DOI:
10.1039/C6RA12208F
(Paper)
RSC Adv., 2016,
6, 74903-74912
One-step in situ synthesis of a novel α-zirconium phosphate/graphene oxide hybrid and its application in phenolic foam with enhanced mechanical strength, flame retardancy and thermal stability
Received
11th May 2016
, Accepted 2nd August 2016
First published on 3rd August 2016
Abstract
A novel α-zirconium phosphate/graphene oxide hybrid (ZGO) with α-zirconium phosphate (α-ZrP) nanoparticles immobilized on the surface of graphene oxide (GO) sheets was successfully synthesized by a one-step in situ method, and characterized by X-ray diffraction (XRD), thermogravimetric analysis (TGA), FTIR spectroscopy and transmission electronic microscopy (TEM). TGA results showed that the modification of α-ZrP nanoparticles on the GO surface significantly improved the thermal stability of the GO. Subsequently, the ZGO was incorporated into phenolic (PF) foams for reducing their high brittleness and friability. At a ZGO dosage of 4 phr (parts per hundreds of resin), the flexural and compressive strengths of the ZGO-toughened PF foams increased by 33.8% and by 39.6%, respectively, and the pulverization ratio decreased by 57.5%, compared with the pure PF foam. Besides, the results of the TGA test, limiting oxygen index (LOI) and cone calorimetric test demonstrated that the addition of ZGO imparted excellent thermal stability and flame retardancy to the PF foam, which was mainly attributed to the synergistic effects between α-ZrP nanoparticles and GO.
1. Introduction
Polymeric foams have been extensively employed as insulation materials in the field of domestic appliances, construction and chemical pipelines.1,2 Polyurethane (PU) and polystyrene (PS) foams are the most popular polymeric foams due to their excellent thermal insulation and mechanical properties.3,4 However, they tend to be flammable and release smoke and some toxic gases, resulting in their restriction in particular applications where fire retardancy is required.5
Phenolic (PF) foams have been a leading candidate as insulation materials of the construction industry because of their excellent fire resistant properties, low production of smoke and toxic gases in fires, no dripping, high thermal stability and good thermal insulation.6–8 Nevertheless, their applications have been restricted by high brittleness and high friability.9
Over the past decades, numerous efforts have been made to improve the toughness of PF foams. The commonly used toughening agents generally include two categories: organic polymers and inter-fillers. The incorporation of organic polymers, such as epoxy resin,10 polyethylene glycol (PEG)11 and polyvinyl alcohol (PVA),12 is an effective approach for improving the toughness of the foams, but deteriorates their flame retardancy because of the flammability of these polymeric toughening agents. Therefore, the development of novel toughening materials to improve the toughness of PF foams and to maintain their excellent flame resistance is of great importance. Hu's group synthesized phosphorus-containing polyurethane13 and phosphorus-containing polyethers14 as flame retardant toughening agents to improve both the toughness and flame resistance of PF foams. Another effective approach to modify the toughness and strength of PF foams is the incorporation of inter-fillers. It is reported that the introduction fibers, including glass fiber, aramid fibers and natural fibers (bamboo and cellulose fiber) could significantly increase the strength and toughness of PF foams.15–17 In addition, Hu et al. prepared glass fiber/nanoclay reinforced PF foams, and found that glass fiber and nanoclay showed good synergistic effects in enhancing the toughness, compressive strength and flame retardancy of PF foams.18 Yang et al. employed functionalized multiwalled carbon nanotubes (MWCNTs) as a reinforced agent in PF foams, and confirmed that carboxyl multi-walled carbon nanotubes could increase the compressive strength and thermal stability, and maintain the excellent flame resistance at the same time.19
Graphene has a unique two-dimensional carbon layer structure with exceptional functions, and has aroused considerable interests as a new category of nano-sized filler in polymer materials to improve their mechanical properties and thermal properties due to its high surface area, high mechanical strength and chemical stability. For example, Yan et al. reported that graphene nanosheets could worked more effectively than carbon nanotubes in improving mechanical properties and flame retardancy of the rigid polyurethane foam (RPUF).20 Zhou et al. reinforced PF foams with GO sheets, and demonstrated that their friability and mechanical properties had been improved greatly because of good compatibility and interaction between GO sheets and PF foam matrix.21 Especially in recent years, graphene exhibits better potential for the fabrication of polymer composites with flame resistance performance22,23 However, bare graphene tends to decompose during combustion because of its weak thermal-oxidative stability, leading to reduce the physical barrier effect, and thus affect its flame retardant effect. Hence, many efforts have been dedicated to increase the flame retardant efficiency of graphene by surface modification. Some organic halogen-free flame retardants, such as phosphorus-containing compounds24 and intumescent flame retardants,25 could be grafted onto the graphene by a certain reaction with the oxygen-containing functionalities. Moreover, inorganic flame retardants, like metal oxides26 and layered double hydroxides (LDHs)27 have been successfully immobilized on the surface of graphene to increase its flame retardant efficiency in polystyrene and epoxy, respectively. In addition, our group recently synthesized a silica nanospheres/graphene oxide (SiO2/GO) hybrid and studied its influence on comprehensive properties of PF foams. It had been found that the incorporation of the SiO2/GO hybrid into PF foams could greatly improve the mechanical strengths, thermal stability and flame retardancy of PF foams.28
In recent years, due to its layered structure, good mechanical property, good chemical and thermal stability,29 alpha-zirconium phosphate (α-Zr(HPO4)2·H2O, α-ZrP) has drawn increasing attention as a synergistic agent in flame retardant polymers.30–35 The flame retardant mechanisms of α-ZrP/polymer nanocomposites mainly depend on the barrier effect of the layered α-ZrP and catalyzing carbonization function. For example, Yang et al. used α-ZrP as a synergistic agent in intumescent flame retarded polypropylene or low-density polyethylene and ethylene-vinyl acetate/aluminum hydroxide hybrids.31,36 Yang et al. also introduced α-ZrP into acrylonitrile-butadiene-styrene copolymer (ABS) to improve its thermal stability through catalyzing carbonization of the polymer itself during pyrolysis.37
In this work, in order to improve the thermal-oxidative stability of GO sheets, a novel α-ZrP/graphene oxide hybrid (ZGO) was first synthesized by a one-step in situ method, and then the ZGO was incorporated into PF foam to study its effect on comprehensive properties of the foams, including mechanical strengths, pulverization ratio, flame retardancy and thermal stability.
2. Experimental
2.1. Materials
Natural graphite powder (99.95% metals basis, 750–850 mesh), were supplied by Aladdin Industrial Co. Ltd (China). Zirconium oxychloride octahydrate (ZrOCl2·8H2O, 98%) was obtained from Sigma-Aldrich company. Phosphoric acid (H3PO4, 85%), hydrochloric acid, H2SO4 (98%), NaNO3, KMnO4, hydrogen peroxide (30%), Tween 80, p-toluenesulfonic acid, and n-pentane were all commercial products with analytical grades purchased from Sinopharm Chemical Reagent Co. (Shanghai, China), and used without further purification. Resol type PF resin was supplied by Shandong Shengquan Chemical Co., Ltd. (Shandong, China).
2.2. Preparation of graphene oxide (GO)
Graphene oxide (GO) was prepared and purified by Hummers method.38 Typically, graphite (2.0 g), NaNO3 (2.0 g) and 98 wt% H2SO4 (80 ml) were mixed and stirred for 2 h in an ice bath. Subsequently, KMnO4 (10 g) was slowly added in the mixture and reacted at 35 °C for 2 h. Then 5% dilute sulfuric acid (200 ml) was slowly added, and the mixture was stirred at 60 °C for 2 h. The temperature was raised to 95 °C, and 30% hydrogen peroxide (20 ml) and distilled water (1000 ml) were added slowly. The mixture was stirred for another 1 h at 95 °C. Finally, a brown solid was collected by centrifugal and washed with 5% hydrochloric acid solution until the manganese and sulfate ions were completely removed. The brown solid was dried at 60 °C for 24 h in a vacuum oven before being used.
2.3. Preparation of α-ZrP and α-ZrP/GO hybrid (ZGO)
2.3.1. Preparation of α-ZrP39. A sample of 1.0 g ZrOCl2·8H2O was first dissolved in 6 ml deionized water, and then 12 ml 85 wt% H3PO4 was slowly added in the above mixture under rapid stirring. After that the precursor was refluxed at 100 °C for 24 h. The products were washed and collected by centrifugation a few times. Finally, the α-ZrP was dried at 65 °C for 24 h, and ground with a mortar into fine powders.
2.3.2. Preparation of α-ZrP/GO hybrid. ZrOCl2·8H2O (1.0 g) was first dissolved in 6 ml deionized water, and then 12 ml 85 wt% H3PO4 was slowly added in the above mixture under rapid stirring. Next the precursor was mixed with 90 ml GO suspension (3 mg ml−1), and the obtained system was refluxed at 100 °C for 24 h. After the reaction, the products were washed and collected by centrifugation a few times. At last, the α-ZrP/GO hybrid was dried at 65 °C for 24 h, and the dried α-ZrP/GO was ground with a mortar into fine powders.
2.4. Preparation of pure PF and the toughened PF foams
Phenolic resin (100 phr), GO, α-ZrP and ZGO were mixed in a certain ratio, and then blowing agent (n-pentane, 8 phr), surfactant (Tween 80, 5 phr) and curing agent (12 phr, p-toluenesulfonic acid/phosphorous acid/distilled water = 2
:
1
:
2 by weight), were mixed at room temperature under rapid stirring. After that the mixture was poured into a mold, cured at 80 °C for 60 min, and the toughened PF foams were obtained. The detailed formulations are given in Table 1. To keep the density of the foams identical (16 ± 0.5 kg m−3), the same amount of the mixture was put into the mould. The foams were carefully cut for various properties testing.
Table 1 Formulations of pure PF foam and the toughened PF foamsa
Sample code |
Phenolic resin (phr) |
GO (phr) |
α-ZrP (phr) |
ZGO (phr) |
Curing agent (12 phr), blowing agent (8 phr), Tween 80 (5 phr). |
Pure PF |
100 |
— |
— |
— |
1ZGO/PF |
100 |
— |
— |
1 |
2ZGO/PF |
100 |
— |
— |
2 |
3ZGO/PF |
100 |
— |
— |
3 |
4ZGO/PF |
100 |
— |
— |
4 |
5ZGO/PF |
100 |
— |
— |
5 |
4GO/PF |
100 |
4 |
— |
— |
4ZrP/PF |
100 |
— |
4 |
— |
2ZrP/2GO/PF |
100 |
2 |
2 |
— |
2.5. Characterization and measurements
Surface morphologies were observed through field emission scan electronic microscopy (FESEM, Hitachi S-4800) and transmission electronic microscopy (TEM, JEOL JEM2011). Solid samples were directly stuck on the conductive tapes for FESEM observation. As for the preparation of TEM samples, a small amount of powder samples were dispersed into ethanol, and the obtained dilute solution was dropped on the copper mesh for TEM observation.
X-ray diffractions (XRD) were performed on a Rigaku D/maxr B diffractometer with Cu Kα radiation. The sample powder was directly pressed into discs and used in the XRD analysis, and the step size was 0.02° and step time is 0.6 s.
Fourier transform infrared (FTIR) spectra were recorded with an EQUINOXSS/HYPERION 2000 spectrometer (Bruker Co., Ltd., Germany). The microstructure of foams was observed by using a XPL-30 TF transflective polarizing microscope (Shanghai Weitu Instrument Co., Shanghai, China) on transmission types.
The flexural strength of the foams was measured by a CMT5105 universal testing machine, according to GB/T 20974-2014 (specified GB/T8812.1-2007). Each specimen used for the test was 120 × 25 × 20 mm3. The compressive strength of the foams was measured by a DXLL-5000 universal testing machine according to GB/T 20974-2014 (specified GB/T8813-2008). Each specimen used for the test was 50 × 50 × 50 mm3. In both measurements, at least five samples were tested to obtain average values. The density was determined according to the dimensions and the weight of the foam.
Thermogravimetric analysis (TGA) tests were carried out by using a STD Q600 (simultaneous differential scanning calorimetry – TGA) thermo-analyzer instrument (TA Co., New Castle, DE, USA) at a heating rate of 10 °C min−1 under nitrogen flow. The weight of all samples was kept within 5 mg in an Al2O3 pan, and samples were heated from room temperature to 800 °C.
The limiting oxygen index (LOI) was measured by an HC-2 oxygen index meter, according to GB/T2406-2009. Each specimen used for the test was 100 × 10 × 10 mm3. The UL 94 vertical test was carried out on a CFZ-3-type horizontal and vertical burning tester according to GB/T2408-2008. Each specimen used for the test was 130 × 13 × 3 mm3. Cone calorimetric tests (CCT) were carried out on a FTT cone calorimeter (dual) according to the standards of ISO 5660. Each specimen used for the test was 100 × 100 × 20 mm3. The heat flux for testing was 35 kW m−2. And the residue char remaining after CCT was observed by a Hitachi S-4800 Scanning Electronic Microscope (SEM).
Pulverization ratio was measured by the weight loss of foams after friction. Each specimen used for testing was 20 × 20 × 20 mm3. Those samples were first loaded with a 20 g weight and then pushed back and forth with a constant force 30 times on fixed sandpaper. Each single-pass friction distance was 250 mm. Pulverization ratios were calculated according to eqn (1):
|
Pulverization ratio = (M1 − M2)/M1 × 100%
| (1) |
where
M1 is the weight before friction and
M2 is the weight after friction.
3. Results and discussion
3.1. Characterization of GO, α-ZrP and ZGO
Fig. 1 presents the XRD patterns of GO, α-ZrP and ZGO. Compared with the peak of natural graphite at 2θ = 24.4°, the XRD pattern of GO exhibits a sharp peak at 2θ = 12.1° corresponding to a d-spacing (d002) of 0.73 nm, indicating the insertion of hydroxyl, carboxyl and epoxy groups into the graphite sheets after the oxidation process of natural graphite.40 The XRD pattern of α-ZrP exhibits the typical profile of α-Zr(HPO4)2·H2O and a typical diffraction peak at 11.7° corresponds to a basal spacing (d002) of 0.76 nm.41 As for a ZGO hybrid, it displays similar characteristic bands from α-ZrP, and the diffraction peak of GO at 2θ = 12.1° is partly overlapped with typical diffraction peak at 11.7° of α-ZrP. These results suggest the successful immobilization of α-ZrP on the surface of GO sheets during the immobilization process.
 |
| Fig. 1 XRD patterns of GO, α-ZrP and ZGO. | |
Fig. 2 shows FTIR spectra of GO, α-ZrP and ZGO. For the FTIR spectrum of GO, a broad and intensive peak appearing at 3430 cm−1 is assigned to –OH stretching band, which may originate from water molecules adsorbed inside GO. Besides, peaks at 1726, 1622, 1385 and 1052 cm−1 correspond to C
O, C
C, C–OH and C–O–C vibration frequencies, respectively. These peaks suggest that graphite has been already oxidized to GO.40 In the case of α-ZrP, the bands at 3592 and 3510 cm−l are attributed to asymmetric –OH stretching vibrations of the lattice water, a peak at 3145 cm−1 to the symmetric stretching vibration of the lattice water, and a peak at 3345 cm−l to the P–OH stretching mode. The bands at 1250 and 595 cm−1 are caused by in-plane and out-of-plane P–OH deformation modes, and the strong broad bands near 1032 and 966 cm−1 are probably due to the stretching modes of PO4.42 These characteristic peaks are in good agreement with the chemical composition of α-ZrP. In the FTIR spectrum of ZGO, all characteristic peaks from GO and α-ZrP appear, and the peaks around 3430 and 1622 cm−1 are overlapped. These results confirm that α-ZrP has been composited with GO.
 |
| Fig. 2 FTIR spectra of GO, α-ZrP and ZGO. | |
The influence of α-ZrP on the thermal stability of GO was investigated by thermogravimetric analysis (TGA). Fig. 3 and 4 present the TGA and DTG curves of GO, α-ZrP and ZGO. It can be seen from the TGA curves that GO has three stages of weight loss. The weight loss of the first stage (13.7 wt%) below 150 °C is mainly caused by evaporation of absorbed and interlayer water of GO sheets. The second stage with a weight loss of 28.2 wt% locating between 150 °C and 300 °C is attributed to evaporation of hydration water and removal of labile functional groups. The weight loss of the third stage (16.3 wt%) is primarily contributed by the removal of more stable oxygen functionalities.43 As for α-ZrP, the weight loss (5.65 wt%) below 200 °C is mainly caused by evaporation of the lattice water, and the weight loss above 200 °C is due to the gradually dehydroxylation of –OH of α-ZrP. The decomposition of ZGO clearly occur in two regions below 800 °C: (1) evaporation of absorbed water and lattice water, and thermal decomposition of labile functional groups are all between 50 and 210 °C; (2) dehydroxylation of the α-ZrP and GO lattice was between 500 and 800 °C. In comparison with the GO, after immobilization of α-ZrP on the surface of GO, the residue percentage of the ZGO hybrid is much higher than GO, suggesting that the combination of α-ZrP with GO significantly improves the thermal resistance. Beside, it can be seen from DTG curves that the maximum mass loss rate of the ZGO hybrid is much lower than that of GO, indicating that the α-ZrP covered on the surface of GO can function as an effective barrier to impede the thermal decomposition of GO at high temperatures.41
 |
| Fig. 3 TGA curves of GO, α-ZrP and ZGO. | |
 |
| Fig. 4 DTG curves of GO, α-ZrP and ZGO. | |
The structure and morphology of GO, α-ZrP and ZGO were also investigated by transmission electron microscopy (TEM). As shown in Fig. 5a, it can be clearly seen that the GO structure exhibits the sheet-like structure with some drapes. Fig. 5b shows that the length dimension of the α-ZrP nanoplatelet is around 110 nm, and it also has a narrow size distribution prepared via the refluxing method. After the reaction with GO sheets, TEM observation of the ZGO (Fig. 5c) exhibits a sheet-like morphology composed of multilayered nanostructures, which indicates that the α-ZrP nanoparticles are successfully immobilized on the surface of GO sheets and possess a uniform particle size of around 12.0 nm.
 |
| Fig. 5 TEM images of (a) GO, (b) α-ZrP, and (c) ZGO. | |
3.2. Microstructures of the toughened PF foams
To study the effect of GO, α-ZrP and ZGO on the microstructures of PF foams, the PF foams modified with them were observed by optical microscope. As shown in Fig. 6, it can be seen that all the PF foams consist of a majority of closed cells. Compared with pure PF foam, the size of cells for ZGO-toughened PF foams is gradually reduced with the increase of dosage of ZGO. When the dosage of ZGO is increased to 4 phr, the shape of cells is relatively round and the average size of the cells is smallest, as shown in Fig. 6a–f. Such tendency can be explained by the reason that the ZGO acts as heterogeneous nucleating agent during cell formation resulting in generating more cells and increasing cell density relatively, and thus cell size of its toughened PF foams is smaller than that of pure PF foam.44 However, the distribution of cell size of sample 5.0ZGO/PF is not very uniform, and the reason is probably due to easy agglomeration of ZGO at a higher loading (5 phr). Besides, the cell size of sample 4.0 ZGO/PF is obviously smaller than the one of samples 4ZrP/PF (Fig. 6g), 4GO/PF (Fig. 6h) and 2ZrP/2GO/PF (Fig. 6i), and the distribution of cells of sample 4.0 ZGO/PF is more uniform than that of other three samples. These results are probably attributed to the differences of surface character of these nanofillers and their dispersion in the PF resin during the forming process. Compared with GO, the surface of ZGO due to the immobilization of α-ZrP becomes less hydrophilic, which is beneficial to the effectiveness of the nucleation of ZGO in the PF foams.45 In comparison, the addition of the only α-ZrP or the mixture of GO and α-ZrP is adverse to the forming of uniform cell structure because of easy agglomeration of α-ZrP in the PF matrix.46 Therefore, the cell structure and cell uniformity of sample 4.0ZGO/PF is better than those of samples 4ZrP/PF, 4GO/PF and 2ZrP/2GO/PF.
 |
| Fig. 6 Optical images of (a) Pure PF foam and PF foams toughened by (b) 1ZGO/PF, (c) 2ZGO/PF, (d) 3ZGO/PF, (e) 4ZGO/PF, (f) 5ZGO/PF, (g) 4ZrP/PF, (h) 4GO/PF, (i) 2ZrP/2GO/PF. The magnification of all images was 40×. | |
3.3. Properties of pure PF and the toughened PF foams
3.3.1. Mechanical properties. Fig. 7 shows flexural and compressive strengths of the toughened PF foams by GO, α-ZrP and ZGO. Compared with the pure PF foam, the flexural and compressive strengths of the toughened foams are obviously improved (Fig. 7). The flexural and compressive strengths of sample 4ZGO/PF are apparently higher than those of samples 4ZrP/PF, 4GO/PF and 2ZrP/2GO/PF at the same loading. These results can be explained from three aspects. First of all, the sheet-like ZGO is inserted into the cell walls of the foams to reinforce the PF foams and constrain the segmental movement of the polymer chains of the PF resins because of its ultrahigh aspect ratio of layer structure.18,20 Secondly, the good interaction and dispersion between ZGO and PF resin matrix can further provide additional constraints to the movement of polymer chains, which results from the formation of ester bonds between residual carbonyl (–COOH) groups on ZGO and hydroxyl (–OH) groups on the PF resins and favour the improvement of mechanical properties.21 Thirdly, the immobilization of inorganic α-ZrP on the surface of GO sheets benefits heterogeneous nucleation of the nanofiller ZGO in PF foams, leading to generating more cells and increasing the cell density to undergo external force.45 On the contrary, the poor dispersion of α-ZrP in the PF resin matrix affects the forming of uniform small cells, thus impairing part of mechanical strengths of sample 4ZrP/PF and 2ZrP/2GO/PF. And the thin cell wall and large cell size of the GO-toughed PF foam also damage its mechanical properties compared with the ZGO-toughed PF foam. Therefore, the ZGO-toughened PF foam shows higher mechanical strengths than those of the ZrP, GO, or the mixture of ZrP and GO toughened PF foams.
 |
| Fig. 7 Flexural and compressive strengths of pure PF foam and the toughened PF foams. | |
As shown in Fig. 8, the flexural and compressive strengths of the ZGO-toughened PF foams increase first with an increase in the loading of ZGO, reach a maximum at 4 phr loading, and decrease slightly after that loading. Generally, the mechanical strengths of the polymeric foams depend on the foam structure, such as the size of cells, the uniformity of cells, the toughness of cell wall.13,18 Compared with pure PF foam, the sample 4ZGO/PF containing 4phr ZGO has the highest flexural and compressive strengths, which increase significantly by 33.8% and 39.6%, respectively. The significant improvement may be attributed to uniform cell morphology, smaller cell size and sheet-like ZGO-toughened thick cell wall, which can resist high external force. However, the strengths no longer increase when the ZGO loading increases to 5 phr, which may be caused by the agglomeration of ZGO particles in the PF resin. These results indicate that there is an optimum loading of ZGO to improve the flexural and compressive strengths of the PF foam.
 |
| Fig. 8 Effect of ZrP/GO content on flexural and compressive strengths of PF foams. | |
3.3.2. Pulverization ratios. The high friability is always a serious drawback of PF foams. Therefore, it is significant to overcome the problem of PF foams in order to expand their application fields. As shown in Fig. 9, it is clear that the pulverization ratios of the toughened PF foams with various nanofillers are all reduced compared with the pure PF foam. Particularly, the pulverization ratio of sample 4ZGO/PF decreases by 57.5%, while the value of samples 4ZrP/PF, 4GO/PF and 2ZrP/2GO/PF decreases by 16.7%, 46,6% and 25.0%, respectively. Moreover, the pulverization ratio of the ZGO toughened PF foams first decreases gradually with the increasing dosage of ZGO, reach the minimum at 4 phr loading, and after the loading increases slightly. The reason for the decrease in the pulverization ratio of the ZGO toughened PF foams may be due to ultrahigh aspect ratio of sheet-like ZGO, good interaction of ZGO with PF resin and high cell density. The slight increase in the pulverization ratio for sample 5ZGO/PF may be caused by non-uniform morphology of cell size resulting from the agglomeration problem of ZGO at a higher dosage.
 |
| Fig. 9 Pulverization ratios of pure PF foam and the toughened PF foams. | |
3.3.3. Flame retardant properties.
LOI and UL 94 rating. The fire-resistant behavior of pure PF and the toughened PF foams was evaluated by limiting oxygen index (LOI) and UL 94 vertical burning tests, and the test results are listed in Table 2. The LOI value of pure PF foam is 38%. The values of the ZGO toughened PF foams increase gradually with the addition of the ZGO content. Moreover, the LOI of the ZGO toughened PF foam is higher than that of GO, α-ZrP or their mixture toughened PF foams at the same loading, indicating some synergistic effect in flame retardancy between GO and α-ZrP nanoparticles. The LOI enhancement is probably because the α-ZrP nanoparticle covered on the surface of GO sheets can strengthen the physical barrier effect of the sheets and impede the decomposition of GO sheets.36 From the Table 2, it is also clear that all samples can pass the V0 rating, indicating the toughened PF foams still remain excellent flame retardancy.
Table 2 LOI and UL 94 rating of pure PF foam and the toughened PF foams
Sample code |
LOI (%) |
UL-94 rating |
Pure PF |
38.0 |
V0 |
1ZGO/PF |
39.0 |
V0 |
2ZGO/PF |
39.5 |
V0 |
3ZGO/PF |
41.5 |
V0 |
4ZGO/PF |
42.0 |
V0 |
5ZGO/PF |
42.5 |
V0 |
4GO/PF |
40.0 |
V0 |
4ZrP/PF |
41.5 |
V0 |
2ZrP/2GO/PF |
40.5 |
V0 |
Cone calorimetry. Fig. 10 shows the heat-release rate (HRR) curves of pure PF and the toughened PF foams from the cone calorimetric test, and the typical data are summarized in Table 3. The peak heat-release rate (PHRR) of pure PF foam is 36 kW m−2, while the PHRR value of the toughened PF foams containing 1phr and 4 phr ZGO decreases by 3.6% and by about 26%, respectively. The total heat release (THR) of the toughened PF foams with 4 phr ZGO is reduced, and the time to ignition (TTI) is increased slightly compared to the ones of pure PF foam. Moreover, the PHRR and THR values of sample 4ZGO/PF are all lower than those of samples 4ZrP/PF, 4GO/PF and 2ZrP/2GO/PF, respectively, which indicates some synergetic flame retardant effect between the GO and α-ZrP.
 |
| Fig. 10 Heat-release rate curves of pure PF foam and the toughened PF foams (35 kW m−2). | |
Table 3 Cone calorimetric data of pure PF foam and the toughened PF foams (35 kW m−2)
Sample code |
TTIa (s) |
PHRRb (kW m−2) |
THRc (MJ m−2) |
Time to ignition. Peak heat release rate. Total heat release. |
Pure PF |
4 |
36 |
6.1 |
1ZGO/PF |
4 |
35 |
7.0 |
4ZGO/PF |
6 |
27 |
4.4 |
4GO/PF |
2 |
28 |
6.0 |
4ZrP/PF |
6 |
31 |
7.1 |
2ZrP/2GO/PF |
6 |
29 |
5.5 |
In order to further elucidate the flame retardant mechanism of the toughened PF foams, the morphology and structure of residues of the toughened foams after combustion were investigated by SEM. As shown in Fig. 11, the charred layer of sample 4ZGO/PF (Fig. 11c) is more uniform and denser than that of samples 4GO/PF, 4ZrP/PF and 2ZrP/2GO/PF (Fig. 11d–f), respectively, and the cell sizes of sample 4ZGO/PF are obviously smaller compared to the ones of other three samples, which leads to better flame retardant performance of sample 4GO/PF. These results can be explained from two aspects. On one hand, the higher cell density and smaller cell size caused by the appropriate amount of ZGO benefit to forming denser charred layer with smaller cell size during combustion. On the other hand, α-ZrP nanoparticles covered on the surface of GO sheets are helpful to protect GO sheets from the thermal decomposition at high temperatures, leading to the formation of more compact char.36
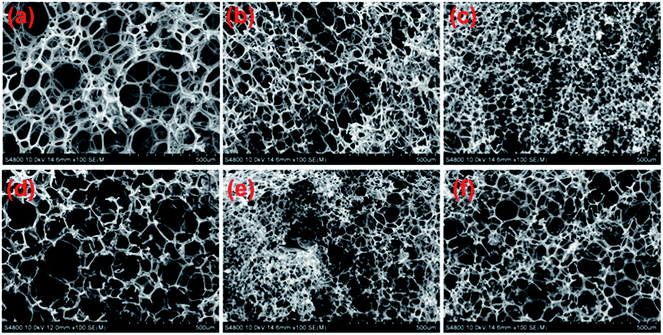 |
| Fig. 11 SEM images of the residue char after CCT: (a) pure PF, (b) 1ZGO/PF, (c) 4ZGO/PF, (d) 4GO/PF, (e) 4ZrP/PF and (f) 2ZrP/2GO/PF. | |
3.4. Thermal decomposition of pure PF and the toughened PF foams
TGA and derivative thermogravimetric (DTG) measurements were carried out to obtain information on the thermal stability of pure PF and the toughened PF foams. As shown in Fig. 12 and 13, the specific degradation temperatures and final char yields at 750 °C are summarized in Table 4. It is clearly seen from the DTG curves (Fig. 13) that the process of thermal decomposition can be grouped into four different stages for pure PF foam. The first degradation stage occurs below 100 °C, which may be on account of the volatilization of residual moisture and blowing agents in the foam. The second stage from 160 °C to 240 °C may be due to the dehydration of further curing of PF foams.47 The third stage takes place in the temperature range 240–400 °C, and the weight loss may be caused by the degradation of surfactants (i.e. Tween 80). The fourth stage happens from 400 to 800 °C, and this is attributed to the process of thermal degradation of PF resin chain scission with a Tmax (the peak temperature in the DTG curve) of 468 °C. All modified PF foams present the similar degradation behavior to that of pure PF foam, but the main difference is the degradation temperature. Compared with pure PF foam, the modified phenolic foams have a higher temperature at 5% weight loss (T−5%) and the temperature at the maximum decomposition rate of DTG peaks (Tmax) is also slightly shifted to a higher temperature. Moreover, the residue at 750 °C of sample 4.0ZGO/PF (49.4%) is higher than that of samples 4ZrP/PF, 4GO/PF and 2ZrP/2GO/PF at the same loading (the value is 46.6%, 47.5% and 45.4%, respectively).
 |
| Fig. 12 TGA curves of pure PF foam and the toughened PF foams. | |
 |
| Fig. 13 DTG curves of pure PF foam and the toughened PF foams. | |
Table 4 TGA and DTG data of pure PF foam and the toughened PF foams
Sample code |
T−5% (°C) |
Tmax (°C) |
Residue at 750 °C (%) |
Pure PF |
163 |
468 |
45.1 |
1ZGO/PF |
193 |
469 |
48.8 |
4ZGO/PF |
204 |
476 |
49.4 |
4GO/PF |
191 |
471 |
46.6 |
4ZrP/PF |
172 |
468 |
47.5 |
2ZrP/2GO/PF |
189 |
474 |
45.4 |
4. Conclusions
In this work, a novel α-ZrP/graphene oxide (ZGO) hybrid was successfully synthesized by a one-step in situ method, and was characterized by XRD, TEM, FTIR and TGA. A morphological study indicates the α-ZrP nanoparticles are covered on the surface of GO sheets, and the TGA results show that the modification of α-ZrP nanoparticles on GO surface significantly improved the thermal stability of the GO. The approach used in this work can provide a promising solution to develop a novel and efficient graphene-based nanofillers for improving mechanical properties, thermal properties and flame retardancy of many polymers.
The incorporation of a suitable amount of ZGO into the phenolic (PF) foam leads to not only an increase in flexural and compressive strengths and a decrease in friability, but also an increase in flame retardancy of the toughened PF foams (an increase in LOI and a reduction in the peak heat release rate). Moreover, the thermal stability of the toughened PF foam is improved. The modified PF foams have potential applications in many fields as thermal insulating materials, e.g. in building industry, transportation, cryogenics and so on.
Acknowledgements
This work was financially supported by the National Natural Science Foundation of China (No. U1205114).
Notes and references
- X. Cao, L. J. Lee, T. Widya and C. Macosko, Polymer, 2005, 46, 775–783 CrossRef CAS.
- M. C. Silva, J. A. Takahashi, D. Chaussy, M. N. Belgacem and G. G. Silva, J. Appl. Polym. Sci., 2010, 117, 3665 CAS.
- L. Shi, Z. M. Li, B. H. Xie, J. H. Wang, C. R. Tian and M. B. Yang, Polym. Int., 2006, 55, 862 CrossRef CAS.
- H. Zhang, Y. Y. Kuo, A. C. Gerecke and J. Wang, Environ. Sci. Technol., 2012, 46, 10990 CrossRef CAS PubMed.
- J. Lefebvre, B. Bastin, M. Le Bras, S. Duquesne, R. Paleja and R. Delobel, Polym. Degrad. Stab., 2005, 88, 28 CrossRef CAS.
- S. Lei, Q. Guo, J. Shi and L. Liu, Carbon, 2010, 48, 2644 CrossRef CAS.
- H. Shen, A. J. Lavoie and S. R. Nutt, Composites, Part A, 2003, 34, 941 CrossRef.
- C. J. Tseng and K. T. Kuo, J. Chin. Inst. Eng., 2002, 25, 753 CrossRef CAS.
- L. Pilato, React. Funct. Polym., 2013, 73, 270 CrossRef CAS.
- M. L. Auad, L. Zhao, H. Shen, S. R. Nutt and U. Sorathia, J. Appl. Polym. Sci., 2007, 104, 1399 CrossRef CAS.
- M. Gao, Y. L. Yang and Z. Q. Xu, Adv. Mater. Res., 2013, 21 CrossRef.
- T. Horikawa, K. Ogawa, K. Mizuno, J. i. Hayashi and K. Muroyama, Carbon, 2003, 41, 465 CrossRef CAS.
- H. Yuan, W. Xing, H. Yang, L. Song, Y. Hu and G. H. Yeoh, Polym. Int., 2013, 62, 273 CrossRef CAS.
- H. Yang, X. Wang, H. Yuan, L. Song, Y. Hu and R. K. K. Yuen, J. Polym. Res., 2012, 19, 1 CrossRef.
- J. P. Basbagill, Fiber reinforced phenolic foam: Climatic effects on mechanical properties and building applications in northern Thailand, ProQuest, 2008 Search PubMed.
- A. Desai, M. L. Auad, H. Shen and S. R. Nutt, J. Cell. Plast., 2008, 44, 15 CAS.
- H. Shen and S. Nutt, Composites, Part A, 2003, 34, 899 CrossRef.
- X. Hu, W. Cheng, W. Nie and D. Wang, Polym. Compos., 2016, 37, 2323 CrossRef CAS.
- Z. Yang, L. Yuan, Y. Gu, M. Li, Z. Sun and Z. Zhang, J. Appl. Polym. Sci., 2013, 130, 1479 CrossRef CAS.
- D. Yan, L. Xu, C. Chen, J. Tang, X. Ji and Z. Li, Polym. Int., 2012, 61, 1107 CrossRef CAS.
- J. Zhou, Z. Yao, Y. Chen, D. Wei and T. Xu, Polym. Compos., 2014, 35, 581 CrossRef CAS.
- N. Hong, J. Zhan, X. Wang, A. A. Stec, T. R. Hull, H. Ge, W. Xing, L. Song and Y. Hu, Composites, Part A, 2014, 64, 203 CrossRef CAS.
- S. Liu, H. Yan, Z. Fang and H. Wang, Compos. Sci. Technol., 2014, 90, 40 CrossRef CAS.
- C. Bao, Y. Guo, B. Yuan, Y. Hu and L. Song, J. Mater. Chem., 2012, 22, 23057 RSC.
- G. Huang, S. Chen, S. Tang and J. Gao, Mater. Chem. Phys., 2012, 135, 938 CrossRef CAS.
- C. Bao, L. Song, C. A. Wilkie, B. Yuan, Y. Guo, Y. Hu and X. Gong, J. Mater. Chem., 2012, 22, 16399 RSC.
- X. Wang, S. Zhou, W. Xing, B. Yu, X. Feng, L. Song and Y. Hu, J. Mater. Chem. A, 2013, 1, 4383 CAS.
- X. Li, Z. Wang and L. Wu, RSC Adv., 2015, 5, 99907 RSC.
- A. Clearfield and G. D. Smith, Inorg. Chem., 1969, 8, 431 CrossRef CAS.
- D. Y. Wang, X. Q. Liu, J. S. Wang, Y. Z. Wang, A. A. Stec and T. R. Hull, Polym. Degrad. Stab., 2009, 94, 544 CrossRef CAS.
- D. Yang, Y. Hu, L. Song, S. Nie, S. He and Y. Cai, Polym. Degrad. Stab., 2008, 93, 2014 CrossRef CAS.
- X. Q. Liu, D. Y. Wang, X. L. Wang, L. Chen and Y. Z. Wang, Polym. Degrad. Stab., 2011, 96, 771 CrossRef CAS.
- H. Lu, C. A. Wilkie, M. Ding and L. Song, Polym. Degrad. Stab., 2011, 96, 885 CrossRef CAS.
- H. Lu and C. A. Wilkie, Polym. Adv. Technol., 2011, 22, 1123 CrossRef CAS.
- Y. Zhang, X. Zeng, H. Li, X. Lai, Y. Guo and R. Zheng, Mater. Lett., 2016, 174, 230 CrossRef CAS.
- D. Yang, Y. Hu, H. Li, L. Song, H. Xu and B. Li, J. Therm. Anal. Calorim., 2015, 119, 619 CrossRef CAS.
- D. D. Yang, Y. Hu, H. P. Xu and L. P. Zhu, J. Appl. Polym. Sci., 2013, 130, 3038 CrossRef CAS.
- W. S. Hummers Jr and R. E. Offeman, J. Am. Chem. Soc., 1958, 80, 1339 CrossRef.
- L. Sun, W. J. Boo, H. J. Sue and A. Clearfield, New J. Chem., 2007, 31, 39 RSC.
- H. K. Jeong, Y. P. Lee, R. J. W. E. Lahaye, M. H. Park, K. H. An, I. J. Kim, C. W. Yang, C. Y. Park, R. S. Ruoff and Y. H. Lee, J. Am. Chem. Soc., 2008, 130, 1362 CrossRef CAS PubMed.
- Z. Wu, L. Zhang, Q. Guan, P. Ning and D. Ye, Chem. Eng. J., 2014, 258, 77 CrossRef CAS.
- D. J. MacLachlan and K. R. Morgan, J. Phys. Chem., 1992, 96, 3458 CrossRef CAS.
- D. C. Marcano, D. V. Kosynkin, J. M. Berlin, A. Sinitskii, Z. Sun, A. Slesarev, L. B. Alemany, W. Lu and J. M. Tour, ACS Nano, 2010, 4, 4806 CrossRef CAS PubMed.
- C. Yang, Z. H. Zhuang and Z. G. Yang, J. Appl. Polym. Sci., 2014, 131, 39734 Search PubMed.
- M. M. Bernal, S. Pardo-Alonso, E. Solórzano, M. Á. Lopez-Manchado, R. Verdejo and M. Á. Rodriguez-Perez, RSC Adv., 2014, 4, 20761 RSC.
- S. A. Song, Y. S. Chung and S. S. Kim, Compos. Sci. Technol., 2014, 103, 85 CrossRef CAS.
- H. Yang, X. Wang, B. Yu, H. Yuan, L. Song, Y. Hu, R. K. K. Yuen and G. H. Yeoh, J. Appl. Polym. Sci., 2013, 128, 2720 CrossRef CAS.
|
This journal is © The Royal Society of Chemistry 2016 |
Click here to see how this site uses Cookies. View our privacy policy here.