DOI:
10.1039/C7RA11461C
(Paper)
RSC Adv., 2017,
7, 53871-53877
Single-faced flame resistance of cotton fabrics modified via mist copolymerization
Received
17th October 2017
, Accepted 16th November 2017
First published on 23rd November 2017
Abstract
Cotton fabrics with single-faced flame resistance are successfully fabricated through a simple mist copolymerization process using pentabromobenzyl acrylate (PBBA) as the functional monomer. The co-monomers are methyl acrylate (MA), which can react with the hydroxyl groups of cellulose by transesterification, and divinyl benzene (DVB), a cross-linker. SEM images indicate that a very thin copolymer layer (the thickness is about 200 nm) was formed on the cotton fiber surface and the flame resistance tests show that the modified fabrics have an improved flammability with longer time to ignition (TTI), lower peak heat release rate (PHRR), lower total heat release (THR), and lower average mass loss rate (AMLR), when compared to the original cotton fabric. The modification also results in good wearing durability because the flame-retardant coating was covalently linked to the cotton fabric surface by many ester groups. Moreover, desired cotton characteristics such as tensile strength, water absorbency, vapor permeability and flexibility are mostly retained because the mist method gives a single-faced modification of the cotton fabrics.
Introduction
Cotton textiles have been widely applied to apparel, bedding, furniture, curtains, wall-hangings, and various industrial supplies due to their flexibility, comfortability, water absorptivity, and air permeability. Recently, numerous new cotton products have also been developed by incorporating useful functionalities such as antimicrobial,1–4 superhydrophobicity,5–8 oil–water separation,9,10 and electrical conduction.11–14 However, cotton is more combustible than most commonly available fibers. The flammability indexes like ignition flaming combustion (Tc) and limiting oxygen index (LOI) values are significantly lower than those of wool, polyamide 6, and polyester.15 Therefore, a lot of flame retardants (FR) and FR treatments for cotton products have been developed to retard ignition or to decrease flame spread.16–21 Some finishing techniques such as dip coating,22–28 layer-by-layer (LBL),29–37 plasma,38 and sol–gel coating,39–42 have been used to modify the flammability of the cotton textiles. However, these approaches have several major shortcomings, for example, (1) some modified fabrics are sensitive for wear, because of less covalent bonds between the cotton fibers and the flame retardants; (2) the coating thickness is uncontrollable, and often affects the desired textile properties such as softness, water absorptivity, and vapor transmissibility; (3) a mass of organic solvent may be produced in the finishing process, and cause serious environmental problems; (4) the contact of the coatings with skin often induces toxic side effects, and (5) the industrial scales are hard to achieve in low cost.
In our previous works,43,44 a “mist polymerization” technique has been used to modify cotton fabric surface. Asymmetrically superhydrophobic,45,46 and wear-resistant47 cotton fabrics were fabricated by feeding atomized monomer solutions to an in situ polymerization to build thin polymeric coatings on the cotton fabrics. The advantages of the mist polymerization include wider range of applicable monomers, tailorable coating thinness and surface morphology, simple operation, single faced modification, and almost no damage to the original properties of the fabric. These features of the mist polymerization method are suitable for fabricating cotton fabric with single faced function.
Pentabromobenzyl acrylate (PBBA) is a polymerizable monomer containing of approximately 71 wt% bromine element,48–50 belonging to the class of organobromine FR, which appears to work even at low concentration.50 Both homopolymerization50–52 and copolymerization53,54 of PBBA were widely studied for the applications in commercial polymer materials such as polystyrene, polyamide 6, and polypropylene.
In this work, a mist copolymerization process utilizing PBBA as the FR monomer is applied to modify cotton fabrics. Methyl acrylate (MA) is used as a co-monomer to enhance the adhesion of the polymer coatings via a transesterification with the hydroxyl groups of cellulose. The flame resistance properties of the resulting cotton fabrics are examined by the burning tests and cone calorimeter experiments. The abrasion resistance, mechanical stability, water absorbability, and moisture transmissibility of the modified cotton fabrics are further characterized.
Experimental
Materials
Pentabromotoluene (PBB) was obtained from TCI Co., Ltd (Shanghai, China). The cotton fabrics were purchased from a local fabric store (60 ends per cm, 30 picks per cm, 0.42 mm thickness, 120 g m−2 weight, 35.2 m2 g−1 specific surface area). Before chemical modification, the cotton samples were cleaned by ultrasonic washing in ethanol (30 min) and deionized water (30 min × 3 times), respectively. Other chemical reagents were purchased from Aladdin Co., Ltd (Shanghai, China), and all used as received without further purification. Deionized water with a resistivity of 18.2 MΩ cm was used in all experiments.
Synthesis of pentabromobenzyl bromide (PBBBr)
PBB (19.6 g, 40.3 mmol), N-bromosuccinimide (NBS, 7.0 g, 39.3 mmol), liquid bromine (Br2, 1.0 mL), benzoyl peroxide (BPO, 2.0 g, 8.3 mmol), and carbon tetrachloride (CCl4, 100 mL) were mixed in a three-neck glass flask (250 mL) in an oil bath, heated at 80 °C for 1 h, added with aqueous hydrogen peroxide 30% (H2O2, 11 mL), and stirred for 4 h. The produced precipitate was washed with CCl4 (80 mL × 3 times), and dried in a vacuum oven at 80 °C for 12 h to obtain the product. Yield = 86.4%; 1H-NMR (400 MHz, CDCl3): 5.01 (–CH2Br); FTIR (KBr): 2957, 1698, 1429, 642 cm−1.
Synthesis of pentabromobenzyl acrylate (PBBA)
PBBBr (21.2 g, 37.5 mmol), a mixture solution of acrylic acid (AA) and sodium acrylate (NaAC) (10.4 mmol L−1, pH = 6.5, 4.6 mL), and 2-methoxyethanol (ME, 63 mL) were mixed, heated at 100 °C for 3 h. The obtained precipitate was washed with deionized water (100 mL × 3 times), and dried in a vacuum oven at 80 °C for 12 h to obtain the product. Yield = 93.5%; 1H-NMR (400 MHz, CDCl3): 6.45 and 5.90 (
CH2–), 6.15 (
CH–), 5.69 (–CH2O–); FTIR (KBr): 3031, 2900, 1730, 1465, 985 cm−1.
Typical procedure of mist polymerization on the cotton surface
PBBA (0.2 g, 0.36 mmol), methyl acrylate (MA, 31 mg, 0.36 mmol) and divinylbenzene (DVB, 7.2 μmol) were dissolved in acetone (15 mL), and used as the monomer solution. An aqueous solution of ammonium ceric nitrate (ACN) (3.0 mL, 18.2 mmol L−1) was atomized using an air compression-type atomizer (DH-M01, DongHan, China), fed (0.36 mL min−1) to a side surface of a cotton fabric sample (30 × 30 mm) for 5 min, and dried at 80 °C for 10 min to obtain ACN treated cotton fabric. The monomer solution was atomized, fed (0.8 mL min−1) to the ACN cotton sample for 5 min, heated at 60 °C overnight and at 180 °C for 5 min, washed with deionized water (50 mL × 3 times), dried at 80 °C for 2 h. Other modified cotton fabric samples were prepared using the procedures shown in Table 1. Fully modified cotton fabric was prepared under a similar process but changed the mist feeding step with an immersion treatment in the monomer solution.
Table 1 Preparation conditions and burning rate of the fabric samples
Sample |
Finishing methods |
Monomers |
Burning rate (mm s−1) |
Burning rateb (mm s−1) |
ACN aqueous solution (18.2 mmol L−1, 5 min) and the monomer solution (PBBA in acetone: 24 mmol L−1, DVB: 0.48 mmol L−1, 5 min). The burning rate of the sample after 150 abrasion cycles. ACN treated for 15 min and the monomer solution treated for 30 min. |
Pristine cotton |
— |
— |
3.00 ± 0.03 |
3.00 ± 0.03 |
FR-cotton1 |
Mista |
PBBA, DVB |
1.76 ± 0.08 |
3.00 ± 0.09 |
FR-cotton2 |
Mist |
PBBA, DVB, AA (24 mmol L−1) |
1.70 ± 0.07 |
2.24 ± 0.11 |
FR-cotton3 |
Mist |
PBBA, DVB, MA (12 mmol L−1) |
1.66 ± 0.08 |
1.98 ± 0.11 |
FR-cotton4 |
Mist |
PBBA, DVB, MA (24 mmol L−1) |
1.60 ± 0.07 |
1.72 ± 0.08 |
FR-cotton5 |
Mist |
PBBA, DVB, MA (36 mmol L−1) |
1.65 ± 0.08 |
1.72 ± 0.09 |
FR-cotton6 |
Immersionc |
PBBA, DVB, MA (24 mmol L−1) |
1.57 ± 0.06 |
1.76 ± 0.11 |
Characterizations
Fourier transform infrared (FTIR) measurements were performed on a Nicolet Avatar 370 spectrometer (Nicolet Company, Madison, USA) in a normal transmission mode. 1H-NMR spectra were recorded on an Avance AV-400 (400 MHz) NMR spectrometer (Bruker, Switzerland) in CDCl3 with TMS as an internal standard. Fabric surface was observed by a JSM-6700F field emission scanning electron microscope (FE-SEM, JEOL, Japan) after gold coating (thickness of approximately 10 nm). Attenuated total reflectance infrared (ATR-IR) spectra were collected utilizing a Nicolet Avatar 370 spectrometer (Nicolet Company, Madison, USA) equipped with an ATR accessory. Fabric abrasion tests were performed using a Martindale abrasion instrument (HZ-8029A, Heng Zhun Instrument Co., Ltd, China) according to the method of DIN EN ISO 12947-3.
The vertical burning test was carried out directly burning the fabric for 10 s in the flame of alcohol burner, referring to the standard test method ENISO 15025. The cotton fabric samples was folded to make the modified surface outward to flame (before burning), and the burning state of the fabrics was recorded by a camera. To compare the flammability of the cotton samples with and without FR modification, a cotton fabric (60 × 60 mm) having half-modified surface was prepared by combining the mist polymerization process (same to FR-cotton4) with a shielding over the other half to keep the original cotton surface. To check the durability of the FR coating, the modified fabric samples after 150 abrasion cycles (abrasion conditions were same to previous works40–42) were evaluated using the flame resistance test described above.
In order to further verify the flammability, the combustion behavior of the cotton fabrics was also evaluated by cone calorimeter (FTT Company, UK) with a heat flux of 35 kW m−2. The flammability indexes of total heat release (THR), peak of heat release (PHRR), time to ignition (TTI), and average mass loss rate (AMLR) were simultaneously measured. According to the ISO 5660 standard, the samples were cut into the size of 100 × 100 mm2 and wrapped with aluminum foil and placed in a frame with grid. The measurement was repeated to triplicate and the average data were reported.
Water absorption ability, water vapor permeability, tensile strength, and flexibility of the modified cotton fabrics were determined using the methods reported in our pervious works.43–47
Results and discussion
Synthesis of the flame retardant monomer
As shown in Fig. 1a, the PBBA monomer was synthesized by reacting AA with PBBBr, which was obtained by brominating PBB. Fig. 1b shows the FTIR spectra of PBBA and PBBBr. The peaks at 624 cm−1 and 1429 cm−1 in the spectrum of PBBBr are attributable to the CH2–Br stretching and –CH2 bending, respectively. However, these peaks disappeared in the spectrum of PBBA, and were displaced by a strong absorption peak at 1730 cm−1, meaning that the CH2–Br structure has been substituted by an acrylate group. The molecular structure of PBBA was further confirmed by the 1H-NMR spectra shown in Fig. 1c. The peak at 5.01 ppm is attributable to the methylene groups in PBBBr, and the peak at 5.69 ppm is corresponded to the –CH2CO2– structure in PBBA. In addition, the peaks at 5.90 ppm and 6.45 ppm are believed due to the cis and trans structures of
CH2, and the peak at 6.15 ppm is assignable to the proton in the
CH– bond.
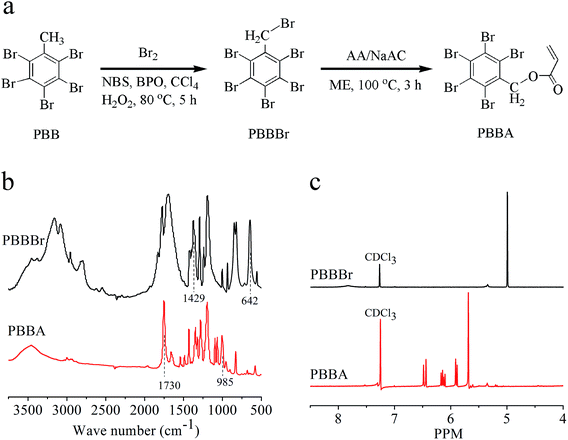 |
| Fig. 1 The synthesis of PBBA monomer (a), FTIR spectra of PBBBr and PBBA (b), 1H NMR spectra of PBBBr and PBBA (c). | |
Fabrication of the FR cotton surfaces
The FR layer on the cotton fabric was obtained through a two-step procedure (Scheme 1). The oxidation of cellulose by ACN gives radicals first. Then the mist copolymerization, which was initiated by the resulting radicals, forms the copolymer layer on the cotton fiber surface. The three monomers in the mist copolymerization play respective roles: DVB is used as a cross-linker; MA is designed to introduce ester groups to react with the hydroxyl groups of cellulose; and PBBA acts as the functional monomer to decrease the flammability of cotton fabric.
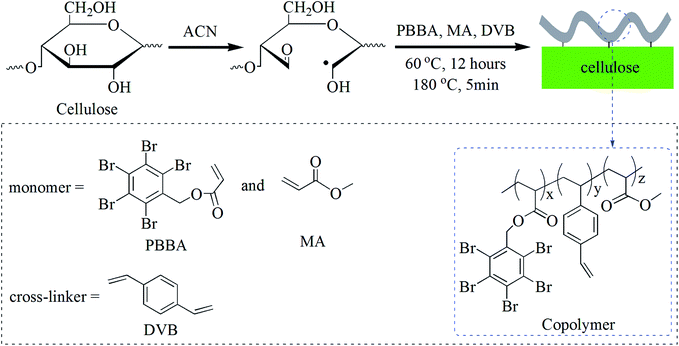 |
| Scheme 1 Scheme of the surface modification on a single side of cotton fabric. | |
Our previous works45,46 reported that the diameters of the mist droplets range from 150 to 500 nm, and only a small number of the droplets (about 3%) is fixed on the cotton surface during the mist feeding. Therefore, mist copolymerization generally results a thin polymeric layer on a single side surface of the substrate.
Five fabric samples (Table 1) were prepared using mist polymerization, and their modified surfaces were examined using ATR-IR surface analysis technique. Fig. 2 compares the ATR-IR spectra with a comparison with pristine cotton. One characteristic peak appeared at 1725 cm−1 in the spectra of modified cotton fabrics but not in the spectra of pristine cotton fabric and the opposite surfaces (data not shown). This peak is attributable to the covalent bond of C
O in the ester structure, meaning that the mist copolymerization took place on the single side surface of the cotton fabric.
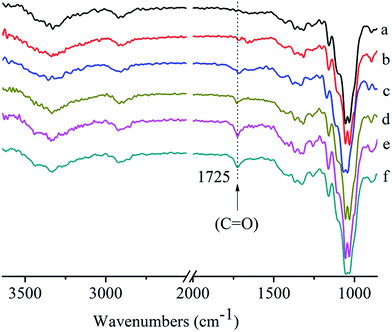 |
| Fig. 2 ATR-IR spectra of pristine cotton (a), FR-cotton1 (b), FR-cotton2 (c), FR-cotton3 (d), FR-cotton4 (e), FR-cotton5 (f). | |
The low-magnification SEM images for pristine cotton and FR-cotton4 (Fig. 3a and b) display nothing significantly different, meaning that the copolymer layer formed on the cotton fiber surface was very thin. The high-magnification SEM images (Fig. 3c–f) further suggest that the copolymer layer possesses a thinness of approximately 200 nm.
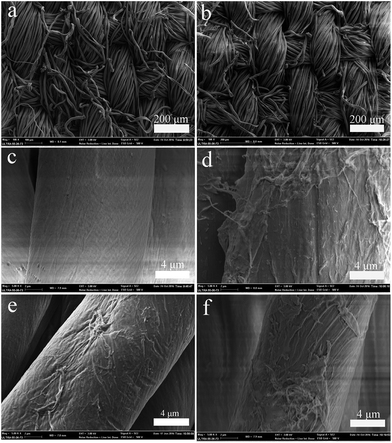 |
| Fig. 3 Low magnification SEM images of pristine cotton (a) and FR-cotton4 (b); high magnification SEM images of pristine cotton (c), FR-cotton1 (d), FR-cotton2 (e), and FR-cotton4 (f). | |
Flame resistance of the FR cotton surfaces
First, the flame resistance of the modified surfaces was tested by burning the fabrics in a flame for 10 s (Fig. 4) as an improved method basing on the standard test method ENISO 15025. Before the burning test, the fabric sample was folded to make the modified surface outward to flame, and the whole burning process was recorded by an optical camera. As a result, the pristine cotton fabric (Fig. 4a) was almost completely burned in 10 s, whereas the modified cottons (Fig. 4b–d) were partly burned. As shown in Table 1, in contrast with the pristine cotton (burning rate was 3 mm s−1), all the modified fabric samples exhibited significant flame resistance effect, especially, FR-cotton4 slowed the burning rate to 1.60 mm s−1. To investigate wearing durability of the FR coatings, the modified surfaces were abraded using a Martindale abrasion instrument. The flame resistance effect of the samples after 150 abrasion cycles was evaluated again using the improved flame resistance method. As shown in Fig. 5, FR-cotton1 (Fig. 5b) was burning fast as pristine cotton (Fig. 5a), suggesting that the FR function was lost after the repeated abrasion tests. In contrast, the copolymer coating containing MA monomer showed a promising abrasion resistance (Fig. 5d). The reason may be assigned to the covalent ester linkages between the copolymer layer and the cellulose chains. When compared with FR-cotton3 (Table 1), FR-cotton4 exhibited more satisfactory stability against repeated abrasion tests. In spite of the increased MA concentration, FR-cotton5 showed the durability similar to FR-cotton4, meaning that 24 mmol L−1 of the MA concentration was enough to enhance the durability against abrasion. After 150 cycles of the abrasion tests under a pressure of 12 kPa, the fabric sample still has good flame retardance (losing 7.5% in burning rate). This result suggested that the modified fabric can be used for practical applications such as curtain.44,55 Moreover, the addition of monomer AA (FR-cotton2) imparted the FR coating without satisfying improvement on the wearing durability (Fig. 5c), suggesting that the transesterification of the MA units occurred more easily than the esterification of the AA units. To further compare the flammability of the modified surfaces, a cotton fabric (60 × 60 mm) with a shelter over its half area, was subjected to the mist copolymerization process (condition is same to FR-cotton4) to make the FR layer coated on the other area of the fabric surface. This special fabric was folded to align the two areas, suspended above the flame to fire it, and quenched immediately after it was ignited for 1.0 seconds. Its burned hollow shown in Fig. 6a indicates that the modified area has improved FR effect by comparing with the original part, suggesting that the copolymer layer on cotton surface can prolong the ignition time. On the other hand, the burning result shown in Fig. 6b indicates that the opposite surface of the fabric has a burning rate same to original cotton. Because the mist copolymerization gives a single-side surface modification, this result is very understandable.
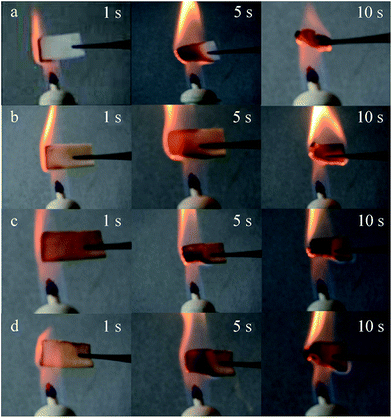 |
| Fig. 4 Photographs of the cotton fabrics in burning. (a) Pristine cotton, (b) FR-cotton1, (c) FR-cotton2, and (d) FR-cotton4. | |
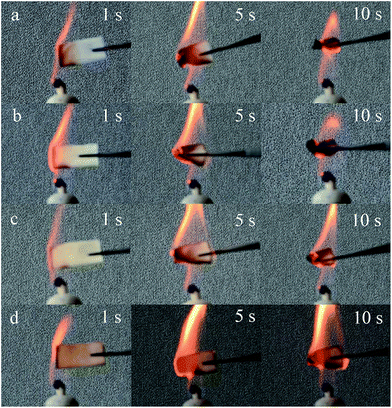 |
| Fig. 5 Photographs of the cotton fabrics (after the abrasion test) in burning. (a) Pristine cotton, (b) FR-cotton1, (c) FR-cotton2, and (d) FR-cotton4. | |
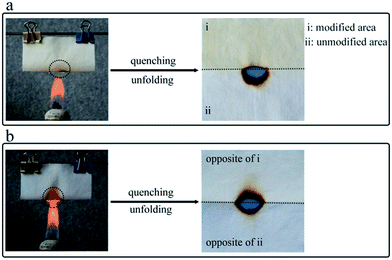 |
| Fig. 6 Photographs of the combustion tests of the special cotton fabric. (a) The modified area was outward to flame. (b) The modified area was inward to flame. | |
To estimate the combustion properties using cone calorimetry method, cotton fabric samples were wrapped with aluminum foil to make the modified surface up on a specimen holder. Fig. 7 shows the heat release rate (HRR) curves of pristine cotton and FR-cotton4 at a heating flow of 35 kW m−2, and the cone calorimetry data were collected in Table 2. Cotton fabric is a flammable material, its peak heat release rate (PHRR) reaches a value ≈ 114 kW m−2. In comparison, the PHRR of the FR-cotton4 was reduced by about 23%. The time to ignition (TTI) of the FR-cotton4 is 6 s, longer than that of the pristine cotton. Both the total heat release (THR) and the average mass loss rate (AMLR) were slightly reduced, indicating again that the copolymer layer has an effective FR function for the cotton textile.
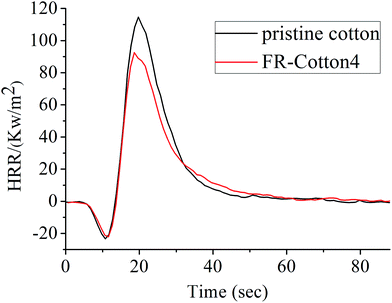 |
| Fig. 7 HRR curves for the pristine cotton and FR-cotton4. | |
Table 2 Cone calorimetry data of the fabric samplesa
Sample |
TTI (s) |
PHRR (kW m−2) |
THR (MJ m−2) |
AMLR (g s−1) |
TTI: time to ignition; PHRR: peak heat release rate; THR: total heat release; AMLR: average mass loss rate. |
Pristine cotton |
4 |
113.97 ± 6 |
13.46 ± 0.7 |
0.024 ± 0.003 |
FR-cotton4 |
6 |
92.51 ± 5 |
12.42 ± 0.5 |
0.020 ± 0.003 |
Influences on the intrinsic properties of cotton
As shown in Fig. 8i, the pristine cotton samples are of excellent water absorptivity (about 260%), but the samples prepared using immersion method (FR-cotton6) are poor at 130%. In contrast, the cotton fabrics modified by the mist copolymerization show good water absorptivity ranging from 245 to 218%, which is slightly lower than that of the original cotton fabric. These results suggest that the single sided modification keeps a large part of the excellent water absorptivity of cotton. For most clothing products, the desired water absorption can lower wetting of sweat, thereby being pleasant for the wearer.
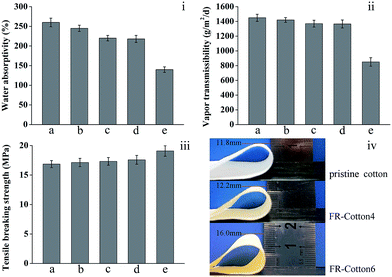 |
| Fig. 8 The comparison in water absorbability (i), water vapor transmissibility (ii), tensile strength (iii), and flexibility (iv) of the cotton fabrics. (a) Pristine cotton, (b) FR-cotton1, (c) FR-cotton2, (d) FR-cotton4, and (e) FR-cotton6. | |
The vapor transmission rate of pristine cotton fabrics is 1450 ± 48 g per m2 per day (Fig. 8ii), indicating that the original cotton fabric has good permeability to water vapor. However, the vapor transmission rate was decreased to about 58% by the immersion treatment (FR-cotton6, 850 ± 43 g per m2 per day). Comparatively, the mist copolymerization process gave acceptable vapor transmission rates above 1300 g per m2 per day, which is very near to that of the original cotton fabric (90%).
The mechanical properties of the cotton fabrics were also studied by measuring the breaking tensile strength. As shown in Fig. 8iii, the pristine cotton fabric has a general breaking strength of 16.85 MPa, whereas the FR-cotton4 was lightly strengthened to 17.31 MPa, indicating that the mechanical damages caused by the finishing treatments are quite small.
Fig. 8iv compares the flexibilities of the modified cotton fabrics. The original cotton fabric exhibited a good flexibility, as the height of the loop less than 11.8 mm. While the FR-cotton6 revealed a large loop height of more than 16.0 mm, meaning that the flexibility damage caused by the immersion method is serious. The sample obtained by the mist copolymerization process (FR-cotton4) has a loop height of 12.2 mm, which is very near to that of the original cotton fabric, suggesting that the mist copolymerization impaired the cotton flexibility insignificantly.
Conclusions
A new type of FR cotton fabric with single faced function was fabricated through a mist copolymerization technique. Unlike most other flame-retardant fabrics, this fabric exhibits asymmetric FR property on two faces: one face is of FR function but the opposite same to original cotton. The modified cotton fabrics delay the burning rate in the combustion tests and show positive FR behavior (including TTI, PHRR, THR and AMLR) in the cone calorimeter experiments. Moreover, the single face modification gives not serious damages on the desired cotton natures such as water absorption and vapor transmissibility. Considering the excellent balance of the new FR function and the intrinsic cotton natures, the method demonstrated in this work is believed to have promising potential in textile industries.
Conflicts of interest
There are no conflicts of interest to declare.
Acknowledgements
This work was financially supported by the Natural Science Foundation of China (51573167) and Public Welfare Technology Application Research Project of Zhejiang Province (2017C31035 and 2017C33154).
References
- Y. Y. Zhang, Q. B. Xu, F. Y. Fu and X. D. Liu, Cellulose, 2016, 23, 2791–2808 CrossRef CAS.
- Y. Gao and R. Cranston, Text. Res. J., 2008, 78, 60–72 CrossRef CAS.
- Y. L. Lam, C. W. Kan and C. W. M. Yuen, Text. Prog., 2012, 44, 175–249 CrossRef.
- Q. B. Xu, L. J. Xie, H. L. Diao, F. Li, Y. Y. Zhang, F. Y. Fu and X. D. Liu, Carbohydr. Polym., 2017, 177, 187–193 CrossRef CAS PubMed.
- I. Ahmad and C. W. Kan, Materials, 2016, 9, 892 CrossRef PubMed.
- A. Milionis, E. Loth and I. S. Bayer, Adv. Colloid Interface Sci., 2016, 229, 57–79 CrossRef CAS PubMed.
- Z. Xue, M. Liu and L. Jiang, J. Polym. Sci., Part B: Polym. Phys., 2012, 50, 1209–1224 CrossRef CAS.
- M. C. Wu, B. H. Ma, T. Z. Pan, S. S. Chen and J. Q. Sun, Adv. Funct. Mater., 2016, 26, 569–576 CrossRef CAS.
- Z. J. Wang, Y. Wang and G. J. Liu, Angew. Chem., Int. Ed., 2016, 55, 1291–1294 CrossRef CAS PubMed.
- Z. J. Wang, M. Lehtinen and G. J. Liu, Angew. Chem., Int. Ed., 2017, 56, 12892–12897 CrossRef CAS PubMed.
- J. Molina, RSC Adv., 2016, 6, 68261–68291 RSC.
- D. P. Hansora, N. G. Shimpi and S. Mishra, RSC Adv., 2015, 5, 107716–107770 RSC.
- A. K. Yetisen, H. Qu, A. Manbachi, H. Butt, M. R. Dokmeci, J. P. Hinestroza, M. Skorobogatiy, A. Khademhosseini and S. H. Yun, ACS Nano, 2016, 10, 3042–3068 CrossRef CAS PubMed.
- J. Chen, J. Xu, K. Wang, X. Qian and R. Sun, ACS Appl. Mater. Interfaces, 2015, 7, 15641–15648 CAS.
- J. Alongi and G. Malucelli, RSC Adv., 2015, 5, 24239–24263 RSC.
- S. Y. Liang, N. M. Neisius and S. Gaan, Prog. Org. Coat., 2013, 76, 1642–1665 CrossRef CAS.
- K. A. Salmeia, S. Gaan and G. Malucelli, Polymers, 2016, 8, 319 CrossRef.
- J. Alongi, F. Carosio and P. Kiekens, Polymers, 2016, 8, 357 CrossRef.
- G. Malucelli, Coatings, 2016, 6, 33 CrossRef.
- M. E. Mngomezulu, M. J. John, V. Jacobs and A. S. Luyt, Carbohydr. Polym., 2014, 111, 149–182 CrossRef CAS PubMed.
- S. Basak and S. W. Ali, Polym. Degrad. Stab., 2016, 133, 47–64 CrossRef CAS.
- Z. Shariatinia, N. Javeri and S. Shekarriz, Carbohydr. Polym., 2015, 118, 183–198 CrossRef CAS PubMed.
- K. Xie, A. Gao and Y. Zhang, Carbohydr. Polym., 2013, 98, 706–710 CrossRef CAS PubMed.
- D. Z. Chen, F. X. Chen, H. W. Zhang, X. Z. Yin and Y. S. Zhou, Cellulose, 2016, 23, 941–953 CrossRef CAS.
- W. W. Gao, G. X. Zhang and F. X. Zhang, Cellulose, 2015, 22, 2787–2796 CrossRef CAS.
- C. H. Xue, L. Zhang, P. Wei and S. T. Jia, Cellulose, 2016, 23, 1471–1480 CrossRef CAS.
- D. D. Zheng, J. F. Zhou, L. Zhong, F. X. Zhang and G. X. Zhang, Cellulose, 2016, 23, 2211–2220 CrossRef CAS.
- S. S. Chen, X. Li, Y. Li and J. Q. Sun, ACS Nano, 2015, 9, 4070–4076 CrossRef CAS PubMed.
- Y. C. Li, J. Schulz and J. C. Grunlan, ACS Appl. Mater. Interfaces, 2009, 1, 2338–2347 CAS.
- Y. C. Li, S. Mannen, A. B. Morgan, S. Chang, Y.-H. Yang, B. Condon and J. C. Grunlan, Adv. Mater., 2011, 23, 3926–3931 CrossRef CAS PubMed.
- J. Alongi, F. Carosio, A. Frache and G. Malucelli, Carbohydr. Polym., 2013, 92, 114–119 CrossRef CAS PubMed.
- F. Carosio, C. Negrell-Guirao, A. Di-Blasio, J. Alongi, G. David and G. Camino, Carbohydr. Polym., 2015, 115, 752–759 CrossRef CAS PubMed.
- J. C. Yang, W. Liao, S. B. Deng, Z. J. Cao and Y. Z. Wang, Carbohydr. Polym., 2016, 151, 434–440 CrossRef CAS PubMed.
- F. Fang, B. Tong, T. X. Du, X. Zhang, Y. D. Meng, X. L. Liu and X. Y. Tian, Cellulose, 2016, 23, 3341–3354 CrossRef CAS.
- H. Pan, W. Wang, Y. Pan, W. Zeng, J. Zhan, L. Song, Y. Hu and K. M. Liew, Cellulose, 2015, 22, 911–923 CrossRef CAS.
- S. Chang, R. P. Slopek, B. Condon and J. C. Grunlan, Ind. Eng. Chem. Res., 2014, 53, 3805–3812 CrossRef CAS.
- K. Ariga, J. P. Hill and Q. Ji, Phys. Chem. Chem. Phys., 2007, 9, 2319–2340 RSC.
- D. Caschera, R. G. Toro, F. Federici, C. Riccucci, G. M. Ingo, G. Gigli and B. Cortese, Cellulose, 2015, 22, 2797–2809 CrossRef CAS.
- J. Alongi, M. Ciobanu and G. Malucelli, Carbohydr. Polym., 2011, 85, 599–608 CrossRef CAS.
- J. Alongi, M. Ciobanu and G. Malucelli, Carbohydr. Polym., 2012, 87, 2093–2099 CrossRef CAS.
- J. Alongi, M. Ciobanu and G. Malucelli, Carbohydr. Polym., 2012, 87, 627–635 CrossRef CAS.
- A. El-Shafei, M. ElShemy and A. Abou-Okeil, Carbohydr. Polym., 2015, 118, 83–90 CrossRef CAS PubMed.
- S. J. Wan, L. Wang, X. J. Xu, C. H. Zhao and X. D. Liu, Soft Matter, 2014, 10, 903–910 RSC.
- G. H. Xi, J. Wang, G. Y. Luo, Y. H. Zhu, W. C. Fan, M. Q. Huang, H. Q. Wang and X. D. Liu, Cellulose, 2016, 23, 915–927 CrossRef CAS.
- L. Wang, G. H. Xi, S. J. Wan, C. H. Zhao and X. D. Liu, Cellulose, 2014, 21, 2983–2994 CrossRef CAS.
- G. H. Xi, W. C. Fan, L. Wang, X. D. Liu and T. Endo, J. Polym. Sci., Part A: Polym. Chem., 2015, 53, 1862–1871 CrossRef CAS.
- W. C. Fan, Y. H. Zhu, G. H. Xi, M. Q. Huang and X. D. Liu, J. Appl. Polym. Sci., 2016, 133, 43024 Search PubMed.
- M. Lewin, J. Zhang, E. Pearce and M. Zammarano, Polym. Adv. Technol., 2010, 21, 825–834 CrossRef CAS.
- Y. Yuan, A. Siegmann and M. Narkis, J. Appl. Polym. Sci., 2010, 60, 1475–1481 CrossRef.
- J. Goldshtein, T. Lublin-Tennenbaum and S. Margel, Polym. Int., 2011, 60, 1587–1593 CrossRef CAS.
- E. M. Gutman and A. L. Bobovitch, J. Therm. Anal. Calorim., 1998, 51, 245–250 CrossRef CAS.
- E. Gutman, A. Bobovitch, A. Pinski, L. Utevski, D. Sondak and M. Muskatel, J. Therm. Anal., 1996, 46, 1541–1550 CrossRef CAS.
- L. Melamed, E. Eden, M. Leifer and P. Georlette, Fire Technol., 2015, 51, 41–52 CrossRef.
- G. D. Merfeld, T. T. Maa, K. Chan and D. R. Paul, Polymer, 2000, 41, 663–674 CrossRef CAS.
- A. Varesano, B. Antognozzi and C. Tonin, Synth. Met., 2010, 160, 1683–1687 CrossRef CAS.
|
This journal is © The Royal Society of Chemistry 2017 |
Click here to see how this site uses Cookies. View our privacy policy here.