Sodium phosphate synthesis through glycerol purification and its utilization for biodiesel production from dairy scum oil to economize production cost†
Received
20th January 2018
, Accepted 3rd April 2018
First published on 5th April 2018
Abstract
In the present study, sodium phosphate was synthesized through glycerol purification. The as-synthesized sodium phosphate was characterized and effectively utilized as a heterogeneous base catalyst for biodiesel production from dairy waste scum oil. In addition, sodium phosphate was synthesized from crude glycerol and the same can be used for biodiesel production, which is economically beneficial. Further, the maximum dairy scum oil methyl ester (DSOME/biodiesel) yield of 97.7% was achieved under optimum conditions of 11
:
1 molar ratio, 4 wt% catalyst loading, 65 °C temperature and 60 min reaction time with stirring at 700 rpm. The activation energy (Ea) of the transesterification reaction was found to be 35.56 kJ mol−1.
Introduction
Nowadays, alternative fuels have attracted much attention due to the depletion of fossil fuels. Biodiesel, well known as fatty acid alkyl ester (FAAE), is an alternative substitute fuel for conventional diesel fuel. Crude glycerol is an important by-product of biodiesel production and 1 kg of crude glycerol is obtained from the production of 10 kg of biodiesel.1 For the sustainable growth of biodiesel industry and decreasing the cost of biodiesel production, effective utilization of crude glycerol is more important. At present, crude glycerol can be utilized for the production of value-added products such as bio-based chemicals including acrolein, hydrogen, glycerol carbonate, acetal, and polyglycerols.2–5 Crude glycerol obtained from biodiesel production process comprises many impurities such as methanol, methyl ester, fatty acids, soaps and glycerides. The amount of each component in crude glycerol depends on the type of feedstock (oil properties) and the process applied for biodiesel production. Purification of glycerol from crude glycerol can play a vital role in decreasing the cost of biodiesel synthesis.6 From the literature, it is known that crude glycerol contains about 20–80% of glycerol.7 Currently, several methods are used for purification of glycerol, including ion exchange resin (IER), distillation and membrane separation technologies (MST). Among these, MST is a cost-effective method for purification of glycerol and this method reduces the amount of organic non-glycerol matter and salt during the purification process.8 Hajek and Skopal employed the MST method for glycerol purification and obtained 86% of glycerol and 99.5% free fatty acids (FFAs).9 Furthermore, KH2PO4 was obtained in the acidification step, which could be used as a fertilizer. In a similar study, 93.34% of pure glycerol was extracted from crude glycerol with ethanol and salts, and fatty acids and NaH2PO4 were separated by decantation and filtration.10 Javani et al. extracted high-quality KH2PO4 and K2HPO4 through step-by-step glycerol purification.11 All these studies highlighted that KH2PO4, K2HPO4 and NaH2PO4 salts are used as fertilizers. In the present study, sodium phosphate was synthesized during the steps involved in the glycerol purification process and it can be used as an effective heterogeneous catalyst in the transesterification reaction. Presently, non-edible oils from sources such as Jatropha, Karanja, Terminalia belerica, Rubber, Mahua, Aegle marmelos and Neem are preferred for biodiesel production because edible oils are used for edible purposes and these oils expensive.12 A large dairy industry produces huge amount of dairy waste scum per day and it consists of fat, unsolicited materials, proteins etc., which are very difficult to dispose due to environmental concerns. Dairy scum oil (DSO) is obtained by removing unwanted materials, suspended particles and water from the dairy waste scum.13 DSO is a non-edible oil and it can be used as a potential resource for biodiesel production. Sivakumar et al. obtained 98% biodiesel yield with optimum conditions of methanol-to-oil molar ratio, reaction time, temperature, KOH catalyst loading and agitation speed.14 In another study Yatish et al. applied response surface methodology and obtained 93% biodiesel yield under optimum reaction conditions.15 Generally, homogeneous base catalysts are preferred over conventional biodiesel production to obtain high yield under mild reaction conditions. Usually, alkaline base catalysts such as sodium and potassium hydroxide are used for biodiesel production with low FFA oils.16 The major drawback of this process is the cost incurred and huge amount of waste water, which is hazardous to the environment owing to the high basicity.17 Presently, processes involving heterogeneous catalysts are preferred due to the easy purification and separation of the final products, which are environmentally friendly.18 An ideal solid catalyst fit for usage needs to possess the following factors: low cost, abundant active sites, increased stability and hydrophobic surface. Various catalysts studied for transesterification include CaO, BaO, MgO, SrO, tri-potassium phosphate, and sodium phosphate.19–21 From the economic point of view, the usage of waste products and heterogeneous catalysts for biodiesel synthesis is important for industrial application. Therefore, the objective of this research study is to synthesize sodium phosphate through glycerol purification and use it for biodiesel production. The optimization of biodiesel production was carried out using dairy waste scum oil with sodium phosphate as a catalyst.
Experimental
Sodium phosphate synthesis through glycerol purification
Initially, a saponification reaction was carried out according to the method reported by Javani et al.11 First, 500 g of crude glycerol was placed in a 1 L beaker. Then, sodium hydroxide was added with a molar ratio ranging from 0.25 to 1.8 and the mixture was stirred at 500 rpm for a period of 60 min at ambient temperature. In a one litre batch glass reactor, 500 g of saponified glycerol was taken and concentrated phosphoric acid was added with stirring until a pH of 11.5 was obtained. Mixing was proceeded for 15 min to complete the precipitation, following which the blend was left undisturbed for 5 h and sifted to expel obtained Na3PO4. Phosphoric acid was added to glycerol to decrease the pH to 2.5 to complete the acidification. Then, the solution was neutralized with 10 M NaOH and the product was extracted by isopropyl alcohol. Finally, refined glycerol was decolorized with activated carbon. The as-synthesized sodium phosphate catalyst was used for transesterification of dairy scum oil.
Transesterification
In this procedure, 100 g of dairy scum oil was taken in a 500 mL three-necked round-bottom flask placed on a hot plate with a magnetic stirrer and equipped with a condenser and a thermostat. The oil was preheated to 60 °C and a desired amount of catalyst and methanol mixture was added. Then, the reaction was carried out for the desired time by varying the temperature at a constant stirring speed of 700 rpm. After completion of the reaction, the reaction mixture was transferred into a settling tank and left undisturbed for settling for a period of 7 to 8 hours. Three distinct phases were separated: catalyst, glycerine and biodiesel. Finally, biodiesel was separated and filtered to obtain pure biodiesel. The biodiesel yield is expressed as shown in eqn (1). |  | (1) |
Results and discussion
Sodium phosphate synthesis and glycerol purification
The process of sodium phosphate extraction and its utilization for transesterification reaction and glycerol purification is shown in Fig. 1. During the saponification, the FFA/soap content reached 99% on increasing the molar ratio of 1.8% NaOH to ester.
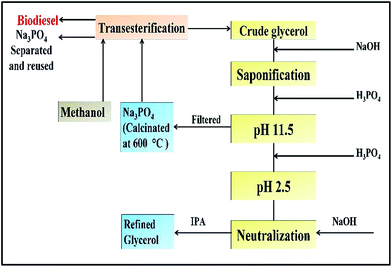 |
| Fig. 1 Synthesis of sodium phosphate through step-by-step glycerol purification process. | |
The addition of H3PO4 to the saponified glycerine-acidification-transforms the soap into three distinct layers, namely, a free fatty acid layer (top), a glycerol-rich layer (middle) and an inorganic salt layer (bottom). The protonated insoluble free fatty acid layer is formed at the top because H+ from H3PO4 can convert the soap bulk to an insoluble FFA layer (eqn (2)).
| R-COONa + H+ → R-COOH + Na+ | (2) |
During acidification, H3PO4 was added to the saponified glycerine until the pH of 11.5 was obtained (IS: 573-1992 standard limit), following which the salt of sodium phosphate was obtained (eqn (3)).
| 3R-COONa + H3PO4 → Na3PO4 + 3RCOOH | (3) |
The obtained sodium phosphate was rinsed and washed with IPA, and then heated at 90 °C to remove IPA for sodium phosphate recover. Upon crystallization, sodium phosphate with purity of 98.3% was obtained and calcined at 600 °C to increase the basicity and stability of the catalyst. The purification of glycerol was achieved according to the method described by Javani et al.11 The quality test for the purified glycerol was performed and the results are shown in Table 1.
Table 1 Properties of purified glycerol
Properties |
Commercial glycerol |
Purified glycerol |
pH |
6.97 ± 0.03 |
6.32 |
Potassium (mg kg−1) |
8.70 ± 4.0 |
8.45 |
Total ASH (%) |
0.0 ± 0.00 |
Nil |
Moisture (%) |
0.01 ± 0.00 |
0.02 |
Sodium (mg kg−1) |
28 ± 10 |
17.0 |
Density (at 20 °C, g mL−1) |
1.27 ± 0.01 |
1.26 ± 0.02 |
Viscosity (in cP at 50 °C, 250 rpm) |
142 ± 1 |
140 ± 2 |
Quality analysis and characterization of sodium phosphate
Table 2 shows the properties of the as-synthesized sodium phosphate catalyst and it reveals that phosphorous (40% mass), heavy metals (<10 ppm), insoluble matter in water (0.3%) and assay (97%) are within the IS 573:1992 standard limit.
Table 2 Quality of sodium phosphate
Properties |
Obtained value |
Limit |
Insoluble matter in water (% mass) |
0.30 |
0.50 |
Phosphates (% mass) |
40.0 |
41.0 |
Heavy metals (e.g., Pb) (% mass) |
<10 ppm |
8 ppm |
Assay (%) |
97% |
— |
Fig. 2 shows the XRD pattern of sodium phosphate rods synthesized via the glycerol purification process. All the diffraction patterns match well with the standard JCPDS card no. 20-1150. It belongs to the monoclinic crystal system and the peaks at 21.1°, 34.5° and 35.48° were indexed to the (101), (121) and (102) planes, respectively. The crystallite size of the materials was calculated using Scherrer's formula as shown in eqn (4):
| D = 0.9λ/β cos θ | (4) |
where
D is the crystallite size,
λ is the wavelength of X-rays and
β is the full width at half maxima. The average crystallite sizes of the as-synthesized sodium phosphate rods were found to be 47 nm.
 |
| Fig. 2 PXRD of sodium phosphate catalyst. | |
Fig. 3 shows the SEM images of sodium phosphate materials obtained on calcination at 600 °C. It is clear from Fig. 3a, b that rod-like morphologies are obtained. The width of rods ranges from 2 to 5 μm and the length ranges from 20 to 50 μm. Some of the rods grown to a size of more than 100 μm showed some small cracks on them. A small number of rods have combined/merged/melted vertically to form well-defined layered structures as shown in Fig. 3a.
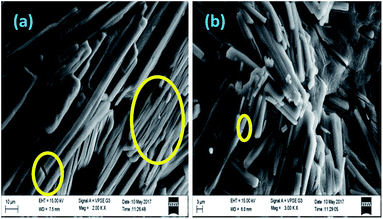 |
| Fig. 3 SEM images of sodium phosphate. | |
The as-synthesized sodium phosphate was used as a heterogeneous base catalyst for transesterification of dairy scum oil.
Optimization of biodiesel production using sodium phosphate catalyst
Effect of catalyst loading and methanol-to-oil molar ratio on biodiesel yield
The type of the catalyst used plays an important role in transesterification. The effect of catalyst loading on biodiesel yield was investigated by varying the catalyst loading from 1.0% to 4.5% with eight different values as shown in Table 3. It is noticed that an increase in catalyst loading increased the yield. The maximum biodiesel yield of 97.1% was achieved at 4% w/w. Further, with an increase in the catalyst loading beyond 4% w/w, the biodiesel yield was reduced due to the increase in the methanol-to-oil (M/O) ratio in the emulsification mixture and the viscosity of the slurry.22 The methanol-to-oil molar ratio is an important factor in the transesterification process. Theoretically, three moles of methanol are required for each mole of oil. In practice, transesterification reaction requires excess methanol in order to push the reaction towards completion. The effect of M/O ratio on biodiesel yield (Table 3) was studied by varying the ratio from 3
:
1 to 13
:
1. A maximum biodiesel yield of 95.8% was achieved at 11
:
1 M/O molar ratio. However, there was a slight decrease in the biodiesel yield from 95.8% to 94.1% with the increase in M/O ratio. This may be due to the agglomeration of methanol and the adhesive nature of the reaction mixture.23
Table 3 Optimization results of Na3PO4-catalyzed biodiesel production process
Catalyst (%) (w/w) |
Biodiesel yield (%) |
M/O (v/v) |
Biodiesel yield (%) |
Temperature (°C) |
Biodiesel (%) |
Time (min) |
Biodiesel yield (%) |
1.0 |
58.8 |
3 |
34.9 |
45 |
80 |
20 |
62.4 |
1.5 |
69.4 |
5 |
45.8 |
50 |
82.6 |
30 |
73.4 |
2.0 |
80.1 |
7 |
65.2 |
55 |
89 |
40 |
87.2 |
2.5 |
83.8 |
9 |
86.8 |
60 |
93.2 |
50 |
93.4 |
3.0 |
88.6 |
11 |
95.8 |
65 |
96.4 |
60 |
96.5 |
3.5 |
92.5 |
13 |
94.1 |
70 |
89.5 |
70 |
96.5 |
4.0 |
97.1 |
|
|
|
|
|
|
4.5 |
93.1 |
|
|
|
|
|
|
Effect of temperature and reaction time on biodiesel yield
The biodiesel conversion takes place at a faster rate with the increase in temperature. The temperature was varied from 45 °C to 70 °C in order to study the effect of temperature on biodiesel yield. The reaction was carried out for 90 min with 4% w/w catalyst loading and 11
:
1 M/O ratio.
A maximum biodiesel yield of 96.4% was achieved at 65 °C. However, with the further increase in temperature from 65 °C to 70 °C, the biodiesel yield decreased due to the vaporization of methanol in the reaction mixture.24 The dependency of the reaction time was studied at different time intervals ranging from 20 to 70 min as shown in Table 3. The other reaction parameters, namely, catalyst loading (4% w/w), M/O ratio (11
:
1) and temperature (65 °C) were kept constant for all experiments. The maximum biodiesel yield of 96.5% was achieved at 60 min reaction time and no significant increase in the biodiesel yield was observed with the further increase in time. Thus, the biodiesel yield was found to increase with an increase in reaction time.25
Kinetic study of transesterification
Apart from the optimization of the reaction process, the determination of biodiesel production kinetics and reaction rate is also important for the scaling-up of the process at the industrial level. The temperature dependence of transesterification of dairy waste scum oil using the sodium phosphate catalyst was studied to recognize the kinetics of the reaction.
The stoichiometric equation of the transesterification reaction can be represented by eqn (5):
where M represents methanol and GL represents glycerol. The reversible reaction in
eqn (3) can be neglected since use of excess methanol in the reaction shifts the reaction in the forward direction. Hence, the rate of reaction (
r) is considered as
eqn (6) which can be altered as
eqn (7):
| 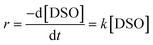 | (6) |
| 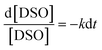 | (7) |
where
k is the rate constant. The conversion of DSO to DSME can be written as [DSO] = [DSO
i][1 −
x], where [DSO
i] is the initial concentration of DSO and
x is the conversion. Substituting this in
eqn [7], we obtain
eqn (8).
|  | (8) |
On simplification of eqn (8), we get the rate constant as eqn (9).
|  | (9) |
The rate constant depends on the reaction temperature. The slope of the graph plotted between −ln[1 − x] vs. t gives the rate constant. Hence, the activation energy required for the transesterification process was determined by considering the Arrhenius equation (eqn (10)). This equation can be modified as eqn (11):
| 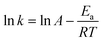 | (11) |
where
Ea is the activation energy (J mol
−1),
A is the Arrhenius constant,
R is the universal gas constant (8.314 J mol
−1 K
−1) and
T is the absolute temperature (K). The slope of the graph plotted between ln
k vs. 1/
T represents the
Ea/
R value. The required activation energy was found to be 36.74 kJ mol
−1. The kinetic study of the present study was compared with the other similar studies and tabulated in
Table 4.
Table 4 Review of kinetic study of transesterification reactiona
Feed stock |
Catalyst |
Alcohol |
Reaction order |
Activation energy (kJ mol−1) |
Ref. |
Ref. = Reference.
|
Dairy scum oil |
Na3PO4 |
Methanol |
Pseudo-first |
36.74 |
Present work |
Canola oil |
Li/Ca–La |
Methanol |
Pseudo-first |
45.6 |
26
|
Waste cottonseed oil |
KF/CaO/NiO |
Methanol |
Pseudo-first |
41.2 |
27
|
Soybean oil |
CaO/Al2O3 |
Methanol |
Pseudo-first |
30.7 |
28
|
Bombax ceiba oil |
CaO NPs |
Methanol |
Pseudo-first |
35.99 |
29
|
Jatropha oil |
Zr/CaO |
Methanol |
Pseudo-first |
29.8 |
30
|
Effect of sodium phosphate catalyst reusability
Reusability is an important feature of the heterogeneous catalyst. The effect of catalyst reusability was studied using optimum reaction conditions. The catalyst was recovered after the first cycle, dried and regenerated for the next cycle. The catalyst shows good catalytic activity up to fourth cycle. After the fourth run, the catalytic activity was reduced to 10% and >80% biodiesel conversion was achieved. Thus, the sodium phosphate catalyst was effectively reused for biodiesel production from dairy scum oil.
Economic considerations
Considering economic benefits, it is important to develop a method for low-cost biodiesel production and glycerol purification. In the present study, the sodium phosphate salt was synthesized via crude glycerol purification process and effectively utilized in biodiesel production, which reduced the cost of biodiesel production. Table 5 shows the prices of the raw materials including phosphoric acid, sodium hydroxide and IPA in comparison to the products including sodium phosphate and glycerol, which highlight the potential of sodium phosphate production. IPA can be recycled and reused in the process. Moreover, sodium phosphate is a heterogeneous catalyst and reused after completion of the reaction. Furthermore, dairy scum oil is also a waste product generated in dairy industries. Sodium phosphate was synthesized from dairy scum crude glycerol, so utilization of dairy scum oil and sodium phosphate for biodiesel production reduces the production cost.
Table 5 Comparison of the prices of the raw materials used in glycerol purification with that of the products
Chemical material |
Quantity |
Pricea (  ) |
ThermoFisher Scientific.
|
Raw material
|
H3PO4 |
500 mL |
810.00 |
NaOH |
500 g |
329.00 |
IPA |
500 mL |
333.00 |
![[thin space (1/6-em)]](https://www.rsc.org/images/entities/char_2009.gif) |
Product
|
Na3PO4 |
500 g |
349.00 |
Glycerol |
500 mL |
419.00 |
Conclusion
During glycerol purification, sodium phosphate salt with 98.3% purity was produced. The utilization of sodium phosphate as a catalyst in biodiesel production contributes to improved economics of biodiesel production. The sodium phosphate catalyst is found to be an efficient catalyst for biodiesel production. The maximum dairy scum oil methyl ester (DSOME/biodiesel) yield of 97.7% was achieved under optimum conditions of 11
:
1 molar ratio, 4 wt% catalyst loading, 65 °C temperature and 60 min of reaction time with stirring speed of 700 rpm. From the kinetic study of the transesterification reaction, the value Ea was found to be 36.74 kJ mol−1.
Conflicts of interest
There are no conflicts to declare.
Acknowledgements
Authors are thankful to Bioenergy Research, Information and Demonstration Centre, Siddaganga Institute of Technology, Tumakuru-572103, Karnataka, India for providing necessary experimental setup to conduct this research.
References
- Z. Chi, D. Pyle, Z. Wen, C. Frear and S. Chen, Process Biochem., 2007, 42, 1537 CrossRef CAS.
- P. S. Kong, M. K. Aroua and W. M. A. W. Daud, Renewable Sustainable Energy Rev., 2016, 63, 533 CrossRef CAS.
- H. W. Tan, A. R. A. Aziz and M. K. Aroua, Renewable Sustainable Energy Rev., 2013, 27, 118 CrossRef CAS.
- O. Valerio, T. Horvath, C. Pond and M. Misra, Ind. Crops Prod., 2015, 78, 141 CrossRef CAS.
- M. R. Nanda, Z. Yuan, W. Qin, M. A. Poirier and X. Chunbao, Aust. Chem. Eng., 2014, 1, 1004 Search PubMed.
- M. Hasheminejad, M. Tabatabaei, Y. Mansourpanah, M. Khatami far and A. Javani, Bioresour. Technol., 2011, 102, 461 CrossRef CAS PubMed.
- J. C. Thompson and B. B. He, Appl. Eng. Agric., 2006, 22, 261 CrossRef.
- R. Manosak, S. Limpattayanate and M. Hunsom, Fuel Process. Technol., 2011, 92, 92 CrossRef CAS.
- M. Hajek and F. Skopal, Bioresour. Technol., 2010, 101, 3242 CrossRef CAS PubMed.
- S. Kongjao, S. Damronglerd and M. Hunsom, Korean J. Chem. Eng., 2010, 27, 944 CrossRef CAS.
- A. Javani, M. Hasheminejad, K. Tahvildari and M. Tabatabaei, Bioresour. Technol., 2012, 104, 788 CrossRef PubMed.
- K. V. Yatish, H. S. Lalithamba, R. Suresh and B. R. Omkaresh, Biofuels, 2016, 9(1), 121 CrossRef.
- H. V. Srikanth, J. Venkatesh, S. Godiganur, S. Venkateswaran and B. Manne, Renewable Energy, 2017, 111, 168 CrossRef CAS.
- P. Sivakumar, K. Anbarasu and S. Ranganathan, Fuel, 2011, 90, 147 CrossRef CAS.
- K. V. Yatish, H. S. Lalithamba, R. Suresh, S. B. Arun and P. Vinay Kumar, Process Saf. Environ. Prot., 2016, 102, 667 CrossRef CAS.
- Z. J. Predojevic, Fuel, 2008, 87, 3522 CrossRef CAS.
- B. H. Hameed, C. S. Goh and L. H. Chin, Fuel Process. Technol., 2009, 90, 1532 CrossRef CAS.
- M. Zabeti, W. M. A. W. Daud and M. K. Aroua, Appl. Catal., A, 2009, 366, 154 CrossRef CAS.
- G. Guan, K. Kusakabe and S. Yamasaki, Fuel Process. Technol., 2009, 90, 520 CrossRef CAS.
- M. Kouzu, T. Kasuno, M. Tajika, Y. Sugimoto, S. Yamanaka and J. Hidaka, Fuel, 2008, 87, 2798 CrossRef CAS.
- K. V. Yatish, H. S. Lalithamba, R. Suresh and H. R. Harsha Hebbar, Renewable Energy, 2018, 122, 561 CrossRef CAS.
- N. Tshizanga, B. Elizabeth Funmilayo Aransiola and O. Oyekola, S. Afr. J. Chem. Eng., 2017, 23, 145 Search PubMed.
- Y. H. Tan, M. O. Abdullah, C. Nolasco-Hipolito and N. A. Z. Syuhada, Renewable Energy, 2017, 114, 437 CrossRef CAS.
- G. Baskar and M. Soumiya, Renewable Energy, 2016, 98, 101 CrossRef CAS.
- B. Gurunathan and A. Ravi, Bioresour. Technol., 2015, 188, 124 CrossRef CAS PubMed.
- M. Kaur and A. Ali, Eur. J. Lipid Sci. Technol., 2014, 116, 80 CrossRef CAS.
- N. Pasupulety, K. Gunda, Y. Liu, G. L. Rempel and F. T. T. Ng, Appl. Catal., A, 2013, 452, 189 CrossRef CAS.
- H. Maleki and M. Kazemeini, J. Fuel Chem. Technol., 2017, 45, 442 CrossRef CAS.
- M. Kaur and A. Ali, Fuel Process. Technol., 2014, 119, 173 CrossRef.
- H. R. Harsha Hebbar, M. C. Math and K. V. Yatish, Energy, 2018, 143, 25 CrossRef CAS.
Footnote |
† Electronic supplementary information (ESI) available: Materials, quality analysis, kinetic study and characterization of sodium phosphate. See DOI: 10.1039/c8se00034d |
|
This journal is © The Royal Society of Chemistry 2018 |
Click here to see how this site uses Cookies. View our privacy policy here.