DOI:
10.1039/C8RA05164J
(Paper)
RSC Adv., 2018,
8, 25445-25455
Porous Fe0/C ceramsites for removal of aqueous Pb(II) ions: equilibrium, long-term performance and mechanism studies†
Received
16th June 2018
, Accepted 10th July 2018
First published on 16th July 2018
Abstract
This study reports the equilibrium, long-term performance and mechanisms in removing Pb(II) ions by metallic iron/carbon (Fe0/C) ceramsites (FCC). The Pb(II) removal equilibrium data was analyzed using the Langmuir, Freundlich and Dubinin–Radushkevich isotherms. At the FCC dosage of 1.14 g L−1, 95.97% of Pb(II) ions were removed from 50 mg L−1 Pb(II) solution at initial pH 6.0. The Langmuir isotherm could fit well with the data at initial pH 3.0 with a maximum monolayer adsorption capacity of 112.36 mg g−1 at 25 °C, while the data obtained at initial pH 6.0 could be described by the Freundlich model, indicating multilayer adsorption of Pb species on the FCC. Column tests demonstrated that FCC achieved the highest Pb(II) removal of 65.86% after 12 days' run compared to 32.35% for Fe0/activated carbon couples and only 1.24% for activated carbon. The X-ray diffraction and X-ray photoelectron spectroscopy analysis revealed that the PbO (dominant Pb species), Pb0, asisite and plumbojarosite appeared after Pb(II) removal. Scanning electron microscopy with energy dispersive X-ray spectroscopy showed that PbO particles with numerous structures were deposited on the FCC surface in a high amount. The decrease of the Fe/C mass ratio from 7.5 : 1 to 0.298
:
1 revealed that microscale Fe0 could been readily corroded by forming galvanic couples between Fe0 and carbon. The mechanisms of Pb(II) removal by the FCC were proposed.
1. Introduction
Nanoscale zero-valent iron (nZVI) is very effective in the removal of heavy metal ions with numerous pathways, including adsorption, complexation, (co-)precipitation and chemical reduction.1–3 Although the nZVI exhibits high efficiencies in removing heavy metal ions, some drawbacks related to ultra-fine particle size are challenging the suitability of nZVI. The decrease of particle size is coupled with rapid corrosion of metallic iron (Fe0) and the formation of corrosion products, which results in particle cementation and short service time for nZVI.4,5 Moreover, the high redox reactivity of nZVI makes it potentially harmful to living organisms such as lung cells.6
Microscale Fe0 materials (iron scraps or sponge iron) are widely applied in wastewater and groundwater treatment by coupling with non-expansive materials such as sands and pumices.6,7 However, in comparison with nZVI, μm and mm sized Fe0 particles show much lower reactivity due to slow corrosion of Fe0 in the Fe0/H2O system. Thus, some methods such as using bimetallics, ultrasound enhancement and combining activated carbon (AC) with Fe0 materials have been attempted to increase removal efficiencies of various pollutants.8–10 Among these alternatives, by coupling Fe0 with AC, the corrosion of Fe0 can be remarkably enhanced as iron–carbon microelectrolysis reactions occur by forming microscopic galvanic cells.10–12 The electrons of galvanic cells are supplied by the Fe0 corrosion, and half-cell reactions can be represented as eqn (1)–(3). The microelectrolysis process has been widely attempted to degrade organic pollutants,12,13 but its application in removing heavy metal ions is relatively rare. In previous reports, high removal efficiencies of heavy metals have been achieved by Fe0/AC couples. Dou et al.10 found that Fe0/AC couples were capable of removing 100% of aqueous As(V), whereas only about 60% and 5% of As(V) was removed by Fe0 and AC, respectively. Yuan et al.11 observed that Fe0/AC-ceramsites achieved higher Pb(II) removal (99.5%) compared to AC-ceramsite (7.8%) and Fe0-ceramsite (39.6%).
Anode (Fe0):
|
Fe − 2e− → Fe2+, Eθ (Fe2+/Fe) = −0.44 V
| (1) |
Cathode (AC):
|
Acid with oxygen: O2 + 4H+ + 4e− → 2H2O, Eθ(O2/H2O) = +1.23 V
| (2) |
|
Neutral to alkaline with oxygen: O2 + 2H2O + 4e− → 4OH−, Eθ(O2/OH−) = +0.40 V
| (3) |
Nevertheless, most of reported Fe0/AC couples were just formed by physically mixing Fe0 powders and granular AC in water.10,14 As the corrosion of Fe0 is a volumetric expansion process, mixed Fe0/AC filters in flow-through treating systems may clog after a short service time.15 Gelatinous iron hydroxides can cement Fe0 and AC particles, resulting in the compaction of fillings.16 By integrating Fe0 materials and AC in one pellet, these disadvantages may be avoided. The microelectrolysis process using integrated Fe0/AC filters has been applied in degradation of organic pollutants with advantages of low pressure drop and long-term operation.13,17 However, these Fe0/AC microelectrolysis filters are rarely applied in removing heavy metals. Moreover, Fe0/AC couples should be costly due to the usage of commercial Fe0 powders and AC although AC can be fabricated from various solid wastes.18−20 Therefore, the development of cost-effective and integrated microelectrolysis filter from cheap raw materials is very expected, and its evaluation of heavy metal removal is necessary.
Lead in the wastewater is extremely toxic to human beings and ecosystems.21–23 Lead can damage nervous systems, kidneys, reproductive systems and other organs.24 Therefore, it is of great concern for developing cost-effective technologies to treat lead contaminated wastewaters.25
In this work, porous Fe0/C ceramsite (FCC), a novel microelectrolysis filter, has been prepared by the direct reduction roasting of magnetite, coal and paper mill sludge. Metallic iron (Fe0) generated from in situ reduction of magnetite, and carbon particles achieved from the carbonization of coal, are served as anode and cathode of the microelectrolysis filter, respectively. Compared to reported Fe0/AC couples or filters, the FCC in this work is cost-effective and eco-friendly by using cheap raw materials and solid waste (paper mill sludge). The objectives of this work are (1) to investigate the effect of initial solution pH on Pb(II) removal by the FCC; (2) to analyze equilibrium data of Pb(II) removal to understand adsorption characteristics of the FCC; (3) to evaluate long-term performance of Pb(II) removal with column tests; (4) to propose Pb(II) removal mechanisms by the FCC with FESEM/EDX, XRD and XPS analysis.
2. Materials and methods
2.1 Materials
The magnetite with Fe content of 66.32% was used as the source of metallic iron. The paper mill sludge was collected from the MCC Paper Yinhe Company of China. The contents of volatiles, fixed carbon and ashes of dried sludge were 42.56%, 2.23% and 55.21%, respectively. The coal with fixed carbon of 58.23% was served as the reducing agent and precursor of cathode. Lead nitrate (Pb(NO3)2), sodium silicate (Na2SiO3·9H2O), Fe0 powders and quartz sands were purchased from Sinopharm Chemical reagent Co. Ltd. (China). All reagents used were of analytical grade (AR).
Fe0 powders were available as fillings with a particle size of between 0.5 and 2.0 mm. The Fe content as specified by the supplier was 97.46%. Quartz sands with SiO2 content of 98.23% were used with a particle size between 0.65 and 0.85 mm. Cylindrical activated carbon (AC) with 3 mm diameter and 4–6 mm height was received from Jinling Environmental Technology Co. Ltd. (China). The AC prepared from coal had a specific surface area of 864.25 m2 g−1. Fe0 powders, quartz sands and AC were used without further treatment.
2.2 Preparation of Fe0/C ceramsites
Fig. S1† (see in the ESI) showed the fabrication procedure of Fe0/C ceramsites (FCC). The magnetite, coal, paper mill sludge and sodium silicate were mixed with a mass ratio of 55
:
14
:
25
:
6. By adding 10% deionized water, wet mixtures were pressed into spheroidal pellets in a pelletizer. Then wet pellets were dried to constant weight at 105 °C in an oven. When the roasting temperature reached 1200 °C, dried pellets in a graphite crucible were transferred into a muffle furnace, and sintered at 1200 °C for 120 min at an oxygen deficient reduction atmosphere. After the calcination, the pellets were cooled down to 300 °C in the furnace, and then taken out to further cool down in air. Finally, porous Fe0/C ceramsites as shown in Fig. S2† were fabricated.
2.3 Batch experiments
By dissolving appropriate amount of Pb(NO3)2 in deionized water, the stock solution with Pb(II) concentration of 800 mg L−1 was prepared, then diluted to obtain desired concentrations. To perform batch tests, spheroidal FCC was firstly crushed and sieved to obtain FCC powders with a size of <0.5 mm. 0.798 g FCC was added into 700 mL Pb(II) solution in a 1000 mL conical flask. The flask was stirred in a thermostated orbital shaker at 25 °C and 190 ± 5 rpm to perform adsorption experiments. The effect of initial pH on Pb(II) removal was performed at the Pb(II) concentration of 50 mg L−1 and FCC dosage of 1.14 g L−1. The initial pH was chosen as 2.0, 3.0, 4.0, 5.0 and 6.0, respectively. The pH was adjusted by adding 0.1 M HCl or 0.1 M NaOH solution. The adsorption equilibrium tests were conducted at initial pH of 3.0 and 6.0 with FCC dosage of 1.14 g L−1. The contact time was 150 min to achieve the adsorption equilibrium. The adsorption capacity qt and qe were calculated by following expressions: |
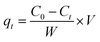 | (4) |
|
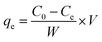 | (5) |
where qt and qe (mg g−1) were the amount of Pb(II) ions adsorbed on the FCC at time t (min) and equilibrium, respectively; C0, Ct and Ce were the Pb(II) concentration (mg L−1) at initial, time t and equilibrium, respectively; V was the solution volume (L), and W was the added amount (g) of the FCC.
2.4 Column experiments
Glass columns of 25 mm inner diameter and 250 mm length were used. A porous glass distributor was fixed at the bottom. From the bottom to the top, the columns were packed as following: (1) fine sands (H1 = 20 mm), (2) a reaction zone (H2 = 150 mm), and (3) resting solution (H3 = 80 mm). The reaction zones were packed with 74.46 g of spheroidal FCC in column 1, 40.41 g of cylindrical AC in column 2, and 5.08 g AC, 38.11 g Fe0 powders and 58.03 g sands in column 3, respectively. For the comparison, the weights of metallic iron and carbon in columns 1 and 3 were set to be same, and sands were filled in column 3 to make same height of reaction zone in column 1 and 3.
Fig. 1 showed the schematic diagram of column experiments. 50 mg L−1 Pb(II) solution with initial pH 6.0 was pumped upwards into the columns from a solution reservoir using a peristaltic pump (BT-300CA/153Y). Tygon tubes were used to connect the solution reservoir, pump, column and outlet. The column experiments were conducted at room temperature (24 ± 3 °C) for 12 days. A stable flow rate of 2.0 mL min−1 was maintained throughout the experiment. In batch and column tests, aqueous samples were firstly filtered through a micro filter with a pore size of 0.45 μm. The Pb(II) concentration was then determined by inductively coupled plasma atomic emission spectrometer (ICP-AES, IRIS Intrepid II XSP).
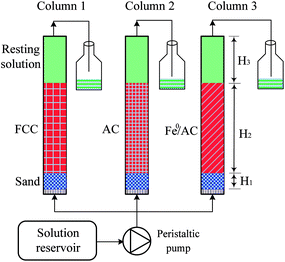 |
| Fig. 1 Schematic diagram of column experiment design. | |
2.5 Analysis and characterization
The carbon content of Fe0/C ceramsites (FCC) was detected with a high frequency combustion and infrared absorption method. The content of metallic iron in the FCC was determined according to Chinese Standard GB/T 6730-1986. The compressive strength of FCC was determined by an intelligent particle strength analyzer (DL-III, China).
The morphology and elemental mapping EDX of fabricated FCC were performed by a scanning electron microscope equipped with an energy-dispersive X-ray spectrometer (SEM/EDX, Carl Zeiss EVO18). But the morphologies and element compositions of the FCC after Pb(II) removal were obtained by a field emission scanning electron microscope equipped with an energy-dispersive X-ray spectrometer (FESEM/EDX, JSM-6701F/Thermo NS7). The crystalline phases of the FCC before and after Pb(II) removal were characterized via X-ray diffraction (XRD, Dmax-RD12 kW, Rigaku) under the conditions of 40 kV, 100 mA and Cu Kα radiation. The data were collected with a 2θ range of 10–90°. The XPS analysis was performed with an X-ray photoelectron spectrometer (Kratos AXIS Ultra DLD) using a monochromatic Al Kα radiation. The binding energy was recorded with a reference to C 1s peak at 284.6 eV of the surface adventitious carbon. XPS data was analyzed using the XPSPEAK41 software. Prior to the FESEM/EDX, XRD and XPS analysis, FCC samples obtained after Pb(II) removal for 12 days were dried in a N2 atmosphere at 105 °C for 2 h.
2.6 Equilibrium modeling
In this work, the equilibrium data of Pb(II) removal was analyzed in terms of the Langmuir, Freundlich and Dubinin–Radushkevich isotherms, respectively. The Langmuir isotherm equation in linear form is: |
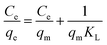 | (6) |
where qm (mg g−1) is a maximum adsorption capacity of Pb(II) ions at complete monolayer coverage, and KL (L mg−1) is a Langmuir constant related to the adsorption energy. The Langmuir isotherm assumes the monolayer coverage of absorbent surface.26–28
The linear form of Freundlich model can be written as:
|
log qe = log KF + 1/n log Ce
| (7) |
where
KF (mg
1−(1/n) L
1/n g
−1) is a measure of the adsorption capacity of adsorbent, and 1/
n is the Freundlich exponent related to adsorption intensity. The Freundlich isotherm is generally applied both monolayer (chemisorption) and multilayer (physisorption) adsorption on heterogeneous surfaces, and the surface sites of the adsorbent have different binding energies.
29–32
The Dubinin–Radushkevich (D–R) isotherm is applied to evaluate if the nature of adsorption is physical or chemical. The linear form of D-R isotherm is written as:
|
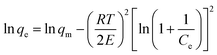 | (8) |
where
qmax (mol g
−1) is the theoretical saturation capacity,
Ce (mol L
−1) is the Pb(
II) concentration at equilibrium,
R (8.314 J mol
−1 K
−1) is the universal gas constant,
T (K) is the absolute temperature,
E (kJ mol
−1) is the mean free energy of adsorption.
33–35
3. Results and discussion
3.1 Characterization of Fe0/C ceramsites
The XRD pattern of Fe0/C ceramsites (FCC) in Fig. 2 showed that the peaks with a 2θ degree at 44.62°, 65.23°, 82.43° corresponded to (110), (200) and (211) lattice planes of metallic iron (Fe0), respectively. No diffraction peaks assigned to magnetite were found, revealing the complete reduction of magnetite to Fe0 in the direct reduction roasting.36
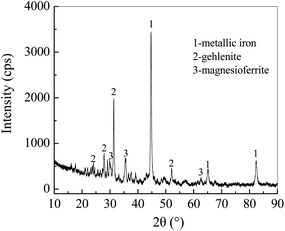 |
| Fig. 2 XRD pattern of fabricated Fe0/C ceramsites. | |
As shown in Fig. 3(a), round white particles were in situ generated Fe0 particles with a size of less than 5 μm. The elemental EDX mapping image (Fig. 3(b)) revealed that light blue particles (Fe0) were uniformly distributed on the FCC surface, and red particles (carbon) with a size of around 10 μm were closely contacted with Fe0 particles. The close distribution of anode (Fe0) and cathode (carbon) in the FCC can facilitate electron transfer in galvanic cells. As summarized in Table S1,† the content of metallic iron in the FCC reached 52.18% with a Fe/C mass ratio of 7.5
:
1. Higher content of metallic iron may lead to longer reaction term of iron–carbon microelectrolysis.10,37 As illustrated in Fig. 3, numerous pores or fractures in the FCC were observed, which resulted in a large porosity of 46.37 vol% (Table S1†). In previous report of fly ash supported zero-valent iron prepared by direct reduction with coke, the Fourier transform infrared spectroscopy (FTIR) analysis demonstrated the existence of surface functional groups such as –OH, carboxyl and C–H groups.38 Thus, these functional groups might also appear on FCC surface due to similar fabrication method. The compressive strength of the FCC reached 53.9 MPa, and the high mechanical strength should be attributed to the generation of gehlenite (2CaO·Al2O3·SiO2) after high temperature reduction roasting.
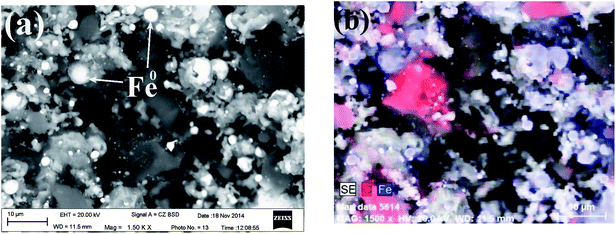 |
| Fig. 3 SEM image (a) and elemental EDX mapping image (b) of Fe0/C ceramsites. | |
3.2 Effect of initial pH on Pb(II) removal
The solution pH strongly influences the Pb(II) removal as it can affect the Fe0 corrosion, surface charge of Fe0/C ceramsite (FCC) and speciation of Pb(II). As shown in Fig. 4(a), the Pb(II) removal rapidly increased in the first 10 min, and then gradually incremented until an adsorption equilibrium reached after 60 min. As initial pH rose from 2.0 to 6.0, the removal rate increased from 74.94% to 95.97%, showing the pH-sensitivity in Pb(II) removal by the FCC. The pH-sensitivity in removing heavy metal ions was also observed by other zero-valent iron sorbents.1,2,11 The corrosion of Fe0 can readily release active Fe(II) and Fe(III) ions, which are further hydrolyzed to generate iron hydroxides (e.g., Fe(OH)3) at the pH > 4.0. The iron hydroxides can effectively remove heavy metal ions by the adsorption, ion exchange and co-precipitation.1,13
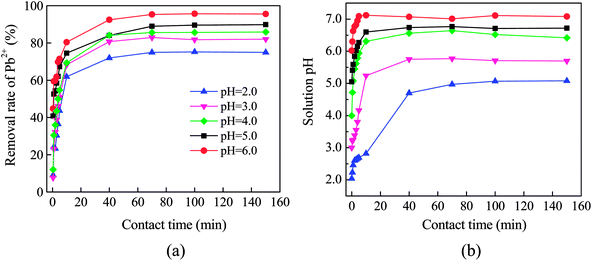 |
| Fig. 4 Effect of initial pH on the Pb(II) removal by Fe0/C ceramsites (a) and variation of solution pH with contact time (b). | |
As shown in Fig. 4(b), the solution pH increased as the removal process proceeded. The equilibrium pH had ascended up to 5.08, 5.71, 6.42, 6.72 and 7.08 from initial pH of 2.0, 3.0, 4.0, 5.0, 6.0, respectively. Other authors also observed the increase of solution pH while immersing Fe0/AC couples in water.11,13,14 The half-cell reactions given in eqn (2) and (3) showed the consumption of H+ ions or release of OH− ions into solution, resulting in the increase of solution pH. Additionally, the dissolution of surface substances and ion exchange of surficial OH− with metal ions also contributed to the elevation of solution pH for Fe0 sorbents.39,40
As the pH can significantly change the speciation of Pb(II), the increase of solution pH may lead to the precipitation of Pb(OH)2. In this case, for the Pb(NO3)2 solution with Pb(II) concentration of 50 mg L−1, the precipitation may occur at pH = 6.67 (Ksp,Pb(OH)2 = 1.2 × 10−15 at 25 °C). As shown in Fig. 4(b), the precipitation of Pb(OH)2 was expected while initial pH was higher than 4.0. Especially, the precipitation would greatly contribute to the Pb(II) removal at initial pH 6.0 since the equilibrium pH had increased up to 7.08.
3.3 Adsorption isotherms
The equilibrium data of Pb(II) removal by the FCC was given in Fig. S3†. The linearized fitting of Langmuir, Freundlich and Dubinin–Raduskevich isotherms was shown in Fig. 5 with isotherm parameters summarized in Table 1. The regression coefficients of three models indicated that the data at initial pH 3.0 could be fitted well with the Langmuir isotherm, but the Freundlich equation was the best to fit the data at initial pH 6.0. The exponent of 1/n between 0 < 1/n < 1.0 represented that the adsorption of Pb(II) on the FCC well obeyed the Freundlich model.1,29,41 In the Langmuir model, the calculated maximum adsorption capacity (qm,cal) was close to experimental one (qm,exp) at initial pH 3.0, but the qm,cal was much higher than the qm,exp at initial pH 6.0. The parameter KL represents the interaction intensity between the adsorbent and the adsorbate.42,43 The larger value of KL at initial pH 3.0 indicated the higher affinity of Pb species on the FCC surface at pH 3.0 than 6.0. The results demonstrated the monolayer coverage of Pb species on the FCC at initial pH 3.0, but multilayer adsorption occurred on FCC surface at initial pH 6.0.29 The precipitation of lead oxides (hydroxides) on the FCC (physisorption) might occur at initial pH 6.0, which resulted in multilayer adsorption of Pb species.
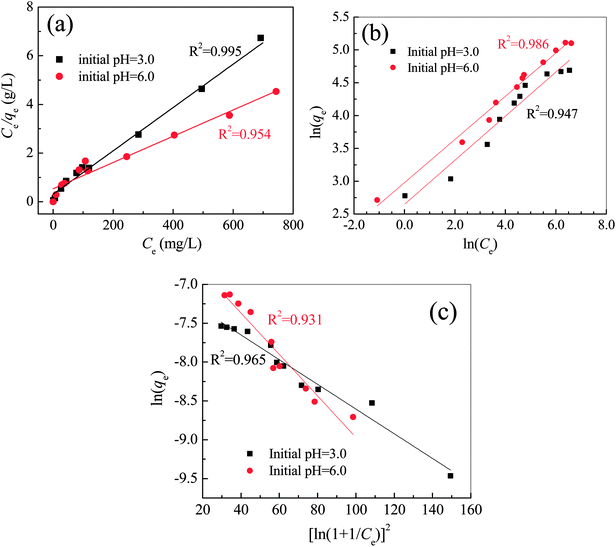 |
| Fig. 5 Linearized fitting of Langmuir (a), Freundlich (b) and Dubinin–Raduskevich (c) isotherms for the Pb(II) removal by Fe0/C ceramsites at 25 °C. | |
Table 1 Regression coefficients and isotherm parameters for Pb(II) removal at initial pH 3.0 and 6.0 by Fe0/C ceramsites at 25 °C
Isotherm |
Parameters |
pH = 3.0 |
pH = 6.0 |
Langmuir 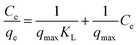 |
qm,cal (mg g−1) |
112.36 |
185.53 |
qm,exp (mg g−1) |
106.64 |
159.68 |
KL (L mg−1) |
0.0285 |
0.00987 |
R2 |
0.995 |
0.954 |
Freundlich ln qe = 1/n ln Ce + ln KF |
KF (mg1−(1/n) L1/n g−1) |
13.41 |
19.87 |
1/n |
0.271 |
0.383 |
R2 |
0.947 |
0.986 |
Dubinin–Raduskevich 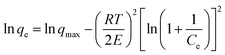 |
qmax (mol g−1) |
0.90 × 10−3 |
1.84 × 10−3 |
E (kJ mol−1) |
13.89 |
7.68 |
R2 |
0.965 |
0.931 |
In the Dubinin–Radushkevich model, the magnitude of E is used to reveal the mechanism of adsorption reactions.44–46 An adsorption process is dominated by chemisorption/ion exchange if E is in the range of 8–16 kJ mol−1, otherwise physical forces may affect the adsorption in the case of E < 8 kJ mol−1.33,47 Therefore, in this case, the Pb(II) removal by the FCC at initial pH 3.0 was controlled by the chemisorption/ion exchange as the E value reached 13.89 kJ mol−1. However, physical forces might contribute to Pb(II) removal at initial pH 6.0 as the E value was reduced to 7.68 kJ mol−1. The E value further suggested that the Pb(II) removal by the FCC at initial pH 3.0 was a chemical nature (chemisorption/ion exchange), but the physical adsorption might be involved in Pb(II) removal at initial pH 6.0.1,48
In this work, the qm,cal of Pb(II) removal by the FCC reached 112.36 mg g−1 at initial pH 3.0 and at 25 °C. For the removal of Pb(II) ions, the maximum monolayer adsorption capacities of various adsorbents were given in Table 2. The adsorption capacity of the FCC was higher than that of carbon materials such as activated carbon and carbon nanotube, and close to that of iron–carbon composites. By considering the usage of cheap raw materials and solid waste in the fabrication of FCC, this novel microelectrolysis filter may be a promising sorbent in wastewater treatment.
Table 2 Comparison studies of maximum monolayer adsorption of Pb(II) ions on various adsorbents and their experimental conditions
Adsorbents |
qm (mg g−1) |
Experimental conditions |
Reference |
Sorbent dosage (g mL−1) |
pH |
T (K) |
Mn3O4-coated activated carbon |
59.52 |
0.2/200 |
5.0 |
303 |
49 |
Activated carbon from apple pulp |
15.96 |
0.1/25 |
5.0 |
298 |
50 |
Iron-activated carbon nanocomposite |
121.9 |
0.05/50 |
6.0 |
298 |
29 |
Cyclone steel dust |
39.8 |
0.1/50 |
5.0 |
298 |
51 |
Modified carbon nanotubes |
100.0 |
0.2/1000 |
6.0 |
303 |
52 |
Chitosan schiff's base@Fe3O4 |
62.5 |
0.5/25 |
5.0 |
303 |
53 |
Chitosan functionalized magnetic particles |
498.6 |
0.1/100 |
6.0 |
303 |
54 |
Sulfuric acid modified Caryota urens seeds |
93.7 |
0.5/100 |
5.0 |
303 |
55 |
Microalga Rhizoclonium hookeri |
81.7 |
0.1/100 |
4.5 |
298 |
56 |
Fe0/C ceramsites |
112.36 |
0.114/100 |
3.0 |
298 |
This work |
3.4 Pb(II) removal in column experiments
Fig. 6 depicted the time-dependent evolution of Pb(II) removal by the FCC, AC and Fe0/AC couples, respectively. The AC achieved the lowest removal of Pb(II). The breakthrough occurred at the fourth day and only 1.24% of Pb(II) removal was achieved after 12 days' run. This poor performance was attributed to low adsorption capacity of Pb(II) ions for unmodified AC as given in Table 2.49,50 In the first 4 days, the Pb(II) removal rate for Fe0/AC couples was slightly higher than that for the FCC. For the FCC, the Fe0 and carbon particles were embedded into ceramsites, the diffusion of Pb(II) ions from bulk solution to reactive sites in the inner surface of ceramsites must be limited. However, for Fe0/AC couples, Fe0 and AC particles were fully contacted with Pb(II) solutions, promoting significant removal of Pb(II) ions at initial stage. However, after 4 days, the Pb(II) removal rate for Fe0/AC couples rapidly reduced. At the end of column test (12 days), the Pb(II) removal rate for Fe0/AC couples was decreased to just 32.35%, but the value for the FCC was still as high as 65.86%. The result revealed that the FCC had good long-term run performance in the Pb(II) removal.
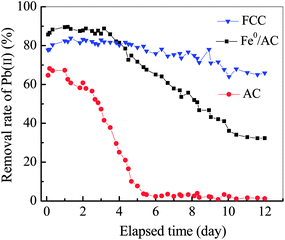 |
| Fig. 6 Variation of removal rate of Pb(II) ions with elapsed time by Fe0/C ceramsites (FCC), Fe0 powders/activated carbon (Fe0/AC) and activated carbon (AC). | |
As shown in Fig. 4(b), the solution pH had increased from 6.0 at initial to 7.08 at equilibrium. The iron hydroxides must be formed in column tests as the precipitation of Fe(III) ions occurs even at pH 2.0–3.0 (Ksp = 4.0 × 10−38 for Fe(OH)3 at 25 °C). For packed Fe0/AC couples, the migration distance of Fe(OH)3 colloids was short because the pore space of packed bed was very limited due to small particle size of Fe0 particles, causing particle cementation and flow disturbance.15,16 Nevertheless, the pore space in FCC packed bed was large enough to allow long distance migration of Fe(OH)3 colloids due to large size (5 mm) of spheroidal FCC. Therefore, the cementation of FCC bed should be significantly alleviated, which supported high Pb(II) removal rate in 12 days' run. However, as seen in Fig. S4,† iron (red) and lead (white) (hydro)oxides were observed to be coated on FCC surface, which might hinder the mass transfer in Pb(II) removal process.
3.5 Lead removal mechanisms
3.5.1 XRD analysis. The XRD analysis was conducted to characterize crystalline phases of Fe0/C ceramsites (FCC) after the Pb(II) removal. By comparing XRD patterns of the FCC before (see in Fig. 2) and after (see in Fig. 7) the Pb(II) removal, it was clear that two XRD patterns were quite different, indicating the occurrence of significant crystalline phase changes in the Pb(II) removal. The diffraction intensity of peaks assigned to Fe0 remarkably decreased, showing the reduced content of metallic iron in the FCC after the removal of Pb(II). As shown in Fig. 7, the peaks with a 2θ degree at 15.04°, 29.07°, 30.29°, 32.56°, 37.81°, 49.14°, 50.69°, 53.11° corresponded to the (200), (111), (100), (020), (021), (202), (022) and (311) lattice planes of massicot (PbO), respectively. The peaks with a 2θ at 31.37°, 36.31°, 52.11°, 62.22° could be assigned to the (111), (200), (220) and (311) lattice planes of metallic lead (Pb0), respectively. In addition, asisite (Pb7O8Cl2), plumbojarosite (Pb(Fe3(OH)6(SO4)2)2) and iron oxyhydroxide (α-FeOOH) were also presented with a lower fraction. By comparing the diffraction intensity of these crystals, it could find that the PbO was dominant Pb containing species.
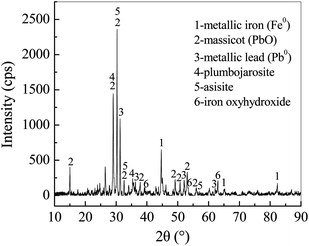 |
| Fig. 7 XRD pattern of Fe0/C ceramsites in the removal of Pb(II) ions after 12 days. | |
The formation of Pb0 suggested that Pb(II) ions could be removed via the reduction of Pb(II) to Pb0 by the FCC. Since the standard reduction potential of Pb(II)/Pb0 (−0.1263 V) is more positive than that of Fe(II)/Fe0 (−0.4402 V),57 Pb(II) can be reduced to Pb0 by the Fe0 via the electrochemical reaction. This result coincided well with previous studies in which Pb0 was formed by presenting n-ZVI in Pb(II) solution.11,58 As the corrosion of microscale Fe0 embedded in the FCC could be enhanced with the galvanic couple effect of Fe0 and carbon, released Fe(II) ions could coexist with Pb(II) ions in bulk solution. Because of their close Ksp (1.2 × 10−15 for Pb(OH)2, 8.0 × 10−16 for Fe(OH)2 at 25 °C) and neutral solution pH (above 7.0), Fe(II) and Pb(II) ions were (co-)precipitated to generate hydroxides on both internal and exterior surface of the FCC. In the previous studies, amorphous Pb(OH)2 was observed on supported n-ZVI composites,58,59 and cerussite (Pb(CO3)2) appeared on biochars.60 But no characteristic peak of lead hydroxides and cerussite appeared in Fig. 7. The thermogravimetric analysis (TGA) had demonstrated that the decomposition temperature of cerussite to PbO and of Pb(OH)2 to PbO were 223–361 °C and <160 °C, respectively.60,61 Therefore, in this work, thermodynamically unstable Pb(OH)2 might be formed as an intermediate which was subsequently transformed into stable PbO via dehydration in sample heating process.59 The presence of PbO and Pb0 as final products indicated that the (co-)precipitation and reduction occurred in the Pb(II) removal by the FCC.
3.5.2 XPS analysis. XPS analysis was conducted to reveal chemical states of Fe and Pb elements on Fe0/C ceramsites (FCC) after the Pb(II) removal. As shown in Fig. 8(a), the elements of Fe, O, Pb, C, Si, Cl and Ca were observed. The high peak intensity of Pb 4f, C 1s and O 1s exhibited the high content of these elements on FCC surface. The high-resolution Fe 2p spectrum (Fig. 8(b)) could be deconvoluted into four peaks at 710.1, 712.3, 722.9 and 725.5 eV. The peaks at 725.5 and 722.9 eV corresponded to the binding energy of 2p1/2 of Fe(III) and Fe(II) species, respectively.62,63 The peaks at 712.3 and 710.2 eV could be assigned to the 2p3/2 of Fe(III) and Fe(II) species, respectively.64 The result showed the coexistence of Fe(III) and Fe(II) species on the FCC surface. However, no peak at around 706.0 eV was observed, indicating the disappearance of Fe0 on FCC surface after Pb(II) removal.2 Since the presence of Fe0 in the FCC after Pb(II) removal was proved by XRD analysis, it clearly indicated that Fe0 particles on FCC surface were completely corroded to release Fe(II) and Fe(III) ions into solution.
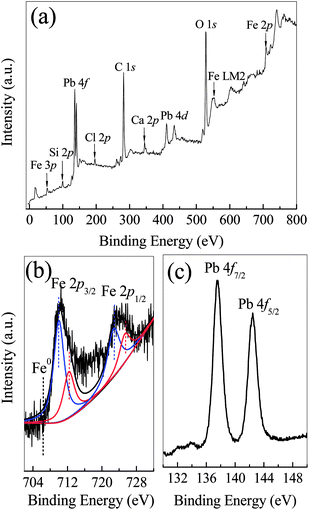 |
| Fig. 8 XPS analysis of Fe0/C ceramsites in the removal of Pb(II) ions after 12 days: wide-scan survey (a) and high-resolution XPS lines of Fe 2p (b) and Pb 4f (c). | |
The high-resolution Pb 4f spectrum was illustrated in Fig. 8(c). Two main peaks at 137.7 and 142.6 eV could be assigned to binding energies of 4f7/2 and 4f5/2 of PbO, respectively.65 No any characteristic peak of Pb0 was observed. The lead species formed by n-ZVI had been quantitatively investigated with a sequential extraction procedure, which revealed a core–shell structure with Pb0 and Fe0 as the inner core and with PbO as the external shells.66 While most of active sites of Fe0 particles in the FCC were covered with the shells, the reduction of Pb(II) to Pb0 might cease.
3.5.3 FESEM/EDX analysis. Fig. 9 showed FESEM/EDX observations for morphologies and elemental constitutions of the FCC after Pb(II) removal for 12 days. As illustrated in Fig. 9(a), ridge-like structures were original FCC materials. Some agglomerates, consisting of much smaller particles, were accumulated into the pores of these ridges. As revealed by EDX analysis at selected area (Fig. 9(b)), these agglomerates were mainly composed with Pb, O and C elements with a low proportion of Fe. As demonstrated by XRD and XPS analysis, the PbO was dominant Pb containing species on the FCC. Therefore, observed agglomerates should be mainly composed of PbO crystals due to extremely high content of Pb element. The Fe/C mass ratio of 0.298
:
1 at selected area was much lower than that of 7.5
:
1 in original FCC, which suggested that the Fe0 was significantly corroded in the microelectrolysis reactions while remaining carbon (cathode) on FCC surface.
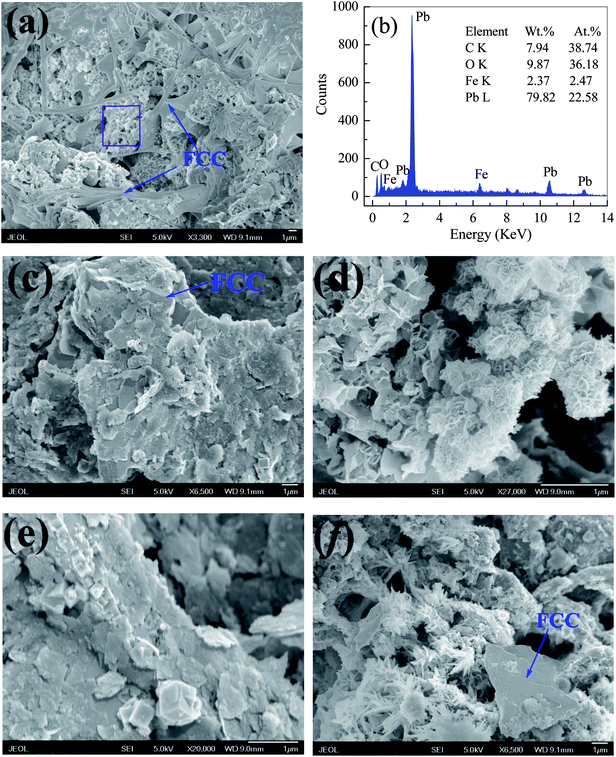 |
| Fig. 9 SEM images of Fe0/C ceramsites after the Pb(II) removal for 12 days and the EDX spectrum at selected area. | |
As shown in Fig. 9(c)–(f), PbO agglomerates had numerous structures of plate (c), flower (d), cuboid (e) and dentrite (f). Especially, a large amount of plate-like PbO particles was deposited on FCC surface in Fig. 8(c) and (e). Actually, PbO with plentiful structures, such as plate and dentrite, can be formed in the precipitation.67,68 Since lots of PbO particles were coated on the inner and exterior surface of the FCC, it could reasonably infer that the precipitation of PbO might be a key pathway in removal of Pb(II) ions by the FCC.
3.5.4 Proposed mechanisms of Pb(II)removal. Compared to n-ZVI, microscale Fe0 was much less active and very hard to be oxidized by Pb(II) and H2O.66 Nevertheless, by forming galvanic couples between Fe0 and carbon, microscale Fe0 in the FCC was readily corroded to release Fe(II) and to deplete H+ ions, which promoted subsequent Pb(II) removal. As shown in Fig. 10, the removal of Pb(II) ions by the FCC might involve four pathways: (1) the reduction of Pb(II) to Pb0 by Fe0; (2) the precipitation of PbO; (3) formation of Pb containing compounds such as asisite and plumbojarosite by reacting with Cl−, SO42− and Fe(III) ions; (4) ion exchange with generated iron hydroxides (eqn (9) and (10)).14 |
Fe(OH)2 + Pb2+ → Fe(OH)OPb+ + H+
| (9) |
|
Fe(OH)3 + Pb2+ → Fe(OH)2OPb+ + H+
| (10) |
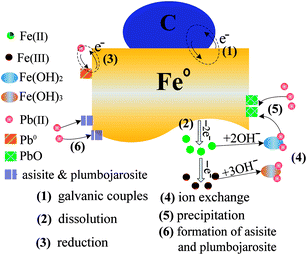 |
| Fig. 10 Proposed mechanism in removing Pb(II) ions from aqueous solution by Fe0/C ceramsites. | |
4. Conclusions
Porous Fe0/C ceramsites (FCC), with the integrated structure of Fe0 (anode) and carbon (cathode) of a microelectrolysis filter, were fabricated from magnetite, coal and paper mill sludge. Batch tests had demonstrated that the Pb(II) removal by the FCC was pH-sensitive with the increase of Pb(II) removal from 74.94% to 95.97% as initial pH was raised from 2.0 to 6.0. The equilibrium data at initial pH 3.0 was well fitted by the Langmuir isotherm, but the data obtained at initial pH 6.0 could be described by the Freundlich model. The precipitation of PbO resulted in multilayer adsorption of Pb species on the FCC as the pH increased from 6.0 to above 7.0. The maximum Pb(II) adsorption capacity of the FCC reached 112.36 mg g−1 at initial pH 3.0 and at 25 °C. Column tests showed that the FCC achieved the highest Pb(II) removal of 65.86% after 12 days' run compared to 32.35% for Fe0/AC couples and only 1.24% for AC.
The XRD and XPS analysis revealed that the PbO (dominant Pb species), Pb0, asisite and plumbojarosite appeared on the FCC after Pb(II) removal. The FESEM examination exhibited that PbO particles, with various structures of plate, flower, cuboid and dentrite, were accumulated on the FCC surface. The XRD, XPS and EDX analysis exhibited the remarkable decrease of metallic iron content in the FCC after the Pb(II) removal, revealing the effective corrosion of microscale Fe0 by forming galvanic couples between Fe0 and carbon. The Pb(II) removal by the FCC might involve reduction, precipitation, ion exchange and formation of Pb containing compounds by reacting with Cl−, SO42− and Fe(III) ions in bulk solution.
Conflicts of interest
There are no conflicts to declare.
Acknowledgements
This work was supported by the National Natural Science Foundation of China (No. 51674017) and the State Scholarship Fund of China Scholarship Council (No. 201706465070).
References
- A. M. Azzam, S. T. EI-Wakeel, B. B. Mostafa and M. F. EL-Shahat, J. Environ. Chem. Eng., 2016, 4, 2196–2206 CrossRef.
- J. Wang, G. J. Liu, T. F. Li and C. C. Zhou, RSC Adv., 2015, 5, 29859–29871 RSC.
- R. Miehr, P. G. Tratnyek, J. Z. Bandstra, M. M. Scherer, M. J. Alowitz and E. J. Bylaska, Environ. Sci. Technol., 2004, 38, 139–147 CrossRef PubMed.
- R. A. Crane and T. B. Scott, J. Hazard. Mater., 2012, 211, 112–125 CrossRef PubMed.
- C. Noubactep, Korean J. Chem. Eng., 2012, 29, 1050–1056 CrossRef.
- C. R. Keenan, R. Goth-Goldstein, D. Lucas and D. L. Sedlak, Environ. Sci. Technol., 2009, 43, 4555–4560 CrossRef PubMed.
- K. Miyajima and C. Noubactep, Chem. Eng. J., 2015, 262, 891–896 CrossRef.
- Y. Ren, J. F. Zhou, B. Lai, W. J. Tang and Y. Zeng, RSC Adv., 2016, 6, 108229–108239 RSC.
- I. Mikhailov, S. Komarov, V. Levina, A. Gusev, J. P. Issi and D. Kuznetsov, J. Hazard. Mater., 2017, 321, 557–565 CrossRef PubMed.
- X. M. Dou, R. Li, B. Zhao and W. Y. Liang, J. Hazard. Mater., 2010, 182, 108–114 CrossRef PubMed.
- L. Yuan, W. Zhi, Q. L. Xie, X. Chen and Y. S. Liu, Environ. Sci.: Water Res. Technol., 2015, 1, 814–822 RSC.
- B. Lai, Y. X. Zhou, P. Yang, J. H. Yang and J. L. Wang, Chemosphere, 2013, 90, 1470–1477 CrossRef PubMed.
- D. Y. Huang, Q. Y. Yue, K. F. Fu, B. J. Zhang, B. Y. Gao, Q. Li and Y. Wang, Desalin. Water Treat., 2016, 57, 4420–4428 Search PubMed.
- H. Modin, K. M. Persson, A. Andersson and M. van Praagh, J. Hazard. Mater., 2011, 189, 749–754 CrossRef PubMed.
- A. Hussam and A. K. M. Munir, J. Environ. Sci. Health, Part A: Toxic/Hazard. Subst. Environ. Eng., 2007, 42, 1869–1878 CrossRef PubMed.
- C. Noubactep, Chemosphere, 2014, 117, 104–107 CrossRef PubMed.
- R. H. Yang, J. Z. Zhu, Y. L. Li and H. Zhang, Int. J. Environ. Res. Public Health, 2016, 13, 457–471 CrossRef PubMed.
- V. K. Gupta, A. Nayak and S. Agarwal, Environmental Engineering Research, 2015, 20, 1–18 CrossRef.
- T. A. Saleh and V. K. Gupta, Adv. Colloid Interface Sci., 2014, 211, 93–101 CrossRef PubMed.
- V. K. Gupta and T. A. Saleh, Environ. Sci. Pollut. Res., 2013, 20, 2828–2843 CrossRef PubMed.
- R. X. Bai, Y. Zhang, Z. G. Zhao, Q. X. Liao, P. Chen, P. P. Zhao, W. H. Guo, F. Yang and L. C. Li, J. Ind. Eng. Chem., 2018, 59, 416–424 CrossRef.
- L. Yuan, W. Zhi, Y. Liu, S. Karyala, P. J. Vikesland, X. Chen and H. S. Zhang, Environ. Sci. Technol., 2015, 49, 824–830 CrossRef PubMed.
- M. Ahmaruzzaman and V. K. Gupta, Ind. Eng. Chem. Res., 2011, 50, 13589–13613 CrossRef.
- D. C. Bellinger, Int. J. Environ. Res. Public Health, 2011, 8, 2593–2628 CrossRef PubMed.
- C. F. Carolin, P. S. Kumar, A. Saravanan, G. J. Joshiba and M. Naushad, J. Environ. Chem. Eng., 2017, 5, 2782–2799 CrossRef.
- S. Suganya and P. S. Kumar, J. Ind. Eng. Chem., 2018, 60, 418–430 CrossRef.
- P. S. Kumar, R. Sivaranjanee, P. S. Rajan and A. Saravanan, J. Ind. Eng. Chem., 2018, 60, 307–320 CrossRef.
- E. Gunasundari and P. S. Kumar, IET Nanobiotechnol., 2017, 11, 317–328 CrossRef PubMed.
- H. Sharififard, F. Pepe, M. Soleimani, P. Aprea and D. Caputo, RSC Adv., 2016, 6, 42845–42853 RSC.
- A. R. Kaveeshwar, S. K. Ponnusamy, E. D. Revellame, D. D. Gang, M. E. Zappi and R. Subramaniam, Process Saf. Environ. Prot., 2018, 114, 107–122 CrossRef.
- E. Gunasundari and P. S. Kumar, J. Ind. Eng. Chem., 2017, 56, 129–144 CrossRef.
- N. Mohammadi, H. Khani, V. K. Gupta, E. Amereh and S. Agarwal, J. Colloid Interface Sci., 2011, 362, 457–462 CrossRef PubMed.
- H. Shafififard, F. Z. Ashtiani and M. Soleimani, Asia-Pac. J. Chem. Eng., 2013, 8, 384–395 CrossRef.
- V. K. Gupta, A. Nayak, S. Agarwal and I. Tyagi, J. Colloid Interface Sci., 2014, 417, 420–430 CrossRef PubMed.
- D. Robati, B. Mirza, M. Rajabi, O. Moradi, I. Tyagi, S. Agarwal and V. K. Gupta, Chem. Eng. J., 2016, 284, 687–697 CrossRef.
- G. S. Liu, V. Strezov, J. A. Lucas and L. J. Wibberley, Thermochim. Acta, 2004, 410, 133–140 CrossRef.
- F. Ju and Y. Y. Hu, Sep. Purif. Technol., 2011, 78, 33–41 CrossRef.
- J. W. Liu, T. Mwamulima, Y. M. Wang, Y. Fang, S. X. Song and C. S. Peng, J. Mol. Liq., 2017, 243, 205–211 CrossRef.
- P. Wu and Y. S. Zhou, J. Hazard. Mater., 2009, 168, 674–680 CrossRef PubMed.
- H. Genc-Fuhrman, P. Wu, Y. S. Zhou and A. Ledin, Desalination, 2008, 226, 357–370 CrossRef.
- V. K. Gupta, R. Kumar, A. Nayak, T. A. Saleh and M. A. Barakat, Adv. Colloid Interface Sci., 2013, 193–194, 24–34 CrossRef PubMed.
- M. Ghaedi, S. Hajjati, Z. Mahmudi, I. Tyagi, S. Agarwal, A. Maity and V. K. Gupta, Chem. Eng. J., 2015, 268, 28–37 CrossRef.
- A. Asfaram, M. Ghaedi, S. Agarwal, I. Tyagi and V. K. Gupta, RSC Adv., 2015, 5, 18438–18450 RSC.
- P. S. Kumar, A. Saravanan, K. A. Kumar, R. Yashwanth and S. Visvesh, IET Nanobiotechnol., 2016, 10, 244–253 CrossRef PubMed.
- G. Neeraj, S. Krishnan, P. S. Kumar, K. R. Shriaishvarya and V. V. Kumar, J. Mol. Liq., 2016, 214, 335–346 CrossRef.
- A. Mittal, J. Mittal, A. Malviya and V. K. Gupta, J. Colloid Interface Sci., 2010, 344, 497–507 CrossRef PubMed.
- Y. M. Hao, M. Chen and Z. B. Hu, J. Hazard. Mater., 2010, 184, 392–399 CrossRef PubMed.
- L. Yuan and Y. S. Liu, Chem. Eng. J., 2013, 215, 432–439 CrossRef.
- M. E. Lee, J. H. Park, J. W. Chung, C. Y. Lee and S. Kang, J. Ind. Eng. Chem., 2015, 21, 470–475 CrossRef.
- T. Depci, A. R. Kul and Y. Onal, Chem. Eng. J., 2012, 200, 224–236 CrossRef.
- Z. B. Bouabidi, M. H. El-Naas, D. Cortes and G. McKay, Chem. Eng. J., 2018, 334, 837–844 CrossRef.
- N. D. V. Quyen, T. N. Tuyen, D. Q. Khieu, H. V. M. Hai, D. X. Tin, P. T. N. Lan and I. Kiyoshi, Bull. Mater. Sci., 2018, 41, 6 CrossRef.
- W. J. Zhang, Y. C. Zhang, Y. Gutha and J. Xu, Int. J. Biol. Macromol., 2017, 105, 422–430 CrossRef PubMed.
- F. C. Christopher, S. Anbalagan, P. S. Kumar, S. R. Pannerselvam and V. K. Vaidyanathan, IET Nanobiotechnol., 2017, 11, 433–442 CrossRef PubMed.
- S. Anbalagan, S. K. Ponnusamy, S. R. P. Selvam, A. Sankaranarayan and A. Dutta, Korean J. Chem. Eng., 2016, 33, 2716–2731 CrossRef.
- S. Suganya, A. Saravanan, P. S. Kumar, M. Yashwanthraj, P. S. Rajan and K. Kayalvizhi, IDA J. Desalin. Water Reuse, 2017, 7, 214–227 CrossRef.
- Y. L. Zhang, Y. M. Li, J. F. Li, G. D. Sheng, Y. Zhang and X. M. Zheng, Chem. Eng. J., 2012, 185, 243–249 CrossRef.
- X. Zhang, S. Lin, Z. L. Chen, M. Megharaj and R. Naidu, Water Res., 2011, 45, 3481–3488 CrossRef PubMed.
- M. H. Liu, Y. H. Wang, L. T. Chen, Y. Zhang and Z. Lin, ACS Appl. Mater. Interfaces, 2015, 7, 7961–7969 CrossRef PubMed.
- Z. T. Shen, Y. Y. Zhang, F. Jin, O. McMillan and A. Al-Tabbaa, Sci. Total Environ., 2017, 609, 1401–1410 CrossRef PubMed.
- S. A. A. Sajadi, A. A. Alamolhoda and S. J. Hashemian, Sci. Iran., 2007, 14, 169–173 Search PubMed.
- Z. Li, H. Chen, H. B. Bao and M. Y. Gao, Chem. Mater., 2004, 16, 1391–1393 CrossRef.
- H. L. Peng, Z. Y. Mo, S. J. Liao, H. G. Liang, L. J. Yang, F. Luo, H. Y. Song, Y. L. Zhong and B. Q. Zhang, Sci. Rep., 2013, 3, 1765 CrossRef.
- P. Marcus and J. M. Grimal, Corros. Sci., 1992, 33, 805–814 CrossRef.
- S. S. Barala, B. Roul, N. Banerjee and M. Kumar, J. Appl. Phys., 2016, 120, 115305 CrossRef.
- N. M. Zhu, Y. S. Xu, L. C. Dai, Y. F. Zhang and G. Q. Hu, J. Hazard. Mater., 2018, 351, 138–146 CrossRef PubMed.
- K. C. Chen, C. W. Wang, Y. I. Lee and H. G. Liu, Colloids Surf., A, 2011, 373, 124–129 CrossRef.
- P. B. Taunk, R. Das, D. P. Bisen and R. K. Tamrakar, Optik, 2016, 127, 6028–6035 CrossRef.
Footnote |
† Electronic supplementary information (ESI) available. See DOI: 10.1039/c8ra05164j |
|
This journal is © The Royal Society of Chemistry 2018 |
Click here to see how this site uses Cookies. View our privacy policy here.