DOI:
10.1039/C7RA04969B
(Paper)
RSC Adv., 2017,
7, 33450-33458
Enhanced tribological performance of PEEK/SCF/PTFE hybrid composites by graphene†
Received
3rd May 2017
, Accepted 27th June 2017
First published on 3rd July 2017
Abstract
Polyetheretherketone (PEEK)/short carbon fiber (SCF)/polytetrafluoroethylene (PTFE)/graphene (GE) composites (PSPGE) with different weight fractions of GE were prepared successfully. The effect of GE on the tribological behavior of PEEK composites was investigated under different applied pressures, sliding speeds and temperatures. Characterization results revealed that the tribological performance was improved with the increase of GE loading, and 2.0 wt% GE filled PEEK/SCF/PTFE composites had the lowest friction coefficient and wear rate. The PSPGE exhibited excellent lubrication and wear resistance efficiency especially under harsh conditions. Moreover, the improved thermal conductivity of the PSPGE composites allowed friction heat to be transferred and further increased the wear resistance. Thus, this newly developed novel PSP2.0GE composite could be applied to many new fields as an advanced friction material.
1. Introduction
Friction and wear are inescapable phenomena, which are associated with energy loss and degradation of materials in our daily life.1 Therefore, developing low-friction and high wear-resistant materials has attracted considerable attention from both academic and industrial points of view.2 In recent years, polymeric composites have been receiving greater attention due to their excellent properties, for example, ease of processing, reduction of energy costs and good tribological performance under dry sliding conditions in engineering applications.3 As one of the most promising friction materials, polyether ether ketone (PEEK) exhibits good thermal stability, excellent wear resistance and outstanding mechanical properties.4,5 PEEK composites are widely used for bearings, valves, gears, nozzles, seal rings and prostheses applications, which replace metal components in various fields (automotive, machinery industries, aerospace, etc.).6 For one of the strategies to improve the friction and wear behaviour of PEEK composites, it is effective to incorporate PEEK composites with a variety of reinforcing agents, including short carbon fibers (SCF),7–9 solid lubricants,10–12 carbon-based particles,13–15 and ceramic particles.16,17 It is widely accepted that SCF/PTFE/graphite filled PEEK is a successful friction material, the SCF/PTFE/graphite fillers exhibit synergistic effects to improve the tribological performance.18–20 Zhang et al.21 reported that a combination of nanoparticles and SCF led to much higher wear resistance than the composites filled only with SCF or nanoparticles. Friction materials filled with nanoparticles exhibited considerably improved performance that cannot be normally achieved by using micro-composites or pure polymers.
Recently, by introducing graphene (GE) nanoparticles into polymers, the development of excellent wear-resistant composites has been intrinsically studied. Their remarkable self lubrication, high thermal conductivity, large specific surface areas, and ultrathin laminated structure are fascinating for industry application.22–25 It has been demonstrated that polymer composites filled with graphene or graphene oxide nanoparticles exhibit significant improvement of tribological performance compared with the original polymer composites.14,22,26–28 For example, Song et al.14 reported the reduction of friction coefficient and wear scar diameter by adding 0.1 wt% of graphene oxide–Si into PEEK. Our previous work22 exhibited that by adding the continuous carbon fiber reinforced PEEK composites with 0.7 wt% GE, the friction coefficient and wear rate of composites dramatically decreased. Wang et al.27 found that the incorporation of 1.2 wt% of multi-layer graphene resulted in 56% reduction in the wear rate of poly(vinyl chloride). Shen et al.26 showed that the wear resistance of epoxy is significantly improved by addition of graphene oxide. The specific wear rate was reduced by 90.0–94.1% with 0.5 wt% of graphene oxide. Remarkably, Kandanur et al.28 found that the wear rates of graphene fillers was 10–30 times lower than that of micro-graphite at the same weight fraction. All these studies point out that graphene is a promising solid lubricant for polymer matrix materials.
In the present work, GE nanoparticles were admixed to PEEK/SCF/PTFE (10 wt% for SCF and PTFE, GE varying from 0 wt% to 3.0 wt%) via a ball-milling and melting mixture process. To the best of our knowledge, little systematic investigation had been reported about the effect of varied content of graphene on tribological properties of SCF filled PEEK composite up to now. Incorporation of nanometer-thick GE into PEEK matrix was to improve the contact-damage resistance and enhancement of the lubrication effect. The tribological performance of the PSPGE composites with various GE contents was investigated under various sliding speeds, pressures and temperatures. Transfer films on the counterpart surface and worn surfaces were characterized by SEM, and probable wear mechanisms were discussed in this paper. The composites with 2.0 wt% nanoscale GE exhibited higher lubrication effectiveness than the composites with the same amount of micro-scale graphite. Temperature dependence of thermal conductivities of samples was measured to explain the enhanced wear resistance under harsh conditions. It was expected that the superb lubrication and wear suppression performance with GE makes the formulation suitable for industrial scale applications.
2. Experimental
2.1. Materials
The PEEK powder (KetaSpire® KT-880SFP, nominal diameter 30 μm) was obtained from Solvay (Belgium). GE was purchased from the Chengdu organic chemistry company, China (purity was 98%, diameter range 0.5–3 μm, platelet thickness range 0.55–3.74 nm). The graphite with average diameter of 30 μm was obtained from Sinopharm Chemical Reagent Co., Ltd, China. The PAN-based SCF with ∼38 μm average lengths and about 8 μm in diameter was purchased from the Sinosteel Engineering & Technology Co., Ltd, China. PTFE powder was supplied by Aladdin Co., Ltd, Shanghai, China (5 μm in diameter).
2.2. Preparation of PSPGE composites
Ball milling was conducted to mix PEEK, SCF, PTFE and GE at room temperature with a rotation speed of 300 rpm for 3 h. Each sample contains 10 wt% of SCF and PTFE, respectively. PEEK/10 SCF/10 PTFE composites and PEEK/10 SCF/10 PTFE/GE composites were milled with varying GE content of 0.5, 1.0, 2.0 and 3.0 wt%. According to the amount of GE, the composites mentioned above were named as PSP, PSP0.5GE, PSP1.0GE, PSP2.0GE and PSP3.0GE, respectively. After ball milling, the mixture was dried in vacuum oven at 120 °C for 4 h to eliminate moisture. The mixture of PEEK was further mixed by melt blending in Haake MiniLab II twin screw extruder executing at 385 °C, with a rotor speed of 100 rpm during 10 min for good dispersion of filler in mixture. After cooling, the samples were divided into granules and hot-pressed at 385 °C into cylinders for tribological (coefficient of friction and specific wear rate) and thermal conductivity measurements.
2.3. Characterization
The tribological tests were conducted under dry sliding condition by a pin-on-disk wear tester (MVF-1A, Hengxu Testing Machine Company, China). The contact schematic diagram of the tribological test was shown in Fig. 1. By using this machine, pin-shaped specimens with diameter of 4 mm and height of 12 mm were prepared. The counter material was AISI 304 stainless steel with a mean roughness, Ra (surface roughness) = 0.15–0.3 μm. In order to reduce the running-in process, the specimens were “pre-worn” with grinding paper before the test (firstly P800 and then P1200) and cleaned with acetone before test. Detailed experimental conditions of the tribological tests performed with the PSP and PSPGE composites were tabulated in Table 1. The temperature was controlled by a heating device and measured under the contact surface. During testing, the counterface temperature was maintained within ±1 °C of the target temperature. The friction force was measured by strain gauges with a torque shaft, and the data accumulated from running-in process was used to calculate the friction coefficient. The specific wear rate was calculated by eqn (1): |
 | (1) |
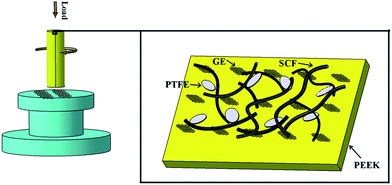 |
| Fig. 1 The schematic diagrams of the tribological contact and the PSPGE composites. | |
Table 1 Experimental conditions of the of PSP composites with different GE weight fractions (0, 0.5, 1.0, 2.0, 3.0 wt%)
No. |
Speed (m s−1) |
Temperature (°C) |
Pressure (MPa) |
1 |
1 |
25 |
1 |
2 |
1 |
25 |
2 |
3 |
1 |
25 |
3 |
4 |
1 |
25 |
4 |
5 |
1.5 |
25 |
4 |
6 |
2 |
25 |
4 |
7 |
2 |
100 |
4 |
8 |
2 |
150 |
4 |
In eqn (1), Δm is the weight change; ρ is the density of the composites; Fn is the applied pressure; L is the sliding distance. The weight and the density of the samples have been tested three times for average of data by a Mettler H78AR balance and a Shimadzu DX-200F densimeter, respectively. All the friction and wear tests were sustained for 3 h. The average values of friction coefficient and specific wear rate were determined from six measurements, which presented with the corresponding error bars, representing the standard deviations. The worn surfaces of the samples and counterpart surfaces were coated with thin gold layers and after that observed by scanning electron microscopy (SEM, SUPRA 40, Zeiss).
Transient plane source method has been introduced to determine thermal conductivity of each composite by using a thermal constant analyzer (Hot Disk 2200, Sweden). The specimens for thermal conductivity tests were cut from the compression molded plates with a dimension of 50 mm × 50 mm × 2 mm. The heat pulse of 20 mW for 15 s was supplied to the samples.
3. Results and discussion
3.1. The effect of applied pressure
It was well-known that the friction and wear behaviors of polymeric composites could be affected by several factors, including sliding speed, temperature and applied pressure during measurements. And it was an effective way to improve tribological performance by adding polymeric composites with a certain amount of GE.33 As shown in Fig. 2, the effect of applied pressure (1, 2, 3, 4 MPa) on the tribological performance of the PSP composites with different GE contents (0, 0.5, 1.0, 2.0, 3.0 wt%) was investigated under 1 m s−1 and 25 °C. The friction coefficients of the PEEK composites decreased after adding GE, and the PSP2.0GE composites exhibited the lowest friction coefficient (Fig. 2a). This might be attributed to the uniform transfer film of the composites transferred onto the surface of the stainless steel counterpart during the friction process.29 GE prevented the asperities of the counterpart from contacting the composite surface, and mechanical property of the transfer film was improved by addition of GE. In addition, friction coefficient slightly decreased with the increase of the applied pressure. The generated high frictional force could shear off the composite, which in favor of forming transfer film.
 |
| Fig. 2 Friction coefficient (a) and specific wear rate (b) of the PSP and PSPGE composites with various contents of GE as a function of applied pressure (1 m s−1, 25 °C). | |
The effect of applied pressure on the specific wear rate of the composites with different GE contents was investigated, and the results were shown in Fig. 2b. The wear rates of the composites were gradually severe by raising the applied pressure from 1 MPa to 4 MPa. This could be explained as the increase of generated heat at the friction surface caused by high applied pressure and led to a reduction of shear strength on interfacial surface. Consequently, the plastic deformation of PEEK resulted to plastic flow and small fragments detachment of matrix.30 Moreover, the PSPGE composites showed much lower wear rate than the PSP composites, and the PSP2.0GE composites exhibited the highest wear resistance among all the samples. At the maximum pressure (4 MPa), the wear rate of the PSP2.0GE composites was (2.4 ± 0.3) × 10−6 mm3 N−1 m−1, approximately 30% of the PSP composite ((8.7 ± 0.4) × 10−6 mm3 N−1 m−1). It could be speculated that the most continuous and homogeneous GE networks were assembled at 2.0 wt% GE additive, which were beneficial to enhance the wear resistance of the PSP composites. In spite of the wear rate of PSPGE composites got severe when the content of GE further increased to 3.0 wt%, it was still lower than that of the PSP composites. The reinforcing mechanism of the GE could be explained as following: a uniform transfer film was generated by PSPGE composites on the surface of the counterparts, which effectively hindered the propagation of wear debris and the micro-cracks, and thereby reduced the wear rate.27,31 We supposed that the reason why wear rate begun to increase after the content of GE exceeded 2.0 wt% might be the formation of stress concentration points due to aggregation of GE. The aggregation generally tended to destroy the uniform structure of the composite.24 After brittle fracture, the distribution of fillers in the composites was shown in Fig. S1.† For the PSP3.0GE composites, it exhibited the relatively severe aggregation of GE in the PEEK than other PSPGE composites, marked with black circle in Fig. S1j.† If the interface adhesion was deteriorated or agglomerated GE generated more wear debris, the wear rate of the composites will be increased consequently.32 Therefore, the sample contains GE up to 2.0 wt% in the formulation improved the tribological performance of PEEK composites, even if the measurements conducted with high pressure of 4 MPa.
3.2. The effect of sliding speed
The effect of sliding speed on the tribological performance of the PSP composites with different GE contents was investigated under relatively high applied pressure (4 MPa), at 25 °C (Fig. 3). As shown in Fig. 3a, when sliding speed was increased from 1 m s−1 to 2 m s−1, the friction coefficients of the composites obviously decreased. Moreover, by adding a certain amount of GE, the friction coefficient decreased gradually and the lowest value (0.13 ± 0.01) of PSP2.0GE obtained with a sliding speed of 2 m s−1. This could be explained that the transfer film could be more easily formed on the frictional surfaces at higher sliding speed, which will lead to the improvement of lubrication condition at the rubbing surfaces and the reduction of friction coefficient.33
 |
| Fig. 3 Friction coefficient (a) and specific wear rate (b) of the PSP and PSPGE composites with various contents of GE under different sliding speeds (4 MPa, 25 °C). | |
According to Fig. 3b, the composites specific wear rates reduced with the increasing of sliding speed. This phenomenon could be explained as following: when the sliding speed was higher, the number of the adhesive points would be largely reduced thanks to the contact time reduction, which led to less adhesive friction force and thus decreased the wear rate.34,35 In addition, the positive effect of GE on the wear resistance was more pronounced for the PSP2.0GE composites. From the observation of Fig. 3b, we could find that when the sliding speed was 1 m s−1, the wear rate changed from (8.7 ± 0.4) × 10−6 mm3 N−1 m−1 of PSP to (2.4 ± 0.3) × 10−6 mm3 N−1 m−1 of PSP2.0GE. As the sliding speed increased to 2 m s−1, the wear rate changed from (2.6 ± 0.3) × 10−6 mm3 N−1 m−1 of PSP to (0.8 ± 0.2) × 10−6 mm3 N−1 m−1 of PSP2.0GE. Therefore, we concluded that the addition of GE to the PEEK composites could reduce the friction coefficient and wear rate at both low and high sliding speeds.
3.3. The effect of temperature
To extend the applications of PSPGE composites as friction materials under harsh conditions, we investigated the friction coefficient and specific wear rate evaluated with various amount of GE and different temperatures were investigated at relatively high applied pressure (4 MPa) and sliding speed (2 m s−1). As presented in Fig. 4a, the friction coefficients decreased with the increase of temperature, and the PSPGE composites exhibited lower friction coefficients than those of the PSP composites. Specifically, the mean friction coefficient of PSP2.0GE composites was around 50% lower than that of PSP composite at 150 °C. The friction surface was polished rapidly due to softening of the adhesive resin at higher temperature, consequently reducing the friction coefficient.36 However, the friction coefficient of the composites increased slightly when the content of GE was increased to 3.0 wt%. As the discussion in Section 3.1 and 3.2, the serious aggregation arose from poor dispersion at 3.0 wt% of GE acted as abrasive third body materials and contributed to an increase in the friction coefficient of the composites.
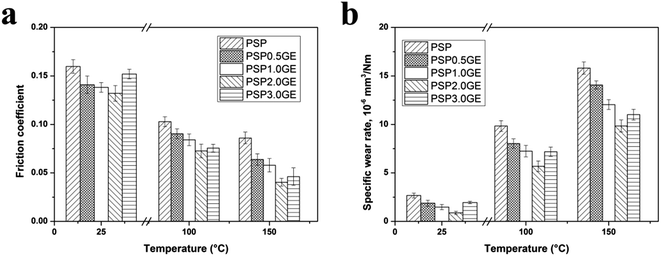 |
| Fig. 4 Friction coefficient (a) and specific wear rate (b) of the PSP and PSPGE composites with various contents of GE as a function of temperature (4 MPa, 2 m s−1). | |
As shown in Fig. 4b, the wear rate of all composites increased with the applied temperature. However, by comparison with the PSP composites, GE filled composites always display lower wear rates with increased temperature. It was obvious that GE made a positive effect on the enhancement of the wear resistance of the traditional PSP composites under high temperature. The enhanced wear resistance could be ascribed to the high strength37 and high thermal conductivity38 of GE, which improved the stress carrying ability and transmission of frictional heat of the composites. The results showed that GE improved the tribological performance of the PSP composites at elevated temperature when it was added to the composite at an appropriate content. Therefore, GE could be considered as a novel high temperature lubricant to enhance the anti-wear performance of PEEK composites under harsh conditions.
3.4. Comparison the lubrication efficiency of graphene and graphite
To demonstrate the lubrication efficiency of the PSPGE composites over the PSPgraphite composites under harsh conditions, we conducted a comparison of tribological performance with GE and graphite at the same ratio (2.0 wt%). In the past few years, micro-scale graphite had been used for enhancing the tribological performance of polymeric composites. It was widely accepted that SCF/PTFE/graphite filled PEEK was a successful friction material, and it had been extensively applied in industry. Fig. 5a displayed the friction coefficients as a function of sliding time of PSP2.0GE composites and PSP2.0graphite composites at 4 MPa, 2 m s−1 and 150 °C. Friction coefficients of the composites rose rapidly during the initial running-in stage, but arrived at relatively stable values (150 to 180 min). The PSP2.0GE composites showed a lower friction coefficient (0.04 ± 0.01) compared with the PSP2.0graphite composites (0.07 ± 0.02) at the same condition (4 MPa, 2 m s−1 and 150 °C). Fig. 5b exhibited the wear rates of the GE-filled and graphite-filled PEEK composites respectively. We could find that the wear rate of the PSP2.0graphite composites was higher than that of PSP2.0GE composites. As a result, nano-scale GE had higher lubrication effectiveness than micro-scale graphite for the PEEK composites at the 2.0 wt% additives under harsh conditions.
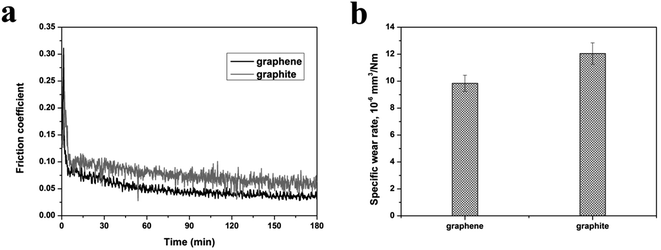 |
| Fig. 5 (a) The friction coefficients as a function of sliding time of PSP2.0GE composites and PSP2.0graphite composites; and (b) wear rate of the PSP2.0GE and PSP2.0graphite composites (4 MPa, 2 m s−1, 150 °C). | |
3.5. SEM analysis of worn surfaces
Fig. 6 presented the typical worn surfaces of PSP and PSP2.0GE composites (4 MPa, 1 m s−1, 25 °C). As shown in Fig. 6a and b, interfacial cracking and debonding were observed, and the dominant wear mechanism of PSP composites was adhesive wear. In addition, the wear debris showed massive or bulk shapes and the running film on the surface of the PSP composites was cracked under repeated stress, which in accordance with the higher wear rate of PSP composites. By contrast, the surface of PSP2.0GE composites was smooth and with slight scratches (Fig. 6c and d), indicating the high stiffness and toughness of GE, which restrained the adhesion and scuffing and provided an excellent wear resistance of the samples during the sliding processes. Moreover, a tenacious and uniform running film was beneficial to improve the anti-wear properties of the PSP2.0GE composites, and it was consistent with the variation in wear rate (Fig. 3b). To further explain the increase of wear rate after filling content of GE beyond 2.0 wt%, the worn surface of PSP3.0GE composites was shown in Fig. S2.† It was found that the fillers were detached from the friction surface and acted as three body abrasive particles, surface abrading and plowing occurred on the worn surface of PSP3.0GE under 4 MPa, 1 m s−1, 25 °C. Moreover, these agglomerates of PSP3.0GE induced plastic deformation in softer regions of the surface. Thus, the tribological performance of PSP3.0GE decreased comparing with PSP2.0GE.
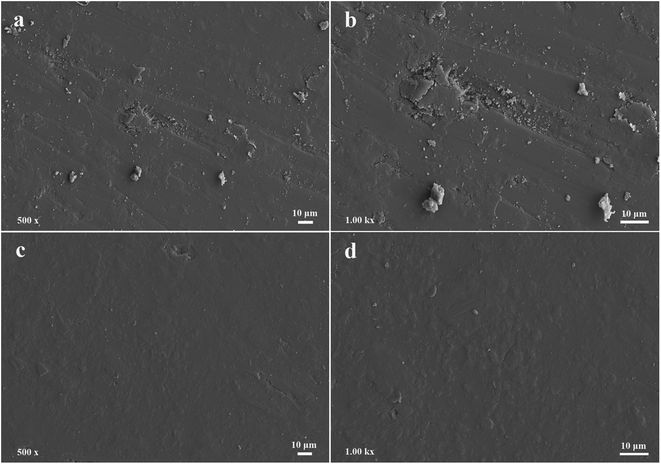 |
| Fig. 6 SEM micrographs of worn surfaces: (a and b) PSP composites and (c and d) PSP2.0GE composites (4 MPa, 1 m s−1, 25 °C). | |
The formation of a transfer film on the counterpart was critical to the tribological performance of polymeric composites especially under dry sliding conditions. Thus, it was essential to elaborate the wear mechanisms by research the transfer film. Fig. 7 displayed the transfer films micrographs of PSP and different contents of GE filled composites formed on the surface of the counterpart. In Fig. 7a, the transfer film of the PSP composites was rough and discontinuous, and a plenty of large-size wear debris were left on the stainless steel surface, implying a high wear rate and low wear resistance. However, after addition of GE, the transfer film of the PSPGE composites became smooth, compact and appears some small-size wear debris (Fig. 7b–e). Especially for the PSP2.0GE, the counterpart was well protected by the uniform and continuous transfer film due to the homogeneous deposition of GE on the counterpart surface. As the content of GE increased to 3.0 wt%, the counterpart surface was characterized by some wear debris, which could be attributed to the poor dispersion of fillers peeled off from the matrix during the sliding process. Therefore, it could be inferred that GE with layered and easily exfoliated structures, which could transfer to the transfer film, provided an excellent anti-wear performance for the PSPGE composites.
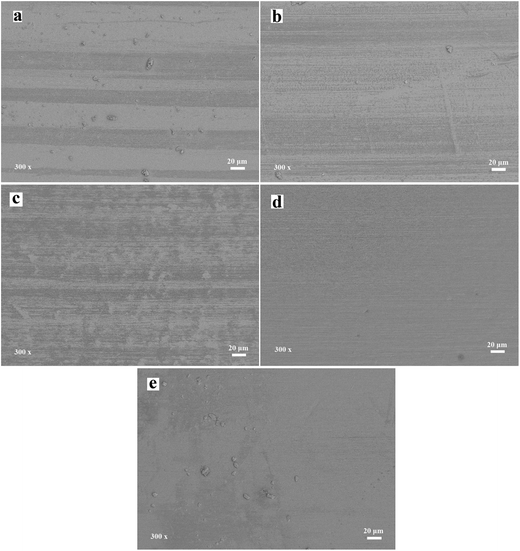 |
| Fig. 7 SEM morphologies of the transfer film on the stainless steel counterpart surface (a) PSP, (b) PSP0.5GE, (c) PSP1.0GE, (d) PSP2.0GE and (e) PSP3.0GE (4 MPa, 1 m s−1, 25 °C). | |
To further demonstrate the superior lubrication efficiency of GE under severe sliding condition (4 MPa, 2 m s−1, 150 °C), the worn surface morphologies of the PSP2.0GE and PSP2.0graphite composites were characterized. Fig. 8a and b showed that the worn surfaces of the PSP2.0graphite composites were rough, accompanied by severe plastic deformation. In addition, the failure SCF and wear debris were shown on the worn surface, which indicated that the abrasion mechanisms of PSP2.0graphite composites were mainly severe adhesive and fatigue wear. High temperature could significantly decrease the shear strength of the sliding surface during the sliding process, and resulted in interface debonding and SCF cracking. By contrast, the plastic deformation and SCF breakage of PSP2.0GE composites was alleviated, displaying less and smaller wear debris (Fig. 8c and d). Besides, the running film formed on the sliding surface which effectively protected the SCF/PEEK interface and reduced SCF failure and improved the wear resistance of the PSP2.0GE composites. This might be attributed to the GE improved the load carrying capacity and the transmission of friction heat. Moreover, filling with GE nanoparticle, the transfer film facilitated the improvement of contact-damage resistance and thereby, resulted in higher wear resistance and lower friction coefficient by comparison with PSP2.0graphite composites. Additionally, more magnifications of SEM images were presented in Fig. S4† for further demonstrate the better lubrication efficiency of GE than graphite under harsh conditions.
 |
| Fig. 8 SEM micrographs of worn surfaces of (a) PSP2.0graphite composites and (c) PSP2.0GE composites; (b) and (d) are magnified images of (a) and (c) (4 MPa, 2 m s−1, 150 °C). | |
To comprehensively investigate the wear behaviors of the GE filled composites under harsh conditions, the SEM images of worn surfaces of PSPGE composites were shown in Fig. S3.† For the PSP composites, the dominant mechanisms were fiber breakage, matrix wear and interface debonding (Fig. S3a†). However, the wear resistances of the PSPGE composites were improved by addition of GE. The worn surfaces of PSP0.5GE and PSP1.0GE composites became smooth and the scuffing alleviated significantly, accompanied with smaller wear debris (Fig. S3c–f†). For the PSP3.0GE composites, due to the presence of GE agglomerates, the worn surfaces were characterized by plastic deformation and with large amount of wear debris (Fig. S3i and j†). However, the wear resistance of the PSP3.0GE was still better than that of PSP composites.
3.6. Thermal conductivity
Polymeric composite with high thermal conductivity was found extensive use in friction materials. For the PSPGE composites, the rapid dissipation of frictional heat produced at the asperity contacts protected the matrix and SCF from degradation and delamination respectively, and helped in the retention of tribological performance of composites. Fig. 9 depicted the temperature dependence of the thermal conductivities of all samples from 25 to 150 °C. It was observed that the thermal conductivities of composites were increased with temperature. For the polymeric composites, the thermal conductivity was affected by the variation of phonon mean free path. At higher temperature, the PEEK chain surrounded with the GE began to vibrate and straight out. Consequently, the mean free path and the phonon propagation length were increased, which contributed to the higher thermal conductivity.39 The higher thermal conductivity of PSPGE composites at elevated temperatures was beneficial to improve the anti-wear properties of the composites under harsh conditions, and it was consistent with the variation in tribological performance as shown in Fig. 4. When the increase on thermal conductivity from PSP to PSP2.0GE was slight at low temperature, the improvement on tribological performances from PSP to PSP2.0GE was not significant either. When the thermal conductivity of the composites at high temperature increased, the tribological performances of PSP2.0GE exhibited dramatical improvement. Thus, it could be concluded that the efficient heat transmission at elevated temperatures made them potentially practical application for the friction materials under harsh conditions. The thermal conductivity of PSP3.0GE was higher than that of PSP2.0GE, but the tribological performance was lower. As discussed above, aggregation of GE was found in PSP3.0GE, which was torn out from the matrix and exerted severe abrasions on the SCF. Therefore, lower tribological performance of PSP3.0GE was ascribed to the worse dispersion of GE. Although good thermal conductivity benefits the tribological performances of composites, dispersion of GE should also be considered for improving wear resistance of composites.
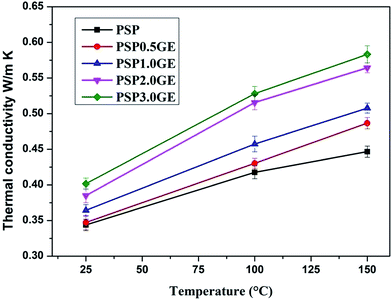 |
| Fig. 9 Temperature dependence of thermal conductivity of composites reinforced with different contents of GE. | |
4. Conclusions
In summary, the effect of applied pressure, sliding speed and temperature on the friction and wear behaviors of PSP composites filled with different amount of GE at dry sliding condition had been studied in this paper. And the thermal conductivity of the PSPGE composites was also investigated. The PSP2.0GE composites showed the best tribological performance among all the PSPGE composites at all applied conditions. Although the improvement on tribological performance from PSP to PSP2.0GE was not significant enough at relative mild condition, the wear rate of PSP2.0GE presented considerate enhancement comparing with PSP composites at harsh conditions. Combining the thermal conductivity of the composites at different temperature, it could be concluded that thermal conductive network had been formed in PSP2.0GE, which was in favor of the wear-suppression in PSPGE composites especially under harsh conditions. Although, the thermal conductivity of the PSPGE composites increased monotonically with higher GE loadings, dispersion of GE also played a key role on the tribological performance of composites, which led lower wear resistance of PSP3.0GE than P2P2.0GE. The comparison between micro-scale graphite and nano-scale GE filled composites exhibited higher lubrication effectiveness than micro-scale graphite for the PSP composites. Therefore, the addition of a certain amount of GE was an effective way in improving friction and wear behaviors of PSP composites. These improved features of PSPGE composites are promising in producing a family of friction materials, which will exert potential application for polymeric engineer materials design and synthesis in industry field.
Acknowledgements
This work was supported by the National Natural Science Foundation of China (Grant No. 21644003, 21501018, 51603020).
References
- S. Xia, Y. Liu, F. Pei, L. Zhang, Q. Gao, W. Zou, J. Peng and S. Cao, Polymer, 2015, 64, 62–68 CrossRef CAS.
- C. Liu, H. Yan, Q. Lv, S. Li and S. Niu, Carbon, 2016, 102, 145–153 CrossRef CAS.
- A. Molazemhosseini, H. Tourani, A. Khavandi and B. Eftekhari Yekta, Wear, 2013, 303, 397–404 CrossRef CAS.
- L. Liu, L. Xiao, M. Li, X. Zhang, Y. Chang, L. Shang and Y. Ao, Colloid Polym. Sci., 2015, 294, 127–133 Search PubMed.
- D. J. Gan, S. Q. Lu, C. S. Song and Z. J. Wang, Mater. Lett., 2001, 48, 299–302 CrossRef CAS.
- B. Yazdani, F. Xu, I. Ahmad, X. Hou, Y. Xia and Y. Zhu, Sci. Rep., 2015, 5, 11579 CrossRef PubMed.
- A. Gebhard, T. Bayerl, A. K. Schlarb and K. Friedrich, Wear, 2010, 268, 871–876 CrossRef CAS.
- A. Godara, D. Raabe and S. Green, Acta Biomater., 2007, 3, 209–220 CrossRef CAS PubMed.
- X. Pei and K. Friedrich, Tribol. Int., 2012, 55, 135–140 CrossRef CAS.
- D. L. Burris and W. G. Sawyer, Wear, 2006, 261, 410–418 CrossRef CAS.
- J. V. Voort and S. Bahadur, Wear, 1995, 181, 212–221 CrossRef.
- G. Y. Xie, G. S. Zhuang, G. X. Sui and R. Yang, Wear, 2010, 268, 424–430 CrossRef CAS.
- M. Kalin, M. Zalaznik and S. Novak, Wear, 2015, 332–333, 855–862 CrossRef CAS.
- H. J. Song, N. Li, Y. J. Li, C. Y. Min and Z. Wang, J. Mater. Sci., 2012, 47, 6436–6443 CrossRef CAS.
- A. M. Díez-Pascual, J. M. González-Domínguez, M. Teresa Martínez and M. A. Gómez-Fatou, Chem. Eng. J., 2013, 218, 285–294 CrossRef.
- H.-B. Qiao, Q. Guo, A.-G. Tian, G.-L. Pan and L.-B. Xu, Tribol. Int., 2007, 40, 105–110 CrossRef CAS.
- Q. Tang, J. Chen and L. Liu, Wear, 2010, 269, 541–546 CrossRef CAS.
- G. Zhang, Z. Rasheva and A. K. Schlarb, Wear, 2010, 268, 893–899 CrossRef CAS.
- G. Zhang and A. K. Schlarb, Wear, 2009, 266, 337–344 CrossRef CAS.
- W. Dong, S. Nie and A. Zhang, Proc. Inst. Mech. Eng., Part J, 2013, 227, 1129–1137 CrossRef CAS.
- G. Zhang, J. Polym. Sci., Part B: Polym. Phys., 2010, 48, 801–811 CrossRef CAS.
- L. Liu, L. Xiao, X. Zhang, M. Li, Y. Chang, L. Shang and Y. Ao, RSC Adv., 2015, 5, 57853–57859 RSC.
- Z. Xu, X. Shi, W. Zhai, J. Yao, S. Song and Q. Zhang, Carbon, 2014, 67, 168–177 CrossRef CAS.
- P. P. Li, Y. P. Zheng, T. Shi, Y. D. Wang, M. Z. Li, C. Chen and J. X. Zhang, Carbon, 2016, 96, 40–48 CrossRef CAS.
- Y. F. Mo, A. Chau, Y. F. Wan, Z. X. Lu and F. C. Huang, Carbon, 2013, 65, 261–268 CrossRef CAS.
- X.-J. Shen, X.-Q. Pei, S.-Y. Fu and K. Friedrich, Polymer, 2013, 54, 1234–1242 CrossRef CAS.
- H. Wang, G. Xie, Z. Zhu, Z. Ying and Y. Zeng, Composites, Part A, 2014, 67, 268–273 CrossRef CAS.
- S. S. Kandanur, M. A. Rafiee, F. Yavari, M. Schrameyer, Z.-Z. Yu, T. A. Blanchet and N. Koratkar, Carbon, 2012, 50, 3178–3183 CrossRef CAS.
- D. Berman, A. Erdemir and A. V. Sumant, Mater. Today, 2014, 17, 31–42 CrossRef CAS.
- A. C. Greco, R. Erck, O. Ajayi and G. Fenske, Wear, 2011, 271, 2222–2229 CrossRef CAS.
- G. W. Yi and F. Y. Yan, Wear, 2007, 262, 121–129 CrossRef CAS.
- Z. Chen, H. Yan, T. Liu and S. Niu, Compos. Sci. Technol., 2016, 125, 47–54 CrossRef CAS.
- G. N. Ren, Z. Z. Zhang, X. T. Zhu, B. Ge, F. Guo, X. H. Men and W. M. Liu, Composites, Part A, 2013, 49, 157–164 CrossRef CAS.
- Q. H. Wang, X. R. Zhang and X. Q. Pei, Mater. Des., 2010, 31, 3761–3768 CrossRef CAS.
- B. Chen, J. Wang and F. Yan, Tribol. Int., 2012, 52, 170–177 CrossRef CAS.
- F. H. Su, Z. Z. Zhang, F. Guo, H. J. Song and W. M. Liu, Wear, 2006, 261, 293–300 CrossRef CAS.
- R. J. Young, I. A. Kinloch, L. Gong and K. S. Novoselov, Compos. Sci. Technol., 2012, 72, 1459–1476 CrossRef CAS.
- A. A. Balandin, S. Ghosh, W. Bao, I. Calizo, D. Teweldebrhan, F. Miao and C. N. Lau, Nano Lett., 2008, 8, 902–907 CrossRef CAS PubMed.
- W. T. Hong and N. H. Tai, Diamond Relat. Mater., 2008, 17, 1577–1581 CrossRef CAS.
Footnote |
† Electronic supplementary information (ESI) available. See DOI: 10.1039/c7ra04969b |
|
This journal is © The Royal Society of Chemistry 2017 |
Click here to see how this site uses Cookies. View our privacy policy here.