DOI:
10.1039/C8NH00223A
(Review Article)
Nanoscale Horiz., 2019,
4, 52-76
Recent advances of bioinspired functional materials with specific wettability: from nature and beyond nature
Received
7th August 2018
, Accepted 4th September 2018
First published on 4th September 2018
Abstract
Through 3.7 billion years of evolution and natural selection, plants and animals in nature have ingeniously fulfilled a broad range of fascinating functions to achieve optimized performance in responding and adapting to changes in the process of interacting with complex natural environments. It is clear that the hierarchically organized micro/nanostructures of the surfaces of living organisms decisively manage fascinating and amazing functions, regardless of the chemical components of their building blocks. This conclusion now allows us to elucidate the underlying mechanisms whereby these hierarchical structures have a great impact on the properties of the bulk material. In this review, we mainly focus on advances over the last three years in bioinspired multiscale functional materials with specific wettability. Starting from selected naturally occurring surfaces, manmade bioinspired surfaces with specific wettability are introduced, with an emphasis on the cooperation between structural characteristics and macroscopic properties, including lotus leaf-inspired superhydrophobic surfaces, fish scale-inspired superhydrophilic/underwater superoleophobic surfaces, springtail-inspired superoleophobic surfaces, and Nepenthes (pitcher plant)-inspired slippery liquid-infused porous surfaces (SLIPSs), as well as other multifunctional surfaces that combine specific wettability with mechanical properties, optical properties and the unidirectional transport of liquid droplets. Afterwards, various top-down and bottom-up fabrication techniques are presented, as well as emerging cutting-edge applications. Finally, our personal perspectives and conclusions with regard to the transfer of micro- and nanostructures to engineered materials are provided.
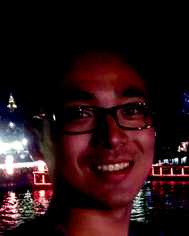
Yihan Sun
| Yihan Sun earned his BSc in applied chemistry from Qingdao University of Science and Technology, China, in 2016 and joined Prof. Guo's biomimetic materials of tribology (BMT) group as a master's-to-PhD student at Lanzhou Institute of Chemical Physics (LICP), Chinese Academy of Sciences (CAS) in the same year. His scientific interests focus on bioinspired functional materials with specific wettability, colloid and interface science and carbon materials. |
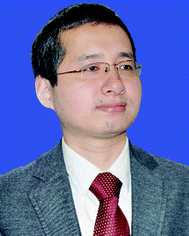
Zhiguang Guo
| Professor Zhiguang Guo received his PhD from Lanzhou Institute of Chemical Physics (LICP), Chinese Academy of Sciences (CAS) in 2007. From October 2007 to August 2008 he worked in the University of Namur (FUNDP), Belgium, as a postdoctoral researcher. From September 2008 to March 2011 he worked for the Fund for Scientific Research (FNRS), Belgium, as a “Chargé de Recherche”. From February 2009 to February 2010 he worked in the Department of Physics, University of Oxford, UK, as a visiting scholar. He is now a full professor at LICP financed by the “Top Hundred Talents” program of CAS. Thus far, he has published more than 200 papers about the interfaces of materials. |
1. Introduction
Nature provides an inexhaustible source of inspiration for the design and construction of aesthetic functional surfaces.1–4 Building blocks on the micro- and/or nanoscopic scales are always organized into sophisticated hierarchical structures on the surfaces of living organisms, which generally result in amazing functions of natural surfaces. For example, the laminated “bricks and mortar” hierarchical structures of nacre and bones are closely associated with their exceptional strength and toughness, in which ordered and hard crystalline ceramic platelets serve as bricks surrounded by a soft adhesive polymeric mortar.5,6 Hierarchical structures that consist of highly crystalline elementary cellulose fibrils and interfibril compounds of hemicellulose and lignin are also responsible for the excellent strength and toughness of lightweight natural wood.7,8 Bioinspired functional surfaces with specific wettability have been extensively investigated, largely because (super)wettability is always associated with other desirable functions, which exhibit great potential in the fields of materials science, medicine, engineering and so on.9–13 Moreover, wettability has a vital significance in determining the effect of the interplay between functional material surfaces and liquid droplets. A combination of wettability and other unprecedented properties/functionalities endows integrated biological surfaces with a wealth of optimized activities. For instance, superhydrophobic cicada wings display good antibacterial activity as well as outstanding antireflectivity.14–16 Superhydrophobic gecko feet also have self-cleaning properties and high adhesion.17,18 Inspiration from these functional biosurfaces with specific wettability can pave the way to achieving harmonization and unification between structures and functionalities, which in turn will give us a direction for the study of biomimetics from both theoretical and practical perspectives.
In general, bioinspired functional materials with specific wettability can be categorized into 10 classes: self-cleaning surfaces inspired by lotus leaves, anisotropic wetting surfaces inspired by plants and insects, antireflective and transparent surfaces inspired by insects and animals, highly adhesive surfaces inspired by red rose petals, gecko feet and the plant Salvinia molesta, surfaces with high wet adhesion inspired by tree frogs, mechanically stable surfaces inspired by nacre, surfaces with low fluid friction inspired by shark skin and water strider legs, antifogging surfaces inspired by insects’ compound eyes, structurally colored surfaces inspired by birds’ feathers, and surfaces for water capture and directional transport of liquids inspired by Stenocara beetles, cactus spines, spider silk and the plant Nepenthes alata. The corresponding references have been listed in the following sections. The abovementioned typical biological materials all possess more than one function (multifunctional integration). Table 1 shows a summary of bioinspired materials with wettability and other properties mentioned in this review.
Table 1 Summary of bioinspired functional materials mentioned in this review
Bioinspired material |
Multiple functionalities |
Ref. |
Nacre |
Superhydrophilicity/underwater superoleophobicity, mechanical properties, strength, toughness |
6 and 99–103
|
Bone |
Excellent mechanical properties |
5
|
Natural wood |
Excellent mechanical properties |
7 and 8
|
Cicada wings |
Superhydrophobicity, antibacterial activity, antireflectivity |
14–16
|
Gecko feet |
Superhydrophobicity, self-cleaning, high adhesion |
17, 18, 99 and 104
|
Bacillus subtilis
|
Superamphiphobicity |
56
|
Springtails |
Superamphiphobicity |
58–61
|
Leafhoppers |
Superamphiphobicity |
57
|
Lotus seedpods |
Superhydrophobicity |
45
|
Cactus stems |
Water harvesting, unidirectional transport of water droplets |
167–171
|
Reeds |
Anisotropic wetting |
55
|
Rice leaves |
Anisotropic wetting |
55
|
Fish scales |
Superhydrophilicity/underwater superoleophobicity |
74
|
Pilot whales |
Underwater superoleophobicity |
78
|
Shark skin |
Underwater superoleophobicity, fluid drag reduction, antifouling behaviour |
139 and 140
|
Filefish |
Anisotropic wetting |
82
|
Seaweed (Saccharina japonica) |
Underwater superoleophobicity |
83
|
Nepenthes pitcher plant |
Continuous directional water transport, omniphobicity |
84 and 172–176
|
Fresh sarcocarps (Chinese yams, white gourds, apples and potatoes) |
Under-oil superhydrophilicity |
97
|
Beetles |
Water harvesting |
98
|
Rose leaves |
Superhydrophobicity, high adhesion |
110–112
|
Salvinia molesta
|
Superhydrophobicity, high adhesion |
120
|
Tree frogs |
Hydrophilicity, high liquid–liquid adhesion |
122 and 130–135
|
Avian feathers |
Non-iridescent structural color, superhydrophobicity |
157
|
Mosquito compound eyes |
Superhydrophobicity, antireflectivity |
158–163
|
Butterfly wings |
Anisotropic wetting, structural colors, antireflectivity |
143–146
|
Water strider legs |
Superhydrophobicity, fluid friction reduction |
141
|
Spider silk |
Water harvesting |
177
|
Peacock feathers |
Structural color, superhydrophobicity |
143–146
|
Moth eyes |
Superhydrophobicity, antireflectivity, self-cleaning |
158–163
|
Fly eyes |
Superhydrophobicity, antireflectivity, |
158–163
|
Earthworms |
Antifouling, self-cleaning, self-replenishing lubrication, anti-wear, friction reduction |
238
|
Biomimicry or bioinspiration means mimicking biology or nature by following basic biomimetic principles.19,20 However, there is a long distance from natural to artificial structures, because biomimicry does not simply comprise copying or duplicating biological structures. Jiang and Xia pointed out the basic rules for the development of bioinspired materials:21 (1) the discovery and selection of amazing properties of biological organisms, namely, “bioinspiration”; (2) the exhaustive determination of the relationships between hierarchical structures and bulk properties; (3) the design and synthesis of suitable target molecules as building blocks; and (4) the construction of hierarchically organized structures to provide ideal functions.
Nevertheless, currently bioinspired surfaces can only be constructed with limited functionalities and cannot achieve an appropriate combination of multiple functionalities in one material surface. In this regard, continual efforts should be further devoted to understanding structure–function relationships and developing state-of-the-art nano/micromanufacturing techniques. In addition, practical applications of technical biomimetic materials provide a direct impetus for rational progress in this field. For instance, self-cleaning textiles have been developed from initial resistance to water to resistance to nearly all liquids, for example organic solvents, cooking oil and blood.22–26 Bearing in mind functional bioinspired (super)wetting surfaces and basic biomimetic principles, it is highly desirable to give a review of recent progress in such surfaces with a focus on hierarchical micro/nanostructures and corresponding functionalities.
In this review, we summarize recent advances (especially those in the last three years) in double-structural and functional materials with specific wettability, mechanical and optical properties and the ability to transport liquid droplets directionally, as well as state-of-the-art fabrication techniques and emerging applications. A summary of recent progress regarding the fabrication of such surfaces is given subsequently. Finally, personal perspectives, current challenges and directions for future research into double-structural and functional materials with specific wettability are briefly addressed.
2. Fascinating properties of bioinspired multiscale functional materials with specific wettability
As mentioned in the preceding section, biological organisms have adapted themselves to achieve advantageous harmonization and unification between surface morphologies and functionalities. In this section, we mainly focus on recent progress in multifunctional bioinspired surfaces reported in the last three years. Apart from initial wettability, some excellent properties related to specific wettability, such as mechanical properties, optical properties and the ability to transport liquid droplets, are reviewed, primarily focusing on high/low adhesion, fluid drag reduction/low friction, air retention under water, antireflectivity, structural colours, water harvesting and directional transport of water droplets. Bioinspired multiscale materials that mimic the unique architectures or functions of living organisms and their corresponding archetypes are also summarized.
2.1 Biomimetic surfaces with specific wettability
Over the past several decades, an abundance of research on functional surfaces with specific wettability has made astonishing progress, because these surfaces have exhibited great advantages in practical applications and hold a unique fascination. For example, a superhydrophobic surface with a water contact angle of greater than 150° has shown great potential in functional coatings with self-cleaning, anti-icing, anticorrosion and antireflective properties.27–33 A surface with superhydrophilic and underwater superoleophobic properties has been extensively used as a filter to separate various oil–water mixtures.34–37 Numerous investigations have stated that the complementary roles of surface morphology and chemical composition are a prerequisite for superwettability.11,38–40 Nonetheless, the existence of double-structural morphology can give rise to amplified wettability due to the chemical composition alone. For instance, a superhydrophobic state cannot be attained without the introduction of micro- or nanostructures, because the maximum contact angle is about 118° on a flat surface modified with fluoride compounds.11
Until now, two classical models have been used to correlate surface structures with wettability, namely, the Wenzel and Cassie–Baxter (CB) models.41,42 According to the Wenzel model, it can be concluded that the roughness factor will amplify the wetting properties of a smooth surface (Fig. 1). When the intrinsic water contact angle (θ) on a smooth material surface is larger than the intrinsic wetting threshold angle (θIWT), the surface is hydrophobic. Superhydrophobicity can be achieved by means of increasing the surface roughness. In contrast, a hydrophilic surface, where the intrinsic water contact angle (θ) on a flat surface is smaller than θIWT, will become more hydrophilic if rough surface structures are introduced. It is noted that the intrinsic water contact angle (θ) and the intrinsic wetting threshold angle (θIWT) of a flat solid surface are determined by the chemical composition of the material surface. As for surface roughness, Koch et al. and Robin et al. pointed out that micro/nanoscale two-tier structures are a prerequisite for ideal superhydrophobicity.43,44 The Koch curve fractal formula describes the relationship between surface roughness and the apparent contact angle (θa) and further points out the importance of nanoscale roughness in promoting superwettability.
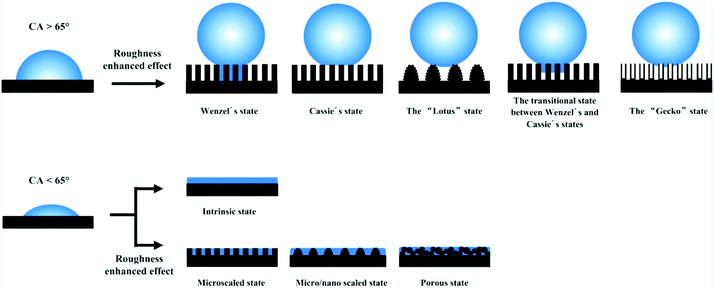 |
| Fig. 1 Various types of superhydrophobic and superhydrophilic models. The top row shows that the hydrophobicity was enhanced via the effect of enhanced roughness. The bottom row indicates that the hydrophilicity was enhanced with the assistance of micro/nanostructures. Reproduced with permission.10 (Copyright©2016, ACS.) | |
In contrast, in the CB regime a novel boundary, namely, a solid/liquid/air triphase interface, is produced. A liquid droplet will only rest on microscale protrusions and nanoscale roughnesses with a very limited contact area. Accordingly, a liquid droplet can easily roll off an inclined surface. In the following section, we will focus on biomimetic surfaces with specific wettability, including superhydrophobic surfaces, superoleophobic or superomniphobic surfaces, superhydrophilic and underwater superoleophobic surfaces, and slippery liquid-infused porous surfaces (SLIPSs), as well as surfaces with other specific forms of wettability.
2.1.1 Biomimetic superhydrophobic surfaces with hierarchical architectures.
Bioinspired superhydrophobic coatings that mimic lotus seedpods and surface structures of golden spherical cactus have been prepared on light metal surfaces.45,46 The as-prepared surfaces possess very similar morphologies to their natural archetypes. Sea-like spherical microstructures decorated with nanoscale cavities and islands in a surface inspired by lotus seedpods (Fig. 2b–f), as well as hybrid microspheres with nanothorn golden-cactus-like structures, are all prerequisites for the required superhydrophobicity and robust corrosion-resisting ability by decreasing the chance of contact between corrosive media and substrates. Su et al. proposed that microscale and nanoscale features have their own roles on a stable water-repellent surface with self-cleaning behavior.47 Furthermore, secondary and tertiary structures play a crucial role in the required superhydrophobic surfaces. Nanostructures on a water-resistant surface can retain the maximum pressure and prevent the transition between the Cassie state and Wenzel state. The sizes of nanostructures should be restricted to less than 740 nm.48–50
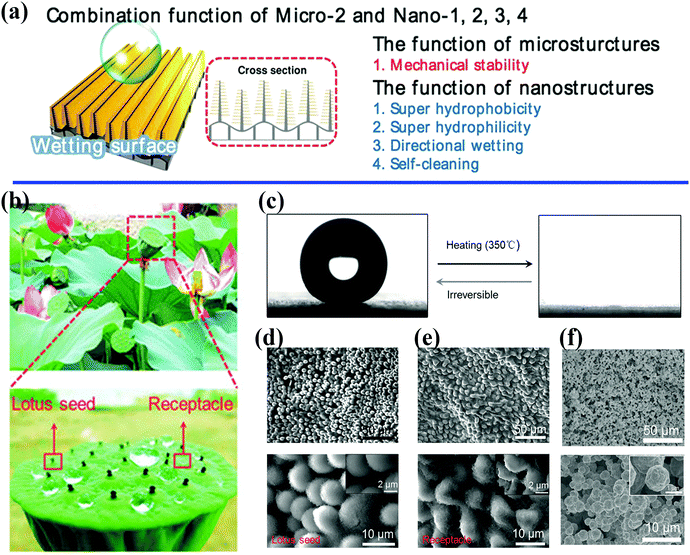 |
| Fig. 2 (a) Schematic illustration of the control of wetting enabled by a unique combination of micro- and nanoscale architectures.40 Reproduced with permission from ref. 40 and Copyright©2014 John Wiley and Sons. (b) Optical photographs of a natural lotus seedpod and water droplets on the surface. (c) The water contact angle changes from 153.9 ± 2.7° to 0° with irreversible changes in wetting. (d and e) SEM images of lotus seedpod surface with hierarchically organized micro/nanostructures. (f) Surface structures on bioinspired surfaces fabricated by electroless deposition and self-assembly technique.45 (b–f) Reproduced with permission from ref. 45 and Copyright©2017 John Wiley and Sons. | |
Microscale features can evidently decrease the area of solid–liquid contact significantly by two orders of magnitude, as well as adhesive forces at the macroscopic level.47,51,52 Moreover, microstructures can attain a critical structural height to offer sufficient mechanical support for superhydrophobic surfaces (Fig. 2a).40 Jiang et al. indicated that nanostructures play a decisive role in superhydrophobic surfaces with high contact angles, whereas hierarchically organized structures are responsible for low sliding angles.53 A large number of biomimetic studies have pointed out the great significance of combinations of multiscale architectures, and the intrinsic properties of materials tend to affect the observed wetting properties and multiple functionalities. Three fundamental design principles for systems with specific wettability have been established:54 (1) micro- and nanostructures play a decisive role for ideal superwetting or super-non-wetting properties; (2) control of the arrangement and orientation of hierarchical structures may affect the motion of probe liquids and the wetting state; and (3) the wetting state of a probe liquid on a rough solid surface is influenced by the intrinsic wetting threshold of the liquid.
With this information in mind, Sun et al. fabricated biomimetic anisotropic graphene surfaces by means of photolithography and laser holography techniques.55 Microgrooved structures prepared by photolithography and hierarchical architectures treated by two-beam laser interference endow the graphene-based surfaces that were obtained with anisotropic wetting properties. As in the case of reeds and rice leaves, the water sliding angles along the parallel direction of the surfaces that were obtained are much less than those along the perpendicular direction. A water droplet can easily roll along the direction parallel to the leaf edge instead of the perpendicular direction. The bioinspired graphene surfaces with an anisotropic wetting property will find promising applications in microfluidic devices and lab-on-a-chip techniques.
2.1.2 Biomimetic superoleophobic and superomniphobic (in air) surfaces with hierarchical structures.
Since the first superhydrophobic surfaces were discovered, breakthroughs in research on superoleophobic and superomniphobic species have led to a great number of investigations into the morphology of such surfaces. A series of surfaces of living organisms with oil-repelling behavior have been found, such as bacterial (Bacillus subtilis) biofilm colonies and pellicles, leafhoppers and springtails.56–61 Much effort has been devoted to understanding superoleophobic behavior and its underlying mechanism.62–67 Apart from the surface composition, Tuteja et al. pointed out that the elaboration of re-entrant structures proves to be the basis for the formation of oil-resistant surfaces,66 although robust oil-repellent surfaces can be obtained from hydrophilic components by means of sophisticated curvatures of re-entrant surfaces. Because the re-entrant geometric angle of such textures Ψ is less than the intrinsic contact angle of oil θ, a force in an upward direction can effectively impede the penetration of water and oil into rough micro/nanostructures and wetting of the solid surface (Fig. 3a).67 Taking the edge effect into consideration, an omniphobic surface should be obtained from microstructures with a critical angle (θc) larger than 180°:68,71
where θ0 and θY are the re-entrant geometric angle and intrinsic contact angle of a flat material surface, respectively. From the above equation, it can be concluded that increases in θ0 and θY are both advantageous for obtaining an omniphobic surface to suspend liquids. These significant design criteria lead to a stable CB state of an oil droplet on a solid surface.
 |
| Fig. 3 (a1 and a2) Schematic of hypothetical solid–air–liquid interfaces of two species of rough surface for which θ < Ψ and θ > Ψ, respectively. (a3) Trapezoidal texture with θ > Ψ ≥ 90°. (a4) Inverted trapezoidal (re-entrant) texture with 90° > θ > Ψ. Reproduced from ref. 67 with permission from RSC. (b) Various re-entrant geometries for superoleophobicity or superomniphobicity.64 (Copyright©2017 RSC.) (c) SEM images of as-prepared superomniphobic surface with triply re-entrant structures. (d) The upper structures of as-prepared triply re-entrant structures are capable of repelling water, whereas the lower structures can repel n-perfluorooctane. (e1–e4) Schematic illustration of various scenarios of required values of θY on non-re-entrant structures (θ0 = 90°), simple re-entrant structures (θ0 = 180°), doubly re-entrant structures (θ0 = 270°) and triply re-entrant structures (θ0 = 360°), respectively.71 (Copyright©2018 John Wiley and Sons, Inc.) | |
Doubly re-entrant rough structures have been demonstrated to provide a powerful means of obtaining a robust superoleophobic surface.58,69 Owing to the vertical overhang with vertical components, the upward direction of surface tension has been proven to suspend a completely wetting oil droplet (e.g., perfluorohexane).70 Six classical rough structures with re-entrant geometries have been summarized by our group, including T-shaped structures, mushroom-like structures, trapezoidal structures, fibrous structures, matchstick-like structures and microsphere structures.64 Gu et al. fabricated a novel triply re-entrant geometry using 3D printing technology (Fig. 3c–e).71 In comparison with the doubly re-entrant pillar structures reported previously, a small overhang at the bottom of the inner vertical overhang was added in the triply re-entrant geometry (Fig. 3c). The structure with the third overhang is favourable for increasing the critical pressure for the transition from the CB to the Wenzel state. The role of a sophisticated micro- and nanostructured hierarchy is more important than that of the intrinsic wetting property of the material.
With regard to real applications, sophisticated re-entrant structures need complex technical apparatus and accurate operations and incur high costs. However, our group synthesized a hierarchical flower-like superamphiphobic perfluorinated silane-modified TiO2 powder by a feasible solvothermal process.72 The surface topography of the resulting powder is similar to that of natural lotus leaves. The flower-like quasi-spheres with micro- and nanoprotrusions can retain air pockets around them to create a stable CB state and exhibit strong liquid-repellent ability for water, glycerol, colza oil and organic solvents with low surface tension. A bioinspired hexagonal tribrachia-post array with a re-entrant geometry for an omniphobic surface was fabricated by the assembly of an SiO2 colloid template and a colloid etching technique.73 The sophisticated topography of the as-prepared surfaces is comparable to that of superoleophobic springtail skin, which is composed of bristles and hexagonal arrays of nanogranules with a negative overhang geometry.
2.1.3 Biomimetic superhydrophilic/underwater superoleophobic surfaces.
Inspired by fish scales, Jiang et al. put forward the new concept of underwater superoleophobicity and the new idea of utilizing this superwetting property for oil–water separation.74 It has been proved that the classical Young's equation, the Wenzel model and the CB model are not only valid for superwetting and super-non-wetting properties in air but are also acceptable for such properties in water or other media.75 A sophisticated hierarchy also plays an essential role in the underwater wetting properties of oil.76,77 It has been proved that a superhydrophilic surface in air generally exhibits a superoleophobic property once immersed in water. The large number of biological examples (such as clamshells, carp, pilot whales, sharks and filefish) with underwater superoleophobicity has triggered new research interest in the construction of materials for oil–water separation and antifouling surfaces.78–82 For example, the thallus of seaweed (Saccharina japonica) is rich in porous structures with massive microfibers and reticular nanostructures, which display a strong underwater superoleophobic property even in a corrosive environment with high ionic strength and high salinity. The strong oil-resisting behavior is ascribed to the polysaccharide component. Inspired by these observations, Cai et al. fabricated a calcium alginate-based salt-tolerant coating with an excellent underwater superoleophobic property.83 Contamination by crude oil of the coating that was obtained can be effectively avoided during immersion for 30 days in artificial seawater. In addition, the mechanical strength of the alginate coating can be further enhanced by developing a double polymer network and introducing an inorganic nanoclay.
2.1.4 Biomimetic slippery liquid-infused porous surfaces (SLIPSs).
The carnivorous plant Nepenthes (pitcher plant) uses hierarchical micro- and nanostructures on its rim (peristome) to trap rainwater or dewdrops to endow the surface with slippery characteristics and liquid-resisting ability. In contrast to superhydrophobic and superoleophobic surfaces in air, the omniphobic behavior of Nepenthes (pitcher plant) mainly relies on the smooth liquid interface created by an intermediary liquid cushion.
To maintain a highly stable lubricating layer, the lubricating liquid must fully wet and permeate into micro/nanotextured substrates with high chemical affinity for the lubricating liquid. To ensure that the porous substrate is wetted preferentially by the lubricating liquid and the lubricating fluid is not replaced by a test liquid, two criteria should be satisfied (Fig. 4):84
ΔE1 = R(γB cos θB − γA cos θA) − γAB > 0 |
ΔE2 = R(γB cos θB − γA cos θA) + γA − γB > 0 |
where
γA,
γB and
γAB are the interfacial tensions at the probe liquid A–air, probe liquid B–air and liquid A–liquid B interfaces, respectively.
R represents the roughness factor.
θA and
θB are the equilibrium contact angles of liquid A and liquid B, respectively, on the porous solid in air. It can be observed that the sophisticated hierarchy plays an essential role in the required stable SLIPS.
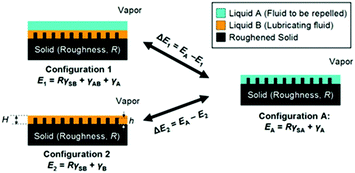 |
| Fig. 4 Working conditions for maintaining a stable lubricating liquid film.84 (Copyright ©2011 Macmillan Publishers Limited.) | |
The two-dimensional (2D) or three-dimensional (3D) porous surface topography of SLIPSs can be obtained from zero-dimensional (0D) nanoparticles, one-dimensional (1D) fibers and bulk materials. For instance, a 2D nanostructured wrinkled polymer surface was fabricated by mimicking the lubricating mechanism of the pitcher plant, whereby inert nontoxic silicone oil was infused into wrinkled surfaces.85 By densely packing 0D silica nanoparticles and polytetrafluoroethylene nanoparticles, two transparent, stable 2D porous surfaces were obtained on commercial glass slides.86,87 1D fibers that act as building blocks have been proven to be promising for the preparation of hierarchically micro/nanostructured surfaces by means of an electrospinning approach. A flexible porous membrane with tunable morphology and high elastic deformability was prepared from a fluorinated-copolymer-modified thermoplastic polyurethane nanofiber using an electrospinning technique.88 After lubricating liquids impregnate the porous membrane, the as-prepared membrane can achieve mechanically responsive smart control of the motion of water droplets and can be further applied in the field of water capture. 3D porous surfaces can be obtained by densely packing nanoparticles and/or selectively etching nanoparticle templates. In this way, opal and inverse opal structures can be obtained. Recently, novel SLIPSs based on 3D hydrogels and organogels were developed.89–96 Thanks to the strong interaction between water/organic solvent molecules and crosslinked polymers, an infused liquid can be trapped tightly in 3D gel networks formed by chemically or physically crosslinking polymers.
2.1.5 Biomimetic surfaces with unconventional specific wettability.
Most recently, the under-oil superhydrophilic property of fresh sarcocarps (including those of Chinese yams, white gourds, apples, and potatoes) induced by the absorption of water has been found by our group (Fig. 5a and b). These biological examples with a moisturizing property and porous surface structures are reminiscent of metal–organic frameworks (MOFs). With this information in mind, we fabricated an MOF-coated stainless-steel mesh with underwater superoleophobic and under-oil superhydrophilic properties.97Fig. 5d and e show the unprecedented anti-crude-oil property under water and unique under-oil superhydrophilic behaviour. Furthermore, the alternating hydrophilic/hydrophobic structures on a beetle's back (Fig. 5f) inspired our group to design and prepare a dual superlyophobic surface with contradictory wetting properties of superhydrophobicity and underwater superoleophobicity.98 Partial modification of CuO-coated substrates with a low concentration of perfluorodecanethiol retained some hydrophilic nanodomains on a superhydrophobic surface (Fig. 5g). Thus, the surface that was obtained can achieve superhydrophobic behaviour in air and superoleophobic behaviour underwater simultaneously (Fig. 5j).
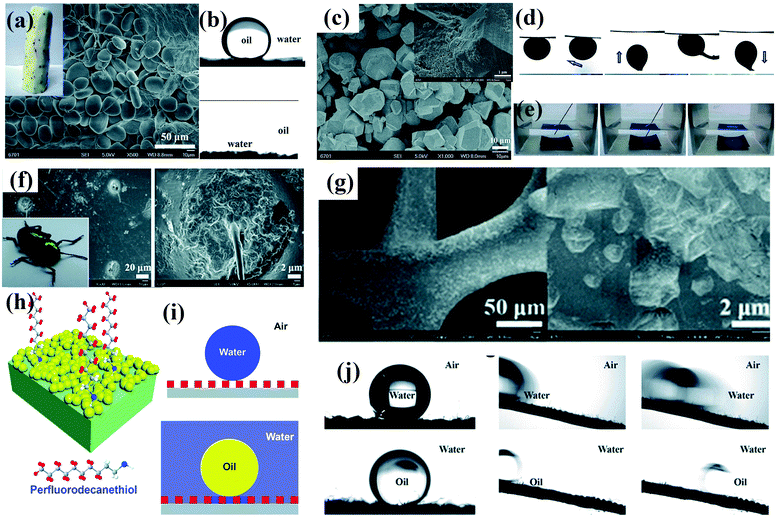 |
| Fig. 5 (a) Photograph and SEM image of a Chinese yam. (b) Chinese yams have underwater superoleophobic (top panel) and under-oil superhydrophilic (bottom panel) properties. (c) SEM image of as-prepared MOF-based membrane. Inset: High-magnification SEM image of the as-prepared membrane. (d) Underwater contact angle of crude oil, sliding angle, and dynamic adhesion of as-prepared membrane. (e) Photographs of the resulting membrane in hexane before and after dripping of a water droplet.97 (Copyright©2018 RSC.) (f) Photograph of a beetle and SEM image of its back. (g) SEM images of partial modification of a CuO-coated nickel foam with a low concentration of perfluorodecanethiol. (h) Schematic illustration of the design of dual superlyophobic surfaces. (i) Wetting model of dual superlyophobic surfaces. (j) Wetting properties of as-prepared dual superlyophobic surfaces.98 (Copyright © 2018 RSC.) Working conditions for retaining a stable lubricating liquid film.84 (Copyright©2011 Macmillan Publishers limited.) | |
Thus far, it can be concluded that the sophisticated hierarchy plays an essential role in surface wettability. Beginning with typical surfaces of living organisms, we introduce the main relationships between micro/nanostructures and surface wettability, including superhydrophobicity, superhydrophilicity/underwater superoleophobicity, superoleophobicity/superamphiphobicity, slippery liquid-infused porous surfaces (SLIPSs) and some unconventional forms of wettability.66 Wetting states have been summarized by Liu.54 However, for some other fascinating wetting properties biological archetypes in nature still cannot be found, which gives us a direction for biomimetic studies to progress this field rationally.
2.2 Mechanical properties
Underwater superoleophobic clamshells exhibit remarkable mechanical strength and toughness owing to a typical ‘‘bricks-and-mortar’’ architecture developed by the orientated arrangement of hard calcium carbonate nanotablets and soft adhesive proteins.99–103 Geckos have the ability to create strong adhesion to surfaces with various roughnesses and orientations owing to the multitude of microscale setae and nanoscopic spatulae on their superhydrophobic foot surfaces.99,104 These bionic surfaces with specific wettability and mechanical properties have attracted much attention because of their potential applications in the fields of microfluidic systems, loss-free transport of liquid microdroplets, drag reduction and biotechnology.105–109 In this section, we will introduce the main recent biomimetic innovations with a combination of specific wettability and mechanical properties.
2.2.1 Superwetting surfaces with high/low adhesion.
Superhydrophobic lotus leaves and red rose petals are representatives of biological surfaces with low and high liquid–solid adhesion, respectively. Historical in-depth studies lay emphasis on the fact that high/low liquid–solid adhesion generally originates from micro/nanostructures with different sizes.110–112 On the other hand, the underlying secrets behind high/low liquid–solid adhesion can be found in the two basic models of wetting, namely, the Wenzel and Cassie states. In the Wenzel state, a liquid can completely fill the grooves of rough structures (Fig. 1). A continuous three-phase contact line leads to an increase in the area of solid–liquid contact. Consequently, a liquid droplet can stick to such surfaces even when turned upside down. However, in the Cassie state the presence of air pockets gives rise to a discontinuous line of solid–liquid contact. In this case, a liquid droplet can only partially contact rough structures, and the solid/liquid adhesive force decreases with the area of solid–liquid contact. On the basis of the above theoretical analysis, it can be speculated that high/low liquid–solid adhesion can be modulated by controlling structural parameters of the surface to keep the surface in the Wenzel state or Cassie state, respectively.113–115 Moreover, besides lotus leaves and red rose petals, many other living organisms have inspired us to fabricate artificial superwetting surfaces with high/low liquid–solid adhesion. For example, the leaf of the floating plant Salvinia molesta is a typical superhydrophobic biological structure with high liquid–solid adhesion.116–118 However, biomimetic innovations that mimic the hierarchical structures in the Salvinia molesta leaf are relatively few because traditional fabrication techniques are far from meeting the requirements for the preparation of elastic egg beater-shaped hairs with hydrophilic patches. Very recently, Chen et al. successfully mimicked the effect of Salvinia and fabricated a biomimetic superhydrophobic egg beater structure according to the structure of natural Salvinia molesta via an additive manufacturing (3D printing) technique (Fig. 6a–d).119 The size of the hierarchical architectures was successfully designed according to their natural counterparts, and the water contact angles on the artificial bioinspired surface range from 152° to 170°. Moreover, the controllable adhesive force (from 23 μN to 55 μN) can be easily tailored using different numbers of egg beater arms for potential applications such as microhands for the manipulation of droplets.
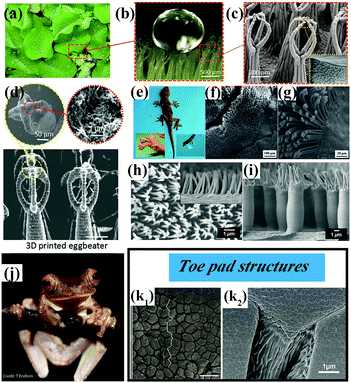 |
| Fig. 6 (a) Optical photograph of Salvinia molesta plant. (b) A water droplet is marble-like on the top surface of a leaf of Salvinia molesta. (c) SEM images of the egg beater hair structure on the top surface of a leaf of Salvinia molesta. (a–c) Reproduced with permission.120 Copyright 2016 IOP Publishing. (d) SEM images of artificial egg beater hair structures prepared by a 3D printing technique.119 (Copyright©2018 John Wiley and Sons.) (e–g) Optical photographs of a gecko and SEM images of its foot.107 (Copyright©2012 RSC.) (h and i) Micropillar structures covered with secondary fibrillar arrays on a surface inspired by a gecko's foot.121 (Copyright©2018 American Chemical Society.) (j and k) Tree frog Rhacophorus pardalis and corresponding SEM images of the topography of its toe pad showing regular and elongated hexagonal epithelial cells (k1) and a dense array of nanopillars covering the pad surface (k2).122,123 (j and k1) Reproduced with permission.122 Copyright©2015 John Wiley and Sons. (k2) Reproduced with permission.123 Copyright©2015 Royal Society Publishing. | |
The superhydrophobic feet of geckos display both strong liquid–solid and solid–solid (dry) adhesive behavior. The high aspect ratio of the microscopic foot hairs can provide high mechanical stability, because structural compliance and adaptability can be achieved when a gecko's foot comes into contact with a solid surface (Fig. 6e–g).125–127 On the other hand, the presence of nanoscale spatulae on the end of each seta is advantageous for increasing the dry-adhesive force,128 because the setae guarantee close contact with a solid surface even when the gecko feet are under a low preload. A high aspect ratio, hierarchy, slanted angles and a spatulate tip are basic characteristics of bioinspired surfaces with dry adhesion behavior.129 For instance, Low et al. prepared gecko-inspired flexible polycarbonate films with hierarchical arrays with a high aspect ratio (Fig. 6h and i).121 The micropillar arrays (primary roughness) can be effectively protected from the poly(sodium 4-styrenesulfonate) matrix during the step of nanoimprinting fibrillar arrays (secondary roughness). As illustrated in Fig. 6h and i, the primary micropillar structures covered with secondary fibrillar arrays are comparable to the two-level hierarchical arrays on a gecko's foot. To achieve unification and harmonization between structure and performance, the dry-adhesive films were further incorporated into robots for climbing purposes. A legged piezoelectric miniature robot (LPMR) equipped with the resulting polymer membranes was seen to climb a smooth glass substrate until the tilt angle exceeded 30°, which is a successful example of mimicking the structure and performance of a gecko.
Tree frogs are able to adhere to and climb on vertical and overhanging surfaces without falling in humid and flooded environments (Fig. 6j). The unique patterned surfaces on the toe pads of tree frogs are the primary sources of formamide for wet adhesion, because the generation of high frictional forces and the distribution of fluid across the pad can be effectively controlled by the surface topography.122,130–135 As shown in Fig. 6k, the toe pads are patterned with a regular hexagonal microstructure of hard epidermal cells separated by narrow channels. The surface of each epidermal cell is covered with densely packed keratin nanopillars. These surface patterns allow liquid to drain out of the contact area and away from strong direct solid–solid (dry) contact on a wet surface. In this case, wet adhesion is transformed into dry adhesion in essence, and a stronger adhesive force and/or frictional force can be obtained. In this regard, Xue et al. fabricated arrays of tree-frog-inspired composite micropatterns composed of polydimethylsiloxane (PDMS) micropillars with embedded hard, rootless polystyrene (PS) nanopillars.124 In this composite system, the PS nanopillars and PDMS are covalently linked, which allows transmission of mechanical stress and deformation. The hierarchical structures alter the stress distribution at the contact interface of the micropillars and therefore enhance the adhesion and friction of the composite micropattern.
2.2.2 Superwetting surfaces for reduction of fluid friction.
Two types of biological surfaces with good fluid drag reducing behavior have been increasingly emulated: (1) superhydrophilic/underwater superoleophobic surfaces inspired by shark skin and carp skin and (2) superhydrophobic surfaces inspired by lotus leaves and Salvinia molesta leaves.136–138 Prominent fluid drag reducing behavior is also closely associated with hierarchically structured surfaces on the micro- and nanoscale. For example, the tooth-like dermal denticles with longitudinal riblets (aligned parallel to the local direction of water flow) on the skin of fast-swimming sharks enable streamwise vortices to be lifted and pinned in the viscous sublayer. The longitudinal riblets that are arranged parallel to the local direction of water flow also allow water to move efficiently over the whole superhydrophilic shark skin.139 In this way, fluid drag can be effectively reduced when sharks swim in a turbulent flow environment.140 Parkin et al. fabricated a TiO2-based superhydrophobic coating on a glass slide and also found that the sailing velocity of a mini-boat with superhydrophobic coatings was always higher than that of its untreated counterpart.141 The drag reduction capacity of such superhydrophobic surfaces can be reflected by their air retention ability, because a lubricating air layer trapped in nano- and microstructures can form a new boundary and effectively reduce the interaction between the solid surface and water. The air retention ability can be reflected by the pressure drop across a microchannel in an experimental setup. Kavalenka et al. fabricated a Salvinia fern-inspired superhydrophobic nanofur surface covered with a dense layer of randomly distributed nano- and microhairs with a high aspect ratio.142 They found that the pressure drop across an experimental microchannel covered with nanofur was 50% lower than that in a channel with a flat surface, which indicated that drag reduction occurred.
2.3 Optical properties
2.3.1 Structural colors.
As a result of predation and being preyed upon, birds and insects have gradually developed vivid and brilliant coloration under the pressure of evolution and natural selection. Besides chemical factors, these iridescent colors arise from sophisticated interactions between light and hierarchical solid surfaces, which are closely related to the diffraction and scattering processes of visible light in structures composed of periodic minute architectures with different dielectric constants.143–146 Such specific materials with structural colors are termed photonic crystals (PCs) and have attracted great research interest because of their unique light-manipulating behavior and practical applications in smart sensors, communications, catalysts, solar cells, bioassays and other fields. In particular, photonic crystals with specific wettability have attracted increasing interest because the specific wettability can endow ordinary photonic crystals with new functions. For instance, superhydrophobic photonic crystals have self-cleaning ability to prevent the adhesion of contaminants to device surfaces.147,148 Hydrophilic target molecules tend to be enriched in a hydrophilic zone because of the same affinity. Thus, photonic crystals with a hydrophilic–hydrophobic micropattern can detect extremely low concentrations of fluorescent analytes of as low as 10−16 mol L−1 in fluorophore-based assays.149
When a solvent droplet drops onto the surface of PCs, the optical color change induced by the solvent-responsive property of the PCs will greatly restrict their potential practical applications. For instance, PCs that can exhibit varying colors under different weather conditions or solvents are unsuitable for outdoor coatings. Wang et al. prepared unique lyophilic but non-wettable inverse opal photonic crystals comprising organosilane-polymerized carbon dots (SiCDPCs) with a closed-cell architecture.150 The distinct lyophilic but non-wetting properties were ascribed to the synergistic effect of the closed-cell structure and organosilane-functionalized carbon dots. Nonpolar or highly viscous solvents do not diffuse into the systems, which results in an invariant reflection spectrum/structural color (Fig. 7a). Conversely, polar solvents will permeate through the barrier owing to “similarity compatibility”. (The organosilane-polymerized carbon dots are polar.) An evident red shift in the reflection spectrum/structural color was observed (Fig. 7b). Song et al. imprinted robust invisible 3D chemical patterns into hollow silica colloidal photonic crystals (HSCPCs),151 in which hydrophilic zones created by treatment with oxygen plasma were developed on HSCPCs that were initially modified with octadecyltrichlorosilane (OTS) (Fig. 7c). The hidden patterns were observed instantaneously (after approximately 100 ms) under a dynamic humid flow (e.g., human breath) rather than a static humid environment, even with a relative humidity of up to nearly 100%. Mechanically sealed colloidal silica crystals were also fabricated by their group.152 The resulting structure possesses an ultrastable photonic band gap (PBG), and liquids with extremely low surface tension (e.g., perfluorohexane) cannot penetrate into the resulting sealed structures, even under high pressure (Fig. 7d). Zhang et al. and Kim et al. also prepared photonic crystals with an invariable stopband and brilliant structural colors.153,154 These non-wettable PCs would find applications in the paint industry and decoration of outdoor structures.
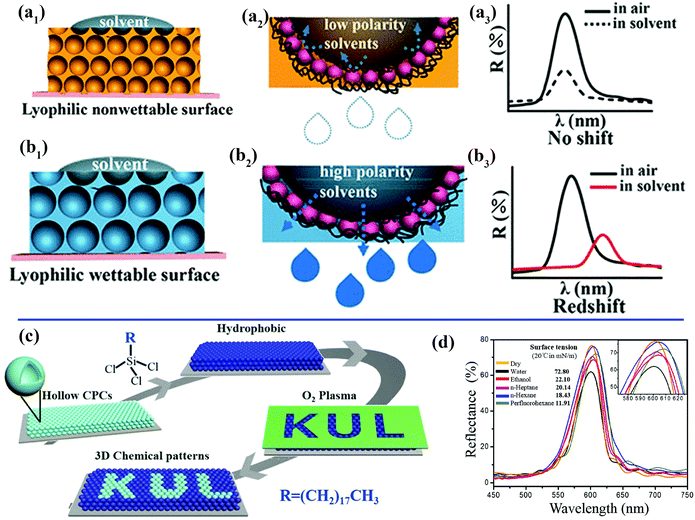 |
| Fig. 7 (a) Schematic illustration of inverse opal photonic crystals comprising closed-cell organosilane-polymerized carbon dots with a lyophilic but non-wetting property toward solvents. (a1) A low-polarity solvent cannot permeate into the resulting structures.150 (a2) Magnified view of the area of contact between a droplet of a nonpolar solvent and the closed-cell structures. (a3) Invariant reflection spectrum/structural color due to the non-wetting property of the sample toward nonpolar solvents. (b) Schematic illustration of the wetting state of solvents on the structure. (b1) A droplet of a nonpolar solvent can permeate through the barrier.150 (b2) Magnified view of the area of contact between droplets of a nonpolar solvent and the resulting film. (b3) Red shift in reflection spectrum/structural color due to the wetting property of the sample towards polar solvents. (Copyright © 2018 ACS.) (c) Schematic illustration of the fabrication process for introducing 3D chemical patterns into colloidal photonic crystals comprising hollow silica spheres.151 (Copyright©2018 John Wiley and Sons.) (d) Unchanged reflection spectra of the non-wetting colloidal photonic crystals recorded with different solvents deposited on their surface. The inset shows an enlargement of the spectra.152 (Copyright©2016 John Wiley and Sons.) | |
Recently, Zhao et al. fabricated a new lubricant-infused polyurethane (PU) inverse opal surface with tunable structural colors and self-reporting wettability.155 The lubricating fluid can infiltrate the pores of the stretchable PU surface under stretching, and a liquid droplet was pinned on the stretched film. However, when the elastic film returns to its relaxed state, a water droplet can slide on the relaxed film with a small sliding angle. Surprisingly, changes in the structural colours of the stretchable film under different degrees of stretching were clearly observed. In this way, the wettability and structural changes induced by simultaneous deformations of the periodic porous structures can be visually self-reported. With the inspiration of the amorphous nanostructures of avian feathers, a film with non-iridescent structural color with high hydrophobicity and mechanical stability was fabricated and exhibited high color saturation under indoor lighting conditions or sunlight.157 A magnetically actuating micropillar array on a flexible polydimethylsiloxane surface with fluid- and light-manipulating ability was fabricated by Kim et al.156 When superhydrophobic black silicon scales are assembled on magnetic micropillars in an in-plane configuration, the motion of directional spreading of a liquid can be controlled because the orientation of the black silicon scales can be switched between symmetric and asymmetric configurations under a magnetic field. When the hybrid surfaces are furnished with photonic crystal scales on magnetic micropillars in an in-plane configuration, changes in the structural color can be induced by a magnetic field. When the strength of an external magnetic field increases from about 0.1 T to about 0.3 T, the structural color of the surface changes vividly from green to blue and then to purple.
2.3.2 Antireflective and transparent surfaces.
The compound eyes and wings of insects provide an enormous range of inspiration for the fabrication of biomimetic technical surfaces with specific wettability and antireflective properties, which result from the synergetic effect of microscale structures and cone-shaped nanoprotuberances on the surface.158–163 A textured coating that features a gradient refractive index is generally considered to be an optimal choice for fabricating antireflective coatings that are optimized for a wide range of wavelengths and incidence angles.164,165 A moth eye-inspired self-cleaning texture with an excellent antireflective property has been successfully transferred to the front surface of a commercial solar cell setup for light harvesting, which achieved enhanced device performance in terms of photoelectric conversion efficiency and service life in a dusty outdoor environment.166 It has been mentioned that such moth eye-like antireflective structures sometimes exhibit self-cleaning behavior, which may originate from superhydrophobicity and/or photoinduced superhydrophilicity. Rodríguez et al. fabricated a moth eye-inspired antireflective coating on a transparent poly(methyl methacrylate) (PMMA) surface loaded with titanium dioxide (TiO2) nanoparticles.167 The initial loss of optical reflectance of 9% on a control polymer substrate was dramatically reduced to 0.6% on the resulting surface, and RhB on the resulting surface was degraded when exposed to UV light irradiation. To imitate the hierarchical structures with hydrophobicity and antireflectivity on cicada wings, a bionic polystyrene (PS) replica with a nanopillar array was prepared, which was analogous to the tapered nanostructures on cicada wings.168 The tapered nanostructures on the PS replica can provide a gradient refractive index that ranges from the value for air (nair) to that for PS (nPS), instead of an abrupt change in refractive index between interfaces with air and PS substrates. The synergistic effect of the gradient refractive index and nanopillars enables light to interact completely with the biosurface, which gives an average reflectance of approximately 4% in the wavelength range of 400–1000 nm.
Optical transparency is an important property of a material and means that incident light is wholly diffused through a surface of the material with little or even no optical loss.146,168 The fabrication of superwetting surfaces with high transparency has become a research focus because of their crucial applications in optical devices such as camera lenses, diving goggles, and solar cell panels. However, increasing the surface roughness poses great challenges for the development of novel superwetting surfaces with high transparency, because unnecessary light scattering increases in the wake of an increase in surface roughness. Rayleigh scattering theory points out that the surface roughness should be less than 100 nm to achieve high transparency on a material surface with a suitable refractive index.169 The white petals of the plant Diphylleia grayi turn colorless when exposed to a rainy environment. A new liquid–liquid (water–cytolymph) interface is created as water gradually penetrates into the loose cell structures with lacunae and intercellular spaces. Because the cytolymph and water have comparable refractive indices, the light scattering effect is dramatically inhibited and the optical transparency is improved in the rain. In this regard, Chen et al. fabricated a superoleophilic/underwater superoleophobic silica glass surface with low oil adhesion and high transparency in water.170 The enhanced transparency in water was caused by (1) water filling the interior spaces of rough structures and (2) the comparable refractive indices of silica and water. Zhang et al. fabricated a robust and transparent superamphiphobic coating using polysiloxane-modified multiwalled carbon nanotubes as a template.171 The transparency is affected by the wall thickness and diameter of the silicone nanotubes, which is controlled by the concentration of the silicone precursor n-hexadecyltrimethoxysilane (HDTMS) and the diameter of the multiwalled carbon nanotubes.
2.4 Surfaces for water harvesting and directional liquid transport
The Namib Desert beetle Stenocara, the cactus Opuntia microdasys, the spider Uloborus walckenaerius and the plant Nepenthes alata have served as rich sources of inspiration for the construction of superwettable surfaces with water harvesting and/or directional liquid transport behavior. Many valuable and meaningful reviews have summarized the detailed mechanism of droplet transport by these living organisms.171–176 We will not describe these research developments but focus on recent progress in bioinspired materials with water droplet transport and water collecting behavior. Xue et al. prepared polyacrylonitrile/graphene oxide (PAN/GO) composite fibers with a bioinspired spindle-knot structure via an electrospinning method.177 Oil droplets under water could aggregate, move along and finally float away from the hydrophilic fiber surface with a spindle-knot structure, which is also advantageous for decreasing accumulation behavior and enhancing antifouling ability. Inspired by the hydrophilic–hydrophobic pattern on the back of Namib Desert beetles, Zhu et al. first fabricated an octadecanethiol (ODT)-modified copper foil as a superhydrophobic region, and 0.1 μL of a dopamine solution was then dripped onto the superhydrophobic surface, which had been prewetted with dichloromethane, to form a hydrophilic area.178 The as-prepared hybrid surfaces were used as fog-collecting materials and exhibited high water collection efficiency. Under a magnetic field, the ferrofluid develops an ordered array of semi-ellipsoidal droplets owing to magnetic hydrodynamic instability. Accordingly, Zhao et al. fabricated an artificial Nepenthes peristome with periodically aligned and overlapping arch-shaped microcavities using a bottom-up ferrofluid assembly technique.179 The topography of the as-prepared surface is similar to that of a natural Nepenthes peristome (Fig. 8a and b), and the resulting surface enabled unidirectional transport of water in a fast and continuous way without any additional energy (Fig. 8c and d).
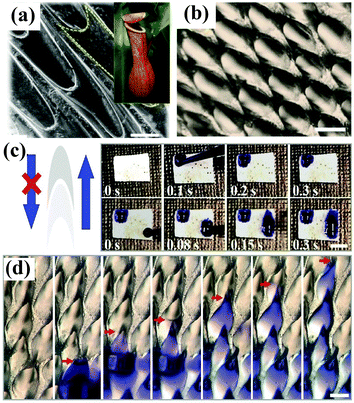 |
| Fig. 8 (a) SEM image of the surface of a Nepenthes peristome. Inset: Optical photograph of a Nepenthes alata plant. (b) Optical image of the as-prepared surface prepared by a ferrofluid assembly technique. (c) Digital images showing the unidirectional transport of water along the protruding direction of the microcavities. (d) Optical images showing a continuous process of water transport. (a–d) Adapted with permission.179 (Copyright©2018 John Wiley and Sons.) | |
3. Preparation of multifunctional surfaces with specific wettability
Hierarchically structured multifunctional surfaces with specific wettability can be fabricated via self-assembly, electrospinning, dip-coating, lithography, etching, electrodeposition, templating methods and other techniques. The approaches used for fabrication are diverse and can be roughly divided into two basic types: top-down and bottom-up methods. The formation of highly controlled micro/nanostructures can be achieved by top-down methods, such as lithography, anodization and laser processing. Bottom-up methods tend to be used to fabricate random surfaces with multiscale structures and include sol–gel techniques, electrospinning, dip-coating, electrodeposition and so forth. However, it is unrealistic to review all the approaches used for fabrication, and we will introduce the main recent typical approaches in this section. A summary of typical approaches used for preparation and their corresponding advantages is given in Table 2.
Table 2 Summary of approaches for the preparation of bioinspired multiscale superwetting functional materials mentioned in this review
Approaches |
Summary of process |
Advantages |
Ref. |
Top-down |
Bottom-up |
Etching |
|
Multiscale roughness is produced by immersing the substrate in the reaction solution or directly corroding/bombarding the substrate using plasma. |
Low cost, easy operation, high surface uniformity |
180–182
|
|
Lithography |
|
The patterned surface morphology of a pre-designed photomask is transferred to hard/soft substrates when light is used to irradiate surfaces coated with a photoresist film in advance. |
Highly ordered structures, large surface areas, unconventional multiscale structures, high reproducibility |
198–203
|
|
Dip-, spray- and spin-coating |
Nanoparticles are assembled on a microscopic length scale via a physical deposition method, which results in desirable hierarchically featured micro/nanostructures. |
Great simplicity, low cost, large-area fabrication |
86, 205–207
|
|
LbL assembly |
Multiple scales are developed via the alternate deposition of negatively and positively charged materials. |
Facile control of surface morphology and thickness |
216 and 217
|
|
Sol–gel method |
Nanostructured particles and other required materials are produced via hydroxylation and condensation of precursors at ambient temperature. The final crystalline structure can be obtained by thermal treatment. |
Operation at ambient temperature |
220 and 221
|
|
Electrodeposition and electropolymerization |
Hierarchically micro/nanostructured coatings on a metal or conducting polymer surface are developed by an electrochemical approach, whereas the surface morphology and structure can be facilely tuned via electrochemical parameters. |
Fast, facile and low-cost operation, facile and precise control of surface topographies and structures |
222–225
|
|
Templating methods |
Polymeric micro/nanostructures are developed by molding a pre-designed replica or taking advantage of closely packed colloidal nanoparticles. |
Large-area fabrication, low cost |
168 and 226–229
|
3.1 Top-down methods
3.1.1 Etching.
Etching processes have the merits of facile techniques, low costs, easy operation, and high surface uniformity. In terms of reaction systems with/without solutions, etching processes can be classified into wet etching and dry etching. A matchstick-like Cu2S@CuxO nanowire-coated copper mesh was fabricated by a wet-etching and sulfurization process.180 A light blue Cu(OH)2 (H-NWM) mesh was first fabricated by immersing a copper slice in a mixed aqueous solution of NaOH and K2S2O8, and the thermodynamically unstable Cu(OH)2 mesh was subsequently treated by soaking in a sodium sulfide solution to obtain a Cu2S@CuxO film (S-NWM) via an anion-exchange reaction. Surprisingly, the resulting mesh can undergo the wettability transition between original superhydrophilicity/underwater superoleophobicity and superhydrophobicity after storage for two weeks in air without any modifier. Wettability-patterned silicon nanospike array structures were fabricated by reactive ion etching (RIE) of silicon with self-organized honeycomb-patterned dry-etching masks and UV/O3 treatment with photomasks.181 Thanks to the beetle-like (super)hydrophilic–(super)hydrophobic patterns and inverted triangular micro/nanostructures like the legs of L. exotica, the resulting surfaces can collect water and transport water against gravity without additional energy consumption. Zhang et al. fabricated single-layered ordered colloidal polystyrene microsphere arrays with a geometric gradient by a combination of colloidal lithography and inclined RIE (Fig. 9),182 and these can be used as effective masks to prepare various hierarchical structures with a geometric gradient. For example, a silicon cone array with a geometric gradient was successfully fabricated and can be further used to control the wetting behavior of fluids via modification with various chemical groups. After being modified with the thermoresponsive polymer poly(N-isopropylacrylamide) (PNIPAM), a silicon cone array can control the direction of water flow by tuning the surface temperature.
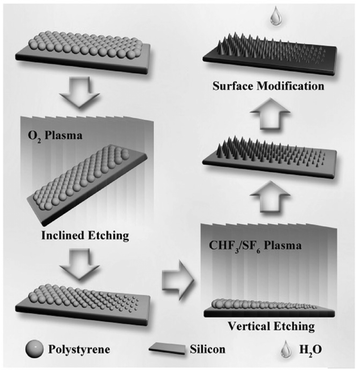 |
| Fig. 9 Schematic of the inclined etching method used for fabricating ordered micro/nanostructures with a geometric gradient.182 (Copyright©2017 John Wiley and Sons.) | |
3.1.2 Lithography.
Lithography techniques, as conventional top-down methods, have been extensively used for the construction of patterned surfaces with well-defined and regular structures. The patterns of a hard or soft pre-designed photomask are transformed into the desired substrates when X-rays, an electron beam or other light sources are used to irradiate surfaces coated with a photoresist. In particular, this method can precisely tailor surface structures with various shapes and sizes.183–186 Lithography techniques are highly reproducible and can be roughly classified into X-ray lithography, electron beam lithography, photolithography, microcontact printing, colloidal lithography, and nanoimprint lithography.187–197 However, these methods require expensive experimental apparatus and long cycles of molding steps, and the fabrication procedures normally produce some defects.
Kota et al. fabricated mushroom-like pillars of a thermoresponsive thiolene/acrylate shape memory copolymer on a silicon wafer by photolithography and a reactive ion etching approach (Fig. 10a).198 After modification with fluorinated silane, a metamorphic superomniphobic silicon surface with a shape memory effect was obtained, and distinctly different wetting transitions of organic liquids with various surface tensions on the resulting mushroom-like pillar texture can be achieved by controlling the surface temperature. An antibacterial and antifouling surface was fabricated by loading titanium dioxide nanoparticles onto a shark skin-inspired surface, whereby solvent-assisted nanoimprint lithography was used to fabricate orthogonal shark skin-patterned surfaces.199 Faure fabricated a hexagonal array of superhydrophobic copper ring-like structures or hollow spheres with high adhesion by means of alternating-current (AC)-assisted colloidal lithography (Fig. 10b).200 Polystyrene spheres can initially be organized into 2D crystals under an AC electric field, and the PS arrays can further serve as a template to fabricate copper bowls or hollow spheres (Fig. 10c and d) by adjusting the concentrations of copper salt solutions.
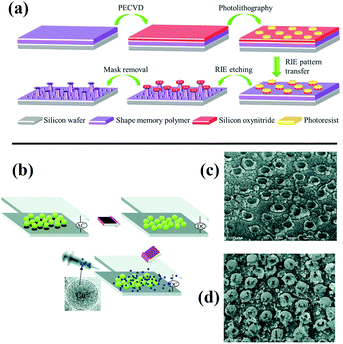 |
| Fig. 10 (a) Schematic diagram of the construction of metamorphic superomniphobic surfaces.198 (Copyright©2018 John Wiley and Sons.) (b) Scheme of preparation of patterned copper surfaces using electro-colloidal lithography. (c and d) SEM images of as-prepared copper bowl and hollow spheres.200 (Copyright © 2018 RSC.) | |
3.2 Bottom-up methods
3.2.1 Physical deposition by dip-, spray- and spin-coating.
The physical deposition methods of dip-, spray- and spin-coating have demonstrated their advantages in the preparation of multiscale structures, such as great simplicity, low cost and scalable preparation.199,201–204 He et al. prepared a robust, substrate-independent and antireflective superhydrophobic coating by a simple spray-coating method (Fig. 11a).205 Silica nanoparticles with a size of 20 nm were first sprayed onto a substrate. Subsequently, a mixed suspension of a hydrophobic silica sol and an acid-catalyzed silica precursor was sprayed to obtain an antireflective coating with self-cleaning properties in air, oil and an oil-contaminated environment. Recently, our group developed a simple spin-coating method for preparing a transparent liquid-infused omniphobic polytetrafluoroethylene (PTFE) film on glass, copper, silica and titanium substrates (Fig. 11b).86 Perfluoropolyether (PFPE) lubricants were tightly bound in porous structures formed by the close packing of PTFE nanoparticles with well-defined sizes and shapes. The resulting omniphobic coating exhibited excellent liquid repellency and self-cleaning and anticorrosion properties, as well as good anti-icing ability. The spin-coating method has the advantages of manipulating the thickness and degree of uniformity of a film on a flat substrate effectively but cannot function in the case of curved substrates. The dip-coating method is generally not restricted by the shapes of substrates and has some distinct advantages such as low cost, fast and easy operation, and scalable preparation. It has also become one of the most commonly used techniques for the manufacture of super-non-wetting fabrics and textiles (including superhydrophobic and superomniphobic species). Cheng et al. fabricated a superhydrophobic fabric via a facile assembly and dip-coating process (Fig. 11c),206 whereby the rough hierarchical structures formed by the aggregation of phytic acid–metal complexes and modification of PDMS endow the pristine fabric with robust superhydrophobicity against ultraviolet irradiation, high temperatures, and immersion in organic solvents. A fluorine-free, water-rich and particle-free system for coating robust superhydrophobic fabrics was fabricated using PDMS as a binder, tetrahydrofuran (THF) as a solvent and water as a non-solvent (Fig. 11d).207 Note that the transparency and other physical properties of the resulting fabrics, including the tensile strength, elongation at break, flexural rigidity and air permeability, are comparable to those of the pristine fabrics.
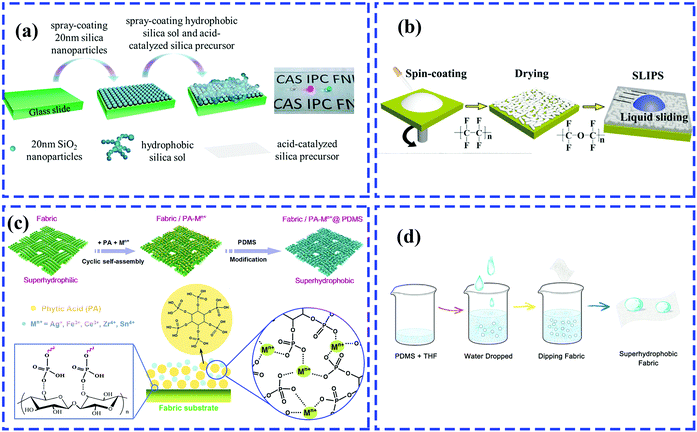 |
| Fig. 11 Schematic of the preparation of a multifunctional rough surface with specific wettability. (a) Spray-coating for fabrication of antireflective superhydrophobic coating.205 (Copyright©2017 ACS.) (b) Spin-coating for preparation of transparent coating infused with lubricating liquids.86 (Copyright©2018 Elsevier.) (c) Dip-coating for construction of superhydrophobic fabrics with phytic acid-metal complexes.206 (Copyright©2018 ACS.) (d) Dip-coating method for developing water-rich, particle-free and non-fluorinated superhydrophobic textiles.207 (Copyright©2018 Elsevier.) | |
3.2.2 Layer-by-layer (LbL) assembly.
The LbL assembly technique is commonly used to construct films with controlled surface morphology and thickness. It generally relies on the alternate deposition of negatively and positively charged materials (such as monomers, polyelectrolytes and nanoparticles) on various substrates.208,209 In particular, the LbL assembly technique has been identified as having great potential in the preparation of superwettable films because the surface textures and functional groups on the outer surface of the film can be facilely tailored.210–215
Using the LbL assembly technique, Shiratori et al. fabricated a robust and transparent hydrophilic surface with excellent antithrombogenicity and antireflective and antifogging abilities, which mainly relied on the hierarchical textures produced by the electrostatic-interaction-induced alternate deposition of poly(allylamine hydrochloride) (PAH)–poly(vinyl alcohol) (PVA)–poly(acrylic acid) (PAA) blends and PVA–PAA blends.216 A healable oil-repellent transparent antifogging film was prepared via the LbL assembly of hyaluronic acid (HA) and branched polyethylenimine (bPEI), followed by the loading of perfluorooctanesulfonic acid potassium salt (PFOS). Fig. 12a shows the remarkable antifogging behavior of the as-prepared F-(HA/bPEI). Thanks to PFOS molecules, various organic liquids can readily slide down the resulting films with a low sliding angle (<10°), and the as-prepared films displayed self-healing behavior after treatment with O2 plasma owing to the water-assisted migration of embedded PFOS molecules (Fig. 12b and c). More significantly, the resulting multilayered polyelectrolyte films exhibited unique structural healing abilities in cutting-healing and abrasion-healing tests. Because the mobility of the polyelectrolyte was increased by absorbed water molecules and the strength of the electrostatic interaction between HA and bPEI decreased fractionally, the flowing materials can cover deep and wide scratches and cuts. The impaired oil repellency, transparency and antifogging ability can be recovered.
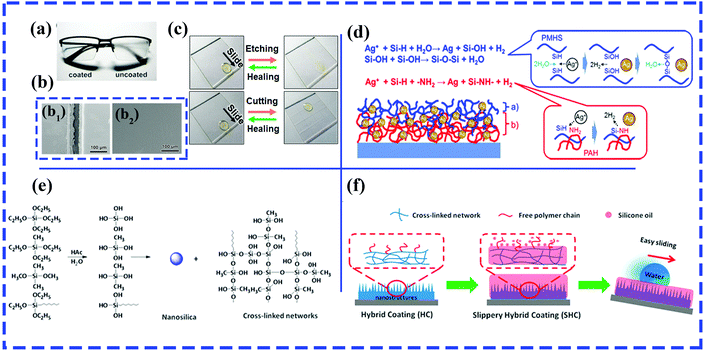 |
| Fig. 12 (a) Comparison of antifogging behavior of a pair of glasses with the left lens coated with F-(HA/bPEI). (b) SEM images of cut F-(HA/bPEI) before (b1) and after (b2) healing. (c) Comparison of wetting properties of as-prepared F-(HA/bPEI) films before and after treatment with oxygen plasma (top row) and by physical cutting (bottom row). (a–c) Reproduced with permission.217 Copyright 2017 ACS. (d) Reactions occurring on (blue color) and within (red color) the surface of the SLIC film.218 (Copyright©2017 ACS.) (e) Condensation reaction between TEOS and two silane coupling agents (MTES and OTES). (f) Schematic of silicone oil-infused hybrid coatings.220 (Copyright © 2016 ACS.) | |
In particular, a slippery liquid-immobilized multilayered polyelectrolyte film with high chemical and physical stability was fabricated via LbL assembly and the immobilization of a polymethylhydrosiloxane (PMHS) lubricant gel.217 Glass slides were first alternately immersed in solutions of positively charged poly(allylamine hydrochloride) (PAH) and negatively charged poly(acrylic acid) (PAA), followed by the loading of silver ions. The multilayered polyelectrolyte films with Ag ions and amine groups provided reactive sites for the immobilization of PMHS by the formation of Si–O–Si linkages on the outer surface and an oxidation–reduction reaction between Si–H groups and Ag ions in the middle layer of the resulting film (Fig. 12d).
3.2.3 Sol–gel method.
The sol–gel method is an ordinary wet-chemistry route for the synthesis of nanostructured particles and other desired materials.219 It is generally carried out at ambient temperature. A typical sol–gel process involves the hydroxylation and condensation of precursors including a chemical solution and a sol. Consequently, a stable, solvent-rich, three-dimensional gel network is developed after a series of hydrolysis, condensation and inorganic polymerization processes.31,219 The structures developed by the sol process play a crucial role in the properties of the gel.
Zhang et al. prepared durable and transparent silicone oil-infused hybrid coatings by impregnating silicone oils into sol–gel-derived nanoscale hybrid coatings.220 The nanoscale hybrid coatings were initially generated by an acetic acid-catalyzed condensation reaction between hydrolyzed tetraethoxysilane (TEOS) and silane coupling agents (methyltriethoxysilane and n-octyltriethoxysilane) (Fig. 12e). The sol that formed was subsequently sprayed onto glass slides/aluminum sheets, followed by a heat-induced gel formation process. After the infiltration of silicone oil into the resulting films with nanoscale roughness and abundant internal cross-linked networks (Fig. 12f), the SLIPS can retain stable and robust slip properties even under harsh working conditions, including high shear rates, elevated evaporation rates and immersion in flowing water.
Zeng et al. developed a vapor–liquid sol–gel approach to prepare a non-fluorinated and highly durable polydimethylsiloxane (PDMS)@silica-coated superhydrophobic polyester textile.221 A piece of hydrophilic textile was soaked in mixtures of tetraethoxysilane (TEOS) and hydroxy-terminated PDMS. Then, a superhydrophobic polyester fabric was obtained by means of three steps: hydrolysis and condensation of TEOS, the development of microaggregates of silica, and further condensation between hydroxy-terminated PDMS and silica. All three steps were performed in the presence of hydrogen chloride vapor. The as-prepared superhydrophobic textiles displayed outstanding durability and stability against attack by a strong acid/base, immersion in boiling/ice water, long-term ultrasonic treatment, repeated laundering and abrasion cycles and will hold great potential in our daily lives and the field of oil–water separation.
3.2.4 Electrodeposition and electropolymerization.
The strong demand for the fabrication of sophisticated micro/nanoscale structures in a fast, facile and low-cost way has enabled electrodeposition and electropolymerization techniques to become a research focus in the manufacture of functional surfaces. In general, this involves an electrochemical oxidation–reduction process that can produce hierarchically micro/nanostructured coatings on a metal or conducting polymer surface. The production of various surface topographies and precisely controlled surface structures can be tuned via electrochemical parameters of the electrodeposition process. The major drawbacks are that the substrate should be conductive and the types of substrate are restricted to metals, alloys, conducting polymers and other conductive materials. A superhydrophilic/superhydrophobic Dianthus caryophyllus-like hierarchical alumina structure was prepared by a high-speed hard anodization (HA) technique followed by modification with perfluorodecyltriethoxysilane (FAS)222 and displayed excellent corrosion inhibition and anti-biofouling abilities. A pristine aluminum plate was first electropolished in perchloric acid. Subsequently, as-prepared hierarchical structures were obtained in a simple two-electrode system in which the electropolished aluminum sheet, a platinum plate and phosphoric acid were used as the anode, cathode and electrolyte solution, respectively. A one-step gradient electrodeposition approach has been developed to prepare a copper nanoparticle-coated stainless-steel mesh with hierarchical architectures and gradients in wettability, geometrical structure and chemical composition (Fig. 13a and b).223 A liquid droplet can move along the direction of wettability gradients and surface topography gradients, whereas the direction and magnitude of wettability gradients can be controlled by changing the current gradient and flow velocity of the electrolyte, which can be achieved via a narrow-strip copper plate and a drain. Our group developed an electrochemical oxidation–polymerization approach to prepare polyaniline-coated and polypyrrole-coated stainless-steel mesh for the on-demand separation of various oil–water mixtures, including light-oil– and heavy-oil–water mixtures.224,225 More significantly, the pore size of the resulting mesh can be facilely tuned by cyclic voltammetry (CV). In this way, the mesh can achieve switchable separation of surfactant-stabilized water-in-oil and oil-in-water emulsions under gravity or a low applied pressure difference.
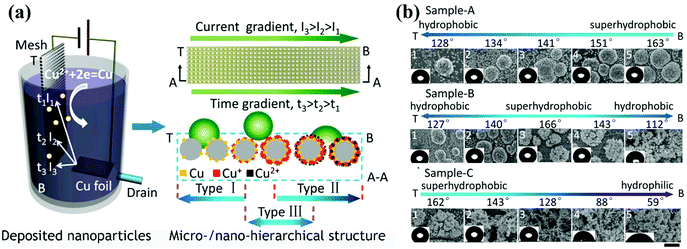 |
| Fig. 13 (a) Schematic diagram of the development of surfaces with various wetting gradients via one-step cathodic deposition by depositing copper particles on a stainless-steel mesh. A current gradient was formed by a narrow-strip copper sheet anode, and a drain was employed to control the deposition time. In this way, gradients in the chemical composition and surface topography were developed. (b) From the top zone (T) to the bottom zone (B) of the stainless-steel mesh, gradients in the wettability and structure of sample-A, sample-B and sample-C were observed. The three samples were prepared via adjusting the voltage and flow velocity of the electrolyte.223 (Copyright©2016 ACS.) | |
3.2.5 Templating methods.
Using tapered nanostructures on cicada wings as templates, Huang et al. obtained an ordered array of nanopillars on a polystyrene replica surface with hydrophobicity and antireflectivity (Fig. 14a).168 Both the structures and the functions of the surface of cicada wings were well reproduced by the replica counterpart. A superhydrophobic–superhydrophilic porous poly(vinylidene fluoride) (PVDF)–multiwalled carbon nanotube (MWCNT) foam was developed by a simple solvent-free method using table salt as a sacrificial template (Fig. 14b–g).226 The table salt particles were removed after immersion in water for 24 h, and porous structures with an interconnected 3D framework were subsequently developed. The use of MWCNT can provide additional roughness on hydrophobic PVDF skeletons by forming submicron structures. Thus, the dose of MWCNT can have obvious impacts on the hydrophobic property of the resulting foams. A durable and stretchable polydimethylsiloxane (PDMS) sponge was fabricated by a cost-effective sugar leaching method.227 Sugar cubes as templates were first immersed in a mixture of a PDMS prepolymer and a curing agent, followed by degassing for 2 h and curing in an oven at 60 °C for 3 h (Fig. 14h). After being immersing in a hot water bath (60 °C), the sugar dissolved and a porous PDMS sponge was obtained. The hydrophobic sponges were transformed into hydrophilic sponges via treatment with air plasma and modification by dip-coating with polyvinyl alcohol (PVA). More significantly, without external power sources independent and continuous transport of liquids was achieved via a combination of capillary wicking and evaporation of water. This leaf-like pumping strategy has great potential in microfluidic devices. Recently, novel metal–organic inverse opals have been fabricated via colloidal templating,225,229 which indicates that this templating method provides a great opportunity for the construction of novel optical devices.
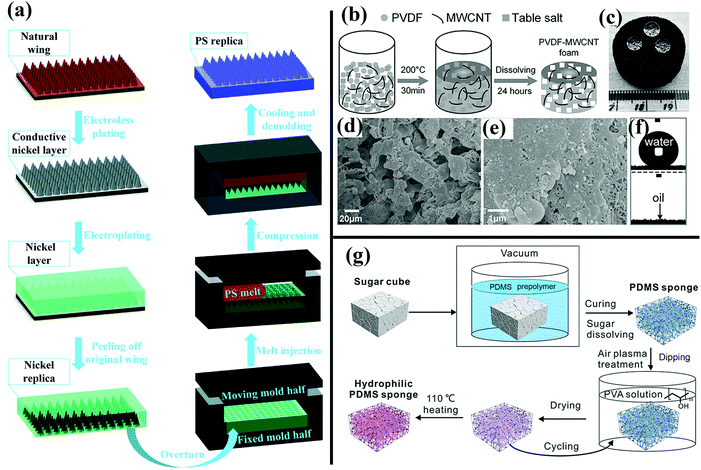 |
| Fig. 14 (a) Schematic of the fabrication of a hydrophobic PS surface templated by cicada wings.168 (Copyright©2017 RSC.) (b) Schematic illustration of preparation of as-prepared PVDF–MWCNT foam. (c and f) Superhydrophobic and superoleophilic behavior of the as-prepared PVDF–MWCNT foam. (d and e) SEM images of the resulting foam. (b–f) Reproduced with permission.226 (Copyright©2017 John Wiley & Sons, Inc.) (g) Illustration of preparation of hydrophilic PVA-modified PDMS–MWCNT foam.227 (Copyright©2017 John Wiley & Sons, Inc.) | |
Besides the abovementioned biomimetic materials, other typical bioinspired functional materials have been extensively investigated, including glass, glass slides, fabrics, sponges, stainless-steel mesh, Si wafers, silica-based materials, inorganic clays, carbon materials, metals and metallic oxides, polymers and hybrid materials.230–249
4. Cutting-edge applications of superwetting functional surfaces
Bioinspired superwetting functional surfaces have various vital applications in scientific research and industrial fields. For instance, a superstrong superamphiphobic textile was prepared using a particle-free polymer coating system.250 As well as outstanding liquid resistance behavior, the as-prepared textile displayed remarkable chemical stability. As shown in Fig. 15a, the coated fabric remained intact when immersed in 98% H2SO4, whereas the pristine textile was degraded. Another significant application of bioinspired superwetting functional surfaces is the enhancement of catalytic efficiency. Feng et al. fabricated a novel photocatalytic system in which anatase-phase TiO2 nanoparticles were anchored onto a superhydrophobic carbon fiber substrate treated with polytetrafluoroethylene.251 The presence of a combined gas/liquid/solid interface virtually suppressed electron–hole recombination, because abundant oxygen was rapidly delivered to the reaction interface, which resulted in a 10-fold increase in the photocatalytic reaction rate in comparison with previous binary-phase systems (Fig. 15b). Thanks to air pockets trapped inside hierarchical structures, super-non-wetting surfaces (especially superhydrophobic species) have great potential for the sustained release of drugs. Zhai et al. prepared electrically actuated nanochannels by immobilizing a perfluorooctanesulfonate (PFOS) ion-doped micro/nanoporous polypyrrole (PPy) film on the surface of an anodic aluminum oxide (AAO) membrane.252 Owing to the wettability-reversible conversion behavior of PPy under a redox potential, the open/closed state of nanochannels can be achieved. More significantly, as-prepared nanochannels with an unprecedentedly high ion gating ratio (over 105) can be further employed in on-demand drug delivery owing to their highly efficient and reversible gating behavior (Fig. 15c). Anionic penicillin G sodium and cationic rhodamine B, which were chosen as model drugs, can be released in a pulsatile way. Fig. 15d shows the separation of organic liquid mixtures of formamide (dyed with methylene blue) and carbon tetrachloride (CCl4) (dyed with Sudan II) using a copper mesh covered with perfluorodecyltriethoxysilane-modified nanoneedles.253 Using the evident difference in surface tension between two different organic liquids, the separation of organic solvents can be feasibly achieved with membranes or other separation materials. A microchip for efficient surface-enhanced Raman scattering (SERS) was obtained on a superhydrophobic substrate patterned with an array of superhydrophilic Au areole dots.254 The as-prepared microchips can achieve the highly sensitive detection of diverse bioanalytes (Fig. 15e). Further significant applications of bioinspired superwetting functional surfaces include sensors for the detection of target analytes in the fields of analytical chemistry, biomedicine and environmental monitoring. Superhydrophobic/superhydrophilic patterned hollow spherical colloidal photonic crystals were prepared to achieve real-time ultrasensitive fluorescence detection.255 As shown in Fig. 15f, the fluorescence intensity was dramatically enhanced. Furthermore, bioinspired superwetting functional surfaces hold great potential for controlling bioadhesion. For example, extremely low attachment of mussels was achieved using SLIPS coatings, which is of vital importance for addressing the issue of marine biofouling (Fig. 15g).256 Bioinspired superwetting surfaces have been applied in energy devices over the past few years. A superhydrophobic quasi-solid electrolyte (SHQSE) suppressed the detrimental growth of dendrites caused by the extensive reaction between Li metal and water, which enabled as-prepared Li–air batteries to exhibit higher stability and a longer service life in a humid atmosphere (RH of 45%) in comparison with ordinary solid Li-ion batteries (Fig. 15h).257
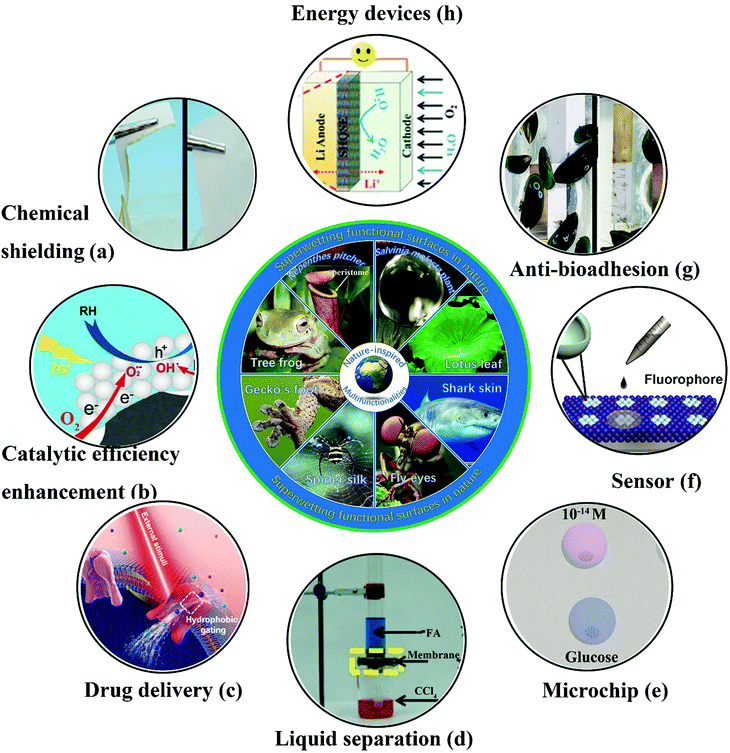 |
| Fig. 15 Cutting-edge applications of bioinspired superwetting functional surfaces. (a) In comparison with the pristine fabric (left), a piece of superomniphobic fabric remained intact when immersed in 98% H2SO4. Reproduced with permission.230 (Copyright©2015 John Wiley and Sons.) (b) Schematic illustration of a solid–liquid–gas triphase superhydrophobic photocatalytic reaction system.231 The availability of sufficient oxygen near the photocatalyst induced by the presence of the triphase interface limits the opportunity for the recombination of electrons and holes. (Copyright©2018 ACS.) (c) Schematic of the wettability-induced tunable gating behavior of biological ion channels under external stimuli. In this way, a drug release process can be controlled in a smart manner.232 (Copyright©2018 John Wiley and Sons.) (d) Using a robust mesh of Cu(OH)2 nanoneedles with tunable wettability, formamide (FA) and carbon tetrachloride (CCl4) can be separated facilely. Reproduced with permission.228 (Copyright©2017 John Wiley and Sons.) (e) A microchip for efficient surface-enhanced Raman scattering (SERS) was fabricated on a superwetting patterned surface and was highly sensitive towards diverse analytes. Reproduced with permission.234 (Copyright©2018 John Wiley and Sons.) (f) Real-time ultrasensitive fluorescence detection was realized on wettability-patterned surfaces consisting of hollow spherical colloidal photonic crystals.235 (Copyright©2017 ACS.) (g) In comparison with the pristine substrate, a silicone oil-infused surface displayed less adhesion of mussels.236 (Copyright©2018 AAAS.) (h) The safety and lifespan of an Li-ion battery were enhanced because the presence of a superhydrophobic electrolyte prevented the crossover of water to the Li metal anode.237 (Copyright©2016 John Wiley and Sons.) | |
5. Summary and outlook
In this review, we have summarized recent advances (especially those in the last three years) in double-structural bioinspired functional materials with specific wettability, ranging from simple superwetting surfaces to other functional surfaces associated with wetting behavior, including superhydrophobic surfaces, superhydrophilic/underwater superoleophobic surfaces, superoleophobic/superomniphobic surfaces, unconventional superwetting surfaces, surfaces with high/low adhesion, fluid-drag-reducing surfaces, structural color, antireflective surfaces and so forth. Every manmade technique or material with a specific function will have natural prototypes. With regard to approaches used for manufacturing, classical top-down and bottom-up fabrication methods have been reported, including lithography, etching, physical deposition, LbL assembly, sol–gel, electrodeposition and templating protocols. The investigation of hierarchical micro- and nanostructures has not only received fundamental scientific interest but also demonstrated promising practical applications in industrial fields. Finally, novel cutting-edge applications have been described.
The idea of the fabrication of superwetting functional materials according to natural design motifs has become a hot research topic in the fields of materials science and surface chemistry. Although various fruitful results have been achieved, research into artificial biomimetic surfaces with superior multiple functionalities is far from mature. Firstly, unrevealed impressive natural prototypes remain to be discovered. For instance, since the effect of the Nepenthes pitcher plant was discovered by Aizenberg in 2011,84 corresponding bioinspired investigations with the aim of mimicking its remarkable liquid resistance and unidirectional transport of liquid droplets have flourished. In particular, lubricating liquids bound in porous structures play an essential role in desirable antifouling properties. However, a major drawback is the loss of lubricating liquids under high shear rates, friction, elevated evaporation rates and other harsh working conditions. In this case, omniphobic and antifouling behavior will not be achieved. With the inspiration of earthworms, a flexible coating of a copolymer of urea and polydimethylsiloxane (PDMS) with self-replenishing lubricating properties was prepared by the breath figure method under humid conditions.258 In contrast to surfaces inspired by the Nepenthes pitcher plant, highly durable antifouling behavior was achieved on surfaces inspired by earthworms because of the adaptive release of lubricating liquid after friction-induced consumption of the lubricating layer, which indicates that nature always provides the optimal schemes for the solution of real-world issues that occur in biomimetic systems.
Secondly, it is exceedingly difficult but highly desirable to translate natural design motifs into manmade materials. The development of multiscale modelling provides a better solution for constructing bridges between natural structures and behavior. For example, since the overhang structures on springtail skins were revealed, various integrated computational models have increasingly been developed, which offer meaningful guidance for the construction of superomniphobic surfaces with mushroom-like, trapezoidal, fibrous and other re-entrant structures.64,66,67 The precise translation of natural design motifs requires a deep understanding of the impressive functions of living organisms and structures on all length scales.
Thirdly, suitable techniques for processing and fabrication also pose great challenges for facilitating the large-scale production of current lab-scale biomimetic superwetting materials. On the one hand, the remarkable functions and performance of natural bioinspired materials are not fully inherited by manmade counterparts fabricated by simple copying or duplication. The precise control of the assembly and arrangement of building blocks or modules under mild conditions is still a prerequisite for ideal multiple functionalities. Superwetting functional materials with integrated multiple functionalities are highly desirable. For example, nacre not only has outstanding strength and stiffness but also displays unique underwater superoleophobic behavior.259 On the other hand, nanoscale preparation techniques will pioneer the field of the mass production of bioinspired functional materials. State-of-the-art nanofabrication approaches, such as direct inkjet printing and 3D printing, will enable the large-scale production and industrialization of superwetting bioinspired functional materials.
Countless living organisms have evolved sophisticated structures and intriguing behavior that provide us with blueprints to emulate. Accordingly, numerous notable achievements have been obtained. In the near future, we believe that more significant progress will be realized in the fabrication and application of superwetting bioinspired functional materials with micro/nanostructures, as well as in the mass production of such bioinspired materials. In addition, the major drawbacks of superwetting bioinspired functional materials, such as poor durability and optical transparency, will be circumvented. More dynamic functions of biological prototypes, such as self-shaping, self-adaptation, self-healing and stimuli-responsiveness, will be mimicked by engineered materials, which will provide a driving force for progress in superwetting bioinspired functional materials for years to come.
Conflicts of interest
The authors declare no conflict of interest.
Acknowledgements
This work was financially supported by the National Natural Science Foundation of China (no. 51522510, 51675513 and 51735013).
Notes and references
- F. Barthelat, Z. Yin and M. J. Buehler, Nat. Rev. Mater., 2016, 1, 16007 CrossRef CAS.
- R. R. Naik and S. Singamaneni, Chem. Rev., 2017, 117, 12581–12583 CrossRef CAS PubMed.
- S. Vignolini and N. Bruns, Adv. Mater., 2018, 30, e1801687 CrossRef PubMed.
- N. Zhao, Z. Wang, C. Cai, H. Shen, F. Liang, D. Wang, C. Wang, T. Zhu, J. Guo, Y. Wang, X. Liu, C. Duan, H. Wang, Y. Mao, X. Jia, H. Dong, X. Zhang and J. Xu, Adv. Mater., 2014, 26, 6994–7017 CrossRef CAS PubMed.
- A. Heuer, D. Fink, V. Laraia, J. Arias, P. Calvert, K. Kendall, G. Messing, J. Blackwell, P. Rieke and D. Thompson,
et al.
, Science, 1992, 255, 1098–1105 CrossRef CAS PubMed.
- F. Song, A. K. Soh and Y. L. Bai, Biomaterials, 2003, 24, 3623–3631 CrossRef CAS PubMed.
- F. Jiang, T. Li, Y. Li, Y. Zhang, A. Gong, J. Dai, E. Hitz, W. Luo and L. Hu, Adv. Mater., 2018, 30, 1703453 CrossRef PubMed.
- J. Song, C. Chen, S. Zhu, M. Zhu, J. Dai, U. Ray, Y. Li, Y. Kuang, Y. Li, N. Quispe, Y. Yao, A. Gong, U. H. Leiste, H. A. Bruck, J. Y. Zhu, A. Vellore, H. Li, M. L. Minus, Z. Jia, A. Martini, T. Li and L. Hu, Nature, 2018, 554, 224–228 CrossRef CAS PubMed.
- L. Wen, Y. Tian and L. Jiang, Angew. Chem., Int. Ed., 2015, 54, 3387–3399 CrossRef CAS PubMed.
- B. Su, Y. Tian and L. Jiang, J. Am. Chem. Soc., 2016, 138, 1727–1748 CrossRef CAS PubMed.
- S. Wang, K. Liu, X. Yao and L. Jiang, Chem. Rev., 2015, 115, 8230–8293 CrossRef CAS PubMed.
- Y. Tian, B. Su and L. Jiang, Adv. Mater., 2014, 26, 6872–6897 CrossRef CAS PubMed.
- Y. Zhang, Y. Chen, L. Shi, J. Li and Z. Guo, J. Mater. Chem., 2012, 22, 799–815 RSC.
- E. P. Ivanova, J. Hasan, H. K. Webb, V. K. Truong, G. S. Watson, J. A. Watson, V. A. Baulin, S. Pogodin, J. Y. Wang and M. J. Tobin, Small, 2012, 8, 2489–2494 CrossRef CAS PubMed.
- M. Sun, G. S. Watson, Y. Zheng, J. A. Watson and A. Liang, J. Exp. Biol., 2009, 212, 3148–3155 CrossRef PubMed.
- M. Wei-Lun, J. Bin and J. Peng, Adv. Mater., 2008, 20, 3914–3918 CrossRef.
- K. Autumn, M. Sitti, Y. A. Liang, A. M. Peattie, W. R. Hansen, S. Sponberg, T. W. Kenny, R. Fearing, J. N. Israelachvili and R. J. Full, Proc. Natl. Acad. Sci. U. S. A., 2002, 99, 12252–12256 CrossRef CAS PubMed.
- M. Kamperman, E. Kroner, A. del Campo, R. M. McMeeking and E. Arzt, Adv. Eng. Mater., 2010, 12, 335–348 CrossRef CAS.
- F. L. Nathan, V. Paul and J. P. Tony, Bioinspiration Biomimetics, 2013, 8, 013001 CrossRef PubMed.
- U. G. K. Wegst, H. Bai, E. Saiz, A. P. Tomsia and R. O. Ritchie, Nat. Mater., 2014, 14, 23 CrossRef PubMed.
- F. Xia and L. Jiang, Adv. Mater., 2008, 20, 2842–2858 CrossRef CAS.
- H. F. Hoefnagels, D. Wu, G. de With and W. Ming, Langmuir, 2007, 23, 13158–13163 CrossRef CAS PubMed.
- J. Zimmermann, F. A. Reifler, G. Fortunato, L.-C. Gerhardt and S. Seeger, Adv. Funct. Mater., 2008, 18, 3662–3669 CrossRef CAS.
- S. Li, J. Huang, Z. Chen, G. Chen and Y. Lai, J. Mater. Chem. A, 2017, 5, 31–55 RSC.
- S. Pan, R. Guo and W. Xu, AIChE J., 2014, 60, 2752–2756 CrossRef CAS.
- T. Zhu, J. Wu, N. Zhao, C. Cai, Z. Qian, F. Si, H. Luo, J. Guo, X. Lai, L. Shao and J. Xu, Adv. Healthcare Mater., 2018, 7, 1701086 CrossRef PubMed.
- M. J. Kreder, J. Alvarenga, P. Kim and J. Aizenberg, Nat. Rev. Mater., 2016, 1, 15003 CrossRef CAS.
- U. Mehmood, F. A. Al-Sulaiman, B. S. Yilbas, B. Salhi, S. H. A. Ahmed and M. K. Hossain, Sol. Energy Mater. Sol. Cells, 2016, 157, 604–623 CrossRef CAS.
- R. Fang, M. Liu, H. Liu and L. Jiang, Adv. Mater. Interfaces, 2018, 5, 1701176 CrossRef.
- Q. Shang and Y. Zhou, Ceram. Int., 2016, 42, 8706–8712 CrossRef CAS.
- Y. Si and Z. Guo, Nanoscale, 2015, 7, 5922–5946 RSC.
- G. Wen, Z. Guo and W. Liu, Nanoscale, 2017, 9, 3338–3366 RSC.
- D. Zhang, H. Qian, L. Wang and X. Li, Corros. Sci., 2016, 103, 230–241 CrossRef CAS.
- F. Zhang, W. B. Zhang, Z. Shi, D. Wang, J. Jin and L. Jiang, Adv. Mater., 2013, 25, 4192–4198 CrossRef CAS PubMed.
- B. Wang, W. Liang, Z. Guo and W. Liu, Chem. Soc. Rev., 2015, 44, 336–361 RSC.
- W. Zhang, Y. Zhu, X. Liu, D. Wang, J. Li, L. Jiang and J. Jin, Angew. Chem., Int. Ed., 2014, 53, 856–860 CrossRef CAS PubMed.
- Z. Xue, S. Wang, L. Lin, L. Chen, M. Liu, L. Feng and L. Jiang, Adv. Mater., 2011, 23, 4270–4273 CrossRef CAS PubMed.
- M. S. Bell, A. Shahraz, K. A. Fichthorn and A. Borhan, Langmuir, 2015, 31, 6752–6762 CrossRef CAS PubMed.
- H. Jang, H. S. Lee, K.-S. Lee and D. R. Kim, ACS Appl. Mater. Interfaces, 2017, 9, 9213–9220 CrossRef CAS PubMed.
- B. Won-Gyu, K. H. Nam, K. Doogon, P. Suk-Hee, J. H. Eui and S. Kahp-Yang, Adv. Mater., 2014, 26, 675–700 CrossRef PubMed.
- A. B. D. Cassie and S. Baxter, Trans. Faraday Soc., 1944, 40, 0546–0550 RSC.
- R. N. Wenzel, Ind. Eng. Chem., 1936, 28, 988–994 CrossRef CAS.
- K. Koch, B. Bhushan, Y. C. Jung and W. Barthlott, Soft Matter, 2009, 5, 1386–1393 RSC.
- T. Verho, J. T. Korhonen, L. Sainiemi, V. Jokinen, C. Bower, K. Franze, S. Franssila, P. Andrew, O. Ikkala and R. H. A. Ras, Proc. Natl. Acad. Sci. U. S. A., 2012, 109, 10210–10213 CrossRef CAS PubMed.
- D. Zang, R. Zhu, W. Zhang, X. Yu, L. Lin, X. Guo, M. Liu and L. Jiang, Adv. Funct. Mater., 2017, 27, 1605446 CrossRef.
- Y. Zhu, F. Sun, H. Qian, H. Wang, L. Mu and J. Zhu, Chem. Eng. J., 2018, 338, 670–679 CrossRef CAS.
- Y. Su, B. Ji, K. Zhang, H. Gao, Y. Huang and K. Hwang, Langmuir, 2010, 26, 4984–4989 CrossRef CAS PubMed.
- W. Barthlott and C. Neinhuis, Planta, 1997, 202, 1–8 CrossRef CAS.
- C. Neinhuis and W. Barthlott, Ann. Bot., 1997, 79, 667–677 CrossRef.
- L. Zhang, Z. Zhou, B. Cheng, J. M. DeSimone and E. T. Samulski, Langmuir, 2006, 22, 8576–8580 CrossRef CAS PubMed.
- R. Mohammadi, J. Wassink and A. Amirfazli, Langmuir, 2004, 20, 9657–9662 CrossRef CAS PubMed.
- K.-Y. Yeh, L.-J. Chen and J.-Y. Chang, Langmuir, 2008, 24, 245–251 CrossRef CAS PubMed.
- L. Feng, S. Li, Y. Li, H. Li, L. Zhang, J. Zhai, Y. Song, B. Liu, L. Jiang and D. Zhu, Adv. Mater., 2002, 14, 1857–1860 CrossRef CAS.
- M. Liu, S. Wang and L. Jiang, Nat. Rev. Mater., 2017, 2, 17036 CrossRef CAS.
- H.-B. Jiang, Y.-Q. Liu, Y.-L. Zhang, Y. Liu, X.-Y. Fu, D.-D. Han, Y.-Y. Song, L. Ren and H.-B. Sun, ACS Appl. Mater. Interfaces, 2018, 10, 18416–18425 CrossRef CAS PubMed.
- A. K. Epstein, B. Pokroy, A. Seminara and J. Aizenberg, Proc. Natl. Acad. Sci. U. S. A., 2011, 108, 995–1000 CrossRef CAS PubMed.
- R. Helbig, J. Nickerl, C. Neinhuis and C. Werner, PLoS One, 2011, 6, e25105 CrossRef CAS PubMed.
- R. Hensel, R. Helbig, S. Aland, H.-G. Braun, A. Voigt, C. Neinhuis and C. Werner, Langmuir, 2013, 29, 1100–1112 CrossRef CAS PubMed.
- J. Nickerl, R. Helbig, H.-J. Schulz, C. Werner and C. Neinhuis, Zoomorphology, 2013, 132, 183–195 CrossRef.
- J. Nickerl, M. Tsurkan, R. Hensel, C. Neinhuis and C. Werner, J. R. Soc., Interface, 2014, 11, 20140619 CrossRef PubMed.
- R. Rakitov and S. N. Gorb, Proc. R. Soc. B, 2013, 280, 20122391 CrossRef PubMed.
- H. Bellanger, T. Darmanin, E. Taffin de Givenchy and F. Guittard, Chem. Rev., 2014, 114, 2694–2716 CrossRef CAS PubMed.
- P. S. Brown and B. Bhushan, APL Mater., 2016, 4, 015703 CrossRef.
- L. Chen, Z. Guo and W. Liu, J. Mater. Chem. A, 2017, 5, 14480–14507 RSC.
- H. Liu, Y. Wang, J. Huang, Z. Chen, G. Chen and Y. Lai, Adv. Funct. Mater., 2018, 28, 1707415 CrossRef.
- A. Tuteja, W. Choi, M. Ma, J. M. Mabry, S. A. Mazzella, G. C. Rutledge, G. H. McKinley and R. E. Cohen, Science, 2007, 318, 1618–1622 CrossRef CAS PubMed.
- J. Yong, F. Chen, Q. Yang, J. Huo and X. Hou, Chem. Soc. Rev., 2017, 46, 4168–4217 RSC.
- F.-M. Chang, S.-J. Hong, Y.-J. Sheng and H.-K. Tsao, J. Phys. Chem. C, 2010, 114, 1615–1621 CrossRef CAS.
- R. L. Webb, Heat Transfer Eng., 1981, 2, 46–69 CrossRef.
- T. L. Liu and C.-J. C. Kim, Science, 2014, 346, 1096–1100 CrossRef CAS PubMed.
- X. Liu, H. Gu, M. Wang, X. Du, B. Gao, A. Elbaz, L. Sun, J. Liao, P. Xiao and Z. Gu, Adv. Mater., 2018, 30, 1800103 CrossRef PubMed.
- L. Chen, Z. Guo and W. Liu, ACS Appl. Mater. Interfaces, 2016, 8, 27188–27198 CrossRef CAS PubMed.
- Y. Wu, S. Zhou, B. You and L. Wu, ACS Nano, 2017, 11, 8265–8272 CrossRef CAS PubMed.
- L. Lin, M. Liu, L. Chen, P. Chen, J. Ma, D. Han and L. Jiang, Adv. Mater., 2010, 22, 4826–4830 CrossRef CAS PubMed.
- Y. C. Jung and B. Bhushan, Langmuir, 2009, 25, 14165–14173 CrossRef CAS PubMed.
- T. Guo, L. Heng, M. Wang and L. Jiang, Adv. Mater., 2016, 28, 8505–8510 CrossRef CAS PubMed.
- X. Meng, M. Wang, L. Heng and L. Jiang, Adv. Mater., 2018, 30, 1706634 CrossRef PubMed.
- C. Baum, F. Simon, W. Meyer, L.-G. Fleischer, D. Siebers, J. Kacza and J. Seeger, Biofouling, 2003, 19, 181–186 CrossRef CAS PubMed.
- G. D. Bixler and B. Bhushan, Nanoscale, 2013, 5, 7685–7710 RSC.
- M. J. Liu, S. T. Wang, Z. X. Wei, Y. L. Song and L. Jiang, Adv. Mater., 2009, 21, 665–669 CrossRef CAS.
- X. L. Liu, J. Zhou, Z. X. Xue, J. Gao, J. X. Meng, S. T. Wang and L. Jiang, Adv. Mater., 2012, 24, 3401–3405 CrossRef CAS PubMed.
- Y. Cai, L. Lin, Z. X. Xue, M. J. Liu, S. T. Wang and L. Jiang, Adv. Funct. Mater., 2014, 24, 809–816 CrossRef CAS.
- Y. Cai, Q. Lu, X. Guo, S. Wang, J. Qiao and L. Jiang, Adv. Mater., 2015, 27, 4162–4168 CrossRef CAS PubMed.
- T.-S. Wong, S. H. Kang, S. K. Y. Tang, E. J. Smythe, B. D. Hatton, A. Grinthal and J. Aizenberg, Nature, 2011, 477, 443 CrossRef CAS PubMed.
- C. S. Ware, T. Smith-Palmer, S. Peppou-Chapman, L. R. J. Scarratt, E. M. Humphries, D. Balzer and C. Neto, ACS Appl. Mater. Interfaces, 2018, 10, 4173–4182 CrossRef CAS PubMed.
- M. Liu, Y. Hou, J. Li, L. Tie and Z. Guo, Chem. Eng. J., 2018, 337, 462–470 CrossRef CAS.
- S. Sunny, N. Vogel, C. Howell, T. L. Vu and J. Aizenberg, Adv. Funct. Mater., 2014, 24, 6658–6667 CrossRef CAS.
- Y. Wang, B. Qian, C. Lai, X. Wang, K. Ma, Y. Guo, X. Zhu, B. Fei and J. H. Xin, ACS Appl. Mater. Interfaces, 2017, 9, 24428–24432 CrossRef CAS PubMed.
- H. Liu, P. Zhang, M. Liu, S. Wang and L. Jiang, Adv. Mater., 2013, 25, 4477–4481 CrossRef CAS PubMed.
- C. Urata, G. J. Dunderdale, M. W. England and A. Hozumi, J. Mater. Chem. A, 2015, 3, 12626–12630 RSC.
- Y. Wang, X. Yao, S. Wu, Q. Li, J. Lv, J. Wang and L. Jiang, Adv. Mater., 2017, 29, 1700865 CrossRef PubMed.
- Q. Wei, C. Schlaich, S. Prevost, A. Schulz, C. Bottcher, M. Gradzielski, Z. Qi, R. Haag and C. A. Schalley, Adv. Mater., 2014, 26, 7358–7364 CrossRef CAS PubMed.
- X. Yao, L. Chen, J. Ju, C. Li, Y. Tian, L. Jiang and M. Liu, Adv. Mater., 2016, 28, 7383–7389 CrossRef CAS PubMed.
- X. Yao, J. Ju, S. Yang, J. Wang and L. Jiang, Adv. Mater., 2014, 26, 1895–1900 CrossRef CAS PubMed.
- X. Yao, S. Wu, L. Chen, J. Ju, Z. Gu, M. Liu, J. Wang and L. Jiang, Angew. Chem., Int. Ed. Engl., 2015, 54, 8975–8979 CrossRef CAS PubMed.
- P. Zhang, H. Liu, J. Meng, G. Yang, X. Liu, S. Wang and L. Jiang, Adv. Mater., 2014, 26, 3131–3135 CrossRef CAS PubMed.
- M. Liu, L. Tie, J. Li, Y. Hou and Z. Guo, J. Mater. Chem. A, 2018, 6, 1692–1699 RSC.
- L. Tie, J. Li, M. Liu, Z. Guo, Y. Liang and W. Liu, J. Mater. Chem. A, 2018, 6, 11682–11687 RSC.
- A. Finnemore, P. Cunha, T. Shean, S. Vignolini, S. Guldin, M. Oyen and U. Steiner, Nat. Commun., 2012, 3, 966 CrossRef PubMed.
- X. Q. Li and H. C. Zeng, Adv. Mater., 2012, 24, 6277–6282 CrossRef CAS PubMed.
- Z. Tang, N. A. Kotov, S. Magonov and B. Ozturk, Nat. Mater., 2003, 2, 413 CrossRef CAS PubMed.
- A. Walther, I. Bjurhager, J. M. Malho, J. Ruokolainen, L. Berglund and O. Ikkala, Angew. Chem., Int. Ed., 2010, 49, 6448–6453 CrossRef CAS PubMed.
- H. B. Yao, Z. H. Tan, H. Y. Fang and S. H. Yu, Angew. Chem., Int. Ed., 2010, 49, 10127–10131 CrossRef CAS PubMed.
- K. Autumn, Y. A. Liang, S. T. Hsieh, W. Zesch, W. P. Chan, T. W. Kenny, R. Fearing and R. J. Full, Nature, 2000, 405, 681 CrossRef CAS PubMed.
- X.-Q. Dou, D. Zhang, C. Feng and L. Jiang, ACS Nano, 2015, 9, 10664–10672 CrossRef CAS PubMed.
- J. Huang, Y. Lai, L. Wang, S. Li, M. Ge, K. Zhang, H. Fuchs and L. Chi, J. Mater. Chem. A, 2014, 2, 18531–18538 RSC.
- K. Liu, J. Du, J. Wu and L. Jiang, Nanoscale, 2012, 4, 768–772 RSC.
- M. Liu, Y. Zheng, J. Zhai and L. Jiang, Acc. Chem. Res., 2010, 43, 368–377 CrossRef CAS PubMed.
- S. Reddy, E. Arzt and A. del
Campo, Adv. Mater., 2007, 19, 3833–3837 CrossRef CAS.
- L. Feng, Y. Zhang, J. Xi, Y. Zhu, N. Wang, F. Xia and L. Jiang, Langmuir, 2008, 24, 4114–4119 CrossRef CAS PubMed.
- P. Chen, L. Chen, D. Han, J. Zhai, Y. Zheng and L. Jiang, Small, 2009, 5, 908–912 CrossRef CAS PubMed.
- Y. Zheng, D. Han, J. Zhai and L. Jiang, Appl. Phys. Lett., 2008, 92, 084106 CrossRef.
- L. Barbieri, E. Wagner and P. Hoffmann, Langmuir, 2007, 23, 1723–1734 CrossRef CAS PubMed.
- C. W. Extrand, Langmuir, 2004, 20, 5013–5018 CrossRef CAS PubMed.
- M. Liu and L. Jiang, Adv. Funct. Mater., 2010, 20, 3753–3764 CrossRef CAS.
- W. Barthlott, S. Wiersch, Z. Čolić and K. Koch, Botany, 2009, 87, 830–836 CrossRef.
- B. J. Glover and H. M. Whitney, Ann. Bot., 2010, 105, 505–511 CrossRef PubMed.
- W. Barthlott, T. Schimmel, S. Wiersch, K. Koch, M. Brede, M. Barczewski, S. Walheim, A. Weis, A. Kaltenmaier, A. Leder and H. F. Bohn, Adv. Mater., 2010, 22, 2325–2328 CrossRef CAS PubMed.
- Y. Yang, X. Li, X. Zheng, Z. Chen, Q. Zhou and Y. Chen, Adv. Mater., 2018, 30, 1704912 CrossRef PubMed.
- C. Zeiger, I. C. R. da Silva, M. Mail, M. N. Kavalenka, W. Barthlott and H. Holscher, Bioinspiration Biomimetics, 2016, 11, 9 Search PubMed.
- H. K. Raut, A. Baji, H. H. Hariri, H. Parveen, G. S. Soh, H. Y. Low and K. L. Wood, ACS Appl. Mater. Interfaces, 2018, 10, 1288–1296 CrossRef CAS PubMed.
- D. M. Drotlef, E. Appel, H. Peisker, K. Dening, A. del Campo, S. N. Gorb and W. J. P. Barnes, Interface Focus, 2015, 5, 20140036 CrossRef PubMed.
- J. Iturri, L. Xue, M. Kappl, L. Garcia-Fernandez, W. J. P. Barnes, H.-J. Butt and A. del Campo, Adv. Funct. Mater., 2015, 25, 1499–1505 CrossRef CAS.
- L. Xue, B. Sanz, A. Luo, K. T. Turner, X. Wang, D. Tan, R. Zhang, H. Du, M. Steinhart, C. Mijangos, M. Guttmann, M. Kappl and A. del Campo, ACS Nano, 2017, 11, 9711–9719 CrossRef CAS PubMed.
- K. Autumn, C. Majidi, R. E. Groff, A. Dittmore and R. Fearing, J. Exp. Biol., 2006, 209, 3558–3568 CrossRef CAS PubMed.
- A. Jagota and S. J. Bennison, Integr. Comp. Biol., 2002, 42, 1140–1145 CrossRef PubMed.
- B. N. J. Persson, J. Chem. Phys., 2003, 118, 7614–7621 CrossRef CAS.
- D. S. Kosov, J. Chem. Phys., 2003, 119, 1–5 CrossRef CAS.
- H. E. Jeong and K. Y. Suh, Nano Today, 2009, 4, 335–346 CrossRef CAS.
- W. J. P. Barnes, P. J. P. Goodwyn, M. Nokhbatolfoghahai and S. N. Gorb, J. Comp. Physiol., A, 2011, 197, 969 CrossRef PubMed.
- W. J. P. Barnes, C. Oines and J. M. Smith, J. Comp. Physiol., A, 2006, 192, 1179–1191 CrossRef PubMed.
- W. Federle, W. J. P. Barnes, W. Baumgartner, P. Drechsler and J. M. Smith, J. R. Soc., Interface, 2006, 3, 689–697 CrossRef CAS PubMed.
- V. Mizuhira, J. Electron Microsc., 2004, 53, 63–78 CrossRef PubMed.
- W. J. P. Barnes, M. Baum, H. Peisker and S. N. Gorb, J. Morphol., 2013, 274, 1384–1396 CrossRef PubMed.
- S. Chakraborti, D. Das, S. K. De and T. C. Nag, Acta Zool., 2014, 95, 63–72 CrossRef.
- P. Ball, Nature, 1999, 400, 507 CrossRef CAS.
- D. W. Bechert, M. Bruse and W. Hage, Exp. Fluids, 2000, 28, 403–412 CrossRef.
- J. P. Rothstein, Annu. Rev. Fluid Mech., 2010, 42, 89–109 CrossRef.
- G. D. Bixler and B. Bhushan, Adv. Funct. Mater., 2013, 23, 4507–4528 CrossRef CAS.
- B. Dean and B. Bhushan, Philos. Trans. R. Soc., A, 2010, 368, 4775–4806 CrossRef PubMed.
- G. B. Hwang, A. Patir, K. Page, Y. Lu, E. Allan and I. P. Parkin, Nanoscale, 2017, 9, 7588–7594 RSC.
- M. N. Kavalenka, F. Vüllers, S. Lischker, C. Zeiger, A. Hopf, M. Röhrig, B. E. Rapp, M. Worgull and H. Hölscher, ACS Appl. Mater. Interfaces, 2015, 7, 10651–10655 CrossRef CAS PubMed.
- E. S. A. Goerlitzer, R. N. K. Taylor and N. Vogel, Adv. Mater., 2018, 30, 1706654 CrossRef PubMed.
- H. Zhou, J. Xu, X. Liu, H. Zhang, D. Wang, Z. Chen, D. Zhang and T. Fan, Adv. Funct. Mater., 2018, 28, 1705309 CrossRef.
- M. Kuang, J. Wang and L. Jiang, Chem. Soc. Rev., 2016, 45, 6833–6854 RSC.
- S. Tadepalli, J. M. Slocik, M. K. Gupta, R. R. Naik and S. Singamaneni, Chem. Rev., 2017, 117, 12705–12763 CrossRef CAS PubMed.
- K. Hyelim, L. Joon-Seok, C. W. Seok and K. Shin-Hyun, Adv. Mater., 2015, 27, 1282–1287 CrossRef PubMed.
- N. Vogel, R. A. Belisle, B. Hatton, T.-S. Wong and J. Aizenberg, Nat. Commun., 2013, 4, 2176 CrossRef PubMed.
- J. Hou, H. Zhang, Q. Yang, M. Li, Y. Song and L. Jiang, Angew. Chem., Int. Ed., 2014, 53, 5791–5795 CrossRef CAS PubMed.
- J. Liu, Z. Xie, Y. Shang, J. Ren, R. Hu, B. Guan, J. Wang, T. Ikeda and L. Jiang, ACS Appl. Mater. Interfaces, 2018, 10, 6701–6710 CrossRef CAS PubMed.
- K. Zhong, J. Li, L. Liu, S. Van Cleuvenbergen, K. Song and K. Clays, Adv. Mater., 2018, 30, 1707246 CrossRef PubMed.
- K. Zhong, L. Liu, J. Lin, J. Li, S. Van Cleuvenbergen, W. Brullot, M. Bloemen, K. Song and K. Clays, Adv. Mater. Interfaces, 2016, 3, 1600579 CrossRef.
- X. Zhang, F. Wang, L. Wang, Y. Lin and J. Zhu, ACS Appl. Mater. Interfaces, 2016, 8, 22585–22592 CrossRef CAS PubMed.
- H. Kang, J.-S. Lee, W. S. Chang and S.-H. Kim, Adv. Mater., 2015, 27, 1282–1287 CrossRef CAS PubMed.
- C. Liu, H. Ding, Z. Wu, B. Gao, F. Fu, L. Shang, Z. Gu and Y. Zhao, Adv. Funct. Mater., 2016, 26, 7937–7942 CrossRef CAS.
- Z. Yang, J. K. Park and S. Kim, Small, 2018, 14, 1702839 CrossRef PubMed.
- Y. Meng, B. Tang, J. Cui, S. Wu, B. Ju and S. Zhang, Adv. Mater. Interfaces, 2016, 3, 1600374 CrossRef.
- X. F. Gao, X. Yan, X. Yao, L. Xu, K. Zhang, J. H. Zhang, B. Yang and L. Jiang, Adv. Mater., 2007, 19, 2213–2217 CrossRef CAS.
- Z. W. Hang, Z. Z. Mu, B. Li, Z. Wang, J. Q. Zhang, S. C. Niu and L. Q. Ren, ACS Nano, 2016, 10, 8591–8602 CrossRef PubMed.
- J. Li, J. Zhu and X. F. Gao, Small, 2014, 10, 2578–2582 CrossRef CAS PubMed.
- C. C. Liu, J. Ju, Y. M. Zheng and L. Jiang, ACS Nano, 2014, 8, 1321–1329 CrossRef CAS PubMed.
- W. L. Min, B. Jiang and P. Jiang, Adv. Mater., 2008, 20, 3914–3918 CrossRef CAS.
- Z. Q. Sun, T. Liao, K. S. Liu, L. Jiang, J. H. Kim and S. X. Dou, Small, 2014, 10, 3001–3006 CrossRef CAS PubMed.
- K. Fukada and S. Shiratori, Ind. Eng. Chem. Res., 2015, 54, 979–986 CrossRef CAS.
- H. K. Raut, A. S. Nair, S. S. Dinachali, V. A. Ganesh, T. M. Walsh and S. Ramakrishna, Sol. Energy Mater. Sol. Cells, 2013, 111, 9–15 CrossRef CAS.
- D. Liu, Q. Wang, W. Shen and D. Wang, J. Mater. Chem. C, 2017, 5, 103–109 RSC.
- I. Navarro-Baena, A. Jacobo-Martín, J. J. Hernández, J. R. Castro Smirnov, F. Viela, M. A. Monclús, M. R. Osorio, J. M. Molina-Aldareguia and I. Rodríguez, Nanoscale, 2018, 10, 15496–15504 RSC.
- H. Xie, H.-X. Huang and Y.-J. Peng, Nanoscale, 2017, 9, 11951–11958 RSC.
- R. G. Karunakaran, C.-H. Lu, Z. Zhang and S. Yang, Langmuir, 2011, 27, 4594–4602 CrossRef CAS PubMed.
- J. Yong, F. Chen, Q. Yang, G. Du, C. Shan, H. Bian, U. Farooq and X. Hou, J. Mater. Chem. A, 2015, 3, 9379–9384 RSC.
- J. Zhang, B. Yu, Z. Gao, B. Li and X. Zhao, Langmuir, 2017, 33, 510–518 CrossRef CAS PubMed.
- H. Chen, P. Zhang, L. Zhang, H. Liu, Y. Jiang, D. Zhang, Z. Han and L. Jiang, Nature, 2016, 532, 85 CrossRef CAS PubMed.
- Y. Chen and Y. Zheng, Nanoscale, 2014, 6, 7703–7714 RSC.
- J. Ju, H. Bai, Y. Zheng, T. Zhao, R. Fang and L. Jiang, Nat. Commun., 2012, 3, 1247 CrossRef PubMed.
- J. Ju, Y. Zheng and L. Jiang, Acc. Chem. Res., 2014, 47, 2342–2352 CrossRef CAS PubMed.
- Y. Zheng, H. Bai, Z. Huang, X. Tian, F.-Q. Nie, Y. Zhao, J. Zhai and L. Jiang, Nature, 2010, 463, 640 CrossRef CAS PubMed.
- J. Zhang, X. Pan, Q. Xue, D. He, L. Zhu and Q. Guo, J. Membr. Sci., 2017, 532, 38–46 CrossRef CAS.
- H. Zhu, R. Duan, X. Wang, J. Yang, J. Wang, Y. Huang and F. Xia, Nanoscale, 2018, 10, 13045–13054 RSC.
- L. Shang, Y. Yu, W. Gao, Y. Wang, L. Qu, Z. Zhao, R. Chai and Y. Zhao, Adv. Funct. Mater., 2018, 28, 1705802 CrossRef.
- C. Zhou, H. Li, J. Lin, K. Hou, Z. Yang, P. Pi, S. Xu, X. Wen and J. Cheng, J. Phys. Chem. C, 2017, 121, 19716–19726 CrossRef CAS.
- Y. Hirai, H. Mayama, Y. Matsuo and M. Shimomura, ACS Appl. Mater. Interfaces, 2017, 9, 15814–15821 CrossRef CAS PubMed.
- P. Xue, J. Nan, T. Wang, S. Wang, S. Ye, J. Zhang, Z. Cui and B. Yang, Small, 2017, 13, 1601807 CrossRef PubMed.
- K. Ellinas, A. Tserepi and E. Gogolides, Langmuir, 2011, 27, 3960–3969 CrossRef CAS PubMed.
- T. Jiang, Z. G. Guo and W. M. Liu, J. Mater. Chem. A, 2015, 3, 1811–1827 RSC.
- D. Wu, S. Z. Wu, Q. D. Chen, S. Zhao, H. Zhang, J. Jiao, J. A. Piersol, J. N. Wang, H. B. Sun and L. Jiang, Lab Chip, 2011, 11, 3873–3879 RSC.
- D. P. Zhan, L. H. Han, J. Zhang, Q. F. He, Z. W. Tian and Z. Q. Tian, Chem. Soc. Rev., 2017, 46, 1526–1544 RSC.
- R. Fürstner, W. Barthlott, C. Neinhuis and P. Walzel, Langmuir, 2005, 21, 956–961 CrossRef PubMed.
- Y. C. Jung and B. Bhushan, ACS Nano, 2009, 3, 4155–4163 CrossRef CAS PubMed.
- Y. Kwon, N. Patankar, J. Choi and J. Lee, Langmuir, 2009, 25, 6129–6136 CrossRef CAS PubMed.
- C. J. Long, J. F. Schumacher and A. B. Brennan, Langmuir, 2009, 25, 12982–12989 CrossRef CAS PubMed.
- M. Reyssat and D. Quéré, J. Phys. Chem. B, 2009, 113, 3906–3909 CrossRef CAS PubMed.
- L. Seung-Mo and K. Tai Hun, Nanotechnology, 2006, 17, 3189 CrossRef.
- A. Steinberger, C. Cottin-Bizonne, P. Kleimann and E. Charlaix, Nat. Mater., 2007, 6, 665 CrossRef CAS PubMed.
- T.-i. Kim, C. H. Baek, K. Y. Suh, S.-M. Seo and H. H. Lee, Small, 2008, 4, 182–185 CrossRef CAS PubMed.
- J. Z. Wang, Z. H. Zheng, H. W. Li, W. T. S. Huck and H. Sirringhaus, Nat. Mater., 2004, 3, 171 CrossRef CAS PubMed.
- T.-S. Wong, A. P.-H. Huang and C.-M. Ho, Langmuir, 2009, 25, 6599–6603 CrossRef CAS PubMed.
- X. Zhang, J. Zhang, Z. Ren, X. Li, X. Zhang, D. Zhu, T. Wang, T. Tian and B. Yang, Langmuir, 2009, 25, 7375–7382 CrossRef CAS PubMed.
- W. Wang, J. Salazar, H. Vahabi, A. Joshi-Imre, W. E. Voit and A. K. Kota, Adv. Mater., 2017, 29, 1700295 CrossRef PubMed.
- F. Dundar Arisoy, K. W. Kolewe, B. Homyak, I. S. Kurtz, J. D. Schiffman and J. J. Watkins, ACS Appl. Mater. Interfaces, 2018, 10, 20055–20063 CrossRef CAS PubMed.
- D. Bazin and C. Faure, Soft Matter, 2017, 13, 5500–5505 RSC.
- J. Dong, Q. Wang, Y. Zhang, Z. Zhu, X. Xu, J. Zhang and A. Wang, ACS Appl. Mater. Interfaces, 2017, 9, 1941–1952 CrossRef CAS PubMed.
- P. Esmaeilzadeh, M. T. Sadeghi, A. Bahramian, Z. Fakhroueian and A. Zarbakhsh, ACS Appl. Mater. Interfaces, 2016, 8, 32011–32020 CrossRef CAS PubMed.
- J. Lin, C. Zheng, W. Ye, H. Wang, D. Feng, Q. Li and B. Huan, J. Appl. Polym. Sci., 2015, 132, 41458 CrossRef.
- J. Yang, Z. Zhang, X. Men, X. Xu and X. Zhu, New J. Chem., 2011, 35, 576–580 RSC.
- T. Ren and J. He, ACS Appl. Mater. Interfaces, 2017, 9, 34367–34376 CrossRef CAS PubMed.
- C. Zhou, Z. Chen, H. Yang, K. Hou, X. Zeng, Y. Zheng and J. Cheng, ACS Appl. Mater. Interfaces, 2017, 9, 9184–9194 CrossRef CAS PubMed.
- S. Gao, X. Dong, J. Huang, S. Li, Y. Li, Z. Chen and Y. Lai, Chem. Eng. J., 2018, 333, 621–629 CrossRef CAS.
- J. J. Richardson, J. Cui, M. Björnmalm, J. A. Braunger, H. Ejima and F. Caruso, Chem. Rev., 2016, 116, 14828–14867 CrossRef CAS PubMed.
- S. Srivastava and N. A. Kotov, Acc. Chem. Res., 2008, 41, 1831–1841 CrossRef CAS PubMed.
- K. Ariga, Y. Yamauchi, G. Rydzek, Q. Ji, Y. Yonamine, K. C.-W. Wu and J. P. Hill, Chem. Lett., 2014, 43, 36–68 CrossRef CAS.
- Y. Ko, H. Baek, Y. Kim, M. Yoon and J. Cho, ACS Nano, 2013, 7, 143–153 CrossRef CAS PubMed.
- K. Manabe, T. Matsubayashi, M. Tenjimbayashi, T. Moriya, Y. Tsuge, K.-H. Kyung and S. Shiratori, ACS Nano, 2016, 10, 9387–9396 CrossRef CAS PubMed.
- K. Manabe, S. Nishizawa, K.-H. Kyung and S. Shiratori, ACS Appl. Mater. Interfaces, 2014, 6, 13985–13993 CrossRef CAS PubMed.
- S. S. Qureshi, Z. Zheng, M. I. Sarwar, O. Félix and G. Decher, ACS Nano, 2013, 7, 9336–9344 CrossRef CAS PubMed.
- J. J. Richardson, M. Björnmalm and F. Caruso, Science, 2015, 348, aaa2491 CrossRef PubMed.
- K. Manabe, M. Matsuda, C. Nakamura, K. Takahashi, K.-H. Kyung and S. Shiratori, Chem. Mater., 2017, 29, 4745–4753 CrossRef CAS.
- F. Xu, X. Li, Y. Li and J. Sun, ACS Appl. Mater. Interfaces, 2017, 9, 27955–27963 CrossRef CAS PubMed.
- Y. Tsuge, T. Moriya, Y. Moriyama, Y. Tokura and S. Shiratori, ACS Appl. Mater. Interfaces, 2017, 9, 15122–15129 CrossRef CAS PubMed.
- S. Laurent, D. Forge, M. Port, A. Roch, C. Robic, L. V. Elst and R. N. Muller, Chem. Rev., 2008, 108, 2064–2110 CrossRef CAS PubMed.
- C. Wei, G. Zhang, Q. Zhang, X. Zhan and F. Chen, ACS Appl. Mater. Interfaces, 2016, 8, 34810–34819 CrossRef CAS PubMed.
- X. Su, H. Li, X. Lai, L. Zhang, J. Wang, X. Liao and X. Zeng, ACS Appl. Mater. Interfaces, 2017, 9, 28089–28099 CrossRef CAS PubMed.
- B. Zhang, X. Hu, Q. Zhu, X. Wang, X. Zhao, C. Sun, Y. Li and B. Hou, Chem. Eng. J., 2017, 312, 317–327 CrossRef CAS.
- Y. P. Hou, S. L. Feng, L. M. Dai and Y. M. Zheng, Chem. Mater., 2016, 28, 3625–3629 CrossRef CAS.
- M. Liu, Y. Hou, J. Li and Z. Guo, Langmuir, 2017, 33, 3702–3710 CrossRef CAS PubMed.
- M. Liu, J. Li and Z. Guo, Chem. Eng. J., 2016, 304, 115–120 CrossRef CAS.
- F. Chen, Y. Lu, X. Liu, J. Song, G. He, M. K. Tiwari, C. J. Carmalt and I. P. Parkin, Adv. Funct. Mater., 2017, 27, 1702926 CrossRef.
- T. Zhou, J. Yang, D. Zhu, J. Zheng, S. Handschuh-Wang, X. Zhou, J. Zhang, Y. Liu, Z. Liu, C. He and X. Zhou, Adv. Sci., 2017, 4, 1700028 CrossRef PubMed.
- J. C. Liu, L. Wan, M. B. Zhang, K. J. Jiang, K. Song, J. X. Wang, T. Ikeda and L. Jiang, Adv. Funct. Mater., 2017, 27, 1605221 CrossRef.
- J. Liu, J. Liu, P. Wu, M. Zhang, J. Wang and L. Jiang, J. Photochem. Photobiol., A, 2018, 355, 125–130 CrossRef CAS.
- K. Liu and L. Jiang, Nano Today, 2011, 6, 155–175 CrossRef CAS.
- L. Qin, N. Chen, X. Zhou and Q. Pan, J. Mater. Chem. A, 2018, 6, 4424–4431 RSC.
- M. Wu, Y. Li, N. An and J. Sun, Adv. Funct. Mater., 2016, 26, 6777–6784 CrossRef CAS.
- H.-Y. Mi, X. Jing, H.-X. Huang and L.-S. Turng, ACS Appl. Mater. Interfaces, 2017, 9, 37529–37535 CrossRef CAS PubMed.
- B. K. Kaang, N. Han, W. Jang, H. Y. Koo, Y. B. Lee and W. S. Choi, Chem. Eng. J., 2018, 331, 290–299 CrossRef CAS.
- Y. Feng, Y. Wang, Y. Wang and J. Yao, J. Mater. Chem. A, 2017, 5, 21893–21897 RSC.
- P. Wang, B. Sun, Y. Liang, H. Han, X. Fan, W. Wang and Z. Yang, J. Mater. Chem. A, 2018, 6, 10404–10410 RSC.
- Q.-Y. Cheng, X.-P. An, Y.-D. Li, C.-L. Huang and J.-B. Zeng, ACS Sustainable Chem. Eng., 2017, 5, 11440–11450 CrossRef CAS.
- J. Zhao, Y. Yang, C. Yang, Y. Tian, Y. Han, J. Liu, X. Yin and W. Que, J. Mater. Chem. A, 2018, 6, 16196–16204 RSC.
- X. Su, H. Li, X. Lai, L. Zhang, X. Liao, J. Wang, Z. Chen, J. He and X. Zeng, ACS Appl. Mater. Interfaces, 2018, 10, 4213–4221 CrossRef CAS PubMed.
- R. Iqbal, B. Majphy and A. K. Sen, ACS Appl. Mater. Interfaces, 2017, 9, 31170–31180 CrossRef CAS PubMed.
- L. Tie, J. Li, M. Liu, Z. Guo, Y. Liang and W. Liu, ACS Appl. Nano Mater., 2018 DOI:10.1021/acsanm.8b01074.
- S. Gao, Y. Zhu, J. Wang, F. Zhang, J. Li and J. Jin, Adv. Funct. Mater., 2018, 1801944 CrossRef.
- X. Su, H. Li, X. Lai, Z. Yang, Z. Chen, W. Wu and X. Zeng, J. Mater. Chem. A, 2018, 6, 16910–16919 RSC.
- M. Long, S. Peng, W. Deng, X. Miao, N. Wen, Q. Zhou, X. Yang and W. Deng, J. Mater. Chem. A, 2017, 5, 22761–22771 RSC.
- G. Ding, W. Jiao, L. Chen, M. Yan, L. Hao and R. Wang, J. Mater. Chem. A, 2018, 6, 19992–17000 Search PubMed.
- F.-F. Chen, Y.-J. Zhu, Z.-C. Xiong, L.-Y. Dong, F. Chen, B.-Q. Lu and R.-L. Yang, ACS Appl. Mater. Interfaces, 2017, 9, 39534–39548 CrossRef CAS PubMed.
- R. Togasawa, M. Tenjimbayashi, T. Matsubayashi, T. Moriya, K. Manabe and S. Shiratori, ACS Appl. Mater. Interfaces, 2018, 10, 4198–4205 CrossRef CAS PubMed.
- M. Wen, J. Zhong, S. Zhao, T. Bu, L. Guo, Z. Ku, Y. Peng, F. Huang, Y.-B. Cheng and Q. Zhang, J. Mater. Chem. A, 2017, 5, 8352–8359 RSC.
- W. Zhang, N. Liu, Q. Zhang, R. Qu, Y. Liu, X. Li, Y. Wei, L. Feng and L. Jiang, Angew. Chem., Int. Ed., 2018, 130, 5842–5847 CrossRef.
- H. Zhou, H. Wang, H. Niu, J. Fang, Y. Zhao and T. Lin, Adv. Mater. Interfaces, 2015, 2, 1400559 CrossRef.
- X. Sheng, Z. Liu, R. Zeng, L. Chen, X. Feng and L. Jiang, J. Am. Chem. Soc., 2017, 139, 12402–12405 CrossRef CAS PubMed.
- Q. Zhang, J. Kang, Z. Xie, X. Diao, Z. Liu and J. Zhai, Adv. Mater., 2018, 30, 1703323 CrossRef PubMed.
- J. Liu, L. Wang, N. Wang, F. Guo, L. Hou, Y. Chen, J. Liu, Y. Zhao and L. Jiang, Small, 2017, 13, 1600499 CrossRef PubMed.
- H. Li, Q. Yang, J. Hou, Y. Li, M. Li and Y. Song, Adv. Funct. Mater., 2018, 28, 1800448 CrossRef.
- K. Zhong, L. Wang, J. Li, S. Van Cleuvenbergen, C. Bartic, K. Song and K. Clays, Langmuir, 2017, 33, 4840–4846 CrossRef CAS PubMed.
- S. Amini, S. Kolle, L. Petrone, O. Ahanotu, S. Sunny, C. N. Sutanto, S. Hoon, L. Cohen, J. C. Weaver, J. Aizenberg, N. Vogel and A. Miserez, Science, 2017, 357, 668–673 CrossRef CAS PubMed.
- S. Wu, J. Yi, K. Zhu, S. Bai, Y. Liu, Y. Qiao, M. Ishida and H. Zhou, Adv. Energy Mater., 2017, 7, 1601759 CrossRef.
- H. Zhao, Q. Sun, X. Deng and J. Cui, Adv. Mater., 2018, 30, 1802141 CrossRef PubMed.
- L.-P. Xu, J. Peng, Y. Liu, Y. Wen, X. Zhang, L. Jiang and S. Wang, ACS Nano, 2013, 7, 5077–5083 CrossRef CAS PubMed.
|
This journal is © The Royal Society of Chemistry 2019 |
Click here to see how this site uses Cookies. View our privacy policy here.