DOI:
10.1039/C7RA00020K
(Paper)
RSC Adv., 2017,
7, 11362-11366
Facile fabrication of durable superhydrophobic SiO2/polyurethane composite sponge for continuous separation of oil from water†
Received
1st January 2017
, Accepted 6th February 2017
First published on 14th February 2017
Abstract
Superhydrophobic porous materials have great potential for oil absorption due to their good stability, high absorption capacity and recyclability. Herein, a simple one-step solution immersion method was employed to fabricate a robust superhydrophobic polyurethane sponge by anchoring hydrophobic SiO2 nanoparticles into a porous polyurethane frame. The durability of the resultant sponge was studied by repeated abrasion tests and immersion in concentrated acid and alkali solutions. After 100 abrasion cycles and strong acid/alkali immersion, the superhydrophobic polyurethane sponge still showed good repellence to water. Importantly, the obtained polyurethane sponge could be used for continuous separation of oil pollutants from the water surface quickly and effectively, making it a promising candidate material for use in oil-spill cleanups.
1. Introduction
With the expansion of oil production and transportation, there is increasing potential for oil spills from industrial accidents and leakage of oil from tankers or ships.1 Alongside the strengthening of environmental protection laws, the need to clean up frequent oil spills and the increasing amount of industrial oily wastewater and chemical leakage has become an increasing global challenge.2–5 As a result, there is a need to develop new materials that can effectively separate large amounts of oil from water.3 Superhydrophobic and superoleophilic materials are regarded as promising candidates for oil/water separation.4 However, most of the reported superhydrophobic materials are mechanically and chemically unstable, such that a slight mechanical abrasion will destroy the micro/nanoscale features that give rise to the roughness that is an essential requirement for superhydrophobicity. Moreover, mechanical contact may also leave impurities on surfaces, reducing their non-wetting properties.5,6 Recently, bulk materials that contain low-surface-energy microstructures have been regarded as good candidates for the design of damage-tolerant water-repellent surfaces. Bulk monoliths can be rendered rough throughout the structure if the uppermost layer is removed upon scrape abrasion, such that the fresh re-entrant surfaces of the bulk material created are also water repellent, making the water-repellent properties very long lasting.7–9
Polyurethane (PU) sponge is a porous polymer that has the special characteristics of high absorption, light weight, porosity, large surface area, low density and good elasticity.10 Recently, superhydrophobic and superoleophilic PU sponges were applied to the separation of oil and water mixtures.4 Ge et al.11 fabricated a superhydrophobic porous sponge, and applied external pumping on the sponge to achieve continuous collection of oil spills in situ from the water surface with high speed and efficiency. Wang et al.1 fabricated a robust superhydrophobic and superoleophilic carbon nanotube/poly(dimethylsiloxane)-coated PU sponge for the continuous absorption and expulsion of oils and organic solvents from water surfaces. Although different superhydrophobic sponges show good properties for oil absorption, some drawbacks still exist. For example, the oils or organic pollutants absorbed by such porous materials are usually removed using mechanical squeezing procedures,12 burning processes13 or solvent-washing methods,14 all of which are complex procedures requiring long production times, thereby limiting their practical applicability. In addition, the stability of the porous sponge toward corrosive liquids, including acidic and basic solutions, was not presented.4
Superhydrophobic and superoleophilic meshes, films and membranes have also attracted wide attention because of their capacity to separate oil and polluted water efficiently.15–18 However, these materials cannot be applied to oil spills because they require the polluted water to be accumulated first and then filtered. Therefore, there remains a need for novel materials for the continuous absorption and removal of oil pollutants from water with a high separation capacity. Herein, through a simple one-step solution immersion method, we fabricated bulk superhydrophobic PU sponge by anchoring hydrophobic SiO2 nanoparticles onto a porous frame. By combining the process with a vacuum pump system, the bulk PU sponge could be used for the continuous absorption and removal of oil pollutants from water surfaces, making the oil and water separation easier and faster. In addition, we demonstrate that the bulk superhydrophobic PU material shows stable super-repellency toward corrosive liquids, including acidic and basic solutions. Importantly, the sponge also showed good mechanical durability, and even more than 100 abrasion cycles or deep cuts could not diminish the material's superhydrophobicity.
2. Methods
2.1 Fabrication of hydrophobic SiO2 nanoparticles
Hydrophobic SiO2 nanoparticles used in this study were ionized and chemically modified with chlorotrimethylsilane (TMCS). In a typical synthesis,19 NaSiO3·5H2O (19.4 g) was dissolved in deionized water (300 ml), followed by the addition of 0.24 M NH4Cl solution (100 ml). The mixture solution was stirred for 3 h at 80 °C. Next, the white product was filtered and washed with deionized water. The obtained white product and TMCS (0.05 mol) were dissolved in ethanol (200 ml) and the resultant solution was refluxed for 3 h. After this time, the resulting product was filtered and dried in vacuum at room temperature for 24 h to yield TMCS-functionalized SiO2 nanoparticles.
2.2 Fabrication of superhydrophobic and superoleophilic polyurethane sponge
Hydrophobic SiO2 nanoparticles (0.18 g) and polydimethylsiloxane (PDMS; 0.05 ml) were dispersed in ethanol (60 g). Then a cleaned PU sponge (purchased from Hebei Warner Building Materials Co.) was immersed in the above solution for approximately 30 min, then removed and dried in an oven at 110 °C for ∼1 h. Herein, PDMS acted as an adhesive to adhere SiO2 nanoparticles to the PU sponge.
2.3 Characterization
The surface morphology of the sample was examined by field emission scanning electron microscopy (FESEM; JSM-6701F). Sessile water contact angle (CA) values were acquired using a DSA-100 optical contact-angle meter (Kruss Company Ltd, Germany) at room temperature (22 °C). The average CA value was determined by measuring the same sample at five different positions. The image of the water droplet on the surface was captured using a digital camera (NIKON, P600). The scratch test was conducted using a homemade scratch tester, as shown in Fig. 1. Sandpaper (1000 mesh) was chosen as the abrasion material and the superhydrophobic sponge was pressed against the sandpaper using steel discs (100 g), before the sandpaper was drawn along the surface at a speed of 0.14 cm s−1.
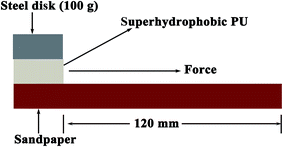 |
| Fig. 1 Illustration of abrasion test for the superhydrophobic sponges. | |
3. Results and discussion
Commercially available PU sponges were adapted to display robust superhydrophobic and superoleophilic properties via a simple technique. This involved immersion in an ethanol solution containing PDMS and TMCS-modified SiO2 nanoparticles. The superhydrophobic and superoleophilic SiO2/PU sponges had a water CA above 150° and an oil CA below 5°. Fig. 2a shows the water droplets deposited on the obtained PU surface. The high superhydrophobic nature of the surface caused the water droplets deposited to form almost perfect spheres, with a water CA 157 ± 1°. When the superhydrophobic PU was immersed in water (Fig. 2b), a shiny gray, mirror-like surface could clearly be seen due to the total reflectance of light at the air layer trapped on the surface. This trapped air effectively prevents wetting of the fabric surface under water.20,21 Note that the obtained bulk PU sponges possess water-repellent properties throughout their whole volume, and when scratched with a sharp object such as a knife, the cut interior surface also shows superhydrophobic properties, as shown in Fig. 2c and d. The water jet from a pipette was able to bounce off the cut PU sponge surface without leaving a trace, indicating the weak interaction between water and the surface (Fig. 2e). Fig. 2f shows a sectional series photograph of a water droplet bouncing on the sample surface. The droplet could bounce several times on the surface.
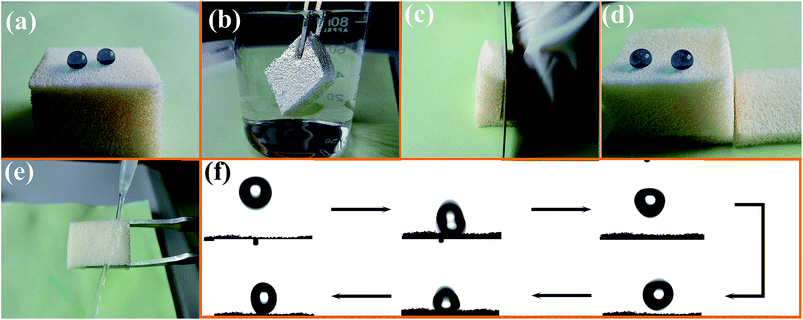 |
| Fig. 2 (a) Photograph of water droplets sitting on the as-prepared PU sponge surface (dyed blue). (b) Superhydrophobic PU immersed in water by an external force showing a silver mirror-like surface. (c) PU sponge cut using a knife. (d) Water droplets sitting on the cut interior surface. (e) A jet of water bouncing off the cut surface (water droplet was colored with methylene blue for ease of observation). (f) Series photograph of water droplet bouncing on the sample surface. | |
Fig. 3a and b show the surface morphology of the pristine PU as observed by scanning electron microscopy (SEM) to be composed of interconnected micropores of 150–500 μm diameter. The magnified image reveals the surface to be relatively smooth, hence being hydrophobic, with a water CA of approximately 123 ± 1° (inset in Fig. 3a). However, as shown in Fig. 3d, the incorporation of the densely distributed SiO2 particles on the PU surface gives rise to a nano-scaled roughness that results in superhydrophobicity, with a water CA of 153 ± 1°.
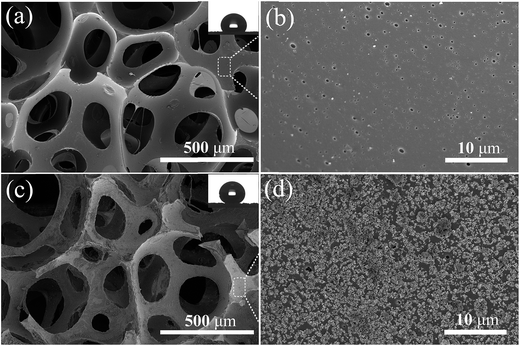 |
| Fig. 3 SEM images of the pristine PU (a and b) under different magnification; (c and d) images of PU coated with hydrophobic SiO2. Inserts are the optical images of a water droplet on the corresponding sponges. | |
Durability is an important factor which influences the real-world application of superhydrophobic surfaces. The major drawback of these nanostructured surfaces is their extremely fragile nature, especially against shearing. Hence the wear resistance of the SiO2-coated PU sponge against abrasion was assessed as shown in Fig. 1. The results show the superhydrophobic PU sponge to be extremely robust. After approximately 100 sandpaper abrasion cycles, the superhydrophobicity of PU was almost consistent with the original surface, with no change in the water CA measured before (153 ± 1°) or after (152 ± 1°) the abrasion cycles. This is despite SEM images showing that compared with the original surface before abrasion (Fig. 3c and d), the microstructure of the PU surface undergoes major changes in appearance after being scraped with sandpaper (Fig. 4). From the high magnification micrograph (Fig. 4b and d), it can be seen that after 50 and 100 cycles of sandpaper abrasion, respectively, the SiO2/PU composite surface retains the rough structures that are necessary for superhydrophobicity. The abrasion damage could not change the chemical composition; hence the composite surface remains water repellent, even after the outer layer is removed.
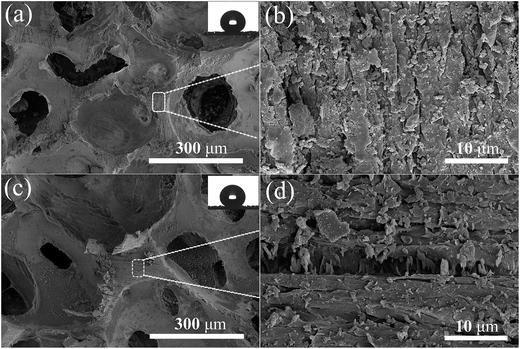 |
| Fig. 4 SEM images of superhydrophobic PU after abrasion with sandpaper. (a and b) 50 cycles; (c and d) 100 cycles. | |
Long-term durability against corrosive liquids is essential for devices used in oil/water separation owing to the complex nature of waste water from industry. Herein, the resistance of the superhydrophobic sponge to acids and alkalis was also evaluated. Fig. 5a and b show the water CA of the superhydrophobic sponge as a function of continuous contact time with strong acidic and alkaline solutions. From Fig. 5a, it can be seen that the water CA value decreases with immersion time in the acidic solution. Even after 24 min of immersion, the material surface still maintains its superhydrophobicity with a static CA of 150 ± 1°. With a further increase in immersion time to 30 min, the CA value decreases slightly to 147 ± 1°, indicating the partial degradation of the superhydrophobic state. For the alkaline solution, however, the SiO2 modified PU displays resistance but shows a decrease in a static CA to 147.4 ± 1° after 18 min of immersion.
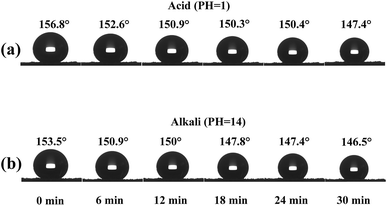 |
| Fig. 5 Variation in water contact angle of superhydrophobic PU as a function of corrosion time. In (a) acid and (b) alkali conditions. | |
It was possible to use the superhydrophobic PU sponge in conjunction with a vacuum system as a filter for the continuous absorption and removal of oil pollutants from water surfaces. As shown in Fig. 6a and b and video 1 in the ESI,† once a piece of treated sponge touches the paraffin oil, the oil penetrated into the superhydrophobic PU immediately and, in combination with a pump, allowed complete removal of the paraffin oil with no obvious oil left behind in the water. Fig. 6c shows the different absorption capacities of the superhydrophobic sponges to various solvents and oils. The absorption capacities were 14–27 times their own weight, depending on the density and viscosity of the oils and solvents. In addition, after being rinsed thoroughly with alcohol and dried, the as-prepared sponges could be reused for oil/water separation for many cycles.
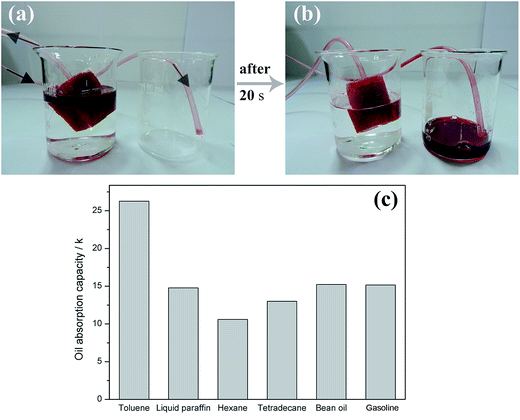 |
| Fig. 6 (a and b) Photographs of the continuous absorbing paraffin oil (dyed red) from water. (c) Absorption capacity of the superhydrophobic PU for different oils and organic solvents. The absorption capacity K shows the weight of each solvent that can be collected in the sponge per gram of sponge. | |
4. Conclusion
In summary, we have demonstrated a simple one-step solution immersion method for the fabrication of superhydrophobic and superoleophilic PU sponges, which can continuously collect oil in situ from a water surface with high speed and efficiency. The synthesized materials do not require expensive or environmentally hazardous fluorochemicals to achieve superhydrophobicity. The obtained bulk PU sponges possess water-repellent properties throughout their entire volume, and deep cuts with a knife do not diminish the superhydrophobicity. A scratch test using sandpaper and corrosion tests using strong acidic and alkaline solutions also show that the PU sponges possess excellent abrasion resistance and superhydrophobicity to withstand the harsh conditions encountered in many real-world applications. We expect that this low-cost process can be widely adopted for the design of robust water-repellent porous materials for the clean-up of large areas of oil spills on the water surface.
Acknowledgements
This work was supported by Joint Talent Cultivation Funds of NSFC-HN (Grant No. U1304529) and the National Nature Science Foundation of China (Grant No. 21403055). The EPSRC are thanked for funding (EP/G036675).
References
- C. F. Wang and S. J. Lin, ACS Appl. Mater. Interfaces, 2013, 5, 8861–8864 CAS.
- X. Y. Zhang, Z. Li, K. S. Liu and L. Jiang, Adv. Funct. Mater., 2013, 23, 2881–2886 CrossRef CAS.
- K. Q. Li, X. R. Zeng, H. Q. Li and X. J. Lai, RSC Adv., 2014, 4, 23861–23868 RSC.
- S. Y. Huang and J. F. Shi, Ind. Eng. Chem. Res., 2014, 53, 4888–4893 CrossRef CAS.
- T. Verho, C. Bower, P. Andrew, S. Franssila, O. Ikkala and R. H. A. Ras, Adv. Mater., 2011, 23, 673–678 CrossRef CAS PubMed.
- X. T. Zhu, Z. Z. Zhang, G. N. Ren, J. Yang, K. Wang, X. H. Xu, X. H. Men and X. Y. Zhou, J. Mater. Chem., 2012, 22, 20146–20148 RSC.
- X. Zhang, Y. G. Guo, H. Z. Chen, W. Z. Zhu and P. Y. Zhang, J. Mater. Chem. A, 2014, 2, 9002–9006 CAS.
- H. Jin, X. L. Tian, O. Ikkala and R. H. A. Ras, ACS Appl. Mater. Interfaces, 2013, 5, 485–488 CAS.
- X. T. Zhu, Z. Z. Zhang, X. H. Men, J. Yang, K. Wang, X. H. Xu and Q. J. Xue, J. Mater. Chem., 2011, 21, 15793–15797 RSC.
- S. Y. Huang, ACS Appl. Mater. Interfaces, 2014, 6, 17144–17150 CAS.
- J. Ge, Y. D. Ye, H. B. Yao, X. Zhu, X. Wang, L. Wu, J. L. Wang, H. Ding, N. Yong, L. H. He and S. H. Yu, Angew. Chem., Int. Ed., 2014, 53, 3612–3616 CrossRef CAS PubMed.
- Q. Zhu, Q. M. Pan and F. T. Liu, Facile removal and collection of oils from water surfaces through superhydrophobic and superoleophilic sponges, J. Phys. Chem. C, 2011, 115, 17464–17470 CAS.
- H. W. Liang, Q. F. Guan, L. F. Chen, Z. Zhu, W. J. Zhang and S. H. Yu, Angew. Chem., Int. Ed., 2012, 51, 5101–5105 CrossRef CAS PubMed.
- X. C. Dong, J. Chen, Y. M. Ma, J. Wang, M. B. Chan-Park, X. M. Liu, L. H. Wang, W. Huang and P. Chen, Chem. Commun., 2012, 48, 10660–10662 RSC.
- L. Feng, Z. Y. Zhang, Z. H. Mai, Y. M. Ma, B. Q. Liu, L. Jiang and D. B. Zhu, Angew. Chem., Int. Ed., 2004, 43, 2012–2014 CrossRef CAS PubMed.
- Y. Shang, Y. Si, A. Raza, L. Yang, X. Mao, B. Ding and J. Yu, Nanoscale, 2012, 4, 7847–7854 RSC.
- W. B. Zhang, Z. Shi, F. Zhang, X. Liu, J. Jin and L. Jiang, Adv. Mater., 2013, 25, 2071–2076 CrossRef CAS PubMed.
- X. Zhang, T. Geng, Y. G. Guo, Z. J. Zhang and P. Y. Zhang, Chem. Eng. J., 2013, 231, 414–419 CrossRef CAS.
- X. Zhang, P. Y. Zhang and Z. J. Zhang, Appl. Surf. Sci., 2012, 258, 7907–7912 CrossRef CAS.
- I. A. Larmour, S. E. J. Bell and G. C. Saunders, Angew. Chem., Int. Ed., 2007, 46, 1710–1712 CrossRef CAS PubMed.
- X. T. Zhu, Z. Z. Zhang, J. Yang, X. H. Xu, X. H. Men and X. Y. Zhou, J. Colloid Interface Sci., 2012, 380, 182–186 CrossRef CAS PubMed.
Footnote |
† Electronic supplementary information (ESI) available: Video showing the continuous absorption process of oil from water surface. See DOI: 10.1039/c7ra00020k |
|
This journal is © The Royal Society of Chemistry 2017 |
Click here to see how this site uses Cookies. View our privacy policy here.