DOI:
10.1039/C7RA05055K
(Paper)
RSC Adv., 2017,
7, 33937-33943
Hierarchical MoS2 microspheres prepared through a zinc ion-assisted hydrothermal route as an electrochemical supercapacitor electrode†
Received
5th May 2017
, Accepted 29th June 2017
First published on 5th July 2017
Abstract
Hierarchical molybdenum disulfide microspheres have been successfully prepared through a zinc ion-assisted hydrothermal route followed by an acid corrosion strategy. It is found that the MoS2 microspheres comprised of numerous nanosheets with few-layered feature exhibit a 3D flower-like morphology. It is believed that the MoS2/ZnS composites can act as a precursor for the formation of hierarchical MoS2 microspheres. Additionally, the electrochemical properties of the as-prepared MoS2 microspheres as an electrode material for supercapacitors have also been investigated. Compared with the MoS2 nanosheet, the resultant MoS2 microsphere demonstrates superior pseudcapacitive properties including high specific capacitance, good cycling and rate capability, which could be credited to its novel hierarchical architecture feature.
1. Introduction
The ever-increasing applications of portable electronic devices and electric vehicles have evoked intensive research interest for developing high-performance energy storage devices.1 As a category of important energy storage devices, supercapacitors have received great attention for their many attractive merits such as excellent cycling stability, high specific capacitance and power density, good charging-discharging rates and safety.2 According to the charge storage mechanism, supercapacitors can be divided into electric double-layer capacitors (EDLC) and pseudocapacitors (PC). Amongst them, pseudocapacitors can store charge by redox-based faradaic reactions, and thus can have higher capacitance values than EDLCs.3 At present, one of key research themes of PCs is exploring new-type and high-performance electrode materials in order to achieve high capacity, long cycle life, high power/energy density and low cost.4 A series of transition metal oxides such as RuO2, CoOx, NiO, MnO2, and so forth, have been widely investigated as classic examples for pseudocapacitors.5–8
The discovery of graphene and its unusual properties have aroused interest in other layered materials.9 Specially, layered transition-metal dichalcogenides which are characteristic of relatively weak interactions between the layers and the strong intralayer covalent bonding interactions have gained more and more attention due to their uncommon electronic, chemical and physical properties as well as potential applications in catalysis, sensors and energy generation and storage.10–14 Thereinto, MoS2 is a typical example existing in different forms such as 2H semiconductor phase (2H-MoS2) and 1T metallic phase (1T-MoS2) and has been reported to possess pseudocapacitive charge-storage property.15–17 MoS2 can store charge based on the ions intercalation into the layers of MoS2 accompanied by a faradaic charge-transfer. This mechanism can be termed as intercalation pseudocapacitance.18,19 Until now, a variety of MoS2-based nanomaterials have been synthesized for supercapacitor applications.20 For example, Huang hydrothermally synthesized 2H-MoS2 nanosheets that demonstrated a specific capacitance of 129 F g−1 at 1 A g−1.21 However, inferior conductivity of 2H-MoS2 would impair its electrochemical performance. To circumvent this issue, fabricating MoS2 with metallic features and compositing MoS2 with other conductive materials have been confirmed as effective ways. For instance, Chhowalla found that chemically exfoliated MoS2 nanosheets contained a high concentration of the metallic 1T phase and can electrochemically intercalate H+ and alkali metal ions with extraordinary efficiency.22 Zhu et al. first employed hydrothermal techniques to synthesize water-coupled metallic MoS2 nanosheets which exhibited excellent capacitive performances.23 2H-MoS2/carbon nanotube and MoS2/carbon aerogel hybrids were also prepared and delivered a high capacitance of 452 and 260 F g−1 at 1 A g−1, respectively.24,25 Additionally, the reduction of active surfaces originating from the overlapping or restacking of MoS2 nanosheets as well as structural instability during repeated ions insertion/extraction can also lead to an unsatisfied electrochemical performances.26–28 Fabricating hierarchical MoS2 nanostructures is considered to be an efficient pathway to solve this problem.29,30 Hierarchical nanostructures, which are assembled from 0D, 1D and 2D nanomaterials as building blocks have attracted significant attention based on the fact that the hierarchical structures could supply efficient channels for transport of both electrons and ions, exhibit high surface area, shorten ion diffusion length, strengthen the structural stability and thus improve their electrochemical performance.31–33 Various MoS2 hierarchical nanostructures such as binder-free nanoarrays, nanosponges and nanoflowers have been reported to manifest superior electrochemical performances.34–36
In a liquid-phase synthetic route towards hierarchical MoS2 nanostructures, some organics including surfactants, polymers, complexing agents, ionic liquids and amines were usually employed as a structure-directing agent which might produce pollutants leading to environmental damage.37–40 Herein, we present a facile zinc ion-assisted hydrothermal method to prepare hierarchical MoS2 microspheres assembled by 2D nanosheets, which exhibit superior electrochemical performance as an electrode for pseudcapacitor.
2. Experimental section
2.1 Zinc ion-assisted hydrothermal synthesis of hierarchical MoS2 microspheres
In a typical synthesis, 1.5 mmol of zinc nitrate hexahydrate was dissolved in 30 mL deionized water to form a clear solution. Then 30 mL of 0.05 M sodium molybdate solution was slowly dropped into the above solution under vigorous stirring. No obvious precipitates can be observed. After that, 9 mmol of thiocarbamide was also dissolved into the above solution. Finally, the resulting solution was transferred into a 100 mL of Teflon-lined stainless steel autoclave and maintained at 240 °C for 24 h. Finally, the hydrothermal products were collected and redispersed into 0.5 M HCl solution to remove possible zinc sulfide residues. Then the products were washed with water and alcohol and dried at 60 °C for 6 h in a vacuum oven. The hydrothermal product was then annealed in a tube furnace at 500 °C for 2 h under nitrogen atmosphere to improve the crystallinity. For comparison, the MoS2 nanosheets as well as ZnS products were also prepared by a similar method.
2.2 Characterizations
X-ray diffraction patterns (XRD) were obtained with a D/Max-2550 X-ray diffractometer using monochromatized CuKα radiation. TEM and HRTEM characterizations were carried out on a JEOL JFL-2010 TEM operating at 200 kV, for which the samples were prepared by dispersing them in acetone and drop-casting onto a 200 mesh copper grid coated with holey carbon. SEM observations were conducted by using a SIRION-100 field emission scanning electron microscopy (SEM). The elemental composition was analyzed by energy dispersive X-ray spectroscopy (EDX, GENENIS-4000). X-ray photoelectron spectra (XPS) were processed on a Perkin-Elmer PHI5000c XPS, using C 1s (B. E. 284.6 eV) as a reference. Raman spectra were recorded using excitation with a 514 nm argon ion laser at 6 mW for 50 s on a Jobin Yvon LabRam HR spectrometer. The nitrogen sorption analysis was conducted at 77 K on a Quantachrome NOVA 2000e sorption analyzer and the Brunauer–Emmett–Teller (BET) surface area was estimated from the adsorption data. Electrochemical impedance spectroscopy (EIS) was obtained by applying a voltage amplitude of 5 mV in the frequency range from 100 kHz to 0.01 Hz on a CHI660E.
2.3 Electrochemical measurements
Electrochemical performance of the supercapacitor was studied by cyclic voltammetry (CV) and galvanostatic charge/discharge (GCD) at an electrochemical station (CHI660E). The electrochemical tests were performed in 3 M KOH electrolyte using a three electrode cell composed of a saturated calomel electrode (SCE) as reference, Pt plate as counter and the samples-based electrode as the working electrode. Working electrodes were fabricated by mixing electroactive material, carbon black and poly(vinylidene fluoride) in a mass ratio of 80
:
10
:
10 to obtain a slurry. Then the slurry was pressed onto the nickle foam current collector (1 cm2) and dried at 60 °C for 12 h. The electroactive mass loading on the nickle foam is calculated to be 3.57 mg. The scan rate of the CV response varied from 5 to 100 mV s−1 with the potential range from −0.2 to 0.45 V. The capacitance values at various scan rate were calculated according to the CV curves as following eqn (1): |
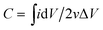 | (1) |
The specific capacitances at different current density were calculated from the GCD curves according to eqn (2):
where
C is the specific capacitance,

is the integrated area of the CV curves,
v is the scan rate, Δ
V is the potential window,
I is the discharge current, Δ
t is the discharge time,
m is the mass of the electroactive material loading on nickle foam.
3. Results and discussions
3.1 Microstructure and morphology of the samples
Fig. 1 shows the XRD patterns of the as-prepared MoS2 nanosheets and MoS2 microspheres. It is clearly seen that all the MoS2 samples agree well with a hexagonal structure of MoS2 (JCPDS 37-1492), in which the diffraction peaks at 2θ = 14.2°, 33.4°, 39.8°, 49.4°, 59.1° and 69.8° can be unambiguously assigned to the (002), (100), (103), (105), (110) and (203) planes, respectively. No obvious peaks from the impurity ZnS phase can be observed in the XRD patterns of Fig. 1b, which confirms that residual zinc sulfide in hydrothermal products has been completely removed by the following acid treatment. The (002) reflection of layered MoS2 at 2θ = 14.2° can be indicative of an interlayer spacing of 0.62 nm according to Bragg's equation, which is in agreement with that of 2H phase MoS2. In comparison with Fig. 1a, the prominently weakened (002) peak in Fig. 1b indicates that the crystal growth of MoS2 layers were inhibited to a certain extent which might be due to the physical confinement of the ZnS produced in hydrothermal process. The stacking layers of MoS2 microspheres could be estimated to be approximately ∼5 layers in the light of FHWM of (002) reflection using Scherrer's equation, visibly less than those of the MoS2 nanosheets (∼11 layers).
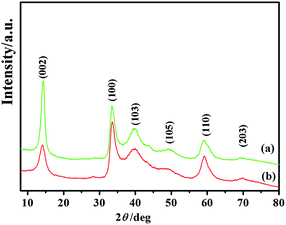 |
| Fig. 1 XRD patterns of (a) the as-prepared MoS2 nanosheets and (b) MoS2 microspheres. | |
Fig. 2a provides the morphology of the as-prepared MoS2 nanosheets, which are scattered nanosheets. In sharp contrast to the MoS2 nanosheets, Fig. 2b indicates that the MoS2 products are hierarchical microspheres with sizes of ∼1.5 μm. Moreover, it can be discerned that these MoS2 microspheres are comprised of folded sheet-like subunits. The neighboring nanosheets on surface are interconnected and obvious open spaces exist between them. With a closer examination with TEM (Fig. 2c), these curled nanosheets stretch out towards the edges of the spheres and aggregate to form relatively loose microspheres. Fig. 2d clearly reveals the few-layered characteristic of the nanosheets in MoS2 microspheres. These dispersed nanosheets display a 4–6 layer thickness with a lattice spacing of 0.62 nm between two adjacent layers, which is in line with XRD results. The de-layered structures can be favourable to decreasing the interlayer resistance and accelerating electron transfer between MoS2 layers. The elemental composition of the MoS2 microspheres were identified by EDX as shown in Fig. 2e. It can be seen that the MoS2 spheres contain C, O, Mo and S elements. The little amount of C and O elements could come from the air adsorption. The atomic ratio of S to Mo is calculated as 2.07, which agrees with the MoS2 stoichiometry.
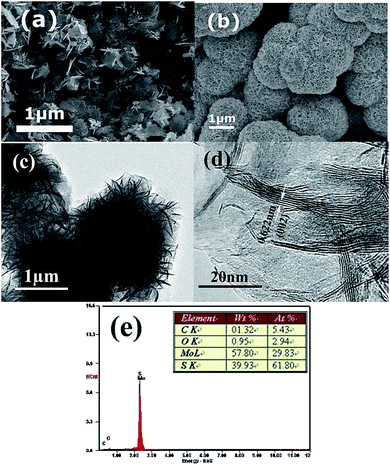 |
| Fig. 2 SEM images of (a) MoS2 nanosheets and (b) MoS2 microspheres; (c) TEM image, (d) HRTEM image and (e) EDX pattern of MoS2 microspheres. | |
The chemical states and compositions of the MoS2 microspheres were studied by XPS. As shown in Fig. 3a, the Mo 3d orbit demonstrates two peaks located at 229.0 and 232.4 eV, which can be ascribed to the doublet of Mo(IV) 3d5/2 and Mo 3d3/2, respectively.41,42 Besides, a small shoulder signal arising from 236.04 eV can be characteristic of a +6 oxidation state.41,42 Fig. 3b reveals that the S 2p core-level XPS spectrum can be divided into two peaks, indicating existence of two chemical environments. The peaks at 161.95 and 163.09 eV can be attributed to the binding energies of S 2p3/2 and S 2p1/2.41,42 The estimated atomic ratio of S
:
Mo is about 2.12, agreeing with the result of EDX.
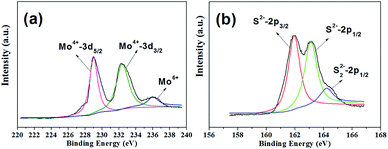 |
| Fig. 3 High-resolution XPS spectra of the as-prepared MoS2 microspheres. (a) Mo 3d; (b) S 2p. | |
Fig. 4 provides the Raman spectra of the as-prepared MoS2 samples. The MoS2 microspheres demonstrate two characteristic peaks situated at 378.25 cm−1 (E12g mode) and 402.24 cm−1 (A1g mode). For the MoS2 nanosheets, the peaks at 378.25 and 403.53 cm−1 correspond to E12g and A1g mode. It is deemed that the E12g mode peak is related to the in-layer displacements of Mo and S atoms, whereas the A1g mode peak involves the out-of-layer symmetric displacements of S atoms along the c-axis.43,44 It is noticed that the intensities of E12g and A1g peaks of the MoS2 microspheres are lower than those of the MoS2 nanosheets, suggesting some defect sites in the crystal structure of MoS2.45 Besides, it can be discerned that the A1g peak of MoS2 microspheres has a down shift in comparison with that of the MoS2 nanosheets, which further confirms the decreased layers.46 In addition, the appearance of E11g, LA as well as 2LA(M) peaks is associated with the vibration of one MoS2 layer against neighboring layers and is called the rigid layer mode.43,44
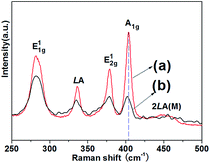 |
| Fig. 4 Raman spectra of the as-prepared (a) MoS2 nanosheets and (b) MoS2 microspheres. | |
The surface area of the as-prepared MoS2 samples were determined by nitrogen adsorption–desorption isotherm measurements. A typical type IV can be observed in Fig. 5, indicating the presence of a mesoporous structure for both samples. The BET specific surface area of the MoS2 microspheres was measured as about 28.39 m2 g−1, which is larger than that of the MoS2 nanosheets (14.06 m2 g−1). The pore-size distribution plots of all samples were obtained from the adsorption branch of the N2 adsorption–desorption isotherms by BJH method. It can be seen that the mesopores with a size of 3.4 nm are dominant in the MoS2 nanosheets. By contrast, the presence of different pores (5.6 and 11.4 nm) for the MoS2 microspheres can be observed with a broad pore-size distribution. Large surface area and porous feature are critical for affording more active sites for electrode reactions and promoting charge carriers transfer at the electrolyte/electrode interface, which results in observably enhanced electrochemical performances.
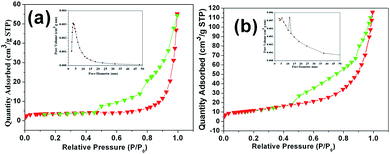 |
| Fig. 5 Nitrogen adsorption–desorption isotherm of (a) MoS2 nanosheets and (b) MoS2 microspheres. The inserted figure is the pore-size distribution. | |
Time-dependent experiment was also carried out to investigate the formation process of the as-prepared MoS2 hierarchical microspheres. It can been observed in Fig. 6a that spherical MoS2/ZnS composites with numerous tiny nanoparticles on the surface were formed at the initial hydrothermal stage. Fig. 6b and c display that with the hydrothermal reaction proceeding, an increasing number of MoS2 nanosheets appeared on the surfaces of the microspheres. For comparison, ZnS samples were also synthesized through a similar hydrothermal route as depicted in Fig. 6d, which manifested a sphere-like morphology.
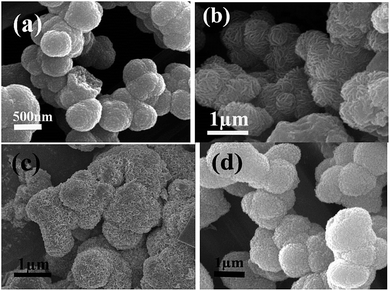 |
| Fig. 6 SEM images of the MoS2 samples prepared by zinc ion-assisted hydrothermal reaction at 240 °C for (a) 1 h, (b) 5 h, (c) 9 h, (d) SEM image of the ZnS samples prepared via a similar hydrothermal process at 240 °C for 24 h. | |
Based on the above results, the formation of the hierarchical MoS2 microspheres in our synthetic route can be illustrated in Fig. 7. Firstly, as MoO42− anions were introduced to the Zn2+-contained solution before hydrothermal treatment, no ZnMoO4 precipitates appeared. The combination of Zn2+–MoO42− might be formed via strong electrostatic attraction. Secondly, during the following hydrothermal process, Zn2+ and MoO42− ions reacted with H2S arising from the decomposition of thiocarbamide to produce small ZnS and MoS2 nanoparticles, respectively. Due to the high surface energy, these nanoparticles were liable to aggregate together to form spherical composite particles. Owing to the anisotropic characteristic, the MoS2 nanoparticles began to evolve into 2D nanosheets. These nanosheets gradually grew larger, interconnected together to form MoS2 nanosheets/ZnS microspheres. With removal of ZnS by acid erosion, the MoS2 microspheres could be obtained. The detailed formation mechanism needs to be further investigated.
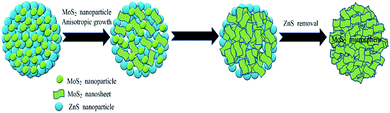 |
| Fig. 7 Illustration of the formation process of the MoS2 microspheres. | |
3.2 Electrochemical performance of the sample electrodes
The pseudocapacitive properties of the MoS2 sample electrodes was tested in a 3 M KOH aqueous electrolyte. The CV curves of both MoS2 electrodes were plotted in Fig. 8a for comparison. Evidently, the CV curves of two electrodes are different from the ideal rectangular curves originating from the electric double-layer capacitance, indicating a typical pseudocapacitive mechanism according to the redox peaks.2,3 The prominent cathodic peaks situated at around 0.16–0.20 V can be attributed to the electrochemical insertion of K+ ions into the MoS2 interlayer. The corresponding anodic peaks located at about 0.27–0.32 V can be attributed to the extraction of K+ ions from layered MoS2.15–19 The nearly symmetrical redox peaks are indicative of high reversibility of the insertion/extration process. As is well known, the specific capacitance is proportional to the area of the CV curves.2,3 It is apparent that the MoS2 microspheres possess a much larger CV curve area than that of MoS2 nanosheets, demonstrating that the MoS2 microspheres have a higher capacitance value. Moreover, it can be seen that the CV area of pure Ni foam is almost negligible compared with those of the MoS2 electrodes, revealing the almost no capacitance contribution of the current collector. The CV curves under the different sweep rates are displayed in Fig. 8b and c, respectively. As the scan rate increases, CV curves of all the electrodes still retain a similar shape in spite of a small shift of peak positions owing to the polarization effect.47 The area under the curve increased with increasing scan rate, meaning that the MoS2 electrodes show the ideal supercapacitive behavior. The increase in current with increasing scan rate indicates that the kinetics of the interfacial faradic redox reactions and the rates of electronic and ionic transmission are rapid enough at scan rates as high as 100 mV s−1.48 Fig. 8d shows the change in scan rate with respect to the specific capacitance. With the scan rate increasing from 5 mV s−1 to 100 mV s−1, according to eqn (1), the specific capacitances of MoS2 nanosheet and MoS2 microsphere electrodes decrease from 211.3 to 85.1 F g−1 and 294.4 to 209.2 F g−1, respectively. Obviously, MoS2 microsphere electrode delivers a higher capacitance retention of 71% than that of MoS2 nanosheet electrode (40%). The decrease in capacitance could be attributed to the presence of inner active sites, which cannot sustain the redox transitions completely at higher scan rates.48
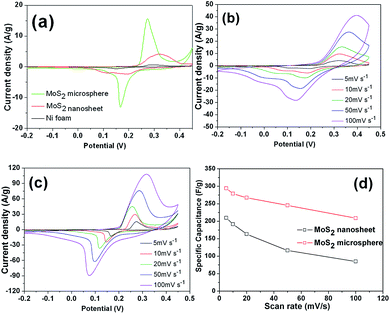 |
| Fig. 8 Electrochemical measurements of MoS2 nanosheet and MoS2 microsphere electrodes: (a) cyclic voltammograms (CV) within the optimized potential range of −0.2 to 0.45 V in 3 M KOH solution at a scan rate of 5 mV s−1, voltammetric responses of (b) MoS2 nanosheet and (c) MoS2 microsphere electrodes at various scan rates, (d) specific capacitance obtained at different scan rates. | |
Galvanostatic charge–discharge was carried out to measure the specific capacitance of electrochemical capacitors at constant current. Fig. 9a shows galvanostatic charge–discharge curves of the MoS2 nanosheet and MoS2 microsphere electrodes at a current density of 1 A g−1, respectively. Apparently, the latter manifests a longer discharging time than that of the former, representing a higher discharge capacitance, which is in agreement with CV results. Fig. 9b and c show charge–discharge curves of the two electrodes at various current densities. For the MoS2 nanosheet electrode, according to eqn (2), the discharge specific capacitance values are calculated to be 217.3, 143.4, 124.3, 90.6 and 58.1 F g−1 at 0.5, 1, 2, 4 and 10 A g−1, respectively. By contrast, the MoS2 microsphere electrode delivers a much higher capacitance of 294.6, 254.0, 185.7, 157.8 and 134.1 F g−1 at 0.5, 1, 2, 4 and 10 A g−1, respectively. The relationship between specific capacitance and current density is illustrated in Fig. 9d. MoS2 microsphere exhibits a capacitance of 134.1 F g−1 at 10 A g−1 with a capacitance retention of 46% relative to 0.5 A g−1. In contrast, the MoS2 nanosheet electrode delivers a much smaller capacitance value of 58.1 F g−1 at 10 A g−1 with only 27% retention compared with 0.5 A g−1. The greatly enhanced electrochemical performances of MoS2 microsphere can be attributed to the robust 3D hierarchical architecture, which can be favorable to offering sufficient surface area for electrochemical reactions and promoting charge carriers transfer at the electrolyte/electrode interface.
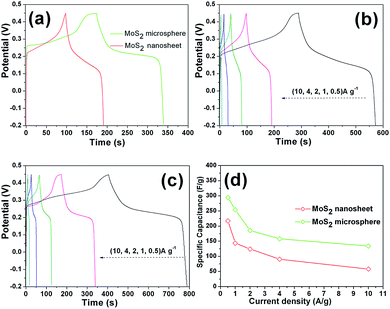 |
| Fig. 9 (a) Galvanostatic charge–discharge curves of the MoS2 sample electrodes at 1 A g−1; galvanostatic charge–discharge curves of (b) the MoS2 nanosheet electrode and (c) the MoS2 microsphere electrode at different current densities; (d) specific discharge capacitances vs. current densities of the two sample electrodes. | |
Furthermore, the good electrochemical properties of the MoS2 microsphere electrode were further confirmed by the long-term cycling test. As shown in Fig. 10a, during 10
000 cycles testing, the MoS2 nanosheet electrode exhibits an obvious capacitance loss up to 44.3%. The obvious decay in capacitance may be caused by chemical dissolution and ion intercalation/deintercalation induced volume change of active materials. For MoS2 microsphere electrode, still 78.5% of the initial capacitance can be maintained after long-term cycles. The capacitive decay observed for MoS2 microsphere electrode during the process of the charge–discharge cycling can be attributed to the partial collapsion of the MoS2 microsphere as shown in Fig. 10b. In comparison with MoS2 nanosheets, the prominently enhanced electrochemical performances of MoS2 microspheres can be attributed to the 3D hierarchical architecture, which can be favorable to maintaining structural integrity, offering sufficient surface area for electrochemical reactions and promoting charge carriers transfer at the electrolyte/electrode interface.
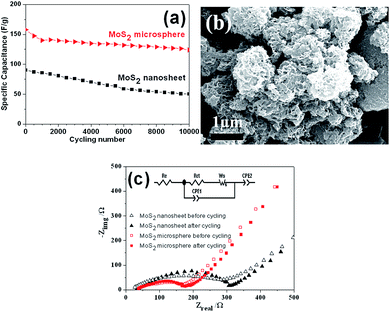 |
| Fig. 10 (a) Cycling performance of the as-prepared MoS2 sample electrodes at 4 A g−1, (b) SEM image of the MoS2 microspheres after cycling and (c) EIS spectra of the sample electrodes before and after cycling, inset is the equivalent circuit. | |
EIS measurements were performed to understand why MoS2 microsphere electrode exhibits a superior electrochemical performance. Fig. 10c displays that both impedance spectra are composed of semicircles in the high frequency region followed by a linear slope in the low frequency region. The diameter of the characteristic depressed semicircle in the high frequency regions is related to charge transfer resistance. A linear region in the low-frequency range corresponds to the diffusive resistance (Warburg impedance). The steeper straight line of MoS2 microsphere reveals a faster ion diffusion in comparison with MoS2 nanosheet. The equivalent circuit (inset of Fig. 10c) for fitting the EIS data contains the internal resistance (Re), the charge transfer resistance (Rct), the constant phase element (CPE1, CPE2) involving the double layer capacitance and the limit capacitance, and Warburg impedance (Ws).21,49 The Re represents a combined resistance of ionic resistance of electrolyte, intrinsic resistance of substrate, and contact resistance at the active material/current collector interface. The Rct is caused by faradaic redox process. The Ws is a result of the frequency dependence of ion diffusion/transport in the electrolyte to the electrode surface. The smaller diameter of the Nyquist circle of MoS2 microsphere means a fast electron transfer process at the electrode/electrolyte interface.50 In addition, it is noted that the diameter of the Nyquist circle after cycling became slightly larger, indicating an increasment of Rct, which is probably due to the loss of adhesion of some active material with the current collector during the charge/discharge cycling.49,51 The Rct values obtained by data fitting according to the equivalent circuit model are summarized in Table 1.
Table 1 Rct values of the MoS2 nanosheet and MoS2 microsphere electrodes before and after cycling
Sample electrode |
Rct/Ω |
Before cycling |
After cycling |
MoS2 nanosheet |
282.3 |
298.4 |
MoS2 microsphere |
139.8 |
147.5 |
4. Conclusions
In conclusion, hierarchical MoS2 microspheres composed of few-layered nanosheets have been successfully synthesized via a facile zinc ion-assisted hydrothermal route combined with an acid erosion method. It is found that the initially generated MoS2/ZnS composites acted as a precursor for the formation of the hierarchical MoS2 microspheres. Furthermore, the hierarchical MoS2 microspheres deliver a high specific capacitance as well as good rate and cycle ability for supercapacitor.
Acknowledgements
We acknowledge financial support from the Guangdong Natural Science Foundation for Joint Training Innovative Talents in East-West-North Guangdong (2014A030307030, 2016A030313667), the Science and Technology Planning Project of Guangdong Province (2014A010106032), the Stong Innovation School of Engineering Program of of Department of Education of Guangdong Province (2014KTSCX157). We also thank the funding of Lingnan Normal University (LZL1502, LZL1402).
Notes and references
- R. Sahoo, A. Pal and T. Pal, Chem. Commun., 2016, 52, 13528–13542 RSC.
- Y. Zheng, Y. Yang, S. Chen and Q. Yuan, CrystEngComm, 2016, 18, 4218–4235 RSC.
- Y. Wang, Y. Song and Y. Xia, Chem. Soc. Rev., 2016, 45, 5925–5950 RSC.
- G. Wang, L. Zhang and J. Zhang, Chem. Soc. Rev., 2012, 41, 797–828 RSC.
- B. Shen, X. Zhang, R. Guo, J. Lang, J. Chen and X. Yan, J. Mater. Chem. A, 2016, 4, 8180–8189 CAS.
- X. Y. Liu, Y. Q. Gao and G. W. Yang, Nanoscale, 2016, 8, 4227–4235 RSC.
- J. Min, J. Liu, M. Lei, W. Wang, Y. Lu, L. Yang, Q. Yang, G. Liu and N. Su, ACS Appl. Mater. Interfaces, 2016, 8, 780–791 CAS.
- T. Zhai, X. Lu, F. Wang, H. Xia and Y. Tong, Nanoscale Horiz., 2016, 1, 109–124 RSC.
- C. N. R. Rao, H. S. S. R. Matte and U. Maitra, Angew. Chem., Int. Ed., 2013, 52, 13162–13185 CrossRef CAS PubMed.
- J. Yang and H. S. Shin, J. Mater. Chem. A, 2014, 2, 5979–5985 CAS.
- K. J. Huang, Y. J. Liu, H. B. Wang, Y. Y. Wang and Y. M. Liu, Biosens. Bioelectron., 2014, 55, 195–202 CrossRef CAS PubMed.
- L. X. Fang, K. J. Huang and Y. Liu, Biosens. Bioelectron., 2015, 71, 171–178 CrossRef CAS PubMed.
- K. J. Huang, Y. J. Liu, Y. M. Liu and L. L. Wang, J. Hazard. Mater., 2014, 276, 207–215 CrossRef CAS PubMed.
- D. Chen, W. Chen, L. Ma, G. Ji, K. Chang and J. Y. Lee, Mater. Today, 2014, 17, 184–193 CrossRef CAS.
- B. Wang, Q. Wu, H. Sun, J. Zhang, J. Ren, Y. Luo, M. Wang and H. Peng, J. Mater. Chem. A, 2017, 5, 925–930 CAS.
- K. Krishnamoorthy, P. Pazhamalai, G. K. Veerasubramani and S. J. Kim, J. Power Sources, 2016, 321, 112–119 CrossRef CAS.
- G. Zhang, H. Liu, J. Qu and J. Li, Energy Environ. Sci., 2016, 9, 1190–1209 CAS.
- S. K. Balasingam, J. S. Lee and Y. Jun, Dalton Trans., 2015, 44, 15491–15498 RSC.
- B. Xie, Y. Chen, M. Yu, T. Sun, L. Lu, T. Xie, Y. Zhang and Y. Wu, Carbon, 2016, 99, 35–42 CrossRef CAS.
- G. Zhang, H. Liu, J. Qu and J. Li, Energy Environ. Sci., 2016, 9, 1190–1209 CAS.
- K. J. Huang, J. Z. Zhang, G. W. Shi and Y. M. Liu, Electrochim. Acta, 2014, 132, 397–403 CrossRef CAS.
- M. Acerce, D. Voiry and M. Chhowalla, Nat. Nanotechnol., 2015, 10, 313–318 CrossRef CAS PubMed.
- X. Geng, Y. Zhang, Y. Han, J. Li, L. Yang, M. Benamara, L. Chen and H. Zhu, Nano Lett., 2017, 17, 1825–1832 CrossRef CAS PubMed.
- K. J. Huang, L. Wang, J. Z. Zhang, L. L. Wang and Y. P. Mo, Energy, 2014, 67, 234–240 CrossRef CAS.
- K. J. Huang, L. Wang, J. Z. Zhang and K. Xing, J. Electroanal. Chem., 2015, 752, 33–40 CrossRef CAS.
- H. Ji, C. Liu, T. Wang, J. Chen, Z. Mao, J. Zhao, W. Hou and G. Yang, Small, 2015, 11, 6480–6490 CrossRef CAS PubMed.
- R. Kumuthini, R. Ramachandran, H. A. Therese and F. Wang, J. Alloys Compd., 2017, 705, 624–630 CrossRef CAS.
- L. Wang, Y. Ma, M. Yang and Y. Qi, Appl. Surf. Sci., 2017, 396, 1466–1471 CrossRef CAS.
- R. Zhou, C. J. Han and X. M. Wang, J. Power Sources, 2017, 352, 99–110 CrossRef CAS.
- S. Zhang, R. Hu, P. Dai, X. Yu, Z. Ding, M. Wu, G. Li, Y. Ma and C. Tu, Appl. Surf. Sci., 2017, 396, 994–999 CrossRef CAS.
- L. Wang, Y. Ma, M. Yang and Y. Qi, Electrochim. Acta, 2015, 186, 391–396 CrossRef CAS.
- Y. Ma, Y. Jia, L. Wang, M. Yang, Y. Bi and Y. Qi, J. Power Sources, 2017, 342, 921–928 CrossRef CAS.
- Y. Wang, L. Yu and X. W. Lou, Angew. Chem., Int. Ed., 2016, 55, 7423–7426 CrossRef CAS PubMed.
- K. Krishnamoorthy, G. K. Veerasubramani, P. Pazhamalai and S. J. Kim, Electrochim. Acta, 2016, 190, 305–312 CrossRef CAS.
- S. K. Balasingam, M. Lee, B. H. Kim, J. S. Lee and Y. Jun, Dalton Trans., 2017, 46, 2122–2128 RSC.
- X. Wang, J. Ding, S. Yao, X. Wu, Q. Feng, Z. Wang and B. Geng, J. Mater. Chem. A, 2014, 2, 15958–15963 CAS.
- P. Sun, W. Zhang, X. Hu, L. Yuan and Y. Huang, J. Mater. Chem. A, 2014, 2, 3498–3504 CAS.
- H. Y. Wang, B. Y. Wang, D. Wang, L. Lu, J. G. Wang and Q. C. Jiang, RSC Adv., 2015, 5, 58084–58090 RSC.
- J. Li, D. Wang, H. Ma, Z. Pan, Y. Jiang, M. Li and Z. Tian, Mater. Lett., 2015, 160, 550–554 CrossRef CAS.
- L. Ma, L. M. Xu, X. P. Zhou and X. Y. Xu, Mater. Lett., 2014, 132, 291–294 CrossRef CAS.
- Y. Yan, B. Xia, N. Li, Z. Xu, A. Fisher and X. Wang, J. Mater. Chem. A, 2015, 3, 131–135 CAS.
- J. Zhou, J. Qin, X. Zhang, C. Shi, E. Liu, J. Li, N. Zhao and C. He, ACS Nano, 2015, 9, 3837–3848 CrossRef CAS PubMed.
- K. G. Zhou, F. Withers, Y. Cao, S. Hu, G. Yu and C. Casiraghi, ACS Nano, 2014, 8, 9914–9924 CrossRef CAS PubMed.
- S. Y. Chen, C. Zheng, M. S. Fuhrer and J. Yan, Nano Lett., 2015, 15, 2526–2532 CrossRef CAS PubMed.
- L. Zhang, W. Fan and T. Liu, RSC Adv., 2015, 5, 43130–43140 RSC.
- H. Li, Q. Zhang, C. C. R. Yap, B. K. Tay, T. H. T. Edwin, A. Olivier and D. Baillargeat, Adv. Funct. Mater., 2012, 22, 1385–1390 CrossRef CAS.
- H. Wang, H. Yi, X. Chen and X. Wang, J. Mater. Chem. A, 2014, 2, 1165–1173 CAS.
- J. Zhang, H. Feng, Q. Qin, G. Zhang, Y. Cui, Z. Chai and W. Zheng, J. Mater. Chem. A, 2016, 4, 6357–6367 CAS.
- Z. Fan, J. Yan, T. Wei, L. Zhi, G. Ning, T. Li and F. Wei, Adv. Funct. Mater., 2011, 21, 2366–2375 CrossRef CAS.
- S. E. Moosavifard, M. F. El-Kady, M. S. Rahmanifar, R. B. Kaner and M. F. Mousavi, ACS Appl. Mater. Interfaces, 2015, 7, 4851–4860 CAS.
- A. Ramadoss, T. Kim, G. S. Kim and S. J. Kim, New J. Chem., 2014, 38, 2379–2385 RSC.
Footnote |
† Electronic supplementary information (ESI) available. See DOI: 10.1039/c7ra05055k |
|
This journal is © The Royal Society of Chemistry 2017 |
Click here to see how this site uses Cookies. View our privacy policy here.