DOI:
10.1039/C7RA08383A
(Paper)
RSC Adv., 2017,
7, 46852-46857
Retardation and reaction mechanisms of magnesium phosphate cement mixed with glacial acetic acid
Received
29th July 2017
, Accepted 18th September 2017
First published on 4th October 2017
Abstract
This study aims to investigate the effect of admixture glacial acetic acid on the setting time, compressive strength, and hydration temperature of magnesium phosphate cement. The mechanism of the effect of glacial acetic acid was analyzed by introducing X-ray diffraction and scanning electron microscopy techniques. It is demonstrated that addition of glacial acetic acid into the hardening process of MPC could directly affect the curing effect and setting time by changing the concentration of H+ in the mixture. At the same time, the strength of the hardened body was improved and the hydration heat release characteristics of MPC were changed, which favored in dealing with limited retarding effect and poor operability of MPC.
1. Introduction
Magnesium phosphate cement (MPC) is a new type of phosphate repair material with early strength and super rapid hardening ability. Compared with Portland cement, MPC has advantages such as rapid low-temperature condensation, high bond strength, minimal dry shrinkage, and good abrasion and frost resistance. Therefore, it is widely used in the quick repair of roads, bridges, airport runways, and radioactive substances, contributing a lot to both civilian and military purposes.1–5
Mainly prepared with certain MgO, phosphate, and retarder, MPC has been favored by its fast hardening, high early strength, low thermal expansion, and good adhesion.6–8 As a superior cementing material, the setting time is a key factor that might influence the range of MPC application. For instance, quick coagulation defects have been hindering the widespread use of MPC, which are mostly overcome using borax as a retarder at present. However, related studies have confirmed that borax can only contribute to limited retardation effects, and its excessive use can significantly reduce the mechanical properties of MPC.9,10 Efforts have been constantly made to improve the preparation technology of MPC. Despite certain achievements, insurmountable technical problems remain.
It has been shown that a certain number of dead-burned magnesia particles immediately react with phosphate in MPC hydration, producing amorphous and crystalline struvite. This struvite adheres to the unreacted dead-burned magnesia particles, leading to solid particle formation. As is known, hydration is an acid–base neutralization reaction,11,12 and hence the cement system undergoes acidic and basic stages during this process, resulting in massive heat release in a short time.13,14
According to acid and alkali neutralization reaction theory, acid additives in the MPC hardening process are supposed to change the H+ concentration in the mixture, which directly affects the cement solidification process that is modified by additives. Thus, the strength of the hardened MPC can be enhanced. Micro-measurements and analyses were conducted to explore the influence of glacial acetic acid additives on the micro-structure of hardened MPC. This study can provide theoretical basis for the engineering application of calcium phosphate cement.
2. Test
2.1 Raw materials and mixing ratio
MPC was prepared by mixing magnesia oxide powder, NH4H2PO4 and compound retarder according to a certain proportion in the laboratory. A commercial dead-burned magnesium oxide calcined at 1700 °C was used, with the MgO content ranging from 90 to 98%. Dead-burned magnesia was characterized by its low chemical reactivity and high resistance to basic slags. The magnesium oxide presented a specific surface area of 1020 m2 kg−1, and the particle size distributions are shown in Fig. 1. The chemical compositions of the commercial dead-burned magnesium oxide are listed in Table 1.
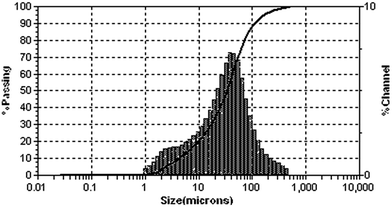 |
| Fig. 1 Size distribution of magnesium oxide powder. | |
Table 1 Chemical composition of magnesium oxide powder/(wt%)
MgO |
SiO2 |
CaO |
Loss |
91.85 |
3.68 |
3.14 |
1.2 |
Industrial grade NH4H2PO4 was used as the soluble phosphate in this study, with maximum particle size of 700 μm and purity greater than 98%. The compound retarder was prepared with industrial borax (NaB4O7·10H2O) and glacial acetic acid in the laboratory, and it is abbreviated as B in the text below. The maximum B particle size was 800 μm and its purity was greater than 98%. Furthermore, 0%, 3%, 6%, and 9% glacial acetic acid were prepared by adding water into glacial acetic acid (glacial acetic acid content ≥ 98%). River sands with a fineness modulus of 2.75 and a saturated surface dry specific gravity of 2720 kg m−3 were used as fine aggregates. Portable water was used for mixing.
MPC pastes were prepared with proportional MgO, NH4H2PO4, B, and glacial acetic acid solution. The liquid–cement ratio (mliquid/mMPC) was set as 0.12 in the laboratory, and the mass ratio of B and MgO powder was 1
:
20. With constant mMgO/mNH4H2PO4 and mliquid/mMPC ratios, the influence of glacial acetic acid on MPC properties was analyzed. The grouping and mixture ratios are shown in Table 2.
Table 2 Mix of MPC pastes
Code name |
mMgO/mNH4H2PO4 |
mB/mMgO |
mliquid/mMPC |
Glacial acetic acid concentration |
M1 |
4 |
5% |
0.12 |
0 |
M2 |
4 |
5% |
0.12 |
3% |
M3 |
4 |
5% |
0.12 |
6% |
M4 |
4 |
5% |
0.12 |
9% |
2.2 Methods
2.2.1 Setting time. A Vicat apparatus was used to measure the setting time of neat MPC mortar. Since the time interval between presetting and final setting could be very short in normal temperature conditions, only the final setting time was measured every 1 min approaching the final set. The setting time of neat MPC mortar was measured according to national standard GB/T 1346-1346 “Test method for water requirement of normal consistency, setting time, and soundness of Portland cement”.
2.2.2 Strength. MPC mortar was mixed with standard sand in the ratio of mMPC
:
mS = 1
:
1.45 and poured into a 40 mm × 40 mm × 160 mm model. The mixture was tamped and vibrated for 60 times in the flow device. After excess mortar was scraped off, samples were demoulded after 3 h and cured to the required age in 20 ± 3 °C environment. The compressive strengths in the 1st, 3rd, 7th, and 28th day were measured using a WED100 electronic universal material tester.
2.2.3 Hydration temperature. With an ambient temperature of 20 °C, a certain amount of water was added into 100 g of MPC as acidic component in dry powder. The minimum temperature was measured, and after 1 min, alkaline components (start timing) were added and mixed evenly. The mixture was then placed in an insulated container. This process was completed within 2 min, during which the initial temperature of the MPC slurry was measured with a thermometer. A K-type thermocouple was inserted into the middle of the slurry and the temperature change during the hydration was recorded by a BTM-4208SD automatic temperature recorder manufactured by Lutron Electronics of Taiwan.
3. Results and discussion
3.1 Setting time
Fig. 2 shows the setting time of MPC mortar when glacial acetic acid solutions with different concentrations were used. The setting time of the glacial acetic acid-free mortar was 14 min when B was added. The performance of glacial acetic acid MPC was greatly improved, and its setting time reached 29 min and 48 min when the concentrations of glacial acetic acid were 3% and 9%, respectively. After adding 6% acetic acid, the setting time of MPC was 34 minutes. Therefore, it was safe to conclude that the retarding effect of glacial acetic acid on MPC was obvious.
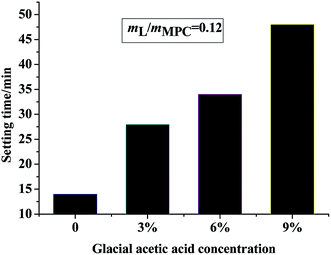 |
| Fig. 2 Effect of glacial acetic acid on setting time. | |
3.2 Compressive strength
Fig. 3 shows the compressive strength of MPC mortar supplemented with glacial acetic acid in different concentrations. The early strength of samples increased rapidly with the glacial acetic acid concentration, exceeding 50 MPa on days 1 and 3. The early strength on Day 7 was 20% higher than that on Day 1, exhibiting a considerable increase. As the reaction proceeded, the long-term strength increased gradually.
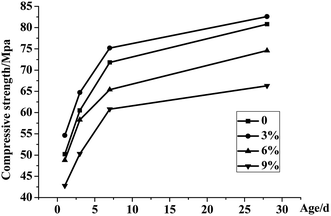 |
| Fig. 3 Development of compressive strength of MPC mortar. | |
The compressive strength growths of mortar with and without glacial acetic acid were consistent, rapid in the early stage, and slow in the late stage, which conformed to the high early strength feature of MPC. On Day 3, the strength of MPC without glacial acetic acid was 60.5 MPa, whereas that with glacial acetic acid was 64.7 MPa. These findings indicated the retarding and early strength effects of glacial acetic acid.
The sample added with glacial acetic acid had a strong intensity, which was apparent in the early strength on days 1 and 3. With the increase in concentration, the strength of MPC continuously increased, reaching the peak at a concentration of 3%. The strength of MPC with glacial acetic acid exceeded 82.6 MPa on Day 28, whereas that without glacial acetic acid was 80.8 MPa. When the acetic acid concentration exceeded 3%, MPC strength began to decline. Therefore, the optimum concentration of glacial acetic acid is about 3%, based on consideration of the retarding effect of glacial acetic acid and the influence of MPC intensity.
3.3 Hydration temperature
The hydration temperature curve of the MPC slurry is presented in Fig. 4, which illustrates the following scenarios.
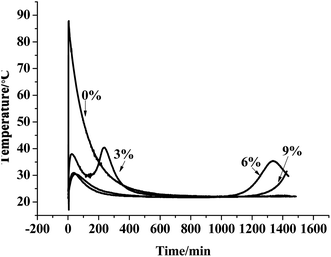 |
| Fig. 4 Effect of glacial acetic acid on temperature of MPC paste. | |
3.3.1 Without addition of glacial acetic acid. At the beginning of the hydration reaction, the temperature of the MPC slurry rapidly increased until reaching the maximum, and then began to decrease. When the temperature approached the ambient temperature, the slurry temperature hardly changed. The hydration temperature curve of the MPC slurry had one temperature peak (centered at 80 °C) and one rest period.
3.3.2 3% concentration of glacial acetic acid. At the beginning of the hydration reaction, the MPC slurry temperature rose to 35 °C and then kept decreasing for a certain period. The test temperature continued to increase to 40 °C and then decreased, and the slurry temperature did not change when the temperature approached ambient temperature. The hydration temperature curve exhibited two closely distributed temperature peaks (both centered around 40 °C) and one rest period. The results showed that acetic acid changed the exothermic characteristics of the MPC slurry and had a significant effect on the first temperature peak, while the second temperature peak appeared at the same time.
3.3.3 6% concentration of glacial acetic acid. When the concentration of glacial acetic acid was 6%, the hydration temperature first increased and then decreased, and then increased again and finally decreased to room temperature. There were two temperature peaks and one rest period as well. The first temperature peak did not exceed 30 °C, and the second was delayed by 16 hours. The peak temperature was lower than 40 °C.
3.3.4 9% concentration of glacial acetic acid. At the beginning of the hydration reaction, the temperature of the MPC slurry increased rapidly until reaching the maximum temperature of 30 °C, and then decreased to the ambient temperature. The temperature of the MPC slurry was stable for a long time. There was only one temperature peak (smaller than 30 °C) and one rest period.The abovementioned analysis showed that the first hydration temperature peak of the MPC paste with glacial acetic acid was significantly lower than that of the MPC slurry without glacial acetic acid, and a second temperature peak was found to appear. With an increase in the glacial acetic acid concentration, the first temperature peak value gradually decreased, while the second temperature peak exhibited a significant time delay, indicating obvious retarding effect of glacial acetic acid on the MPC slurry.
3.4 Microstructures alteration
Fig. 5(a) and (b) show XRD patterns of the MPC paste hardened with no glacial acetic acid and with 3% glacial acetic acid, respectively, under the standard conditions for 28 days. As seen in the XRD pattern of the MPC-cured hardened body, the diffraction peak of MgO was strong, indicating the presence of abundant unhydrated MgO. Fig. 4(b) shows the formation of a new diffraction peak corresponding to magnesium acetate (C4H6O4Mg·4H2O), while the other diffraction peaks correspond to MgO, NH4H2PO4, MgNH4PO4·6H2O (commonly known as struvite). Glacial acetic acid could react with magnesium ions to form hydrated magnesium acetate gel in the hydration reaction.
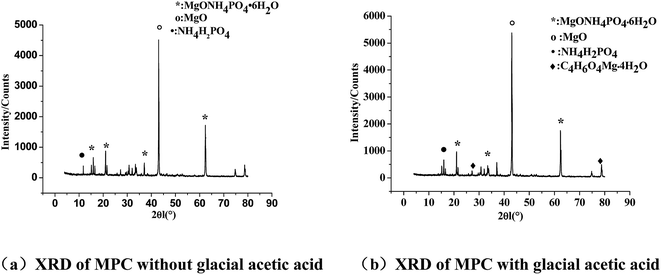 |
| Fig. 5 XRD pattern of hardened MPC paste for 28 d soaking. | |
Fig. 6(a) and (b) show the SEM images of MPC cured without acetic acid as well as the micro morphology on Day 28 after addition of acetic acid. Bulk hydration products were formed in MPC hardenite without glacial acetic acid, which were interlocked, forming a network structure. However, acicular hydrated magnesium acetate crystals were inserted among bulk hydration products in MPC hardenite with glacial acetic acid. The acicular crystals joined and interlaced each other to form a compact structure. Given the action of acetic acid, grains of hydration products of the MPC-hardened body should be much smaller, leading to more compact structures.
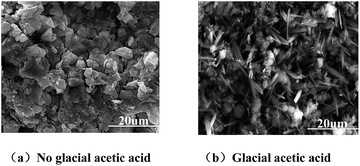 |
| Fig. 6 SEM diagram of MPC. | |
4. Mechanism analysis
4.1 Reaction mechanism of MPC
As shown in Fig. 7, the hydration reaction process of the MPC hydration system could be divided into the following stages.
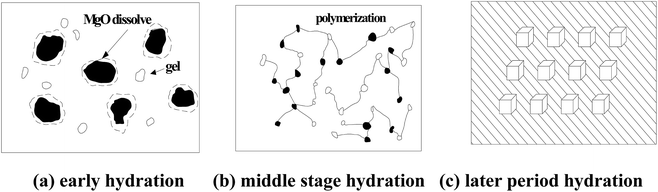 |
| Fig. 7 Schematic of hardening and setting of MPC. | |
4.1.1 Early hydration. As shown in Fig. 7(a), after MPC was mixed with water, the soluble NH4H2PO4 was rapidly dissolved in a small amount of water, forming an acidic aqueous solution. The dead-burned MgO was gradually dissolved in acidic liquid medium, and then it was ionized and hydrolyzed into hydrated magnesium ion [Mg(H2O)62+], which then reacted with NH4+ and PO43− in the medium to form an amorphous magnesium-ammonium phosphate complex hydrated gel where MgNH4PO4·H2O·6H2O was the main reaction product. With the increase in hydration products, MgNH4PO4·6H2O gradually precipitated.
4.1.2 Mid-hydration. As shown in Fig. 7(b), the water in the MPC slurry was gradually consumed and evaporated with the ongoing hydration reaction accompanied by massive heat release, and the hydrated product gel tended to form an infinite 3D network structure. The temperature had exceeded 35 °C when the MPC hydration system coagulated. With sufficient hydration heat release, enough activation energy enabled the acid–base neutralization of the MPC hydration system after condensation to continue through the diffusion of reactive ions. During this process, a large amount of heat was further released, promoting the rapid temperature increase of the MPC hydration system. Low water content and high temperature was observed in the gradually hardened MPC hydration system. In addition to MgNH4PO4·6H2O, the hydration reaction also generated a number of hydration products with low-crystalline water.
4.1.3 Late hydration. As shown in Fig. 7(c), with the formation of hydration products, a large amount of these products distributed around the MgO particles and formatted the hydration product film, thereby hindering the diffusion of magnesium ions on the surface of MgO powder. The hydration reaction rate slowed down and the heat release dropped. When phosphate was completely consumed, the hydration reaction stopped. Crystals of hydration products and cores of unreacted MgO powder were connected to form a network structure, hardening the MPC system.
4.2 Retarding mechanism of glacial acetic acid
Glacial acetic acid is an organic acid, and its retardation on MPC mainly occurs in a molecular structure that is based on complex formation with –COOH. After MPC was mixed with water, soluble NH4H2PO4 was quickly dissolved in a small amount of water and transformed into acidic NH4H2PO4 saturated aqueous medium. Mg2+ is a divalent cation with a coordination number of 4, and its weak combination can form unstable complexes in an acidic environment. In the alkaline medium of cement hydration products, the carboxyl group formed an unstable complex with free Mg2+ (Fig. 8) in the early hydration control of liquid Mg2+ concentration, thereby resulting in retardation. Along with the process of hydration, the unstable complex broke down and the hydration continued normally without affecting the hydration of the cement at the later stage; thus, magnesium reaction products of glacial acetic acid and Mg2+ existed in MPC (Fig. 5). The carboxyl group easily associated with water molecules through hydrogen bonds, and the hydrogen bonded between water molecules enabled the cement powder surface to form a stable layer of solvated water, thereby preventing direct contact of the cement particles and hindering hydration (Fig. 2). At the same time, a study about the effect of pH on the cement hydration showed that the organic acid with pH value <5 can promote the early strength of cement hydration. The dissociation constant pH of glacial acetic acid is 1.8 × 10−5, which has a promotive effect on the early strength of MPC (Fig. 3).
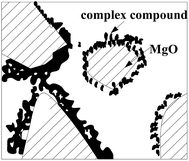 |
| Fig. 8 Schematic of glacial acetic acid retarding. | |
4.3 Choice mechanism of glacial acetic acid concentration
Condensation of MPC could be attributed to the network structure within the slurry as glacial acetic acid did not modify the final hydration products. With small amounts of acetic acid, the unstable complex content was low, thereby generating fine grain struvite after the start of hydration. This condition did not prevent the mutual movement of cement particles, and the slurry remained plastic. When the amount of hydration products increased to a sufficient number and only when crystals became flocculent or needle-shaped could the cement particles cross-link with one another to form a network structure to achieve normal condensation. If the acetic acid concentration was high, unstable complexes also increased, which was associated with corresponding increase of the struvite formation at the beginning of hydration as well as slightly faster condensation. However, crystals of hydration products generated greater internal stress in the growth process. If the acetic acid concentration was extremely high, which could be attributed to the massive crystal nuclei of hydration products generated by rapid hydration in the MPC hydration system, the small size of these crystal nuclei as well as the weak crystallinity and numerous crystal defects resulted in poor crystal stability. At the same time, the hydration products of low-bound water generated by hydration gradually absorb moisture in the air into MgNH4PO4, resulting in more cracks on the hardened MPC. This condition determined that the compressive strength would decrease after its early rapid growth. Then, along with the extension of the hydration age, the compressive strength gradually recovered and increased. Therefore, the appropriate concentration of glacial acetic acid should be the key to determine the MPC coagulation time. In identifying the optimum concentration of glacial acetic acid, the setting time should not be the exclusive consideration. The effect of setting time on the strength at different ages and the stability of cement and the hydration temperature should also be taken into account. According to above analyses, the suitable concentration of glacial acetic acid should be approximately 3%.
5. Conclusions
(1) Glacial acetic acid could affect the setting time and fluidity of MPC. The addition of glacial acetic acid delayed the setting time of the MPC cement paste, implying excellent retardation characteristics. It also increased the fluidity and thus the performance of glacial acetic acid mixed with acid cement slurry. Therefore, it is safe to conclude that glacial acetic acid could be used as a very good retarder for magnesium acetate phosphate.
(2) Glacial acetic acid affected the strength of the MPC slurry. At 3% concentration of glacial acetic acid, the compressive strength of MPC reached the maximum. Owing to the role of functional groups, glacial acetic acid contributed greatly to the early strength of MPC.
(3) By reducing the initial temperature of the MPC hydration system, the setting time of the MPC slurry was significantly prolonged. The shapes of the exotherm of hydration were different from that of the MPC slurry containing only borax, of which only a large exothermic peak appeared at the initial stage of hydration reaction. Two exothermic peaks and one induction period appeared during the hydration process, and the maximum temperature of the system decreased, thereby reducing the total hydration heat.
Conflicts of interest
There are no conflicts to declare.
Acknowledgements
Authors would like to acknowledge the Fundamental Research Funds for the Central Universities (2015XKMS011) and the Science and Technology Program of Henan Province of China (172102210393).
References
- Q. Yang, S. Zhang and X. Wu, Deicer-scaling resistance of phosphate cement-based binder for rapid repair of concrete, Cem. Concr. Res., 2002, 32, 165–168 CrossRef CAS.
- J. Jiangbo, X. Ming and W. Hongtao, Research on preparation and properties of marine magnesium phosphate cement based materials, J. Funct. Mater., 2012, 43, 828–830 Search PubMed.
- L. Zhenyu, Q. Jueshi and L. Zhongyuan, Effects of different temperature treatment to properties of magnesium phosphate cement, J. Funct. Mater., 2012, 43, 2035–2070 Search PubMed.
- L. Dongxu, L. Pengxiao and F. Chunhua, Research on water resistance of magnesium phosphate cement, J. Build. Mater., 2009, 12, 505–510 Search PubMed.
- L. Kai, J. Fan and Z. Chao, Failure mechanism of dipotassium hydrogen phosphate modified magnesia-phosphate cements under water curing condition, J. Chin. Ceram. Soc., 2012, 40, 1693–1698 Search PubMed.
- T. Michalowski and A. Pietrzyk, A thermodynamic study of stuviter + water system, Talanta, 2006, 68, 594–601 CrossRef CAS PubMed.
- J. Hongyi and C. Changming, Influence of admixtures on the dissolution rate of chloride ion in magnesia cement, Journal of Wuhan University of Technology, 2010, vol. 32, pp. 37–40 Search PubMed.
- Q. Yang, B. Zhu and X. Wu, Characteristics and durability test of magnesium phosphate cement-based material for rapid repair of concrete, Mater. Struct., 2000, 33, 229–234 CrossRef CAS.
- Q. Yang, S. Zhang and X. Wu, Deicer-scaling resistance of phosphate cement-based binder for rapid repair of concrete, Cem. Concr. Res., 2002, 32, 165–168 CrossRef CAS.
- Z. Ding, B. Dong and F. Xing, Cementing mechanism of potassium phosphate based magnesium phosphate cement, Ceram. Int., 2012, 38, 6281–6288 CrossRef CAS.
- Q. Yang, S. Zhang and X. Wu, Deicer-scaling resistance of phosphate cement-based binder for rapid repair of concrete, Cem. Concr. Res., 2002, 32, 165–168 CrossRef CAS.
- J. Jiangbo, X. Ming and W. Hongtao, Research on preparation and properties of marine magnesium phosphate cement based materials, J. Funct. Mater., 2012, 43, 828–830 Search PubMed.
- B. Yu, Z. Chen and L. Yu, Water-resisting ability of cemented broken rocks, Int. J. Min. Sci. Technol., 2016, 26, 449–454 CrossRef.
- L. Dongxu, L. Pengxiao and F. Chunhua, Research on water resistance of magnesium phosphate cement, J. Build. Mater., 2009, 12, 505–510 Search PubMed.
|
This journal is © The Royal Society of Chemistry 2017 |
Click here to see how this site uses Cookies. View our privacy policy here.