DOI:
10.1039/C7RA09427B
(Paper)
RSC Adv., 2017,
7, 49010-49014
Ni3+ doped cobalt–nickel layered double hydroxides as high-performance electrode materials for supercapacitors†
Received
25th August 2017
, Accepted 12th October 2017
First published on 18th October 2017
Abstract
Co–Ni layered double hydroxides (LDHs), as promising supercapacitor electrode materials with high specific capacity, have suffered from poor rate properties and cycling stability. Doping and topochemical oxidation of Ni ions is considered as an efficient route to overcome these drawbacks. In this work, Ni3+ doped cobalt–nickel layered double hydroxides (Co–Ni-LDHs) were synthesized by pulse laser ablation of a Ni target in CoCl2 aqueous solution. The existence of Ni3+ ions doped in Co–Ni-LDHs decreases the conductive resistance, and increases the mobility of surface charge and transfer rate of the electrolyte. As a result, the Ni3+ doped Co–Ni-LDHs display a maximum specific capacitance of 2275 F g−1 and 1450 F g−1 at the current density of 1 A g−1 and 20 A g−1, respectively, indicating a high rate of specific capacitance. Moreover, the capacitance retention is 80% after 1800 cycles at the current density of 6 A g−1, manifesting good cycling stability of Ni3+ doped Co–Ni-LDHs.
Introduction
Transition metal-based layered double hydroxide materials (LDHs) are considered as one of the most promising materials for pseudocapacitors, owing to the low cost, environmental friendliness and high theoretical capacitance.1–4 Compared to monometallic hydroxide, LDHs present two kinds of metal inserted in the host layer, which could provide richer redox reactions and offer an effective way of achieving improved electrochemical performance.5,6 However, the poor rate capacitance and cycle stability due to the severe large volume expansion and the poor conductivity limit the practical applications of LDH structures for supercapacitor materials. To overcome these disadvantages, substantial efforts are focused on the efficient incorporation of highly conductive materials such as graphene, CNT, conductive polymers into the LDHs composites to improve the conductivity.7,8 For example, Huang et al.9 fabricated CoNiAl-LDH nanosheets attached on sandwich-like reduced graphene oxide (RGO) with 1866 F g−1 at the current density of 1 A g−1 while maintaining 1360 F g−1 at the current density of 10 A g−1. Another strategy is to design hierarchical or porous structure with high surface area grown on the current collector (nickel foam,10 conductive textile substrate11) to buffer the volume expansion.12,13 But the low material loading masses are not suitable for the application.
Recently, engineering M3+ in LDHs phase has emerged as an effective approach to solving this problem. The M3+ (M = Ni, Co) species of LDHs play a key role in the efficiency of the active metal sites as well as controlling electron-transfer rate.14–17 Wang18 etched Al in Ni–Co–Al LDH by NaOH to enable the partial conversion of Co2+ to Co3+ with enhanced conductivity. Compared to Ni–Co–Al LDH, Ni–Co–Al LDHs after NaOH treatment display the lower resistance which lead to faster electrode kinetics. Moreover, theoretical studies19 has demonstrated the spin-up states of Ni3+ in monolayer NiTi-LDH (0.9 nm) can improve density of states values around the Fermi level, demonstrating a half-metallic characteristic to improve carrier mobility and electrical conductivity. Therefore, M3+ in LDHs are desirable to improve electrochemical performance.20,21 Although good results were obtained by doping M3+, special chemical treatments to the precursor are generally needed to induce the transformation from M2+ to M3+. For example, Co3+ doped layered double hydroxides were synthesized through a topochemical oxidative reaction employing bromine (Br2),22 O2,17 NO3− ions9 as an oxidizing agent, or chemical etching of Al in Ni–Co–Al LDH by NaOH.10,20 Therefore, it still needs to explore a simple and green strategy method to synthesize M3+ doped layered double hydroxides materials.
Laser ablation in liquids (LAL) technique has been demonstrated a novel strategy to fabricate nanomaterials with the desired size, structures and components.23–25 Also, it's an effective route to achieving doping ions into hydroxides. For example, our group has fabricated Mn-doped Ni(OH)2 nanosheets,26 Co-doped Ni(OH)2 (ref. 27) by laser ablation of a Mn or Co target in NiCl2 aqueous solution. In this work, by laser ablation of a Ni target in CoCl2 aqueous solution, doping and topochemical oxidation of Ni3+ ions were simultaneously accomplished in one step. We successfully fabricated the Ni3+ doped cobalt–nickel layered double hydroxides (Co–Ni-LDHs). Moreover, as-synthesized Ni3+ doped Co–Ni-LDHs used as electrode materials for supercapacitors display high rate specific capacitance and excellent cycling stability.
Experimental
LAL assisted formation of Co–Ni-LDHs
As shown in Fig. S1,† firstly, a nickel target (99.99% in purity) is fixed in a vessel filled with 18 mL 0.01 M CoCl2 solution, and ablated for 30 min by a Nd:YAG laser with wavelength of 1064 nm, pulse duration of 10 ns and per pulse laser energy of 120 mJ. The obtained colloidal solution was aged for 15 h. The precipitate is the final products, subsequently washed with ethanol and deionized water alternately for three times for characterization and application in supercapacitors.
Structural characterization of Co–Ni-LDHs
Scanning electron microscopy (SEM) system (Sirion 200 FEG) was used to observe the morphology of the Co–Ni-LDHs nanostructures. Energy dispersive X-ray spectrometry (EDX) was used to determine the element content. A transmission electron microscopy (TEM) system (JEOL, JEM-2010) with a 200 kV acceleration voltage was used to obtain the structural information of the products and element distribution. X-ray diffraction (XRD) analysis of the collected powder products was performed by using a Philips X'Pert system with Cu-Kα radiated (λ = 1.5419 Å). The surface chemical states were analysed by X-ray photoelectron spectroscopy (XPS; Thermo ESCACLB 250). The surface area and porosity of the samples were measured using an Omnisorp 100CX Analyzer (Beckman Coulter, Inc., USA).
Supercapacitors performance of Co–Ni-LDHs
The as-prepared samples were used as electro-active materials for supercapacitors. The electrochemical performances of electrodes were evaluated on a Zahner electrochemical workstation (Germany) at room temperature and measured in 3 M KOH electrolyte. The working electrode was prepared by dispersing the samples into N-methyl pyrrolidone and mixed with polyvinylidene fluoride and acetylene black in a mass ratio of 8
:
1
:
1 and then painted on Ni foam. The mass loading of the powders on the nickel foam (1 cm × 1 cm) was determined by subtracting the weight before deposition from that after deposition and calculated to be around 3 mg cm−2. The test system is a standard three-electrode configuration, including an Ag/AgCl electrode as a reference electrode and a platinum foil as the counter electrode. The specific capacitance of the electrode could be calculated according to eqn (1). Where C is the specific capacitance (F g−1), I is the current density (A), t is the discharge time (s), ΔV is the potential window (V), and m is the mass of the active materials (g), respectively. |
 | (1) |
Results and discussion
Fig. 1a presents the XRD pattern of as-synthesized Co–Ni-LDHs. The two prominent low-angle diffraction peaks located at 11.21° and 22.69° are assigned to (003) and (006) lattice planes of the hydrotalcite-like LDHs phase, which are similar to the standard XRD peaks for α-Co(OH)2 phase (JCPDS no. 42-1467).28 In addition, the (00h) reflections present sharp, symmetric and high diffraction intensity, suggesting that the synthesized structure is well crystallized with a regular interlayer and the preferential orientation growth along 〈00h〉 zone axis. Corresponding SEM and TEM image of Co–Ni-LDHs (Fig. 1c and d) show typical morphology of aggregated nanosheets that interconnect with each other to form a porous structure. Calculated by the Barrett–Joyner–Halenda (BJH) model (Fig. 1b), the specific surface area and pore diameter is of 201.9 m2 g−1 and 11.3 nm, respectively, which is much larger than that of Ni(OH)2 nanosheets (114 m2 g−1)29 and floss-like Ni–Co binary hydroxides (106.5 m2 g−1).30 Such large specific surface area and nanosheets-based porous structures allow high access of electrolyte to the integrated nanosheets, which is crucial for the reduction of the interface contact resistance between the electrodes and electrolyte.31 TEM image of several separated nanosheets (Fig. 1e) reveals a hexagonal shape of Co–Ni-LDHs, and the corresponding SAED pattern (inset in Fig. 1e) presents perfect hexagonal diffraction spots well matched with d-spacing of (110) lattice plane, indexed as the two-dimensional in-plane reflections. EDS spectrum (Fig. S2 in ESI†) of products demonstrates that the element ratio of Co and Ni is to be 0.55
:
0.45, thus it can be marked as Co0.55Ni0.45-LDHs. Also, the EDS elemental mapping images (Fig. 1f and g) verify that all elements (Co, Ni, and O) are uniformly distributed in Co0.55Ni0.45-LDHs.
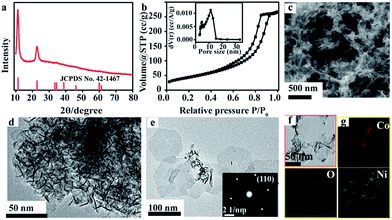 |
| Fig. 1 (a) XRD pattern of Co–Ni-LDHs, (b) N2 adsorption desorption isotherms and pore-size-distribution curves of Co–Ni-LDHs, (c) SEM image of Co–Ni-LDHs, (d) TEM image of Co–Ni-LDHs, (e) TEM image and the corresponding SAED pattern of individual Co–Ni-LDHs nanosheets, (f and g) EDX elemental mapping images of Co–Ni-LDHs. | |
XPS spectra are used to analyse the valence states of Co0.55Ni0.45-LDHs. The C 1s peak at 284.8 eV is calibrated the binding energies of other elements. The survey XPS spectra of Co0.55Ni0.45-LDHs (Fig. S3a†) present sharp photoelectron peaks of Co, Ni, O and C elements. Fig. S3b† shows the fine XPS spectrum of O 1s, the peak located at 531.1 eV is related to hydroxyl ions.35 In the Co 2p region (Fig. 2a), one pair of binding energies located at 782.5 eV and 798.5 eV coincide with Co2+.32,33 While in the Ni 2p region (Fig. 2b), two typical Ni3+ 2p3/2 and Ni2+ 2p3/2 peaks located at 856.3 eV and 855.9 eV are co-existed in the Co0.55Ni0.45-LDHs.33 It means that Ni3+ ions are doped in Co0.55Ni0.45-LDHs, which is ascribed to the unique LAL reaction process described as follows. As pulse laser irradiating on the interface between Ni target and liquid, a plasma plume including atoms, ions, radicals and Ni3+, Ni2+ with high temperature and high pressure is produced. Subsequent ultrasonic and adiabatic expansion of the hot plasma lead to a quick cooling of the plume region to form Ni clusters. The as-formed Ni clusters interacted with the surrounding aqueous solution, this processes involved in the generation of hydroxyl ions and the formation of the nuclei of Ni3+ doped Co0.55Ni0.45-LDHs which finally grow into network nanosheets.34,35
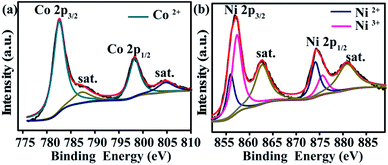 |
| Fig. 2 XPS spectra of Co0.55Ni0.45-LDHs (a) Co 2p, (b) Ni 2p. | |
Co0.55Ni0.45-LDHs are used as electrode materials for supercapacitors, electrochemical performance are investigated by cyclic voltammetry (CV), galvanostatic charge–discharge measurements. CV curves of Co0.55Ni0.45-LDHs (Fig. 3a) at the first test cycle present obvious redox peaks, revealing pseudocapacitive characteristics, which differ from the nearly rectangular CV shapes for conventional EDLCs.36 The reactions involved could be interpreted as follows:37
Ni(OH)2 + OH− ↔ NiOOH + H2O + e− |
Co(OH)2 + OH− ↔ CoOOH + H2O + e− |
CoOOH + OH− ↔ CoO2 + H2O + e− |
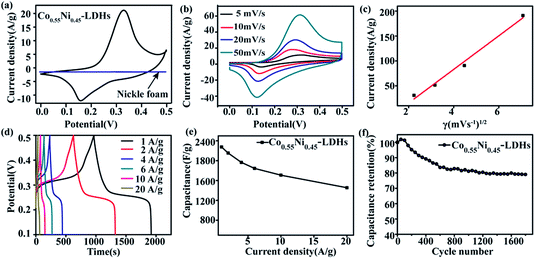 |
| Fig. 3 (a) CV curves of Co0.55Ni0.45-LDHs at scan rate of 5 mV s−1, (b) CV curve of Co0.55Ni0.45-LDHs at various scan rates, (c) the linear relationship of Co0.55Ni0.45-LDHs between the oxidation peak currents and the square root of scan rates, (d) galvanostatic charge–discharge curves of Co0.55Ni0.45-LDHs at 1, 2, 4, 6, 10, and 20 A g−1, (e) the specific capacitance of the Co0.55Ni0.45-LDHs at 1, 2, 4, 6, 10, and 20 A g−1, (f) cycling performance at a scan rate of 6 A g−1 of Co0.55Ni0.45-LDHs. | |
In addition, CV curves within the potential window of 0.0–0.5 V (vs. Ag/AgCl) at various scan rates from 5 to 50 mV s−1 is evaluated and shown in Fig. 3b. With the rising of scan rate, the currents increase and the potentials of redox peaks shift to a more negative or positive position. This phenomenon is mainly due to the fact that the increasing of scan rate would cause the rising in the internal diffusion resistance within the pseudoactive materials.38,39 Here, the good linear relationship between the oxidation peak currents and the square root of scan rates (Fig. 3c) confirms that the electrode reaction of Co0.55Ni0.45-LDHs is diffusion controlled.40 Furthermore, even at the high scan rate of 50 mV s−1, the shape of CV curve does not significantly distort, implying the nature of fast electron transport.
To further evaluate the rate capacity and cycling stability of the prepared Co0.55Ni0.45-LDHs, galvanostatic charge–discharge (GCD) measurements were conducted. Fig. 3d shows the GCD of the Co0.55Ni0.45-LDHs at different current densities from 1 A g−1 to 20 A g−1 in a voltage range of 0.1–0.5 V. The well-defined charge and discharge plateaus in all curves demonstrate the existence of redox reaction, confirming the previous CV results. The specific capacitance of the Co0.55Ni0.45-LDHs (Fig. 3e) composite is calculated to be 2275, 2153, 1965, 1845, 1708 and 1450 F g−1 at the current discharge of 1, 2, 4, 6, 10, and 20 A g−1 according to eqn (1). The specific capacitance retention of Co0.55Ni0.45-LDHs at different current densities is displayed in Fig. S4.† The high capacity retention of 64% is achieved for Co0.55Ni0.45-LDHs when the current density is increased from 1 A g−1 to 20 A g−1, displaying high rate capability. Fig. 3f displays the cyclic performance of the obtained Co0.55Ni0.45-LDHs composite at a current density of 6 A g−1. It can be seen that the specific capacitance shows a gradual decrease at first, and it is nearly constant after 800 cycles. After 1800 cycles, there is still 80% capacitance retention for Co0.55Ni0.45-LDHs electrode, indicating a good cycling stability.
In comparison with the previously reported results (Table 1), including RGO@CoNiAl-LDH,9 floss-like Ni–Co binary hydroxides30 and α phase Ni–Co bimetallic hydroxides,36 here synthesized Co0.55Ni0.45-LDHs exhibit better specific capacitance. The achieved high specific capacitance, excellent rate capability and the long cycle life may be understood as following issues: (a) the Ni3+ promote electron transportation to reduce the conductivity of Co0.55Ni0.45-LDHs,19 (b) the high specific surface area and porous structure of Co0.55Ni0.45-LDHs could shorten the diffusion distance between the electrolyte and electrodes, which can promote deep ions diffusion in electrochemical reaction,32,41 (c) the uniform distribution of Ni is a key factor to ensure the electron transfer, which can effectively optimize the electrical conductivity and durability of the electrode materials.21
Table 1 Comparison of various relative results of Co–Ni-LDHs
Material |
Mass loading (mg) |
Voltage range (V) |
Specific capacitance (F g−1) |
Current density (A g−1) |
Ref. |
Co0.55Ni0.45-LDHs |
3 |
0.1–0.5 |
1708 |
10 |
This work |
3 |
0.1–0.5 |
1450 |
20 |
This work |
Ni3+ doped NiTi-LDHs |
2 |
0–0.45 |
1500 |
20 |
19 |
RGO@CoNiAl-LDHs |
2 |
0–0.45 |
1360 |
10 |
8 |
α phase Ni–Co hydroxides |
2–3 |
0–0.55 |
1350 |
20 |
33 |
Floss-like Ni–Co hydroxides |
3 |
0–0.5 |
594 |
10 |
27 |
Ni(OH)2 hexagonal platelets |
3 |
0.6–0 |
628 |
10 |
39 |
CoNiAl-LDHs/GO |
5 |
0.35 to −0.1 |
618 |
20 |
8 |
Conclusions
In summary, Ni3+ doped Co0.55Ni0.45-LDHs were prepared by liquid-phase laser ablation method. Detailed characterization reveals Ni3+ doped Co0.55Ni0.45-LDHs hexagonal sheet-like shape, high specific surface area, porous structures and uniform distribution of Co, Ni elements. As electrode materials for supercapacitors, Co0.55Ni0.45-LDHs yields a maximum specific capacitance of 2275 F g−1 at 1 A g−1, and 1450 F g−1 at the high current density of 20 A g−1, which indicates high rate capacity. Furthermore, Co0.55Ni0.45-LDHs present 80% capacitance retention after 1800 cycles at 6 A g−1, meaning long cycle life for energy storage applications. Overall, this work provided a novel and efficient strategy in engineering M3+ in LDHs phase and confirmed that is an effective approach for improving their supercapacitor performance for practical energy storage devices.
Conflicts of interest
There are no conflicts to declare.
Acknowledgements
This work was financially supported by the National Basic Research Program of China (2014CB931704), the National Natural Science Foundation of China (NSFC, No. 51371166, 11304315, 51571186, 11504375) and the CAS/SAFEA (International Partnership Program for Creative Research Teams).
References
- Y. Zhao, J. Liu, Y. Hu, H. Cheng, C. Hu, C. Jiang, L. Jiang, A. Cao and L. Qu, Adv. Mater., 2013, 25, 591 CrossRef CAS PubMed.
- J. Pu, Y. Tong, S. B. Wang, E. H. Sheng and Z. H. Wang, J. Power Sources, 2014, 250, 250 CrossRef CAS.
- Z. Chen, Y. Qin, D. Weng, Q. Xiao, Y. Peng, X. Wang, H. Li, F. Wei and Y. Lu, Adv. Funct. Mater., 2009, 19, 3420 CrossRef CAS.
- R. Birjega, A. Matei, M. Filipescu, F. Stokker-Cheregi, C. Luculescu, D. Colceag, R. Zavoianu, O. D. Pavel and M. Dinescu, Appl. Surf. Sci., 2013, 278, 122 CrossRef CAS.
- R. R. Salunkhe, B. P. Bastakoti, C. T. Hsu, N. Suzuki, J. H. Kim, S. X. Dou, C. C. Hu and Y. Yamauchi, Chem.–Eur. J., 2014, 20, 3084 CrossRef CAS PubMed.
- W. L. Ma, L. Wang, J. Y. Xue and H. T. Cui, J. Alloys Compd., 2016, 662, 315 CrossRef CAS.
- L. Wang, D. Wang, X. Y. Dong, Z. J. Zhang, X. F. Pei, X. J. Chen, B. Chen and J. Jin, Chem. Commun., 2011, 47, 3556 RSC.
- J. H. Fang, M. Li, Q. Q. Li, W. F. Zhang, Q. L. Shou, F. Liu, X. B. Zhang and J. P. Cheng, Electrochim. Acta, 2012, 85, 248 CrossRef CAS.
- P. P. Huang, C. Y. Cao, Y. B. Sun, S. L. Yang, F. Wei and W. G. Song, J. Mater. Chem. A, 2015, 3, 10858 CAS.
- N. Abushrenta, X. C. Wu, J. N. Wang, J. F. Liu and X. M. Sun, Sci. Rep., 2015, 5, 13082 CrossRef CAS PubMed.
- G. N. Nagaraju, G. S. R. Raju, Y. H. Ko and J. S. Yu, Nanoscale, 2016, 8, 812 RSC.
- Q. B. Zhang, H. X. Chen, J. X. Wang, D. G. Xu, X. H. Li, Y. Yang and K. Zhang, ChemSusChem, 2014, 7, 2325 CrossRef CAS PubMed.
- J. P. Cheng, J. H. Fang, M. Li, W. F. Zhang, F. Liu and X. B. Zhang, Electrochim. Acta, 2013, 114, 68 CrossRef CAS.
- F. Gu, X. Cheng, S. F. Wang, X. Wang and P. S. Lee, Small, 2015, 11, 2044 CrossRef CAS PubMed.
- P. Vialat, P. Rabu, C. Mousty and F. Leroux, J. Power Sources, 2015, 293, 1 CrossRef CAS.
- V. M. Iluc, A. J. M. Miller, J. S. Anderson, M. J. Monreal, M. P. Mehn and G. L. Hillhouse, J. Am. Chem. Soc., 2011, 13, 13055 CrossRef PubMed.
- P. Vialat, C. Mousty, C. Taviot-Gueho, G. Renaudin, H. Martinez, J. C. Dupin, E. Elkaim and F. Leroux, Adv. Funct. Mater., 2014, 24, 4831 CrossRef CAS.
- X. Wang, C. Y. Yan, A. Sumboja, J. Yan and P. S. Lee, Adv. Energy Mater., 2014, 4, 1301240 CrossRef.
- Y. F. Zhao, Q. Wang, T. Bian, H. J. Yu, H. Fan, C. Zhou, L. Z. Wu, C. H. Tung, D. O'Hare and T. Zhang, Nanoscale, 2015, 7, 7168 RSC.
- X. L. Wu, L. L. Jiang, C. L. Long, T. Wei and Z. J. Fan, Adv. Funct. Mater., 2015, 25, 1648 CrossRef CAS.
- H. Chen, L. F. Hu, M. Chen, Y. Yan and L. M. Wu, Adv. Funct. Mater., 2014, 24, 934 CrossRef CAS.
- J. B. Liang, R. Z. Ma, N. B. Iyi, Y. S. Ebina, K. Takada and T. Sasaki, Chem. Mater., 2010, 22, 371 CrossRef CAS.
- H. M. Zhang, J. Liu, Y. X. Ye, Z. F. Tian and C. H. Liang, Phys. Chem. Chem. Phys., 2013, 15, 5684 RSC.
- J. Liu, C. H. Liang, H. M. Zhang, Z. F. Tian and S. Y. Zhang, J. Phys. Chem. C, 2012, 116, 4986 CAS.
- J. Liu, C. H. Liang, G. P. Xu, Z. F. Tian, G. S. Shao and L. D. Zhang, Nano Energy, 2013, 2, 328 CrossRef CAS.
- Z. F. Tian, C. H. Liang, J. Liu, H. M. Zhang and L. D. Zhang, J. Mater. Chem., 2011, 21, 18242 RSC.
- D. W. Liang, S. L. Wu, J. Liu, Z. F. Tian and C. H. Liang, J. Mater. Chem. A, 2016, 4, 10609 CAS.
- Z. P. Liu, R. Z. Ma, M. Osada, K. Takada and T. Sasaki, J. Am. Chem. Soc., 2005, 127, 13869 CrossRef CAS PubMed.
- W. P. Sun, X. H. Rui, M. Ulaganathan, S. Madhavi and Q. Y. Yan, J. Power Sources, 2015, 295, 323 CrossRef CAS.
- Y. F. Tang, Y. Y. Liu, W. C. Guo, S. X. Yu and F. M. Gao, Ionics, 2015, 21, 1655 CrossRef CAS.
- J. C. Chen, C. T. Hsu and C. C. Hu, J. Power Sources, 2014, 253, 205 CrossRef CAS.
- W. Quan, Z. L. Tang, Y. Hong, S. T. Wang and Z. T. Zhang, Electrochim. Acta, 2015, 182, 445 CrossRef CAS.
- X. Q. Cai, X. P. Shen, L. B. Ma, Z. Y. Ji, C. Xu and A. H. Yuan, Chem. Eng. J., 2015, 268, 251 CrossRef CAS.
- X. Y. Liu, Y. Q. Gao and G. W. Yang, Nanoscale, 2016, 8, 4227 RSC.
- P. S. Liu, W. P. Cai and H. B. Zeng, J. Phys. Chem. C, 2008, 112, 3261 CAS.
- S. P. Simon and Y. Gogotsi, Nat. Mater., 2008, 7, 845 CrossRef PubMed.
- D. D. Xia, H. C. Chen, J. J. Jiang, L. Zhang, Y. D. Zhao, D. Q. Guo and J. W. Yu, Electrochim. Acta, 2015, 156, 108 CrossRef CAS.
- J. Li, M. Yang, J. Wei and Z. Zhou, Nanoscale, 2012, 4, 4498 RSC.
- L. J. Li, J. Xu, J. L. Lei, J. Zhang, F. McLarnon, Z. D. Wei, N. B. Li and F. S. Pan, J. Mater. Chem A, 2015, 3, 1953 CAS.
- Y. W. Li, J. H. Yao, C. J. Liu, W. M. Zhao, W. X. Deng and S. K. Zhong, Int. J. Hydrogen Energy, 2010, 35, 2539 CrossRef CAS.
- S. D. Min, C. J. Zhao, Z. M. Zhang, G. R. Chen, X. Z. Qian and Z. P. Guo, J. Mater. Chem., 2015, 3, 3641 RSC.
Footnote |
† Electronic supplementary information (ESI) available: Fig. S1 laser-assisted assembly for Co–Ni-LDHs structure, Fig. S2 EDX spectrum and the table of corresponding elements calculation of Co0.55Ni0.45-LDHs, Fig. S3 XPS spectra of Co0.55Ni0.45-LDHs (a) survey, (b) O 1s 2p, Fig. S4 the specific capacitance retention of Co0.55Ni0.45-LDHs. See DOI: 10.1039/c7ra09427b |
|
This journal is © The Royal Society of Chemistry 2017 |
Click here to see how this site uses Cookies. View our privacy policy here.