DOI:
10.1039/D0RA01892A
(Paper)
RSC Adv., 2020,
10, 26834-26842
A modified ‘skeleton/skin’ strategy for designing CoNiP nanosheets arrayed on graphene foam for on/off switching of NaBH4 hydrolysis†
Received
28th February 2020
, Accepted 16th May 2020
First published on 17th July 2020
Abstract
CoNiP nanosheet array catalysts were successfully prepared on three-dimensional (3D) graphene foam using hydrothermal synthesis. These catalysts were prepared using 3D Ni–graphene foam (Ni/GF), comprising nickel foam as the ‘skeleton’ and reduced graphene oxide as the ‘skin’. This unique continuous modified ‘skeleton/skin’ structure ensure that the catalysts had a large surface area, excellent conductivity, and sufficient surface functional groups, which promoted in situ CoNiP growth, while also optimizing the hydrolysis of sodium borohydride. The nanosheet arrays were fully characterized and showed excellent catalytic performance, as supported by density functional theory calculations. The hydrogen generation rate and activation energy are 6681.34 mL min−1 g−1 and 31.2 kJ mol−1, respectively, outperforming most reported cobalt-based catalysts and other precious metal catalysts. Furthermore, the stability of mockstrawberry-like CoNiP catalyst was investigated, with 74.9% of the initial hydrogen generation rate remaining after 15 cycles. The catalytic properties, durability, and stability of the catalyst were better than those of other catalysts reported previously.
1. Introduction
Hydrogen is a promising clean energy carrier and a promising future alternative to fossil fuels.1–6 However, the production of hydrogen, and its efficient and safe storage, remain serious challenges that hinder practical applications. Sodium borohydride (NaBH4) is a promising system address these issues,7–9 owing to its high hydrogen density (10.8 wt%), good storage stability, nontoxicity, and safe reaction conditions. Therefore, NaBH4 hydrolysis is considered as an attractive process for producing pure hydrogen at room temperature.10,11 However, the catalyst plays a vital role in practical applications, accelerating this hydrolysis reaction in a controlled manner. Among existing catalysts, noble metal catalysts, such as platinum and platinum-based alloys, exhibit the best catalytic activity.12–15 However, the high cost and scarcity of such catalysts has limited their widespread use. Therefore, the development of high-performance and low-cost alternative catalysts is a major unresolved challenge.
Transition metals have been reported as new low-cost earth-abundant catalysts that can be further enhanced by doping with P or B,16 with examples including Ni–P,17 Co–P,18 Fe–P,19 Co2P20 and Co–B.21 Furthermore, introducing graphene can effectively obtain a higher catalyst surface area. For example, Zhang et al.22 prepared a cobalt nanocomposite catalyst supported on graphene oxide (GO) that showed excellent catalytic properties for NaBH4 hydrolysis. However, π–π interactions and van der Waals forces caused the two-dimensional graphene plate layers to combine, thereby reducing the effective catalyst surface area.23–25 To solve this problem, research has focused on 3D graphene. To prepare 3D graphene, nickel foam has been widely used due to its unique structure and low production cost.16,26,27 Using nickel foam as a template solves the powder catalyst separation problem, and prevents easy combination and other shortcomings, while allowing convenient collection and recycling. Furthermore, the hydrogen production rate of NaBH4 hydrolysis can be controlled by changing the contact area.
Herein, we reported a modified ‘skeleton/skin’ strategy for designing CoNiP nanosheets arrayed on graphene foam for use as on/off switches and reusable catalysts and explored their practical applications as NaBH4 hydrolysis catalysts. Fig. 1 shows the preparation procedure of the hydrolysis catalyst based on Ni/GF-supported CoNiP. The whole three-dimensional structure was based on nickel foam, and the graphene foam was prepared using the solution casting method.27 The resulting Ni/GF material showed superior performance, good conductivity, a large surface area, and a surface with sufficient functional groups, which not only promoted in situ the growth of the CoNiP nanochip array on the Ni/GF bracket, but also helped to improve the hydrogen production rate and circulation stability of NaBH4 hydrolysis.
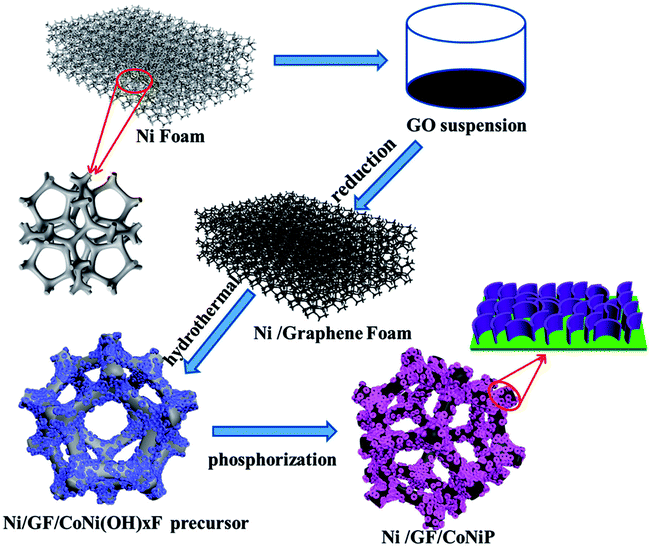 |
| Fig. 1 Schematic diagram of the preparation of Ni/GF/CoNiP nanosheets. | |
2. Materials and methods
2.1 Materials
All chemicals were of analytical grade and used without further purification. Sodium borohydride (NaBH4), cobalt nitrate hexahydrate (Co(NO3)2·6H2O), nickel nitrate hexahydrate (Ni(NO3)2·6H2O), ammonium fluoride (NH4F), urea (CO(NH2)2), and sodium hypophosphite (NaH2PO2) were obtained with a purity of 99% from Alfa Aesar Co., Ltd. (Tianjin, China). All experiments were performed using deionized water as solvent.
2.2 Synthesis of Ni/GF material
GO was prepared using a modified Hummers method.28 Ni foam was used as both the 3D skeleton template and reducing agent to prepare GF. Briefly, a piece of Ni foam (2 × 3 cm) was treated sequentially with acetone and 6 M HCl to remove the oxide layer, then washed with ethanol and deionized water. The Ni foam was then immersed in an aqueous GO suspension (2 mg mL−1) at 70 °C for 24 h.27,29 During this process, the Ni foam surface was completely covered with the GO solution, and GO was thermally reduced and deposited on the Ni foam to form Ni/GF. The as-obtained Ni/GF was collected and repeatedly rinsed with ethanol.
2.3 Synthesis of Ni/GF/CoNi(OH)xF
The precursor (Ni/GF/(CoNiOH)xF) was prepared using a hydrothermal method. Co(NO3)2·6H2O (1 mmol), Ni(NO3)2·6H2O (1 mmol), NH4F (8 mmol), and urea (10 mmol) were dissolved in deionized water (80 mL) and sonicated for 10 min. Ni/GF was then added to the above solution, which was then transferred into a 100 mL Teflon-lined stainless-steel autoclave, sealed, and heated at 100 °C for 8 h. After allowing to cool to room temperature, the Ni/GF/(CoNiOH)xF precursor was washed with deionized water and ethanol six times to remove unreacted substances and absorbed Co2+ and Ni2+ ions. Finally, the precursor was dried at 70 °C for 24 h in a vacuum drying furnace.
2.4 Synthesis of Ni/GF/CoNiP
The CoNi(OH)xF/NF precursor and NaH2PO2 (0.1 g) were placed in a closed porcelain crucible, with the two substances separated by a carbon cloth (NaH2PO2 under the cloth and CoNi(OH)xF/NF precursor above the cloth). The crucible was then heated to 300 °C for 2 h at a heating rate of 3 °C min−1 and then cooled to room temperature. The resulting Ni/GF/CoNiP was washed with deionized water and dried at 70 °C in a vacuum drying furnace. Then, the milled powder was taken out and kept in a glove box. For comparison, Co–P, Ni–P, and Co–Ni–P were prepared on blank NiF and Ni/GF using the same method described above. Fig. 1 shows a schematic diagram of the preparation of Ni/GF/CoNiP.
2.5 Characterization
The Ni/GF/CoNiP catalyst structures were analyzed by X-ray diffraction (XRD; 1820, Philips, Netherlands). The elemental valence states of the Ni/GF/CoNiP catalysts were determined by X-ray photoelectron spectroscopy (XPS; Thermo Electron ESCALAB 250). The morphologies of the Ni/GF/CoNiP catalysts were determined by scanning electron microscopy (SEM; JSM-6360LV, JEOL Ltd., Japan) and transmission electron microscopy (TEM; JEOL 2010, JEOL, Japan). The Ni/GF/CoNiP catalyst structures were also analyzed using high-angle annular dark-field scanning transmission electron microscopy (HAADF-STEM). The crystalline phase and growth direction of Ni/GF/CoNiP were determined using selected area electron diffraction (SAED). Finally, energy dispersive X-ray (EDX) mapping was used to further analyze the structural composition of the Ni/GF/CoNiP catalyst.
2.6 Hydrogen generation measurements
The catalytic activity of Ni/GF/CoNiP in NaBH4 hydrolysis was analyzed by testing the hydrogen generation rate. The volume of hydrogen produced was determined from the equivalent displacement of water. The weight of displaced water was recorded with a balance and used to determine the volumetric measurement at constant time intervals. Typically, the Ni/GF/CoNiP catalyst was placed at the bottom of a volumetric flask. At a certain temperature, a solution (10 mL) containing 1.0 wt% NaOH and 1.5 wt% NaBH4 was injected into the flask. A water bath was used to keep the system under isothermal conditions. The weight of the CoNiP catalyst was determined according to the following equation:
mCoNiP catalyst = mNi/GF/CoNiP − mNi/GF |
where mCoNiP catalyst, mNi/GF/CoNiP and mNi/GF represent the weight of CoNiP catalyst, Ni/GF/CoNiP sample and Ni/GF before hydrothermal treatment, respectively.
2.7 DFT calculations
First-principles computations on the basis of DFT were performed using the Vienna Ab Initio Simulation Package (VASP).30 We use the generalized gradient approximation (GGA)31 of Perdew–Burke–Ernzerhof (PBE) to describe the exchange–correlation density. The core–valence interaction was described by the frozen-core projector augmented wave (PAW) method, and the truncation energy for the plane wave expansion wave function was 400 eV. The semicore p states remained fixed for the cobalt pseudopotentials. For the CoNiP@GO structure, we used simplified model calculations, and the unit cell was used to build the metal surface with one layer of graphene for the hydrogen adsorption study. The Brillouin zone was sampled using a 4 × 4 × 1 Monkhorst–Pack mesh. The geometry optimizations were performed by using the conjugated gradient method with the convergence value set at an energy of 10−4 eV and 0.05 eV Å−1 in force. The vacuum separation was set to more than 20 Å to avoid interactions and periodic images. The effects of van der Waals (vdW)32 interactions were considered in the calculations discussed below.
3. Results and discussion
3.1 Synthesis and characterization
Ni/GF was synthesized by solution casting using the Ni foam scaffold as the template,27 which provided a large specific surface area for a high active material loading.33 The morphologies of NiF and Ni/GF were analyzed by SEM, as shown in Fig. S1a and b.† Fig. S1a† shows a smooth NiF surface, while Fig. S1b† shows a 3D porous structure and rough surface, with a characteristic wrinkle morphology originating from graphene oxide. The reduced graphene oxide nanosheets were assembled on the Ni foam template, forming a ‘skeleton/skin’ structure analogous to that found in the human body, with NiF as the skeleton, and the reduce grapheme oxide coating as the skin.27 The structure of Ni/GF was characterized by Raman spectroscopy. As shown in Fig. S2,† the ID/IG values for GO and Ni/GF were 0.97 and 1.23, respectively, which were attributed to the increased sp2 domains in the Ni/GF sample, confirming the formation of rGO on NiF. As shown in Fig. S3,† compared with the Ni/GF sample, the Ni/GF/CoNiP nanosheet still retained the unique ‘skeleton/skin’ structure. As shown in Fig. 2a, after hydrothermal treatment, the CoNi(OH)xF nanosheets uniformly covered the Ni/GF surface. After phosphidation, the as-obtained CoNiP maintained the characteristics of the nanoarray, as shown in Fig. 2b. However, the surface of the phosphidated CoNiP nanosheet was rougher than that of the precursor, and the porous structure was clearly visible. Interestingly, the CoNiP material showed a nanosheet morphology with vertically growth on the Ni/GF. Multiple nanosheets formed a hydrangea-like shape. As shown in Fig. 2c–g, EDX analysis of CoNiP further confirmed the presence of Co, Ni, and P elements in the Ni/GF/CoNiP nanosheet, which was consistent with XPS analysis. TEM imaging shows that CoNi(OH)xF was deposited on Ni/GF as an ultrathin nanoplate, as shown in Fig. 2h and i. The HRTEM image shown in Fig. 2i contains lattice fringes of 0.291 nm, corresponding to the (110) planes of CoNiP.29,34 The SAED pattern (Fig. 2i, inset) corresponds to the (110), (111), (210), and (300) planes.26,35 These results confirm the successful preparation of a CoNiP nanoarray on Ni/GF with a modified ‘skeleton/skin’ structure.
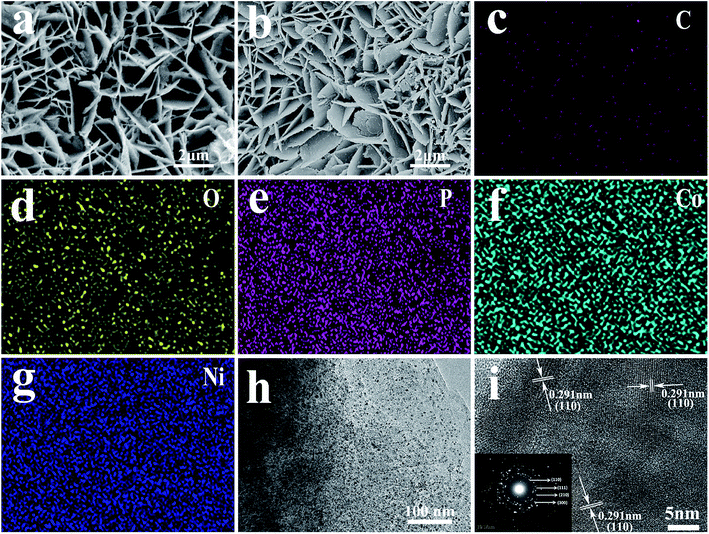 |
| Fig. 2 SEM images of (a) CoNi(OH)xF, (b) Ni/GF/CoNiP nanocomposite; EDX mapping images of (c) C, (d) O, (e) P, (f) Co and (g) Ni. (h) TEM images of the Ni/GF/CoNiP nanocomposite; (i) SAED image of Ni/GF/CoNiP. | |
As-synthesized Ni/GF/CoNiP was characterized by powder X-ray diffraction. As shown in Fig. 3a, diffraction peaks at 2θ = 44.6°, 52.5°, and 76.4° were assigned to NiF. Furthermore, the phosphidated sample showed peaks at 2θ = 41.0°, 47.7°, and 54.4°, which were indexed to the (111), (210), and (300) planes of the CoNiP phase (JCPDS no. 71-2336), respectively.16,26,35–37 The XRD results are consistent with HRTEM. As shown in Fig. 3b, no obvious Co–P peaks were found, which might be due to the low loading, good dispersion, and quantum size of Co–P.37 Next, the Ni/GF/CoNiP composition was further characterized by XPS.
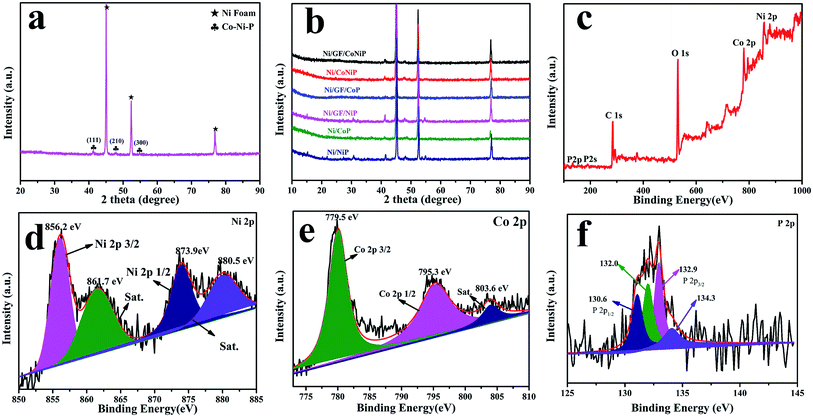 |
| Fig. 3 XRD patterns of (a) as-prepared Ni/GF/CoNiP and (b) as-prepared catalysts. (c) Full XPS spectrum of Ni/GF/CoNiP; (d–f) XPS spectra of (d) Ni 2p, (e) Co 2p, and (f) P 2p. | |
XPS analysis was used to study the elemental composition and valence states of Ni/GF/CoNiP. The XPS survey spectrum showed the presence of Ni, Co, P, and O elements (Fig. 3c). The presence of oxygen might be due to surface oxidation of CoNiP.26,38 High-resolution XPS spectra of Co 2p, Ni 2p, and P 2p are shown in Fig. 3d–f. The binding energy (BE) for Co (779.5 eV) was assigned to Co2+ species.34,39 The Co 2p XPS spectrum showed two main peaks for Co 2p3/2 and Co 2p1/2 at 779.5 and 795.3 eV, respectively.40,41 The BE for oxidized Ni (856.2 eV) was assigned to Ni2+ species. The Ni 2p XPS spectrum showed a doublet for Ni 2p3/2 at 856.2 eV and Ni 2p1/2 at 873.9 eV.40 Furthermore, the Co 2p peak at 803.6 eV and Ni 2p peaks at 861.7 and 880.5 eV were well fitted with three shake-up satellites.42 As observed from the P 2p spectrum, two peaks at 130.6 and 132.9 eV are observed, corresponding to P 2p1/2 and P 2p3/2, respectively, which can be attributed to P bonded to Co and Ni (metal phosphides).43 Other peaks located at 132.0 and 134.3 eV can be assigned to oxidized P species,44,45 which might be attributed to exposure to air or partial phosphidation of the precursor.40
3.2 Effect of different types of catalyst on hydrogen generation rate and kinetics of hydrolysis using Ni/GF/CoNiP
The catalytic activity of different samples for NaBH4 hydrolysis in alkali solution was evaluated. The catalysts were used to hydrolyze a solution (10 mL) containing 1.0 wt% NaOH and 1.5 wt% NaBH4 solution. When using only nickel foam used as skeleton structure, the relationship between hydrogen volume produced by NaBH4 hydrolysis and reaction time when catalyzed by NiF/CoNiP, NiF/CoP, NiF/NiP, and NiF yields the curves shown in Fig. 4a. NiF/CoNiP had the best catalytic activity. Next, the graphene was poured onto the nickel foam to form the unique modified ‘skeleton/skin’ structure. As shown in Fig. 4b, when NaBH4 came into contact with the catalyst, Ni/GF did not release any hydrogen, indicating that it had no catalytic effect. All other catalysts except Ni/GF/NiP afforded 100% of the theoretical hydrogen yield. The loading of Ni/GF/CoNiP, Ni/GF/CoP, Ni/GF/NiP, NiF/CoNiP, NiF/CoP, NiF/NiP were 0.023 g, 0.033 g, 0.061 g, 0.081 g, 0.079 g, 0.071 g, respectively. The HG rates clearly decreased in following order: Ni/GF/CoNiP > Ni/GF/CoP > Ni/GF/NiP > NiF/CoNiP > NiF/CoP > NiF/NiP. The Ni/GF/CoNiP catalyst showed the highest hydrogen generation rate (HGR) of 2289.83 mL min−1 g−1 at 303 K, which was about twice that obtained using NiF/CoNiP (1620.57 mL min−1 g−1) and much higher than those obtained using NiF/CoP (683.72 mL min−1 g−1), NiF/NiP (10.35 mL min−1 g−1), Ni/GF/NiP (47.28 mL min−1 g−1), and Ni/GF/CoP (1294.65 mL min−1 g−1) as catalysts. These results showed that the synergistic interaction among Co, Ni, and P might play an important role in the hydrolysis of NaBH4. Furthermore, nickel foam as a skeleton and graphene as a skin provided a high number of active sites for Co–Ni–P catalysts. These active sites might also play a significant role in the enhanced catalytic activity of the Ni/GF/CoNiP catalyst in NaBH4 hydrolysis.
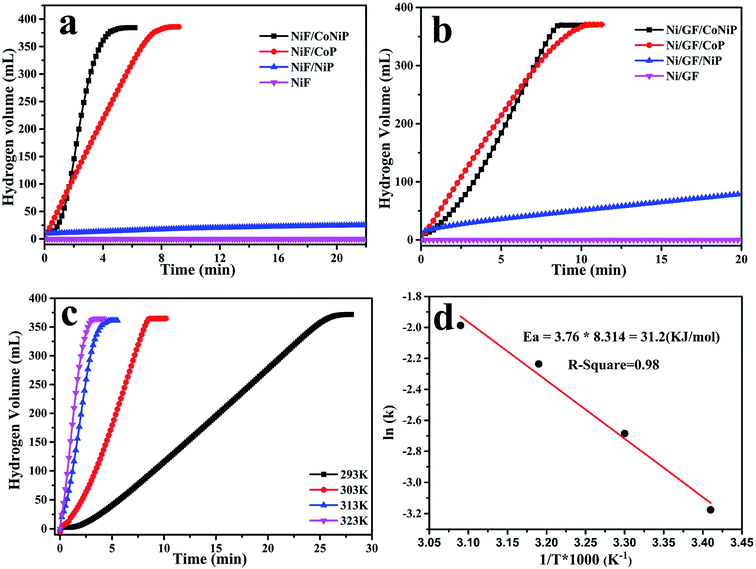 |
| Fig. 4 Effect of (a and b) different samples and (c) hydrolysis temperatures on the hydrogen generation rate from NaBH4 solution catalyzed by the mockstrawberry-like Ni/GF/CoNiP catalyst using 1.5 wt% NaBH4 and 1.0 wt% NaOH solution; (d) the corresponding Arrhenius plot of ln k versus 1/T. | |
To determine the activation energy (Ea) of NaBH4 hydrolysis catalyzed by Ni/GF/CoNiP, we performed hydrolysis tests at temperatures ranging from 298 K to 323 K, with all other parameters remaining unchanged. The hydrogen generation yield versus reaction time for the hydrolysis of NaBH4 in alkaline solution catalyzed by Ni/GF/CoNiP at different temperatures is shown in Fig. 4c. As expected, higher reaction temperatures resulted in an increased HGR. The Ea can be estimated using the Arrhenius equation:
where
k is the rate constant at various temperatures,
k0 is the pre-exponential factor,
R is the gas constant, and
T is the absolute temperature of the hydrolytic reaction. An Arrhenius plot is shown in
Fig. 4d. Based on the Arrhenius slope, the
Ea for the hydrolysis of NaBH
4 catalyzed by Ni/GF/CoNiP was determined to be approximately 33.5 kJ mol
−1, which was low compared with those of most previously reported catalysts (
Table 1). This low
Ea might be due to the synergy among Co, Ni, and P. The CoNiP nanoarray was small and could be evenly fixed to the Ni/GF carrier, which prevented it from accumulating during hydrolysis. Meanwhile, the high-ratio surface area and highly hydrophilic rGO provided a good platform and more active sites for the CoNiP nanoarray. These results indicated that Ni/GF/CoNiP showed excellent catalytic performance for hydrogen generation from NaBH
4.
Table 1 Catalyst systems, synthetic method, HGR, and Ea values for NaBH4 hydrolysis catalyzed by catalysts previously reported in the literature
Catalyst |
Synthetic method |
Ea (kJ mol−1) |
Ref. |
CoP/Cu foam |
Electroless plating |
46.8 |
46 |
CoNiMoP/Al2O3 |
Electroless deposition |
52.4 |
47 |
CoNiP/Pd–TiO2 |
Electroless deposition |
57.0 |
48 |
NiCoP NA/Ti |
Electroless deposition |
52.68 |
49 |
NiCoB |
Chemical reduction |
62 |
50 |
CoNiP/Cu sheet |
Electroless plating |
53.5 |
51 |
CoP/Cu sheet |
Electroless plating |
60.2 |
52 |
CoNiPB |
Chemical reduction |
29 |
53 |
Ni/GF/CoNiP |
Hydrothermal |
31.2 |
This work |
3.3 Stability of Ni/GF/CoNiP
Catalyst durability and recyclability are important factors that determine their potential practical applications. Therefore, hydrolysis experiments were performed to recycle the catalyst 15 times at 323 K. As shown in Fig. 5a, Ni/GF/CoNiP had decreased activity in the fourth cycle, but a fairly uniform initial rate increase in each cycle with reasonable catalytic effects. This reduced performance may be caused by the slight loss of catalyst material with each recycling application and a decrease in active sites54 However, Ni/GF/CoNiP still retained 74.8% of its initial catalytic activity for NaBH4 hydrolysis after 15 recover/reuse cycles. This excellent cycle performance might result from the catalyst having a ‘skeleton/skin’ structure, even though the lamellar structure collapses after 15 cycles, since the nanosheet structure is retained. This phenomenon may decrease the catalyst surface area or number of active sites, resulting in a reduced HGR from NaBH4. Fig. 5c shows SEM images of the Ni/GF/CoNiP catalyst after 15 cycles. However, the XRD patterns before and after catalyst cycling were almost identical, as shown in Fig. 5d, and the hydrogen conversion rate was 100%, demonstrating a higher stability and recyclability performance compared with other catalysts reported in the literature (see Table S1†).
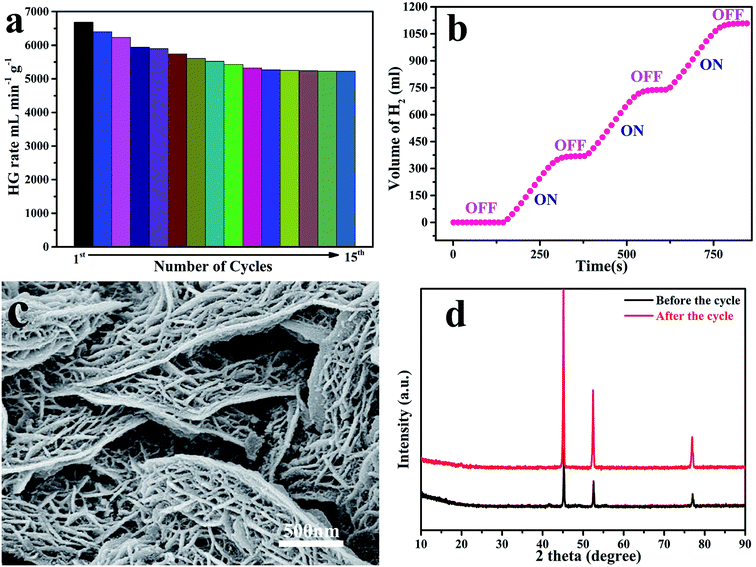 |
| Fig. 5 (a) Histogram of hydrogen generation rate versus number of cycles for Ni/GF/CoNiP catalyst after 15 cycle tests using 1.5 wt% NaBH4 and 1.0 wt% NaOH solution; (b) ‘on–off’ control of H2 production. (c) SEM images of the Ni/GF/CoNiP catalyst after 15 cycles; (d) XRD patterns of the Ni/GF/CoNiP catalyst before cycling and after 15 cycles. | |
The recovery process of our bulk catalysts was much simpler than that of powdered catalysts. As Ni/GF/Co–Ni–P is easily separated from the NaBH4 solution, it can be used as an ‘on/off’ switch for on-demand hydrogen production. Fig. 5b shows time control of hydrogen generation with repeated reactivation of the system without compromising catalytic activity. Hydrogen generation on demand can be easily achieved by immersing Ni/GF/CoNiP in solution or removing it from the same solution.55,56 The removal of Ni/GF/CoNiP terminates the hydrolysis reaction without releasing hydrogen (‘off’), but hydrogen evolution occurs again after reimmersing Ni/GF/CoNiP in the fuel solution (‘on’).
3.4 DFT calculations
DFT calculations were conducted to provide further insight into the promoting effects of the CoNiP@graphene interface on NaBH4 hydrolysis. The surface of graphene oxide is complicated. Our calculations implify the model and retain the main feature of the experimental situation. It is comparable between CoP, NIP, CoNiP, CoNiP@graphene. The theoretical hydrogen amount released by NaBH4 hydrolysis was 10.8 wt%, with half of the hydrogen atoms provided by H2O. The HGR was proportional to the pH value of the BH4− solution. NaBH4 in aqueous alkaline solution produces hydrogen gas by contact with selected catalyst CoNiP@graphene. The total reaction can be described as follows:57
Kaufman and Sen reported that dissociative adsorption of BH4− ion would occur on catalyst M (M = Co, Ni).52 The NaBH4 dehydrogenation process contains four key steps, as follows:
|
2M + BH4− ⇔ MBH3− + M–H*
| (1) |
|
MBH3− ⇔ BH3 + M + eM−
| (2) |
|
M + eM− + H′2O → M–H′* + OH′−
| (3) |
|
M–H* + M–H′* → 2M + HH′
| (4) |
where M–H* represents an intermediate in which a hydrogen atom is adsorbed on an active site on the catalyst surface. In order to distinguish hydrogen atoms from different pathways, we use the H′ symbol to indicate hydrogen atoms from water.
Eqn (1) shows that protons from BH
4− combine with electrons to form adsorbed H atoms.
Eqn (3) shows that the active site on the catalyst combines with H in water to form an adsorbed hydrogen atom. As shown in
Fig. 6a, the differential charge map clearly indicates the transfer of charge. An analysis of the electronic potential showed that electron transfer occurred from BH
4− to the CoNiP@graphene surface according to charge accumulation (yellow) and depletion regions (blue). The metallic catalyst would then transfer electrons (e
M−) to molecular H
2O to generate hydrogen with another active site.
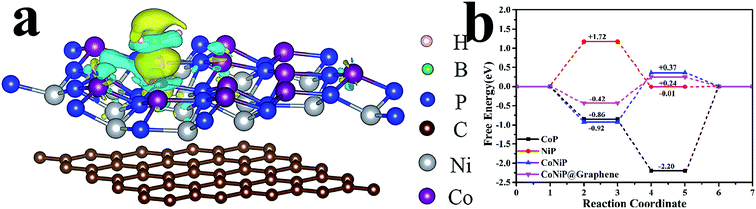 |
| Fig. 6 (a) Differential charge map and (b) Gibbs free energy of CoNiP@graphene. | |
The Gibbs free energy of hydrogen adsorption (ΔGH) on the active sites can be used as an indicator of hydrogen production activity. The free energy for hydrogen adsorption (ΔGH) was calculated using the equation ΔGH = ΔEH + ΔEZPE − TΔSH, where ΔEH is the hydrogen chemisorption energy, and ΔSH and ΔEZPE are the differences in entropy and zero-point energy between the adsorbed H and gas phase H2. The optimal activity should be obtained at ΔGH* ≈ 0.53 Excessively high and low ΔGH values lead to a decrease in hydrogen production reactivity. As shown in Fig. 6b, the Gibbs free energy of CoNiP@ graphene was closer to 0 than those of CoP, NiP, and CoNiP catalysts. Higher ΔGH values suggest weak bonds between the protons and active sites, while lower ΔGH values indicate a large surface adsorption energy for hydrogen atoms, both of which hinder the reaction. Compared with CoNiP, the free energy of CoNiP@graphene after graphene adsorption was greatly reduced, owing to the increase in electron density on the metal catalysts near the graphene substrate. Our DFT calculations found that graphene loaded on the CoNiP catalyst showed enhanced hydrolysis activity, which was consistent with the experimental results.
4. Conclusions
In summary, NiCoP nanosheet arrays supported on 3D graphene foam with a unique continuous modified ‘skeleton/skin’ structure by hydrothermal method and successfully used as efficient catalyst for the hydrolysis of alkaline NaBH4 solution. The resulting Ni/GF/CoNiP catalyst exhibited excellent performance, providing a maximum HGR of 6681.34 mL min−1 g−1 at 323 K and a low activation energy of 31.2 kJ mol−1, along with controllability and durability. Furthermore, thanks to their unique continuous modified ‘skeleton/skin’ reticulate architecture, about 74.9% of the initial hydrogen generation rate was retained after 15 cycles, suggesting excellent cycling stability. As expected, this catalyst was superior to previously reported CoNiP, CoxP, and NiP catalysts. As the Ni/GF/CoNiP catalyst for activating and accelerating the hydrolysis of alkaline NaBH4 was prepared in a simple, cost-effective, and efficient manner, this material has great potential for meeting future demands of hydrogen for fuel-cell-powered vehicles.
Conflicts of interest
There are no conflicts of interest to declare.
Acknowledgements
The authors gratefully acknowledge support from the National Natural Science Foundation of China (51971068, 551671062, 5187011196 and U1501242), National Key Research and Development Program of China (2018YFB1502103, 2018YFB1502105), Chinesisch-Deutsche Kooperationsgruppe: Integrated Computational Materials Engineering of Electrochemical Storage Systems (GZ1528), Guangxi Bagui Scholar Foundation, Guangxi Collaborative Innovation Centre of Structure and Property for New Energy and Materials (2012GXNSFGA06002), Guangxi Science and Technology Project (AA19182014, AD17195073, 2017AD23029), and Guangxi Major Science and Technology Special Project (AA17202030-1). We also thank the Guangxi Advanced Functional Materials Foundation and Application Talents Small Highlands, and the Innovation Project of Guangxi Graduate Education (2019YCXS112), jointly sponsor by Guangxi Key Laboratory of Information Materials (Guilin University of Electronic Technology), P. R. China (Project No. 191010-K). F. R. is grateful to the Canada Research Chairs program for partial salary support.
References
- Y. Zou, Y. Yin, Y. Gao, C. Xiang, H. Chu, S. Qiu, E. Yan, F. Xu and L. Sun, Int. J. Hydrogen Energy, 2018, 43, 4912–4921 CrossRef CAS.
- H. Shu, L. Lu, S. Zhu, M. Liu, Y. Zhu, J. Ni, Z. Ruan and Y. Liu, Catal. Commun., 2019, 118, 30–34 CrossRef CAS.
- T. Bao, L. Song and S. Zhang, Chem. Eng. J., 2018, 351, 189–194 CrossRef CAS.
- Y. Yu, T. He, A. Wu, Q. Pei, A. Karkamkar, T. Autrey and P. Chen, Angew. Chem., 2019, 131, 3134–3139 CrossRef.
- M. Liu, X. Xiao, S. Zhao, S. Saremi-Yarahmadi, M. Chen, J. Zheng, S. Li and L. Chen, Int. J. Hydrogen Energy, 2019, 44, 1059–1069 CrossRef CAS.
- S. Deng, Y. Zhong, Y. Zeng, Y. Wang, X. Wang, X. Lu, X. Xia and J. Tu, Adv. Sci., 2018, 5, 1700772 CrossRef PubMed.
- J. Guo, Y. Hou, B. Li and Y. Liu, Int. J. Hydrogen Energy, 2018, 43, 15245–15254 CrossRef CAS.
- O. V. Netskina, D. I. Kochubey, I. P. Prosvirin, S. E. Malykhin, O. V. Komova, V. V. Kanazhevskiy, Y. G. Chukalkin, V. I. Bobrovskii, D. G. Kellerman, A. V. Ishchenko and V. I. Simagina, Mol. Catal., 2017, 441, 100–108 CrossRef CAS.
- D. Kılınç, Ö. Şah
n and C. Saka, Int. J. Hydrogen Energy, 2018, 43, 251–261 CrossRef. - L. Z. Ouyang, H. Zhong, Z. M. Li, Z. J. Cao, H. Wang, J. W. Liu, X. K. Zhu and M. Zhu, J. Power Sources, 2014, 269, 768–772 CrossRef CAS.
- J. Cheng, C. Xiang, Y. Zou, H. Chu, S. Qiu, H. Zhang, L. Sun and F. Xu, Ceram. Int., 2015, 41, 899–905 CrossRef CAS.
- Y. V. Larichev, O. V. Netskina, O. V. Komova and V. I. Simagina, Int. J. Hydrogen Energy, 2010, 35, 6501–6507 CrossRef CAS.
- D. Xu, H. Zhang and W. Ye, Catal. Commun., 2007, 8, 1767–1771 CrossRef CAS.
- P. Krishnan, T.-H. Yang, W.-Y. Lee and C.-S. Kim, J. Power Sources, 2005, 143, 17–23 CrossRef CAS.
- K. Biswas, S. Chattopadhyay, Y. Jing, R. Che, G. De, B. Basu and D. Zhao, Ind. Eng. Chem. Res., 2019, 58, 2159–2169 CrossRef CAS.
- M. Lu, L. Wang, B. Jiang and J. Zheng, J. Electrochem. Soc., 2019, 166, D69–D76 CrossRef CAS.
- M. Ledendecker, S. Krick Calderon, C. Papp, H. P. Steinruck, M. Antonietti and M. Shalom, Angew. Chem., 2015, 54, 12361–12365 CrossRef CAS PubMed.
- K. W. Cho and H. S. Kwon, Catal. Today, 2007, 120, 298–304 CrossRef CAS.
- H. Jiang, B. Chen, J. Pan, C. Li, C. Liu, L. Liu, T. Yang, W. Li, H. Li, Y. Wang, L. Chen and M. Chen, J. Alloys Compd., 2017, 728, 328–336 CrossRef CAS.
- X. Wang, C. Liu, C. Wu, X. Tian, K. Wang, W. Pei and Q. Wang, Electrochim. Acta, 2020, 330, 135191 CrossRef CAS.
- O. Kaan Ozdemir, A. Hasimoglu and A. Sems Ahsen, J. Renewable Sustainable Energy, 2013, 5, 063135 CrossRef.
- F. Zhang, C. Hou, Q. Zhang, H. Wang and Y. Li, Mater. Chem. Phys., 2012, 135, 826–831 CrossRef CAS.
- S. Yin, Z. Niu and X. Chen, Small, 2012, 8, 2458–2463 CrossRef CAS PubMed.
- C. Li and G. Shi, Nanoscale, 2012, 4, 5549–5563 RSC.
- G. Xia, Y. Tan, F. Wu, F. Fang, D. Sun, Z. Guo, Z. Huang and X. Yu, Nano Energy, 2016, 26, 488–495 CrossRef CAS.
- M. Kong, Z. Wang, W. Wang, M. Ma, D. Liu, S. Hao, R. Kong, G. Du, A. M. Asiri, Y. Yao and X. Sun, Chemistry, 2017, 23, 4435–4441 CrossRef CAS PubMed.
- K. Chi, Z. Zhang, Q. Lv, C. Xie, J. Xiao, F. Xiao and S. Wang, ACS Appl. Mater. Interfaces, 2017, 9, 6044–6053 CrossRef CAS PubMed.
- W. S. Hummers and R. E. Offeman, J. Am. Chem. Soc., 1957, 80, 1339 CrossRef.
- Z. Zhang, K. Chi, F. Xiao and S. Wang, ACS Appl. Mater. Interfaces, 2015, 3, 12828–12835 CAS.
- G. Kresse and J. Furthmüller, Phys. Rev. B: Condens. Matter Mater. Phys., 1996, 54, 11169–11186 CrossRef CAS PubMed.
- J. P. Perdew, K. Burke and M. Ernzerhof, Phys. Rev. Lett., 1996, 77, 3865–3868 CrossRef CAS PubMed.
- R. F. W. Bader, I. Keaveny and P. E. Cade, J. Chem. Phys., 1967, 47, 3381–3402 CrossRef CAS.
- F. Yang, B. Cao, Y. Tao, M. Hu, C. Feng, L. Wang, Z. Jiang, D. Cao and Y. Zhang, J. Power Sources, 2015, 298, 38–45 CrossRef CAS.
- Y. Li, H. Zhang, M. Jiang, Y. Kuang, X. Sun and X. Duan, Nano Res., 2016, 9, 2251–2259 CrossRef CAS.
- A. Han, H. Chen, H. Zhang, Z. Sun and P. Du, ACS Appl. Mater. Interfaces, 2016, 4, 10195–10202 CAS.
- C. Wang, J. Jiang, T. Ding, G. Chen, W. Xu and Q. Yang, Adv. Mater. Interfaces, 2016, 3, 1500454 CrossRef.
- J. Huang, Y. Li, Y. Xia, J. Zhu, Q. Yi, H. Wang, J. Xiong, Y. Sun and G. Zou, Nano Res., 2017, 10, 1010–1020 CrossRef CAS.
- Q. Liu, J. Tian, W. Cui, P. Jiang, N. Cheng, A. M. Asiri and X. Sun, Angew. Chem., Int. Ed., 2014, 53, 6710–6714 CrossRef CAS PubMed.
- L. Song, S. Zhang and Q. Wei, Powder Technol., 2011, 212, 367–371 CrossRef CAS.
- Y. Pan, Y. Liu and C. Liu, J. Power Sources, 2015, 285, 169–177 CrossRef CAS.
- Y. Bai, H. Zhang, L. Liu, H. Xu and Y. Wang, Chemistry, 2016, 22, 1021–1029 CrossRef CAS PubMed.
- M. Yan, Y. Yao, J. Wen, L. Long, M. Kong, G. Zhang, X. Liao, G. Yin and Z. Huang, ACS Appl. Mater. Interfaces, 2016, 8, 24525–24535 CrossRef CAS PubMed.
- G. Li, X. Zhang, H. Zhang, C. Liao and G. Jiang, Appl. Catal., B, 2019, 249, 147–154 CrossRef CAS.
- Y. Bai, H. Zhang, Y. Feng, L. Fang and Y. Wang, ACS Appl. Mater. Interfaces, 2016, 4, 9072–9079 CAS.
- J. Auvergniot, A. Cassel, D. Foix, V. Viallet, V. Seznec and R. Dedryvère, Solid State Ionics, 2017, 300, 78–85 CrossRef CAS.
- T. H. Oh and S. Kwon, Int. J. Hydrogen Energy, 2012, 37, 15925–15937 CrossRef CAS.
- L. Wang, Z. Li, P. Zhang, G. Wang and G. Xie, Int. J. Hydrogen Energy, 2016, 41, 1468–1476 CrossRef CAS.
- M. Rakap, E. E. Kalu and S. Özkar, J. Alloys Compd., 2011, 509, 7016–7021 CrossRef CAS.
- K. Li, M. Ma, L. Xie, Y. Yao, R. Kong, G. Du, A. M. Asiri and X. Sun, Int. J. Hydrogen Energy, 2017, 42, 19028–19034 CrossRef CAS.
- J. C. Ingersoll, N. Mani, J. C. Thenmozhiyal and A. Muthaiah, J. Power Sources, 2007, 173, 450–457 CrossRef CAS.
- Y. Wang, G. Li, S. Wu, Y. Wei, W. Meng, Y. Xie, Y. Cui, X. Lian, Y. Chen and X. Zhang, Int. J. Hydrogen Energy, 2017, 42, 16529–16537 CrossRef CAS.
- C. M. Kaufman and B. Sen, J. Chem. Soc., Dalton Trans., 1985, 2, 307–313 RSC.
- R. Fernandes, N. Patel and A. Miotello, Int. J. Hydrogen Energy, 2009, 34, 2893–2900 CrossRef CAS.
- A. M. Pornea, M. W. Abebe and H. Kim, Chem. Phys., 2019, 516, 152–159 CrossRef CAS.
- T. R. Cook, D. K. Dogutan, S. Y. Reece, Y. Surendranath, T. S. Teets and D. G. Nocera, Chem. Rev., 2010, 110, 6474–6502 CrossRef CAS PubMed.
- F. Erogbogbo, T. Lin, P. M. Tucciarone, K. M. LaJoie, L. Lai, G. D. Patki, P. N. Prasad and M. T. Swihart, Nano Lett., 2013, 13, 451–456 CrossRef CAS PubMed.
- Y. Zhou, C. Fang, Y. Fang, F. Zhu, H. Liu and H. Ge, Int. J. Hydrogen Energy, 2016, 41, 22668–22676 CrossRef CAS.
Footnote |
† Electronic supplementary information (ESI) available. See DOI: 10.1039/d0ra01892a |
|
This journal is © The Royal Society of Chemistry 2020 |
Click here to see how this site uses Cookies. View our privacy policy here.