DOI:
10.1039/C7RA08937F
(Paper)
RSC Adv., 2017,
7, 51993-52000
Synthesis of core–shell structured magnetic mesoporous silica microspheres with accessible carboxyl functionalized surfaces and radially oriented large mesopores as adsorbents for the removal of heavy metal ions†
Received
12th August 2017
, Accepted 13th October 2017
First published on 8th November 2017
Abstract
In this work, we report the fabrication of novel multifunctional microspheres which are composed of ordered mesoporous silica shells with accessible carboxyl functionalized surfaces and radially oriented large mesopores, and nonporous silica-coated magnetite cores (Fe3O4), aiming to remove heavy metal ions from aqueous media. The well-designed multifunctional microspheres were thoroughly characterized with transmission electron microscopy, scanning electron microscopy, infrared spectroscopy, N2 adsorption–desorption, X-ray diffraction as well as magnetization measurements. The as-prepared microspheres possess unique properties including stably grafted and accessible carboxyl groups, highly open mesopores (11.03 nm), high magnetization (34.5 emu g−1), and large BET surface areas (165 m2 g−1), and as a result, the as-prepared microspheres exhibit an enhanced performance for the removal of Cd(II), Cu(II), and Pb(II) from wastewater, with a high adsorption capacity, a rapid adsorption rate, and an easy magnetically separable process.
1. Introduction
Rapid industrialization has generated heavy metal contamination and intensified the presence of heavy metals in water. Accumulated heavy metals do great harm to the environment and to human health even at quite low concentrations. Many methods have been applied for treating heavy metals in wastewater, such as chemical precipitation,1 solvent extraction,2 ion-exchange,3 adsorption4–6 and nanofiltration.7 Among these methods, adsorption has received more attention due to its high efficiency, simplicity, and low cost.8–10
Owing to its excellent features (such as high surface area, large pore volume, regular and tunable pore size, and chemical stability), mesoporous silica has been extensively employed as an adsorbent to remove different heavy metal ions.11,12 Up to now, although mesoporous silica adsorbents have been developed, their practical applications in treating wastewater are still limited by inconvenient recycling. Recently, significant efforts have been devoted to the application of core–shell structured magnetic mesoporous silica in the adsorption of heavy metals due to convenient magnetic separation and recycling processes. To get enhanced adsorption performance, a further step beyond the preparation of mesoporous silica is the construction of core–shell structured magnetic mesoporous silica by combining the advantages of mesoporosity with the magnetic properties, which could lead to excellent candidates for treating heavy metals in wastewater.13,14
On the other hand, functional groups such as amino or thiol groups can be immobilized on mesoporous silica by a grafting process to fine-tune the interactions with heavy metal ions, through which the adsorption performance can be elevated to the next level.15,16 However, the uncontrollable post-synthesis grafting process may give rise to pore plugging, which is disadvantageous to the adsorption capacity and kinetics. The construction of mesoporous silica integrating functionalized surfaces and accessible mesopores has long been one of the most attractive targets for various groups, aiming to make the surface active for the immobilization of heavy metal ions and to improve the efficiency of mesopore usage and rapid mass transfer.17,18
On the basis of comprehensive considerations, we prepared core–shell structured magnetic mesoporous silica microspheres with a carboxyl functionalized surface and radially oriented large mesopores, which combined the advantages of good magnetic separability, suitable surface properties and a mesoporous structure.19 The radially oriented large mesopores on the magnetic microspheres are sufficiently large avoiding the plugging caused by surface modification, so that the carboxyl groups immobilized inside the mesopores could maintain accessible formation. The obtained core–shell structured magnetic mesoporous silica microspheres showed fast adsorption speed, high capacity and good recycling stability for trapping Cd(II), Cu(II), and Pb(II) from wastewater.
2. Experimental
2.1 Chemicals
Cetyltrimethylammonium bromide (CTAB) and (3-aminopropyl)trimethoxysilane (APTMS) were purchased from Aladdin Industrial Corporation. Other chemicals were purchased from Beijing Chemical Corp. All chemicals were directly used as received without any further purification. Deionized water was used in all experiments.
2.2 Methods
2.2.1 Synthesis of the Fe3O4@SiO2@mSiO2 microspheres. The Fe3O4 and Fe3O4@SiO2 microspheres were prepared as previously described.20 Briefly, 0.6 g of CTAB and 0.2 g of triethanolamine (TEA) were dissolved in deionized water (60 mL) by vigorous mechanical stirring to obtain a clear dispersion. Afterwards, 0.15 g of the Fe3O4@SiO2 microspheres was added and treated ultrasonically for 30 min. Into the resulting dispersion, 0.2 mL of tetraethyl orthosilicate (TEOS) and 0.18 mL of cyclohexane were added consecutively. The mixture was ultrasonicated for 15 min and was then mechanically stirred at 60 °C for 12 h. The product was collected with the help of a magnetic field, followed by washing repeatedly with deionized water and ethanol. Finally, the product was dried at 60 °C overnight, then calcined at 550 °C for 6 h (here, it was named Fe3O4@SiO2@mSiO2).
2.2.2 Synthesis of the amino functionalized Fe3O4@SiO2@mSiO2 microspheres. In a typical procedure, 0.1 g of the Fe3O4@SiO2@mSiO2 microspheres was added into the mixed solution containing 50 mL of toluene and 4 mL of APTMS, then the mixture was refluxed at 110 °C with continuous stirring for 24 h. The product was washed with water and ethanol several times, and dried at 60 °C for 6 h (here, it was named Fe3O4@SiO2@mSiO2–NH2).
2.2.3 Synthesis of the carboxyl functionalized Fe3O4@SiO2@mSiO2 microspheres. 0.1 g of the Fe3O4@SiO2@mSiO2–NH2 microspheres was dispersed in a 30 mL glutaral solution (5 wt%) and ultrasonicated for 1 h. The recovered solid was washed with deionized water to remove the physically adsorbed species, and re-dispersed in 30 mL of a H2O2 solution (30 wt%) by mechanically stirring at 40 °C for 6 h. The product was magnetically separated, washed several times with deionized water, and dried at 60 °C for 6 h (here, it was named Fe3O4@SiO2@mSiO2–COOH).
2.3 Characterizations
Transmission electron microscopy (TEM) was performed on a JEM-2000. Scanning electron microscopy (SEM) was measured on a JSM-5600. Infrared spectroscopy was measured on a Perkin-Elmer series using the KBr pellet technique. The specific surface area was measured at 77 K using N2 adsorption–desorption isotherms and BJH methods on a Micromeritics ASAP 2020 HD88 analyzer (USA). X-ray diffraction (XRD) was carried out using a Bruker D8 Advance X-ray diffractometer with a Cu Kα X-ray source operating at 9 kV and 200 mA. Magnetization measurements of the samples were measured with a Quantum Design vibrating sample magnetometer (VSM) at room temperature in an applied magnetic field sweeping from −15 to 15 kOe. The concentrations of the heavy metal ions in the solutions were measured by atomic absorption spectroscopy.
2.4 Regeneration studies
For the potential practical application of the Fe3O4@SiO2@mSiO2–COOH microspheres, adsorbent reusability is desirable. In this work, the used Fe3O4@SiO2@mSiO2–COOH microspheres were transferred to 1 M HCl solution and shaken by ultrasonication for 1 h, then washed with deionized water several times in order to reuse them in the next cycle.
3. Results and discussion
3.1 Controlled fabrication of multifunctional core–shell structured magnetic mesoporous silica microspheres
The core–shell structured Fe3O4@SiO2@mSiO2–COOH microspheres can be constructed through a multistep approach (Scheme 1). First, the Fe3O4 microspheres are prepared via a solvothermal reaction based on the reduction of Fe(III) salts. The Fe3O4 microspheres have a nearly spherical shape with a mean diameter of about 350 nm (Fig. S1a–c, see ESI†). By using the Stöber method, a thin silica layer can coat the Fe3O4 microspheres to form the Fe3O4@SiO2 microspheres (Fig. S1d–f†). The SiO2 shell can effectively prevent the chemical degradation and aggregation of the Fe3O4 microspheres for application in harsh liquid environments. The Fe3O4@SiO2 microspheres still keep the spherical shape and exhibit a core–shell structure. It also can be clearly seen that the Fe3O4 cores are black spheres and that the SiO2 shell shows a gray color with an average thickness of about 30 nm. The Fe3O4@SiO2 microspheres are subsequently coated with a layer of mesoporous SiO2 through a surfactant templating approach involving the controlled hydrolysis of TEOS with CTAB as the surfactant, and then calcined in air to form the radially oriented large mesopores (Fig. S1g–i†). The Fe3O4@SiO2@mSiO2 microspheres are nearly monodispersed with a clearly distinguishable three-layer structure including an Fe3O4 core, a SiO2 interlayer, and a mesoporous SiO2 outerlayer with a ∼50 nm thickness. Finally, in order to introduce the carboxyl functional groups, the Fe3O4@SiO2@mSiO2 microspheres are first activated using APTMS, resulting in amino-functionalized Fe3O4@SiO2@mSiO2. Then glutaral is grafted on these amino groups and treated with H2O2 (for details, see Experimental section), through which the Fe3O4@SiO2@mSiO2–COOH microspheres are prepared (Fig. 1a). The Fe3O4@SiO2@mSiO2–COOH (Fig. 1b and c) microspheres with a mean diameter of about 510 nm still keep the morphological properties of the Fe3O4@SiO2@mSiO2 microspheres. It can be seen that the Fe3O4@SiO2@mSiO2–COOH microspheres are well dispersed without the occurrence of aggregation and the radially oriented large mesopores are well preserved after the multistep modification, indicating the uniform properties of the sample.
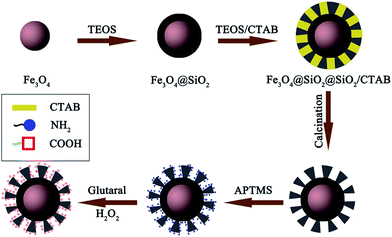 |
| Scheme 1 Schematic illustration of the formation process of the Fe3O4@SiO2@mSiO2–COOH microspheres. | |
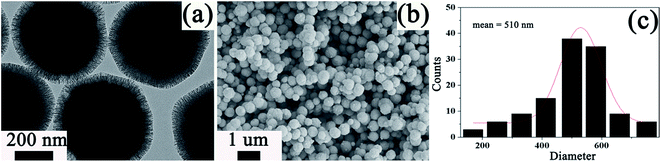 |
| Fig. 1 TEM and SEM of the Fe3O4@SiO2@mSiO2–COOH microspheres (a and b), and size distribution histogram of the Fe3O4@SiO2@mSiO2–COOH microspheres calculated from the SEM images (c). | |
FTIR spectroscopy was carried out throughout the whole surface modification process of the Fe3O4@SiO2@mSiO2, Fe3O4@SiO2@mSiO2–NH2 and Fe3O4@SiO2@mSiO2–COOH microspheres (Fig. 2). All microspheres exhibit absorption bands centered around 575 cm−1 (Fe–O vibration modes), 799 cm−1 (Si–O–Si symmetric stretching), 1081 cm−1 (Si–O–Si asymmetric stretching), 1635 cm−1 (the δO–H of adsorbed water and δN–H of free or protonated amino groups), and 3400 cm−1 (O–H and N–H stretching bands).16 Compared with the Fe3O4@SiO2@mSiO2 microspheres (Fig. 2a), the absorption peak of the Si–OH bands at 949 cm−1 in the Fe3O4@SiO2@mSiO2–NH2 microspheres (Fig. 2b) disappeared upon functionalization, indicating that aminosilane groups are grafted on surface silanols. Moreover, two new absorption bands at 1589 cm−1 (N–H asymmetric stretching) and 691 cm−1 (N–H symmetric stretching) can be observed, further indicating the introduction of amino groups. After the Fe3O4@SiO2@mSiO2–NH2 microspheres react with glutaral and hydrogen peroxide (Fig. 2c), the absorption bands at 1589 cm−1 (N–H asymmetric stretching) and 691 cm−1 (N–H symmetric stretching) are nearly invisible, indicating new species grafting on the amino groups. The new absorption at 1715 cm−1 assigned to the –COOH groups is clearly visible, which suggests that the carboxylic functional groups are successfully introduced upon multi-step surface functionalization. In addition, the new bands at 1560 cm−1 and 1401 cm−1 can be attributed to the symmetric COO− vibration and to the carboxyl-carbonate structures, respectively. By reaction with NaOH, when the pH is equal to 7, the determined COOH loading is ca. 0.05 mmol g−1 for the Fe3O4@SiO2@mSiO2–COOH microspheres.
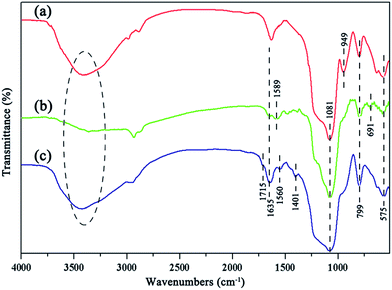 |
| Fig. 2 FTIR spectra of the Fe3O4@SiO2@mSiO2 (a), Fe3O4@SiO2@mSiO2–NH2 (b), and Fe3O4@SiO2@mSiO2–COOH (c) microspheres. | |
N2 adsorption–desorption measurements of the Fe3O4@SiO2@mSiO2 and Fe3O4@SiO2@mSiO2–COOH microspheres show type IV curves with H1 hysteresis loops (Fig. 3A), indicating well-uniform mesopores. In the pore size distribution curves, the samples exhibit a similar narrow pore size distribution in the range of 5–20 nm (Fig. 3B). The pore size, surface area and pore volumes slightly reduced after surface modification (Table 1), which can be attributed to the introduction of functional groups in the mesopores. According to previous studies, surface modification would lead to a remarkable perturbation of the pore size, surface area, and pore volume. However, no such phenomenon occurred in this work, suggesting that the surface modification method adopted in this work is suitable and the highly open mesopores can be preserved. The small angle XRD patterns of the Fe3O4@SiO2@mSiO2 and Fe3O4@SiO2@mSiO2–COOH microspheres show a strong diffraction peak between 2θ = 2° and 3°, indicating an ordered mesostructure (Fig. 3C). After surface modification, the mesoporous nature is intact, which is consistent with the TEM characterization. However, a gradual decrease in the intensities and a slight shift to higher angles for the peak can be observed, suggesting that the functional groups have been grafted inside the pores, which is similar to the previous case. The wide angle XRD pattern of the Fe3O4@SiO2@mSiO2–COOH microspheres exhibits almost the same feature as that of pure Fe3O4 except for a broad peak centered at 2θ = 22° (Fig. S2†), indicating that the coated SiO2 is amorphous.
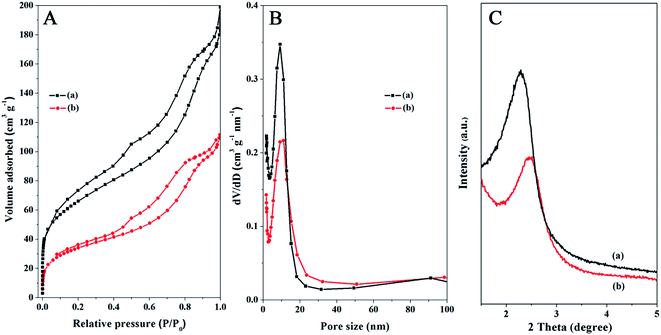 |
| Fig. 3 N2 adsorption–desorption isotherms (A), the pore size distributions (B), and the small-angle XRD patterns (C) of the Fe3O4@SiO2@mSiO2 (a) and Fe3O4@SiO2@mSiO2–COOH (b) microspheres. | |
Table 1 Textural properties of the Fe3O4@SiO2@mSiO2 and Fe3O4@SiO2@mSiO2–COOH microspheres
Sample |
Pore size (nm) |
BET surface area (m2 g−1) |
Pore volume (cm3 g−1) |
Fe3O4@SiO2@mSiO2 |
11.08 |
193 |
0.23 |
Fe3O4@SiO2@mSiO2–COOH |
11.03 |
165 |
0.17 |
The magnetic properties of the Fe3O4@SiO2@mSiO2 and Fe3O4@SiO2@mSiO2–COOH microspheres are characterized at room temperature as shown in Fig. 4. The saturation magnetizations of the Fe3O4@SiO2@mSiO2 and Fe3O4@SiO2@mSiO2–COOH microspheres are 37.6 and 34.5 emu g−1, respectively. Although the magnetization saturation value of the Fe3O4@SiO2@mSiO2–COOH microspheres is lower than that of the Fe3O4@SiO2@mSiO2 microspheres due to the grafting of the carboxyl group, the Fe3O4@SiO2@mSiO2–COOH microspheres still show strong magnetization. It can be seen that the Fe3O4@SiO2@mSiO2–COOH microspheres are quickly attracted to the side of the vial with the aid of an external magnetic field, and the microspheres can redisperse well again with shaking (Fig. 4, inset).
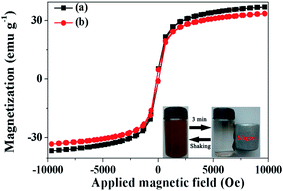 |
| Fig. 4 Magnetic curves of the Fe3O4@SiO2@mSiO2 (a) and the Fe3O4@SiO2@mSiO2–COOH (b) microspheres, where the inset shows the separation process of the Fe3O4@SiO2@mSiO2–COOH microspheres using a magnet. | |
3.2 Adsorption behavior of the Fe3O4@SiO2@mSiO2–COOH microspheres
Fig. 5a shows the adsorption isotherms of the heavy metal ions (Cd(II), Cu(II), and Pb(II)) onto the prepared adsorbent Fe3O4@SiO2@mSiO2–COOH microspheres at room temperature, which are expressed as plots of the solid-phase pollutant concentration vs. the liquid-phase pollutant concentration. It can be observed that the amount of heavy metal ions adsorbed gradually increases with the concentration of heavy metal ions. The maximum adsorption capacities for Cd(II), Cu(II), and Pb(II) are 395, 476, and 357 mg g−1, respectively. The adsorption of heavy metal ions on the Fe3O4@SiO2@mSiO2–COOH microspheres quickly reaches 88%, 77%, and 88% (349, 366 and 316 mg g−1) of the total capacity at low concentrations below 420 mg L−1 for Cd(II), Cu(II), and Pb(II), respectively. Fe3O4@SiO2@mSiO2–COOH microspheres exhibit a high adsorption capacity at low concentration, that may be derived from the complexation between the metal ions and the surface carboxyl groups.
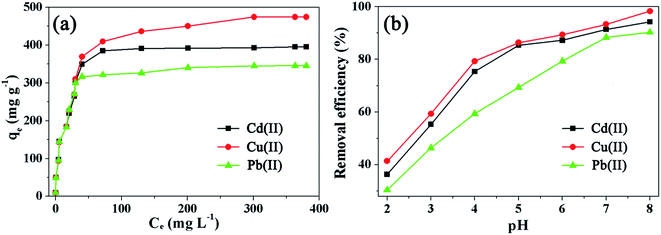 |
| Fig. 5 Adsorption isotherms (a) and the pH effect (b) of the Fe3O4@SiO2@mSiO2–COOH microspheres with different heavy metal ions. | |
The adsorption capacity of a given porous adsorbent strongly depends on the pore texture and surface properties. Fe3O4@SiO2@mSiO2–COOH microspheres combine the highly open large mesopores and the accessible carboxyl functionalized surfaces, which lead to a high adsorption capacity compared with that of other similar magnetic adsorbents (Table S1†). However, because of the substantial increase in mass caused by the large-sized Fe3O4, the Fe3O4@SiO2@mSiO2–COOH microspheres show a smaller BET surface area value, thus leading to a lower adsorption capacity compared with that of some mesoporous adsorbents.
The adsorption of heavy metal ions is significantly affected by the solution pH. As shown in Fig. 5b, when the pH increases from 2.0 to 8.0, the percentage of removed heavy metal ions (Cd(II), Cu(II), and Pb(II)) increases gradually. The adsorption capacity of the Fe3O4@SiO2@mSiO2–COOH microspheres is strong under near-neutral and alkaline conditions while it is poor under strong acidic conditions. Under near-neutral and alkaline conditions, the negatively charged carboxylate ions exhibit a much stronger coordinative affinity towards heavy metal ions, and they can capture the target metal ions by forming chelate complexes, which leads to the high removal efficiency of Cd(II), Cu(II), and Pb(II).
Three adsorption models named Langmuir, Freundlich and Temkin are employed to describe the adsorption, and are presented in eqn S(2)–S(4)†.21–24 The comparisons between the empirical adsorption isotherms and their fitting curves obtained from the above three models are shown in Fig. S3,† and the corresponding parameters obtained from nonlinear regression are shown in Table 2. Based on the value of the correlation coefficients (R2), it can be seen that the Langmuir isotherm is a more suitable isotherm for the experimental data, illustrating that the form of the heavy metal ions on the surface of the Fe3O4@SiO2@mSiO2–COOH microspheres is a monolayer adsorption and the major binding sites in the sorbent are homogeneously distributed. A high value of KL indicates higher affinity.
Table 2 Adsorption isotherm models and corresponding parameters for the removal of Cd(II), Cu(II), and Pb(II) on the Fe3O4@SiO2@mSiO2–COOH microspheres
Metal ions |
Langmuir isotherm |
Freundlich isotherm |
Temkin isotherm |
KL (L g−1) |
aL (L mmol−1) |
R2 |
KF (L g−1) |
nF |
R2 |
A |
B |
R2 |
Cd(II) |
412 |
0.059 |
0.96 |
110 |
0.219 |
0.89 |
46 |
12 |
0.91 |
Cu(II) |
513 |
0.039 |
0.96 |
100 |
0.278 |
0.93 |
38 |
9 |
0.63 |
Pb(II) |
359 |
0.102 |
0.96 |
116 |
0.202 |
0.83 |
40 |
8 |
0.69 |
The kinetics of Cd(II), Cu(II), and Pb(II) onto the Fe3O4@SiO2@mSiO2–COOH microspheres are presented in Fig. 6a. It can be seen that an adsorption equilibrium is attained only within ∼30 min. Notably, the adsorption of the heavy metal ions is very rapid in the first 20 min, then the adsorption rate reduces and the adsorption amount of the heavy metal ions is almost constant from 20–30 min and gradually increases with prolonged contact time. The initial rapid adsorption within the first 20 min can be ascribed to a slight resistance for the diffusion and adsorption of the heavy metal ions into the highly open and carboxyl functionalized mesopores. After that, heavy metal ions have to traverse farther and deeper into the available adsorption sites, thus slowing down the adsorption rate from 20–30 min. The intra-particle diffusion model describes the movement of species from the bulk of the solution to the solid phase. It can be defined as follows:
where
qt is the amount of the adsorbates at time
t (mg g
−1),
kid is the intra-particle diffusion equation constant (mg g
−1 min
−1/2),
c is the film thickness, and
t is the time (min). As seen in
Fig. 6b, the plots of
qt against
t1/2 first fit the linear behavior according to the intra-particle diffusion model, then a deviation occurs, indicating that the adsorption is at least a two-step process. The first step is controlled by the intra-particle diffusion and the second step can be ascribed to the pore diffusion.
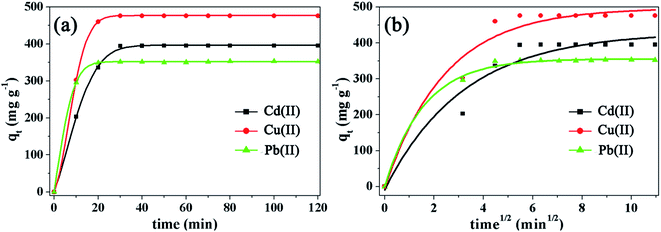 |
| Fig. 6 Adsorption rate (a) and intra-particle diffusion model (b) of the Fe3O4@SiO2@mSiO2–COOH microspheres with different heavy metal ions. | |
In order to further understand the mechanisms of adsorption and the heterogeneity of the adsorbent surface, the kinetic experimental data have been evaluated using a pseudo-first-order kinetic model and a pseudo-second-order kinetic model,25 respectively (Fig. S3†). Due to diffusion and adsorption being often experimentally inseparable, the heavy metal ion adsorption onto the Fe3O4@SiO2@mSiO2–COOH microspheres may be a complicated process that includes diffusion, coordinate bond formation and chemical reactions simultaneously. From the results obtained (Table 3), the value of R2 of the pseudo-second-order model is closer to 1 compared with that of the pseudo-first-order model, suggesting that the adsorption process can be accurately described by the pseudo-second-order model, thus the adsorption of heavy metal ions onto the Fe3O4@SiO2@mSiO2–COOH microspheres may take place based on a chemical process through the sharing or the exchange of electrons. Additionally, it is found that repeated washing of the used Fe3O4@SiO2@mSiO2–COOH microspheres with an acid solution and with deionized water can lead to its regeneration. Through repeated adsorption–desorption cycles as shown in Fig. 7, the adsorption efficiency decreased slightly in sequential cycles. And Fe3O4@SiO2@mSiO2–COOH still shows absorption bands at 1715 cm−1, 1560 cm−1 and 1401 cm−1 in the FTIR spectrum after multiple reuses (Fig. S4†), proving the existence of the carboxylic functional groups. However, the decrease in the absorption intensity indicates the leaching of adsorption sites, thus resulting in the adsorption efficiency decreasing in sequential cycles. After multiple reuses Fe3O4@SiO2@mSiO2–COOH still maintains a high adsorption capacity, and the pore size, BET surface area and pore volume structure of Fe3O4@SiO2@mSiO2–COOH only exhibit a slight decrease (Table S2†), suggesting the stability and reusability of the Fe3O4@SiO2@mSiO2–COOH microspheres, which is owing to their unique textural structure and surface properties.
Table 3 Kinetic adsorption parameters of heavy metal ions on the Fe3O4@SiO2@mSiO2–COOH microspheres obtained using a pseudo-first-order kinetic model and a pseudo-second-order kinetic model
Metal ions |
Pseudo-first-order |
Pseudo-second-order |
k1 (min−1) |
qe1 (mg g−1) |
R2 |
k2 (min−1) |
qe2 (mg g−1) |
R2 |
Cd(II) |
69 |
370 |
0.76 |
0.12 |
445 |
0.95 |
Cu(II) |
85 |
457 |
0.86 |
0.20 |
515 |
0.96 |
Pb(II) |
65 |
346 |
0.97 |
0.55 |
363 |
0.99 |
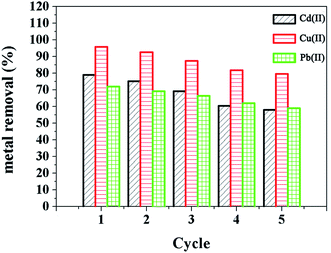 |
| Fig. 7 Sorption–desorption cycles of the Fe3O4@SiO2@mSiO2–COOH microspheres with different heavy metal ions. | |
4. Conclusions
In conclusion, we describe the synthesis of novel core–shell structured magnetic mesoporous silica microspheres combining well designed surface properties and a mesoporous structure and we also describe their enhanced adsorption performance. The obtained Fe3O4@SiO2@mSiO2–COOH microspheres possess a number of important features as a recyclable adsorbent: they contain a mesoporous SiO2 shell with radially oriented large mesopores (11.03 nm) and accessible carboxyl functionalized surfaces for an enhanced adsorption performance, a high field-responsive magnetic Fe3O4 core for efficient magnetic separation, and a SiO2 inter-layer for protecting the Fe3O4 core from chemical dissolution. Owing to the well-defined nanostructure and the highly integrated functions, the prepared material is very suitable as an adsorbent for the removal of heavy metal ions (Cd(II), Cu(II), and Pb(II)), and exhibits a high adsorption capacity, a rapid adsorption rate, and an easy separation process. In addition, the adsorbent can be regenerated by acid treatment and reused in the next cycle with good stability. To get enhanced adsorption performance, this contribution takes further steps to coordinate mesoporous structures with surface properties, which could possibly inspire a lot of future research.
Conflicts of interest
There are no conflicts to declare.
Acknowledgements
This work was supported by the Jilin Province Science & Technology Department Project (Grant no. 20150520020JH, 20160519020JH and 20170520122JH), the National Natural Science Foundation of China (Grant no. 51608050, 51601018 and 51671035), and the Science and Technology Research Project of the Education Department of Jilin Province (Grant no: 2016327).
References
- M. M. Matlock, B. S. Howerton and D. A. Atwood, Chemical precipitation of heavy metals from acid mine drainage, Water Res., 2002, 36(19), 4757–4764 CrossRef CAS PubMed.
- S. Otsuki, T. Nonaka and N. Takashima, et al., Oxidative desulfurization of light gas oil and vacuum gas oil by oxidation and solvent extraction, Energy Fuels, 2000, 14(6), 1232–1239 CrossRef CAS.
- P. B. Hamilton, Ion exchange chromatography of amino acids. A single column, high resolving, fully automatic procedure, Anal. Chem., 1963, 35, 2055–2064 CrossRef CAS.
- S. H. Huang and D. H. Chen, Rapid removal of heavy metal cations and anions from aqueous solutions by an amino-functionalized magnetic nano-adsorbent, J. Hazard. Mater., 2009, 163(1), 174–179 CrossRef CAS PubMed.
- Y. Gao, X. Chen and J. Zhang, et al., Chitin-Derived Mesoporous, Nitrogen-Containing Carbon for Heavy-Metal Removal and Styrene Epoxidation, ChemPlusChem, 2015, 80(10), 1556–1564 CrossRef CAS.
- J. Song, H. Kong and J. Jang, Adsorption of heavy metal ions from aqueous solution by polyrhodanine-encapsulated magnetic nanoparticles, J. Colloid Interface Sci., 2011, 359(2), 505–511 CrossRef CAS PubMed.
- B. A. M. Al-Rashdi, D. J. Johnson and N. Hilal, Removal of heavy metal ions by nanofiltration, Desalination, 2013, 315, 2–17 CrossRef CAS.
- S. Babel and T. A. Kurniawan, Low-cost adsorbents for heavy metals uptake from contaminated water: a review, J. Hazard. Mater., 2003, 97(1), 219–243 CrossRef CAS PubMed.
- G. Crini, Non-conventional low-cost adsorbents for dye removal: a review, Bioresour. Technol., 2006, 97(9), 1061–1085 CrossRef CAS PubMed.
- M. Rafatullah, O. Sulaiman and R. Hashim, et al., Adsorption of methylene blue on low-cost adsorbents: a review, J. Hazard. Mater., 2010, 177(1), 70–80 CrossRef CAS PubMed.
- L. Mercier and T. J. Pinnavaia, Access in mesoporous materials: advantages of a uniform pore structure in the design of a heavy metal ion adsorbent for environmental remediation, Adv. Mater., 1997, 9(6), 500–503 CrossRef CAS.
- X. Feng, G. E. Fryxell and L. Q. Wang, et al., Functionalized monolayers on ordered mesoporous supports, Science, 1997, 276(5314), 923–926 CrossRef CAS.
- J. P. K. Reynhardt, Y. Yang and A. Sayari, et al., Periodic mesoporous silica-supported recyclable rhodium-complexed dendrimer catalysts, Chem. Mater., 2004, 16(21), 4095–4102 CrossRef CAS.
- N. Baccile and F. Babonneau, Organo-modified mesoporous silicas for organic pollutant removal in water: Solid-state NMR study of the organic/silica interactions, Microporous Mesoporous Mater., 2008, 110(2), 534–542 CrossRef CAS.
- S. Wu, F. Li and R. Xu, et al., Synthesis of thiol-functionalized MCM-41 mesoporous silicas and its application in Cu(II), Pb(II), Ag(I), and Cr(III) removal, J. Nanopart. Res., 2010, 12(6), 2111–2124 CrossRef CAS.
- Q. Yuan, N. Li and Y. Chi, et al., Effect of large pore size of multifunctional mesoporous microsphere on removal of heavy metal ions, J. Hazard. Mater., 2013, 254, 157–165 CrossRef PubMed.
- J. Sun, H. Zhang and R. Tian, et al., Ultrafast enzyme immobilization over large-pore nanoscale mesoporous silica particles, Chem. Commun., 2006, 12, 1322–1324 RSC.
- J. Yang, D. Shen and Y. Wei, et al., Monodisperse core-shell structured magnetic mesoporous aluminosilicate nanospheres with large dendritic mesochannels, Nano Res., 2015, 8(8), 2503–2514 CrossRef CAS.
- H. Wang, Y. F. Yu and Q. W. Chen, et al., Carboxyl-functionalized nanoparticles with magnetic core and mesopore carbon shell as adsorbents for the removal of heavy metal ions from aqueous solution, Dalton Trans., 2011, 40(3), 559–563 RSC.
- Y. Chi, Q. Yuan and Y. Li, et al., Synthesis of Fe3O4@SiO2-Ag magnetic nanocomposite based on small-sized and highly dispersed silver nanoparticles for catalytic reduction of 4-nitrophenol, J. Colloid Interface Sci., 2012, 383(1), 96–102 CrossRef CAS PubMed.
- N. Yeddou and A. Bensmaili, Equilibrium and kinetic modelling of iron adsorption by eggshells in a batch system: effect oftemperature, Desalination, 2007, 206(1–3), 127–134 CrossRef CAS.
- A. Mittal, L. Kurup and J. Mittal, Freundlich and Langmuir adsorption isotherms and kinetics for the removal of Tartrazine from aqueous solutions using hen feathers, J. Hazard. Mater., 2007, 146(1), 243–248 CrossRef CAS PubMed.
- M. M. Saeed, A. Rusheed and N. Ahmed, Modeling of iron adsorption on HTTA-loaded polyurethane foam using Freundlich, Langmuir and DR isotherm expressions, J. Radioanal. Nucl. Chem., 1996, 211(2), 283–292 CrossRef CAS.
- A. O. Dada, A. P. Olalekan and A. M. Olatunya, et al., Langmuir, Freundlich, Temkin and Dubinin–Radushkevich isotherms studies of equilibrium sorption of Zn2+ unto phosphoric acid modified rice husk, IOSR J. Appl. Chem., 2012, 3(1), 38–45 CrossRef.
- Y. S. Ho and G. McKay, Pseudo-second order model for sorption processes, Process Biochem., 1999, 34(5), 451–465 CrossRef CAS.
Footnote |
† Electronic supplementary information (ESI) available. See DOI: 10.1039/c7ra08937f |
|
This journal is © The Royal Society of Chemistry 2017 |
Click here to see how this site uses Cookies. View our privacy policy here.