DOI:
10.1039/C6RA17670D
(Paper)
RSC Adv., 2016,
6, 74886-74894
Iron and nitrogen co-functionalized porous 3D graphene frameworks as an efficient oxygen reduction catalyst†
Received
11th July 2016
, Accepted 26th July 2016
First published on 29th July 2016
Abstract
Porous 3D graphene decorated by Fe species and N-doping (Fe/N-GAs) has been prepared by a cost-effective strategy. Benefiting from the characteristics of coordinating with metals and possessing a high nitrogen content, poly-2,6-diaminopyridine (PDAP) is preferably selected as nitrogen doping source. It is found that the active site species and defects on Fe/N-GAs samples are influenced by both pyrolyzing temperature and content of Fe, moreover, the Fe content can affect the morphology and structure of Fe/N-GAs, so the electrocatalytic activity towards the ORR on Fe/N-GAs can be tuned. The Fe/N-GAs with highly effective activity sites, connected pores and high surface area exhibit comparable activity (Eonset = −0.04 V vs. SCE, E1/2 = −0.21 V vs. SCE, JL = 6.65 mA cm−2) to commercial Pt/C, better stability and better tolerance to methanol than Pt/C in alkaline medium as well as improved activity compared to N-GAs in acidic medium.
1. Introduction
With the growing global energy crisis, there is considerable research on energy storage and conversion systems, such as metal–batteries and fuel cells.1 The oxygen reduction reaction (ORR) is crucial for commercial fuel cells and metal–air batteries applications. However, one of the technical challenges for the development of these technologies is the sluggish kinetics of the ORR. To date, the state-of-the-art catalyst for the ORR is Pt-based catalyst. Nevertheless, the Pt-based catalyst still suffers from several serious problems including high cost as well as instability, which have hindered its practical and large-scale application.2,3 Accordingly, extensive efforts have been devoted to exploring desirable non-precious metal or metal-free catalyst with better ORR performance to replace Pt-based catalyst. In general, the ORR performance is associated with the species and the density of catalytic active sites, specific surface area, conductivity and mass transport in catalyst layer. Among them, the two crucial factors are: (1) the species of active sites, which are determined by chemical structure; (2) the surface area and the appropriate pores structure for mass transport of ORR-relevant species. However, some achievements has been gained, how to controllably synthesize non-precious catalyst with appropriate porous structure and more effective catalytic active sites still remains a challenge.
To substitute for Pt-based catalysts, much progress has moved to synthesize non-noble metal catalysts to promote ORR, such as heteroatom doped carbon materials,4–7 metal–N4 compounds,8,9 metal chalcogenide,10,11 metal oxide,12,13 metal–nitrogen–carbon compound.14–20 In recent years, a new type of iron carbide supported on doped carbon has been prepared by various strategies applied as a extraordinarily efficient catalyst, not only exhibiting highly active than Pt/C in alkaline solution but also showing comparable ORR performance with Pt/C in acidic solution.21–25 The superior ORR performance is because that Fe3C nanoparticle is not the direct active sites, but it can activate graphitic carbon shells which are active sites.21
Recently, three-dimensional (3D) graphene materials (3DGMs) have attracted much attention, owing to they not only displaying continuously interconnected porous structures and high specific surface area, which facilitate mass transfer for reacting species and more active sites exposure, but also providing high electrical conductivity for fast charge transport. The catalytic performance on carbon-based catalyst highly relates to surface chemical structure. Hence, to modify the graphene sheets on 3DGMs is essential to improve catalytic activity for ORR. Heteroatom doping is well considered as one of effective strategy to functionalize graphene. Therefore, heteroatom-doped 3DGMs have been extensively observed as an efficient ORR catalyst.26–28
From the above-mentioned viewpoint, it has been well recognized that the specific surface area and chemical structure of the catalyst largely determine electrocatalytic performance. Within this context, it is of extreme significance to improve the density of effective active sites and increase the specific surface area to make more effective active sites accessible. To integrate the advantages of Fe, N-based carbon materials and 3DGMs, thus, we have prepared Fe and nitrogen co-functionalized 3DGMs by a cost-effective method. Here, poly-2,6-diaminopyridine (PDAP) which both possesses rich nitrogen and can coordinate with Fe is preferentially chose as doped source. The Fe, N-functionalized catalyst displays superiorly active towards ORR in comparison with only N-functionalized catalyst in both alkaline and acid media.
2. Experimental section
2.1 Materials
2,6-Diaminopyridine (DAP) was purchased from Aladdin. Natural flake graphite was gained from Sinopharm Chemical Reagent Co., Ltd. Ammonium persulfate (APS) was bought from Tianjin Guangfu Technology Development Co. Ltd (China). 20 wt% Pt on Vulcan XC-72 (Pt/C catalyst) was provided with Alfa Aesar. All other reagents were used directly.
2.2 Instrumentation
The samples morphology was observed by scanning electron microscopy (SEM, JEOL JSM-6701F electron microscope operating at 5 kV) and transmission electron microscopy (TEM, JEOL-2010 transmission electron microscope operating at 200 kV). Nitrogen adsorption and desorption isotherms were measured on a Micromeritics ASAP-2020 sorption analyser at 77 K. Raman spectra analysis was operated on a LabRAM HR Evolution Raman spectrometer at 785 nm. X-ray photoelectron spectroscopy (XPS) analysis was collected by an ESCLAB 250 spectrometer with a monochromatized Al Kα X-ray source.
2.3 Synthesis of N-GAs and Fe/N-GAs
The graphite oxide was prepared by a modified Hummers method. Firstly, the procedure for synthesizing N-GAs was as the following: 80 mg DAP and the appropriate APS were added to 2 mg mL−1 of 20 mL graphene oxide (GO) dispersion solution. Then the above mixture was dispersed by ultrasonic vibration for 30 min. Subsequently, this mixture was hydrothermally reacted at 180 °C in a Teflon lined stainless-steel autoclave for 20 h to form a 3D graphene hydrogels encapsulated in poly-2,6-diaminopyridine (GHs@PDAP). Then the PDAP coated graphene aerogels (GAs@PDAP) was accessible by a freeze-drying method from GHs@PDAP. Following, GAs@PDAP was pyrolyzed at 900 °C in a tubular furnace at the atmosphere of Ar gas for 2 h in order to form N-doped graphene aerogels (N-GAs). Then, Fe/N-GAs were prepared as the similar process as N-GAs except for adding different amount of ferric nitrate nonahydrate in the hydrothermal process, in which Fe ion can coordinate with nitrogen group in PADP, subsequently, the powder was leached in 1 M HCl aqueous solution by stirring for 24 h, as illustrated in Scheme 1. The Fe/N-GAs prepared by using different amount of ferric nitrate was denoted as x-Fe/N-GAs, where x stands for the weight of ferric nitrate nonahydrate. What's more, N-GAs 800 or N-GAs 1000 represented that GAs@PDAP was pyrolyzed at 800 or 900 °C, respectively. In addition, the synthesized process for N-doped 2D graphene (N-G) was the same as that of N-GAs except the mixture was reacted by stirring at 80 °C in an oil bath. Lastly, 3D graphene aerogels (GAs) was prepared as the similar process as GAs@PDAP in addition to adding DAP and APS.
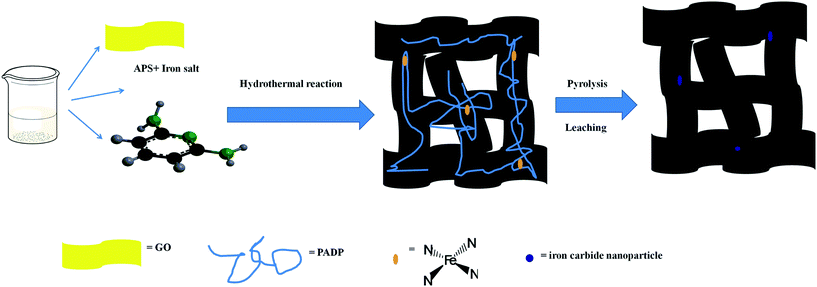 |
| Scheme 1 Schematic illustration of the synthesis route of Fe/N-GAs. | |
2.4 Electrochemical measurements
The rotating disk electrode (RDE, d = 5 mm), current–time chronoamperometric response (i–t), methanol tolerance experiment and rotating ring disk electrode (RRDE, disk = 5.61 mm) were conducted on a Pine Instrument Company AF-MSRCE modulator speed rotator on a CHI660E electrochemical workstation (CH Instruments, Shanghai CHENHUA company) employing a standard three-electrode system. A modified GCE, a platinum wire and a saturated calomel reference electrode (SCE) were used as working, counter and reference electrode, respectively. 1.0 mg catalyst was added to 1.0 mL ethanol to form a homogeneous ink by ultrasonic vibration for 2 h. To modify the electrode, the catalyst ink was dropped onto a freshly polished electrode surface with catalyst loading of 425 μg cm−2. Then Nafion was used as protector to prevent the catalyst from losing. The modification of GC electrode and electrochemical characterizations were operated at room temperature. Prior to the test, the electrolyte solutions were purged O2 for 30 min for making the solution saturated with O2. Moreover, the headspace of electrochemical cell was continuously purged with O2 during the measurement.
The kinetic parameters on Fe/N-GAs and Pt/C during the ORR process were evaluated by the Koutecky–Levich equation as follows:
|
 | (1) |
where
J is the measured current density,
JK and
JL are the kinetic and diffusion-limiting current densities, respectively,
F is the Faraday constant (
F = 96
![[thin space (1/6-em)]](https://www.rsc.org/images/entities/char_2009.gif)
485 C mol
−1),
ω is the angular velocity of the disk (
ω = 2π
N,
N is the linear rotation speed),
C0 is the bulk concentration of O
2 dissolved in the electrolyte,
D0 is the O
2 diffusion coefficient,
ν is the kinematic viscosity of the electrolyte, (
C0 = 1.2 × 10
−3 mol L
−1,
D0 = 1.9 × 10
−5 cm
2 s
−1,
ν = 0.01 cm
2 s
−1 for both 0.5 M H
2SO
4 and 0.1 M KOH solutions),
n is the transfer number.
The electron transfer number (n) and H2O2 yield on Fe/N-GAs and Pt/C during the ORR process were calculated from the following equations:
|
 | (2) |
|
 | (3) |
where
iD and
iR are the disk current and the ring current, respectively. And
N = 0.37 is the current collection efficiency.
3. Results and discussion
3.1 Characterizations
The morphologies of the as-prepared samples were examined by SEM and TEM. Typical SEM and TEM images are exhibited in Fig. 1. As shown in Fig. 1a–c, all N-GAs samples pyrolyzed at different temperature display interconnected porous 3D network with crumpled sheets, indicating that a porous 3D interconnected structure has not been destroyed by gas releasing at high temperature pyrolysis. Furthermore, the 3D structure is demonstrated by TEM image. As shown in Fig. 1d, N-GAs pyrolyzed at 900 °C show wrinkled structure and abundant pores, which contribute to more active sites exposure and mass transport.29 The high resolution TEM image of N-GAs cross-sectional view suggests that adjacent interlayer distance is approximate 0.35 nm in Fig. 1e, close to the d-spacing of the (002) crystal plane of graphite (0.335 nm).30 After introducing a few amount of ferric salt, the morphology of Fe/N-GAs is not changed much compared to that of N-GAs samples, still showing a 3D porous structure (Fig. 1f), while a little more amount of ferric salt is added, the morphology is evidently changed, displaying non-uniform structures with few nanoparticles (Fig. 1g). However, no obvious nanoparticle has been seen in Fig. 1f. To confirm the Fe species existence of 4-Fe/N-GAs, the TEM was employed. In Fig. 1h, trace and tiny nanoparticles are observed due to few amount iron salt addition and leaching by acid, the inset of HRTEM image shows clear lattice fringe, where the measured lattice spacing of 0.21 nm is corresponded to (112) plane of Fe5C2, indicating the successful introduction of Fe5C2 nanoparticles into N-GAs.
 |
| Fig. 1 SEM images of (a) N-GAs 800, (b) N-GAs, (c) N-GAs 1000, (f) 4-Fe/N-GAs, (g) 8-Fe/N-GAs, TEM images of (d) N-GAs, (h) 4-Fe/N-GAs, inset: HRTEM images of iron-based nanoparticles and (e) HRTEM images of N-GAs. | |
The structure of the as-prepared samples was measured by Raman spectroscopy. All samples show a D band and a G band centered at 1339 and 1594 cm−1, respectively (Fig. 2a). The D peak corresponds to the disorder-induced structure in the aromatic rings, and the G peak reflects an ordered graphitic carbon atoms.30 Moreover, the ratio of D band to G band intensity is employed to evaluate the defect level. As shown in Fig. 2b, it is found that the N-GAs samples display higher ID/IG ratio than GAs, implying that more defects degree is produced in the carbon lattice by N-doping. Furthermore, the ID/IG ratio decreases with increase the pyrolysis temperature ascribed to higher graphitization degree at higher pyrolysis temperature.31 In addition, 4-Fe/N-GAs show a relatively lower ID/IG ratio owing to the improved graphitization degree of graphene generated by metal.32 The X-ray diffraction (XRD) patterns of Fe/N-GAs samples in Fig. 2c presents two typical peaks located at 43.39° and 26.6°, which are indexed to Fe5C2 (PDF card no. 51-0997) and graphitic carbon, respectively. This result verifies that iron carbide is formed during the pyrolyzing process, which is identified as a highly active sites in both alkaline and acidic solutions.21,22 As displayed in Fig. 2d, the specific area for N-GAs, 4-Fe/N-GAs and 8-Fe/N-GAs is 378.68 m2 g−1, 430.19 m2 g−1 and 366.80 m2 g−1 determined by nitrogen adsorption–desorption isotherms. And the corresponding textural parameters are listed in Table 1. It is found that 8-Fe/N-GAs show smaller surface area than 4-Fe/N-GAs, possibly attributed to the destruction of 3D structures which is displayed by SEM in Fig. 1g.
 |
| Fig. 2 (a) Raman spectra of GAs, N-GAs pyrolyzed at different temperature and 4-Fe/N-GAs. (b) The ID/IG ratio of different samples. (c) XRD patterns of 4-Fe/N-GAs and 8-Fe/N-GAs. (d) N2 adsorption–desorption isotherms at 77 K of N-GAs and 4-Fe/N-GAs. | |
Table 1 BET surfaces area, BJH adsorption average pore size and BJH adsorption cumulative volume of pores of N-GAs and 4-Fe/N-GAs
Samples |
BET surfaces area/m2 g−1 |
Pore size/nm |
Pore volume/cm3 g−1 |
N-GAs |
378.68 |
54.56 |
0.320 |
4-Fe/N-GAs |
430.19 |
39.69 |
0.471 |
8-Fe/N-GAs |
366.80 |
37.94 |
0.300 |
To investigate the chemical composition of samples, XPS measurements were conducted. The C 1s, N 1s and O 1s peaks of all samples are showed in XPS survey spectra, suggesting that carbon is successfully doped by nitrogen (in Fig. S1†). However, the Fe signals are not obviously exhibited in Fe/N-GAs samples due to the low content of Fe (Table 2) and Fe encapsulated in carbon layers. Depicted in Fig. 3a–c, the high resolution XPS N 1s spectra of N-GAs, 4-Fe/N-GAs and 8-Fe/N-GAs are deconvoluted into four peaks: pyridinic N (398.12 ± 0.08 eV), pyrrolic N (399.46 ± 0.16 eV), graphitic N (401.00 ± 0.20 eV) and oxidized N (402.88 ± 0.09 eV). Moreover, the high resolution XPS N 1s spectra of N-GAs pyrolyzed at different temperature are showed in Fig. S2.† Fig. 3d demonstrates that the oxidized N percentage increases with adding ferric salt as well as with increase amount of ferric salt, which is considered to play little effect on ORR activity.33 However, the graphitic N percentage decreases. The reported researches indicates that oxygen reduction activity can be enhanced on graphitic-, pyridinic- and pyrrolic-N species. Nevertheless, the selectivity and catalytic activity for ORR are strongly affected by N bonding configurations. It has been confirmed that graphitic N can enhance the limiting-current density, as well as pyridinic N can improve the onset potential, while pyrrolic N has little effect for ORR.34 The atomic percentage content of elements and N species is presented in detail in Table 2. Compared to other samples, N-GAs possesses comparatively higher graphitic N and pyridinic N content, which is beneficial to ORR.34,35 Furthermore, the total N content decreases as well as graphitic N and pyridinic N content becomes lower with ferric salt addition. So, we can draw a conclusion that the existence of Fe species can hinder the N doping compared to N-GAs in our experimental system.
Table 2 Atomic percentage of C, N, O, Fe and N functionalities from XPS survey spectra
Samples |
C 1s |
N 1s |
O 1s |
Fe 2p |
N at% |
Pyridinic N |
Pyrrolic N |
Graphitic N |
Oxidized N |
N-GAs 800 |
93.38 |
3.9 |
2.72 |
— |
1.06 |
0.74 |
1.48 |
0.62 |
N-GAs |
94.12 |
3.28 |
2.6 |
— |
0.91 |
0.64 |
1.23 |
0.50 |
N-GAs 1000 |
95.9 |
2.31 |
1.79 |
— |
0.51 |
0.26 |
1.20 |
0.34 |
4-Fe/N-GAs |
94.30 |
2.54 |
3.03 |
0.13 |
0.46 |
0.51 |
0.89 |
0.68 |
8-Fe/N-GAs |
94.48 |
2.02 |
3.33 |
0.17 |
0.40 |
0.26 |
0.65 |
0.71 |
 |
| Fig. 3 Analysis of the doping N types in N-GAs (a), 4-Fe/N-GAs (b), 8-Fe/N-GAs (c) and percentage variation of nitrogen functionalities for N-GAs, 4-Fe/N-GAs and 8-Fe/N-GAs (d). | |
3.2 Electrocatalytic evaluations in alkaline solution
The electrocatalytic activity for ORR on samples was firstly examined by liner sweep voltammetry (LSV) measurement. Fig. 4a and c show LSV curves at different rotation speed on N-GAs and 4-Fe/N-GAs samples, the diffusion-limiting current is enhanced with increase the rotation speed (from 200 to 2500 rpm) due to the shortened diffusion distance at high rotation speeds. The corresponding K–L plots (J−1 versus ω−1/2) at different potential are illustrated in Fig. 4b and d, good linear relation with similar constant slopes is observed, suggesting the first-order reaction kinetics for ORR on N-GAs and 4-Fe/N-GAs as to the dissolved O2 concentration together with a similar electron transfer number for ORR in the selected potential range. Fig. 4e and f describe LSV curves for as-prepared samples and Pt/C at the rotation rate of 1600 rpm, it is found that 4-Fe/N-GAs exhibits highly active towards ORR in the terms of onset potential (Eonset = −0.04 V vs. SCE), half-wave potential (E1/2 = −0.21 V vs. SCE) and diffusion-limiting current density (JL = 6.65 mA cm−2). The Eonset and E1/2, and JL for ORR on samples are summarized in Table S1.† Also, 4-Fe/N-GAs display comparable ORR activity with Pt/C catalyst. It is worth noting that a few amount of ferric salt in the experimental system can promote the more positive onset potential, half-wave potential and higher diffusion-limiting current density, whereas more ferric salt amount can only boost more positive onset potential and half-wave potential, but reduce diffusion-limiting current density.
 |
| Fig. 4 LSV curves of (a) N-GAs and (c) 4-Fe/N-GAs at different rotation speeds in 0.1 M KOH saturated with O2 at the scan rate of 10 mV s−1, K–L plots of (b) N-GAs and (d) 4-Fe/N-GAs at different potentials, respectively, (e) and (f) LSV curves of different samples at 1600 rpm in 0.1 M KOH saturated with O2 at the scan rate of 10 mV s−1, (g) Tafel plots for O2 reduction on N-GAs, 4-Fe/N-GAs and Pt/C in 0.1 M KOH solution saturated with O2 at 1600 rpm, (h) the kinetic current density (JK) at fixed potentials. | |
As discussed in the introductory part, there are several crucial factors influencing the ORR performance of catalyst. In our case, first and foremost, the active sites as to N-GAs samples originate from N doping, therefore, the ORR activity is highly dependent on density and species of N. From the analysis of XPS and N2-adsorption isotherms results, N-GAs are provided with higher pyridinic N and graphitic N content as well as high surface area (378.68 m2 g−1). Thus, it exhibits higher activity towards ORR (Fig. S3†). Then, for Fe/N-GAs samples, the active sites should be generated by both N doping and iron carbide activation. Although pyridinic N and graphitic N content on 4-Fe/N-GAs is reduced in comparison with N-GAs, it still displays improved ORR activity, we think, it is due to the fact that trace iron carbide nanoparticles on 4-Fe/N-GAs are considered as efficiently active sites. Furthermore, it possesses higher surface area (430.19 m2 g−1) that can facilitates the active sites exposure. 8-Fe/N-GAs show smaller diffusion-limiting current density due to the fact that it has lower nitrogen content coupled with broken 3D structure which may impede mass transfer and lower the surface area (366.80 m2 g−1). Moreover, both Fe/N-GAs display more positive onset and half-wave potentials than that of N-GAs owing to the fact that Fe/N-GAs have lower defects density from a lower ID/IG ratio. Lastly, owing to the porous 3D structures that can promote the mass transfer and active sites exposure, N-GAs present better activity as regards to onset potential compared to N-G, therefore, porous 3D graphene is a advantaged candidate catalyst instead of 2D graphene.
In order to further evaluate the ORR performance on N-GAs, 4-Fe/N-GAs and Pt/C, the mass-corrected Tafel plots (E vs. log
JK) was plotted as shown in Fig. 4g derived from LSV curves at 1600 rpm (Fig. 4f). Tafel slopes for N-GAs, 4-Fe/N-GAs and Pt/C are −90, −108 and 95 mV dec−1 at low overpotentials region, indicating that the rate-determining step is the first electron transfer on oxygen reduction. Upon a mechanistic view point, a little smaller Tafel slope of N-GAs than Pt/C suggests that N-GAs exhibit improved ORR kinetics compared to Pt/C.35,36 Fig. 4h shows the kinetic current density (JK) for samples in selected potentials according to the K–L equation (eqn (1)). The kinetic current density of 4-Fe/N-GAs is calculated to be 32.34 mA cm−2 at −0.4 V vs. SCE, which is higher than that of N-GAs (20.29 mA cm−2) and Pt/C (18.64 mA cm−2), thus, again, indicating 4-Fe/N-GAs possesses superior activity for ORR ascribed to rapid mass transfer, high surface area coupled with effectively active sites exposure in the porous 3D architectures.
To further examine the ORR activity on samples, RRDE measurements were carried out to determine the 4e selectivity. From the disk and ring current exhibited in Fig. 5a, the HO2− yield (%) and the electron transfer number at different potentials on N-GAs, 4-Fe/N-GAs and Pt/C can be calculated based on eqn (2) and (3). As presented in Fig. 5b, the number of the electron transfer for N-GAs and 4-Fe/N-GAs is close to 3.9. In Fig. 5c, no obvious HO2− is detected, and the HO2− yield is lower than 5.5%, confirming that ORR is a direct a 4-electron process on both N-GAs and 4-Fe/N-GAs.
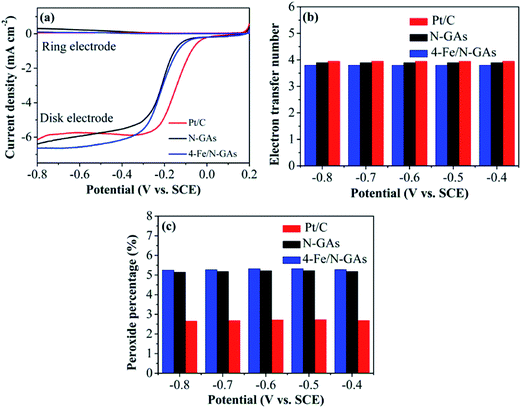 |
| Fig. 5 (a) Rotating ring disk electrode (RRDE) measurements of N-GAs, 4-Fe/N-GAs and Pt/C in 0.1 M KOH saturated with O2 with a scan rate of 10 mV s−1 at a rotation speed of 1600 rpm. (b) Electron transfer number of N-GAs, 4-Fe/N-GAs and Pt/C at selected potentials. (c) Hydrogen peroxide percentage N-GAs, 4-Fe/N-GAs and Pt/C at selected potentials. | |
3.3 Electrocatalytic evaluations in acidic solution
To promote the commercial development of PEMFC, it is increasing important to synthesize catalysts with highly active in acidic medium. Consequently, the ORR activity evaluation in 0.5 M H2SO4 on N-GAs, 4-Fe/N-GAs and Pt/C was also performed by liner sweep voltammetry (LSV) measurement (Fig. 6a). It is found that 4-Fe/N-GAs display highly improved activity than N-GAs in acidic solution owing to the fact that iron carbide nanoparticles encapsulated in carbon are considered as effectively active sites in acidic medium.22 The 4-Fe/N-GAs show a similar onset potential as well as diffusion-limiting current density, but exhibits a worse half-wave potential (ΔE1/2 = 200 mV) compared to Pt/C. Fig. 6b exhibits RRDE voltammograms on 4-Fe/N-GAs and Pt/C, respectively. Calculated from eqn (2) and (3), as shown in Fig. 6c, the electron transfer number for 4-Fe/N-GAs is about 3.50 and the HO2− yield is near to 21% which is higher than Pt/C. Kinetic current density (JK) is also observed in Fig. 6d, JK on 4-Fe/N-GAs is much lower than that of Pt/C, but higher than N-GAs, indicating a highly enhanced activity for ORR in acidic medium. Although the 4-Fe/N-GAs shows inferior activity to Pt/C, this work play a crucial role in guiding our future works: how to reasonable design and controllable synthesis of the porous carbon-based catalyst with appropriate active sites such as iron carbide and heteroatom-doping, high surface area and proper pore size is our next work focus in order to improve the ORR activity in acidic solution.
 |
| Fig. 6 (a) LSV curves of N-GAs, 4-Fe/N-GAs and Pt/C, (b) rotating ring disk electrode (RRDE) measurements of 4-Fe/N-GAs and Pt/C, (c) electron transfer number and hydrogen peroxide yield of 4-Fe/N-GAs and Pt/C at fixed potentials, (d) the kinetic current density (JK) at fixed potentials, all above tests were conducted in O2-saturated 0.5 M H2SO4 with the rotation rate of 1600 rpm at a scan rate of 10 mV s−1. | |
The stability and resistance to methanol crossover effect towards ORR are significant factors in FCs technology. Firstly, the stability was assessed on N-GAs, 4-Fe/N-GAs and Pt/C by chronoamperometric measurement (Fig. 7a). The current density decreases by 9.50%, 17.5% and 20.3% compared to its initial current as to N-GAs, 4-Fe/N-GAs and Pt/C after 10
000 s testing, indicating better stability for N-GAs and 4-Fe/N-GAs. In addition, in Fig. 7b, N-GAs and 4-Fe/N-GAs further exhibit a better tolerance to methanol with no apparent change in current upon addition of 3 M methanol into electrolyte, while Pt/C displays sharp decrease in current under the same conditions. Notably, thus, 4-Fe/N-GAs shows outstanding activity, high stability and better tolerance to methanol in alkaline solution, together with improved activity in acidic solution.
 |
| Fig. 7 (a) durability evaluation on N-GAs, 4-Fe/N-GAs and Pt/C at −0.36, −0.4 and −0.2 V vs. SCE in O2-saturated 0.1 M KOH with a rotation speed of 1600 rpm for 10 000 s. (b) Chronoamperometric response for ORR at N-GAs, 4-Fe/N-GAs and Pt/C with a rotation speed of 1600 rpm in O2− saturated 0.1 M KOH solution with 3 M methanol added after about 300 s. | |
4. Conclusion
To conclude, we have synthesized Fe, N co-functionalized porous 3D graphene catalyst by a simple and cost-effective strategy. The as-prepared catalysts possesses interconnected porous 3D network and effectively active sites. The active site species and defects on N-GAs catalyst could be tuned by controlling the pyrolysis temperature, thus, the electrocatalytic activity can be adjusted. Also, the influence of Fe species on structures and properties of N-GAs is observed. It is found that the existence of Fe species will affect the total N content, defects and morphology of N-GAs, the N-GAs with appropriate Fe functionality possess superior activity, high stability and better tolerance to methanol in alkaline medium as well as improved activity in acidic medium due to effective active sites species, high surface area and synergetic effect between Fe species and the doped-N. Inspiring by this work, we will rationally design, controllably synthesize hierarchically porous carbon materials functionalized by metal and heteroatom doping and observe effect of morphology, pores distribution, active sites species and density of catalyst on catalytic performance at different pH solutions in the following work.
Acknowledgements
The work has been supported by the Natural Science Foundation of China (No. 21273024) and Natural Science Foundation of Jilin Province, China (No. 20160101298JC).
References
- G. Wu and P. Zelenay, Acc. Chem. Res., 2013, 46, 1878–1889 CrossRef CAS PubMed.
- X. L. Sun, D. G. Li, Y. Ding, W. L. Zhu, S. J. Guo, Z. L. Wang and S. H. Sun, J. Am. Chem. Soc., 2014, 136, 5745–5749 CrossRef CAS PubMed.
- S. Zhang, X. Zhang, G. M. Jiang, H. Y. Zhu, S. J. Guo, D. Su, G. Lu and S. H. Sun, J. Am. Chem. Soc., 2014, 136, 7734–7739 CrossRef CAS PubMed.
- J. M. Su, X. C. Cao, J. Wu, C. Jin, J. H. Tian and R. Z. Yang, RSC Adv., 2016, 6, 24728–24737 RSC.
- S. N. Bhange, S. M. Unniab and S. Kurungot, J. Mater. Chem. A, 2016, 4, 6014–6020 CAS.
- Z. Q. Jiang, X. S. Zhao, X. N. Tian, L. J. Luo, J. H. Fang, H. Q. Gao and Z. J. Jiang, ACS Appl. Mater. Interfaces, 2015, 7, 19398–19407 CAS.
- M. Hassan, E. Haque, A. I. Minett and V. G. Gomes, ChemSusChem, 2015, 8, 4040–4048 CrossRef CAS PubMed.
- R. Jasinski, Nature, 1964, 201, 1212–1213 CrossRef CAS.
- L. L. Cui, G. J. Lv and X. Q. He, J. Power Sources, 2015, 282, 9–18 CrossRef CAS.
- W. L. Gu, L. Y. Hu, W. Hong, X. F. Jia, J. Li and E. Wang, Chem. Sci., 2016, 7, 4167–4173 RSC.
- S. Dou, L. Tao, J. Huo, S. Y. Wang and L. M. Dai, Energy Environ. Sci., 2016, 9, 1320–1326 CAS.
- Z. J. Wang, B. Li, X. M. Ge, F. W. T. Goh, X. Zhang, G. J. Du, D. Wuu, Z. L. Liu, T. S. A. Hor, H. Zhang and Y. Zong, Small, 2016, 12, 2580–2587 CrossRef CAS PubMed.
- W. Xia, R. Q. Zou, L. An, D. G. Xia and S. J. Guo, Energy Environ. Sci., 2015, 8, 568–576 CAS.
- Y. F. Yao, Y. You, G. X. Zhang, J. G. Liu, H. R. Sun, Z. G. Zou and S. H. Sun, ACS Appl. Mater. Interfaces, 2016, 8, 6464–6471 CAS.
- Q. H. Lai, Q. Su, Q. W. Gao, Y. Y. Liang, Y. X. Wang, Z. Yang, X. G. Zhang, J. P. He and H. Tong, ACS Appl. Mater. Interfaces, 2015, 7, 18170–18178 CAS.
- Z. H. Li, M. F. Shao, L. Zhou, R. K. Zhang, C. Zhang, M. Wei, D. G. Evans and X. Duan, Adv. Mater., 2016, 28, 2337–2344 CrossRef CAS PubMed.
- K. Strickland, E. Miner, Q. Y. Jia, U. Tylus, N. Ramaswamy, W. T. Liang, M. T. Sougrati, F. Jaouen and S. Mukerjee, Nat. Commun., 2016, 6, 7343 CrossRef PubMed.
- J. Wei, Y. Liang, Y. X. Hu, B. Kong, G. P. Simon, J. Zhang, S. P. Jiang and H. T. Wang, Angew. Chem., Int. Ed., 2016, 55, 1355–1359 CrossRef CAS PubMed.
- K. Artyushkova, A. Serov, S. Rojas-Carbonell and P. Atanassov, J. Phys. Chem. C, 2015, 119, 25917–25928 CAS.
- J. J. Yan, H. Y. Lu, Y. P. Huang, J. Fu, S. Y. Mo, C. Wei, Y. E. Miao and T. X. Liu, J. Mater. Chem. A, 2015, 3, 23299–23306 CAS.
- M. L. Xiao, J. B. Zhu, L. G. Feng, C. P. Liu and W. Xing, Adv. Mater., 2015, 27, 2521–2527 CrossRef CAS PubMed.
- G. Y. Zhong, H. J. Wang, H. Yu and F. Peng, J. Power Sources, 2015, 286, 495–503 CrossRef CAS.
- Y. L. Liu, X. Y. Xu, P. C. Sun and T. H. Chen, Int. J. Hydrogen Energy, 2015, 40, 4531–4539 CrossRef CAS.
- W. X. Yang, X. J. Liu, X. Y. Yue, J. B. Jia and S. J. Guo, J. Am. Chem. Soc., 2015, 137, 1436–1439 CrossRef CAS PubMed.
- Y. Hu, J. O. Jensen, W. Zhang, L. N. Cleemann, W. Xing, N. J. Bjerrum and Q. F. Li, Angew. Chem., Int. Ed., 2014, 53, 3675–3679 CrossRef CAS PubMed.
- H. Hu, Z. B. Zhao, W. B. Wan, Y. Gogotsi and J. S. Qiu, Adv. Mater., 2013, 25, 2219–2223 CrossRef CAS PubMed.
- M. Wu, Z. Y. Dou, J. J. Chang and L. L. Cui, RSC Adv., 2016, 6, 22781–22790 RSC.
- V. Chabot, D. Higgins, A. Yu, X. C. Xiao, Z. W. Chen and J. J. Zhang, Energy Environ. Sci., 2014, 7, 1564–1596 CAS.
- L. F. Lai, J. R. Potts, D. Zhan, L. Wang, C. K. Poh, C. Tang, H. Gong, Z. X. Shen, J. Y. Lin and R. S. Ruoff, Energy Environ. Sci., 2012, 5, 7936–7942 CAS.
- J. A. Turnbull, M. S. Stagg and W. T. Eeles, Carbon, 1966, 3, 387–392 CrossRef CAS.
- Q. L. Zhu, W. Xia, T. Akita, R. Q. Zou and Q. Xu, Adv. Mater., 2016 DOI:10.1002/adma.201600979.
- H. L. Tang, S. C. Cai, S. L. Xie, Z. B. Wang, Y. X. Tong, M. Pan and X. H. Lu, Adv. Sci., 2016, 3, 1500265 CrossRef.
- D. Deng, X. Pan, L. Yu, Y. Cui, Y. Jiang, J. Qi, W. X. Li, Q. Fu, X. Ma, Q. Xue, G. Sun and X. Bao, Chem. Mater., 2011, 23, 1188–1193 CrossRef CAS.
- L. F. Lai, J. R. Potts, D. Zhan, L. Wang, C. K. Poh, C. Tang, H. Gong, Z. X. Shen, J. Y. Linand and R. S. Ruoff, Energy Environ. Sci., 2012, 5, 7936–7942 CAS.
- W. H. He, C. H. Jiang, J. B. Wang and L. H. Lu, Angew. Chem., Int. Ed., 2014, 53, 9503–9507 CrossRef CAS PubMed.
- K. Elumeeva, J. Ren, M. Antonietti and T. P. Fellinger, ChemElectroChem, 2015, 2, 584–591 CrossRef CAS.
Footnote |
† Electronic supplementary information (ESI) available. See DOI: 10.1039/c6ra17670d |
|
This journal is © The Royal Society of Chemistry 2016 |
Click here to see how this site uses Cookies. View our privacy policy here.