DOI:
10.1039/C7RA07578B
(Paper)
RSC Adv., 2017,
7, 46388-46394
Properties of a new renewable sesame protein adhesive modified by urea in the absence and presence of zinc oxide
Received
10th July 2017
, Accepted 12th September 2017
First published on 29th September 2017
Abstract
Sesame protein (SP) is a new renewable resource for wood adhesives because of its brilliant performance, which is non-toxic and harmless to human health during the process of using plywood. This study was focused on the application of sesame protein to produce wood adhesive via urea and zinc oxide (ZnO) modification. The pH value, solid content, apparent viscosity, bonding strength, infrared spectra, thermal stability, and fracture surface of urea-modified sesame protein adhesives in the absence of ZnO (USP) and in the presence of ZnO (ZUSP) were investigated in detail. The results suggested that the pH value and solid content of the ZUSP adhesives increased, whereas the apparent viscosity of the ZUSP adhesives showed an increasing trend when ZnO was introduced. The wet shear strength of the ZUSP adhesives improved remarkably, which achieved the required value for interior use (≥0.70 MPa), which was in accordance with the China National Standard. The infrared spectra (FTIR) indicated that the chelation reaction occurred between the USP adhesive and ZnO that improved the water resistance. The thermal stability of the ZUSP adhesives was better than that of the USP adhesive, as confirmed by the thermogravimetric analysis (TGA). After ZnO was introduced, the fracture surface of the ZUSP adhesives became more compact as compared to that of the USP adhesive, as confirmed by scanning electron microscopy. The ZUSP adhesive is a favorable potential candidate as a green-adhesive for the plywood industry, which will promote the utilization of sesame protein.
1 Introduction
Wood adhesives play a predominant role in the practical production of plywood. Currently, formaldehyde-based adhesives such as urea- (UF), phenol- (PF), and melamine-formaldehyde (MF) resins play a prominent part in the wood adhesives industry.1 These resins have huge advantages such as low price and viscosity, high bonding strength, and great water resistance, which are in fundamental demand for wood adhesives;2 however, problems, such as lack of renewability and formaldehyde emission, which are harmful to the environment and human health, associated with these resins have attracted serious concern from researchers. Therefore, these issues have generated an urgent requirement of new renewable and environmentally friendly adhesives for wood.3,4
Plant protein-based adhesives are renewable, substantial and low-cost, and this kind of wood adhesives have received increasing attention by researchers to replace the formaldehyde-based adhesives. Many researchers have investigated plant protein-based adhesives such as soy protein-based adhesive, peanut protein-based adhesive, and cotton protein-based adhesive.5–11 However, the low-water resistance and solid content of the plant protein-based adhesives have limited their application in the wood adhesive industry.12 It is essential to improve water resistance of plant protein-based adhesives to expand their application. Many chemical methods have been used to modify plant protein-based adhesives to enhance the water resistance, which can be classified into three categories: denaturing agent modification, protein molecular modification, and protein and resin blend modification.13–19
Currently, China has the largest global sesame production industry in the world. Sesame meal is a by-product of the extraction of sesame oil in sesame seeds, which is primarily used as a livestock feed and fertilizer, but this does not take full advantage of the sesame protein. Therefore, the issue of sesame protein utilization has received attention from researchers. The proteins in sesame seeds are mainly composed of globulins (67.3%), albumins (8.6%), glutelins (6.9%), and prolamins (1.4%).20 Many chemical reactions can take place in the functional groups, such as carboxyl (–COOH), hydroxyl (–OH), amino (–NH2), and thiol (–SH) groups, of the sesame protein. Therefore, sesame protein can be easily modified to change the physical properties of sesame protein-based adhesives.
Urea has been used in many fields because of its peculiar properties, which acts as a structure breaker and maker for many proteins (both fibrous and globular), micellar aggregated systems consisting of many synthetic tanning (syntans), and vegetable materials, surfactants, polymers, peptides, and emulsions, and its properties depend on many conditions such as temperature and nature of the added substrates.21–25 For plant protein adhesives, urea was widely used as a denaturing agent for modified protein because of its useful properties, which could break the structure of sesame protein and expose the inner functional groups such as –NH2, –COOH, and –OH.26 However, it was difficult for the plant protein-based adhesive modified by only this method to meet the requirement of interior use of plywood, and it could not achieve high water resistance. The bivalent metals easily form coordinated bonds, which are features of chelates. The coordinated bond, also called a complex bond, is composed of a metal and a ligand aligned in a way that the available electrons from the coordination atoms are in close proximity to those from the metal.27 Zinc oxide (ZnO) could be used to react with –NH2 of sesame protein by chelation, which could remarkably enhance the properties, such as bonding strength and water resistance, of an adhesive. Therefore, urea and zinc oxide modification could be an impactful way to prepare a sesame protein-based adhesive.
The objective of this research was to expand the utilization of sesame protein and improve the bonding strength and water resistance by modifying sesame protein with urea and zinc oxide. In this study, the physicochemical properties, including the solid content and pH value, surface structure of cured adhesives, functional groups, thermal stability, and rheological properties, of modified sesame protein-based adhesives were analyzed. Herein, a three-ply plywood was fabricated with a modified adhesive, and its dry shear strength and water resistance were tested.
2 Materials and methods
2.1 Materials
Dehulled sesame was purchased from Kangbo Huixin Oil Company (Henan, China), which was obtained by wet decortication from sesame seeds. Urea (Luoyang Reagent Company, Henan, China) and zinc oxide (ZnO, Xilong Chemical Industry Company, Fujian, China) were analytical-grade reagents. Poplar veneer (400 × 400 × 2.1 mm, 10% moisture content) was provided by the Zhengzhou Bio Biologic Materials Company (Henan, China).
2.2 Preparation of the sesame protein
2.2.1 Defatting of the dehulled sesame. Dehulled sesame was pressed by a hydraulic oil press at room temperature and milled into flours (≥40 mesh). The dehulled sesame flours were defatted by petroleum ether via soxhlet extraction for 8 h at 50 °C and dried in an oven for 2 h at 50 °C. The defatted dehulled sesame flours were used for protein extraction.
2.2.2 Extraction of sesame protein. Sesame protein was extracted using an alkali method.28 The defatted dehulled sesame flours were dispersed in deionized water (ratio 1
:
20 w/v), the pH value was adjusted to 10 using 1 M NaOH, and stirring was carried out for 3 h at 50 °C. The slurry was centrifuged at 4000 rpm for 10 min. The pH value of the supernatant was adjusted to 4.2 using 1 M HCl, and stirring was carried out for 5 min at 50 °C. The suspension was preserved at 4 °C for 20 min and then centrifuged at 4000 rpm for 10 min. The precipitates were obtained by washing twice with deionized water and adjusting the pH valur to 7.0 using 1 M NaOH and then freeze-dried. The sesame protein was milled into a powder using a ball mill. The composition of the sesame protein was analyzed according to the China National Standards (84.1% sesame protein, 3.5% moisture, 3.5% ash, 4.9% fat, 0.11% fiber, 0.08% oxalic acid, and 2.8% polysaccharide).
2.3 Preparation of the sesame protein adhesive
For the sesame protein adhesives, sesame protein (10 g) was added to the urea solution (80 mL, 3 mol L−1), and the mixture was stirred for 20 min at 25 °C. Zinc oxide (0, 4, 8, 12, 16, and 20% based on the mass of sesame protein) was added to the sesame protein adhesive, and the mixture was stirred for 220 min at 25 °C to obtain a urea-modified sesame protein adhesive (USP) and ZnO-modified sesame protein adhesive containing urea (ZUSP) (4, 8, 12, 16, and 20% ZUSP).
2.4 Solid content test
The solid content of the adhesive samples was tested by an oven-drying method. Approximately 3 g (weight β) of the adhesive was placed in an oven and dried at 105 °C for several hours until a constant weight (weight α) was achieved. The solid content value was calculated by the following eqn (1). Reported values are the average of the three parallels for each adhesive. |
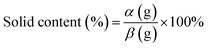 | (1) |
2.5 pH test
The pH value of the adhesive was measured by a pH meter. The pH buffers (pH value 4.00, 6.86, and 9.18) were selected according to the pH of the adhesive sample. The pH of the adhesive was tested by the electrode after calibration. The average pH value was calculated from three parallel samples.
2.6 Apparent viscosity test
The apparent viscosity of the adhesive samples was determined using a RS-6000 rheometer (Thermo Fisher scientific corporation, Waltham, MA) with a parallel plate fixture (20 mm diameter). The distance between the cone and plate was set to 1 mm for all tests. The experiments were conducted under a steady shear flow at 25 °C. The shear rates ranged from 0.01 to 100 s−1 in 10 s−1 increments. An average of three parallels was recorded as the value of the apparent viscosity of a specimen.
2.7 Preparation of a three-ply plywood
Three-ply plywood samples were prepared under the following conditions: 240 g m−2 glue spreading for a single surface, 130 °C hot pressing temperature, 1.3 MPa hot pressing pressure, and 10 min hot pressing time. The plywood samples were placed under ambient conditions for 12 h after hot pressing.
2.8 Bonding strength test
The dry shear strength and the water resistance (wet shear strength, Type II plywood, ≥0.70 MPa) of the plywood were tested according to the China National Standard GB/T 9846.3-2004. Herein, twelve plywood specimens (100 × 25 mm) cut from two plywood panels were immersed in water at 63 °C for 3 h and then placed under ambient conditions for 10 min before wet shear strength testing. The dry shear strength of the twelve plywood specimens was directly measured without the soaking treatment. The bonding strength of the plywood specimens was determined using a mechanical testing machine (CMT6203, Xin San Si Materials Company, Shenzhen, China) operating at a speed of 5.0 mm min−1. The force N required to break the glued area was determined. The bonding strength was calculated from eqn (2). The reported bonding strength data were the average of the twelve parallels for each plywood specimen. |
 | (2) |
2.9 Fourier transform infrared (FTIR) spectroscopy test
The adhesive samples were cured in an oven at 120 °C until an invariable weight was achieved and milled into a powder. The FTIR spectra of the cured adhesive samples were obtained using a Nicolet 6700 spectrometer (Thermo Nicolet Corporation, Madison, WI) in the range from 500 to 4000 cm−1 and scanned 32 times at a 8 cm−1 resolution.
2.10 Thermogravimetric (TG) measurement
The adhesive samples were cured in an oven at 120 °C until an invariable weight was achieved and milled into a powder. The thermal stabilities of the cured adhesive samples were analyzed by a TGA instrument (TA Q50, Waters Company, USA). Approximately 5 mg of the cured adhesive samples was loaded in the pan and heated from 40 to 600 °C at a rate of 10 °C min−1 under a nitrogen environment.
2.11 Scanning electron microscopy (SEM) test
The adhesive samples were cured in an oven at 120 °C until an invariable weight was achieved. The surface structure of the cured adhesive samples was observed using a QUANTA FEG 250 scanning electron microscope (FEI Company, Hillsboro, USA). The surface was sputter coated with gold prior to examining it using a microscope.
3 Results and discussion
3.1 Solid content and pH value of the sesame protein-based adhesives
Solid content is a fundamental physical parameter for a wood adhesive that influences the adhesive performance during the hot-pressing process. In general, a lower solid content in the adhesive indicates that the larger water content needs to be removed from the adhesive, which has a detrimental effect on the hot-pressing process.29 However, the exorbitant solid content of the adhesive results in a more difficultly in the coating procedure where the adhesive cannot be well-distributed; this causes a rapid decrease in the water resistance of the adhesive. The average value of the solid content of USP/ZUSP adhesives was calculated from three parallel samples and is shown in Fig. 1. The solid content of the sesame protein adhesives increased gradually from 23.46% to 25.02% when the ZnO content increased from 0 to 20%. This behavior was attributed to one reason that more addition of ZnO in ZUSP adhesives led to a high solid content.
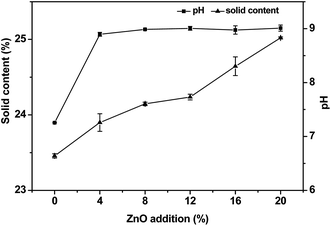 |
| Fig. 1 The solid content and pH value of the USP/ZUSP adhesives. | |
The pH of the protein adhesive is important for the production process of plywood, which can easily change the color of the wood veneer in the hot-pressing process. The pH value of the USP/ZUSP adhesives is shown in Fig. 1. The pH value of the USP adhesive was 7.26. After introducing ZnO, the pH value of the ZUSP adhesives maintained at around 9. ZnO is an alkaline substance, and the pH value increases when the addition amount of ZnO is increased from 4 to 20%.
3.2 Apparent viscosity measurement
The apparent viscosity of the USP/ZUSP adhesives is shown in Fig. 2, and the initial viscosity of the USP/ZUSP adhesives is presented in Table 1. With the shear rate increasing from 0.01 to 100 s−1, the apparent viscosity of the USP/ZUSP adhesives decreased. This phenomenon indicated that the USP/ZUSP adhesives belonged to shear thinning fluid. When the addition amount of ZnO was increased from 0 to 16%, the initial viscosity of the ZUSP adhesives decreased from 71
560 to 8520 mPa s. This behavior was due to the following reasons: urea destroyed the globular structure of the sesame protein into small molecular chain protein and led to high viscosity; the chelation reaction between ZnO and the small molecular chain protein, which formed a regular structure, decreased the viscosity of the ZUSP adhesives; and the salting-in occurred with a low concentration of ZnO decreased the viscosity of the ZUSP adhesives with the increase in the addition amount of ZnO addition from 0 to 16%. Moreover, the size of the ZUSP adhesives gradually decreased with the increase in the ZnO addition amount from 0 to 16% that was observed in SEM (Fig. 7). However, when the ZnO addition amount was increased to 20%, the viscosity of the ZUSP adhesive increased to 20
120 mPa s. This result showed that the chelation reaction between ZnO and protein was saturated, and the viscosity was increased with more ZnO addition. However, the adhesive with a high viscosity would decrease the flowability; this would cause more difficultly in the coating process.2 Therefore, the addition amount of ZnO should not be too high.
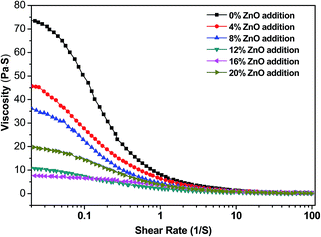 |
| Fig. 2 Apparent viscosity of the USP/ZUSP adhesives. | |
Table 1 The initial viscosity of the USP/ZUSP adhesive
ZnO addition (%) |
0 |
4 |
8 |
12 |
16 |
20 |
Initial viscosity (mPa s) |
71 560 |
45 730 |
36 950 |
11 200 |
8520 |
20 120 |
3.3 Bonding strength of the sesame protein-based adhesives
The bonding strength of the USP/ZUSP adhesives is shown in Fig. 3. For the USP adhesive (0% ZnO), the dry shear strength was 1.37 MPa. As the ZnO addition amount increased from 4 to 12%, the dry shear strength increased from 2.11 MPa to 2.47 MPa, which increased from 54.0% to 80.3% compared with the USP adhesive. Upon further increasing the ZnO addition amount to 20%, the dry shear strength decreased by 11.3% to 2.19 MPa as compared to 12% for the ZUSP adhesive, but was still better than that of the USP adhesive. The wet shear strength of the USP adhesive without ZnO was 0.40 MPa, which failed to achieve the required value for interior use (≥0.70 MPa) in accordance with the China National Standard (GB/T 9843.3-2004). This behavior was attributed to one reason. Urea is a denaturing agent that can break the secondary structure of the sesame protein via the reaction between the oxygen and hydrogen atoms of urea and hydroxyl group of protein, which breaks down the hydrogen bonding of protein and forms a much small molecular chain protein; this leads to low water resistance of the USP adhesive. As shown in Fig. 1, the wet shear strength of the ZUSP adhesive with 4% ZnO increased by 97.5% to 0.79 MPa, which reached the required value for interior use. By increasing the content of ZnO to 8%, the wet shear strength of the ZUSP adhesive increased by 152.5% and reached a maximum value of 1.01 MPa. Upon further increasing the content of ZnO in the adhesives, the wet shear strength of the ZUSP adhesive with 20% ZnO decreased by 37.6% to 0.63 MPa, which failed to achieve the required value for interior use as compared to 8% for the ZUSP adhesive. These behaviors were attributed to the following reasons. The chelation between zinc ion and –NH2 of the sesame protein might be the main reason for the improvement of the water resistance, which acted as a bridge to connect ZnO and protein like a network structure that prevented moisture intrusion. However, increase in the content of ZnO from 12 to 20% did not further enhance the wet shear strength of the ZUSP adhesive because of the excessive addition of ZnO. Therefore, the adhesive with a high solid content and low viscosity would lead to an over-penetration into the wood and low water resistance.
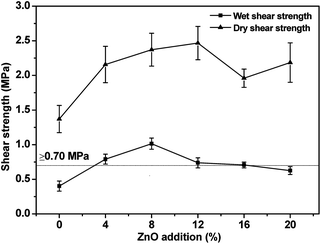 |
| Fig. 3 Bonding strength of the USP/ZUSP adhesives. | |
3.4 FTIR spectroscopy measurement
The FTIR spectra of the USP/ZUSP adhesives is shown in Fig. 4. The peaks observed at 3448 and 3352 cm−1 were attributed to the bending vibrations of free and bound O–H and N–H groups, which could form hydrogen bonds with the carbonyl group of the peptide linkage in the protein, respectively; this was confirmed by Mandal, A. B. by examining NMR experiments through the plots of changes in the chemical shifts as a function of temperature.30 The key absorption peaks of the USP/ZUSP adhesives were located at 1668 and 1624 cm−1, which were characteristic of amide I (C
O stretching) and amide II (N–H bending), respectively. The bands corresponding to –CH bending and –C–O–C– stretching were 1452 and 1161 cm−1, respectively. However, a new absorption peak was observed at 2215 cm−1 in the FTIR spectra of the ZUSP adhesives, which could be attributed to the stretching vibration of the ring structure. The result showed that chelation reaction occurred between USP adhesive and ZnO. With the increase in the addition amount of ZnO from 0 to 20% in the adhesive, the peak observed at 2215 cm−1 gradually increased; this was due to the chelation reaction between ZnO and the –NH2 groups and –COOH groups of the sesame protein molecules. The sesame protein with two or more donor atoms (called polydents) could bind with a zinc ion within its electronic dents or claws by electron sharing between zinc ion and ligand (–NH2, –COOH) and form a stable ring structure that improved the water resistance. The likely reaction mechanism is presented in Fig. 5.
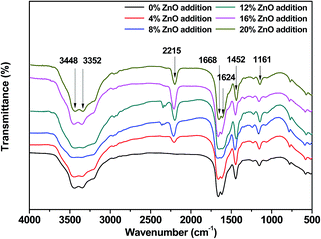 |
| Fig. 4 FTIR spectra of the USP/ZUSP adhesives. | |
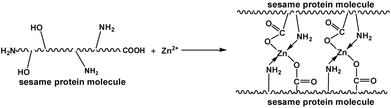 |
| Fig. 5 The reaction process between the sesame protein and zinc oxide. | |
3.5 TG analysis
The thermogravimetric (TG) and derivative thermogravimetric (DTG) curves of the cured USP/ZUSP adhesives are shown in Fig. 6. The thermal degradation process of the cured adhesives could be divided into four stages. In the first stage (I), the evaporation of residual moisture in the cured adhesives resulted in a small weight loss in the temperature range from 40 °C to 145 °C. The second stage (II) was related to the degradation of small molecules from sesame protein that were broken by urea and the breakage of unstable chemical bond in the temperature range from 145 °C to 250 °C. Compared with the ZUSP adhesives, the USP adhesive showed a strong peak (derivative weight) in the second stage, and the residual weight of the USP adhesive in stage (II) was 49.2% that was less than that of the ZUSP adhesives with 4–20% added amount of ZnO (51.9, 58.4, 58.3, 62.1, and 66.3%); this indicated that the process of urea modification produced more unstable chemical bonds and small molecules that presented a low water resistance. The third stage (III) was associated with the decomposition of the skeleton structure of the sesame protein in the temperature range from 250 °C to 370 °C. During this stage, the protein backbone was absolutely decomposed and released all kinds of gases including CO2, CO, and NH3.31 The peak (derivative weight) in stage (III) decreased with the increasing ZnO addition amount in ZUSP adhesives; this indicated that the main structure of the ZUSP adhesive changed as the ZnO addition amount increased. With an increase in the ZnO addition amount from 4 to 20% in the ZUSP adhesives, the final weight loss in stage (III) increased from 25.9% to 41.6%. The fourth stage (IV) was attributed to the decomposition of the cross-linking substance (the ring structure) between the –NH2 from the sesame protein and zinc ion with chelation in the temperature range from 370 °C to 540 °C. Longtime urea modification could unfold sesame protein structure and expose more active groups such as –NH2 and –COOH, which were responsible for the chelation reaction. The ring structure formed by the chelation reaction has high thermal stability that improves water resistance. In this stage, the thermal degradation behavior showed a significant difference with and without ZnO. The ZUSP adhesives had a weak peak (derivative weight) in this stage as compared to the USP adhesive, which had higher water resistance than the USP adhesive because of chelation. Finally, the residual weight of the adhesive with an increase in the ZnO addition amount from 0 to 20% was 11.9, 16.3, 21.8, 23.0, 28.1, and 28.7%, which indicated a better thermal stability of the ZUSP adhesive with the formation of nanomaterials.
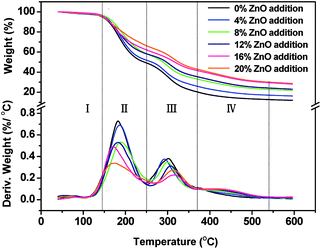 |
| Fig. 6 The thermogravimetric (TG) and derivative thermogravimetric (DTG) curves of the USP/ZUSP adhesives. | |
3.6 SEM analysis
The fracture surface of the cured USP/ZUSP adhesives observed by scanning electron microscopy is presented in Fig. 7; the fracture surface of the cured USP adhesive (0% ZnO) had a large number of holes and cracks and it also appeared very loose and disordered due to moisture vaporization during the hot-press process. Thus, the water resistance of the USP adhesive was low as compared to that of the ZUSP adhesives. After ZnO was introduced, the holes and cracks disappeared and the fractured surface of the cured ZUSP adhesives was more compact. These results showed that ZnO might fill the holes and cracks of the USP adhesive and cause the chelation reaction between itself and the USP adhesive that effectively prevented moisture penetration to improve the water resistance. In the ZUSP adhesive with 8% added amount of ZnO, the fracture surface was ordered and rough such that it could easily combine with the rough surface of wood specimens, and this behavior resulted in high water resistance as compared to that of other ZUSP adhesives. With an increase in the ZnO addition amount to 20%, the fracture surface of the cured adhesive was smoother than that of other cured ZUSP adhesives; this decreased the bonding capacity between adhesive and wood specimens, but it was still better than that of the USP adhesive. Therefore, ZnO improved the water resistance of the ZUSP adhesive.
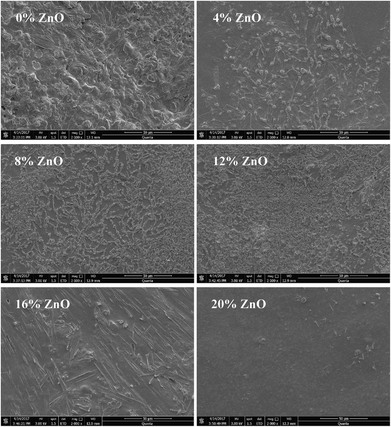 |
| Fig. 7 SEM image of the fracture surface of the cured USP/ZUSP adhesives. | |
4 Conclusions
The solid content of ZUSP adhesives gradually increased and the pH value maintained at around 9 when ZnO was added; the apparent viscosity of the ZUSP adhesives showed an increasing trend. In view of wet shear strength, the optimum addition amount of ZnO was 8%. The wet shear strength of the ZUSP adhesives remarkably increased when ZnO was introduced. The wet shear strength of the ZUSP adhesive with 8% ZnO increased by 152.5% as compared to that of the USP adhesive, which achieved the required value for interior use (≥0.70 MPa) in accordance with the China National Standard (GB/T 9843.3-2004). Based on the FTIR spectra, the chelation reaction occurred between the USP adhesive and ZnO that might improve the water resistance. The TGA showed that the thermal stability of the ZUSP adhesives was better than that of the USP adhesive. The SEM images suggested that the fracture surface of the ZUSP adhesive was more compact as compared to that of the USP adhesive. Our research results suggest that the sesame protein extracted from sesame meal would be a new renewable material to be used as a low-cost and high-performance adhesive in the plywood industry.
Conflicts of interest
There are no conflicts to declare.
Acknowledgements
The authors are grateful for fund from Modern Agro-industry Technology Research System (CARS14-1-29).
Notes and references
- J. Luo, J. Luo, Q. Gao and J. Li, Ind. Crops Prod., 2015, 63, 281–286 CrossRef CAS.
- H. Li, C. Li, Q. Gao, S. Zhang and J. Li, Ind. Crops Prod., 2014, 59, 35–40 CrossRef CAS.
- P. Nordqvist, M. Lawther, E. Malmström and F. Khabbaz, Ind. Crops Prod., 2012, 38, 139–145 CrossRef CAS.
- A. Pizzi, J. Adhes. Sci. Technol., 2006, 20, 829–846 CrossRef CAS.
- F. Eslah, M. Jonoobi, M. Faezipour, M. Afsharpour and A. A. Enayati, Int. J. Adhes. Adhes., 2016, 71, 48–54 CrossRef CAS.
- H. Lei, Z. Wu, M. Cao and G. Du, Polymers, 2016, 8, 256 CrossRef.
- G. Qi, N. Li, D. Wang and X. S. Sun, J. Am. Oil Chem. Soc., 2016, 93, 1509–1517 CrossRef CAS.
- J. Li, X. Li, J. Li and Q. Gao, RSC Adv., 2015, 5, 80136–80141 RSC.
- H. N. Cheng, C. Ford, M. K. Dowd and Z. He, Ind. Crops Prod., 2016, 85, 324–330 CrossRef CAS.
- H. N. Cheng, C. Ford, M. K. Dowd and Z. He, Int. J. Adhes. Adhes., 2016, 68, 156–160 CrossRef CAS.
- Z. He, D. C. Chapital and H. N. Cheng, J. Appl. Polym. Sci., 2016, 133, 43637–43643 Search PubMed.
- H. Liu, C. Li and X. S. Sun, Ind. Crops Prod., 2015, 74, 577–584 CrossRef CAS.
- N. S. Hettiarachchy, U. Kalapathy and D. J. Myers, J. Am. Oil Chem. Soc., 1995, 72, 1461–1464 CrossRef CAS.
- W. Huang and X. Sun, J. Am. Oil Chem. Soc., 2000, 77, 705–708 CrossRef CAS.
- W. Huang and X. Sun, J. Am. Oil Chem. Soc., 2000, 77, 101–104 CrossRef CAS.
- J. Luo, J. Luo, C. Yuan, W. Zhang, J. Li, Q. Gao and H. Chen, RSC Adv., 2015, 5, 100849–100855 RSC.
- G. Qi, N. Li, D. Wang and X. S. Sun, Ind. Crops Prod., 2013, 46, 165–172 CrossRef CAS.
- J. Luo, X. Li, H. Zhang, Q. Gao and J. Li, Int. J. Adhes. Adhes., 2016, 71, 99–104 CrossRef CAS.
- Z. Zhong and X. S. Sun, J. Biobased Mater. Bioenergy, 2007, 1, 380–387 CrossRef.
- R. Nilo Rivas, J. E. Dench and J. C. Caygill, J. Sci. Food Agric., 1981, 32, 565–571 CrossRef CAS.
- A. B. Mandal, S. Ray, A. M. Biswas and S. P. Moulik, J. Phys. Chem., 1980, 84, 856–859 CrossRef CAS.
- A. B. Mandal, D. Mukherjee and D. Ramaswamy, Leather Sci., 1983, 28, 283–288 Search PubMed.
- A. B. Mandal, D. Ramaswamy, D. K. Das and M. Santapp, Colloid Polym. Sci., 1982, 260, 702–707 CAS.
- A. B. Mandal, M. Kanthimathi, K. Govindaraju and D. Ramaswamy, J. Soc. Leather Technol. Chem., 1983, 67, 147–158 CAS.
- C. Rose and A. B. Mandal, Int. J. Biol. Macromol., 1996, 18, 41–53 CrossRef CAS PubMed.
- X. Sun and B. Ke, J. Am. Oil Chem. Soc., 1999, 76, 977–980 CrossRef CAS.
- S. L. Vieira, Rev. Bras. Cienc. Avic., 2008, 10, 73–79 CrossRef.
- E. Onsaard, P. Pomsamud and P. Audtum, As. J. Food Ag-Ind., 2013, 3, 420–431 Search PubMed.
- Q. Gao, J. Li, S. Q. Shi, K. Liang and X. Zhang, BioResources, 2012, 7, 5622–5633 Search PubMed.
- A. B. Mandal and R. Jayakumar, J. Chem. Soc., Faraday Trans., 1994, 90, 161–165 RSC.
- S. N. Das, M. Routray and P. L. Nayak, Polym.-Plast. Technol. Eng., 2008, 47, 576–582 CrossRef CAS.
|
This journal is © The Royal Society of Chemistry 2017 |
Click here to see how this site uses Cookies. View our privacy policy here.