DOI:
10.1039/C8SE00274F
(Communication)
Sustainable Energy Fuels, 2018,
2, 1699-1706
Facile conversion of levulinic acid to γ-valerolactone using a high surface area magnetically separable Ni/NiO catalyst†
Received
11th June 2018
, Accepted 27th June 2018
First published on 27th June 2018
Abstract
A study on the conversion of levulinic acid (LA) to γ-valerolactone (GVL) and methyl levulinate (ML) has been done using a high surface area Ni/NiO catalyst. The hydrogenation of levulinic acid over the Ni/NiO catalyst showed high mass activity for γ-valerolactone formation (16 mmol gcat−1 h−1) at 110 °C at 40 bar pressure. The presence of acidity effects the conversion of LA to GVL and ML. First-principles DFT calculations were used to calculate the adsorption energy and transition state for the reaction. The Ni/NiO catalyst showed 99% LA conversion and 94% GVL selectivity at 110 °C in methanol, which is higher than the reported activity of Ni-based catalysts (RANEY® Ni and Ni/Al2O3).
Introduction
The convenient and facile synthesis of γ-valerolactone (GVL) is a much sought-after goal in industry. GVL has potential applications as a biofuel blended with gasoline,1 as a drug-precursor to γ-hydroxybutyric acid (GHB),2 as a green solvent,3,4 and in the perfume and flavor industries.4,5 GVL has been synthesized starting from levulinic acid (LA) by various researchers using different types of catalysts (homogeneous and heterogeneous), as well as, in a variety of solvents and reaction conditions.5–10 In its application as a biofuel, it has been estimated that an efficient process using a cheap feedstock could bring the cost of production of GVL to $ 2–3 per gallon.11–14 However, the process still achieves maximum conversion with catalysts that are both expensive and synthesized via conventionally non-green methods.15,16 In this study, we report an excellent conversion of levulinic acid into γ-valerolactone and methyl levulinate under relatively mild conditions and using an inexpensive support-free porous nickel catalyst synthesized by a green method. Homogeneously distributed metallic nickel sites were incorporated into nickel oxide using double reducing agents. Use of double reducing agents to prepare metal catalysts is reported in the literature.17,18 Support-free catalysts are inexpensive as well as save catalyst preparation time. Porous metals eliminate support influence and have the advantage of having a large surface area. Support-free metal catalysts may have an advantage against the sintering effect. Also, the morphology and structure of porous metal catalysts can be controlled.19,20 Methyl levulinate is more valuable than gamma-valerolactone and levulinic acid. These levulinates, as byproducts of levulinic acid hydrogenation, are also useful in the fragrance industry, as flavorings, and as additives in diesel. Especially, ethyl levulinate is reported as an additive to diesel fuel to modify fuel properties.21,22 The high porosity and total acidity of the catalyst increase the LA conversion to methyl levulinate.20–22 In this work, we report the Ni/NiO catalyst system and its catalytic activity for the conversion of LA to GVL in methanol solvent. The reactions were carried out at different pressures and temperatures and with variation in catalyst amount. The recyclability and magnetic separation of the catalyst were also studied.
Experimental
Materials
Levulinic acid (98%) was purchased from Acros Organics. Nickel nitrate hexahydrate, ethanol sodium hydroxide, and hydrazine hydrate were purchased from Merck India. Octadecyl dimethyl 3-trimethoxysilyl propyl ammonium chloride (ODAC) (60 vol% in methanol) and methanol (99.9%) were purchased from Sigma Aldrich Chemicals. RANEY® Ni was purchased from Merck India. The supported Ni catalyst (Ni/Al2O3) was procured from Johnson Matthey.
Synthesis of the catalyst
The catalyst was synthesized by a chemical reduction method and using the organosilane (ODAC) template.17,23 The synthesis procedure was performed as reported earlier in the literature.17 In the chemical reduction method, a combination of two reducing agents was used for maximum reduction of the Ni precursor to Ni/NiO as well as for homogeneous formation of metallic nickel sites.17,18 The catalyst was calcined at 550 °C under an air atmosphere for 6 hours to remove the remnant organic impurities. The mesoporous Ni/NiO catalyst is magnetically recoverable. The catalyst was finally reduced under a stream of hydrogen at 450 °C for 4 hours.
To prepare the silica-leached Ni/NiO catalyst, the silica from the catalyst (1 g) was removed as sodium silicate by treating 4 times with 30 ml, 1 M NaOH solution at 80 °C, followed by filtering and washing with excess water.
Characterization of the catalyst
Powder X-ray diffraction patterns were obtained using a diffractometer (Bruker) with Cu-Kα radiation at 40 kV and 40 mA. The scans were taken at a 10–80° 2θ range with a scan rate of 1° min−1. The transmission electron microscopy (TEM) observations of the catalyst were carried out with a Hitachi H7100 electron microscope at 75 kV. The sample was slurried with ethanol and sonicated for 5 minutes and deposited on a copper grid for the analysis.
The surface area and pore volumes of the catalyst were examined by N2 adsorption–desorption isotherms at 77 K using a Belsorp-Max, BEL, Japan. The samples were pre-treated under vacuum at 300 °C before exposing to nitrogen gas at 77 K for analysis.
The surface acidity of the catalyst was measured using an ammonia adsorption–desorption technique using a chemical adsorption instrument (Micrometrics 2720) with a thermal conductivity detector.
Lewis and Brønsted acid sites were confirmed by pyridine adsorbed FT-IR spectroscopy (REMSPEC Technologies). The spectrum was recorded in the frequency range of 1300–1600 cm−1 with a resolution of 4 cm−1 for 37 scans.
Inductively coupled plasma-atomic emission spectrometry (ICP-AES) analysis (DRE, PS-3000UV, LEEMAN LABS INC., USA) was done to determine the elemental composition of the catalyst.
X-ray absorption measurements were carried out at the dispersive EXAFS beamline (BL-9) at the INDUS-2 Synchrotron Source (2.5 GeV, 100 mA) in transmission mode at the Raja Ramanna Centre for Advanced Technology (RRCAT), Indore, India.
The liquid products were analyzed using a gas chromatograph (Agilent-6890-GC-5973) equipped with a 30mHP-5 capillary. The conversion and selectivity for each reaction were calculated using known external standards. Chromatograms are shown in Fig. S5–S7.†
First-principles quantum mechanical spin-polarized DFT calculations were carried out using the CASTEP (Cambridge Serial Total Energy Package)24 with the generalized gradient approximation of Perdew, Burke, and Ernzerhof (GGA-PBE).25 The adsorption energy was calculated as Eads = Esurf+adsorbate − Esurf − Eadsorbate, where Esurf+adsorbate, Esurf, and Eadsorbate are the calculated total energies of the NiO (Ni) surface with the adsorbate, the NiO (Ni) surface, and the adsorbate species, respectively. All constituents were optimized with the DMol3 package of Material Studio.26 The transition state of the reaction was calculated through the linear (LST) and quadratic synchronous transit methods (QST) method proposed by Halgren and Lipscomb in 1977.27–29 This method uses a guess for the reaction pathway called the Minimum energy path (MEP) (Fig. S4†) and optimizes the geometries of several images along this path simultaneously.
Catalytic hydrogenation of levulinic acid
Before the reaction, the catalyst was heated to 450 °C under a stream of H2 for 4 hours to obtain the maximum amount of Ni0 species, which are proposed to be the active species. We called this as the activated catalyst. All the hydrogenation reactions reported in this study were done using this catalyst. The catalytic hydrogenation reactions were carried out in a 25 ml stirred reactor (Parr Instrument Company). In a typical reaction, 5 ml levulinic acid was mixed in 15 ml methanol solvent. The reaction mixture was filled into the reactor vessel. The reactions were performed at different pressures (10, 20, 30 and 40 bar) and temperatures (80, 90, 100 and 110 °C) with the variation in the catalyst amount (from 2 wt% to 20 wt%). The reactor vessel was purged with H2 three times before each reaction. The reaction products were separated from the catalyst magnetically. The separated catalyst was dried in an oven at 100 °C for two days. The dried catalyst was then characterized for its structural stability.
Results and discussion
The powder XRD pattern shows the presence of both Ni and NiO in the sample (Fig. 1). The XRD pattern of the catalyst before reduction showed sharp peaks of Ni planes of (111) and (220) at 2θ values of 44° and 76°, respectively, and peaks of NiO planes corresponding to (111) and (220) at 2θ values of 37° and 63°, respectively. The XRD pattern of reduced catalyst showed the peaks of the metallic nickel with planes (111), (200) and (220) at 2θ values of 44°, 52° and 76°, respectively. The peaks due to NiO were absent in the reduced catalyst indicating the complete reduction of NiO into Ni on the surface of the catalyst. The crystalline size of Ni in Ni/NiO was 7 nm as determined from the Ni (111) plane using the Scherrer equation. TEM images show the morphology in which dark-colored spherical Ni nanoparticles are present on grey sheet-like NiO (Fig. 2a). The particle size from TEM analysis was ranging from 6 to 15 nm (Fig. 2c). The SAED pattern (Fig. 2b) shows the crystalline nature of the catalyst. TEM-EDAX analysis (Fig. 2d) shows the presence of a negligible amount of Si (1.9 wt%) in the catalyst system.
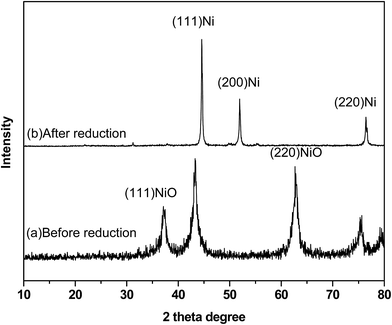 |
| Fig. 1 XRD pattern of the Ni/NiO catalyst (a) before reduction (b) after reduction. | |
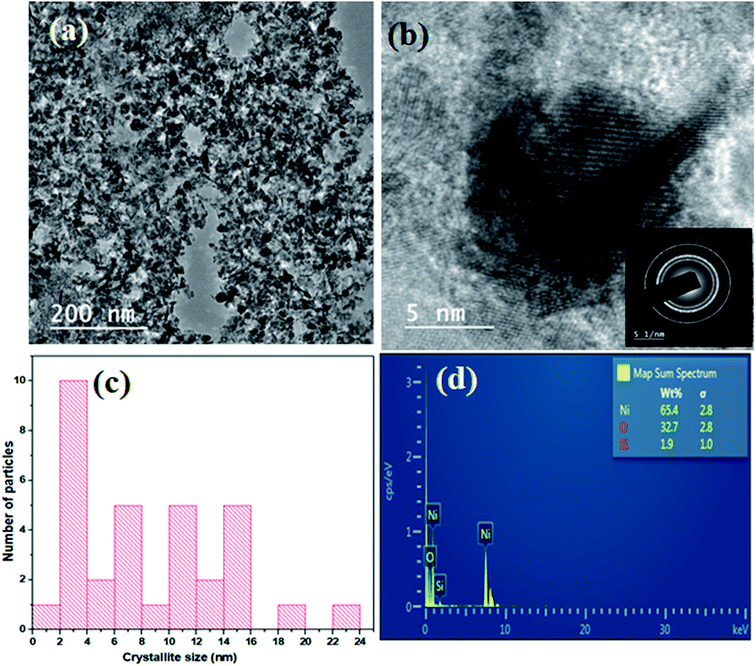 |
| Fig. 2 TEM image and particle size distributions of the Ni/NiO catalyst. | |
The N2 adsorption–desorption analysis of the catalyst showed a high surface area (250 m2 g−1) and a large pore diameter of 8 nm, indicating that catalytic reactions can take place both on the catalyst surface and within the pores of the catalyst (Fig. 3).
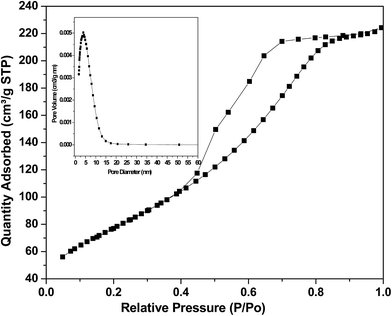 |
| Fig. 3 N2 adsorption–desorption isotherms and pore size distribution curves (inset) of the Ni/NiO catalyst. | |
The ammonia TPD analysis determined the intrinsic acidity of 0.2 mmol g−1 (Fig. S2a†), which along with reducing properties could aid in the catalytic conversion of LA to GVL and ML.23,30 The presence of both Lewis and Brønsted acid sites in the Ni/NiO catalyst was confirmed by pyridine adsorbed FTIR analysis (Fig. S2b†). The Ni/NiO catalyst showed two bands (Fig. S3†) at 1580 and 1444 cm−1, ascribed to Lewis-acid sites. The FTIR band at 1539 cm−1 corresponds to the adsorption of pyridine on Brønsted acidic sites.17 The origin of Lewis acidity may be ascribed to unsaturated Ni species, whereas Brønsted acid sites originate from the linkages of Si with Ni in the Ni/NiO framework (Scheme 1).23b
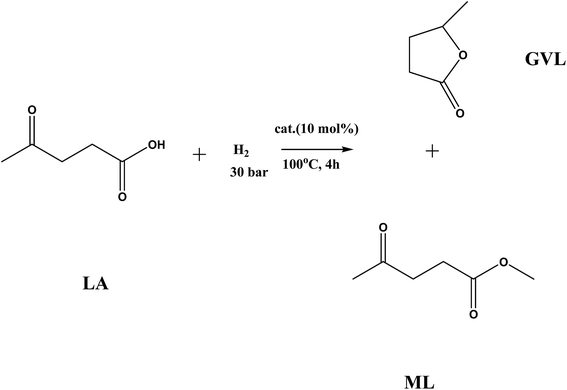 |
| Scheme 1 Scheme for conversion of LA to GVL and ML. | |
ICP-AES analysis shows that the ratio of Ni/Si is 51 in the fresh catalyst (Table S1†), which was in fair agreement with the TEM and SEM-EDAX results (Fig. S3†). The spent catalyst showed the same ratio of nickel to silicon which indicates that NiO leaching did not take place during the levulinic acid hydrogenation reaction.
The surface area of different nickel catalysts is listed in Table S2.† The surface area of Ni/Al2O3 is 110 m2 g−131 and that of RANEY® nickel32 is 56 m2 g−1. Ni/NiO has the surface area of 250 m2 g−1 which is almost 4 times higher than the surface area of RANEY® nickel and 2 times higher than that of Ni/Al2O3. The high specific surface area of the Ni/NiO catalyst would contribute to the higher accessibility of active sites for reactants, and can increase the reaction rate. The Ni/NiO catalyst was prepared using the organosilane surfactant as a template to obtain a mesoporous catalyst with a high surface area (250 m2 g−1), high metal dispersion (15%) and intrinsic acidity. The high specific surface area is obtained due to the removal of the template after calcination at high temperature (550 °C), leading to pore formation, thermal stability, and crystallinity. The general advantage for preparation of a Ni/NiO catalyst through this route is the controllable morphology of Ni/NiO.
The metal dispersion of the Ni/NiO catalyst is 15% which is 3 times higher than that of RANEY® nickel. The Ni/NiO catalyst is expected to show better catalytic activity, ascribed to the availability of more Ni active sites (higher dispersion) in the Ni/NiO catalyst system. Mesoporous Ni/NiO has a concentration of 30 wt% Ni and 70 wt% NiO as determined from EXAFS analysis.
Catalytic studies
The results of the catalytic hydrogenation of LA to GVL and ML at 110 °C and different pressures with 10 wt% catalyst loading, in methanol solvent, are tabulated in Table 1. The results for hydrogenation reactions at different temperatures are shown in Table S2.† The selectivity to GVL decreases with the increase in temperature and pressure, which can be attributed to the higher activity of the solvent leading to higher yields of ML.
Table 1 Catalytic hydrogenation of levulinic acid under different conditions at 10 wt% catalyst concentration and 110 °C (reaction time: 4 h, solvent: methanol)
Entry # |
Pressure (bar) |
Total conversion |
Selectivity (GVL) |
Selectivity (ML) |
1 |
10 |
90 |
64 |
36 |
2 |
20 |
92 |
82 |
18 |
3 |
30 |
98 |
90 |
10 |
4 |
40 |
99 |
94 |
06 |
The LA conversion and GVL selectivity were <5% in the absence of a catalyst. Table 2 shows the catalytic performance for LA hydrogenation conversion over different Ni-based catalysts. The levulinic hydrogenation over the Ni/NiO catalyst showed 99% conversion and 94% selectivity for GVL at 110 °C in methanol. Under similar reaction conditions, LA conversion was 90%, and selectivity (GVL) was 87% over the RANEY® Ni catalyst. At 120 °C, LA conversion was 99%, and the selectivity of GVL was 94% with the Ni/NiO catalyst whereas the RANEY® Ni catalyst showed 93% conversion of LA and 88% selectivity of GVL.32 The supported Ni catalyst (Ni/Al2O3) showed 89% LA conversion and 90% GVL selectivity for LA hydrogenation under the same reaction conditions. The turn-over-frequency (TOF) of Ni/NiO (70 wt% Ni content) catalyst for LA hydrogenation is about 1.5 times higher than that of the RANEY® nickel (80 wt% Ni content), and slightly higher than that of the Ni/Al2O3 (12 wt% Ni content) (Table 2).
Table 2 Catalytic performance, LA conversion, and selectivity (GVL) over Ni/NiO and comparative study with different catalystsa
Catalyst |
Solvent |
Temp./°C |
% Conversion (X) |
(%) Selectivity (GVL) |
TOF (h−1) |
The reaction has been performed at 110–120 °C, 40 bar, 4 h; 10 wt% catalyst, LA 5 ml, methanol 15 ml.
Reaction conditions: cat. 200 mg, LA 500 mg, methanol 20 ml, 110 °C, 40 bar, 2 h.
|
Ni/NiO |
Methanol |
110 |
99 |
94 |
250 |
RANEY® Ni |
Methanol |
110 |
90 |
87 |
180 |
Ni/NiO |
Methanol |
120 |
99 |
94 |
250 |
RANEY® Ni32b |
Methanol |
120 |
94 |
88 |
— |
Ni/Al2O3 |
Methanol |
120 |
89 |
90 |
230 |
Table S3† shows the effect of amount of catalyst loading (wt%) with respect to feed (LA). The optimum reaction conditions for the hydrogenation using the Ni/NiO catalyst were 110 °C temperature, 40 bar pressure of H2 and with 10 wt% catalyst loading. Higher catalyst loading resulted in similar product yields as with 10 wt% loading. A maximum GVL selectivity of 94% was obtained under the above reaction conditions due to smaller Ni particles, controllable surface morphology and acid density.3 The presence of active catalyst species of Ni0, high surface area and acid sites in this case can be a plausible reason for higher selectivity and reusability as also reported in previous literature.20,32 It has been reported that Lewis acid sites are responsible for converting LA and its esters to alkyl 4-hydroxypentanoate which is then converted to GVL in the presence of Brønsted acid sites.30 The Ni/NiO catalyst has both Lewis and Brønsted acid sites which were analyzed by the pyridine adsorbed FTIR spectrum (Fig. S2b†). The presence of Brønsted acid sites has a positive effect on the conversion of LA to GVL and ML. To corroborate the hypothesis, the reactions were carried out using an activated catalyst (freshly reduced under a H2 stream at 450 °C for four hours) and the catalyst where Ni0 sites were oxidized before the reaction. The activated catalyst had a higher conversion rate (99% at 110 °C and 40 bar H2 pressure) compared to the oxidized catalyst which showed 35% conversion. To confirm the formation of methyl levulinate due to methanol as a solvent, the reaction was done in the absence of solvent, and the results are tabulated in Table S5.† The conversion of 95% and a 100% selectivity of GVL were obtained at 200 °C and 40 bar in the absence of a solvent. The solvent-free hydrogenation of levulinic acid over the Ni/Al2O3 catalyst showed 44% and 92% LA conversions at 180 °C and 200 °C, respectively, and 100% GVL selectivity at 180 °C and 200 °C with 50 bar H2 pressure.33
The recyclability of the Ni/NiO catalyst was compared with the RANEY® Ni and Ni/Al2O3 catalysts. The Ni/NiO catalyst was active till the fourth cycle with 94% LA conversion and 92% GVL selectivity, whereas the Ni/Al2O3 catalyst deactivated in the second cycle with 45% LA conversion and 78% GVL selectivity. The RANEY® Ni catalyst also deactivated in the second run with 50% LA conversion and 80% GVL selectivity. The low recovery (70%) and structural degradation of used RANEY® Ni might lead to a sharp decline in catalytic performance during the recycling experiment,32 indicating that Ni/NiO is more stable than RANEY® Ni in recycling experiments. The lower recyclability of the Ni/Al2O3 catalyst could be due to the sintering of its large Ni particles resulting in esterification of LA.33 The better recyclability of the Ni/NiO catalyst indicates its more stable structure with low sintering and agglomeration of Ni nanoparticles than that of RANEY® Ni and Ni/Al2O3.
The reaction was also carried out with the silica-leached catalyst where the acidic content was reduced. The conversion of levulinic acid decreased to 72% at 110 °C and 40 bar as compared to the non-leached catalyst.
Activation energy
The kinetic order of the hydrogenation reaction was calculated using the data from Tables S6 and S7.† The reaction was found to be of half-order with respect to H2 and independent of LA concentration. The plot between ln
K and 1000/T (K−1) is shown in Fig. S1.† The activation energy for the LA conversion was 37.4 ± 2.1 kJ mol−1. The activation energy for hydrogenation of levulinic acid over the NiO catalyst is reported to be 93 kJ mol−1 under the same conditions.34 The activation energy for levulinic acid hydrogenation of the reported NiO catalyst is 2.5 times higher than that of the mesoporous Ni/NiO catalyst. The hydrogenation of levulinic acid over the Ni/NiO catalyst showed higher mass activity for γ-valerolactone formation (16 mmol gcat−1 h−1) as compared to a recently reported Ni/NiO catalyst (14 mmol gcat−1 h−1).34
Theoretical studies
Theoretical calculations were used to explain the mechanism of levulinic acid hydrogenation over the Ni/NiO surface.24,25,34 The primary first-principles calculations were performed using CASTEP to improve the understanding of the adsorption behavior of the Ni/NiO surface and reactants in the reaction. The adsorption energies of levulinic acid and H2 on the Ni/NiO surface were calculated and a plausible mechanism was drawn using the transition state. Based on XRD and TEM observations, a surface model of NiO (111) was constructed, and the metallic Ni was put onto the surface to represent the model of the Ni/NiO surface (Fig. 4). The optimized lowest energy structures of the Ni/NiO surface, levulinic acid, and H2 adsorbed on the Ni/NiO (111) surface are shown in Fig. 4. The adsorbed species (LA) is stabilized on the Ni/NiO (111) surface (Fig. 4(ii)). The values of adsorption energy of H2 and levulinic acid on Ni/NiO (111) surfaces are −0.15 (Fig. 4(iii)) and −11.89 eV (Fig. 4(ii)), respectively, which are more negative than those reported for Ni or NiO separately in the literature.29 Lower adsorption energy for LA indicates that it is preferentially adsorbed on the Ni/NiO (111) surface compared to H2. The adsorption energy value of −11.89 eV was obtained due to the strong interaction between levulinic acid and Ni/NiO (111), whereas, the levulinic acid adsorption energy value on Ni (111) was reported to be only −0.40 eV.34 As levulinic acid prefers to adsorb on the NiO surface and H2 on the Ni surface,34 having both of them in the single catalyst is expected to give better hydrogenation efficiency. On the Ni/NiO surface, adsorption of levulinic acid is stronger than that of H2, unlike on Ni (111) where the competitive adsorption of H2 and levulinic acid takes place because of their similar adsorption energy values.34
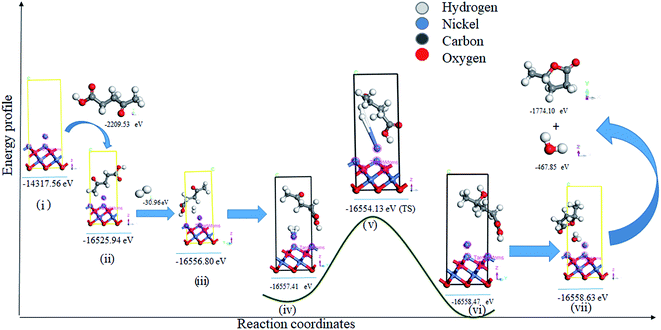 |
| Fig. 4 Energy profile of different adsorbed species over the NiO (Ni) surface. | |
Thus, the reaction takes place between adsorbed levulinic acid over the Ni/NiO surface with adsorbed hydrogen (at Ni sites), which seems a feasible pathway for levulinic acid hydrogenation into 4-hydroxy-pentanoic acid (HVA). This goes through an apparent activation energy value of 3.2 eV (Fig. 4(v) and S4†).
Conclusions
A high-surface area magnetically separable Ni/NiO catalyst with inherent Lewis and Brønsted acidity was synthesized. The catalyst showed high conversion (>90%) and high selectivity (>90%) in the hydrogenation of LA to GVL. The active catalytic species is Ni0. The activation energy was determined to be 37.4 ± 2.1 kJ mol−1. The used catalyst was separated magnetically and reusable with 5% loss in activity and 2% loss in GVL selectivity in the fourth cycle. The adsorption energy for levulinic acid hydrogenation was calculated to be −11.89 eV on the surface of the Ni/NiO catalyst system where the LA hydrogenation to GVL goes through a HVA intermediate.
Conflicts of interest
There are no conflict to declare.
Acknowledgements
H.S. thanks the UGC-RGNF for a research fellowship. N.I. and R.Y. thank CSIR for a research fellowship. The staff of Hydroprocessing Area, CSIR-IIP, Dehradun is kindly acknowledged for their kind help and support.
References
- J. A. Melero, G. Moralesa, J. Iglesias, M. Paniagua, B. Hernandez and S. Penedo, Efficient conversion of levulinic acid into alkyl levulinates catalyzed by sulfonic mesostructured silicas, Appl. Catal., A, 2013, 466, 116–122 CrossRef.
- L. J. Marinetti, B. J. Leavell, C. M. Jones, B. R. Hepler, D. S. Isenschmid and R. L. Commissaris, Gamma-butyrolactone (GBL) and gamma valerolactone (GVL): similarities and differences in their effects on the acoustic startle reflex and the conditioned enhancement of startle in the rat, Pharmacol., Biochem. Behav., 2012, 101, 602–608 CrossRef PubMed.
- L. Yan, Q. Yao and Y. Fu, Conversion of levulinic acid and alkyl levulinates into biofuels and high-value chemicals, Green Chem., 2017, 19, 5527–5547 RSC.
- R. V. Christian, H. D. Brown and R. M. Hixon, Derivatives of γ-valerolactone, 1,4-pentanediol and 1,4-di-(β-cyanoethoxy)-pentane1, J. Am. Chem. Soc., 1947, 69, 1961–1963 CrossRef.
- C. Li, G. Xu, Y. Zhai, X. Liu, Y. Ma and Y. Zhang, Hydrogenation of biomass-derived ethyl levulinate into γ-valerolactone by activated carbon supported bimetallic Ni and Fe catalysts, Fuel, 2017, 203, 23–31 CrossRef.
- Q. Xu, X. Li, T. Pan, C. Yu, J. Deng, Q. Guo and J. Fu, Supported copper catalysts for highly efficient hydrogenation of biomass-derived levulinic acid and γ-valerolactone, Green Chem., 2016, 18, 1287–1294 RSC.
- B. Fabos, M. Y. Lui, Y. F. Mui, Y. Y. Wong, L. T. Mika, L. Qi, E. Csefalvay, V. Kovacs, T. Szucs and I. T. Horvath, Use of Gamma-Valerolactone as an Illuminating Liquid and Lighter Fluid, ACS Sustainable Chem. Eng., 2015, 3, 1899–1904 CrossRef.
- J. N. Putro, A. Kurniawan, F. E. Soetaredjo, S. Y. Lin, Y. H. Ju and S. Ismadji, Production of gamma-valerolactone from sugarcane bagasse over TiO2-supported platinum and acid-activated bentonite as a co-catalyst, RSC Adv., 2015, 5, 41285–41299 RSC.
- J. Deng, Y. Wang, T. Pan, Q. Xu, Q. X. Guo and Y. Fu, Conversion of carbohydrate biomass to γ-valerolactone by using water-soluble and reusable iridium complexes in acidic aqueous media, ChemSusChem, 2013, 6, 1163–1167 CrossRef PubMed.
-
(a) M. Chalid, A. A. Broekhius and H. J. Heeres, Experimental and kinetic modeling studies on the biphasic hydrogenation of levulinic acid to γ-valerolactone using a homogeneous water-soluble Ru–(TPPTS) catalyst, J. Mol. Catal. A: Chem., 2011, 341, 14–21 CrossRef;
(b) J. M. Tukacs, R. V. Jones, F. Darvas, G. Dibó, G. Lezsak and L. T. Mika, Synthesis of γ-valerolactone using a continuous-flow reactor, RSC Adv., 2013, 3, 16283–16287 RSC.
- W. Li, J. H. Xie, H. Lin and Q. L. Zhou, Highly efficient hydrogenation of biomass-derived levulinic acid to γ-valerolactone catalyzed by iridium pincer complexes, Green Chem., 2012, 14, 2388–2390 RSC.
- J. M. Tukacs, D. Kiraly, A. Stradi, G. Novodarszki, Z. Eke, G. Dibo, T. Kegl and L. T. Mika, Efficient catalytic hydrogenation of levulinic acid: a key step in biomass conversion, Green Chem., 2012, 14, 2057–2065 RSC.
- S. Kang, J. Fu, Y. Ye, W. Liao, Y. Xiao, P. Yang and G. Liu, One-pot production of hydrocarbon oils from biomass derived γ-valerolactone, Fuel, 2018, 216, 747–751 CrossRef.
- A. M. R. Galletti, C. Antonetti, V. D. Luise and M. A. Martinelli, A sustainable process for the production of γ-valerolactone by hydrogenation of biomass-derived levulinic acid, Green Chem., 2012, 14, 688–694 RSC.
- A. S. Amarasekara and M. A. Hasan, Pd/C catalyzed conversion of levulinic acid to γ-valerolactone using alcohol as a hydrogen donor under microwave conditions, Catal. Commun., 2015, 60, 5–7 CrossRef.
-
(a) R. A. Bourne, J. G. Stevens, J. Ke and M. Poliakoff, Maximising opportunities in supercritical chemistry: the continuous conversion of the levulinic acid to γ-valerolactone in CO2, Chem. Commun., 2007, 44, 4632–4634 RSC;
(b) K. Shimizu, S. Kanno and K. Kon, Hydrogenation of levulinic acid to γ-valerolactone by Ni and MoOx co-loaded carbon catalyst, Green Chem., 2014, 16, 3899–3903 RSC.
- H. Singh, A. Rai, R. Yadav and A. K. Sinha, Glucose hydrogenation to sorbitol over unsupported mesoporous Ni/NiO catalyst, Mol. Catal., 2018, 451, 186–191 CrossRef.
- C. Nicholas, T. Nelson, A. R. Purnima, D. R. Malinda and V. Javier, Template Synthesis and Chemical Behavior of Nickel Nanoparticles within High Aspect Ratio Silica Capsules, J. Phys. Chem. C, 2013, 117, 25826–25836 CrossRef.
- K. Xinchen, S. Xiaofu, M. Xiaoxue, Z. Pei, Z. Zhanrong, M. Qinglei and H. Buxing, Synthesis of Hierarchical Porous Metals Using Ionic-Liquid-Based Media as Solvent and Template, Angew. Angew. Chem., Int. Ed., 2017, 56, 12683–12686 CrossRef PubMed.
- K. I. Tominaga, A. Mori, Y. Fukushim, S. Shimad and K. Sato, Mixed-acid systems for the catalytic synthesis of methyl levulinate from cellulose, Green Chem., 2011, 13, 810–812 RSC.
- K. I. Shimizu, S. Kanno and K. Kon, Hydrogenation of levulinic acid to γ-valerolactone by Ni and MoOx co-loaded carbon catalysts, Green Chem., 2014, 16, 3899–3903 RSC.
-
(a) K. Xiangjin, W. Shuxiang, L. Xiaole and L. Junhai, Efficient Conversion of Levulinic Acid to Ethyl Levulinate over a Silicotungstic-Acid-Modified Commercially Silica-Gel Sphere Catalyst, Energy Fuels, 2016, 30, 6500–6504 CrossRef;
(b) V. V. Kumar, G. Naresh, M. Sudhakar, C. Anjaneyulu, S. K. Bhargava, J. Tardio, V. K. Reddy, A. H. Padmasric and A. Venugopal, An investigation on the influence of support type for Ni catalyzed vapour phase hydrogenation of aqueous levulinic acid to γ-valerolactone, RSC Adv., 2016, 6, 9872–9879 RSC.
-
(a) X. Jingfang, S. Hu, M. Junxian, Q. Xingtai, X. Pei, W. Xizhang, W. Qiang and H. Zheng, Porous hierarchical nickel nanostructures and their application as a magnetically separable catalyst, J. Mater. Chem., 2012, 22, 11927 RSC;
(b) C. Deng, J. Zhang, L. Dong, M. Huang, B. Li, G. Jin, J. Gao, F. Zhang, M. Fan, L. Zhang and Y. Gong, The effect of positioning cations on acidity and stability of the framework structure of Y zeolite, Sci. Rep., 2016, 6, 23382 CrossRef PubMed.
- J. Clark Stewart, D. S. Matthew, J. C. Pickard, J. P. Hasnip and I. J. Probert, First principles methods using CASTEP, Z. Kristallogr., 2005, 220, 567–570 Search PubMed.
- P. P. John, B. Kieron and E. Matthias, Generalized Gradient Approximation Made Simple, Phys. Rev. Lett., 1996, 77, 3865–3868 CrossRef PubMed.
- B. Delley, From molecules to solids with the DMol (3) approach, J. Chem. Phys., 2000, 113, 7756–7764 CrossRef.
- T. A. Halgen and W. N. Lipscomb, The synchronous-transit method for determining reaction pathways and locating molecular transition states, Chem. Phys. Lett., 1977, 49, 225–232 CrossRef.
- H. Graeme and J. Hannes, Improved tangent estimate in the nudged elastic band method for finding minimum energy paths and saddle points, J. Chem. Phys., 2000, 113, 9978 CrossRef.
- J. G. Wang and H. J. Jiao, CO2 Reforming of CH4 on Ni (111): A Density Functional Theory Calculation, J. Phys. Chem. B, 2006, 110, 9976–9983 CrossRef PubMed.
- L. Fukun, F. J. Liam, C. Zhenping, L. Yingwen, L. Sijie, L. Hongming, L. Jinxing and L. Xuehui, Catalytic transfer hydrogenation of butyl levulinate to γ-valerolactone over zirconium phosphates with adjustable Lewis and Brönsted acid sites, Appl. Catal., B, 2017, 214, 67–77 CrossRef.
- Q. Y. Bi, X. L. Du, Y. M. Liu, Y. Cao, H. Y. He and K. N. Fan, Efficient Subnanometric Gold-Catalyzed Hydrogen Generation via Formic Acid Decomposition under Ambient Conditions, J. Am. Chem. Soc., 2012, 134, 8926–8933 CrossRef PubMed.
- Z. Rong, Z. Sun, L. Wang, J. Lv, Y. Wang and Y. Wang, Efficient conversion of levulinic acid into γ-valerolactone over Raney Ni catalyst prepared from melt-quenching alloy, Catal. Lett., 2014, 144, 1766–1771 CrossRef.
- K. Hengst, M. Schubert, W. P. Hudson, C. Lu, W. Kleist and J. D. Grunwaldt, Synthesis of γ-valerolactone by hydrogenation of levulinic acid over supported nickel catalysts, Appl. Catal., A, 2015, 502, 18–26 CrossRef.
- S. Song, Y. Sikai, C. Jiahui, D. Lu, W. Guangjun, G. Naijia and L. Landong, Heterostructured Ni/NiO composite as a robust catalyst for the hydrogenation of levulinic acid to γ-valerolactone, Appl. Catal., B, 2017, 217, 115–124 CrossRef.
Footnote |
† Electronic supplementary information (ESI) available. See DOI: 10.1039/c8se00274f |
|
This journal is © The Royal Society of Chemistry 2018 |
Click here to see how this site uses Cookies. View our privacy policy here.