DOI:
10.1039/C6RA27286J
(Paper)
RSC Adv., 2017,
7, 7227-7237
Development of a harvesting technique for large-scale microalgal harvesting for biodiesel production
Received
24th November 2016
, Accepted 13th January 2017
First published on 23rd January 2017
Abstract
Harvesting imposes a major constraint in microalgal downstream processes and cost-effective production of various high value products. In this study, different harvesting techniques were assessed under a single domain to identify the most suitable one for large-scale harvesting of green microalgae for biodiesel purpose. In the laboratory, Scenedesmus obliquus showed a flocculation efficiency of 83.2% at pH 12 after 1 h. Maximum flocculation efficiencies of 80.2, 95 and 91%, respectively were observed for FeCl3 at 200 mg L−1, alum at 250 mg L−1 and chitosan at 20 mg L−1 after 1 h. Electro-flotation at 24 V and dissolved air flotation with 1 mg L−1 of alum also revealed flocculation efficiencies of 99 and 91% respectively, after 1 h. For Chlorella vulgaris, similar trends were also observed. Under field trials with 1000 L algal suspension, electro-flotation required a voltage of 60 V to achieve a flocculation efficiency of ∼90% after 24 h. Dissolved air flotation also showed a flocculation efficiency of same magnitude after 7 h, but with 10 mg L−1 of alum. Thus electro-flotation required a profoundly higher voltage with increasing culture volume, whereas for dissolved air flotation a much higher concentration of alum was entailed. Both the processes also depicted a significantly longer time period to achieve the required flocculation efficiency. On the other hand, pH-induced flocculation was found to be the most pertinent one for large-scale set-ups, and emerged to be efficient, cost-effective and eco-friendly as the supernatant can be reused as growth medium by re-supplementing the nutrients and adjusting the pH.
1 Introduction
In the current scenario, microalgal lipids have received much attention as a green and renewable resource with the potential to be transesterified to biodiesel, an alternative to the conventional diesel fuel. However, microalgal suspension being very dilute in nature makes the biomass harvesting highly expensive.1 The energy requirement for separation of microalgae by centrifugation process can go up to 1 MJ kg−1 of dry biomass.2 Report also shows that the harvesting cost of microalgae may go up to 30% of the total cost of biomass production,3 thus playing a major role in the price hike of microalgal products. Therefore, development of a suitable harvesting technique for microalgae carries immense importance, which must be energy efficient, cost-effective and non-polluting in nature.
Microalgal biomass recovery faces many challenges. Due to the low biomass concentration relative to the volume of liquid of algal suspension, which typically varies between 0.3 to 5.0 g L−1 dry biomass,4,5 separation of biomass becomes a highly tedious task. For industrial applications, a high concentration, 300–400 g L−1 dry biomass is required, thus requiring a concentration up to 1000 fold. Moreover, the zeta potential of microalgal cells creates a stable suspension.6 There are other criteria which are to be considered in harvesting technologies along with the flocculation efficiency and the cost effectiveness. The most important one was the reusability of the culture medium, as it can reduce the water use along with diminishing the cultivation cost.
Various harvesting techniques are practiced these days, viz. centrifugation, filtration, gravity settling, flocculation, etc. Since centrifugation carries a high cost, it is not preferred for large scale installations.7 Flocculation has an added advantage over centrifugation as a large volume of cultures can be handled, and is both cost and energy efficient. Flocculation of microalgae can be achieved by the use of various inorganic salts, viz. Al2(SO4)3, AlCl3, Fe2(SO4)3, FeCl3, ZnSO4, ZnCl2, CaSO4, CaCl2, MgSO4, MgCl2, (NH4)2SO4, and NH4Cl,8 chitosan,9,10 cationic starch,11 etc. Flocculating microalgal species can also be used effectively to concentrate microalgae which are of non-flocculating in nature.12 Moreover, an electrolytic process of microalgal separation has also been found to be highly efficient.13 In this process, microalgal surface charges are neutralized as they move towards the anode, thereby allowing the microalgal cells to form aggregates followed by settling to the bottom. In recent years, it has been reported that dissolved air flotation (DAF) can be applied to harvest microalgae more efficiently than other settling methods.14 In this process, microalgal flocs are formed and are carried upwards with the air bubbles to form a layer at the surface, which can then be sieved out from the top.
A critical perusal of the available literature revealed that in spite of various harvesting techniques studied and are found efficient for laboratory scale cultures, none of those is defined yet for large-scale harvesting of microalgal biomass. Hence, in this investigation, a comparison of various existing harvesting techniques has been carried out with two microalgal species, viz. Scenedesmus obliquus and Chlorella vulgaris to find out an efficient method for microalgal harvesting feasible for large-scale exploitation, keeping in mind of non-polluting in nature and cost-effectiveness. This study also considers another most important aspect of the large-scale algal production system, i.e. the reuse of the supernatant after harvesting the microalgal biomass.
2 Materials and methods
2.1. Organisms and culture conditions
Axenic cultures of two chlorophycean microalgae, Scenedesmus obliquus (Trup.) Kutz. (SAG 276-3a, Gottingen, Germany) and Chlorella vulgaris (A 96, University of Madras, India) were used in the present investigation. The microalgal cultures were grown at 25 ± 2 °C; the photoperiod was maintained for 14 h at a light intensity of 75 μmol photon m−2 s−1 photosynthetically active radiation (PAR). Both the microalgae were cultured in the N 11 medium15 at pH 6.8. The N 11 medium constituents were 1.0 g L−1 KNO3, 0.083 g L−1 Na2HPO4·H2O, 0.052 g L−1 KH2PO4, 0.05 g L−1 MgSO4·7H2O, 0.01 g L−1 CaCl2·H2O, 1 mL Fe-EDTA stock (10 g chelate per liter) and 1 mL trace metal mix. The batch cultures were maintained in 250 mL Erlenmeyer flasks with 100 mL of N 11 medium. No air or CO2 was sparged to the cultures, and the cultures were hand shook 2–3 times daily to avoid settling. These batch cultures were referred to be control cultures.
For laboratory scale studies, the test microalgae were grown in 4 L capacity haffkine flasks (maximum working volume: 2 L) under the above culture conditions. The experiments were conducted in triplicate. As the age of the cultures plays a major role in flocculation, 20–21 days old cultures were always used for the experiments. Experiments were conducted by transferring the cultures into 1 L glass cylinders (height 45 cm, Borosil made) maintaining the same optical density (O.D. at 540 nm: 1.20 ± 0.02) at the initiation of the experiment. The initial biomass concentration was maintained at 1 g L−1. Outdoor large-scale cultivation was carried out in raceway ponds (14 × 4 × 0.75 m). 16
000 L culture volume was maintained in each raceway pond at 30 cm height, and the culture was aerated by the use of mechanical paddle wheels. This was used for large-scale studies. The age of the cultures (20–21 days) was also maintained for large-scale experiments.
2.2. Flocculation studies at laboratory
2.2.1. pH-Induced flocculation. Experiments were conducted by the addition of NaOH (1 N) and HCl (1 N) to adjust the pH at various levels (pH 2, 3, 5, 10 and 12), and kept a set of glass cylinders as control (pH 7.0). Following adjustment of pH, each glass cylinder was stirred rapidly at a rpm of 80 for a time duration of 2 min and with moderate stirring at 20 rpm for a time duration of 30 min. The flocs were left to settle without any agitation for a time period of 30 min.16 The set-up of the experiment was so provided to agitate the whole algal suspension uniformly by placing the stirrer blade at 2.5 cm from the bottom of the cylinder. After 1 h, the optical densities of the samples were recorded at 540 nm (this wavelength is not sensitive to change in the culture conditions or absorption shifts)17 by cautiously pipetting out samples from the cylinders at 10 cm height from the bottom. Flocculation efficiency was analysed as described in the later part of this section.
2.2.2. Flocculation by addition of inorganic chemicals. Inorganic compounds (alum and ferric chloride) were used at various concentrations to study their effects on flocculation. The concentrations were varied from a minimum value until the flocculation efficiency became constant. Stock solutions of both the compounds were prepared at a concentration of 10 g L−1. Aliquots of algal cultures were taken in 1 L cylinders, and the flocculants were added accordingly. Concentrations of each flocculant were used in triplicate, and the pH was maintained at pH 7.0. The pH of the solutions was maintained at neutral to observe the effects of the selected inorganic chemicals on flocculation without the influence of the solution pH. Each set of glass cylinders were agitated by the protocol mentioned above. The mixing of the algal samples was found to be necessary, as that will provide uniform mixing of the algal cells with the flocculating agents to form uniform suspension. A control set, without the addition of any flocculants, was also prepared to serve as the reference. Before addition of any flocculant, the optical density of the algal suspension was recorded at 540 nm, and was referred as the initial optical density. As described above, after addition of the flocculant, the solution was vigorously stirred, followed by mild stirring and finally left to settle. Flocculation efficiency was calculated by pipetting out the samples after 1 h, as detailed in the sub section 2.4.
2.2.3. Flocculation by addition of chitosan. The cationic polymer, chitosan was used to study its effect on flocculation. 5 g of chitosan was dissolved in 500 mL of acetic acid (0.1 M) followed by mild stirring and heating at about 55 °C overnight to form 10 g L−1 chitosan solution. The stock solution was then added to the experimental vessels at a range of 10–40 mg L−1. As mentioned above, the pH was maintained at neutral to see the effect of chitosan on flocculation of the test microalgae. The above mentioned flocculation protocol was employed, and the flocculation efficiency was calculated according to the sub section 2.4.
2.2.4. Dissolved air flotation (DAF). Dissolved air flotation experiments were carried out in glass vessels of dimension 30 × 12 × 18 cm, containing an algal suspension of 5 L. Two compressor pumps (model: Rocker 320, make: Tarson) were used in these experiments, one for sparging the air and another for sparging the water with/without flocculant (alum) from a plastic jar to the settling tank. Both the pumps were of 1/6 hp and had a maximum flow rate of 23 L min−1. The flow rate was controlled by the help of a controller and the saturation pressure was maintained at 75 psi with a recycle ratio of 15%. The pH of the experimental sets was normalized to 7.0 before the initiation of the experiments. The sparged air bubbles had a diameter range of 60–150 μm. The microalgal cells were carried upwards with the air bubbles. The flocculated biomass was sieved out from the top of the glass vessels. Flocculation efficiency was calculated according to the sub section 2.4.
2.2.5. Flocculation by electro-flotation. Electro-flotation experiments were conducted in glass vessels of dimension 60 × 30 × 30 cm, containing an algal suspension of 45 L from the raceway ponds. The voltage supply was 6, 12 and 24 V through copper and aluminum electrodes, maintaining a current supply of 1.5 A. The copper electrodes acted as cathodes were provided at the bottom of the vessels as meshes, to provide a better surface area for the production of micro bubbles to float the microalgal cells to the top of the vessel. The dimension of the copper mesh was 25 × 25 cm. The aluminum electrodes were used as anodes, and were placed on both sides of the vessels separated by a distance of 60 cm. Long aluminum pipes with length 30 cm and diameter 4 cm were used. The voltage supply was controlled with the help of a DC power supply by connecting the anode to the positive and cathode to the negative terminals of the power supply.The power consumption was calculated by the formula as given below18
where,
U is the voltage (V),
I the current (A),
t the time of the electroflotation (h),
V is the volume of the microalgal suspension (m
3),
ηa is the flocculation efficiency, and
Ci is the initial biomass concentration (kg m
−3).
2.3. Field-scale study
From the laboratory-scale experiments, three techniques, i.e. pH-induced flocculation by NaOH, DAF and electro-flotation were selected for field trials.
For field-scale flocculation experiments, 1000 L tanks were used. The tanks were filled with 20–21 days old S. obliquus and C. vulgaris cultures by directly pumping from the raceway ponds. NaOH solution was added sufficiently to increase the solution pH. The cultures were stirred by the help of a stainless steel stirrer driven by a 0.25 hp motor, Fig. 3a and b. The tank was fitted with the stirrer in the middle with 3 stainless steel stirrer blades of 30 cm length. The assembly was attached to the motor with the help of a shaft and were used for stirring. The length of the stirrer blades was so chosen to provide uniform stirring to the whole suspension. The rpm of the motor was controlled by a rpm regulator at 80 rpm for 2 min and 20 rpm for 30 min. The culture was left to settle for 30 min and the optical density was recorded. At the beginning of each experiment, the optical density was recorded at 540 nm, and was referred as the initial optical density. To observe the effects of pH on flocculation, pH was set to the best value recorded for the laboratory-scale studies.
For electro-flotation experiments, aluminum pipes were placed along the inner surface of the tanks as anodes. The dimension of the aluminum pipes was 90 cm in length and 4 cm in diameter. The length of the anode was so chosen that it is immersed completely in the algal solution to provide better electrical conductivity in the solution. The anode to anode distance was 10 cm, and seven aluminum pipes were used as anodes for each tank. Two copper plates of 1000 cm2 were placed at the bottom of each tank to act as cathodes. The large surface area of the copper plates provide better flow of microbubbles. The voltage was varied by a DC power supply (Metravi, India), and the current was maintained at 2 A (Fig. 4a and b).
Dissolved air flotation was carried out with the help of two compressor pumps of 80 psi pressure (Rockyvac 320, Tarsons, India) for each tank. One pump was connected to the finely perforated air sparger with micro openings for sparging micro bubbles into the experimental tank. The saturation pressure was maintained at 75 psi. The other pump was connected to a vessel containing the flocculant. The flocculant was sparged into the tanks slowly. The flocculated microalgae formed a layer at the top of the tank which were sieved out.
2.4. Determination of flocculation efficiency
Flocculation efficiency varies with the variation in the sampling height. Therefore, the sampling height was maintained at 10 cm from the bottom for all sets of experiments. For laboratory-scale studies, the cylinders were graduated with the help of a stainless steel ruler, and 10 cm height was marked along the side of the cylinders. At different time intervals, an adequate amount of supernatant was pipetted out from the top of the cylinder from the above-mentioned height. For large-scale experiments the sampling height was also maintained at 10 cm. The optical density was recorded in a Lambda 25S UV-VIS spectrophotometer (Perkin Elmer, USA) at a wavelength of 540 nm. The initial as well as all the observations down the time-course of study were recorded. The flocculation efficiency was determined as follows:
Flocculation efficiency (%) = (1 − A/B) × 100 |
where, A = final optical density at 540 nm, B = initial optical density at 540 nm.
2.5. Lipid extraction from algal samples
Bligh and Dyer19 protocol using chloroform and methanol as solvents was followed for total lipid extraction from the algal samples (Pl. refer to Mandal and Mallick20 for details). Lipid content was expressed as % dry cell weight (dcw). The weight of the biomass obtained from the control set-up was taken into account for calculating the lipid yield, as the biomass concentration of all setups was approximately same for the experiments. This was to avoid the presence of the flocculants which might interfere in the biomass yield.
To get a clear-cut evidence of various harvesting techniques on lipid recovery, experiments were also conducted in nitrogen- and phosphorus-starved cultures, as both the conditions were reported to stimulate lipid accumulation in microalgae profoundly. For nitrogen starvation, the test microalgae were grown in the N 11 medium by substituting KNO3 by equimolar concentration of KCl. Similarly, KH2PO4 and Na2HPO4·H2O of the medium were substituted by equimolar concentrations of KCl and Na2SO4, respectively to achieve P starvation.
2.6. Nutrients analyses of the supernatant of pH-induced flocculation experiments
The supernatant obtained after the pH-induced flocculation by NaOH, was siphoned out and the pH was normalized with the addition of 1 N HCl. The nutrient concentrations were analyzed using the following protocols. The nitrate concentration was estimated following Nicholas and Nason.21 The orthophosphate concentration was measured using the stannous chloride method of APHA.22 All other nutrients, viz. potassium, magnesium, sodium, calcium, zinc and copper concentrations were analyzed by Atomic Absorption Spectroscopy (Perkin Elmer A Analyst 800 Atomic Absorption Spectrophotometer, USA). The concentration of sodium was estimated by the use of Ion Chromatography (Metrohm Compact IC Flex Ion Chromatograph, Switzerland). Fresh nutrients were supplemented accordingly to reach the original medium composition. Micronutrients were also re-supplemented, and the growth pattern of both the test microalgae was studied and compared with the growth curves obtained under the original N 11 medium.
2.7. Statistical analysis
The reproducibility of the results was checked by repeating the experiments up to three times. Duncan's new multiple range test (DMRT) was used for statistical analysis with MSTAT-C software (Plant and Soil Sciences Division, Michigan State University, USA).
3 Results and discussion
3.1. Harvesting experiments at laboratory scale
3.1.1. pH-Induced flocculation of microalgae. The flocculation efficiency of the test microalgae was investigated as a function of pH variation from 2–12. For both the microalgae, pH range of 10–12 was found to be the most suitable range for flocculation within an hour. For S. obliquus, the maximum flocculation efficiency recorded to be 83.2% for pH 12 at the end of 1 h, whereas for pH 7, the value was only 17.3% (Fig. 1a). In C. vulgaris, the flocculation efficiency reached up to 65.1% for pH 12 and 62.2% for pH 10 after 1 h (Fig. 1a). For pH 7, similar to S. obliquus, 17% flocculation efficiency was recorded for C. vulgaris. Acidic pHs, except pH 2, did not register considerable flocculation at the early hour of the experiments. Thus, these results depicted that alkaline pH range was more suitable for harvesting of green microalgae. This was in accordance with the previous report of Wu et al.,23 where a pH range of 10.5–12.5, demonstrated flocculation efficiency of 90% in two green microalgae, Scenedesmus sp. and C. vulgaris, with a culture density of 0.75 and 0.67 g L−1, respectively. The lower flocculation efficiency as observed in this study could be ascribed to the higher biomass concentration (1.0 g L−1) taken for the experimentation.
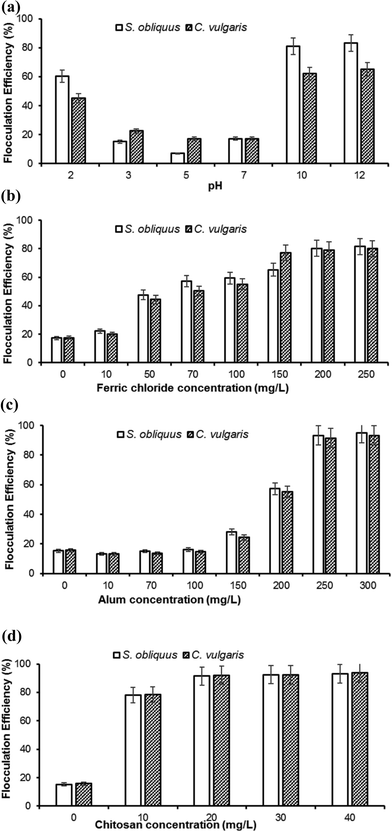 |
| Fig. 1 (a) Flocculation efficiency recorded for S. obliquus and C. vulgaris by variation of pH after 1 h under laboratory condition. Number of replicates: 3. (b) Flocculation efficiency recorded for S. obliquus and C. vulgaris with varied ferric chloride concentrations after 1 h under laboratory condition. Number of replicates: 3. (c) Flocculation efficiency recorded for S. obliquus and C. vulgaris with varied alum concentrations after 1 h under laboratory condition. Number of replicates: 3. (d) Flocculation efficiency recorded for S. obliquus and C. vulgaris with varied chitosan concentrations after 1 h under laboratory condition. Number of replicates: 3. | |
According to Molina et al.,24 cations played a vital role in flocculation, and the Mg2+ ions present in the medium was converted into magnesium hydroxide precipitates at higher pH. Magnesium hydroxide with its positive superficial charges could attract the negative surface charges of microalgae and formed a milky layer coating around the microalgal cells. The loss of negative surface charges did not allow the microalgal cells to repel from each other and flocs were formed. This lead to flocculation and due to the action of gravity settled down to the bottom of the surface.25 The difference in flocculation efficiencies in both the microalgal species can be explained by their structural differences, as C. vulgaris cells are unicellular, whereas the S. obliquus cells are joined together in a number of 2–4. Thus, it can be inferred that the unicellular nature of C. vulgaris cells helps them to stay suspended in the medium in a better way than S. obliquus.
3.1.2. Flocculation of microalgae by inorganic chemicals. Inorganic chemical flocculation was carried out for the test microalgae by the addition of ferric chloride and alum. The concentrations of ferric chloride were varied from 0 to 250 mg L−1. The pH of ferric chloride solution was found to be acidic as ferric hydroxide was formed by the combination of ferric ions with hydroxide groups in the solution. Thus, the medium pH of the experimental setups was adjusted to normal range (pH 7.0). Flocculation efficiency of 80.2% was recorded after 1 h at a concentration of 200 mg L−1, and 65.3% at 150 mg L−1 for S. obliquus, whereas the control culture without the addition of ferric chloride depicted a flocculation efficiency of ∼17% only after 1 h (Fig. 1b). The flocculation efficiency was not found to increase subsequently with the increase in concentration of ferric chloride above 200 mg L−1. Flocculation efficiency for C. vulgaris, without the addition of ferric chloride, was found to be 17.5% after 1 h, whereas 77.2 and 79.2% were recorded for 150 and 200 mg L−1 ferric chloride, respectively (Fig. 1b). A recent report of Chatsungnoen and Chisti16 depicted a settling rate of 60% for C. vulgaris by the addition of 200 mg L−1 of ferric chloride, which was increased above 90% with an increase in the flocculant dose up to 300–500 mg L−1 for a biomass concentration of 1 g L−1. At lower biomass concentration of 0.54 g L−1, a higher flocculation efficiency (>90%) was achieved for the microalga Scenedesmus sp. after 1 h with a flocculant dosage of 150 mg L−1.26 Thus, higher concentrations of ferric chloride are required for obtaining higher flocculation efficiency for higher biomass concentrations. One earlier report also showed that Chlorella zofingiensis cells were around 10 times larger than the precipitates of ferric hydroxide.27 C. vulgaris and S. obliquus are in the range of 5–20 μm.28 Thus, the positively charged precipitates get attracted to the negatively charged microalgal cells. The ferric hydroxide precipitates are much smaller in comparison to the microalgal cells, which did not meet the requisite to completely cover the microalgal cells at lower doses. This reason became the prime cause for the requirement of sufficient amount of ferric hydroxide in the solution. Thus higher flocculation efficiency was observed with the increase in ferric chloride concentration.Alum concentration was varied from 0 to 300 mg L−1. The flocculation efficiency reached above 90% at 250 mg L−1 of alum after 1 h for both the test microalgae (Fig. 1c). Chen et al.26 recorded a flocculation efficiency 93% with 300 mg L−1 alum for the microalga Scenedesmus sp. Earlier report also depicted that at a lower biomass concentration of 0.25 g L−1 with a flocculant dose of 115 mg L−1 alum, 85% flocculation efficiency was achieved for the same microalga.29 The mechanism of flocculation by the alum is that aluminum hydroxide is formed while adding alum to the medium. The positively charged aluminum ions cause neutralization of surface (negative) charges of algae, which brings the individual cells to come together to form flocs, and thus settle down to the bottom.30
3.1.3. Flocculation by chitosan. In both the microalgae, ∼90% flocculation efficiency was recorded after 1 h for 20–40 mg L−1 of chitosan (Fig. 1d). Whereas, the flocculation efficiency of the control samples of S. obliquus, i.e. without addition of any flocculant was very low; it was observed to be around 15% after 1 h. For C. vulgaris, 15.7% flocculation efficiency was recorded at the end of 1 h for control setups. The mechanism occurring in chitosan flocculation may be likely due to static patch effects with partial charge neutralization. With the addition to reducing or neutralizing the negative surface charge on microalgal cells, the polymer flocculants can also bring the microalgal cells together by physically linking one or more cells through a process called bridging.3,31 Xu et al.32 reported that 10 mg L−1 chitosan can exhibit 90% flocculation in Chlorella sorokiniana at pH 7 with a biomass density of 1 g L−1. However, a significantly higher concentration (80 mg L−1) of chitosan requirement was observed for Scenedesmus sp.26 In another report, 20 mg L−1 chitosan concentration induced a flocculation efficiency of more than 90% in Chlorella vulgaris with a lower biomass density of 0.25 mg L−1.29 Therefore, in addition to biomass concentration, species/strain-specific response could be the possible reason for these variations. The biomass concentration and molecular weight of the polymers plays a major role in the flocculation process as the higher biomass concentration will accelerate the cell–cell encounters in concentrated suspensions. The higher molecular weight polymers are more efficient due to their better bridging abilities.3
3.1.4. Dissolved air flotation. Dissolved air flotation was carried out on both the microlagal species with/without alum, since it was reported that addition of coagulants increased the flocculation efficiency.33 The hypothesis behind this is that high pressure sparging of flocculant helps in the formation of algal flocs quickly, which are then carried upward by the air bubbles. The flocculation efficiency reached up to 90% after 1 h with alum concentration of 1 mg L−1 (Fig. 2). Contrary to this, DAF without alum seemed to be inefficient as in both the cases a maximum of 25% flocculation efficiency was recorded even after 1.5 h. Zhang et al.34 reported that harvesting efficiency become very high for Chlorella zofingiensis with an increase in Al3+ concentration, and ∼90% flocculation efficiency was achieved with 10 mg g−1 Al3+ concentration only after 10 min. The addition of coagulants helps in forming larger flocs and better attachment with the generated microbubbles, which is not possible without the addition of coagulants, as both the bubbles as well as the microalgal cells tend to have negative surface charge. The difference in flocculants doses was clearly evident in this study as 1 mg g−1 alum concentration was sufficient to achieve 90% flocculation, albeit with an increased time duration of 1 h.
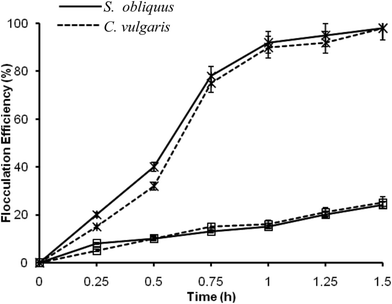 |
| Fig. 2 Flocculation efficiency recorded for S. obliquus and C. vulgaris by dissolved air flotation with and without alum under laboratory condition. × represents with alum (1 mg L−1) and □ represents without alum. Number of replicates: 3. | |
3.1.5. Electro-flotation. Electro-flotation was carried out on both the microalgal species at 6, 12 and 24 V. A pictorial view of electro-flotation set-up in the laboratory showing flocculation of S. obliquus at the initiation of experiment and after 1 h, is shown in the Fig. 3a and b. The flocculation efficiency was seen to vary subsequently with the variation in DC voltage. 95% flocculation efficiency was observed for S. obliquus at 24 V after a retention time 45 min. This was only 7.5 and 42%, respectively for 6 and 12 V. 99% flocculation efficiency was achieved after 1 h retention time with an application of 24 V (Fig. 3c). The flocculation efficiency was seen to follow the same trend in both the microalgal species, but with a marginally lower value for C. vulgaris. The voltage supplied to the electrochemical system determines the charge amount that is to be released from the electrodes. The increase in voltage value imposed into the system leads to faster electrolysis which in turn enhances the electrolysis process, leading to generation of more micro-bubbles which drives the flotation of microalgal flocs.35 The flocculation efficiency of the microalgae depends on applied electricity and also on the microalgal conductivity.29 Misra et al.13 observed a flocculation efficiency of 65% with 8.9 V for S. obliquus cultures. Recently, Zhou et al.,35 demonstrated that 4–6 V can exhibit a flocculation efficiency of more than 90% in Chlorella sp. depending on the culture condition and electrode distance.
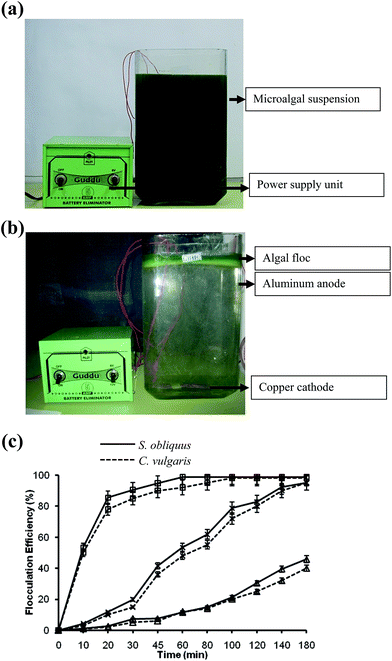 |
| Fig. 3 Electro-flotation set-up in the laboratory showing flocculation of S. obliquus (a) at the initiation of experiment and (b) after 1 h. (c) Flocculation efficiency recorded for S. obliquus and C. vulgaris by electro-flotation under laboratory condition. □: 24 V, ×: 12 V, and △: 6 V. Number of replicates: 3. | |
3.1.6. Lipid recovery with different harvesting techniques. Lipid content was analyzed from the harvested microalgal biomass obtained with various harvesting techniques for control, N- and P-starved cultures. It was apparent from Table 1 that the above harvesting techniques had no remarkable effects on the lipid content of both the microalgal species. The possible reason could be that the microalgal cells might not be affected notably during this short exposure to the applied processes.
Table 1 Lipid recovery with respect to various harvesting techniques under laboratory scale studiesa
Name of the microalga |
Method |
Condition |
Lipid contentb (% dcw) |
Control |
N-starved |
P-starved |
Note: values are means ± standard deviations of three independent observations. Values superscripted by ‘a’ symbolize they are not significantly different from each other (P > 0.05, DMRT). For all the processes the maxima values were considered. Separate analysis was done for each column and each microalga. Total lipids were extracted after completion of 1 h of different flocculation experiments. |
S. obliquus |
Control |
N 11 medium |
11.51 ± 1.21a |
41.52 ± 3.17a |
29.53 ± 2.15a |
pH-Induced flocculation by NaOH |
pH 12 |
11.62 ± 0.89a |
40.81 ± 3.02a |
28.35 ± 28.21a |
FeCl3-induced flocculation |
200 mg L−1 |
11.52 ± 1.15a |
41.23 ± 4.14a |
29.15 ± 2.25a |
Alum-induced flocculation |
250 mg L−1 |
10.93 ± 0.91a |
40.51 ± 3.08a |
28.92 ± 2.31a |
Chitosan-induced flocculation |
20 mg L−1 |
11.24 ± 1.24a |
39.56 ± 3.19a |
29.31 ± 2.10a |
Dissolved air flotation |
With alum (1 mg L−1) |
10.91 ± 1.05a |
40.22 ± 4.01a |
29.41 ± 2.05a |
Without alum |
10.82 ± 1.32a |
41.63 ± 3.20a |
30.13 ± 2.14a |
Electro-flotation |
24 V |
10.52 ± 1.41a |
41.53 ± 3.41a |
28.41 ± 2.24a |
C. vulgaris |
Control |
N 11 medium |
12.13 ± 1.32a |
42.14 ± 3.25a |
31.72 ± 2.26a |
pH-Induced flocculation by NaOH |
pH 12 |
12.44 ± 1.32a |
42.13 ± 3.12a |
32.13 ± 2.27a |
FeCl3-induced flocculation |
150 mg L−1 |
12.14 ± 1.21a |
42.91 ± 3.45a |
32.40 ± 2.35a |
Alum-induced flocculation |
250 mg L−1 |
12.21 ± 1.14a |
41.50 ± 3.31a |
31.91 ± 2.42a |
Chitosan-induced flocculation |
20 mg L−1 |
13.13 ± 1.21a |
41.52 ± 3.28a |
32.71 ± 2.35a |
Dissolved air flotation |
With alum (1 mg L−1) |
12.23 ± 1.12a |
42.81 ± 4.18a |
32.15 ± 2.17a |
Without alum |
12.21 ± 1.04a |
41.73 ± 3.24a |
31.51 ± 2.24a |
Electro-flotation |
24 V |
11.82 ± 1.12a |
42.21 ± 3.19a |
31.11 ± 2.31a |
3.1.7. Comparison of various harvesting techniques studied under laboratory scale. The harvesting techniques studied in the laboratory scale were performed with various levels of flocculation concentration and its effect on microalgal harvesting was observed. The harvested microalgae were further processed to see the effect of harvesting conditions on the end product i.e. lipid yield. The effect of starvation conditions was also performed to see the outcome on the lipid yield from the microalgal strains. The harvesting techniques were compared based on the results of flocculation efficiency, economic sustainability and their effects on lipid yield.Table 2 compares the flocculation efficiency, flocculant dose/kg harvested biomass, and the costs incurred with different techniques. In case of ferric chloride and alum, although the flocculation efficiency was found to be high enough and the flocculants bulk prices were notably low, the required doses were profoundly high. Thus, with the high concentrations of ferric chloride and alum, the nutritive value of the supernatant (medium) was essentially lost. Moreover, the use of such high concentrations of inorganic chemicals was not environment friendly, thus made them incongruous for large-scale operation. With chitosan, high flocculation efficiency was also recorded. However, the price of this cationic polymer was found to be considerably high (1 g of chitosan costs 2 US $, HiMedia Bioscience & Laboratory Chemicals, India; bulk price of chitosan was 300 US $ for 1 kg, http://www.alibaba.com), and therefore, it would increase the cost of harvesting significantly, thus seems to be not a feasible approach for large-scale operation.
Table 2 Comparison of flocculation efficiency, flocculant dose/kg harvested biomass and the costs for the two test microalgae under laboratory scale study
Harvesting method |
Flocculation efficiency (%) after 1 h |
Flocculant dose/kg harvested biomass |
Cost/kg biomass (in US $) |
Costs of laboratory grade chemicals (HiMedia Biosciences and Laboratory Chemicals Catalogue, India, 2015–16). Costs of bulk purchase (http://www.alibaba.com). |
pH-Induced flocculation by NaOH |
65–83 |
74–84 g |
0.63–0.72a |
0.02–0.03b |
FeCl3-induced flocculation |
79–80 |
100–135 g |
1.6–2.2a |
0.48–0.64b |
Alum-induced flocculation |
93–95 |
225–252 g |
3.0–3.3a |
0.07–0.08b |
Chitosan-induced flocculation |
91–92 |
17–19 g |
16.2–18.0a |
5.4–6.0b |
Dissolved air flotation |
90 |
0.892 g alum + electricity consumed by two pumps |
0.75a |
Electro-flotation |
99 |
0.5 kW h power consumption + cost of electrodes (aluminum and copper) |
1.5a |
In case of DAF, the flocculation efficiency was also recorded to be high. Furthermore, the amount of alum used was relatively less in quantity. Therefore, the discarded medium (supernatant) with low alum concentration can be reused, which needs further examination. Electro-flotation also showed profoundly high flocculation efficiency, and had no negative impact on lipid recovery. In the case of pH-induced flocculation by NaOH, the flocculation efficiency was found to be comparatively low. However, the supernatant can be reused for microalgal cultivation after pH neutralization and nutrient re-supplementation, which would ultimately lead to a decrease in the production cost. It is also apparent from Table 2 that the cost of harvesting was the lowest for the pH-induced flocculation by NaOH. Hence, the above three techniques (pH-induced flocculation by NaOH, DAF and electro-flotation) were checked further at field level.
3.2. Harvesting experiments at field-scale
Although many researchers, nowadays, are focusing their attention to combat the problem of microalgal harvesting for low-cost biofuel production,16,36–38 a technique feasible for large-scale application is yet be comprehended. Therefore, there is a need to see the performance of the above selected flocculation techniques at field level.
3.2.1. pH-Induced flocculation by NaOH. pH-Induced flocculation by NaOH was carried out in 1000 L tanks at pH 12. A pictorial view of flocculation of S. obliquus in a 1000 L tank is presented in the Fig. 4a and b. About 75% flocculation efficiency was recorded for S. obliquus after 1 h, and for C. vulgaris, the flocculation efficiency was ∼60%, Fig. 4c, which was consistent with the results obtained for laboratory scale study. Thus, it can be concluded that pH-induced flocculation by NaOH can be used to harvest microalgae from large-scale set-ups.
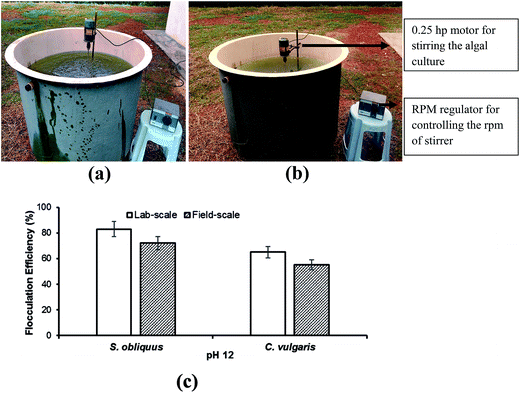 |
| Fig. 4 pH-Induced flocculation at pH 12 set-up in 1000 L tank showing flocculation of S. obliquus (a) at the initiation of experiment and (b) after 1 h. (c) Flocculation efficiency recorded for S. obliquus and C. vulgaris at pH 12 after 1 h under field scale. Number of replicates: 3. | |
3.2.2. Flocculation by electro-flotation. Electro-flotation experiments at field-scale were carried out by using copper and aluminum electrodes. Aluminum pipes were attached to the inner wall of the 1000 L tank and acted as anodes. Two copper plates of 1 ft2 area were placed in the bottom and acted as cathodes. A pictorial view of the set-up is provided in the Fig. 5a and b. Electro-flotation was found to be highly efficient at 24 V in the laboratory scale experiments. In the field scale set-up of 1000 L, 24 V was not found adequate as only ∼50% flocculation was observed after 24 h (Fig. 5c). With an increase in the voltage to 60 V, >90% flocculation was achieved after 24 h for both the test microalgae. At the first hour of the experiment, only 48–50% flocculation was recorded. The flocculation efficiency depends upon the applied voltage as well as the microalgal conductivity, thus the requirement of voltage and time were found to increase with the increasing volume of cultures. The voltage required was more to generate more microbubbles on a large surface area and consecutively to float the microalgal cells to the top.35 Following these reasons, due to increased power consumption with the increase in the volume of cultures, this method was not found to be feasible for large-scale harvesting.
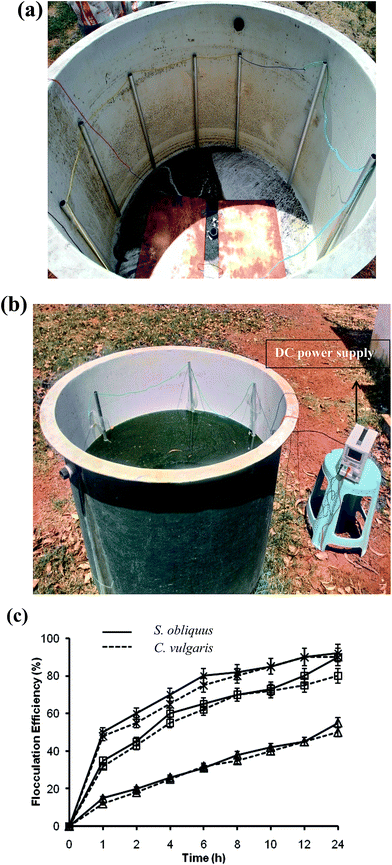 |
| Fig. 5 (a) Set-up for electro-flotation. 1000 L tanks with hollow aluminium pipes as anode attached to the inner wall of the tank. Two copper plates of 1000 cm2 each were used as cathodes. (b) Flocculated microalgae by electro-flotation. (c) Flocculation efficiency recorded for S. obliquus and C. vulgaris by electro-flotation at field scale. × represents 60 V, □ represents 48 V, and △ represents 24 V. Number of replicates: 3. | |
3.2.3. Dissolved air floatation. Dissolved air flotation was carried out with varying alum concentration from of 1.0 to 10 mg L−1 (Fig. 6). 90% flocculation efficiency was achieved after 7 h with 10 mg L−1 alum for S. obliquus. Contrary to the laboratory scale study, flocculation efficiency achieved with 1 mg L−1 alum concentration in 1000 L tanks was only 40% at the end of 7 h. Thus, the alum concentration required at field scale was much higher than the laboratory scale set-ups of 1 mg L−1 only, which indicates the need for more alum with increase in the volume of cultures. The quantity of alum increased as floc formation was not adequate enough in lower doses and the efficiency decreased. The floc should be large enough to get attached to the air bubbles to float up to the surface. The higher recycle ratio of 15% helped in producing better micro bubble formation which increased the efficiency with increase in coagulant doses. The flocculation time was also found to rise significantly. C. vulgaris also followed a similar pattern (data not shown).
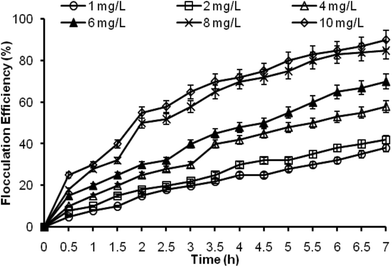 |
| Fig. 6 Flocculation efficiency recorded for S. obliquus by dissolved air flotation with various alum concentrations in field scale studies. Number of replicates: 3. | |
3.2.4. Reuse of the supernatant from pH-induced flocculation by NaOH. pH-Induced flocculation by NaOH was found to be efficient for microalgal harvesting. Thus, the supernatant, after adjusting the pH and re-supplementing nutrients, was explored to be reused as growth medium. Table 3 depicts the concentrations of the essential nutrients in the supernatant after harvesting. Accordingly, the adjusted medium was re-supplemented with the required essential nutrients. The concentration of sodium was found to be in the same range before and after harvesting due to the use of NaOH to reach pH 12. This is also a major advantage of the use of NaOH with respect to other flocculation methods. The time-course study (Fig. 7) depicted that the growth pattern in the fresh N 11 medium and the adjusted medium (supernatant obtained from the pH-induced flocculation experiments, pH normalised and nutrient re-supplemented) was comparable. This finding was also supported by the earlier work of Wu et al.23 and Kim et al.,39 where reuse of the flocculated medium was advocated after harvesting of the algal biomass by pH increase and/or with the use of bioflocculant, respectively. The nutrient concentrations of the medium were rechecked after every fresh inoculation of algal culture. The culture medium was not reused after three consecutive re-supplementations, and a fresh culture medium was prepared for microlagal cultivation, since after three consecutive uses fouling smell from the medium was sensed.
Table 3 Concentration of essential nutrients in the medium before cultivation and after harvestinga
Essential nutrients in the medium |
Concentration before cultivation (mg L−1) |
Concentration in the supernatant (mg L−1) |
Number of replicates: 3. |
Potassium |
412.21 ± 10.10 |
102.14 ± 8.10 |
Sodium |
27.14 ± 1.10 |
32.24 ± 1.30 |
Nitrate |
595.12 ± 13.10 |
89.08 ± 4.41 |
Phosphate |
102.04 ± 6.20 |
53.15 ± 5.20 |
Magnesium |
4.91 ± 0.79 |
2.96 ± 0.84 |
Iron |
0.21 ± 0.01 |
0.10 ± 0.02 |
Copper |
0.021 ± 0.001 |
0.011 ± 0.001 |
Zinc |
0.49 ± 0.05 |
0.060 ± 0.003 |
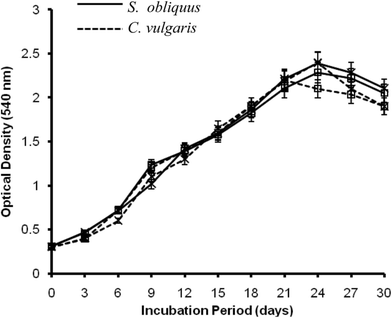 |
| Fig. 7 Comparative growth curves of S. obliquus and C. vulgaris in N 11 and the adjusted media. × represents N 11 (control) and □ represents pH and nutrients adjusted medium. Number of replicates: 3. | |
3.2.5. Comparison of the selected harvesting techniques studied at field scale. The large-scale harvesting techniques were compared on the basis of economic sustainability and the effect on lipid productivity. Large-scale microalgal cultures deal with a large volume and economy plays a major role in the selection of the harvesting technique. Table 4 presents a comparison of flocculation efficiency, costs as well as the flocculant dose/kg harvested microalgal biomass, under field-scale study. Interestingly, the pH-induced flocculation by NaOH showed a reduction in cost as compared to the laboratory scale study, since less NaOH was required to raise the pH of the cultures to pH 12. This is because the pH of the raceway pond cultures reached high enough up to pH 9.5 after 20–21 days. On the contrary, a tremendous rise in cost was seen for electro-flotation. An increase in cost was also recorded for DAF. Further, the requirement of alum was found to increase with the volume of cultures, which will lead to rise in aluminium ions in the medium. Since aluminium is a toxic heavy metal, so it is undesirable in the growth medium for microalgae cultivation. Conversely, the rise in the concentration of Na ions in the medium in case of pH-induced flocculation by NaOH is desirable as sodium is a major nutrient for microalgal growth. Moreover, the cost of the process is also found to be the lowest as compared to the other methods. Thus from this study it can be concluded that pH-induced flocculation by NaOH, microlagal harvesting can be conducted at a much lower cost and efficiently in large-scale set-ups.
Table 4 Comparison of flocculation efficiency, flocculant dose/kg harvested biomass and costs under field scale study
Harvesting methods |
Flocculation efficiency (%) after 1 h |
Flocculant dose/kg harvested biomass |
Cost/kg biomass (in US $) |
Costs of laboratory grade chemicals (HiMedia Biosciences and Laboratory Chemicals Catalogue, India, 2015–16). Costs of bulk purchase (http://www.alibaba.com). |
pH-Induced flocculation by NaOH |
60–75 |
50–62 g NaOH + 0.2 kW h power consumption |
0.50–0.53a |
0.04–0.05b |
Dissolved air flotation |
24–30 |
30–35 g alum + electricity consumed by two pumps |
1.05–1.28a |
0.886–0.888b |
Electro-flotation |
48–50 |
60–65 kW h power consumption + cost of electrodes (aluminum and copper) |
6.31–6.84a |
4 Conclusion
Various harvesting techniques were assessed under a single domain for efficient recovery of microalgal biomass for further processing. Using inorganic chemicals, high flocculation efficiency could be obtained within less time but the flocculants could not be separated from the medium, which would lead to water pollution. Chitosan could be used at low doses, but the price of this polymer was found to be prohibitive for large-scale operations. Among the three techniques studied at field level, pH-induced flocculation by NaOH emerged to be efficient, cost-effective and eco-friendly as the supernatant could be reused as growth medium by re-supplementing with essential nutrients and adjusting the pH.
Acknowledgements
Financial support from Indian Council of Agricultural Research, New Delhi, India, and the research facilities provided by Indian Institute of Technology Kharagpur, India, are thankfully acknowledged. The first author wishes to acknowledge Miss Reeza Patnaik and Mr Sashi Sonkar, Ph.D. Scholars, Indian Institute of Technology Kharagpur, for helping in preparation of the manuscript.
References
- J. R. Benemann, J. C. Weissman, B. L. Koopman and W. J. Oswald, Nature, 1977, 268, 19–23 CrossRef CAS.
- S. Sawayama, T. Minowa and S. Y. Yokoyama, Biomass Bioenergy, 1999, 17, 33–39 CrossRef CAS.
- E. M. Grima, E. H. Belarbi, F. G. A. Fernandez, A. R. Medina and Y. Chisti, Biotechnol. Adv., 2003, 20, 491–515 CrossRef.
- Y. H. M. Li, N. Wu and C. D. C. N. Lan, Biotechnol. Prog., 2008, 24, 815–820 CAS.
- B. Wang, Y. Li, N. Wu and C. Lan, Appl. Microbiol. Biotechnol., 2008, 79, 707–718 CrossRef CAS PubMed.
- E. W. Becker, Microalgae Biotechnology & Microbiology, Cambridge University Press, 1994, pp. 56–62 Search PubMed.
- L. Christenson and R. Sims, Biotechnol. Adv., 2011, 29, 686–702 CrossRef CAS PubMed.
- A. Papazi, P. Makridis and P. Divanach, J. Appl. Phycol., 2010, 22, 349–355 CrossRef CAS.
- J. Morales, J. De la Noue and G. Picard, Aquacultural Engineering, 1985, 4, 57–70 CrossRef.
- A. Lavoie and J. Noüe de la, J. World Maric. Soc., 2009, 14, 685–694 CrossRef.
- D. Vandamme, I. Foubert, B. Meesschaert and K. Muylaert, J. Appl. Phycol., 2010, 22, 525–530 CrossRef.
- S. Salim, R. Bosma, M. H. Vermuë and R. H. Wijffels, J. Appl. Phycol., 2011, 23, 849–855 CrossRef PubMed.
- R. Misra, A. Guldhe, P. Singh, I. Rawat, T. A. Stenstrom and B. Faizal, Bioresour. Technol., 2015, 176, 1–7 CrossRef CAS PubMed.
- C. Y. Chen, K. L. Yeh, R. Aisyah, D. J. Lee and J. S. Chang, Bioresour. Technol., 2011, 102, 71–81 CrossRef CAS PubMed.
- J. C. Soeder and A. Bolze, Physiol. Plant., 1981, 52, 233–238 CrossRef.
- T. Chatsungnoen and Y. Chisti, Algal Res., 2016, 13, 271–283 CrossRef.
- J. M. S Rocha, J. E. C. Garcia and M. H. F. Henriques, Biomol. Eng., 2003, 20, 237–242 CrossRef.
- S. Gao, M. Du, J. Tian, J. Yang, F. Ma and J. Nan, J. Hazard. Mater., 2010, 182, 827–834 CrossRef CAS PubMed.
- E. G. Bligh and W. J. Dyer, Can. J. Biochem. Physiol., 1959, 37, 911–917 CrossRef CAS PubMed.
- S. Mandal and N. Mallick, Appl. Microbiol. Biotechnol., 2009, 84, 281–291 CrossRef CAS PubMed.
- D. J. Nicholas and A. Nason, Methods in Enzymology III, Academic Press, New York, 1957, pp. 961–984 Search PubMed.
- American Public Health Association (APHA), Standard methods for the examination of water and waste water, Washington DC, USA, 20th edn, 1998, p. 1220 Search PubMed.
- Z. Wu, Y. Zhu, W. Huang, C. Zhang, T. Li, Y. Zhang and A. Li, Bioresour. Technol., 2012, 110, 496–502 CrossRef CAS PubMed.
- G. E. M. Molina, E. H. Belarbi and A. F. G. Fernandez, Biotechnol. Adv., 2003, 20, 491–515 CrossRef.
- G. A. Parks, Equilibrium concepts in natural water systems, Advances in Chemistry Series, American Chemistry Society, Washington, DC, 1967, p. 67 Search PubMed.
- L. Chen, C. Wang, W. Wang and J. Wei, Bioresour. Technol., 2013, 133, 9–15 CrossRef CAS PubMed.
- N. B. Wyatt, L. M. Gloe, P. V. Brady, J. C. Hewson, A. M. Grillet, M. G. Hankins and P. I. Pohl, Biotechnol. Bioeng., 2012, 109, 493–501 CrossRef CAS PubMed.
- B. Pawlak and J. Kopeć, Oceanologia, 1998, 40, 345–353 Search PubMed.
- D. Vandamme, I. Foubert, I. Fraeye and K. Muylaert, Bioresour. Technol., 2012, 124, 508–511 CrossRef CAS PubMed.
- V. M. Rwehumbiza, R. Harrison and L. Thomsen, Chem. Eng. J., 2012, 200/202, 168–175 CrossRef.
- N. Uduman, Y. Qi, M. K. Danquah, G. M. Forde and A. Hoadley, J. Renewable Sustainable Energy, 2010, 2, 012701 CrossRef.
- Y. Xu, S. Purton and F. Baganz, Bioresour. Technol., 2013, 129, 296–301 CrossRef CAS PubMed.
- B. Koopman and E. P. Lincoln, Agric. Wastes, 1983, 5, 231–246 CrossRef.
- X. Zhang, P. Amendola, J. C. Hewson, M. Sommerfeld and Q. Hu, Bioresour. Technol., 2012, 116, 477–484 CrossRef CAS PubMed.
- W. Zhou, L. Gao, W. Cheng, L. Chen, J. Wang, H. Wang, W. Zhang and T. Liu, Algal Res., 2016, 18, 7–14 CrossRef.
- J. E. Coons, D. M. Kalb, T. Dale and B. L. Marrone, Algal Res., 2014, 6, 250–270 CrossRef.
- K. Pirwitz, L. R. Struckmann and K. Sundmacher, Bioresour. Technol., 2015, 196, 145–152 CrossRef CAS PubMed.
- J. Liu, Y. Tao, J. Wu, Yi. Zhu, B. Gao, Y. Tang and A. Li, Bioresour. Technol., 2014, 167, 367–375 CrossRef CAS PubMed.
- D. G. Kim, H. J. La, C. Y. Ahn, Y. H. Park and H. M. Oh, Bioresour. Technol., 2011, 102, 3163–3168 CrossRef CAS PubMed.
|
This journal is © The Royal Society of Chemistry 2017 |
Click here to see how this site uses Cookies. View our privacy policy here.