DOI:
10.1039/C7RA10831A
(Paper)
RSC Adv., 2017,
7, 56426-56432
Zwitterionic polymers showing upper critical solution temperature behavior as draw solutes for forward osmosis
Received
30th September 2017
, Accepted 8th December 2017
First published on 15th December 2017
Abstract
We synthesized the zwitterionic homopolymer polysulfobetaine (PBET), which shows upper critical solution temperature (UCST) characteristics, via free radical polymerization in order to investigate its suitability as a draw solute for the forward osmosis (FO) process. The FO and recovery properties of PBET were systematically investigated. The UCST characteristics of the monomer sulfobetaine (BET) were not confirmed, while the UCST of PBET was confirmed to be approximately 40 °C. This result suggests that PBET can be easily recovered from aqueous solutions by cooling them to below the UCST. In an active layer facing feed solution (AL-FS) system containing 20 wt% PBET at a temperature of 50 °C, the water flux and reverse solute flux of PBET were found to be approximately 3.22 LMH and 0.36 gMH, respectively. Thus, we investigated the suitability of homopolymers having UCST characteristics as draw solutes for the FO process for the first time.
1 Introduction
Membrane separation has been widely used as a water treatment technology in order to provide fresh water to humankind. One of the membrane separation processes, forward osmosis (FO), shows superior energy efficiency to other methods, and FO has therefore received some attention as a next-generation water treatment technology.1,2 However, improving the energy efficiency of the recovery of draw solutes from water is important for the commercialization of FO technology.3 An economic method of recovering draw solutes has been actively investigated as interest in energy efficiency has increased, with attention being paid to the recovery characteristics of draw solutes.4
Draw solutes are largely divided into inorganic-based, organic-based, and inorganic/organic hybrid draw solutes. Materials that have been identified as inorganic-based draw solutes include conventional inorganic salts.5 For example, Elimelech et al. have investigated ammonium bicarbonate (NH4HCO3) that was derived from two substances, ammonia (NH3) and carbon dioxide (CO2), as a draw solute. However, the decomposition of NH4HCO3 into NH3 and CO2 in the separation process requires a high temperature (>60 °C), and it is known that it is difficult to completely remove decomposed NH3 from solutions.6 As an alternative to the approaches used previously, one study has reported the direct use of an inorganic draw solution that had undergone FO as a fertilizer, without a prior recovery process.7
Organic-based draw solutes include organic molecules, polyelectrolytes, hydrogels, and responsive polymers.8–13 The molecular sizes of such organic molecules are large compared to inorganic molecules, and their reverse solute flux is low compared to inorganic draw solutes.10 Studies have reported that pure water can be obtained through distillation after FO filtration using volatile organic molecules such as dimethyl ether as draw solutes.5,14,15 Polyelectrolytes16,17 have the advantage of negligibly small reverse solute fluxes in the FO process when compared to the organic molecules previously described.18 As another example, hydrogels typically form composites with FO membranes that capture water in a crosslinked hydrogel network during the FO process. The hydrogel can then be dehydrated by various external stimuli to remove this water, resulting in the volume of the hydrogel contracting and pure water being obtained.19–21 However, hydrogels have a disadvantage in that the difference between the osmotic pressure of the draw solution and the feed solution is reduced due to the Gibbs–Donnan effect. Responsive polymers can be separated from water by controlling their solubility in response to external stimuli such as CO2 and temperature.22–27 For example, amine-type polymers are quaternized in response to external CO2. The polarity of these quaternized polymers, which have ionic charges, induces the movement of water. On the other hand, the dequaternized polymer loses its ionic charge and become an insoluble salt, allowing it to be separated from water.22 Thermo-responsive polymers are draw solutes that utilize lower critical solution temperature (LCST) and upper critical solution temperature (UCST) characteristics, and they can be simply separated from water by controlling their solubility through temperature changes.23–28 A previous study reported that a thermo-responsive copolymer contains monomers that are responsible for the osmotic pressure and the recovery properties, respectively, and that the copolymer can have a trade-off relationship between the osmotic pressure and the recovery depending on the molar ratio of the monomers that induce each property.24 Although research on thermo-responsive draw solutes with LCST characteristics is active, few studies have reported the development of draw solutes using UCST characteristics.
Inorganic/organic hybrid draw solutes include hydroacid complexes and functionalized MNPs (magnetic nanoparticles). Hydroacid complexes are coordination complexes of metals with organic molecules that induce high osmotic pressure and have low reverse solute fluxes.29–31 Functionalized MNPs are prepared by the ligand exchange of organic molecules that induce osmotic pressure on nano-sized metals with magnetic properties, allowing them to be separated from water using a magnetic field after FO.32,33 Some studies have investigated multi-functional MNPs by attaching organic molecules responsive to temperature, light, and CO2 to MNPs.34–36
In this study, we synthesized a zwitterionic homopolymer of sulfobetaine that is known to have UCST properties that are biocompatible37 and responsive to temperature changes38 as a draw solute candidate for the FO process (Fig. 1). The feasibility of a homopolymer with UCST characteristics as a next-generation draw solute for FO was investigated systematically, including a study of the FO characteristics and recovery method of this draw solute.
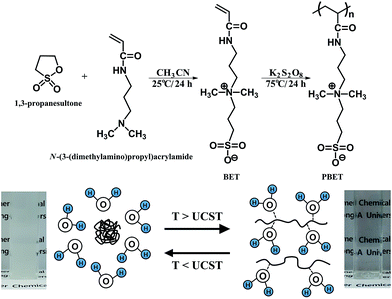 |
| Fig. 1 Synthetic route to zwitterionic homopolymer polysulfobetaine (PBET) and schematic diagram of upper critical solution temperature (UCST) behavior. | |
2 Experimental
2.1. Reagents and instrumentations
1,3-Propanesultone (PS) and N-(3-(dimethylamine)propyl)acrylamide were purchased from Tokyo Chemical Industry Co., Ltd., and acetonitrile was purchased from Sigma Aldrich Co., LLC. Potassium persulfate was purchased from Fluka. All reagents were used without further purification. Fourier transform-infrared (FT-IR) spectrometry (Thermo Fisher Scientific, NICOLET 380) and Fourier transform nuclear magnetic resonance (NMR) spectrometry (Aglient, MR400 DD2) were used to identify the synthesized structure. Infrared spectrometry was performed on the attenuated total reflection (ATR) mode between 4000 and 670 cm−1. The number average molecular weight (Mn) and polydispersity index were investigated by gel permeation chromatography (GPC). Relative molecular weight measurement was performed using a Shodex GPC-101 with columns SB-806 M HQ in series with a refractive index (RI) detector. Poly(ethylene oxide) and poly(ethylene glycol) were used as standard materials for calibration. The thermal properties of the samples were analysed by measuring weight changes according to temperature using a thermogravimetric analyser (SETARAM Instrumentation, SETSYS Evolution). The rheological properties of the samples were investigated by measuring the shear rate changes using a cone and plate rheometer with a diameter of 40 mm and an angle of 2° (TA Instrument, AR G2, stress control type). The osmotic pressure was measured using an osmometer (KNAUER, SEMI-MICRO OSMOMETER K-7400) by the freezing point depression method. The UCST was measured by observing the turbidity of the draw solution according to the temperature change using a thermocouple (WOOJIN Instrument, WJ-3500). In addition, UCST was undoubtedly determined by observing the transmittance at a wavelength of 550 nm using UV-Vis spectrophotometer (V-1100 DIGITAL SPECTROPHOTOMETER, EMCLAB instruments) coupled with temperature controller (TC-200P, Misung Scientific. Co. Ltd.) by increasing the temperature from 25 to 50 °C. The water flux was determined by measuring the height difference between the solutions on both sides of a home-made U-shaped tube which face two L-shaped glass tubes using clamp. The reverse solute flux was measured by using a conductivity meter (METTLER TOLEDO, Seven2Go pro) to determine the conductivity difference before and after the experiment.
2.2. Synthesis
We synthesized the zwitterionic homopolymer polysulfobetaine (PBET) using free radical polymerization in order to confirm its usability as a draw solute for FO. The synthetic route used was as follows: 30.61 g (0.251 mol) of PS and 39.15 g of N-(3-(dimethylamino)propyl)acrylamide (0.251 mol, 100 mol% PS) were dissolved in acetonitrile (41.15 g, 1.003 mol, 400 mol% PS). The temperature was maintained at 25 °C, and the mixed solution was reacted for 24 h under a nitrogen atmosphere. The resulting solution was precipitated with ethanol and separated via filtration. The solvent was then dried to obtain monomer N,N′-dimethyl(acrylamidopropyl)ammonium propane sulfonate (BET). Nuclear magnetic resonance (NMR) spectrometry is used to determine and confirm BET composition (Fig. 2(a)).
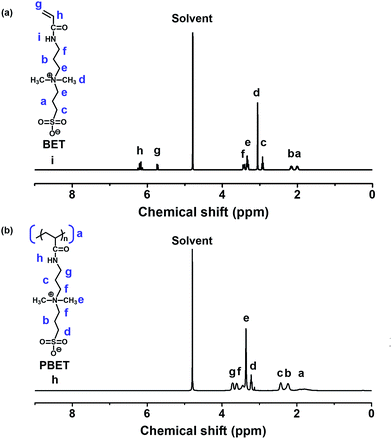 |
| Fig. 2 Nuclear magnetic resonance (NMR) spectra: (a) monomer N,N′-dimethyl(acrylamidopropyl)ammonium propane sulfonate (BET), (b) polysulfobetaine (PBET). | |
1H-NMR of BET [400 MHz, D2O, δ/ppm]: 1.97–2.04 (m, 2H, (–CH2–CH2–CH2–)), 2.12–2.20 (m, 2H, (–CH2–CH2–CH2–)), 2.91–2.95 (t, 2H (–CH2–CH2–SO3−)), 3.06 (s, 6H, (CH3–N+–CH3)), 3.30–3.36 (t, 4H, (–CH2–N+–CH2–)), 3.41–3.45 (t, 2H, (–NH–CH2–CH2–)), 5.71–5.74 (d, 2H, (H2C
CH–CO–)), 6.13–6.25 (t, 1H, (H2C
CH–CO–)).
BET (20 g) and potassium persulfate (1 g, 5 wt% of BET) were mixed into 80 mL of distilled water and held at a temperature of 75 °C for 24 h under a nitrogen atmosphere. The solution was then added to a dialysis tube (Membrane Filtration Products, Inc., Cellu Sep T1 (molecular weight cut off: 3500 Da)) for 24 h to remove the impurities by dialysis. The solution was then heated to 110 °C to remove the remaining water, allowing pure PBET (Mn = 18
000 and polydispersity index = 2.30) to be obtained. Nuclear magnetic resonance (NMR) spectrometry is used to determine and confirm PBET composition (Fig. 2(b)).
1H-NMR of PBET [400 MHz, D2O, δ/ppm]: 1.64–1.97 (m, 3H, (–CH2–CH–)), 2.18–2.33 (m, 2H, (–CH2–CH2–CH2–)), 2.38–2.47 (t, 2H, (–CH2–CH2–CH2–)), 3.20–3.24 (t, 2H (–CH2–CH2–SO3−)), 3.36 (s, 6H, (CH3–N+–CH3)), 3.42–3.46 (t, 2H, (–CH2–CH2–N+–)), 3.57–3.65 (t, 2H, (–N+–CH2–CH2–)), 3.68–3.75 (t, 2H, (–NH–CH2–CH2–)).
2.3. FO performance
Water flux, which is an important property for the FO process, was investigated. The water flux was measured using a small-scale FO system connected to a home-made, cap-fixed L-shaped glass tubes.24,27 A membrane (Hydration Technologies Inc. (HTI), thin film composite FO membrane) was placed in a channel (diameter: 2.3 cm) between two glass tubes. The PBET draw solution was added into one tube, and distilled water was added into the other. The glass tubes were placed into a water bath held at a constant temperature. Measurement of water flux was performed in the active layer facing feed solution method (AL-FS). The temperature was maintained at 50 ± 1 °C during the FO process using a temperature control device (BROOKFILED, TC-500), and the solution was stirred using a magnetic bar and a solenoid (AS ONE, OCTOPUS CS-4). The water flux was determined by measuring the height difference of solution before and after the FO process. The water flux (Jw, (L m−2 h−1, LMH)) was calculated from the volume change of the draw solution using eqn (1). |
 | (1) |
where ΔV is the volume change of the draw solution over time Δt and A is the effective membrane area (4.15 × 10−4 m2).
The reverse solute flux (Js) was determined by analysing the quantity of solute that diffused from the draw solution into the feed solution during the FO process, and the total dissolved solid (TDS) of the feed solution was also measured. The reverse solute flux (Js, g m−2 h−1, gMH) was calculated from the difference between the conductivities of the feed solution before and after the FO process using eqn (2).
|
 | (2) |
where Δ
C (mol L
−1) is the concentration change of the feed solution after time Δ
t and Δ
V (L) is the volume change after time Δ
t.
3 Results and discussion
3.1. Synthesis and characterization of zwitterionic homopolymer polysulfobetaine (PBET)
The synthetic route to zwitterionic homopolymer polysulfobetaine (PBET) is shown in Fig. 1, where it can be seen that PBET is a zwitterionic homopolymer of sulfobetaine. The chemical structures of the synthesized monomer and homopolymer were identified by 1H-NMR spectrometry, respectively. We synthesized the zwitterionic monomer N,N′-dimethyl(acrylamidopropyl)ammonium propane sulfonate (BET). The 1H-NMR spectrum and assignments of the respective peaks of monomer BET was indicated in Fig. 2(a). 1H-NMR spectrum of BET indicates the presence of protons from the vinyl group of BET (δ = 5.71–5.74 ppm (peak h), 6.13–6.25 (peak h)). The proton peaks from the quaternized ammonia cation (δ = 3.06 ppm (peak d)) show the inclusion of the cation moiety in the zwitterionic BET. The anion moiety in the zwitterionic BET is not observed that is not containing hydrogen because of structure of sulfur trioxide. Based on the 1H-NMR analysis, we identified that BET was successfully synthesized, and then synthesized polysulfobetaine (PBET) via free radical polymerization. The disappearance of the vinyl double bond peaks at 5.71–5.74 (H2C
CH–CO–) and 6.13–6.25 (H2C
CH–CO–) ppm and inclusion of BET due to the presences of the proton peaks of amide and quaternized ammonium after the free radical polymerization demonstrate the successful synthesis of PBET as shown in 1H-NMR spectrum of PBET (Fig. 2(b)). We synthesized the zwitterionic homopolymer PBET via free radical polymerization using BET as monomer. The synthesized materials were analysed using FT-IR spectroscopy to confirm that PBET had been synthesized. As shown in Fig. 3, the PBET infrared spectrum confirmed the presence of the amide group (–CO–NH–) through the C
O stretching peak at 1625 cm−1 and the N–H stretching peak at 1521 cm−1. The peak at 1037 cm−1 relates to the stretching of O
S
O, and the peak at 944 cm−1 indicates the stretching of a quaternary ammonium cation. The characteristic IR peaks of the functional groups were identical to those seen in the FT-IR spectra of other polysulfobetaines, confirming that polysulfobetaine was synthesized.39,40
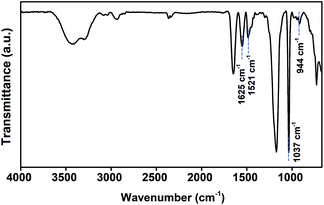 |
| Fig. 3 Fourier transform-infrared (FT-IR) spectrum of PBET. | |
3.2. Thermogravimetry
To analyse the thermal properties of PBET, its pyrolysis behavior was measured up to 800 °C at a heating rate of 10 °C min−1 under an argon atmosphere. The thermogravimetric curve is shown in Fig. 4. The first weight loss, which began at approximately 100 °C, was due to the loss of the water absorbed in the PBET.40 According to the thermogram, the total water content of the polymer was approximately 5 wt%, and thermal decomposition of PBET did not occur in this temperature range. The second transition was confirmed to be cause by the thermal decomposition of the polymer between 254 °C and 483 °C, with the weight decreasing by approximately 62% in this range. At this range, the polymer backbone and branched groups such as quaternized ammonium, and sulfonate groups were fragmented, whereupon hydrocarbons were formed. Finally, generated hydrocarbons remained about 15 wt% char at 800 °C.41 This pyrolysis behavior is similar to that of polysulfobetaine, as reported previously by other research groups.41,42 Therefore, this thermal analysis indicates that the homopolymer PBET having thermal stability at operating temperature higher than UCST is available for draw solute in the forward osmosis process, of which UCST characteristics will be mentioned later.
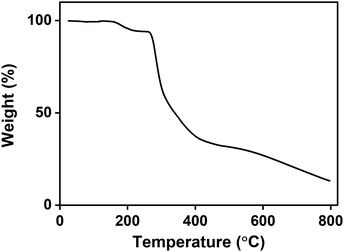 |
| Fig. 4 Thermogravimetric curve of PBET. | |
3.3. Viscosity
Viscosity is an important factor that affects the FO behavior of a draw solution, and has a substantial effect on the efficiency of the FO process. Typically, a solution with a high viscosity can induce ICP (internal concentration polarization) and ECP (external concentration polarization) on the membrane, which can reduce the water flux of the draw solution.18,43 The viscosity of PBET was measured as 50 °C, which is higher than the phase separation temperature of PBET, as will be discussed later. For comparison purposes, the viscosity of the monomer BET was measured at room temperature and at 50 °C by varying the shear rate from 0.1 to 100 [s−1]. The results are shown in Fig. 5. Fig. 5(a) and (b) show that the viscosity of BET was observed in the range between 1 cP and 1.47 cP at room temperature and 50 °C, with no significant changes in viscosity according to concentration being indicated. As shown in Fig. 5(c), the viscosity of PBET was approximately 1.62, 3.65, 7.36, and 17.69 cP according to concentration of 5, 10, 15, and 20 wt% at 50 °C, respectively. These results are similar to those of other draw solutes, where increases in viscosity with increasing concentration were also observed.16,44 This confirms that the polymer PBET had a relatively higher viscosity than its monomer, BET.
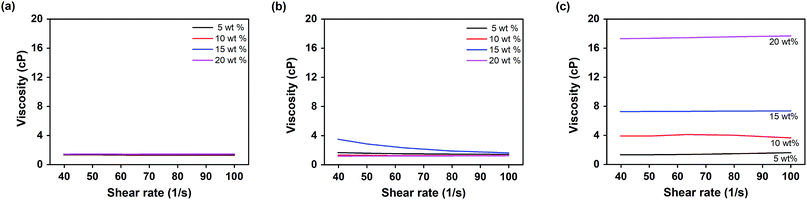 |
| Fig. 5 Viscosity according to the shear rate: (a) BET at room temperature, (b) BET at 50 °C, (c) PBET at 50 °C. | |
3.4. Osmotic pressure
The osmotic pressure of a draw solution is closely related to its concentration, suggesting that osmotic pressure is an important factor when determining FO performance. We used the freezing point depression method to measure the osmotic pressure in order to investigate the usability of PBET as a draw solute. The osmotic pressure of the monomer BET was measured to be approximately 194, 379, 630, and 898 mOsmol kg−1 at concentrations of 5, 10, 15, and 20 wt%, respectively (Fig. 6). These results show that the osmotic pressure increased with increasing concentration, as has been observed in other electrolyte systems that can induce osmotic pressure.16,45 However, since PBET is insoluble at room temperature, it was impossible to measure its osmotic pressure using the freezing point depression method.
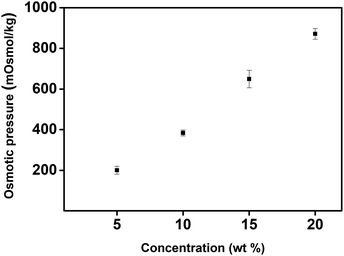 |
| Fig. 6 Osmotic pressure according to the concentration of N,N′-dimethyl(acrylamidopropyl)ammonium propane sulfonate (BET) measured by freezing point depression method. | |
3.5. Recovery properties
The separation of draw solutes from water in the FO process enables the sustainable use of draw solutes. In order to overcome the trade-off between the osmotic pressure and recovery temperature that occurs in thermo-responsive copolymer-based draw solutes, a homopolymer-type draw solute was designed and used in this study. The UCST is defined as the critical temperature at which the draw solute and water in a draw solution change from a homogeneous phase to a heterogeneous phase. To confirm that the draw solute and water were separated into heterogeneous phases, phase separation temperature should be determined transmittance curve of BET and PBET in aqueous solutions according to the temperature change using UV-Vis spectrophotometer. The monomer BET did not show any changes in transmittance curve according to the temperature change from 0 °C to 100 °C (figure not shown), which suggests that BET and water cannot be separated from each other by changing the temperature. Fig. 7 shows transmittance curve of PBET aqueous solution according to the temperature change. The UCST was closely examined by observing the transmittances using UV-Vis spectrophotometer at 550 nm. The transmittance curve exhibits drastic change at approximately 40 °C, which can signify the critical temperature. When the temperature of the PBET solution was higher than the critical temperature, the transmittance of the PBET aqueous solution was approximately 100%. This result indicates that PBET and water were in homogeneous phase. However, when the solution temperature was lower than the critical temperature, the transmittance of the PBET aqueous solution was approximately 0%, which PBET and water were separated into each other becoming heterogeneous phase. As shown in Fig. 1, the solubility of PBET in an aqueous solution depends on the temperature. When the solution temperature is lower than the critical temperature, the ion–ion interactions between the sulfobetaine moieties are stronger than the sulfobetaine–water interactions causing the polymer chains to aggregate and resulting in PBET forming a heterogeneous phase with water. On the other hand, when the solution temperature is higher than the critical temperature, the sulfobetaine–water interaction becomes stronger than the ion–ion interactions between the sulfobetaine moieties, and PBET and water form a homogeneous phase. The critical temperature for the phase separation of PBET and water was found to be approximately 40 °C. We believe that the UCST of PBET was about 40 °C as a result of the transmittance according to the temperature. Therefore, PBET can be simply separated from water by controlling the solubility through temperature changes, and the energy required for this process can be obtained using geothermal heat or the waste heat of power plants.
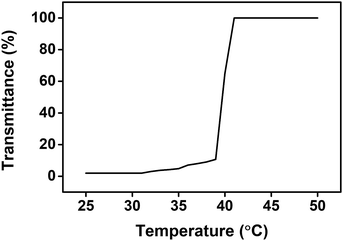 |
| Fig. 7 Transmittance curve of PBET aqueous solution according to the temperature change using UV-Vis spectrophotometer. | |
3.6. Water flux and reverse solute flux
The water flux and reverse solute flux were measured, giving an indication of the FO performance of recoverable PBET (Fig. 8). Measurements of water flux and reverse solute flux were performed in the AL-FS method using home-made glass tubes. The measurements were performed at a temperature of 50 °C, which was above the UCST. Typically, the concentration of the draw solution has an important effect on the FO performance because an increase in the concentration of the draw solution results in an increase in the osmotic pressure, and an increase in osmotic pressure results in an increase in the water flux.6 As expected, the water flux increased to 0.92, 1.39, 2.30, and 3.22 LMH as the concentration of the draw solutes was increased to 5, 10, 15, and 20 wt%, respectively. The measurement of the reverse solute flux was performed simultaneously under the same conditions at which the water flux measurements were conducted, and the amount of reversely diffused draw solutes was determined by comparing the conductivity of the feed solution before and after the FO process. Previous studies have reported that the average pore size of the membrane is small compared to the size of draw solute in an aqueous solution, leading to imperfect prevention of back diffusion to the feed solution.46 The reverse solute flux is generated due to the difference between the concentrations of the draw solution and the feed solution, and the concentration gradient generated on the active layer of the membrane increases according to the difference between the concentrations of the solutions. Thus, the reverse solute flux increases as the concentration of the draw solution increases.47 The reverse solute flux was 0.27, 0.29, 0.35, and 0.36 gMH at draw solute concentrations of 5, 10, 15, and 20 wt%, respectively.
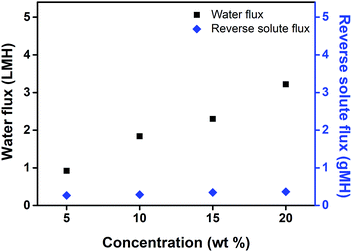 |
| Fig. 8 Water flux and reverse solute flux of PBET according to the concentration at 50 °C during forward osmosis process. | |
4 Conclusions
We synthesized polysulfobetaine (PBET), a type of zwitterionic homopolymer, by using free radical polymerization in order to confirm its usability as draw solute in forward osmosis. In aqueous solutions, PBET shows UCST characteristics, which plays an important role in imparting recoverability to PBET. The UCST of PBET was found to be approximately 40 °C. The water flux of PBET was identified to be approximately 3.22 LMH at 20 wt% and at 50 °C in active layer facing feed solution (AL-FS) system, and the reverse solute flux was identified to be approximately 0.36 gMH under the same conditions. Therefore, a thermo-responsive homopolymer containing zwitterionic moieties that shows an UCST has been shown to be a new draw solute that may surpass the limitations of existing technologies, such as the trade-off between osmotic pressure and recovery temperature in copolymer systems. As a result, this research provides a deep understanding of new ways of developing draw solutes, and could provide inspiration for the design and synthesis of thermo-responsive organic materials.
Conflicts of interest
There are no conflicts to declare.
Acknowledgements
This research was supported by the Basic Science Research Program through the National Research Foundation of Korea (NRF) funded by the Ministry of Education, Science and Technology (NRF-2015R1C1A1A01051654). Financial supports by the Dong-A University Research Fund are gratefully acknowledged.
Notes and references
- P. H. Gleick, in Water in crisis, Pacific Institute for Studies in Dev., Environment & Security. Stockholm Env. Institute, Oxford Univ. Press, 1993, p. 473 Search PubMed.
- L. Chekli, S. Phuntsho, H. K. Shon, S. Vigneswaran, J. Kandasamy and A. Chanan, Desalin. Water Treat., 2012, 43, 167–184 CrossRef CAS.
- S. Zou, H. Yuan, A. Childress and Z. He, Environ. Sci. Technol., 2016, 50, 6827–6829 CrossRef CAS PubMed.
- D. L. Shaffer, J. R. Werber, H. Jaramillo, S. Lin and M. Elimelech, Desalination, 2015, 356, 271–284 CrossRef CAS.
- J. R. McCutcheon, R. L. McGinnis and M. Elimelech, Desalination, 2005, 174, 1–11 CrossRef CAS.
- A. Achilli, T. Y. Cath and A. E. Childress, J. Membr. Sci., 2010, 364, 233–241 CrossRef CAS.
- S. Phuntsho, H. K. Shon, S. Hong, S. Lee and S. Vigneswaran, J. Membr. Sci., 2011, 375, 172–181 CrossRef CAS.
- E. M. Garcia-Castello, J. R. McCutcheon and M. Elimelech, J. Membr. Sci., 2009, 338, 61–66 CrossRef CAS.
- R. E. Kravath and J. A. Davis, Desalination, 1975, 16, 151–155 CrossRef CAS.
- K. Lutchmiah, L. Lauber, K. Roest, D. J. Harmsen, J. W. Post, L. C. Rietveld, J. B. van Lier and E. R. Cornelissen, J. Membr. Sci., 2014, 460, 82–90 CrossRef CAS.
- H. Y. Ng, W. Tang and W. S. Wong, Environ. Sci. Technol., 2006, 40, 2408–2413 CrossRef CAS PubMed.
- H. T. Nguyen, S.-S. Chen, N. C. Nguyen, H. H. Ngo, W. Guo and C.-W. Li, J. Membr. Sci., 2015, 489, 212–219 CrossRef CAS.
- Y. Cai, W. Shen, J. Wei, T. H. Chong, R. Wang, W. B. Krantz, A. G. Fane and X. Hu, Environ. Sci.: Water Res. Technol., 2015, 1, 341–347 CAS.
- G. Batchelder, US Pat. 3 171 799, 1962.
- N. Sato, Y. Sato and S. Yanase, Desalination, 2014, 349, 102–105 CrossRef CAS.
- Q. Ge, J. Su, G. L. Amy and T.-S. Chung, Water Res., 2012, 46, 1318–1326 CrossRef CAS PubMed.
- E. Tian, C. Hu, Y. Qin, Y. Ren, X. Wang, X. Wang, P. Xiao and X. Yang, Desalination, 2015, 360, 130–137 CrossRef CAS.
- Q. Ge, P. Wang, C. Wan and T.-S. Chung, Environ. Sci. Technol., 2012, 46, 6236–6243 CrossRef CAS PubMed.
- D. Li, X. Zhang, J. Yao, G. P. Simon and H. Wang, Chem. Commun., 2011, 47, 1710–1712 RSC.
- Y. Cai, W. Shen, S. L. Loo, W. B. Krantz, R. Wang, A. G. Fane and X. Hu, Water Res., 2013, 47, 3773–3781 CrossRef CAS PubMed.
- J. Wei, Z.-X. Low, R. Ou, G. P. Simon and H. Wang, Water Res., 2016, 96, 292–298 CrossRef CAS PubMed.
- Y. Cai, W. Shen, R. Wang, W. B. Krantz, A. G. Fane and X. Hu, Chem. Commun., 2013, 49, 8377–8379 RSC.
- M. Noh, Y. Mok, S. Lee, H. Kim, S. H. Lee, G.-w. Jin, J.-H. Seo, H. Koo, T. H. Park and Y. Lee, Chem. Commun., 2012, 48, 3845–3847 RSC.
- J.-j. Kim, J.-S. Chung, H. Kang, Y. A. Yu, W. J. Choi, H. J. Kim and J.-C. Lee, Macromol. Res., 2014, 22, 963–970 CrossRef CAS.
- Y. Kohno, S. Saita, Y. Men, J. Yuan and H. Ohno, Polym. Chem., 2015, 6, 2163–2178 RSC.
- Y. Zhong, X. Feng, W. Chen, X. Wang, K.-W. Huang, Y. Gnanou and Z. Lai, Environ. Sci. Technol., 2015, 50, 1039–1045 CrossRef PubMed.
- J.-j. Kim, H. Kang, Y.-S. Choi, Y. A. Yu and J.-C. Lee, Desalination, 2016, 381, 84–94 CrossRef CAS.
- W. Li, J. Li, J. Gao, B. Li, Y. Xia, Y. Meng, Y. Yu, H. Chen, J. Dai, H. Wang and Y. Guo, Biomaterials, 2011, 32, 3832–3844 CrossRef CAS PubMed.
- Q. Ge and T.-S. Chung, Chem. Commun., 2013, 49, 8471–8473 RSC.
- Q. Ge, F. Fu and T.-S. Chung, Water Res., 2014, 58, 230–238 CrossRef CAS PubMed.
- N. T. Hau, S.-S. Chen, N. C. Nguyen, K. Z. Huang, H. H. Ngo and W. Guo, J. Membr. Sci., 2014, 455, 305–311 CrossRef.
- M. M. Ling and T.-S. Chung, Desalination, 2011, 278, 194–202 CrossRef CAS.
- S. Y. Park, H.-W. Ahn, J. W. Chung and S.-Y. Kwak, Desalination, 2016, 397, 22–29 CrossRef CAS.
- Q. Zhao, N. Chen, D. Zhao and X. Lu, ACS Appl. Mater. Interfaces, 2013, 5, 11453–11461 CAS.
- S. Chen, C. X. Guo, Q. Zhao and X. Lu, Chem.–Eur. J., 2014, 20, 14057–14062 CrossRef CAS PubMed.
- H. Han, J. Y. Lee and X. Lu, Chem. Commun., 2013, 49, 6122–6124 RSC.
- S. Jiang and Z. Cao, Adv. Mater., 2010, 22, 920–932 CrossRef CAS PubMed.
- O. Azzaroni, A. A. Brown and W. T. Huck, Angew. Chem., 2006, 118, 1802–1806 CrossRef.
- Y.-F. Mi, Q. Zhao, Y.-L. Ji, Q.-F. An and C.-J. Gao, J. Membr. Sci., 2015, 490, 311–320 CrossRef CAS.
- E. O. Ningrum, A. Purwanto, H. Ni'mah, S. Sumarno, D. I. Dewitasari and E. O. Mulyadi, AIP Conf. Proc., 2017, 1840, 090007 CrossRef.
- R. Lalani and L. Liu, Polymer, 2011, 52, 5344–5354 CrossRef CAS.
- Z. Dong, J. Mao, M. Yang, D. Wang, S. Bo and X. Ji, Langmuir, 2011, 27, 15282–15291 CrossRef CAS PubMed.
- P. H. Duong, S. Chisca, P.-Y. Hong, H. Cheng, S. P. Nunes and T.-S. Chung, ACS Appl. Mater. Interfaces, 2015, 7, 3960–3973 CAS.
- M. L. Stone, A. D. Wilson, M. K. Harrup and F. F. Stewart, Desalination, 2013, 312, 130–136 CrossRef CAS.
- J. R. McCutcheon, R. L. McGinnis and M. Elimelech, J. Membr. Sci., 2006, 278, 114–123 CrossRef CAS.
- W. A. Phillip, J. S. Yong and M. Elimelech, Environ. Sci. Technol., 2010, 44, 5170–5176 CrossRef CAS PubMed.
- C. Y. Tang, Q. She, W. C. Lay, R. Wang and A. G. Fane, J. Membr. Sci., 2010, 354, 123–133 CrossRef CAS.
|
This journal is © The Royal Society of Chemistry 2017 |
Click here to see how this site uses Cookies. View our privacy policy here.