research Fellowship Programme. We also acknowledge support from Kambeton Company.
References
- M. Freund, Paraffin products: properties, technologies, applications, Elsevier Science Limited, 1982, vol. 14 Search PubMed.
- S. Ogden, L. Klintberg, G. Thornell, K. Hjort and R. Bodén, Review on miniaturized paraffin phase change actuators, valves, and pumps, Microfluid. Nanofluidics, 2014, 17, 53–71, DOI:10.1007/s10404-013-1289-3.
- G. Song, S. Ma, G. Tang, Z. Yin and X. Wang, Preparation and characterization of flame retardant form-stable phase change materials composed by EPDM, paraffin and nano magnesium hydroxide, Energy, 2010, 35, 2179–2183, DOI:10.1016/j.energy.2010.02.002.
- Y. Cai, Y. Hu, L. Song, Q. Kong, R. Yang, Y. Zhang, Z. Chen and W. Fan, Preparation and flammability of high density polyethylene/paraffin/organophilic montmorillonite hybrids as a form stable phase change material, Energy Convers. Manag., 2007, 48, 462–469, DOI:10.1016/j.enconman.2006.06.021.
- F. Kuznik, D. David, K. Johannes and J.-J. Roux, A review on phase change materials integrated in building walls, Renew. Sustain. Energy Rev., 2011, 15, 379–391, DOI:10.1016/j.rser.2010.08.019.
- K. Cellat, F. Tezcan, G. Kardaş and H. Paksoy, Comprehensive investigation of butyl stearate as a multifunctional smart concrete additive for energy-efficient buildings, Int. J. Energy Res., 2019, 43, 7146–7158, DOI:10.1002/er.4740.
- K. Cellat, B. Beyhan, C. Güngör, Y. Konuklu, O. Karahan, C. Dündar and H. Paksoy, Thermal enhancement of concrete by adding bio-based fatty acids as phase change materials, Energy Build., 2015, 106, 156–163, DOI:10.1016/j.enbuild.2015.05.035.
- K. Cellat, B. Beyhan, Y. Konuklu, C. Dündar, O. Karahan, C. Güngör and H. Paksoy, 2 years of monitoring results from passive solar energy storage in test cabins with phase change materials, Sol. Energy, 2020, 200, 29–36, DOI:10.1016/j.solener.2019.01.045.
- S. Ramakrishnan, J. Sanjayan, X. Wang, M. Alam and J. Wilson, A novel paraffin/expanded perlite composite phase change material for prevention of PCM leakage in cementitious composites, Appl. Energy, 2015, 157, 85–94, DOI:10.1016/j.apenergy.2015.08.019.
- S. Drissi, T.-C. Ling, K. H. Mo and A. Eddhahak, A review of microencapsulated and composite phase change materials: alteration of strength and thermal properties of cement-based materials, Renew. Sustain. Energy Rev., 2019, 110, 467–484, DOI:10.1016/j.rser.2019.04.072.
- L. F. Cabeza, A. Castell, C. Barreneche, A. de Gracia and A. I. Fernández, Materials used as PCM in thermal energy storage in buildings: a review, Renew. Sustain. Energy Rev., 2011, 15, 1675–1695, DOI:10.1016/j.rser.2010.11.018.
- A. M. Khudhair and M. M. Farid, A review on energy conservation in building applications with thermal storage by latent heat using phase change materials, Energy Convers. Manag., 2004, 45, 263–275, DOI:10.1016/S0196-8904(03)00131-6.
- E. K. Asimakopoulou, D. I. Kolaitis and M. A. Founti, Fire safety aspects of PCM-enhanced gypsum plasterboards: an experimental and numerical investigation, Fire Saf. J., 2015, 72, 50–58, DOI:10.1016/j.firesaf.2015.02.004.
- L. Haurie, J. Mazo, M. Delgado and B. Zalba, Fire behaviour of a mortar with different mass fractions of phase change material for use in radiant floor systems, Energy Build., 2014, 84, 86–93, DOI:10.1016/j.enbuild.2014.07.026.
- P. Sittisart and M. M. Farid, Fire retardants for phase change materials, Appl. Energy, 2011, 88, 3140–3145, DOI:10.1016/j.apenergy.2011.02.005.
- K.-S. Lim, S.-T. Bee, L. T. Sin, T.-T. Tee, C. T. Ratnam, D. Hui and A. R. Rahmat, A review of application of ammonium polyphosphate as intumescent flame retardant in thermoplastic composites, Composites, Part B, 2016, 84, 155–174, DOI:10.1016/j.compositesb.2015.08.066.
- L. Li, G. Wang and C. Guo, Influence of intumescent flame retardant on thermal and flame retardancy of eutectic mixed paraffin/polypropylene form-stable phase change materials, Appl. Energy, 2016, 162, 428–434, DOI:10.1016/j.apenergy.2015.10.103.
- M. Atagür, S. Demiroğlu and M. Ö. Seydibeyoğlu, Flame Retardancy of Composites and Nanocomposites Based on PU Polymers, in Polyurethane Polym., Elsevier, 2017, pp. 499–524. DOI:10.1016/b978-0-12-804065-2.00017-6.
- B. Wang, H. Sheng, Y. Shi, W. Hu, N. Hong, W. Zeng, H. Ge, X. Yu, L. Song and Y. Hu, Recent advances for microencapsulation of flame retardant, Polym. Degrad. Stab., 2015, 113, 96–109, DOI:10.1016/j.polymdegradstab.2015.01.008.
- L. Sun, F. Wang, Y. Xie, J. Feng and Q. Wang, The combustion performance of medium density fiberboard treated with fire retardant microspheres, Bioresources, 2012, 7, 593–601, DOI:10.15376/biores.7.1.0593-0601.
- S. Giraud, S. Bourbigot, M. Rochery, I. Vroman, L. Tighzert and R. Delobel, Microencapsulation of phosphate: application to flame retarded coated cotton, Polym. Degrad. Stab., 2002, 77, 285–297, DOI:10.1016/S0141-3910(02)00063-0.
- S. Demirbağ and S. A. Aksoy, Encapsulation of phase change materials by complex coacervation to improve thermal performances and flame retardant properties of the cotton fabrics, Fibers Polym., 2016, 17, 408–417, DOI:10.1007/s12221-016-5113-z.
- X. Qiu, L. Lu and Z. Chen, Preparation and characterization of flame retardant phase change materials by microencapsulated paraffin and diethyl ethylphosphonate with poly(methacrylic acid-co-ethyl methacrylate) shell, J. Appl. Polym. Sci., 2015, 132(17) DOI:10.1002/app.41880.
- J. Kosny, E. Kossecka, A. Brzezinski, A. Tleoubaev and D. Yarbrough, Dynamic thermal performance analysis of fiber insulations containing bio-based phase change materials (PCMs), Energy Build., 2012, 52, 122–131, DOI:10.1016/j.enbuild.2012.05.021.
- D. A. Davis, D. E. Work and T. J. Riazzi, Microencapsulation of a Phase Change Material with enhanced flame resistance, US Pat. Application No. 12/575,507, 2010.
- G. Fang, H. Li, Z. Chen and X. Liu, Preparation and properties of palmitic acid/SiO2 composites with flame retardant as thermal energy storage materials, Sol. Energy Mater. Sol. Cells, 2011, 95, 1875–1881, DOI:10.1016/j.solmat.2011.02.010.
- P. Zhang, Y. Hu, L. Song, J. Ni, W. Xing and J. Wang, Effect of expanded graphite on properties of high-density polyethylene/paraffin composite with intumescent flame retardant as a shape-stabilized phase change material, Sol. Energy Mater. Sol. Cells, 2010, 94, 360–365, DOI:10.1016/j.solmat.2009.10.014.
- P. Zhang, Y. Hu, L. Song, H. Lu, J. Wang and Q. Liu, Synergistic effect of iron and intumescent flame retardant on shape-stabilized phase change material, Thermochim. Acta, 2009, 487, 74–79, DOI:10.1016/j.tca.2009.01.006.
- Y. Cai, Q. Wei, F. Huang, S. Lin, F. Chen and W. Gao, Thermal stability, latent heat and flame retardant properties of the thermal energy storage phase change materials based on paraffin/high density polyethylene composites, Renew. Energy, 2009, 34, 2117–2123, DOI:10.1016/j.renene.2009.01.017.
- Y. Cai, Q. Wei, F. Huang and W. Gao, Preparation and properties studies of halogen-free flame retardant form-stable phase change materials based on paraffin/high density polyethylene composites, Appl. Energy, 2008, 85, 765–775, DOI:10.1016/j.apenergy.2007.10.017.
- X. Du, Y. Fang, X. Cheng, Z. Du, M. Zhou and H. Wang, Fabrication and Characterization of Flame-Retardant Nanoencapsulated n-Octadecane with Melamine–Formaldehyde Shell for Thermal Energy Storage, ACS Sustain. Chem. Eng., 2018, 6, 15541–15549, DOI:10.1021/acssuschemeng.8b03980.
- X. Du, S. Wang, Z. Du, X. Cheng and H. Wang, Preparation and characterization of flame-retardant nanoencapsulated phase change materials with poly(methylmethacrylate) shells for thermal energy storage, J. Mater. Chem. A, 2018, 6, 17519–17529, 10.1039/c8ta07086e.
- C. Amaral, R. Vicente, J. Eisenblätter and P. A. A. P. Marques, Thermal characterization of polyurethane foams with phase change material, Cienc. Tecnol. Mater., 2017, 29, 1–7, DOI:10.1016/j.ctmat.2016.06.015.
- R. Chen, X. Huang, R. Zheng, D. Xie, Y. Mei and R. Zou, Flame-retardancy and thermal properties of a novel phosphorus-modified PCM for thermal energy storage, Chem. Eng. J., 2020, 380, 122500, DOI:10.1016/j.cej.2019.122500.
- L. Xu, X. Liu, Z. An and R. Yang, EG-based coatings for flame retardance of shape stabilized phase change materials, Polym. Degrad. Stab., 2019, 161, 114–120, DOI:10.1016/j.polymdegradstab.2019.01.020.
- Y. Jiang, P. Yan, Y. Wang, C. Zhou and J. Lei, Form-stable phase change materials with enhanced thermal stability and fire resistance via the incorporation of phosphorus and silicon, Mater. Des., 2018, 160, 763–771, DOI:10.1016/j.matdes.2018.10.020.
- Y. Zhang, B. Tang, L. Wang, R. Lu, D. Zhao and S. Zhang, Novel hybrid form-stable polyether phase change materials with good fire resistance, Energy Storage Materials, 2017, 6, 46–52, DOI:10.1016/j.ensm.2016.10.001.
- C. Guo, Y. Chen and L. Li, Investigation on interfacial interaction and thermal properties of flame retarded wood-plastic form-stable phase change material, Compos. Interfaces, 2019, 26, 597–610, DOI:10.1080/09276440.2018.1522192.
- J. Wang, Y. Wang and R. Yang, Flame retardance property of shape-stabilized phase change materials, Sol. Energy Mater. Sol. Cells, 2015, 140, 439–445, DOI:10.1016/j.solmat.2015.05.007.
- P. Zhang, L. Song, H. Lu, J. Wang and Y. Hu, The influence of expanded graphite on thermal properties for paraffin/high density polyethylene/chlorinated paraffin/antimony trioxide as a flame retardant phase change material, Energy Convers. Manag., 2010, 51, 2733–2737, DOI:10.1016/j.enconman.2010.06.009.
- Y. Wang and J. Zhao, Preliminary study on decanoic/palmitic eutectic mixture modified silica fume geopolymer-based coating for flame retardant plywood, Constr. Build. Mater., 2018, 189, 1–7, DOI:10.1016/j.conbuildmat.2018.08.205.
- Y.-H. Huang, Y.-X. Cheng, R. Zhao and W.-L. Cheng, A high heat storage capacity form-stable composite phase change material with enhanced flame retardancy, Appl. Energy, 2020, 262, 114536, DOI:10.1016/j.apenergy.2020.114536.
- T. Ma, L. Li, Q. Wang and C. Guo, High-performance flame retarded paraffin/epoxy resin form-stable phase change material, J. Mater. Sci., 2019, 54, 875–885, DOI:10.1007/s10853-018-2846-7.
- B. Beyhan, K. Cellat, Y. Konuklu, C. Gungor, O. Karahan, C. Dundar and H. Paksoy, Robust microencapsulated phase change materials in concrete mixes for sustainable buildings, Int. J. Energy Res., 2017, 41, 113–126, DOI:10.1002/er.3603.
- TS EN 802, Turkish Standard for Design of Concrete Mixes, Ankara, 2009.
- EN ISO 1716, Reaction to fire tests for products - determination of the gross heat of combustion (calorific value), 2018.
- ISO 1182, Reaction to fire tests for products - non-combustibility test, 2010.
- EN ISO 11925-2, Reaction to fire tests - ignitability of products subjected to direct impingement of flame - part 2: single-flame source test, 2011.
- EN 13501-1:2007+A1:2009, Fire classification of construction products and building elements in part 1: classification using data from reaction to fire tests, 2009.
|
This journal is © The Royal Society of Chemistry 2020 |