DOI:
10.1039/D0RA02267E
(Paper)
RSC Adv., 2020,
10, 17515-17523
Enhanced thermal stability, hydrophobicity, UV radiation resistance, and antibacterial properties of wool fabric treated with p-aminobenzenesulphonic acid†
Received
11th March 2020
, Accepted 23rd April 2020
First published on 5th May 2020
Abstract
Wool fibre is a popular fibre for the manufacture of apparel and floor coverings, but it does not have adequate thermal stability, antistatic, UV resistance, and antibacterial properties that are required for some applications, such as outerwear and hospital gowns. In this work, a wool fabric was treated with para-aminobenzenesulphonic acid (ABSA) by the oxidative polymerisation method and its effect on the thermal stability, UV radiation resistance, electrical conductivity and antibacterial properties of the treated fabric was systematically evaluated. It was found that the ABSA treatment had synergistic effects on the various functional properties of the treated fabric. The ABSA treatment not only made the fabric antibacterial but also enhanced its UV radiation absorption capability, surface hydrophobicity, electro-conductivity, tensile strength, and thermal stability. The maximum degradation temperature of the wool fibre increased from 339.5 °C to 349.6 °C and the UV-B transmission through the fabric at 290 nm reduced to 1.5%. The surface hydrophobicity of the treated fabric samples also improved as the surface contact angle of the fabric increased from 119.5° for the untreated to 131.7° for the fabric treated with 4% ABSA. The surface electrical resistance decreased from 1200 × 109 to 484 × 109 Ohm cm−1, and the treated fabric also showed excellent antibacterial activity against Staphylococcus aureus and Klebsiella pneumoniae. The developed treatment could be used in the textile industry as an energy-efficient process for the multi-functionalisation of wool and other polyamide fibres.
Introduction
Because of their exceptional warmth, fire-retardancy, stain-resistance, and odour control properties, wool fibres are used for the manufacture of apparel and interior textiles.1,2 However, wool fibre has poor UV protection, antibacterial, and antistatic properties. To enhance these properties, wool fabrics are treated with various organic compounds and polymers by multi-stage treatments, which increase the treatment cost and time. Technical textiles (such as workwear), as well as outdoor textiles, need to have multifunctional properties, such as antistatic, UV protective, and antibacterial properties. Multi-stage treatments are usually used to introduce these properties. However, if they can be introduced by a single treatment, it may reduce the fibre damage, production cost, and time.
To make wool fabric UV protective, a range of methods including the treatment with silver and cupric oxide nanoparticles,3,4 honeysuckle extract,5 β-cyclodextrin,6 and UV absorbers derived from hydroxyphenyl benzotriazole,7 have been investigated. UV radiation absorbers and nanoparticles provide some levels of protection to the wearer from detrimental solar irradiation but some of these compounds and nanoparticles may have harmful effects on human health.
Antibacterial treatments are frequently used for the treatment of textile fabrics to protect the wearer from harmful bacteria and fungi. Quaternary ammonium compounds,8 chitosan,9 polyhexamethylene biguanide,10 ε-poly-L-lysine,11 and silver nanoparticles,4 have been investigated to make wool fabric antibacterial. Wool fabrics treated with quaternary ammonium compounds not only provide antibacterial activity but also enhance their antistatic properties. However, some of these compounds, such as triclosan (which is a chlorinated bisphenol), are known to produce antibiotic resistance.12 These treatments provide protection against only selective bacterium class and therefore, there is a need to develop new antibacterial treatments that do not produce antibiotic resistance.
The generation of static electricity in apparel can have serious effects as the static charge can cause fire and damage to electronic equipment. Wool fibre-made apparel is mostly used as outerwear and can encounter electronic equipment, and the static charge formed in the apparel may damage them. Polyaniline is one of the most explored polymers for making textiles electro-conductive and antistatic.13,14 However, its monomer, aniline, is not only highly toxic with an LD50 (rat) value of 100 mg kg−1 but also a possible carcinogen.15 Moreover, aniline is soluble in water only at highly acidic conditions but at that conditions, it cannot be absorbed into wool fibre as both aniline and wool fibre are cationic. However, its sulphonated derivatives, such as ABSA with an LD50 (rat) value of 12
300 mg kg−1 could be an eco-friendly alternative.16 ABSA can readily be absorbed into the wool fibres by electrostatic attractions and also can be polymerised at ambient conditions like aniline.15,17 It has been reported that polyaniline treated fabrics showed very good antibacterial activity,18,19 but no published literature until present reported the application of ABSA to any textile fibre as an antibacterial agent.
Recently the synthesis of sulphonated polyaniline, a self-doped electroconductive polymer, has attracted the attention as an alternative to polyaniline,20–22 but the poor reactivity of some sulphonic acid derivatives of aniline containing an electron attractive sulfonic acid group made the synthesis of high molecular weight polymer difficult.23 Therefore, the synthesis of sulphonated polyaniline is carried out either by sulphonation of polyaniline or by copolymerisation with sulphonic acid derivatives of aniline.20,24–26 In situ polymerisation of various sulphonated derivatives of aniline at mild conditions without using any oxidising agent produces only dimers as the presence of the amino group in the ortho position and methoxy group in the benzene ring inhibits their polymerisation.27 The oxidative polymerisation of 2-methoxyaniline-5-sulphonic acid successfully produced a mixture of low (Mn = 2436) and high molecular weight (Mn = 6869) polymers. However, they showed poor electrical conductivity (9 × 10−3 S cm−1) compared to the doped-polyaniline,26,28 but that could be enough for antistatic applications.
The target of this work is to develop an energy-efficient treatment that makes wool fabric multifunctional. In this work, for the first time, we are reporting the application of ABSA for the improvement of various physical and chemical properties of wool fabric. The effect of ABSA treatment on thermal stability, mechanical properties, antibacterial, antistatic, and UV radiation resistance of wool fabric were systematically investigated and reported.
Experimental
Materials
A plain-woven wool fabric of 126 g m−2 having 15 ends per cm and 12 picks per cm made from merino wool fibres of average 19 μm diameter. ABSA, potassium peroxydisulphate (PPS), acetic acid, and sodium acetate were of analytical reagent grade, and they were supplied by Sigma-Aldrich Limited (USA). Sandozin MRN and Sandoclean PC were purchased from Arkema Chemicals, Switzerland. Albegal FFA was supplied by Huntsman Chemicals, USA. Softly®, a wool fibre washing detergent, was purchased from Pental Products Limited (Australia).
Treatment of wool fabric with ABSA by oxidative polymerisation
The treatment of wool fabric with ABSA was carried out in an Ahiba laboratory dyeing machine (Model 1000, Datacolor International, Switzerland) using materials to liquor ratio of 1
:
30. Wool fabric samples were placed in the treatment bath prepared with the required quantity of ABSA, 1 g l−1 Albegal FFA (antifoaming agent), and 0.25 g l−1 Sandozin MRN. A wool fabric sample wrapped on a perforated stainless-steel carrier was introduced into the bath. The pH of the bath was set at 3.0 ± 0.1 and the temperature of the bath was then slowly increased to 25 °C at 1 °C min−1, held for 15 min, PPS added and held for 120 min. After the completion of the polymerisation treatment, the liquor drained, and the treated samples were washed with 1 g l−1 Sandoclean PC at 50 °C for 15 min. They were then rinsed with cold water several times and dried at 60 °C for 30 min.
Thermal stability and mechanical properties
The thermal stability of ABSA-treated and untreated wool fabrics was assessed by thermo-gravimetric (TG) analysis. 12 mg of treated and untreated wool fabric samples were heated by a Shimadzu Thermogravimetric Analyser (Model: TGA-50H, Shimadzu Corporation, Japan) from room temperature to 600 °C at a heating rate of 10 °C min−1 under the nitrogen atmosphere. The tensile properties were measured at 20 ± 2 °C and 65 ± 2% relative humidity (RH) according to ASTM Test Method D5035-06: Standard Test Method for Breaking Force and Elongation of Textile Fabrics (Strip Method) by using an Instron Universal Tensile Testing Machine (Model 4204, Instron Testing Systems, Inc., Norwood, USA) by extending a 25.4 × 152.4 mm sample at 50 mm min−1 using a gauge length of 100 mm. The samples were pre-conditioned at the above-mentioned conditions for 3 days and at least 10 samples were tested for each treatment.
Surface characterisations
The contact angle was measured in a dynamic mode by using a KSV Contact Angle Measurement Apparatus (Model: CAM 100, KSV Instruments, Helsinki, Finland). For each treatment, the contact angle was measured at 10 positions of top and bottom surfaces of the fabric and the average contact angle was reported. The first measurement was taken immediately after placing the droplet of water on the test fabric surface and then at 30 s interval until 120 s. The surface morphologies of the fabric were examined by a Hitachi scanning electron microscope (Model: TM3030 Plus, Hitachi Corporation, Japan) at an accelerated voltage of 15 kV without any conductive coating. The elemental analysis of C, O, N, and S was carried out by an energy dispersive X-ray (EDX) using the same scanning electron microscope that was used for the surface morphology study equipped with Quantax 75 energy dispersive X-ray attachment. The change in chemical characteristics of the surface of the treated wool fabrics was assessed by the Fourier transform infrared (FTIR) spectroscopy. The FTIR spectra of the fabric surface were recorded by a spectrometer (Model: System 2000, PerkinElmer Corporation, USA) equipped with an attenuated total reflectance (ATR) attachment at a resolution of 4 cm−1 in the range from 650 to 4000 cm−1 by using a ZnSe crystal and 64 scans were signal-averaged. The untreated and various ABSA-treated wool fabrics were preconditioned at the standard atmospheric conditions (20 ± 2 °C and 50 ± 2% relative humidity) for 48 h and the surface resistance measurement was carried out at that standard atmospheric conditions at an applied voltage of 100 V by a surface/volume resistance meter with a concentric ring probe (Model 152-1, Trek, Inc., Lockport, USA). At least 10 measurements were taken for each treated sample at various positions of the fabric and the averages are reported here.
Assessment of UV radiation transmission and the durability of the treatment to washing
The diffuse transmittance of UV light through a fabric sample was measured at the wavelength of 200 to 400 nm by a Thermo Scientific UV-vis spectrometer (Model: Evolution 220, Thermo Fisher Scientific Inc., Waltham, USA) equipped with an integrating sphere reflectance accessory (ISA-220). The UV radiation transmittance through the fabric was assessed at 290 nm as the UV-B radiation can severely damage human skin.
Antibacterial activity
The antibacterial activity of wool fabrics treated with various concentrations of ABSA was performed according to the AATCC Test Method 147-1999 (Assessment of Textile Materials: Parallel Streak Method) against Staphylococcus aureus and Klebsiella pneumoniae. In this method, the bacterial culture was prepared using a nutrient broth of 5 g l−1 peptone and 3 g l−1 beef extracts with the pH set at 6.8 ± 0.1. Five streaks of 100 times diluted bacteria were placed on the sterilised agar gel in a Petri dish by using an inoculating loop and a specimen was gently placed in intimate contact with the agar surface. The Petri dishes were incubated for 48 h at 37 ± 2 °C and the growth of bacteria along the side and underneath of the test specimen was observed.
Results and discussion
Polymerisation of ABSA and the interaction with wool fibre
The possible mechanism of polymerisation of ABSA and the interaction of the polymerisation product with wool fibre are shown in Scheme 1. The oxidative polymerisation of ABSA possibly did not produce a high molecular weight polymer rather produced dimers of ABSA due to the steric hindrance induced by the sulfonic acid group at the C4 position of ABSA,23 which can act as an ionic crosslinking agent. The sulphonate groups of dimers of ABSA formed ionic crosslinking with the two protonised amino groups of two macromolecular chains of wool fibre as shown in Scheme 1.
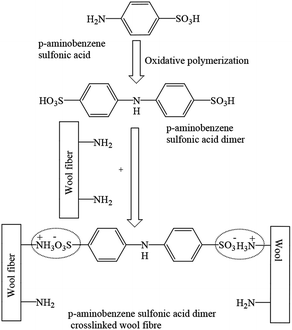 |
| Scheme 1 Formation of ABSA dimer and its interaction with amino groups of wool fibre. | |
Electrical conductivity and the durability of the treatment to washing
The electrical conductivity was measured by measuring the surface resistance, the higher the surface resistance the lower the electrical conductivity. Fig. 1(a) shows the surface electrical resistance of wool fabric treated with various concentrations of ABSA treated at pH 3 for 60 minutes. The untreated wool fabric showed quite high electrical resistance, 1200 × 109 Ohm cm−1. The treatment with ABSA had a positive effect on the reduction of surface resistance of wool fabrics. Even at 1% on the weight of fibre (owf) of ABSA dosage, the surface resistance was reduced to 690.4 × 109 Ohm cm−1. Further increase in the ABSA concentration to 4% owf reduced the surface resistance to 532.7 × 109 Ohm cm−1.
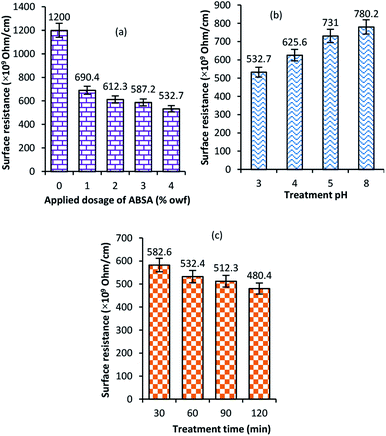 |
| Fig. 1 Effect of applied dosage of ABSA (a), treatment pH (b) and time (c) on the average surface resistance of wool fabrics treated with ABSA. | |
Fig. 1(b) shows the effect of treatment pH on the surface resistance of the ABSA-treated fabrics. The surface resistance increased with the increase in the treatment pH. The lowest surface resistance was shown by the fabric treated at pH 3. The surface resistance is inversely proportional to the applied dosage of ABSA. The increase of pH reduces the absorption of ABSA by wool. Wool fibres absorb ABSA in acidic conditions as the isoelectric point of wool fibre in an aqueous medium is at pH 4.5 (i.e. above this pH point wool fibre is anionic), and the decrease in pH below 5 increases the cationic charge of wool fibre. Therefore, the absorption of ABSA by wool was the highest at pH 3 and the fabric treated at pH 3 showed the lowest surface charge. Fig. 1(c) shows the effect of treatment time on the wool fabric treated at pH 3 with 4% ABSA. The increase in treated time decreased the surface resistance as the increase in treatment time increased the absorption of ABSA into the wool fibre. The sodium dodecylbenzene sulphonate and cetyltrimethylammonium bromide mixed surfactant-doped polyaniline nanofibres showed electrical conductivity as high as 0.102 S cm−1.29 It was reported that ABSA as a dopant at the ABSA to aniline ratio of 3
:
7 produced a polyaniline film that had an electrical conductivity of 2.4 × 10−3 S cm−1 compared to 100% polyaniline film, which exhibited the conductivity of 3.3 × 10−8 S cm−1. However, the increase of the ABSA ratio to 7
:
3, the electrical conductivity of polyaniline decreased to 5.7 × 10−3 S cm−1. The separation of the low molecular weight components of poly(2-methoxyaniline-5-sulphonic acid) from the high molecular weight components increased the electrical conductivity of the produced film to 9 × 10−3 S cm−1.28 The wool fabric treated with 4% ABSA in this work exhibited quite poor electrical conductivity, which is consistent with the results reported for the sulphonated polyaniline films and nylon and polyester fabric treated with polyaniline.24,30 However, this level of conductivity is enough for the application as an antistatic fabric. As the optimum pH and treatment time are 3 and 120 min respectively, further experiments were carried out at those conditions.
The durability of the treatment to washing was measured by measuring the surface resistance of the fabric treated with 4% owf ABSA at pH 3 for 30 min after 5, 10, 15 and 20 cycles of washing in a Wascator. Fig. S1 (ESI†) shows the surface resistance of fabric after various cycles of washing. The unwashed fabric showed the surface resistance of 480.4 × 109 Ohm cm−1. Hardly any change of the surface resistance observed for the fabric washed for 5 cycles of washing. Even after 20 washing only a marginal increase in the surface resistance was observed (495.3 × 109 Ohm cm−1), which shows that the treatment is quite durable to washing.
Thermal stability
Fig. 2 shows the thermogravimetric curves of untreated and ABSA-treated wool fabric at 4% owf. It is evident that the thermal stability of wool fabric considerably improved as the temperature of the maximum degradation moved from a lower temperature to a higher temperature. The untreated wool fabric showed a mass loss at three stages: from room temperature to 110 °C, 241 to 457 °C and 457 to 600 °C. The maximum mass loss occurred at 241 to 457 °C and it was ∼53%. The next highest mass loss (almost 9%) occurred at room temperature to 105 °C, which is mainly due to the loss of absorbed moisture. The wool fabric treated with 4% owf ABSA had a mass loss at two stages: 247 to 505 °C and 505 to 600 °C. At room temperature to 247 °C, very negligible mass loss was observed (∼1.5%) compared to 9% mass loss observed for the control wool, which suggests that the ABSA treatment considerably reduced the moisture content of wool fibre.
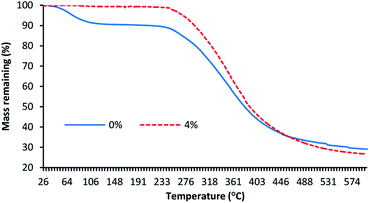 |
| Fig. 2 The thermogravimetric weight loss curves of untreated and 4% owf ABSA treated wool fabrics. | |
In the first stage, the maximum mass loss (∼73.5%) occurred due to the loss of volatiles formed by the thermal degradation of wool keratin and ABSA. The maximum degradation temperature of the control wool was at 339.5 °C, which moved to 349.6 °C for the wool fabric treated with 4% owf ABSA. The maximum mass loss occurred at the second stage (for the ABSA treated wool at the first-stage) due to the loss of volatiles formed by the thermal degradation of wool keratin with the elimination of hydrogen sulphide gas due to the destruction of disulphide bonds of wool, which is thought to be the primary cause of mass loss at this stage.31,32 However, it can be seen the char yield decreased from 29.1% for the control wool fabric to 26.7% for the wool fabric treated with ABSA, which suggest that the degradation of ABSA possibly continued with an increase in the temperature or the degradation products of ABSA induced further degradation of wool keratin. Possibly, the increase in sulphur content in the ABSA-treated wool increased its thermal stability as sulphur species slowed down the thermal degradation of wool by destroying the radicals generated during the combustion of wool fibre.31
Surface hydrophobicity
Table 1 shows the contact angle of the untreated and treated wool fibre surface and the optical micrographs of the water droplets on the surface of the fabric are shown in Fig. S2 (ESI†). The treatment of wool fabric with ABSA made the fabric strongly hydrophobic. The control wool fabric showed some level of hydrophobicity as the contact angle at 0 s was 119.5°, which slowly decreased to 115.9° after 120 s, which is consistent with the previously published data.33,34 The surface of the untreated wool fabric is hydrophobic because of the presence of 18-methyl eicosanoic acid (18-MEA), which is bonded to the fibre surface through thioester bonds. The contact angle, especially at 120 s, increased with an increase in the ABSA concentrations. The highest contact angle was shown by the surface of wool fabric treated with 4% owf ABSA, and the contact angle increased to 131.7°, which was stable at least for 120 s. The blocking of water-loving amino groups of wool by crosslinking with ABSA polymer enhanced the hydrophobicity of wool fabric.
Table 1 The dynamic contact angle of untreated and ABSA-treated wool fabrics at various times
ABSA dosage (% owf) |
Average contact angle (°) at |
0 s |
30 s |
60 s |
90 s |
120 s |
0 |
119.5 |
117.3 |
116.6 |
116.0 |
115.9 |
1 |
120.2 |
120.5 |
120.0 |
119.9 |
120.2 |
2 |
124.1 |
124.4 |
124.6 |
124.6 |
124.5 |
3 |
130.0 |
130.0 |
129.8 |
129.6 |
128.9 |
4 |
131.7 |
131.7 |
131.8 |
131.6 |
131.7 |
UV transmission through the wool fabric
Fig. 3 shows the UV light transmission through the untreated and treated fabrics. UV radiation levels are divided into three zones, UV-A (320–400 nm), UV-B (290–320 nm) and UV-C (200–290 nm). Of the solar UV radiation reaches the earth, 6% in the UV-B region and the rest 94% in the UV-A region but UV-B is 1000 times more damaging compared to the UV-A. Therefore, the fabric's ability to block UV-B is the determining factor to protect the wearer from the damaging effects of sun exposure. Therefore, for apparels, UV transmission at 290 nm is measured.35 For the untreated control fabric, the UV transmission at 290 nm is 3.86%. Generally, a fabric showing less than 2% of UV-B transmission is treated as a good UV protective fabric. The increase in ABSA concentration progressively decreased the UV light transmission through the fabric, and at 4% ABSA concentration, the UV light transmission reduced to 1.56% at 290 nm. The results suggest that the treatment of wool fabric with ABSA considerably increased its UV protection capability. The UV-vis spectrum of ABSA measured by others shows that ABSA and polyaniline both have an absorption peak at 248 nm suggesting that it may absorb UV radiation.36,37 Therefore, it is not unusual that ABSA dimer treated wool fabric showed good UV radiation absorption capacity.
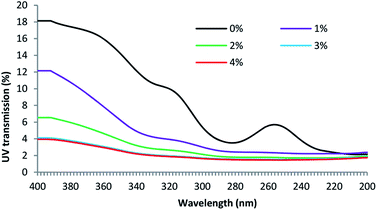 |
| Fig. 3 Effect of ABSA concentration on the UV transmission through wool fabrics treated with ABSA. | |
Antibacterial properties
Table 2 shows the antibacterial performance of wool fabric treated with various concentrations of ABSA against Staphylococcus aureus (Gram-positive) and Klebsiella pneumoniae (Gram-negative) bacteria. The untreated fabric did not show any antibacterial activity and no zone of inhibition as spontaneous growth of bacteria was observed directly under the specimens for both types of bacteria (not shown). In the case of 1% ABSA, scanty growth of bacteria directly under the test specimens was observed and no zone of inhibition was observed (not shown). The increase of concentration of ABSA suppressed the growth of both types of bacteria directly under the test specimens but the samples did not show any zone of inhibition even at the highest concentration investigated (4% owf). Therefore 2% owf should be the lowest concentration of ABSA consistent with the non-leaching type antibacterial treatments. The results suggest that no leaching of ABSA took place into agar gel medium and ABSA is quite effective as an antibacterial agent.
Table 2 Antibacterial performance of wool fabric treated with different concentrations of ABSA against Gram-positive and Gram-negative bacteria
ABSA conc. (%) |
Antibacterial performance against |
Staphylococcus aureus |
Klebsiella pneumoniae |
2 |
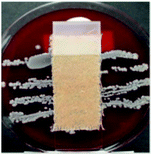 |
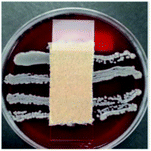 |
3 |
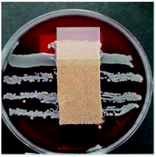 |
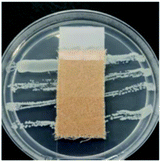 |
4 |
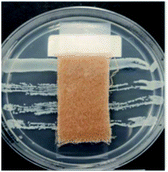 |
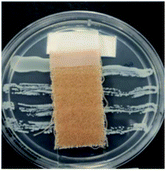 |
Hejchman et al. reported that N-(3,5-dichloro-2-hydroxybenzylidene)-4-aminobenzenesulphonic acid showed strong antibacterial activity against Staphylococcus aureus.38 Antibacterial activity of poly(sodium 4-styrene sulphonate) against Neisseria gonorrhoeae, and Chlamydia trachomatis is already known.39 Yadav et al. found that 4-[1-(substituted aryl/alkyl carbonyl)-benzoimidazol-2-yl]-benzenesulphonic acids showed excellent antibacterial activity.40 Linear alkyl benzene sulphonic acid also reported to have antibacterial activity against some aquatic bacteria.41 Therefore, it is not surprising that ABSA-treated fabric showed good antibacterial activity. ABSA polymer probably induced changes in the pHin and also caused hyperpolarisation of the cell membrane of bacteria resulting in the death of bacteria.42
Tensile properties
The mechanical properties were assessed to observe the effect of ABSA addition to wool on its tensile strength, breaking tenacity and elongation at break. The addition of ABSA to wool only showed a marginal effect on the tensile strength of wool fibre as shown in Table 3. The tensile strengths in the warp and weft directions shown by the untreated fabric were 11.1 ± 0.2 and 9.6 ± 0.3 MPa respectively. The tensile strength in both directions slightly increased with an increase in the applied dosage of ABSA as the tensile strength increased from 11.1 ± 0.2 and 9.6 ± 0.3 MPa to 12.0 ± 0.2 and 10.3 ± 0.3 MPa respectively for the fabric treated with 3% owf of ABSA. Further increase in the concentration did not further increase the tensile strength. On the other hand, the breaking tenacity, elongation at peak and elongation at break of the fabric slightly decreased with an increase in the applied dosage of ABSA. It appears that anionic sulphonate groups of ABSA dimers formed ionic crosslinking with the cationic amino groups of wool fibre, which increased the tensile strength of the fabric but decreased the molecular chain movement in wool fibre resulting in a decrease in elongation at peak and elongation at break. It is known that ionic crosslinking and polymeric coating increases the tensile strength of the coated fabric but reduces the extensibility.43,44 Therefore, ionic crosslinking probably caused the increase in the tensile strength of the ABSA-treated fabric.
Table 3 Mechanical properties of wool fabric treated with various concentrations of ABSA
ABSA dosage (% owf) |
Warp-direction |
Weft-direction |
Tensile strength (MPa) |
Elongation at peak (%) |
Breaking force (N) |
Elongation at break (%) |
Tensile strength (MPa) |
Elongation at peak (%) |
Breaking force (N) |
Elongation at break (%) |
0 |
11.1 ± 0.2 |
55.4 ± 1.1 |
179 ± 4 |
58.8 ± 1.1 |
9.6 ± 0.3 |
52.7 ± 2.1 |
142 ± 1 |
67.0 ± 0.3 |
1 |
11.6 ± 0.3 |
52.9 ± 2 |
179 ± 2 |
56.2 ± 0.9 |
10.0 ± 0.2 |
50.1 ± 1.6 |
144 ± 3 |
67.8 ± 0.8 |
2 |
11.9 ± 0.3 |
50.9 ± 2 |
178 ± 3 |
59.3 ± 1.2 |
10.2 ± 0.2 |
49.8 ± 2.2 |
143 ± 3 |
68.2 ± 1.3 |
3 |
12.0 ± 0.2 |
50.2 ± 3 |
174 ± 2 |
57.9 ± 0.8 |
10.3 ± 0.3 |
50.0 ± 1.5 |
141 ± 2 |
67.3 ± 0.7 |
4 |
12.0 ± 0.2 |
50.7 ± 3 |
167 ± 4 |
59.7 ± 2.1 |
10.3 ± 0.3 |
53.0 ± 2.1 |
140 ± 2 |
69.0 ± 0.8 |
Elemental analysis
The EDX spectra of wool fabric treated with various concentrations of ABSA are shown in Fig. S3 (ESI†) and the chemical compositions are provided in Table S1 (ESI†). The treatment with ABSA had a considerable effect on the elemental compositions of wool fibre, especially on the sulphur content of the fibre. The composition of C, O, N, and S of untreated wool fibre was 52.68, 25.92, 19.79 and 1.61% respectively as shown in Table S1 (ESI†). The C and O content decreased, and the S content increased with an increase in the concentration of ABSA. The S content increased from 1.61% for the control fabric to 4.55% for the fabric treated with 4% owf ABSA. As ABSA contains sulphur, suggests the presence of ABSA in the treated wool fibres. The elemental mappings of wool fabric treated with various concentrations of ABSA are shown in Fig. 4, which shows that all the elements including the S element are uniformly distributed in the treated fibres suggesting that ABSA was uniformly absorbed into the wool fibre.
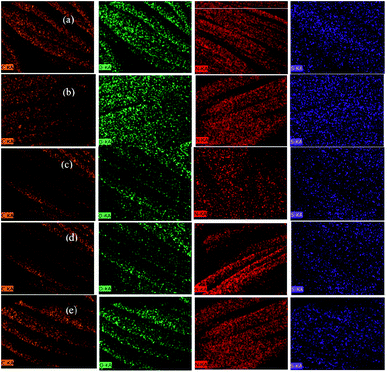 |
| Fig. 4 Elemental mapping of C, N, O, and S of untreated wool fabric (a) and also wool fabric samples treated with 1 (b), 2 (c), 3 (d), and 4% (e) owf ABSA. | |
Surface morphologies
SEM scanning was carried out to observe the surface coverage of wool fibres by poly(ABSA) at different concentrations of ABSA monomer. Fig. 5 shows the SEM images of wool fabrics treated with 1, 2, 3, and 4% ABSA at 25 °C. The wool fabric surface treated with 1% ABSA still exhibited the typical scaly structure of the wool fibre with some uniform but small size deposition of ABSA on the fibre surface. The surface coverage of wool fibre gradually increased with an increase in the concentration of ABSA. The fabric treated with 2% ABSA showed more coverage of fibre surface by ABSA compared to the wool fabric sample treated with 1% ABSA. The fabric treated with 4% ABSA not only shows the coverage of single fibre with ABSA but also shows the binding of fibres by the formed ABSA polymer. The formation of the film suggests that ABSA was polymerised to poly(ABSA) by oxidative polymerisation. However, the small increase in tensile strength of the treated wool fabric (only 8.2%) suggests that the polymerisation only produced low molecular weight polymer and the formed ABSA films could be quite weak. Therefore, the increase in ABSA concentration only marginally increased the tensile strength of the fabric.
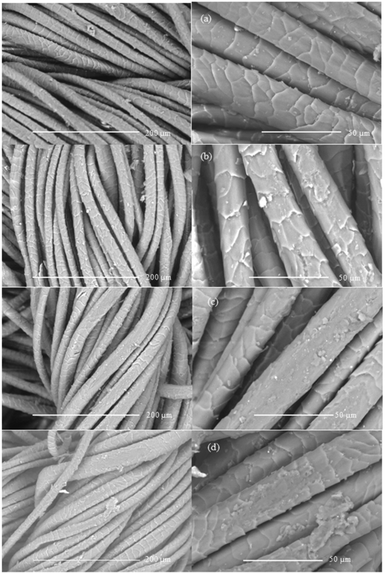 |
| Fig. 5 SEM micrographs of wool fabrics treated with 1 (a), 2 (b), 3 (c), and 4% (d) at pH 3 and 25 °C. | |
ATR-FTIR
The ATR-FTIR spectra of untreated and wool fabrics treated with various concentrations of ABSA are shown in Fig. 6. The spectrum of wool fibre shows typical IR bands of wool fibre, such as wool keratin-related IR bands of amide III, amide II and amide I peak at 1227, 1350, 1540, and 1635 cm−1, respectively.45 The peak at 1506 cm−1 could be attributed to the C–N stretching and also to the N–H in-plane bending vibrations (amide II). The broad IR band at 3250 cm−1 could be attributed to the hydroxyl groups of wool fibre. The band at 1040 cm−1 could be attributed to the Bunte-salt groups of wool fibre. Conversely, the wool fabric treated with ABSA shows new bands at 668, 800, and 1030 cm−1 and they could be attributed to the benzene ring, C–S bond, and sulphonate groups of ABSA respectively. The spectra of ABSA-treated wool fabrics also show new IR bands at 1261 cm−1, which is due to the C–N stretching vibration of ABSA. The intensity of IR bands of sulphonate groups at 1030 cm−1 increased with an increase in the concentration of ABSA. The presence of sulphonate groups (–SO3) in the spectra of wool fabric treated with various concentrations of ABSA suggests the presence of ABSA in the treated fabric and the decrease in the intensity of amide peaks suggest the formation of crosslinking of ABSA with the amino groups of wool fibre.
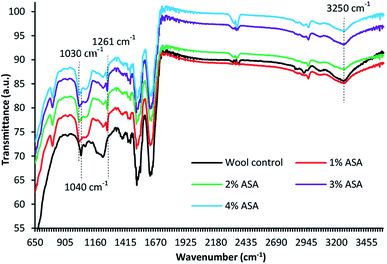 |
| Fig. 6 ATR-FTIR spectra of wool fabrics treated with various concentrations of ABSA at 25 °C for 120 min. | |
Conclusions
This work has demonstrated that ABSA can be used for the multi-functionalisation of wool fabric, which not only made the fabric antibacterial but also increased the tensile strength, hydrophobicity, UV radiation absorption, and antistatic properties of the treated fabric. The treatment pH and time, and ABSA dosage had a great effect on the antistatic properties of the fabric. The treatment with ABSA also increased the UV radiation absorption capacity of wool fabric thereby increasing its UV protection capability and reduced the surface resistivity to a level suitable for antistatic applications. Moreover, the treated fabric showed very strong antibacterial activity against Staphylococcus aureus and Klebsiella pneumoniae. The developed treatment could be used in industry for the multi-functionalisation of wool and other polyamide fibres.
Conflicts of interest
There are no conflicts to declare.
Acknowledgements
The author acknowledges the financial support received from the Ministry of Business Innovation and Employment (MBIE) of the New Zealand Government through Grant #C10X0824. The authors would like to thank Gail Krsinic of Advantage Networking Ltd. for SEM analysis, Barbara Müller of R. J. Hill Laboratories for the antibacterial performance assessment, and Stewart Collie for suggestions to improve the quality of the article.
Notes and references
- M. M. Hassan and C. M. Carr, J. Adv. Res., 2019, 18, 39–60 CrossRef CAS
. - M. M. Hassan and J. Shao, Key Eng. Mater., 2015, 671, 32–39 Search PubMed
. - A. B. Rezaie, M. Montazer and M. M. Rad, J. Cleaner Prod., 2017, 166, 221–231 CrossRef CAS
. - M. M. Hassan, Colloids Surf., A, 2019, 581, 123819 CrossRef CAS
. - S.-S. Sun and R.-C. Tang, Ind. Eng. Chem. Res., 2011, 50, 4217–4224 CrossRef CAS
. - N. A. Ibrahim and E. M. R. El-Zairy, Carbohydr. Polym., 2009, 76, 244–249 CrossRef CAS
. - J.-H. Riedel and H. Höcker, Text. Res. J., 1996, 66, 684–689 CrossRef CAS
. - W. Tian, Y. Hu, W. Wang and D. Yu, RSC Adv., 2015, 5, 91932–91936 RSC
. - M. Sadeghi-Kiakhani, S. Safapour and F. Ghanbari-Adivi, Int. J. Biol. Macromol., 2019, 134, 1170–1178 CrossRef CAS PubMed
. - Y. Gao, X. Yu, A. P. Pierlot, R. J. Denning and R. Cranston, J. Mater. Sci., 2011, 46, 3020–3026 CrossRef CAS
. - M. Kaisersberger-Vincek, J. Štrancar and V. Kokol, Text. Res. J., 2017, 87, 1604–1619 CrossRef CAS
. - N. P. Brenwald and A. P. Fraise, J. Hosp. Infect., 2003, 55, 141–144 CrossRef CAS PubMed
. - R. Hirase, T. Shikata and M. Shirai, Synth. Met., 2004, 146, 73–77 CrossRef CAS
. - G. A. Planes, J. L. Rodriguez, M. C. Miras, G. Garcia, E. Pastor and C. A. Barbero, Phys. Chem. Chem. Phys., 2010, 12, 10584–10593 RSC
. - D. J. McCarthy, W. R. Waud, R. F. Struck and D. L. Hill, Cancer Res., 1985, 45, 174–180 CAS
. - A. K. Nanda and K. Kishore, Macromolecules, 2002, 35, 6505–6510 CrossRef CAS
. - N.-L. Shi, X.-M. Guo, H. Jing, J. Gong, C. Sun and K. Yang, J. Mater. Sci. Technol., 2006, 22, 289–290 CAS
. - D. Seshadri and N. Bhat, Indian J. Fibre Text. Res., 2005, 30, 204–206 CAS
. - M. M. Hassan and J. R. McLaughlin, ACS Appl. Mater. Interfaces, 2013, 5, 1548–1555 CrossRef CAS PubMed
. - X.-L. Wei, Y. Z. Wang, S. M. Long, C. Bobeczko and A. J. Epstein, J. Am. Chem. Soc., 1996, 118, 2545–2555 CrossRef CAS
. - I. Mav, M. Žigon and A. Šebenic, Synth. Met., 1999, 101, 717–718 CrossRef CAS
. - Y. Liao, V. Strong, W. Chian, X. Wang, X.-G. Li and R. B. Caner, Macromolecules, 2012, 45, 1570–1579 CrossRef CAS
. - S. Shimizu, T. Saitoh, M. Uzawa, M. Yuasa, K. Yano, T. Maruyama and K. Watanabe, Synth. Met., 1997, 85, 1337–1338 CrossRef CAS
. - I. Mav, M. Žigon, A. Šebenic and J. Vohlidal, J. Polym. Sci., Part A: Polym. Chem., 2000, 38, 3390–3398 CrossRef CAS
. - F. Masdarolomoor, P. C. Innis, S. Ashraf, R. B. Caner and G. G. Wallace, Macromol. Rapid Commun., 2006, 27, 1995–2000 CrossRef CAS
. - A. Murugesan, B. Meenarathi, S. Palanikumar, L. Kannammal and R. Anbarasan, Adv. Polym. Technol., 2016, 35, 21522–21531 CrossRef
. - E. I. Mostafa Moujahid, M. Dubois, J.-P. Besse and F. Leroux, Chem. Mater., 2005, 17, 373–382 CrossRef
. - F. Masdarolomoor, P. C. Innis, S. Ashraf, R. B. Caner and G. G. Wallace, Synth. Met., 2005, 153, 181–184 CrossRef CAS
. - D. Kim, J. Choi, J.-Y. Kim, Y.-K. Han and D. Sohn, Macromolecules, 2002, 35, 5314–5316 CrossRef CAS
. - N. Muthukumar and G. Thilagavathi, Indian J. Chem. Technol., 2012, 19, 434–441 CAS
. - M. M. Hassan and J. R. McLaughlin, New J. Chem., 2018, 42, 18919–18927 RSC
. - E. Manefee and L. Yee, Text. Res. J., 1965, 35, 801–812 CrossRef
. - E. Pakdel, W. A. Daoud and X. G. Wang, Appl. Surf. Sci., 2013, 275, 397–402 CrossRef CAS
. - M. M. Hassan and S. J. Leighs, Appl. Surf. Sci., 2017, 419, 348–356 CrossRef CAS
. - D.-H. Zhou, Y.-H. Li, J.-U. Wang, P. Xu and X. Han, Mater. Lett., 2011, 65, 3601–3604 CrossRef CAS
. - J. Fan, Y.-H. Guo, J. Wang and M.-H. Fan, J. Hazard. Mater., 2009, 166, 904–910 CrossRef CAS PubMed
. - C. Dhivya, S. S. A. Vandarkuzhali and N. Radha, Arabian J. Chem., 2019, 12, 3785–3798 CrossRef CAS
. - E. Hejchman, H. Kruszewska, D. Maciejewska, B. Sowirka-Taciak, M. Tomczyk, A. Sztokfisz-Ignasiak, J. Jankowski and I. Młynarczuk-Biały, Monatsh. Chem., 2019, 150, 255–266 CrossRef CAS
. - B. C. Herold, N. Bourne, D. Marcellino, R. Kirkpatrick, D. M. Strauss, L. J. Zaneveld, D. P. Waller, R. A. Anderson, C. J. Chany, B. J. Barham, L. R. Stanberry and M. D. Cooper, J. Infect. Dis., 2000, 181, 770–773 CrossRef CAS PubMed
. - S. Yadav, P. Kumar, E. De Clercq, J. Balzarini, J. Pannecouque, S. K. Dewan and B. Narasimhan, Eur. J. Med. Chem., 2010, 45, 5985–5997 CrossRef CAS PubMed
. - Y. Maehara and S. I. Miyoshi, Biocontrol Sci., 2017, 22, 229–232 CrossRef CAS PubMed
. - G.-H. Li, X. Wang, Y.-F. Xu, B.-G. Zhang and X.-D. Xia, Eur. Food Res. Technol., 2014, 238, 589–596 CrossRef CAS
. - M. M. Hassan, ACS Omega, 2018, 3, 17656–17667 CrossRef CAS PubMed
. - M. M. Hassan, Ind. Eng. Chem. Res., 2014, 53, 10954–10964 CrossRef CAS
. - J. M. Cardamone and W. C. Damert, Text. Res. J., 2006, 6, 78–85 CrossRef
.
Footnote |
† Electronic supplementary information (ESI) available. See DOI: 10.1039/d0ra02267e |
|
This journal is © The Royal Society of Chemistry 2020 |
Click here to see how this site uses Cookies. View our privacy policy here.