DOI:
10.1039/C7RA08448J
(Paper)
RSC Adv., 2017,
7, 48454-48460
Deep oxidative desulfurization catalyzed by (NH4)xH4−xPMo11VO40 (x = 1, 2, 3, 4) using O2 as an oxidant
Received
31st July 2017
, Accepted 10th October 2017
First published on 16th October 2017
Abstract
NH4+ doped PMoV composites catalytic materials are successfully prepared. The NH4+ doped H4PMo11VO40 composites have been tested as highly efficient catalysts in the ultra-deep desulfurization of fuel oils. The reaction conditions are optimized by testing the load of NH4+, temperature, O2 flow velocity, and DBT concentrations. The optimal reaction conditions are given as follows: 0.1 g (NH4)3HPMo11VO40 as catalyst, reaction time 2 h, O2 flow velocity 100 mL min−1, and reaction temperature 120 °C, with a conversion of DBT reaching up to 100% in 90 min, and this catalyst could be used more than five times without significant loss of activity.
1. Introduction
In recent years, environmental pollution has become a more and more serious problem for China or around the world. Environmental concerns make restrictions to the sulfur content of fuel oils more and more exigent. Since 2017, Beijing of China has begun to implement the “Beijing six” fuel standard that called for the sulfur level in oil to be less than 10 ppmw. Industrially, hydrodesulphurization (HDS) of fuel oils is mature in the process of removing thiols, sulfides and disulfides, but has to be operated at severe conditions to reduce refractory sulfur-containing compounds (dibenzothiophene (DBT) and its derivatives) to an ultra-low level.1,2 A promising alternative technology of HDS is oxidative desulfurization (ODS) process.3 The main advantage of ODS is that sulfur compounds can be removed without using hydrogen, at ambient pressure and at relatively low temperature.1,2 In this process, the organosulfur compounds are oxidized to corresponding sulfoxides/sulfones with catalyst and an oxidant agent, and the oxidized sulfur compounds are highly polarized, subsequently removed from the gasoline/diesel by extraction/distillation using water-soluble polar solvents.4 It is showed that the combination of ODS and extraction gets desulfurization more efficient.5 Our previous works show the sulfur content of diesel can be reduced to be lower than 50 ppm.6,7 Due to a short reaction time, at ambient conditions and high efficiency, ODS combined with extraction has been regarded as the most promising to obtain ultra clean fuels.3
However, various studies on the ODS process have employed different oxidizing agents, such as O2,8,9 ozone,10 organic peracids, organic hydroperoxides,11,12 superoxide anions,13,14 and hydrogen peroxide.15 Taking account of economic cost, ecologically benign and safety, the using of O2 as an oxidant for ODS is highly desirable.16 However, the O2 is inactive because its ground state is a low-energy triplet, thus the catalysts has to be used to activated it.16
Indeed, the redox properties of polyoxometalates (POMs) is its most important feature, POMs can be easily tuned by adjusting the amount of protons and changing the metal in the primary structure. The redox properties are responsible for the oxygen insertion reaction, which is necessary for generating oxidized products.17,18 Our works19,20 confirmed that introducing V element into the Keggin unit, such as H4PMo11VO40, for instance, obtains a significant enhancement of ODS activity. Some researchers conclude that under reaction conditions VO2+ cations are formed, and the resulting cubic vanadyl POMs salts was assumed to be an active phase in the catalytic process.21 But H4PMo11VO40, is easily dissolve in water and is difficult to perform separation of reactions and catalyst. Recently, Wang et al.8 found one of polyoxometalates (POMs), ammonium salts, (NH4)5H6PV8Mo4O40 pose 100% removal ratio for DBT in 6 h without sacrificial agent. As a larger cation, NH4+, instead the H+, and (NH4)xH4−xPMo11VO40 (APMV) is not dissolve the water and can easily separated with excellent stability.22 In this work, we prepared four kinds the POMs by doped NH4+, (NH4)xH4−xPMo11VO40 (x = 1, 2, 3, 4). To our knowledge, there have been no reports about ODS using them as catalyst.
2. Experimental
2.1. Catalyst preparation
The methods used to prepare the precursors of these catalysts with the nominal composition MoO3 21.35 g, V2O5 1.22 g, 85% wt H3PO4 1.6 g and deionized water were added to a three-neck flask and heated to reflux under vigorous stirring for 12 h. Nominal NH4Cl were dissolved in 50 mL of deionized water and dropped into the flask at 80 °C. With nominal NH4Cl weight as ratio with Mo mol. number, different load of NH4+ is prepared, (NH4)xH4−xPMo11VO40 (x = 1, 2, 3, 4). All the samples were calcinated at 300 °C for 4 h.
2.2. Catalyst characterization
The XRD data were obtained with Philips PW 1050/81 diffractometer using Ni-filtered Cu Kα radiation. A range from 10–80 °C was scanned with a step of 0.02° per second, and 2 s of acquisition time. Infrared spectra (FT-IR) were recorded on a Thermo Nicolet 480 equipped with a MCT detector, the samples (1 wt%) were pressed to form KBr pellets for analysis.
2.3. Experimental method and products analysis
Model oils with S-content were prepared by dissolving DBT, BT, or 4,6-DBT in n-octane, respectively. The oxidative desulfurization catalytic tests were performed in a three-neck flask with equipped with a stirrer. The oxidative reaction was carried out with 15 mL of model oil, 10 mL PEG-600, O2 as an oxidant. The solution was sampled periodically and analyzed by Agilent Technologies 1260 Infinity Liquid Chromatography equipped with C18 column (250 × 4.6 mm). The mobile phase was 85% methanol aqueous solution. Sulfur removal rate was calculated as follows: sulfur removal (%) = (C0 − C)/C0 × 100, where C0 = initial concentrations of sulfur solution, C = the concentration of sulfur solution after degradation, the peak area value of chromatograms corresponds to the concentration of sulfur solution.
3. Result and discussion
3.1. Characterization of the catalysts
3.1.1 XRD. The patterns of XRD of APMV is presented in Fig. 1, all the samples exhibit three strong diffraction peaks at 2θ = ∼10°, 18–26° and 28–36°, which are characteristic of the Keggin structure.23 These confirmed that with or without NH4+, the composites keep uniform size and stable Keggin structure. When the NH4+ introducing to the H4PMo11VO40, the peak of d-spacing of plane (222) appear. It is should be noted that two diffraction peaks at 2θ = 15.1° and 21.4°,24 only appear for the catalysts containing NH4+, the intensities of these peaks weaken as the number of NH4+ decreases. Therefore, these two diffraction lines could be considered as characteristic of the presence of NH4+ cations-containing polyoxometalates.
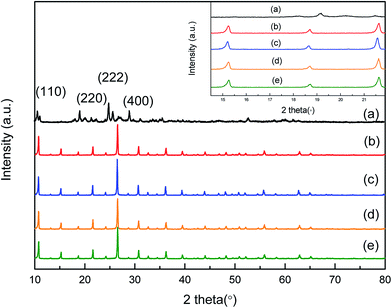 |
| Fig. 1 X-ray diffraction patterns of (a) H4PMo11VO40 (b) (NH4)H3PMo11VO40 (c) (NH4)2H2PMo11VO40 (d) (NH4)3HPMo11VO40 and (e) (NH4)4PMo11VO40. | |
3.1.2 FT-IR spectra. The FT-IR spectra of the catalysts are given in Fig. 2, each spectrum has four strong absorption peaks at 1065, 965, 865, and 785 cm−1, which correspond to the P–Oa, Mo–Od, Mo–Ob–Mo, and Mo–Oc–Mo asymmetric stretching vibrations, respectively; these are constant with the Keggin structure of the heteropolyanion.25 The spectra also have two small absorption peaks at 1416 and 1030 cm−1, which are respectively attributed to the N–H deformations of the NH4+ cations and V
O of the vanadyl species of [PMo11VO40] Keggin units.23
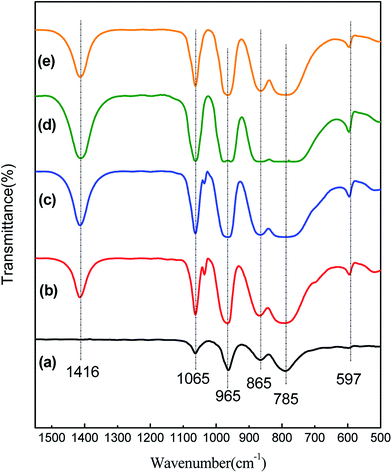 |
| Fig. 2 FT-IR spectra of the samples: (a) H4PMo11VO40 (b) (NH4)H3PMo11VO40 (c) (NH4)2H2PMo11VO40 (d) (NH4)3HPMo11VO40 and (e) (NH4)4PMo11VO40. | |
3.1.3 Elemental analysis. The element analysis results are given in Table 1, it is shown that the indeed NH4+/PMo11VO40 proportion depends on the preparation condition, is slight different from nominal values. It is shown from the indeed molar ratio of Mo/N is 14.6 for (NH4)H3PMo11VO40, and its expected values should be 11, this means a small quantity of NH4Cl is lost in the catalyst prepare process. But the trend of indeed Mo/N molar ratio is in accordance with nominal values. At same time, the Mo/V and Mo/P molar ratio are similar between their nominal values versus indeed values, respectively.
Table 1 Composition of the samples determined by elemental analysis
Samples |
Composition (wt%) |
Molar ratioa |
N |
P |
Mo |
V |
Mo/N |
Mo/V |
Mo/P |
Nominal values are given in parentheses. |
(NH4)H3PMo11VO40 |
0.61 |
1.74 |
61.03 |
2.61 |
14.6(11) |
11.1(11) |
11.3(11) |
(NH4)2H2PMo11VO40 |
1.11 |
1.68 |
60.10 |
2.71 |
7.9(5.5) |
11.4(11) |
11.5(11) |
(NH4)3HPMo11VO40 |
1.50 |
1.71 |
60.07 |
2.47 |
5.8(3.7) |
11.9(11) |
11.4(11) |
(NH4)4PMo11VO40 |
2.10 |
1.63 |
59.03 |
2.46 |
4.1(2.8) |
11.8(11) |
11.7(11) |
3.2. Oxidation of model sulfur compounds
3.2.1 Influence of the ratio of NH4+/[PMo11VO40]4−. DBT is firstly chosen as the typical sulfide to investigate the catalytic performance of samples using O2 as an oxidant. Aim to find suitable ratio of NH4+/[PMo11VO40]4−, a comparison of DBT removal efficiency of model oil for different samples, is shown Fig. 3(a). It is seen that the sulfur removal efficiency of APMV follows the order of (NH4+)3HPMo11VO40 > (NH4+)4PMo11VO40 > (NH4+)2H2PMo11VO40 > (NH4+)H3PMo11VO40, and the maximal DBT removal ratio 100% is achieved with (NH4+)3HPMo11VO40 in 90 min. It shows that NH4+ cation performs great role over the activity of sulfur removal, similar trend obtained when the reaction time is 60 min, thus the (NH4+)3HPMo11VO40 catalyst was chosen for further research.
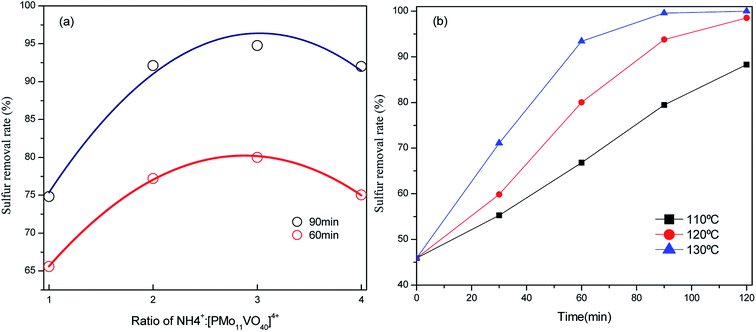 |
| Fig. 3 (a) The sulfur removal ratio of the NH4+ doped contents, (b) the sulfur removal ratio of DBT under different reaction temperature (reaction conditions: 0.1 of catalyst, DBT in 15 mL n-octane (320 ppm), oxidant O2). | |
3.2.2 Influence of the reaction temperature. As shown in Fig. 3(b), temperature play an important role in the oxidation of DBT, it is seen that the sulfur removal activity of (NH4+)3HPMo11VO40 follow the order of 130 °C > 120 °C > 110 °C. The sulfur removal rate reach as high as almost 100% at 130 °C in 90 min, corresponds to 120 °C, 110 °C, their removal ratio are 93%, 75%, respectively. However, the DBT removal ratio also reach 100% at 120 °C in 2 h, from the viewpoint of security and economy, an optimal temperature of 120 °C can be recommended.The kinetics studies of the oxidative reaction were taken under different reaction temperatures. The result in Fig. 4(a) show that plot ln(C0/Ct) versus the reaction time under different temperature follow the pseudo-first-order kinetics. The rate constant k of the oxidation reaction increased from 0.0169 (at 110 °C) to 0.0609 (at 130 °C), means higher temperature benefits the oxidation reaction. Based on the reaction rates vs. temperatures, the apparent activation energy for the oxidation of DBT can derived from the Arrhenius equation and is 21.68 kJ mol−1 (Fig. 4(b)).
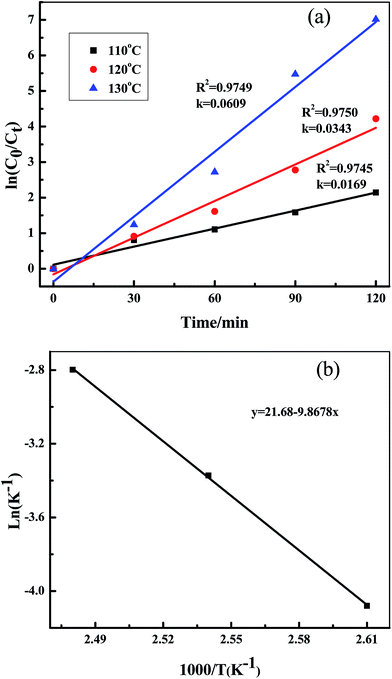 |
| Fig. 4 (a) Pseudo-first-order kinetics for the oxidative of DBT (320 ppm) under different reaction temperatures in the ODS system (reaction conditions: 0.1 of catalyst, DBT (320 ppm) in 15 mL n-octane, oxidant O2), (b) Arrhenius activation energies for DBT removal with (NH4)3HPMo11VO40 as catalyst. | |
3.2.3 Influence of molar ratio O2/DBT. The reaction was carried out over (NH4)3HPMo11VO40 using different O2 flow velocity (Fig. 5(a)). The sulfur removal rate was found to near 100% after 90 min with O2 flow velocity 100 mL min−1. The sulfur removal rata almost keep 45% without O2, this value is the extraction DBT value of PEG-600. This confirms that the O2 is indispensable role for this reaction, with the increase of O2 flow velocity, the sulfur removal rate increase greatly, this implies that an increase of the O2 concentration promotes this reaction. On the other hand, this plot of Fig. 5(a) demonstrates that the optimal conditions for sulfur removal are an high O2 flow velocity (100 mL min−1).
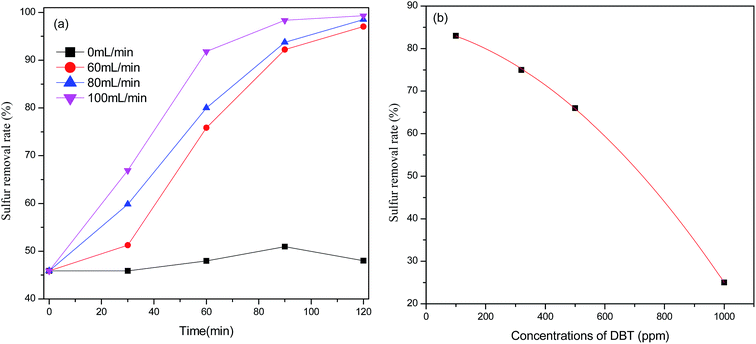 |
| Fig. 5 (a) Effect of sulfur removal ratio of DBT (320 ppm) under different O2 flow velocity; (b) the influence of DBT concentrations on the catalytic activity in 1 h. | |
3.2.4 Influence of DBT concentrations. For the process interest, the influence of DBT concentration is also investigated. Fig. 5(b) show that, the sulfur removal rate is decrease with the increase of DBT concentration. At same time, this results show an significant change in reaction efficiency to sulfur removal was observed for increasing the catalyst weight, means that the catalyst amount has positive influence on catalytic activity. At the same O2 flow velocity (80 mL min−1), for the 100 ppm/15 mL model oil, 0.1 of catalyst was used, the ratio of sulfur/catalyst is 100 ppm/0.1 g, sulfur removal ratio is 83%. With the content of sulfur increase to 320 and 450 ppm, the sulfur removal ratio is 75% and 67%, respectively. The decrease of sulfur removal ratio attributes to the higher ratio of sulfur vs. catalyst (320 ppm/0.1 g, 450 ppm/0.1 g, respectively). When sulfur content reach as high as 1000 ppm, the load of catalyst becomes one-tenth of previous reaction mixture (100 ppm/0.1 g), results in the sulfur removal ratios plumper to 23%. Our experimental confirm that when load of catalyst increase to 1.0 g, the sulfur removal ratio reach as high as 83% in 1 hour.From the above discussion, the optimal reaction condition is as follows: 15 mL of model oil, 10 mL PEG-600, 0.1 g (NH4)3HPMo11VO40 as catalyst, reaction time 2 h, O2 flow velocity 100 mL min−1, and reaction temperature 120 °C.
3.2.5 For different sulfur substrates. Three typical sulfur-containing compounds DBT, 4,6-DBT and BT were chosen to investigate the desulfurization performance under same reaction conditions. As shown in Fig. 6, the removal ratio of DBT, 4,6-DBT and BT are 100%, 79% and 57% in 2 h, respectively. Obviously, the order of removal efficiency follows as: BT < 4,6-DBT < DBT. The oxidation of sulfur compounds is in accordance with the electrophilic addition mechanism, i.e., the order of electron density for S-compounds mentioned above is BT (5.739) < DBT (5.758) < 4,6-DBT (5.760)16 and thus the higher electron density on S atom may contribute to the better reactivity. The three sulfur-containing compounds are basically conformed to the order except for 4,6-DBT. The reasonable explanation was that 4,6-DBT has two methyl groups, led to large steric hindrance, it exhibits the lower reactivity than that of DBT. Previous work16 obtained relative energies of excited states of BT (36.1 kcal mol−1) > 4,6-DBT (13.9 kcal mol−1) > DBT (13.4 kcal mol−1), this order is in agreement with our results. Above discussions show that the activity of sulfur compounds not only has intimate relation with the electron density of S atom, but also with the micro-dynamics of ODS reaction.
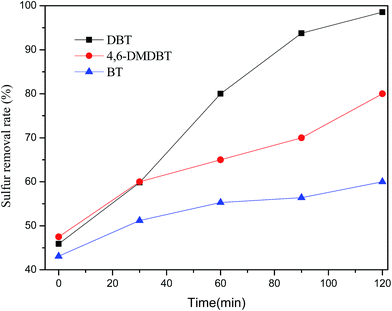 |
| Fig. 6 Sulfur removal of different substrates catalyzed by (NH4)3HPMo11VO40 (reaction conditions: 0.1 g catalyst, 4,6-DBT, DBT, and BT (320 ppm) in 15 mL n-octane, O2 80 mL min−1, 120 °C). | |
3.2.6 Investigation of real fuel. The ODS of real diesel was performed at follow conditions: 1.0 g (NH4)3HPMo11VO40 as catalyst, reaction time 2 h, 15 mL real diesel at 1000 ppm sulfur, O2 flow velocity 100 mL min−1, and reaction temperature 120 °C. As shown in Fig. 7, the sulfur removal ratio reaches as high as 91% at 120 min. This results indicate that (NH4)3HPMo11VO40 perform high efficiency for the ODS of real diesel.
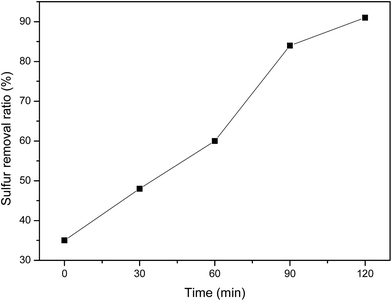 |
| Fig. 7 The effect of time on the sulfur content for real diesel. | |
3.3. Reusability of catalyst
Scheme 1 shows the color of reaction mixtures before and after reaction. The catalyst performs obvious color change, from deep yellow (refer to VVPMo composites) change to light blue (refer to VIVPMo composites). This result is in well agreement with published work.8
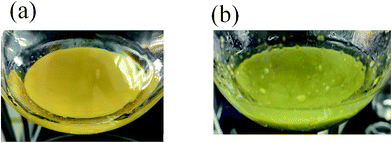 |
| Scheme 1 The reaction mixture before (a) and after (b) testing. | |
Recycling experiments were investigated and the results are presented in Fig. 8. After the each reaction was finished, the catalyst was separated from the reaction mixture by filtration/centrifugal. It is seen that the sulfur removal performance has no obvious drop during the five times reactions, this result further confirms (NH4)3HPMo11VO40 catalyst has excellent reusability.
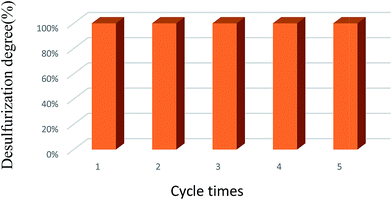 |
| Fig. 8 Effect of the recycles on the desulfurization of DBT with (NH4)3HPMo11VO40 as catalyst. | |
The XRD results of fresh (a), used (b) catalyst are given in Fig. 9. Prior to characterization of the sample, the liquid phases were separated by decantation, and calcinated at 300 °C for 4 h. The XRD spectra of fresh and used sample were very similar, this result demonstrates this catalyst holds good stability.
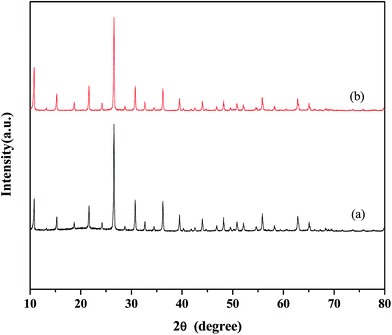 |
| Fig. 9 X-ray diffraction patterns of fresh (a), used (b) catalysts. | |
3.4. The mechanism for DBT oxidation with oxygen
As shown in Scheme 2, the reaction mixture applied herein is typical system consisting of a polar solvent (PEG-600) and a nonpolar phase (n-octane). In this system, the DBT preferentially resides in the non-polar phase, whereas the oxidants and catalyst primarily reside in the polar phase. Firstly, DBT were extracted into PEG-600 and reacted with O2 with the help of catalyst. The active oxygen species were produced through the process of VIV transferring to VV in (NH4)xH4−xPMo11VO40 with O2. The O2 was activate, and form an active species when O2 coordinated to VV, and change VIV to VV. Then, the active species oxidized DBT to DBTO2 when the catalyst recovered.
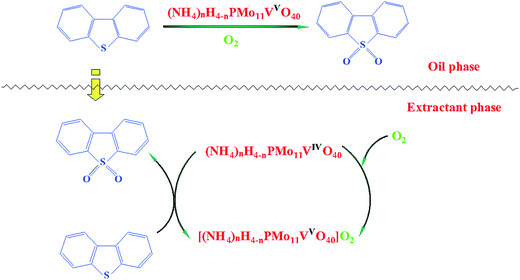 |
| Scheme 2 The reaction mechanism. | |
4. Conclusions
In sum, a kind of NH4+ doped PMoV composite catalytic material are successfully prepared. The (NH4+)3HPMo11VO40 composite has been tested as the highly efficient in the ultra-deep desulfurization of fuel oils with a conversion of DBT reaching up to 100%, and this catalyst could be used for more than five times without significant loss of activity.
Conflicts of interest
There are no conflicts to declare.
Acknowledgements
We would like to acknowledge for the financial support of Key Project of Tianjin Research Program of Application Foundation and Advanced Technology (No. 14JCZDJC40600) and National Undergraduate Innovation and Entrepreneurship Training Project (No. 201710057010).
References
- F. Pelardy, A. S. Santos, A. Daudin, E. Devers, T. Belin and S. Brunet, Appl. Catal., B, 2017, 206, 24–34 CrossRef CAS.
- F. Pelardy, A. Daudin, E. Dever, C. Dupont, P. Raybaud and S. Brunnet, Appl. Catal., B, 2016, 183, 317–327 CrossRef CAS.
- B. Berleff, J. Claubnitzer, W. Korth, P. Wasserscheid, A. Jess and J. Albert, ACS Sustainable Chem. Eng., 2017, 5, 4110–4118 CrossRef.
- D. Piccinino, I. Abdalghani, G. Botta, M. Crucianelli, M. Passacantando, M. L. D. Vacri and R. Saladina, Appl. Catal., B, 2017, 200, 392–401 CrossRef CAS.
- M. Nagai, N. T. Tung, Y. Adachi and K. Kobayashi, Catal. Today, 2016, 271, 91–101 CrossRef CAS.
- Y. Tian, Y. Yao, Y. Zhi, L. Yan and S. Lu, Energy Fuels, 2015, 29, 618–625 CAS.
- Z. Lu, E. Guo, H. Zhong, Y. Tian, Y. Yao and S. Lu, Energy Fuels, 2016, 30, 7214–7220 CrossRef CAS.
- M. Shi, D. Zhang, X. Yu, Y. Li, X. Wang and W. Yang, Fuel Process. Technol., 2017, 160, 136–142 CrossRef CAS.
- S.-W. Li, J.-R. Li, Y. Gao, L.-L. Liang, R.-L. Zhang and J.-S. Zhao, Ind. Eng. Chem. Res., 2017, 197, 551–561 CAS.
- C. Ma, D. Chen, F. Liu, X. Sun, F. Xiao and B. Dai, RSC Adv., 2015, 5, 96945–96952 RSC.
- J. M. Campos-Martin, M. C. Capel-Sanchez, P. Perez-Presas and J. L. G. Fierro, J. Chem. Technol. Biotechnol., 2010, 85, 879–890 CrossRef CAS.
- D. Wang, E. W. Qian, H. Amano, K. Okata, A. Ishihara, F. Murrieta, J. Navarret and F. Jimenez-Cruz, Appl. Catal., A, 2003, 253, 91–99 CrossRef CAS.
- F. S. Mjalli, O. U. Ahmed, T. Al-Wahaibi, Y. Al-Wahaibi and I. M. AlNashef, Rev. Chem. Eng., 2014, 30, 337–378 CAS.
- Y. Shiraishi, K. Tachilban, T. Hirai and I. Komasawa, Ind. Eng. Chem. Res., 2002, 41, 4362–4375 CrossRef CAS.
- P. Wu, W. Zhu, A. Wei, B. Bai, Y. Chao, C. Li, H. Li and S. Dai, Chem.–Eur. J., 2015, 21, 15421–15427 CrossRef CAS PubMed.
- X. Zeng, X. Xiao, Y. Li, J. Chen and H. Wang, Appl. Catal., B, 2017, 209, 98–109 CrossRef CAS.
- Z. Long, Y. Zhou, G. Chen, W. Ge and J. Wang, Sci. Rep., 2014, 4, 3651–3655 CrossRef CAS PubMed.
- Z. Long, Y. Zhou, G. Chen, P. Zhao and J. Wang, Chem. Eng. J., 2014, 239, 19–25 CrossRef CAS.
- Y. Yao, H. Zhang, Y. Lu, Y. Zhi and S. Lu, React. Kinet., Mech. Catal., 2016, 118, 621–632 CrossRef CAS.
- S. Lu, H. Zhang, D. Wu, X. Han, Y. Yao and Q. Zhang, RSC Adv., 2016, 16, 79520–79525 RSC.
- T. Ilkenhans, B. Herzog, T. Brown and R. Schlögl, J. Catal., 1995, 153, 275–292 CrossRef CAS.
- F. Cavani, R. Mezzogori, A. Pigamo and F. Trifiro, Top. Catal., 2003, 23, 119–124 CrossRef CAS.
- F. Jing, B. Karyniok, F. Dumeignil and E. Bordes-Richard, Catal. Sci. Technol., 2014, 4, 2938–2945 CAS.
- F. Jing, B. Karyniok, F. Dumeignil and E. Bordes-Richard, J. Catal., 2014, 309, 121–135 CrossRef CAS.
- H. Zhang, R. Yan, L. Yang, Y. Diao, L. Wang and S. Zhang, Ind. Eng. Chem. Res., 2012, 52, 4484–4490 CrossRef.
|
This journal is © The Royal Society of Chemistry 2017 |
Click here to see how this site uses Cookies. View our privacy policy here.