DOI:
10.1039/C7RA06486A
(Paper)
RSC Adv., 2017,
7, 40705-40710
High-flux polyamide reverse osmosis membranes by surface grafting 4-(2-hydroxyethyl)morpholine
Received
10th June 2017
, Accepted 14th August 2017
First published on 21st August 2017
Abstract
Surface modification is a common approach to improve the desalination performance of polyamide (PA) reverse osmosis (RO) membranes. Nevertheless, the water flux normally decreases due to the additional hydraulic resistance of the surface modification layer. Surface grafted PA RO membrane with 4-(2-hydroxyethyl)morpholine was first fabricated to improve water flux in this study. 4-(2-Hydroxyethyl)morpholine was in situ grafted onto the nascent PA membrane by the reaction between the –OH group of 4-(2-hydroxyethyl)morpholine and the unreacted –COCl groups of the nascent PA membrane and residual trimesoyl chloride. The surface grafted RO membranes were characterized by X-ray photoelectron spectrometry, field emission scanning electron microscopy, atomic force microscopy and contact angle measurement. The surface grafting conditions, including 4-(2-hydroxyethyl)morpholine dipping time, heat treatment time, and 4-(2-hydroxyethyl)morpholine concentration, were optimized by characterizing the desalination performance under brackish water desalination conditions. The resulting surface grafted membrane exhibited a water flux of 125.71 L m−2 h−1 and a salt rejection of 98.6%. The surface grafted membrane surpassed the control polyamide membrane with 41.9% increase in the water flux. Our results demonstrated that surface modification by in situ grafting 4-(2-hydroxyethyl)morpholine is a promising approach to fabricate high-flux RO membranes.
1 Introduction
At present, reverse osmosis (RO) is the most promising desalination technology.1 Polyamide (PA) thin film composite (TFC) membranes are widely applied in the commercial RO membrane market.2 The traditional PA TFC RO membrane is most often fabricated by interfacial polymerization between m-phenylenediamine and trimesoyl chloride.3 However, the inadequate hydrophilicity and highly cross-linked structure of such PA TFC RO membrane essentially limited desalination performance.4–6 Thus, many studies have been devoted to improving the desalination performance of PA TFC RO membrane over the past decades.7–15
The modification of PA TFC RO membrane by surface coating or grafting could be applied successfully due to easy integration into the existing RO membrane manufacturing process.16–25 A series of PEG-based hydrogels were applied as coatings to PA TFC RO membrane by Sagle et al.26 The coated membranes exhibited improved antifouling performance, with a loss of water flux. Bernstein et al. modified low pressure RO membrane by concentration polarization enhanced radical graft polymerization using different monomers.27,28 The boron removal performance was improved owing to sealing the defects of RO membrane by surface modification. The PA TFC RO membrane functionalized with graphene oxide was fabricated by Perreault et al.29 Graphene oxide functionalization improved the antimicrobial performance significantly. Yang et al. grafted and deposited pyridine-based zwitterionic copolymers onto TFC RO membranes via initiated chemical vapor deposition.30 The antifouling performance and chlorine stability were improved by ultrathin zwitterionic coatings. The aforementioned studies demonstrated that surface modification was an effective method to improve the salt rejection and antifouling performance of PA TFC RO membrane. However, the water flux normally decreased due to the additional hydraulic resistance of surface modification layer.3
4-(2-Hydroxyethyl)morpholine contains a hydrophilic morpholine portion and the reactive –OH group which can react with TMC during the IP process. Zhao et al. fabricated the high-flux RO membrane by incorporating 4-(2-hydroxyethyl)morpholine as hydrophilic additive into the amine solution during the IP process.5 The water flux was enhanced significantly. However, the majority of 4-(2-hydroxyethyl)morpholine was embedded in the PA bulk.3
Herein, for the first time, the surface grafted PA RO membrane with 4-(2-hydroxyethyl)morpholine was fabricated to improve water flux. 4-(2-Hydroxyethyl)morpholine was in situ grafted onto the nascent PA membrane by the reaction between the –OH group of 4-(2-hydroxyethyl)morpholine and the unreacted –COCl groups of nascent PA membrane and residual trimesoyl chloride during the RO membrane preparation process (Fig. 1). The surface grafted RO membranes were characterized by X-ray photoelectron spectrometer, field emission scanning electron microscopy, atomic force microscopy and contact angle goniometer. Finally, the surface grafting conditions, including 4-(2-hydroxyethyl)morpholine dipping time, heat treatment time, and 4-(2-hydroxyethyl)morpholine concentration, were optimized by characterizing the desalination performance of surface modified PA RO membranes.
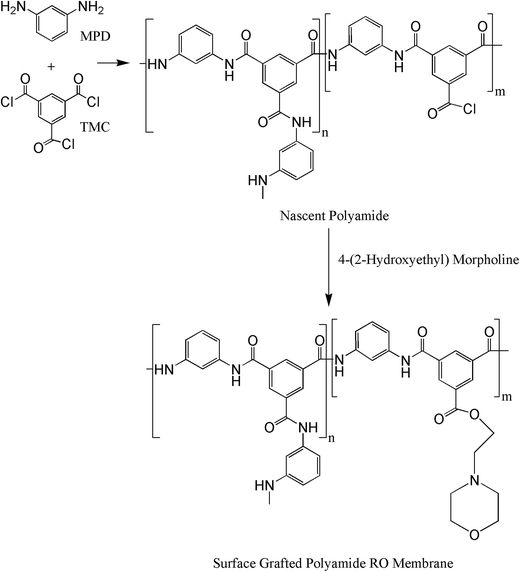 |
| Fig. 1 Grafting reactions of 4-(2-hydroxyethyl)morpholine onto the nascent polyamide membrane. | |
2 Experimental section
2.1 Materials
m-Phenylenediamine (MPD), (±)-camphor-10-sulfonic acid (CSA), trimethylamine (TEA) and 4-(2-hydroxyethyl)morpholine were purchased from Aladdin (Shanghai, China). Trimesoyl chloride (TMC) was received from TCI (Shanghai, China). Isopar G was obtained from ExxonMobil Chemical (Shanghai, China). Isopropanol (IPA) and sodium chloride (NaCl) were purchased from Sinopharm (Shanghai, China).
2.2 Preparation of surface grafted PA TFC RO membrane
The schematic diagram for fabrication process of surface grafted membrane was shown in Fig. 2. The polysulfone support was first immersed in an amine aqueous solution containing 2 wt% MPD and 5 wt% CSA–TEA salt for 6 min. After removing the excess amine droplets by tissue papers, a 0.1 wt% TMC/Isopar G solution was poured onto the amine saturated support to react for 20 s. The excess TMC solution was then drained by standing vertically for 1 min. Next, the nascent PA membrane was immediately soaked in a 0.5–2 wt% 4-(2-hydroxyethyl)morpholine in IPA solution of pH 9.5 adjusted with TEA for 10–50 s. Finally, the membrane was cured in the oven at 90 °C for 4–8 min.
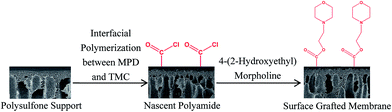 |
| Fig. 2 Schematic diagram for the fabrication process of surface grafted membrane. | |
With the exception of the 4-(2-hydroxyethyl)morpholine dipping step, the preparation process of control PA membrane without IPA solution treatment is identical to that of surface grafted membrane. In addition, the PA membrane only treated by IPA solution without 4-(2-hydroxyethyl)morpholine was also prepared under the same preparation conditions.
2.3 Characterization of surface grafted PA TFC RO membrane
The successful grafting of 4-(2-hydroxyethyl)morpholine on membrane surface was examined by X-ray photoelectron spectrometer (XPS, ESCALAB 250). The membrane morphologies were assessed by field emission scanning electron microscopy (FESEM, HITACHI S-4800) and atomic force microscopy (AFM, Agilent 5500). The contact angles of both control polyamide membrane and surface grafted membrane were measured by contact angle goniometer (Krüss DSA 30).
The feed solution of 2000 ppm NaCl was used to evaluate the water flux and salt rejection in a cross-flow stainless steel cell (Sterlitech) under 1.55 MPa at room temperature. The membrane with an active area of 42 cm2 were compacted for 3 h to reach the steady state. After that, the water flux and salt rejection were determined, according to the reported method in the literature.4–6 All the water flux and salt rejection results are the average values of at least three membrane samples.
3 Results and discussion
3.1 Characterization of surface grafted membrane
The elemental composition of membrane surface was analyzed by XPS. The oxygen-to-carbon (O/C) ratio of 4-(2-hydroxyethyl)morpholine (1/3) is higher than that of control polyamide membrane (0.165), thus the oxygen-to-carbon (O/C) ratio of surface grafted membrane is expected to be increased. As presented in Table 1, the O/C ratio of surface grafted membranes increased with the increase in 4-(2-hydroxyethyl)morpholine concentration. The grafting degree of surface grafted membranes with 0.5%, 1.0%, 1.5% and 2.0% 4-(2-hydroxyethyl)morpholine concentration was 15.8%, 22.4%, 32.1% and 37.6%, respectively. The XPS analysis verified successful grafting of 4-(2-hydroxyethyl)morpholine on membrane surface.
Table 1 Relative surface atomic concentration of the control polyamide membrane and surface grafted membrane with different 4-(2-hydroxyethyl)morpholine concentration
Sample |
Atoms percent (mol%) |
O/C |
C/N |
Grafting degree (%) |
C |
O |
N |
Control polyamide |
75.07 |
12.36 |
12.58 |
0.165 |
5.97 |
0 |
Surface grafted membrane-0.5 |
73.84 |
14.08 |
12.09 |
0.191 |
6.11 |
15.8 |
Surface grafted membrane-1.0 |
73.39 |
14.83 |
11.78 |
0.202 |
6.23 |
22.4 |
Surface grafted membrane-1.5 |
72.68 |
15.82 |
11.50 |
0.218 |
6.32 |
32.1 |
Surface grafted membrane-2.0 |
72.27 |
16.42 |
11.31 |
0.227 |
6.39 |
37.6 |
The effects of surface grafting on membrane morphologies were investigated by SEM and AFM. The SEM images of both membrane surface and cross section morphology are shown in Fig. 3. The ridge-and-valley structure was observed in both control polyamide membrane and surface grafted membrane. However, the thickness of surface grafted membrane decreased. In the previously reported literature,31,32 n-hexane solution was used to wash away the residual reagents of nascent PA membrane surface during the fabrication process. Likewise, some residual reagents on nascent PA membrane surface were washed away by the IPA modification solution. Therefore, the thickness of the active layer of the modified membrane was thinner than that of the control PA membrane.
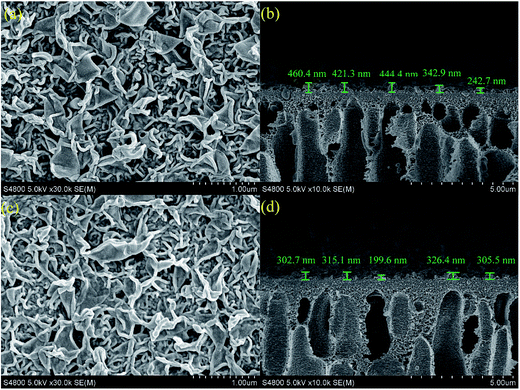 |
| Fig. 3 SEM images for (a) the surface of control polyamide membrane, (b) the cross section of control polyamide membrane, (c) the surface of surface grafted membrane with 0.5 wt% 4-(2-hydroxyethyl)morpholine and (d) the cross section of surface grafted membrane with 0.5 wt% 4-(2-hydroxyethyl)morpholine. | |
The surface roughness of both control polyamide membrane and surface grafted membrane with 0.5 wt% 4-(2-hydroxyethyl)morpholine was measured by AFM. As shown in Fig. 4, the mean roughness (Ra) decreased from 45.4 nm for control polyamide membrane to 24.9 nm for surface grafted membrane with 0.5 wt% 4-(2-hydroxyethyl)morpholine. The AFM results demonstrated the membrane surface was smoothened by surface grafting 4-(2-hydroxyethyl)morpholine.
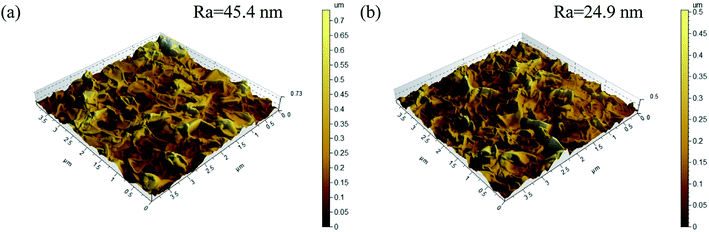 |
| Fig. 4 AFM images of (a) control polyamide membrane and (b) surface grafted membrane with 0.5 wt% 4-(2-hydroxyethyl)morpholine. | |
The membrane surface hydrophilicity was assessed by water contact angle. As presented in Fig. 5, the water contact angle of control PA membrane was 90.7°, which is consistent with the contact angle value of hand-cast PA membranes reported in the literature.33,34 After surface grafting 4-(2-hydroxyethyl)morpholine, the water contact angle reduced to 81.8°. The relatively hydrophilic 4-(2-hydroxyethyl)morpholine grafted onto the PA surface was responsible for the increased hydrophilicity.
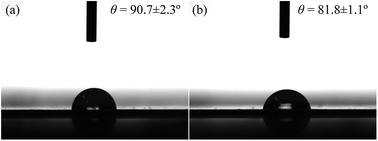 |
| Fig. 5 Water contact angle of (a) control polyamide membrane and (b) surface grafted membrane with 0.5 wt% 4-(2-hydroxyethyl)morpholine. | |
3.2 Effects of 4-(2-hydroxyethyl)morpholine concentration on desalination performance
The effects of 4-(2-hydroxyethyl)morpholine concentration on desalination performance were depicted in Fig. 6. The flux was improved considerably from 88.57 L m−2 h−1 for control PA membrane to 125.71 L m−2 h−1 for surface grafted membrane with 0.5 wt% 4-(2-hydroxyethyl)morpholine (15.8% grafting degree), while the salt rejection changed slightly from 98.8% to 98.6%. As presented in Table 1, the carbon-to-nitrogen (C/N) ratio increased by surface grafting 4-(2-hydroxyethyl)morpholine. The increase of C/N ratios suggests less cross-linking for surface grafted membrane,35,36 thus more free volume was created. Moreover, the membrane hydrophilicity was improved and the membrane thickness was reduced by surface grafting. Therefore, the water flux increased significantly. However, with further increase in 4-(2-hydroxyethyl)morpholine concentration, the flux decreased due to the additional hydraulic resistance of surface grafting layer. As a result, 0.5% was determined as the optimal 4-(2-hydroxyethyl)morpholine concentration.
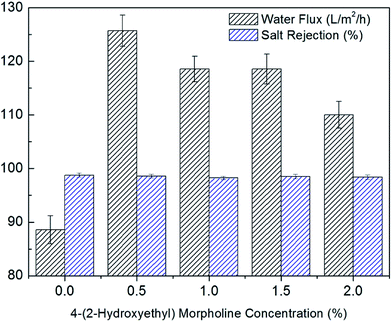 |
| Fig. 6 Effects of 4-(2-hydroxyethyl)morpholine concentration on desalination performance (20 s dipping time and 6 min heat treatment time). | |
3.3 Effects of 4-(2-hydroxyethyl)morpholine dipping time on desalination performance
The effects of 4-(2-hydroxyethyl)morpholine dipping time on desalination performance were investigated. As shown in Fig. 7, the flux increased from 117.14 L m−2 h−1 for 10 s dipping time to 125.71 L m−2 h−1 for 20 s dipping time, while the salt rejection changed slightly. A longer 4-(2-hydroxyethyl)morpholine dipping time allows more –OH group of 4-(2-hydroxyethyl)morpholine to react with the –COCl group of nascent PA membrane, which creates more free volume and increases the membrane hydrophilicity. Therefore, the water flux increased. However, the flux decreased by further increasing dipping time. The flux decrease was attributed to the additional hydraulic resistance of surface grafting layer. As a result, 20 s was selected as the optimal 4-(2-hydroxyethyl)morpholine dipping time.
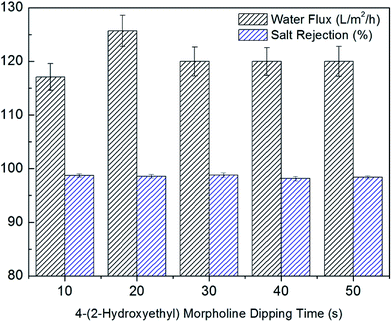 |
| Fig. 7 Effects of 4-(2-hydroxyethyl)morpholine dipping time on desalination performance (6 min heat treatment time and 0.5 wt% 4-(2-hydroxyethyl)morpholine). | |
3.4 Effects of heat treatment time on desalination performance
Heat treatment was used to promote the additional cross-linking reactions and expedite the complete removal of Isopar G and IPA.37 The effects of heat treatment time on desalination performance were shown in Fig. 8. The optimal flux was received as the heat treatment was 6 min. The surface grafted membrane showed a water flux of 125.71 L m−2 h−1 and a salt rejection of 98.6%. When the heat treatment was less than 6 min, the cross-linking reactions were not complete. After 6 min, the polysulfone support was destroyed and the water flux decreased.37,38 As a result, 6 min was selected as the optimal heat treatment time.
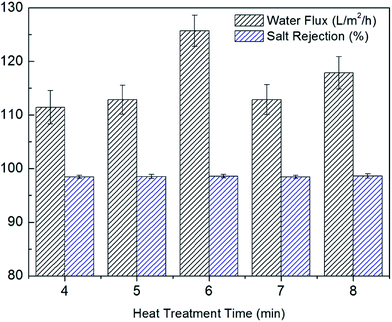 |
| Fig. 8 Effects of heat treatment time on desalination performance (20 s dipping time and 0.5 wt% 4-(2-hydroxyethyl)morpholine). | |
3.5 Effect of IPA on desalination performance
The PA membrane only treated by IPA solution without 4-(2-hydroxyethyl)morpholine showed a water flux of 102.86 L m−2 h−1 and a salt rejection of 97.9%. The PA membrane only treated by IPA solution surpassed the control polyamide membrane with 16.1% increase in the water flux. However, the salt rejection decreased dramatically from 98.8% to 97.9%. Some residual reagents on nascent PA membrane surface were washed away by IPA solution, thus the water flux increased and salt rejection decreased. In addition, surface grafted membrane with 0.5 wt% 4-(2-hydroxyethyl)morpholine surpassed the PA membrane only treated by IPA solution with 22.2% increase in the water flux, while the salt rejection increased significantly from 97.9% to 98.6%. Compared to IPA solution without 4-(2-hydroxyethyl)morpholine, the IPA solution with 4-(2-hydroxyethyl)morpholine provided not only hydrophilicity for improving water flux but also charge repulsion for enhancing salt rejection.
4 Conclusions
The novel surface grafted PA RO membrane with significantly improved water flux was successfully fabricated. The successful grafting of 4-(2-hydroxyethyl)morpholine on membrane surface was confirmed by XPS. The membrane surface roughness decreased due to surface grafting 4-(2-hydroxyethyl)morpholine, while the surface hydrophilicity increased. The surface grafting conditions, including 4-(2-hydroxyethyl)morpholine dipping time, heat treatment time, and 4-(2-hydroxyethyl)morpholine concentration, were optimized. The resulting surface grafted membrane showed a water flux of 125.71 L m−2 h−1 and a salt rejection of 98.6%. The surface grafted membrane surpassed the control polyamide membrane with 41.9% increase in the water flux.
Conflicts of interest
There are no conflicts to declare.
Acknowledgements
The authors thank the reviewers for their valuable comments. We acknowledge the National Natural Science Foundation of China (Grant No. 51408581), Natural Science Foundation of Fujian Province (Grant No. 2016J05143), Bureau of International Cooperation, CAS (132C35KYSB20160018) and Bureau of Frontier Sciences & Education, CAS (QYZDB-SSW-DQC044) for the financial support of this work.
References
- M. Elimelech and W. A. Phillip, Science, 2011, 333, 712–717 CrossRef CAS PubMed.
- B. Khorshidi, T. Thundat, B. A. Fleck and M. Sadrzadeh, RSC Adv., 2015, 5, 54985–54997 RSC.
- D. Li, Y. Yan and H. Wang, Prog. Polym. Sci., 2016, 61, 104–155 CrossRef CAS.
- L. Zhao, P. C.-Y. Chang, C. Yen and W. S. W. Ho, J. Membr. Sci., 2013, 425–426, 1–10 CAS.
- L. Zhao, P. C.-Y. Chang and W. S. W. Ho, Desalination, 2013, 308, 225–232 CrossRef CAS.
- L. Zhao and W. S. W. Ho, J. Membr. Sci., 2014, 455, 44–54 CrossRef CAS.
- S. S. Shenvi, A. M. Isloor and A. F. Ismail, Desalination, 2015, 368, 10–26 CrossRef CAS.
- W. J. Lau, S. Gray, T. Matsuura, D. Emadzadeh, J. P. Chen and A. F. Ismail, Water Res., 2015, 80, 306–324 CrossRef CAS PubMed.
- D. Li and H. Wang, J. Mater. Chem., 2010, 20, 4551–4566 RSC.
- H. J. Kim, M. Y. Lim, K. H. Jung, D. G. Kim and J. C. Lee, J. Mater. Chem. A, 2015, 3, 6798–6809 CAS.
- B.-H. Jeong, E. M. V. Hoek, Y. Yan, A. Subramani, X. Huang, G. Hurwitz, A. K. Ghosh and A. Jawor, J. Membr. Sci., 2007, 294, 1–7 CrossRef CAS.
- H. Huang, X. Qu, X. Ji, X. Gao, L. Zhang, H. Chen and L. Hou, J. Mater. Chem. A, 2013, 1, 11343–11349 CAS.
- T. Wang, L. Dai, Q. Zhang, A. Li and S. Zhang, J. Membr. Sci., 2013, 440, 48–57 CrossRef CAS.
- L.-F. Liu, Z.-B. Cai, J.-N. Shen, L.-X. Wu, E. M. V. Hoek and C.-J. Gao, J. Membr. Sci., 2014, 469, 397–409 CrossRef CAS.
- K. P. Lee, T. C. Arnot and D. Mattia, J. Membr. Sci., 2011, 370, 1–22 CrossRef CAS.
- V. Kochkodan and N. Hilal, Desalination, 2015, 356, 187–207 CrossRef CAS.
- J. Mansouri, S. Harrisson and V. Chen, J. Mater. Chem., 2010, 20, 4567–4586 RSC.
- D. Rana and T. Matsuura, Chem. Rev., 2010, 110, 2448–2471 CrossRef CAS PubMed.
- J. Wu, Z. Wang, W. Yan, Y. Wang, J. Wang and S. Wang, J. Membr. Sci., 2015, 496, 58–69 CrossRef CAS.
- J. Wang, Z. Wang, J. Wang and S. Wang, J. Membr. Sci., 2015, 493, 188–199 CrossRef CAS.
- G. Ye, J. Lee, F. Perreault and M. Elimelech, ACS Appl. Mater. Interfaces, 2015, 7, 23069–23079 CAS.
- W. Ma, A. Soroush, T. V. A. Luong, G. Brennan, M. S. Rahaman, B. Asadishad and N. Tufenkji, Water Res., 2016, 99, 188–199 CrossRef CAS PubMed.
- H. Li, L. Peng, Y. Luo and P. Yu, RSC Adv., 2015, 5, 98566–98575 RSC.
- J. S. Louie, I. Pinnau and M. Reinhard, J. Membr. Sci., 2011, 367, 249–255 CrossRef CAS.
- Q. Zhang, C. Zhang, J. Xu, Y. Nie, S. Li and S. Zhang, Desalination, 2016, 379, 42–52 CrossRef CAS.
- A. C. Sagle, E. M. V. Wagner, H. Ju, B. D. McCloskey, B. D. Freeman and M. M. Sharma, J. Membr. Sci., 2009, 340, 92–108 CrossRef CAS.
- R. Bernstein, S. Belfer and V. Freger, Environ. Sci. Technol., 2011, 45, 3613–3620 CrossRef CAS PubMed.
- R. Bernstein, S. Belfer and V. Freger, Environ. Sci. Technol., 2011, 45, 5973–5980 CrossRef CAS PubMed.
- F. Perreault, M. E. Tousley and M. Elimelech, Environ. Sci. Technol. Lett., 2014, 1, 71–76 CrossRef CAS.
- R. Yang, H. Jang, R. Stocker and K. K. Gleason, Adv. Mater., 2014, 26, 1711–1718 CrossRef CAS PubMed.
- J. Hu, Z. Lv, Y. Xu, X. Zhang and L. Wang, J. Membr. Sci., 2016, 505, 119–129 CrossRef CAS.
- J. Hu, Y. Pu, M. Ueda, X. Zhang and L. Wang, J. Membr. Sci., 2016, 520, 1–7 CrossRef CAS.
- A. Tiraferri, Y. Kang, E. P. Giannelis and M. Elimelech, ACS Appl. Mater. Interfaces, 2012, 4, 5044–5053 CAS.
- X. Lu, S. R.-V. Castrillón, D. L. Shaffer, J. Ma and M. Elimelech, Environ. Sci. Technol., 2013, 47, 12219–12228 CrossRef CAS PubMed.
- M. L. Lind, A. K. Ghosh, A. Jawor, X. Huang, W. Hou, Y. Yang and E. M. V. Hoek, Langmuir, 2009, 25(17), 10139–10145 CrossRef CAS PubMed.
- G. N. B. Baroña, J. Lim, M. Choi and B. Jung, Desalination, 2013, 325, 138–147 CrossRef.
- W. Xie, G. M. Geise, B. D. Freeman, H.-S. Lee, G. Byun and J. E. McGrath, J. Membr. Sci., 2012, 403–404, 152–161 CrossRef CAS.
- A. K. Ghosh, B. H. Jeong, X. Huang and E. M. V. Hoek, J. Membr. Sci., 2008, 311, 34–45 CrossRef CAS.
|
This journal is © The Royal Society of Chemistry 2017 |
Click here to see how this site uses Cookies. View our privacy policy here.