DOI:
10.1039/C7RA01728F
(Paper)
RSC Adv., 2017,
7, 18293-18304
Ag3PO4/CoFe2O4 magnetic nanocomposite: synthesis, characterization and applications in catalytic reduction of nitrophenols and sunlight-assisted photocatalytic degradation of organic dye pollutants
Received
10th February 2017
, Accepted 21st March 2017
First published on 27th March 2017
Abstract
A novel magnetically recyclable Ag3PO4/CoFe2O4 nanocomposite (containing 30 wt%. CoFe2O4) was synthesized by a facile hydrothermal method. The composition and microstructure of the nanocomposite was fully characterized by X-ray diffraction (XRD), Fourier transform infrared spectroscopy (FTIR), UV-visible spectroscopy (UV-vis), field emission scanning electron microscopy (FESEM)-energy dispersive X-ray (EDX) spectroscopy, transmission electron microscopy (TEM), and a vibrating sample magnetometer (VSM). Thereafter, the catalytic performance of the Ag3PO4/CoFe2O4 nanocomposite was investigated. The Ag3PO4/CoFe2O4 nanocomposite showed high efficiency for the degradation of methylene blue (MB) and Rhodamine B (RhB) dyes under direct sunlight irradiation. The photocatalytic activity of Ag3PO4/CoFe2O4 under sunlight irradiation was almost 1.5 and 4.7 times as high as those of the pure Ag3PO4 and CoFe2O4, respectively. The enhancement of sunlight photocatalytic activity in Ag3PO4/CoFe2O4 should be assigned to the effective separation and transfer of photogenerated charges originating from the well-matched overlapping band-structures. Trapping experiments indicated that superoxide anion (˙O2−) radicals were the main reactive species for dye degradation in the present sonocatalytic system. A proposed mechanism for the enhanced photocatalytic activity is also discussed based on the experimental results. In addition, the catalytic activity of the nanocomposite in the reduction of nitrophenols by using NaBH4 was evaluated. The results showed that Ag3PO4/CoFe2O4 exhibited the best performance in the reduction of 4-nitrophenol (4-NP) and 2-nitrophenol (2-NP) and revealed 100% conversion into the corresponding amino derivatives within 24–46 min with rate constant equal to 0.0714 min−1 and 0.0329 min−1, respectively. Moreover, due to the existence of the CoFe2O4, the Ag3PO4/CoFe2O4 nanocomposite could be magnetically separated from the reaction mixture and reused without any change in structure.
1. Introduction
Solar energy is the most clean, abundant and renewable energy source. The energy from the sun that hits the earth for one hour is much more than that needed by human beings for one year.1,2 It is well-known that the ultraviolet (UV) region occupies only approximately 4% of the entire solar spectrum, while 43% of the energy is that of visible light.3,4 Therefore, the development of novel efficient photocatalysts, particularly visible light responsive catalysts, is necessary for the efficient utilization of solar energy in photocatalysis.5–7 Developing a novel photocatalyst with efficient visible-light absorption and excellent stability remains a great challenge.
Among various photoactive materials, silver orthophosphate (Ag3PO4) has attracted considerable attention and found to be an excellent photocatalyst in visible light region because of its superior semiconductor property for directly splitting water, degrading organic contaminants and photodecomposition of organic dyes.7,8 Ag3PO4 has a relatively narrow band gap (2.36–2.43 eV) and is thus active under visible-light irradiation (λ < 530 nm).9 Unfortunately, Ag3PO4 suffers from the structural stability issues because the photocatalytic process is usually accompanied by the transformation of Ag+ into Ag0 in the absence of a sacrificial reagent. However, previous investigations have demonstrated that combining two or more semiconductors to fabricate an appropriate composite structure may be a good strategy.10,11
To date, many efforts had been tried, and some Ag3PO4-based hybrid composite, such as Ag3PO4/WO3,12 Ag3PO4/CeO2,13 Ag3PO4/(Cr)–SrTiO3,14,15 Ag3PO4/In(OH)3,16 BiOCl/Ag3PO4,17 Ag3PO4/BiVO4,18 g-C3N4/Ag3PO4,19–21 Ag/Ag2S/Ag3PO4,22 Ag3PO4/ZnO,23 Ag3PO4/SnO2,24 Ag3PO4/TiO2,25,26 AgX/Ag3PO4 (X = Cl, Br, I),27,28 Ag3PO4/Nb2O5
29 and CdS/Ag3PO4
30 had been successfully synthesized, which showed enhanced photocatalytic stability and activity than pure Ag3PO4. But these composites are difficult to separate and recycle, seriously limiting their extensive application. Therefore, fabrication of well-defined and easy separated Ag3PO4-based photocatalysts from the suspended reaction system via a simple process remains to be a great challenge. To overcome this shortfall, coupling with magnetic materials is highly desirable. Magnetic based materials can be easily recovered by a magnet and can be reused for photocatalysis reaction several times without any appreciable reduction in photocatalytic efficiency.31,32 Although, pure magnetic materials are easily recovered, their photocatalytic activities are very weak. They usually take long time to degrade the organic pollutant. Therefore, it is desirable to couple the magnetic photocatalyst with photocatalyst having high photocatalytic efficiency. Such composite photocatalysts can exhibit good magnet-controlled recyclability as well as superior photocatalytic activity with improved stability. In this regard, cubic CoFe2O4 is known to have high magnetic performance as well as excellent chemical stability. CoFe2O4 nanoparticles themselves have a strong magnetic property, and therefore, CoFe2O4 based composites can be magnetically separable in a suspension by virtue of their own magnetic properties without introduction of additional magnetic particles.
Considering the above, in the present work we have synthesized magnetically recyclable Ag3PO4/CoFe2O4 nanocomposite by a simple hydrothermal route. The visible light photocatalytic activity of the as-synthesized Ag3PO4/CoFe2O4 nanocomposite was evaluated for the degradation methylene blue (MB) and Rhodamine B (RhB) dyes under natural sunlight irradiation. In addition, the catalytic activity of this magnetic nanocomposite for the reduction of nitrophenols was investigated. The recycle experiments and possible photodegradation mechanism in Ag3PO4/CoFe2O4 system were also proposed.
2. Experimental
2.1. Materials
Cobalt(II) nitrate hexahydrate (Co(NO3)2·6H2O, 98%), iron(III) nitrate nanohydrate (Fe(NO3)3·9H2O, 98%), silver nitrate (AgNO3, 98%), disodium hydrogen phosphate (Na2HPO4, 98.5%), sodium borohydride (NaBH4, 98.5%), 2-nitrophenol (99%), 4-nitrophenol (98%), methylene blue (99%) and Rhodamine B (99%) were obtained from Merck chemical company and used as received without further purification.
2.2. Synthesis of CoFe2O4 nanoparticles
In a typical synthesis, 1.72 g of iron(III) nitrate nanohydrate (Fe(NO3)3·9H2O) and 0.62 g cobalt (II) nitrate hexahydrate (Co(NO3)2·6H2O) were dissolved in 25 mL of water by magnetic stirring for 30 min. After that, the mixture was adjusted to a pH of 12.0 with 6 M NaOH solution and stirred for 60 min, yielding a homogeneous emulsion. The resulting mixture was transferred into a 50 mL Teflon-lined stainless steel autoclave and heated to 180 °C for 12 h. The reaction mixture was allowed to cool to room temperature and the precipitate was filtered, washed with distilled water five times, and dried in a vacuum oven at 60 °C for 12 h.
2.3. Synthesis of Ag3PO4/CoFe2O4 nanocomposite
The preparation of Ag3PO4/CoFe2O4 (30 wt%) nanocomposite was carried out as follows: in a typical experiment, 26 mg CoFe2O4 powder was added into 20 mL deionized water and sonicated for 10 min to get uniform dispersion. Then, 1.0 mL Na2HPO4 (0.15 mol L−1) and 3.0 mL AgNO3 (0.15 mol L−1) aqueous solutions were added into the suspension and sonicated for 3 h. The dispersed mixture was added to a Teflon-lined stainless steel autoclave for hydrothermal treatment at 160 °C for 3 h. Then, the reaction mixture was allowed to cool to room temperature and the precipitate was filtered, washed with distilled water three times, and dried in an oven at 80 °C for 6 h. The exact content of CoFe2O4 in the nanocomposite was also confirmed by using ICP-AES. The CoFe2O4 content measured was 29.45 wt% which is in agreement with the theoretical amount (30 wt%). For comparison, pure Ag3PO4 was also prepared under the same conditions without adding CoFe2O4.
2.4. Characterization techniques
The XRD patterns of the samples were obtained on an X-ray diffractometer (PANalytical/X'Pert Pro MPD) using Ni-filtered Cu Kα radiation (λ = 1.54059 Å) radiation FT-IR spectra were recorded on a Schimadzu system FT-IR 160 spectrophotometer in transmission mode from 4000 to 400 cm−1 using KBr pellets. UV-vis spectra of samples (photocatalysts, nitrophenols and dyes) were analyzed at room temperature using a CARY 100 double beam spectrophotometer operated at a resolution of 2 nm with quartz cells with path length of 1 cm in the wavelength range of 200 to 750 nm. UV-visible DRS of the photocatalysts samples were recorded with a Shimadzu UV-2450 spectrophotometer over the spectral range 200–700 nm. The shape and morphology of samples were observed by a MIRA3 TESCAN scanning electron microscope (SEM) equipped with a link energy-dispersive X-ray (EDX) analyzer. The particle size was determined by a LEO-912AB transmission electron microscope (TEM) at an accelerating voltage of 80 kV. TEM samples were prepared by dropping the ethanol dispersion on a carbon coated copper grid. Magnetic measurements were carried out at room temperature using a vibrating sample magnetometer (VSM, Magnetic Daneshpajoh Kashan Co., Iran) with a maximum magnetic field of 10 kOe. The content of CoFe2O4 in the nanocomposite was determined by inductively coupled plasma atomic emission spectroscopy (ICP-AES, model OEC-730).
2.5. Catalytic reduction tests
In order to study the catalytic performance of the as-synthesized Ag3PO4/CoFe2O4 nanocomposite in reductive processes, the reduction of 4-nitrophenol (4-NP) to 4-aminophenol (4-AP) by excess NaBH4 in aqueous solution was used as the model reaction. For the catalytic reduction tests, freshly prepared aqueous solution of NaBH4 (0.5 mL, 20 mM) was mixed with aqueous solution (3 mL, 0.2 mM) of 4-NP in the quartz cell (1.0 cm path length and 4 mL volume). The color of the solution immediately changed from yellow to colorless. Then, 5 mg of Ag3PO4/CoFe2O4 nanocatalyst was added into the solution. The progress of reduction was monitored by UV-vis spectrophotometry in a range of 200–550 nm, with cycling over an interval of 2 min at ambient temperature. The reduction of 2-nitrophenol (2-NP) to 2-aminophenol (2-AP) was also investigated under the same conditions.
2.6. Photocatalytic degradation tests
To evaluate the photocatalytic activity of the Ag3PO4/CoFe2O4 nanocomposite, the degradation of methylene blue (MB) and Rhodamine B (RhB) organics in water was studied under direct natural sunlight irradiation. The photocatalytic experiments were executed on the days of bright sunny light in between 10 am to 2 pm in the summer session of Khoramabad city, Lorestan province, western region of Iran and the average intensity of light measured was ∼185 mW cm−2 (CHY 332, Digital Light Meter). In a typical photocatalytic reaction, 25 mg of Ag3PO4/CoFe2O4 nanocomposite was add to 50 mL of an aqueous solution of dye with initial concentration (C0) of 15 mg L−1. The mixture was kept in the dark for 30 min under continuous stirring to achieve the adsorption–desorption equilibrium of dye on the photocatalyst surface. Photocatalytic degradation was carried out by illuminating the suspension under natural sunlight. The degradation of dyes was monitored by UV-vis spectroscopy at different time intervals. For comparison, the photocatalytic activity of pure Ag3PO4 (15 mg) and CoFe2O4 (10 mg) were also investigated under the same conditions.
Various scavengers, including p-benzoquinone (BQ; 5 mmol L−1), triethanolamine (TEA; 5 mmol L−1), isopropyl alcohol (IPA; 5 mmol L−1), KI (5 mmol L−1) and AgNO3 (Ag+; 0.5 mmol L−1), were added into the solution of MB to detect the active species generated in the photodegradation experimental process. The photocatalytic process was the same as that described in the above. To test the recyclability, the Ag3PO4/CoFe2O4 nanocomposite was separated with an external magnet after dye had been completely degraded and washed with deionized water three times before the next photocatalytic reaction.
3. Results and discussion
3.1. Characterization of Ag3PO4/CoFe2O4 nanocomposite
The XRD patterns of the as-prepared Ag3PO4, CoFe2O4, and Ag3PO4/CoFe2O4 nanocomposite are presented in Fig. 1. For the as-prepared Ag3PO4 sample in Fig. 1(a), it can be seen that all the diffraction peaks can be well indexed to a body-centered cubic phase (JCPDS no. 01-084-0192; space group, P
3n; a0 = 6.0095 Å) and no other features were observed. From the XRD Pattern of the as-prepared CoFe2O4 nanoparticles in Fig. 1(b), it is obvious that all the diffraction peaks match very well with standard data of CoFe2O4 (JCPDS no. 01-022-1086; space group, Fd
m; a0 = 8.3919 Å), and no trace of any impurity phase was found. As observed in Fig. 1(c), the XRD pattern of composite sample exhibits diffraction peaks corresponding to both Ag3PO4 and CoFe2O4 and no other impure peaks can be observed, indicating that the sample is composed of Ag3PO4 and CoFe2O4 and the Ag3PO4/CoFe2O4 composite has been successfully prepared.
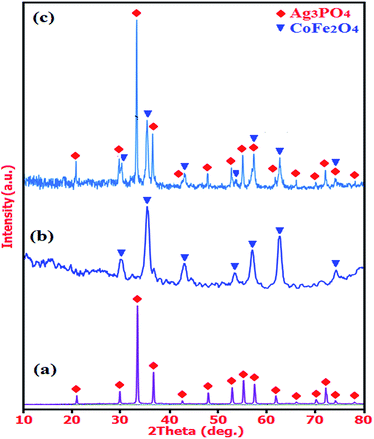 |
| Fig. 1 XRD patterns of (a) Ag3PO4, (b) CoFe2O4 and (c) Ag3PO4/CoFe2O4 nanocomposite. | |
FT-IR spectra of the as-prepared Ag3PO4, CoFe2O4, and Ag3PO4/CoFe2O4 nanocomposite are indicated in Fig. 2. For Ag3PO4 sample in Fig. 2(a), the sharp peaks at ca. 925 and 550 cm−1 are the characteristic asymmetric stretching and bending vibration of PO43− groups, respectively.33 In the case of CoFe2O4 (Fig. 2(b)), the two peaks in the range of 400 to 600 cm−1 are due to the Fe(III)–O and Co(II)–O bond of spinel-type oxide.34–37 In the FT-IR spectrum of the Ag3PO4/CoFe2O4 sample in Fig. 2(a), the representative PO43− group stretching vibration mode at 930 cm−1 is also observed besides the featured absorption bands of CoFe2O4 in the 400–600 cm−1 range. This is a good proof that Ag3PO4/CoFe2O4 nanocomposite was formed in the present study, as evidenced by the above XRD results. In all samples, the peaks at 1635 and 3350 cm−1 are attributed to the typical stretching vibrations of –OH group of adsorbed water.
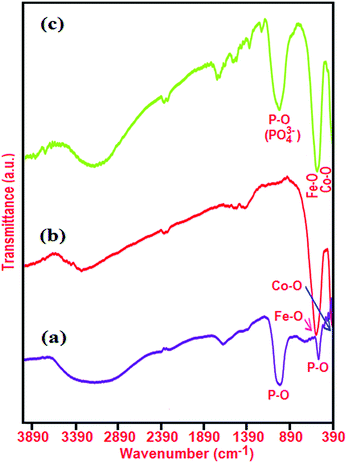 |
| Fig. 2 IR spectra of (a) Ag3PO4, (b) CoFe2O4 and (c) Ag3PO4/CoFe2O4 nanocomposite. | |
Further investigation was carried out by energy dispersive X-ray spectroscopy (EDX) to characterize the composition of the as-prepared Ag3PO4/CoFe2O4 nanocomposite as shown in Fig. 3. It can be clearly seen that Co, O, Ag, Fe and P elements are all existed in the product, which is consistent with the results obtained from XRD patterns. The inset of Fig. 3 shows a representative SEM image of the nanocomposite with corresponding EDX elemental mappings. Brighter area in the elemental map indicates a higher concentration of the corresponding element in that area. Different elements were shown in different colors in order to identify their positions within the nanomaterials. As presented in the inset of Fig. 3, the corresponding elemental mappings distribution show the existence of Ag, Co, Fe, P and O. From the maps, it can be seen that the elements are uniformly distributed over the nanocomposite, confirming the homogeneity of the sample.
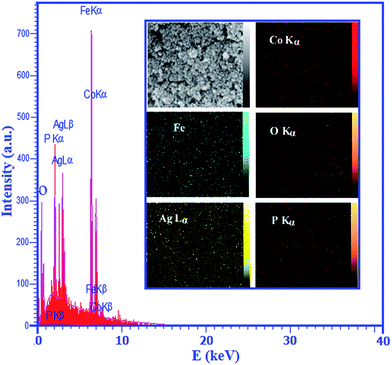 |
| Fig. 3 EDX analysis of the Ag3PO4/CoFe2O4 nanocomposite. The inset shows the corresponding elemental mappings of the nanocomposite. | |
It is well known that UV-vis diffuse reflectance spectroscopy is an important characterization technique for semiconductor photocatalysts. The UV-vis diffuse reflectance spectra of the as-prepared Ag3PO4, CoFe2O4 and Ag3PO4/CoFe2O4 composite were measured and the results are shown in Fig. 4. It can be seen clearly that the pure Ag3PO4 and CoFe2O4 show absorption bands with absorption edges at ca. 530 and 500 nm, respectively (Fig. 4(a), curves i and ii). However, after coupling Ag3PO4 with CoFe2O4, the obtained nanocomposite material also exhibited the band with absorption edge even above 530 nm (Fig. 4(a), curve iii). Additionally, it is noted that the absorption intensity of the Ag3PO4/CoFe2O4 suspension was mainly enhanced in the visible region compared to that of the Ag3PO4, which indicates that the ability of Ag3PO4/CoFe2O4 to absorb visible light was increased. For the Ag3PO4/CoFe2O4 nanocomposite, in addition to the absorption band of Ag3PO4, the adsorption band of CoFe2O4 also appeared. An obvious red shift in the absorption edge of Ag3PO4/CoFe2O4 also occurs, in contrast to Ag3PO4. The band gap energy (Eg) of samples can be deducted from the formula:38 (αhν)1/2 = B(hν − Eg), where α, ν, and B are absorption coefficient, light frequency and proportionality constant, respectively. The (αhν)2 versus hν curve for the Ag3PO4, CoFe2O4 and Ag3PO4/CoFe2O4 are shown in Fig. 4(b). The value of hν extrapolated to α = 0 gives the absorption band gap energy. From (Fig. 4(b), curves i and ii), the band gap energies for the pure Ag3PO4 and CoFe2O4 were estimated to be 2.36 and 1.86 eV respectively, which is in agreement with the results reported previously,39,40 On the other hand, the band gap energy of the Ag3PO4/CoFe2O4 nanocomposite was found to be 2.18 eV, indicating that the introduction of CoFe2O4 decreases the Eg of Ag3PO4. Furthermore, the decrease of Eg upon composite formation confirms electronic coupling between Ag3PO4 and CoFe2O4. The visible or sunlight photocatalytic activity of Ag3PO4/CoFe2O4 could be attributed to the existence of this red shifted broad band.
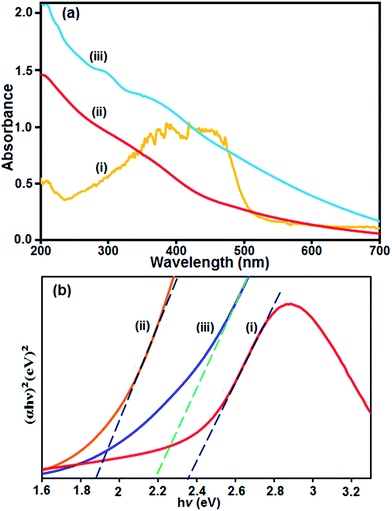 |
| Fig. 4 (a) UV-vis absorption spectra of (i) Ag3PO4, (ii) CoFe2O4, and (iii) Ag3PO4/CoFe2O4 nanocomposite. (b) The curve of (αhν)2 versus (hν) for (i) Ag3PO4, (ii) CoFe2O4 and (iii) Ag3PO4/CoFe2O4 nanocomposite. | |
The shape and size of the Ag3PO4/CoFe2O4 particles were analyzed by TEM and the images are shown in Fig. 5. As can be seen in Fig. 5(a–c), the obtained nanocomposite was formed mainly from cube-like particles. In fact, Ag3PO4 contains a cubic like structure with the lengths of 10–30 nm while CoFe2O4 shows a sphere-like shape. Furthermore, the high magnification TEM image in Fig. 5(d) indicates that the dark particles of CoFe2O4 with size around 10–25 nm are loaded on the surface of bright Ag3PO4 plates. As deduced from the TEM analysis, the particle size distribution was narrow, ranging from 10 to 30 nm, and the mean particle diameter was ∼20 nm. These results were consistent with the average particle size calculated by the Debye–Scherer formula from the XRD pattern.
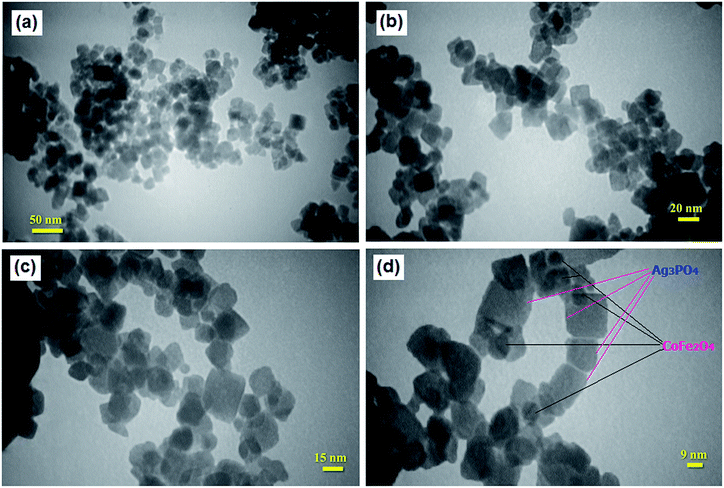 |
| Fig. 5 TEM images of the Ag3PO4/CoFe2O4 nanocomposite. | |
Fig. 6 shows the magnetic hysteresis of CoFe2O4 and Ag3PO4/CoFe2O4 samples at room temperature under an applied magnetic field of ±10 kOe. It is obvious from Fig. 6, the hysteresis loops of samples are characteristic of ferromagnetic behavior. However, the magnetic saturation (Ms) of the Ag3PO4/CoFe2O4 is lower than that of the pure CoFe2O4. From curves in Fig. 6, the Ms values for CoFe2O4 and Ag3PO4/CoFe2O4 were found to be 63.36 and 27.44 emu g−1, respectively. In general, Ms of samples mainly depends on the content of magnetic component.41 The content of magnetic component in the Ag3PO4/CoFe2O4 is less than that of pure CoFe2O4, hence, its Ms value is relatively low. However, compared with the non-magnetic Ag3PO4 catalyst, a magnetic Ag3PO4/CoFe2O4 composite catalyst can be separated from the heterogeneous reaction system by an external magnetic field as shown in the inset of Fig. 6.
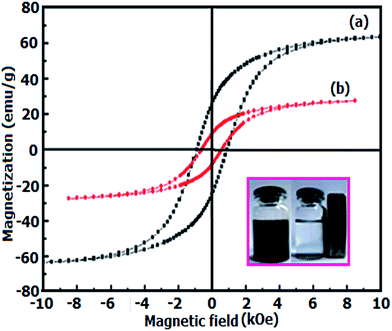 |
| Fig. 6 Room-temperature magnetization curve as a function of applied magnetic field for (a) pure CoFe2O4 and (b) Ag3PO4/CoFe2O4 nanocomposite. The photo inset shows magnetically separable of the nanocomposite. | |
3.2. Catalytic reduction of nitrophenols over Ag3PO4/CoFe2O4
Nitrophenols and their derivatives are some of the most refractory pollutants that occur in industrial waste water. They generally result from the production process of insecticides, synthetic dyes and herbicides.42,43 Therefore, the removal of nitrophenols from industrial waste water is crucial for environmental health. However, nitrophenols are biologically and chemically stable compounds and it is difficult to remove them by natural microbial degradation.44 Therefore it is necessary to develop environment friendly and clean techniques for the removal of such pollutants from industrial waste water.45–51 In this work, the catalytic activity of the Ag3PO4/CoFe2O4 nanocomposite for the reduction of 4-nitrophenol (4-NP) and 2-nitrophenol (2-NP) with sodium borohydride (NaBH4) was evaluated. The catalytic reduction process of 4-NP was monitored by UV-vis spectroscopy as shown in Fig. 7. It was seen that an absorption peak of 4-NP undergoes a red shift from 317 to 400 nm immediately upon the addition of aqueous solution of NaBH4, corresponding to a significant change in solution color from light yellow to yellow-green due to formation of 4-nitrophenolate ion. In the absence of catalyst, the absorption peak at 400 nm remained unaltered for a long duration, indicating that the NaBH4 itself cannot reduce 4-nitrophenolateion without a catalyst. In addition, the pure Ag3PO4 and CoFe2O4 nanoparticles show low activity in the 4-NP reduction, and therefore, they can not be regarded as effective catalysts for this reaction. However, in the presence of Ag3PO4/CoFe2O4 nanocomposite and NaBH4, the 4-NP was easily reduced. As can be seen in Fig. 7(a), the intensity of the absorption peak of 4-NP at 400 nm decreased gradually with time and after about 24 min it approximately disappeared. In the meantime, a new absorption peak appeared at 297 nm and increased progressively in intensity. This new peak is attributed to the typical absorption of 4-aminophenol (4-AP). This result suggests that the catalytic reduction of 4-NP exclusively yielded 4-AP, without any other side products. In the reduction process, the overall concentration of NaBH4 was 20 mM and 4-NP was 0.2 mM. Considering the much higher concentration of NaBH4 compared to that of 4-NP, it is reasonable to assume that the concentration of BH4− remains constant during the reaction. In this context, pseudo-first-order kinetics could be used to evaluate the kinetic reaction rate of the current catalytic reaction, together with the UV-vis absorption data in Fig. 7(a). The absorbance of 4-NP is proportional to its concentration in solution; the absorbance at time t (At) and time t = 0 (A0) are equivalent to the concentration at time t (Ct) and time t = 0 (C0). The rate constant (k) could be determined from the linear plot of ln(Ct/C0) versus reduction time in seconds. The rate constants (k) were determined from the slope of linear plots of ln(C0/C) versus time (minutes); its value were determined to be 0.0098, 0.0268, and 0.0714 min−1 for reduction 4-NP by CoFe2O4, Ag3PO4 and Ag3PO4/CoFe2O4, respectively (Fig. 7(b)).
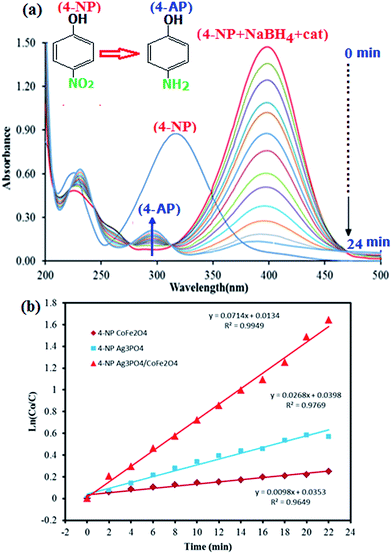 |
| Fig. 7 (a) UV-vis spectral changes during the reduction of 4-nitrophenol (4-NP, 0.2 mM) with NaBH4 (20 mM) over Ag3PO4/CoFe2O4 catalyst (5 mg), and (b) plot of ln(C0/Ct) against the reaction time. | |
Fig. 8 shows the UV-vis absorption spectra of the reduction of 2-nitrophenol by NaBH4 at various reaction times in the presence of Ag3PO4/CoFe2O4 nanocomposite. The observed peak at 414 nm for the 2-NP shows a gradual decrease in intensity with time and a new peak appeared at 291 nm indicating the formation of 2-aminophenol (2-AP). As shown in Fig. 8(b), it took 46 min for the complete reduction of 2-NP in the presence of Ag3PO4/CoFe2O4 nanocomposite (0.5 mg). As can be seen in Fig. 8(b), the corresponding k value was 0.0329 min−1 which is greater than of those of pure CoFe2O4 (0.0044 min−1) and Ag3PO4 (0.0148 min−1). The results indicated that Ag3PO4/CoFe2O4 exhibited considerably high activity for the reduction of nitrophenols with NaBH4 as the hydrogen donor.
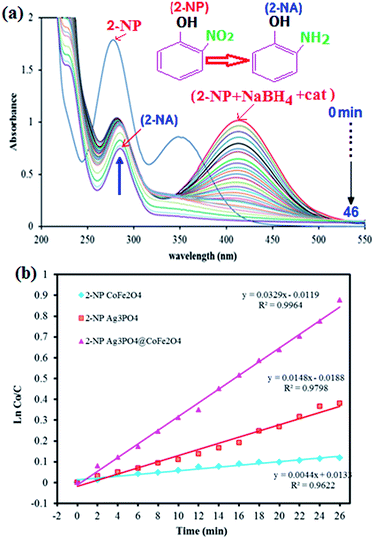 |
| Fig. 8 (a) UV-vis spectral changes during the reduction of 2-nitrophenol (2-NP, 0.2 mM) with NaBH4 (20 mM) over Ag3PO4/CoFe2O4 catalyst (5 mg), and (b) plot of ln(C0/Ct) against the reaction time. | |
3.3. Photocatalytic degradation of organic dyes over Ag3PO4/CoFe2O4
The photocatalytic degradation of organic pollutants has attracted considerable interest because of its potential to solve serious environmental problems, such as aesthetic pollution, printing/textile wastewater, toxicity and perturbation to aquatic life, as well as making use of the unlimited and sustainable energy from the sun. Various photocatalysts have been successfully developed for environmental remediation.52 Among them, TiO2 is one of the best because of its nontoxicity, acceptable stability and high photocatalytic activity.53 However, TiO2 is responsive only to UV light, which accounts for no more than 4% of the solar spectrum, greatly limiting its photocatalytic efficiency and practical applications. Developing a novel photocatalyst with efficient sunlight or visible-light absorption and excellent stability remains a great challenge. In this regard, Ag3PO4/CoFe2O4 nanocomposite prepared in this work can be an appropriate candidate. The photocatalytic activity of magnetic Ag3PO4/CoFe2O4 nanocomposite was evaluated by the degradation of methylene blue (MB) and Rhodamine B (RhB) dyes in aqueous solutions under direct sunlight irradiation and at room temperature. The UV-vis spectral changes of MB aqueous solution over Ag3PO4/CoFe2O4 photocatalyst are plotted in Fig. 9(a) as a function of irradiation time. It shows that the intensity of maximum absorption peak of MB at 663 nm decreases dramatically as time increases and nearly disappears within 90 min. For comparison purposes, we additionally performed the experiments on the degradation of MB with pure Ag3PO4 and CoFe2O4 samples under identical experimental conditions. As observed in Fig. 9(b), the degradation efficiency (C/C0) of MB over CoFe2O4, Ag3PO4 and Ag3PO4/CoFe2O4. Photocatalysts were found to be 47%, 84% and 98%, respectively, within 90 min sunlight irradiation. To understand the photocatalytic degradation kinetic of MB degradation, the pseudo-first-order model was used: ln(C0/C) = kt, where C0 and C are the dye concentrations before and after irradiation, respectively, k is the pseudo-first-order rate constant, and t is the reaction time. As shown in Fig. 9(c), the k values for the degradation of MB over CoFe2O4, Ag3PO4 and Ag3PO4/CoFe2O4 catalysts were determined to be 0.0052, 0.0175 and 0.0245 min−1, respectively. This finding indicates that the photocatalytic activity of Ag3PO4 could be improved by the incorporation of CoFe2O4 nanoparticles.
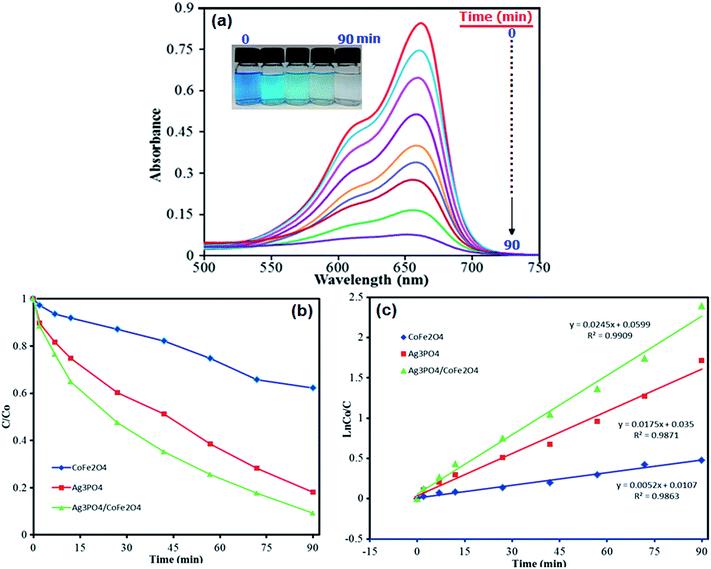 |
| Fig. 9 (a) UV-vis spectral changes of MB aqueous solution over Ag3PO4/CoFe2O4 under sunlight irradiation at different time intervals, (b) concentration changes of MB as a function of irradiation time. (c) Plot of ln(C0/C) vs. irradiation time. Conditions: [MB] = 50 mL, 15 mg L−1; [photocatalyst] = 25 mg/50 mL at 25 °C. | |
As shown in Fig. 10, similar behavior was observed for photocatalytic degradation of RhB dye in the presence of Ag3PO4/CoFe2O4 nanocomposite and under direct sunlight irradiation. It is obvious from Fig. 10(a) that the absorption peak of RhB at 554 nm decreased significantly as time increases, indicating the efficient degradation of this cationic dye in the presence of the Ag3PO4/CoFe2O4 nanocomposite. The degradation efficiency (C/C0) of RhB over CoFe2O4, Ag3PO4 and Ag3PO4/CoFe2O4 photocatalysts was found to be 47, 80 and 100%, respectively, after 90 min sunlight irradiation (Fig. 10(b) as shown in Fig. 10(c), the pseudo-first-order rate constant (k) values for the degradation of MB over CoFe2O4, Ag3PO4 and Ag3PO4/CoFe2O4 catalysts were determined to be 0.0059, 0.0149 and 0.0266 min−1, respectively.
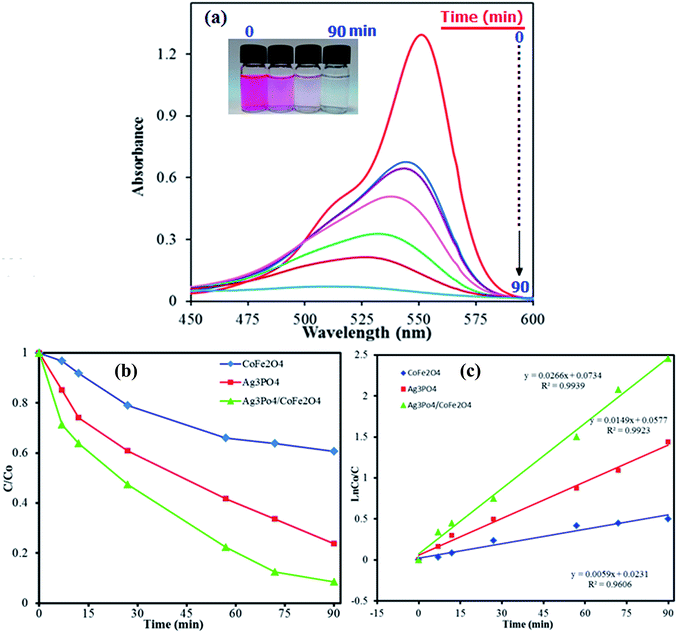 |
| Fig. 10 (a) UV-vis spectral changes of RhB aqueous solution over Ag3PO4/CoFe2O4 under sunlight irradiation at different time intervals, (b) concentration changes of RhB as a function of irradiation time. (c) Plot of ln(C0/C) vs. irradiation time. Conditions: [RhB] = 50 mL, 15 mg L−1; [photocatalyst] = 25 mg/50 mL at 25 °C. | |
In photocatalytic degradation, some active species, including hydroxyl radicals (˙OH), superoxide anion radicals (˙O2−), photogenerated holes (h+) and electrons (e−), are formed by light irradiation.54,55 To determine which active species play an important role in dye photodegradation using Ag3PO4/CoFe2O4 under sunlight irradiation, a series of experiments on quenching active species was conducted by adding individual scavengers to the photocatalytic reaction system. The different scavengers used in this study were BQ (˙O2− quencher), TEA (h+ quencher), IPA (˙OH quencher), KI (h+ and ˙OH quencher) and Ag+ (e− quencher) during MB degradation.
As a consequence of quenching, the photocatalytic reaction is partly inhibited and leads to low MB conversion. The extent of decrease caused by scavengers in the conversion indicated the importance of the corresponding reactive species.
The effects of the series of scavengers were evaluated by comparing the degradation extents of MB under sunlight irradiation. Fig. 11 shows that RhB photodegradation using Ag3PO4/CoFe2O4 is greatly suppressed after adding BQ as ˙O2− scavenger, which suggests that ˙O2− is the main reactive species in the photocatalytic process. When TEA, IPA or KI are added, the photodegradation activity of Ag3PO4/CoFe2O4 slightly decreases, which indicates that h+ and ˙OH play a minor but synergistic role. The addition of AgNO3 has a moderate effect, which implies that e− is reactive but is not the significant active species in the photocatalytic reaction. In summary, the main reactive species involved in MB degradation over Ag3PO4/CoFe2O4 is ˙O2−, with e−, h+ and ˙OH also being generated during the photocatalytic reaction under direct sunlight irradiation.
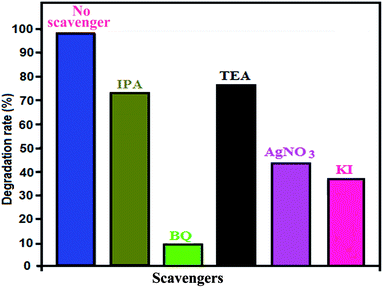 |
| Fig. 11 Effects of various active scavengers on the degradation of MB over Ag3PO4/CoFe2O4 nanocomposite under irradiation with sunlight. | |
The general principle for the enhanced photocatalytic performance of nanocomposite photocatalysts is that they have different electronic energy levels so that charge separation can be enhanced. In order to understand the band structure of Ag3PO4/CoFe2O4 nanocomposite, the potentials of the conduction band (CB) and valence band (VB) edges of Ag3PO4 and CoFe2O4 were calculated according to the Mulliken electronegativity theory, which is shown as follow in eqn (1) and (2):
where
EVB and
ECB stand for the conduction band and valence band edge potential respectively,
χ is the absolute electronegativity of the semiconductor, which is the geometric mean of the electronegativities of the constituent atoms,
56 and
Ec is the energy of free electrons on the hydrogen scale (about 4.5 eV
vs. NHE),
57 Eg is the band gap of semiconductor. The
χ value is calculated to be 5.92 eV for Ag
3PO
4 and 5.47 eV for CoFe
2O
4, respectively. The calculated
ECB and
EVB edge positions for Ag
3PO
4 are 0.49 and 2.85 eV, and for CoFe
2O
4 are 0.14 and 1.9 eV, respectively, which are close to previous reported values.
58,59
On the basis of the above results and the detection of active species in the photodegradation process, a possible photocatalytic mechanism for dye photodegradation using Ag3PO4/CoFe2O4 nanocomposite has been proposed as follows and illustrated in Fig. 12.60–64 Under irradiation with sunlight, both CoFe2O4 and the Ag3PO4 can absorb the photon energy and produce the electron–hole pairs (eqn (3)). Since, the flat band potential of CoFe2O4 is more negative than that of Ag3PO4, the electrons keep transferring from CoFe2O4 to Ag3PO4 until the Fermi level equilibrium of both is attained. Meanwhile, photoinduced holes from valence band (VB) of Ag3PO4 would be immigrated to the less positive VB of CoFe2O4 and further reacted with the absorbed H2O molecules or hydroxyl ion (OH−) to form active oxidants such as hydroxyl radicals (˙OH) (eqn (4)). At the same time, the accumulated electrons on the surface of Ag3PO4 reacts with absorbed oxygen to form oxidants such as superoxide ions (˙O2−) (eqn (5)). Therefore, the generated active species, such as ˙O2−, h+ and ˙OH, effectively react to degrade the dye molecules to CO2, H2O or other products (eqn (6)). The proposed mechanism of photocatalytic dye degradation using Ag3PO4/CoFe2O4 heterostructure can be described as follows:
|
Ag3PO4/CoFe2O4 + sunlight → eCB(Ag3PO4)− + hVB(CoFe2O4)+
| (3) |
|
hVB+ + H2O/OH− → ˙OH + H+
| (4) |
|
MB or RhB + ˙O2− (hVB+, ˙OH) → inorganic products (CO2, NO3−, SO42−, H2O, …)
| (6) |
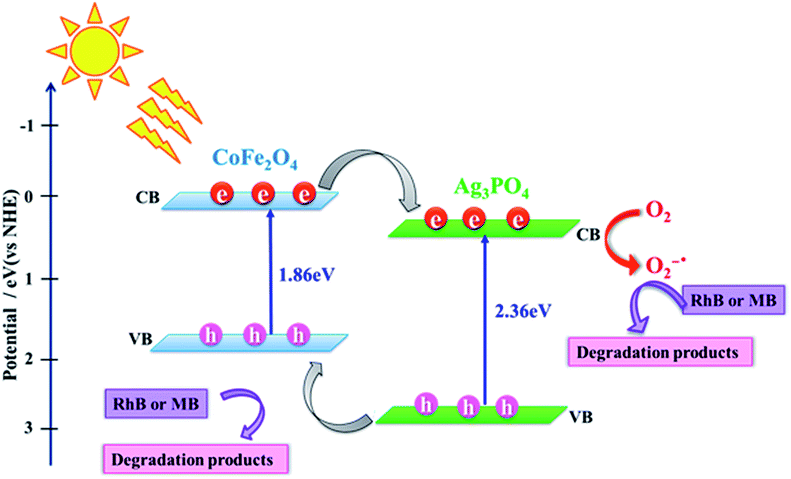 |
| Fig. 12 A proposed mechanism for photocatalytic degradation of dyes over Ag3PO4/CoFe2O4 nanocomposite under direct sunlight irradiation. | |
According to the above-suggested mechanism, electrons in the CB of CoFe2O4 can migrate to the CB of Ag3PO4 because the interfacial contact formed between CoFe2O4 and Ag3PO4 effectively hinders the recombination of electron–hole pairs and thus enhances photodegradation efficiency, compared to those of pure Ag3PO4 and CoFe2O4.
Furthermore, RhB and MB dyes demonstrate the strong absorption bands in the visible region at wavelengths of 552 and 663 nm. Therefore, they can undergo photosensitization under visible sunlight irradiation. The mechanism of indirect dye photosensitization induced degradation on the nanocomposite can be explained in the following procedure.65,66 First, the dye molecules (e.g. RhB) are absorbed on the surface of nanocomposite and then transferred into its excited state (RhB*) under sunlight irradiation (eqn (7)). Second, the electrons are injected from the RhB* into the conduction band of the Ag3PO4 where the electrons are trapped by the molecules' oxygen (eqn (8) and (9)). Third, the electrons in the CB of Ag3PO4 react with O2 to produce ˙O2− radicals for further degradation of RhB+˙ (eqn (10)). In fact, the Ag3PO4/CoFe2O4 is served only as an electron-mediator, which may be favorable for the effective separation and transfer of the injected electrons and cationic RhB radicals. Thus, the photo-generated electrons in the excited dyes and molecular oxygen play a crucial role in the indirect dye photosensitization pathway.
|
Dyes (e.g. RhB) + hν → dyes* (e.g. RhB*)
| (7) |
|
RhB* → RhB+˙ + eCB(Ag3PO4)−
| (8) |
|
RhB+˙ + ˙O2− → degradation products (CO2, H2O, …)
| (10) |
3.4. Reusability and photostability tests
To evaluate the reusability and photostability of the Ag3PO4/CoFe2O4 nanocomposite catalyst, recycling experiments were performed. It was separated from the reaction mixture after its first use in the degradation of MB. The recovered catalyst was found to be reusable for five runs without significant loss in activity. As shown in Fig. 13, nearly 7% of decrease could be observed after four times recycle. For each recycle, the centrifuge supernatant was collected and analyzed by Atomic Absorption Spectroscopy. It was shown that no silver metal signal during the course of the recycling reaction, confirming the stability of the catalyst.
 |
| Fig. 13 Recyclability of the Ag3PO4/CoFe2O4 nanocomposite in the photodegradation of MB under sunlight irradiation. | |
Furthermore, the structural stability the recovered Ag3PO4/CoFe2O4 photocatalyst was confirmed by XRD and FT-IR after five runs (Fig. 14). As shown in Fig. 14(a) and (b), XRD pattern and FT-IR spectrum of the recovered photocatalyst did not show significant change after the fifth run in comparison with those of the fresh catalyst (see Fig. 1(c) and 2(c)). These observations confirm that the structure of the Ag3PO4/CoFe2O4 nanocomposite is stable under the reaction conditions and was not affected by the reactants. The morphology of the recycled Ag3PO4/CoFe2O4 photocatalyst particles after several runs of catalytic degradation of MB was also analyzed. Fig. 14(d) and (c) show two representative TEM images of the Ag3PO4/CoFe2O4 photocatalyst after 5 cycles of catalytic reaction. It could be observed that the recovered catalyst almost kept initial size and morphology (see Fig. 6) even after five runs of catalytic reaction. The surface of individual cubic Ag3PO4 particles is still decorated with CoFe2O4, revealing the strong binding between the CoFe2O4 nanoparticles and cubic Ag3PO4 particles.
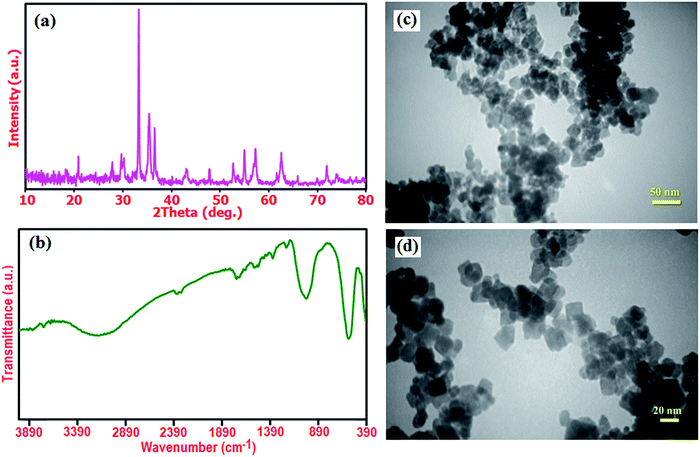 |
| Fig. 14 (a) XRD pattern, (b) FT-IR spectrum, (c) and (d) TEM images of the recovered Ag3PO4/CoFe2O4 photocatalyst after five runs of catalytic reaction. | |
4. Conclusions
In summary, we have presented a facile method for the synthesis of novel magnetic Ag3PO4/CoFe2O4 nanocomposite through the hydrothermal method. Compared with the pure Ag3PO4 and CoFe2O4, the Ag3PO4/CoFe2O4 exhibited superior activity reduction 2- and 4-NP. Also, the nanocomposite was used to degrade MB and RhB organic dyes pollutants under sunlight. Because the efficient separation of electron–hole pairs, the photocatalytic activity of Ag3PO4/CoFe2O4 is higher than that of pure Ag3PO4 and CoFe2O4. Furthermore, the Ag3PO4/CoFe2O4 nanocatalyst could be easily separated from wastewater for reuse by simply applying an external magnetic field. This study provides a green, low-cost, simple and rapid procedure for the degradation of organic dyes pollutants in aqueous wastewater solutions by using solar energy.
Acknowledgements
The authors gratefully acknowledge the Lorestan University Research Council and Iran Nanotechnology Initiative Council (INIC) for their financial supports.
References
- N. S. Lewis and D. G. Nocera, Proc. Natl. Acad. Sci. U. S. A., 2006, 103, 15729–15735 CrossRef CAS PubMed.
- N. S. Lewis, Science, 2007, 315, 798–801 CrossRef CAS PubMed.
- M. N. Chong, B. Jin, C. W. K. Chow and C. Saint, Water Res., 2010, 44, 2997–3027 CrossRef CAS PubMed.
- M. Ni, M. K. H. Leung, D. Y. C. Leung and K. Sumathy, Renewable Sustainable Energy Rev., 2007, 11, 401–425 CrossRef CAS.
- X. Y. Guo, C. F. Chen, S. Y. Yin, L. J. Huang and W. P. Qin, J. Alloys Compd., 2015, 619, 293–297 CrossRef CAS.
- B. Liu, Y. Fang, Z. Li and S. Xu, J. Nanosci. Nanotechnol., 2015, 15, 889–920 CrossRef CAS PubMed.
- P. V. Kamat, Chem. Rev., 1993, 93, 267–300 CrossRef CAS.
- Z. Yi, J. Ye, N. Kikugawa, T. Kako, S. Ouyang, H. Stuart-Williams, H. Yang, J. Cao, W. Luo, Z. Le, Y. Liu and R. Withers, Nat. Mater., 2010, 9, 559–564 CrossRef CAS PubMed.
- Y. Bi, S. Ouyang, N. Umezawa, J. Cao and J. Ye, J. Am. Chem. Soc., 2011, 133, 6490–6492 CrossRef CAS PubMed.
- W. Yao, B. Zhang, C. Huang, C. Ma, X. Song and Q. Xu, J. Mater. Chem., 2012, 22, 4050–4055 RSC.
- S. B. Rawal, S. D. Sung and W. I. Lee, Catal. Commun., 2012, 17, 131–135 CrossRef CAS.
- J. Q. Zhang, K. Yu, Y. F. Yu, L. L. Lou, Z. Q. Yang, J. W. Yang and S. X. Liu, J. Mol. Catal. A: Chem., 2014, 391, 12–18 CrossRef CAS.
- Z. M. Yang, G. F. Huang, W. Q. Huang, J. M. Wei, X. G. Yan, Y. Y. Liu, C. Jiao, Z. Wan and A. L. Pan, J. Mater. Chem. A., 2014, 2, 1750–1756 CAS.
- X. J. Guan and L. J. Guo, ACS Catal., 2014, 4, 3020–3026 CrossRef CAS.
- J. Guo, S. Ouyang, P. Li, Y. Zhang, T. Kako and J. H. Ye, Appl. Catal., B, 2013, 134, 286–292 CrossRef.
- J. J. Guo, S. X. Ouyang, H. Zhou, T. Kako and J. H. Ye, J. Phys. Chem. C, 2013, 117, 17716–17724 CAS.
- B. C. Cao, P. Y. Dong, S. Cao and Y. H. Wang, J. Am. Ceram. Soc., 2013, 96, 544–548 CrossRef CAS.
- C. J. Li, P. Zhang, R. Lv, J. W. Lu, T. Wang, S. P. Wang, H. F. Wang and J. L. Gong, Small, 2013, 9, 3951–3956 CrossRef PubMed.
- Y. H. Song, H. Xu, C. Wang, J. J. Chen, J. Yan, Y. G. Xu, Y. P. Li, C. B. Liu, H. M. Li and Y. C. Lei, RSC Adv., 2014, 4, 56853–56862 RSC.
- H. Katsumata, T. Sakai, T. Suzuki and S. Kaneco, Ind. Eng. Chem. Res., 2014, 53, 8018–8025 CrossRef CAS.
- F. J. Zhang, F. Z. Xie, S. F. Zhu, J. Liu, J. Zhang, S. F. Mei and W. Zhao, Chem. Eng. J., 2013, 228, 435–441 CrossRef CAS.
- J. T. Tang, W. Gong, T. J. Cai, T. Xie, C. Deng, Z. S. Peng and Q. Deng, RSC Adv., 2013, 3, 2543–2547 RSC.
- W. Liu, M. L. Wang, C. X. Xu, S. F. Chen and X. L. Fu, Mater. Res. Bull., 2013, 48, 106–113 CrossRef CAS.
- L. Zhang, H. Zhang, H. Huang, Y. Liu and Z. Kang, New J. Chem., 2012, 36, 1541–1544 RSC.
- C. Tang, E. Liu, J. Fan, X. Hu, L. Kang and J. Wan, Ceram. Int., 2014, 40, 15447–15453 CrossRef CAS.
- X. L. Ma, H. H. Li, Y. H. Wang, H. Li, B. Liu, S. Yin and T. Sato, Appl. Catal., B, 2014, 158, 314–320 Search PubMed.
- P. Amornpitoksuk and S. Suwanboon, Adv. Powder Technol., 2014, 25, 1026–1030 CrossRef CAS.
- P. Amornpitoksuk and S. Suwanboon, Adv. Mater. Res., 2014, 970, 29–32 CrossRef.
- R. Shao, X. Zeng, Z. Cao, H. Dong, L. Wang, F. Wang, J. Liu, Z. Li and Q. Liang, RSC Adv., 2015, 5, 102101–102107 RSC.
- Y. K. Jo, I. Y. Kim, J. M. Lee, S. Nahm, J. W. Choi and S. J. Hwang, Mater. Lett., 2014, 114, 152–155 CrossRef CAS.
- G. Xi, B. Yue, J. Cao and J. Ye, Chem.–Eur. J., 2011, 17, 5145–5154 CrossRef CAS PubMed.
- M. M. Ye, Q. Zhang, Y. X. Hu, J. P. Ge, Z. D. Lu, L. He, Z. L. Chen and Y. D. Yin, Chem.–Eur. J., 2010, 16, 6243–6250 CrossRef CAS PubMed.
- Y. M. Moustafa and K. El-Egili, J. Non-Cryst. Solids, 1998, 240, 144–153 CrossRef CAS.
- S. Q. Huang, Y. G. Xu, M. Xie, H. Xu, M. Q. He, J. X. Xia, L. Y. Huang and H. M. Li, Colloids Surf., A, 2015, 478, 71–80 CrossRef CAS.
- N. Adeela, K. Maaz, U. Khan, S. Karim, A. Nisar, M. Ahmad, G. Ali, X. F. Han, J. L. Duan and J. Liu, J. Alloys Compd., 2015, 639, 533–540 CrossRef CAS.
- N. Quandt, R. Roth, F. Syrowatka, M. Steimecke and S. G. Ebbinghaus, J. Solid State Chem., 2016, 233, 82–89 CrossRef CAS.
- R. Kurchania, D. Rathore and R. K. Pandey, J. Mater. Sci.: Mater. Electron., 2015, 26, 9355–9365 CrossRef CAS.
- Z. Jiao, Y. Zhang, H. Yu, G. Lu, J. Ye and Y. Bi, Chem. Commun., 2013, 49, 636–638 RSC.
- Z. G. Yi, J. H. Ye, N. Kikugawa, T. Kako, S. X. Ouyang, H. Stuart-Williams, H. Yang, J. Y. Cao, W. J. Luo, Z. S. Li, Y. Liu and R. L. Withers, Nat. Mater., 2010, 9, 559–564 CrossRef CAS PubMed.
- Y. Fu and X. Wang, Ind. Eng. Chem. Res., 2011, 50, 7210–7218 CrossRef CAS.
- I. Lascu, S. K. Banerjee and T. S. Berquó, Geochem., Geophys., Geosyst., 2010, 11, 1–22 CrossRef.
- F. K. Higson, Adv. Appl. Microbiol., 1992, 37, 1–19 CAS.
- M. J. Vaidya, S. M. Kulkarni and R. V. Chaudhari, Org. Process Res. Dev., 2003, 27, 202–208 CrossRef.
- A. H. Abbar, A. H. Sulaymon and M. G. Jalhoom, Electrochim. Acta, 2007, 53, 1671–1679 CrossRef CAS.
- Y. Du, H. L. Chen, R. Z. Chen and N. P. Xu, Appl. Catal., A, 2004, 277, 259–264 CrossRef CAS.
- K. Polat, M. Aksu and A. Pekel, J. Appl. Electrochem., 2002, 32, 217–223 CrossRef CAS.
- M. Nasrollahzadeh, S. M. Sajadi, A. Rostami-Vartooni and M. Khalaj, J. Mol. Catal. A: Chem., 2015, 396, 31–39 CrossRef CAS.
- M. Nasrollahzadeh, S. M. Sajadi, A. Rostami-Vartooni, M. Alizadeh and M. Bagherzadeh, J. Colloid Interface Sci., 2016, 466, 360–368 CrossRef CAS PubMed.
- A. Rostami-Vartooni, M. Nasrollahzadeh, M. Salavati-Niasari and M. Atarod, J. Alloys Compd., 2016, 689, 15–20 CrossRef CAS.
- M. Nasrollahzadeh, M. Bagherzadeh and H. Karimi, J. Colloid Interface Sci., 2016, 465, 271–278 CrossRef CAS PubMed.
- Q. Geng and J. Du, RSC Adv., 2014, 4, 16425–16428 RSC.
- M. J. Sevrin, C. R. J. Stephenson and J. J. Douglas, Org. Process Res. Dev., 2016, 20, 1134–1147 CrossRef.
- Y. Bai, I. Mora-Seró, F. D. Angelis, J. Bisquert and P. Wang, Chem. Rev., 2014, 114, 10095–10130 CrossRef CAS PubMed.
- K. Yu, S. Yang, C. Liu, H. Chen, H. Li, C. Sun and S. A. Boyd, Environ. Sci. Technol., 2012, 46, 7318–7326 CrossRef CAS PubMed.
- H. Zhang, X. Lv, Y. Li, Y. Wang and J. Li, ACS Nano, 2010, 4, 380–386 CrossRef CAS PubMed.
- X. Xin, J. Y. Lang, T. T Wang, Y. G. Su, Y. X. Zhao and X. J. Wang, Appl. Catal., B, 2016, 181, 197–209 CrossRef CAS.
- Y. G. Su, X. Xin, Y. F. Wang, T. T. Wang and X. J. Wang, Chem. Commun., 2014, 50, 4200–4202 RSC.
- M. Ge, N. Zhu, Y. Q. Zhao, J. Li and L. Liu, Ind. Eng. Chem. Res., 2012, 51, 5167–5173 CrossRef CAS.
- Y. I. Choi, Y. I. Kim, D. W. Cho, J. S. Kang, K. T. Leung and Y. Sohn, RSC Adv., 2015, 5, 79624–79634 RSC.
- G. Li and L. Mao, RSC Adv., 2012, 2, 5108–5111 RSC.
- D. Zhang and F. Zeng, J. Mater. Sci., 2012, 47, 2155–2161 CrossRef CAS.
- S. S. Patil, M. G. Mali, M. S. Tamboli, D. R. Patil, M. V. Kulkarni, H. Yoon, H. Kim, S. S. Al-Deyab, S. S. Yoon, S. S. Kolekar and B. B. Kale, Catal. Today, 2015, 260, 126–134 CrossRef.
- S. Zhang, J. Li, H. Niu, W. Xu, J. Xu, W. Hu and X. Wang, ChemPhysChem, 2013, 78, 192–199 CAS.
- D. Guo, R. Wen, M. Liu, H. Guo, J. Chen and W. Weng, Appl. Organomet. Chem., 2015, 29, 690–697 CrossRef CAS.
- J. Jiang, K. Zhao, X. Y. Xiao and L. Z. Zhang, J. Am. Chem. Soc., 2012, 134, 4473–4476 CrossRef CAS PubMed.
- J.-M. Wu and T.-W. Zhang, J. Photochem. Photobiol., A, 2004, 162, 171–177 CrossRef CAS.
|
This journal is © The Royal Society of Chemistry 2017 |
Click here to see how this site uses Cookies. View our privacy policy here.