Simultaneous production of biomethane and food grade CO2 from biogas: an industrial case study†
Received
2nd October 2018
, Accepted 15th November 2018
First published on 21st November 2018
Abstract
This work presents a case study on the first large-scale industrial biogas upgrading process with simultaneous purification of methane and CO2 in one of Europe's largest biogas production and purification plants in Northern Italy. A preliminary study was performed on a pilot plant, constructed as a model of the industrial plant where the final experiments were performed. The full-scale anaerobic digestion plant has a digestive capacity of 400
000 tonnes of biomass per year and it can treat 6250 m3 h−1 of biogas. The first objective was a biogas upgrading process that achieves distribution grid-quality methane via different purification steps. The second objective and most innovative aspect is the further purification of CO2 from a useless waste product to a high purity gas for the food and beverage industry. The chemical purity of different process streams was analysed by a certified laboratory and was compared with the guidelines of the European Industrial Gas Association and International Society of Beverage Technologists (EIGA/ISBT) for CO2 used in the food industry. The microbiological purity was found to be far below the limit values defined in the European Collaborative Action. With a purity of 96.3 vol%, methane respects the purity requirement for the household network. With a purity of 98.1 vol% before, and 99.9 vol% after the final distillation process, CO2 proves to be chemically and microbiologically suitable for food applications, thus closing the CO2 loop in biogas production. An evaluation of the economic and energetic aspects and a comparison with alternative purification processes highlights the profitability of the process.
Broader context
Biogas is a mixture of methane, carbon dioxide, and several minor compounds, produced by spontaneous digestion of biomass in nature, in landfill sites or in dedicated waste treatment plants. The biomethane, as a source of renewable energy, may provide an important contribution to our fight against climate change. In the context of climate change, the reduction of anthropogenic greenhouse gas emissions into the atmosphere is one of the most difficult challenges of our industrialized modern society. This necessitates the replacement of traditional fossil fuels by CO2-neutral renewable energy sources, as well as the capture and the storage or reuse of CO2. The present paper describes a process that uses both approaches at the same time: the production of biomethane from organic household waste, and the simultaneous sequestration and purification of CO2 for use in food and beverage applications. The same concept can easily be extended to other sources of organic waste, from farming, from agriculture or from the food industry itself, or it may be applied to the biogas released from existing landfill sites. This waste-to-valuable concept will give an important contribution to a more sustainable society with lower impact of human activities on the environment.
|
1. Introduction
1.1. CO2 emissions and remedies
Global warming and climate change caused by the emission of greenhouse gases are among the most challenging environmental problems to solve in our days. Carbon dioxide is a major greenhouse gas and its production is mostly related to the use of fossil fuels for energy production.1 The first agreement on the climate changes was the Kyoto Protocol signed in 1997 and related to the United Nations Framework Convention on Climate Change (UNFCCC). Based on the “common but differentiated responsibilities” principle, it required the reduction of the emissions by 5% in the industrialized countries, in order to introduce a maximum of only 5.85 Gt per year of CO2 into the atmosphere, instead of 6 Gt per year.2 For this reason, many countries have adopted alternative and environmentally friendly energy policies.3–5 A new agreement to combat the climate change was proposed in Paris on December 2015,6 and a total of 181 out of 197 Parties have ratified it until September 2018.7 The action plan is to reduce greenhouse gas emissions by at least 50% to limit the rise of the global average temperature to 2 °C by 2050.8 These objectives can only be reached by the increased use of renewable sources of energy, with the promotion of plans for CO2 capture and storage (CCS) or utilization (CCU). In the last few years, the attention on CCS and CCU to mitigate the greenhouse effect has strongly increased. It was estimated that these techniques have the potential to reduce the future CO2 emissions by 20%.9 The substantial difference between CCS and CCU is the final destination of the captured CO2. In CCS, the captured CO2 is transferred to a suitable site for long-term storage,10 while in CCU the captured CO2 is converted into valuable products.11–13 The two factors that determine the environmental impact and the CO2 mitigation potential are the capacity, i.e. the amount of CO2 that can be stored or used, and the life time of storage, i.e. the total time before it returns into the atmosphere as ‘free’ CO2. Generally, CCS techniques have a higher CO2 mitigation potential than CCU because of a higher storage capacity and higher life-time of storage with respect to the CCU. However, CCS has associated costs related to the storage process itself that must be taken into account, e.g. geological storage about 2–29 $ per ton and ocean storage about 22–114 $ per ton,14 while the direct utilization of CO2 has additional costs related to the further purification to the required level. Furthermore, the practice of CO2 storage presents a large number of risks, such as leakages, seismicity, ground movement and displacement of brine.15 These risks are in common with the geological CO2 extraction, that paradoxically has increased due to the industrial use of CO2. Therefore, CCS techniques cannot be the only solution, and it becomes increasingly important to identify methods that allow CO2 reutilization. This becomes increasingly important in this moment, where there is an enormous lack of commercial CO2 in Europe because, for instance, some licences to extract CO2 from underground reserves in Tuscany (Italy) are not being renewed. The reuse of anthropogenic CO2 would reduce the necessity to extract CO2 from natural deposits and promotes at the same time a circular bio-economy of CO2.16 The shift from waste to a commercial product means that the produced CO2 will become a profit and not a cost factor in the business budget. The types of CO2 use are essentially two: the first, its conversion into different products, and the second, its direct utilization as such.17 CO2 can be fixed and converted into more complex organic molecules like polyurethane and polystyrene,18–20 into urea and ammonia, which can be used as a fertilizer.21,22 It can be used as feedstock to produce fuels,23,24 and already decades ago it was recognized as a potential monomer for the synthesis of sustainable polymers,25 for commodity plastics or niche applications26 and in recent years it is still investigated as a building block for green polycarbonate.27 Other opportunities for chemical recycling of carbon dioxide are the dry reforming of methane with CO2, and the reverse water gas shift reaction to produce CO, or the production of new fuels.28–30 Since chemical conversion requires high amounts of energy that give the process its own carbon footprint, the direct CO2 utilization without any conversion is an even more attractive alternative. Examples of direct CO2 utilization in the chemical industry are enhanced oil recovery (EOR) and enhanced coal-bed methane (ECBM) recovery.31 In the pharmaceutical and medical fields, CO2 is used in a mixture with oxygen/air to promote deep breathing or for surgical dilation by means of intra-abdominal insufflations.32 Among the different CCU techniques, the use of CO2 in the food market represents a relatively small but significant storage capacity and a moderate life time of storage (Table 1). Its main use is in packaging, as preservative agent that increases the food shelf-life,33 or for the carbonation of soft drinks, mineral water, and beer.
Table 1 Selection of the main CCU applications10,14,17,34
CO2 application field |
CO2 feedstock |
Product |
Market [Mt per year] |
CO2 used [Mt] |
Life timea |
Ref. |
Time from product use until return/reconversion to ‘free’ CO2.
|
Food |
8 |
8 |
Months to years |
17
|
Organic carbonates |
2.6 |
0.2 |
Decades/centuries |
17
|
Inorganic carbonates |
8 |
3 |
Decades/centuries |
10
|
Polyurethanes |
10 |
<10 |
Decades/centuries |
14
|
Technological |
10 |
10 |
Days/years |
17
|
Methanol |
24 |
<8 |
6 months |
14 and 34
|
Urea |
90 |
65 |
6 months |
10 and 14
|
1.2. State of the art on the CO2 supply, renewable energy and a novel method of CO2 recovery
Nowadays, the industrial CO2 supply chain is mostly based on fossil fuel combustion (carbon, natural gas, fuel oil, etc.);35 on gasification of solid fuels (carbon, oil shale, etc.);36 on extraction of CO2 from geological reservoirs; and on CO2 separation from petrochemical and chemical processes (such as syngas). All these techniques have a negative environmental impact, enhancing the CO2 level in the atmosphere. The total CO2 release is only in part balanced by the natural absorption in the form of marine and mineral carbonate sediments.37,38 Any natural CO2 absorption process is a long-term phenomenon and therefore the geological CO2 extraction alters the natural equilibrium of the release/adsorption cycle. Approaches to limit the release of CO2 into the atmosphere should therefore be aimed at reducing the extraction from underground reserves and at an increased reuse of the already available gas, while a second approach should focus on the mitigation of CO2 production. Since fossil fuel consumption is the main cause of global warming by CO2 emission, the search for renewable and eco-sustainable energy is currently one of the main driving forces in many fields of scientific research. The energy supply in the world depends for approximately 90% on traditional energy sources.39 Besides the environmental aspect, this also forms a threat for the industrial productivity and economic growth, when these fossil fuels will be exhausted. In contrast, renewable energy technologies guarantee energy security through their non-exhaustive nature and unlimited availability and accessibility. Moreover, most renewable energies do not produce additional CO2, or the amount produced can easily be offset by CO2 absorption for natural plant growth.39 In this context, biogas obtained by anaerobic digestion of biomass is an important source of eco-sustainable energy. This process has the advantage over composting or storage in landfills, that it avoids uncontrolled release of methane and CO2 into the atmosphere. This is especially relevant for methane, being a 25 times more powerful greenhouse gas than CO2.40 The additional advantage over combustion of organic waste in waste-to-energy power plants, is that it enables the subsequent recovery of biogas as a valuable energy source. Raw biogas is a water vapour saturated mixture of 50–65 vol% methane, 30–40 vol% CO2, traces of hydrogen sulphide, oxygen, nitrogen, ammonia, siloxanes and volatile organic compounds.41 Since the energy density of biogas is proportional to its methane concentration, removal of the CO2 and other impurities is required both for an optimum performance and for minimum emission of toxic or greenhouse gases. Various studies propose the use of CO2/CH4 selective polymeric membranes42–47 or other materials48,49 for the biogas upgrading process and indicate the purified biomethane as a renewable energy source to be used for heating, electricity production or co-generation.41,50–52
This paper presents a case study on the feasibility of biogas upgrading at full industrial scale to distribution grid quality methane, and simultaneous recovery of CO2, starting from organic waste (Fig. 1).
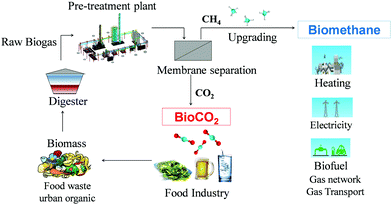 |
| Fig. 1 Schematic representation of the sustainable cycle of anaerobic digestion with simultaneous production of biomethane and food grade BioCO2. | |
The most innovative aspect of this case study is the final purification of CO2 to food-grade quality. We will successfully demonstrate that it is indeed possible to achieve simultaneous production of high purity bio-CO2 for the food and beverage industry, and biomethane for the distribution grid. This is an important demonstration of how it is possible to completely close the CO2 loop,22 with both economic and ecological advantage.
2. Industrial plant
2.1. Digestion plant and biomass feed
The digestion plant is located on the industrial site of Montello SPA. (Montello, IT) and it handles up to 400
000 ton per year of biomass with a treatment capacity of 6250 m3 h−1 of biogas. The biomass used is the organic fraction of solid urban waste (FORSU) of the Lombardy region in the North of Italy. The digestion plant includes a first step of biomass pre-treatment, followed by thermophilic anaerobic digestion. The elevated temperatures of the latter (55 °C) have the advantage of thermal destruction of most pathogenic bacteria.
2.2. Plant for biogas purification
The biogas purification plant was built by Tecno Project Industriale Srl (Curno-BG, IT). The biogas stream from the digester is first collected in the gasometer, after which a series of heat exchangers cools the feed stream from about 50 °C to 10 °C. In this stage, most of the water vapour condenses and heavy organic compounds are separated from the lighter gases. The partially dehydrated raw biogas is then fed into five parallel lines where the purification takes place, each with a capacity of 1250 m3 h−1 of biogas. Every line has six purification steps (Fig. 2) water scrubbing, desulphurization, VOC removal system, compression, coal purification, and membrane separation unit.
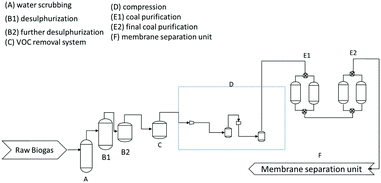 |
| Fig. 2 Scheme of one of the five parallel raw biogas purification lines. | |
The scrubbing with cold water at the discharge pressure of the blowers further removes undesirable less volatile and water soluble compounds. The desulphurization step then removes H2S and other sulphides by chemical-physical precipitation in the solid phase, where they react with ferrous or ferric oxide (FeO3/FeO2) to be oxidized and fixed in non-toxic compounds. The coal purification step on active carbon filters removes most organic impurities, like halogenated hydrocarbons, volatile organic compounds, terpenes and siloxanes, via adsorption and molecular sieving mechanisms. After this step, the gas stream is fed at 13–16 bar to the three-step membrane separation process (Fig. 3).
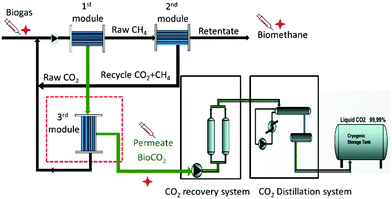 |
| Fig. 3 Schematic illustration of the CO2/CH4 separation process based on the three-stage membrane separation and CO2 recovery unit.53–55 The syringe and the red symbol indicate the gas sampling points. | |
2.3. Section of the CH4/CO2 membrane separation
The main CO2/CH4 separation occurs in the membrane section. The separation takes place in a set of three different modules that provide the consecutive passage of each gas stream through two membrane modules, each with a recycle of the waste stream from the second stage (Fig. 3).
The membranes are polyimide hollow fibre modules, approximately 1.3 m long, containing several tens of thousands of hollow fibres, each of diameter 0.5 mm. The commercial SEPURAN® modules (Evonik)56 can operate up to a temperature of 50 °C and a pressure of 17 bar. These membranes are characterized by excellent performance in terms of CO2/CH4 separation, having a good selectivity and high CO2 permeability. The first membrane module produces a methane-enriched retentate and a CO2 rich permeate. The methane rich retentate is sent to the second membrane module and further CO2 removal yields purified biomethane in the retentate of the 2nd module. The permeate of this module contains a mixture of CO2 and methane, and is recycled into the raw biogas feed stream of the first module for maximum methane and CO2 recovery. The CO2 rich permeate coming from the first stage flows into a 3rd membrane module. This module produces a permeate of nearly pure CO2, while the retentate is recycled into the raw feed of the 1st module in order to minimize CO2 and methane losses. The dense membrane barrier does not allow the passage of microorganisms and guarantees that the CO2 stream is completely bacteria and fungi-free.
2.4. CO2 recovery plant
The residual impurities in the combined CO2 streams, coming from the five membrane separation lines, are removed in the CO2 recovery unit with a pure CO2 capacity of 750 kg h−1 (Fig. 3). The CO2 recovery section includes a liquefying step and cryogenic units with a series of elements for the compression, drying and purification of the gas stream. Upon cooling to −30 °C, the CO2 separates from the non-condensable gases (N2, O2, and CH4), yielding high purity CO2 (99.9+%). The non-condensable gases must be purged to avoid their accumulation, but a fraction of this stream can be fed back to the membrane section to minimise gas losses.
3. Analysis and methods
The chemical and biological analyses of gas streams were carried out by LabAnalysis Srl. (Montello-BG, IT) according to the typical techniques used to control air pollution and gas purity for food marketing. These techniques are based on the gas filtration trough specific and suitable filters to solid or liquid agar in order to determine the eventual presence of chemical and microbiological impurities.
3.1. Chemical analysis
The gas samples are collected at three different points, highlighted with a syringe in Fig. 3: off-ramp for Biogas (raw Biogas), retentate of the 2nd membrane module (biomethane), permeate of the 3rd membrane module (BioCO2). For the analysis of particulate matter, a constant volume of biogas was filtrated with suitable analytic filters, having pores with size smaller than that of the particles expected. The amounts of the impurities were determined from the weight change of the filter before and after the analysis. The methods used to analyse the amount of volatile impurities change as function of the type of impurities and are given in Table 2.
Table 2 The techniques and methods used to analyse the chemical impurities
Compound |
Analysis method |
Compound |
Analysis method |
Environmental Protection Agency.
International Society of Beverage Technologists.
|
Aromatic hydrocarbons |
EPAa TO-1757 |
Mercaptans |
GC-FPD |
Gas and vapours |
GC-FID |
Metals |
ICP AES |
Halogenated hydrocarbons |
EPAa TO-1757 |
Ammonia |
Niosh 6015 199458 |
Phosphate |
ISBTb procedure 9.0 |
Hydrogen cyanide |
Spectrophotometer |
Acetaldehyde |
HPLC |
Amines |
HS-GC-MS |
Nitrogen oxide |
Chemiluminescence |
|
|
An organoleptic analysis was carried according to the ISBT 15.0/ISO 4120:2004 test to determine the smell, taste and appearance of the final BioCO2. The purity of CO2 was compared with the guidelines applied by the European Industrial Gases Association and by the International Society of Beverage Technologists (EIGA/ISBT) for CO2 used in the food industry.59
3.2. Biological analysis
The biological analyses were performed on the CO2 stream coming from the 3rd membrane separation step (Fig. 3). A given volume of gas was inoculated into the culture medium, allowing the eventual quantification and determination of the microorganism cell types. The bacterial and fungal count was evaluated on the basis of the colony forming units per volume of gas (CFU m−3).
The data are compared with the guidelines proposed by the European Collaborative Action (ECA) of the Commission of the European Communities.60Table 3 reports the guidance ranges of the ECA for the control of contamination of air in domestic and indoor environments, such as hospitals, schools and offices.
Table 3 Guidelines proposed by the European Collaborative Action (ECA) of the Commission of the European Communities for the control of contamination of air in indoor environments60,61
Microorganism |
Contamination level |
Domestic (CFU m−3) |
Indoora (CFU m−3) |
Indoor refers to community environments such as hospitals, schools, offices.
|
Bacterial |
Very low |
<100 |
<50 |
Low |
<500 |
<100 |
Intermediate |
<2500 |
<500 |
High |
<10 000 |
<2000 |
Very high |
>10 000 |
>2000 |
|
Fungal |
Very low |
<100 |
<50 |
Low |
<500 |
<100 |
Intermediate |
<2500 |
<500 |
High |
<10 000 |
<2000 |
Very high |
>10 000 |
>2000 |
4. Results and discussion
4.1. Raw biogas chemical analysis
The composition of the raw biogas from the anaerobic digestion was monitored for almost one year (Fig. 4). The raw biogas consisted of 29–41 vol% of CO2, with an average of 37 vol%, and 58–68 vol% of methane, with an average of 61 vol%. The average amount of residual compounds, including ca. 1 vol% of water and <0.5 vol% of O2, is slightly more than 2 vol%. The water content depends mostly on the efficiency of the condensation step, which in turn depends on the flow rates and on the gas composition, while the O2 content depends on the intake of the raw biomass and on the subsequent conversion during digestion.62 The concentrations of the impurities of the raw biogas, such as hydrocarbons, ketones, ethers, esters and alcohols during the one-year measurement campaign are given in Fig. 5. The concentrations of the majority of the impurities remain mostly constant as a function of time, allowing a stable and reliable management of the separation process. Interestingly, only the terpenes (limonene, β-pynene, 2-menthene, and α-terpynene) seem to have seasonal fluctuations, probably related to changes in the citrus fruit consumption.
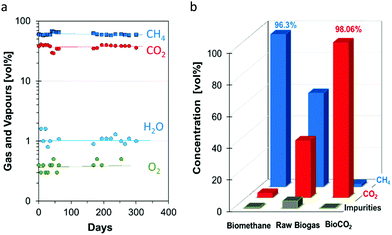 |
| Fig. 4 (a) Gas composition of raw biogas; (b) comparison of the concentration of CO2, CH4 and impurities for raw biogas, and the values for biomethane (retentate of the second module) and BioCO2 after the membrane separation (permeate of the third module). | |
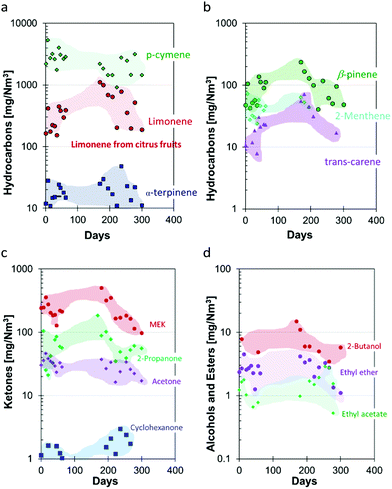 |
| Fig. 5 Concentration of the pollutants (a and b) hydrocarbons, (c) ketones, (d) alcohols, ethers and esters in the raw biogas stream as a function of time. Data clouds are shaded as a guide to the eye. | |
4.2. Biomethane and BioCO2 chemical analysis
Fig. 4b shows the compositions of the raw biogas, biomethane and BioCO2 in a representative test. The purification process concentrates the methane in the retentate of 2nd module, from 59 vol% in the raw biogas to 96.3 vol% in the biomethane. The CO2 concentration decreases from 36.1 vol% in the raw biogas to 2.9 vol% in the biomethane stream. The total concentration of impurities in the biomethane, such as powders, mineral oils, water, oxygen, hydrogen, nitrogen, carbon monoxide, mercaptans, carbon disulphide, carbonyl sulphide, ammonia, hydrochloric acid, hydrofluoric acid, limonene, acetone, isopropanol, methylethylketone (MEK) dramatically decreases. Thus, as the most important result of the methane upgrading, the heating value of methane is increased, allowing a more efficient electrical and thermal energy production.
With a purity of 96.3 vol%, a Wobbe Index of 50 MJ Sm−3 and a density of 0.56 kg m−3, the purified methane respects the requirements for the household network (Table 4).63 The “BioCO2” produced by the membrane separation units (Fig. 4b) contains 98.06 vol% CO2, 1.68 vol% CH4 and 0.26 vol% of other total impurities. The volumetric CO2 concentration thus increased from 36 vol% in the raw biogas to 98 vol% in the permeate of the 3rd module (purified BioCO2).
Table 4 Composition of biomethane from the membrane step compared to the threshold limit for biomethane quality63
Parameter |
Allowed threshold |
Measured after membrane unit |
Purity |
>80 vol% |
96.3 vol% |
Wobbe index (MJ Sm−3) |
47.31–52.33 |
50.02 |
Density (g cm−3) |
0.5548–0.8 |
0.56 |
Heating value (MJ Sm−3) |
34.95–45.28 |
37.48 |
Water dew point (°C) |
<−5 |
−27 |
Hydrocarbon dew point (°C) |
<0 |
−44 |
The concentration of the other impurities decreases from 1.2 vol% in the raw biogas to 0.26 vol% in the BioCO2. The majority of these impurities consists of water (120 ppm) and O2 (200 ppm) (Table 6 and Table S1, ESI†). The concentration of the aromatic hydrocarbons is in the order of ppb. In particular, benzene has a ten times lower concentration (0.002 ppm) with respect to the limit value of 0.02 ppm identified by the EIGA/ISBT for the use in food or beverages. All sulphide concentrations are below the limit. Amines are present in concentrations below 0.1 ppm and ammonia, with a concentration of less than 1 ppm, is far below the limit of 2.5 ppm. The hydrocarbons, such as limonene, are completely absent in the CO2 stream, since the membrane is apparently impermeable for these species. The p-cymene concentration decreases from 10 ppm in the raw biogas to 0.003 ppm in the final CO2 stream. Although the elimination of most pollutants by the membrane unit raises the CO2 purity to 98.06 vol%, this is still insufficient for a food grade quality, and thus a final purification step is needed in the CO2 recovery unit (Section 4.4).
4.3. Microbiological analysis of the CO2
The bacterial count is less than 20 CFU m−3 and the fungal concentration is less than 1 CFU m−3 (Table 5). This confirms that the microbiological content of the BioCO2 stream is below all levels specified by the guidelines of the European Collaborative Action for indoor environments like hospitals, schools and offices (Fig. 6).60
Table 5 Type and concentration (in CFU m−3) of bacterial and mycetic contamination
Total bacterial count |
<20 |
|
|
Fungus
|
<1 |
Escherichia coli
|
<1 |
Candida
|
<1 |
Clostridium perfringens
|
<1 |
Streptococcus
|
<1 |
Sulphite reducing clostridium |
<1 |
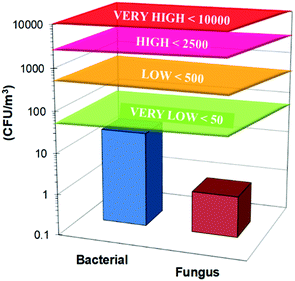 |
| Fig. 6 Total bacterial and mycetic count for the BioCO2 stream. The lines indicate the limit values for air pollution assessment in indoor environments defined by the European Collaborative Action.60 | |
The presence of pathogens such as Candida, Faecal streptococcus, Escherichia coli, Clostridium perfringens and Clostridia was excluded. Their concentrations are below 1 CFU m−3 and no growth was observed for each of these microorganisms. The absence of microorganisms is due to the dense nature of the gas separation membranes, which is impermeable for microorganisms with a size in the order of microns, whereas it is permeable for gases with a kinetic diameter in the order of a few Angstroms.
4.4. Production of food grade CO2
Although microbiologically clean, the methane, acetaldehyde, oxygen, and water levels in the CO2 from the 3rd membrane stage still exceed the threshold limit for food-grade quality (Table 6) and require further purification. This is done in the final liquefying section (Fig. 3). The liquefaction and the thermal treatment at −33 °C allow a first separation between condensable pollutants and CO2 on the one hand, and non-condensable gases on the other hand. In an additional distillation and condensation step, the CO2 reaches a chemical purity of 99.9 vol% with food grade quality, according to the EIGA/ISBT standard of the European Industrial Gas Association and the International Society of Beverage Technologists (Table 6).
Table 6 Composition of CO2 after the membrane step and after the final liquefying step CO2 compared to the threshold limit for food-grade quality (EIGA/ISBT standard)59
Parameter |
Limits EIGA/ISBT |
After membrane |
Liquefied CO2 |
Threshold |
Measured |
Measured |
Purity |
99.9 vol% |
98.06 vol% |
99.998 vol% |
Humidity |
20 ppm v/v max |
120 ppm v/v |
— |
Acidity |
Comply with test |
Comply with test |
Comply with test |
O2 |
30 ppm v/v max |
200 ppm v/v |
1.9 ppm v/v |
NH3 |
2.5 ppm v/v max |
2.5 ppm v/v |
2.5 ppm v/v |
NO |
2.5 ppm v/v max |
<0.14 ppm v/v |
<0.14 ppm v/v |
CO |
10 ppm v/v max |
<1 ppm |
<0.5 ppm v/v |
Phosphate |
Comply with test |
Comply with test |
Comply with test |
Acetaldehyde |
0.2 ppm v/v max |
0.3 ppm v/v |
<0.1 ppm v/v |
Aromatic hydrocarbons |
0.02 ppm v/v max |
<0.001 ppm |
<0.001 ppm v/v |
Non-VR |
10 ppm p/p max |
5 ppm |
5 ppm |
Non-VOC |
5 ppm p/p max |
1 ppm |
1 ppm |
|
Total sulphides |
0.1 ppm v/v max |
<0.1 ppm |
<0.06 ppm v/v |
–CS2 |
0.1 ppm v/v max |
<0.1 ppm |
<0.02 ppm v/v |
–H2S |
0.1 ppm v/v max |
<0.1 ppm |
<0.02 ppm v/v |
–COS |
0.1 ppm v/v max |
<0.1 ppm |
|
–SO2 |
1 ppm v/v max |
<0.1 ppm |
<0.1 ppm v/v |
|
Appearance in water |
No colour or turbidity |
No colour or turbidity |
No colour or turbidity |
Odour |
Odourless |
Odourless |
Odourless |
The organoleptic test demonstrated that the CO2 is odourless, tasteless and colourless. In the liquid phase, the CO2 does not present oil and particulate. The correct acidity and the absence of reducing substances are confirmed by the ISBT procedure.
5. Energetic and economic analysis
The total energy consumption calculated for the raw biogas purification with the membrane separation unit in our system is 0.27–0.29 kWh Nm−3. The precise energy costs depend on the purity and the efficiency of the recovery of the purified gases and is in line with the values reported in the literature64 but it is lower than that reported for other biogas upgrading technologies.65,66 For instance, the membrane separation process is much more convenient compared to pressure swing absorption that needs 0.46 kWh Nm−3, physical absorption with 0.49–0.67 kWh Nm−3 and it is close to chemical absorption of 0.3 kWh Nm−3 (Table 7). Compared to the latter, however, the membrane process has the enormous advantage that it uses less chemicals.
Table 7 Energy consumption of biogas upgrading technologies
Upgrading techniques |
Energy consumption (kWh Nm−3) |
Ref. |
Pressure swing absorption |
0.46 |
64 and 67
|
Physical absorption |
0.49–0.67 |
67
|
Chemical absorption |
0.3 |
68
|
Membrane technology |
0.21–0.3 |
64
|
The average household use of methane in Italy is estimated to be about 1250 Nm3 per year, with an average expenditure of ca. €1000.69,70 This means that the Montello/Tecno Project biogas upgrading plant, with its biogas treatment capacity of 6250 Nm3 h−1 and its total biomethane production capacity of 3000 Nm3 h−1 can satisfy the energy demand of 21
000 families, with a daily saving of natural gas of nearly €17
000. Paturska et al. report that for the best out of five scenarios, the cost of biomethane injected into the gas grid is 19% higher than the cost of natural gas.71 However, the unique aspect of our plant is that CO2 has an additional value, which partly compensates for the higher methane production cost. With an annual production of 7000 tonnes of food-grade CO2, with a base cost of 25 € per ton,72 the CO2 production brings an additional profit of ca. 500 € per day. Besides this economic aspect, the most important point is that this CO2 is not released directly into the atmosphere. Since the world-wide use of CO2 in the food industry is currently estimated as 8 × 106 ton per year,73 this single plant is capable of providing 0.1% of the food grade CO2 demand. Thus, if all organic waste would be treated in the same way, a thousand of similar separation plants worldwide would be sufficient to cover more than the entire CO2 demand of the food market. For the citizen, the costs for the separate organic waste collection and its transport must also be taken into account. Considering a representative cost of solid urban waste disposal of about €18–150 per ton,74 our plant's biomass handling capacity of 400
000 ton per year corresponds to a reduction of unsorted household waste, worth 7.2–60 M€ per year. Besides the organic fraction of household waste, there is an enormous potential in this field. It is estimated that in Italy alone, there are approximately 2500 smaller biogas production plants installed at farms, agricultural companies, waste disposal sites, et cetera, distributed over the entire territory. Now these plants produce mainly raw biogas for cogeneration, or in some cases the biogas is upgraded to pure biomethane for the natural gas grid or for other uses of pure methane, while still none of them is producing pure CO2. Since a large part of the cost of CO2 is related to its transport, delocalized CO2 production facilities would reduce this problem, and associated with biogas production from organic waste, they also solve an energetic and ecological problem.
6. Conclusions
The present case study demonstrates the feasibility to produce food-grade CO2 from raw biogas by an appropriate purification process, starting from anaerobic digestion of organic household waste. The fundamental achievement of this work is that the CO2 produced is suitable for the food market, which has the most restrictive quality specifications, and thus for any other market. The produced biomethane, with a purity of over 96 vol% is of sufficiently high quality to be introduced into the methane distribution grid. This makes the present process the first successful example of simultaneous production of sustainable energy in the form of biomethane, and re-use of CO2 instead of its disposal as a waste material. Two enormous advantages of the membrane process over traditional processes are that it requires no amines or alkaline solutions for CO2 sorption, and that the dense membranes are absolute barrier materials for microorganisms, so that the CO2 is by definition microbiologically clean. With the simultaneous production of pure biomethane and pure bioCO2 from organic waste at industrial scale, we have demonstrated that it is possible to completely close the CO2 loop in biogas production.
The produced biomethane has a somewhat higher cost than natural gas, but this is partially compensated by the commercial value of the pure CO2 obtained. The process can in principle be applied to any kind of organic waste, thus forming an enormous potential source of renewable energy and environmentally impact-free CO2.
Conflicts of interest
There are no conflicts to declare.
Acknowledgements
LabAnalysis Srl is gratefully acknowledged for the chemical and microbiological analysis of the gas streams.
References
- R. E. H. Sims, H.-H. Rogner and K. Gregory, Energy Policy, 2003, 31, 1315–1326 CrossRef.
-
UNFCCC, Kyoto Protocol, Kyoto, Japan, 1998 Search PubMed.
- C. Mitchell and P. Connor, Energy Policy, 2004, 32, 1935–1947 CrossRef.
- H. Winkler, Energy Policy, 2005, 33, 27–38 CrossRef.
- J. A. Cherni and J. Kentish, Energy Policy, 2007, 35, 3616–3629 CrossRef.
-
UNFCCC, Paris agreement, Paris, France, 2015 Search PubMed.
- Paris Agreement – Status of Ratification, https://unfccc.int/process/the-paris-agreement/status-of-ratification, accessed 1 October 2018.
-
D. L. Hartmann, A. M. G. K. Tank and M. Rusticucci, IPCC AR5, 2013, pp. 31–39 Search PubMed.
-
R. Guerrero-Lemus and J. M. Martínez-Duart, Renewable Energies CO2, 2012, vol. 3, pp. 353–373 Search PubMed.
- M. E. Boot-Handford, J. C. Abanades, E. J. Anthony, M. J. Blunt, S. Brandani, N. Mac Dowell, J. R. Fernández, M.-C. Ferrari, R. Gross, J. P. Hallett, R. S. Haszeldine, P. Heptonstall, A. Lyngfelt, Z. Makuch, E. Mangano, R. T. J. Porter, M. Pourkashanian, G. T. Rochelle, N. Shah, J. G. Yao and P. S. Fennell, Energy Environ. Sci., 2014, 7, 130 RSC.
- R. M. Cuéllar-Franca and A. Azapagic, J. CO2 Util., 2015, 9, 82–102 CrossRef.
- J. Patricio, A. Angelis-Dimakis, A. Castillo-Castillo, Y. Kalmykova and L. Rosado, J. CO2 Util., 2017, 17, 50–59 CrossRef.
- N. MacDowell, N. Florin, A. Buchard, J. Hallett, A. Galindo, G. Jackson, C. S. Adjiman, C. K. Williams, N. Shah and P. Fennell, Energy Environ. Sci., 2010, 3, 1645 RSC.
- IPCC Special Report on Carbon Dioxide Capture and Storage, Prepared by Working Group III of the Intergovernmental Panel on Climate Change, Special Report on Carbon Dioxide Capture and Storage, UK and New York, NY, USA, 2005.
- K. Damen, A. Faaij and W. Turkenburg, Clim. Change, 2006, 74, 289–318 CrossRef.
- M. Peters, B. Köhler, W. Kuckshinrichs, W. Leitner, P. Markewitz and T. E. Müller, ChemSusChem, 2011, 4, 1216–1240 CrossRef PubMed.
- M. Mikkelsen, M. Jørgensen and F. C. Krebs, Energy Environ. Sci., 2010, 3, 43–81 RSC.
- T. Sakakura, J. C. Choi and H. Yasuda, Chem. Rev., 2007, 107, 2365–2387 CrossRef PubMed.
- Y. Kuwahara and H. Yamashita, J. CO2 Util., 2013, 1, 50–59 CrossRef.
- N. von der Assen, A. Sternberg, A. Kätelhön and A. Bardow, Faraday Discuss., 2015, 183, 291–307 RSC.
- C. Song, Catal. Today, 2006, 115, 2–32 CrossRef.
- Q. He, G. Yu, T. Tu, S. Yan, Y. Zhang and S. Zhao, Environ. Sci. Technol., 2017, 51, 8841–8850 CrossRef PubMed.
- E. V. Kondratenko, G. Mul, J. Baltrusaitis, G. O. Larrazabal, J. Perez-Ramirez, G. O. Larrazábal and J. Pérez-Ramírez, Energy Environ. Sci., 2013, 6, 3112 RSC.
- L. S. Fan, L. Zeng, W. Wang and S. Luo, Energy Environ. Sci., 2012, 5, 7254–7280 RSC.
- S. Inoue, H. Koinuma and T. Tsuruta, J. Polym. Sci., Part B: Polym. Lett., 1969, 7, 287–292 CrossRef.
- J. C. Jansen, R. Addink, K. Te Nijenhuis and W. J. Mijs, Macromol. Chem. Phys., 1999, 200, 1407–1420 CrossRef.
- M. Taherimehr and P. P. Pescarmona, J. Appl. Polym. Sci., 2014, 131 Search PubMed.
- G. Centi and S. Perathoner, Catal. Today, 2009, 148, 191–205 CrossRef.
- Q. Chen, M. Lv, Z. Tang, H. Wang, W. Wei and Y. Sun, J. CO2 Util., 2016, 14, 1–9 CrossRef.
- N. Meiri, R. Radus and M. Herskowitz, J. CO2 Util., 2017, 17, 284–289 CrossRef.
- F. van Bergen, J. Gale, K. J. Damen and A. F. B. Wildenborg, Energy, 2004, 29, 1611–1621 CrossRef.
- J. M. Barnard, D. Chaffin, S. Droste, A. Tierney and T. Phernetton, Obstet. Gynecol., 1995, 85, 669–674 CrossRef PubMed.
- A. Amanatidou, R. A. Slump, L. G. M. Gorris and E. J. Smid, J. Food Sci., 2000, 65, 61–66 CrossRef.
- K. Armstrong and P. Styring, Front. Energy Res., 2015, 3, 8 Search PubMed.
- C. D. Keeling, Tellus, 1973, 25, 174–198 CrossRef.
- T. Weimer, R. Berger, C. Hawthorne and J. C. Abanades, Fuel, 2008, 87, 1678–1686 CrossRef.
-
M. A. Arthur, W. E. Dean and S. O. Schlanger, The Carbon Cycle and Atmospheric CO2: Natural Variations Archean to Present, 1985, vol. 32, pp. 504–529 Search PubMed.
- A. Sanna, M. R. Hall and M. Maroto-Valer, Energy Environ. Sci., 2012, 5, 7781–7796 RSC.
- S. R. Bull, Proc. IEEE, 2001, 89, 1216–1226 CrossRef.
- Y. Le Maho, J. D. Whittington, N. Hanuise, L. Pereira, M. Boureau, M. Brucker, N. Chatelain, J. Courtecuisse, F. Crenner, B. Friess, E. Grosbellet, L. Kernaléguen, F. Olivier, C. Saraux, N. Vetter, V. A. Viblanc, B. Thierry, P. Tremblay, R. Groscolas and C. Le Bohec, Nat. Methods, 2014, 11, 1242–1244 CrossRef PubMed.
- S. Rasi, J. Läntelä and J. Rintala, Energy Convers. Manage., 2011, 52, 3369–3375 CrossRef.
- E. Esposito, G. Clarizia, P. Bernardo, J. C. Jansen, Z. Sedláková, P. Izák, S. Curcio, B. de Cindio and F. Tasselli, Chem. Eng. Process., 2015, 94, 53–61 CrossRef.
- Z. Sedláková, M. Kárászová, J. Vejražka, L. Morávková, E. Esposito, A. Fuoco, J. C. Jansen and P. Izák, Chem. Eng. Technol., 2017, 821–828 CrossRef.
- P. Dolejš, V. Poštulka, Z. Sedláková, V. Jandová, J. Vejražka, E. Esposito, J. C. Jansen and P. Izák, Sep. Purif. Technol., 2014, 131, 108–116 CrossRef.
- M. R. Khdhayyer, E. Esposito, A. Fuoco, M. Monteleone, L. Giorno, J. C. Jansen, M. P. Attfield and P. M. Budd, Sep. Purif. Technol., 2017, 173, 304–313 CrossRef.
- S. Wang, X. Li, H. Wu, Z. Tian, Q. Xin, G. He, D. Peng, S. Chen, Y. Yin, Z. Jiang and M. D. Guiver, Energy Environ. Sci., 2016, 9, 1863–1890 RSC.
- C. Y. Chuah, K. Goh, Y. Yang, H. Gong, W. Li, H. E. Karahan, M. D. Guiver, R. Wang and T.-H. Bae, Chem. Rev., 2018, 118, 8655–8769 CrossRef PubMed.
- C. Kunkel, F. Viñes and F. Illas, Energy Environ. Sci., 2016, 9, 141–144 RSC.
- C. Kunkel, F. Viñes and F. Illas, ACS Appl. Energy Mater., 2018, 1, 43–47 CrossRef.
-
P. Kaparaju and J. Rintala, The Biogas Handbook, Elsevier, Oxford, 2013 Search PubMed.
- E. Ryckebosch, M. Drouillon and H. Vervaeren, Biomass Bioenergy, 2011, 35, 1633–1645 CrossRef.
- M. Kárászová, Z. Sedláková and P. Izák, Chem. Pap., 2015, 69, 1277–1283 Search PubMed.
-
M. Ungerank and H. Roegl, Control of gas composition of a gas separation system having membranes, US Pat., US14442804, 2013 Search PubMed.
-
H. Gebhardt, P. Nagler, S. Buchholz, S. Cornelissen, E. Schulze and A. Marx, Evonik: Bioeconomy and Biobased Products, John Wiley & Sons, Inc., 2016 Search PubMed.
-
M. Ungerank, R. Harald and Evonik, SEPURAN®, Control of gas composition of gas separation system having membranes, US 9770687 B2, 2017 Search PubMed.
-
T. Viesser, M. Ungerank, J. Balster, C. Führer and Evonik Fibres GmbH, Method for producing polymide membranes, US 2016/0144323 A1, 2015.
-
Environmental Protection Agency (EPA), Compendium of Methods for the Determination of Toxic Organic Compounds in Ambient Air, 1999, pp. 1–53 Search PubMed.
-
National Institute for Occupational Saftey and Health (NIOSH), Ammonia: Manual of Analytical Methods (NMAM), 1994, vol. 4 Search PubMed.
-
European Industrial Gases Association, Carbon dioxide source qualification quality standards and verification, 2008 Search PubMed.
-
European collaborative action (ECA) of the Commison of the European Communities, Report No. 12 Biological Particles in Indoor Environment, Luxembourg, 1994, vol. 17.
-
P. Anzidei, L. Frusteri, R. Giovinazzo and F. Venanzetti, INAIL: Il monitoraggio microbiologico negli ambienti di lavoro, Campionamento e analisi, Milan, 2010 Search PubMed.
- N. Abatzoglou and S. Boivin, Biofuels, Bioprod. Biorefining, 2009, 3, 42–71 CrossRef.
-
S. P. A. Edison Stoccaggio, Codice di rete: Requisiti Di Qualità Del Gas Allegato 11a, Milan, 2008 Search PubMed.
- A. Makaruk, M. Miltner and M. Harasek, Sep. Purif. Technol., 2010, 74, 83–92 CrossRef.
- Q. Sun, H. Li, J. Yan, L. Liu, Z. Yu and X. Yu, Renewable Sustainable Energy Rev., 2015, 51, 521–532 CrossRef.
-
A. Petersson and A. Wellinger, IEA Bioenergy, 2009, pp. 1–20 Search PubMed.
-
F. Bauer, C. Hulteberg, T. Persson and D. Tamm, Biogas upgrading – Review of commercial technologies, 2013 Search PubMed.
-
M. Persson, O. Jonsson and A. Wellinger, IEA Bioenergy, 2007, pp. 1–32 Search PubMed.
-
Eurostats, Natural gas price
statistics, 2016 Search PubMed.
-
European Commission, Gas Market, 2017, vol. 10.
- A. Paturska, M. Repele and G. Bazbauers, Energy Procedia, 2015, 72, 71–78 CrossRef.
- K. Verbeeck, L. C. Buelens, V. V. Galvita, G. B. Marin, K. M. Van Geem and K. Rabaey, Energy Environ. Sci., 2018, 11, 1788–1802 RSC.
- P. Markewitz, W. Kuckshinrichs, W. Leitner, J. Linssen, P. Zapp, R. Bongartz, A. Schreiber and T. E. Müller, Energy Environ. Sci., 2012, 5, 7281 RSC.
-
European Commission, Use of Economic Instruments & Waste Management Performances – Final Report, Brussels, 2012.
Footnote |
† Electronic supplementary information (ESI) available. See DOI: 10.1039/c8ee02897d |
|
This journal is © The Royal Society of Chemistry 2019 |
Click here to see how this site uses Cookies. View our privacy policy here.