DOI:
10.1039/D0RA00773K
(Paper)
RSC Adv., 2020,
10, 9663-9671
One-pot multicomponent synthesis of thieno[2,3-b]indoles catalyzed by a magnetic nanoparticle-supported [Urea]4[ZnCl2] deep eutectic solvent†
Received
24th January 2020
, Accepted 28th February 2020
First published on 6th March 2020
Abstract
In this study, we have developed the synthesis of thieno[2,3-b]indole dyes via a multicomponent reaction of cheap and available reagents such as sulfur, acetophenones, and indoles using a magnetic nanoparticle-supported [Urea]4[ZnCl2] deep eutectic solvent as a green catalyst. The synthesis of a series of diversely functionalized thieno[2,3-b]indole has been successfully performed in a one-pot reaction. Among a total of 25 compounds synthesized, there are 21 new compounds with full characterization such as FT-IR, 1H and 13C NMR, HRMS (ESI). Due to the deep eutectic solvent coated surface of the magnetic nanoparticles, the catalyst could be recovered by an external magnet and reused in five consecutive runs without a considerable decrease in catalytic activity.
1. Introduction
Thieno[2,3-b]indoles are common structural motifs in a variety of biological activities and therapeutically useful compounds leading to potential applications in treating epilepsy, neurological diseases,1 plant-growth regulatory properties,2 battery devices,3–7 and polymer conductors.4 Due to the potential applications of thieno[2,3-b]indoles, the development of new and efficient synthetic protocols for these compounds has received considerable attention. Traditionally, thieno[2,3-b]indoles are synthesized using functionalized 2-alkynylphenylisothiocyanates, 1-alkylisatins, and indole-2-thiones as starting materials, and require several steps to afford the desired products (Scheme 1).8–10 Although these classical approaches have been extensively used, there is ongoing research for new methods that have simpler work-ups, are atom-economical with good to excellent yields, use recyclable catalysts and use readily inexpensive starting materials. To date, only two reports have described the synthesis of thieno[2,3-b]indoles via a one-pot multicomponent reaction which provides a greener approach than the classical methods. Li and coworkers reported the Brønsted acid-catalyzed three-component synthesis of thieno[2,3-b]indoles starting from indoles, alkenes or alkynes, and sulfur powder.11 Ni and coworkers demonstrated the synthesis of 3-substituted thieno[2,3-b]indoles via cascade cyclization by Brønsted acid-promoted annulation of indoles, ketones, and sulfur powder.12 However, the low yields, narrow substrate scope, and the inability to recycle catalysts remain a crucial challenge to industrial application.
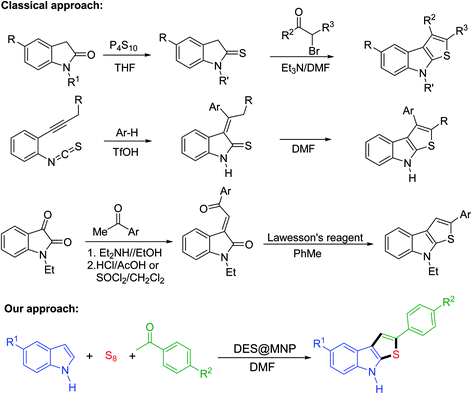 |
| Scheme 1 Approaches to thieno[2,3-b]indoles. | |
The development of new catalysts is necessary for the advancement of organic synthesis.13–15 Over the last decade, several synthetic approaches have been reported in the field by employing deep eutectic solvents as catalysts.16–20 However, significant drawbacks including difficult catalyst recovery, tedious product separation, and the requirement of greater stoichiometric amounts of DES as dual catalyst/solvent limited their widespread application.15,21–23 Hence, the idea for using supported DES always exists in our mind, which combines the prominent feature of DES and the benefits of heterogeneous catalysts, including ease of handling, separation, and recycling. Magnetic nanoparticles (MNPs) have recently been shown to be catalyst supports due to their easy preparation, low cost, high stability, high surface area, and simple recovery by magnetic forces.24 Due to these unique properties, many MNPs supported catalysts have been employed in magnetic catalysts in organic syntheses,23–31 biomass conversion,32 and biodiesel production.33 Thus, we focused our attention on the combination of the attractive properties of MNPs and DESs to produce a novel catalyst which can be highly dispersed in the reaction mixture (like a homogenous catalyst) and easily separated by a magnet and reused (like a heterogeneous catalyst).34
Because of the concerns about the development of a novel catalyst in green and sustainable chemistry, we report here the one-pot three-component synthesis of thieno[2,3-b]indoles from readily available indoles, acetophenones, and sulfur powder using a magnetically recyclable DES@MNP catalyst. The outstanding features of the current work are good to excellent yield, high regioselectivity, a broad substrate scope, and a recyclable catalyst.
2. Experimental
2.1. Preparation of the magnetic nanoparticle-supported Lewis acidic deep eutectic solvent (DES@MNP)
Synthesis of silica-coated Fe3O4 nanoparticles (Fe3O4@SiO2@(CH2)3Cl). The magnetic nanoparticle-supported deep eutectic solvent catalyst was prepared following the procedure shown in Scheme 1. Firstly, the magnetic nanoparticle Fe3O4 was synthesized by the coprecipitation method reported in the previous literature. The mixture of FeCl2 and FeCl3 was dissolved in 200 mL water under ultrasonic irradiation. The potassium hydroxide solution (1.0 M) was added slowly until pH 12.0. After 120 min sonication, Fe3O4 was washed with water and ethanol to pH 7.5, separated by a magnetic and drying at 80 °C for 12 h. Fe3O4 was coated with a layer of silica by refluxing mixture Fe3O4 (1.0 g), 3.0 mL ammonia solution, and 3.0 mL of tetraethylorthosilicate (TEOS) in 100 mL ethanol for 8 h. Next, Fe3O4@SiO2 (5.0 g) and (3-chloropropyl)triethoxysilane (4.820 g, 20.0 mmol) in 100 mL toluene were refluxed for 12 h. The prepared Fe3O4@SiO2@(CH2)3Cl was separated using a permanent magnet, followed by washing with ethanol and dried at 80 °C for 6 h.
Synthesis of DES. The [Urea]4[ZnCl2] DES was synthesized by adding urea (1.2 g, 20.0 mmol) to zinc chloride (0.680 g, 5.0 mmol) and stirring to afford a transparent liquid at 100 °C for 30 min.
Synthesis of DES@MNP. Fe3O4@SiO2@(CH2)3Cl (3.0 g) and DES [Urea]4[ZnCl2] (1.880 g, 5.0 mmol) were added round-bottomed flask and stirred vigorously at 100 °C for 18 h. After completion of the reaction, the DES@MNP was collected by an external magnet and washed with ethanol (3 × 20.0 mL) and dried under reduced pressure at 60 °C for 6 h.
2.2. General experimental procedure for the synthesis of 2-phenyl-8H-thieno[2,3-b]indole
Indole (1.0 mmol, 117 mg), acetophenone (2.0 mmol, 240 mg), and elemental sulfur power (5.0 mmol, 160 mg) were added into a round-bottom flask precharged with DES@MNP (10 mol%, 30 mg) in DMF (1.5 mL). The mixture reaction was then stirred at 140 °C for 12 h under the opening atmosphere. After completion of the reaction as checked by TLC, and the reaction mixture dissolved in 5.0 mL ethyl acetate. The DES@MNP catalyst was separated out by magnet and washed further with anhydrous acetone (3 × 5.0 mL) and ethanol (3 × 5.0 mL) for the next experiments. The reaction mixture was diluted with water (15.0 mL) and extracted with EtOAc (3 × 20.0 mL). The organic layer was dried over sodium sulfate, and the solvent was recovered under reduced pressure. Next, the residue was purified by column chromatography on silica gel using dichloromethane/petroleum ether = 2
:
3 as the eluent to afford the pure product. The product identity was confirmed by melting point, FT-IR, 1H NMR, 13C NMR, and MS.
3. Results and discussion
3.1. Catalyst characterization
Initially, the DES@MNP was synthesized following the procedure presented in Scheme S1 (see ESI†).35 First, Fe3O4 was prepared by a coprecipitation method similar to a previously reported literature, followed by a SiO2 coating procedure afforded Fe3O4@SiO2. Subsequently, Fe3O4@SiO2 was functionalized using (3-chloropropyl)triethoxysilane by surface capping method to provide Fe3O4@SiO2@(CH2)3Cl. The precursor [Urea]4[ZnCl2] deep eutectic solvent was prepared by mixing of ZnCl2 with urea (1
:
4 molar ratio) at 100 °C until a clear solution was obtained. Finally, the treatment of DES with Fe3O4@SiO2@(CH2)3Cl in acetone at 100 °C for 18 h provides the DES@MNP catalyst. The structure of DES@MNP was characterized by various techniques including FT-IR, Raman, TGA, SEM, TEM, XRD, VSM, EDX and ICP-MS (see the ESI†).
FT-IR spectra of Fe3O4@SiO2 magnetic nanoparticles showed peaks at around 580, 1095, 1645, and 3419 cm−1, which are attributed to the Fe–O–Fe, Si–O–Si and O–H groups (Fig. S1, ESI†). For DES-supported Fe3O4@SiO2, additional peaks were observed for C
C, C–N, N–H, which confirms successful immobilization (Fig. S1, ESI†). The characteristic peaks of DES@MNP were at the same wavenumbers with the precursors, with a small shift due to the interaction between DES and the support. The Raman peak at 485 cm−1 can be interpreted as stretching vibration of the Zn–Cl bond (Fig. S2, ESI†). The stability of the DES@MNP was proved by the thermogravimetric (TG) analysis. DES@MNP showed a sharp decrease in weight (40%) was observed at 250−650 °C, which is attributed to the organic composition grafting. Thus, the DES@MNP is stable at around 250 °C (Fig. S3, ESI†).
The magnetic properties of the DES@MNP and the neat Fe3O4 were recorded by vibrating sample magnetometry (Fig. S4, ESI†). The saturation magnetization of these samples was found to decrease from 69.2 to 30.8 emu g−1 due to the silica coating and the organic grafting on the surface of Fe3O4. However, it was sufficient for the recovery of the DES@MNP from the reaction mixture using an external magnet. In addition, the XRD pattern of the coated nanoparticles functionalized DES was carried out to confirm the crystalline nature. The XRD pattern (Fig. S5, ESI†) of the DES@MNP showed the diffraction peak positions and the relative intensities of the peaks, which matched well with the standard Fe3O4 sample (JCPDS file no. 19-0629). The SEM image of DES@MNP revealed that the catalyst was obtained in uniform nanometer-sized particles (Fig. S6a, ESI†). TEM image showed a well-defined core–shell structure with relatively nanosize distribution, a dark Fe3O4 core surrounded by a grey silica shell, and the average size of the obtained particles are 15–25 nm (Fig. S6b, ESI†). The chemical composition of DES@MNP was recorded by energy-dispersive X-ray spectroscopy (EDX), confirming the presence of C, O, N, Fe, Zn, Si, and Cl elements in the structure of the catalyst (Fig. S7, ESI†). The EDX revealed that the mass percent of Zn was 26.69%. This calculation was in good agreement with ICP-MS data for Zn analysis reporting the content of elemental Zn as 277
600 ppm, corresponding to Zn2+ loading of 4.10 mmol g−1.
3.2. The activity of DES@MNP for the synthesis of 2-phenyl-8H-thieno[2,3-b]indole
In a preliminary survey of reactions, DES@MNP was found to be catalytically active in a one-pot multi-component reaction of indole, acetophenone, and sulfur as a model reaction (Table 1). Previously, this reaction can also be accomplished with acetic acid as a homogeneous catalyst.12 However, the method suffers from difficulties in the recovery of the catalyst, moderate yield, high temperature for longer reaction time. These drawbacks can be overcome by using DES@MNP as a magnetically recoverable catalyst. To our delight, the expected product was obtained in excellent yield (87%) at 140 °C for 12 h when DES@MNP was employed. The reactions were also tested using Brønsted acids as the catalysts at 140 °C for 12 h in DMF; the desired product was obtained in 67–72% yield (Table 1, entries 1–5). Next, several Lewis acids were screened in the model reaction (Table 1, entries 6–10). Among these Lewis acids, ZnCl2 was shown to be a suitable catalyst that provided the desired product in 80% yield. At this point, we revealed that ZnCl2 could play an essential role in promoting the condensation of indole, sulfur, and acetophenone and this is the reason we developed the new catalyst with ZnCl2 active sites. Additionally, the control experiment in the absence of catalyst did not generate the expected product. The support Fe3O4, Fe3O4@SiO2, and Fe3O4@SiO2@(CH2)3Cl were also not reactive under these conditions (Table 1, entries 11–13). The typical [Urea]4[ZnCl2] DES provided the desired product in 82% yield, but the homogeneous DES was difficult to recover and reuse with the loss of the catalytic activity. The combination of nanoparticle and DES increased the reaction yield as well as selectivity and made the recovery of the catalyst much more comfortable by using an external magnet. The reaction proceeds effectively because the nano-catalyst possesses a high surface area increasing the adsorption of reactants on the surface of the active Zn2+ sites on the DES@MNP. Interestingly, DES@MNP showed a higher yield in comparison with HCOOH catalyst (75% yield) which was reported by Ni and coworkers.12
Table 1 Screening of different catalysts on the synthesis of 2-phenyl-8H-thieno[2,3-b]indole
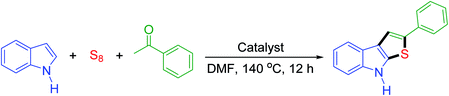
|
Entrya |
Type of catalysts |
Catalyst (mol%) |
Yieldb (%) |
Reaction conditions: acetophenone (2.0 mmol), indole (1.0 mmol), sulfur (5.0 mmol) and catalysis (10 mol%) were heated in DMF (1.5 mL) at 140 °C for 12 h. Yield of 2-phenyl-8H-thieno[2,3-b]indole was isolated by column chromatography (dichloromethane/petroleum ether). |
1 |
Brønsted acids |
H2SO4 |
72 |
2 |
HCl |
70 |
3 |
H3PO4 |
67 |
4 |
CH3COOH |
75 |
5 |
CF3COOH |
80 |
6 |
Lewis acids |
AlCl3 |
73 |
7 |
FeCl3 |
57 |
8 |
ZnCl2 |
80 |
9 |
SnCl4 |
65 |
10 |
CuCl2 |
42 |
11 |
Control experiment |
Fe3O4 |
— |
12 |
Fe3O4@SiO2 |
— |
13 |
Fe3O4@SiO2@(CH2)3Cl |
— |
14 |
[Urea]4[ZnCl2] |
82 |
15 |
Fe3O4@SiO2@(CH2)3–[Urea]4[ZnCl2] |
87 |
The additive DMF plays a vital role in the yield and regio-selectivity control for the thieno[2,3-b]indole synthesis.12 Next, we turned our attention to the optimization of the additives to obtain the major corresponding regioselective product where the phenyl substituent was attached at the C-2 position in the thieno[2,3-b]indole. The results are presented in Table S1 (ESI†). Among these additives, DMF was the best additive under the current method. The reaction proceeds efficiently with DABCO or N-ethylmorpholine to provide the desired product in 75 and 81%, respectively.
When solid catalysts promote organic synthesis, the solvent plays a vital role in the reaction rate, depending on the nature of these catalysts. The solvent effect on the catalytic activity of DES@MNP was further investigated, and the results are shown in Table S2 (ESI†). The three-component cyclization reaction was carried out at 140 °C, using acetophenone, indole, and sulfur molar ratio of 1
:
2
:
5, in the presence of 10 mol% DES@MNP catalyst and 0.3 mL DMF as an additive, in 1.5 mL organic solvent. A significant drop in reaction yield was observed for the other solvents, whereas a higher reaction activity was observed in DMF as a double role of additive and solvent. It was proposed that the DMF solvent could form the active precursor when interacted with sulfur and acetophenone, affording reaction rate enhancement (please see the proposed mechanism in Scheme S2†).
Next, the effect of reaction time and temperature were investigated (ESI, Table S3 and S4†). The three-component reaction was conducted in DMF for 12 h, using acetophenone
:
indole
:
sulfur molar ratio of 1
:
2
:
5 in the presence of 10 mol% of DES@MNP catalyst. It was shown that no expected product was detected for the reaction at 80 °C. The low yield of the product was obtained at 100 °C. Increasing the reaction temperature to 140 °C led to a significantly improved reaction yield of 2-phenyl-8H-thieno[2,3-b]indole. The reaction time was also screened and the best yield was observed at 12 h (please see in ESI, Table S4†). The reactant molar ratio was investigated in the model reaction at 140 °C for 12 h. It was found that the reaction yield was significantly affected by the reactant molar ratio. The results revealed that the use of fewer than 4 equivalents of sulfur gave rise to the low yields of the desired product. However, when 4 or 5 equivalents of sulfur were employed, the yields dramatically increased.
To further define the scope and limitations of the present method, various indoles and acetophenones were examined. As shown in Table 2, the process was highly useful for the preparation of thieno[2,3-b]indole derivatives (Fig. 1). Acetophenone bearing various substituents at the para position could smoothly proceed under the present method provided the desired product in good to excellent yields. When acetophenone and acetophenone bearing electron-donating groups were employed to couple with indole, the desired product was obtained in higher yields than 4-fluoroacetophenone and 2-acetylthiophene. To our delight, good to excellent yields were observed when the methyl, methoxyl, halo, and nitro groups were located at the C-5 in the NH-unprotected indole ring. Indoles with halogens were all reactive, but 5-bromoindole produced the product in slightly higher yields than 5-fluoroindole and 5-chloroindole. 5-Nitroindole, which is known to deactivate many organic reactions in which it is used, was found to be a feasible reagent in our method producing 5-nitro-2-phenyl-8H-thieno[2,3-b]indole in 54% yield. It is noteworthy that these unprotected 1H-indoles worked well in this protocol to provide the desired product in high yields without the need for protection of the NH position when compared with previous literature.12 Additionally, significant regioselectivities of products were observed in over 95% making the isolation of products more efficient. Thus, the novel DES@MNP is a highly active catalyst for the synthesis of thieno[2,3-b]indole derivatives.
Table 2 Substrate scope for the synthesis of 2-phenyl-8H-thieno[2,3-b]indole derivatives
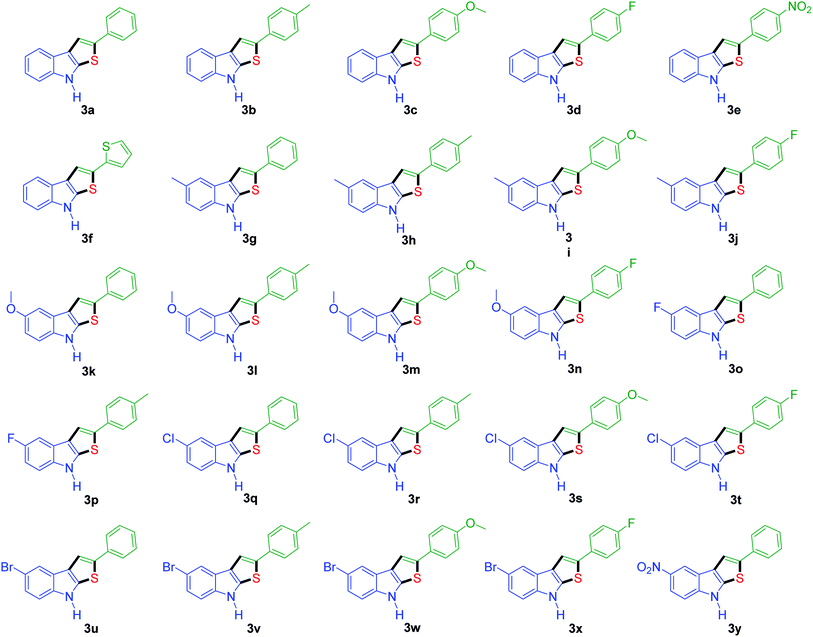 |
| Fig. 1 The structure of various 2-phenyl-8H-thieno[2,3-b]indole compounds. | |
Although several homogeneous catalysts in our research such as CF3COOH, ZnCl2, [Urea]4[ZnCl2] also exhibited high activity in the reaction (please see in Table 1). However, the main drawback is the difficulty in the recovery and reuse of these homogeneous catalysts. The prominent feature of the current method is the ease of separation of DES@MNP by an external magnet. The DES@MNP was recovered and reused over five consecutive runs, by repeatedly separating the DES@MNP catalyst from the reaction mixture by a magnet, washed with an organic solvent, dried under vacuum in 30 min, and then reused for next cycle. Interestingly, the reaction still afforded 83% yield of the desired product in the fifth run (Fig. 2). Remarkably, the structure of the recovered DES@MNP catalyst could be maintained under the current method, as confirmed by FT-IR (Fig. S8, ESI†).
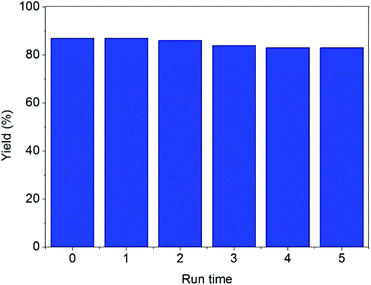 |
| Fig. 2 Recycling experiments. | |
The active sites on the heterogeneous catalyst can dissolve into the liquid phase during a reaction and act as a homogeneous catalyst. To confirm whether active zinc species dissolved from the DES@MNP promoted to the formation of the desired product (A), the leaching test was investigated. The model reaction was stopped after 8 h, separation of DES@MNP from the reaction mixture by a magnet. The reaction mixture without catalyst was then stirred for further 8 h and analyzed by GC-MS. It was found that no additional desired product was obtained in the absence of DES@MNP catalyst (Fig. 3). Thus, the leaching of zinc from the catalyst to the solution was negligible. Additionally, the content of Zn species in reaction filtrate was recorded by ICPMS, and the result was measured less than 1 ppm of Zn. Obviously, there was no contribution from the leaching of active Zn species in the reaction solution, and the synthesis of thieno[2,3-b]indole could only occur in the presence of the DES@MNP.
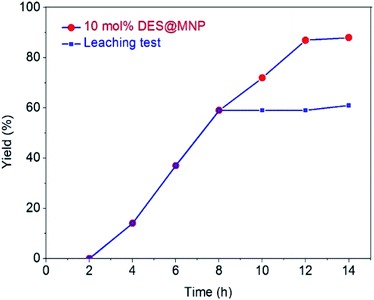 |
| Fig. 3 Leaching test. | |
3.3. Reaction mechanism research
To determine the mechanism insights for the synthesis of thieno[2,3-b]indole via a multicomponent reaction, some mechanistic experiments were carried out. According to the above control experiments and previous literature, a proposed mechanism was depicted in Scheme 2. Assisted by DES@MNP, the reaction proceeds via the initial formation of 1-(dimethylamino)-2-phenyl-1H-thiiren-1-ium (A), which is a resonance to form A′ (Willgerodt–Kindler reaction). The intermediate (A) reacts with indole via a ring-opening addition, followed by ring closure and then eliminated one molecule of dimethylamine to afford the target product. To check the conformability of the plausible mechanism for the same reaction with the absence of indole catalyzed by DES@MNP, we also carried out the reaction of acetophenone, elementary sulfur, and DMF under optimized conditions. The (A′) product was obtained in a yield of 65%. Next, the indole was then subjected to the reaction mixture and the desired product was achieved in 87% yield (ESI†). Thus, it is not doubtful that the multicomponent synthesis of thieno[2,3-b]indole reported herein must also undergo formation the precursor (A) and the DMF solvent plays an important role in the reaction mechanism. Although the reaction mechanism is not clear now, the protocol possesses attractive merits including simply and efficiently recyclable catalyst, wide scope of substrates, high yield, and high regioselectivity.
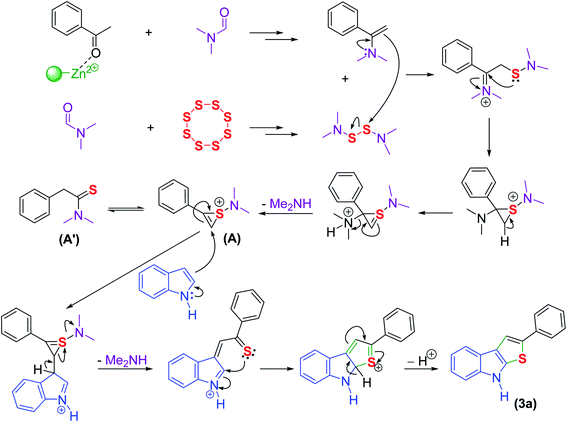 |
| Scheme 2 Proposed reaction mechanism. | |
4. Conclusion
In conclusion, we have developed a catalyst for the synthesis of thieno[2,3-b]indole via the one-pot multicomponent reaction of indoles, acetophenones, and sulfur. The corresponding products are smoothly formed in high yields and regioselectivity under mild conditions. More importantly, we have described the first example of using DES@MNP-catalyzed the thieno[2,3-b]indole synthesis via multicomponent reaction with cheap and readily available reactants. DES@MNP was shown to be the extremely powerful catalyst to activate the reaction leading to total conversions even various substrates bearing electron-rich or electron-poor substituents. Further development and applications of multicomponent reactions of direct construction of thienoindole from elemental sulfur and indoles are currently under investigation in our laboratory. We hope that DES@MNP will find their applications in many organic syntheses, especially in green and sustainable syntheses of biologically active compounds.
Conflicts of interest
There are no conflicts to declare.
Acknowledgements
This research is funded by Vietnam National Foundation for Science and Technology Development (NAFOSTED) under grant number 104.01-2019.26. We thank MSc Duy-Khiem Nguyen Chau (North Carolina State University, USA) and MSc Mai Hoang Ngoc Do (IPH-HCM) for their help.
References
- J. Yang, Y. Cai, Y. Zhou, C. Zhang, P. Liang, B. Zhao, J. Shao, N. Fu, W. Huang and X. Dong, Dyes Pigments, 2017, 147, 270–282 CrossRef CAS.
- K. Kanbe, M. Okamura, S. Hattori, H. Naganawa, M. Hamada, Y. Okami and T. Takeuchi, Biosci., Biotechnol., Biochem., 2014, 57, 632–635 CrossRef.
- R. A. Irgashev, A. A. Karmatsky, S. A. Kozyukhin, V. K. Ivanov, A. Sadovnikov, V. V. Kozik, V. A. Grinberg, V. V. Emets, G. L. Rusinov and V. N. Charushin, Synth. Met., 2015, 199, 152–158 CrossRef CAS.
- F. Baert, C. Cabanetos, M. Allain, V. Silvestre, P. Leriche and P. Blanchard, Org. Lett., 2016, 18, 1582–1585 CrossRef CAS PubMed.
- H. Qi, Y. Zhang, Q. Tao, J. Chen, Z. Li, X. Xu, H. Tan, Q. Peng and W. Zhu, Tetrahedron, 2016, 72, 7430–7437 CrossRef CAS.
- Y. Wen, W. Wu, Y. Li, Y. Li, T. Qin, Y. Tang, L. Wang and J. Zhang, Org. Electron., 2016, 38, 61–68 CrossRef CAS.
- Y. Wen, W. Wu, Y. Li, W. Zhang, Z. Zeng, L. Wang and J. Zhang, J. Power Sources, 2016, 326, 193–202 CrossRef CAS.
- T. Otani, S. Kunimatsu, T. Takahashi, H. Nihei and T. Saito, Tetrahedron Lett., 2009, 50, 3853–3856 CrossRef CAS.
- R. A. Irgashev, A. A. Karmatsky, G. L. Rusinov and V. N. Charushin, Beilstein J. Org. Chem., 2015, 11, 1000–1007 CrossRef CAS PubMed.
- H. Z. Boeini, Helv. Chim. Acta, 2009, 92, 1268–1272 CrossRef CAS.
- B. Li, P. Ni, H. Huang, F. Xiao and G.-J. Deng, Adv. Synth. Catal., 2017, 359, 4300–4304 CrossRef CAS.
- P. Ni, B. Li, H. Huang, F. Xiao and G.-J. Deng, Green Chem., 2017, 19, 5553–5558 RSC.
- L. Wu, A. Mendoza-Garcia, Q. Li and S. Sun, Chem. Rev., 2016, 116, 10473–10512 CrossRef CAS PubMed.
- E. L. Smith, A. P. Abbott and K. S. Ryder, Chem. Rev., 2014, 114, 11060–11082 CrossRef CAS PubMed.
- Q. Zhang, K. De Oliveira Vigier, S. Royer and F. Jerome, Chem. Soc. Rev., 2012, 41, 7108–7146 RSC.
- X.-d. Tang, Y.-f. Zhang and J.-j. Li, Catal. Commun., 2015, 70, 40–43 CrossRef CAS.
- Q. Wang, X. Yao, Y. Geng, Q. Zhou, X. Lu and S. Zhang, Green Chem., 2015, 17, 2473–2479 RSC.
- C. Vidal, J. García-Álvarez, A. Hernán-Gómez, A. R. Kennedy and E. Hevia, Angew. Chem., Int. Ed., 2016, 55, 16145–16148 CrossRef CAS PubMed.
- S. B. Phadtare and G. S. Shankarling, Green Chem., 2010, 12, 458–462 RSC.
- A. P. Abbott, D. Boothby, G. Capper, D. L. Davies and R. K. Rasheed, J. Am. Chem. Soc., 2004, 126, 9142–9147 CrossRef CAS PubMed.
- S. Khandelwal, Y. K. Tailor and M. Kumar, J. Mol. Liq., 2016, 215, 345–386 CrossRef CAS.
- F. Keshavarzipour and H. Tavakol, J. Iran. Chem. Soc., 2015, 13, 149–153 CrossRef.
- D. Shahabi and H. Tavakol, J. Mol. Liq., 2016, 220, 324–328 CrossRef CAS.
- V. Polshettiwar, R. Luque, A. Fihri, H. Zhu, M. Bouhrara and J. M. Basset, Chem. Rev., 2011, 111, 3036–3075 CrossRef CAS PubMed.
- Y. Zhang and C. Xia, Appl. Catal., A, 2009, 366, 141–147 CrossRef CAS.
- Q. Zhang, H. Su, J. Luo and Y. Wei, Green Chem., 2012, 14, 201–208 RSC.
- Y. Kong, R. Tan, L. Zhao and D. Yin, Green Chem., 2013, 15, 2422–2433 RSC.
- B. Karimi, F. Mansouri and H. Vali, Green Chem., 2014, 16, 2587–2596 RSC.
- R. K. Sharma, S. Dutta, S. Sharma, R. Zboril, R. S. Varma and M. B. Gawande, Green Chem., 2016, 18, 3184–3209 RSC.
- F. Keshavarzipour and H. Tavakol, Appl. Organomet. Chem., 2017, 31, e3682 CrossRef.
- M. T. Jafari-Chermahini and H. Tavakol, ChemistrySelect, 2019, 4, 1895–1902 CrossRef CAS.
- Q. Bao, K. Qiao, D. Tomida and C. Yokoyama, Catal. Commun., 2008, 9, 1383–1388 CrossRef CAS.
- Z. Wu, Z. Li, G. Wu, L. Wang, S. Lu, L. Wang, H. Wan and G. Guan, Ind. Eng. Chem. Res., 2014, 53, 3040–3046 CrossRef CAS.
- H. Tavakol and F. Keshavarzipour, Appl. Organomet. Chem., 2017, 31, e3811 CrossRef.
- T. T. Nguyen, N.-P. Thi Le, T. T. Nguyen and P. H. Tran, RSC Adv., 2019, 9, 38148–38153 RSC.
Footnote |
† Electronic supplementary information (ESI) available. See DOI: 10.1039/d0ra00773k |
|
This journal is © The Royal Society of Chemistry 2020 |
Click here to see how this site uses Cookies. View our privacy policy here.