DOI:
10.1039/C7RA03103C
(Paper)
RSC Adv., 2017,
7, 24040-24045
Visible light-induced PET-RAFT polymerization of methacrylates with novel organic photocatalysts
Received
16th March 2017
, Accepted 23rd April 2017
First published on 3rd May 2017
Abstract
Light-emitting diode (LED) technology in the visible spectrum holds great promise for photopolymerization because of its characteristic virtues such as low energy consumption, no ozone release, low heat generation, simple and safe operation, high performance, etc. In this work, two organic agents, 4-methoxybenzaldehyde (PC1) and 2,4,6-tri-(p-methoxyphenyl) pyrylium tetrafluoroborate (PC2), were employed as the photocatalysts for the photoinduced electron transfer-reversible addition–fragmentation chain transfer (PET-RAFT) polymerization under irradiation of various LED lights (purple, blue and white LEDs) at room temperature, using methyl methacrylate (MMA) as the model monomer and typical 2-cyanoprop-2-yl 1-dithionaphthalate (CPDN) as the RAFT agent. It has been found that the polymerization could be carried out smoothly with a wide range of wavelengths of visible light and could be extended to other methacrylates such as ethyl methacrylate (EMA) and n-butyl methacrylate (n-BMA). In addition, the “living” feature of this polymerization system was demonstrated by its polymerization kinetics and was confirmed by a chain-extension experiment.
1. Introduction
Compared with traditional polymerization methods, controlled/living radical polymerization (LRP) has advantages of synthesizing well-designed polymeric materials with predetermined molecular weight, narrow weight distribution and diverse architectures. Thanks to the effort of researchers, great achievements in the development of LPR methods have been made. Different strategies to modulate the balance between dormant and activate species have been found in recent years, such as nitroxide-mediated radical polymerization (NMP),1 atom transfer radical polymerization (ATRP),2 and reversible addition–fragmentation chain transfer (RAFT) polymerization.3
It is well known that various physical and chemical stimuli can be used to control the reversible activation of dormant species in LRPs.4 For example, Matyjaszewski and co-workers successfully controlled the initiation and growth steps of LRP by exploiting the unique aspects of electro-chemistry to control the ratio of activator to deactivator in ATRP.4(a) UV irradiation was also used to develop a LRP including iniferter polymerization.5 Unfortunately, UV irradiation would lead to the decomposition of dithioesters in the process of RAFT polymerization.3(f) However, as a more environmentally friendly external stimulus, light-emitting diodes (LED) in the visible spectrum is the most ideal stimulus due to its characteristic virtues such as low energy consumption, no ozone release, low heat generation, simple and safe operation, high performance. Now it has been successfully used in various LRP methods with controlled molecular and narrow molecular weight distribution under mild conditions.6
On the other hand, since Hawker and co-workers developed a kind of transition metal photoredox catalyst (e.g., fac-[Ir(ppy)3]) for photoinduced ATRP,7 Boyer and co-workers established a highly efficient photoinduced electron transfer RAFT (PET-RAFT) polymerization using this kind of metal photoredox catalysts.8 Frustratingly, the resultant polymers are easily contaminated by the transition metal catalyst, and therefore limited its application fields (e.g., electronic materials) significantly. Therefore, organic photocatalyst is highly promising to solve the problem of PET-RAFT mentioned above. Now, some organic photocatalysts, such as methylene blue, fluorescein, rhodamine 6G, Nile red, eosin Y, porphyrin compounds, chlorophyll a (Chl a), and pheophorbide, were explored.9 In order to enrich the library of organic photocatalyst, in this work, by combination of both advantages of visible LED lights and PET-RAFT polymerization, the commercially available organic catalyst 4-methoxybenzaldehyde (PC1) and the synthesized 2,4,6-tri-(p-methoxyphenyl) pyrylium tetrafluoroborate (PC2) were used as the organic photocatalyst for the PET-RAFT polymerization of methacrylates under irradiation of visible LED lights at room temperature. The effect of solvent and wavelength of LED lights and polymerization kinetics was studied in detail.
2. Experimental section
2.1. Materials
Monomers, methyl methacrylate (MMA, 99+%) purchased from Shanghai Chemical Reagents Co. Ltd. (Shanghai, China), ethyl methacrylate (EMA, 98+%) and n-butyl methacrylate (n-BMA, 99%) purchased from TCI (Shanghai, China) were removed the inhibitor by passing through a neutral alumina column before use. The RAFT agent 2-cyanoprop-2-yl 1-dithionaphthalate (CPDN) was prepared according to the method reported by the literature.10 Tetrahydrofuran (THF, analytical reagent) purchased from Nanjing Chemical Reagent Co. 4-Methoxybenzaldehyde (PC1) and 4′-methoxyacetophenone were purchased from Univ-bio (Shanghai, China). Ethyl ether boron fluoride (BF3·Et2O) was purchased from Innochem (Beijing, China). Toluene (analytical reagent), anisole (analytical reagent), N,N-dimethylformamide (DMF), 1,4-dioxane (analytical reagent), acetone (analytical reagent), dimethyl sulfoxide (DMSO), N,N-dimethylacetamide (DMAc, analytical reagent) were purchased from Chinasun Specialty Products Co. Ltd. and used as received unless mentioned.
2.2. Synthesis of 2,4,6-tri-(p-methoxyphenyl) pyrylium tetrafluoroborate (PC2)
The synthetic route of PC2 is shown in Scheme 1. Details are as follows: to a flask containing 4-methoxybenzaldehyde (6.1 mL, 50.3 mmol, 1 equiv.) and p-acetylanisole (15.07 g, 100.4 mmol, 2 equiv.) was added BF3·Et2O (15.0 mL, 121.5 mmol, 2.4 equiv.) dropwise over 5 min. The solution was placed in an oil bath set to 100 °C for 2 h. After cooled to room temperature, the crude material was diluted with acetone (200 mL) and Et2O (250 mL) and filtered to give a rust-colored solid. The solids were washed with warm acetone (175 mL) and dried under vacuum to give the pyrylium tetrafluoroborate as an orange solid (5.01 g, 20% of yield). The structure of PC2 was analysed by 1H NMR spectroscopy (Fig. 1), and its spectral matched that previously reported.11
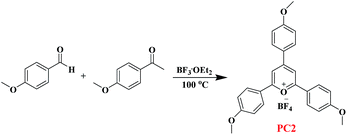 |
| Scheme 1 The synthetic pathway of organic photocatalyst 2,4,6-tri-(p-methoxyphenyl) pyrylium tetrafluoroborate (PC2). | |
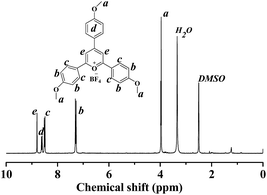 |
| Fig. 1 1H NMR of the organic photocatalyst (PC2). | |
2.3. Typical procedures for PET-RAFT polymerization
A typical polymerization procedure with the molar ratio of [MMA]0
:
[PC1]0
:
[CPDN]0 = 400
:
50
:
1 was described as follows. A mixture was obtained by adding CPDN (6.4 mg), MMA (1.0 mL), PC1 (0.14 mL), and solvent (DMAc, 0.5 mL) to a clean ampoule with a stir bar. The mixture was thoroughly bubbled with argon for 20 min to eliminate the dissolved oxygen, and then the ampoule was flame-sealed and irradiated under LED light with stirring at room temperature (25 °C), which was kept by a fanning. After the desire polymerization time, the ampoule was opened and the mixture was diluted by THF. After precipitation with plenty of petroleum ether in a glass, and standing overnight, it was filtered and dried in a vacuum oven at 40 °C until constant weight. The monomer conversion was determined by gravimetrically. The other procedures for PET-RAFT polymerization of MMA using PC2 as the organic photocatalyst were similar as that as described above.
2.4. Characterization
The number-average molecular weight (Mn,GPC) and molecular weight distribution (Mw/Mn) of the resultant polymers were determined by using a TOSOH HLC-8320 gel permeation chromatograph (GPC) equipped with a refractive-index detector (TOSOH), using TSKgel guardcolumn SuperMP-N (4.6 × 20 mm) and two TSKgel SupermultiporeHZ-N (4.6 × 150 mm) with measurable molecular weights ranging from 5 × 102 to 5 × 105 g mol−1. THF was used as the eluent at a flow rate of 0.6 mL min−1 and 40 °C. GPC samples were injected using a TOSOH plus autosampler and calibrated with PMMA standards purchased from TOSOH. 1H NMR spectra were recorded on Bruker 300 MHz nuclear magnetic resonance (NMR) instrument using CDCl3 as the solvent and tetramethylsilane (TMS) as the internal standard at ambient temperature.
3. Results and discussion
3.1. Effect of solvent on the polymerization catalyzed by PC1
Firstly, we investigated the commercially available 4-methoxybenzaldehyde (PC1) photocatalyst12 for this PET-RAFT polymerization system for the first time. Subsequently, the effect of solvent including toluene, anisole, 1,4-dioxane, DMAc, and DMF on the PET-RAFT polymerization were studied under irradiation of white LED light at room temperature, and the results are shown in Table 1. It can be seen that all the polymerizations were carried out smoothly and that relatively faster polymerization rate was observed in more polar solvents (e.g., DMAc, DMF) due to its basicity.12 Taking into account the molecular weight and molecular weight distribution of the resultant polymers, DMAc (entry 5 in Table 1) as the solvent additionally preferred to be used.
Table 1 Effect of solvent on the PET-RAFT polymerizationa
Entry |
Solvent |
Conv. (%) |
Mn,thb (g mol−1) |
Mn,GPC (g mol−1) |
Mw/Mn |
Polymerization condition: R = [MMA]0 : [PC1]0 : [CPDN]0 = 400 : 50 : 1, VMMA = 1.0 mL, mCPDN = 6.4 mg, VPC1 = 0.14 mL; temperature = 25 °C, Vsolvent = 0.5 mL, under irradiation of white LED (λmax = 440, 540 nm, 1.2 mW cm−2), time = 60 h. Mn,th = ([M]0/[CPDN]0) × Mw,MMA × conv.%. |
1 |
None |
20.6 |
8200 |
13 500 |
1.27 |
2 |
Toluene |
16.7 |
6700 |
12 700 |
1.26 |
3 |
Anisole |
22.3 |
8900 |
15 600 |
1.24 |
4 |
DMF |
27.6 |
11 000 |
16 300 |
1.62 |
5 |
DMAc |
24.4 |
9760 |
16 610 |
1.21 |
3.2. Effect of the wavelength of LED and the amount of organic photocatalyst on the polymerization
In order to investigate the effect of wavelength of LED on the PET-RAFT polymerization at room temperature, we kept the optimized polymerization conditions constant and changed the wavelength of LED (purple LED, blue LED and white LED). As shown in Table 2, the polymerization could be carried out successfully in all cases although the polymerization rate changed with the wavelength, which increased with decrease of wavelength. For example, the monomer conversion was 56.6%, 95.7% and 96.6% for the case under irradiation of purple, blue and white LED light, respectively. This is contributed to the fact that higher energy for the shorter wavelength of LED light. In addition, the effect of the amount of PC1 on the polymerization was also investigated, and the results are shown in Table 3. It can be seen that increasing the amount of catalyst enhanced the polymerization rate as expected.
Table 2 Effect of the wavelength of LED on the PET-RAFT polymerizationa
Entry |
Time (h) |
Conv. (%) |
Mn,the (g mol−1) |
Mn,GPC (g mol−1) |
Mw/Mn |
Polymerization condition: R = [MMA]0 : [PC1]0 : [CPDN]0 = 400 : 50 : 1, VMMA = 1.0 mL, VPC1 = 0.14 mL, mCPDN = 6.4 mg, VDMAc = 0.5 mL, temperature = 25 °C. White LED (λmax = 440, 540 nm, 1.2 mW cm−2). Blue LED (λmax = 464 nm, 0.8 mW cm−2). Purple LED (λmax = 391 nm, 0.8 mW cm−2). Mn,th = ([M]0/[CPDN]0) × Mw,MMA × conv.%. |
1b |
48 |
13.0 |
5200 |
12 200 |
1.32 |
2b |
72 |
56.6 |
22 600 |
30 600 |
1.16 |
3c |
48 |
49.2 |
19 700 |
25 000 |
1.23 |
4c |
72 |
95.7 |
38 200 |
45 300 |
1.26 |
5d |
48 |
53.5 |
21 400 |
27 400 |
1.11 |
6d |
72 |
96.6 |
38 600 |
46 400 |
1.15 |
Table 3 Effect of the amount of organic photocatalyst on the PET-RAFT polymerizationa
Entry |
R |
Conv. (%) |
Mn,thb (g mol−1) |
Mn,GPC (g mol−1) |
Mw/Mn |
Polymerization condition: R = [MMA]0 : [PC1]0 : [CPDN]0, VMMA = 1.0 mL, VPC1 = 0.14 mL, mCPDN = 6.4 mg, VDMAc = 0.5 mL, temperature = 25 °C, white LED (λmax = 440, 540 nm, 1.2 mW cm−2), time = 72 h. Mn,th = ([M]0/[I]0) × Mn,MMA × conv.%. |
1 |
400 : 20 : 1 |
30.2 |
12 100 |
19 500 |
1.25 |
2 |
400 : 30 : 1 |
32.3 |
12 900 |
20 400 |
1.24 |
3 |
400 : 40 : 1 |
43.1 |
17 200 |
25 500 |
1.18 |
4 |
400 : 50 : 1 |
53.7 |
21 500 |
28 200 |
1.11 |
5 |
400 : 200 : 1 |
63.7 |
25 500 |
38 500 |
1.16 |
3.3. Kinetics of the polymerization catalyzed by PC1 under irradiation of different light
In order to further investigate the detailed polymerization behaviors under various wavelength of LED, the polymerization kinetics of MMA was conducted with the molar ratio of [MMA]0
:
[PC1]0
:
[CPDN]0 = 400
:
50
:
1 under irradiation of white LED, blue LED and purple LED, respectively. Fig. 2(A) shows the kinetic plots of ln([M]0/[M]) versus time. The first-order polymerization kinetics was observed in all cases, which indicating a constant concentration of propagating radicals during these polymerization processes. It should be noted that induction period of the polymerization under blue LED (17 h) and purple LED (15 h) is much shorter than that under white LED (46 h). Fig. 2(B) shows the evolution of Mn,GPC and Mw/Mn versus monomer conversion, and it can be seen that the molecular weights increased linearly with monomer conversion while keeping narrow molecular weight distributions. All these results indicated the “living” features of the PET-RAFT polymerization at room temperature.
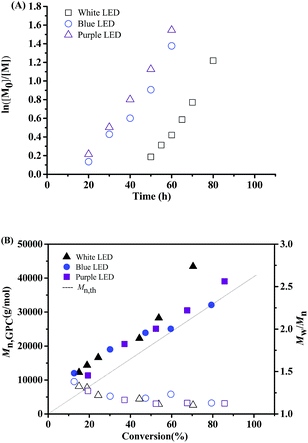 |
| Fig. 2 ln([M]0/[M]) as a function of time (A) and evolution of number-average molecular weight (Mn,GPC) and molecular weight distribution (Mw/Mn) versus conversion (B) under irradiation of different LED lights. Polymerization conditions: R = [MMA]0 : [PC1]0 : [CPDN]0 = 400 : 50 : 1, VMMA = 1.0 mL, VPC1 = 0.14 mL, mCPDN = 6.4 mg, VDMAc = 0.5 mL, temperature = 25 °C. | |
3.4. PET-RAFT polymerization catalyzed by PC2
As reported by the reference, 2,4,6-tri-(p-methoxyphenyl) pyrylium tetrafluoroborate (PC2) is a good organic photocatalyst for cationic polymerization.13 In this work, we employed it as the photocatalyst for the PET-RAFT polymerization, and the results are shown in Table 4. The polymerization could be carried out under irradiation of white, blue and purple LED lights. In order to investigate the potential interference with classical photoRAFT (iniferter) initiation,14 we also carried out the control experiments in the absence of photocatalyst PC2 under blue and purple LED lights. The results are listed in entries 8–11 in Table 4. It can be seen that an enhanced polymerization rate for the photocatalyst was observed. For example, monomer conversion increased from 39.5% (entry 11) in the absence of photocatalyst to 59.2% (entry 7) for the case of photocatalyst PC2 under purple LED light. These results indicated that classical photoRAFT (iniferter) initiation actually existed in the polymerization system; however, the addition of photocatalyst could enhance the polymerization rate significantly. From the GPC results, the resultant polymers are well-controlled with narrow molecular weight distributions except for that (entries 2 and 3) under irradiation of white LED light, indicating that PC2 can also serve as a good candidate for the PET-RAFT polymerization. In order to explain the experimental phenomenon, we tested the absorption spectrum of PC2 (Fig. 3). It can be seen that the emission wavelengths of purple and blue LED lights are within the range of absorption wavelength of PC2, which facilitated to achieve high efficiency of photocatalyst.15
Table 4 Effect of the wavelength of LED on the polymerization in the presence/absence of PC2
Entry |
Time (h) |
Conv. (%) |
Mn,thf (g mol−1) |
Mn,GPC (g mol−1) |
Mw/Mn |
Polymerization condition: a,b,cR = [MMA]0 : [PC2]0 : [CPDN]0 = 400 : 0.5 : 1, VMMA = 1.0 mL, mPC2 = 5.7 mg, mCPDN = 6.4 mg, VDMAc = 0.5 mL. aWhite LED (λmax = 440, 540 nm, 1.2 mW cm−2). b,dBlue LED (λmax = 464 nm, 0.8 mW cm−2). c,ePurple LED (λmax = 391 nm, 0.8 mW cm−2). d,eR = [MMA]0 : [CPDN]0 = 400 : 1, VMMA = 1.0 mL, mCPDN = 6.4 mg, VDMAc = 0.5 mL. fMn,th = ([M]0/[CPDN]0) × Mw,MMA × conv.%. a–eTemperature = 25 °C. |
1a |
24 |
— |
— |
— |
— |
2a |
48 |
9.1 |
3600 |
3900 |
1.54 |
3a |
72 |
35.5 |
14 200 |
21 300 |
1.62 |
4b |
24 |
23.0 |
9200 |
15 100 |
1.35 |
5b |
48 |
47.3 |
18 900 |
26 800 |
1.36 |
6c |
24 |
30.1 |
12 000 |
19 500 |
1.24 |
7c |
48 |
59.2 |
23 700 |
30 000 |
1.23 |
8d |
24 |
12.7 |
5400 |
8100 |
1.15 |
9d |
48 |
34.2 |
14 000 |
18 900 |
1.26 |
10e |
24 |
17.4 |
7200 |
13 600 |
1.24 |
11e |
48 |
39.5 |
16 100 |
23 300 |
1.29 |
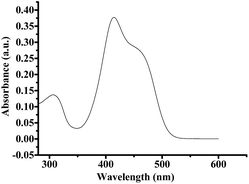 |
| Fig. 3 UV-vis absorption spectrum of the synthetic photocatalyst PC2. | |
3.5. End analysis, chain extension and versatility for other monomers
The chain-end of the resultant PMMA, catalysed by PC1, was analyzed by 1H NMR spectroscopy, as shown in Fig. 4. The chemical shifts at δ = 0.8–1.2 ppm were corresponded to methyl protons of the PMMA repeat units and naphthalene moieties in CPDN; and the chemical shifts at δ = 7.4–8.1 ppm were corresponded to the aromatic protons of the naphthalene units in CPDN,16 which indicated that the CPDN moieties were attached to the polymer chain-end successfully. In order to further verify the end functionality of the resultant PMMA, a chain extension experiment was conducted with fresh MMA monomer using PMMA (Mn,GPC = 14
300 g mol−1, Mw/Mn = 1.31) as the macro-RAFT agent. From Fig. 5, it was found that the Mn,GPC increased to 19
200 g mol−1 (Mw/Mn = 1.14) after chain extension. Based on the above experimental results, we can draw the conclusion that polymeric product has a high degree of chain-end functionality, further verifying the “living” features of this polymerization system.
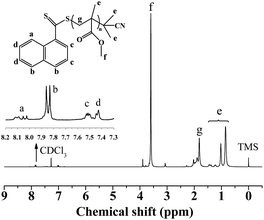 |
| Fig. 4 1H NMR spectrum of the resultant PMMA catalysed by PC1 with CDCl3 as solvent. | |
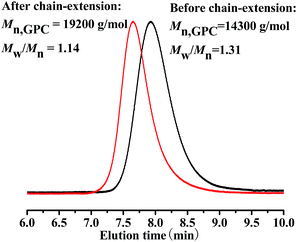 |
| Fig. 5 GPC traces of before and after chain extension using random polymer PMMA as the macro-RAFT agent (Mn,GPC = 14 300 g mol−1, Mw/Mn = 1.31). Polymerization conditions: [MMA]0 : [PC1]0 : [CPDN]0 = 400 : 50 : 1, VMMA = 1.0 mL, VPC1 = 0.14 mL, temperature = 25 °C, VDMAc = 0.5 mL, under irradiation of purple LED (391 nm, 0.8 mW cm−2). | |
In order to investigate the versatility of the polymerization system, EMA and n-BMA were used as the monomers to conduct PET-RAFT polymerization. The results are shown in Table 5. It can be seen that the polymerization system is also suitable for EMA and n-BMA, verifying by the controlled molecular weights and molecular weight distributions of the resultant polymers in the cases of both PC1 and PC2.
Table 5 Versatility for other monomers catalyzed by PC1 and PC2a
Entry |
Catalyst |
Monomer |
Conv. (%) |
Mn,thd (g mol−1) |
Mn,GPC (g mol−1) |
Mw/Mn |
Polymerization conditions: under irradiation of blue LED (λmax = 464 nm, 0.8 mW cm−2), temperature = 25 °C, time = 48 h. R = [monomer]0 : [PC1]0 : [CPDN]0 = 400 : 50 : 1. R = [monomer]0 : [PC2]0 : [CPDN]0 = 400 : 0.5 : 1. Mn,th = ([M]0/[CPDN]0) × Mw,MMA × conv.%. |
1b |
PC1 |
EMA |
44.1 |
20 100 |
26 800 |
1.24 |
2b |
PC1 |
n-BMA |
39.7 |
22 500 |
30 700 |
1.27 |
3c |
PC2 |
EMA |
46.3 |
21 100 |
28 300 |
1.22 |
4c |
PC2 |
n-BMA |
43.6 |
24 800 |
31 400 |
1.13 |
4. Conclusions
The two novel organic agents 4-methoxybenzaldehyde and 2,4,6-tri-(p-methoxyphenyl) pyrylium tetrafluoroborate were explored as the photocatalysts for the PET-RAFT polymerization of methacrylates (e.g., MMA, EMA and n-BMA) under irradiation of LED lights successfully for the first time. Through the experiments, we investigated the effect of the types of solvents and lights on the polymerization and screened the optimal polymerization conditions. It was found that DMAc as the solvent can improve the polymerization rate and controllability due to the better solubility for the polymerization system. In addition, the polymerization was well-controlled under irradiation of blue and purple LED lights.
Acknowledgements
The financial support from the Nature Science Key Basic Research of Jiangsu Province for Higher Education (No. 16KJA150003), the National Natural Science Foundation of China (No. 21674071) and the Project Funded by the Priority Academic Program Development of Jiangsu Higher Education Institutions (PAPD) is gratefully acknowledged.
Notes and references
-
(a) M. K. Georges, R. P. N. Veregin, P. M. Kazmaier and G. K. Hamer, Macromolecules, 1993, 26, 2987–2988 CrossRef CAS;
(b) C. J. Hawker, A. W. Bosman and E. Harth, Chem. Rev., 2001, 101, 3661–3688 CrossRef CAS PubMed;
(c) V. Sciannamea, R. Jérôme and C. Detrembleur, Chem. Rev., 2008, 108, 1104–1126 CrossRef CAS PubMed;
(d) J. Nicolas, Y. Guillaneuf, C. Lefay, D. Bertin, D. Gigmes and B. Charleux, Prog. Polym. Sci., 2013, 38, 63–235 CrossRef CAS;
(e) J. C. Scaiano, T. J. Connolly, N. Mohtat and C. N. Pliva, Can. J. Chem., 1997, 75, 92–97 CrossRef CAS;
(f) S. Hu, J. H. Malpert, X. Yang and D. C. Neckers, Polymer, 2000, 41, 445–452 CrossRef CAS;
(g) A. Goto, J. C. Scaiano and L. Maretti, Photochem. Photobiol. Sci., 2007, 6, 833–835 RSC;
(h) D. L. Versace, Y. Guillaneuf, D. Bertin, J. P. Fouassier, J. Lalevee and D. Gigmes, Org. Biomol. Chem., 2011, 9, 2892–2898 RSC;
(i) J. Morris, S. Telitel, K. E. Fairfull-Smith, S. E. Bottle, J. Lalevee, J. L. Clement, Y. Guillaneuf and D. Gigmes, Polym. Chem., 2015, 6, 754–763 RSC.
-
(a) M. Kato, M. Kamigaito, M. Sawamoto and T. Higashimura, Macromolecules, 1995, 28, 1721–1723 CrossRef CAS;
(b) J. S. Wang and K. Matyjaszewski, J. Am. Chem. Soc., 1995, 117, 5614–5615 CrossRef CAS;
(c) K. Matyjaszewski and J. H. Xia, Chem. Rev., 2001, 101, 2921–2990 CrossRef CAS PubMed;
(d) M. Kamigaito, T. Ando and M. Sawamoto, Chem. Rev., 2001, 101, 3689–3746 CrossRef CAS PubMed;
(e) L. J. Bai, L. F. Zhang, Z. P. Cheng and X. L. Zhu, Polym. Chem., 2012, 3, 2685–2697 RSC;
(f) W. W. He, H. J. Jiang, L. F. Zhang, Z. P. Cheng and X. L. Zhu, Polym. Chem., 2013, 4, 2919–2938 RSC;
(g) Z. B. Guan and B. Smart, Macromolecules, 2000, 33, 6904–6906 CrossRef CAS;
(h) X. W. Jiang, J. Wu, L. F. Zhang, Z. P. Cheng and X. L. Zhu, Macromol. Rapid Commun., 2014, 35, 1879–1885 CrossRef CAS PubMed;
(i) M. Ciftci, M. A. Tasdelen and Y. Yagci, Polym. Chem., 2014, 5, 600–606 RSC;
(j) X. Pan, N. Malhotra, J. Zhang and K. Matyjaszewski, Macromolecules, 2015, 48, 6948–6954 CrossRef CAS;
(k) X. W. Jiang, L. F. Zhang, Z. P. Cheng and X. L. Zhu, Macromol. Rapid Commun., 2016, 37, 1337–1343 CrossRef CAS PubMed;
(l) B. J. Zhang, L. Yao, X. D. Liu, L. F. Zhang, Z. P. Cheng and X. L. Zhu, ACS Sustainable Chem. Eng., 2016, 4, 7066–7073 CrossRef CAS;
(m) X. D. Liu, L. F. Zhang, Z. P. Cheng and X. L. Zhu, Polym. Chem., 2016, 7, 689–700 RSC;
(n) Z. C. Huang, Y. Gu, X. D. Liu, L. F. Zhang, Z. P. Cheng and X. L. Zhu, Macromol. Rapid Commun., 2016 DOI:10.1002/marc.201600461.
-
(a) J. Chiefari, Y. Chong, F. Ercole, J. Krstina, J. Jeffery, T. P. Le, R. T. Mayadunne, G. F. Meijs, C. L. Moad and G. Moad, Macromolecules, 1998, 31, 5559–5562 CrossRef CAS;
(b) C. Boyer, V. Bulmus, T. P. Davis, V. Ladmiral, J. Q. Liu and S. Perrier, Chem. Rev., 2009, 109, 5402–5436 CrossRef CAS PubMed;
(c) D. J. Keddie, Chem. Soc. Rev., 2014, 43, 496–505 RSC;
(d) B. Wenn, M. Conradi, A. D. Carreiras, D. M. Haddleton and T. Junkers, Polym. Chem., 2014, 5, 3053–3060 RSC;
(e) R. K. Bai, Y. Z. You and C. Y. Pan, Macromol. Rapid Commun., 2001, 22, 315–319 CrossRef CAS;
(f) L. Lu, H. J. Zhang, N. F. Yang and Y. L. Cai, Macromolecules, 2006, 39, 3770–3776 CrossRef CAS;
(g) Z. Li, W. J. Chen, Z. B. Zhang, L. F. Zhang, Z. P. Cheng and X. L. Zhu, Polym. Chem., 2015, 6, 1937–1943 RSC;
(h) Z. Li, W. J. Chen, L. F. Zhang, Z. P. Cheng and X. L. Zhu, Polym. Chem., 2015, 6, 5030–5035 RSC.
-
(a) A. J. D. Magenau, N. C. Strandwitz, A. Gennaro and K. Matyjaszewski, Science, 2011, 332, 81–84 CrossRef CAS PubMed;
(b) N. Bortolamei, A. A. Isse, A. J. D. Magenau, A. Gennaro and K. Matyjaszewski, Angew. Chem., Int. Ed., 2011, 50, 11391–11394 CrossRef CAS PubMed;
(c) Y. Kwak and K. Matyjaszewski, Macromolecules, 2010, 43, 5180–5183 CrossRef CAS.
-
(a) T. Otsu and M. Yoshida, Macromol. Rapid Commun., 1982, 3, 127–132 CrossRef CAS;
(b) L. F. Fan, H. J. Jiang, L. F. Zhang, Z. P. Cheng and X. L. Zhu, RSC Adv., 2015, 5, 31657–31663 RSC.
-
(a) S. Shanmugam, J. Xu and C. Boyer, J. Am. Chem. Soc., 2015, 137, 9174–9185 CrossRef CAS PubMed;
(b) Y. G. Zhao, M. M. Yu, S. L. Zhang, Y. C. Liu and X. F. Fu, Macromolecules, 2014, 47, 6238–6245 CrossRef CAS;
(c) X. L. Miao, W. Zhu, Z. B. Zhang, W. Zhang, X. L. Zhu and J. Zhu, Polym. Chem., 2014, 5, 551–557 RSC;
(d) X. L. Miao, J. J. Li, Z. B. Zhang, Z. P. Cheng, W. Zhang, J. Zhu and X. L. Zhu, Polym. Chem., 2014, 5, 46414648 Search PubMed;
(e) X. D. Liu, L. F. Zhang, Z. P. Cheng and X. L. Zhu, Polym. Chem., 2016, 7, 3576–3588 RSC;
(f) X. D. Liu, L. F. Zhang, Z. P. Cheng and X. L. Zhu, Chem. Commun., 2016, 52, 10850–10853 RSC;
(g) Z. C. Huang, L. F. Zhang, Z. P. Cheng and X. L. Zhu, Polymers, 2017, 9, 4 CrossRef;
(h) T. G. McKenzie, Q. Fu, M. Uchiyama, K. Satoh, J. Xu, C. Boyer, M. Kamigaito and G. G. Qiao, Adv. Sci., 2016, 3, 1500394 CrossRef PubMed.
- B. P. Fors and C. J. Hawker, Angew. Chem., Int. Ed., 2012, 51, 8850–8853 CrossRef CAS PubMed.
-
(a) J. Xu, K. Jung, A. Atme, S. Shanmugam and C. Boyer, J. Am. Chem. Soc., 2014, 136, 5508–5519 CrossRef CAS PubMed;
(b) J. Xu, K. Jung and C. Boyer, Macromolecules, 2014, 47, 4217–4229 CrossRef CAS.
-
(a) S. Shanmugam, J. Xu and C. Boyer, J. Am. Chem. Soc., 2015, 137, 9174–9185 CrossRef CAS PubMed;
(b) S. Shanmugam, J. Xu and C. Boyer, Chem. Sci., 2015, 6, 1341–1349 RSC;
(c) J. Xu, S. Shanmugam, H. T. Duong and C. Boyer, Polym. Chem., 2015, 6, 5615–5624 RSC;
(d) S. Shanmugam, J. Xu and C. Boyer, Angew. Chem., Int. Ed., 2016, 55, 1036–1040 CrossRef CAS PubMed;
(e) S. Shanmugam, J. Xu and C. Boyer, Polym. Chem., 2016, 7, 6437–6449 RSC.
- J. Zhu, X. L. Zhu, Z. P. Cheng, F. Liu and J. M. Lu, Polymer, 2002, 43, 7037–7042 CrossRef CAS.
- M. Martiny, E. Steckhan and T. Esch, Chem. Ber., 1993, 126, 1671–1682 CrossRef CAS.
- E. Arceo, E. Montroni and P. Melchiorre, Angew. Chem., Int. Ed., 2014, 53, 12064–12068 CrossRef CAS PubMed.
- Q. Michaudel, V. Kottisch and B. P. Fors, Angew. Chem., Int. Ed., 2017 DOI:10.1002/anie.201701425.
-
(a) T. G. McKenzie, Q. Fu, E. H. H. Wong, D. E. Dunstan and G. G. Qiao, Macromolecules, 2015, 48, 3864–3872 CrossRef CAS;
(b) B. Wenn and T. Junkers, Macromolecules, 2016, 49, 6888–6895 CrossRef CAS.
- N. Corrigan, S. Shanmugam, J. Xu and C. Boyer, Chem. Soc. Rev., 2016, 45, 6165–6212 RSC.
-
(a) L. J. Bai, L. F. Zhang, J. L. Pan, J. Zhu, Z. P. Cheng and X. L. Zhu, Macromolecules, 2013, 46, 2060–2066 CrossRef CAS;
(b) J. L. Pan, L. F. Zhang, L. J. Bai, Z. B. Zhang, H. Chen, Z. P. Cheng and X. L Zhu, Polym. Chem., 2013, 4, 2876–2883 RSC.
|
This journal is © The Royal Society of Chemistry 2017 |
Click here to see how this site uses Cookies. View our privacy policy here.