DOI:
10.1039/C7RA05687G
(Paper)
RSC Adv., 2017,
7, 42590-42596
Propionic acid-based deep eutectic solvents: synthesis and ultra-deep oxidative desulfurization activity
Received
20th May 2017
, Accepted 16th August 2017
First published on 4th September 2017
Abstract
Propionic acid-based deep eutectic solvents (C3H6O2/X ZnCl2, X from 0.1 to 0.6) were synthesized by stirring a mixture of propionic acid and zinc chloride at 100 °C. C3H6O2/0.5 ZnCl2 was characterized by infrared spectroscopy, electrospray ionization mass spectrometry and 1H NMR spectroscopy. The oxidative desulfurization (ODS) of model oil and gasoline was investigated with C3H6O2/0.5 ZnCl2 DESs as an extractant and catalyst, and hydrogen peroxide (H2O2) as an oxidant. Some influence factors such as acidity of DESs, reaction temperature, H2O2 to sulfur (H2O2/S) molar ratio, and volume ratio of DESs to oil were studied. The results indicated that the desulfurization rates of dibenzothiophene (DBT), 4,6-dimethyl-dibenzothiophene (4,6-DMDBT), and gasoline can reach 99.42%, 98.80%, and 66.67%, respectively, under conditions of 30 °C, an H2O2/S molar ratio of 4, and volume ratio of DESs to oil of 0.15/1 over a period of 180 min. The desulfurization rate of DBT in model oil reached 96.31% after five recycles in the C3H6O2/0.5 ZnCl2–H2O2 systems.
1 Introduction
With the rapid development of the automotive industry, the problems of pollutant emissions are becoming increasingly serious. In order to reduce the environmental pollution caused by SOx produced through burning fuel,1 many countries have laid down strict environmental regulations to limit the sulfur content of fuel oil to under 10 mg L−1.2 The low concentration of sulfur compounds in oil has been a hot spot in academic research.
Hydrogenation desulfurization (HDS)3,4 is the most effective method for removing aliphatic sulfide in fuel. However, HDS has some limitations, including stringent operating conditions such as high temperature, high pressure5 and low desulfurization activity for DBT and its derivatives.6,7 In recent years, as a supplement of HDS, oxidative desulfurization (ODS)8–10 has attracted wide attention. Oxidative desulfurization has some advantages such as mild reaction conditions and a high desulfurization rate for DBT and its derivatives. In the ODS process, organic sulfides in fuel were oxidized to the corresponding sulfoxides and sulfones under the action of catalyst and hydrogen peroxide.11 There are several oxidants, including H2O2,12 molecular oxide,13 ozone14 and organic peroxide.15 However, H2O2 is the most used in the ODS process because it produces harmless by products.16
Deep eutectic solvents (DESs), analogues of ionic liquids (ILs), can be obtained by simply stirring the mixture containing two or three safe and cheap raw materials. DESs possess some special advantages17 such as non-toxic, biodegradability, low vapor pressure and excellent thermal/chemical stability. DESs have been applied in various fields18 such as separation, catalysis, electrochemistry and synthesis. Meanwhile, DESs have also been used in extractive desulfurization. Gano et al.19 found extractive desulfurization rates of 64% and 44% for DBT and thiophene (TH) using FeCl3-based DESs as extractant. Li et al.20 found that a series of ammonium-based DESs and the extractive desulfurization rate of 82.83% can be obtained for one cycle. Gano et al.21 found that extractive desulfurization rate of SnCl2·2H2O-based DESs can be up to 69.57% and 47.28% for DBT and TH. Tang et al.8 reported that 84.5% extractive desulfurization rate of arenium ion deep eutectic solvents for real oil can be achieved. Li et al.22 found the synthesis of carboxylic acid-based DESs and its application to extractive desulfurization, and desulfurization rates of 80.47%, 81.75% and 72% for DBT, BT and TH in a single stage. In order to achieve higher desulfurization rate, the oxidative desulfurization exhibits higher desulfurization rate than extractive desulfurization rate. For instance, Yin et al.23 reported that choline chloride/p-toluenesulfonic acid (ChCl/pTsOH) and tetrabutylammonium chloride/p-toluenesulfonic acid (TBAC/p-TsOH) were synthesized and their oxidative desulfurization rates were 99.99% each. Lü et al.24 found a series of oxalate-based deep eutectic solvents and the oxidative desulfurization rate of TBAC 2OXA was 91%. Liu et al.25 reported that the removal rate of DBT can be up to 99.1% using choline chloride/polyethylene glycol (ChCl/PEG) DESs. Zhu et al.26 reported that the removal rate of DBT can reach 98.6% using air, extractant, irradiation of UV and isobutyraldehyde via liquid–liquid extraction and photochemical oxidative desulfurization, and the removal rate of DBT can reach 95.3% using a temperature-responsive magnetic ionic liquid (IL) N-butylpyridinium tetrachloroferrate ([BPy][FeCl4]) as a catalyst.27 Our research group28 reported that the removal rate of DBT in model oil can go up to 99.23% using C9H10O2 0.5 ZnCl2 DESs under optimal reaction conditions. In this study, C3H6O2/X ZnCl2 (X from 0.1 to 0.6) DES was synthesized by stirring a mixture of propionic acid and zinc chloride under 100 °C. Compared with phenylpropanoic acid-based DESs and reported literature,23–27 the raw material is more easily obtained and inexpensive. Meanwhile, oxidative desulfurization activity of C3H6O2/X ZnCl2 can attach to effective of reported literature under more mild condition. In the ODS system, C3H6O2/0.5 ZnCl2 DESs were used as an extractant and a catalyst, and H2O2 as an oxidant. Formation and structure of C3H6O2/0.5 ZnCl2 have been confirmed by FT-IR, 1H NMR and ESI-MS spectroscopies. The reaction conditions such as acidity of DESs, reaction temperature, molar ratio of H2O2/S, and volume ratio of DESs to oil were optimized. Furthermore, catalytic oxidative desulfurization mechanism of DBT in model oil is discussed in detail.
2 Experiment
2.1 Materials
DBT (98%), BT (97%), TH (99.8%) and 4,6-DMDBT (98%) were purchased from Aladdin Reagent Co., Ltd. H2O2 (30 wt%), n-octane (AR grade), propionic acid (AR grade), zinc chloride (AR grade) and carbon tetrachloride (AR grade) were purchased from Sinopharm Chemical Reagent Co., Ltd.
2.2 Synthesis and characterization of deep eutectic solvents
C3H6O2·X ZnCl2 (X from 0.1 to 0.6) DESs were synthesized using zinc chloride (ZnCl2) and propionic acid as raw materials. The mixture of zinc chloride (ZnCl2) and propionic acid was heated at 100 °C until a homogeneous liquid was formed. The synthesis of DES is shown in Fig. 1.
 |
| Fig. 1 Synthesis of DESs. | |
In order to further analyze the structure, some characterizations were performed. Gas chromatography was determined on an Agilent 7890A GC with an FID detector using a 30 m packed HP5 column. FT-IR (NEXUS8700, Thermo Electron, KBr), 1H NMR (Bruker Avance 600 MHz spectrometer, Germany) and ESI-MS (Bruker Daltonics APEX-II, USA) spectroscopies were also used to analyzed the samples. GC-MS analysis was conducted using an Agilent 7890/5975C-GC/MSD to characterize the oxidized sulfur compounds in deep eutectic solvents after the desulfurization reaction. The sulfur content of gasoline was measured using a WK-2D comprehensive micro coulomb analyzer (Jiangsu jiang electric analysis instrument Co., Ltd).
2.3 Desulfurization procedure and recycling
A model oil of 500 μg mL−1 was prepared by dissolving 1.437 g DBT in 500 mL n-octane. The ODS experiments were performed in a three-necked flask. The mixture of model oil, H2O2 and DESs was stirred at 30 °C for 180 min. The upper oil phase was taken out after 20 min and analyzed by gas chromatography on an Agilent 7890A GC with an FID detector using a 30 m packed HP5 column. The desulfurization rate is calculated by following equation.
Desulfurization rate = (Stot − Sres)/Stot × 100% |
where Stot is the total sulfur concentration and Sres is the residual sulfur concentration after t min. The DESs phase was treated using a rotary evaporator and CCl4. The water in DESs phase was removed using a rotary evaporator. The oxidative product, dibenzothiophene sulfone (DBTO2) was extracted by CCl4 three times every 30 min; subsequently, CCl4 in DESs phase was removed using a rotary evaporator. The recovered DESs were reused in the next ODS.
3 Results and discussion
3.1 FT-IR characterization
To determine the structure of the DES, FT-IR analysis of ZnCl2, C3H6O2 and C3H6O2/0.5 ZnCl2 was performed. Results of analysis are shown in Fig. 2. The characteristic peaks of propionic acid at 934 cm−1 (bending vibration peak of OH, out of plane); 1079 and 1238 cm−1 (stretching vibration peak of C–C); 1291 cm−1 (stretching vibration peak of C–O); 1418 and 1469 cm−1 (bending vibration peak of C–H); 1717 cm−1 (stretching vibration peak of C
O); 2558, 2641 and 2981 cm−1 (stretching vibration peak of OH) can also be observed in the DES. The peaks of OH groups in ZnCl2 (3300–3700 cm−1) and propionic acid (2800 and 3300 cm−1) appear to be shifted and broadened due to the formation of H-bonding in the DES.29
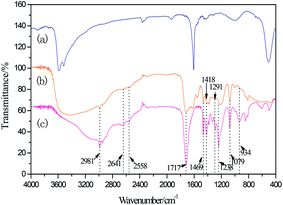 |
| Fig. 2 FT-IR spectra of (a) ZnCl2; (b) C3H6O2/0.5 ZnCl2; (c) C3H6O2. | |
3.2 1H NMR characterization
To further determine the interaction between ZnCl2 and C3H6O2, C3H6O2 and C3H6O2/0.5 ZnCl2 were characterized using 1H NMR. From the results shown in Fig. 3, it can be seen that the peak positions of 1 and 2 do not change, but peak intensity is obviously weak in DES. The peak positions of 3 obviously shifted from 10.8 ppm to 11.9 ppm. It can be shown that H of OH occur the moving of electric charge.30 Hence, it can be concluded that DESs have been formed between C3H6O2 and ZnCl2.
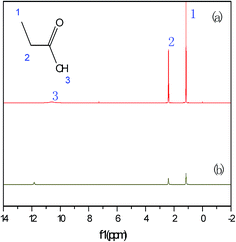 |
| Fig. 3 1H NMR of (a) C3H6O2; (b) C3H6O2/0.5 ZnCl2. | |
3.3 ESI-MS spectra
The structures of C3H6O2/0.5 ZnCl2 were further determined by ESI-MS spectral analysis. As shown in Fig. 4, from the ESI-MS spectra of C3H6O2/0.5 ZnCl2, intensive peaks can be observed at m/z = 171, 309, 444, which correspond to ZnCl3−, Zn2Cl5−, Zn3Cl7−. This result is in accordance with a previous report.31 It can be concluded that C3H6O2/0.5 ZnCl2 has been formed.
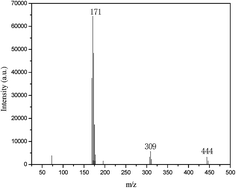 |
| Fig. 4 ESI-MS spectra of C3H6O2/0.5 ZnCl2. | |
3.4 Influence of different Lewis acidic DESs on ODS
The Lewis acidity of the DESs depends on the molar ratio of propionic acid to zinc chloride, which has a significant effect on desulfurization rate. A series of C3H6O2/X ZnCl2 (X from 0.1 to 0.6) were prepared by changing the molar ratio of C3H6O2 to ZnCl2. As shown in Fig. 5, the desulfurization rate increases when the molar ratio of C3H6O2 to ZnCl2 was increased from 0.1 to 0.2. Desulfurization rate decreases when the molar ratio of C3H6O2 to ZnCl2 exceeds 0.6 and the desulfurization rate is stable when molar ratio of C3H6O2 to ZnCl2 ranges from 0.2 to 0.5. This result is in good agreement with previous literature.25 When the molar ratio of C3H6O2 to ZnCl2 was increased, the Lewis acidity of the catalyst was also enhanced. In a certain range, the strong acidity is beneficial for the oxidation desulfurization process because H2O2 produces hydroxyl radicals ˙OH and oxygen radicals O˙. However, very strong acidity results in direct decomposition of hydrogen peroxide32 to produce oxygen and water. Therefore, the highest desulfurization rate of 99.23% in 60 min was obtained when the molar ratio of C3H6O2 to ZnCl2 is 1
:
0.5. Therefore, C3H6O2/0.5 ZnCl2 used as extractant and catalyst undergoes the following desulfurization experiments.
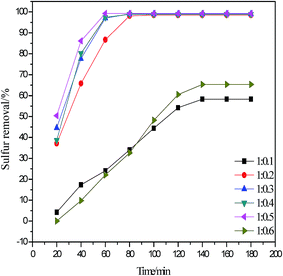 |
| Fig. 5 Influence of different acidic DESs on oxidative desulfurization (V(oil) = 5 mL, V(DESs)/V(oil) = 0.2/1, n(H2O2)/n(S) = 6, 40 °C). | |
3.5 Influence of the reaction temperature on ODS
The reaction temperature is an important factor for ODS. As shown in Fig. 6, when the reaction time exceeds 100 min, the desulfurization rate remains unchanged. The higher the reaction temperature, ranging from 30 °C to 60 °C, the shorter the balance time of desulfurization reaction. The trend is consistent with a previous study.33 However, the reaction temperature of 30 °C was considered as the optimal reaction temperature since low temperature ensures safety and low cost.
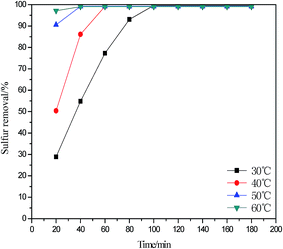 |
| Fig. 6 Influence of reaction temperature on oxidative desulfurization (V(oil) = 5 mL, V(DESs)/V(oil) = 0.2/1, n(H2O2)/n(S) = 6). | |
3.6 Influence of H2O2/S molar ratio on ODS
In order to achieve industrialization for ODS, it is very important to use small dosages of H2O2. As shown in Fig. 7, the desulfurization process was performed using C3H6O2/0.5 ZnCl2 DESs as an extractant and a catalyst under different H2O2/S molar ratios at 30 °C. The desulfurization rate obviously increases from 5.06% to 99.81% when H2O2/S molar ratio changes from 0 to 4. According to the stoichiometric ratio, 2 mol H2O2 was required to oxidize 1 mol of DBT into sulfone. However, a higher desulfurization rate of 99.81% is obtained at an H2O2/S molar ratio of 4 instead of 2; this could be ascribed to loss and decomposition of some H2O2 in ODS process.34 Meanwhile, the desulfurization rate is maintained when H2O2/S molar ratio continually increases. Hence, H2O2/S molar ratio of 4 was selected as the optimal H2O2/S molar ratio for C3H6O2/0.5 ZnCl2 system in the present study.
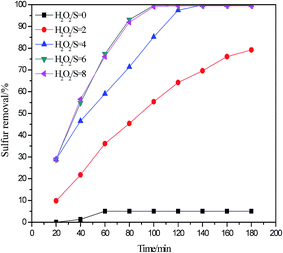 |
| Fig. 7 Influence of H2O2/S molar ratio on oxidative desulfurization (V(oil) = 5 mL, V(DESs)/V(oil) = 0.2/1, 30 °C). | |
3.7 Influence of volume ratio of DESs to oil on ODS
DESs were used as an extractant and catalyst in the ODS system. The amount of DES has an important influence on sulfur removal. As shown in Fig. 8, the desulfurization rate increased from 50.19% to 99.42% when the volume ratio of DESs to oil was increased from 0.05/1 to 0.15/1. However, the desulfurization rate slightly increases when volume ratio of DESs to oil was increased from 0.15/1 to 0.20/1. Hence, the volume ratio of DESs to oil of 0.15/1 was selected as the excess volume ratio of DESs to oil results in increased costs.
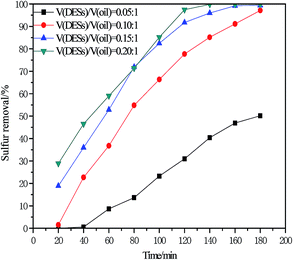 |
| Fig. 8 Influence of V(DESs)/V(oil) on oxidative desulfurization (V(oil) = 5 mL, n(H2O2)/n(S) = 4, 30 °C). | |
3.8 Influence and kinetic analysis of different sulfur compounds on ODS
The oxidative desulfurization experiment of four sulfur compounds such as DBT, 4,6-DMDBT, BT and TH were performed under optimal reaction conditions. As shown in Fig. 9(a), the desulfurization rate follows the order: DBT (99.42%) > 4,6-DMDBT (98.80%) > BT (68.36%) > TH (45.65%). This order of desulfurization rate agreed with a previous study.22 The desulfurization order is correlated to the electron cloud density of the sulfur atom in organic sulfides such as 4,6-DMDBT (5.760), DBT (5.758), BT (5.739) and TH (5.696).35,36 Larger electron cloud density and higher desulfurization activity are obtained. However, the desulfurization rate of 4,6-DMDBT was influenced by steric hindrance of two methyl groups even through the electron cloud density of 4,6-DMDBT is the largest in four sulfurs. Hence, the desulfurization rate of 4,6-DMDBT is slightly lower than that of DBT.
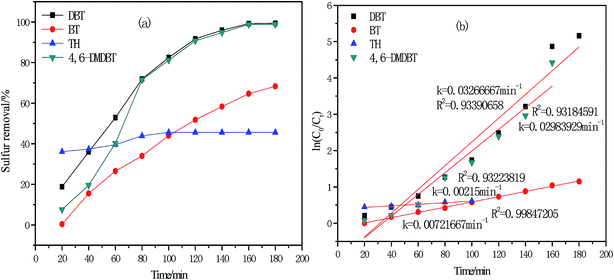 |
| Fig. 9 (a) Influence of different sulfur compounds on oxidative desulfurization (V(oil) = 5 mL, V(DESs)/V(oil) = 0.15/1, n(H2O2)/n(S) = 4, 30 °C); (b) kinetic analysis of different sulfur compounds. | |
Meanwhile, it is science and strictness with the combination of theoretical method and experimental method. On the basis of experimental data and related research, it is known that ODS follows the first order reaction kinetics equation.37
|
 | (1) |
|
 | (2) |
where
C0 is the total sulfur concentration,
Ct is the residual sulfur concentration after
t min,
R2 is the correlation coefficient and
k is the reaction kinetics constant. As shown in
Fig. 9(b), the reaction kinetics constant
k is 0.03266667, 0.02983929, 0.00721667 and 0.00215 min
−1 for DBT, 4,6-DMDBT, BT and TH, respectively. The correlation coefficient
R2 is 0.93390658, 0.93184591, 0.99847205 and 0.93223819 for DBT, 4,6-DMDBT, BT and TH, respectively. It can be concluded that the theory is in agreement with the experiment.
3.9 Recovery and regeneration of DESs
The recovery and regeneration of DESs is very important for large-scale applications. After every oxidative desulfurization experiment, the upper oil phase was separated using a separating funnel. Oxidative product of DBT in DESs phase at the bottom was separated and extracted using CCl4 as an extractant. CCl4 was removed using a rotary evaporator. The desulfurization experiment was performed using recovered DESs, fresh H2O2 and model oil for the next cycle. As shown in Fig. 10, the desulfurization rate was decreased to 96.31% after five recycles. It can be attributed to the regeneration of DESs containing some oxidative product of DBT and partly to DESs losses in oil during recycling experiments.38,39
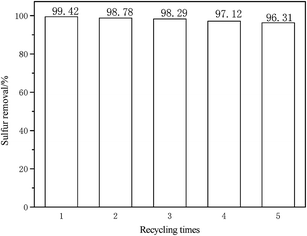 |
| Fig. 10 Influence of recycle and regeneration of DESs on oxidative desulfurization (V(oil) = 5 mL, V(DESs)/V(oil) = 0.15/1, n(H2O2)/n(S) = 4, 30 °C). | |
3.10 Analysis of oxidation products using GC-MS
In order to identify the oxidation products of DBT, after the oxidative desulfurization reaction, a reverse extraction experiment was conducted using CCl4 as an extractant and detected by GC-MS analysis. The results of the analysis are shown in Fig. 11. It can be seen that dibenzothiophene sulfone (DBTO2, m/z = 216.0) exists in carbon tetrachloride40 and no other types of sulfur-containing compounds were obtained. In other words, under optimum conditions, DBT could be completely removed and converted into DBTO2.
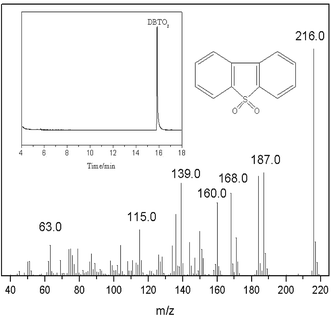 |
| Fig. 11 Analysis of oxidation products using GC-MS. | |
3.11 Catalytic mechanism of DESs for oxidative desulfurization
Based on the experimental results and analysis, the proposed process of catalytic extractive oxidative desulfurization of DBT in the model oil in the presence of C3H6O2/0.5 ZnCl2 DESs and H2O2 is shown in Fig. 12. The entire oxidative desulfurization process can be described as follows. First, DBT in the model oil is extracted to DESs phase. Second, DBT is oxidized to DBTO2 by the action of hydroxyl radicals and peroxy-C3H6O2/0.5 ZnCl2. The hydroxyl radicals are produced by the reaction of H2O2 and the zinc ions in C3H6O2/0.5 ZnCl2.28 The formation of peroxy-C3H6O2/0.5 ZnCl2 is the result of oxidation of C3H6O2/0.5 ZnCl2 by H2O2. In the ODS process, DBT is oxidized to DBTO2 when peroxy-C3H6O2/0.5 ZnCl2 is transformed into C3H6O2/0.5 ZnCl2. The oxidative desulfurization process is continually conducted until H2O2 is completely decomposed to form hydroxyl radicals.
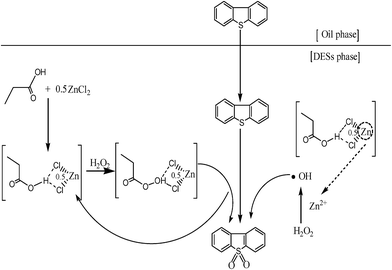 |
| Fig. 12 Mechanism of oxidative desulfurization. | |
3.12 Catalytic oxidative desulfurization of gasoline
The oxidative desulfurization ability of C3H6O2/0.5 ZnCl2 for the FCC gasoline (sulfur content of 303 ppm) was also investigated. As shown in Table 1, the oxidative desulfurization rate was 66.67% for gasoline with reaction temperature of 30 °C, an H2O2/S molar ratio of 4 and volume ratio of DESs to oil of 0.15/1. The oxidative desulfurization rate of gasoline is lower than that of model oil (99.42%) due to the presence of more complex sulfur compounds in gasoline oil.41
Table 1 Comparison of catalytic oxidative desulfurization of model oil and real oil by C3H6O2/0.5 ZnCl2 and other acidic ionic liquids
Catalyst |
Model oil |
Real oil |
Desulfurization rate |
Reaction condition |
Ref. |
Model oil |
Real oil |
For model oil. For real oil. |
[C4min]Cl/3ZnCl2 |
500 ppm |
FCC diesel fuel (460 ppm) |
99.9 |
63.5 |
45 °C; t = 3 h; IL/oil = 1/2; O/S = 8a or 60b. |
38 |
C9H10O2 0.5ZnCl2 |
500 ppm |
Kerosene (153 ppm) |
99.23 |
76.16 |
50 °C; t = 80 mina or 60 minb; IL/oil = 1.25/5; O/S = 6 |
26 |
[C38MPy]FeCl4 |
500 ppm |
Gasoline (468 ppm) |
100 |
44.2 |
25 °C; t = 30 min; IL/oil = 1/5a or 1/3b; O/S = 6. |
39 |
[(C8H17)3CH3N]Cl/FeCl3 |
500 ppm |
FCC gasoline (360 ppm) |
97.9 |
66.67 |
25 °C; t = 1 h; V(oil) = 5 mL; IL(0.702 mmola or 1.404 mmolb); O/S = 14. |
40 |
C3H6O2/0.5 ZnCl2 |
500 ppm |
Gasoline (303 ppm) |
99.42 |
66.67 |
30 °C; t = 3 ha or 40 minb; IL/oil = 0.75/5; H2O2/S = 4 |
This work |
In this study, desulfurization effect of C3H6O2/0.5 ZnCl2 is compared with relevant research about different acidic ionic liquids and DESs were used for oxidative desulfurization, whose results are listed in Table 1. As shown in Table 1, compared with desulfurization research of other acidic ionic liquids, the experimental results show that C3H6O2/0.5 ZnCl2 has higher desulfurization activity for model oil and gasoline. Meanwhile, on the basis of our previous research,28 milder reaction conditions are achieved with C3H6O2/0.5 ZnCl2 DESs as an extractant and catalyst and H2O2 as oxidant. Furthermore, C3H6O2/0.5 ZnCl2 DESs exhibit some advantages such as simple synthesis method, mild reaction conditions and easily obtainable raw material.
4 Conclusions
In this study, a series of propionic acid-based DESs with different molar ratios of ZnCl2 were used. The oxidative desulfurization system with C3H6O2/0.5 ZnCl2 DESs as a catalyst and extractant and H2O2 as an oxidant was investigated. H2O2 was decomposed into hydroxyl excited state (˙OH) under the action of Zn2+ from C3H6O2/0.5 ZnCl2 DESs. The reaction conditions, including different acidity DESs, reaction temperature, H2O2/S molar ratio, volume ratio of DESs to oil and recycling of DESs, were optimized. The optimal reaction conditions of 30 °C, an H2O2/S molar ratio of 4 and volume ratio of DESs to oil of 0.15/1 were obtained. Desulfurization rates of DBT, 4,6-DMDBT, gasoline up to 99.42%, 98.8%, 66.67%, respectively, were obtained. The propionic acid-based DESs might be a novel option in the desulfurization process to achieve clean fuel.
Conflicts of interest
There are no conflicts to declare.
Acknowledgements
The authors acknowledge the financial support of the Natural Science Foundation of China (Project no. 21003069) and the Doctoral Fund of Liaoning Province (201501105).
References
- W. Zhu, H. Li and X. Jiang, et al., Green Chem., 2008, 10(6), 641–646 RSC.
- S. Ribeiro, C. M. Granadeiro and P. Silva, et al., Catal. Sci. Technol., 2013, 3(9), 2404–2414 CAS.
- C. Yansheng, L. Changping and J. Qingzhu, et al., Green Chem., 2011, 13(5), 1224–1229 RSC.
- P. S. Kulkarni and C. A. M. Afonso, Green Chem., 2010, 12(7), 1139–1149 RSC.
- X. M. Yan, Z. Mei and P. Mei, et al., J. Porous Mater., 2014, 21(5), 729–737 CrossRef CAS.
- J. Chen, C. Chen and R. Zhang, et al., RSC Adv., 2015, 5(33), 25904–25910 RSC.
- J. Xiong, W. Zhu and W. Ding, et al., Ind. Eng. Chem. Res., 2014, 53(51), 19895–19904 CrossRef CAS.
- X. Tang, Y. Zhang and J. Li, et al., Ind. Eng. Chem. Res., 2015, 54(16), 4625–4632 CrossRef CAS.
- R. Abro, A. A. Abdeltawab and S. S. Al-Deyab, et al., RSC Adv., 2014, 4(67), 35302–35317 RSC.
- C. Mao, R. Zhao and X. Li, et al., RSC Adv., 2017, 7(21), 12805–12811 RSC.
- J. Zhang, W. Zhu and H. Li, et al., Green Chem., 2009, 11(11), 1801–1807 RSC.
- S. Cui, F. Ma and Y. Wang, React. Kinet. Catal. Lett., 2007, 92(1), 155–163 CrossRef CAS.
- H. Lü, J. Gao and Z. Jiang, et al., Chem. Commun., 2007, 2, 150–152 RSC.
- C. Ma, B. Dai and P. Liu, et al., J. Ind. Eng. Chem., 2014, 20(5), 2769–2774 CrossRef CAS.
- K. J. Stanger and R. J. Angelici, Energy Fuels, 2006, 20(5), 1757–1760 CrossRef CAS.
- S. Xun, W. Zhu and D. Zheng, et al., RSC Adv., 2015, 5(54), 43528–43536 RSC.
- F. Ilgen, D. Ott and D. Kralisch, et al., Green Chem., 2009, 11(12), 1948–1954 RSC.
- Q. Zhang, K. D. O. Vigier and S. Royer, et al., Chem. Soc. Rev., 2012, 41(21), 7108–7146 RSC.
- Z. S. Gano, F. S. Mjalli and T. Al-Wahaibi, et al., Chem. Eng. Process., 2015, 93, 10–20 CrossRef CAS.
- C. Li, D. Li and S. Zou, et al., Green Chem., 2013, 15(10), 2793–2799 RSC.
- Z. S. Gano, F. S. Mjalli and T. Al-Wahaibi, et al., Int. J. Chem. Eng., 2015, 6(5), 367 CAS.
- J. Li, H. Xiao and X. Tang, et al., Energy Fuels, 2016, 30(7), 5411–5418 CrossRef CAS.
- J. Yin, J. Wang and Z. Li, et al., Green Chem., 2015, 17(9), 4552–4559 RSC.
- H. Lü, P. Li and C. Deng, et al., Chem. Commun., 2015, 51(53), 10703–10706 RSC.
- W. Liu, W. Jiang and W. Zhu, et al., J. Mol. Catal. A: Chem., 2016, 424, 261–268 CrossRef CAS.
- W. Zhu, C. Wang and H. Li, et al., Green Chem., 2015, 17(4), 2464–2472 RSC.
- W. Zhu, P. Wu and L. Yang, et al., Chem. Eng. J., 2013, 229, 250–256 CrossRef CAS.
- C. Mao, R. Zhao and X. Li, Fuel, 2017, 189, 400–407 CrossRef CAS.
- M. Francisco, A. van den Bruinhorst and M. C. Kroon, Green Chem., 2012, 14(8), 2153–2157 RSC.
- H. Lü, S. Wang and C. Deng, et al., J. Hazard. Mater., 2014, 279, 220–225 CrossRef PubMed.
- S. I. Hsiu, J. F. Huang and I. W. Sun, et al., Electrochim. Acta, 2002, 47(27), 4367–4372 CrossRef CAS.
- Y. Dong, Y. Nie and Q. Zhou, Chem. Eng. Technol., 2013, 36(3), 435–442 CrossRef CAS.
- X. Chen, H. Guo and A. A. Abdeltawab, et al., Energy Fuels, 2015, 29(5), 2998–3003 CrossRef CAS.
- H. Gao, C. Guo and J. Xing, et al., Green Chem., 2010, 12(7), 1220–1224 RSC.
- W. S. Zhu, H. Li and Q. Q. Gu, et al., J. Mol. Catal. A: Chem., 2011, 336(1), 16–22 CrossRef CAS.
- C. Komintarachat and W. Trakarnpruk, Ind. Eng. Chem. Res., 2006, 45(6), 1853–1856 CrossRef CAS.
- L. Li, J. Zhang and C. Shen, et al., Fuel, 2016, 167, 9–16 CrossRef CAS.
- H. F. M. Zaid, F. K. Chong and M. I. A. Mutalib, Fuel, 2017, 192, 10–17 CrossRef.
- P. Wu, B. Dai and Y. Chao, et al., J. Mol. Catal., 2017, 436, 53–59 CrossRef.
- M. Zhang, W. Zhu and H. Li, et al., Chem. Eng. J., 2014, 243, 386–393 CrossRef CAS.
- W. Zhu, G. Zhu and H. Li, et al., J. Mol. Catal. A: Chem., 2011, 347(1), 8–14 CrossRef CAS.
|
This journal is © The Royal Society of Chemistry 2017 |
Click here to see how this site uses Cookies. View our privacy policy here.