Core–shell structural PANI-derived carbon@Co–Ni LDH electrode for high-performance asymmetric supercapacitors†
Received
10th March 2018
, Accepted 12th April 2018
First published on 14th April 2018
Abstract
Carbon/metal nanocomposites have been considered promising electrode materials for application in supercapacitors owing to their combination of good electrical conductivity, excellent cycle stabilities of the electronic double layer capacitor (EDLC) and high specific capacitance of the pseudocapacitor. Here, a core–shell structured polyaniline derived carbon nanowire@Co–Ni layered double hydroxide (PANC@Co–Ni LDH) nanomaterial was successfully synthesized via a novel facile electrodeposition–carbonization–electrodeposition route. The core-like PANC full of N atoms retains its innate long-chain structure and provides a lot of active sites for the uniform growth of the shell-like Co–Ni LDH, resulting in a cross-linked active network structure with numerous electroactive sites, abundant pores, and adequate large space and reaction interface, which contribute to the rapid diffusion and transportation of the electrolyte ions and electrons. Therefore, as-obtained PANC@Co–Ni LDH showed a high specific capacitance of 1529.52 F g−1 at 0.5 A g−1 in a three electrode system and offered outstanding rate properties with no obvious capacitance attenuation (1425.17 F g−1) when the current density increased to 10 A g−1. Moreover, an asymmetric supercapacitor using PANC@Co–Ni LDH as the positive electrode and PANC as the negative electrode was fabricated, which revealed a high specific capacitance of 214.28 F g−1 and superior energy density of 38.73 W h kg−1 with a power density of 0.92 kW kg−1, suggesting great potential in practical energy storage devices.
Introduction
In recent years, supercapacitors (SCs) as eco-friendly energy storage devices have been widely applied to electronics, mobile electrical systems, energy management, memory back-up systems, and industrial power arrays due to their advantages, such as long service life, rapid charge/discharge rate and high power density.1–4 Typical SCs usually consist of electrode materials, electrolyte, separator and current collector. Most closely related to an improvement in the electrochemical performance of SCs are the optimization and development of electrode materials, which can be divided into four categories: carbon materials,5–7 conducting polymers,8–10 metal oxides11–15 and composites. Among these, composites have attracted more attention because of the complementary advantages of various electrode materials. Carbon material/metal nanocomposites that possess the excellent cycling properties of carbon materials and the high specific capacitance of metal oxides have been widely studied as the best partners.
In the carbon material/metal system,16–18 the extremely fashionable choice of carbon materials belongs to the one-dimensional (1D) carbon nanotubes (CNTs)19 and multiwall carbon nanotubes (WMCNTs) due to their higher length–diameter ratio and better electrical conductivity in comparison with 2D graphene, carbides and nitrides (MXene)20–22etc. However, CNTs or MWCNTs are usually synthesized through a sophisticated method like chemical vapor deposition (CVD)23,24 and the obtained highly crystalline CNTs need extra treatment (like acid-oxidation) to generate some functional groups such as hydroxyl or carboxyl25 on the surface, to allow easy and efficient combination with metal oxides. Alternatively, a conducting polymer like PANI could be directly transformed to a novel kind of carbon material after a one-step direct carbonization process, which retains the original 1D nanowire structure and offers more active sites compared to CNT. Remarkably, the PANI-derived carbon (PANC) is rich in N atoms,26–29 facilitating electron conduction rate, material activity (extra pseudocapacitance) and wettability. As to transition metal oxides, Co–Ni layered double hydroxide (Co–Ni LDH)30–33 with its high specific capacitance has been demonstrated to be an outstanding PSC material for SCs because of the combined effect of binary redox states (Ni2+/Ni3+ and Co2+/Co3+ couples) and the unique layered crystal structure, which could reduce the difficulty of the electrolyte ions diffusing among electrode materials. Based on the above considerations, in this paper, we have successfully prepared a core–shell structured PANI-derived carbon/Co–Ni LDH (PANC@Co–Ni LDH) nanocomposite. The obtained electrode material showed excellent rate capability with a slight capacitance loss of 10% as the current density increased 20 fold. Moreover, in order to enlarge the voltage window and realize its practical application, an asymmetric supercapacitor (ASC) was assembled with a negative PANC electrode and a positive PANC@Co–Ni LDH electrode. The fabricated ASC devices exhibited excellent cycle stability with a capacitance retention of 84.73% even after 10
000 charge–discharge tests over a large voltage range of 0–1.4 V, providing an advanced electrode material for energy supply units.
Experimental
Materials
Carbon fiber paper (CFP) was purchased from SGL Technology Company. Sulfuric acid (98% H2SO4), aniline (99.5%), CoCl2·6H2O, Ni(NO3)2·6H2O and KOH were purchased from Sinopharm Chemical Reagents and used without further purification. The CFP was cut into 1 × 2 cm2 pieces and cleaned with acetone and deionized (DI) water several times to remove the surface oxide.
Synthesis of PAN-carbon (PANC) NWs
Typically, the PANC materials were prepared via carbonization of the electrodeposited polyaniline (PANI). The electrodeposition process was performed in a three-electrode system with 60 ml of 0.2 M H2SO4 solution and 3 ml of aniline as electrolyte, CFP as the working electrode, Pt as the counter electrode and a saturated calomel electrode (SCE) as the reference electrode. The PANI-x@CFP samples were obtained after deposition at a scan rate of 100 mV s−1 for x (x = 20, 25, 30, 35 and 40) cycles at room temperature. Then, as-prepared PANI-x@CFP were washed with DI water several times and dried at 60 °C for 12 hours. After being fully dried, PANI-x@CFP was put into a quartz tube and carbonized at 800 °C under nitrogen atmosphere for 2 h.
Synthesis of the PANC@LDH NWs
The PANC@Co–Ni LDH NWs materials were prepared by employing the electrodeposition method in the aforementioned three-electrode system. The differences are that PANC-35 materials play the role of working electrode and the electrolyte contains 50 ml of 0.15 M CoCl2·6H2O and 0.15 M Ni(NO3)2·6H2O. The electrodeposition was carried out at a constant potential of −1.0 V for 100–400 s. The final samples were denoted as PANC@LDH-T (T = 100, 200, 300, 400 s). The electrochemical synthesis process of Co–Ni LDH was divided into two steps:
(i) The reduction of NO3− on the working electrode
| NO3− + H2O + 2e− → NO2− + 2OH− | (1) |
(ii) The generated OH− leads to the coprecipitation of Co–Ni LDH on the surface of PANC
| Co2+ + Ni2+ + 4OH− → CoNi(OH)4 | (2) |
Fabrication of PANC@LDH//PANC asymmetric supercapacitors (ASC)
The ASC device was fabricated with LDH-300@PANC and PANC-35 (1 × 1 cm2, respectively) as the positive and negative electrodes, respectively, filter paper as the separator, and 6 M KOH as the electrolyte in a stainless steel CR2032 coin construction. The total active mass loading of the device is about 18.9 mg.
Materials characterization
A field emission scanning electron microscope (FESEM, Magellan 400) equipped with an energy dispersive X-ray spectrometer (SEM-EDX, Magellan 400) and transmission electron microscope (TEM, JEOL JSM-2010F) were used to characterize the morphology, microstructure and elemental compositions of the as-fabricated samples. The X-ray diffraction (XRD) was measured with a Japanese Rigaku 2550 X-ray powder diffractometer with Cu Kα radiation (λ = 1.54056 Å) operating at 40 kV and 250 mA. The surface chemical states of the samples were investigated utilizing X-ray photoelectron spectroscopy (XPS) measurement performed on a VG ESCALAB MK II electron spectrometer.
Electrochemical measurements
The electrodeposition process was finished by employing a CHI 760D electrochemical work station (CH Instruments Inc., Shanghai, China). The CV, GCD and EIS tests were carried out using an IVIUM (Netherlands) electrochemical work station at room temperature, and the cycling stability of the fabricated devices was tested by a LAND CT21001A. The EIS were investigated by applying an AC voltage with 5 mV amplitude in a frequency range from 0.01 Hz to 100 kHz at open circuit potential.
The calculations for all devices were obtained according to our previous reports.4
Results and discussion
Structure and morphology characterization
The PANC@Co–Ni LDH core–shell nanostructure was synthesized in three steps, as illustrated in Scheme 1: (i) a PANI nanowire array was deposited on a carbon fiber paper (CFP) substrate by an electrochemical polymerization method; (ii) PANI nanowires were carbonized to prepare the PAN-carbon (PANC); (iii) Co–Ni LDH directly grew on the surface of the PANC via electrodeposition. The CFP substrate was selected because of its good conduction and excellent flexibility.33 As-obtained PANC materials retain the nanowire structure of PANI perfectly and contain high levels of nitrogen/oxygen functional groups, which are beneficial for the in situ growth of Co–Ni LDH.
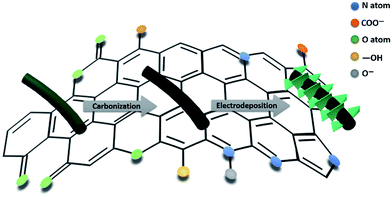 |
| Scheme 1 Schematic illustration of the synthesis of PANC and PANC@LDH nanowires. | |
X-ray diffraction pattern (XRD) measurements were conducted to characterize the crystal structure of the as-prepared hybrids (the PANC@Co–Ni LDH-300 and PANC-35 NWs), as shown in Fig. 1a. The two broad peaks located at about 23° and 43.7° for the PANC correspond to the (002) of the stacked graphene layers and (100) planes of the ordered graphitic structure. After coating with the Co–Ni LDH layer, the (003), (006), (012) and (110) planes that represent the Co–Ni LDH material were clearly observed, proving the successful growth of the LDH shell with high crystallinity on the surface of the PANC NWs.
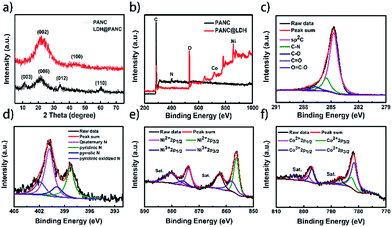 |
| Fig. 1 Structural characterization of the prepared PANC-35 and PANC@Co–Ni-300 LDH samples: (a) XRD patterns; (b) XPS survey; (c) high-resolution C 1s spectra and (d) N 1s spectra of PANC samples; (e) high-resolution Ni 2p and (f) Co 2p spectra of PANC@Co–Ni LDH materials. | |
The prepared PANC-35 and PANC@Co–Ni LDH-300 samples were then characterized by X-ray photoelectron spectroscopy (XPS). Fig. 1b shows the XPS survey of these two samples. The existence of O, C, N elements can clearly be seen in the PANC materials. The high-resolution O 1s spectra of the PANC (Fig. S1†) can be deconvoluted into 4 peaks at 530.1, 532.3, 533.1 and 534.5 eV, corresponding to O-I (carbonyl oxygen of quinones), O-II (carbonyl oxygen atoms in esters, anhydrides, and oxygen atoms in hydroxyl groups), O-III (non-carbonyl (ether-type) oxygen atoms in esters and anhydrides) and O-IV (carboxylic groups with COOH or adsorbed water and/or oxygen). Subsequently, high-resolution C 1s and N 1s spectra of PANC are presented in Fig. 1b and c, respectively. The primary peak at 284.8 eV and the weak peaks at 285.4 eV, 286.7 eV, 287.8 eV and 289.8 eV, corresponding to C
C and C–N, C–O, C
O, O
C–O bonds, can be observed. Depending on the position of the N atoms in the carbon network, the high-resolution N 1s spectrum can be classified into quaternary N (400.6 eV), pyridinic N (398.2 eV), pyrrolic N (399.7 eV) and pyridinic oxidized N (402.4 eV),34 proving that the N atom can be retained intact after carbonization of PANI. That is to say, PANC can serve as a self N-doped carbon-based material. In addition, the N, O elements on the PANC surface could enhance its wettability and conductivity in favor of the transmission of electrolyte ions and electrons. The Ni 2p spectrum (Fig. 1e) shows two kinds of nickel peaks, where the binding energies of 873.8 and 855.6 eV correspond to the Ni 2p1/2 and Ni 2p3/2 signals of (Ni2+), and peaks at 874.9 and 856.9 eV can be ascribed to Ni 2p1/2 and Ni 2p3/2 (Ni3+). The deconvoluted spectrum of Co 2p (Fig. 1f) with binding energies of 797.5 eV and 782.1 eV can be attributed to Co 2p1/2 and Co 2p3/2 (Co2+), and 795.4 and 780.5 eV can be ascribed to Co 2p1/2 and Co 2p3/2 (Co3+), suggesting the successful synthesis of Co–Ni LDH in the nanocomposites.
Fig. 2a and b show the FESEM images of PANI-35 and PANC-35. The PANI nanowires (Fig. 2a) homogeneously grow on the surface of CFP with a three-dimensional cross-linked network. It is noteworthy that after carbonization at 800 °C for 2 h, the PANC materials retain a slender interwoven nanowire morphology, which benefits rapid electron-conduction. The XRD patterns also indicate that the PANI nanowires were utterly carbonized to PANC (see Fig. S9†). Fig. S2† shows the SEM images of PANC-20, PANC-25 and PANC-30. The length of the PANC nanowires is shorter than that of PANC-35, but when the electrodeposition time was increased to 40 cycles, the length grew longer and the mass loading on the CFP increased to 7.8 mg compared to PANC-35 (Fig. S3†), when the accumulation of carbon fibers appeared, which impedes the passage of ions and reduces specific capacitance. Therefore, in the following experiments we chose PANC-35 as the template for the electrodeposited Co–Ni LDH nanosheets.
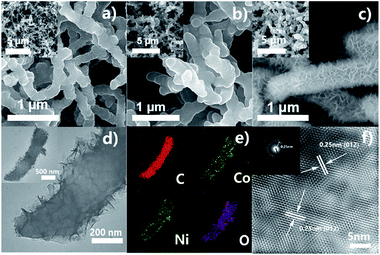 |
| Fig. 2 (a–c) FESEM images of the obtained PANI-35, PANC-35, PANC@Co–Ni LDH-300 sample; (d, e) TEM images of PANC@Co–Ni LDH with the corresponding elemental mapping images of C, Co, Ni and O elements; (f) FFT image of PANC@Co–Ni LDH-300; the inset is the SAED pattern. | |
In order to obtain the optimum electrodeposition time (T) for Co–Ni LDH, we performed a contrast test (T = 100, 200, 300, 400 s). The SEM with different T in Fig. S4† revealed that the amount of Co–Ni LDH increases as T rises; the typical nanoflakes structure of Co–Ni LDH has not universally formed under 100 s but 400 s is too long, even beginning to aggregate. Based on this, the sample PANC@Co–Ni LDH-300 was further investigated, as shown in Fig. 2c–f. Co–Ni LDH aligned vertically on the PANC, as can be found from Fig. 2c and d. The corresponding elemental mapping images of C, Co, Ni and O elements (Fig. 2e) demonstrated a well-defined core–shell structure of PANC@Co–Ni LDH. The lattice fringes of the nanoflakes exhibited an interplane spacing of 0.25 nm, corresponding to the (012) plane of Co–Ni LDH, as shown in Fig. 2f, the FFT image of the PANC@LDH sample, which is in great agreement with the XRD and XPS results (the high quality HRTEM is provided in Fig. S7†). This special core–shell structure of the PANC@Co–Ni LDH materials will reach its full potential in the good conductivity of core-like PANC and high specific capacitance of shell-like Co–Ni LDH.35,36
Electrochemical characterization of negative electrode materials
The electrochemical behavior of the PANC-x electrodes was systematically measured in a three-electrode configuration using 6 M KOH as electrolyte. Fig. 3a–c shows the cyclic voltammograms (CV), galvanostatic discharge–charge (GCD) profiles and Nyquist plots of the PANC-x. The lack of redox peaks appearing in the CV curves revealed its carbon materials based electrical double-layer capacitor (EDLC) type. The smallest closed area in the CV curves, the longest discharge time at the same current density together with the lowest Rct (resistance of charge-transfer = 1.46 Ω) of the PANC-35 sample demonstrated that 35 cycles is the optimal number of electrodeposition cycles, which is in accordance with aforementioned SEM and XRD results. The specific capacitance of PANC-x (Fig. 3d) intuitively proved the best performance by PANC-35, which shows the largest specific capacitance of 224.26 F g−1 among all the PANC-x samples (PANC-20 167.12 F g−1; PANC-25 165.18 F g−1; PANC-30 171.4 F g−1; PANC-40 178.05 F g−1), corresponding to the results of the CV measurements. The CV curves of PANC-35 at different scan rates were measured, as displayed in Fig. 3e. The rectangular shapes of the CV curves of the PANC-35 electrode were still retained at scan rates varying from 5 to 100 mV s−1, demonstrating its excellent rate properties. From the GCD curves of PANC-35 at different current densities (Fig. 3d), we can see that there is no obvious voltage drop even at a high current of 10 A g−1, which means there is little equivalent series resistance. The calculated specific capacitance based on the GCD curves showed an excellent capacitance retention of 74.1% when current densities improved 20 fold. The comparison of the specific capacitance of various N-doped carbon materials in the three-electrode system revealed the high capacitance of the PANC-35 samples, as shown in Table S1.† The excellent electrochemical properties of PANC-35 are mainly attributed to its unique porous nanostructures and self N-doped carbon component. More specifically: (1) the opening hierarchical porous nanowires could stimulate ions in electrolyte transport over the entire surface of the PANC. (2) The PANC nanowires as a self N-doped carbonaceous supported skeleton with outstanding electrical conductivity, facilitate electron transport and could enhance its rate performance. (3) The self N-doped carbon could ameliorate the wettability and electrochemical activity, resulting in further improvement in the specific capacitance.4,38
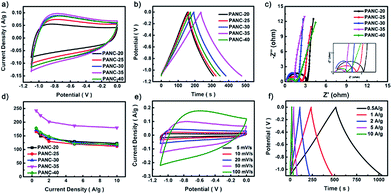 |
| Fig. 3 (a) CV curves of the various PANC-x at a scan rate of 50 mV s−1; (b) GCD curves of the various PANC-x at a current density of 1 A g−1; (c) Nyquist plots of PANC-x. Inset is the magnification of Warburg semicircles from the spectra; (d) the specific capacitance of the PANC-x at different current densities; (e) CV curves of the PANC-35 at various scan rates; (f) GCD curves of the PANC-35 at different current densities. | |
PANC@LDH: positive electrode material
To determine the most effective electrodeposition time (T) for Co–Ni LDH-T, a series of comparison experiments were carried out first, as shown in Fig. 4a–d. The CV curves of the LDH@CFP showed a pair of strong redox peaks, indicating that the capacitance characteristics are mainly provided by faradaic redox reactions. Fig. 4b displays the CV curves of the PANC@LDH-T (T = 100, 200, 300 and 400 s) in 6 M KOH aqueous at a scan rate of 4 mV s−1. It is obvious that shell-like Co–Ni LDH-300 coated PANC NWs reached a maximum closed area compared to the others, which is also demonstrated by the longest charge time and the highest specific capacitance of 1529.52 F g−1 (Fig. 4c and d). That the capacitance decreased significantly when the deposition time rose to 400 s might be explained by the excessive deposition of LDH, the reduction of the electrochemical activity and unaccomplished redox reaction of Co–Ni LDH. The final mass loading of the PANC@LDH-300 hybrid electrode was found by weighing to be 13.4 mg (Fig. S6†).
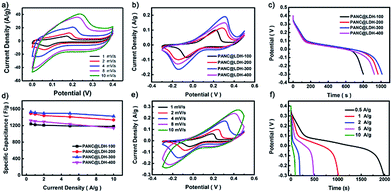 |
| Fig. 4 (a) CV curves of the LDH@CFP (b) CV curves of the PANC@LDH-T (T = 100, 200, 300 and 400 s) at a scan rate of 4 mV s−1; (c) GCD curves and the specific capacitance of the PANC@LDH-T at different current densities; (d) The rate capability of PANC@LDH-T; (e) CV curves of the PANC@LDH-300 at various scan rates; (f) GCD curves of the PANC@LDH-300 at different current densities. | |
Fig. 4e shows the CV curves of the PANC@LDH-300 at different scan rates varying from 1 to 10 mV s−1. Obvious redox peaks were observed from the CV curves. However, when the scan rate increased from 1 to 10 mV s−1, the redox peaks shifted gradually and got less distinct due to the fast-insufficient redox reactions and the polarization effect of the PANC@LDH-300 electrode. Fig. 4f displays the corresponding GCD profiles of various PANC@LDH-T samples in a potential window ranging from −0.3 to 0.4 V. The platforms confirmed the redox process. On the basis of the GCD curves, the specific capacitance of the electrode was calculated and a capacitance retention of 93.17% was obtained, suggesting the excellent rate performance of the PANC@Co–Ni LDH-300 electrode. Table S2† shows the electrochemical performance comparison of LDH-300@PANC with the LDHs in previous reports, which reveals that the PANC@Co–Ni LDH-300 is also a competitive electrode material for SCs. These excellent performances of the PANC@Co–Ni LDH-300 electrode can be accounted for by the following reasons. Firstly, the self N-doped PANC NWs with good wettability and conductivity enables the Co–Ni LDH nanoflakes to be deposited and the Co–Ni LDH to have a large open surface, which could improve the utilization efficiency of the electrode. Secondly, the core–shell structure of PANC@Co–Ni LDH shortens the electron transport distance and reduces the charge transfer resistance.34,37,39 Thirdly, the good interfacial contact between the Co–Ni LDH and PANC NWs greatly lowers the internal resistance of the electrode.18
LDH@PANC//PANC: asymmetric supercapacitor device
To evaluate the practical application of the synthesized electrode materials, an ASC was fabricated using PANC@Co–Ni LDH-300 as the positive electrode and PANC-35 as the negative electrode. Fig. 5a and b depict the CV and GCD curves of the fabricated devices, which realize the improvement in the potential windows. Fig. 5c presents its CV curves at various scan rates from 5 to 50 mV s−1 under a wide potential window of 0–1.4 V. It can be seen that the CV curves have a similar rectangular shape with no obvious redox peaks as the scan rate increases, which indicates a quick I–V response and high reversible energy storage ability. The specific capacitance of the ASC device calculated with the GCD curves (Fig. 5d), are 214.28 F g−1, 200.83 F g−1, 178.98 F g−1 and 152.36 F g−1, corresponding to current densities of 2, 4, 6, 8 A g−1. The relatively higher specific capacitance can be proved from Table S3.† The cyclic performance is also an important factor for evaluating SCs; therefore, the long-term cyclic stabilities of the as-assembled ASC were tested at a current density of 2 A g−1 for 10
000 cycles, as shown in Fig. 5e. Almost 84.73% (211.25 F g−1) of the initial capacitance (249.23 F g−1) was retained after 10
000 cycles, showing outstanding cycle properties. The maximum energy density and power density of the ASC device were calculated as 38.73 W h kg−1 (0.92 kW kg−1) and 4.2 kW kg−1 (14.01 W h kg−1), which are much higher than those of traditional AC//AC SCs (∼10 W h kg−1) and previously reported ASC devices listed in Table S3.† As a visualized demonstration for practical application, a red light-emitting diode (LED) was easily lit by two ASCs connected in series for about 10 minutes (the inset of Fig. 5f), confirming that our devices can be used for portable energy storage.
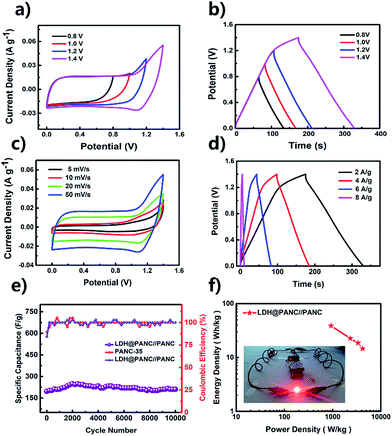 |
| Fig. 5 (a) CV curves and (b) GCD curves of the PANC@LDH//PANC ASC with different working voltage windows; (c, d) CV and GCD curves of the fabricated ASC devices; (e) cycling stability of PANC@LDH//PANC ASC at a current density of 2 A g−1 and corresponding coulombic efficiency; (f) Ragone plots of the PANC@LDH//PANC ASC; the inset is the photographs of the LED indicator powered by two tandem connected ASC devices. | |
Conclusions
In summary, a novel core–shell PANC@Co–Ni LDH electrode material was successfully synthesized by a facile electrochemical deposition and carbonization method. Owing to the good conductivity of the self N-doped PANC structures and high theoretical specific capacitance of the Co–Ni LDH nanoflakes, the fabricated PANC@Co–Ni LDH//PANC ASC delivered a high specific capacitance of 214.28 F g−1 with a wide potential window of 1.4 V, excellent cycling stability with 85.17% of the initial capacitance attenuation after 10
000 cycles and a high energy density of 38.73 W h kg−1 at a power density of 0.92 kW kg−1. Such good results provide a powerful candidate for advanced electrode materials.
Conflicts of interest
There are no conflicts to declare.
Acknowledgements
The authors sincerely acknowledge financial support from National Natural Science Foundation of China (NSFC Grant No. 21571080) and Natural Science Foundation of Jilin province (No. 20170101193JC).
Notes and references
- L. Li, Z. Lou, D. Chen, K. Jiang, W. Han and G. Shen, Small, 2017, 2829 Search PubMed.
- W. Li, D. Chen, Z. Li, Y. Shi, Y. Wan, J. Huang, J. Yang, D. Zhao and Z. Jiang, Electrochem. Commun., 2007, 9, 569–573 CrossRef CAS.
- M. R. Lukatskaya, B. Dunn and Y. Gogotsi, Nat. Commun., 2016, 7, 12647 CrossRef PubMed.
- Y. Xi, G. Wei, J. Li, X. Liu, M. Pang, Y. Yang, Y. Ji, V. Y. Izotov, Q. Guo and W. Han, Electrochim. Acta, 2017, 233, 26–35 CrossRef CAS.
- S. Zhong, C. Zhan and D. Cao, Carbon, 2015, 85, 51–59 CrossRef CAS.
- D. Pech, M. Brunet, H. Durou, P. Huang, V. Mochalin, Y. Gogotsi, P. L. Taberna and P. Simon, Nat. Nanotechnol., 2010, 5, 651–654 CrossRef CAS PubMed.
- Y. Gogotsi, A. Nikitin, H. Ye, W. Zhou, J. E. Fischer, B. Yi, H. C. Foley and M. W. Barsoum, Nat. Mater., 2003, 2, 591–594 CrossRef CAS PubMed.
- M. Liu, B. Li, H. Zhou, C. Chen, Y. Liu and T. Liu, Chem. Commun., 2017, 53, 2810–2813 RSC.
- M. Kim, C. Lee and J. Jang, Adv. Funct. Mater., 2014, 24, 2489–2499 CrossRef CAS.
- Y. Gawli, A. Banerjee, D. Dhakras, M. Deo, D. Bulani, P. Wadgaonkar, M. Shelke and S. Ogale, Sci. Rep., 2016, 6, 21002 CrossRef CAS PubMed.
- X. Xiao, H. Song, S. Lin, Y. Zhou, X. Zhan, Z. Hu, Q. Zhang, J. Sun, B. Yang, T. Li, L. Jiao, J. Zhou, J. Tang and Y. Gogotsi, Nat. Commun., 2016, 7, 11296 CrossRef CAS PubMed.
- M. A. Garakani, S. Abouali, Z.-L. Xu, J. Huang, J.-Q. Huang and J.-K. Kim, J. Mater. Chem. A, 2017, 5, 3547–3557 CAS.
- Z. Gu and X. Zhang, J. Mater. Chem. A, 2016, 4, 8249–8254 CAS.
- Z. Gu, H. Nan, B. Geng and X. Zhang, J. Mater. Chem. A, 2015, 3, 12069–12075 CAS.
- Y. Qian, R. Liu, Q. Wang, J. Xu, D. Chen and G. Shen, J. Mater. Chem. A, 2014, 2, 10917–10922 CAS.
- R. R. Salunkhe, K. Jang, S.-w. Lee, S. Yu and H. Ahn, J. Mater. Chem., 2012, 22, 21630 RSC.
- Z. Tang, C.-h. Tang and H. Gong, Adv. Funct. Mater., 2012, 22, 1272–1278 CrossRef CAS.
- X. Li, J. Shen, W. Sun, X. Hong, R. Wang, X. Zhao and X. Yan, J. Mater. Chem. A, 2015, 3, 13244–13253 CAS.
- S. Zeng, H. Chen, F. Cai, Y. Kang, M. Chen and Q. Li, J. Mater. Chem. A, 2015, 3, 23864–23870 CAS.
- O. Mashtalir, M. Naguib, V. N. Mochalin, Y. Dall'Agnese, M. Heon, M. W. Barsoum and Y. Gogotsi, Nat. Commun., 2013, 4, 1716 CrossRef PubMed.
- S. Xu, G. Wei, J. Li, W. Han and Y. Gogotsi, J. Mater. Chem. A, 2017, 5, 17442–17451 CAS.
- S. Xu, G. Wei, J. Li, Y. Ji, N. Klyui, V. Izotov and W. Han, Chem. Eng. J., 2017, 317, 1026–1036 CrossRef CAS.
- P. Singh and K. Pal, Electrochim. Acta, 2017, 242, 47–55 CrossRef CAS.
- Z. Zhang, L. Wang, Y. Li, Y. Wang, J. Zhang, G. Guan, Z. Pan, G. Zheng and H. Peng, Adv. Energy Mater., 2017, 7, 1601814 CrossRef.
- M. Radoičić, G. Ćirić-Marjanović, V. Spasojević, P. Ahrenkiel, M. Mitrić, T. Novaković and Z. Šaponjić, Appl. Catal., B, 2017, 213, 155–166 CrossRef.
- K. Kan, L. Wang, P. Yu, B. Jiang, K. Shi and H. Fu, Nanoscale, 2016, 8, 10166–10176 RSC.
- J. J. Langer and S. Golczak, Polym. Degrad. Stab., 2007, 92, 330–334 CrossRef CAS.
- D.-s. Yuan, T.-x. Zhou, S.-l. Zhou, W.-j. Zou, S.-s. Mo and N.-n. Xia, Electrochem. Commun., 2011, 13, 242–246 CrossRef CAS.
- P. Hasin, V. Amornkitbamrung and N. Chanlek, J. Catal., 2017, 351, 19–32 CrossRef CAS.
- D. Du, X. Wu, S. Li, Y. Zhang, W. Xing, L. Li, Q. Xue, P. Bai and Z. Yan, J. Mater. Chem. A, 2017, 5, 8964–8971 CAS.
- Y. Chen, W. K. Pang, H. Bai, T. Zhou, Y. Liu, S. Li and Z. Guo, Nano Lett., 2017, 17, 429–436 CrossRef CAS PubMed.
- S. Liu, S. C. Lee, U. Patil, I. Shackery, S. Kang, K. Zhang, J. H. Park, K. Y. Chung and S. Chan Jun, J. Mater. Chem. A, 2017, 5, 1043–1049 CAS.
- Z. Yin, Y. Bu, J. Ren, S. Chen, D. Zhao, Y. Zou, S. Shen and D. Yang, Chem. Eng. J., 2018, 03, 100 Search PubMed.
- W. H. Choi, M. J. Choi and J. H. Bang, ACS Appl. Mater. Interfaces, 2015, 7, 19370–19381 CAS.
- L. Zhang, T. You, T. Zhou, X. Zhou and F. Xu, ACS Appl. Mater. Interfaces, 2016, 8, 13918–13925 CAS.
- Y. Zhu, J. Ren, X. Yang, G. Chang, Y. Bu, G. Wei, W. Han and D. Yang, J. Mater. Chem. A, 2017, 5, 9952–9959 CAS.
- X. Wang, S. Chen, D. Li, S. Sun, Z. Peng, S. Komarneni and D. Yang, ACS Sustainable
Chem. Eng., 2018, 6, 633 CAS.
- J. Cui, Y. Xi, S. Chen, D. Li, X. She, J. Sun, W. Han, D. Yang and S. Guo, Adv. Funct. Mater., 2016, 26, 8487–8495 CrossRef CAS.
- M. Shao, Z. Li, R. Zhang, F. Ning, M. Wei, D. G. Evans and X. Duan, Small, 2015, 11, 3530–3538 CrossRef CAS PubMed.
Footnote |
† Electronic supplementary information (ESI) available. See DOI: 10.1039/c8se00123e |
|
This journal is © The Royal Society of Chemistry 2018 |
Click here to see how this site uses Cookies. View our privacy policy here.