DOI:
10.1039/C6RA25738K
(Paper)
RSC Adv., 2017,
7, 3233-3239
Highly active MnOx–CeO2 catalyst for diesel soot combustion†
Received
24th October 2016
, Accepted 1st December 2016
First published on 13th January 2017
Abstract
A series of MnOx–CeO2 composites have been prepared via a facile coprecipitation method and used as catalysts for diesel soot combustion. It is found that the content of manganese oxide has a considerable influence on both the morphology and catalytic activity for diesel soot combustion in the copresence of NOx and O2. Superior catalytic activity (Tf = 360 °C) was obtained over the optimized catalyst CM20 [Mn/(Mn + Ce) equals to 20 at%], which is believed to be attributable to the following two aspects: (1) the abundant pore structure, presenting between the loosely-packed homogeneous particles with similar sizes to that of the soot particles, which is beneficial for mass transfer and heat diffusion as well as the sufficient contact between catalyst and soot; (2) high concentration of Mn4+ and Ce3+ cations derived from the charge transfer between Mn and Ce species as active sites can adsorb and activate NO and O2, and then greatly facilitate NO2 production.
1. Introduction
Soot, as one of the main pollutants from diesel emission, has caused severe environmental problems like haze,1 and several emission control strategies have been adopted to meet the demands of more and more stringent legislation, such as improvements in fuel oil,2 modifications of the engine or process3,4 and exhaust after-treatment systems.5 For example, the diesel particulate filter (DPF) used in the after-treatment systems has so far been the most promising technological option. When the diesel exhaust flows through DPF, over 90% of the soot can be trapped and then be continuously or periodically combusted to CO2.6 However, the combustion temperature of soot (around 600 °C)7 is far beyond the normal diesel exhaust temperature range (175–400 °C),8 making the regeneration of DPF an intractable problem. Aimed at the passive regeneration of DPF, many kinds of catalysts, such as noble metals,9 transition metal oxides,10 perovskite and/or perovskite-like mixed oxides,11 spinel mixed oxides,12 alkaline metal/alkaline-earth metal oxides,13 and the popular ceria-based oxides,14–19 have been developed to decrease the soot combustion temperature. Additionally, many researches demonstrate that the introduction of macropores or large voids into the catalysts can greatly facilitate the heat and mass transfer as well as improve the contact between soot and the catalysts, eventually to reach a high activity towards soot oxidation.11,20–25 For example, Wei et al.23 synthesized a three-dimensionally ordered macroporous (3DOM) LaFeO3 catalyst loaded with tiny golden nanoparticles (∼2.9 nm), showing the temperature of maximum soot combustion rate (Tm) at 366 °C under loose contact mode between soot and catalyst. Recently, Nascimento et al.25 synthesized Ag/CeOx/FeOy catalysts supported on cordierite for the control of diesel soot emission, showing further decreased Tm (334 °C), and Tf (finishing soot combustion temperature, 400 °C), exhibiting great potential in application. However, the high-cost, the sensitivity to sulfur, and easily sintering characteristic of noble metal catalysts,26,27 as well as the difficulty in the synthesis of 3DOM materials hinder the industrial application of this kind of catalysts.
MnOx–CeO2 composites have been widely used in many catalytic reaction processes, such as wet oxidation of toxic organic pollutants28 and oxidation of gaseous29 or even liquid pollutants,30 and proved to be a promising substitute for noble metal catalysts. But for catalytic soot combustion, the previously reported approaches are still hard to achieve a satisfactory performance on MnOx–CeO2 composites, i.e., Tm = 393–420 °C, Tf > 400 °C, maybe due to the unsufficient catalyst–soot contact that will restrict the full use of the active sites of the catalysts.10,31–34
Herein, a series of MnOx–CeO2 composites was synthesized through a facile modified coprecipitation method. Especially, the optimized catalyst CM20 [Mn/(Mn + Ce) = 20 at%] shows uniform particle morphology with hierarchically porous structure which is much beneficial to the sufficient contact between catalyst and soot, as well as the high concentration of Mn4+–Ce3+ cations on the surface that favors NO2 production, thus exhibiting an excellent catalytic activity for the removal of soot in NOx/O2 atmosphere, i.e., ignition temperature (Ti) = 280 °C, Tm = 326 °C and Tf = 360 °C. The possible catalytic mechanism for the soot combustion is also proposed.
2. Experimental
2.1 Catalyst preparation
All the chemicals used in this study were of analytical grade, and were used without further purification. MnOx–CeO2 composites were prepared by the co-precipitation method reported before35 with some modification. A typical preparation procedure is as follows: firstly, 7.5 mmol nitrate including Ce(NO3)3·3H2O and Mn(NO3)2 (50 wt% in aqueous solution) was dissolved in 30 mL deionized water. Then, 30 mL water solution including 30 mmol NaHCO3 was quickly poured into the nitrate solution and the mixture was stirred for 30 min at room temperature. Next, the precipitates were filtered and washed with deionized water and ethyl alcohol alternately for several times. After drying at 100 °C, the precursors were grinded and then calcined under static air at 500 °C for 2 h with a heating rate of 1 °C min−1. The obtained catalysts were designated CMy, where y (%) is the Mn/(Mn + Ce) atomic ratio in the recipe. In addition, we prepared two single oxides (CeO2 and MnOx) for reference with the same synthesis condition.
2.2 Catalyst characterization
The nitrogen adsorption and desorption curves were obtained using Micromeritics Tristar 3000 at 77 K, and the specific surface area and the pore size distribution were calculated using the Brunauer–Emmett–Teller (BET) and Barrett–Joyner–Halenda (BJH) methods, respectively. Powder X-ray diffraction (XRD) patterns of the prepared samples were got using a Rigaku D/Max 2200 PC diffractometer with Cu Kα radiation (40 kV and 40 mA). Field emission scanning electron microscopy (FE-SEM) imaging was performed using Hitachi S-4800. Transmission electron microscopic (TEM) images, selected area electron diffraction (SAED) patterns and element mapping images were obtained using a JEOL-2010F electron microscope operated at 200 kV. X-ray photoelectron spectroscopy (XPS) signals were recorded using an ESCAlab 250 instrument. The fitting of the Mn element was carried out using Gaussian fitting parameters. The temperature-programed reduction with hydrogen (H2-TPR) experiments were performed using a Micromeritics Chemisorb 2750 instrument in a 5% H2/N2 flow (25 mL min−1) using 50 mg catalyst with a heating rate of 10 °C min−1. The uptake amount of H2 was measured using a thermal conductivity detector (TCD).
2.3 Activity testing
Carbon black from Degussa (diameters: 10–50 nm) was used as the model soot particles. Following a well-accepted procedure, soot (10 mg) and catalyst (100 mg) were carefully mixed for 20 min with a spatula to simulate the loose contact mode, then silica pellets (1 g) were added and mixed by the spatula for another 10 min. It is worth noting that silica pellets were added to avoid pressure drop and favor heat transfer.36 A gas mixture of 500 ppm NO, 10% O2 and balance N2 was feed with a flow rate of 200 mL min−1. The space velocity was thus calculated to be 120
000 mL (g h)−1. Afterwards, the mixture was heated to 650 °C at a heating rate of 5 °C min−1 in a tube furnace equipped with a thermal couple. To minish the error of the measurement to a least extent, the temperature of the tube furnace was monitored with a standard thermal couple, every gas flow was verified with a mechanical flow meter and the concentration of NOx was measured by a NOx analyzer (Thermo Fisher 42i-LS). The analysis of the emissions from the reactor was performed using an online GC-FID analyzer (GC2060 from Shanghai Ruimin Instrument Corp. Ltd.) equipped with a methane converter. The catalytic activities (conversion and selectivity) were calculated as indicated in previous reports in the literature, in terms of Ti, Tm and Tf values, which were respectively defined as the temperatures at 10%, 50% and 90% of soot conversion, and selectivity to CO2 as well, which was quantified: selectivity (%) = SCO2(total)/[SCO(total) + SCO2(total)], where SCOx(total) represents the area under the COx–temperature curve in the range of RT – 650 °C (x = 1 or 2).37,38
3. Results and discussion
3.1 Catalytic activity measurements
Fig. 1 shows the catalytic activity of the CMy composites, references MnOx and CeO2, and NULL (without catalyst) towards soot oxidation under loose contact mode. It is obvious that compared with NULL, all the CMy composites and the references MnOx, CeO2 show much lower characteristic temperatures and higher selectivity to CO2 in the soot oxidation. Thereinto, CM20 shows the lowest characteristic temperatures (Ti = 280 °C, Tm = 326 °C, and Tf = 360 °C) as well as the highest selectivity to CO2 (95.6%), indicating that the interaction between Mn and Ce species can greatly improve the catalytic activity toward the soot oxidation. Even compared with the noble-metal based catalysts supported on 3DOM oxides or cordierite, as well as the MnOx–CeO2 catalysts prepared by other methods, CM20 still shows much lower characteristic temperatures (especially Tf) for soot combustion under similar reaction conditions (loose contact mode, shown in Table S1†). It should be noted that even at a higher space velocity [330
000 mL (gcatal h)−1, the highest one among those shown in Table S1†], CM20 still shows a much lower Tm value (350 °C) than that of other reported MnOx–CeO2 catalysts (393–420 °C) shown in Table S1.† Fig. S1 and S2† indicates good stability in both catalytic activity and structure for these CMy composite catalysts (herein, CM33 was chosen as an example). In order to understand the different catalytic performances on these prepared catalysts, XRD analysis, N2 adsorption/desorption analysis and SEM/TEM observations were conducted to reveal both the phase composition and the morphology/pore structure of different catalysts.
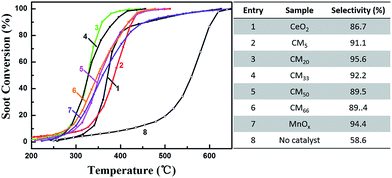 |
| Fig. 1 Catalytic activity (left) and selectivity to CO2 (right) for soot combustion over different catalysts or NULL (without catalyst) under loose contact mode. Reaction conditions: 500 ppm NO and 10% O2 in N2 with a total flow of 200 mL min−1, mass of soot–catalyst–silica is 10–100–1000 mg. | |
3.2 XRD analyses
Fig. 2 shows the XRD patterns of different CMy composites and the references MnOx and CeO2. It is found that the reference CeO2 exhibits a single phase of cubic CeO2 (JCPDS 43-1002), while MnOx shows three distinguishable manganese oxides of Mn2O3 (JCPDS 73-1826), MnO2 (JCPDS 72-1982) and Mn5O8 (JCPDS 39-1218). In addition, compared with reference CeO2, all the CMy composites show relatively wide diffraction peaks corresponding to cubic CeO2 phase, without detectable Mn-containing phases or obvious peak shift, indicating that manganese oxides may exist in the form of highly dispersive and/or amorphous species, thus decreasing the crystallinity of CeO2. More interestingly, CM20 shows the biggest FWHM (the full width at half maximum) values of the main XRD peaks among all the CMy composites, suggestive of the smallest crystalline grain according to the Scherrer equation, and the corresponding most abundant surface defect sites, which are beneficial for the improvement of catalytic activity.
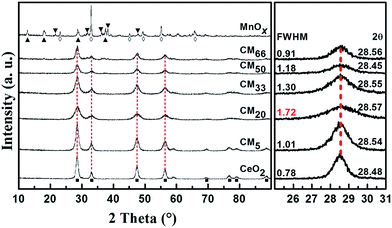 |
| Fig. 2 XRD patterns of different CMy composites and the references MnOx and CeO2 (left), (■-CeO2; ◊-Mn2O3; ▲-MnO2; ▼-Mn5O8), and the enlarged region between 25° and 31° of the patterns showing the corresponding FWHM values and peak positions of 2θ (right). | |
3.3 SEM & TEM measurements for CM20
The typical SEM images and the corresponding EDS spectrum, as well as TEM image and the corresponding element mapping of CM20 shown in Fig. 3 indicate that CM20 is solely composed of uniform particles with loose packing, leaving abundant large pores, as indicated by the arrows in Fig. 3b, which is very different from the morphologies of all the other studied catalysts in Fig. S3† (CeO2, CM5, CM50, CM66 and MnOx). The pore sizes in CM20 are measured to be within 16–103 nm (Fig. 3b), which are consistent with its pore size distribution (10–159 nm) by N2 adsorption/desorption analysis shown in Fig. S4† and summarized in Table S2.† As can be seen in Table S2,† the specific surface areas of CMy composites are all larger than that of reference MnOx and CeO2. Especially, CM20 shows much enlarged specific surface area and pore volume as well. Besides, its pore size is also broadened. It is believed that the similar particle size of the sample CM20 to that of soot particles (Fig. S3-f†), and the abundant large pores in CM20 are both helpful to its sufficient contact with soot. Also, its high specific surface area and pore volume both favor the dispersion of active sites, thus making a great contribution to catalytic oxidation of soot. The atomic ratio of Mn/(Mn + Ce) is calculated to be 21.9%, according to EDS spectrum in Fig. 3c, similar to that of the starting solution. As can be found in Fig. 3d–f, both the Ce species and Mn species are homogeneously distributed in the prepared composite, indicating that manganese species shows highly dispersive with ceria species. The H2-TPR results (Fig. S5†) confirm the interaction between Mn and Ce species in CMy composites. Especially, CM20 shows excellent redox activity, which can be mainly attributed to the interaction between Ce and Mn species, inducing the changes of the local atomic environment for each element, as detected by the following XPS measurements.
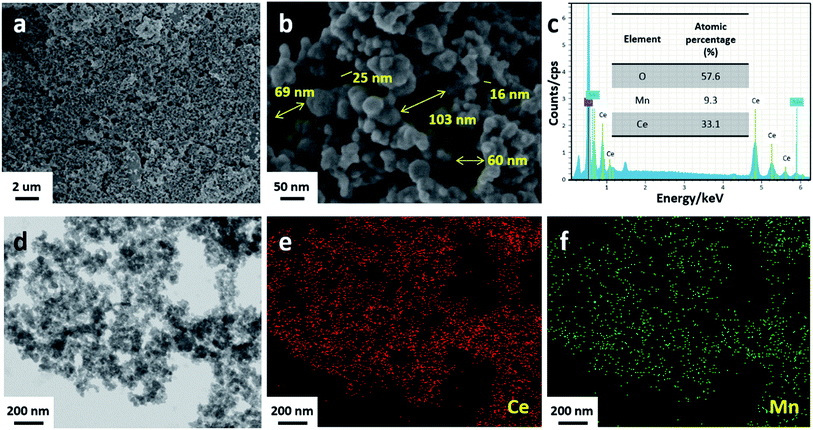 |
| Fig. 3 Low-magnification SEM image (a), high-magnification SEM image (b), EDS spectrum (c), typical TEM image (d) and the element mapping (e and f) of CM20. | |
3.4 XPS measurements
Fig. 4 shows the Mn 2p, Ce 3d and O 1s XPS spectra of the series of CMy composites, as well as the references MnOx and CeO2. The analysis results of different samples are summarized in Table 1, based on the careful peak fitting procedure. The O 1s XPS spectra of the sample CMy and the references MnOx and CeO2 can be deconvoluted into two components after Gaussian fitting, as shown in Fig. 4c, which can be ascribed to lattice oxygen Olatt (529.6 eV) and adsorbed oxygen Oads (532.4 eV), respectively. Generally, adsorbed oxygen species always correspond to the numbers of oxygen vacancies,39 which are beneficial for the activation of gaseous oxygen molecules in the feed gas. The existence of oxygen vacancies in CMy can also be evidently confirmed by the results of Raman spectroscopy analysis (Fig. S6†). Compared with reference CeO2, the main peak in the Raman spectra of CMy, the F2g mode of CeO2 shows a distinct red-shift from 464 to (433–452) cm−1, indicating that the interaction between Mn and Ce disturbed the fluorite-like structure to some extent and resulted in the formation of the oxygen vacancies in the CeO2 lattice.40 It is noting that the peak at 652 cm−1 for MnOx also shifts down to (605–637) cm−1 for CMy composites, which could also be related to the formation of oxygen vacancies in CMy.40 Usually, the high ratio of Oads/Olatt indicates a high activity toward oxidation reaction. But in the present work, CM20, though with the lowest Oads/Olatt ratio among all the studied catalysts, still shows the highest catalytic activity for soot combustion in NOx/O2, which suggests that there exists another key factor besides adsorbed oxygen species determining the catalytic activity.
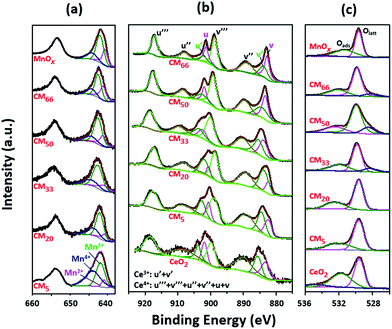 |
| Fig. 4 XPS spectra of (a) Mn 2p, (b) Ce 3d and (c) O 1s for all CMy composites and the reference MnOx and/or CeO2. | |
Table 1 XPS surface composition analysis of CMy composites and the references MnOx and/or CeO2
Sample |
Oads/(Oads + Olatt) (%) |
Mn2+/Mn3+/Mn4+ (%) |
Ce3+/(Ce3+ + Ce4+) (%) |
MnOx |
54.9 |
27.5/52.1/20.3 |
|
CM66 |
33.3 |
35.2/48.7/16.1 |
17.3 |
CM50 |
31.1 |
22.1/56.9/21.1 |
19.2 |
CM33 |
30.5 |
20.1/58.5/21.3 |
24.9 |
CM20 |
21.2 |
16.0/54.9/29.0 |
27.6 |
CM5 |
27.7 |
8.0/56.8/35.1 |
22.0 |
CeO2 |
46.6 |
|
18.2 |
As shown in the Fig. 4 and Table 1, both Mn and Ce species present various valence states. Thereinto, it is found that the ratio of Ce3+/(Ce3+ + Ce4+) firstly increases and then decreases with the increase of y in CMy, and the value reaches to a maximum value of 27.6% in CM20, which indicates the charge transfer between Mn and Ce within the interface (eqn (1)), as supported by the previous reports demonstrating negative charge transfer either from Mn to Ce or from Ce to Mn.41–45 Such a charge transfer will lead to the strong interaction between Ce and Mn species and thus the formation of uniform nanoparticles.46 This strong interaction between Mn and Ce can also be reflected in the results of H2-TPR profiles shown in Fig. S5,† in which, all of the CMy composites especially CM20 and CM33 show much lower reduction peak temperature than that for either MnOx or CeO2. Additionally, it is reported that the Mn4+ and Ce3+ can absorb and activate NO and O2,47,48 thus the Mn4+ and Ce3+ cations could serve as active sites for the catalytic soot combustion in NOx/O2 atmosphere, by promoting the formation of NO2.
|
Ce4+ + Mn3+ ↔ Ce3+ + Mn4+
| (1) |
To further verify the role of Mn4+ and Ce3+ cations in the catalytic soot oxidation, a parameter “Ω” (defined in eqn (2)) was introduced to quantify the concentration of Mn4+ and Ce3+ cations in the CMy composites.
Where
a = (1 −
y)[Ce
3+/(Ce
3+ + Ce
4+)],
b =
y[Mn
4+/(Mn
2+ + Mn
3+ + Mn
4+)], and
y is that in CM
y. Moreover, the relationship between “
Ω” value and the catalytic activity over the different catalysts CM
y are shown in
Fig. 5. It is found that for the CM
y composites, the larger
Ω value is, the higher catalytic activity is, which confirms the role of Mn
4+ and Ce
3+ cations as active sites for catalytic soot combustion in NO
x/O
2 over CM
y composites. Nevertheless, the sample CM
66 seems an exception with a lower
Ω value, showing higher catalytic activity than CM
50, which can be ascribed to the higher specific surface area and pore volume of CM
66 (72 m
2 g
−1 and 0.22 cm
3 g
−1, Table S2
†) than those of CM
50 (53 m
2 g
−1 and 0.11 cm
3 g
−1, Table S2
†).
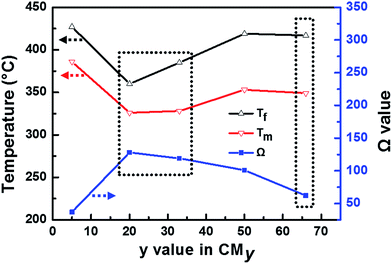 |
| Fig. 5 The different characteristic temperatures (Tm and Tf) and values of “Ω” as a function of y in CMy. Reaction conditions for catalytic soot combustion: 500 ppm NO and 10% O2 in N2 with a total flow of 200 mL min−1, mass of soot–catalyst–silica is 10–100–1000 mg, under loose contact mode. | |
3.5 SEM and TEM measurements for CM33
It is worth noting that, compared with CM20, CM33 shows a little lower catalytic activity and Ω value, and similar specific surface area but significantly lower pore volume. Therefore, the TEM and SEM analyses for CM33 were further performed, as shown in Fig. 6. It can be found that very different from the homogeneous morphology of CM20 particles shown in Fig. 3, CM33 shows some complex morphology in addition to the highly dispersive particles, such as micro-flakes (1 in Fig. 6c) and microspheres (3 in Fig. 6c). These two kinds of morphologies can also be found in the Ce-rich samples (CeO2 and CM5 in Fig. S3†), and the Mn-rich samples (CM50, CM66 and MnOx in Fig. S3†), respectively. Apparently, either the micro-flakes or the microsphere morphology in CM33 lacks the porous structure, thus leading to the lower pore volume than CM20 (Table S2†), which can strongly affect the efficient contact between catalyst and soot particles and decrease the activity for soot oxidation. Nevertheless, the main component in CM33 still presents similar size and chemical composition (Fig. 6b, 2 in Fig. 6c and S7†) to CM20 particles (Fig. 3), thus it remains higher catalytic activity than other reference samples. Therefore, it is reconfirmed that the homogeneous particles morphology with hierarchically porous structure is one of the key factors in the catalytic process of soot oxidation.
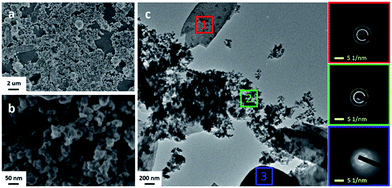 |
| Fig. 6 Low-magnification SEM image (a), high-magnification SEM image (b), TEM image (c) of CM33, and the corresponding SAED patterns to the different areas in (c). | |
Overall, the catalytic activity for soot oxidation in NOx/O2 atmosphere can be ascribed to the following two aspects: (1) abundant Mn4+ and Ce3+ cations (large Ω value) serve as active sites by promoting NO2 production, e.g., CM20 with the largest Ω value (Ω = 128) shows the best activity toward the soot oxidation. (2) The high surface area and pore volume as well as the typical morphology of the particles with hierarchically porous structure could improve the dispersion of active species and soot diffusion, e.g., CM66 with a lower Ω value (Ω = 62) exhibits a relatively high activity for soot oxidation due to its high specific surface area and pore volume.
3.6 A possible catalytic mechanism for soot oxidation
Based on the above results and analyses, a possible mechanism for the catalytic soot combustion in NOx/O2 over the sample CM20 was proposed, as shown in Scheme 1. In this catalytic reaction, the efficient contact between the catalyst and soot, and the abundant active Mn4+–Ce3+ species are two crucial issues determining the excellent catalytic performance. Generally, soot combustion over catalyst in NOx/O2 atmospheres is believed to follow two different pathways:49 (i) direct soot combustion by surface active oxygen species, (ii) NO-aided soot combustion. In Route (i), oxygen species absorbed and activated by oxygen vacancies (VO) on the catalyst surface can directly oxidize soot into CO2 (reaction (3), where O* is the active oxygen species).50
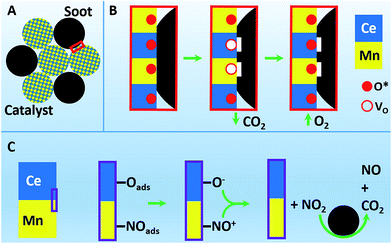 |
| Scheme 1 Schematic illustration of (A) the sufficient mixing of CM20 and soot particles, and the possible pathways of soot combustion on CM20 in NOx/O2: (B) Route (i): direct soot combustion by surface active oxygen species; (C) Route (ii): NO-aided soot combustion. | |
While in Route (ii), the NO-aided soot combustion can be expressed as the following reactions:
|
NOads + Mn4+ → NO+–Mn3+
| (4) |
|
Oads + Ce3+ → O−–Ce4+
| (5) |
|
NO+–Mn3+ + O−–Ce4+ → NO2 + Mn3+ + Ce4+
| (6) |
As supported by previous reports, it can be rationally deduced that the abundant Mn4+ and Ce3+ cations in CM20 play different roles in the catalytic process. Therein, Mn4+ could adsorb and activate NO into active species NO+, as shown in reaction (4);47 while Ce3+ could activate the absorbed oxygen Oads into O− (reaction (5)).48 Such resultant NO+ and O− species will react with each other to form NO2 at the interface between Ce and Mn oxides (reaction (6)),51 meanwhile, the produced Ce4+–Mn3+ will react through reaction (1) to recover the active site Ce3+–Mn4+, thus completing the catalysis cycle. Then in reaction (7),52 the produced NO2, as a stronger oxidant than O2, can be reduced back to NO by soot, which meanwhile can be oxidized to CO2 at low temperatures. In order to further confirm the role of NOx in the catalytic soot oxidation process, the temperature-programed oxidation of NO over CM33 with or without soot was further investigated, as shown in Fig. 7. It was found that with the addition of soot into the catalytic NO oxidation system, the NO2 proportion in NOx (= NO + NO2) decreases in temperature range 200–400 °C, especially in the range of 300–375 °C, where the CO2 concentration reaches its peak values. This coincidence confirms the reaction between NO2 and C, which facilitates CO2 production at the expense of NO2 (reaction (7)). Moreover, catalysis activity measurement over CM20 without the presence of NO was also conducted for comparison to the case with NO existing in the feed gas, as shown in Fig. S8,† clearly demonstrating the positive effect of NO on the catalytic activity towards soot oxidation.
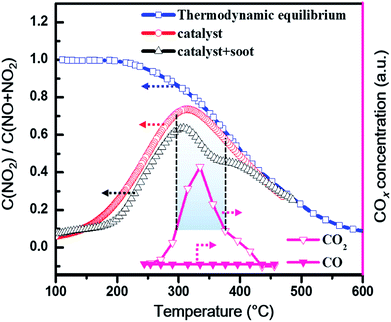 |
| Fig. 7 The temperature-programed oxidation of NO over CM33 with or without soot under loose contact mode. Reaction conditions: 500 ppm NO and 10% O2 in N2 with a total flow of 200 mL min−1, the mass of (soot–)catalyst–silica is (10–)100–1000 mg. | |
4. Conclusions
In summary, a facile co-precipitation method has been adopted to prepare a series of MnOx–CeO2 composites for the catalytic oxidation of soot in the simulated diesel emission. Thereinto, the optimized CM20 shows the highest catalytic activity (Tf = 360 °C), under loose contact mode. The excellent catalytic activity can be attributed to its uniform particle morphology with hierarchically porous structure and the rich active Mn4+ and Ce3+ cations resulting from the suitable doping amount of Mn, which greatly accelerate soot oxidation in NOx/O2. A possible mechanism was proposed to interpret the role of Mn4+–Ce3+ species as well as the active oxygen species in the catalytic process of soot combustion in NOx/O2. The MnOx–CeO2 composites prepared by this low-cost and easily-scalable method could find the promising practical application in the catalytic removal of soot in the diesel exhaust.
Acknowledgements
This research was sponsored by National Key Basic Research Program of China (2013CB933200), China National Funds for Distinguished Young Scientists (51225202) and National Natural Science Foundation of China (51502330).
Notes and references
- H. Horvath, Atmos. Environ., 1993, 27, 293–317 CrossRef.
- L. L. N. Guarieiro, A. F. de Souza, E. A. Torres and J. B. de Andrade, Atmos. Environ., 2009, 43, 2754–2761 CrossRef CAS.
- Z. Gao and W. Schreiber, Proc. Inst. Mech. Eng., Part D, 2002, 216, 619–628 CrossRef.
- D. B. Kittelson, J. Aerosol Sci., 1998, 29, 575–588 CrossRef CAS.
- D. Fino, Sci. Technol. Adv. Mater., 2007, 8, 93–100 CrossRef CAS.
- B. A. A. L. van Setten, M. Makkee and J. A. Moulijn, Catal. Rev.: Sci. Eng., 2001, 43, 489–564 CAS.
- E. Obeid, L. Lizarraga, M. N. Tsampas, A. Cordier, A. Boréave, M. C. Steil, G. Blanchard, K. Pajot and P. Vernoux, J. Catal., 2014, 309, 87–96 CrossRef CAS.
- X. H. Yu, Z. Zhao, Y. C. Wei, J. Liu, J. M. Li, A. J. Duan and G. Y. Jiang, Chin. J. Catal., 2015, 36, 1957–1967 CrossRef CAS.
- J. O. Uchisawa, A. Obuchi, Z. Zhao and S. Kushiyama, Appl. Catal., B, 1998, 18, L183–L187 CrossRef.
- X. D. Wu, S. Liu, F. Lin and D. Weng, J. Hazard. Mater., 2010, 181, 722–728 CrossRef CAS PubMed.
- J. F. Xu, J. Liu, Z. Zhao, C. M. Xu, J. X. Zheng, A. J. Duan and G. Y. Jiang, J. Catal., 2011, 282, 1–12 CrossRef CAS.
- D. Fino, N. Russo, G. Saracco and V. Specchia, J. Catal., 2006, 242, 38–47 CrossRef CAS.
- L. Castoldi, R. Matarrese, L. Lietti and P. Forzatti, Appl. Catal., B, 2009, 90, 278–285 CrossRef CAS.
- J. Liu, Z. Zhao, J. Q. Wang, C. M. Xu, A. J. Duan, G. Y. Jiang and Q. Yang, Appl. Catal., B, 2008, 84, 185–195 CrossRef CAS.
- P. Sudarsanam, B. Hillary, B. Mallesham, B. G. Rao, M. H. Amin, A. Nafady, A. M. Alsalme, B. M. Reddy and S. K. Bhargava, Langmuir, 2016, 32, 2208–2215 CrossRef CAS PubMed.
- S. Putla, M. H. Amin, B. M. Reddy, A. Nafady, K. A. Al Farhan and S. K. Bhargava, ACS Appl. Mater. Interfaces, 2015, 7, 16525–16535 CAS.
- P. Sudarsanam, K. Kuntaiaha and B. M. Reddy, New J. Chem., 2014, 38, 5991–6001 RSC.
- P. Sudarsanam, B. Hillary, D. K. Deepa, M. H. Amin, B. Mallesham, B. M. Reddy and S. K. Bhargava, Catal. Sci. Technol., 2015, 5, 3496–3500 CAS.
- P. Sudarsanam, A. Rangaswamy and B. M. Reddy, RSC Adv., 2014, 4, 46378–46382 RSC.
- G. B. Zhang, H. R. Chen, Y. Gong, Z. Shu, D. N. He, Y. Zhu, X. X. Zhou, X. Q. Fan, H. J. Zhang and J. L. Shi, Catal. Commun., 2013, 35, 105–109 CrossRef CAS.
- E. D. Banus, V. G. Milt, E. E. Miro and M. A. Ulla, Appl. Catal., B, 2013, 132, 479–486 CrossRef.
- K. Krishna, A. Bueno-Lopez, M. Makkee and J. A. Moulijn, Appl. Catal., B, 2007, 75, 189–200 CrossRef CAS.
- Y. C. Wei, J. Liu, Z. Zhao, Y. Chen, C. Xu, A. Duan, G. Jiang and H. He, Angew. Chem., Int. Ed., 2011, 50, 2326–2329 CrossRef CAS PubMed.
- C. M. Cao, Y. X. Zhang, D. S. Liu and M. Meng, Small, 2015, 11, 3659–3664 CrossRef CAS PubMed.
- L. F. Nascimento, J. F. Lima, P. C. de Sousa Filho and O. A. Serra, Chem. Eng. J., 2016, 290, 454–464 CrossRef CAS.
- Y. Nagahara, S. Sugawara and K. Shinohara, J. Power Sources, 2008, 182, 422–428 CrossRef CAS.
- I. Heo, J. W. Choung, P. S. Kim, I. S. Nam, Y. I. Song, C. B. In and G. K. Yeo, Appl. Catal., B, 2009, 92, 114–125 CrossRef CAS.
- S. T. Hussain, A. Sayari and F. C. Larachi, Appl. Catal., B, 2001, 34, 1–9 CrossRef CAS.
- D. Delimaris and T. Ioannides, Appl. Catal., B, 2008, 84, 303–312 CrossRef CAS.
- X. Y. Wang, Q. Kang and D. Li, Appl. Catal., B, 2009, 86, 166–175 CrossRef CAS.
- X. D. Wu, F. Lin, L. Wang, D. Weng and Z. Zhou, J. Environ. Sci., 2011, 23, 1205–1210 CrossRef CAS.
- M. L. Fu, K. L. Wang, R. P. Yu, X. E. Wen, M. Zhang, B. C. Huang, J. L. Wu, D. Q. Ye and H. Liang, Chin. J. Inorg. Chem., 2012, 28, 1593–1600 CAS.
- H. L. Zhang, Y. Zhu, S. D. Wang, M. Zhao, M. C. Gong and Y. Q. Chen, Fuel Process. Technol., 2015, 137, 38–47 CrossRef CAS.
- F. Lin, X. D. Wu, S. Liu, D. Weng and Y. Y. Huang, Chem. Eng. J., 2013, 226, 105–112 CrossRef CAS.
- L. N. Cai, Z. H. Hu, P. Branton and W. C. Li, Chin. J. Catal., 2014, 35, 159–167 CrossRef CAS.
- X. D. Wu, F. Lin, H. B. Xu and D. Weng, Appl. Catal., B, 2010, 96, 101–109 CrossRef CAS.
- J. Liu, Z. Zhao, J. Q. Wang, C. M. Xu, A. J. Duan, G. Y. Jiang and Q. Yang, Appl. Catal., B, 2008, 84, 185–195 CrossRef CAS.
- A. L. Kustov and M. Makkee, Appl. Catal., B, 2009, 88, 263–271 CrossRef CAS.
- S. H. Xie, Y. X. Liu, J. G. Deng, X. T. Zhao, J. Yang, K. F. Zhang, Z. Han and H. X. Dai, J. Catal., 2016, 342, 17–26 CrossRef CAS.
- X. M. Zhang, Y. Q. Deng, P. F. Tian, H. H. Shang, J. Xu and Y. F. Han, Appl. Catal., B, 2016, 191, 179–191 CrossRef CAS.
- Z. Zeng and M. Greenblatt, Phys. Rev. B: Condens. Matter Mater. Phys., 2001, 63, 224410 CrossRef.
- S. Imamura, Ind. Eng. Chem. Res., 1999, 38, 1743–1753 CrossRef CAS.
- X. D. Wu, H. N. Yu, D. Weng, S. Liu and J. Fan, J. Rare Earths, 2013, 31, 1141–1147 CrossRef CAS.
- P. Venkataswamy, D. Jampaiah, F. J. Lin, I. Alxneit and B. M. Reddy, Appl. Surf. Sci., 2015, 349, 299–309 CrossRef CAS.
- F. Larachi, J. Pierre, A. Adnot and A. Bernis, Appl. Surf. Sci., 2002, 195, 236–250 CrossRef CAS.
- J. Verhelst, D. Decroupet and D. de Vos, Catal. Sci. Technol., 2013, 3, 1579–1590 CAS.
- J. Wang, J. Z. Zhu, X. X. Zhou, Y. Y. Du, W. M. Huang, J. J. Liu, W. Q. Zhang, J. L. Shi and H. R. Chen, J. Mater. Chem. A, 2015, 3, 7631–7638 CAS.
- D. Jampaiah, K. M. Tur, S. J. Ippolito, Y. M. Sabri, J. Tardio, S. K. Bhargava and B. M. Reddy, RSC Adv., 2013, 3, 12963–12974 RSC.
- S. Liu, X. D. Wu, D. Weng and R. Ran, J. Rare Earths, 2015, 33, 567–590 CrossRef CAS.
- P. G. Harrison, I. K. Ball, W. Daniell, P. Lukinskas, M. Cespedes, E. E. Miro and M. A. Ulla, Chem. Eng. J., 2003, 95, 47–55 CrossRef CAS.
- Z. P. Wang, M. X. Chen and W. F. Shangguan, Acta Phys.-Chim. Sin., 2009, 25, 79–85 CAS.
- S. J. Jelles, R. R. Krul, M. Makee and J. A. Moulijn, Catal. Today, 1999, 53, 623–630 CrossRef CAS.
Footnote |
† Electronic supplementary information (ESI) available: Catalytic performance of samples reported in literatures together with CM20, and NULL as reference; SEM images of MnOx, CMy (y = 66, 50 and 5), CeO2 and soot; N2 adsorption/desorption isotherms & pore size distributions of CM20 and CM33; structural properties and H2-TPR profiles of all the catalysts studied, SEM-EDS results of different areas in CM33. See DOI: 10.1039/c6ra25738k |
|
This journal is © The Royal Society of Chemistry 2017 |
Click here to see how this site uses Cookies. View our privacy policy here.