DOI:
10.1039/D0RA01588A
(Paper)
RSC Adv., 2020,
10, 11982-11989
Assembly of graphene oxide on cotton fiber through dyeing and their properties
Received
19th February 2020
, Accepted 17th March 2020
First published on 24th March 2020
Abstract
Materials with electrical conductivity are preferred for electronics, medical, space and other applications. Flexible, stretchable and washable conductive fabrics have been preferred over metallic materials. However, the currently available conductive fabrics are mainly made using a dip-drying process which makes it difficult to obtain a regular assembly structure of graphene sheets on the fibers. In this research, we report the development of conductive cotton fabrics through simple dyeing, graphene oxide (GO) with two distinct sizes was used to dye the fabrics which were later reduced using hydrazine hydrate. The regularity of graphene sheets on the surface of the cotton fiber can be improved by level assembly, it is beneficial to the conductive stability of the later drawing, bending and friction process. The results show that, the fabrics coated with graphene had excellent fastness to washing, friction and bending. After 20 washings and exposure to 2000 rubbing and 1000 bending cycles, the fabrics had excellent conductivity retention of 86%, 55% and 99%, respectively. In addition, the introduction of graphene causes the dyed fabric to have good infrared absorption and excellent UV resistance. Using cotton fabrics and GO to impart conductivity and UV resistance would be an affordable, sustainable and novel approach to develop functionalized materials for various applications.
1. Introduction
Functionalized materials, particularly those made from natural polymers, provide a unique opportunity to develop devices, sensors and other aids for various applications. Among the various functionalizations, making polymers conductive is desired for biosensors, actuators, rechargeable batteries, separator films etc.1 Similarly, functionalization has also been done to improve anti-flammable, antibacterial and pH and temperature responsive materials.2 A recent trend has been to develop functionalized fabrics for energy storage, health care and protective applications.3,4 Various forms of materials including fibers, particles, nanowires and fabrics have been developed. Fabrics offer higher flexibility both in terms of design and applications and hence are widely functionalized for specific uses. In addition to fabrics, fibers have also been developed using conductive polymers such as polyaniline and polypyrrole.5
Cotton is the most commonly available and used natural cellulose fiber. Fabrics have been made from cotton since time immemorial not only for clothing but also as bandages, gauze and for wide variety of applications. Cotton fabrics are not only inexpensive, biodegradable and available in different shapes, sizes and configurations, they are also easily modifiable and are hydrophilic. Many attempts have been made to functionalize cotton fabrics to meet specific needs. Treating cotton fabrics with silver nanowires provided considerable resistance against Gram positive and Gram negative bacterial and also able to efficiently block UV rays with a UV protection factor of 113 and increase hydrophobicity of the fabrics up to a contact angle of 156°.6 ZnO nanoparticles were dyed onto cotton fabrics (up to 10% on weight of the fabrics) resulting in excellent UV resistance up to 20 cycles after washing.7 Thermal and flame resistant properties of cotton fabrics were substantially improved after functionalizing with a novel nitrogen containing carboxyl functionalized organophosphorous.8
Graphene based materials, particularly graphene oxide has been extensively used to modify polymers including fabrics. Synthetic graphene oxide was deposited (up to 19.5%) onto silk fabrics by dry coating and reducing using L-ascorbic acid solution. Modified silk fabrics had improved fire resistance, smoke suppression and sheet resistance. The GO modified silk fabrics were assembled into a sensitive and flexible sensor for incorporating into a wearable device.9 GO was dyed onto acrylic yarns and immobilized and later converted into graphene by treating with sodium hydrosulfite solution. The modified fibers had electrical resistivity ranging from 102 to 1010 Ω cm−1.10 Thermally reduced graphene oxide nanosheets were coated onto flexible carbon fabric for developing supercapacitors. The GO containing carbon acted as excellent supercapacitors with capacitance values as high as 70 F g−1 at 5 mV s−1.11
Studies have reported the use of graphene and graphene oxide to modify the functions and stability of cotton fabrics as well. For instance, flexible conductive cotton fabrics were developed by depositing graphene oxide dispersion and later reducing the GO by hot pressing at 180 °C for 60 minutes. Modified fabrics had good performance even after 400 cycles with electrical resistance varying from −3500 kΩ to −10 kΩ.12 Instead of GO, graphene nanoribbons were wet coated onto cotton fabrics with uniform distribution and good interaction. In addition to increase in strength and modulus by 59 and 61%, respectively, the fabrics were also conductive and suitable for fabricating smart textiles.13 Using three different approaches (direct adsorption, radiation induced crosslinking and chemical crosslinking), GO was fixed onto cotton fabrics to improve their antibacterial performance. An antibacterial activity of up to 98% before washing and >90% even after 100 washing cycles was reported.14 Using a simple heat treatment, GO was reduced onto cotton fabrics to obtain good electrical conductivity, surface hydrophobicity and ultraviolet protection even after considerable bending and washing.15
However, most conductive GO-based fabrics are fabricated by dip-drying process, and there are no reports on dyeing GO particles onto cotton fabrics to improve conductive stability and other properties, including infrared adsorption and UV resistance. In the dyeing process, the free enthalpy of graphene sheets in water is lower, the direction of graphene sheets in water is easier, and the arrangement of graphene flakes on the fiber surface is more uniform and regular compared to dip-drying process, the differences between the two methods are shown in Fig. 1. In this paper, cotton fabrics have been dyed with GO of two distinct sizes and the morphology, structure, conductive stability in the drawing, bending and friction process and other properties (infrared adsorption and UV resistance) of modified fabrics have been studied.
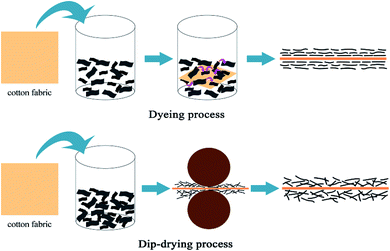 |
| Fig. 1 The differences between the dyeing process and dip-drying process. | |
2. Experiment section
2.1. Materials
Graphite powder (particle size < 30 μm) was purchased from Sino pharm Chemical Reagent Co. Ltd., China. Commercial 100% cotton woven fabrics (plain weave, 560 × 276, 109 g m−2), other agents, chemicals including sulfuric acid (H2SO4, 98 wt%), hydrogen peroxide (H2O2, 30 wt%), NaOH, hydrazine hydrate (N2H4·H2O), sodium nitrate (NaNO3) and potassium permanganate (KMnO4), were supplied by the Sino pharm Chemical Reagent Co. Ltd., Shanghai, China. Deionized water was used for all the experiments in this study.
2.2. Experimental
2.2.1. Preparation of GO. GO was prepared using the modified Hummers' method.16 The specific preparation process is as follows: precisely 5 g of graphite, potassium persulfate (5 g), phosphorus pentoxide (5 g) and concentrated sulfuric acid (98 wt%, 50 mL) were added into a beaker, and then slowly heated up to 80 °C for 5 h. After stirring with deionized water, the mixture was allowed to stand, and the supernatant was removed by layering and later filtered by adding water and drying. The product obtained was called pre-oxidized graphite. Concentrated sulfuric acid (98 wt%, 46 mL) and sodium nitrate (1 g) were added in an ice water bath and thoroughly mixed. The pre-oxidized graphite was then slowly added to the beaker and stirred until dissolution. The potassium permanganate (6 g) was added to the beaker in batches and was left to react for 2 h (45 °C), conditioned for 30 min and later combined with 5% sulfuric acid and centrifuged for 10 min. The produced obtained was washed repeatedly with deionized water until the pH became neutral resulting in the GO required for further studies.
2.2.2. Treated cotton fabrics by dyeing. The cotton fabric was immersed in a known concentration of GO solution at room temperature for 30 min and the dyeing was performed at 100 °C and pH of 10 with a bath ratio of 1
:
30. The dyeing time was maintained at 60 min. After dyeing, the fabrics were reduced by hydrazine hydrate at 90 °C for 3 h and then washed with cold water to dry. The dyeing process curve and the appearance of the fabric before and after dyeing is shown in Fig. 3 and 2, respectively.
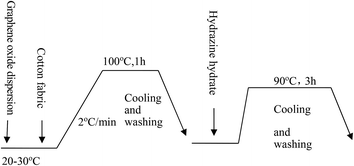 |
| Fig. 2 Dyeing process curve. | |
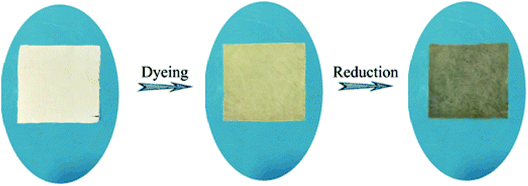 |
| Fig. 3 The appearance of cotton fabric before and after dyeing and reduction treatments. | |
2.3. Characterization
The morphology of the prepared GO samples was analyzed by field emission scanning electron microscopy (FE-SEM). The prepared GO was tested for changes in the carboxyl group content using X-ray photoelectron spectroscopy (XPS). The electrical conductivity of the fabric was tested using a universal meter. The thermal conductivity of the fabric was tested using an infrared thermal imager (FLK-TIR32 9HZ, Fluke, USA). The UV resistance of the fabric was tested in an UV tester (UV-2000, Labsphere Inc. USA).
3. Results and discussion
3.1. Morphology of GO
Considerable changes can be observed in the surface features of cotton fibers before and after treating with GO of different particle sizes as shown in Fig. 4. Untreated fibers have smooth and clear appearance (a). The surface of cotton fiber treated with pure macro GO becomes more rougher, and show considerable amounts of deposits on the surface (b). With increasing the ratio of superfine size GO in the blend makes the surface smoother gradually (as shown in (c) and (d)), especially for the cotton fiber dyed with a ratio of 50 macro/50 superfine GO as shown in Fig. 4(d), there is almost no stacking phenomenon and has an unique ridged shape morphology. However, as the proportion of the superfine layers increases further, there is a peeling phenomenon in Fig. 4(e), and also deposited unevenly on the surface of fiber by pure superfine GO in Fig. 4(f). With the increase of the proportion of superfine GO, there are strong π–π conjugation and van der Waals interaction between GO sheets enlarging the specific surface area, and therefore, it is prone to agglomeration. This formation has a direct relationship with subsequent performance.
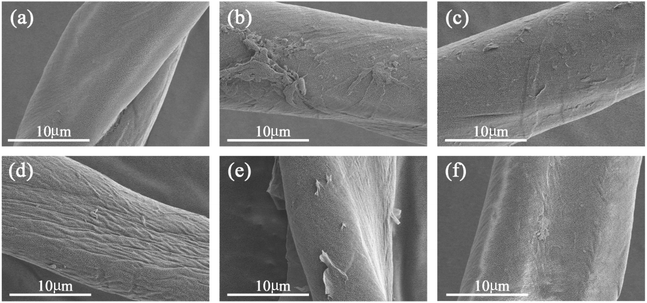 |
| Fig. 4 Morphology of cotton fabrics dyed by GO of different particle sizes: (a) SEM image of 100% cotton fabric; (b) cotton woven fabric dyed by macro GO; (c) cotton fabric dyed by 75 macro/25 superfine GO; (d) cotton fabric dyed by 50 macro/50 superfine GO; (e) cotton fabric dyed by 25 macro/75 superfine GO; (f) cotton fabric dyed by superfine GO. | |
Combining macro GO particles with superfine ones increases their average size as seen from Fig. 5. Without any superfine particles, the size of GO is 1467 nm, and decreases to 759 nm when the proportion is 25 macro/75 superfine GO, the average particle size of pure superfine GO is about 530 nm.
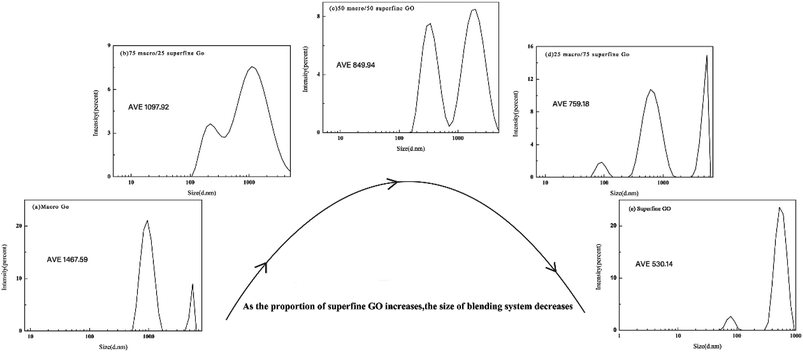 |
| Fig. 5 Size distribution of GO with different proportions of macro/superfine particles: (a) macro GO; (b) 75 macro/25 superfine GO; (c) 50 macro/50 superfine GO; (d) 25 macro/75 superfine GO; (e) superfine GO. | |
3.2. Carboxyl content of GO surface
A progressive decrease in carboxyl content on the surface of the fibers occurs as the ratio of the smaller size GO increases. As seen from Fig. 6, highest carboxyl group content of 40% was obtained when the macro GO was used. The number of functional groups decrease because of the formation of layers and also due to oxidation17,18 which decreases the number of groups. Also, large sized particles not only have higher number of carboxyl group content but also have better sorption on the fibers due to their higher polarity. Although the smaller GO has lower number of carboxyl group content, they have a larger specific surface area and also tend to form aggregates. When the macro and superfine pieces of GO are mixed, the aggregation on the fiber surface can be reduced. An optimum ratio of small and large particles is necessary to achieve the desired properties.
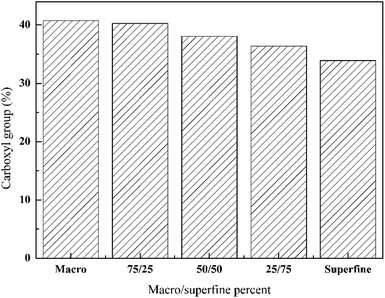 |
| Fig. 6 Carboxyl content on cotton fabrics dyed using different ratios of macro/superfine GO. | |
3.3. Electrical performance of cotton fabrics
3.3.1. Electrical resistance of dyed fabrics. Electrical resistance of the dyed fabrics was heavily dependent on the size of the GO particles. It can be seen from the Fig. 7 that the specific resistance of the cotton fabric dyed with macro GO is the smallest, which is 1800 Ω cm, and with 75/25 GO is 2300 Ω. cm, which are much smaller than the resistivity requirement of the conductive fiber (107 Ω cm). It can be prepared antistatic fabrics for use in special occasions and conductive fabrics resistant to electromagnetic radiation. As the proportion of the superfine GO increases, the electrical conductivity deteriorates, mainly due to the lower conductive ability of superfine GO sheets compared with that of macro GO sheets.19 This result provides an important research basis for the design and preparation of new flexible materials with excellent conductivity-stability.
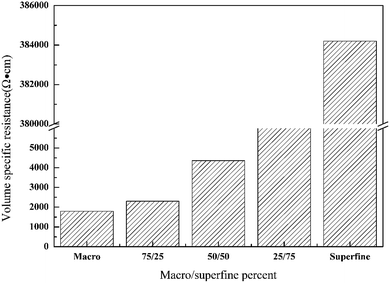 |
| Fig. 7 Volume specific resistance of cotton fabric dyed with GO of different sizes. | |
3.3.3. Electromechanical properties of dyed fabrics. Durability of GO to bending and stretching was excellent as seen from Fig. 10. There was no apparent change in resistance of the fabrics even when bent at 90° for 1000 times. Decrease in resistance was more prominent when fabrics were bent at 135° particularly above 500 cycles. Resistance of the weft yarns was higher and more stable than warp yarns, indicating that the electrical properties of the warp direction are more excellent. That is because when the fabrics were drawn, the fibers squeezed together and flattened and finally the warp and weft fibers formed an integrated hole with no observable gaps. This process could change the contact area from point-to-point to line-to-line and finally face-to-face, resulting in an increase in motion space of electrons20 and an improvement in transfer rate. The SEM images (Fig. 10(c and d)) show that the graphene oxide layer on the surface of the fiber still exists after several times of bending, and will not fall off. It also shows that GO can be assembled regularly on the surface of cotton fiber by dyeing.
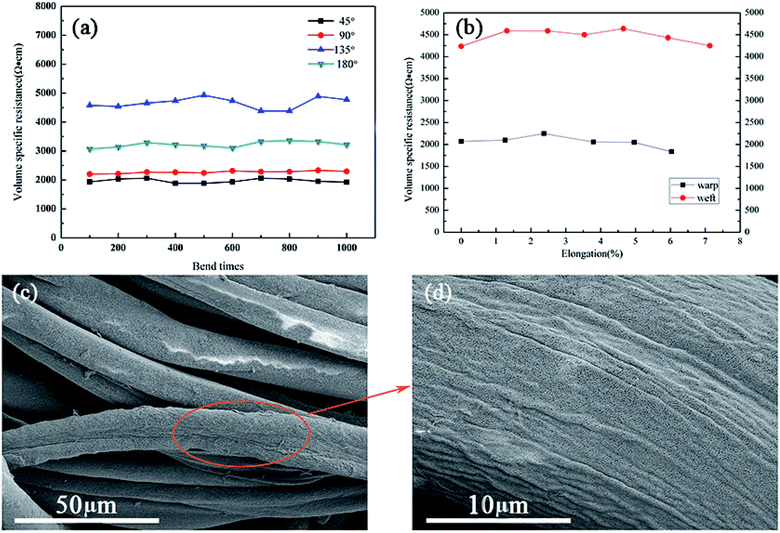 |
| Fig. 10 Pictures of electromechanical properties of dyed fabrics: (a) bending-conductivity of dyed cotton fabrics by multiple bending at different angles; (b) tensile-conductivity of dyed cotton fabrics; (c) SEM images of dyed fabrics dyed with 75 macro/25 superfine GO by bending 1000 times at 180°; (d) partial enlarged detail. | |
3.4. Applications of GO modified cotton fabrics
3.4.1. Infrared absorption. The dyed cotton fabric and the undyed cotton fabric are processed to form a T-shirt and the photo of the T-shirt worn by the human body is shown in Fig. 11(a), where in the front piece of the T-shirt is a cotton fabric dyed with GO. The back piece is an undyed cotton fabric. The infrared absorption test data of this T-shirt is shown in Fig. 11(b) and (c). From the data analysis, the maximum temperature of the front is 34.2 °C, the lowest temperature is 30.6 °C, the average temperature is 32 °C (shown in Fig. 11(b)); and the maximum temperature of the back part is 37.4 °C, the lowest is 32.2 °C and the average temperature of the human body is 33.9 °C (shown in Fig. 11(c)). Mainly due to the wearing of the dyed fabric, the infrared rays emitted by the human body itself are absorbed by the GO, resulting in a decrease in temperature. The back sheet is free of dyed fabric and the infrared light emitted by the human body is converted into heat energy, which causes the surface temperature to rise. The conclusion shows that the addition of GO can change the infrared radiation characteristics of the human body, reduced the infrared emissivity of fabric, and attenuate the energy generated by the infrared radiation of the human body,21,22 and thereby reducing the probability of the target human body being detected and achieving the stealth effect, especially suitable for processing infrared stealth functional textiles.
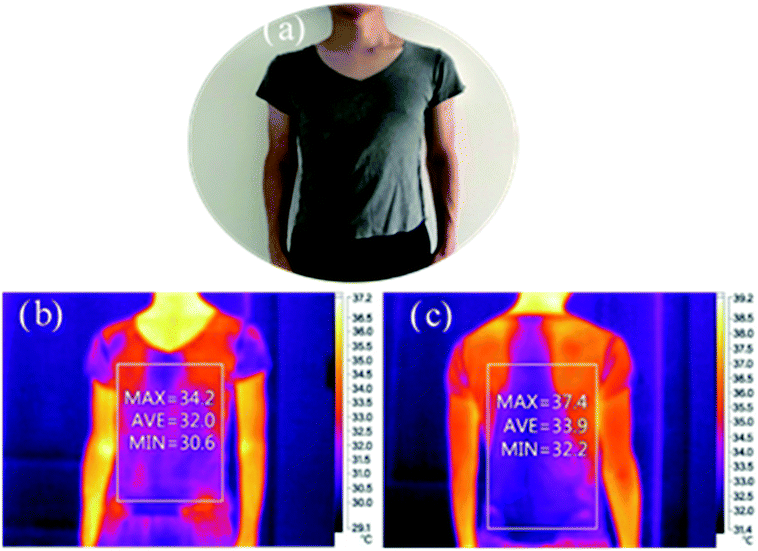 |
| Fig. 11 The infrared thermal imaging of model wearing T-shirt: (a) the photo of a model wearing T-shirt; (b) the front data of T-shirt; (c) the back data of T-shirt. | |
3.4.2. Ultraviolet resistance. After dyed with 75 macro/25 superfine, the GO was present on the fabrics is about 1.25% by calculation. When washing 2 to 10 cycles. The details of UV resistance are as shown in Table 1. The dyed cotton fabric and the undyed cotton fabric are processed to form a T-shirt in Fig. 12. From Table 1 and Fig. 12, it can be seen that GO treated fabrics were able to provide substantial increase in UV absorption. Untreated fabrics had average UPF of only 19 compared to 108 for treated fabrics. Such high UV resistance is due to the ability of GO to absorb and reflect UV light. Extent of UV resistance provided by the dyed fabrics could be rated excellent (UPF > 40) as per ASTM D6603-2012. Previous studies on increasing UV resistance of fabrics using GO have also shown similar results.23
Table 1 Ultraviolet resistance of cotton fabrics dyed with GO
Numerical value |
Undyed |
After dyed |
Washing cycles |
2 |
4 |
6 |
8 |
10 |
TUVA/% |
8.46 |
1.04 |
1.09 |
1.12 |
1.16 |
1.17 |
1.16 |
TUVB/% |
4.25 |
0.88 |
0.92 |
0.97 |
0.98 |
0.98 |
0.99 |
AVE UPF |
19.04 |
108.24 |
105.37 |
103.59 |
103.40 |
102.60 |
102.95 |
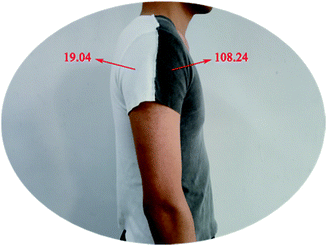 |
| Fig. 12 The side photo of the model wearing T-shirt containing 1.25% GO (75% macro/25% superfine). | |
4. Conclusions
In our work, a simple approach of assembly of GO on cotton fiber through dyeing has been used to impart excellent conductive stability, infrared absorption and UV resistance. The extent of improvement in properties was dependent on the size of the GO used: the large size (macro) particles assembled on the fiber surface makes it have good electrical conductivity, whereas blended with superfine particles can make the surface smoother of fiber, and has better conductivity with a volume specific resistance of 2300 Ω cm. GO on the fabrics was resistant to washing and bending up to 1000 times. A high UPF of 102 was imparted after dyeing with GO even after 10 washing cycles. In addition, the dyed fabrics showed heat infrared absorption capability when worn on the body. GO dyed cotton fabrics show potential for use in electronics, space, medical and other applications.
Conflicts of interest
There are no conflicts to declare.
Acknowledgements
We gratefully acknowledge the financial support from the National Natural Science Foundation of China (51703079), General Scientific Research Projects of Zhejiang Education Department (Y201738106), Key Laboratory of Yarn Materials Forming and Composite Processing Technology, Zhejiang Province, Jiaxing University (MTC-2020-12) and Key Program in College of Nanhu (N41472001-42).
References
- T. Das, B. K. Sharma, A. K. Katiyar and J. H. Ahn, J. Semicond., 2018, 39, 011007 CrossRef.
- N. V. Bhat, D. T. Seshadri, M. M. Nate and A. V. Gore, J. Appl. Polym. Sci., 2006, 102, 4690–4695 CrossRef CAS.
- B. Ouadil, O. Cherkaoui, M. Safi and M. Zahouily, Appl. Surf. Sci., 2017, 414, 292–302 CrossRef CAS.
- D. P. Dubal, N. R. Chodankar, D. H. Kim and P. Gomezromero, Chem. Soc. Rev., 2018, 47, 2065–2129 RSC.
- Z. Stempien, T. Rybicki, E. Rybicki, M. Kozanecki and M. I. Szynkowska, Synth. Met., 2015, 202, 49–62 CrossRef CAS.
- M. R. Nateghi and M. Shateri-Khalilabad, Carbohydr. Polym., 2015, 117, 160–168 CrossRef CAS PubMed.
- L. E. Román, J. Huachani, C. Uribe, J. Solís, M. Gómez, S. Costa and S. Costa, Appl. Surf. Sci., 2019, 469, 204–212 CrossRef.
- G. Rosace, A. Castellano, V. Trovato, G. Iacono and G. Malucelli, Carbohydr. Polym., 2018, 196, 348–358 CrossRef CAS PubMed.
- Y. M. Ji, Y. Z. Li, G. Q. Chen and T. L. Xing, Mater. Des., 2017, 133, 528–535 CrossRef CAS.
- B. Fugetsu, E. Sano, H. W. Yu, K. Mori and T. Tanaka, Carbon, 2010, 12, 3340–3345 CrossRef.
- A. Ramadoss, B. Saravanakumar and S. J. Kim, Nano Energy, 2015, 15, 587–597 CrossRef CAS.
- J. S. Ren, C. X. Wang, X. Zhang, T. Carey, K. L. Chen, Y. J. Yin and F. Torrisi, Carbon, 2017, 111, 622–630 CrossRef CAS.
- L. Gan, S. M. Shang, C. W. M. Yuen and S. X. Jiang, Compos. Sci. Technol., 2015, 117, 208–214 CrossRef CAS.
- J. M. Zhao, B. Deng, M. Lv, J. Y. Li, Y. J. Zhang, H. Q. Jiang, C. Peng, J. Li, J. Y. Shi, Q. Huang and C. H. Fan, Adv. Healthcare Mater., 2013, 2, 1259–1266 CrossRef CAS.
- G. M. Cai, Z. L. Xu, M. Y. Yang, B. Tang and X. G. Wang, Appl. Surf. Sci., 2017, 393, 441–448 CrossRef CAS.
- W. S. Hummers Jr and R. E. Offeman, J. Am. Chem. Soc., 1958, 80, 1339 CrossRef.
- L. L. Zhang and X. S. Zhao, Chem. Soc. Rev., 2009, 38, 2520–2531 RSC.
- M. Terrones, A. R. Botello-Méndez, J. Campos-Delgado, F. López-Urías, Y. I. Vega-Cantú, F. J. Rodríguez-Macías, A. L. Elías, E. Muñoz-Sandoval, A. G. Cano-Márquez, J.-C. Charlier and H. Terrones, Nano Today, 2010, 5, 351–372 CrossRef.
- Y. S. Jun, S. Sy, W. Ahn, H. Zarrin, L. Rasen, R. Tjandra, B. M. Amoli, B. X. Zhao, G. Chiu and A. P. Yu, Carbon, 2015, 95, 653–658 CrossRef CAS.
- H. Ma, W. Wu, J. D. Cao, B. B. Yue and H. X. Zhang, Carbon, 2017, 114, 731–739 CrossRef CAS.
- X. H. Wu, J. Lyu, G. Hong, X. C. Liu and X. T. Zhang, Langmuir, 2018, 34, 9004–9014 CrossRef CAS PubMed.
- K. J. Yuan, H. C. Wang, J. Liu, X. M. Fang and Z. G. Zhang, Sol. Energy Mater. Sol. Cells, 2015, 143, 29–37 CrossRef CAS.
- M. W. Tian, X. L. Hu, L. Q. Qu, S. F. Zhu, Y. N. Sun and G. T. Han, Carbon, 2016, 96, 1166–1174 CrossRef CAS.
|
This journal is © The Royal Society of Chemistry 2020 |
Click here to see how this site uses Cookies. View our privacy policy here.