DOI:
10.1039/C8NH00170G
(Review Article)
Nanoscale Horiz., 2019,
4, 77-98
Harnessing the unique properties of 2D materials for advanced lithium–sulfur batteries
Received
9th July 2018
, Accepted 29th August 2018
First published on 29th August 2018
Abstract
In the past decade, lithium–sulfur batteries have attracted tremendous attention owing to their high theoretical energy densities. The electrochemical performances of lithium–sulfur batteries are strongly dependent on the electrode materials. Among all the electrode material candidates, the application of 2D materials in lithium–sulfur batteries including a sulfur cathode, a lithium anode, a separator and/or an electrolyte has gained great success in enhancing their electrochemical performance by overcoming their intrinsic obstacles. Thus, it is necessary to summarize the relationships between the unique features of 2D materials and the electrochemical performances of lithium–sulfur batteries, guiding the development of next-generation lithium–sulfur batteries. In this review, we focus on recent advances in harnessing the unique properties of 2D materials, including their high surface area, 2D feature, high mechanical strength, plentiful active sites and functional groups to improve the electrochemical properties of sulfur cathodes, lithium anodes, electrolytes and/or separators, respectively. Finally, we propose possible directions and strategies for harnessing various properties of 2D materials to promote the development and applications of lithium–sulfur batteries.
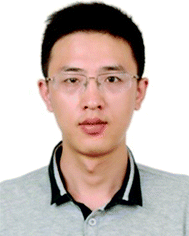
Bin Li
| Dr Bin Li is an Assistant Professor in School of Materials Science and Engineering at Beihang University. He received his BS degree and PhD degree in material science from Beihang University in 2009 and 2016 respectively. His research interests focused on electrochemical energy storage technology, including metallic lithium anode design and fabrication, sulfur cathode design and fabrication, and energy storage electrochemistry. |
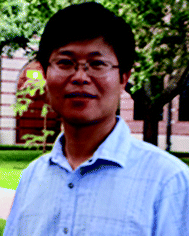
Shubin Yang
| Shubin Yang is a Professor in School of Materials Science and Engineering, Beihang University. He received his PhD from Beijing University of Chemical Technology in 2008 after carrying out a thesis on high-performance lithium ion batteries under the guidance of Prof. Huaihe Song. And then he pursued postdoctoral research with Prof. K. Muellen and P. M. Ajayan at Max Planck Institute for Polymer Research and Rice University respectively. His current research interests involve in graphene, MXenes, and other two-dimensional materials for energy storage and conversions. |
Introduction
Future methods of energy generation and consumption must be changed to reduce carbon emissions effectively, according to the provisions of the Paris climate agreement. Energy storage is essential for the wide usage of renewable energy, such as wind and solar energy, owing to their intermittence.
Among all energy storage technologies, electrochemical energy storage (EES) is the most important, since there are various types available based on different redox reactions or the Faraday effect.1–3 Although various electrochemical energy storage devices have been explored and applied in practice, they still hardly meet the increasing requirements of consumers. Hence, the development of an electrochemical energy storage device with high energy density, environmental friendliness and low cost is urgent.4–6
A lithium–sulfur battery, composed with both a high capacity sulfur cathode (1675 mA h g−1) and a metallic lithium anode (3860 mA h g−1), is a promising candidate for an electrochemical energy storage devices due to its high theoretical gravimetric and volumetric energy densities (2567 W h kg−1 or 2199 W h L−1).7–11 As presented in Fig. 1a, a lithium–sulfur battery is composed of a sulfur cathode, a lithium anode, an electrolyte and/or a separator, where the lithium ions transport through the electrolyte and the electrons flow through the external circuit to deliver power to an energy source or electrical appliance. The overall reaction of a lithium–sulfur battery takes place according to the following equations:12–14
| Overall: S8 + 16Li ⇌ 8Li2S | (1) |
| Cathode: S8 + 16Li+ + 16e− ⇌ 8Li2S | (2) |
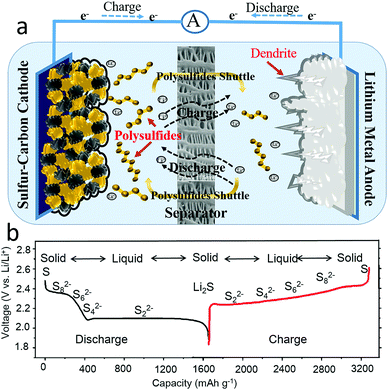 |
| Fig. 1 The electrochemical fundamentals of the lithium–sulfur battery. Typically, a lithium–sulfur battery is composed of a sulfur–carbon cathode, a metallic lithium anode, an electrolyte and a separator (a). The theoretical voltage profiles in an organic electrolyte indicate the complex electrochemical reaction process (b). | |
From the half reaction of the sulfur cathode, it can clearly be seen that sixteen electrons and sixteen lithium ions transfer during a discharge–charge process. The complex electrochemical process of the sulfur cathode is reflected in the theoretical voltage profile, as shown in Fig. 1b, where there are two voltage plateaus on the discharge profile and one voltage plateau on the charge curve. The full charge states of a cyclic α-octasulfur molecule (S8) and the full discharge products of Li2S or Li2S2 were insoluble in electrolytes, while the intermediate products of Sx2− (2 < x ≤ 8) were soluble in common organic electrolyte, causing two phase conversions from solid to liquid and liquid to solid.15 Meanwhile, the solid state S8 and Li2S or Li2S2 were essentially insulative, which means a high charge-transfer resistance.16,17 More importantly, these phase conversions show sluggish kinetics with a limitation step, which has not been clear until now. Thus, the fundamental issues of the sulfur cathode could be summarized in four categories: (1) insulation of active materials, (2) easy solubility of intermediate products in organic electrolytes, (3) large volume change, and (4) sluggish kinetics during the charge–discharge processes.
From the half reaction of the lithium anode, the charge process is a lithium plating process.18–22 Although the electrochemical reaction is simple, the deposition of the lithium anode is complicated, and can be roughly divided into three stages:23–25 formation of solid electrolyte interphase (SEI) films, nucleation and stable growth of lithium. The solid electrolyte interphase (SEI) films are generated spontaneously and instantaneously on the metal lithium surface when highly active lithium is in contact with an organic electrolyte, inducing the consumption of electrolyte and forming a barrier against lithium-ion transportation.26–28 In the initial lithium deposition, the nucleation sites were randomly generated and inhomogeneously dispersed on the electrode surface, affording uneven lithium dendrites. After the nucleation, lithium was continuously deposited on the nucleation sites and gradually formed coarse dendrites, which might pierce the separator, leading to the failure of the battery, and even fire or an explosion. Additionally, the lithium plating process will induce an infinite volume change in the lithium metal anode.29 Therefore, there are three issues with the lithium metal anode: (1) inhomogeneous nucleation sites on the electrode, (2) random growth of dendrites and (3) an infinite volume change in the lithium metal anode.
To overcome the above issues of both the sulfur cathode and the lithium anode, one efficient strategy is to construct hybrid electrode materials by tuning the synergistic effect of the distinct components.30 In the cathode, various sulfur-containing hybrids, including sulfur–carbonaceous materials (mesoporous carbons, carbon nanotubes, graphene, and carbon fibers), sulfur–polymers, and sulfur-transition metal compounds (MXenes), have been explored and have displayed improved cycle stabilities owing to the enhanced electrical conductivities of their overall sulfur cathodes and efficiently inhibited polysulfide shuttle.10 In the anode, some lithium-based hybrids such as lithium–graphene, lithium–MXenes and lithium–metal sponges have been developed to prevent the random growth of dendrites via materials with high mechanical strength, and to accommodate the volume change via porous hosts.31
In the past decade, publications on lithium–sulfur batteries have continuously increased, as summarized in Fig. 2. It is found that there are more than 4000 papers on hybrid electrode materials for lithium–sulfur batteries. Among these, there are a large number of hybrids involving two-dimensional (2D) or atomically layered materials. Hence, it is necessary to summarize the relationships between the unique features of 2D materials and the electrochemical performances of lithium–sulfur batteries, guiding the development of next-generation lithium–sulfur batteries. Therefore, we focus on recent advances in harnessing the unique properties of 2D materials to improve the properties of lithium–sulfur batteries. This review involves the following main sections: (1) various 2D materials and their advantages for lithium–sulfur batteries, classifying the roles of 2D materials in lithium–sulfur batteries; (2) harnessing the unique properties of 2D materials for sulfur cathodes, lithium anodes, electrolytes and separators, respectively; (3) summary and prospects, proposing possible directions for harnessing the various properties of 2D materials to promote the rapid development of lithium–sulfur batteries.
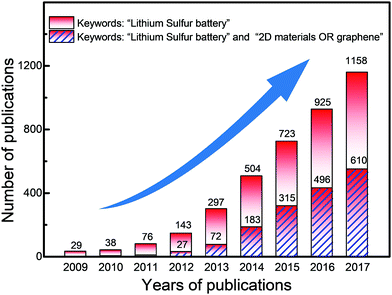 |
| Fig. 2 The number of recent publications about the lithium–sulfur battery, counted in the web of science using the keywords “lithium–sulfur battery”, and publications with the keywords “lithium–sulfur battery” and “2D materials or graphene”. These results indicate the continuous increase in interest in the lithium–sulfur battery and the application of 2D materials in the lithium–sulfur battery. | |
2D materials and their advantages for lithium–sulfur batteries
Since the discovery of graphene in 2004, various two-dimensional (2D) materials have been explored, including graphene derivatives,32–36 transition metal oxides (TMOs),32–39 dichalcogenides (TMDs),40–42 carbides/carbonitrides (MXenes),43–45 and black phosphorus (BP).46,47 These 2D materials usually possess strong covalent bonds in a plane and weak interlayer bonds (van der Waals' forces).48,49 Owing to their atomically layered structure, 2D materials commonly exhibit some unique features, including electronic, optical and mechanical properties, holding great and promising potential in fundamental science and technological applications.50–53 When compared with traditional materials, the 2D materials exhibited unique properties of electric conductivity, flexibility, mechanical strength, and high surface area. With graphene as a representative,54 its conductivity is ∼10
000 cm2 V−1 s−1 at room temperature, its mechanic strength is ∼1 TPa and its theoretical surface area is 2630 m2 g−1. Moreover, the 2D materials possess flexibility and the feature of controllable assembly, ensuring more extensive applications. 2D materials have already been explored in the various fields of electronics,55–58 catalysis59–62 and energy storage.63–67 Therefore, corresponding to the inherited issues of the sulfur cathode and lithium anode, 2D materials exhibited innate advantages to simultaneously address these issues by creating hybrid electrodes with 2D materials (Fig. 3).
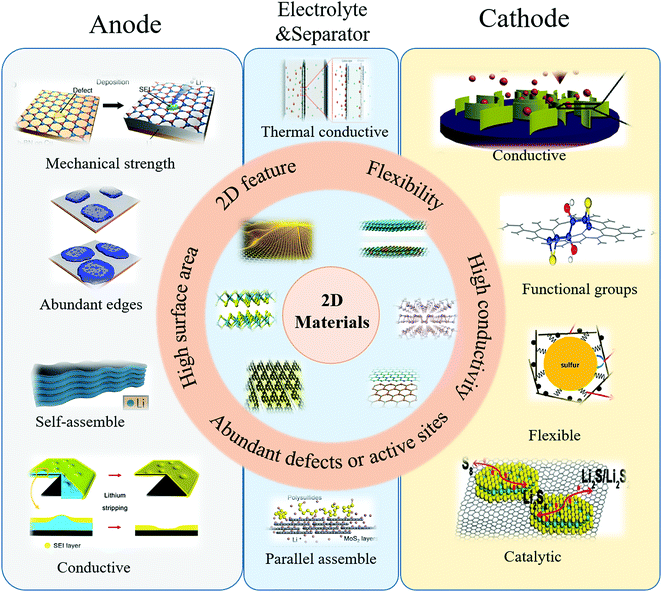 |
| Fig. 3 Overall schematic diagram of harnessing the unique properties of 2D materials for lithium–sulfur batteries, including application of 2D materials in the sulfur cathode, lithium anode and electrolyte and separators. | |
In the sulfur cathode, to address the issues of an insulative active material, soluble intermediate products, large volume change and sluggish kinetics, the unique properties of 2D materials have been harnessed: (1) high electric conductivity of 2D materials, including graphene and MXenes (Ti3C2X, X = F, OH), which were utilized to improve the electron transfer of isolated sulfur and Li2S; (2) abundant functional groups of hydroxyl, pyridine nitrogen, pyrrole nitrogen and defects on/in 2D materials, which were explored for inhibiting the polysulfide shuttle effect by anchoring polysulfides in the cathode; (3) good flexibility of 2D materials, which were employed to enwrap the active material to buffer the volume change; (4) the unique sulfur-catalytic property of 2D materials, which were developed to ameliorate the sluggish kinetics.
In the lithium anode, to tackle the random dendrite growth and infinite volume change of the metallic lithium anode, some properties of 2D materials were explored: (1) the plentiful edges of 2D materials, which were utilized as uniform nucleation seeds for controllable lithium deposition; (2) the high mechanical strength of 2D materials, which were employed to suppress the coarse dendrites, preventing the vertical growth of lithium dendrites; (3) the self-assembling feature of 2D materials, which were developed as lithium hosts to circumvent the infinite volume change.
In addition, to overcome the issues of the sulfur cathode and lithium anode, some unique properties of 2D materials were also harnessed in full cell configurations: (1) the high mechanical strength of 2D materials, which were exploited to suppress the lithium dendrites by adding 2D materials into gel electrolytes; (2) the tunable porous structure of 2D materials, which were employed as a matrix to create hybrid electrolytes to inhibit polysulfide shuttle; (3) the high thermal conductivities of 2D materials, such as boron nitride, which were used as interlayers to inhibit lithium dendrite growth by guiding thermal dispersion; (4) the parallel self-assembly feature of 2D materials, which were utilized to obtain thin films as interlayers to inhibit polysulfide shuttle.
Harnessing the unique properties of 2D materials for sulfur cathodes
Improving electron transfer via high electric conductivity
The electronic conductivities of sulfur and the product Li2S are only 5 × 10−30 and 10−13 S cm−1, respectively, which dramatically hinder electron transfer during charge–discharge processes.68–70 In this regard, many conductive 2D materials, such as graphene and MXenes (Ti2C3), can efficiently promote charge transfer in overall electrodes composed of sulfur and 2D materials.71–80 Theoretically, the electronic conductivity of graphene is ∼10 000 cm2 V−1 s−1 at room temperature, which is significantly higher than that of traditional materials. The conductivity of graphene nanosheets is as high as that of copper, which is the material mainly used as the current collector in lithium-ion batteries.81–83 Owing to its outstanding conductivity, graphene has been introduced into the sulfur cathode to improve electron transportation and has replaced the traditional copper collector since the early 2010s. As shown in Fig. 4a, a sulfur composite was sandwiched between two graphene films, in which one acts as the current collector to improve the electron transportation and the other behaves like a barrier to suppress the polysulfide shuttle.84 The graphene nanosheets were closely assembled to form a continuous conductive layer, ensuring fast charge transfer in the electrode, as illustrated in Fig. 4b. Owing to the ideal sandwiched structure, the hybrid cathode exhibited improved electrochemical performances in terms of a high reversible capacity of over 1000 mA h g−1 based on the mass of sulfur and a good cycle stability up to 100 cycles (Fig. 4c). The improved electrochemical performances were mainly attributed to the enhanced conductivity of the hybrid cathode, as demonstrated by quantitative analysis of the electrochemical impedance spectroscopy (EIS). It is clear that the value of the charge-transfer resistance (Rct) of the hybrid cathode is only 52.6 Ω, which is much lower than the values for cathodes without graphene (∼1100.5 Ω) (Fig. 4d). To further harness the high electronic conductivity of graphene, our group developed graphene–sulfur nanowalls vertically aligned on a conductive substrate by an electrochemically controlled assembly method (Fig. 4e).85 During this electrochemically controlled assembly process, the graphene oxide was reduced to graphene, facilitating the fast transportation of electrons. The nanosized sulfur was impregnated into the gaps between the assembled graphene nanosheets, which were vertically connected to the collector, facilitating the fast transfer of electrons in the ideal cathode. When the graphene–sulfur nanowalls were applied as a cathode without any binder or additive, they exhibited an outstanding rate capability, retaining a reversible capacity of ∼410 mA h g−1 at a high rate of 8C (1C = 1672 mA h gsulfur−1) (Fig. 4f). Such a good rate capability of lithium–sulfur batteries should be ascribed to the excellent conductivity of graphene and their well-designed structure, facilitating the fast transfer of both electrons and ions. In addition to these mentioned representative works, a series of sulfur–graphene hybrids with different structures and morphologies have been developed and exhibited improved cycle stabilities by harnessing the high electron conductivity of graphene.
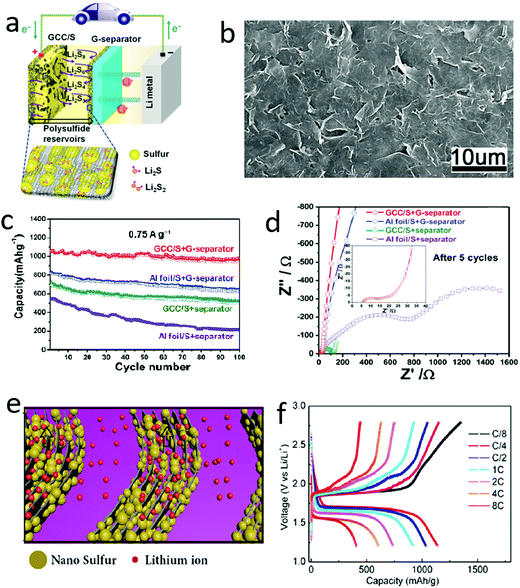 |
| Fig. 4 Schematic of using graphene nanosheets to improve the conductivity of a sulfur cathode (a) and the SEM image of the graphene–sulfur composite (b). (c) Comparison electrochemical results of the graphene–sulfur cathode illustrating that with the high conductivity of graphene, the reversible capacity and capacity retention were both enhanced. (d) The EIS spectrum of the GCC/S cathode indicated that the charge transfer resistance has been significantly reduced by introducing graphene into the electrode. Schematic of a vertical graphene–sulfur array for a lithium–sulfur battery (e) and the voltage profiles at various rates ranging from 8/C to 8C (f), indicating that such a graphene array enhanced the rate performance of lithium–sulfur batteries. (a–d) Reproduced with permission from ref. 84. Copyright 2014, Wiley-VCH. (e and f) Reproduced with permission from ref. 85. Copyright 2015, American Chemical Society. | |
Similar to graphene, other conductive 2D materials were also employed to address the insulation issue of sulfur electrodes. It is known that transition metal carbides, carbonitrides and nitrides (MXenes) are emerging 2D materials, and they also exhibit high electron conductivity (>103 S cm−1) due to the metallic phases of transition metals. As illustrated in Fig. 5a,86 the outside atomic layer of Ti atoms exhibits a metallic property, supplying excellent conductivity, and it can act as a fast electron transfer medium for active materials during the electrochemical processes. Moreover, the Ti2C possessed a typical accordion-like structure, which facilitated the hosting of the active sulfur (Fig. 5b). Due to its unique structure and high conductivity, the Ti2C–sulfur hybrid showed a high reversible capacity of more than 1450 mA h g−1 at C/20 and around 1000 mA h g−1 at 1C (Fig. 5c). Subsequently, there were several reports exploring MXene–sulfur composites, significantly enhancing the electrochemical performances by harnessing the high electron conductivity of MXenes. Apart from the ideal atomic layers, other non-layered 2D materials with high electronic conductivities, such as VN nanosheets, have also been developed to enhance the conductivity of sulfur-containing hybrids.87 Through kinetic analysis of the sulfur–VN–graphene hybrid, it was found that VN had a large influence on the electrochemical polarization and charge-transfer resistance of the sulfur cathode. The redox peaks of the CV curves of a sulfur cathode with VN/G were shifted towards the equilibrium potential, compared with a cathode with only RGO (Fig. 5d). And the voltage hysteresis of the sulfur cathode with VN/G was also lower than that of RGO (Fig. 5e). Hence, harnessing the electronic conductivities of various 2D materials is becoming a good strategy to address the insulating problem of sulfur, which can significantly improve the electrochemical performance. When compared with traditional conductive additives (carbon black, SUPER P Li), graphene exhibited lower dosage and higher electronic conductivity. Moreover, the 2D materials can easily build 3D conductivity networks to enhance the electron transfer in the entire electrode.
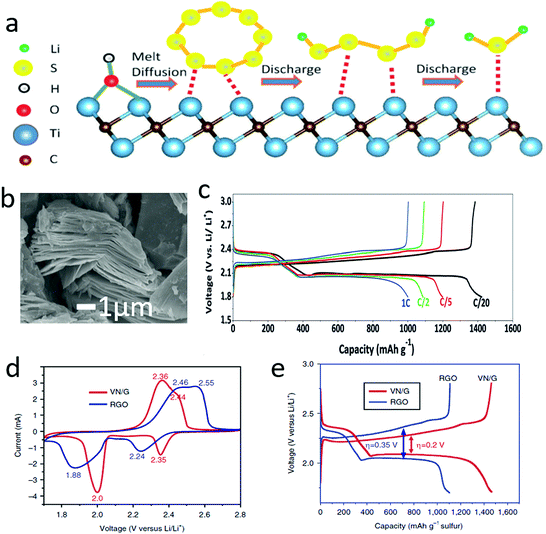 |
| Fig. 5 Schematic of Ti2C nanosheets for enhancing the conductivity of sulfur during the lithiation/dilithiation process (a). SEM image of Ti2C showing a typical accordion structure composed of nanosheets (b). The voltage profile of a lithium–sulfur battery with a Ti2C–S cathode with different current densities (c). The cyclic voltammetric (CV) curve of a lithium–sulfur battery with a VN/G–S cathode, indicating that the electrochemical polarization was significantly reduced according to the decreased overpotential (d). A voltage profile comparison of the lithium–sulfur battery indicated that the voltage difference between charge and discharge has been reduced by the VN/G–S cathode, thus enhancing the energy efficiency of the lithium–sulfur battery (e). (a–c) Reproduced with permission from ref. 86. Copyright 2015, Wiley-VCH. (d and e) Reproduced with permission from ref. 87. Copyright 2017, Nature Publishing Group. | |
Anchoring polysulfides via tunable functional groups and defects
As mentioned above, the dissolution and shuttle of polysulfides are inevitable during lithiation/delithiation processes, causing low coulombic efficiencies and fast capacity decay.88–94 To circumvent the polysulfide shuttle issue, one efficient strategy is to anchor the polysulfides into a matrix.95–102 In this respect, some 2D nanosheets commonly have high surface areas, plentiful defects, tunable doping atoms and abundant functional groups in the basal planes, with great potential for trapping polysulfides.103–109 Taking graphene as representative, there are various topological, point, large vacancy, line and Stone–Wales defects, which influence the distribution of electron clouds and the polarity of different areas. Moreover, these defects supply sites for grafting functional groups. For instance, hydroxyl, carboxyl, carbonyl, amino, and halogen sulfates can easily be grafted onto graphene oxide (GO) as a perfect sulfur/polysulfide immobilizer or immobilizer precursor.110–112 In 2011, a well-known study was undertaken by Prof. Zhang's research group, in which theoretical results revealed that sulfur could be strongly absorbed by the functional groups of graphene oxide (Fig. 6a).113 And they then demonstrated by soft X-ray absorption spectroscopy (XAS) analysis, that there was a strong chemical interaction between S and the hydroxyl group of GO (Fig. 6a). Thus, the GO–sulfur cathode showed a high reversible capacity of 950 mA h g−1 at 0.1C, and a good cyclic stability of 50 cycles without obvious capacity decay (Fig. 6b). Distinguishing them from traditional materials, 2D materials can supply abundant sulfur anchored sites in the basal 2D planes. For example, some functionalized graphenes with pyrrole-like or pyridine-like nitrogen atoms were explored and showed highly negative electron donor features (Fig. 6c).114 The nitrogen atoms in graphene provided efficient sites for anchoring polysulfides, which significantly improved the long cycling stability and high rate capability of the sulfur cathode (Fig. 6d).
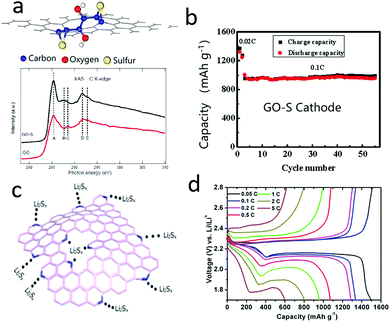 |
| Fig. 6 Schematic of the oxygen functional group on graphene oxide which chemically absorbs sulfur and the detection of the functional group (a). The cycling performance of the GO–S cathode indicated that the GO could efficiently anchor polysulfide in the cathode (b). Schematic of the anchoring effect of the nitrogen atoms which are doped on graphene, showing that the polysulfide was absorbed on the graphene (c). The voltage profile of an NG–S cathode showing an improved chemical performance (d). (a and b) Reproduced with permission from ref. 113. Copyright 2011, American Chemical Society. (c and d) Reproduced with permission from ref. 114. Copyright 2014, American Chemical Society. | |
Similar to functionalized graphene, MXenes are 2D materials with tunable functional groups, including hydroxyl and halogen, which have also been developed as a polysulfide riveting matrix. As shown in Fig. 7a and b, the polysulfides were closely dispersed on the MXene (Ti3C2Tx, T = –OH, –F) nanosheets with a crumpled structure and doped nitrogen atoms due to their strong interaction via reverse polarization.115 These defects and doped nitrogen atoms exhibited higher polarity than the original MXenes, and were more attractive to the polysulfides. This could be further demonstrated, as shown in Fig. 7c, where the color of the highly concentrated polysulfide solution faded rapidly with the absorption of N doped crumpled MXene (Fig. 7c). Thus, the hybrid cathode composed of sulfur and N doped crumpled MXene exhibited a good cycle stability up to 200 cycles (more than 900 mA h g−1 at 0.2C). More systematic investigations were achieved by Zhang and his co-workers, using a first-principles method to calculate the adsorption energies of the polysulfides Li2S8, Li2S6, Li2S4 on various two-dimensional layered materials, such as V2O5, MoO3, TiS2, ZrS2, VS2, NbS2, MoS2, TiCl2, and ZrCl2 (Fig. 7d and e).116 By analysing the interaction and electronic structure between polysulfides and layered materials, including configuration distortion, binding strength, and charge transfer, it was found that the appropriate adsorption of Li2Sn could prevent polysulfide shuttle while the overly strong binding strength could cause the decomposition of Li2Sn species. Thus, most of the layered 2D materials could be explored to inhibit polysulfide shuttle to enhance the cycling performance of sulfur cathodes. When compared with other materials, the atomic layers possess a high surface area and more edges, defects and functional groups for functionalization as polysulfide anchoring sites. These defects, edges and functional groups show more easily tunable adsorption energies than traditional materials, enhancing the electrochemical performances of sulfur cathodes.
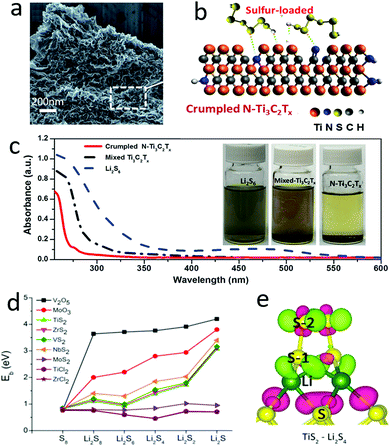 |
| Fig. 7 The SEM image of Ti3C2Tx–sulfur showing a typical nanosheet with a crumpled texture (a). Schematic of Ti3C2Tx anchoring polysulfides with chemical bonding (b). The UV-vis spectrum of a polysulfide solution with and without Ti3C2Tx absorption, showing a significant absorption effect by N–Ti3C2Tx (c). (d) The binding energy of 2D layered materials with polysulfides, indicating that most of the layered materials exhibited a high absorption ability for the polysulfides Li2S8, Li2S6, Li2S4. (e) Schematic of the interconnection of layered TiS2 with soluble Li2S4. (a–c) Reproduced with permission from ref. 115. Copyright 2018, Wiley-VCH. (d and e) Reproduced with permission from ref. 116. Copyright 2015, American Chemical Society. | |
Buffering volume change via the good flexibility of 2D materials
With gradual lithiation from original S8 to Li2S, the density of the active materials was reduced from 2.36 and 1.66 g cm−3, associated with a large volume expansion of up to 180%.117 This would cause a severe volume change issue when sulfur was employed as the cathode material for lithium–sulfur batteries.118–124
To alleviate or solve this issue, many researchers are focusing on harnessing the good flexibility of 2D nanosheets to generate a series of 2D nanosheet-wrapped sulfur hybrids.125–127 For example, graphene covered sulfur particles were first explored by Dai's group (Fig. 8a and b), when the volume change was efficiently accommodated, leading to an improved cycle stability up to 50 cycles (Fig. 8c).128 Following this strategy, multi-layered graphene shells were initially fabricated by Prof. Amine and his co-workers via a facile reaction between burning metallic Mg and CO2, and then utilizing the product as a host to encapsulate sulfur.129 Interestingly, owing to the hierarchical structure, the traditional α-octasulfur molecule in this hybrid was partially converted to small sulfur molecules of S2 and S4, allowing the coexistence of different sulfur species in the graphene nanocages (Fig. 8d and e). Coupled with this good effect to buffer the volume change of the active materials during the charge–discharge process, a high reversible capacity of 1420 mA h g−1 and a good cycling stability up to 100 cycles were achieved (Fig. 8f).
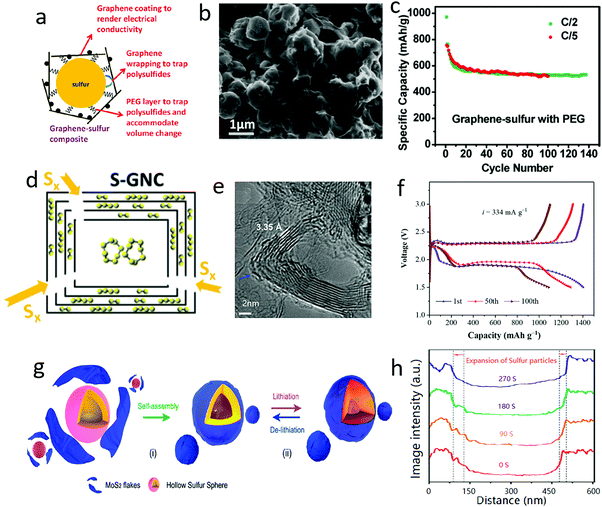 |
| Fig. 8 Schematic illustrating a sulfur particle wrapped in graphene oxide with the help of PEG (a). The SEM image of G@S (b). The electrochemical performance of a G@S cathode (c). Schematic of a sulfur–graphene nanocages (S–GNC) composite with the inner cavity of the GNC partially filled with S8 and the graphene layers encapsulating smaller S2 and S4 (d). TEM image of graphene nanocages, illustrating the nanocage structure of the graphene (e). The voltage profile of an S–GNC composite cathode (f). Schematic of sulfur wrapped with MoS2 nanoflakes and its effect on buffering volume changes during the lithiation/delithiatium process (g). The volume change of the MoS2 wrapped sulfur nanoparticles during the lithiation process (h). (a–c) Reproduced with permission from ref. 128. Copyright 2011, American Chemical Society. (d–f) Reproduced with permission from ref. 129. Copyright 2018, Wiley-VCH. (g and h) Reproduced with permission from ref. 130. Copyright 2018, Wiley-VCH. | |
Apart from graphene, other 2D materials, such as MoS2 nanoflakes, were also used to encapsulate sulfur particles (Fig. 8g), which could be clearly demonstrated by in situ transmission electron microscope (TEM) analysis.130 The in situ TEM observations showed that the volume expansion of MoS2-coated sulfur increased by around 33 to 48% during the lithiation process (Fig. 8h), significantly lower than the theoretical value of 80%. MoS2 nanoflakes played a good role in buffering the volume change of sulfur, leading to a very high capacity of 1660 mA h g−1 in the initial cycles and a long cycle life of up to 1000 cycles. Distinguishing them from traditional bulk materials, the outstanding flexibility of 2D materials afforded unique tunable encapsulation and hierarchical porous structures as hosts for sulfur.
Enhancing the multi-step conversion reactions via the sulfur-catalytic property of 2D materials
During the charge and discharge process, there exist electrochemical conversions between sulfur and lithium sulfides, associated with double phase conversions and multi electron transfer, which are the essence of the sluggish kinetics of the sulfur cathode.131–136 To accelerate the electrochemical conversion process, metal-based catalysts, such as Pt and Ni on graphene, were initially induced into the sulfur cathode, as shown in Fig. 9a, in which Pt could obviously catalyze the conversion process of dissolving long-chain polysulfides to short-chain polysulfides and subsequent products.137 The exchange current densities (i0) of the Pt/graphene electrodes were 3.18 mA cm−2 for the cathodic process and 0.29 mA cm−2 for the anodic process, which were twice as high as those of a pristine graphene electrode (1.18 mA cm−2 for the cathodic process and 0.17 mA cm−2 for the anodic process), indicating the enhancement in polysulfide conversion rate (Fig. 9b). Thus, the utilization ratios of active materials were greatly increased and the shuttle effect was significantly restricted, leading to a 40% specific capacity enhancement, and 99.3% Coulombic efficiency at a current rate of 0.2C and good stability over 100 cycles.
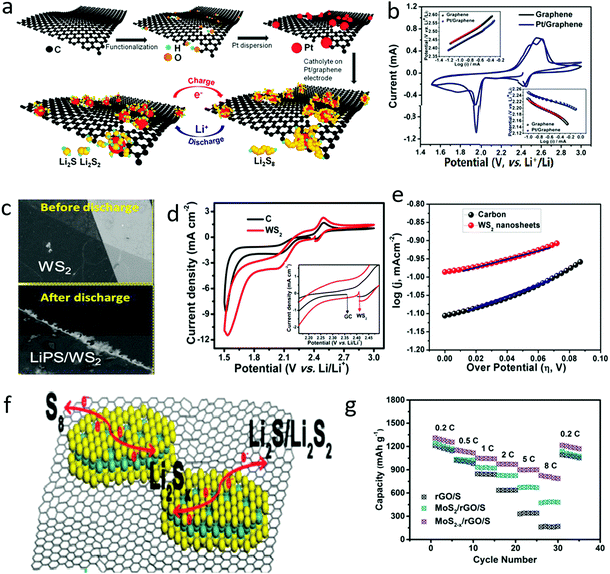 |
| Fig. 9 Schematic of the preparation of G–Pt and its interaction with PS during the charge/discharge process of an Li–S battery (a). The cyclic voltammetric (CV) curve of a sulfur cathode with G and G–Pt, indicating the improvement in the sluggish kinetics of polysulfide conversion (b). The SEM image of WS2 nanosheets before and after discharge, showing that the polysulfide was deposited on the edge of the nanosheets (c). The electrochemical behavior of electrochemicals with electrocatalysts of WS2 indicating the enhanced conversion process (d and e). Schematic of defect abandoned MoS2 nanosheets on graphene for accelerating the electrochemical conversion of polysulfide (f). A comparison of electrochemical performance indicated that the improved conversion process is beneficial for the rate performance of lithium–sulfur batteries (g). (a and b) Reproduced with permission from ref. 137. Copyright 2015, American Chemical Society. (c–e) Reproduced with permission from ref. 138. Copyright 2017, American Chemical Society. (f and g) Reproduced with permission from ref. 139. Copyright 2017, Royal Society of Chemistry. | |
The 2D materials commonly exhibited high electrochemical activities due to abundant edges and plentiful defects, where the electron transfer is twice as strong as the bulk counterparts. Furthermore, the edges of the 2D materials can even change the pathway of electron transfer. Thus, various 2D materials have been developed as electrocatalysts for sulfur cathodes. For example, 2D transition metal sulfides, such as WS2 and MoS2, have also shown catalytic properties for polysulfide conversion. The edge-enriched 2D WS2 and MoS2 showed higher activity than their bulk counterparts. As demonstrated by in situ spectroscopic and microscopic analysis, higher order liquid polysulfides were initially adsorbed at the edges of thin monolayer/few-layer TMDs and then subsequently converted to lower order solid species (Fig. 9c), leading to high electrocatalytic activity and low polarization (Fig. 9d and e).138 More specifically, the reduction and oxidation redox currents (Ipc and Ipa) of the WS2 electrode were 11.5 and 2.35 mA, respectively, which were higher than those of a carbon electrode (8.5 and 1.71 mA). More importantly, the exchange current density of the WS2 electrode was 11.8 × 10−3 mA cm−2, higher than that of a carbon electrode (8.5 × 10−3 mA cm−2), leading to significantly enhanced fast electrochemical reaction behavior. Therefore, the sulfur cathode with a WS2 catalyzer delivered a reversible capacity of 590 mA h g−1 at a high rate of 0.5C and long-term stability over 350 cycles.
Similarly, a MoS2–graphene composite was also introduced into a sulfur cathode, where the MoS2 benefited the acceleration of the conversion of polysulfides and the graphene matrix contributed to the fast electron transfer (Fig. 9f).139 Thus, by adding only 4 wt% MoS2−x/rGO into the sulfur cathode, the capacity of the cathode could be stabilized at 826.5 mA h g−1 at a high rate of 8C, almost 5 times that of a sulfur cathode with graphene alone (Fig. 9g). In this manner, various 2D materials, such as Ti3C2Tx, were also introduced into a sulfur cathode to further address the sluggish kinetics and to enhance the electrochemical performance of sulfur cathodes. Moreover, these 2D materials possessed more high-energy sites, such as edges and defects, showing higher catalytic activity to accelerate the conversion of polysulfides.
Harnessing the unique properties of 2D materials for lithium anodes
Promoting the uniform nucleation via the plentiful edges of 2D materials
To circumvent the lithium dendrite issue, one efficient strategy is to control the uniform nucleation of lithium by employing some metal seeds (Au, Ag, Zn), diamond or 2D materials with plentiful edges and defects.140–146 At the edges of conductive 2D materials, the charge concentration could induce lithium ion accumulation, facilitating the formation of initial nucleation seeds. Similarly, the defects, vacancies and distortions in 2D materials also have high energy to absorb the solvated lithium ions, leading to the accumulation of lithium in the defects. Therefore, graphene with plentiful edges and defects could be exploited as nucleation sites for guiding lithium deposition.147–149 As demonstrated by Lee and his co-workers, lithium was firstly nucleated at the edges of graphene, and then continuously deposited around the graphene islands (Fig. 10a–e).147 This was attributed to the small amount of lithium ions inserted into the graphene, acting as nucleation seeds. Thus, the lithium anode exhibited a long cycling stability over 100 cycles with a flat voltage profile (at a current density of 2 mA cm−2). Very recently, the graphene with plentiful edges could be produced on the conductive carbon fibers by a chemical vapor deposition (CVD) approach, as shown in Fig. 10f and g.148 These edges could serve as seeds, guiding uniform Li deposition into the pores of edge-enriched graphene networks. This hybrid lithium anode exhibited a long lifespan of 1000 cycles with a Coulombic efficiency of 99.7%.
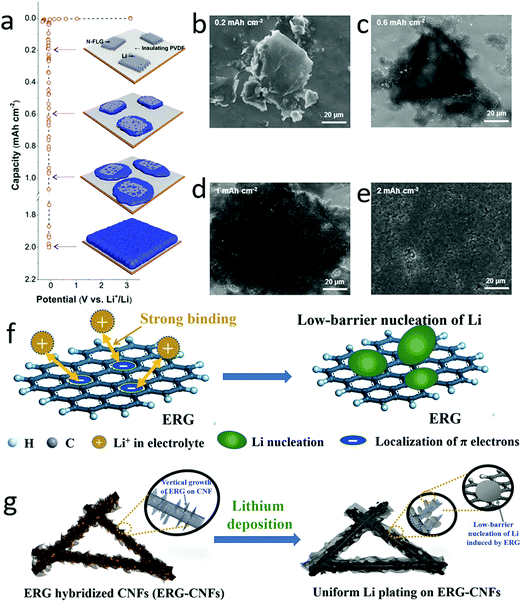 |
| Fig. 10 Employment of graphene edges as nucleation seeds for lithium deposition. Schematic of few-layered nitrogen doped graphene on PVDF as nucleation sites for regulating lithium deposition (a). The SEM images of lithium deposited on the electrode with different graphene nucleation seeds, indicating that the lithium was gradually deposited without dendrite growth (b–e). Schematic of the localization of π electrons on graphene for inducing lithium nucleation (f). Schematic of edge-rich graphene hybridized CNFs for dendrite-free lithium deposition (g). (a–e) Reproduced with permission from ref. 147. Copyright 2016, American Chemical Society. (f and g) Reproduced with permission from ref. 148. Copyright 2018, Wiley-VCH. | |
Suppressing dendrite growth via the high mechanical strength of 2D materials
Many researchers have demonstrated that the additional high mechanical strength layers of protective films could suppress the growth of lithium dendrites.150–154 2D materials were employed as the additional layers due to their unique advantages of high strength, ultrathin structure and assembly features. As demonstrated by Cui and his co-workers, hexagonal boron nitride (h-BN) nanosheets were ideal alternatives to protect the lithium anode (Fig. 11a).155 The atomic h-BN layer coated on anode current collectors not only suppressed the growth of lithium dendrites but also prevented the erosion of metallic lithium in organic electrolytes (Fig. 11a). When h-BN protection was applied for a lithium anode, it was found that the deposited lithium was sandwiched between the h-BN protective layers and the current collector. The protected anode showed smooth lithium deposition during the lithium stripping/plating processes due to the outstanding mechanical strength and chemical stability of the h-BN protective layers. The h-BN coated lithium anode exhibited stable cycling over 50 cycles and a high Coulombic efficiency of ∼97%. Similarly, a graphene protection layer was fabricated on a metallic lithium anode by spraying a graphene oxide suspension onto the lithium surface, in which the graphene oxide was reduced by the highly active metallic lithium and assembled as a thin film on the electrode surface (Fig. 11b).156 As a consequence, the obtained graphene protected lithium anode exhibited a high stability up to 1000 cycles at a current density of 5 mA cm−2 in a symmetrical cell, and also showed an ultralong lifespan of 300 cycles in an Li–LiPF6 full cell with a carbonate electrolyte (Fig. 11c). Besides h-BN and graphene nanosheets, various 2D materials, such as silicene, germanene, stanene, phosphorene, SnS, and SnSe, have also been regarded as good protective layers for lithium anodes, which were investigated theoretically and systematically by Zhang and his co-workers by first-principles calculations.157 It was demonstrated that the mechanical strength, defect pattern and crystalline structure of 2D materials have a significant effect on the electrochemical performance of lithium anodes.
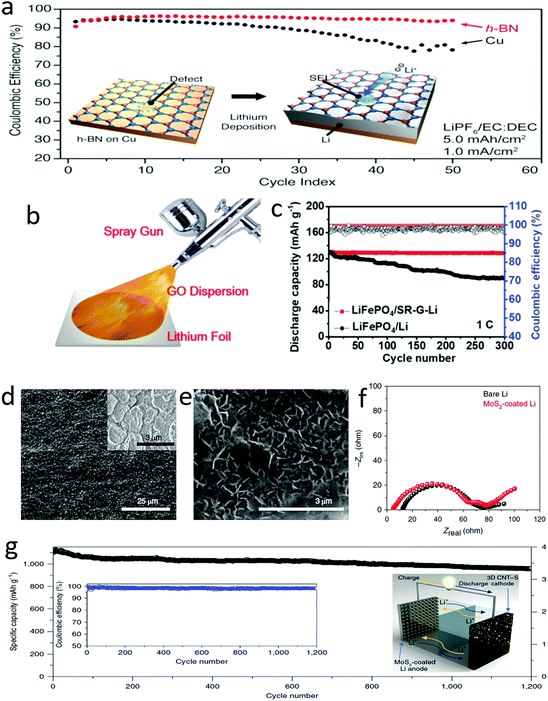 |
| Fig. 11 Suppressing lithium dendrites by using 2D materials as a protective layer. Schematic of an atomic thickness BN layer for suppressing lithium dendrite growth and the corresponding electrochemical performance (a). Schematic of the fabrication of the G protected films on lithium foil (b). The cycling stability of a full cell with a G–Li anode (c). SEM images of MoS2 layer and lithiation MoS2 layer on lithium metal (d and e). The comparison results of the EIS spectra of MoS2 coated Li and bare Li, indicating that the MoS2 coating did not increase the charge transfer resistance of the lithium anode (f). The electrochemical performance of an MoS2 coated Li anode with a sulfur cathode as the counter electrode (g). (a) Reproduced with permission from ref. 155. Copyright 2014, American Chemical Society. (b and c) Reproduced with permission from ref. 156. Copyright 2018, Wiley-VCH. (d–f) Reproduced with permission from ref. 158. Copyright 2018, Nature Publishing Group. | |
Very recently, an ultrathin MoS2 film with a thickness of 10 nm enabled the efficient suppression of the growth of lithium dendrites (Fig. 11d–f).158 Such an ultrathin layer exhibited sufficient strength as high as that of a traditional protective layer of the thickness of micrometers, supplying the same function of suppressing the growth of dendrites. Thus, the MoS2-coated Li-metal anode exhibited a low voltage hysteresis at a high current density of 10 mA cm−2, and a threefold longer lifespan than that of a bare Li anode. If a full cell was composed of this protected lithium anode and a 3D carbon nanotube–sulfur cathode, it showed a high specific energy density of ∼589 W h kg−1 and a stable Coulombic efficiency of ∼98% for over 1200 cycles at 0.5C (Fig. 11g). Employing the 2D nanosheets as protective layers could significantly promote the application of a lithium anode in lithium-based batteries with high energy densities and a long-term stability up to 1200 cycles. The protective layers of a lithium anode composed with ultrathin 2D materials are superior to the protective layers composed of other materials due to their high strength and convenient lithium transfer pathway. Thus, a very thin protective 2D layer can efficiently suppress the growth of dendrites.
Circumventing infinite volume change via the self-assembly feature of 2D materials
Although the lithium anode existed in the full charge state, it gradually dissolved and was even exhausted in the full discharge state, showing an infinite volume change.29,159–161 To circumvent or eliminate the infinite volume change of the lithium anode, a series of porous materials, such as 3D metal foams,162–164 hollow carbon spheres,141,165 layered graphene oxide films166–170 and MXenes film,171,172 have been explored as hosts for metallic lithium. In particular, 2D materials such as graphene, graphene oxide and MXenes are ideal hosts, since they exhibit many unique properties, including light weight, high strength, chemical stability and self-assembly features. By harnessing their self-assembly nature, graphene oxide films with uniform and nanoscaled gaps could be generated. This film could react with pre-store lithium via a molten-infiltration strategy, affording a high lithium loaded Li–rGO composite (Fig. 12a–c).173 When using this composite as an anode, there is only a small volume change (∼20%) during the lithium plating/stripping processes, significantly buffering the volume change of the lithium anode. Hence, a high capacity retention and low voltage hysteresis were achieved with the hybrid lithium anode applied to lithium-based batteries.
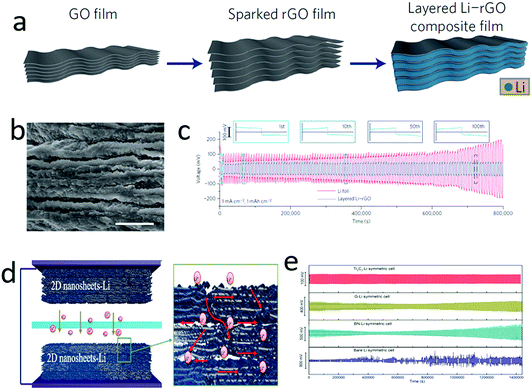 |
| Fig. 12 Graphene was explored as the host for a lithium anode. Schematic illustrating the fabrication process of layered lithium–graphene (Li–G) composites (a). The SEM image of the layer structured Li–G (b). The voltage profile of a symmetric Li–G electrode, showing a low and stable voltage–time curve (c). Schematic illustrated the Ti3C2 nanosheets as a host for a metallic lithium anode (d). The electrochemical performance of several nanosheets–Li anode (e), indicating that the nanosheets host is helping the cycling stability of the lithium anode and the Ti3C2 nanosheets achieve the highest performance. (a–c) Reproduced with permission from ref. 173. Copyright 2016, Nature Publishing Group. (d and e) Reproduced with permission from ref. 171. Copyright 2017, Elsevier. | |
Owing to the lithiophobic feature of most 2D materials with molten lithium, it was very difficult to realize a hybrid between lithium and 2D materials. Very recently, our group developed a facile method to roll and fold lithium foil with various 2D nanosheets, efficiently solving their lithiophobic problem (Fig. 12d).171 In this manner, a series of lithium-2D nanosheet composites were obtained, including Ti3C2 nanosheet–Li, BN nanosheet–Li, and graphene–Li. In these hybrids, the lithium deposition was confined in the nanoscaled gaps of the 2D nanosheets. Owing to the high electron conductivity and abundant functional groups on Ti3C2 nanosheets, lithium could homogeneously nucleate between the gaps of MXenes, and then continuously grow to a uniform film, as demonstrated by in situ TEM observation. Consequently, a symmetric cell configured with Ti3C2 MXene–lithium electrodes exhibited an ultralow voltage hysteresis of 32 mV at 1 mA cm−2 after 200 cycles (Fig. 12e).
Harnessing the unique properties of 2D materials for electrolytes and separators of lithium–sulfur batteries
Achieving gel-based electrolytes to suppress lithium dendrites via the high mechanical strength of 2D materials
Although gel electrolytes have a certain mechanical strength to resist dendrite growth, the lithium dendrite growth still pierces the electrolytes and separators.150,151,174–177 According to Newman's analysis, if the strength (shear modulus) of a gel-based electrolyte was less than 1.8GLi (GLi is the shear modulus of metallic lithium), the dendrite would easily grow vertically through the electrolyte and induce a short circuit in the batteries.178–180 Thus, harnessing the high mechanical strength of 2D nanosheets into the gel-based electrolyte becomes an efficient method for avoiding the vertical growth of lithium dendrites.181,182 For instance, Lee and his co-workers developed a functional gel electrolyte with 2D boron nitride nanoflakes (BNNFs) to achieve long cycling stability lithium metal batteries (LMBs) (Fig. 13a).183 The functional gel–electrolyte showed a porous surface and layered structure, in which BNNFs supplied sufficient lithium-ion transfer channels to facilitate lithium-ion transport through the electrolyte and an increased mechanical modulus of the gel electrolyte to suppress excessive dendrite growth (Fig. 13b and c). Thus, the optional functional gel electrolyte exhibited long stable cycling up to 1940 h at 1 mA cm−2, while that without BNNFs was only 178 h. Similarly, 2D graphitic carbon nitride (g-C3N4) was also added into a gel electrolyte to enhance the electrochemical performance of the lithium metal anode (Fig. 13d and e).184 In the traditional di(ethylene glycol)dimethyl ether based gel electrolyte, the g-C3N4 nanosheets were added to increase mechanical strength. Based on the obtained g-C3N4–gel electrolyte, the lithium symmetrical cell exhibited a remarkable electrochemical performance in terms of long cycling stability at a high reversible capacity of 6 mA h cm−2 and a low voltage gap of less than 100 mV at a current density of 2 mA cm−2 (Fig. 13f and g).
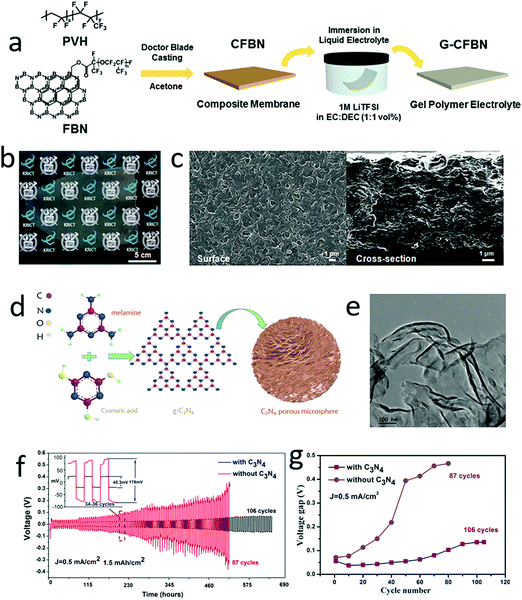 |
| Fig. 13 Schematic of the preparation of functional boron nitride (FBN) enhanced gel polymer electrolyte (a). The optical graph of FBN enhanced gel polymer electrolyte exhibited a semitransparent electrolyte (b). The SEM image of the surface and section of the gel polymer electrolyte (c). Schematic of the synthesis of C3N4 porous microspheres (d). The TEM image of the C3N4 nanosheets (e). The electrochemical performance of an Li–Li symmetrical battery with C3N4 enhanced gel polymer electrolyte, indicating a high cycling stability of the battery with C3N4 enhanced gel electrolyte (f). The voltage gap of the symmetrical battery during the charge and discharge process (g). (a–c) Reproduced with permission from ref. 183. Copyright 2017, Royal Society of Chemistry. (d–g) Reproduced with permission from ref. 184. Copyright 2017, American Chemical Society. | |
Creating hybrid electrolytes to inhibit polysulfide shuttle via the tunable porous structure of 2D materials
Very recently, a type of hybrid electrolyte with a liquid electrolyte and solid matrix has been developed for lithium–sulfur batteries for simultaneously suppressing dendrite growth and polysulfide shuttle.185,186 For instance, a mesoporous film composed of sandwich-like silica–graphene nanosheets was employed as a hybrid electrolyte, which had good chemical stability, high mechanical strength and a high surface area (Fig. 14).187 The silica–graphene nanosheets showed mesopores with a diameter of about 2.8 nm, which efficiently prevented the polysulfide shuttle (Fig. 14d). And the porous structure supplied a large surface area for absorbing sufficient liquid electrolyte, ensuring high ionic conductivity (0.117 mS cm−1, as high as a liquid electrolyte). More importantly, the high-strength silica–graphene could efficiently inhibit lithium dendrite growth, leading to a long lifespan (Fig. 14c). With such hybrid electrolytes, the lithium–sulfur battery exhibited a high reversible capacity of over 800 mA h g−1 at 0.05C and slow capacity decay.
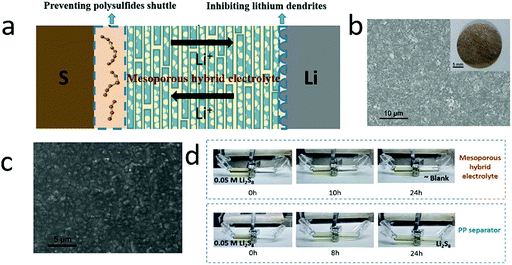 |
| Fig. 14 Schematic of silica–graphene hybrid electrolyte for simultaneously inhibiting lithium dendrite growth in the anode and suppressing polysulfide shuttle in the cathode (a). The SEM image (photograph) of the silica–graphene films (b). The surface SEM image of the lithium anode after 10 cycles, showing a smooth surface without dendrites (c). The optical graph of suppressing the polysulfide diffusion by the hybrid electrolyte (d). (a–d) Reproduced with permission from ref. 187. Copyright 2018, Wiley-VCH. | |
Modifying separators to suppress lithium dendrites via the high thermal conductivity of 2D materials
Modifying the separators was a direct method to protect the separators from piercing by lithium dendrites and to suppress the growth of dendrites. Taking advantage of their high thermal conductivity and sufficient mechanical strength, 2D materials were ideal candidates to protect the separators of lithium metal batteries (Fig. 15a).188 For example, BN films with a thickness of several micrometers were modified on the separator via a facile vacuum filtration method, showing an enhanced thermal conductivity, leading to a long lifespan of the lithium metal anode (Fig. 15b). In a conventional organic carbonate-based electrolyte, a cell with a BN modified separator exhibited a good stability and a high Coulombic efficiency of about 92% at a current density of 0.5 mA cm−2 over 100 cycles. Further, on the basis of BN nanosheets, Hu's group further modified the other side of the separator to simultaneously resist polysulfide shuttle (Fig. 15c and d).189 The designed trilayer separator was composed of a commercial polypropylene separator, BN sheets for suppressing dendrite growth and a carbon layer for resisting the polysulfide shuttle (Fig. 15e). By using such a trilayer separator for a lithium–sulfur battery, an outstanding specific capacity of 702 mA h g−1 at a rate of 4C, and a high capacity preserved over 250 cycles were achieved (Fig. 15f). The BN nanosheets efficiently suppressed the dendrite growth, leading to a stable function of the cell with high Coulombic efficiency and high cycling stability.
 |
| Fig. 15 An interlayer composed with 2D materials for suppressing lithium dendrite growth. Schematic of a BN interlayer for suppressing lithium dendrite growth and the optical graph of the BN modified separator (a). The temperature distribution images of the BN modified separator, indicated the BN interlayer facilitating the thermal conductivity of the lithium anode with dendrite growth (b). Schematic of the BN interlayer for preventing lithium dendrite growth and a carbon interlayer for inhibiting polysulfide shuttle (c). The optical graph of the modified separator (d). Schematic of the bifunctional separator for inhibiting the polysulfide shuttle and the optical graph of the shuttle process (e). The electrochemical performance of lithium–sulfur batteries with different interlayers modifying the separator (f). (a and b) Reproduced with permission from ref. 188. Copyright 2015, American Chemical Society. (d) Reproduced with permission from ref. 189. Copyright 2017, Nature Publishing Group. | |
Adding interlayers to inhibit polysulfides shuttles via the parallel self-assembly feature of 2D materials
To inhibit polysulfide shuttle, one efficient strategy is to confine the dissolving polysulfides in the cathode by creating a barrier between the cathode and the separator.190–194 For example, a positively charged amino group was grafted onto boron nitride nanosheets, which efficiently trapped and easily released the polysulfide anions during the charge/discharge process (Fig. 16a).195 Thus, a functional boron nitride–graphene thin film (FBN/G) with a thickness of several hundred nanometers was developed as an interlayer for lithium–sulfur batteries (Fig. 16b). This interlayer could not only entrap the polysulfide shuttle on the cathode surface but also decrease the charge transfer resistance, leading to an ultralong lifespan over 1000 cycles with capacity degradation of only 0.0067% and 0.0037% per cycle at 1C and 3C, respectively (Fig. 16c). Metal sulfides, such as MoS2, were also developed as an interlayer for trapping polysulfides.196–201 Distinguishing it from other polymer separators, the MoS2 surface could absorb a high density of lithium ions, which enhanced the lithium-ion conductivity, resulting in fast lithium diffusion and facile lithium transportation (Fig. 16d).202 Meanwhile, the dissolving polysulfides were blocked in the cathode due to the compact stacking structure, delivering a high initial capacity of 808 mA h g−1 and a low cycling decay of 0.083% per cycle in 600 cycles. Additionally, the Coulombic efficiency of a full cell with an MoS2 interlayer was maintained at over 99.5% during the 600 cycles, indicating that the polysulfide shuttle was efficiently prevented and the Li ion transfer was negligibly influenced.
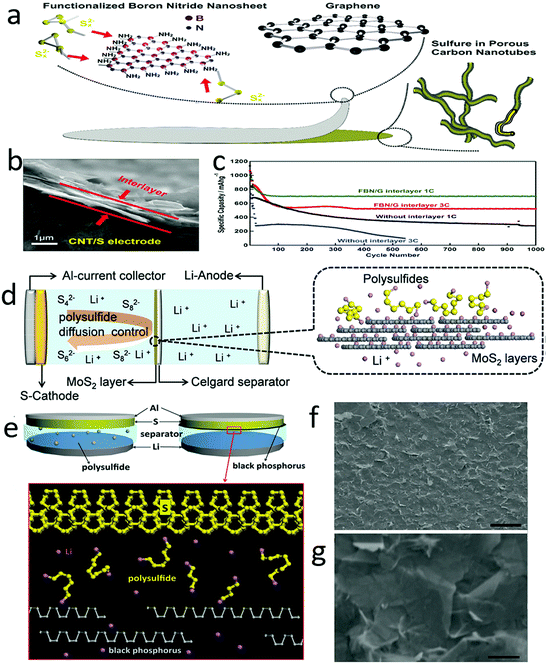 |
| Fig. 16 An interlayer for preventing polysulfide shuttle. Schematic of the interlayer which was composed of graphene and nitrogen doped boron nitride nanosheets (a). The SEM image of the sectional view of the interlayer, showing that the thickness of the interlayer was only hundreds of nanometers (b). The electrochemical performance of a lithium–sulfur battery with an interlayer, illustrating an improved reversible capacity, with capacity maintained as well as rate performance (c). Schematic of employing MoS2 as an interlayer for suppressing polysulfide diffusion (d). Schematic of using black phosphorus (BP) nanosheets as an interlayer for preventing polysulfide shuttle (e). The SEM images of BP films and BP nanosheets (f and g). (a–c) Reproduced with permission from ref. 195. Copyright 2017, Wiley-VCH. (d) Reproduced with permission from ref. 202. Copyright 2017, Wiley-VCH. (e–g) Reproduced with permission from ref. 203. Copyright 2016, Wiley-VCH. | |
Another sample was a black phosphorus nanosheets (BPs) modified Celgard separator, which was developed by Cui and his co-workers (Fig. 16e–g).203 The BPs interlayers possessed the advantages of strong physical adsorption and chemical bonding with the polysulfide shuttle, high electron conductivity and ultrahigh Li diffusivity, efficiently suppressing the polysulfide shuttle and facilitating fast lithium ion transfer. With the BPs modified separator, the lithium–sulfur cells exhibited increased specific capacity and enhanced cyclability, even in a cathode with a high sulfur loading. The improved electrochemical performance could be attributed to the BP interlayer, which provided strong bonding to lithium and sulfur.
Summary and prospects
In this review, we have summarized the recent progress in the application of 2D materials for lithium–sulfur batteries by harnessing their unique properties. The fundamental electrochemistry of the lithium–sulfur battery was introduced for analysing the essential issues of both the cathode and the anode. We presented some selective 2D materials with unique features and classified their applications in sulfur cathodes, lithium anodes and configurations of lithium–sulfur batteries. In the sulfur cathode, to solve the issues of poor electrical conductivity, polysulfide shuttle, large volume change and sluggish kinetics, we individually summarized the corresponding strategies for the perspectives of harnessing the unique properties of 2D materials, including high electron conductivity, tunable functional groups, good flexibility and the rich sulfur-catalytic property for improving the electrochemical performance. In the lithium anode, some features of 2D materials, such as abundant defects and edges, high mechanical strength and self-assembly features were harnessed to overcome the nucleation, random dendrite growth and infinite volume change problems of lithium anodes. In the full cell configuration, the high surface area, high strength, high thermal conductivity and parallel self-assembly feature of 2D materials were made use of in separators and electrolytes of lithium–sulfur batteries.
In each section, corresponding to the essential issue, only one or two unique properties were introduced, but the effects of the 2D materials on the electrode were not individual. The functions of 2D materials in lithium–sulfur batteries are integrated. For example, by applying functional graphene in a sulfur cathode,118 the conductivity significantly enhanced the conductivity of sulfur, the functional groups of graphitic nitrogen inhibited the polysulfide shuttle, the flexible property buffered the volume change, leading to the high performance of a sulfur–graphene hybrid cathode. When applying BN nanosheets in a lithium anode,187 not only can the high mechanical strength suppress the dendrite growth, but the functional groups can also guide the lithium ion flux. Thus, the application of 2D materials in lithium–sulfur batteries is an integrated utilization of 2D materials, and various unique properties were explored to enhance the electrochemical performance.
Lithium–sulfur batteries have made great progress, especially by exploring and harnessing the unique properties of 2D materials, but the application of lithium–sulfur batteries was still far from meeting expectations, including the unsatisfying rate capability of the sulfur cathode and the still uncontrollable lithium nucleation. Thus, there are still several aspects to be further explored and there is a need to harness the unique properties of 2D materials for lithium–sulfur batteries:
Harnessing the sulfur-catalytic properties of 2D materials or hybrids to further improve the rate capabilities of sulfur cathodes
In the case of the sulfur cathode, a full discharge process involves a sixteen-electron transfer, double phase conversion and multi-step processes, which leads to poor rate capability. The newest and most efficient characterization strategies should be explored and utilized to determine the electrochemical reaction process and clarify the kinetic limited steps, such as in situ atomic force microscopy (AFM), X-ray diffraction (XRD) and fine electrochemical testing methods. To directly accelerate the sluggish steps and to achieve high rate capabilities, one optimal strategy is to explore new and efficient catalysts and to apply them in lithium–sulfur batteries. Thus, further harnessing sulfur-catalytic 2D materials, such as transient metal sulfides with a 1T phase, tunable catalytic sites or high-energy active facets to achieve good high-rate capabilities is one promising direction.
Harnessing the hierarchical porous structure of 2D materials-built architectures to improve the loading of sulfur cathodes
The actual application of a lithium–sulfur battery requires a high energy density and long cycling stability, which means a high mass loading of sulfur in the cathode.204,205 However, most reported electrochemical performances of lithium–sulfur batteries were achieved with low active material loading (<2 mg cm−2), excess electrolytes and an extreme excess of lithium metal anode by assembling coin-type cells.206 To overcome the low sulfur loading, and meanwhile to maintain the diffusion of electrons and ions, one efficient strategy is still to harness the hierarchical porous structure of 2D material (graphene, MXenes)-built architectures to host more sulfur.
Tuning the active sites on 2D materials to guide the nucleation and growth of lithium
Although the growth of lithium dendrites can be partially suppressed by high-strength protective films, electrolytes or separators, uncontrollable lithium dendrite growth still exists and poses potential safety hazards. The uneven lithium nucleation during the initial deposition process is the root of the uncontrollable growth of lithium dendrites. Thus, inducing homogenously dispersed nucleation sites for guiding controllable lithium deposition is becoming the most efficient strategy, such as Au nanoparticles, diamonds and functional groups of –Ti and –N. Among all the nucleation seed candidates, 2D materials exhibited several advantages, like supplying more active sites, such as functional groups of –Ti and –N,207,208 and high energy facets and edges, possessing more anchoring sites for nucleation seeds, such as gold and silver. Thus, tuning the active sites on 2D materials to guide the nucleation and growth of lithium is one potential direction for solving the random growth of lithium dendrites.
Harnessing the high thermal conductivities of 2D materials to self-melt the growth of lithium dendrites
While the growth of lithium dendrites is still beyond control, one efficient remedial method is to eliminate the existing coarse lithium dendrites though a local thermal melt method. As demonstrated by Nikhil Koratkar,209 the existing lithium dendrites can be melted by external thermal annealing at around 60–80 °C. More specifically, by maintaining the lithium anode with dendrites at 70 °C for 3 days, the dendrites disappeared, leaving a smooth anode surface. 2D materials such as BN exhibited excellent thermal conductivity, and have been explored as a thermal conductivity interlayer to suppress the growth of lithium dendrites.210,211 However, the thermal conductivity of 2D materials has not been explored to eliminate lithium dendrites. Thus, harnessing the high thermal conductivities of 2D materials to prolong the lifespan of lithium–sulfur batteries may become a new resolution of problems in lithium anodes.
Conflicts of interest
There are no conflicts to declare.
Acknowledgements
This work was financially supported by National Key R&D Program of China (No. 2018YFB0104201) and National Science Foundation of China (No. 51702010, 51622203 and 51572007), and “Recruitment Program of Global Experts”.
Notes and references
- B. Dunn, H. Kamath and J. M. Tarascon, Science, 2011, 334, 928–935 CrossRef CAS PubMed.
- S. Chu and A. Majumdar, Nature, 2012, 488, 294–303 CrossRef CAS PubMed.
- Y. Liu, P. He and H. Zhou, Adv. Energy Mater., 2018, 8, 1701602 CrossRef.
- S. Chu, Y. Cui and N. Liu, Nat. Mater., 2017, 16, 16–22 CrossRef PubMed.
- D. Larcher and J. Tarascon, Nat. Chem., 2015, 7, 19–29 CrossRef CAS PubMed.
- J. B. Goodenough and Y. Kim, Chem. Mater., 2010, 22, 587–603 CrossRef CAS.
- H. Peng, J. Huang and Q. Zhang, Chem. Soc. Rev., 2017, 46, 5237–5288 RSC.
- A. Manthiram, Y. Fu and Y. Su, Acc. Chem. Res., 2012, 46, 1125–1134 CrossRef PubMed.
- P. G. Bruce, S. A. Freunberger, L. J. Hardwick and J. Tarascon, Nat. Mater., 2012, 11, 19–29 CrossRef CAS PubMed.
- Y. Yang, G. Zheng and Y. Cui, Chem. Soc. Rev., 2013, 42, 3018–3032 RSC.
- S. Zhang, K. Ueno, K. Dokko and M. Watanabe, Adv. Energy Mater., 2015, 5, 1500117 CrossRef.
- Q. Pang, X. Liang, C. Y. Kwok and L. F. Nazar, J. Electrochem. Soc., 2015, 162, A2567–A2576 CrossRef CAS.
- A. Manthiram, Y. Fu, S. Chung, C. Zu and Y. Su, Chem. Rev., 2014, 114, 11751–11787 CrossRef CAS PubMed.
- A. Rosenman, E. Markevich, G. Salitra, D. Aurbach, A. Garsuch and F. F. Chesneau, Adv. Energy Mater., 2015, 5, 1500212 CrossRef.
- Z. Yang, Z. Zhu, J. Ma, D. Xiao, X. Kui, Y. Yao, R. Yu, X. Wei, L. Gu, Y. Hu, H. Li and X. Zhang, Adv. Energy Mater., 2016, 6, 1600806 CrossRef.
- A. Manthiram, S. Chung and C. Zu, Adv. Mater., 2015, 27, 1980–2006 CrossRef CAS PubMed.
- D. Bresser, S. Passerini and B. Scrosati, Chem. Commun., 2013, 49, 10545–10562 RSC.
- D. Lin, Y. Liu and Y. Cui, Nat. Nanotechnol., 2017, 12, 194–206 CrossRef CAS PubMed.
- A. Kushima, K. P. So, C. Su, P. Bai, N. Kuriyama, T. Maebashi, Y. Fujiwara, M. Z. Bazant and J. Li, Nano Energy, 2017, 32, 271–279 CrossRef CAS.
- J. Tan, A. M. Tartakovsky, K. Ferris and E. M. Ryan, J. Electrochem. Soc., 2016, 163, A318–A327 CrossRef CAS.
- G. Bieker, M. Winter and P. Bieker, Phys. Chem. Chem. Phys., 2015, 17, 8670–8679 RSC.
- D. Lu, Y. Shao, T. Lozano, W. D. Bennett, G. L. Graff, B. Polzin, J. Zhang, M. H. Engelhard, N. T. Saenz, W. A. Henderson, P. Bhattacharya, J. Liu and J. Xiao, Adv. Energy Mater., 2015, 5, 1400993 CrossRef.
- N. Kittner, F. Lill and D. M. Kammen, Nat.
Energy, 2017, 2, 17125 CrossRef.
- J. M. Tarascon and M. Armand, Nature, 2001, 414, 359–367 CrossRef CAS PubMed.
- A. Manthiram, X. Yu and S. Wang, Nat. Rev. Mater., 2017, 2, 16103 CrossRef CAS.
- Y. Li, Y. Li, A. Pei, K. Yan, Y. Sun, C. Wu, L. Joubert, R. Chin, A. L. Koh, Y. Yu, J. Perrino, B. Butz, S. Chu and Y. Cui, Science, 2017, 358, 506–510 CrossRef CAS PubMed.
- M. D. Tikekar, S. Choudhury, Z. Tu and L. A. Archer, Nat. Energy, 2016, 1, 16114 CrossRef CAS.
- B. Wu, J. Lochala, T. Taverne and J. Xiao, Nano Energy, 2017, 40, 34–41 CrossRef CAS.
- A. Eftekhari, ACS Sustainable Chem. Eng., 2018 DOI:10.1021/acssuschemeng.7b04330.
- A. Eftekhari and D. Kim, J. Mater. Chem. A, 2017, 5, 17734–17776 RSC.
- B. Li, Y. Wang and S. Yang, Adv. Energy Mater., 2018, 8, 1702296 CrossRef.
- A. S. Childress, P. Parajuli, J. Zhu, R. Podila and A. M. Rao, Nano Energy, 2017, 39, 69–76 CrossRef CAS.
- R. Raccichini, A. Varzi, D. Wei and S. Passerini, Adv. Mater., 2017, 29, 1603421 CrossRef PubMed.
- M. Lotya, Y. Hernandez, P. J. King, R. J. Smith, V. Nicolosi, L. S. Karlsson, F. M. Blighe, S. De, Z. Wang, I. T. McGovern, G. S. Duesberg and J. N. Coleman, J. Am. Chem. Soc., 2009, 131, 3611–3620 CrossRef CAS PubMed.
- Y. Xue, Q. Zhang, W. Wang, H. Cao, Q. Yang and L. Fu, Adv. Energy Mater., 2017, 7, 1602684 CrossRef.
- R. Raccichini, A. Varzi, S. Passerini and B. Scrosati, Nat. Mater., 2015, 14, 271–279 CrossRef CAS PubMed.
- L. Cong, H. Xie and J. Li, Adv. Energy Mater., 2017, 7, 1601906 CrossRef.
- J. Xu, J. Zhang, W. Zhang and C. Lee, Adv. Energy Mater., 2017, 7, 30 Search PubMed.
- J. Mei, T. Liao, L. Kou and Z. Sun, Adv. Mater., 2017, 29, 1700176 CrossRef PubMed.
- Y. Liu, J. Wu, K. P. Hackenberg, J. Zhang, Y. M. Wang, Y. Yang, K. Keyshar, J. Gu, T. Ogitsu, R. Vajtai, J. Lou, P. M. Ajayan, B. C. Wood and B. I. Yakobson, Nat. Energy, 2017, 2, 17127 CrossRef CAS.
- Q. Yun, Q. Lu, X. Zhang, C. Tan and H. Zhang, Angew. Chem., Int. Ed. Engl., 2018, 57, 626–646 CrossRef CAS PubMed.
- Y. Gao, X. Wu, K. Huang, L. Xing, Y. Zhang and L. Liu, CrystEngComm, 2017, 19, 404–418 RSC.
- B. Anasori, M. R. Lukatskaya and Y. Gogotsi, Nat. Rev. Mater., 2017, 2, 16098 CrossRef CAS.
- J. Sun, H. Lee, M. Pasta, H. Yuan, G. Zheng, Y. Sun, Y. Li and Y. Cui, Nat. Nanotechnol., 2015, 10, 980–985 CrossRef CAS PubMed.
- L. Ding, Y. Wei, Y. Wang, H. Chen, J. Caro and H. Wang, Angew. Chem., Int. Ed., 2017, 56, 1825–1829 CrossRef CAS PubMed.
- J. Sun, G. Zheng, H. Lee, N. Liu, H. Wang, H. Yao, W. Yang and Y. Cui, Nano Lett., 2014, 14, 4573–4580 CrossRef CAS PubMed.
- M. R. Lukatskaya, B. Dunn and Y. Gogotsi, Nat. Commun., 2016, 7, 12647 CrossRef PubMed.
- M. F. El-Kady, Y. Shao and R. B. Kaner, Nat. Rev. Mater., 2016, 1, 16033 CrossRef CAS.
- E. Morales-Narváez, L. F. Sgobbi, S. A. S. Machado and A. Merkoçi, Prog. Mater. Sci., 2017, 86, 1–24 CrossRef.
- R. Fang, S. Zhao, S. Pei, X. Qian, P. Hou, H. Cheng, C. Liu and F. Li, ACS Nano, 2016, 10, 8676–8682 CrossRef CAS PubMed.
- M. Zhao, M. Sedran, Z. Ling, M. R. Lukatskaya, O. Mashtalir, M. Ghidiu, B. Dyatkin, D. J. Tallman, T. Djenizian, M. W. Barsoum and Y. Gogotsi, Angew. Chem., Int. Ed., 2015, 54, 4810–4814 CrossRef CAS PubMed.
- G. Zhou, E. Paek, G. S. Hwang and A. Manthiram, Nat. Commun., 2015, 6, 7760 CrossRef CAS PubMed.
- G. Li, J. Sun, W. Hou, S. Jiang, Y. Huang and J. Geng, Nat. Commun., 2016, 7, 10601 CrossRef CAS PubMed.
- A. Eftekhari and H. Garcia, Mater. Today Chem., 2017, 4, 1–16 CrossRef.
- C. S. Boland, U. Khan, G. Ryan, S. Barwich, R. Charifou, A. Harvey, C. Backes, Z. Li, M. S. Ferreira, M. E. Mobius, R. J. Young and J. N. Coleman, Science, 2016, 354, 1257–1260 CrossRef CAS PubMed.
- M. Pumera and Z. Sofer, Chem. Soc. Rev., 2017, 46, 4450–4463 RSC.
- F. Yi, H. Ren, J. Shan, X. Sun, D. Wei and Z. Liu, Chem. Soc. Rev., 2018, 47, 3152–3188 RSC.
- B. Radisavljevic and A. Kis, Nat. Mater., 2013, 12, 815–820 CrossRef CAS PubMed.
- M. R. Lukatskaya, S. Kota, Z. Lin, M. Zhao, N. Shpigel, M. D. Levi, J. Halim, P. Taberna, M. W. Barsoum, P. Simon and Y. Gogotsi, Nat. Energy, 2017, 2, 17105 CrossRef CAS.
- S. Navalon, J. R. Herance, M. Alvaro and H. Garcia, Chemistry, 2017, 23, 15244–15275 CrossRef CAS PubMed.
- J. Wang, D. Liu, H. Huang, N. Yang, B. Yu, M. Wen, X. Wang, P. K. Chu and X. Yu, Angew. Chem., Int. Ed., 2018, 57, 2600–2604 CrossRef CAS PubMed.
- F. Li, M. Xue, J. Li, X. Ma, L. Chen, X. Zhang, D. R. MacFarlane and J. Zhang, Angew. Chem., Int. Ed., 2017, 56, 14718–14722 CrossRef CAS PubMed.
- H. Liu, H. Tang, M. Fang, W. Si, Q. Zhang, Z. Huang, L. Gu, W. Pan, J. Yao, C. Nan and H. Wu, Adv. Mater., 2016, 28, 8170–8176 CrossRef CAS PubMed.
- X. Yu, S. Yun, J. S. Yeon, P. Bhattacharya, L. Wang, S. W. Lee, X. Hu and H. S. Park, Adv. Energy Mater., 2018, 1702930 CrossRef.
- J. Gu, Z. Du, C. Zhang, J. Ma, B. Li and S. Yang, Adv. Energy Mater., 2017, 7, 1700447 CrossRef.
- J. Gu, B. Li, Z. Du, C. Zhang, D. Zhang and S. Yang, Adv. Funct. Mater., 2017, 27, 1700840 CrossRef.
- M. Kühne, F. Paolucci, J. Popovic, P. M. Ostrovsky, J. Maier and J. H. Smet, Nat. Nanotechnol., 2017, 12, 895–900 CrossRef PubMed.
- G. Zhou, D. Wang, F. Li, P. Hou, L. Yin, C. Liu, G. Q. M. Lu, I. R. Gentle and H. Cheng, Energy Environ. Sci., 2012, 5, 8901–8906 RSC.
- C. Wang, X. Wang, Y. Yang, A. Kushima, J. Chen, Y. Huang and J. Li, Nano Lett., 2015, 15, 1796–1802 CrossRef CAS PubMed.
- L. Kong, B. Li, H. Peng, R. Zhang, J. Xie, J. Huang and Q. Zhang, Adv. Energy Mater., 2018, 1800849 CrossRef.
- W. Bao, D. Su, W. Zhang, X. Guo and G. Wang, Adv. Funct. Mater., 2016, 26, 8746–8756 CrossRef CAS.
- Y. Zhang, Z. Mu, C. Yang, Z. Xu, S. Zhang, X. Zhang, Y. Li, J. Lai, Z. Sun, Y. Yang, Y. Chao, C. Li, X. Ge, W. Yang and S. Guo, Adv. Funct. Mater., 2018, 1707578 CrossRef.
- X. Zhu, W. Zhao, Y. Song, Q. Li, F. Ding, J. Sun, L. Zhang and Z. Liu, Adv. Energy Mater., 2018, 1800201 CrossRef.
- N. Li, M. Zheng, H. Lu, Z. Hu, C. Shen, X. Chang, G. Ji, J. Cao and Y. Shi, Chem. Commun., 2012, 48, 4106 RSC.
- Y. C. Jeong, J. H. Kim, S. H. Kwon, J. Y. Oh, J. Park, Y. Jung, S. G. Lee, S. J. Yang and C. R. Park, J. Mater. Chem. A, 2017, 5, 23909–23918 RSC.
- Y. Fu, C. Zu and A. Manthiram, J. Am. Chem. Soc., 2013, 135, 18044–18047 CrossRef CAS PubMed.
- G. Tan, R. Xu, Z. Xing, Y. Yuan, J. Lu, J. Wen, C. Liu, L. Ma, C. Zhan, Q. Liu, T. Wu, Z. Jian, R. Shahbazian-Yassar, Y. Ren, D. J. Miller, L. A. Curtiss, X. Ji and K. Amine, Nat. Energy, 2017, 2, 17090 CrossRef CAS.
- G. Zhou, L. Yin, D. Wang, L. Li, S. Pei, I. R. Gentle, F. Li and H. Cheng, ACS Nano, 2013, 7, 5367–5375 CrossRef CAS PubMed.
- X. Yang, L. Zhang, F. Zhang, Y. Huang and Y. Chen, ACS Nano, 2014, 8, 5208–5215 CrossRef CAS PubMed.
- J. Xu, J. Shui, J. Wang, M. Wang, H. Liu, S. X. Dou, I. Jeon, J. Seo, J. Baek and L. Dai, ACS Nano, 2014, 8, 10920–10930 CrossRef CAS PubMed.
- A. Gupta, T. Sakthivel and S. Seal, Prog. Mater. Sci., 2015, 73, 44–126 CrossRef CAS.
- S. Chowdhury and R. Balasubramanian, Prog. Mater. Sci., 2017, 90, 224–275 CrossRef CAS.
- H. Sun, L. Mei, J. Liang, Z. Zhao, C. Lee, H. Fei, M. Ding, J. Lau, M. Li, C. Wang, X. Xu, G. Hao, B. Papandrea, I. Shakir, B. Dunn, Y. Huang and X. Duan, Science, 2017, 356, 599–604 CrossRef CAS PubMed.
- G. Zhou, S. Pei, L. Li, D. Wang, S. Wang, K. Huang, L. Yin, F. Li and H. Cheng, Adv. Mater., 2014, 26, 625–631 CrossRef CAS PubMed.
- B. Li, S. Li, J. Liu, B. Wang and S. Yang, Nano Lett., 2015, 15, 3073–3079 CrossRef CAS PubMed.
- X. Liang, A. Garsuch and L. F. Nazar, Angew. Chem., Int. Ed., 2015, 54, 3907–3911 CrossRef CAS PubMed.
- Z. Sun, J. Zhang, L. Yin, G. Hu, R. Fang, H. Cheng and F. Li, Nat. Commun., 2017, 8, 14627 CrossRef PubMed.
- D. Peramunage and S. Licht, Science, 1993, 261, 1029–1032 CrossRef CAS PubMed.
- M. Barghamadi, A. S. Best, A. I. Bhatt, A. F. Hollenkamp, M. Musameh, R. J. Rees and T. Ruether, Energy Environ. Sci., 2014, 7, 3902–3920 RSC.
- N. Li, Z. Weng, Y. Wang, F. Li, H. Cheng and H. Zhou, Energy Environ. Sci., 2014, 7, 3307–3312 RSC.
- L. Wang, Y. Wang and Y. Xia, Energy Environ. Sci., 2015, 8, 1551–1558 RSC.
- A. Jozwiuk, B. B. Berkes, T. Weiß, H. Sommer, J. Janek and T. Brezesinski, Energy Environ. Sci., 2016, 9, 2603–2608 RSC.
- R. Demir-Cakan, M. Morcrette, Gangulibabu, A. Gueguen, R. Dedryvere and J. Tarascon, Energy Environ. Sci., 2013, 6, 176–182 RSC.
- X. Tao, J. Wang, Z. Ying, Q. Cai, G. Zheng, Y. Gan, H. Huang, Y. Xia, C. Liang, W. Zhang and Y. Cui, Nano Lett., 2014, 14, 5288–5294 CrossRef CAS PubMed.
- J. Liu, W. Li, L. Duan, X. Li, L. Ji, Z. Geng, K. Huang, L. Lu, L. Zhou, Z. Liu, W. Chen, L. Liu, S. Feng and Y. Zhang, Nano Lett., 2015, 15, 5137–5142 CrossRef CAS PubMed.
- J. Song, Z. Yu, M. L. Gordin and D. Wang, Nano Lett., 2016, 16, 864–870 CrossRef CAS PubMed.
- J. He, Y. Chen, W. Lv, K. Wen, C. Xu, W. Zhang, Y. Li, W. Qin and W. He, ACS Nano, 2016, 10, 10981–10987 CrossRef CAS PubMed.
- Z. Xiao, Z. Yang, L. Zhang, H. Pan and R. Wang, ACS Nano, 2017, 11, 8488–8498 CrossRef CAS PubMed.
- J. Wu and L. Wang, J. Mater. Chem. A, 2018, 6, 2984–2994 RSC.
- J. Jia, K. Wang, X. Zhang, X. Sun, H. Zhao and Y. Ma, Chem. Mater., 2016, 28, 7864–7871 CrossRef CAS.
- A. Hoefling, D. T. Nguyen, P. Partovi-Azar, D. Sebastiani, P. Theato, S. Song and Y. J. Lee, Chem. Mater., 2018, 30, 2915–2923 CrossRef CAS.
- J. Chen, R. Yuan, J. Feng, Q. Zhang, J. Huang, G. Fu, M. Zheng, B. Ren and Q. Dong, Chem. Mater., 2015, 27, 2048–2055 CrossRef CAS.
- B. Li, S. Li, J. Liu and J. Xu, RSC Adv., 2015, 5, 40310–40315 RSC.
- J. Xu, D. Su, W. Zhang, W. Bao and G. Wang, J. Mater. Chem. A, 2016, 4, 17381–17393 RSC.
- C. B. Bucur, M. Jones, M. Kopylov, J. Spear and J. Muldoon, Energy Environ. Sci., 2017, 10, 905–911 RSC.
- Z. Ma, L. Tao, D. Liu, Z. Li, Y. Zhang, Z. Liu, H. Liu, R. Chen, J. Huo and S. Wang, J. Mater. Chem. A, 2017, 5, 9412–9417 RSC.
- K. Park, J. H. Cho, J. Jang, B. Yu, A. T. De la Hoz, K. M. Miller, C. J. Ellison and J. B. Goodenough, Energy Environ. Sci., 2015, 8, 2389–2395 RSC.
- A. Bhargav, Y. Ma, K. Shashikala, Y. Cui, Y. Losovyj and Y. Fu, J. Mater. Chem. A, 2017, 5, 25005–25013 RSC.
- X. Ji, S. Evers, R. Black and L. F. Nazar, Nat. Commun., 2011, 2, 325 CrossRef PubMed.
- F. Wu, E. Zhao, D. Gordon, Y. Xiao, C. Hu and G. Yushin, Adv. Mater., 2016, 28, 6365–6371 CrossRef CAS PubMed.
- P. Xiao, F. Bu, G. Yang, Y. Zhang and Y. Xu, Adv. Mater., 2017, 29, 1703324 CrossRef PubMed.
- Z. Wang, Y. Dong, H. Li, Z. Zhao, H. Bin Wu, C. Hao, S. Liu, J. Qiu and X. W. D. Lou, Nat. Commun., 2014, 5, 5002 CrossRef CAS PubMed.
- L. Ji, M. Rao, H. Zheng, L. Zhang, Y. Li, W. Duan, J. Guo, E. J. Cairns and Y. Zhang, J. Am. Chem. Soc., 2011, 133, 18522–18525 CrossRef CAS PubMed.
- Y. Qiu, W. Li, W. Zhao, G. Li, Y. Hou, M. Liu, L. Zhou, F. Ye, H. Li, Z. Wei, S. Yang, W. Duan, Y. Ye, J. Guo and Y. Zhang, Nano Lett., 2014, 14, 4821–4827 CrossRef CAS PubMed.
- W. Bao, L. Liu, C. Wang, S. Choi, D. Wang and G. Wang, Adv. Energy Mater., 2018, 8, 1702485 CrossRef.
- Q. Zhang, Y. Wang, Z. W. Seh, Z. Fu, R. Zhang and Y. Cui, Nano Lett., 2015, 15, 3780–3786 CrossRef CAS PubMed.
- Z. Li, H. B. Wu and X. W. D. Lou, Energy Environ. Sci., 2016, 9, 3061–3070 RSC.
- S. Chung, C. Chang and A. Manthiram, Energy Environ. Sci., 2016, 9, 3188–3200 RSC.
- C. Chen, D. Li, L. Gao, P. P. R. M. Harks, R. Eichel and P. H. L. Notten, J. Mater. Chem. A, 2017, 5, 1428–1433 RSC.
- Y. Hwa, H. K. Seo, J. Yuk and E. J. Cairns, Nano Lett., 2017, 17, 7086–7094 CrossRef CAS PubMed.
- L. Ma, H. Yuan, W. Zhang, G. Zhu, Y. Wang, Y. Hu, P. Zhao, R. Chen, T. Chen, J. Liu, Z. Hu and Z. Jin, Nano Lett., 2017, 17, 7839–7846 CrossRef CAS PubMed.
- Y. Wang, L. Yu and X. W. D. Lou, Angew. Chem., Int. Ed., 2016, 55, 7423–7426 CrossRef CAS PubMed.
- Z. Li, J. Zhang and X. W. D. Lou, Angew. Chem., 2015, 127, 13078–13082 CrossRef.
- C. Tang, B. Li, Q. Zhang, L. Zhu, H. Wang, J. Shi and F. Wei, Adv. Funct. Mater., 2016, 26, 577–585 CrossRef CAS.
- T. Lin, Y. Tang, Y. Wang, H. Bi, Z. Liu, F. Huang, X. Xie and M. Jiang, Energy Environ. Sci., 2013, 6, 1283 RSC.
- H. Xu, Y. Deng, Z. Shi, Y. Qian, Y. Meng and G. Chen, J. Mater. Chem. A, 2013, 1, 15142 RSC.
- Z. Wei Seh, W. Li, J. J. Cha, G. Zheng, Y. Yang, M. T. McDowell, P. Hsu and Y. Cui, Nat. Commun., 2013, 4, 1331 CrossRef PubMed.
- H. Wang, Y. Yang, Y. Liang, J. T. Robinson, Y. Li, A. Jackson, Y. Cui and H. Dai, Nano Lett., 2011, 11, 2644–2647 CrossRef CAS PubMed.
- Y. Yuan, G. Tan, J. Wen, J. Lu, L. Ma, C. Liu, X. Zuo, R. Shahbazian-Yassar, T. Wu and K. Amine, Adv. Funct. Mater., 2018, 1706443 CrossRef.
- W. Tang, Z. Chen, B. Tian, H. Lee, X. Zhao, X. Fan, Y. Fan, K. Leng, C. Peng, M. Kim, M. Li, M. Lin, J. Su, J. Chen, H. Y. Jeong, X. Yin, Q. Zhang, W. Zhou, K. P. Loh and G. W. Zheng, J. Am. Chem. Soc., 2017, 139, 10133–10141 CrossRef CAS PubMed.
- S. Yu, X. Huang, K. Schwarz, R. Huang, T. A. Arias, J. D. Brock and H. D. Abruña, Energy Environ. Sci., 2018, 11, 202–210 RSC.
- J. Conder, R. Bouchet, S. Trabesinger, C. Marino, L. Gubler and C. Villevieille, Nat. Energy, 2017, 2, 17069 CrossRef CAS.
- H. Chen, C. Wang, Y. Dai, S. Qiu, J. Yang, W. Lu and L. Chen, Nano Lett., 2015, 15, 5443–5448 CrossRef CAS PubMed.
- T. Wang, R. Villegas Salvatierra, A. S. Jalilov, J. Tian and J. M. Tour, ACS Nano, 2017, 11, 10761–10767 CrossRef CAS PubMed.
- T. Zhou, W. Lv, J. Li, G. Zhou, Y. Zhao, S. Fan, B. Liu, B. Li, F. Kang and Q. Yang, Energy Environ. Sci., 2017, 10, 1694–1703 RSC.
- Y. Luo, N. Luo, W. Kong, H. Wu, K. Wang, S. Fan, W. Duan and J. Wang, Small, 2018, 14, 1702853 CrossRef PubMed.
- H. Al Salem, G. Babu, C. V. Rao and L. M. R. Arava, J. Am. Chem. Soc., 2015, 137, 11542–11545 CrossRef CAS PubMed.
- G. Babu, N. Masurkar, H. Al Salem and L. M. R. Arava, J. Am. Chem. Soc., 2016, 139, 171–178 CrossRef PubMed.
- H. Lin, L. Yang, X. Jiang, G. Li, T. Zhang, Q. Yao, G. W. Zheng and J. Y. Lee, Energy Environ. Sci., 2017, 10, 1476–1486 RSC.
- R. Mukherjee, A. V. Thomas, D. Datta, E. Singh, J. Li, O. Eksik, V. B. Shenoy and N. Koratkar, Nat. Commun., 2014, 5, 3710 CrossRef CAS PubMed.
- K. Yan, Z. Lu, H. Lee, F. Xiong, P. Hsu, Y. Li, J. Zhao, S. Chu and Y. Cui, Nat. Energy, 2016, 1, 16010 CrossRef CAS.
- X. Cheng, M. Zhao, C. Chen, A. Pentecost, K. Maleski, T. Mathis, X. Zhang, Q. Zhang, J. Jiang and Y. Gogotsi, Nat. Commun., 2017, 8, 336 CrossRef PubMed.
- Z. Li, X. Li, L. Zhou, Z. Xiao, S. Zhou, L. Li and L. Zhi, Nanoscale, 2018, 10, 4675–4679 RSC.
- G. Bieker, M. Winter and P. Bieker, Phys. Chem. Chem. Phys., 2015, 17, 8670–8679 RSC.
- B. Wu, S. Wang, W. J. Evans, D. Z. Deng, J. Yang and J. Xiao, J. Mater. Chem. A, 2016, 4, 15266–15280 RSC.
- H. Jung, B. Lee, M. Lengyel, R. Axelbaum, J. Yoo, Y. S. Kim and Y. Jun, J. Mater. Chem. A, 2018, 6, 4629–4635 RSC.
- H. Kang, S. Woo, J. Kim, J. Yu, S. Lee and Y. Kim, ACS Appl. Mater. Interfaces, 2016, 8, 26895–26901 CrossRef CAS PubMed.
- Q. Song, H. Yan, K. Liu, K. Xie, W. Li, W. Gai, G. Chen, H. Li, C. Shen, Q. Fu, S. Zhang, L. Zhang and B. Wei, Adv. Energy Mater., 2018, 1800564 CrossRef.
- R. Zhang, X. Chen, X. Chen, X. Cheng, X. Zhang, C. Yan and Q. Zhang, Angew. Chem., Int. Ed., 2017, 56, 7764–7768 CrossRef CAS PubMed.
- X. Cheng, H. Peng, J. Huang, R. Zhang, C. Zhao and Q. Zhang, ACS Nano, 2015, 9, 6373–6382 CrossRef CAS PubMed.
- Y. Zhang, X. Xia, X. Wang, C. Gu and J. Tu, RSC Adv., 2016, 6, 66161–66168 RSC.
- L. Chen, J. G. Connell, A. Nie, Z. Huang, K. R. Zavadil, K. C. Klavetter, Y. Yuan, S. Sharifi-Asl, R. Shahbazian-Yassar, J. A. Libera, A. U. Mane and J. W. Elam, J. Mater. Chem. A, 2017, 5, 12297–12309 RSC.
- A. A. Assegie, J. H. Cheng, L. M. Kuo, W. N. Su and B. J. Hwang, Nanoscale, 2018, 10, 6125–6138 RSC.
- Y. Lu, Z. Tu and L. A. Archer, Nat. Mater., 2014, 13, 961–969 CrossRef CAS PubMed.
- K. Yan, H. Lee, T. Gao, G. Zheng, H. Yao, H. Wang, Z. Lu, Y. Zhou, Z. Liang, Z. Liu, S. Chu and Y. Cui, Nano Lett., 2014, 14, 6016–6022 CrossRef CAS PubMed.
- M. Bai, K. Xie, K. Yuan, K. Zhang, N. Li, C. Shen, Y. Lai, R. Vajtai, P. Ajayan and B. Wei, Adv. Mater., 2018, 1801213 CrossRef PubMed.
- H. Tian, Z. W. Seh, K. Yan, Z. Fu, P. Tang, Y. Lu, R. Zhang, D. Legut, Y. Cui and Q. Zhang, Adv. Energy Mater., 2017, 7, 1602528 CrossRef.
- E. Cha, M. D. Patel, J. Park, J. Hwang, V. Prasad, K. Cho and W. Choi, Nat. Nanotechnol., 2018, 13, 337–344 CrossRef CAS PubMed.
- C. Yang, K. Fu, Y. Zhang, E. Hitz and L. Hu, Adv. Mater., 2017, 29, 1701169 CrossRef PubMed.
- A. Zhamu, G. Chen, C. Liu, D. Neff, Q. Fang, Z. Yu, W. Xiong, Y. Wang, X. Wang and B. Z. Jang, Energy Environ. Sci., 2012, 5, 5701–5707 RSC.
- D. Lin, Y. Liu and Y. Cui, Nat. Nanotechnol., 2017, 12, 194–206 CrossRef CAS PubMed.
- R. Zhang, X. Cheng, C. Zhao, H. Peng, J. Shi, J. Huang, J. Wang, F. Wei and Q. Zhang, Adv. Mater., 2016, 28, 2155–2162 CrossRef CAS PubMed.
- L. Li, S. Li and Y. Lu, Chem. Commun., 2018, 54, 6648–6661 RSC.
- H. Zhao, D. Lei, Y. He, Y. Yuan, Q. Yun, B. Ni, W. Lv, B. Li, Q. Yang, F. Kang and J. Lu, Adv. Energy Mater., 2018, 1800266 CrossRef.
- M. Zhu, B. Li, S. Li, Z. Du, Y. Gong and S. Yang, Adv. Energy Mater., 2018, 1703505 CrossRef.
- A. Wang, X. Hu, H. Tang, C. Zhang, S. Liu, Y. Yang, Q. Yang and J. Luo, Angew. Chem., Int. Ed., 2017, 56, 11921–11926 CrossRef CAS PubMed.
- A. Wang, S. Tang, D. Kong, S. Liu, K. Chiou, L. Zhi, J. Huang, Y. Xia and J. Luo, Adv. Mater., 2018, 30, 1703891 CrossRef PubMed.
- H. Wang, C. Wang, E. Matios and W. Li, Nano Lett., 2017, 17, 6808–6815 CrossRef CAS PubMed.
- J. Zhao, G. Zhou, K. Yan, J. Xie, Y. Li, L. Liao, Y. Jin, K. Liu, P. Hsu, J. Wang, H. Cheng and Y. Cui, Nat. Nanotechnol., 2017, 12, 993–999 CrossRef CAS PubMed.
- W. Deng, X. Zhou, Q. Fang and Z. Liu, Adv. Energy Mater., 2018, 8, 1703152 CrossRef.
- B. Li, D. Zhang, Y. Liu, Y. Yu, S. Li and S. Yang, Nano Energy, 2017, 39, 654–661 CrossRef CAS.
- S. Liu, X. Xia, Y. Zhong, S. Deng, Z. Yao, L. Zhang, X. Cheng, X. Wang, Q. Zhang and J. Tu, Adv. Energy Mater., 2018, 8, 1702322 CrossRef.
- D. Lin, Y. Liu, Z. Liang, H. Lee, J. Sun, H. Wang, K. Yan, J. Xie and Y. Cui, Nat. Nanotechnol., 2016, 11, 626–632 CrossRef CAS PubMed.
- R. Xu, X. Xia, X. Wang, Y. Xia and J. Tu, J. Mater. Chem. A, 2017, 5, 2829–2834 RSC.
- J. Kim, D. H. Kim, S. H. Joo, B. Choi, A. Cha, K. M. Kim, T. Kwon, S. K. Kwak, S. J. Kang and J. Jin, ACS Nano, 2017, 11, 6114–6121 CrossRef CAS PubMed.
- W. Liu, S. W. Lee, D. Lin, F. Shi, S. Wang, A. D. Sendek and Y. Cui, Nat. Energy, 2017, 2, 17035 CrossRef CAS.
- H. Peng, D. Wang, J. Huang, X. Cheng, Z. Yuan, F. Wei and Q. Zhang, Adv. Sci., 2016, 3, 1500268 CrossRef PubMed.
- H. Lee, D. J. Lee, Y. Kim, J. Park and H. Kim, J. Power Sources, 2015, 284, 103–108 CrossRef CAS.
- P. Barai, K. Higa and V. Srinivasan, J. Electrochem. Soc., 2017, 164, A180–A189 CrossRef CAS.
- T. Foroozan, F. A. Soto, V. Yurkiv, S. Sharifi-Asl, R. Deivanayagam, Z. Huang, R. Rojaee, F. Mashayek, P. B. Balbuena and R. Shahbazian-Yassar, Adv. Funct. Mater., 2018, 28, 1705917 CrossRef.
- K. Liu, P. Bai, M. Z. Bazant, C. Wang and J. Li, J. Mater. Chem. A, 2017, 5, 4300–4307 RSC.
- N. B. Aetukuri, S. Kitajima, E. Jung, L. E. Thompson, K. Virwani, M. Reich, M. Kunze, M. Schneider, W. Schmidbauer, W. W. Wilcke, D. S. Bethune, J. C. Scott, R. D. Miller and H. Kim, Adv. Energy Mater., 2015, 5, 1500265 CrossRef.
- J. Shim, H. J. Kim, B. G. Kim, Y. S. Kim, D. Kim and J. Lee, Energy Environ. Sci., 2017, 10, 1911–1916 RSC.
- J. Hu, J. Tian and C. Li, ACS Appl. Mater. Interfaces, 2017, 9, 11615–11625 CrossRef CAS PubMed.
- A. Vizintin, M. U. M. Patel, B. Genorio and R. Dominko, ChemElectroChem, 2014, 1, 1040–1045 CrossRef CAS.
- K. S. Korf, Y. Lu, Y. Kambe and L. A. Archer, J. Mater. Chem. A, 2014, 2, 11866–11873 RSC.
- N. Zhang, B. Li, S. Li and S. Yang, Adv. Energy Mater., 2018, 1703124 CrossRef.
- W. Luo, L. Zhou, K. Fu, Z. Yang, J. Wan, M. Manno, Y. Yao, H. Zhu, B. Yang and L. Hu, Nano Lett., 2015, 15, 6149–6154 CrossRef CAS PubMed.
- P. J. H. Kim, J. Seo, K. Fu, J. Choi, Z. Liu, J. Kwon, L. Hu and U. Paik, NPG Asia Mater., 2017, 9, e375 CrossRef CAS.
- Y. Dong, S. Zheng, J. Qin, X. Zhao, H. Shi, X. Wang, J. Chen and Z. Wu, ACS Nano, 2018, 12, 2381–2388 CrossRef CAS PubMed.
- J. Hwang, H. M. Kim, S. Shin and Y. Sun, Adv. Funct. Mater., 2018, 28, 1704294 CrossRef.
- S. Chung, L. Luo and A. Manthiram, ACS Energy Lett., 2018, 3, 568–573 CrossRef CAS.
- P. Zhu, J. Zhu, J. Zang, C. Chen, Y. Lu, M. Jiang, C. Yan, M. Dirican, R. Kalai Selvan and X. Zhang, J. Mater. Chem. A, 2017, 5, 15096–15104 RSC.
- D. Zhang, Y. Yin, C. Liu and S. Fan, Chem. Commun., 2015, 51, 322–325 RSC.
- Y. Fan, Z. Yang, W. Hua, D. Liu, T. Tao, M. M. Rahman, W. Lei, S. Huang and Y. Chen, Adv. Energy Mater., 2017, 7, 1602380 CrossRef.
- H. Peng, D. Wang, J. Huang, X. Cheng, Z. Yuan, F. Wei and Q. Zhang, Adv. Sci., 2016, 3, 1500268 CrossRef PubMed.
- T. Zhuang, J. Huang, H. Peng, L. He, X. Cheng, C. Chen and Q. Zhang, Small, 2016, 12, 381–389 CrossRef CAS PubMed.
- G. Zhou, L. Li, D. Wang, X. Shan, S. Pei, F. Li and H. Cheng, Adv. Mater., 2015, 27, 641–647 CrossRef CAS PubMed.
- Z. Xiao, Z. Yang, L. Wang, H. Nie, M. Zhong, Q. Lai, X. Xu, L. Zhang and S. Huang, Adv. Mater., 2015, 27, 2891–2898 CrossRef CAS PubMed.
- J. Huang, T. Zhuang, Q. Zhang, H. Peng, C. Chen and F. Wei, ACS Nano, 2015, 9, 3002–3011 CrossRef CAS PubMed.
- K. Sun, Q. Zhang, D. C. Bock, X. Tong, D. Su, A. C. Marschilok, K. J. Takeuchi, E. S. Takeuchi and H. Gan, J. Electrochem. Soc., 2017, 164, A1291–A1297 CrossRef CAS.
- Z. A. Ghazi, X. He, A. M. Khattak, N. A. Khan, B. Liang, A. Iqbal, J. Wang, H. Sin, L. Li and Z. Tang, Adv. Mater., 2017, 29, 1606817 CrossRef PubMed.
- J. Sun, Y. Sun, M. Pasta, G. Zhou, Y. Li, W. Liu, F. Xiong and Y. Cui, Adv. Mater., 2016, 28, 9797–9803 CrossRef CAS PubMed.
- X. Yang, C. Cheng, Y. Wang, L. Qiu and D. Li, Science, 2013, 341, 534–537 CrossRef CAS PubMed.
- B. Li, S. Li, J. Xu and S. Yang, Energy Environ. Sci., 2016, 9, 2025–2030 RSC.
- W. Kang, N. Deng, J. Ju, Q. Li, D. Wu, X. Ma, L. Li, M. Naebe and B. Cheng, Nanoscale, 2016, 8, 16541–16588 RSC.
- L. Wang, P. Hu, Y. Long, Z. Liu and X. He, J. Mater. Chem. A, 2017, 5, 22855–22876 RSC.
- A. J. Mannix, B. Kiraly, M. C. Hersam and N. P. Guisinger, Nat. Rev. Chem., 2017, 1, 14 CrossRef CAS.
- L. Li, S. Basu, Y. Wang, Z. Chen, P. Hundekar, B. Wang, J. Shi, Y. Shi, S. Narayanan and N. Koratkar, Science, 2018, 359, 1513–1516 CrossRef CAS PubMed.
- S. Lu and A. J. H. McGaughey, J. Appl. Phys., 2017, 121, 115103 CrossRef.
- H. Mousavi, J. Khodadadi, J. Moradi Kurdestany and Z. Yarmohammadi, Phys. Lett. A, 2016, 380, 3823–3827 CrossRef CAS.
|
This journal is © The Royal Society of Chemistry 2019 |
Click here to see how this site uses Cookies. View our privacy policy here.