DOI:
10.1039/C8NH00480C
(Communication)
Nanoscale Horiz., 2019,
4, 867-873
Environmentally benign modification of breathable nanofibrous membranes exhibiting superior waterproof and photocatalytic self-cleaning properties†
Received
12th December 2018
, Accepted 20th February 2019
First published on 20th February 2019
Abstract
Environmentally benign waterproof and breathable membranes with high-performance and photocatalytic self-cleaning properties were prepared by combining water-based hydrophobic materials and photo-sensitive inorganic nanoparticle coatings with electrospun nanofiber matrices. The membranes exhibited prominent water-resistant behavior, high breathability, superior mechanical strength as well as significant degradation capability to organic pollutants.
Conceptual insights
Wearable, environmentally benign smart membranes featuring high-performing waterproof breathable properties and self-cleaning performance are highly desirable but have not been reported yet. Herein, we present, for the first time, a feasible and efficient strategy to create a novel eco-friendly, high-performance and photocatalytic self-cleaning waterproof and breathable membrane by electrospinning polyacrylonitrile (PAN) nanofiber matrices followed by a stepwise impregnation route. The environmentally benign water-based coating with short fluorinated segments conferred good hydrophobic behavior to the fibers and at the same time obviously decreased pore size of the pristine membranes. The subsequent employment of a photofunctional zinc oxide nanoparticle (ZnO NPs) coating not only further enhanced the waterproof properties of the fibrous membranes but also endowed the membranes with desirable photodegradation activity. Consequently, the resulting fibrous membranes exhibited unprecedented integrated properties with prominent hydrostatic pressure of 98.7 kPa, high water vapor transmission rate of 12.0 kg m−2 d−1, excellent tensile strength of 17.9 MPa, along with significant chemical degradation capability. This facile and cost-effective fabrication of such materials would be valuable for the design of wearable textiles for various applications in protective garments, health care and military uniform systems.
|
Introduction
As the largest organ in our bodies, human skin is the physical barrier through which we interact with our surroundings, allowing us to sweat and protecting us from external invasive substances.1,2 Working in the same manner as human skin, waterproof and breathable membranes (WBM) identified as “second skin” have gained much attention due to their widespread applications ranging from protective garments and medical instruments to sophisticated electronics.3,4 The existing commercial WBM mainly fall into two categories: hydrophilic nonporous membranes and hydrophobic microporous membranes. Owing to the higher level of comfort, microporous membranes have received considerable interest. Presently, a wide variety of strategies have been developed to fabricate microporous WBM, such as mechanical stretching, phase separation, and melt-blown techniques. Nonetheless, these methods are still subject to complex preparation processes, limited raw materials, and difficulty in coordinating the waterproof behavior and breathability simultaneously.
Electrospun membranes,5–8 which possess ultrathin diameters, high porosity, interconnected pores, and ease of scalable production, show promise as building blocks to construct WBM. Until now, different kinds of WBM have been investigated, such as polyurethane,9 polyacrylonitrile (PAN),10 polyvinylidene fluoride,11 and so forth. PAN nanofibers have attracted significant attention because of their good spinnability, small fiber diameter, as well as tunable porous structure.12 Bagherzadeh et al. first reported PAN nanofibrous membranes (NFM), but the hydrophilicity of the fibers resulted in low hydrostatic pressure (4 kPa).13 In order to improve the hydrophobicity, Sheng et al. introduced a polymer containing long perfluorooctyl (–C8F17) segments into PAN fibers: the resultant membranes exhibited high waterproof performance (114 kPa), and good water vapor transmission (WVT) rate.14 Although perfluorinated polymers impart surfaces with remarkable amphiphobic properties which are highly desirable for modern textiles, unfortunately the persistence and environmental hazards of long perfluoroalkyl (Rfn, n ≥ 8) chains are hampering their extensive applications.15,16 Thus, designing environmentally benign materials has become an inevitable trend of social and technological development. Recently, our group employed environmentally friendly fluorinated polymers with six fluorinated atoms (C6) to modify electrospun PAN fibers: the prepared membranes displayed good water resistance (83.4 kPa) and modest moisture permeability.17 It is certain that chemicals with shorter perfluoroalkyl chain would be less harmful and provide higher security.18 Currently, the most ecofriendly water and oil auxiliaries are waterborne fluorinated chemicals containing shorter chains of four fluorinated atoms (C4). At the cutting edge of advanced fluorochemical textile agents, they hold great promise as key building units for preparing environmentally benign and high performing WBM.
On the other hand, due to increasingly serious environmental pollution and energy shortages, energy conservation has become a worldwide issue.19 It is reported that large amounts of energy are consumed for cleaning surface contamination.20 Protective and self-cleaning garments are also in urgent demand for military, health and environmental applications. Thus, engineering self-cleaning fabrics which can remove or degrade pollutants without washing has become a research emphasis of material scientists. In general, there are two routes to realize self-cleaning: superhydrophobicity and superhydrophilicity.21,22 Typical superhydrophobic surfaces like butterfly wings and lotus leaves exhibit water contact angles greater than 150° and slide angles less than 5°, which can remove dust and particles physically.23 However, the superhydrophobic performance will gradually deteriorate because of the lowered surface roughness and adhesion of oily pollutants in practical use.24 For superhydrophilic surfaces, the adsorbed dirt, pollutants, and contaminants would chemically break down into small molecules on exposure to ultraviolet (UV) light with a photocatalyst. There are also limited examples of superhydrophobic and photocatalytic surfaces in the literature,25–27 however, without exception, these surfaces cannot possess waterproof behavior and breathability simultaneously. Thus, constructing photocatalytic self-cleaning and waterproof breathable materials, which to the best of our knowledge has not been reported, is of great significance and very imperative.
Herein, we report the synthesis of a novel membrane with environmentally benign, waterproof, breathable, and photocatalytic self-cleaning behavior. The ecofriendly water-based finishing agent (PM3635) was coated on the pristine PAN nanofiber substrate, conferring robust waterproof performance to the PAN fibrous membranes (Scheme 1a). Subsequently, zinc oxide nanoparticles (ZnO NPs) were introduced on the surface of the fibers, which not only decreased the maximum pore size (dmax) bringing about greatly improved hydrostatic pressure, but also resulted in fibrous membranes with significant photocatalytic self-cleaning performance. Moreover, the effects of PM3635 and ZnO NPs concentration on the surface chemical composition, wettability and porous structure of fibrous membranes were fully investigated. The fibrous membranes were able to provide good integrated properties, indicating promising applications in a variety of fields.
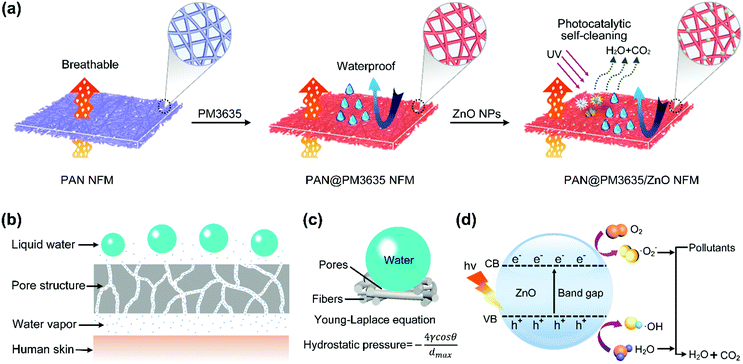 |
| Scheme 1 (a) Schematic illustration of the preparation of PAN@PM3635/ZnO waterproof breathable and photocatalytic self-cleaning fibrous membranes, (b) waterproof and breathable mechanism of porous fibrous membranes, (c) waterproof mechanism based on the Young–Laplace equation, and (d) photocatalytic self-cleaning mechanism of PAN@PM3635/ZnO NFM. | |
Results and discussion
Effect of PM3635 concentration
The systematic design of fibrous WBM is based on pore size effects. The pore size of fibrous membranes should be larger than the diameter of a water vapor molecule (0.0004 μm) but smaller than that of a tiny water droplet (100 μm),28,29 so that water vapor can transport freely while water droplets cannot penetrate into the porous structure, as shown in Scheme 1b. As a rule, water resistance is quantified by hydrostatic pressure, and higher hydrostatic pressure indicates better waterproof behavior. According to our previous studies, the hydrostatic pressure has been confirmed to rely on the dmax of fibrous membranes and advancing water contact angle (θ) of flat films, and their relationship is consistent with the Young–Laplace equation3,30 (Scheme 1c). Therefore, in order to obtain WBM with better waterproof performance, the dmax of fibrous membranes should be small. Notably, the above discussion is based on the premise that the materials used must be hydrophobic. In our present work, the hydrophobic surface was constructed by virtue of ecofriendly PM3635 waterborne hydrophobic agent. On the other hand, to achieve desired photocatalytic self-cleaning performance, ZnO NPs were introduced onto the surface of the fibers. The photocatalytic degradation process is illustrated in Scheme 1d: energy from UV light promotes the excitation of electrons from the valence band (VB) to the conduction band (CB), generating pairs of negative electrons (e−) in the CB and positive holes (h+) in the VB. The active e− and h+ react with oxygen (O2) and water (H2O) to create superoxide radicals (O2−) and hydroxyl radicals (˙OH), respectively. These active oxygen species play an important role in the subsequent oxidation–reduction reaction and convert the organic compounds into carbon dioxide (CO2) and H2O.31,32
We regulated the concentration of PM3635 from 0 to 4 wt%, and the influence of the PM3635 content on the morphology and surface wettability of PAN@PM3635 NFM was investigated. SEM images of PAN@PM3635 NFM with various PM3635 contents are depicted in Fig. 1a–d. It can be seen that all the fibrous membranes demonstrate a typical three-dimensional network structure with uniform diameter distribution. Nanofibers assemble into a mutually connected porous structure, which is quite favorable for vapor permeability, thus electrospun membranes usually exhibit good breathability. The pristine PAN nanofibers were smooth and stacked loosely, and after modification with water repellents the fibers demonstrated a closely packed arrangement. At high concentrations of PM3635, an adhesive structure appeared and gradually increased in some areas. With PM3635 concentration increased from 0 to 4 wt%, the fiber diameter increased slightly from 273 to 357 nm (Fig. 1e). As exhibited in Fig. 1f, the average pore size decreased from 1.20 to 0.61 μm, meanwhile the pore structure became more regular, the dmax also decreased from 1.55 to 0.87 μm (Fig. S1, ESI†), which could be attributed to the increased bonding points. Due to the close packed arrangement of fibers, the porosity of the fibrous membranes decreased from 85.4% to 55.8% (Fig. S2, ESI†).
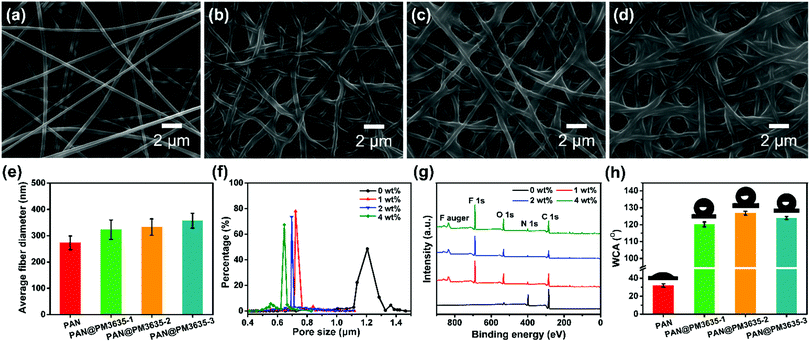 |
| Fig. 1 SEM images of (a) PAN, (b) PAN@PM3635-1, (c) PAN@PM3635-2, and (d) PAN@PM3635-3 NFM. (e) Average fiber diameter, (f) pore size distribution, (g) XPS spectra, and (h) WCA of PAN@PM3635 NFM with different PM3635 concentrations. | |
The wettability of fibrous membranes is dominated by their surface energy and their surface roughness. The chemical element composition of the surfaces of the fibers was confirmed by X-ray photoelectron spectroscopy (XPS) analysis, as displayed in Fig. 1g. Compared with the pristine PAN membrane, the characteristic peak of F1s appeared at 689.1 ± 0.2 eV for PAN@PM3635 NFM, indicating that fluorine was distributed on the fiber surface. The bands located at 285.2 ± 0.2, 400.2 ± 0.3, and 532.7 ± 0.1 eV were assigned to C1s, N1s and O1s, respectively. As the PM3635 concentration increased from 1 to 2 wt%, the fluorine atom content among C, S, N, O and F increased from 22.7% to 28.1%, meanwhile F/C concurrently increased from 0.41 to 0.57 (Table S1, ESI†), signifying that more fluorine is present on the fiber surface. Nevertheless, upon successive increment of PM3635 to 4 wt%, the fluorine content reduced to 23.8%, and the F/C ratio synchronously declined to 0.46, indicating that excess PM3635 was not conducive to the surface migration of fluorine. Subsequently, the water contact angle (WCA) of PAN@PM3635 NFM with various PM3635 concentrations was characterized, as shown in Fig. 1h. Pristine PAN NFM showed hydrophilicity with WCA of 36°, then WCA increased with the introduction of PM3635, which could be ascribed to the increased amount of fluorine atoms, and it reached the maximum value of 126.8° when PM3635 was 2 wt%. Upon further increase of the PM3635 concentration, the WCA of PAN@PM3635-3 NFM decreased, which could be caused by the decreased surface roughness originating from the excess bonding structure, so we chose PAN@PM3635-2 for further investigation.
Effect of ZnO NPs concentration
Morphologies and structures.
For the sake of constructing waterproof breathable and photocatalytic self-cleaning fibrous membranes, ZnO NPs dispersion was adopted in the experiment to improve the uniformity of the nanoparticle distribution and the bonding strength with the fibrous membrane matrix. As displayed in Fig. 2a–d, the FE-SEM images indicate that fibers notably exhibited hierarchical structure on the surface. With the increment of ZnO NP contents, the nanoparticles on the fibers clearly increased and the pores among the nanofibers were gradually filled; further increase of the ZnO NPs led to the appearance of aggregates. Fig. 2e and Fig. S3 (ESI†) verified the relatively homogeneous distribution of Zn, C, S, O and F on the fibers of PAN@PM3635-2/ZnO-3 at the nanoscale. Additionally, based on the semiquantitative estimation of EDX (Fig. 2f and Table S2, ESI†), the calculated content of ZnO NPs in the membrane was 22.9 wt%, demonstrating that the PAN@PM3635-2/ZnO NFM with high ZnO NP content could be achieved in a facile and general process.
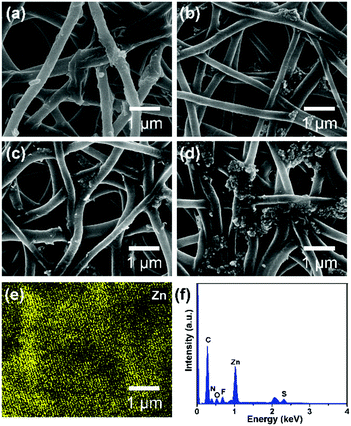 |
| Fig. 2 FE-SEM images of (a) PAN@PM3635-2/ZnO-1, (b) PAN@PM3635-2/ZnO-2, (c) PAN@PM3635-2/ZnO-3 and (d) PAN@PM3635-2/ZnO-4. (e) Elemental mapping image of Zn on PAN@PM3635-2/ZnO-3, and (f) EDX spectrum of a selected area of PAN@PM3635-2/ZnO-3. | |
Porous structure, waterproof breathable and mechanical performance
It is obvious that a smaller pore size contributes to higher hydrostatic pressure, so the effect of ZnO NP concentration on the pore structure of PAN@PM3635-2/ZnO NFM was investigated. As can be seen from Fig. 3a, the apertures of PAN@PM3635-2/ZnO-1 NFM varied from 0.20 to 1.04 μm, and they were distributed mainly at 0.68 μm. With the increase of ZnO NP contents, the pore diameter decreased gradually, primarily distributed at 0.49, 0.47 and 0.44 μm. In addition, because the nanoparticles filled in the pores between the stacked fibers, the dmax of the corresponding membranes was also reduced from 1.04 to 0.62 μm, as shown in Fig. 3b. On the other hand, owing to the hydrophilicity of the used ZnO NPs, as the concentration of ZnO NPs increased from 2 to 8 wt%, WCA of the prepared fibrous membranes decreased from 126.7° to 107.5°, which is consistent with the previous studies.27 As ZnO NP concentration was increased from 2 to 6 wt%, the hydrostatic pressure values of PAN@PM3635-2/ZnO NFM were 69.2, 77.4, and 98.7 kPa, which increased regularly with the gradually reduced dmax. However, the waterproof performance of PAN@PM3635-2/ZnO-4 NFM was reduced to 92.3 kPa, which was likely due to the aggregation of ZnO NPs resulting in enlarged dmax. Subsequently, we investigated the moisture and air permeability of PAN@PM3635-2/ZnO NFM, as exhibited in Fig. 3d. With ZnO NP concentration increased from 2 to 8 wt%, the WVT rate of PAN@PM3635-2/ZnO NFM reduced from 12.4 to 11.8 kg m−2 d−1, and the air permeability also reduced from 8.45 to 4.35 mm s−1, which could be ascribed to the decrease of porosity (Fig. S4, ESI†) impeding the freedom of transport of gaseous molecules. Taken together, PAN@PM3635-2/ZnO-3 NFM possessed the best waterproof and breathable properties. Afterwards, we performed a typical test to demonstrate the relevant performance of the membrane. As displayed in Fig. 3e, the self-standing PAN@PM3635-2/ZnO-3 NFM was fixed within an assembled container consisting of a lower closed chamber (with an air inlet pipe) and an upper open tube. Above the membrane, a certain volume of water was injected into the open tube: as can be seen from the photograph, the membrane could bear the weight of the water without any leakage, which clearly confirmed that the membrane exhibited good waterproof properties. Lots of air bubbles were generated in the upper container, revealing good breathability of the fibrous membrane. At the same time, the fibrous membranes also possessed good under-water stability (Fig. S5, ESI†). In addition, the resultant fibrous membrane exhibited satisfactory mechanical properties outperforming pristine PAN NFM, which is of great significance for practical applications. In terms of waterproof breathable and tensile strength properties, PAN@PM3635-2/ZnO-3 NFM exhibited comparable overall performances compared with the fibrous membranes containing long perfluoroalkyl chains (Fig. S6, ESI†).
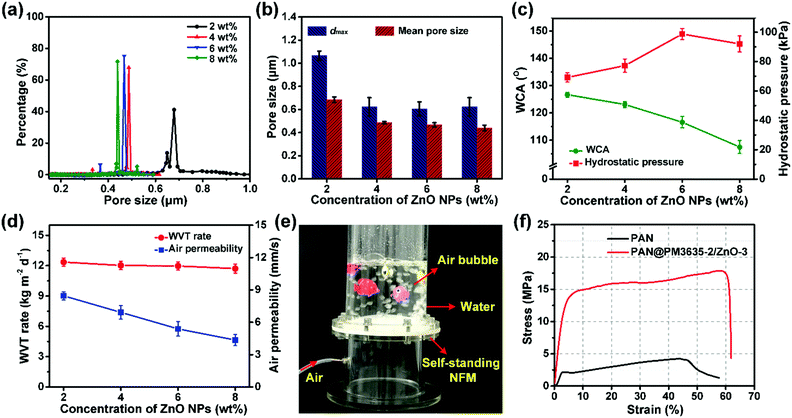 |
| Fig. 3 (a) Pore size distribution, (b) dmax and mean pore size, (c) WCA and hydrostatic pressure, (d) WVT rate and air permeability of PAN@PM3635-2/ZnO NFM with various ZnO concentrations. (e) Photograph demonstrating waterproof and breathable performance of PAN@PM3635-2/ZnO-3 NFM. (f) Stress–strain curves of PAN and PAN@PM3635-2/ZnO-3 NFM. | |
Photocatalytic self-cleaning activity
The photocatalytic degradation capability of PAN@PM3635-2/ZnO NFM was tested against the breakdown of MB and the light absorption after UV exposure for different time periods was measured. For PAN@PM3635-2/ZnO-1 fibrous membranes, under irradiation with UV light the blue color of the initial MB aqueous solution gradually lightened and it was almost totally discoloured after 100 min (Fig. 4a). According to the absorbance value of the solution, it took 110 minutes for PAN@PM3635-2/ZnO-1 fibrous membranes to completely degrade the MB solution. With the increase of ZnO NP concentration, the degradation rate gradually increased: for membranes containing 4, 6 and 8 wt% of ZnO NPs the duration times were 90, 80, and 70 minutes, respectively (Fig. 4 and Fig. S7, ESI†). From Fig. 4d we can see that the photodecomposition of MB without the employment of any photocatalyst (blank) could be neglected, which could ensure the accuracy of the results. After UV irradiation for 60 minutes, the degradation of MB dye was about 72.9%, 75.1%, 89.0% and 98.2% for PAN@PM3635-2/ZnO-1, PAN@PM3635-2/ZnO-2, PAN@PM 3635-2/ZnO-3, and PAN@PM3635-2/ZnO-4 NFM, respectively. In addition, to further demonstrate the self-cleaning performance of the ZnO NP functionalized fibrous membranes, PAN@PM3635-2/ZnO-3 NFMs stained by Nite writer pen with blue and purple colours were exposed to UV light for different times, as shown in Fig. 4e. The stained colours on the initial membranes were obvious, after 120 minutes of UV irradiation significant stain removal could be observed for the ZnO coated membranes compared with the pristine PAN samples, indicating good photocatalytic self-cleaning property of PAN@PM3635-2/ZnO-3 NFM.33
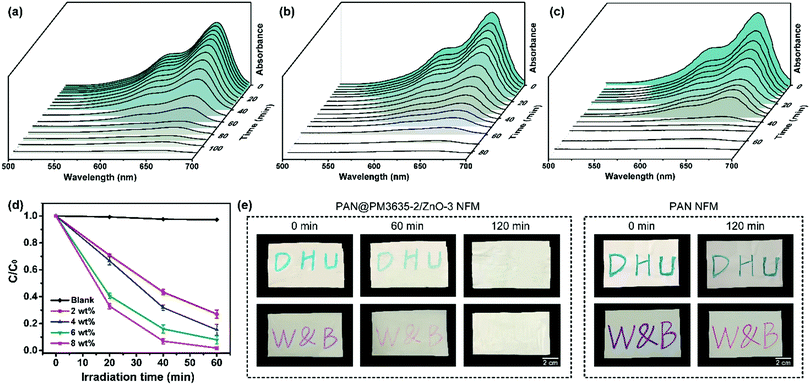 |
| Fig. 4 (a) Absorption spectra of MB dye under UV irradiation of (a) PAN@PM3635-2/ZnO-1, (b) PAN@PM3635-2/ZnO-3, and (c) PAN@PM3635-2/ZnO-4. (d) Photocatalytic degradation properties of corresponding fibrous membranes. (e) The decoloration process of stains under UV irradiation of PAN@PM3635-2/ZnO-3 and PAN NFM; the images were collected after exposure for 0, 60 and 120 min. | |
Conclusions
In summary, we have demonstrated a cost-effective and feasible technique to fabricate waterproof breathable membranes with high-performance, eco-friendliness and self-cleaning behavior. An environmentally benign waterborne hydrophobic coating was introduced onto the surface of the nanofibers, endowing the fibrous membranes with good amphiphobic properties. In addition, the utilization of ZnO NPs not only obviously decreased the dmax of the fibrous membranes making for significantly enhanced hydrostatic pressure, but also imparted the membranes with significant chemical degradation behavior against pollutants. With the aid of the small pore size, good hydrophobicity and interconnected porous structure, the as-prepared fibrous membranes exhibited superior hydrostatic pressure of 98.7 kPa, high moisture permeability of 12.0 kg m−2 d−1, excellent mechanical strength of 17.9 MPa, along with desired photocatalytic self-cleaning performance, suggesting their promise for application in protective garments, medical and military uniform systems.
Experimental
Preparation of PAN@PM3635/ZnO NFM
PAN NFM were prepared by electrospinning of PAN/DMAc solution, followed by removal of the DMAc solvent. Waterborne PM3635 emulsions with various concentrations (0, 1, 2 and 4 wt%) were obtained by diluting the emulsion with different amounts of deionized water. Pristine PAN NFM were fully immersed into 100 mL PM3635 emulsion for 30 min, then dried at room temperature and placed in a vacuum oven for 20 min with a temperature of 130 °C. The corresponding membranes were denoted as PAN, PAN@PM3635-1, PAN@PM3635-2, and PAN@PM3635-3 (see the ESI† for experimental details). In the following experiment, PAN@PM3635-2 membranes were coated with ethanol/deionized water containing a series of concentrations of ZnO NP suspensions (2, 4, 6, and 8 wt%) for 30 min. The coated membranes were desiccated in a vacuum drying chamber at 130 °C for 20 min. The prepared membranes were denoted as PAN@PM3635-2/ZnO-1, PAN@PM3635-2/ZnO-2, PAN@PM3635-2/ZnO-3, and PAN@PM3635-2/ZnO-4.
Measurements
The waterproof properties were examined using a hydrostatic pressure tester (YG812C, Nantong Hongda Experiment Instruments Co., Ltd, China). The WVT rate was determined according to the method described in our previous work.9 The tensile strength of fibrous membranes was tested using an XQ-1C tensile strength tester (Shanghai New Fiber Instrument Co., Ltd, China). Photocatalytic properties of ZnO NPs coated fibrous membranes were measured by the degradation of methylene blue (MB) solution. The MB solution was placed on the surface of the fibrous membranes with direct contact at a determined volume (4 mL) with a concentration of 10 mg L−1.34 Afterwards, the photocatalytic degradation was triggered using a 24 W UV lamp with wavelength of 254 nm for a predetermined time, similar to our previous studies.35 After equilibration, the solution was tested using a UV-vis spectrophotometer (U-3900 Hitachi High-Tech Science Corporation, Japan).
Conflicts of interest
The authors declare no conflicts of interest.
Acknowledgements
This work is supported by the National Natural Science Foundation of China (51473030, 51503028 and 51673037), the Shanghai Rising-Star Program (16QA1400200), the Fundamental Research Funds for the Central Universities (2232019G-01), the Program for Professor of Special Appointment (Eastern Scholar) at Shanghai Institutions of Higher Learning (TP2016019), the State Key Laboratory for Modification of Chemical Fibers and Polymer Materials, Donghua University (KF1824).
Notes and references
- M. L. Hammock, A. Chortos, B. C. Tee, J. B. Tok and Z. Bao, Adv. Mater., 2013, 25, 5997–6038 CrossRef CAS PubMed.
- T. H. Chang, K. Li, H. Yang and P. Y. Chen, Adv. Mater., 2018, 30, e1802418 CrossRef PubMed.
- Y. Li, Z. Zhu, J. Yu and B. Ding, ACS Appl. Mater. Interfaces, 2015, 7, 13538–13546 CrossRef CAS PubMed.
- Y. Li, F. Yang, J. Yu and B. Ding, Adv. Mater. Interfaces, 2016, 3, 1600516 CrossRef.
- X. Wang, J. Yu, G. Sun and B. Ding, Mater. Today, 2016, 19, 403–414 CrossRef CAS.
- Y. Si, Z. Zhang, W. Wu, Q. Fu, K. Huang, N. Nitin, B. Ding and G. Sun, Sci. Adv., 2018, 4, eaar5931 CrossRef PubMed.
- H. Gu, W. Fan and T. Liu, Nanoscale Horiz., 2017, 2, 277–283 RSC.
- S. Jiang, B. C. Ma, W. Huang, A. Kaltbeitzel, G. Kizisavas, D. Crespy, K. A. I. Zhang and K. Landfester, Nanoscale Horiz., 2018, 3, 439–446 RSC.
- J. Zhao, X. Wang, L. Liu, J. Yu and B. Ding, ACS Appl. Mater. Interfaces, 2018, 10, 30887–30894 CrossRef CAS PubMed.
- J. Sheng, M. Zhang, Y. Xu, J. Yu and B. Ding, ACS Appl. Mater. Interfaces, 2016, 8, 27218–27226 CrossRef CAS PubMed.
- F. Yang, Y. Li, X. Yu, G. Wu, X. Yin, J. Yu and B. Ding, RSC Adv., 2016, 6, 87820–87827 RSC.
- J. Sheng, Y. Xu, J. Yu and B. Ding, ACS Appl. Mater. Interfaces, 2017, 9, 15139–15147 CrossRef CAS PubMed.
- R. Bagherzadeh, M. Latifi, S. S. Najar, M. A. Tehran, M. Gorji and L. Kong, Text. Res. J., 2012, 82, 70–76 CrossRef CAS.
- J. Sheng, Y. Li, X. Wang, Y. Si, J. Yu and B. Ding, Sep. Purif. Technol., 2016, 158, 53–61 CrossRef CAS.
- D. Soto, A. Ugur, T. A. Farnham, K. K. Gleason and K. K. Varanasi, Adv. Funct. Mater., 2018, 28, 1707355 CrossRef.
- Q. Zhang, Q. Wang, J. Jiang, X. Zhan and F. Chen, Langmuir, 2015, 31, 4752–4760 CrossRef CAS PubMed.
- J. Wang, Y. Li, H. Tian, J. Sheng, J. Yu and B. Ding, RSC Adv., 2014, 4, 61068–61076 RSC.
- J. Jiang, G. Zhang, Q. Wang, Q. Zhang, X. Zhan and F. Chen, ACS Appl. Mater. Interfaces, 2016, 8, 10513–10523 CrossRef CAS PubMed.
- K. Han, L. Heng and L. Jiang, ACS Nano, 2016, 10, 11087–11095 CrossRef CAS PubMed.
- C. Zhu, J. Shi, S. Xu, M. Ishimori, J. Sui and H. Morikawa, Cellulose, 2017, 24, 2657–2667 CrossRef CAS.
- M. Ashraf, P. Champagne, C. Campagne, A. Perwuelz, F. Dumont and A. Leriche, J. Ind. Text., 2016, 45, 1440–1456 CrossRef CAS.
- S. Afzal, W. A. Daoud and S. J. Langford, J. Mater. Chem. A, 2014, 2, 18005–18011 RSC.
- T. Darmanin and F. Guittard, Prog. Polym. Sci., 2014, 39, 656–682 CrossRef CAS.
- T. Kamegawa, Y. Shimizu and H. Yamashita, Adv. Mater., 2012, 24, 3697–3700 CrossRef CAS PubMed.
- Z.-Y. Deng, W. Wang, L.-H. Mao, C.-F. Wang and S. Chen, J. Mater. Chem. A, 2014, 2, 4178–4184 RSC.
- W. Zhang, X. Lu, Z. Xin and C. Zhou, Nanoscale, 2015, 7, 19476–19483 RSC.
- C. R. Crick, J. C. Bear, A. Kafizas and I. P. Parkin, Adv. Mater., 2012, 24, 3505–3508 CrossRef CAS PubMed.
- G. R. Lomax, J. Mater. Chem., 2007, 17, 2775–2784 RSC.
- A. Mukhopadhyay and V. K. Midha, J. Ind. Text., 2008, 37, 225–262 CrossRef CAS.
- L. Zhang, Y. Li, J. Yu and B. Ding, RSC Adv., 2015, 5, 79807–79814 RSC.
- M. Rehan, N. A. M. Abdel-Wahed, A. Farouk and M. M. El-Zawahry, ACS Sustainable Chem. Eng., 2018, 6, 5911–5928 CrossRef CAS.
- P. Kumbhakar, A. Pramanik, S. Biswas, A. K. Kole, R. Sarkar and P. Kumbhakar, J. Hazard. Mater., 2018, 360, 193–203 CrossRef CAS PubMed.
- T. Viet Ha Tran and B.-K. Lee, J. Photochem. Photobiol., A, 2017, 338, 13–22 CrossRef.
- S. Kundu, A. Kafizas, G. Hyett, A. Mills, J. A. Darr and I. P. Parkin, J. Mater. Chem., 2011, 21, 6854–6863 RSC.
- J. Song, X. Wang, J. Yan, J. Yu, G. Sun and B. Ding, Sci. Rep., 2017, 7, 1636 CrossRef PubMed.
Footnote |
† Electronic supplementary information (ESI) available: experimental details; dmax of PAN@PM3635 NFM fabricated from various concentrations of PM3635; porosity of PAN@PM3635 NFM with different PM3635 concentrations; elemental mapping images of C, S, O and F of PAN@PM3635-2/ZnO-3 NFM; porosity of PAN@PM3635-2/ZnO NFM with different concentrations of ZnO NPs; under-water stability of PAN@PM3635-2/ZnO-3 NFM; comparison of comprehensive properties among PAN@PM3635-2/ZnO-3 NFM and fibrous membranes containing long perfluoroalkyl chain; absorbance spectra of MB dye under UV irradiation of PAN@PM3635-2/ZnO-2 NFM; XPS data of PAN@PM3635 membranes with various concentrations of PM3635; typical EDX results of PAN@PM3635-2/ZnO-3 NFM. See DOI: 10.1039/c8nh00480c |
|
This journal is © The Royal Society of Chemistry 2019 |
Click here to see how this site uses Cookies. View our privacy policy here.