DOI:
10.1039/C8RA06886K
(Paper)
RSC Adv., 2018,
8, 40962-40967
Tungstic acid-functionalized Fe3O4@TiO2: preparation, characterization and its application for the synthesis of pyrano[2,3-c]pyrazole derivatives as a reusable magnetic nanocatalyst†
Received
17th August 2018
, Accepted 5th November 2018
First published on 6th December 2018
Abstract
A new magnetic nanocatalyst based on the immobilization of tungstic acid onto 3-chloropropyl-grafted TiO2-coated Fe3O4 nanoparticles (Fe3O4@TiO2@(CH2)3OWO3H) was prepared, characterized, and applied for the synthesis of pyrano[2,3-c]pyrazole derivatives. The characterization was performed using FT-IR spectroscopy, X-ray diffraction (XRD), scanning electron microscopy (SEM), energy-dispersive X-ray spectroscopy (EDS), and vibrating sample magnetometry (VSM) analysis. Pyranopyrazoles were synthesized in the presence of this novel catalyst via a three-component reaction of 3-methyl-1-phenyl-2-pyrazolin-5-one, malononitrile, and aromatic aldehydes with high yields. It is a low cost, nontoxic and thermally stable catalyst, which shows a long life and can be reused for several catalytic cycles without deactivation or selectivity loss.
Introduction
Despite the many benefits of homogeneous catalysts such as high activity and selectivity, heterogeneous catalytic systems have surpassed them due to the high capability for recycling and reutilization.1 Over the past century, nanocatalysts as a bridge between heterogeneous and homogeneous catalysis have drawn great attention for application in different fields. The significant advantage of nanoparticles is their high specific surface area to volume ratio leading to increase in the contact with the reactants.2–4 They also have many other advantages such as presence of various surface reactive sites, high activity, selectivity, and desired resilience, which make them recognized as a pioneering technology in green chemistry.5 Despite the several mentioned benefits of nanomaterials, they are difficult to separate. Therefore, it is important to design recoverable and well-dispersed nanocatalysts.
Recently, Fe3O4 magnetite nanoparticles (MNPs) have been intensively used as catalytic supports owing to the facility of isolation from the reaction mixture using an external magnet. Furthermore, these systems possess highly potential active sites for loading of other functional groups to prepare novel heterogeneous catalysts.6–11 To prevent Fe3O4 nanoparticles from oxidation in an air atmosphere and in order to increase the surface area and simplify the surface functionalization, a protective shell can be formed on their surface.12
TiO2 have been successfully applied as a nontoxic, low cost and highly effective catalyst that has good mechanical resistance and stability in acidic and oxidative environments. TiO2 was also found to be a good support material for heterogeneous catalysis due to the strong metal support interaction, chemical stability, and acid–base property.13–15 Because of the small size of TiO2 particles and difficulties in the separation of catalyst from the reaction media, there are some significant drawbacks in using TiO2 as a heterogeneous catalyst. Immobilization of TiO2 on magnetic nanoparticles as suitable alternative supports to produce magnetically recoverable heterogeneous catalysts allows a convenient recovery of magnetic catalyst under an external magnetic field.16,17
In recent years, there has been increasing attention in the synthesis of pyrano[2,3-c]pyrazoles as an important class of heterocyclic compounds.18–21 This interest has resulted from their vital biological activities such as analgesic, antitumor, anticancer, and anti-inflammatory as well as their potential as inhibitors of human Chk1 kinase.22,23 The pyrano[2,3-c]pyrazoles subunit is present in various pharmaceutical and medicinally useful molecules.24 They are also the main building blocks in the synthesis of natural products as well as in heterocyclic compounds.25
Taking the above facts into consideration and in continuation of our research on the synthesis of heterogeneous catalysts,26–31 in this study, we have immobilized tungstic acid on TiO2-coated Fe3O4 magnetic nanoparticles (Fe3O4@TiO2@(CH2)3OWO3H) and then investigated its performance as a novel strong, recoverable, and stable acid nanocatalyst for synthesis of pyrano[2,3-c]pyrazole derivatives.
Experimental
Chemicals were purchased from Fluka, Merck and Aldrich chemical companies. Known products were identified via comparison of their structural data and physical properties with their reported data in the literature. Melting points were determined by an electrothermal kSB1N apparatus. Fourier transform infrared (FT-IR) spectra were recorded on a Shimadzu-470 spectrometer using KBr pellets. The morphology of the particles was observed by scanning electron microscopy (SEM) under acceleration voltage of 26 kV. X-ray powder diffraction (XRD) patterns were recorded using a Bruker AXS (D8 Advance) X-ray diffractometer with Cu Kα radiation (λ = 0.15418 nm). Energy dispersive spectroscopy (EDS) was obtained using TESCAN Vega model instrument. The magnetic measurement was carried out in a vibrating sample magnetometer (VSM; Kashan university, Kashan, Iran) at room-temperature.
Preparation of Fe3O4 MNPs
A solution of FeCl2·4H2O (1 g, 5 mmol) and FeCl3·6H2O (2.7 g, 10 mmol) (dissolved in 45 mL double distilled water) was degassed with an argon gas, heated to 80 °C and stirred for 30 minutes. Then, sodium hydroxide solution (5 mL, 10 M) was slowly added dropwise. After stirring at 80 °C for 1 h under argon atmosphere, Fe3O4 MNPs was separated by an external magnet and washed with double distilled water until pH 9 and then dried at 60 °C.32
Synthesis of nano-Fe3O4@TiO2
The prepared Fe3O4 MNPs were dispersed in a mixture of absolute ethanol and acetonitrile (125
:
45 mL) by sonication for 20 min. Then, ammonia aqueous solution (0.75 mL, 25%) was added under vigorous stirring for 30 minutes. After that, tetraethyl orthotitanate (TEOT) (1.5 mL) dissolved in absolute ethanol (20 mL) was slowly added to the above suspension, under continuous mechanical stirring at 30 °C. This mixture was stirred for 1.5 h to obtain nano-Fe3O4@TiO2. The resulting precipitate was collected by an external magnet and washed with absolute ethanol and dried at room-temperature.33
Preparation of Fe3O4@TiO2@(CH2)3Cl
A mixture of Fe3O4@TiO2 (0.2 g) and 3-chloropropyltrimethoxysilane (2 mL) was stirred with an argon gas under reflux conditions for 12 h. Next, the obtained product was separated by a normal magnet and washed using toluene, ethanol–water mixture, and distilled water. Finally, obtained Fe3O4@TiO2@(CH2)3Cl was dried in an oven at 60 °C.
Preparation of Fe3O4@TiO2@(CH2)3OWO3H (1)
In the final stage, a mixture of Fe3O4@TiO2@(CH2)3Cl (0.5 g) and Na2WO4·2H2O (0.25 g) in DMSO (5 mL) was stirred at reflux under argon atmosphere for 12 h. After cooling, the obtained catalyst was decanted and washed twice with DMSO, once with distilled water, and dried at 60 °C for 6 h. Then, the functionalized magnetic nanoparticles were added to the flask containing HCl (30 mL, 0.1 N) and stirred for 1 h at room-temperature. The resulting catalyst was decanted, washed with DMSO and water, and finally dried in oven at 60 °C for 12 h.
General procedure for the synthesis of pyranopyrazole derivatives 5
Fe3O4@TiO2@(CH2)3OWO3H (0.003 g) was added to a mixture of aldehydes (1 mmol), 3-methyl-1-phenyl-2-pyrazolin-5-one (1 mmol), and malononitrile (1 mmol). The mixture was stirred under solvent-free conditions at 80 °C for the requisite time. The reaction progress was screened using TLC. After completion of the reaction, ethanol (5 mL) was added to the reaction mass and the catalyst was collected with an external magnet. Additional purification was achieved by recrystallization from hot ethanol.
6-Amino-4-(2,4-dihydroxyphenyl)-3-methyl-1-phenyl-1,4-dihydropyrano[2,3-c]pyrazole-5-carbonitrile (5q). White crystals, IR (KBr): νmax = 3424, 3309, 3183, 2923, 2854, 2211, 1590, 1511, 1400, 1351, 1255, 1189, 1045, 842, 800 cm−1. 1H NMR (400 MHz, DMSO-d6): δ = 9.68 (s, 1H), 7.92 (s, 1H), 7.76 (s, 2H), 7.52–7.75 (m, 2H), 7.25–7.27 (m, 2H), 6.89 (s, 2H), 6.45 (d, 2H, J = 4 Hz), 6.32 (s, 1H), 5.53 (s, 1H), 1.82 (s, 3H). 13C NMR (100 MHz, DMSO-d6): δ = 166.61, 162.25, 161.98, 159.71, 155.85, 153.63, 138.27, 126.38, 123.14, 117.11, 114.33, 108.82, 107.09, 103.83, 101.35, 75.76, 42.11, 26.12. Anal. calcd for C20H16N4O3: C, 66.66; H, 4.48; N, 15.55. Found: C, 66.58; H, 4.53; N, 15.60.
6-Amino-4-(5-bromo-2-hydroxyphenyl)-3-methyl-1-phenyl-1,4-dihydropyrano[2,3-c]pyrazole-5-carbonitrile (5r). Yellow crystals, IR (KBr): νmax = 3455, 3347, 3212, 2935, 2210, 1646, 1608, 1554, 1477, 1388, 1280, 1222, 1087, 802, 470 cm−1. 1H NMR (400 MHz, DMSO-d6): δ = 8.71 (s, 1H), 7.71 (d, 2H, J = 4 Hz), 7.52 (t, 2H, J = 4 Hz), 7.36 (s, 1H), 7.27–7.30 (m, 2H), 6.83–6.93 (m, 2H), 6.61 (d, 1H, J = 4 Hz), 5.46 (s, 1H), 2.04 (s, 3H). 13C NMR (100 MHz, DMSO-d6): δ = 162.97, 162.31, 158.22, 158.17, 151.67, 140.98, 137.22, 127.62, 121.35, 118.38, 118.06, 118.03, 117.24, 116.73, 97.66, 75.22, 47.56, 23.87. Anal. calcd for C20H15BrN4O2: C, 56.75; H, 3.57; N, 13.24. Found: C, 56.70; H, 3.51; N, 13.29.
Results and discussion
Fe3O4@TiO2@(CH2)3OWO3H (1) was prepared following the protocol shown in Scheme 1. Firstly, Fe3O4 nanoparticles were synthesized via coprecipitation method.32 Subsequently, tetraethyl orthotitanate (TEOT), as a coating agent, reacts with Fe3O4 to develop TiO2 layer on the Fe3O4 backbone.33 The OH groups on the titanium coating magnetic nanoparticles (Fe3O4@TiO2) can be functionalized with 3-chloropropyltriethoxysilan molecule. Finally, the chloride group was replaced by tungstic acid to prepare Fe3O4@TiO2@(CH2)3OWO3H (1) as a magnetic nanocatalyst. The obtained catalyst was characterized via FT-IR, X-ray diffraction patterns (XRD), scanning electron microscopy (SEM), energy-dispersive X-ray spectroscopy (EDS), and vibrating sample magnetometer (VSM) analysis.
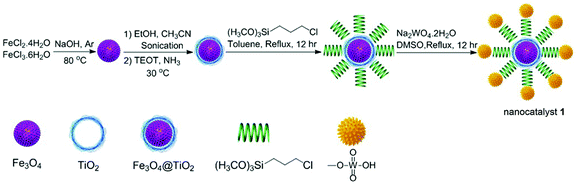 |
| Scheme 1 Preparation of Fe3O4@TiO2@(CH2)3OWO3H (1). | |
Fig. 1 shows the X-ray diffraction (XRD) patterns of the synthesized nano-Fe3O4@TiO2 and Fe3O4@TiO2@(CH2)3OWO3H in the range 20–70°. In Fig. 1c, the following signals at (220), (210), (400), (511), and (440) and 2θ = 30.10°, 35.60°, 43.40°, 53.50°, 57.20°, and 62.80 planes confirm that the main formed phase was a cubic Fe3O4, which is in agreement with the JCPD 79-0417 standard.34 Also, the mentioned indexes revealed that the new catalyst in Fig. 1c has the similar structure to Fe3O4 nanoparticles in Fig. 1a, and this shows that no phase change was observed after surface modification of the magnetite nanoparticles. The peak that confirmed the presence of tungstate group appeared in the range of 2θ = 22°.35 The particle size of the prepared catalyst could be approximated using the Debye–Scherrer equation, D = kλ/β
cos
θ, where D is the average crystalline size, λ is the X-ray wavelength, k is the Scherrer constant, β is the half width of XRD diffraction lines, and θ is the Bragg diffraction angle. The particle size relevant to the Debye–Scherrer equation was calculated to be 23 nm.
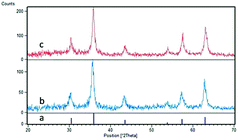 |
| Fig. 1 The XRD patterns of (a) Fe3O4, (b) Fe3O4@TiO2, and (c) Fe3O4@TiO2@(CH2)3OWO3H. | |
The FT-IR spectra of the Fe3O4, Fe3O4@TiO2, Fe3O4@TiO2@(CH2)3Cl, and Fe3O4@TiO2@(CH2)3OWO3H are shown in Fig. 2. The broad peak at about 2600–3700 cm−1 could be attributed to the overlapping of OH stretching bands (corresponding to uncoated OH and acidic OH). The presence of characteristic peaks corresponding to Fe–O stretching vibration near 584 cm−1 in all compared spectra was a confirmation of how nanostructure of Fe3O4 was preserved throughout the process. In Fig. 2b, the peaks discerned at 1118 cm−1 and 1400 cm−1 can be ascribed to the stretching vibration modes of Ti–O and Fe–O–Ti bonds, respectively. In Fig. 2c, CH2 bending, as a broad band and symmetric CH2 and asymmetric CH2 of the alkyl chains appeared at 1480 cm−1 and 2860–2923 cm−1, respectively. In Fig. 2d, after modification of Fe3O4@TiO2@(CH2)3Cl with tungstic acid, new bonds appeared at 887 cm−1, which corresponded to W
O vibrations (Fig. 3).
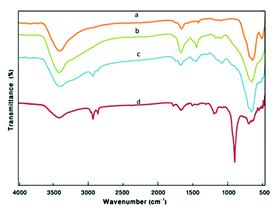 |
| Fig. 2 The FT-IR spectra of (a) Fe3O4 MNPs, (b) Fe3O4@TiO2, (c) Fe3O4@TiO2@(CH2)3Cl, and (d) Fe3O4@TiO2@(CH2)3OWO3H. | |
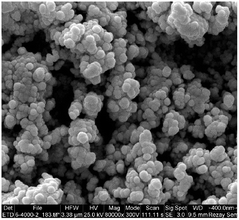 |
| Fig. 3 The SEM image of catalyst 1. | |
Surface morphology of Fe3O4@TiO2@(CH2)3OWO3H was observed via scanning electron microscopy (SEM). The result demonstrates that the sample consists of homogeneous spherical nanoparticles with diameters in the range of 33.79–90.72 nm (Fig. 4).
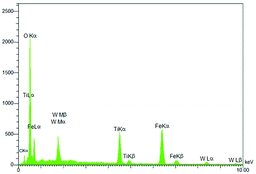 |
| Fig. 4 EDS analysis of Fe3O4@TiO2@(CH2)3OWO3H. | |
Energy-dispersive X-ray spectroscopy (EDS) was used for the structural characterization of Fe3O4@TiO2@(CH2)3OWO3H. As can be seen in Fig. 4, the components of this catalyst included Fe, Ti, O, C and W, which indicate the acceptable concordance with the expectations and also confirm the successful incorporation of tungstate groups.
The vibrating sample magnetometer (VSM) was applied to evaluate the magnetic measurement of the prepared catalyst (Fig. 5). In the present method, the magnetic behavior of the above catalyst has been calculated by drawing the hysteresis loops at room-temperature. The below magnetization curves shows the saturation magnetization of Fe3O4@TiO2 nanoparticles and Fe3O4@TiO2@(CH2)3OWO3H, which were diminished to 23.4 emu g−1 from 65.8 emu g−1 for Fe3O4@TiO2. As can be seen, the difference of saturation magnetization between Fe3O4@TiO2 nanoparticles and Fe3O4@TiO2@(CH2)3OWO3H was small.
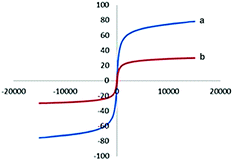 |
| Fig. 5 Room-temperature magnetization curves of (a) Fe3O4@TiO2 and (b) Fe3O4@TiO2@(CH2)3OWO3H. | |
After full structural characterization of nano-Fe3O4@TiO2@(CH2)3OWO3H, it has been successfully applied to synthesis of pyrano[2,3-c]pyrazole derivatives 5 via a three-component reaction of 3-methyl-1-phenyl-2-pyrazolin-5-one 2, aromatic aldehydes 3, malononitrile 4 under solvent-free conditions (Scheme 2).
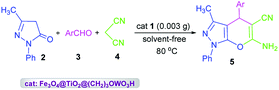 |
| Scheme 2 Synthesis of pyranopyrazoles 5 in the presence of nanocatalyst 1. | |
In order to find the most appropriate reaction conditions, the reaction of 3-methyl-1-phenyl-2-pyrazolin-5-one (1 mmol), benzaldehyde (1 mmol), and malononitrile (1 mmol) was selected as a model reaction. The desired product was not produced in the absence of a catalyst even after a long reaction time. Then, we attempted with different amounts of Fe3O4@TiO2@(CH2)3OWO3H as catalyst under various conditions. The obtained data for several catalyst loads, temperatures, and solvents are summarized in Table 1. It was seen that the selection of 0.003 g of catalyst 1 at 80 °C under solvent-free conditions would be the best of choice (Table 1, entry 11).
Table 1 Optimization of the model reaction
Entry |
Solvent |
Catalyst (g) |
T (°C) |
Time (h) |
Yielda (%) |
Isolated yields. |
1 |
EtOH |
0.005 |
Reflux |
180 |
52 |
2 |
CHCl3 |
0.005 |
Reflux |
180 |
50 |
3 |
Toluene |
0.005 |
Reflux |
180 |
45 |
4 |
H2O |
0.005 |
Reflux |
180 |
40 |
5 |
CH3CN |
0.005 |
Reflux |
180 |
40 |
6 |
MeOH |
0.005 |
Reflux |
180 |
50 |
7 |
— |
0.005 |
60 |
180 |
70 |
8 |
— |
0.005 |
80 |
120 |
75 |
9 |
— |
0.005 |
100 |
120 |
75 |
10 |
— |
0.004 |
80 |
120 |
80 |
11 |
— |
0.003 |
80 |
75 |
90 |
12 |
— |
0.003 |
100 |
75 |
85 |
13 |
— |
0.003 |
110 |
75 |
80 |
14 |
— |
0.007 |
80 |
75 |
85 |
Under these conditions, a range of aryl aldehydes, containing both electron-donating and electron-withdrawing groups were examined and resulted in good to excellent yields of the products in short reaction times (Table 2).
Table 2 Fe3O4@TiO2@(CH2)3OWO3H-catalyzed synthesis of pyrano[2,3-c]pyrazoles 5a
Entry |
Ar |
Time (min) |
Yieldb (%) |
Mp (°C) |
Reaction conditions: 3-methyl-1-phenyl-2-pyrazolin-5-one (1 mmol), arylaldehyde (1 mmol), malononitrile (1 mmol), and Fe3O4@TiO2@(CH2)3OWO3H (0.003 g), 80 °C. Isolated yields. Novel product. |
5a |
C6H5 |
75 |
90 |
170–172 (ref. 36) |
5b |
4-OCH3C6H4 |
90 |
87 |
174–175 (ref. 36) |
5c |
2,4-Cl2C6H3 |
80 |
84 |
185–186 (ref. 36) |
5d |
4-ClC6H4 |
70 |
90 |
172–174 (ref. 36) |
5e |
2-BrC6H4 |
82 |
78 |
166–167 (ref. 17) |
5f |
3-ClC6H4 |
85 |
86 |
157–159 (ref. 17) |
5g |
2-ClC6H4 |
80 |
89 |
144–146 (ref. 36) |
5h |
4-NO2C6H4 |
70 |
79 |
194–196 (ref. 36) |
5k |
4-C3H7C6H4 |
90 |
88 |
169–170 (ref. 36) |
5l |
4-BrC6H4 |
77 |
78 |
183–184 (ref. 36) |
5m |
4-OHC6H4 |
95 |
92 |
211–212 (ref. 36) |
5n |
4-(PhCH2O) C6H4 |
100 |
80 |
160–161 (ref. 36) |
5p |
3-OC2H5 4-OH C6H3 |
95 |
83 |
169–171 (ref. 36) |
5q |
2,4-(OH)2 C6H3 |
110 |
80 |
320–321c |
5r |
5-Br 2-OH C6H3 |
120 |
83 |
314–315c |
Due to the importance of recoverability and recyclability of the catalyst from both practical and economical viewpoints, we next examined the reusability of Fe3O4@TiO2@(CH2)3OWO3H in the reaction of 3-methyl-1-phenyl-2-pyrazolin-5-one, benzaldehyde, and malononitrile under optimized reaction conditions. Fe3O4@TiO2@(CH2)3OWO3H was separated by a permanent magnet from the reaction mixture, washed with methanol, and reused in the next run without further treatment. The results revealed that the catalyst could be reused for five cycles without remarkable loss in catalytic performance. The data are exhibited in Fig. 6.
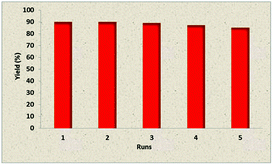 |
| Fig. 6 Reusability of catalyst 1 in the reaction between 3-methyl-1-phenyl-2-pyrazolin-5-one, malononitrile, and benzaldehyde. | |
The proposed formation mechanism of product 5 is given in Scheme 3. Initially, intermediate 6 was formed via the condensation of activated aromatic aldehydes and malononitrile in the presence of acid catalyst 1. It is reasonable to suppose that the intermediate 6 was attached by c-4 of 3-methyl-1-phenyl-2-pyrazolin-5-one which rearranged into intermediate 7. Cyclization of 7 by the nucleophilic attack of C
O group on the cyano moiety gives 8. Finally, a sequence of tautomerization of 8 generates the related product.
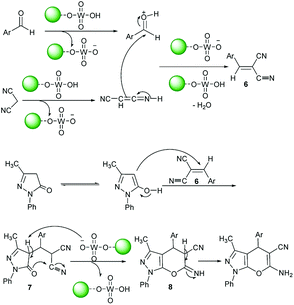 |
| Scheme 3 Proposed mechanism for the synthesis of product 5 catalyzed by catalyst 1. | |
The major advantages of the presented protocol over existing methods can be seen by comparing our results with those of some recently reported procedures, as shown in Table 3.
Table 3 Comparison of the results for the synthesis of 5a by other catalysts
Entry |
Catalyst |
Catalyst loading |
Condition |
Time (min)/yielda (%) |
Isolated yields. This study. |
1 |
Piperidine |
0.05 mL |
EtOH, MW |
8/61 (ref. 37) |
2 |
γ-Alumina |
30 mol% |
H2O, reflux |
50/80 (ref. 38) |
3 |
Mg/Al HT |
0.1 g |
EtOH, r.t. |
60/87 (ref. 39) |
4 |
p-Toluene sulfonic acid |
0.05 g |
H2O, reflux |
55/86 (ref. 40) |
5 |
Triethylbenzylammonium chloride |
0.15 g |
H2O, 90 °C |
360/99 (ref. 41) |
6 |
Catalyst 1 |
0.003 g |
80 °C, solvent-free |
75/90b |
Conclusions
In this study, we have introduced for the first time a green and recyclable nanomagnetic solid acid catalyst, namely Fe3O4@TiO2@(CH2)3OWO3H. Structural verification was performed using FT-IR, XRD, SEM, EDS and VSM. This novel Fe3O4-based heterogeneous nanocatalyst was successfully used for the synthesis of pyrano[2,3-c]pyrazoles. Besides recyclability, its advantages like operational simplicity, good chemical yields combined with step- and atom-economic aspects are the main promising points of this study which make this strategy highly attractive.
Conflicts of interest
There are no conflicts to declare.
Acknowledgements
The authors gratefully acknowledge partial support of this study by Yasouj University, Iran.
Notes and references
- M. A. Zolfigol and M. Yarie, Appl. Organomet. Chem., 2017, 31, 3598 CrossRef.
- S. Shylesh, V. Schünemann and W. R. Thiel, Angew. Chem., Int. Ed., 2010, 49, 3428 CrossRef CAS PubMed.
- B. Karimi, F. Mansouri and H. M. Mirzaei, ChemCatChem, 2015, 7, 1736 CrossRef CAS.
- B. K. Khosravian and M. Farahi, New J. Chem., 2017, 41, 11584 RSC.
- R. K. Sharma, S. Sharma, S. Dutta, R. Zboril and M. B. Gawande, Green Chem., 2015, 17, 3207 RSC.
- H. Woo, K. Lee, S. Park and K. H. Park, Molecules, 2014, 19, 699 CrossRef PubMed.
- R. Hudson, Y. Feng, R. S. Varma and A. Moores, Green Chem., 2014, 16, 4493 RSC.
- M. B. Gawande, P. S. Branco and R. S. Varma, Chem. Soc. Rev., 2013, 42, 3371 RSC.
- J. Safari and Z. Zarnegar, RSC Adv., 2015, 5, 17738 RSC.
- H. Kefayati, M. Golshekan, S. Shariati and M. Bagheri, Chin. J. Catal., 2015, 36, 572 CrossRef CAS.
- J. S. Yoo, Catal. Today, 1998, 44, 27 CrossRef CAS.
- L. Tan, X. Zhang, Q. Liu, J. Wang, Y. Sun, X. Jing, J. Liu, D. Songa and L. Liuc, Dalton Trans., 2015, 44, 6909 RSC.
- Q. J. Xiang, K. L. Lv and J. G. Yu, Appl. Catal., B, 2010, 96, 557 CrossRef CAS.
- X. Yu, S. Liu and J. Yu, Appl. Catal., B, 2011, 104, 12 CrossRef CAS.
- M. Abbas, B. P. Raoc, V. Reddy and C. Kim, Appl. Catal., B, 2009, 89, 527 CrossRef.
- W. P. Kwan and B. M. Voelker, Environ. Sci. Technol., 2003, 37, 1150 CrossRef CAS PubMed.
- R. Sharifi Aliabadi and N. O. Mahmoodi, RSC Adv., 2016, 6, 85877 RSC.
- A. R. Moosavi-Zare, M. A. Zolfigol and A. Mousavi-Tashar, Res. Chem. Intermed., 2016, 42, 7305 CrossRef CAS.
- R. Sharifi Aliabadi and N. O. Mahmoodi, RSC Adv., 2016, 6, 85877 RSC.
- G. Vasuki and K. Kumaravel, Tetrahedron Lett., 2008, 49, 5636 CrossRef CAS.
- G. M. Reddy and J. R. Garcia, J. Heterocycl. Chem., 2017, 54, 89 CrossRef CAS.
- M. N. Nasr and M. M. Gineinah, Arch. Pharm., 2002, 335, 289 CrossRef CAS PubMed.
- S. A. El-Assiery, G. H. Sayed and A. Fouda, Acta Pharm., 2004, 54, 143 CAS.
- X. H. Yang, P. H. Zang, Z. M. Wang, F. Jing and Y. H. Zhou, Ind. Crops Prod., 2014, 52, 413 CrossRef CAS.
- M. Farahi, M. Davoodi and M. Tahmasebi, Tetrahedron Lett., 2016, 57, 1582 CrossRef CAS.
- M. Farahi, F. Tamaddon, B. Karami and S. Pasdar, Tetrahedron Lett., 2015, 56, 1887 CrossRef CAS.
- M. Farahi, B. Karami, R. Keshavarz and F. Khosravian, RSC Adv., 2017, 7, 46644 RSC.
- H. Mohamadi Tanuraghaj and M. Farahi, RSC Adv., 2018, 8, 27818 RSC.
- M. Farahi, B. Karami, Z. Banaki, F. Rastgoo and K. Eskandari, Monatsh. Chem., 2017, 148, 1469 CrossRef CAS.
- S. Akrami, B. Karami and M. Farahi, RSC Adv., 2017, 7, 34315 RSC.
- M. C. Mascolo, Y. Pei and T. A. Ring, Materials, 2013, 6, 5549 CrossRef CAS PubMed.
- F. Nemati, M. Heravi and A. Elhampour, RSC Adv., 2015, 5, 45775 RSC.
- A. Amoozadeh, S. Golian and S. Rahimi, RSC Adv., 2015, 5, 45974 RSC.
- C. Santato, M. Odziemlowski, M. Ulmann and J. Augustynski, J. Am. Chem. Soc., 2001, 123, 10639 CrossRef CAS PubMed.
- M. Farahi, B. Karami, I. Sedighimehr and H. Mohamadi Tanuraghaj, Chin. Chem. Lett., 2014, 25, 1580 CrossRef CAS.
- G. M. Reddy and J. R. Garcia, J. Heterocycl. Chem., 2017, 54, 89 CrossRef CAS.
- J. F. Zhou, S. J. Tu, H. Q. Zhu and S. J. Zhi, Synth. Commun., 2002, 32, 3363 CrossRef CAS.
- H. Mecadon, M. R. Roham, M. Ranjbangshi and B. Myrbon, Tetrahedron Lett., 2011, 52, 2523 CrossRef CAS.
- S. W. Kshirsagar, N. R. Patil and S. D. Samant, Synth. Commun., 2011, 41, 1320 CrossRef CAS.
- M. M. Heravi, N. Javanmard, H. A. Oskooi and B. Baghernejad, Gazi University Journal of Science, 2011, 24, 227 Search PubMed.
- M. M. Heravi, A. Ghods, F. Derikvand, K. Bakhtiari and F. F. Bamoharram, J. Iran. Chem. Soc., 2010, 7, 615 CrossRef CAS.
Footnote |
† Electronic supplementary information (ESI) available. See DOI: 10.1039/c8ra06886k |
|
This journal is © The Royal Society of Chemistry 2018 |
Click here to see how this site uses Cookies. View our privacy policy here.