DOI:
10.1039/C7RA03007J
(Paper)
RSC Adv., 2017,
7, 19849-19855
Magnetically recyclable self-assembled thin films for highly efficient water evaporation by interfacial solar heating†
Received
13th March 2017
, Accepted 23rd March 2017
First published on 4th April 2017
Abstract
Magnetic microspheres including Fe3O4, MnFe2O4, ZnFe2O4, and CoFe2O4 have been synthesized via a simple solvothermal method followed by surface hydrophobization with 1H,1H,2H,2H-perfluorooctyltrichlorosilane. The hydrophobic magnetic microspheres can self-assemble into a thin film under simulated solar light irradiation and float on the surface of water. The formed film was used as photothermal material for water evaporation based on a new concept of interfacial solar heating. The water evaporation efficiency was significantly enhanced by the Fe3O4 thin film, and is about 1.4, 1.7 and 2.2 times higher than that without the formation of a Fe3O4 thin film, Fe3O4 uniformly dispersed in water, and water evaporation itself, respectively. The temperature gradient distributions from the surface to the bottom of the water directly demonstrated the advantage of interfacial solar heating for water evaporation. We believe that the water evaporation efficiency with the magnetic thin film is mainly due to the high light absorption, rapid heat transfer and good solid–liquid adhesion performance. In addition, the hydrophobic magnetic microspheres also have advantages over other reported photothermal materials due to their easy recycling, non-toxicity, low dose, and low cost.
Introduction
More and more people in the world, especially in the Middle East, Africa, and some island countries, are suffering from a shortage of fresh water because of climate change, population growth, water resource pollution, etc.1,2 Sea water desalination has been labeled as the main solution to the water shortage since it can offer abundant fresh water for drinking and for industry use.3 In practical applications, two mature processes are widely used for sea water desalination, which are reverse osmosis (RO) and multi-stage flash (MSF) distillation.4 However, both of these desalination processes consume a large quantity of electrical energy resulting in a high water charge and a large emission of greenhouse gases.5 Furthermore, the growth of marine organisms may be affected or they may even be killed during the seawater intake process and high salinity seawater discharge process.6,7 In addition, these two desalination processes cannot be carried out in some remote and rural areas where electric power and centralized water desalination are still unavailable.
Recently, a new strategy named “Air–Water Interface Solar Heating” has been employed for seawater desalination.8,9 In this new desalination process, solar absorption materials float on the surface of seawater or brackish water, and only heat the water surface while avoiding uniformly heating the bulk water. Therefore, the evaporation efficiency will be significantly enhanced due to the high light-to-heat conversion rate. Up to now, solar absorption materials including Au nanoparticles, Al nanoparticles, carbon nanotubes, graphite, graphene, polypyrrole, etc.9–21 have been investigated for water evaporation based on the above new concept. However, photothermal materials are usually immobilized on some floating supporting materials, which results in a decrease of the surface-to-volume ratio and the inadequate utilization of these functional materials since part of the material surfaces is adhered to the supporting materials.22 In some cases, they may detach from the support since the immobilization is typically realized through physical adhesion. In addition, some of these solar adsorption materials are high-cost, toxic, and difficult to recycle. The dosage of the solar absorption materials used for solar evaporation is usually large or not given in some cases,8,20,23 which not only causes material wastage but also prevents comparison of solar evaporation efficiencies among reported solar absorption materials.
In this paper, we demonstrate the “Air–Water Interface Solar Heating” process for water evaporation using magnetic microspheres (Fe3O4, MnFe2O4, ZnFe2O4, and CoFe2O4) as the solar adsorption materials. The magnetic microspheres were surface modified with 1H,1H,2H,2H-perfluorooctyltrichlorosilane (PFOTS) so that they could float on the surface of water. After that, a thin film was assembled during the simulated solar light irradiation. The formation of the thin film with a low Fe3O4 dose significantly enhanced the water evaporation efficiency. Furthermore, we also demonstrated the new concept of interfacial solar heating for water evaporation by measuring the temperature from the surface to the bottom of the water. Finally, the recycling properties and chemical stability of the hydrophobic magnetic microspheres were also investigated.
Experimental
Materials
Iron(III) chloride (FeCl3, 97%) and PFOTS (97%) were purchased from Sigma-Aldrich Co, USA. Manganese(II) chloride (MnCl2, >98%), zinc(II) chloride (ZnCl2, >98%), cobalt(II) chloride (CoCl2, >99%), anhydrous sodium acetate (NaAc, >99%), polyethylene glycol (PGE, >99%), ethylene glycol (EG, >99%), ethanol, and n-hexane (>99%) were purchased from Shanghai Chemical Reagent Co, China. All of the reagents used were of analytical grade and used without further purification.
Synthesis of Fe3O4 and MFe2O4 (M = Mn, Zn, Co) microspheres
The Fe3O4 and MFe2O4 (M = Mn, Zn, Co) microspheres were synthesized via a simple solvothermal process, which has been reported elsewhere.24 Typically, to prepare the Fe3O4 microspheres, 0.811 g of FeCl3 was firstly dissolved in 40 mL of ethylene glycol (GE) to form a transparent solution, then 3.6 g of NaAc and 1.0 g of polyethylene glycol (PEG) were added to the above transparent solution. The mixture was stirred vigorously for 2 h and then transferred to a 50 mL teflon-lined stainless-steel autoclave. The autoclave was heated at 200 °C for 8 h and then cooled to room temperature. The black products were collected and washed with ethanol three times. The MFe2O4 (M = Co, Mn, Zn) microspheres were synthesized by the coprecipitation of M(II) and Fe(III) chlorides (the molar ratio of M2+/Fe3+ = 0.5). Typically, 0.811 g (5 mmol) of FeCl3 and 0.315 g (2.5 mmol) of MnCl2 were firstly dissolved in 40 mL of ethylene glycol to form a transparent solution, then the same synthesis process as for the preparation of the Fe3O4 microspheres was followed.
Hydrophobization of the magnetic microspheres
The as-prepared Fe3O4 and MFe2O4 (M = Mn, Zn, Co) magnetic microspheres were firstly washed with n-hexane 3 times, then transferred into 4 mL of n-hexane (containing 0.5% PFOTS). The mixture was sonicated for 20 min and dried in air at 60 °C for 4 h.
Characterization
The crystal structures of the samples were analyzed using a D/Max-RA X-ray diffractometer (Rigaku, Japan) with Cu Kα radiation (λ = 1.5418 Å). The morphologies and sizes of the samples were examined by a transmission electron microscope (TEM, a JEOL JEM1200EX microscope at an accelerating voltage of 100 kV). The BET surface areas and pore size distributions of the samples were measured by a nitrogen adsorption–desorption experiment (Quantachrome, ASIC-2 measuring instrument). The ultraviolet-visible-near-infrared (UV-Vis-NIR) diffuse reflectance spectra of the samples were characterized using a UV-Vis-NIR spectrophotometer system (U-4100, Hitachi Japan), carrying out absolute hemispherical measurements. The reference was the reflection of the blank BaSO4 sample. In order to test the hydrophobicity of the samples, small amounts of powder were pressed into a disc to measure the contact angle using an OCA20 contact angle measuring device (Dataphysics, Germany).
Water evaporation
Water evaporation experiments were carried out at a room temperature of 25 ± 1 °C and at an air humidity of ∼60%. The magnetic powder floated on the surface of 200 mL of water in a 250 mL beaker. Before the experiment, the magnetic powder floating on the surface of water was irradiated under a 300 W xenon lamp for 4 h to form a thin film. The beaker was then placed on an electronic balance to measure the weight of the evaporated water. A 300 W xenon lamp (CEL-HXF300, 15A, Beijing Jin Yuan Science and Technology Co., China, the wavelength spectrum and intensity can be found in Fig. S1, ESI†) was used as a solar light simulator. The light source was vertically fixed to the surface of the water at a distance of 5.5 cm. The water temperatures from the surface to the bottom were measured using a Type K-thermocouple and recorder (YUWESE, SSN-61). The concentrations of dissolved Fe3+ in the water during the evaporation process were determined using a PerkinElmer NexION 350Q ICP-MS Spectrometer.
Results and discussion
Characterization of magnetic microspheres
The XRD patterns of the as-prepared samples are shown in Fig. S2, ESI.† All of the diffraction peaks can be readily indexed to the cubic spinel structure of Fe3O4 (JCPDS 75-1609), MnFe2O4 (JCPDS 74-2403), ZnFe2O4 (JCPDS 22-1012), and CoFe2O4 (JCPDS 22-1086). No characteristic peaks of other impurities were detected in the XRD patterns, indicating the high purity of all of the samples. The morphologies and sizes of the magnetic microspheres were characterized using a transmission electron microscope (TEM), and the results are shown in Fig. 1. The solvothermal method leads to the complete formation of solid spherical structures, and the average particle sizes of the Fe3O4, MnFe2O4, ZnFe2O4 and CoFe2O4 microspheres are about 480 nm, 285 nm, 320 nm, and 135 nm, respectively. The surface areas, pore volumes and pore size distributions of the magnetic microspheres were investigated using N2 adsorption–desorption isotherms, the results are shown in Fig. S3, ESI.† The data concerning the BET surface areas, pore volumes and average pore sizes of the different magnetic microspheres are presented in Table S1, ESI.†
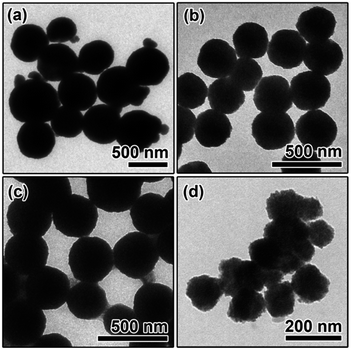 |
| Fig. 1 TEM images of (a) Fe3O4, (b) MnFe2O4, (c) ZnFe2O4, and (d) CoFe2O4 microspheres. | |
Fig. 2 shows the Ultraviolet-Visible-Near-Infrared (UV-Vis-NIR) absorption spectra of these four magnetic microspheres. For all of the samples, the photo-response from the ultraviolet (<400 nm) to the visible (400–760 nm) and near-infrared (760–2200 nm) spectral regions can be observed. Herein, the solar absorption of the Fe3O4, MnFe2O4, ZnFe2O4 and CoFe2O4 microspheres can be calculated using the following equation:25
|
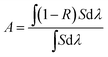 | (1) |
where
A is the solar absorption,
R is the reflectance of the sample,
S is the solar spectral irradiance (W m
−2 nm
−1), and
λ is the wavelength (nm). Here, (1 −
R)·
S represents the sample absorption of solar spectral irradiance. The solar absorption of the Fe
3O
4, MnFe
2O
4, ZnFe
2O
4 and CoFe
2O
4 microspheres was therefore calculated to be 86.05%, 82.20%, 88.78%, and 83.68%, respectively. It has been reported that when the nanoparticles absorb solar energy, the energy is dissipated into the surrounding water, otherwise the particles will absorb heat and melt.
17 In our case, almost none of the magnetic microspheres were dissolved in water during evaporation (which will be discussed later), indicating the high heat exchange between the water and the magnetic particles. The detailed solar absorptions in the ultraviolet to visible and infrared wavelength regions of all samples are displayed in Table S2, ESI.
†
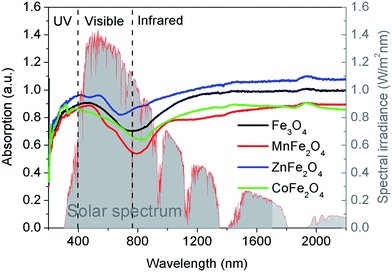 |
| Fig. 2 Solar spectrum and UV-Vis-NIR absorption spectra of the magnetic microspheres. | |
To achieve the self-floating capability, the magnetic microspheres were modified by hydrophobization with PFOTS. To test the hydrophobic properties, the magnetic powder was pressed into a disc (the same as the KBr pellet pressing method). After the hydrophobic modification of Fe3O4, it exhibited a high water contact angle of ∼146° (as shown in Fig. 3a). Furthermore, the water droplet still firmly adhered to the surface when we rotated the disc with a tilt angle of 60°, 90° or 180° (see Fig. 3b–d), which indicates the high adhesion properties of the fluoroalkylsilane modified Fe3O4 microspheres. According to Wenzel’s wetting behavior,26–28 the modified hydrophobic surface has a double wetting property, one is the high contact angle and the other is the high adhesion performance, which not only makes the material float on the surface of the water but also penetrates the surface of the material to achieve the maximum contact area and the maximum heat transfer. The water evaporation efficiency with the fluoroalkylsilane modified Fe3O4 microspheres will be enhanced due to Wenzel’s wetting behavior. In addition, the water contact angles of MnFe2O4, ZnFe2O4 and CoFe2O4 are 110°, 122°, and 120° (see Fig. S4, ESI†), respectively. Though the water contact angles are slightly less than that of Fe3O4, the materials are also hydrophobic.
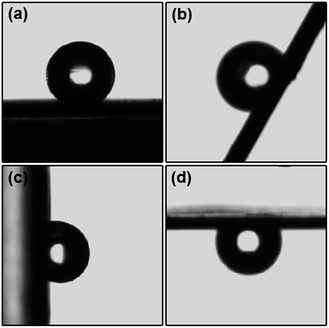 |
| Fig. 3 The shapes of a water droplet on the Fe3O4 discs at different tilt angles of (a) 0°, (b) 60°, (c) 90°, and (d) 180°. | |
Water evaporation
For the application of the hydrophobic magnetic microspheres in water evaporation, the hydrophobic magnetic microspheres were first floated on the surface of water (see Fig. 4 top). After irradiation under a xenon lamp for 4 hours, a thin film was assembled with the assistance of the water molecules’ thermal motion (see Fig. 4 bottom). The thickness of the thin film is composed of one or two Fe3O4 microspheres, therefore it can be calculated to be approximately 0.5–1.0 μm (see Fig. S5, ESI†). The formation of a thin film with magnetic microspheres will benefit light adsorption since the entire water surface is covered with this thin film. Therefore, the water evaporation efficiency will significantly increase due to the large area of the film, less aggregation of the particles, and the high-efficiency of the heat transfer. Fig. 5 shows the effect of the formation of the thin film on the water evaporation efficiency with the Fe3O4 microspheres. It can be clearly seen that the water evaporation efficiency with Fe3O4 with the formation of a thin film is significantly higher than that without the formation of a thin film. The water evaporation with the Fe3O4 microspheres with and without the formation of a thin film, and the Fe3O4 microspheres uniformly dispersed in the water, can be modeled by zero-order kinetics. The water evaporation reaction can be described simply by m − m0 = −kt, where m and m0 are the actual water mass at time t and initial water mass respectively, and k is the water evaporation efficiency. The zero-order kinetics equations and the water evaporation efficiency (k) of the different samples and processes are calculated in Table S3, ESI.† The water evaporation efficiency with the Fe3O4 thin film is about 1.4, 1.7, and 2.2 times higher than that without the formation of a thin film, Fe3O4 uniformly dispersed in water, and water itself, respectively. These results strongly prove the advantage of interfacial solar heating for water evaporation. We therefore conclude that the interfacial solar heating process for water evaporation is an efficient technique for future application in sea water or brackish water desalination.
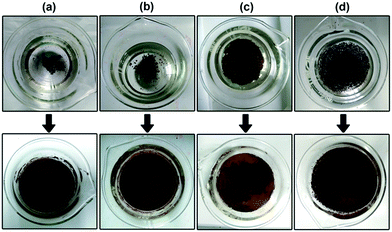 |
| Fig. 4 Digital photos of (a) 50 mg (0.25 g L−1), (b) 150 mg (0.75 g L−1), (c) 300 mg (1.5 g L−1), and (d) 600 mg (3.0 g L−1) of the Fe3O4 microspheres floating on the water surface (bottom) with and (top) without formation of a thin film. | |
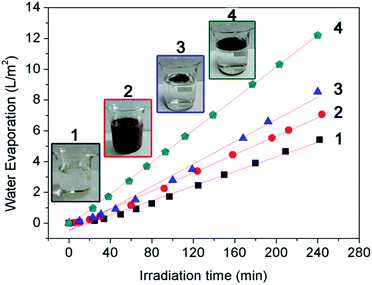 |
| Fig. 5 Water evaporation performances with 150 mg of the Fe3O4 microspheres floating on the water surface with and without the formation of a thin film, 150 mg of Fe3O4 uniformly dispersed in the water, and water itself evaporating under solar light irradiation. | |
Moreover, the water evaporation efficiencies with different dosages of the Fe3O4 microspheres floating on the water surface with and without the formation of a thin film were also investigated to double check the interfacial heating effect, and the results are shown in Fig. 6. Without the formation of a thin film, the water evaporation efficiencies obviously increased on increasing the dosage of the Fe3O4 microspheres. This is because the increased dosage of the Fe3O4 microspheres led to the larger light-adsorption area on the water surface (as shown in the top of Fig. 4). However, with the formation of a thin film, the water evaporation efficiencies remained almost unchanged on increasing the dosage of Fe3O4. This is because the addition of 50 mg of the Fe3O4 microspheres is enough for the formation a thin film with an area of 39.59 cm2 (the same as the area of the beaker mouth) on the surface of the water. Further increasing the addition of the Fe3O4 microspheres just leads to the overlap and aggregation of the surface. The water evaporation efficiencies with different dosages ranging from 50 mg to 600 mg of the Fe3O4 microspheres floating on the water surface with the formation of thin films are 0.05079, 0.05159, 0.05388, and 0.05731 L m−2 min−1, which are 1.6, 1.4, 1.3, and 1.1 times correspondingly higher than those without the formation of the thin films.
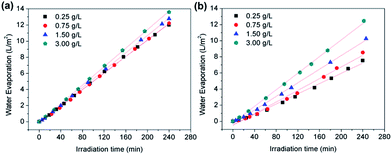 |
| Fig. 6 Water evaporation performances with different dosages of the Fe3O4 microspheres floating on the water surface (a) with and (b) without the formation of a thin film. | |
The high-efficiency heat transfer by interfacial solar heating was directly proven by measuring the temperature change during the water evaporation process. Fig. 7a shows the temperature change at the distance of 1.5 cm from the water surface in different evaporation processes (including water evaporation by Fe3O4 floating on the water surface with the formation of a thin film, Fe3O4 uniformly dispersed in the water, and water evaporating itself). It can be obviously seen that the temperature in the process of Fe3O4 floating on the water surface with the formation of a thin film possesses the fastest heating rate. The temperature rises up to 55.5 °C at the evaporation time of 2 h, which is 5.7 °C higher than that of the Fe3O4 microspheres uniformly dispersed in the water. In addition, to further confirm the interfacial heating effect, we vertically moved a temperature probe from the surface to the bottom of the water to measure the temperature change during the water evaporation process. Fig. 7b clearly displays the temperature distributions during water evaporation by the Fe3O4 microspheres floating on the water surface with the formation of a thin film. At the same irradiation time, the temperature increased with the decreasing distance from the water surface. For example, at the irradiation time of 2 h, the temperatures at the distances from the water surface of 0.7 cm, 1.5 cm, 2.0 cm, 4.0 cm, and 6.5 cm (bottom) are 66.3 °C, 55.5 °C, 47.1 °C, 40.1 °C and 40.0 °C, respectively, which strongly confirms the interfacial heating effect of only heating the water surface while avoiding the uniform heating of the bulk water.
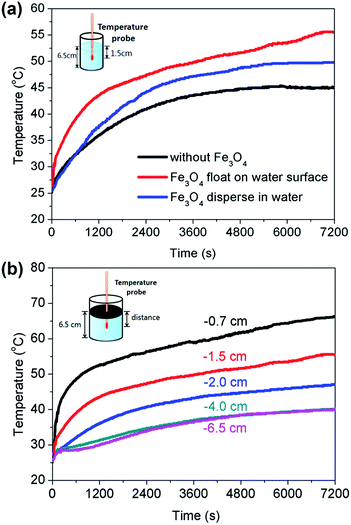 |
| Fig. 7 (a) The temperature change at the distance of 1.5 cm from the water surface in different evaporation processes; (b) the temperature distributions during water evaporation by the Fe3O4 microspheres floating on the water surface with the formation of a thin film. | |
To confirm the photothermal effect of the other three types of hydrophobic MFe2O4 (M = Mn, Zn, Co) microspheres, the water evaporation experiments were carried out with the addition of MFe2O4 (M = Mn, Zn, Co) with a dosage of 150 mg (0.75 g L−1), and the results are shown in Fig. 8. The zero-order kinetics equations and evaporation efficiencies are also displayed in Table S3, ESI.† The water evaporation efficiency follows the order of MnFe2O4 < ZnFe2O4 < CoFe2O4 < Fe3O4. Generally, the water evaporation efficiency can be influenced by the light adsorption capacity, porosity, water contact angle, and adhesion effect of the magnetic microspheres. Here, the Fe3O4 microspheres possess the best water evaporation efficiency due to their big water contact angle, good adhesion effect and good light adsorption capacity. By contrast, the MnFe2O4 microspheres possess the worst water evaporation efficiency because they have the smallest water contact angle and the worst light adsorption capacity.
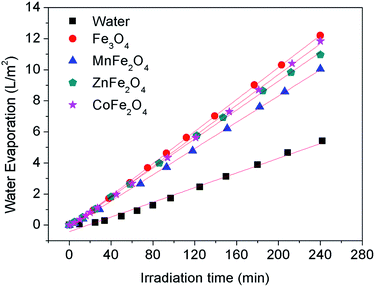 |
| Fig. 8 Water evaporation performance with different hydrophobic magnetic microspheres floating on the water surface with the formation of a thin film. | |
Cycling
Magnetic particles have advantages over other solar adsorption materials due to their convenient separation and recycling in liquid-phase reactions by applying external magnetic fields.29 Herein, we demonstrate the quick separation of the Fe3O4 microspheres using a 46 mm × 46 mm × 22 mm cuboid NdFeB magnet (as shown in Fig. 9a and b), in which the magnetic particles can be completely separated from the water surface within 10 seconds. To exploit the stability of the hydrophobic magnetic microspheres, the water evaporation efficiencies were monitored for ten cycles. A very slightly decreased water evaporation efficiency can be observed after ten cycles (as shown in Fig. 9c). Furthermore, the Fe3O4 microspheres still have a large water contact angle of 140° (see Fig. S6, ESI†) with the crystal structure unchanged (see Fig. S7, ESI†) after 10 cycles, which also confirms the high stability of the hydrophobic Fe3O4 microspheres. In addition, we also studied the chemical stability of the Fe3O4 microspheres by measuring the dissolved Fe3+ during the water evaporation process. The concentration of Fe3+ in the water was measured to be 0.37 mg L−1 (0.0248% of Fe3O4) in the first run, and gradually decreased to 0.11 mg L−1 (0.0075% of Fe3O4) in the fifth run. After 6 cycles, no Fe3+ could be detected. Firstly, we want to point out that the solar heating process is used to harvest fresh water, and the released ferric ions cannot be evaporated to the fresh water. Secondly, according to the Surface Water Quality Criteria set by the US Environmental Protection Agency (EPA), the concentration of iron for Class I is ≤1.0 mg L−1, which means that the maximum concentration of the released ferric ions in the reaction solution still satisfies the Surface Water Quality Criteria. The concentration of the released ferric ions in the condensed water is 0.024 mg L−1, which also satisfies the Surface Water Quality Criteria. Furthermore, PFOTS is a stable chemical, which cannot be decomposed completely by advanced oxidation processes (AOPs) such as UV irradiation, ozonation, TiO2-based photocatalysis, the persulfate oxidation process, etc.30–32 Our previous study also demonstrated that PFOTS cannot be decomposed under simulated sunlight irradiation with the light intensity of ∼1000 W m−2 for 4 days.33 These measurements demonstrated the high chemical stability of the hydrophobic Fe3O4 microspheres during the water evaporation process.
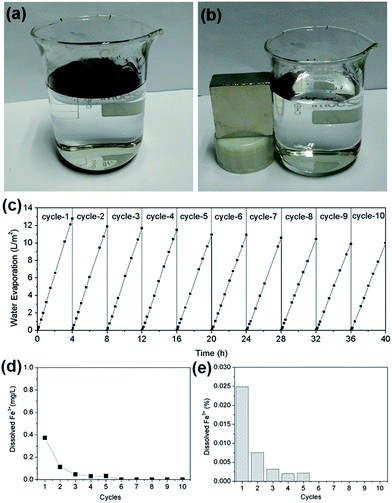 |
| Fig. 9 (a and b) Separation process of hydrophobic Fe3O4 microspheres. (c) 10 cycles of water evaporation with hydrophobic Fe3O4 microspheres. (d) The concentration and (e) the proportion of the dissolved Fe3+ after different cycles of water evaporation. | |
Conclusions
In summary, surface hydrophobized magnetic microspheres including Fe3O4, MnFe2O4, ZnFe2O4, and CoFe2O4 were used for water evaporation based on the new concept of interfacial solar heating. The self-assembly of a thin Fe3O4 film on the water surface significantly enhanced the water evaporation efficiency, which is 1.4, 1.7 and 2.2 times higher than that without the formation of a thin film, Fe3O4 uniformly dispersed in the water, and water itself evaporated under simulated solar light, respectively. The temperature distributions from the surface to the bottom of the water directly and strongly confirmed the interfacial heating effect. The enhanced water evaporation efficiency is mainly due to the high light-absorption capacity, rapid heat-transfer property and good solid–liquid adhesion performance. In addition, the magnetic microspheres have advantages over other reported photothermal materials due to their easy recycling, non-toxicity, good chemical stability, low dose, and low cost. Therefore, we believe our present work will offer a new approach to use photothermal materials for solar sea water or brackish water desalination.
Acknowledgements
This work was financially supported by the National Natural Science Foundation of China (No. 51108406), and the Important National Science and Technology Specific Projects (2012ZX07408-002, 2012ZX07403-004).
Notes and references
- W. Barnaby, Nature, 2009, 458, 282–283 CrossRef CAS PubMed.
- M. A. Montgomery and M. Elimelech, Environ. Sci. Technol., 2007, 41, 17–24 CrossRef PubMed.
- M. A. Shannon, P. W. Bohn, M. Elimelech, J. G. Georgiadis, B. J. Marinas and A. M. Mayes, Nature, 2008, 452, 301–310 CrossRef CAS PubMed.
- A. D. Khawaji, I. K. Kutubkhanah and J.-M. Wie, Desalination, 2008, 221, 47–69 CrossRef CAS.
- R. Semiat, Environ. Sci. Technol., 2008, 42, 8193–8201 CrossRef CAS PubMed.
- S. Lattemann and T. Höpner, Desalination, 2008, 220, 1–15 CrossRef CAS.
- N. Ahmad and R. E. Baddour, Ocean Coast Manag., 2014, 87, 1–7 CrossRef.
- Y. Zeng, J. Yao, B. A. Horri, K. Wang, Y. Wu, D. Li and H. Wang, Energy Environ. Sci., 2011, 4, 4074–4078 CAS.
- L. Zhang, B. Tang, J. Wu, R. Li and P. Wang, Adv. Mater., 2015, 27, 4889–4894 CrossRef CAS PubMed.
- K. Bae, G. Kang, S. K. Cho, W. Park, K. Kim and W. J. Padilla, Nat. Commun., 2015, 6, 10103 CrossRef CAS PubMed.
- L. Zhou, Y. Tan, J. Wang, W. Xu, Y. Yuan, W. Cai, S. Zhu and J. Zhu, Nat. Photonics, 2016, 10, 393–398 CrossRef CAS.
- Y. Ito, Y. Tanabe, J. Han, T. Fujita, K. Tanigaki and M. Chen, Adv. Mater., 2015, 27, 4302–4307 CrossRef CAS PubMed.
- Y. Liu, J. Chen, D. Guo, M. Cao and L. Jiang, ACS Appl. Mater. Interfaces, 2015, 7, 13645–13652 CAS.
- Y. Liu, S. Yu, R. Feng, A. Bernard, Y. Liu, Y. Zhang, H. Duan, W. Shang, P. Tao and C. Song, Adv. Mater., 2015, 27, 2768–2774 CrossRef CAS PubMed.
- J. Lou, Y. Liu, Z. Wang, D. Zhao, C. Song, J. Wu, N. P. Dasgupta, W. Zhang, D. Zhang and P. Tao, ACS Appl. Mater. Interfaces, 2016, 8, 14628–14636 CAS.
- O. Neumann, C. Feronti, A. D. Neumann, A. Dong, K. Schell, B. Lu, E. Kim, M. Quinn, S. Thompson and N. Grady, Proc. Natl. Acad. Sci. U. S. A., 2013, 110, 11677–11681 CrossRef CAS PubMed.
- O. Neumann, A. S. Urban, J. Day, S. Lal, P. Nordlander and N. J. Halas, ACS Nano, 2012, 7, 42–49 CrossRef PubMed.
- X. Wang, G. Ou, N. Wang and H. Wu, ACS Appl. Mater. Interfaces, 2016, 8, 9194–9199 CAS.
- Y. Wang, L. Zhang and P. Wang, ACS Sustainable Chem. Eng., 2016, 4, 1223–1230 CrossRef CAS.
- Y. Zeng, K. Wang, J. Yao and H. Wang, Chem. Eng. Sci., 2014, 116, 704–709 CrossRef CAS.
- H. Ghasemi, G. Ni, A. M. Marconnet, J. Loomis, S. Yerci, N. Miljkovic and G. Chen, Nat. Commun., 2014, 5, 4449 CAS.
- A. Haarstrick, O. M. Kut and E. Heinzle, Environ. Sci. Technol., 1996, 30, 817–824 CrossRef CAS.
- Z. Wang, Y. Liu, P. Tao, Q. Shen, N. Yi, F. Zhang, Q. Liu, C. Song, D. Zhang and W. Shang, Small, 2014, 10, 3234–3239 CrossRef CAS PubMed.
- H. Deng, X. Li, Q. Peng, X. Wang, J. Chen and Y. Li, Angew. Chem., Int. Ed., 2005, 44, 2782–2785 CrossRef CAS PubMed.
- T. Lin, C. Yang, Z. Wang, H. Yin, X. Lü, F. Huang, J. Lin, X. Xie and M. Jiang, Energy Environ. Sci., 2014, 7, 967–972 CAS.
- R. N. Wenzel, Ind. Eng. Chem., 1936, 28, 988–994 CrossRef CAS.
- S. Wang and L. Jiang, Adv. Mater., 2007, 19, 3423–3424 CrossRef CAS.
- L. B. Zhang, J. B. Wu, M. N. Hedhili, X. L. Yang and P. Wang, J. Mater. Chem. A, 2015, 3, 2844–2852 CAS.
- M. Ye, Q. Zhang, Y. Hu, J. Ge, Z. Lu, L. He, Z. Chen and Y. Yin, Chem.–Eur. J., 2010, 16, 6243–6250 CrossRef CAS PubMed.
- M. F. Rahman, S. Peldszus and W. B. Anderson, Water Res., 2014, 50, 318–340 CrossRef CAS PubMed.
- O. Quinones and S. A. Snyder, Environ. Sci. Technol., 2009, 43, 9089–9095 CrossRef CAS PubMed.
- M. Chen, S. Lo, Y. Lee, J. Kuo and C. Wu, J. Hazard. Mater., 2016, 303, 111–118 CrossRef CAS PubMed.
- M. Ye, J. Jia, Z. Wu, C. Qian, R. Chen, P. G. O’Brien, W. Sun, Y. Dong and G. A. Ozin, Adv. Energy Mater., 2017, 7, 1601811 CrossRef.
Footnote |
† Electronic supplementary information (ESI) available: Spectrum of the xenon lamp; XRD, N2 adsorption–desorption, and contact angles of MFe2O4 microspheres; XRD, and contact angles of Fe3O4 microspheres after 10 cycles; BET surface areas, total pore volume, average pore diameters, and proportion of light absorption of MFe2O4 microspheres; evaporation efficiencies of different water evaporation processes. See DOI: 10.1039/c7ra03007j |
|
This journal is © The Royal Society of Chemistry 2017 |
Click here to see how this site uses Cookies. View our privacy policy here.