DOI:
10.1039/C6RA15230A
(Paper)
RSC Adv., 2016,
6, 74895-74902
Ultra-small nickel phosphide nanoparticles as a high-performance electrocatalyst for the hydrogen evolution reaction†
Received
12th June 2016
, Accepted 27th July 2016
First published on 29th July 2016
Abstract
Development of efficient and robust abundant electrocatalysts for the hydrogen evolution reaction (HER) remains challenging. Previous studies have demonstrated that Ni2P nanostructures are efficient HER catalysts. In this study, we systematically investigated the synthesis of highly monodisperse, small-sized Ni2P nanoparticles with sizes ranging from 2 nm to 10 nm. Similar nanostructures were used to systematically analyze and compare catalytic activities for the HER. The resulting small-sized product possesses a high accessible surface area and a high density of exposed (001) facets. These favorable structural features render the Ni2P nanoparticles as highly active catalysts for the HER in acidic solutions. Experimental results show that 5.4 nm sample exhibits the optimal HER performance, with an HER overpotential of approximately 78 mV under an electrocatalytic current density of 10 mA cm−2 and a Tafel slope of 41.4 mV per decade. These products also show enhanced stability after a series of 500 potential cycles and constant current density during the test.
Introduction
With the rapid consumption of fossil fuels and serious environmental problems, hydrogen has been proposed as a renewable, secure, and clean alternative energy source1,2 because of its high energy density and clean combustion products.1,3 Electrochemical and photoelectrochemical water-splitting has attracted considerable research attention to achieve cost-effective and sustainable hydrogen production.4–6 Study of catalysts for hydrogen evolution reaction (HER) aims to decrease the electrochemical overpotential and increase energy conversion efficiency. Currently, the noble metal platinum (Pt) is the most popular catalyst for the HER because it produces negligible overpotential for a large current density and features long-term stability in acidic media.7–10 However, the limited availability and high price of Pt have sparked extensive research efforts toward the search for novel high-performing HER electrocatalysts.1,7,11
Over past decade, scientists have focused on searching for cost-effective, earth-abundant materials with high HER activity at low overpotentials to obtain efficient hydrogen economy. Several families of earth-abundant materials, including transition metal sulfides,12–23 selenides,12,24–30 phosphides,12,31–49 nitrides,12,50,51 and borides,52,53 are promising electrocatalysts for HER. Transition metal phosphides, including Ni2P,12,31,32,36,41,45,46,49 CoP,33,42,43,47 Co2P48 and FeP,38,44 have been identified as promising HER electrocatalysts. These materials can catalyze the high-temperature hydrodesulfurization (HDS) reaction,54 as does MoS2 and many of the other known HER catalysts.55,56
Nickel phosphide (Ni2P), which adopts the hexagonal Fe2P structure, is one of the most efficient HDS catalysts and outperforms commercially used Ni–Mo–S/Al2O3 catalysts in terms of activity and resistance to poisoning.32,57–59 Furthermore, density functional theory calculations have indicated that Ni2P can lead to high active sites of the surface (001), which enhance the rate of HER and renders the material comparable with [NiFe] hydrogenase.57 In the past three years, a variety of Ni–P HER catalysts with different compositions and morphologies have been reported,29,32,35,36,60–63 and their catalytic performance toward HER was carefully investigated. Among the aforementioned nickel phosphides, nanostructuring, i.e. tailing the size of Ni2P particles, is an important and useful approach to improve the intrinsic activity of catalysts. In this context, Ni2P nanoparticles with a size of 20 nm has been reported to show high electrocatalytic activity and stability for HER in acidic solutions.32 Based on this fact, with the increasing the total surface area relative to the geometric surface area that accompanies decreasing particle size, the number of available catalytic sites is expected to increase, thereby relaxing the stringent requirements of intrinsic catalytic activity required to achieve a specified level of performance.31–41 From this point of view, controlling the size of Ni2P particles is important to improve the catalytic performance of particles for HER.
In earlier reports, the strategies on preparation of Ni2P nanocrystals has been widely reported in literature.64–78 Among these, solution-based strategies that involve reaction of salts or organometallic reagents together with phosphines,73,74,78 or transformation of metal or metal oxide nanoparticles with phosphines,71,72,75–77 have a high potential to enable control of size. For example, Brock and co-workers reported the formation of nearly monodisperse spherical Ni2P nanoparticles through the reaction of metal nickel at 350 °C, with trioctylphosphine (TOP) as P source.77 This strategy is successful in the preparation of N–P nanomaterials. This mechanism of formation often leads to hollow particles as a result of the Kirkendall effect.75,76,79,80 Furthermore, the crystal structure, size, morphology, and composition of the can be controlled by varying reaction conditions, such as precursor ratio (P
:
Ni), oleylamine (OAm) quantity, temperature, and heating time. To our knowledge, compared with traditional II–VI and III–V nanoparticles,81 the ability to control size has yet to be demonstrated for Ni2P nanoparticles, especially for those with size below 10 nm.
In this work, we systematically investigated the synthesis of small-sized Ni2P nanoparticles through reaction of Ni(AC)2 with P(SiMe3)3 in a noncoordinating solvent, octadecene (ODE). The size of particles was found to be tunable from 2–10 nm by only changing the concentration of OAm from 0–0.4 M. This facile synthetic method enhances the convenience of systematically comparing the structural property (size) and catalytic activity for HER and establishing the relationship between size and catalytic activity. We find that the small-sized Ni2P nanoparticles (5.4 nm) not only decreases the overpotential but also decreases the Tafel slope, thus significantly improving the HER catalytic performance. The optimal performance among the three samples used can achieve a catalytic current density of 20 mA cm−2 at an overpotential of 93 mV with a Tafel slope of 41.4 mV per decade using 0.5 M H2SO4 solution by deposition of 5.4 nm Ni2P nanoparticles at a mass loading of approximately 1 mg cm−2 onto a 0.20 cm2 Ti foil substrate. Small sized Ni2P therefore is an active HER electrocatalyst that is comprised entirely of inexpensive and earth-abundant elements while exhibiting improved performance relative to other comparable earth-abundant electrocatalysts.
Experimental section
Materials
Technical grade (90%) octadecene (ODE), nickel(II) acetate tetrahydrate (Ni(AC)2·4H2O, 99.99%), oleic acid (OA, 90%), trioctylphosphine (TOP, 90%), and tris(trimethylsilyl)phosphine (P(SiMe3)3, 95%) are purchased from Alfa. Oleylamine (OAm, 70%), Pt/C (20 wt% Pt on Vulcan XC-72R) and Nafion-117 solution (5% in a mixture of lower aliphatic alcohols and water) are purchased from Aldrich. Sulfuric acid (98%), n-hexane, toluene, acetone, chloroform, and methanol are obtained from Beijing Chemical Reagent Ltd., China. All reagents are used as received without further experimental purification.
Synthesis of Ni precursor solution (0.1 M)
0.2514 g of Ni(AC)2 (1.0 mmol) is dissolved in 0.9 mL of oleic acid (2.5 mmol) and 9.1 mL of ODE at 220 °C under N2 flow to form a light yellow solution. Then cool down to the room temperature, the solution turns green.
Synthesis of P precursor solution (0.1 M)
0.2500 g of P(SiMe3)3 (1 mmol) is dissolved in 10 mL of ODE to form a clear colorless solution.
Synthesis of 2.8 nm Ni2P nanoparticles
In a typical reaction, 2 mL of Ni precursor solution (0.1 M, 0.2 mmol) and 3 mL of ODE are loaded into a reaction flask. The solution is heated to 180 °C under N2 flow. 1 mL of P precursor solution (0.1 M, 0.1 mmol) is injected quickly into the reaction flask, then the reaction temperature is set to 180 °C to grow nanoparticles. After 20 min, the solution is cooled down to room temperature.
Synthesis of 5.4 nm Ni2P nanoparticles
In a typical reaction, 2 mL of Ni precursor solution (0.1 M, 0.2 mmol), 0.2 mL of OAm, and 3 mL of ODE are loaded into a reaction flask. The solution is heated to 180 °C under N2 flow. 1 mL of P precursor solution (0.1 M, 0.1 mmol) is injected quickly into the reaction flask, and the reaction temperature is set to 180 °C to grow nanoparticles. After 20 min, the solution is cooled down to room temperature.
Synthesis of 8.1 nm Ni2P nanoparticles
In a typical reaction, 2 mL of Ni precursor solution (0.1 M, 0.2 mmol), 0.5 mL of OAm, and 3 mL of ODE are loaded into a reaction flask. The solution is heated to 180 °C under N2 flow. 1 mL of P precursor solution (0.1 M, 0.1 mmol) is injected quickly into the reaction flask, and the reaction temperature is set to 180 °C to grow nanoparticles for 20 min. Finally, the solution is cooled down to room temperature.
Synthesis of 9.5 nm Ni2P nanoparticles
In a typical reaction, 2 mL of Ni precursor solution (0.1 M, 0.2 mmol), 1.0 mL of OAm, and 3 mL of ODE are loaded into a reaction flask. The solution is heated to 180 °C under N2 flow and 1 mL of P precursor solution (0.1 M, 0.1 mmol) is injected quickly, and the reaction temperature is set to 180 °C to grow nanoparticles for 20 min and cooled down to room temperature.
Crystallization and purification of Ni2P nanoparticles
The samples are isolated by adding isopropanol into the hexane/ODE solution. After centrifugation, decantation and drying under a flow of N2, the resulting Ni2P nanoparticles are dispersed in 4 mL of ODE in a reaction flask. 1 mL of TOP is add into the reaction flask and heated to 300 °C for 5 min under N2 flow. Finally, the solution is cooled down to room temperature. The samples are isolated by adding acetone into the hexane/ODE solution.
Electrochemical measurements
Typically, 10 mg of Ni2P NCs and 2 mL of n-hexane are mixed together to form a stock solution. 5 μL of the stock solution is used to deposit the nanoparticles onto 0.2 cm2 pieces of titanium foil. The nanoparticle-modified Ti foils are annealed for 2 h at 450 °C under N2 flow after deposition and drying. Anchor the foils onto a polyvinyl chloride-coated copper wire using Ag paint. Two-part epoxy is then used to cover all surfaces except for the nanoparticle films. To evaluate the electrochemical activities toward HER for various electrocatalysts, linear sweep voltammetry (LSV) measurements are conducted in 0.5 M H2SO4 in a three-electrode electrochemical cell with a scan rate of 5 mV s−1 using a saturated calomel electrode (SCE) as the reference electrode, a platinum electrode as the counter electrode, and the Ti electrode with various catalysts as the working electrode on a CHI662E potentiostat (CH Instruments, China) at room temperature. All of the potentials are calibrated to a reversible hydrogen electrode (RHE). Prior to any electrochemical measurement, the electrolyte solution is purged with N2 flow for 1 h to remove completely the oxygen, and stable polarization performance curves are recorded after 10 cycles. All the potentials reported in our manuscript are against RHE. Pt/C ink was prepared by dispersing 2 mg of Pt/C (20 wt% Pt on Vulcan XC-72) in 0.4 mL of EtOH with 17.5 μL of 5 wt% Nafion solution, 5 μL of the stock solution was used. The stability of the catalyst electrodes was characterized by chronoamperometry applying an external bias of 150 mV.
Characterization
Low-resolution TEM images are taken on a JEOL 100CX transmission electron microscope with an acceleration voltage of 100 kV. Carbon-coated copper grids are dipped in chloroform solutions of SAMPLE and taken out to deposit nanoparticles on their carbon films. High-resolution TEM images (HR-TEM) pictures are taken using a Taitan microscope with an acceleration voltage of 300 kV. X-ray powder diffraction (XRD) patterns are obtained using a Philips PW1830 X-ray diffract meter operated at 40 kV and 30 mA with Cu Kα radiation. Measurements are performed in a 2θ (θ: diffraction angle) range from 30 to 60 degrees. Elemental compositions of NCs are determined by energy-dispersive spectroscopy (EDS) using a Philips ESEM XL30 scanning electron microscope equipped with a field emission gun and operated at 10 kV.
Results and discussion
In our previous work, we found that reaction temperature is one of the most significant factors in controlling the particle size.82,83 In this study, reaction temperature was used to control the synthesis of Ni2P nanoparticles through the injection of the P precursor into the reaction solution as described in the experimental section. Experimental results show that virtually the same size was observed in samples prepared at 100 °C and 180 °C (Fig. S1†), indicating that the reaction is invalid in the control of particle sizes. This finding is highly similar to our previous report on the preparation of InP nanoparticles,84 in which particle size is almost independent of reaction temperature. However, our previous experimental results show that the size of InP nanoparticles is controllable through the introduction of amine into the reaction system.85 A more detailed mechanism study on the size tunability of colloidal particles synthesized in the presence of amine has been reported recently.86 On this basis, we conducted the synthesis of Ni2P nanoparticles through the reaction of Ni(AC)2 with P(SiMe3)3 as P source. The reaction was carried out in a noncoordinating solvent ODE in presence of OAm via a two-step process involving the generation of precursor particles at 180 °C, followed by further reaction and crystallization at 300 °C. In a typical reaction, 2 mL of the Ni precursor solution (0.2 mmol), 0.2 mL of OAm, and 3 mL of ODE are loaded into a reaction flask. The solution is heated to 180 °C under N2 flow. A 1 mL volume of P precursor solution (0.1 mmol) is rapidly injected into the reaction flask. Reaction temperature is set to 180 °C to grow nanoparticles for 20 min. Subsequently, 1 mL of TOP is added into the reaction flask, which was heated to 300 °C for 5 min under N2 flow. Finally, the solution is cooled down to room temperature. The samples are isolated by the addition of acetone into the hexane/ODE solution for further use.
Fig. 1a and d show the wide-field TEM images of three representative samples obtained at different amine concentrations (0.1, 0.2, 0.3, and 0.5 mM). The as-prepared samples displayed a nearly spherical shape with narrow size distribution and a standard deviation of 5–10% without post-preparation fractionation or size sorting. The particle size can be tuned from 2.8, 5.4, and 8.1 nm to 9.5 nm, as the increase in amine concentration from 0 M to 0.4 M. We show the correlation between diameters of the nanoparticles and the concentration of OAm in Fig. 1f. Notably, with the further increased use of OAm to 0.8 M, the particle size of as-prepared samples remained almost unchanged (not shown here). Thus, the particle size of the resulting particles was found to be strongly dependent on amine concentration ranging from 0 M to 0.4 M, with the other reaction conditions being constant (Fig. 1f). This variation trend in particle size was confirmed using prepared CdSe and InP nanoparticles in previous reports; the results showed the amine group coordinates to metal carboxylate precursors, and changing the reaction rate of the metal precursor with chalcogenides.87,88 Similarly, this influence is the result of the tuned reactivity of nickel precursors in the noncoordinating solvent. That a relatively inertial precursor results in a relatively low nuclei concentration has been proposed and experimentally corroborated.89 As a result, more precursors remained, and the final particle size is relatively large after subsequent growth. We found that the size of synthesized particles is also tunable by changing the reaction temperature in the presence of amine. For example, particles with 11.8 nm size are obtainable in the presence of amine (0.2 M) and at a reaction temperature of 120 °C (Fig. S2†); however, we did not provide more detailed information on the relation of reaction temperature to particle size in the presence of amine. The high-resolution TEM images (Fig. 1e) show an 8.1 nm nanoparticle without evidence of crystallinity, as proven by the lack of continuous lattice fringes throughout particle. This finding suggests that the particles are amorphous. To further characterize crystal structure, we investigated the crystallographic properties of the particles by powder X-ray diffraction (XRD). No distinguishable diffraction peaks are observable in the XRD patterns of the samples synthesized at 180 °C (Fig. 2a), thus suggesting that the as-synthesized nanoparticles are amorphous. The chemical composition of the resulting products is determined mainly by energy-dispersive spectroscopy (EDS) (Fig. 2b), which verifies that Ni and P are present in a 2
:
1 ratio, indicating the formation of amorphous Ni2P nanoparticles.
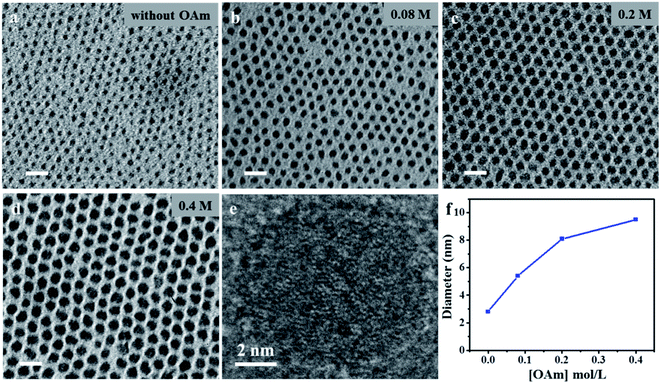 |
| Fig. 1 Low-magnification TEM images of as prepared products with different sizes synthesized at 180 °C by tuning the concentration of OAm: (a) 2.8, (b) 5.4, (c) 8.1, and (d) 9.5 nm. The scale bar is 20 nm. (e) HRTEM image of an 8.1 nm amorphous nanoparticles. (f) Diameters of particles synthesized at 180 °C in octadecene as a function of the added OAm. | |
 |
| Fig. 2 (a) XRD patterns of as prepared samples with different sizes synthesized at 180 °C. (b) EDS spectrum of the sample with a size of 8.1 nm. | |
Previous reports showed that low reaction temperature results in the formation of amorphous Ni2P nanoparticles by using TOP as anion precursor, and subsequent heating to 300 °C for 30 min converts amorphous particles to crystalline solid product.77 Hence, the as-prepared products (at 180 °C) were further heated to high reaction temperature. Fig. 3a–c show the TEM images of the amorphous products after annealing at 300 °C for 5 min, corresponding to the samples shown in Fig. 1. These particles completely remain spherical, and the size of particles was virtually unchanged before and after annealing. Notably, amorphous particles with extremely small size particles become unstable after high temperature annealing. For example, particles of 2.8 nm size resulted in an undesired Ostwald ripening or defocusing of size distribution (Fig. S3†). High-resolution TEM analysis shows that the annealed nanoparticles are single crystalline with continuous lattice fringes throughout the particle. In Fig. 3d, the observed 5.2, 3.4, and 2.2 Å lattice fringes correspond to the (010), (001), and (0
1) planes of Ni2P, respectively. Among other facets, Ni2P (001) crystal planes have previously been predicted theoretically as an active HER catalyst.32,57,90–92 This result indicates that amorphous Ni2P nanoparticles become crystalline upon heating to 300 °C, as is consistent with results reported in the literature.77
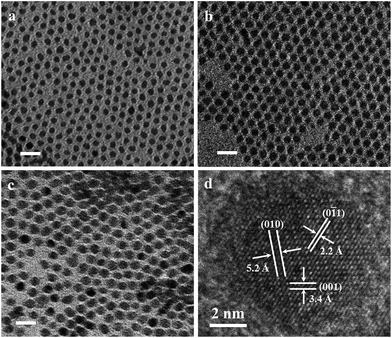 |
| Fig. 3 Low-magnification TEM images of the samples with different sizes after annealing at 300 °C for 5 min: (a) 5.4, (b) 8.1, and (c) 9.5 nm. The scale bar is 20 nm. (d) High-resolution TEM image of the sample shown in (b). | |
To further identify the crystal structure of the as-prepared samples, we investigated the crystallographic properties by powder XRD. In comparison with the results shown in Fig. 2, the XRD pattern of the samples is composed of the characteristic peaks of bulk Ni2P, which consists of the (111), (201), and (210) peaks at 40.8°, 44.6°, and 47.3°, respectively. All diffraction peaks in Fig. 4a show that each size of amorphous Ni2P nanoparticles are completely converted into crystalline-phase pure samples and further confirm the formation of Fe2P-type in high yield (JCPDS card no: 74-1385).32,77 The diffraction peaks were broad because of the finite particle size. Moreover, the broad diffraction peak at about 54.5° is due to the overlap of the (002) and (211) peaks at 54.2°, and 54.9°. Scherrer analysis of the peak widths indicates an average grain size of 5.9, 8.4, and 10.4 nm. Consistent with Scherrer analysis, the crystal domain sizes estimated from the peak width by using the Scherrer equation match reasonably well with the sizes of nanoparticles determined by TEM in Fig. 3a–c. The chemical composition of the resulting nanoparticles after crystallization is determined mainly by EDS (Fig. 4b). EDS analysis of an ensemble of the samples with annealing at 300 °C consistently yielded a particle ratio of 1.9
:
1. The resulting NCs were thoroughly washed with hexane to remove any excess TOP.
 |
| Fig. 4 (a) XRD patterns of as prepared samples with different sizes after annealing at 300 °C for 5 min. (b) EDS spectrum of 8.1 nm crystallographic nanoparticles. | |
The electrocatalytic HER activities of 5.4, 8.1, and 9.5 nm Ni2P particles under acidic conditions with the use of a 0.5 M H2SO4 solution are assessed by linear sweep voltammetry (LSV) with a three-electrode setup. To remove the organic residue, the as-made Ni2P NCs are deposited onto 0.2 cm2 pieces of titanium foil and annealed at 450 °C for 2 hours at the heating rate of 2.0 °C min−1 under N2 flow. After annealing, the foils are attached to a polyvinyl chloride-coated Cu wire. Then, a two-part epoxy is used to insulate all conductive surfaces from the electrode solution except for the Ni2P nanoparticle-decorated side of the Ti electrode, which functioned as the working electrode.32 During the annealing process, the Ni2P particles remained spherical, as determined by TEM (Fig. S8†).
Previous studies have shown that the HER activity of Ni2P particles is highly dependent on the (001) crystal planes.32 Thus, designing smaller particles with more activity sites is one effective strategy to enhance activity. Fig. 5a shows the polarization curves of Ti electrodes modified by 5.4, 8.1, and 9.5 nm Ni2P particles (Ni2P loading: 1.0 mg cm−2) with a scan rate of 5 mV s−1. In sharp contrast, 5.4 nm Ni2P nanoparticles are highly active toward the HER. The HER of 5.4 nm Ni2P particles begins at an overpotential of approximately 30 mV; beyond this overpotential, the HER current density increases rapidly, whereas the largest Ni2P particles began at 50 mV. The 5.4, 8.1, and 9.5 nm Ni2P particle electrodes require overpotentials of −78 ± 3, −91 ± 2, and −102 ± 3 mV, respectively, to produce cathodic current densities of −10 mA cm−2 and require overpotentials of −93 ± 2, −111 ± 2, and −127 ± 3 mV, respectively, to produce cathodic current densities of −20 mA cm−2. The Tafel plots of the particles derived from the polarization curves shown in Fig. 5a fit well with the Tafel equation η = b
log
j + a, where j is the current density, b is the Tafel slope, and a is the intercept relative to the exchange current density (j0) at different overpotential ranges; the region of η = 10–125 mV was selected to provide a clear comparison, as shown in Fig. 5b. The Tafel plots resulted in slopes of approximately 41.4, 44.9, and 46.7 mV per decade, respectively, for the Ni2P particle catalyst. Compared with previous works,18,32,93–95 the electrochemical data indicate that ultra-small sized Ni2P particles are highly active HER catalysts (Table 1). Aside from a stringent requirement for high activity, good durability is another important criterion for electrocatalyst selection. The stability of catalytic response is further evaluated by cycling the particles continuously for 500 cycles ranging from +0.22 to −0.23 V versus RHE at a scan rate of 5 mV s −1 (Fig. 6). After 500 cycles, the overpotential required by the 8.1 nm Ni2P-decorated Ti electrode to reach a current density of −20 mA cm−2 increased by only 15 mV (from −111 mV to −126 mV), indicating good durability. Some of the Ni2P particles detach from the electrode during the long tests, therefore, the increase in galvanostatic overpotential may be attributable to a decrease in mass loading over time. The Ni2P NPs are too small to be stable in neutral and basic solution. The Ni2P quickly degraded to Ni, and the HER performance declined rapidly. We also carried out the stability test of 8.1 nm samples by i–t test (Fig. S9†), and investigate the morphology and composition of the catalyst after long-term stability test by XRD, EDS and SEM (Fig. S10 and S11†). The calculations used to determine the TOF values are shown (Table S1†). These calculations thus represent only an estimate of the actual TOFs because the calculation does not account for surface area obscured by interparticle contacts or for porosity. Additionally, the specific active sites of Ni2P are not known explicitly. The TOFs of Ni2P NPs with different sizes are different. The relationship between BET, size, and the amount of specific active sites is under researching.
 |
| Fig. 5 (a) Polarization curves of Ni2P nanoparticles along with data for comparison of glassy carbon, Ti foil, and Pt in 0.50 M H2SO4. (b) Corresponding Tafel plots of various sizes of Ni2P nanoparticles with Tafel slops of ∼41.4, 44.9, and 46.7 mV per decade along with data for comparison of Pt/C with Tafel slops of ∼30 mV per decade. | |
Table 1 Comparison of different HER electrocatalysts available from the literature
Reference |
Material |
Size |
η (mV vs. RHE) for J = −10 mA cm−2 |
Tafel slop (mV dec−1) |
Stability |
This study |
Ni2P NCs |
5.4 nm |
−78 |
41.4 |
Stable |
32 |
Ni2P NPs |
21 nm |
−130 |
48 |
Stable |
93 |
CoP/CNT |
2–3 nm |
−122 |
54 |
Stable |
95 |
NiS2 |
80–200 nm |
N/A |
48.8 |
N/A |
95 |
FeCoS2 |
50–100 nm |
−196 |
47.5 |
N/A |
18 |
WS2 |
5–20 nm |
−142 |
48 |
Stable |
94 |
MoS2 nanosheet |
100–200 nm |
−190 |
50 |
Stable |
 |
| Fig. 6 Polarization curves of 8.1 nm Ni2P nanoparticles in 0.5 M H2SO4 initially and after 100, 200, 300, 400, and 500 CV sweeps between +0.22 and −0.23 V vs. RHE. | |
Conclusions
Small-sized Ni2P nanoparticles are obtained for the first time through reaction of Ni(AC)2 with P(SiMe3)3. The size of particles is tunable within a range of 2–10 nm by changing only the concentration of OAm from 0–0.4 M at a reaction temperature. Subsequent heating to 300 °C for 5 min converts amorphous particles to crystalline Ni2P particles, as identified by high-resolution TEM and XRD measurements. This facile synthetic method imparts convenience to the systematic comparison of the structural property (size) and catalytic activity for HER and establishment of the relationship between size and catalytic activity. Experimental results show that the small-sized Ni2P nanoparticles not only reduced the overpotential but also decreased the Tafel slope, thus significantly improving HER catalytic performance. The optimal performance among the three samples used can achieve a catalytic current density of 20 mA cm−2 at an overpotential of 93 mV, resulting in a Tafel slope of 41.4 mV per decade H2SO4 by deposition of 5.4 nm Ni2P nanoparticles at a mass loading of approximately 1 mg cm−2 onto a 0.20 cm2 Ti foil substrate.
Acknowledgements
This work was supported by the National Natural Science Foundation of China (21373097 and 51072067).
References
- J. A. Turner, Science, 2004, 305, 972 CrossRef CAS PubMed.
- N. S. Lewis and D. G. Nocera, Proc. Natl. Acad. Sci. U. S. A., 2006, 103, 15729 CrossRef CAS PubMed.
- M. S. Dresselhaus and I. L. Thomas, Nature, 2001, 414, 332 CrossRef CAS PubMed.
- H. B. Gray, Nat. Chem., 2009, 1, 7 CrossRef CAS PubMed.
- D. G. Nocera, Acc. Chem. Res., 2012, 45, 767 CrossRef CAS PubMed.
- M. G. Walter, E. L. Warren, J. R. McKone, S. W. Boettcher, Q. Mi, E. A. Santori and N. S. Lewis, Chem. Rev., 2010, 110, 6446 CrossRef CAS PubMed.
- M. S. Faber and S. Jin, Energy Environ. Sci., 2014, 7, 3519 CAS.
- S. Schuldiner, J. Electrochem. Soc., 1959, 106, 891 CrossRef CAS.
- K. C. Neyerlin, W. B. Gu, J. Jorne and H. A. Gasteiger, J. Electrochem. Soc., 2007, 154, B631 CrossRef CAS.
- W. C. Sheng, H. A. Gasteiger and Y. Shao-Horn, J. Electrochem. Soc., 2010, 157, B1529 CrossRef CAS.
- P. C. K. Vesborg and T. F. Jaramillo, RSC Adv., 2012, 2, 7933 RSC.
- Q. Lu, Y. Yu, Q. Ma, B. Chen and H. Zhang, Adv. Mater., 2016, 28, 1917 CrossRef CAS PubMed.
- C. G. Morales-Guio and X. Hu, Acc. Chem. Res., 2014, 47, 2671 CrossRef CAS PubMed.
- T. P. Nguyen, S. Choi, J.-M. Jeon, K. C. Kwon, H. W. Jang and S. Y. Kim, J. Phys. Chem. C, 2016, 120, 3929 CAS.
- T. Wang, L. Liu, Z. Zhu, P. Papakonstantinou, J. Hu, H. Liu and M. Li, Energy Environ. Sci., 2013, 6, 625 CAS.
- D. Voiry, H. Yamaguchi, J. Li, R. Silva, D. C. Alves, T. Fujita, M. Chen, T. Asefa, V. B. Shenoy, G. Eda and M. Chhowalla, Nat. Mater., 2013, 12, 850 CrossRef CAS PubMed.
- J. D. Benck, T. R. Hellstern, J. Kibsgaard, P. Chakthranont and T. F. Jaramillo, ACS Catal., 2014, 4, 3957 CrossRef CAS.
- L. Cheng, W. Huang, Q. Gong, C. Liu, Z. Liu, Y. Li and H. Dai, Angew. Chem., Int. Ed., 2014, 53, 7860 CrossRef CAS PubMed.
- M. A. Lukowski, A. S. Daniel, C. R. English, F. Meng, A. Forticaux, R. J. Hamers and S. Jin, Energy Environ. Sci., 2014, 7, 2608 CAS.
- M. A. Lukowski, A. S. Daniel, F. Meng, A. Forticaux, L. Li and S. Jin, J. Am. Chem. Soc., 2013, 135, 10274 CrossRef CAS PubMed.
- M. S. Faber, R. Dziedzic, M. A. Lukowski, N. S. Kaiser, Q. Ding and S. Jin, J. Am. Chem. Soc., 2014, 136, 10053 CrossRef CAS PubMed.
- M. S. Faber, M. A. Lukowski, Q. Ding, N. S. Kaiser and S. Jin, J. Phys. Chem. C, 2014, 53, 7860 Search PubMed.
- D. Kong, J. J. Cha, H. Wang, H. R. Lee and Y. Cui, Energy Environ. Sci., 2013, 6, 3553 CAS.
- D. Kong, H. Wang, Z. Lu and Y. Cui, J. Am. Chem. Soc., 2014, 136, 4897 CrossRef CAS PubMed.
- F. H. Saadi, A. I. Carim, J. M. Velazquez, J. H. Baricuatro, C. C. L. McCrory, M. P. Soriaga and N. S. Lewis, ACS Catal., 2014, 4, 2866 CrossRef CAS.
- D. Kong, H. Wang, J. J. Cha, M. Pasta, K. J. Koski, J. Yao and Y. Cui, Nano Lett., 2013, 13, 1341 CrossRef CAS PubMed.
- A. I. Carim, F. H. Saadi, M. P. Soriaga and N. S. Lewis, J. Mater. Chem. A, 2014, 2, 13835 CAS.
- F. Gong, X. Xu, Z. Li, G. Zhou and Z. S. Wang, Chem. Commun., 2013, 49, 1437 RSC.
- H. Zhang, B. Yang, X. Wu, Z. Li, L. Lei and X. Zhang, ACS Appl. Mater. Interfaces, 2015, 7, 1772 CAS.
- H. Liang, L. Li, F. Meng, L. Dang, J. Zhuo, A. Forticaux, Z. Wang and S. Jin, Chem. Mater., 2015, 27, 5702 CrossRef CAS.
- B. You, N. Jiang, M. Sheng, M. W. Bhushan and Y. Sun, ACS Catal., 2016, 6, 714 CrossRef CAS.
- E. J. Popczun, J. R. McKone, C. G. Read, A. J. Biacchi, A. M. Wiltrout, N. S. Lewis and R. E. Schaak, J. Am. Chem. Soc., 2013, 135, 9267 CrossRef CAS PubMed.
- M. Zeng, H. Wang, C. Zhao, J. Wei, W. Wang and X. Bai, Sci. Bull., 2015, 60, 1426 CrossRef CAS.
- T. Wang, K. Du, W. Liu, Z. Zhu, Y. Shao and M. Li, J. Mater. Chem. A, 2015, 3, 4368 CAS.
- J. Kibsgaard and T. F. Jaramillo, Angew. Chem., Int. Ed., 2014, 53, 14433 CrossRef CAS PubMed.
- P. Jiang, Q. Liu and X. Sun, Nanoscale, 2014, 6, 13440 RSC.
- P. Xiao, M. A. Sk, L. Thia, X. Ge, R. J. Lim, J.-Y. Wang, K. H. Lim and X. Wang, Energy Environ. Sci., 2014, 7, 2624 CAS.
- J. F. Callejas, J. M. McEnaney, C. G. Read, J. C. Crompton, A. J. Biacchi, E. J. Popczun, T. R. Gordon, N. S. Lewis and R. E. Schaak, ACS Nano, 2014, 8, 11101 CrossRef CAS PubMed.
- J. M. McEnaney, J. C. Crompton, J. F. Callejas, E. J. Popczun, A. J. Biacchi, N. S. Lewis and R. E. Schaak, Chem. Mater., 2014, 26, 4826 CrossRef CAS.
- J. M. McEnaney, J. Chance Crompton, J. F. Callejas, E. J. Popczun, C. G. Read, N. S. Lewis and R. E. Schaak, Chem. Commun., 2014, 50, 11026 RSC.
- M. H. Hansen, L. A. Stern, L. Feng, J. Rossmeisl and X. Hu, Phys. Chem. Chem. Phys., 2015, 17, 10823 RSC.
- J. Tian, Q. Liu, A. M. Asiri and X. Sun, J. Am. Chem. Soc., 2014, 136, 7587 CrossRef CAS PubMed.
- D. Zhou, L. He, W. Zhu, X. Hou, K. Wang, G. Du, C. Zheng, X. Sun and A. M. Asiri, J. Mater. Chem. A, 2016, 4, 10114 CAS.
- P. Jiang, Q. Liu, Y. Liang, J. Tian, A. M. Asiri and X. Sun, Angew. Chem., Int. Ed., 2014, 53, 12855 CrossRef CAS PubMed.
- Y. Pan, Y. Liu and C. Liu, J. Power Sources, 2015, 285, 169 CrossRef CAS.
- Y. Pan, W. Hu, D. Liu, Y. Liu and C. Liu, J. Mater. Chem. A, 2015, 3, 13087 CAS.
- Y. Pan, Y. Lin, Y. Chen, Y. Liu and C. Liu, J. Mater. Chem. A, 2016, 4, 4745 CAS.
- Y. Pan, Y. Liu, Y. Lin and C. Liu, ACS Appl. Mater. Interfaces, 2016, 8, 13890 CAS.
- Y. Pan, N. Yang, Y. Chen, Y. Lin, Y. Li, Y. Liu and C. Liu, J. Power Sources, 2015, 297, 45 CrossRef CAS.
- W. F. Chen, J. T. Muckerman and E. Fujita, Chem. Commun., 2013, 49, 8896 RSC.
- B. Cao, G. M. Veith, J. C. Neuefeind, R. R. Adzic and P. G. Khalifah, J. Am. Chem. Soc., 2013, 135, 19186 CrossRef CAS PubMed.
- M. D. Scanlon, X. Bian, H. Vrubel, V. Amstutz, K. Schenk, X. Hu, B. Liu and H. H. Girault, Phys. Chem. Chem. Phys., 2013, 15, 2847 RSC.
- H. Vrubel and X. Hu, Angew. Chem., Int. Ed., 2012, 124, 12875 CrossRef.
- S. T. Oyama, J. Catal., 2003, 216, 343 CrossRef CAS.
- R. Prins, V. H. J. De Beer and G. A. Somorjai, Catal. Rev., 1989, 31, 1 CAS.
- J. R. Grechowiak, I. Wereszczako-Zielinska and K. Mrozinska, Catal. Today, 2007, 119, 23 CrossRef.
- P. Liu and J. A. Rodriguez, J. Am. Chem. Soc., 2005, 127, 14871 CrossRef CAS PubMed.
- P. Liu, J. A. Rodriguez and J. T. Muckerman, J. Phys. Chem. B, 2004, 108, 18796 CrossRef CAS.
- P. C. K. Vesborg, B. Seger and I. Chorkendorff, J. Phys. Chem. Lett., 2015, 6, 951 CrossRef CAS PubMed.
- Z. P. Huang, Z. B. Chen, Z. Z. Chen, C. C. Lv, H. Meng and C. Zhang, ACS Nano, 2014, 8, 8121 CrossRef CAS PubMed.
- Z. H. Pu, Q. Liu, C. Tang, A. M. Asiri and X. P. Sun, Nanoscale, 2014, 6, 11031 RSC.
- A. R. J. Kucernak and V. N. N. Sundaram, J. Mater. Chem. A, 2014, 2, 17435 CAS.
- Y. Pan, Y. R. Liu, J. C. Zhao, K. Yang, J. L. Liang, D. D. Liu, W. H. Hu, D. P. Liu, Y. Q. Liu and C. G. Liu, J. Mater. Chem. A, 2015, 3, 1656 CAS.
- W. Maneeprakorn, C. Q. Nguyen, M. A. Malik, P. O'Brien and J. Raftery, Dalton Trans., 2009, 2103 RSC.
- S. J. Sawhill, D. C. Phillips and M. E. Bussell, J. Catal., 2003, 215, 208 CrossRef CAS.
- S. J. Sawhill, K. A. Layman, D. R. Van Wyk, M. H. Engelhard, C. Wang and M. E. Bussell, J. Catal., 2005, 231, 300 CrossRef CAS.
- S. Yang and R. Prins, Chem. Commun., 2005, 4178 RSC.
- A. Panneerselvam, M. A. Malik, M. Afzaal, P. O'Brien and M. Helliwell, J. Am. Chem. Soc., 2008, 130, 2420 CrossRef CAS PubMed.
- S. Liu, X. Liu, L. Xu, Y. Qian and X. Ma, J. Cryst. Growth, 2007, 304, 430 CrossRef CAS.
- X. Hu and J. C. Yu, Chem. Mater., 2008, 20, 6743 CrossRef CAS.
- E. Muthuswamy and S. L. Brock, J. Am. Chem. Soc., 2010, 132, 15849 CrossRef CAS PubMed.
- A. E. Henkes and R. E. Schaak, Chem. Mater., 2007, 19, 4234 CrossRef CAS.
- J. Park, B. Koo, K. Y. Yoon, Y. Hwang, M. Kang, J. G. Park and T. Hyeon, J. Am. Chem. Soc., 2005, 127, 8433 CrossRef CAS PubMed.
- K. Senevirathne, A. W. Burns, M. E. Bussell and S. L. Brock, Adv. Funct. Mater., 2007, 17, 3933 CrossRef CAS.
- R. K. Chiang and R. T. Chiang, Inorg. Chem., 2007, 46, 369 CrossRef CAS PubMed.
- A. E. Henkes, Y. Vasquez and R. E. Schaak, J. Am. Chem. Soc., 2007, 129, 1896 CrossRef CAS PubMed.
- E. Muthuswamy, G. H. L. Savithra and S. L. Brock, ACS Nano, 2011, 5, 2402 CrossRef CAS PubMed.
- J. Wang, A. C. Johnston-Peck and J. B. Tracy, Chem. Mater., 2009, 21, 4462 CrossRef CAS.
- Y. Yin, R. M. Rioux, C. K. Erdonmez, S. Hughes, G. A. Somorjai and A. P. Alivisatos, Science, 2004, 304, 711 CrossRef CAS PubMed.
- H. J. Fan, M. Knez, R. Scholz, D. Hesse, K. Nielsch, M. Zacharias and U. Gösele, Nano Lett., 2007, 7, 993 CrossRef CAS PubMed.
- D. V. Talapin, J. S. Lee, M. V. Kovalenko and E. V. Shevchenko, Chem. Rev., 2010, 110, 389 CrossRef CAS PubMed.
- R. Xie and X. Peng, Angew. Chem., Int. Ed., 2008, 120, 7791 CrossRef.
- D. Li, L. Peng, Z. Zhang, Z. Shi, R. Xie, M.-Y. Han and W. Yang, Chem. Mater., 2014, 26, 3599 CrossRef CAS.
- D. Battaglia and X. Peng, Nano Lett., 2002, 2, 1027 CrossRef CAS.
- R. G. Xie, D. Battaglia and X. G. Peng, J. Am. Chem. Soc., 2007, 129, 15432 CrossRef CAS PubMed.
- R. García-Rodríguez and H. Liu, J. Am. Chem. Soc., 2012, 134, 1400 CrossRef PubMed.
- Y. Guo, K. Marchuk, S. Sampat, R. Abraham, N. Fang, A. V. Malko and J. Vela, J. Phys. Chem. C, 2012, 116, 2791 CAS.
- K. L. Sowers, B. Swartz and T. D. Krauss, Chem. Mater., 2013, 25, 1351 CrossRef CAS.
- C. Pu, J. Zhou, R. Lai, Y. Niu, W. Nan and X. Peng, Nano Res., 2013, 6, 652 CrossRef CAS.
- J. O. M. Bockris and E. C. Potter, J. Electrochem. Soc., 1952, 99, 169 CrossRef CAS.
- P. Liu, J. A. Rodriguez, T. Asakura, J. Gomes and K. Nakamura, J. Phys. Chem. B, 2005, 109, 4575 CrossRef CAS PubMed.
- P. Liu, J. A. Rodriguez, Y. Takahashi and K. Nakamura, J. Catal., 2009, 262, 294 CrossRef CAS.
- Q. Liu, J. Tian, W. Cui, P. Jiang, N. Cheng, A. M. Asiri and X. Sun, Angew. Chem., Int. Ed., 2014, 126, 6828 CrossRef.
- J. Xie, H. Zhang, S. Li, R. Wang, X. Sun, M. Zhou, J. Zhou, X. W. David Lou and Y. Xie, Adv. Mater., 2013, 25, 5807 CrossRef CAS PubMed.
- M. S. Faber, M. A. Lukowski, Q. Ding, N. S. Kaiser and S. Jin, J. Phys. Chem. C, 2014, 118, 21347 CAS.
Footnote |
† Electronic supplementary information (ESI) available. See DOI: 10.1039/c6ra15230a |
|
This journal is © The Royal Society of Chemistry 2016 |
Click here to see how this site uses Cookies. View our privacy policy here.