A self-cooling and flame-retardant electrolyte for safer lithium ion batteries†
Received
7th March 2018
, Accepted 12th April 2018
First published on 12th April 2018
Abstract
The rational design of flame-retardant electrolytes is essential for improving the safety of lithium ion batteries. Cooling is the key to curbing thermal runaway and compatibility is the basis to ensure electrochemical performance. Here we design a composite electrolyte with a double safety protection mechanism with self-cooling and flame-retardant effects simultaneously. N,N-Dimethylacetamide (DMAC) as a Lewis base can improve the thermal stability and perfluoro-2-methyl-3-pentanone (PFMP) with a self-cooling function can act as an internal micro-fire-extinguisher. Acceptable electrochemical performance is ensured via the introduction of a fluorocarbon surfactant (FS) that can improve the interface compatibility. This composite electrolyte is a good alternative for lithium ion batteries as it presents beneficial properties both in electrochemical performance and thermal stability.
1. Introduction
Since the commercialization of the lithium ion battery, it has been an indispensable part of portable electronics.1 With the further development of the electric vehicle industry and the upgrade of energy storage equipment, power batteries with a high energy density are gradually being promoted. However, the safety issue has always been prominent and has not yet been well resolved.2–4 Explosion accidents related to lithium ion batteries used in mobile phones and electric vehicles have caused widespread controversy in recent years. Improving the safety of lithium ion batteries is a basic guarantee to ensure their long-term and extensive application.3,5
The safety problem of lithium ion batteries is generally considered to be closely related to the electrolyte. The commercial electrolyte is a nonaqueous system consisting of lithium hexafluorophosphate (LiPF6) and organic solvents such as ethylene carbonate (EC), propylene carbonate (PC), dimethyl carbonate (DMC) and their mixtures.6–8 This LiPF6-based electrolyte provides an appropriate dielectric constant, viscosity and conductivity to support normal electrochemical performance. However, it is also extremely flammable, especially under abuse conditions including overcharging, short-circuiting, extrusion and high temperatures.9 Thermal decomposition of lithium ion batteries can occur beyond 69 °C when triggered by damage to the solid electrolyte interface (SEI) film and the electrolyte.10,11 The exposed lithium will further react with the electrolyte and the decomposition of the cathode material will release oxygen.12 Commercial batteries use protective devices such as safety valves but the effect is limited and the intrinsic safety problem has not yet been solved. Thus, the development of a non-flammable electrolyte is the ultimate means to improve the safety of lithium ion batteries.13
Over the years, many researchers have carried out countless related studies on the thermal decomposition mechanism of the electrolyte and how to reduce its flammability. Comprehensive results have shown that the thermal decomposition of LiPF6 is the main cause of the thermal instability.14,15 The produced PF5 is a strong Lewis acid that will react with trace amounts of water and organic solvents, accompanied by the release of flammable free radicals and HF (Fig. 1). These self-accelerating thermal decomposition reactions are irreversible and easily cause thermal runaway if the heat cannot be effectively evacuated in time. It is necessary to reduce the flash point of the electrolyte and reduce the reactivity of the lithium salt.16 Electrolyte additives including phosphorus compounds,17 succinonitrile18 and fluoride19 have been widely studied, and the thermal stability of the electrolyte has been improved. However, single flame-retardant additives always have to face the problem of how to simultaneously improve flame-retardant efficiency and ensure electrochemical performance.13 Besides, complete non-combustibility often requires greater amounts of flame-retardant additive, and this high content will cause great changes in the physical properties of the electrolyte and thus affect its compatibility.20
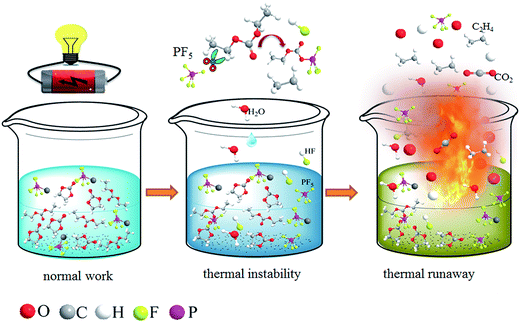 |
| Fig. 1 Schematic of the thermal runaway process of the lithium ion battery electrolyte. A battery under normal work conditions consists of organic solvents and lithium salt. Water and heat cause the thermal decomposition of LiPF6, the produced Lewis acid PF5 attacks the solvent molecules, and the combustion of large amounts of active free radicals leads to thermal runaway. | |
In this study, we proposed a composite electrolyte additive including perfluoro-2-methyl-3-pentanone (PFMP), N,N-dimethylacetamide (DAMC) and a fluorocarbon surfactant (FS). This design is based on a synergistic concept21 to combine the advantages of various types of flame-retardant material to allow for a lower amount to be used. We established a double protection mechanism for battery safety using DMAC as a Lewis base22 and PFMP for its self-cooling function. This aims to improve the thermal stability of the electrolyte and promptly extinguish fires when thermal runaway occurs. The total heat generation of the standard electrolyte (1.0 M LiPF6/EC + DEC (1
:
1 wt)) is reduced by 88.25% with the optimized electrolyte additive amounts. We mainly investigated the electrochemical properties of LiNi1/3Co1/3Mn1/3O2 (NCM) and a graphite material, and the introduction of a FS improved the interface compatibility. We demonstrated that this composite electrolyte for lithium ion batteries displayed high safety and an acceptable electrochemical performance.
2. Materials and method
2.1 Preparation of the composite electrolyte
The commercial electrolyte (1.0 M LiPF6/EC + DEC (1
:
1 wt), Guotai-Huarong New Chemical Materials Co.) was used as a standard electrolyte. Different amounts of PFMP (C6F12O, Minnesota Mining and Manufacturing Co., 99%), DMAC (C4H9NO, Aladdin, 99.9%) and a FS (F(CF2)6CH2CH2O(CH2CH2O)y (y = 5–14), DuPont Co., 99%) were added into the standard electrolyte to obtain a series of composite electrolytes. All operations were carried out under an argon atmosphere in a glove box (O2 and H2O < 1 ppm).
2.2 Combustion test of the electrolyte
Combustion tests were conducted to confirm the self-extinguishing effect of PFMP. PFMP will vaporize at 49 °C when an igniter is near to the electrolyte. The electrolyte was firstly ignited and then different amounts of PFMP were added to it and the combustion of the electrolyte was observed. PFMP in 2.5–10 vol% proportions was added externally to the composite electrolyte that already contained DMAC.
2.3 Electrochemical characterization
Artificial graphite, LiFePO4 (LFP) (ShenZhen BTR New Energy Materials Co. Ltd) and Li(Ni1/3Co1/3Mn1/3)O2 (NCM) (Hefei Guoxuan High-Tech Power Energy Co. Ltd) were selected to be further mixed with acetylene black and polyvinylidene fluoride (PVDF) at a frequently used ratio of 8
:
1
:
1 (wt%). The electrodes were dried for 10 h at 75 °C and punched into circular disks of 100 μm thickness and 14 mm diameter. CR2032 coin cells with different composite electrolytes were encapsulated in an argon-filled glove box for further testing. To study the influence of the composite electrolyte on cycle performance, a galvanostatic charge and discharge examination at 0.2C was conducted on NCM/Li and Li/C cells using a multichannel battery cycler (Neware BTS). The voltage range was set to 2.0–4.2 V and 2.0–0.01 V for the NCM/Li and Li/C cells, respectively. For the cycle test of the LFP/Li cells, the voltage range was set to 2.5–3.7 V. A CHI 604A electrochemical workstation was used to evaluate the AC impedance and electrochemical stability window of the electrolyte. Linear sweep voltammetry (LSV) was carried out on a three-electrode cell with a scan rate of 1 mV s−1. Stainless steel was used as the working electrode and lithium foil was used as the reference and counter electrodes. The AC impedance test was carried out with a voltage amplitude of 5 mV, and a frequency range from 1 MHz to 0.01 Hz. The ionic conductivity of the composite electrolyte was tested using a Model DDS-307A conductivity meter at room temperature.
The morphology of the electrolyte material after the cycle test was observed using a scanning electron microscope (SEM, FEI Sirion200). The obtained electrode was rinsed with DMC three times and dried overnight to ensure there were no impurities in the sample. The composition analysis of the graphite anode surface cycled in different electrolytes was obtained using XPS (ESCALAB 250, Thermo-VG Scientific) with a radiation source of Al Kα.
2.4 Thermal stability test
The thermal stabilities of the composite electrolyte and composite electrolyte/electrode coexisting system were measured using a C80 micro-calorimeter at 0.2 °C min−1 with the reaction vessel filled with argon from 30 °C to 300 °C. Before the thermal stability test, the NCM/composite electrolyte/Li cells were pre-cycled twice between 2.0 and 4.2 V at 0.2 C, and were finally charged to 4.2 V. The Li/composite electrolyte/C cells were pre-cycled twice between 0.01 and 2.0 V at 0.2 C, and then discharged to 0.01 V. Next, disassembly was executed to obtain electrode materials that would avoid short-circuiting. The obtained electrode materials needed to be rinsed with volatile DMC to remove the residual electrolyte. For the thermal stability test, the quality of the different electrolytes involved in the test was essentially equal, and the mass ratio of the electrode/electrolyte coexisting sample was 1
:
1.3 (wt%). For the full cell thermal analysis test, the NCM/C full cell was also pre-cycled twice between 2.0 and 4.2 V at 0.2 C, and was finally charged to 4.2 V. The electrodes were wrapped in a separator to prevent electric leakage.
3. Results and discussion
3.1 A double safety protection mechanism with self-cooling and flame-retardant effects
For a normal lithium ion battery with a LiPF6-based organic electrolyte, the internal thermal decomposition reactions mainly involve the SEI film, the reaction of lithium with the electrolyte, the electrode materials and their mixtures.23–26 The thermal decomposition of the electrolyte is closely related to each part and the heat generation of the cathode rises rapidly in the presence of the electrolyte, and this is the source of most of the heat generation during thermal runaway. Experiments have shown that the production of PF5 from LiPF6 is the main cause of the thermal instability of the electrolyte.14–16,27 The thermal stability of the standard electrolyte (1.0 M LiPF6/EC + DEC (1
:
1 wt)), FS and LiPF6 was tested using a C80 micro-calorimeter under an argon atmosphere and the results are shown in Fig. 2a. The FS has a good thermal stability and no obvious strong exothermic processes. The thermal decomposition reaction of the standard electrolyte starts at 175 °C. The first peak is an endothermic process, and this is followed by a broad exothermic peak. The total heat generation of the standard electrolyte under an argon atmosphere is −251.70 J g−1. From the test results for LiPF6, it can be seen that the melting temperature of LiPF6 is 157.39 °C and that this is then followed by a thermal decomposition reaction to produce PF5. This is very consistent with the first decomposition process of the standard electrolyte. This verifies that the thermal decomposition of the electrolyte is caused by the decomposition product of LiPF6. The produced PF5 is a strong Lewis acid that has a high reactivity with organic solvents, and the produced HF will corrode the electrode.16,28 Thus, we tried to reduce the reactivity of the lithium salt to improve the safety of the electrolyte. The nitrogen-containing flame-retardant additive (DMAC) was introduced as it is likely to attack LiPF6 to form an acid–base complex.29,30 This is beneficial for inhibiting the decomposition of the electrolyte and for stabilizing the electrode.31 As shown in Fig. 2b, DMAC is very stable and the endothermic process seen is its vaporization. By exposing the standard electrolyte with and without DMAC to air atmosphere for 20 days at room temperature, it can be seen that the color of the standard electrolyte without DMAC is deeper. Thus DMAC suppresses the decomposition of the electrolyte to improve its stability. However, it is difficult to realize a completely non-flammable material by relying on only a small amount (5 vol%, Fig. 2d), while a high concentration may reduce the electrochemical performance. Li et al.30 proposed that more electrolyte decomposition products are observed on electrodes with 10% DMAC addition. Thus, we further selected PFMP32 as an efficient fire extinguishing agent to try to cool the battery system when thermal runaway occurs. The thermal stability test results of PFMP are shown in Fig. 2c. There is an obvious vaporization endothermic process of PFMP, and the introduction of PFMP will not influence the thermal decomposition of LiPF6 (Fig. S1 in the ESI†). When PFMP is added to the burning electrolyte, the flame can be extinguished immediately (Fig. 2d). This direct way to introduce a fire extinguishing agent into the electrolyte can extinguish the flame in time to avoid further spreading.
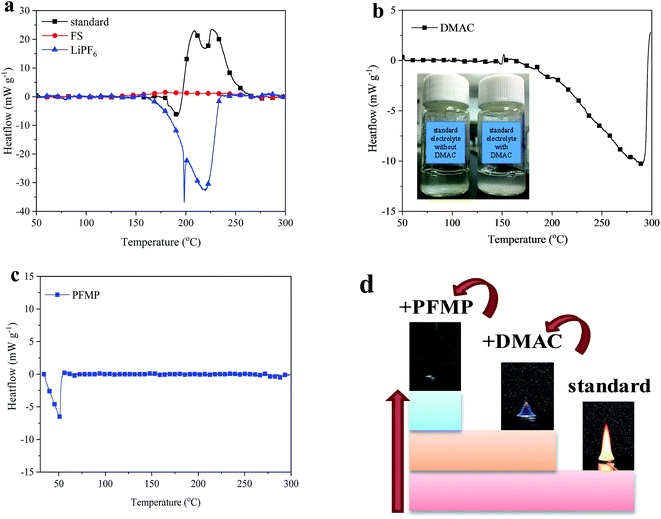 |
| Fig. 2 Thermal stability of (a) the standard electrolyte, a FS and LiPF6, (b) DMAC (the inset shows the standard electrolyte with or without DMAC after exposing to air for 20 days) and (c) PFMP. (d) The combustion test of the electrolyte with different additives. | |
Considering the high fluorine content of PFMP, it should also be a good choice as an electrolyte additive because the film forming effect of the fluorine element can improve electrochemical performance.33,34 However, PFMP is not miscible with the conventional electrolyte, a better infiltration is necessary to improve the compatibility of the additives and matrix (Fig. S2 in the ESI†). Thus, we also introduced a fluorocarbon surfactant to make the composite electrolyte system more homogeneous. This fluorocarbon surfactant is conducive to improving the interface compatibility to improve electrochemical performance (Fig. S3 in the ESI†). Thus, we initially established a kind of composite electrolyte with self-cooling and flame-retardant effects based on the above discussion. The preparation of the composite electrolyte and the double safety protection mechanism are shown in Fig. 3. DMAC reduces the attack ability of Lewis acid to provide the first type of protection. If thermal runaway occurs, PFMP will act as a cooling and extinguishing agent to achieve the second type of protection. This design minimizes the amount of flame-retardant material used and provides effective protection.
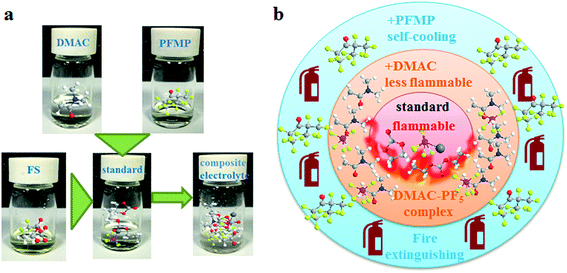 |
| Fig. 3 Schematic of the composition (a) and the double safety protection mechanism (b) of the composite electrolyte including PFMP, DAMC and a FS. A commercial electrolyte (1.0 M LiPF6/EC + DEC (1 : 1 wt)) was used as the standard electrolyte. | |
3.2 Electrochemical performance of the composite electrolyte
An acceptable electrolyte flame-retardant additive must ensure the electrochemical performance, primarily. The electrochemical window of the electrolyte was firstly tested. The linear sweep voltammetry (LSV) results (Fig. S4 in the ESI†) show that the composite electrolyte additive was stable before 4.0 V. The main electrolyte decomposition reaction occurs after 4.8 V. The oxidation current around 4.2 V comes from the oxidation of the composite additives. Dong et al. studied an electrolyte additive as a film forming additive for LiNi0.5Co0.2Mn0.3O2 cathode materials with an oxidation potential of around 4.0 V to improve cycle performance.35 The compatibility varies with different electrolyte materials.36 In order to determine the appropriate amounts of additive to use for better electrochemical and thermal stability performance, we compared several kinds of composite electrolyte with different PFMP amounts (Table 1). The amount of DMAC was fixed at 5 vol% without further discussion based on previous research.37
Table 1 Composite electrolyte (CE): composition and ionic conductivity
Sample |
Concentration (vol%) |
Ionic conductivity (S cm−1) |
PFMP |
DMAC |
FS |
Standard |
0 |
0 |
0 |
7.56 |
CE-1 |
2.5 |
5 |
2.5 |
8.05 |
CE-2 |
5 |
5 |
2.5 |
8.13 |
CE-3 |
10 |
5 |
2.5 |
7.96 |
CE-4 |
15 |
5 |
2.5 |
8.17 |
As shown in Fig. 4 and S5,† the cycle performance of the Li/C half cells with the composite electrolyte is different with an increasing amount of PFMP. When the amount of PFMP reaches 15 vol%, there is a significant decline in capacity (Fig. 4a). This should be closely related to the increased impedance of CE-4 that is shown in Fig. 4c. A higher amount of PFMP will affect the interface compatibility between the electrolyte and electrode and this is limited by the dispersibility and infiltration of PFMP. Meanwhile a better cycle performance was obtained with 2.5–10 vol% PFMP, and the impedance test results were very consistent with the results of the cycle performance. An appropriate PFMP amount brings about an increase in ionic conductivity (Table 1) with the low viscosity of PFMP and the reduced impedance. For NCM as the cathode material, the same test was conducted, and the related results are presented in Fig. 4b and d. It can be seen that the compatibility of the composite electrolyte with the NCM material is not as good as the compatibility with the graphite anode. Capacity decay and increased impedance can be observed for the different composite electrolytes. The test results of the NCM material further demonstrated that the increased impedance led to a degradation of the cycle performance. As shown in Fig. S4,† there is an oxidation current for the composite electrolyte between 4.0 and 4.2 V that is included in the electrochemical window of the NCM material. So, to further discuss the influence of this oxidation current, another cathode material LiFePO4 (LFP) was used to conduct the cycle test. The working voltage of LFP is 2.5–3.7 V and this does not include the first oxidation voltage (4.0 V) of the composite electrolyte. It can be seen that a capacity decay also appears for LiFePO4 materials with the CE-3 composite electrolyte. Thus, the capacity decay should be caused by the increased impedance. As shown in Fig. S6,† the initial charge and discharge efficiency of the graphite anode in the standard and CE-3 composite electrolytes is 59.95% and 72.43%, respectively. The initial reversible capacity is 325 and 367 mA h g−1, correspondingly. For the NCM material, the initial charge and discharge efficiency is also improved from 70.72% to 86.26%, but the capacity decay increases with the CE-3 electrolyte. The better electrochemical performance of the anode materials with the composite electrolytes is also likely related to the changes of the SEI film on the anode and the film forming effect33,34 of the fluorine element. This can be proven by looking at the scanning electron microscopy (SEM) and X-ray photoelectron spectroscopy (XPS) results. After the room temperature cycle test, the Li/C half cells with the composite electrolyte (CE-3) and standard electrolyte were disassembled separately to obtain the graphite anode for SEM and XPS (Fig. 5). By looking at Fig. 5b, it can be seen that the surface morphology of the graphite material with the standard and composite electrolytes was different. The surface of the graphite material cycled in the composite electrolyte was smoother and without deposition products of side reactions. Furthermore, an XPS survey (Fig. 5a) was conducted. The results show that both of the samples contained the same constituent elements. Previous studies have shown that the SEI components mainly include (CH2OCO2Li)2, ROCO2Li, Li2CO3, LiF and so on.38 Our test results are consistent, but it is notable that the intensity of the fluorine and oxygen elements of the two samples is very different. More of the fluorine element and less of the oxygen element were observed for the graphite sample cycled in the composite electrolyte, and this indicates that the composition of the SEI film had indeed changed. The relative atomic percentages of the graphite anode cycled in the standard and composite (CE-3) electrolytes are tabulated in Table S1.† Fluorine reagents are involved in the formation of the SEI film, and the types and amounts of the fluorine-containing chemical groups and alkyl lithium carbonate salts (Fig. 5c–f) may cause a better cycle performance and different surface morphology. The cycle performance of the full cell (NCM/C) with the standard and CE-3 composite electrolytes is shown in Fig. S7.† 85% of the capacity of the full cell with the standard electrolyte can be achieved with the CE-3 composite electrolyte.
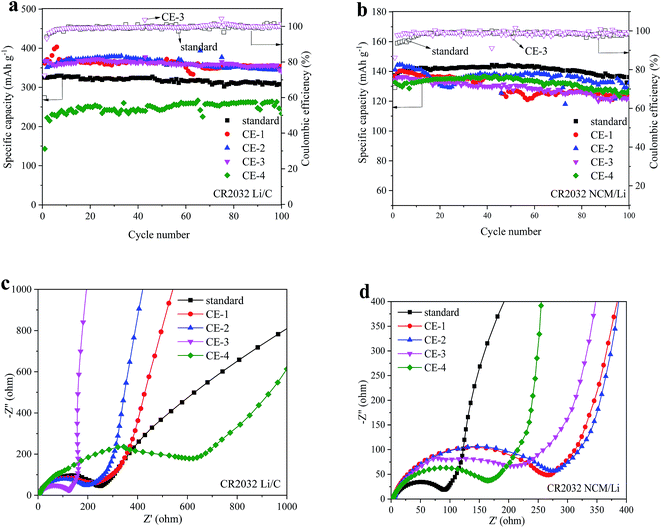 |
| Fig. 4 Cycle performance of the Li/C and NCM/Li half cells with the standard and composite electrolytes at 0.2C (a and b). The AC impedances of the Li/C and NCM/Li half cells with the standard and composite electrolytes (c and d). | |
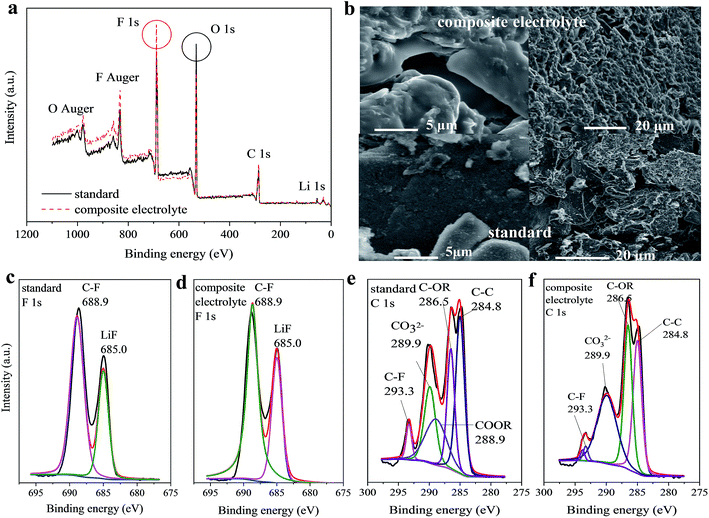 |
| Fig. 5 XPS survey (a) and SEM pictures (b) of the graphite anode surface cycled in the standard and composite (CE-3) electrolytes . High-resolution XPS analysis of graphite with the standard electrolyte (c and e) and composite electrolyte (d and f). The spectra of F1s and C1s are presented with peak deconvolution. | |
3.3 Thermal stability of the composite electrolyte
Based on the above discussion, the use of PFMP should be less than 15 vol% to ensure the electrochemical performance. More importantly, a detailed comparison between the composite electrolyte and the standard electrolyte in terms of the thermal stability is shown in Fig. 6a and Table S2† to illustrate the improved safety. The C80 test results show that the composite electrolyte exhibits an extremely high thermal stability. The standard electrolyte has a wide exothermic peak after 200 °C, while the heat flow curves of the composite electrolytes are quite different. Since PFMP has a boiling point of 49 °C, the composite electrolyte has an endothermic peak in the lower temperature stage, which is the self-cooling effect. As the temperature increases, an endothermic process occurs at 167 °C for the composite electrolyte (CE-3) with a heat absorption of 72.90 J g−1, which is larger than the standard electrolyte that has a value of 20.55 J g−1. When the temperature increases to 230 °C, there is an exothermic phenomenon for the CE-3 composite electrolyte with a heat generation of only −102.47 J g−1, while the standard electrolyte releases more heat at 196 °C with a heat generation of −272.25 J g−1. The total reaction heat of the CE-3 composite electrolyte is −29.57 J g−1, which is only 12% of the value for the standard electrolyte. The delayed exothermic process and reduced heat generation demonstrate that a better thermal stability can be obtained with PFMP and DMAC. In addition, the CE-2 composite electrolyte has a larger heat generation of −160.90 J g−1 than that of CE-3. Furthermore, for the standard electrolyte with 2.5% FS and 10% PFMP, the heat generation also decreased compared with that of the standard electrolyte (Fig. S8 in the ESI†). This proves that PFMP also has a fire retardation effect as well as a self-cooling effect. Therefore, in order to maximize the protection effect of PFMP and ensure the electrochemical performance, the CE-3 composite electrolyte should be the suitable choice.
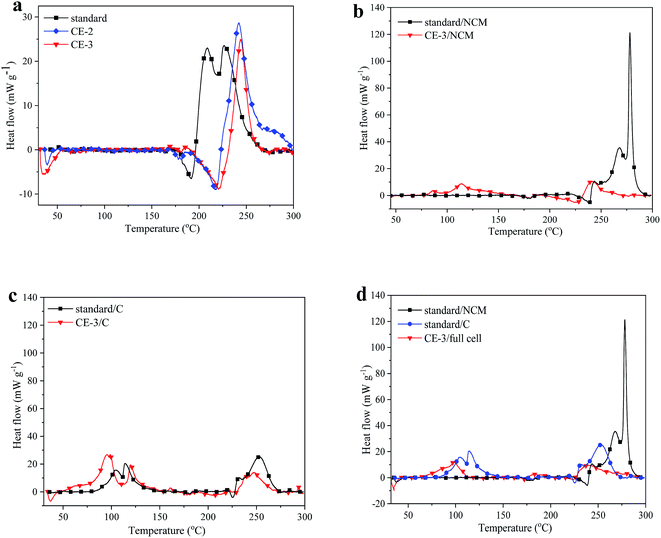 |
| Fig. 6 Thermal stability of the composite electrolytes and the full cell system. Heat flow of (a) the composite electrolytes CE-2 and CE-3, (b) the NCM/electrolyte, (c) the C/electrolyte and (d) the NCM/CE-3/C full cell. | |
For a real lithium ion battery, various components are integral. Thermal decomposition of the electrolyte is the key to triggering the reaction of each component. Thus, it is more meaningful to study the thermal stability of the electrode materials in the presence of the electrolyte. C80 tests were conducted for the cathode (NCM) and anode (C) materials with the standard and CE-3 composite electrolytes. The relevant results are shown in Fig. 6b and c. The total heat generation of the NCM material with the CE-3 composite electrolyte was only −99.96 J g−1. The exothermic peak at around 120 °C should be the decomposition of side reaction products of the CE-3 electrolyte on the surface of the NCM cathode. The total heat generation for the NCM material with the standard electrolyte was −337.96 J g−1. Thus, the composite electrolyte had an obvious inhibition effect on the heat generation of the NCM cathode material. The NCM material has gained widespread interest because of its high energy density and excellent cycle performance.39 However, the safety performance of the NCM material is not good enough compared with the LiFePO4 material, and so it increases the thermal risk of the lithium ion battery. The large exothermic peak after 230 °C disappears for NCM with the standard electrolyte when it is replaced by the composite electrolyte. Usually, the large exothermic reaction of the cathode material is the main reason for thermal runaway in lithium ion batteries.40 Thus the composite electrolyte can reduce the heat generation of the cathode and the fire risk of lithium ion batteries. The weakening of the thermogenic reaction is mainly due to the Lewis base effect of DMAC that prevents the electrolyte from reacting violently with the cathode material, as well as the decomposition of NCM. For the graphite anode material, the composite electrolyte has no obvious effect on safety improvement (Fig. 6c). The exothermic peak near 60 °C is related to the thermal decomposition of the SEI film and the exothermic peak near 250 °C is caused by the reaction between graphite and the electrolyte. Fig. 6d shows the heat flow plots of the NCM/CE-3/C full cells including the electrolyte, electrode and separator. For the full cell system, the anode decomposition is negligible compared to that of the cathode. In comparison with the single electrode material/composite electrolyte system, it can be seen that the composite electrolyte is extremely effective in the full cell system. In the temperature range of 30–300 °C, there are only some weak exothermic reactions in the full cell system. This means that the whole system is very stable, and this is consistent with the analysis shown in Fig. 6b.
From the above analysis, it can be found that this composite electrolyte is unique in that there is a double safety protection mechanism with self-cooling and flame-retardant effects. DMAC reduces the attack ability of Lewis acid to provide the first type of protection. If thermal runaway occurs, PFMP will act as a cooling and extinguishing agent to achieve the second type of protection. Heating phenomena are common during the use of lithium ion batteries, and PFMP can be released by vaporization when used in appropriate amounts to prevent the temperature from rising further. Furthermore, this physical effect is reversible without any chemical destruction reactions occurring. Once the electrolyte catches fire, PFMP can act as an internal micro-extinguisher to put out the fire.
4. Conclusions
A composite electrolyte with a double safety protection mechanism with self-cooling and flame-retardant effects was proposed for improving the safety of lithium ion batteries. It can effectively ameliorate the thermal stability of the electrolyte without unacceptable degradation of the electrochemical performance. The safety mechanism of the composite electrolyte is multi-stage and multi-component. PFMP acts as not only a flame-retardant additive but also an internal extinguishing agent. DMAC is an effective Lewis base that could form a base–acid composite with the acid substance PF5 that is released by LiPF6. The thermal stability and electrochemical performance for the Li/C and NMC/Li half cells and full cells were investigated in detail to determine the 10 vol% PFMP, 5 vol% DMAC and 2.5 vol% FS formula as an appropriate choice. When the amount of PFMP increases to 15 vol%, the electrochemical performance of the cell appears to fade seriously, and this is caused by the increase of impedance. Thermal analysis shows that the composite electrolyte can effectively enhance the thermal stability of the NCM cathode but the electrochemical compatibility needs to be improved.
Conflicts of interest
There are no conflicts to declare.
Acknowledgements
This work was supported by the National Key R&D Program of China (No. 2016YFB0100306), the National Natural Science Foundation of China (No. 51674228 and No. 51604297), and the External Cooperation Program of BIC, CAS (No. 211134KYSB20150004). Dr Q. S. Wang was supported by the Youth Innovation Promotion Association, CAS (No. 2013286).
References
- M. Armand and J.-M. Tarascon, Building better batteries, Nature, 2008, 451(7179), 652–657 CrossRef CAS PubMed.
- V. Etacheri, R. Marom, R. Elazari, G. Salitra and D. Aurbach, Challenges in the development of advanced Li-ion batteries: a review, Energy Environ. Sci., 2011, 4(9), 3243–3262 CAS.
- J. B. Goodenough and Y. Kim, Challenges for rechargeable Li batteries, Chem. Mater., 2009, 22(3), 587–603 CrossRef.
- J.-M. Tarascon and M. Armand, Issues and challenges facing rechargeable lithium batteries, Nature, 2001, 414(6861), 359–367 CrossRef CAS PubMed.
- N. S. Choi, Z. Chen, S. A. Freunberger, X. Ji, Y. K. Sun, K. Amine, G. Yushin, L. F. Nazar, J. Cho and P. G. Bruce, Challenges facing lithium batteries and electrical double-layer capacitors, Angew. Chem., Int. Ed., 2012, 51(40), 9994–10024 CrossRef CAS PubMed.
- D. Aurbach, Y. Talyosef, B. Markovsky, E. Markevich, E. Zinigrad, L. Asraf, J. S. Gnanaraj and H.-J. Kim, Design of electrolyte solutions for Li and Li-ion batteries: a review, Electrochim. Acta, 2004, 50(2), 247–254 CrossRef CAS.
- D. Ruzmetov, V. P. Oleshko, P. M. Haney, H. J. Lezec, K. Karki, K. H. Baloch, A. K. Agrawal, A. V. Davydov, S. Krylyuk and Y. Liu, Electrolyte stability determines scaling limits for solid-state 3D Li ion batteries, Nano Lett., 2011, 12(1), 505–511 CrossRef PubMed.
- K. Xu, Nonaqueous liquid electrolytes for lithium-based rechargeable batteries, Chem. Rev., 2004, 104(10), 4303–4418 CrossRef CAS PubMed.
- K. Liu, W. Liu, Y. Qiu, B. Kong, Y. Sun, Z. Chen, D. Zhuo, D. Lin and Y. Cui, Electrospun core-shell microfiber separator with thermal-triggered flame-retardant properties for lithium-ion batteries, Sci. Adv., 2017, 3(1), e1601978 CrossRef PubMed.
- A. Hammami, N. Raymond and M. Armand, Lithium-ion batteries: Runaway risk of forming toxic compounds, Nature, 2003, 424(6949), 635–636 CrossRef CAS PubMed.
- Q. Wang, P. Ping, X. Zhao, G. Chu, J. Sun and C. Chen, Thermal runaway caused fire and explosion of lithium ion battery, J. Power Sources, 2012, 208, 210–224 CrossRef CAS.
- Y. Baba, S. Okada and J.-i. Yamaki, Thermal stability of LixCoO2 cathode for lithium ion battery, Solid State Ionics, 2002, 148(3), 311–316 CrossRef CAS.
- A. Yamada, E. Watanabe, J. Wang, K. Sodeyama, K. Takada, Y. Tateyama and Y. Yamada, Fire-extinguishing organic electrolytes for safe batteries, Nat. Energy, 2017, 1 CAS.
- B. Ravdel, K. Abraham, R. Gitzendanner, J. DiCarlo, B. Lucht and C. Campion, Thermal stability of lithium-ion battery electrolytes, J. Power Sources, 2003, 119, 805–810 CrossRef.
- Q. Wang, J. Sun, G. Chu, X. Yao and C. Chen, Effect of LiPF6 on the thermal behaviors of four organic solvents for lithium ion batteries, J. Therm. Anal. Calorim., 2006, 89(1), 245–250 CrossRef.
- S. E. Sloop, J. K. Pugh, S. Wang, J. Kerr and K. Kinoshita, Chemical Reactivity of PF5 and LiPF6 in Ethylene Carbonate/Dimethyl Carbonate Solutions, Electrochem. Solid-State Lett., 2001, 4(4), A42–A44 CrossRef CAS.
- A. Granzow, Flame retardation by phosphorus compounds, Acc. Chem. Res., 1978, 11(5), 177–183 CrossRef CAS.
- H. Jia, J. Wang, F. Lin, C. W. Monroe, J. Yang and Y. NuLi, TPPi as a flame retardant for rechargeable lithium batteries with sulfur composite cathodes, Chem. Commun., 2014, 50(53), 7011–7013 RSC.
- T. Yim, M.-S. Park, S.-G. Woo, H.-K. Kwon, J.-K. Yoo, Y. S. Jung, K. J. Kim, J.-S. Yu and Y.-J. Kim, Self-extinguishing lithium ion batteries based on internally embedded fire-extinguishing microcapsules with temperature-responsiveness, Nano Lett., 2015, 15(8), 5059–5067 CrossRef CAS PubMed.
- K. Xu, M. S. Ding, S. S. Zhang, J. L. Allen and T. R. Jow, An attempt to formulate nonflammable lithium ion electrolytes with alkyl phosphates and phosphazenes, J. Electrochem. Soc., 2002, 149(5), A622–A626 CrossRef CAS.
- S. Izquierdo-Gonzales, W. Li and B. L. Lucht, Hexamethylphosphoramide as a flame retarding additive for lithium-ion battery electrolytes, J. Power Sources, 2004, 135(1), 291–296 CrossRef CAS.
- A. Xiao, W. Li and B. L. Lucht, Thermal reactions of mesocarbon microbead (MCMB) particles in LiPF6-based electrolyte, J. Power Sources, 2006, 162(2), 1282–1288 CrossRef CAS.
- A. Andersson and K. Edström, Chemical composition and morphology of the elevated temperature SEI on graphite, J. Electrochem. Soc., 2001, 148(10), A1100–A1109 CrossRef CAS.
- D. Aurbach, E. Zinigrad, Y. Cohen and H. Teller, A short review of failure mechanisms of lithium metal and lithiated graphite anodes in liquid electrolyte solutions, Solid State Ionics, 2002, 148(3), 405–416 CrossRef CAS.
- P. Balakrishnan, R. Ramesh and T. P. Kumar, Safety mechanisms in lithium-ion batteries, J. Power Sources, 2006, 155(2), 401–414 CrossRef CAS.
- P. Ping, Q. Wang, P. Huang, J. Sun and C. Chen, Thermal behaviour analysis of lithium-ion battery at elevated temperature using deconvolution method, Appl. Energy, 2014, 129, 261–273 CrossRef CAS.
- C. L. Campion, W. Li and B. L. Lucht, Thermal decomposition of LiPF6-based electrolytes for lithium-ion batteries, J. Electrochem. Soc., 2005, 152(12), A2327–A2334 CrossRef CAS.
- P. Ping, Q. Wang, J. Sun, H. Xiang and C. Chen, Thermal stabilities of some lithium salts and their electrolyte solutions with and without contact to a LiFePO4 electrode, J. Electrochem. Soc., 2010, 157(11), A1170–A1176 CrossRef CAS.
- A. Xiao, W. Li and B. L. Lucht, Thermal reactions of mesocarbon microbead (MCMB) particles in LiPF6-based electrolyte, J. Power Sources, 2006, 162(2), 1282–1288 CrossRef CAS.
- W. Li, A. Xiao, B. Lucht, M. Smart and B. Ratnakumar, Surface analysis of electrodes from cells containing electrolytes with stabilizing additives exposed to high temperature, J. Electrochem. Soc., 2008, 155(9), A648–A657 CrossRef CAS.
- M. Xu, L. Hao, Y. Liu, W. Li, L. Xing and B. Li, Experimental and theoretical investigations of dimethylacetamide (DMAc) as electrolyte stabilizing additive for lithium ion batteries, J. Phys. Chem. C, 2011, 115(13), 6085–6094 CAS.
- J. L. Pagliaro and G. T. Linteris, Hydrocarbon flame inhibition by C6F12O (Novec 1230): Unstretched burning velocity measurements and predictions, Fire Saf. J., 2017, 87, 10–17 CrossRef CAS.
- K. Sato, I. Yamazaki, S. Okada and J. Yamaki, Mixed solvent electrolytes containing fluorinated carboxylic acid esters to improve the thermal stability of lithium metal anode cells, Solid State Ionics, 2002, 148(3–4), 463–466 CrossRef CAS.
- K. Schroder, J. Alvarado, T. A. Yersak, J. Li, N. Dudney, L. J. Webb, Y. S. Meng and K. J. Stevenson, The effect of fluoroethylene carbonate as an additive on the solid electrolyteinterphase
on silicon lithium-ion electrodes, Chem. Mater., 2015, 27(16), 5531–5542 CrossRef CAS.
- P. Dong, D. Wang, Y. Yao, X. Li, Y. Zhang, J. Ru and T. Ren, Stabilizing interface layer of LiNi0.5Co0.2Mn0.3O2 cathode materials under high voltage using p-toluenesulfonyl isocyanate as film forming additive, J. Power Sources, 2017, 344, 111–118 CrossRef CAS.
- L. Jiang, Q. Wang and J. Sun, Electrochemical performance and thermal stability analysis of LiNixCoyMnzO2 cathode based on a composite safety electrolyte, J. Hazard. Mater., 2018, 351, 260–269 CrossRef CAS PubMed.
- Q. Wang, L. Feng and J. Sun, A Multi-Component Additive to Improve the Thermal Stability of Li(Ni1/3Co1/3Mn1/3)O2-Based Lithium Ion Batteries, Energies, 2016, 9(6), 424 CrossRef.
- P. Verma, P. Maire and P. Novák, A review of the features and analyses of the solid electrolyte interphase in Li-ion batteries, Electrochim. Acta, 2010, 55(22), 6332–6341 CrossRef CAS.
- C.-T. Hsieh, C.-Y. Mo, Y.-F. Chen and Y.-J. Chung, Chemical-wet Synthesis and Electrochemistry of LiNi1/3Co1/3Mn1/3O2 Cathode Materials for Li-ion Batteries, Electrochim. Acta, 2013, 106, 525–533 CrossRef CAS.
- H. Maleki, G. Deng, I. Kerzhner-Haller, A. Anani and J. N. Howard, Thermal Stability Studies of Binder Materials in Anodes for Lithium-Ion Batteries, J. Electrochem. Soc., 2000, 147(12), 4470–4475 CrossRef CAS.
Footnote |
† Electronic supplementary information (ESI) available. See DOI: 10.1039/c8se00111a |
|
This journal is © The Royal Society of Chemistry 2018 |
Click here to see how this site uses Cookies. View our privacy policy here.