DOI:
10.1039/C7RA13119D
(Paper)
RSC Adv., 2018,
8, 4478-4482
Nano metal oxides as efficient catalysts for selective synthesis of 1-methoxy-2-propanol from methanol and propylene oxide†
Received
7th December 2017
, Accepted 10th January 2018
First published on 24th January 2018
Abstract
Nano metal oxides such as Fe2O3, Fe3O4, CuO, NiO, ZnO and SnO2 were prepared and characterized using XRD, SEM and TEM analysis. These as-prepared metal oxide materials were used as catalysts for the etherification of methanol with propylene oxide (PO). The results showed that α-Fe2O3 exhibited outstanding catalytic performance with 97.7% conversion and 83.0% selectivity to MP-2 at 160 °C for 8 h. Furthermore, the relationship between the catalytic activity or selectivity and surface basicity or energy gap was investigated. This catalyst could be easily recovered and reused due to its heterogeneous catalytic nature.
Introduction
Glycol ethers are considered to be important chemicals that combine the best solvency features of alcohols and ethers for synthesizing organic compounds.1 They are widely used as industrial solvents for coating materials, printing ink, dyeing leather etc. Due to the low toxicity of propylene glycol ether, it is expected to be a safe substitute for toxic ethylene glycol ether. Although there are several methods for synthesizing propylene glycol ether, the propylene oxide route is the most convenient and industrially feasible in terms of atom-economy and energy-efficiency. In this method, the epoxide ring of propylene oxide may open at the C–O bond and react with alcohols to form propylene glycol ether, catalyzed by acid or base catalysts. These catalysts include earlier homogeneous acids or bases, such as NaOH, alcoholic sodium, H2SO4 and BF3 etc.,2,3 and later solid acids or bases, e.g. acidic zeolites,4 Mg/Al hydrotalcite,5 Zn–Mg–Al oxides,1 MgO6 and amine-modified porous silica7 etc. Very recently, brucite-layer materials,8 Al2O3/MgO,9 and basic and acidic ionic liquids10,11 have been developed as highly efficient catalysts for the selective synthesis of propylene glycol ether. Because there is much research interest in developing environmentally benign catalysis, we wish to report the preparation of nano metal oxides using a simple method, and highlight their catalytic performance for the synthesis of 1-methoxymethane-2-propanol (MP-2) via an atom–economic reaction. The simply prepared Fe2O3 catalyst, which is inexpensive and environmentally benign, demonstrated excellent catalytic performance for the synthesis of MP-2. The results are disclosed herein.
Experimental
Preparation of the catalysts
Iron oxide was prepared using the following procedure.12 30 mL of FeCl3 aqueous solution (1 mol L−1), 2.5 g of urea and 2 mL of polyethylene glycol (PEG-400) as a dispersant were added to a three-necked flask fitted with a reflux condenser and an electric heater. Ammonia solution (28%) was added dropwise to the mixed solution to maintain a pH of 3.7 to afford Fe(OH)3. Thereafter, the reactor was heated to 80 °C and aged at this temperature for 8 h. The mixed solution was then ultrasonically treated at room temperature for 20 min, followed by filtration to remove the filtrate. The obtained solid was washed with deionized water and anhydrous ethanol. Thereafter, it was dried at 100 °C for 12 h, and then calcined at 500 °C for 2 h in a muffle furnace to afford nano-iron oxide. Other oxides, such as CuO, ZnO, NiO and SnO2, were prepared with the same method to that of iron oxide, using CuSO4, ZnSO4, NiCl and SnCl4 aqueous solutions as precursors. However, the pH values for precipitation of Cu(OH)2, Zn(OH)2, Ni(OH)2 and Sn(OH)4 were adjusted to 4.7, 6.0, 7.2 and 2.5, respectively. Fe3O4 was prepared according to the literature.13
Catalyst characterization
XRD of the sample was performed on a Bruker-D8 Advance X-ray diffractometer with Cu Kα radiation (40 kV and 36 mA). TEM measurements were taken on a JEM-2100 electron microscope (JEOL Japan) with an acceleration voltage of 200 kV. The morphology of the catalysts was observed using a Hitachi S-4800 scanning electron microscope (SEM).
Catalytic test and analytic procedure
1.0 mL (14.4 mmol) of propylene oxide, 21 mL (0.52 mol) of methanol and 0.1 g of iron oxide catalyst were added, in turn, into a stainless steel 100 mL autoclave with a magnetic stirrer in an electric heater. The reactor was heated to 160 °C with fast stirring and the reaction was carried out at this temperature for 8 h. When the reaction was complete, the mixture was filtered to remove the catalyst and the filtrate was analyzed using GC (Agilent 7820) with a FID detector equipped with HP-5, a 30 m × 0.32 mm × 0.25 μm column and GC-MS (Agilent GC 7890A-5975C).
Results and discussion
Characterization of the catalysts
Fig. 1 presents the XRD pattern of the prepared iron oxide sample recorded in the 2θ range of 10–90°. It can be seen from the figure that typical diffraction peaks at 2θ values of 24.1, 33.2, 35.6, 41.0, 49.5, 54.2, 57.7, 62.4 and 64.0° correspond to the diffractions of the (012), (104), (110), (113), (024), (116), (018), (214) and (300) planes, respectively. The intense peaks of the XRD pattern indicate that the Fe2O3 product was well crystallized and no impurity diffraction peaks were observed, implying that almost single phase Fe2O3 was successfully prepared. All diffraction peaks were perfectly indexed, which was in agreement with the data of α-Fe2O3 (hematite, JCPDS 33-0664). Moreover, the average crystallite size of the product was estimated to be 31.7 nm using the Debye–Scherrer equation. The XRD patterns of the other metal oxides, such as CuO, NiO, ZnO, SnO2 and Fe3O4, are shown in Fig. SI1–5.†
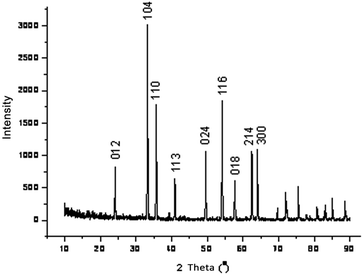 |
| Fig. 1 XRD pattern of Fe2O3. | |
SEM and TEM. Fig. 2 shows the scanning electron microscopy (SEM) image of the Fe2O3 sample. As seen from the figure, iron oxide particles of about 30 nm in size were well dispersed and their sizes were in agreement with the value calculated using the Debye–Scherrer equation. In addition, the transmission electron microscopy (TEM) image of the Fe2O3 sample also showed the same result as the SEM of Fe2O3. Nano-particles of about 30 nm in size are shown in Fig. 3. The SEM and/or TEM images of other metal oxides, such as CuO, NiO, ZnO, SnO2 and Fe3O4 (TEM), are shown in Fig. SI6–10.† The morphologies of these oxides can also be seen in Fig. SI6–10:† particles of about 20 nm for Fe3O4, particles of 200–300 nm for CuO, particles of about 100 nm for ZnO, and aggregations composed of ∼30 nm sized particles for SnO2 and NiO.
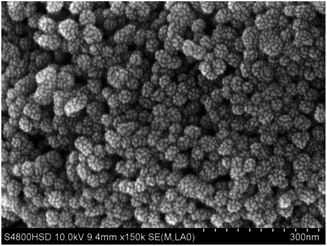 |
| Fig. 2 SEM image of iron oxide sample. | |
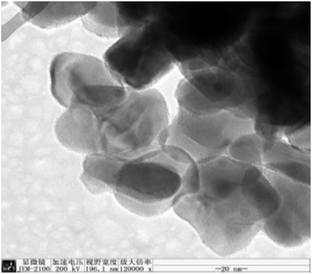 |
| Fig. 3 TEM image of the iron oxide sample. | |
Catalytic activity. The catalytic activity of α-Fe2O3 and the other metal oxides such as Fe3O4, CuO, NiO, ZnO and SnO2 for the etherification of methanol with propylene oxide (PO) was assessed. The results are summarized in Table 1. The data show that the α-Fe2O3 catalyst possessed very high activity for etherification with a conversion of 97.7% and 83.0% selectivity to 1-methoxy-2-propanol (MP-2) at 160 °C for 8 h, corresponding to a TON (turnover number, converted moles per mole catalyst) of 11.5 mol molFe−1 (entry 1). Also, the CuO catalyst displayed the same activity as α-Fe2O3, with a conversion of 97.9% (entry 2), but the selectivity to MP-2 was relatively low with a MP-2/MP-1 (2-methoxy-1-propanol) ratio of only 1.17. Although Fe3O4 and NiO had a higher MP-2/MP-1 ratio, their catalytic activities for the etherification were lower (entry 3 and 4), exhibiting 26.5 and 56.3% conversions with TONs of 3.0 mol molFe−1 and 6.1 mol molNi−1, respectively. Similarly, ZnO and SnO2 presented almost the same conversions and selectivities to MP-2 (entry 5 and 6). The difference in the catalytic activity of these metal oxides was not directly related to their particle size (Fig. SI6–10†), but was instead related to their acid–base properties on the surface.1 Compared with the reported works in the literature, α-Fe2O3 exhibited higher activity, although the catalysts Mg, Al-LDH and Zn, Mg, Al-LDH displayed high conversions of 92.4% or 95.9% and 96.5% or 90.9% of selectivity to MP-2, achieving TONs of 12.8 and 16.7,1,5 respectively. However, the preparation process for these catalysts was more complicated than that of α-Fe2O3.
Table 1 Catalytic activity of some metal oxidesa
Entry |
Oxides |
Conv. (%) |
Sel. (%) |
TON |
Rat. |
Eg14 |
Bas.14 |
Reaction conditions: reaction temperature = 160 °C, time = 8 h, catalyst = 0.1 g, molar ratio of methanol to PO = 36 : 1; Conv. = conversion, Sel. = selectivity to MP-2, TON = turn over number (mol molM−1, M = Fe, Cu, Ni, Zn and Sn), rat. = ratio of MP-2/MP-1, Eg = energy gap, Bas. = basicity. |
1 |
α-Fe2O3 |
97.7 |
83.0 |
11.5 |
4.88 |
2.00 |
1.008 |
2 |
CuO |
97.9 |
54.0 |
11.5 |
1.17 |
1.95 |
0.991 |
3 |
Fe3O4 |
26.5 |
80.4 |
3.0 |
4.10 |
— |
— |
4 |
NiO |
56.3 |
80.5 |
6.1 |
4.13 |
3.80 |
0.997 |
5 |
ZnO |
65.9 |
59.3 |
7.7 |
1.46 |
3.40 |
1.001 |
6 |
SnO2 |
59.7 |
59.0 |
13.0 |
1.44 |
3.80 |
0.927 |
It has been previously reported that in α-Fe2O3, oxide ions (O2−) are arranged along the plane of a hexagonal closed-packed lattice, whereas two-thirds of the octahedral interstices are occupied by Fe3+ cations in the basal plane.15 Acid–base ion pairs (O2−–Fe3+) are inevitably formed on the surface of α-Fe2O3, and play an important role the addition reaction. The acidic sites (Fe3+) are responsible for PO conversion, and the basic sites (O2−) are beneficial for generating MP-2,11 which is confirmed by the basicity order list in Table 1. Furthermore, the catalytic activity of the metal oxides is related to their energy gap,14 that is, the lower the energy gap, the higher the activity of these metal oxides, because it is easier for electrons to transition when the energy gap is low, enhancing the formation of acid-basic sites on the surface. On the other hand, α-Fe2O3 catalysts usually possess redox properties for catalyzing organic synthesis reactions, such as oxidation of toluene, benzylation of benzene and other aromatics etc.16,17 The redox species in the reaction systems are advantageous for the ring opening reaction of PO.18 Therefore, the excellent catalytic performance of the α-Fe2O3 catalyst compared with the other metal oxides was ascribed to the surface properties.
Effect of reaction conditions
Using α-Fe2O3 as the catalyst, the effect of reaction time on the catalytic activity was investigated. As shown in Fig. 4, the conversion of PO increased as the reaction proceeded from 3 to 8 h at 110 °C. The conversion approached to 57.6% as the reaction was carried out for 8 h. Then, the conversion slightly increased as the reaction time was prolonged to 9 h, implying that the thermodynamic equilibrium of the reaction was almost achieved at that time. Furthermore, the selectivity to MP-2 increased as the time was prolonged from 3 to 5 h, while on the contrary, the selectivity to MP-1 was decreased over this range. The selectivity to MP-2, as well as MP-1, was almost constant during the reaction time from 5 to 9 h.
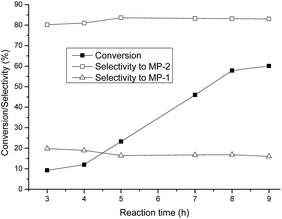 |
| Fig. 4 Dependence of reactivity on the reaction time. Reaction conditions: temperature = 110 °C, catalyst = 0.1 g, molar ratio of methanol to PO = 36 : 1. | |
As the reaction temperature was raised, the conversion rapidly increased to a maximum at 160 °C, and basically remained unchanged at 170 °C (Fig. 5). The change in the conversion with temperature was probably due to the control of the reaction kinetics, that is, high temperature can accelerate the reaction rate and shorten the time needed to reach equilibrium. Thus, increasing the reaction temperature is greatly advantageous to forming the product. Unexpectedly, the selectivity to MP-2 was independent of the reaction temperature in the range from 110 to 190 °C, retaining the value at 83.0% over the whole temperature range. This is rare in the catalytic synthesis of organic compounds.
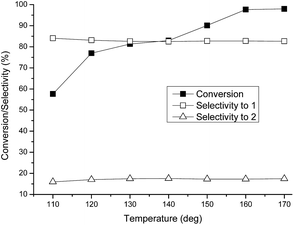 |
| Fig. 5 Dependence of reactivity on the reaction temperature. Reaction conditions: reaction time = 8 h, catalyst = 0.1 g, molar ratio of methanol to PO = 36 : 1. | |
Reactivity of other alcohols
Other alcohols such as ethanol, propanol, butanol, iso-butanol, amyl alcohol, iso-amyl alcohol and octanol were then applied as alternatives to methanol, and the etherification reactions of PO with these alcohols were also examined in the presence of α-Fe2O3 as a catalyst under the same conditions (Table 2). As shown in the table, the reactivity was reduced as the length of the carbon chain in the alcohols increased (entry 1–8), so that octanol exhibited very low reactivity for this reaction with 31.6% conversion (entry 8). By comparison, the lower reactivity of iso-butanol and iso-amyl alcohol compared to that of butanol and amyl alcohol is related to the steric effect of secondary alcohols (entry 4–7). Furthermore, the selectivity to 1-alkoxy-2-alcohol was also lower than that of the methanol system, with 48.0 to 64.2% selectivity achieved.
Table 2 Reactivity of other alcohols with PO
Entry |
Alcohols |
Conv. (%) |
Sel. to MP-2 (%) |
1 |
Methanol |
97.7 |
82.6 |
2 |
Ethanol |
69.8 |
50.9 |
3 |
Propanol |
64.7 |
49.6 |
4 |
Butanol |
63.9 |
64.2 |
5 |
Iso-butanol |
50.2 |
52.1 |
6 |
Amyl alcohol |
51.6 |
50.0 |
7 |
Iso-amyl alcohol |
41.6 |
48.0 |
8 |
Octanol |
31.6 |
50.0 |
The stability of the catalyst
In order to further evaluate the performance of the α-Fe2O3 catalyst, reuse tests of α-Fe2O3 were conducted. The catalyst was separated by filtration after the first test, and then reused for the next run under the same conditions. The results are depicted in Fig. 6.
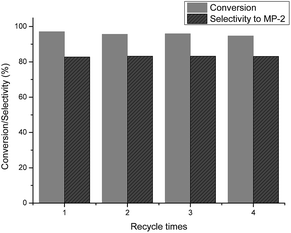 |
| Fig. 6 The reusability of the catalyst. | |
As shown in the figure, the catalytic activity of the reused catalyst was almost unaffected even at the fourth run, exhibiting >95.0% conversion and retaining 83.0% selectivity to MP-2. The SEM image of the reused catalyst is shown in Fig. 7. Aggregation of the Fe2O3 nanoparticles was observed when they were reused four times, but their phase composition did not change, as shown in the XRD pattern of the used Fe2O3 catalyst (Fig. 8). These results imply that the catalyst can be efficiently recovered and recycled.
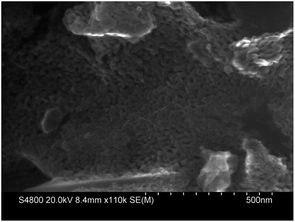 |
| Fig. 7 SEM image of the used catalyst. | |
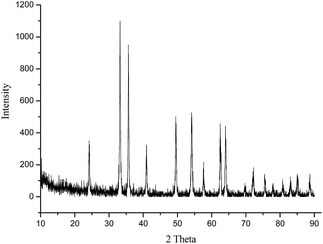 |
| Fig. 8 XRD pattern of the catalyst after being used four times. | |
Conclusions
Nano metal oxide materials were prepared and characterized using XRD, SEM and TEM analysis. These oxides were used for the etherification of methanol with propylene oxide (PO) to form 1-methoxy-2-propanol (MP-2). The as-prepared Fe2O3 material, recognized as α-Fe2O3, was found to be an effective catalyst for the etherification of methanol with propylene oxide (PO), with 97.7% conversion and 83.0% selectivity to MP-2 at 160 °C for 8 h, and achieving a TON of 11.5 mol molFe−1. The high catalytic activity and selectivity to MP-2 of this catalyst, which was prepared using a simple method, can be attributed to its low energy gap and high basicity. This catalyst can be easily recovered and reused due to its heterogeneous catalytic nature. Thus, the simply prepared and environmentally benign α-Fe2O3 catalyst demonstrates great potential for application in industry.
Conflicts of interest
There are no conflicts to declare.
Acknowledgements
We make a great acknowledgement for the financial support of this work from the National Natural Science Foundation of China (No. 21671050, 41571199), the Natural Science Foundation of Heilongjiang Province (No. 2015003, B201119) and the Foundation for academic leaders of Harbin (No. 2013RFXXJ009).
Notes and references
- W. Cheng, W. Wang, Y. Zhao, L. Liu, J. Yang and M. He, Appl. Clay Sci., 2008, 42, 111 CrossRef CAS.
- H. A. Pecorini and J. T. Banchero, Ind. Eng. Chem., 1956, 48, 1287 CrossRef.
- H. C. Chitwood and B. T. Freurec, J. Am. Chem. Soc., 1948, 68, 680 CrossRef.
- W. Y. Zhang, H. Wang, Q. B. Li, Q. N. Dong, N. Zhao and W. Wei, Appl. Catal., A, 2005, 294, 188 CrossRef CAS.
- H. Y. Zeng, Y. J. Wang, Z. Feng, K. Y. You, C. Zhao, J. W. Sun and P. L. Liu, Catal. Lett., 2010, 137, 94 CrossRef CAS.
- W. Y. Zhang, H. Wang, W. Wei and Y. H. Sun, J. Mol. Catal. A: Chem., 2005, 231, 83 CrossRef CAS.
- X. Zhang, W. Zhang, J. Li, N. Zhao, W. We and Y. H. Sun, Catal. Commun., 2007, 8, 437 CrossRef CAS.
- M. N. Timofeeva, A. E. Kapustin, V. N. Panchenko, E. O. Butenko, V. V. Krupskaya, A. Gil and M. A. Vicente, J. Mol. Catal. A: Chem., 2016, 423, 22 CrossRef CAS.
- Y. Zhang, B. Lu, X. Wang, J. Zhao and Q. Cai, Appl. Catal., A, 2011, 408, 125 CrossRef CAS.
- C. Y. De, Q. H. Cai, X. G. Wang, J. X. Zhao and B. Lu, J. Chem. Technol. Biotechnol., 2011, 86, 105 CrossRef CAS.
- Y. Bai, Q. Cai, X. Wang and B. Lu, Kinet. Catal., 2011, 52, 396 CrossRef.
- H. Tang, H. Wang, B. Lu, J. Zhao and Q. Cai, Mol. Catal., 2017, 431, 27 CrossRef CAS.
- W. Zhang, B. Lu, H. Tang, J. Zhao and Q. Cai, J. Magn. Magn. Mater., 2015, 381, 401 CrossRef CAS.
- R. R. Reddy, Y. N. Ahammed, P. A. Azeem, K. R. Gopal and T. V. R. Rao, J. Non-Cryst. Solids, 2001, 286, 169 CrossRef CAS.
- M. Mishra and D.-M. Chun, Appl. Catal., A, 2015, 498, 126 CrossRef CAS.
- X. Li, X. You, B. Lu, X. Wu, J. Zhao and Q. Cai, Ind. Eng. Chem. Res., 2014, 53, 20085 CrossRef CAS.
- S. Fan, Y. Pan, H. Wang, B. Lu, J. Zhao and Q. Cai, Mol. Catal., 2017, 442, 20 CrossRef.
- Y. Ogata, Y. Sawaki and H. Shimizu, J. Org. Chem., 1978, 43, 1760 CrossRef CAS.
Footnote |
† Electronic supplementary information (ESI) available. See DOI: 10.1039/c7ra13119d |
|
This journal is © The Royal Society of Chemistry 2018 |
Click here to see how this site uses Cookies. View our privacy policy here.