DOI:
10.1039/C7RA10125B
(Paper)
RSC Adv., 2017,
7, 55318-55325
Designing multifunctional SO3H-based polyoxometalate catalysts for oxidative desulfurization in acid deep eutectic solvents
Received
11th September 2017
, Accepted 20th November 2017
First published on 6th December 2017
Abstract
Deep eutectic solvents (DESs) are ‘green’ sustainable solvents with wide applications such as extractive desulfurization of fuel; however, their low extraction efficiency is a major limitation to such applications. In this work, several SO3H-functionalized polyoxometalates were prepared and applied to oxidative desulfurization of fuels with acidic DESs as extractants and 30 wt% of H2O2 as an oxidant. Compared with neutral POM catalysts, acidic catalysts, such as [PSTEtA]3PW12O40, exhibited higher catalytic performance with 100% desulfurization efficiency. However, in the absence of DESs sulfur removal was only 9.6% with [PSTEtA]3PW12O40 used as a catalyst. To study the role of the DESs, three types of DESs were evaluated on extraction and oxidation of dibenzothiophene (DBT), with acidic DES ChCl/2Ac exhibiting the best performance. The effects of different reaction conditions, such as the amount of H2O2 and ChCl/2Ac, reaction temperature and time, different sulfur compounds, and fuel composition, were investigated. Combined with the kinetic study, results suggested that oxidation of DBT was attributed to a pseudo-first-order kinetic reaction. The activities of different sulfur compounds decreased in the order of DBT > 3-methylbenzothiophene (3-MBT) > 4-methyldibenzothiophene (4-MDBT) > 4,6-dimethyldibenzothiophene (4,6-DMDBT) > benzothiophene (BT). Compared with aromatics, the sulfur removal could be strongly affected by olefins, showing a drop of up to 66.6%.
1. Introduction
An increasing number of countries have implemented stringent environmental regulations and fuel standards impel refineries to produce low-sulfur fuel, but technical or economic issues mean these continue to be challenges for many less developed countries. Hydrodesulfurization (HDS) is a widely used technology for deep removal of sulfur compounds from diesel under high temperature and pressure.1–4 However, removal of alkylated dibenzothiophenes (DBTs), such as 4,6-dimethyldibenzothiophene, requires high temperature and pressure, and high-activity catalysts, making the HDS process very expensive.5–7 Several techniques have been developed to address this limitation, the most widely researched of which are oxidative desulfurization (ODS),8–10 adsorptive desulfurization (ADS),11 extractive desulfurization (EDS),12 and biodesulfurization (BDS).13 Oxidative desulfurization has several advantages over the other techniques because of its mild operating conditions and high efficiency for removing DBTs.14
Ionic liquids (ILs) are used in many research fields including synthesis, catalysis, materials science, electrochemistry, and separation processes because of their unique physicochemical properties, namely, thermal stability, non-volatility, non-flammability and adjustable miscibility.15–19 ILs have been reported as benign extractants and efficient catalysts in oxidative desulfurization of fuel.20–23 However, the high cost of the complex synthesis and purification steps may hinder their potential industrial applications.24 Deep eutectic solvents (DESs) have emerged as alternatives to ILs because they have similar characteristics to ILs but are cheaper to produce (lower cost of the raw materials), less toxic, and often biodegradable.25,26 They are formed of quaternary ammonium salts and hydrogen bond donors with a melting point significantly lower than that of either individual component.12,27–29 In 2013, ammonium-based DESs were first applied to extractive desulfurization of fuel.30 Although desulfurization efficiency can reach 99.48%, five extractive steps are required. Another two DESs, choline chloride–glycerol and chlorinated paraffins-52/AlCl3/aromatic, have been prepared and used for extraction of sulfur compounds from fuel;31,32 however, their desulfurization efficiency still cannot match the current stringent standards.
Using a combination of extraction and photochemical oxidative desulfurization of fuels with DESs, it was found that aromatic sulfur compounds can be removed efficiently with air as oxidant under UV light irradiation.33 Without light irradiation, Lü et al. developed an oxalate-based acidic DES in ODS of dibenzothiophene (DBT) under mild reaction conditions.28 This DES was used not only as an extractant but also a catalyst. Simultaneously, Li and his group exploited another acidic DES based on p-toluenesulfonic acid.34 The desulfurization efficiency of benzothiophene (BT) from model oil can reach 99.99%. Therefore, acidic DESs are promising catalysts for oxidative desulfurization.
Polyoxometalates (POMs), especially organic–inorganic hybrid POMs, have been attracting increasing attention in the field of catalytic oxidation because of the tuneable acidic and redox properties of POMs and various cations.35–40 However, the POMs generally show low catalytic activity without solvents or supports in the field of oxidative desulfurization from diesel oil.41,42 Moreover, little research has focused on the use of sulfonic group-substituted POM-based hybrids as catalysts. In the present study, new SO3H-functionalized POMs were prepared to enhance the catalytic performance and different types of DESs were used as extractants. It was found that removal of DBT can reach 100% with acidic POMs as catalysts in acidic DES ChCl/2Ac, which is much higher than that of the neutral POMs. The kinetic models were studied under different molar ratios of H2O2 to DBT and temperatures.
2. Experimental
2.1. Preparation of POM catalysts and DESs
Synthesis of trimethylammonium propanesulfonate (PSTEtA): 1,3-propanesultone (PS, 0.1 mol) was dissolved in 50 mL dichloromethane and stirred for 10 min in an oil bath. Then triethylamine (TEtA, 0.1 mol) was added to the mixture dropwise. The reaction was heated at 40 °C for 24 h. The product (97% of yield) was obtained by filtration, washing by ethyl acetate and diethyl ether and dried at 100 °C. Synthesis of [PSTEtA]nH3−nPW12O40 (n = 1, 2, 3): PSTEtA aqueous solution was added to phosphotungstic acid aqueous solution with a molar ratio of n
:
1 and stirred for 24 h. The final product was dried at 100 °C for 8 h after the water was removed by rotary evaporation. [TBA]3PW12O40 was prepared using the same method as for [PSTEtA]nH3−nPW12O40, where the molar ratio of tetrabutylammonium chloride ([TBAC]) and H3PW12O40 was 3
:
1. Elemental analysis calcd (%) for [TBA]3PW12O40: C 15.99, H 3.02, N 1.17; found: C 15.90, H 2.96, N 1.13. Calcd (%) for [PSTEtA]3PW12O40: C 9.13, H 1.87, N 1.18; found: C 9.05, H 1.86, N 1.08. Other POM catalysts, [1-butyl-3-methylimidazolium]3PW12O40 ([C4mim]3PW12O40), [1-(3-sulfonic group) propyl-3-methylimidazolium]3PW12O40 ([PSmim]3PW12O40) and [(3-sulfonic acid) propylpyridinium]3PW12O40 ([PSPy]3PW12O40), have been synthesized and characterized in previous reports.42
The DESs were prepared by simply mixing choline chloride (ChCl) and butyltrimethylammonium (BTAC) as hydrogen bond donors (HBDs) at a molar ratio of 1
:
2 to obtain homogenous transparent liquids. The mixture was heated to 80 °C in oil bath and reacted at a stirring speed of 800 rpm for 4 h. The detailed products are ChCl/2Ac, ChCl/2PEG, ChCl/2EG, ChCl/2BG, ChCl/2Gl, ChCl/2Fo, ChCl/2Pr, and ChCl/2U with acetic acid (Ac), polyethylene glycol-200 (PEG), ethylene glycol (EG), [1,3-butyleneglycol] (BG), glycerol (2Gl), formic acid (Fo), propanoic acid (Pr), and urea (U) as HBDs, respectively. BTAC/2Ac was prepared with BTAC and acetic acid.
2.2. Characterization
To determine the successful synthesis of the POM catalysts, they were characterized by nuclear magnetic resonance (NMR), Fourier transform infrared spectroscopy (FT-IR) and mass spectrometry (MS). In addition, the solubility of DESs in model oil was detected by 1HNMR and FT-IR.
2.3. Desulfurization test
A certain amount of catalyst was added to a self-made two-necked reaction flask. Then, appropriate amounts of H2O2, DES and 5 mL model oil were added. The mixture was reacted at a stirring speed of 1000 rpm for 2.5 h at a set temperature. The supernatant was stratified after the reaction, and the sulfur content in the model oil was measured by gas chromatography with flame ionization detector and the detection limit of the gas chromatography was 0.15 ppm after calculation. The detailed analysis method used Agilent 7890A, HP-5 column, 30 m long × 0.32 mm inner diameter (id) × 0.25 μm film thickness; injector port temperature, 250 °C; detector temperature, 300 °C; oven temperature, starting at 100 °C and rising to 200 °C at 15 °C min−1 for DBT, BT and 3-MBT, starting at 100 °C and rising to 160 °C at 20 °C min−1 and then rising to 230 °C at 25 °C min−1 for 4-MDBT and 4,6-DMDBT. The formula for calculating the sulfur removal (SR) of model oil is as follows:
SR (%) = (1 − Ct/C0) × 100 |
where C0 represents the initial sulfur content and Ct represents the sulfur content of the model oil after a period of time, respectively.
3. Results and discussion
3.1. Characterization of the POM catalysts
Fig. 1 shows the FT-IR spectra of [PSTEtA]3PW12O40 and [TBA]3PW12O40. The bands ranging from 3000 to 2800 cm−1 are assigned to the stretching vibration of C–H of alkyl chain. The peaks in the range of 1560 cm−1 to 1460 cm−1 are attributed to the bending vibration of C–H. The characteristic peaks at 1080, 980, 897 and 813 cm−1 are assigned to the Keggin structure of PW12O403−.43 The broad stretching vibrations of S
O at about 1218 cm−1 are ascribed to sulfonic groups in catalysts.44 These observations show the corresponding functional groups in the catalysts. The following MS analysis of the catalysts further confirms the presence of both cations and Keggin anions.
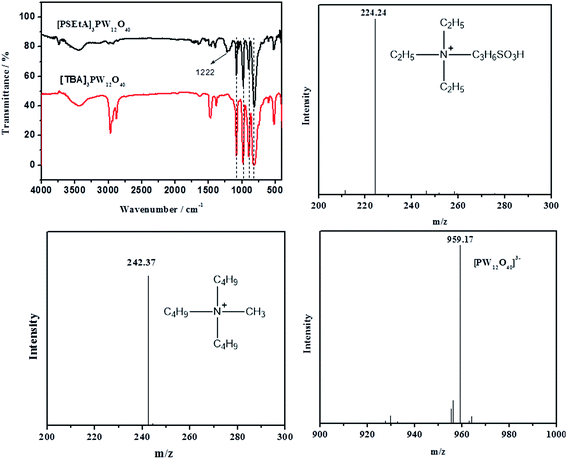 |
| Fig. 1 Characterization of the POM catalysts. | |
3.2. Oxidative desulfurization with different POM catalysts
POMs have been verified to be efficient catalysts; however, previous work has shown that POM-based catalysts have low activity in catalytic oxidation of aromatic sulfides without a suitable solvent.45 Here, two neutral POM catalysts and three acidic POM catalysts were tested for oxidative removal of DBT using DES ChCl/2Ac as extractant and H2O2 as oxidant. As shown in Fig. 2, the sulfur removal was only 15.9% and 30.0% with [C4mim]3PW12O40 and [TBA]3PW12O40 as catalysts. After the catalyst was modified with a SO3H group in the imidazole ring, the catalytic activity of the three acidic catalysts improved remarkably and more than 96.0% of DBT was removed. Sulfur-free fuel can be achieved using [PSTEtA]3PW12O40 as a catalyst. This could be explained by two functions of the SO3H group. The first is that it can transfer to peroxysulfonic acid in the presence of H2O2.46 The second is that the structure of DBT can be distorted by the acidity of the SO3H group, which makes it more susceptible to oxidization.47
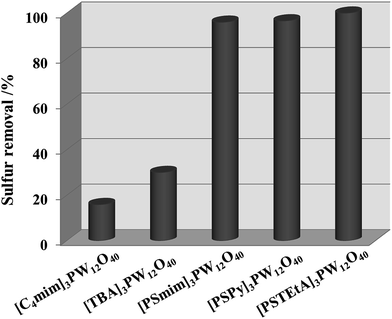 |
| Fig. 2 Oxidative desulfurization with different catalysts. Experimental conditions: n(catalyst)/n(S) = 1 : 11, ChCl/2Ac = 2 mL, O/S = 3, oil = 5 mL, T = 40 °C, t = 2.5 h. | |
3.3. Effect of different kinds of DESs as extractants
As mentioned above, the extractants have a significant impact on oxidation of sulfur compounds. Three types of DES, that is acidic, neutral and basic DESs, were investigated on oxidative desulfurization using [PSTEtA]3PW12O40 as the catalyst. As can be seen from Table 1, the extractive efficiency of most DESs is no more than 30% except for ChCl/2PEG (45.4%). It is evident that deep desulfurization cannot be obtained by mere extraction, and that it is necessary to introduce oxidation assisted by a catalyst and oxidant. After oxidation, the sulfur removal increased to 81.5% using neutral DES ChCl/2EG as an extractant, followed by ChCl/2PEG (68.9%), ChCl/2Gl (47.2%), and ChCl/2BG (44.6%). In comparison, acidic and basic DESs exhibited better desulfurization efficiency and 100% and 90.8% removal of DBT from model oil was obtained with ChCl/2Ac and ChCl/2U, respectively. As observed from the experimental phenomena, the catalyst [PSTEtA]3PW12O40 can dissolve in acidic and basic DESs but it can hardly dissolve in neutral DESs. Herein, it is concluded that the homogeneous system showed better performance than the heterogeneous system.
Table 1 Sulfur removal with different DESs as extractantsa
Entry |
DESs |
Sulfur removal/% |
EDSb |
ECODSc |
Experimental conditions: DES = 2 mL, model oil = 5 mL, T = 40 °C. t = 10 min. m(catalyst) = 0.025 g, O/S = 3, t = 2.5 h. |
1 |
ChCl/2EG |
21.6 |
81.5 |
2 |
ChCl/2BG |
25.1 |
44.6 |
3 |
ChCl/2Gl |
12.2 |
47.2 |
4 |
ChCl/2PEG |
45.4 |
68.9 |
5 |
ChCl/2Fo |
18.7 |
85.0 |
6 |
ChCl/2Ac |
19.8 |
100 |
7 |
BTAC/2Ac |
27.0 |
95.6 |
8 |
ChCl/2Pr |
28.1 |
98.1 |
9 |
ChCl/2U |
8.8 |
90.8 |
The solubility of DESs in model oil is seen as an important factor in selecting an extractant because of the potential for cross-contamination. In a previous work, it was confirmed that neutral and basic DESs, except for ChCl/2Gl and ChCl/2Pr, can dissolve in oil.48 Here, FT-IR spectra were used to determine the solubility of acidic DESs in oil. As shown in Fig. 3, the peak at about 1722 cm−1 is attributed to a stretching vibration of C
O in BTAC/2Ac and ChCl/2Pr, indicating that the two DESs can dissolve in n-octane and then might pollute the oil. Therefore, these two DESs cannot be used as extractants even though they have high desulfurization efficiency. There are no obvious new peaks in the IR spectra in n-octane after mixing with another three DESs, ChCl/2Fo, ChCl/2Ac and BTAC/2Ac, implying that they would not pollute the oil. Therefore, ChCl/2Ac was selected to optimize the reaction conditions as described in the following section.
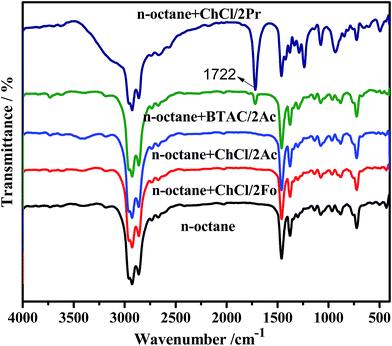 |
| Fig. 3 Mutual solubility between model oil and DESs through FT-IR spectra. | |
3.4. Effect of different conditions on sulfur removal
H2O2 and TBHP are commonly used oxidants, and are efficient in oxidation of sulfur compounds.49,50 As presented in Fig. 4, the desulfurization efficiency reached 100% when the molar ratio of H2O2 and sulfur (O/S) was 3
:
1 in 2.5 h; however, this reached only 35.8% using TBHP as oxidant under the same conditions. Thus H2O2 appears to be more effective in this system. The effect of the amount of H2O2 was investigated on oxidative desulfurization. Sulfur removal reached as high as 96.4% when the O/S molar ratio was 2
:
1. In an attempt to achieve sulfur-free oil, a little more H2O2 was added. Continuously increasing the amount of H2O2, the reaction time of complete oxidation could be shortened from 150 min to 120 min. Therefore, the optimal O/S molar ratio is 3
:
1.
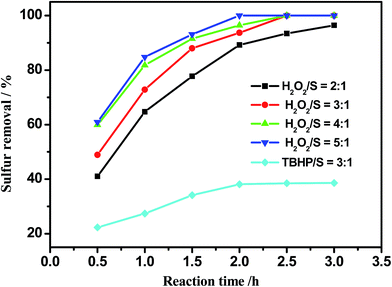 |
| Fig. 4 Effect of the oxidant on sulfur removal. Experimental conditions: m(catalyst) = 0.025 g, ChCl/2Ac = 2 mL, oil = 5 mL, T = 40 °C. | |
To determine the effect of H2O2 on reaction kinetics, the kinetic curves were fitted by plotting ln(C0/Ct) against reaction time. The pseudo-first-order kinetic model equation was given by ln(C0/Ct) = kt, where C0 and Ct were the initial sulfur concentration and the sulfur concentration at time t, respectively. As can be seen from Fig. 5, oxidation of DBT corresponds to a pseudo-first-order model in the entire given O/S molar ratio with R2 among 0.9989 to 0.9995. The rate constant k of the oxidation reaction increases with increasing amount of H2O2, while it does not affect the reaction order. Therefore, it can be concluded that the reaction of H2O2 in the oxidation of DBT obeyed pseudo-zero-order reaction.
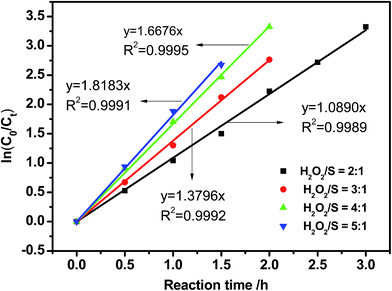 |
| Fig. 5 Pseudo-first-order kinetic model for oxidation of DBT with different amounts of H2O2. | |
Fig. 6 shows that the desulfurization efficiency was merely 9.6% at 3 h without DES as extractant. After addition of DES ChCl/2Ac as extractant, the sulfur removal increased sharply to 92.1% when the volume ratio of DES to oil was 1
:
5. Thus, to some extent, the more DES added may mean improved desulfurization performance. Generally, DESs obtained from cheap materials make themselves low-cost, that is, more DES can be added to this system to promote reaction activity without consideration of cost. However, the sulfur removal reached 95.2% at VDES/VOil = 2
:
5 and decreased gradually from 95.2% to 76% when the VDES/VOil was further increased to 5
:
5. A possible explanation could be that excess DES may dilute the concentration of catalyst and H2O2.
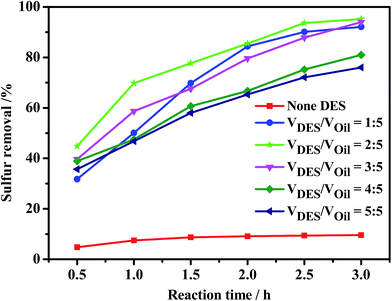 |
| Fig. 6 Effect of the amount of ChCl/2Ac on sulfur removal. Experimental conditions: m(catalyst) = 0.0184 g, O/S = 3, oil = 5 mL, T = 40 °C. | |
Reaction temperature has a vital effect on the conversion rate of DBT. As shown in Fig. 7, the sulfur removal was only 86.7% at 30 °C in 2.5 h, and then increased to 100% at 40 °C. However, the sulfur removal decreased to 92.8% when the reaction temperature increased to 50 °C. A possible reason for this is kinetic competition of the self-decomposition of H2O2. The linear fit of ln(C0/Ct) against reaction time demonstrates the pseudo-first-order kinetic characteristics for oxidation of DBT at 30 °C and 40 °C with correlation coefficients (R2) of 0.9963 and 0.9992, respectively (Fig. 8A). However, the R2 value is only 0.9466 when the reaction at 50 °C is hypothesized as a pseudo-first-order kinetic model. It also can be seen from Fig. 8B that the data point cannot match this kinetic model. Also, oxidation of DBT exhibits pseudo-second-order kinetics at the value of R2 = 0.9913. These results indicate that the reaction kinetics turn from pseudo-first-order to pseudo-second-order with increasing temperature. The apparent activation energy (Ea) can be calculated from the data at 30 °C and 40 °C by the Arrhenius formula ln
k = ln
A − Ea/RT, with an Ea value of 10.8 kJ mol−1.
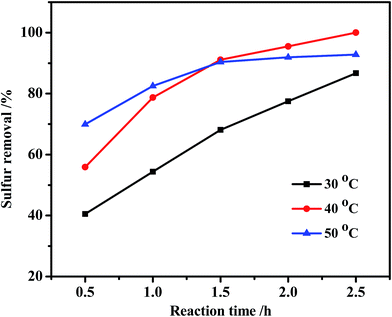 |
| Fig. 7 Effect of reaction temperature on sulfur removal. Experimental conditions: m(catalyst) = 0.025 g, O/S = 3, ChCl/2Ac = 2 mL, oil = 5 mL. | |
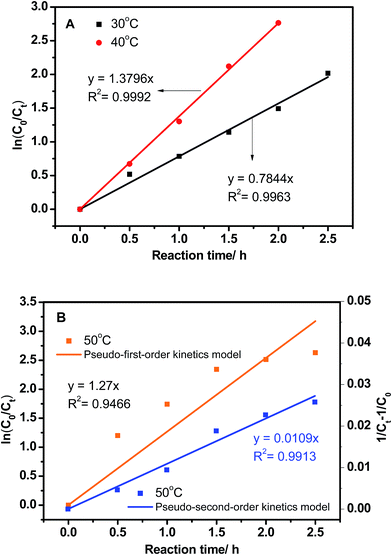 |
| Fig. 8 Kinetic model for oxidation of DBT at different reaction temperatures. (A) 30 °C and 40 °C; (B) 50 °C. | |
3.5. Oxidative desulfurization of different model oils
It is known that alkylated thiophenes are the refractory sulfur compounds in the HDS process. Here, another five kinds of sulfur compounds, BT, DBT, 3-MBT, 4-MDBT and 4,6-DMDBT, were evaluated on catalytic activity of the system. Fig. 9 shows that the mere extraction of all the sulfur compounds is lower than 20.6%. After addition of catalyst, a dramatic increase of sulfur removal was observed with the desulfurization efficiency following the order: DBT > 3-MBT > 4-MDBT > 4,6-DMDBT > BT. As reported by Otsuki and Li,51,52 the difference among different sulfur compounds is controlled by electron density, steric hindrance or Fukui function. The lowest removal of BT could be attributed to its lowest electron density. Compared with BT, 3-MBT displayed the second best performance, which might be because of its higher electron density than BT and no steric hindrance. The order for f+(r) Fukui function on S site is DBT > 4-MDBT > 4,6-DMDBT, which can explain the order of sulfur removal for the three sulfur compounds.
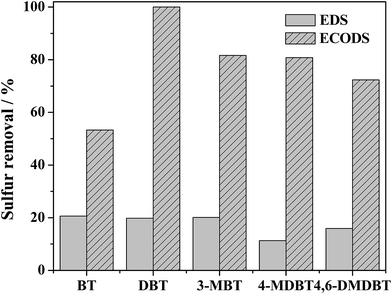 |
| Fig. 9 Catalytic oxidation of different sulfur compounds. Experimental conditions: m(catalyst) = 0.025 g, O/S = 3, ChCl/2Ac = 2 mL, oil = 5 mL, T = 40 °C, EDS time = 10 min, ECODS time = 2.5 h, EDS = extractive desulfurization, ECODS = extraction and oxidative desulfurization. | |
Actual oil contains a certain amount of aromatic hydrocarbons, olefins, and so on. Herein toluene, p-xylene and cyclohexene were chosen to model actual oil.53,54 As shown in Fig. 10, the sulfur removal decreased from 100% to 91.8%, 81.8% and 82.8% with 5%, 10% and 15% of toluene in model oil. With an additional 10% p-xylene, the sulfur removal decreased to 89.0%. However, the sulfur removal decreased sharply to 33.4% with 10% cyclohexene in model oil. The results suggest that the olefins in model fuel have a more negative impact than aromatics on oxidation of DBT. Therefore, full consideration should be given to study the effect of olefins in oxidative desulfurization in future industrial applications.
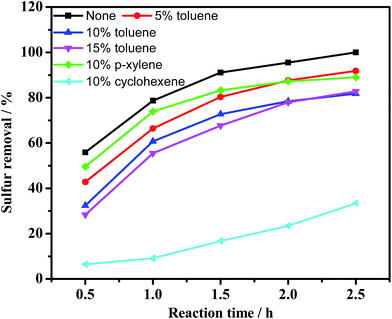 |
| Fig. 10 Effect of aromatics and olefins on sulfur removal. Experimental conditions: m(catalyst) = 0.025 g, O/S = 3, ChCl/2Ac = 2 mL, oil = 5 mL, T = 40 °C. | |
3.6. The proposed mechanism
Generally speaking, POM-based catalysts can form active peroxo species after reacting with H2O2, which can oxidize DBT to DBTO2.55,56 However, the catalytic activity can be affected by various factors, such as solvents, and cations of POMs catalysts. As shown in Fig. 2, acidic catalysts have higher desulfurization efficiency than neutral ones, which confirms the important role of the acidic group. Thus the sulfur atom of DBT might be protonated or form a hydrogen bond between S atom and SO3H group, which will make the sulfur compound more susceptible to oxidization.30 Three POM catalysts were obtained by changing the molar ratio (1
:
1, 2
:
1, 3
:
1) of [PSTEtA]Cl and H3PW12O40 to study the roles of acidity and cations. The Brønsted acidities of the three catalysts were determined by FT-IR using pyridine as a probe molecule. From Fig. 11, it can be seen that the three catalysts have the same peak at 1539 cm−1, indicating their almost equal acidity. However, the sulfur removal follows the order [PSTEtA]H2PW12O40 < [PSTEtA]2HPW12O40 < [PSTEtA]3PW12O40 (Fig. 12). As reported in the literature,46 the SO3H group can be oxidized into peroxysulfonic acid in the presence of H2O2. Therefore, it is suggested that the SO3H functionalized cation might have multi-ability and the active oxygen species may include peroxotungsten and peroxysulfonic acid.
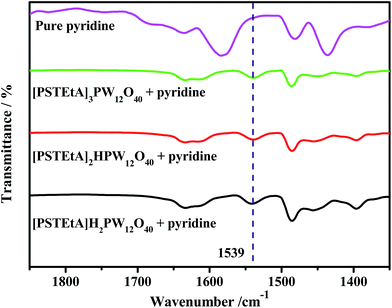 |
| Fig. 11 Determination of the Brønsted acidity by FT-IR. | |
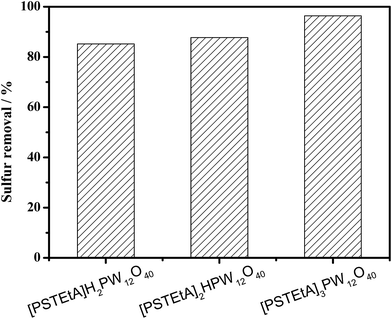 |
| Fig. 12 Sulfur removal with catalysts of different cations. Experimental conditions: n(catalyst)/n(DBT) = 1 : 11, ChCl/2Ac = 2 mL, O/S = 2, oil = 5 mL, T = 40 °C, t = 2.5 h. | |
In the absence of DESs, the catalysts showed low desulfurization efficiency (Fig. 6). According to previous work on ECODS, DBT should first be extracted in DES phase and then oxidized to DBTO2 (GC-MS analysis, m/z = 216) by the active oxygen species in DES, in which the acidic group plays an important role.
4. Conclusions
In summary, several POMs were synthesized as catalysts for oxidative desulfurization with DESs as extractants. Compared with the neutral catalysts, the SO3H-functional acidic catalysts exhibited better catalytic activities. The results showed that sulfur removal could reach 100% at 2.5 h with [PSTEtA]3PW12O40 as a catalyst and ChCl/2Ac as an extractant. Oxidation of DBT followed a pseudo-first-order kinetic model at reaction temperatures of 30 °C and 40 °C, then transferred to a pseudo-second-order kinetic model at 50 °C. The amount of H2O2 can increase the desulfurization efficiency but not affect the reaction order. Desulfurization efficiency with different sulfur compounds followed the order DBT > 3-MBT > 4-MDBT > 4,6-DMDBT > BT, which can be explained by electron density, steric hindrance or Fukui function. In addition, olefins have a greatly negative impact on oxidation of DBT and this should be taken into account in industrial applications.
Conflicts of interest
There are no conflicts to declare.
Acknowledgements
This work was financially supported by the National Natural Science Foundation of China (No. 21506080, 21576122, and 21646001), Natural Science Foundation of Jiangsu Province (No. BK20150485), Advanced Talents of Jiangsu University (No. 15JDG053), A Project Funded by the Priority Academic Program Development of Jiangsu Higher Education Institutions.
References
- H. Liu, Y. Li, C. Yin, Y. Wu, Y. Chai, D. Dong, X. Li and C. Liu, Appl. Catal., B, 2016, 198, 493–507 CrossRef CAS.
- Q. Gu, G. Wen, Y. Ding, K.-H. Wu, C. Chen and D. Su, Green Chem., 2017, 19, 1175–1181 RSC.
- B. Jiang, H. Yang, L. Zhang, R. Zhang, Y. Sun and Y. Huang, Chem. Eng. J., 2016, 283, 89–96 CrossRef CAS.
- G. Miao, D. Huang, X. Ren, X. Li, Z. Li and J. Xiao, Appl. Catal., B, 2016, 192, 72–79 CrossRef CAS.
- L. Xia, H. Zhang, Z. Wei, Y. Jiang, L. Zhang, J. Zhao, J. Zhang, L. Dong, E. Li, L. Ruhlmann and Q. Zhang, Chem.–Eur. J., 2017, 23, 1920–1929 CrossRef CAS PubMed.
- S. Mandizadeh, M. Salavati-Niasari and M. Sadri, Sep. Purif. Technol., 2017, 175, 399–405 CrossRef CAS.
- A. E. S. Choi, S. Roces, N. Dugos and M.-W. Wan, Fuel, 2016, 180, 127–136 CrossRef CAS.
- J. Dou and H. C. Zeng, ACS Catal., 2014, 4, 566–576 CrossRef CAS.
- P. W. Wu, W. S. Zhu, Y. H. Chao, J. S. Zhang, P. F. Zhang, H. Y. Zhu, C. F. Li, Z. G. Chen, H. M. Li and S. Dai, Chem. Commun., 2016, 52, 144–147 RSC.
- Y. Li, X. Zhang, D. Zhang, Y. Li, X. Wang and S. Wang, RSC Adv., 2017, 7, 43681–43688 RSC.
- J.-j. Li, H. Zhang, X.-d. Tang and H. Lu, RSC Adv., 2016, 6, 100352–100360 RSC.
- C. P. Li, J. J. Zhang, Z. Li, J. M. Yin, Y. N. Cui, Y. Liu and G. Yang, Green Chem., 2016, 18, 3789–3795 RSC.
- F. S. Mjalli, O. U. Ahmed, T. Al-Wahaibi, Y. Al-Wahaibi and I. M. AlNashef, Rev. Chem. Eng., 2014, 30, 337–378 CAS.
- S.-x. Lu, H. Zhong, D.-m. Mo, Z. Hu, H.-l. Zhou and Y. Yao, Green Chem., 2017, 19, 1371–1377 RSC.
- A. S. Amarasekara, Chem. Rev., 2016, 116, 6133–6183 CrossRef CAS PubMed.
- W. Jiang, W. S. Zhu, Y. H. Chang, Y. H. Chao, S. Yin, H. Liu, F. X. Zhu and H. M. Li, Chem. Eng. J., 2014, 250, 48–54 CrossRef CAS.
- S. J. Zhang, J. Sun, X. C. Zhang, J. Y. Xin, Q. Q. Miao and J. J. Wang, Chem. Soc. Rev., 2014, 43, 7838–7869 RSC.
- X. Y. Luo, F. Ding, W. J. Lin, Y. Q. Qi, H. R. Li and C. M. Wang, J. Phys. Chem. Lett., 2014, 5, 381–386 CrossRef CAS PubMed.
- W. Jiang, W. S. Zhu, H. P. Li, X. Wang, S. Yin, Y. H. Chang and H. M. Li, Fuel, 2015, 140, 590–596 CrossRef CAS.
- H. Zhao, G. A. Baker and Q. Zhang, Fuel, 2017, 189, 334–339 CrossRef CAS.
- H. Yang, B. Jiang, Y. Sun, L. Hao, Z. Huang and L. Zhang, Chem. Eng. J., 2016, 306, 131–138 CrossRef CAS.
- F.-t. Li, B. Wu, R.-h. Liu, X.-j. Wang, L.-j. Chen and D.-s. Zhao, Chem. Eng. J., 2015, 274, 192–199 CrossRef CAS.
- A. Alizadeh, M. Fakhari, M. M. Khodeai, G. Abdi and J. Amirian, RSC Adv., 2017, 7, 34972–34983 RSC.
- Q. Zhang, K. D. O. Vigier, S. Royer and F. Jerome, Chem. Soc. Rev., 2012, 41, 7108–7146 RSC.
- A. Paiva, R. Craveiro, I. Aroso, M. Martins, R. L. Reis and A. R. C. Duarte, ACS Sustainable Chem. Eng., 2014, 2, 1063–1071 CrossRef CAS.
- C.-f. Mao, R.-x. Zhao and X.-p. Li, RSC Adv., 2017, 7, 42590–42596 RSC.
- A. P. Abbott, D. Boothby, G. Capper, D. L. Davies and R. K. Rasheed, J. Am. Chem. Soc., 2004, 126, 9142–9147 CrossRef CAS PubMed.
- H. Lü, P. Li, C. Deng, W. Ren, S. Wang, P. Liu and H. Zhang, Chem. Commun., 2015, 51, 10703–10706 RSC.
- W. Jiang, H. P. Li, C. Wang, W. Liu, T. Guo, H. Liu, W. S. Zhu and H. M. Li, Energy Fuels, 2016, 30, 8164–8170 CrossRef CAS.
- C. Li, D. Li, S. Zou, Z. Li, J. Yin, A. Wang, Y. Cui, Z. Yao and Q. Zhao, Green Chem., 2013, 15, 2793–2799 RSC.
- X. D. Tang, Y. F. Zhang, J. J. Li, Y. Q. Zhu, D. Y. Qing and Y. X. Deng, Ind. Eng. Chem. Res., 2015, 54, 4625–4632 CrossRef CAS.
- H. F. M. Zaid, C. F. Kait and M. I. A. Mutalib, Fuel, 2017, 192, 10–17 CrossRef.
- W. S. Zhu, C. Wang, H. P. Li, P. W. Wu, S. H. Xun, W. Jiang, Z. G. Chen, Z. Zhao and H. M. Li, Green Chem., 2015, 17, 2464–2472 RSC.
- J. Yin, J. Wang, Z. Li, D. Li, G. Yang, Y. Cui, A. Wang and C. Li, Green Chem., 2015, 17, 4552–4559 RSC.
- S. H. Xun, W. S. Zhu, Y. H. Chang, H. P. Li, M. Zhang, W. Jiang, D. Zheng, Y. J. Qin and H. M. Li, Chem. Eng. J., 2016, 288, 608–617 CrossRef CAS.
- S. H. Xun, W. S. Zhu, D. Zheng, L. Zhang, H. Liu, S. Yin, M. Zhang and H. M. Li, Fuel, 2014, 136, 358–365 CrossRef CAS.
- Z. Yao, H. N. Miras and Y.-F. Song, Inorg. Chem. Front., 2016, 3, 1007–1013 RSC.
- S.-W. Li, R.-M. Gao, R.-L. Zhang and J.-s. Zhao, Fuel, 2016, 184, 18–27 CrossRef CAS.
- A. Nisar, Y. Lu, J. Zhuang and X. Wang, Angew. Chem., Int. Ed., 2011, 50, 3187–3192 CrossRef CAS PubMed.
- W. Ma, Y. Xu, K. Ma and H. Zhang, Appl. Catal., A, 2016, 526, 147–154 CrossRef CAS.
- Y. Zhang, H. Lue, L. Wang, Y. Zhang, P. Liu, H. Han, Z. Jiang and C. Li, J. Mol. Catal. A: Chem., 2010, 332, 59–64 CrossRef CAS.
- W. L. Huang, W. S. Zhu, H. M. Li, H. Shi, G. P. Zhu, H. Liu and G. Y. Chen, Ind. Eng. Chem. Res., 2010, 49, 8998–9003 CrossRef CAS.
- W. Jiang, D. Zheng, S. H. Xun, Y. J. Qin, Q. Q. Lu, W. S. Zhu and H. M. Li, Fuel, 2017, 190, 1–9 CrossRef CAS.
- E. Rafiee, F. Mirnezami and M. Kahrizi, J. Mol. Struct., 2016, 1119, 332–339 CrossRef CAS.
- H. Y. Lü, C. L. Deng, W. Z. Ren and X. Yang, Fuel Process. Technol., 2014, 119, 87–91 CrossRef.
- Y. Usui, K. Sato and M. Tanaka, Angew. Chem., Int. Ed., 2003, 42, 5623–5625 CrossRef CAS PubMed.
- B. Y. Zhang, Z. X. Jiang, J. Li, Y. N. Zhang, F. Lin, Y. Liu and C. Li, J. Catal., 2012, 287, 5–12 CrossRef CAS.
- W. Liu, W. Jiang, W. Q. Zhu, W. S. Zhu, H. P. Li, T. Guo, W. H. Zhu and H. M. Li, J. Mol. Catal. A: Chem., 2016, 424, 261–268 CrossRef CAS.
- X. Xiao, H. Zhong, C. Zheng, M. Lu, X. Zuo and J. Nan, Chem. Eng. J., 2016, 304, 908–916 CrossRef CAS.
- A. Bazyari, A. A. Khodadadi, A. H. Mamaghani, J. Beheshtian, L. T. Thompson and Y. Mortazavi, Appl. Catal., B, 2016, 180, 65–77 CrossRef CAS.
- S. Otsuki, T. Nonaka, N. Takashima, W. H. Qian, A. Ishihara, T. Imai and T. Kabe, Energy Fuels, 2000, 14, 1232–1239 CrossRef CAS.
- H. P. Li, W. S. Zhu, S. W. Zhu, J. X. Xia, Y. H. Chang, W. Jiang, M. Zhang, Y. W. Zhou and H. M. Li, AIChE J., 2016, 62, 2087–2100 CrossRef CAS.
- K.-S. Cho and Y.-K. Lee, Appl. Catal., B, 2014, 147, 35–42 CrossRef CAS.
- J. Xiao, L. Wu, Y. Wu, B. Liu, L. Dai, Z. Li, Q. Xia and H. Xi, Appl. Energy, 2014, 113, 78–85 CrossRef CAS.
- H. Lu, P. Li, Y. Liu, L. Hao, W. Ren, W. Zhu, C. Deng and F. Yang, Chem. Eng. J., 2017, 313, 1004–1009 CrossRef CAS.
- W. S. Zhu, W. L. Huang, H. M. Li, M. Zhang, W. Jiang, G. Y. Chen and C. R. Han, Fuel Process. Technol., 2011, 92, 1842–1848 CrossRef CAS.
|
This journal is © The Royal Society of Chemistry 2017 |
Click here to see how this site uses Cookies. View our privacy policy here.