DOI:
10.1039/C9RA04320A
(Paper)
RSC Adv., 2019,
9, 28038-28052
Immobilized copper-layered nickel ferrite on acid-activated montmorillonite, [(NiFe2O4@Cu)(H+-Mont)], as a superior magnetic nanocatalyst for the green synthesis of xanthene derivatives
Received
9th June 2019
, Accepted 22nd August 2019
First published on 6th September 2019
Abstract
In this study, the immobilization of copper-layered nickel ferrite on the surface and in the cavities of acid-activated montmorillonite (H+-Mont) was investigated. In this context, magnetic nanoparticles (MNPs) of NiFe2O4 as the prime magnetic cores were prepared. Next, through the reduction of Cu2+ ions with sodium borohydride, the nanoparticles of Cu0 were immobilized on the nanocore-surface of NiFe2O4, and the constituent NiFe2O4@Cu MNPs were obtained. Moreover, through the activation of montmorillonite K10 (Mont K10) with HCl (4 M) under controlled conditions, the H+-Mont constituent was prepared. The nanostructured NiFe2O4@Cu was then intercalated within the interlayers and on the external surface of the H+-Mont constituent to afford the novel magnetic nanocomposite (NiFe2O4@Cu)(H+-Mont). The prepared clay nanocomposite was characterized using FTIR spectroscopy, SEM, EDX, XRD, VSM and BET analyses. The obtained results showed that through acid-activation, the stacked-sheet structure of Mont K10 was exfoliated to tiny segments, leading to a significant increase in the surface area and total pore volume of the H+-Mont constituent as compared to those of montmorillonite alone. SEM analysis also exhibited that the dispersion of NiFe2O4@Cu MNPs in the interlayers and on the external surface of acid-activated montmorillonite was carried out successfully, and the nanoparticle sizes were distributed in the range of 15–25 nm. The BET surface analysis also indicated that through the immobilization of NiFe2O4@Cu MNPs, the surface area and total pore volume of the H+-Mont system were decreased. The catalytic activity of (NiFe2O4@Cu)(H+-Mont) was further studied towards the synthesis of substituted 13-aryl-5H-dibenzo[b,i]xanthene-5,7,12,14(13H) tetraones 3(a–k) and 3,3,6,6-tetramethyl-9-aryl-3,4,5,6,7,9-hexahydro-1H-xanthene-1,8(2H) diones 5(a–k) via the pseudo-one-pot three-component cyclocondensation of 2-hydroxy-1,4-naphthoquinone (Lawsone)/dimedone and aromatic aldehydes in a mixture of H2O–EtOH (1
:
1 mL) as a green solvent at 80–90 °C. The (NiFe2O4@Cu)(H+-Mont) MNPs can be easily separated from the reaction mixture by an external magnetic field and reused for seven consecutive cycles without significant loss of catalytic activity.
1. Introduction
Among O-containing heterocyclic compounds, xanthene derivatives are very important. These materials have attracted significant attention of many pharmacologists and synthetic chemists due to their broad spectrum of biological properties such as insecticidal, antifungal and urease activity,1 analgesic,2 antiinflammatory,2 antibacterial,3 antioxidant,4 and antiproliferative activity,5 trypanothione reductase (TryR) inhibition,6 chloroquine (CQ) potentiation,6 and antimalarial6 and anticancer activity.7 Moreover, some xanthene materials have been used as antagonists for paralyzing the action of zoxalamine8 and dyes,9–11 in laser technology,12 as pH-sensitive fluorescent agents13 and as bactericides in agriculture.14 These capabilities indicate the significant impact of xanthenes as the source of valuable drugs and rationalize the immense interest of numerous researchers towards their synthesis; a literature review has shown that using Fe3O4,15 ZrO2,16 silica sulfuric acid,17 (HPO3)n,18 HOAc,19 HClO4/SiO2,20 PPA/SiO2,20 SbCl3/SiO2,21 silica chloride,22 NaHSO4·SiO2,22 FeCl3/SiO2,23 InCl3,18 InCl3·4H2O/ionic liquid,24 In(OTf)3,25 SO42−/TiO2,26 Fe3O4@SiO2@SO3H,27 Fe3O4@TiO2@SO3H,28 ZrO2@SO3H,29 n-Bu4HSO4,30 [Hmim]TFA,31 p-dodecylbenzenesulfonic acid,32 p-dodecylbenzenesulfonic acid/ultrasound,33 Dowex-50W,34 amberlyst-15,35 montmorillonite K10,36 Fe3+-montmorillonite,37 1,1,3,3-N,N,N′,N′-tetramethylguanidinium trifluoroacetate/TFA,38 Et3(PhCH2)NBr,39 TMSCl,40 DABCO,41 CuI/poly(4-vinylpyridine),42 graphene oxide-incorporated strontium NPs,43 choline chloride/itaconic acid,44 (NH4)2HPO4,45 and polyaniline-p-toluenesulfonate46 1,8-dioxo-octahydroxanthenes have been prepared. In this context, some procedures involving Dowex-50W,34 1,1,3,3-N,N,N′,N′-tetramethylguanidinium trifluoroacetate/TFA,38 graphene oxide-incorporated strontium NPs,43 choline chloride/itaconic acid,44 [Msim]Cl,47 [Hmim][HSO4],47 [Et3N–SO3H]Cl,47 [Et3NH][HSO4],47 H2SO4,48 [Bmim][HSO4],48 [Bmim][BF4],49 N-sulfonic acid poly(4-vinylpyridinium) hydrogen sulfate,50 p-toluene sulfonic acid,51 amberlyst-15,52 and FeCl3·6H2O53 have also been reported for the preparation of 5H-dibenzo[b,i]xanthene tetraone materials. Aligned with the manifold capabilities of xanthene derivatives, therefore, the development of simple, efficient and clean synthetic protocols using green and highly reactive environmental benign catalysts is still needed.
Previously reported studies indicate the usefulness of Cu nanoparticles because of their low cost, high thermal and electrical conductivity, antifungal and antibacterial properties, and catalytic activity in organic synthesis; Cu is the most commonly investigated transition metal elements.54–59 In spite of the great convenience of Cu NPs, however, they have a strong tendency to agglomerate as well as a high affinity to react with air oxygen. These characteristics extensively diminish the surface areas and catalytic activities of copper nanoparticles. In order to overcome the mentioned drawbacks, the immobilization of Cu NPs on the surface of solid supports, especially magnetically nanoparticles (MNPs) of metal oxides, may be a prime choice. Among the various magnetic metal oxides, NiFe2O4 MNPs have attracted the attention of scientists due to their excellent magnetic, physical and electrical properties and high thermal stability (up to 900 °C) as well as their usefulness in drug delivery, ferrofluids, pigments, microwave devices, gas sensors and catalysts.60–64 In this area, the immobilization of copper nanoparticles on nickel ferrite (NiFe2O4@Cu) was successfully reported for the efficient reduction of nitroarenes to arylamines with NaBH4.65 Observation of the results reveals that because of the synergic influences of copper element and the core magnetic material, this type of immobilization dramatically accelerates the rates of reduction reactions. Moreover, feasible and efficient separation of the applied catalyst system from the reaction mixture can be carried out using an external magnetic field.
Clay minerals of the smectite group, such as montmorillonite K10 (Mont K10), are considered to be ecofriendly and suitable solid supports on which metal nanoparticles can be stabilized in the interlamellar spaces.66–68 Mont K10 is a stacked-sheet clay mineral that belongs to the family of 2
:
1 phyllosilicates. It is composed of one sandwiched-Al3+ octahedral sheet between two Si4+ tetrahedral sheets69 and has several advantages in terms of high surface area, swelling, cation exchange ability, low cost, ease of handling and non-corrosiveness.70 This micro/mesoporous material, in both its natural and modified forms, possesses both Brønsted and Lewis acid characteristics. Although montmorillonite K10 possesses inherent acidity, further activation of montmorillonite with strong acids such as HCl can exfoliate the adjacent sheets to tiny segments, leading to dramatic increases in surface area and Brønsted acidity as well as the generation of numerous pores with micro/meso dimensions.71
A literature review shows that the synthesis of xanthene materials catalyzed by copper nanoparticles has not yet been investigated. Therefore, in line with the outlined strategies and in continuation of our research program towards the synthesis and application of magnetic nanocatalysts,65,72–76 herein, we wish to introduce the immobilization of copper-layered nickel ferrite on acid-activated montmorillonite, (NiFe2O4@Cu)(H+-Mont) (Fig. 1), with the aims of (i) combining the catalytic activity of the copper-layered nickel ferrite constituent with the Brønsted and Lewis acidity of the H+-Mont clay mineral, affording prominent catalytic activity of the final catalyst system and (ii) avoiding aggregation and improving the stability of the copper nanoparticles as well as the shelf life capability of the NiFe2O4@Cu MNPs via immobilization in the interlamellar spaces of the clay mineral. Further examination indicated that the prepared nanostructured (NiFe2O4@Cu)(H+-Mont) exhibited excellent catalytic activity towards the one-pot Knoevenagel reaction of 2-hydroxy-1,4-naphthoquinone (Lawsone)/dimedone with aromatic aldehydes in a mixture of H2O–EtOH (1
:
1 mL) as a green solvent to afford 5H-dibenzo[b,i]xanthene tetraones and hexahydroxanthene diones (Fig. 2).
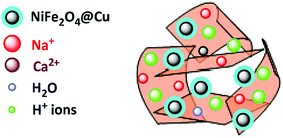 |
| Fig. 1 Magnetic nanoparticles of (NiFe2O4@Cu)(H+-Mont). | |
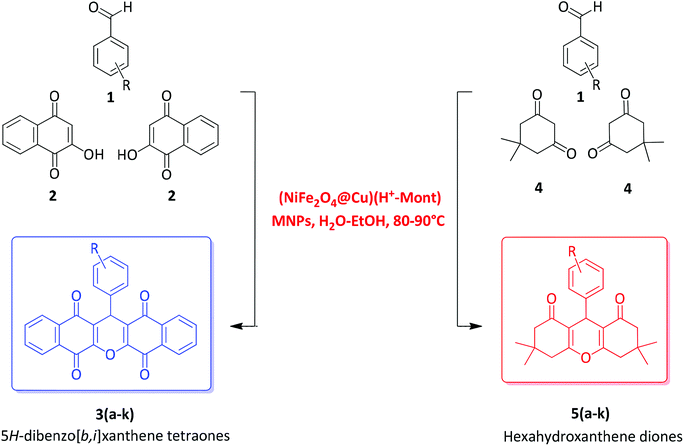 |
| Fig. 2 Synthesis of xanthene materials catalyzed by (NiFe2O4@Cu)(H+-Mont) MNPs. | |
2. Experimental
2.1. Instruments and reagents
All chemicals were purchased from chemical companies, were of the best quality and were used without further purification. 1H, 13C NMR and FT-IR spectra were recorded on 300 MHz Bruker Avance and Thermo Nicolet Nexus 670 spectrometers. Melting points were recorded on an Electrothermal 9100 melting point apparatus and are uncorrected. TLC was applied to monitor the reactions over silica gel-coated 60 F254 aluminum sheets. The magnetic properties of the nanocatalysts were measured using vibration sample magnetometer (VSM, Meghnatis Daghigh Kavir Co., Iran) analysis under an external magnetic field of up to 20 kOe. The morphologies and size distributions of the nanoparticles were examined by scanning electron microscopy (SEM) using an FESEM-TESCAN MIRA3 instrument. X-ray diffraction (XRD) measurements were carried out on X'PertPro Panalytical diffractometer (Holland) at 40 kV and 30 mA with Cu Kα radiation (λ = 1.5418 Å). Signal data were recorded from 2θ = 10° to 80° with a step interval of 0.05°.
2.2. Synthesis of NiFe2O4 MNPs
A mixture of Ni(OAc)2·4H2O, Fe(NO3)3·9H2O, NaOH and NaCl in a molar ratio of 1
:
2
:
8
:
2, respectively, was ground for 60 min in the absence of solvent. The reaction was exothermic and was accompanied by the release of heat. When the reaction was complete, the mixture was washed several times with deionized water to remove NaCl and residual contaminants, followed by drying at 80 °C for 10 h. The resulting powder was calcinated at 900 °C for 2 h to obtain magnetic nanoparticles of NiFe2O4.65
2.3. Synthesis of NiFe2O4@Cu MNPs
A mixture of NiFe2O4 (1 g) containing an aqueous solution of CuCl2·2H2O (0.25 g in 30 mL H2O) was prepared. The resulting mixture was stirred for 30 min at room temperature; NaBH4 (0.11 g in 30 mL H2O) was then added dropwise over 20 min (N2 atmosphere). The mixture was then stirred for 2 h. After that, the magnetic nanoparticles of NiFe2O4@Cu were separated by magnetic decantation and then washed with ethanol and deionized water. Drying under air atmosphere afforded NiFe2O4@Cu MNPs.65
2.4. Preparation of homoionic Na+-exchanged montmorillonite (Na+-Mont)
To a beaker containing an aqueous solution of NaCl (2 M, 200 mL), montmorillonite K10 (10 g) was added, and the mixture was stirred vigorously for 2 h at room temperature. The mixture was then allowed to settle, and the aqueous phase was decanted. Then, the solid residue was again charged with an aqueous solution of NaCl (2 M, 200 mL). The procedure was repeated 3 more times. Finally, the aqueous phase was decanted and the solid residue was washed frequently with distilled water until the conductivity of the liquid filtrate reached the conductivity of distilled water. The resulting product was then dried at 50 °C in an oven to afford homoionic Na+-exchanged montmorillonite (Na+-Mont).74
2.5. Preparation of acid-activated montmorillonite (H+-Mont)
To a round-bottom flask containing an aqueous solution of HCl (4 M, 100 mL), Na+-Mont (5 g) was added. The resulting dispersion was stirred under reflux conditions for 2 h. After cooling, the mixture was filtered, and the resulting montmorillonite was washed frequently with distilled water to remove any Cl− ions from the clay mineral (tested with AgNO3). The acid-activated clay was collected and dried in an oven (50 °C) to afford acid-activated montmorillonite (H+-Mont).76
2.6. Synthesis of (NiFe2O4@Cu)(H+-Mont) MNPs
Individual suspensions of H+-Mont (4.2 g) in deionized water (200 mL; the pH value of the resulting suspension was adjusted to ∼5 by 3 wt% HCl) and NiFe2O4@Cu (2.1 g) in deionized water (200 mL; the pH value of the resulting suspension was adjusted to ∼9 by 3 wt% aqueous ammonia) were irradiated by ultrasound for 30 min. The two suspensions were combined, followed by stirring for 2 h. The clay nanocomposite, (NiFe2O4@Cu)(H+-Mont), was separated by magnetic decantation and then washed with EtOH. Drying under air atmosphere afforded the final product in a weight ratio of 2
:
1 for NiFe2O4@Cu
:
H+-Mont.
2.7. Determining the cation-exchange capacity (CEC) of the clay minerals
The cation-exchange capacities (CEC) of the clay minerals were measured through a reported procedure.77 In this context, a clay mineral (such as Mont K10) (0.5 g) was dispersed in a standard alcoholic solution of CaCl2 (10 mL, 0.05 M) and the prepared mixture was stirred at room temperature for 24 h. The suspension was filtered, washed with EtOH (20 mL) and dried at room temperature for 12 h. The Ca2+-exchanged clay mineral was then transferred to a volumetric flask (250 mL). By adding distilled water, the volume of the flask was increased to the standard limit (250 mL). The amount of Ca2+ was determined by titration with a standard solution of EDTA. The difference in the concentrations of Ca2+ before and after cation-exchange processing afforded the CEC (meq. g−1) of the clay mineral.
2.8. General procedure for the synthesis of 13-aryl-5H-dibenzo[b,i]xanthene-5,7,12,14(13H)-tetraones
In a round-bottom flask (10 mL) equipped with a magnetic stirrer, a mixture of 2-hydroxy-1,4-naphthoquinone (2, 2 mmol), aromatic aldehyde (1, 1 mmol) and (NiFe2O4@Cu)(H+-Mont) (20 mg) in H2O–EtOH (1
:
1 mL) was prepared. The resulting mixture was stirred at 80 °C for a particular time, as mentioned in Table 4. The progress of the reaction was monitored by TLC (eluent, n-hexane/EtOAc: 10/4). After completion of the reaction, EtOAc (3 mL) was added, and stirring of the reaction mixture was continued for 5 min. The nanocatalyst was then separated from the reaction mixture by an external magnetic field. After that, the organic layer was separated from the aqueous solution. Evaporation of the solvent under reduced pressure afforded the crude 5H-dibenzo[b,i]xanthene tetraone. Further purification could be carried out by recrystallization from hot EtOH, affording the products 3(a–k) in 70% to 98% yields. Selected spectral data for the products are given as follows:
2.8.1. 13-Phenyl-5H-dibenzo[b,i]xanthene-5,7,12,14(13H)-tetraone (3a). FT-IR (KBr, ν cm−1): 3346, 1651, 1594, 1360, 1267, 1043, 725; 1H NMR (300 MHz, CDCl3): δ (ppm) 6.26 (s, 1H, CH), 7.21–7.34 (s, 4H, Ar), 7.65–7.79 (m, 4H, Ar), 8.08–8.19 (m, 5H, Ar); 13C NMR (75 MHz, CDCl3): δ (ppm) 32.2, 122.6, 129.6, 132.7, 137.9, 154.8, 181.3, 184.7.
2.8.2. 13-(2-Chlorophenyl)-5H-dibenzo[b,i]xanthene-5,7,12,14(13H)-tetraone (3b). FT-IR (KBr, ν cm−1): 3267, 1638, 1591, 1464, 1354, 1267, 1035, 971, 725, 643; 1H NMR (300 MHz, CDCl3): δ (ppm) 6.09 (s, 1H, CH), 7.12–7.25 (m, 2H, Ar), 7.28–7.38 (m, 2H, Ar), 7.74–7.86 (m, 4H, Ar), 7.86–8.06 (m, 4H, Ar).
2.8.3. 5H-Dibenzo[b,i]xanthene-5,7,12,14(13H)-tetraone (3d). FT-IR (KBr, ν cm−1): 3071, 1676, 1602, 1351, 1263, 1209, 968, 942, 770, 735; 1H NMR (300 MHz, CDCl3): δ (ppm) 2.49 (s, 2H, CH2), 7.71–7.85 (m, 4H, Ar), 7.95–7.97 (m, 4H, Ar).
2.8.4. 13-(4-Methoxyphenyl)-5H-dibenzo[b,i]xanthene-5,7,12,14(13H)-tetraone (3e). FT-IR (KBr, ν cm−1): 3345, 3071, 2932, 1654, 1594, 1468, 1361, 1275, 1041, 730, 464; 1H NMR (300 MHz, CDCl3): δ (ppm) 3.77 (s, 3H, OCH3), 6.35 (s, 1H, CH), 6.84–6.94 (m, 2H, Ar), 7.11–7.18 (m, 1H, Ar), 7.21–7.29 (m, 1H, Ar), 7.64–7.80 (m, 4H, Ar), 8.04–8.15 (m, 4H, Ar); 13C NMR (75 MHz, CDCl3): δ (ppm) 33.12, 54.1, 122.8, 125.5, 126.2, 126.6, 128.1, 128.6, 129.5, 132.9, 135.1, 154.1, 157.4, 181.5, 184.1.
2.8.5. 13-(p-Tolyl)-5H-dibenzo[b,i]xanthene-5,7,12,14(13H)-tetraone (3g). FT-IR (KBr, ν cm−1): 3174, 3013, 1638, 1585, 1382, 1347, 1275, 1218, 973, 880, 736, 666; 1H NMR (300 MHz, CDCl3): δ (ppm) 3.79 (s, 3H, CH3), 6.18 (s, 1H, CH), 6.83 (d, 2H, Ar), 7.21 (d, 2H, Ar), 7.65–7.79 (m, 4H, Ar), 8.07–8.15 (m, 4H, Ar); 13C NMR (75 MHz, CDCl3): δ (ppm) 36.9, 113.8, 122.9, 126.3, 127.2, 128.1, 129.6, 129.8, 132.7, 132.2, 135.0, 154.7, 158.4, 181.3, 184.7.
2.8.6. 13-(2-Hydroxyphenyl)-5H-dibenzo[b,i]xanthene-5,7,12,14(13H)-tetraone (3h). FT-IR (KBr, ν cm−1): 3222, 1641, 1589, 1480, 1354, 1237, 1041, 975, 728; 1H NMR (300 MHz, DMSO-d6): δ (ppm) 5.74 (s, 1H, CH), 7.08–7.29 (m, 4H, Ar), 7.70–7.98 (m, 8H, Ar), 11.48 (bs, 1H, OH).
2.8.7. 13-(4-Nitrophenyl)-5H-dibenzo[b,i]xanthene-5,7,12,14(13H)-tetraone (3i). FT-IR (KBr, ν cm−1): 3330, 2923, 2859, 1654, 1592, 1519, 1346, 1265, 1038, 724; 1H NMR (300 MHz, CDCl3): δ (ppm) 6.38 (s, 1H, CH), 7.31–7.36 (m, 1H, Ar), 7.44–7.51 (m, 1H, Ar), 7.71–7.84 (m, 5H, Ar), 8.08–8.18 (m, 5H, Ar).
2.8.8. 13-(3-Nitrophenyl)-5H-dibenzo[b,i]xanthene-5,7,12,14(13H)-tetraone (3j). FT-IR (KBr, ν cm−1): 3337, 2923, 1654, 1594, 1526, 1349, 1267, 1035, 726; 1H NMR (300 MHz, CDCl3): δ (ppm) 6.25 (s, 1H, CH), 7.42–7.48 (m, 1H, Ar), 7.63–7.84 (m, 6H, Ar), 8.10–8.19 (m, 5H, Ar).
2.8.9. 13-(4-Pyridyl)-5H-dibenzo[b,i]xanthene-5,7,12,14(13H)-tetraone (3k). FT-IR (KBr, ν cm−1): 3463, 2918, 2852, 1671, 1597, 1499, 1351, 1268, 1159, 944, 803, 724, 574; 1H NMR (300 MHz, CDCl3): δ (ppm) 2.94 (s, 1H, CH), 6.78 (bs, 2H, Pyridyl), 7.64–8.01 (m, 8H, Ar), 8.62 (d, 2H, Pyridyl).
2.9. General procedure for the synthesis of 3,3,6,6-tetramethyl-9-aryl-3,4,5,6,7,9-hexahydro-1H-xanthene-1,8(2H)-diones
Synthesis of hexahydroxanthene diones was carried out using the procedure described in Section 2.8 with dimedone (4, 2 mmol) at 90 °C. Selected spectral data for the products are given as follows:
2.9.1. 3,3,6,6-Tetramethyl-9-phenyl-3,4,5,6,7,9-hexahydro-1H-xanthene-1,8(2H)-dione (5a). FT-IR (KBr, ν cm−1): 2949, 1662, 1650, 1363, 1350, 1197, 1163, 1143, 997, 700; 1H NMR (300 MHz, CDCl3): δ (ppm) 0.99 (s, 6H, 2Me), 1.10 (s, 6H, 2Me), 2.13–2.23 (d, 4H, 2CH2), 2.43 (s, 4H, 2CH2), 4.69 (s, 1H, CH), 6.98–7.31 (m, 5H, Ar).
2.9.2. 9-(2-Chlorophenyl)-3,3,6,6-tetramethyl-3,4,5,6,7,9-hexahydro-1H-xanthene-1,8(2H)-dione (5b). FT-IR (KBr, ν cm−1): 2952, 2636, 1723, 1628, 1381, 1241, 838, 757; 1H NMR (300 MHz, CDCl3): δ (ppm) 1.02 (s, 6H, 2Me), 1.10 (s, 6H, 2Me), 2.18 (s, 4H, 2CH2), 2.45 (s, 4H, 2CH2), 5.01 (s, 1H, CH), 7.00–7.26 (m, 4H, Ar).
2.9.3. 9-(4-Chlorophenyl)-3,3,6,6-tetramethyl-3,4,5,6,7,9-hexahydro-1H-xanthene-1,8(2H)-dione (5c). FT-IR (KBr, ν cm−1): 2953, 2881, 1665, 1472, 1388, 1195, 1153, 1010, 834, 759; 1H NMR (300 MHz, CDCl3): δ (ppm) 1.00 (s, 6H, 2Me), 1.11 (s, 6H, 2Me), 2.14–2.28 (s, 4H, 2CH2), 2.47 (s, 4H, 2CH2), 4.72 (s, 1H, CH), 7.17–7.27 (m, 4H, Ar).
2.9.4. 9-(2-Methoxyphenyl)-3,3,6,6-tetramethyl-3,4,5,6,7,9-hexahydro-1H-xanthene-1,8(2H)-dione (5h). FT-IR (KBr, ν cm−1): 2951, 1724, 1661, 1487, 1368, 1242, 1195, 1143, 831, 759; 1H NMR (300 MHz, CDCl3): δ (ppm) 0.91 (s, 6H, 2Me), 1.04 (s, 6H, 2Me), 2.12 (s, 4H, 2CH2), 2.37 (s, 4H, 2CH2), 3.72 (s, 3H, OCH3), 4.82 (s, 1H, CH), 6.82–7.35 (m, 3H, Ar).
2.9.5. 9-(2-Hydroxyphenyl)-3,3,6,6-tetramethyl-3,4,5,6,7,9-hexahydro-1H-xanthene-1,8(2H)-dione (5i). FT-IR (KBr, ν cm−1): 2951, 2829, 1721, 1627, 1379, 1239, 1161, 1026, 877, 754; 1H NMR (300 MHz, CDCl3): δ (ppm) 1.01 (s, 6H, 2Me), 1.04 (s, 6H, 2Me), 1.96 (s, 2H, CH2), 2.34–2.38 (s, 4H, 2CH2), 2.34–2.64 (s, 4H, 2CH2), 4.68 (s, 1H, CH), 7.01–7.27 (m, 4H, Ar), 10.47 (bs, 1H, OH).
2.9.6. 3,3,6,6-Tetramethyl-9-(4-nitrophenyl)-3,4,5,6,7,9-hexahydro-1H-xanthene-1,8(2H)-dione (5j). FT-IR (KBr, ν cm−1): 2950, 2875, 2631, 1599, 1514, 1363, 1259, 1155, 851; 1H NMR (300 MHz, CDCl3): δ (ppm) 0.81 (s, 6H, 2Me), 0.95 (s, 6H, 2Me), 2.01–2.16 (s, 4H, 2CH2), 2.47 (s, 4H, 2CH2), 4.54 (s, 1H, CH), 7.73 (s, 2H, Ar), 8.01 (s, 2H, Ar).
2.9.7. 3,3,6,6-Tetramethyl-9-(3-nitrophenyl)-3,4,5,6,7,9-hexahydro-1H-xanthene-1,8(2H)-dione (5k). FT-IR (KBr, ν cm−1): 2954, 2882, 1668, 1600, 1527, 1456, 1359, 1192, 1145, 752; 1H NMR (300 MHz, CDCl3): δ (ppm) 0.99 (s, 6H, 2Me), 1.11 (s, 6H, 2Me), 2.13–2.28 (s, 4H, 2CH2), 2.51 (s, 4H, 2CH2), 4.83 (s, 1H, CH), 7.37–8.03 (m, 4H, Ar).
3. Results and discussion
3.1. Synthesis and characterization of (NiFe2O4@Cu)(H+-Mont) MNPs
Synthesis of the (NiFe2O4@Cu)(H+-Mont) MNPs was carried out through a seven-step procedure: (i) swelling (hydration) of montmorillonite K10 by vigorous stirring of the clay mineral in distilled water. Due to this process, Mont K10 can absorb water between its interlamellar spaces; hence, the stacked sheets of the clay mineral move apart. The swelling expands the surface area of montmorillonite and exposes the cations of the interlayers to contribute Brønsted and Lewis acidity character;70 (ii) stirring of the swelled montmorillonite in an aqueous solution of NaCl to afford homoionic Na+-exchanged montmorillonite. Through simple ion-exchange, many cations of the interlayers in montmorillonite K10 are exchanged with Na+ ions. The diffusion of Na+ ions endows the clay mineral with a high capacity for exchanging Na+ ions with various guest species (transition metals, complexes and H+ ions). In other words, the ions are encapsulated in the interlamellar spaces; therefore, the acidity (Brønsted and Lewis) of the clay mineral can be changed for different purposes; (iii) stirring of the homoionic Na+-exchanged Mont in an aqueous solution of HCl to afford acid-activated Mont; (iv) preparation of NiFe2O4 MNPs via solid state grinding of Ni(OAc)2·4H2O and Fe(NO3)3·9H2O in the presence of NaOH; (v) mixing of NiFe2O4 MNPs with an aqueous solution of CuCl2·2H2O; (vi) reduction of Cu2+ ions to Cu0 with NaBH4 to afford NiFe2O4@Cu MNPs; and finally, (vii) preparation of (NiFe2O4@Cu)(H+-Mont) MNPs via simple mixing of the individual sonicated suspensions of NiFe2O4@Cu and H+-Mont constituents (Fig. 3). In this context, through the electrostatic attraction of NiFe2O4@Cu (positive charge) to H+-Mont (negative charge) compartments and the repulsion within the H+-Mont layers/segments, nanosegments of NiFe2O4@Cu are dispersed on the surface and in the interlamellar spaces of the H+-Mont constituent.
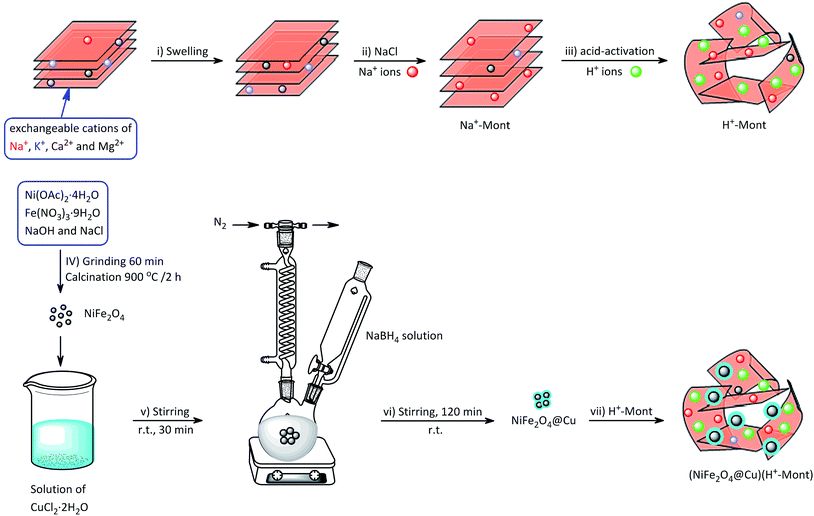 |
| Fig. 3 Preparation of the (NiFe2O4@Cu)(H+-Mont) MNPs. | |
The concentration of exchangeable cations in a clay mineral is called the cation exchange capacity (CEC), and it is measured in milli-equivalents per 100 g of dried clay.77 The measured CEC results for the Mont K10 and Na+-Mont clays were 85 and 110 meq. g−1, respectively, representing the successful replacement of Na+ ions instead of other cations in the interlamellar spaces of the clay minerals.
3.2. Characterization of the (NiFe2O4@Cu)(H+-Mont) MNPs
3.2.1. XRD analysis. The phase purities and structural elucidation of the NiFe2O4, NiFe2O4@Cu, Mont K10, Na+-Mont, H+-Mont and (NiFe2O4@Cu)(H+-Mont) systems were studied using wide-angle X-ray diffraction analysis (Fig. 4 and 5). In the diffractogram of NiFe2O4 (Fig. 4a), the peaks at 2θ = 30.40°, 35.77°, 37.40°, 43.51°, 54.21°, 57.60°, 63.11°, 71.90°, 75.20° and 76.05° correspond to the (2 2 0), (3 1 1), (2 2 2), (4 0 0), (4 2 2), (5 1 1), (4 4 0), (6 2 0), (5 3 3) and (4 4 4) reflection planes of standard cubic spinel NiFe2O4 (JCPDS 54-964), respectively, showing the high phase purity and crystallinity of the prepared sample. In this context, the XRD pattern of NiFe2O4@Cu MNPs (Fig. 4b) shows that in addition to the reflection planes of NiFe2O4, the peaks present at 2θ = 27.40° and 48.02° can be attributed to the reflection planes of copper species. The XRD pattern of montmorillonite K10 (Fig. 5a) also shows that along with hkl and two-dimensional hk reflections, the commercial clay mineral contains impurities of quartz, cristobalite and feldspar. Moreover, analysis of the pattern of homoionic Na+-exchanged montmorillonite (Fig. 5b) reveals that the intensity of the reflection peaks notably increased. This increase is attributed to the diffusion of Na+ ions in the interlamellar spaces of the clay mineral via ion-exchange processing.78,79 Despite this, the XRD pattern of the H+-Mont (Fig. 5c) system shows a decrease in the intensity of the reflection peaks. This can be attributed to exfoliation/destruction of layers in the Na+-Mont clay during HCl-activation.80 In continuation, the XRD pattern of (NiFe2O4@Cu)(H+-Mont) (Fig. 5e) shows that upon combining the NiFe2O4@Cu and H+-Mont constituents, no structural changes occurred in the clay matrix, and the pattern of the nanocomposite contains the characteristic peaks of both compartments.
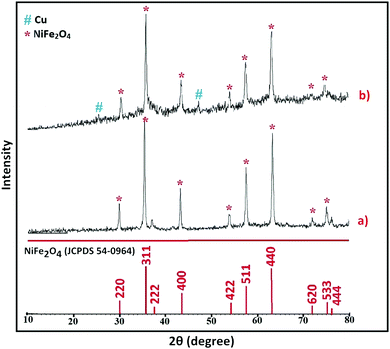 |
| Fig. 4 XRD patterns of (a) NiFe2O4 and (b) the NiFe2O4@Cu MNPs. | |
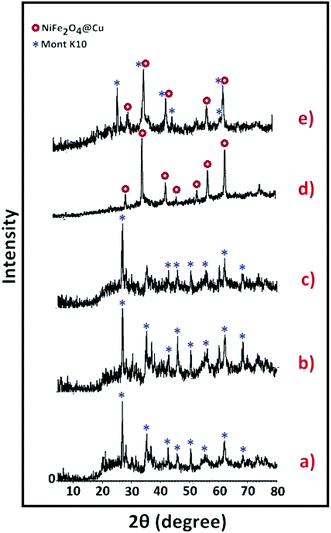 |
| Fig. 5 XRD patterns of (a) Mont K10, (b) Na+-Mont, (c) H+-Mont, (d) NiFe2O4@Cu and (e) (NiFe2O4@Cu)(H+-Mont). | |
3.2.2. SEM analysis. The morphologies and size distributions of the particles in the prepared NiFe2O4, NiFe2O4@Cu, Mont K10, H+-Mont and (NiFe2O4@Cu)(H+-Mont) systems were investigated by scanning electron microscopy (SEM). The SEM images of NiFe2O4 (Fig. 6a and b) and NiFe2O4@Cu (Fig. 6c and d) present that the morphologies of the two MNPs are quite different: NiFe2O4 is composed of polygon/irregular segments, resulting in surfaces with low porosity and a size distribution of the particles in the range of 10 to 25 nm. The SEM images of NiFe2O4@Cu show that through the immobilization of copper nanoparticles on the surface of NiFe2O4, the porosity of the surface was extensively increased, and the nanocomposite is constituted of agglomerated tiny spherical segments. Moreover, the particle sizes are distributed in the range of 10 to 40 nm.
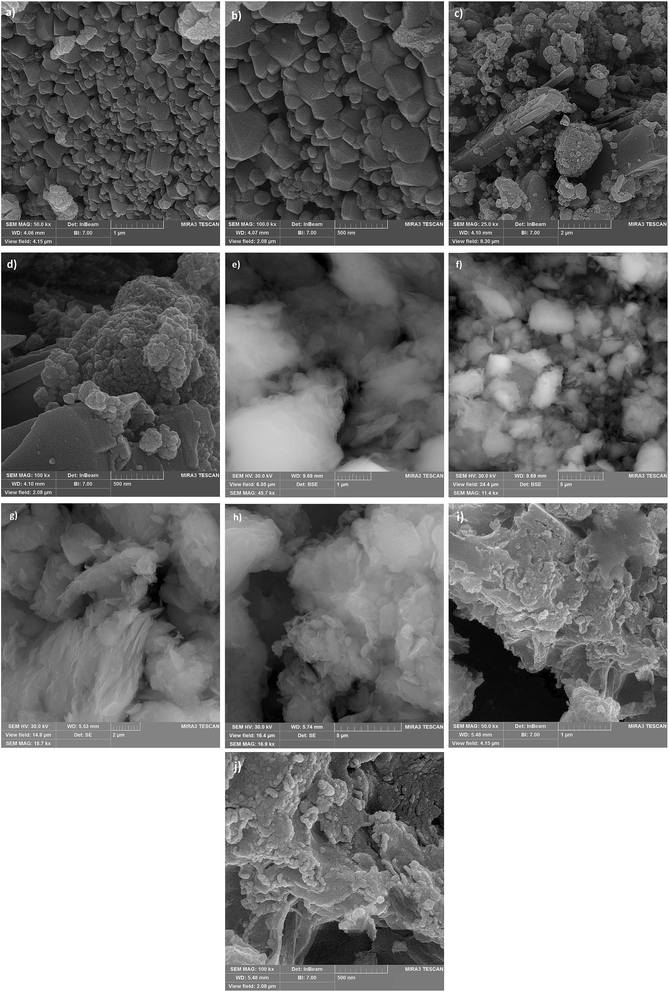 |
| Fig. 6 SEM images of NiFe2O4 (a and b), NiFe2O4@Cu (c and d), Mont K10 (e and f), H+-Mont (g and h) and (NiFe2O4@Cu)(H+-Mont) (i and j). | |
SEM images of Mont K10 and acid-activated Mont are also illustrated in Fig. 6e–h. Comparison of the images shows that through the acid-activation, the stacked sheets of Mont K10 were exfoliated into tiny segments. This phenomenon can be interpreted by the major elimination of Al3+ and Fe2+/3+ contents from the octahedral sites when the activation of montmorillonite with HCl was carried out. Moreover, through the elimination of Al3+ and Fe2+/3+ ions from the interlayers, numerous pores on the surface and internal sheets of montmorillonite were generated, increasing the surface area of the H+-Mont system. In this context, the depicted SEM images of the (NiFe2O4@Cu)(H+-Mont) MNPs (Fig. 6i and j) present that the nanocatalyst is composed of stacked-sheet structures containing agglomerated rough/irregular segments. The sizes of the particles in the (NiFe2O4@Cu)(H+-Mont) system are distributed in the range of 18 to 25 nm. The SEM analysis also exhibited that anchoring of the (NiFe2O4@Cu) constituent on the surface of the clay compartment was carried out successfully, leading to a decrease of the surface porosity in comparison to that of the NiFe2O4@Cu MNPs.
3.2.3. N2 adsorption–desorption analysis. Nitrogen adsorption–desorption analysis is commonly utilized to study the specific surface areas of nanocomposite systems. In addition, information regarding the pore sizes and total pore volumes of nanomaterials is accessible using this analysis. In this area, Fig. 7 shows the N2 adsorption–desorption profiles for the Mont K10, H+-Mont and (NiFe2O4@Cu)(H+-Mont) systems. Based on BDDT IUPAC classification, the shapes of the isotherms for all samples are closer to that of isotherm IV, with H3 hysteresis loops in the desorption profiles. This type of isotherm is characteristic of micro/mesoporous materials.81
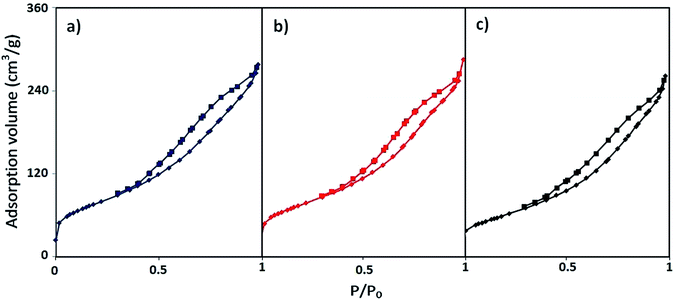 |
| Fig. 7 N2 adsorption–desorption isotherms of the (a) Mont K10, (b) H+-Mont and (c) (NiFe2O4@Cu)(H+-Mont) systems. | |
In this context, the surface properties of the Mont K10, H+-Mont, (NiFe2O4@Cu)(H+-Mont) and NiFe2O4@Cu systems, including SBET (m2 g−1), Vm (cm3 g−1), average pore diameter (nm), Vp (cm3 g−1) and total pore volume (cm3 g−1), are summarized in Table 1. Investigation of the results indicates that the surface area and total pore volume of H+-Mont notably increased versus those of Mont K10 alone. This phenomenon is attributed to the exfoliation of stacked sheets to tiny segments and the formation of numerous new pores, affording increases of the pore volume and specific surface area.82,83 In contrast, anchoring NiFe2O4@Cu MNPs on the H+-Mont compartments decreases the surface area and total pore volume, while the average pore radius of the particles was found to increase. This is attributed to physical occupancy of some of the pores in montmorillonite K10 by NiFe2O4@Cu MNPs.84
Table 1 Surface properties of the examined clay composite systems
Sample |
SBET (m2 g−1) |
Vm (cm3 g−1) |
Average pore diameter (nm) |
Vp (cm3 g−1) |
Total pore volume (cm3 g−1) |
Mont K10 |
250.11 |
51.835 |
6.427 |
0.4016 |
0.4298 |
H+-Mont |
280.52 |
50.313 |
6.7483 |
0.419 |
0.5081 |
(NiFe2O4@Cu)(H+-Mont) |
119.52 |
27.461 |
7.9242 |
0.2326 |
0.2368 |
NiFe2O4@Cu |
14.84 |
3.41 |
34.74 |
0.128 |
0.129 |
3.2.4. FT-IR analysis. FT-IR is a sensitive tool that was utilized to elucidate the structures as well as the functional groups of the Mont K10, H+-Mont and (NiFe2O4@Cu)(H+-Mont) materials (Fig. 8). The absorption band at 3620 cm−1 for Mont K10 is attributed to the vibration of hydroxyl groups bonded to Si4+, Al3+ or Mg2+ ions. The absorption bands at 3433 and 1635 cm−1 show the H–O–H stretching and bending vibrations of the adsorbed water in the interlayers of montmorillonite, and the bands at 522 and 464 cm−1 correspond to the bending vibrations of Si–O–Al and Si–O–Si, respectively.85–87 In this context, comparison of the FT-IR patterns of the Mont K10 and H+-Mont systems reveals that through the acid-activation of montmorillonite by HCl, the position of the strong band at 1054 cm−1 (showing the stretching vibration of Si–O in tetrahedral sites) shifted to 1080 cm−1. This fact demonstrates the successful ion-exchange processing of H+-Mont clay. In the case of (NiFe2O4@Cu)(H+-Mont), the stretching vibration of Si–O shifted to 1038 cm−1. This movement is attributed to dispersion of the NiFe2O4@Cu MNPs on the surface and in the interlamellar spaces of the clay constituent. In addition, the bands at 2926 and 2865 cm−1 confirmed the immobilization of NiFe2O4@Cu MNPs in the clay matrix through the conformational changes in the metal-linked-clay interactions.88–90
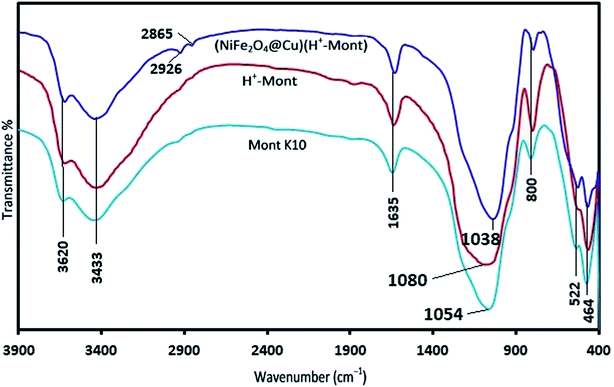 |
| Fig. 8 FT-IR spectra of the Mont K10, H+-Mont and (NiFe2O4@Cu)(H+-Mont) systems. | |
3.2.5. VSM analysis. Next, the magnetic behavior of NiFe2O4, NiFe2O4@Cu and the (NiFe2O4@Cu)(H+-Mont) MNPs was studied using vibrating sample magnetometer (VSM) analysis. The magnetization curves of the samples (Fig. 9) present nonlinear reversibility with small hysteresis loops. In addition, the s-shapes shown in the magnetization graphs are characteristic of soft ferromagnetic materials.91 The magnetization (Ms) values of NiFe2O4 (curve a) and NiFe2O4@Cu (curve b) were found to be 43.458 emu g−1 and 33.135 emu g−1, respectively. The decrease in the value of Ms for the NiFe2O4@Cu MNPs is attributed to the presence of diamagnetic copper metal. In this context, due to the existence of the non-magnetic clay mineral constituent, the saturation magnetization value of the (NiFe2O4@Cu)(H+-Mont) MNPs (curve c) notably decreased to 11.57 emu g−1. This level of magnetization (11.57 emu g−1) is still large enough for magnetic separation.
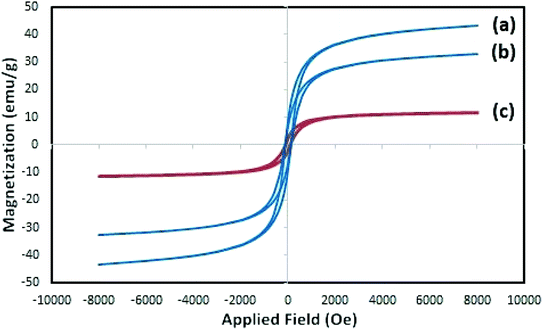 |
| Fig. 9 Magnetization curves of (a) NiFe2O4, (b) NiFe2O4@Cu and (c) the (NiFe2O4@Cu)(H+-Mont) MNPs. | |
3.3. Synthesis of xanthene derivatives catalyzed by (NiFe2O4@Cu)(H+-Mont) MNPs
After the successful synthesis and characterization of the (NiFe2O4@Cu)(H+-Mont) MNPs, the catalytic activity of the prepared nanocomposite was further investigated towards the tandem Knoevenagel–Michael reaction of aromatic aldehydes with 2-hydroxy-1,4-naphthoquinone (Lawsone).
The study was primarily carried out by optimizing the condensation reaction of 2-hydroxy-1,4-naphthoquinone (2 mmol) and 4-chlorobenzaldehyde (1 mmol) in the presence and absence of (NiFe2O4@Cu)(H+-Mont) MNPs under different conditions, including changes in the reaction solvent, amount of nanocatalyst and temperature. The results of this investigation are illustrated in Table 2. Observation of the results shows that in the absence of the nanocatalyst, the reaction did not show appropriate efficiency (entries 1 and 2). However, by adding a small amount of (NiFe2O4@Cu)(H+-Mont) MNPs, the rate of the condensation reaction was dramatically accelerated. The examinations also present that among the various solvents, a mixture of H2O–EtOH was the best choice. Moreover, utilizing 20 mg of the nanocatalyst per 1 mmol of 4-chlorobenzaldehyde in a mixture of H2O–EtOH (1
:
1 mL) at 80 °C were the requirements to afford 13-(4-chlorophenyl)-5H-dibenzo[b,i]xanthene-5,7,12,14(13H)-tetraone (3c) in 95% isolated yield (Table 2, entry 11), while the reaction was carried out with 100% conversion. Investigation of the results also exhibits that although decreasing the loading of the nanocatalyst from 20 mg to 10 mg decreased the yield of condensation reaction (entry 12), increasing the nanocatalyst from 20 mg to 30 mg also diminished the yield from 95% to 75% (entry 13). A possible explanation for the decrease of the yield (utilizing a larger amount of nanocatalyst) is encapsulation/environing of the starting materials by the nanocatalyst, followed by decreasing the inter-collision of the reactants to afford the final product. In summary, the conditions mentioned in entry 11 (Table 2) were selected as the optimum reaction conditions.
Table 2 Optimization experiments for the synthesis of 13-(4-chlorophenyl)-5H-dibenzo[b,i]xanthene-5,7,12,14(13H)-tetraone (3c) catalyzed by (NiFe2O4@Cu)(H+-Mont) MNPsa
Entry |
Nanocatalyst (mg) |
Solvent (2 mL) |
Temp. (°C) |
Time (min) |
Yieldb (%) |
The condensation reactions were carried out with 2-hydroxy-1,4-naphthoquinone (2 mmol) and 4-chlorobenzaldehyde (1 mmol). Isolated yield. |
1 |
— |
EtOH |
60 |
240 |
5 |
2 |
— |
H2O |
60 |
240 |
5 |
3 |
20 |
EtOH |
60 |
45 |
60 |
4 |
20 |
H2O |
60 |
30 |
70 |
5 |
20 |
EtOH–H2O (1 : 1) |
60 |
30 |
85 |
6 |
20 |
DMF |
60 |
120 |
40 |
7 |
20 |
EtOAc |
60 |
120 |
50 |
8 |
20 |
CH3CN |
60 |
120 |
55 |
9 |
20 |
Solvent-free |
60 |
120 |
60 |
10 |
20 |
EtOH–H2O (1 : 1) |
r.t. |
120 |
60 |
11 |
20 |
EtOH–H2O (1 : 1) |
80 |
20 |
95 |
12 |
10 |
EtOH–H2O (1 : 1) |
80 |
20 |
70 |
13 |
30 |
EtOH–H2O (1 : 1) |
80 |
120 |
75 |
In order to clarify the role of nanocatalyst in the synthesis of dibenzo[b,i]xanthene tetraone 3c, the catalytic activity of the (NiFe2O4@Cu)(H+-Mont) MNPs was compared to those of the potentially active species (Cu0 NPs, NiFe2O4, NiFe2O4@Cu, Mont K10, H+-Mont and Na+-Mont) under the optimized reaction conditions. The results in Table 3 show that performing the title reaction in the presence of Cu0 NPs, NiFe2O4@Cu and the modified montmorillonites led to poor yields of 3c. However, the immobilized NiFe2O4@Cu MNPs on acid-activated montmorillonite, (NiFe2O4@Cu)(H+-Mont), dramatically accelerated the rate of the reaction (Table 3, entry 7).
Table 3 Comparison of the catalytic activity of (NiFe2O4@Cu)(H+-Mont) MNPs with those of other potentially active species in the synthesis of dibenzo[b,i]xanthene tetraone 3ca
Entry |
Catalysta |
Time (min) |
Yieldb (%) |
All reactions were carried out in H2O–EtOH (1 : 1 mL) under oil bath (80 °C) conditions using 20 mg of the nanocatalyst. Isolated yield. |
1 |
Cu0 NPs |
60 |
70 |
2 |
NiFe2O4 |
60 |
65 |
3 |
NiFe2O4@Cu |
60 |
70 |
4 |
Mont K10 |
60 |
60 |
5 |
H+-Mont |
60 |
80 |
6 |
Na+-Mont |
60 |
60 |
7 |
(NiFe2O4@Cu)(H+-Mont) |
20 |
95 |
The capability of (NiFe2O4@Cu)(H+-Mont) MNPs in the synthesis of dibenzo[b,i]xanthene tetraones was further studied towards the one-pot Knoevenagel–Michael reaction of substituted aromatic aldehydes with 2-hydroxy-1,4-naphthoquinone under the optimized reaction conditions. The results of this investigation are illustrated in Table 4. The table reveals that various aryl aldehydes, including electron releasing or withdrawing functionalities, participated successfully in the condensation reaction within 20 to 80 min at 80 °C to afford the corresponding dibenzo[b,i]xanthene tetraone materials in high to excellent yields.
Table 4 Preparation of dibenzo[b,i]xanthene tetraones catalyzed by (NiFe2O4@Cu)(H+-Mont) MNPsa
The generality of this synthetic method was also studied by examining the condensation reactions of aromatic aldehydes with dimedone as another source of 1,3-dicarbonyl compounds. The obtained results present that the utilized conditions for the synthesis of xanthene materials with 2-hydroxy-1,4-naphthoquinone were also efficient for the case-synthesis with dimedone material. Therefore, substituted aromatic aldehydes (1 mmol) were reacted with dimedone (2 mmol) in the presence of (NiFe2O4@Cu)(H+-Mont) (20 mg) at 90 °C in a one-pot procedure to afford the cyclization products of 9-aryl-3,3,6,6-tetramethyl-3,4,5,6,7,9-hexahydro-1H-xanthene-1,8(2H) diones. The results of this investigation are illustrated in Table 5. As can be seen, all reactions were carried out successfully within 15 to 210 min to afford tetramethyl xanthene diones 5(a–k) in high to excellent yields.
Table 5 Preparation of tetramethylxanthene diones using (NiFe2O4@Cu)(H+-Mont) MNPsa

|
Entry |
Ar- |
Product |
Time (min) |
Yieldb (%) |
Mp (°C)16,19,43 |
Found |
Reported |
All reactions were carried out under solvent-free conditions. Yields refer to isolated pure products. |
1 |
C6H5 |
5a |
50 |
90 |
202–204 |
202–204 (ref. 16) |
2 |
2-ClC6H4 |
5b |
35 |
95 |
226–227 |
226–228 (ref. 43) |
3 |
4-ClC6H4 |
5c |
20 |
96 |
231–233 |
230–232 (ref. 16 and 43) |
4 |
2,4-Cl2C6H3 |
5d |
15 |
97 |
242–244 |
243–245 (ref. 19) |
5 |
3-OH, 4-MeOC6H3 |
5e |
50 |
80 |
175–177 |
— |
6 |
4-OH, 3-MeOC6H3 |
5f |
50 |
75 |
170–172 |
— |
7 |
3-MeOC6H4 |
5g |
100 |
75 |
176–177 |
175–178 (ref. 19) |
8 |
2-MeOC6H4 |
5h |
210 |
60 |
229–230 |
230–231 (ref. 16) |
9 |
2-OHC6H4 |
5i |
80 |
75 |
247–249 |
— |
10 |
4-O2NC6H4 |
5j |
20 |
97 |
222–224 |
221–223 (ref. 43) |
11 |
3-O2NC6H4 |
5k |
20 |
98 |
174–176 |
175–177 (ref. 19) |
Although the exact mechanism of this synthetic protocol is not clear, a mechanism depicted in Fig. 10 presents the role of (NiFe2O4@Cu)(H+-Mont) MNPs in promoting the formation of xanthene materials. The mechanism shows that the carbonyl moiety of the aryl aldehyde can be activated by the clay nanocatalyst through the existence of numerous Lewis and Brønsted acidity sites. Then, the enolic form of the 1,3-dicarbonyl compound readily reacts with the activated aldehyde to form the Knoevenagel intermediate I. Next, through the activation of intermediate I with the nanocatalyst followed by Michael addition of the second enole form of 1,3-dicarbonyl material, the intermediate II is produced. Through ring closing of the intermediate II, finally, the xanthene material is produced.
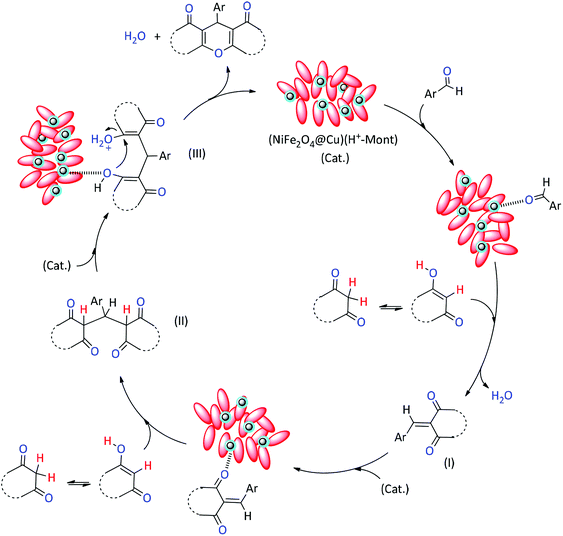 |
| Fig. 10 A proposed mechanism for the Knoevenagel–Michael reaction of aryl aldehydes with 1,3-dicarbonyl compounds catalyzed by (NiFe2O4@Cu)(H+-Mont) MNPs. | |
The usefulness of (NiFe2O4@Cu)(H+-Mont) MNPs in the one-pot syntheses of 3c and 5c was also highlighted by a comparison of the obtained results with current and previously reported protocols (Tables 6 and 7). A case study shows that in terms of reaction time, conditions, reusability of the nanocatalyst and yield of the mentioned products, the present work presents a more efficient process than previous systems. On the basis of product yield, solvent-free conditions and rate of the condensation reaction, however, better results with previous systems are observable (Table 6, entries 4–7).
Table 6 Synthesis of dibenzo[b,i]xanthene tetraone 3c with (NiFe2O4@Cu)(H+-Mont) MNPs and other reported promoters
Entry |
Catalyst |
Time (min) |
Yield (%) |
Conditions |
Temp (°C) |
Reusability |
Ref. |
Present work. |
1 |
(NiFe2O4@Cu)(H+-Mont) |
20 |
95 |
EtOH–H2O |
80 |
7 |
a |
2 |
Graphene oxide-Sr NPs |
105 |
89 |
Solvent-free |
80 |
6 |
43 |
3 |
Choline-Cl/itaconic acid |
90 |
90 |
Ionic liquid |
90 |
5 |
44 |
4 |
[Msim]Cl |
5 |
95 |
Solvent-free |
80 |
5 |
47 |
5 |
[Hmim][HSO4] |
4 |
92 |
Solvent-free |
80 |
5 |
47 |
6 |
[Et3N–SO3H]Cl |
5 |
98 |
Solvent-free |
80 |
5 |
47 |
7 |
[Et3NH][HSO4] |
4 |
93 |
Solvent-free |
80 |
5 |
47 |
8 |
[Bmim][HSO4] |
90 |
86 |
EtOH |
Reflux |
— |
48 |
9 |
N-Sulfonic acid poly(4-vinylpyridinium) HSO4 |
15 |
94 |
Solvent-free |
60 |
5 |
50 |
10 |
p-TSA |
150 |
80 |
Solvent-free |
100 |
— |
51 |
11 |
FeCl3·6H2O |
90 |
95 |
Solvent-free |
90 |
— |
53 |
Table 7 Synthesis of xanthene dione 5c catalyzed by (NiFe2O4@Cu)(H+-Mont) MNPs and other reported promoters
Entry |
Catalyst |
Time (min) |
Yield (%) |
Conditions |
Temp (°C) |
Reusability |
Ref. |
Present work. |
1 |
(NiFe2O4@Cu)(H+-Mont) |
20 |
96 |
EtOH–H2O |
90 |
7 |
a |
2 |
ZrO2 NPs |
19 |
87 |
Solvent-free |
100 |
— |
16 |
3 |
HOAc |
10 |
81 |
Solvent-free |
80 |
— |
19 |
4 |
NaHSO4·SiO2 |
390 |
94 |
CH3CN |
Reflux |
— |
22 |
5 |
Nano Fe3O4@TiO2@SO3H |
40 |
89 |
Solvent-free |
110 |
4 |
28 |
6 |
Nano ZrO2@SO3H |
96 |
93 |
Solvent-free |
100 |
5 |
29 |
7 |
[Hmim]TFA |
150 |
93 |
Ionic liquid |
80 |
4 |
31 |
8 |
Amberlyst-15 |
300 |
94 |
CH3CN |
Reflux |
3 |
35 |
9 |
Montmorillonite K10 |
80 |
90 |
Solvent-free |
100 |
— |
36 |
10 |
Fe3+-montmorillonite |
360 |
88 |
EtOH |
Reflux |
4 |
37 |
11 |
CuI/poly(4-vinylpyridine) |
8 |
90 |
Solvent-free |
80 |
8 |
42 |
12 |
Graphene oxide-Sr NPs |
60 |
92 |
Solvent-free |
80 |
6 |
43 |
3.4. Recycling of the (NiFe2O4@Cu)(H+-Mont) MNPs
In order to examine the green and economic aspects of (NiFe2O4@Cu)(H+-Mont) MNPs as well as the stability of the (NiFe2O4@Cu) moiety on the surface of acid-activated montmorillonite, the reusability of this nanocatalyst towards the synthesis of xanthene material 5c was also investigated. After completion of the reaction, the nanocatalyst was magnetically separated from the reaction mixture and washed with water and then EtOAc, followed by drying in an oven for use in the next cycle. The obtained results showed that the recycled (NiFe2O4@Cu)(H+-Mont) can be successfully reused at least 7 times without significant loss of its catalytic activity. It is also concluded that after each run, the nature of the clay nanocatalyst remains intact and the (NiFe2O4@Cu) moiety is tightly immobilized on the surface of the acid-activated montmorillonite, most probably via electrostatic attractions between NiFe2O4 (positive charge) and the Mont layer (negative charge).
4. Conclusions
In this work, the synthesis of copper-layered nickel ferrite anchored on acid-activated montmorillonite, (NiFe2O4@Cu)(H+-Mont), as a new class of clay composite systems was investigated. The prepared magnetic clay was then characterized using SEM, EDX, XRD, FT-IR, BET and VSM analyses. The catalytic activity of the nanocomposite was also studied towards the synthesis of xanthene derivatives via one-pot cyclocondensation of 2-hydroxy-1,4-naphthoquinone (Lawsone)/dimedone with various aryl aldehydes in a mixture of H2O–EtOH (1
:
1 mL) as a green solvent at 80 °C to 90 °C, which afforded the products in high to excellent yields. Investigation of the results exhibited that the synergic influence of the copper-layered nickel ferrite constituent with H+-Mont resulted in a dramatic enhancement of the rate of the reaction. The facile separation of the nanocatalyst by an external magnetic field, generality, short reaction times, high product yields and low loading of the nanocatalyst as well as the excellent reusability of the magnetic clay are the key features which make this synthetic method a prominent choice for the synthesis of xanthenes as biologically active materials.
Conflicts of interest
The authors declare that they do not have any conflict of interest.
Acknowledgements
The authors gratefully acknowledge the financial support of this work by the research council of Urmia University.
References
- J. M. Khurana, D. Magoo, K. Aggarwal, N. Aggarwal, R. Kumar and C. Srivastava, Eur. J. Med. Chem., 2012, 58, 470–477 CrossRef CAS.
- H. N. Hafez, M. I. Hegab, I. S. Ahmed-Farag and A. B. A. El-Gazzar, Bioorg. Med. Chem. Lett., 2008, 18, 4538–4543 CrossRef CAS.
- O. Evangelinou, A. G. Hatzidimitriou, E. Velali, A. A. Pantazaki, N. Voulgarakis and P. Aslanidis, Polyhedron, 2014, 72, 122–129 CrossRef CAS.
- A. Ilangovan, K. Anandhan, K. M. Prasad, P. Vijayakumar, R. Renganathan, D. A. Ananth and T. Sivasudha, Med. Chem. Res., 2015, 24, 344–355 CrossRef CAS.
- C. Spatafora, V. Barresi, V. M. Bhusainahalli, S. Di Micco, N. Musso, R. Riccio, G. Bifulco, D. Condorelli and C. Tringali, Org. Biomol. Chem., 2014, 12, 2686–2701 RSC.
- K. Chibale, M. Visser, D. van Schalkwyk, P. J. Smith, A. Saravanamuthu and A. H. Fairlamb, Tetrahedron, 2003, 59, 2289–2296 CrossRef CAS.
- N. Mulakayala, P. V. N. S. Murthy, D. Rambabu, M. Aeluri, R. Adepu, G. R. Krishna, C. M. Reddy, K. R. S. Prasad, M. Chaitanya, C. S. Kumar, M. V. B. Rao and M. Pal, Bioorg. Med. Chem. Lett., 2012, 22, 2186–2191 CrossRef CAS.
- G. Saint-Ruf, H. T. Hieu and J. P. Poupelin, Naturwissenschaften, 1975, 62, 584–590 CrossRef CAS.
- B. B. Bhowmik and P. Ganguly, Spectrochim. Acta, Part A, 2005, 61, 1997–2003 CrossRef.
- S. A. Hilderbrand and R. Weissleder, Tetrahedron Lett., 2007, 48, 4383–4385 CrossRef CAS.
- G. Pohlers, J. Scaiano and R. Sinta, Chem. Mater., 1997, 9, 3222–3230 CrossRef CAS.
- M. T. Ahmad, A. King, D. K. Ko, B. H. Cha and J. Lee, J. Phys. D: Appl. Phys., 2002, 35, 1473–1476 CrossRef CAS.
- A. Ojida, I. Takashima, T. Kohira, H. Nonaka and I. Hamachi, J. Am. Chem. Soc., 2008, 130, 12095–12101 CrossRef CAS.
- T. Hideu, JP 56005480, Jpn, Tokyo, KohoChem. Abstr., 1981, 95, p. 80922b.
- B. Karami, S. J. Hoseini, K. Eskandari, A. Ghasemi and H. Nasrabad, Catal. Sci. Technol., 2012, 2, 331–338 RSC.
- P. Bansal, N. Kaur, C. Prakash and G. R. Chaudhary, Vacuum, 2018, 157, 9–16 CrossRef CAS.
- M. Seyyedhamzeh, P. Mirzaei and A. Bazgir, Dyes Pigm., 2008, 76, 836–839 CrossRef CAS.
- B. Karami, S. Nejati and K. Eskandaric, Curr. Chem. Lett., 2015, 4, 169–180 CrossRef.
- N. Hazeri, A. Masoumnia, M. T. Mghsoodlou, S. Salahi, M. Kangani, S. Kianpour, S. Kiaee and J. Abonajmi, Res. Chem. Intermed., 2015, 41, 4123–4131 CrossRef CAS.
- S. Kantevari, R. Bantu and L. Nagarapu, J. Mol. Catal. A: Chem., 2007, 269, 53–57 CrossRef CAS.
- Z. H. Zhang and Y. H. Liu, Catal. Commun., 2008, 9, 1715–1719 CrossRef CAS.
- B. Das, P. Thirupathi, K. R. Reddy, B. Ravikanth and L. Nagarapu, Catal. Commun., 2007, 8, 535–538 CrossRef CAS.
- H. R. Shaterian, A. Hosseinian and M. Ghashang, Phosphorus, Sulfur Silicon Relat. Elem., 2008, 183, 3136–3144 CrossRef CAS.
- X. Fan, X. Hu, X. Zhang and J. Wang, Can. J. Chem., 2005, 83, 16–20 CrossRef CAS.
- D. H. Jung, Y. R. Lee, S. H. Kim and W. S. Lyoo, Bull. Korean Chem. Soc., 2009, 30, 1989–1995 CrossRef CAS.
- T. S. Jin, J. S. Zhang, A. Q. Wang and T. S. Li, Synth. Commun., 2005, 35, 2339–2345 CrossRef CAS.
- F. Nemati and S. Sabaqian, J. Saudi Chem. Soc., 2017, 21, S383–S393 CrossRef CAS.
- A. Amoozadeh, S. Golian and S. Rahmani, RSC Adv., 2015, 5, 45974–45982 RSC.
- A. Amoozadeh, S. Rahmani, M. Bitaraf, F. B. Abadi and E. Tabrizian, New J. Chem., 2016, 40, 770–780 RSC.
- J. Ma, X. Zhou, X. Zhang, C. Wang, Z. Wang, J. Li and Q. Li, Aust. J. Chem., 2007, 60, 146–148 CrossRef CAS.
- M. Dabiri, M. Baghbanzadeh and E. Arzroomchilar, Catal. Commun., 2008, 9, 939–942 CrossRef CAS.
- T. S. Jin, L. B. Liu, Y. Zhao and T. S. Li, Synth. Commun., 2005, 35, 2379–2385 CrossRef CAS.
- T. S. Jin, J. S. Zhang, A. Q. Wang and T. S. Li, Ultrason. Sonochem., 2006, 13, 220–224 CrossRef CAS.
- G. I. Shakibaei, P. Mirzaei and A. Bazgir, Appl. Catal., A, 2007, 325, 188–192 CrossRef CAS.
- B. Das, P. Thirupathi, I. Mahender, V. S. Reddy and Y. K. Rao, J. Mol. Catal. A: Chem., 2006, 247, 233–239 CrossRef CAS.
- M. Dabiri, S. Azimi and A. Bazgir, Chem. Pap., 2008, 62, 522–526 CAS.
- G. Song, B. Wang, H. Luo and L. Yang, Catal. Commun., 2007, 8, 673–676 CrossRef CAS.
- A. Rahmati, Chin. Chem. Lett., 2010, 21, 761–764 CrossRef CAS.
- D. Q. Shi, Q. Y. Zhuang, J. Chen, X. S. Wang, S. J. Tu and H. W. Hu, Chin. J. Org. Chem., 2003, 23, 694–696 CAS.
- S. Kantevari, R. Bantu and L. Nagarapu, ARKIVOC, 2006, xvi, 136–148 Search PubMed.
- P. Paliwal, S. R. Jetti, A. Bhatewara, T. Kadre and S. Jain, ISRN Org. Chem., 2013, 526173, DOI:10.1155/2013/526173.
- J. Albadi, M. Keshavarz, M. Abedini and M. Khoshakhlagh, J. Chem. Sci., 2013, 125, 295–298 CrossRef CAS.
- S. R. Mousavi, H. R. Nodeh, E. Z. Afshari and A. Foroumadi, Catal. Lett., 2019, 149, 1075–1086 CrossRef CAS.
- P. Liu, J. W. Hao, S. J. Liang, G. L. Liang, J. Y. Wang and Z. H. Zhang, Monatsh. Chem., 2016, 147, 801–808 CrossRef CAS.
- F. Darviche, S. Balalaie, F. Chadegani and P. Salehi, Synth. Commun., 2007, 37, 1059–1066 CrossRef CAS.
- A. John, P. J. P. Yadav and S. Palaniappan, J. Mol. Catal. A: Chem., 2006, 248, 121–125 CrossRef CAS.
- H. R. Shaterian, M. Sedghipour and E. Mollashahi, Res. Chem. Intermed., 2014, 40, 1345–1355 CrossRef CAS.
- J. M. Khurana, A. Lumb, A. Chaudhary and B. Nand, J. Heterocycl. Chem., 2014, 51, 1747–1751 CrossRef CAS.
- Y. Li, B. Du, X. Xu, D. Shi and S. Ji, Chin. J. Chem., 2009, 27, 1563–1568 CrossRef CAS.
- N. G. Khaligh and F. Shirini, Ultrason. Sonochem., 2015, 22, 397–403 CrossRef CAS.
- Z. N. Tisseh, S. C. Azimi, P. Mirzaei and A. Bazgir, Dyes Pigm., 2008, 79, 273–275 CrossRef CAS.
- S. Ko and C. F. Yao, Tetrahedron Lett., 2006, 47, 8827–8829 CrossRef CAS.
- D. Liu, S. Zhou, J. Gao, L. Li and D. Xu, J. Mex. Chem. Soc., 2013, 57, 345–348 CAS.
- N. K. Ojha, G. V. Zyryanov, A. Majee, V. N. Charushin, O. N. Chupakhin and S. Santra, Coord. Chem. Rev., 2017, 353, 1–57 CrossRef CAS.
- M. B. Gawande, A. Goswami, F. X. Felpin, T. Asefa, X. Huang, R. Silva, X. Zou, R. Zboril and R. S. Varma, Chem. Rev., 2016, 116, 3722–3811 CrossRef CAS.
- B. Zeynizadeh, M. Zabihzadeh and Z. Shokri, J. Iran. Chem. Soc., 2016, 13, 1487–1492 CrossRef CAS.
- A. Alexakis, N. Krause and S. Woodward, Copper-Catalyzed Asymmetric Synthesis, Wiley-VCH, Weinheim, 2014 Search PubMed.
- F. Alonso, Y. Moglie, G. Radivoy and M. Yus, Org. Biomol. Chem., 2011, 9, 6385–6395 RSC.
- J. M. Welter, Copper: Better Properties for Innovative Products, Wiley-VCH, Weinheim, 2007 Search PubMed.
- L. Yang, Y. Xie, H. Zhao, X. Wu and Y. Wang, Solid-State Electron., 2005, 49, 1029–1033 CrossRef CAS.
- L. Luo, Q. Li, Y. Xu, Y. Ding, X. Wang, D. Deng and Y. Xu, Sens. Actuators, B, 2010, 145, 293–298 CrossRef CAS.
- P. Sivakumar, R. Ramesh, A. Ramanand, S. Ponnusamy and C. Muthamizhchelvan, J. Alloys Compd., 2013, 563, 6–11 CrossRef CAS.
- A. Ren, C. Liu, Y. Hong, W. Shi, S. Lin and P. Li, Chem. Eng. J., 2014, 258, 301–308 CrossRef CAS.
- A. S. A. Bakr, Y. M. Moustafa, E. A. Motawea, M. M. Yehia and M. M. H. Khalil, J. Environ. Chem. Eng., 2015, 3, 1486–1496 CrossRef CAS.
- B. Zeynizadeh, I. Mohammadzadeh, Z. Shokri and S. A. Hosseini, J. Colloid Interface Sci., 2017, 500, 285–293 CrossRef CAS.
- O. S. Ahmed and D. K. Dutta, Langmuir, 2003, 19, 5540–5541 CrossRef CAS.
- B. J. Borah, D. Dutta, P. P. Saikia, N. C. Barua and D. K. Dutta, Green Chem., 2011, 13, 3453–3460 RSC.
- P. P. Sarmah and D. K. Dutta, Green Chem., 2012, 14, 1086–1093 RSC.
- A. Usuki, N. Hasegawa, H. Kadoura and T. Okamoto, Nano Lett., 2001, 1, 271–272 CrossRef CAS.
- B. S. Kumar, A. Dhakshinamoorthy and K. Pitchumani, Catal. Sci. Technol., 2014, 4, 2378–2396 RSC.
- P. Malla, P. Ravindranathan, S. Komarneni and R. Roy, Nature, 1991, 351, 555–557 CrossRef CAS.
- S. Karami, B. Zeynizadeh and Z. Shokri, Cellulose, 2018, 25, 3295–3305 CrossRef CAS.
- B. Zeynizadeh and S. Rahmani, RSC Adv., 2019, 9, 8002–8015 RSC.
- S. Rahmani and B. Zeynizadeh, Res. Chem. Intermed., 2019, 45, 1227–1248 CrossRef CAS.
- B. Zeynizadeh, S. Rahmani and E. Eghbali, Polyhedron, 2019, 168, 57–66 CrossRef CAS.
- B. Zeynizadeh, S. Rahmani and S. Ilkhanizadeh, Polyhedron, 2019, 168, 48–56 CrossRef CAS.
- D. Dutta, B. J. Borah, L. Saikia, M. G. Pathak, P. Sengupta and D. K. Dutta, Appl. Clay Sci., 2011, 53, 650–656 CrossRef CAS.
- B. Sahin and T. Kaya, Appl. Surf. Sci., 2016, 362, 532–537 CrossRef CAS.
- E. Şennik, S. Kerli, Ü. Alver and Z. Z. Öztürk, Sens. Actuators, B, 2015, 216, 49–56 CrossRef.
- S. K. Bhorodwaj and D. K. Dutta, Appl. Catal., A, 2010, 378, 221–226 CrossRef CAS.
- S. Brunauer, L. S. Deming, W. E. Deming and E. Teller, J. Am. Chem. Soc., 1940, 62, 1723–1732 CrossRef CAS.
- J. Ji, P. Zeng, S. Ji, W. Yang, H. Liu and Y. Li, Catal. Today, 2010, 158, 305–309 CrossRef CAS.
- P. K. Saikia, P. P. Sarmah, B. Borah, L. Saikia, K. Saikia and D. K. Dutta, Green Chem., 2016, 18, 2843–2850 RSC.
- S. K. Bhorodwaj, M. G. Pathak and D. K. Dutta, Catal. Lett., 2009, 133, 185–191 CrossRef CAS.
- B. Tyagi, C. D. Chudasama and R. V. Jasra, Appl. Clay Sci., 2006, 31, 16–28 CrossRef CAS.
- J. Madejova and P. Komadel, Clays Clay Miner., 2001, 49, 410–432 CrossRef CAS.
- K. Wang, L. Wang, J. Wu, L. Chen and C. He, Langmuir, 2005, 21, 3613–3618 CrossRef CAS.
- M. Mekewi, A. Darwish, M. Amin, G. Eshaq and H. Bourazan, Egypt. J. Pet., 2016, 25, 269–279 CrossRef.
- R. Das, S. S. Nath and R. Bhattacharjee, J. Fluoresc., 2011, 21, 1165–1170 CrossRef CAS.
- B. Bagchi, S. Kar, S. K. Dey, S. Bhandary, D. Roy, T. K. Mukhopadhyay, S. Das and P. Nandy, Colloids Surf., B, 2013, 108, 358–365 CrossRef CAS.
- K. R. Reddy, W. Park, B. C. Sin, J. Noh and Y. Lee, J. Colloid Interface Sci., 2009, 335, 34–39 CrossRef CAS.
|
This journal is © The Royal Society of Chemistry 2019 |
Click here to see how this site uses Cookies. View our privacy policy here.