DOI:
10.1039/C6RA15190F
(Paper)
RSC Adv., 2016,
6, 73203-73209
Fabrication of a graphene coated nonwoven textile for industrial applications
Received
11th June 2016
, Accepted 20th July 2016
First published on 21st July 2016
Abstract
A cost effective electrically conductive textile for large scale applications would revolutionise numerous industries. Herein, we demonstrate a novel processing approach to produce conductive textiles for industrial applications. A conductive nonwoven textile was successfully fabricated using a simple dip coating method. The nonwoven polyester was coated with liquid crystallite graphene oxide with subsequent non-toxic chemical reduction. The process is readily scalable. The graphene coated fabric has been characterized by electron microscopy as well as by electrical, mechanical, thermal and abrasion resistance measurements. It was found that the electrical surface resistivity of the prepared polyester–graphene composite fabric was 330 Ω □−1. The electrical surface resistivity was 3 and 150 times lower than that of polypyrrole coated woven polyester fabric and graphene coated nonwoven fabrics, respectively, in previously published reports. The hybrid polyester–graphene textile prepared here should find applications in high-performance geotextiles or as heating elements.
Introduction
Electrically conductive textiles have been used in numerous applications, including health care, the military, and wearable electronics. They have also been used as heating elements in industrial and residential heating components, such as carpet, automobile seats and de-icing of aircraft driveways.1 Using electrically conductive nonwoven textiles in heating applications will have benefits over metal heating elements, as they are free of corrosion, have low manufacturing costs, are flexible, can be formed into required shapes and are lightweight. In addition, conductive textiles can be used in industrial applications such as electrokinetic geosynthetics (EKGs), which is a class of material used to replace conventional electrodes in leak detection systems. The most commonly used electrodes are metals, such as iron, steel or copper.2–4 EKGs may be single composition materials that are electrically conductive or composite materials in which at least one element is electrically conductive. EKGs based on polymeric materials have some advantages over metal electrodes, including corrosion resistance, being able to form a variety of shapes, and low cost. A low cost electrically conductive nonwoven textile that can be produced on a large scale with easy installation will provide a more affordable mechanism over the abovementioned EKG materials.
Numerous studies have been reported for textiles modified with different types of conductive materials for smart textiles and heat generation applications. Most research has focused on either coating or blending of polyester fibres or yarns with conductive materials.5–14 The methods used to incorporate conductive materials with fibres or yarns require sophisticated processes and/or equipment, which compromises large scale production. In contrast, process complications can be reduced considerably by incorporating conductive materials directly onto preformed textile fabrics using polymerisation, deposition of metals, weaving or integration of metal fibres or wires.1,13,15–21
Electrical conductors have been incorporated into textiles via printing or coating to obtain lightweight conducting materials. Printing or coating techniques can avoid high temperature gradients in heating elements, as the temperature generated is distributed over the surface of the fibre composites.20,22 Further, dip coating methods are attractive because of their similarity to dying processes already used in industry. Recently, the fabrication of a conductive polyester nonwoven textile was reported with a one-step dying-like approach using an aqueous dispersion of reduced graphene oxide (rGO) with polyurethane as the adhesive layer to give a minimum surface resistance of 5 × 104 Ω □−1.23 A similar approach is used in the current work.
Physical properties, commercial availability and easy processability are the major factors to consider in large scale applications. Polyester is considered one of the “greatest” man-made fibres and widely used in many hybrid composite applications due to its outstanding physical properties.24–26 Mechanical properties, durability, abrasion resistance and resistance to weather are major characteristics of polyester fibres. Polyester fibres are readily converted to nonwoven textiles.27,28 This involves wet-laid29 and melt-blown30 web forming processes combined with mechanical methods such as needle punching and chemical or thermal bonding.31–34 Nonwoven polyester textiles are strong, permeable, and resistant to stretching, heating, shrinking, abrasion, mildew and most chemicals; this enables them to be used in applications such as filtering, geotextiles, thermal insulation, disposable hygiene products such as surgical gowns, and diapers, and in many other areas.35–40 Moreover, its thermal, mechanical and optical properties make graphene a choice material to be used for a wide variety of applications.41–46 Graphene oxide (GO) produced by chemical methods can be manufactured on a large scale.47–49 The aim of this study is to investigate methods to generate high conductivity, abrasion resistant coatings on non-woven fabric using a dip coating method. Herein, we report a simple method of fabricating a conductive nonwoven coating with liquid crystalline graphene oxide (LCGO) solution followed by chemical reduction for large scale industrial applications.
Materials and methods
Preparation of LCGO
GO was prepared from intercalated graphite flakes (3772, Asbury Graphite Mills USA). Typically, the intercalated graphite flakes were first thermally expanded at 700 °C under nitrogen atmosphere for 5 s or less. The resulting expanded graphite (270 to 300 times volume expansion) was used as the precursor for GO synthesis. Typically, 10 g expanded graphite and 1 L of sulphuric acid were mixed and stirred in a flask using a mechanical stirrer, and the temperature was reduced using an ice–salt bath. After 15 min of stirring, 45 g of KMnO4 was slowly added over a 1/2 h period. The slow stirring was continued for 3 h. The temperature was raised to 55 °C and maintained for 3 h. The reaction mixture became more viscous and the colour changed from green to grey. The contents were cooled with an ice bath for 30 minutes, and then 1 L Milli-Q water was added dropwise with continued ice-bath cooling. The addition of the initial 500 mL of Milli-Q water occurred over approximately 90 minutes, followed by addition of the remaining 500 mL over 30 minutes. This procedure can be performed overnight depending on the requirement to maintain a low temperature. The dropwise addition of 100 mL of 40% hydrogen peroxide (H2O2) solution changed the colour of the mixture to bright yellow. The contents were further diluted with 10 L of Milli-Q water and allowed to settle overnight. The clear supernatant acid was decanted, and 500 mL of diluted hydrogen chloride (∼10%) was added to the reaction mixture to remove the manganese salts. The contents were stirred for 30 minutes and allowed to settle. The washing process was repeated 2 to 3 times until the pH of the supernatant was ∼2. The contents were finally dialysed until the pH of the washing water was ∼3.4. The GO was obtained as a viscous dispersion with a 130 to 145% increase in weight based on graphite.47,48,50 Two different concentration dispersions with LCGO contents of 0.25% wt and 0.6% wt were prepared.
Preparation of conductive nonwoven textile
Polyester nonwoven textile with a linear density of 180 g m−2, supplied by Bidim Nonwoven Geotextiles (Australia), was cleaned in purified water via ultra-sonication. For the first coating cycle, the pre-treated nonwoven material was dipped in the LCGO solution for 1 to 2 minutes and then removed. Then, the LCGO dip coated textile was dried in air at room temperature for 24 h. Subsequent coatings were applied using the same procedure, up to the 6th coating cycle. Fig. 1 outlines the preparation method used. The amount of GO coated onto the nonwoven textile was controlled by changing the number of coating steps and by using different LCGO concentrations. Nonwoven textiles with different numbers of coatings were prepared by dipping the textile in the LCGO-0.25% wt and LCGO-0.6% wt dispersions.
 |
| Fig. 1 Representation of the fabrication of the rGO samples. (a) Cleaning in purified water, (b) dipping the nonwoven textile in LCGO solution, (c) drying in air, (d) chemical reduction, (e) washing and drying to remove excess GO. The number of coating cycles can be increased by repeating processes “b” and “c”. | |
Reduction of GO
Chemical reduction was carried out to convert GO to reduced graphene oxide. The obtained LCGO coated nonwoven samples were chemically reduced after drying overnight using 5 g of sodium dithionite and sodium bisulfite mixed in a 4
:
1 ratio and dissolved in 900 mL of water. The reduction process was carried out at 95 °C for 1 h. Next, the reduced graphene oxide coated nonwoven specimens (rGO) were washed in Milli-Q water to remove any remaining salts. The rGO samples were designated as per Table 1.
Table 1 Preparation of LCGO coated nonwoven samples
LCGO (%) in coating solution |
Number of coating cycles |
Designation of rGO samples |
0.25 |
X = 1, 2, 3, 4, 5, 6 |
R′X |
0.6 |
X = 1, 2, 3, 4, 5, 6 |
RX |
Characterisation
X-ray photoelectron spectroscopy. X-ray Photoelectron Spectroscopy (XPS) was carried out to evaluate the graphene coating and chemical reduction. XPS is a spectroscopic surface sensitive technique that measures the composition of a material at the parts per thousand range. The material is irradiated with an X-ray beam while simultaneously measuring the number of electrons that escape and their kinetic energy. XPS was conducted using a SPECS PHOIBOS 100 Analyser installed in a high-vacuum chamber with a base pressure below 10 to 8 mbar; X-ray excitation was provided by Al Kα radiation with photon energy hν = 1486.6 eV at a high voltage of 12 kV and a power of 120 W. The XPS binding energy spectra were recorded at the pass energy of 20 eV in the fixed analyser transmission mode. Analysis of the XPS data was carried out using the commercial CasaXPS 2.3.15 software package. The elemental compositions of the LCGO coated nonwoven material after the 3rd coating (GO3) and the rGO samples (R1, R2, R3) were analysed.
Electrical properties. The effects of mechanical bending on the electrical resistances of the rGO coated specimens were investigated with 20 mm × 20 mm samples, as shown in Fig. 2. The electrical resistivity was characterised during and after bending. The deformation was carried out on a Shimadzu EZ mechanical tester with a deformation rate of 20 mm min−1 and a stroke of 9 mm for fifty bending and release cycles. The multimeter was connected to the specimens during the deformation test to continuously monitor the electrical resistance.
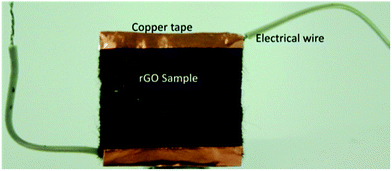 |
| Fig. 2 An image of an rGO sample connected with insulated electrical wires for characterisation of its electrical properties during bending. | |
The surface resistivity of the samples was determined from
where the resistance
R is measured using a multimeter;
σs is the surface resistivity,
W is the width and
L is the length.
Thermal behaviour. The thermal characteristics of the R3 sample were evaluated by an infrared camera. The sample size was 200 mm × 200 mm and the sample was mounted onto a frame with nonconductive strings. Then, the two insulated wires were attached to R3 using cupper tapes, which were connected to a power source via alligator clips. The R3 sample was heated by applying a voltage of 32.5 V (DC). A thermographic camera was used for infrared video capturing with the arrangement shown in Fig. 3.
 |
| Fig. 3 (a) As-prepared graphene coated textile sample (R3), (b) apparatus arrangement including (b1) infrared camera, (b2) power source, (b3) screen and (b4) rGO sample, (c) heating of nonwoven rGO (R3) prepared using 3 coating cycles of 0.6 wt% LCGO. | |
Morphological observation. The surface morphology of the rGO sample (R3), LCGO coated nonwoven textile and raw nonwoven textile was observed by scanning electron microscope (SEM, JEOL JSM-7500 FA). The surfaces of the samples were coated with platinum before analysis. In addition, optical images of the rGO samples with different numbers of coating cycles (1st, 2nd, 3rd and 6th coating) were captured by optical microscope (model LECIA M205 A) to observe the differences in GO deposition in the nonwoven textiles.
Abrasion wear resistance. The abrasion resistance test was conducted on a 90 mm diameter circular sample of R3. The sample was uniformly placed under one kilogram as an abrading load, and the rotary stage containing the sample was rotated at 100 rpm for 1 h. The sample was abraded against a high-density polyethylene (HDPE) sheet supplied by Bidim Nonwoven Geotextiles (Australia). The resistance was measured after every 1 h, and the resistance change was calculated.
Results and discussion
Graphene oxide coating
The percentage weight increment of the samples for successive coating cycles is illustrated in Fig. 4. As can be seen in the graph, the coating mass increases approximately linearly with the number of coating cycles. The amount of GO adsorbed onto the surface of the fabric increased when a more concentrated LCGO solution was used. The GO adsorption to the fibre surface is influenced by the concentration of LCGO, the fibre surface tension and the surface area of the fibres. The chemical interaction between the nonwoven textile and GO is a result of van der Waals forces, hydrogen bonding between the atoms of the ester groups of the polyester fibres and the anionic functionalities of LCGO.51
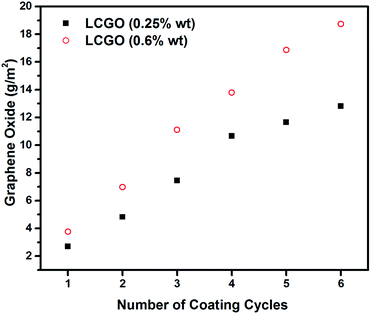 |
| Fig. 4 GO deposition onto nonwoven textile as a function of the number of coating cycles for two different coating solutions with the indicated concentrations of LCGO. | |
XPS
Elemental analysis was carried out for the nonwoven samples to investigate the nature of the coating and chemical reduction processes. The chemical process was used to reduce the oxygen containing groups in order to convert GO into rGO. rGO is a chemically improved version of graphene with a conjugated structure and modified thermal and electrical properties. As can be seen in Table 2, the percentage of carbon increases with the number of coating cycles. This further confirms the increase of GO mass with successive coating cycles. In addition, the percentage of oxygen decreased by approximately 17% for the highest conductive sample (R3) which was obtained after the chemical reduction of GO3, due to the removal of oxygen containing groups.
Table 2 XPS data
Sample |
Mass of elements (%) |
Carbon (C) |
Oxygen (O) |
1st coating reduced (R1) |
77.22 |
22.78 |
2nd coating reduced (R2) |
81.75 |
18.75 |
3rd coating reduced (R3) |
83.56 |
16.44 |
3rd coating non reduced (GO3) |
66.87 |
33.13 |
Morphological observations
The surface morphology of the as-received nonwoven fabric, GO coated sample and rGO sample are shown in Fig. 5(a–c), respectively. As can be seen in Fig. 5(a), fibres are randomly distributed within the nonwoven material. The absorbed LCGO is encapsulated in the interfibre porous areas around the individual fibres, as presented in Fig. 5(b) and (c). Polyester fibres are inherently hydrophobic, due to the lack of polar groups. The hydrophobicity of the polyester fibre counteracts the entry of water molecules into the interior of the fibres. Therefore, it can be assumed that the amount of LCGO absorbed into the fibre interior is minimal. As can be clearly seen in Fig. 5(d), GO is deposited in the interstices of the fibres. Fig. 5(e) presents the rGO layers in the fibre composite. The dimensions of the interstices, the number of interstices per unit mass of the nonwoven textile, and regional variations in the fibre packing density will influence the GO absorbed into the nonwoven composite. The low magnification photographic view of the as-prepared conducting nonwoven textile clearly shows the uniformly coated fabric structure (Fig. 5(f)).
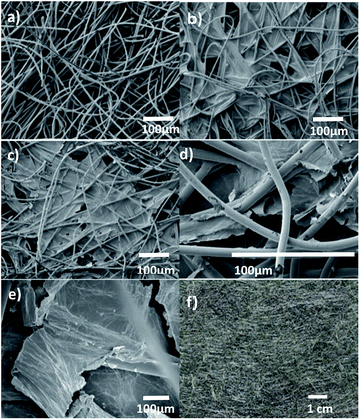 |
| Fig. 5 SEM images of (a) raw nonwoven textile, (b) LCGO coated nonwoven textile, (c) rGO sample, (d) rGO in the interstices of fibres, and (e) rGO layers; (f) photograph of the as-prepared conducting graphene nonwoven textile. | |
Optical microscope images of raw nonwoven and rGO samples after the 1st, 2nd, 3rd and 6th coating cycles are presented in Fig. 6(a–f). As can be seen in the optical images, after the 3rd coating cycle, most of the interstices in the nonwoven textile are covered by the GO. Therefore, it can be mentioned that more GO layers are deposited on the surface of the textile, forming thicker GO layers after the 3rd coating cycle, which has less interaction with the fibres in the nonwoven textile, as seen in Fig. 6(e).
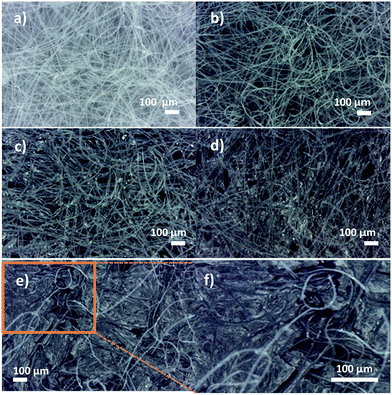 |
| Fig. 6 Optical microscope images of the samples: (a) raw nonwoven and as-prepared nonwoven reduced graphene oxide after the (b) 1st, (c) 2nd, (d) 3rd and (e) 6th coating cycles; (f) at higher magnification. | |
Electrical properties
The surface resistivities of the samples were calculated to analyse the relationship of the electrical resistivity to the number of coating cycles. The surface resistivities of the rGO samples and the percentage weight of GO added to the nonwoven textile are presented in Fig. 7 as a function of the number of coating cycles. It was found that the lowest surface resistivity, which is 330 Ω □−1, was reported after the 3rd coating cycle in LCGO 0.6% wt. The rGO categories exhibited enhanced electrical conductivity values with increasing GO addition up to the 3rd coating cycle; from the 4th coating cycle, the samples exhibited nonlinear behaviour in surface resistance with increasing amount of GO added to the fabric. The possible major factor contributing to the high resistivity after the first coating cycle even with a higher concentration of LCGO is the disconnections within the fibre matrix, which reduce the number of conductive pathways. The increasing number of dip coating cycles after the 3rd coating and the subsequent reduction under identical conditions did not result in any further improvement in the surface resistance. As a result, increased GO deposition on the surface of the nonwoven fabric caused less interaction of LCGO with the polyester fibres. During the reduction process, less interaction occurred and the unstable rGO layers delaminated from the sample so that a small amount of reduced GO remained in the nonwoven textile. Further, the thick rGO layers with less bonding to the fibres have a high chance of separating from the sample. Therefore, the addition of further GO to the nonwoven textile did not contribute to a decrease in the electrical resistivity, due to the instability of the rGO layers within the fibre matrix. The value of maximum conductivity reported in this study is a 150 fold enhancement of the surface conductivity of the rGO deposited nonwoven polyester reported in the literature.23
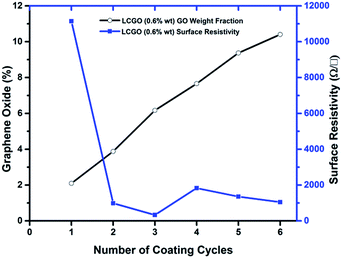 |
| Fig. 7 Surface resistivity and % addition of GO as a function of the number of coating cycles of LCGO (0.6% wt). | |
The optimum conditions for the as-prepared nonwoven textiles are 6% and 4% GO addition to the textile with LCGO concentrations of 0.6% wt and 0.25% wt, respectively. To evaluate the durability of the as-prepared samples, the bending-electrical resistance performance of the rGO nonwoven textiles was measured. The resistance change during fifty bending cycles was monitored for groups of samples in order to understand the material behaviour during and after bending. The changes in the electrical resistance as a fraction of the initial resistance (ΔR/R0) for the rGO samples are shown in Fig. 8. The conducting nonwoven samples were subjected to repeated bending-relaxation to 90° up to 50 cycles. These samples suffered 1.14% maximum change in average ΔR/R0 when bent to 90°. In addition, all the samples exhibited a stable resistance change during bending for 50 consecutive cycles.
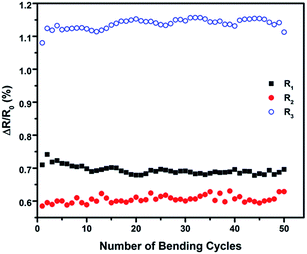 |
| Fig. 8 The average normalised resistance change of rGO-0.6 wt% specimens during fifty bending cycles. The resistivity values R1, R2, and R3 are for the rGO nonwoven textiles after the 1st, 2nd and 3rd coatings, respectively. | |
Thermal behaviour
The thermal behaviour of the fabric was analysed in order to confirm the capability of the material in heating applications. A sample of fabric measuring 200 mm × 200 mm with 6 wt% of GO was heated to an average temperature of 36 °C with 32.5 V and 0.05 A within 10 min. The thermal behaviour of the sample exhibited comparable heating capacity to a textile heating element published in the literature with 44.3% wt addition of polyethylenedioxythiophene/p-toluene sulfonic acid.1
Abrasion resistance
The abrasion resistance of textile materials is a very complex phenomenon that is affected by many factors, mainly classified as fibre, yarn, and fabric properties and finishing processes. Some of these parameters affect the fabric surface, whereas some have an influence on the internal structure of the fabrics. For example, fibre characteristics such as composite ratio and fineness play a significant role in surface abrasion, while yarn and fabric characteristics such as yarn linear density and interlacing coefficient are significantly related to structural abrasion. The mechanical properties and dimensions of the fibres are important for abrasion. Fibre type, fibre fineness and fibre length are the main parameters that affect abrasion. The abrasion resistance of the nonwoven sample was evaluated in multi directions by rotating the nonwoven sample against a fixed load, abrading with a geo-membrane. The electrical resistance was increased by 20% after 6000 abrading cycles. The percentage increment of the electrical resistance is well bellow the 200% change in the electrical resistance mentioned in the literature, where the resistance changed from 10 Ω □−1 to 30 Ω □−1 after 10
000 cycles.1
Conclusion
The above analysis justifies the successful combination of polyester nonwoven textile with graphene oxide from a simple dip coating technique. The surface electrical resistivity of 330 Ω □−1 and self-heating to 36 °C within 10 minutes can be considered to be well suited to many industrial applications. The average resistance changed minimally during bending. The abrasion resistance test with 20% electrical resistance change after 6000 abrading cycles further confirms the usability of the conductive nonwoven textile in industrial applications. Furthermore, by considering the morphological observations, it can be mentioned that nonwoven polyester is the most appropriate material to be used in conductive coating processes, especially when dealing with hydrophobic fibres, as most of the GO layers are encapsulated between intestinal regions of the textile. Polyester fibres are inherently resistant to climatic changes, and nonwoven polyester has already been used in geo-textile applications. The prepared textile can be used as an EKG material in leakage detection surveys, due to its excellent electrical conductive properties in comparison with the EKG materials discussed in the introduction. In addition, due to its heating properties, this textile can be used as a heating component for both industrial and residential applications such as floor carpets and car seats and can be further improved for de-icing of aircraft driveways. The LCGO coated nonwoven material can be proposed as a superlative manufacture-feasible, flexible, corrosion-free and lightweight material which will open up new avenues in conductive textiles.
Acknowledgements
The authors thank the ARC under Discovery Early Career Researcher Award (J. Foroughi DE12010517). The authors also thank AIIM for Gold funding and the ANFF Materials Node for their provision of research facilities; they also acknowledge the use of facilities within UOW Electron Microscopy.
References
- K. Opwis, D. Knittel and J. S. Gutmann, Oxidative in situ deposition of conductive PEDOT: PTSA on textile substrates and their application as textile heating element, Synth. Met., 2012, 162(21–22), 1912–1918 CrossRef CAS.
- A. Ben Othmen, Detecting defects in geomembranes of landfill liner systems: durable electrical method, Int. J. Geotech. Eng., 2013, 7(2), 130–135 CrossRef.
- R. B. Hamir, Electrically conductive geosynthetics for consolidation and reinforced soil, Geotextiles and Geomembranes, 2001, 19(8), 455–482 CrossRef.
- A. B. Fourie, Improved estimates of power consumption during dewatering of mine tailings using electrokinetic geosynthetics (EKGs), Geotextiles and Geomembranes, 2010, 28(2), 181–190 CrossRef.
- X. Jin, et al., Preparation and properties of a new coating method for preparing conductive polyester fibers with permanent conductivity, J. Appl. Polym. Sci., 2006, 102(3), 2685–2691 CrossRef CAS.
- R. Fryczkowski, Polyester Fibres Finished with Polyaniline, Fibres, 2005, 13(5), 141–143 CAS.
- A. Harlin, et al., Development of polyester and polyamide conductive fibre, J. Mater. Sci., 2005, 40(20), 5365–5371 CrossRef CAS.
- E. Romero, et al., Synthesis of PPy/PW12O403− organic–inorganic hybrid material on polyester yarns and subsequent weaving to obtain conductive fabrics, Text. Res. J., 2011, 81(14), 1427–1437 CrossRef CAS.
- K. K. Gupta, S. M. Abbas and A. C. Abhyankar, Ultra-lightweight hybrid woven fabric containing stainless steel/polyester composite yarn for total EMI shielding in frequency range 8–18 GHz, J. Electromagn. Waves Appl., 2015, 29(11), 1454–1472 CrossRef.
- R. Perumalraj and K. S. Narayanan, Nano silver conductive composite material for electromagnetic compatibility, J. Reinf. Plast. Compos., 2014, 33(11), 1000–1016 CrossRef CAS.
- U. Khan, High strength composite fibres from polyester filled with nanotubes and graphene, J. Mater. Chem., 2012, 22(25), 12907–12914 RSC.
- K. Liu, Preparation of polyester/reduced graphene oxide composites via in situ melt polycondensation and simultaneous thermo-reduction of graphene oxide, J. Mater. Chem., 2011, 21(24), 8612–8617 RSC.
- H. W. Cui, K. Suganuma and H. Uchida, Highly stretchable, electrically conductive textiles fabricated from silver nanowires and cupro fabrics using a simple dipping–drying method, Nano Res., 2015, 8(5), 1604–1614 CrossRef CAS.
- A. Mirabedini, J. Foroughi and G. G. Wallace, Developments in conducting polymer fibres: from established spinning methods toward advanced applications, RSC Adv., 2016, 6(50), 44687–44716 RSC.
- V. Janickis and I. Ancutienė, Modification of polyester textile by conductive copper sulfide layers, Poliesterinio Audinio Modifikavimas Elektrai Laidžiais Vario Sulfidų Sluoksniais, 2009, 20(2), 136–140 CAS.
- T. Bashir, et al., Stretch sensing properties of conductive knitted structures of PEDOT-coated viscose and polyester yarns, Text. Res. J., 2014, 84(3), 323–334 CrossRef CAS.
- S. Maity, et al., Polypyrrole based electro-conductive textiles for heat generation, J. Text. Inst., 2014, 105(8), 887–893 CrossRef CAS.
- T. Lin, et al., Polymerising pyrrole on polyester textiles and controlling the conductivity through coating thickness, Thin Solid Films, 2005, 479(1–2), 77–82 CrossRef CAS.
- B. Zhang, et al., Study on property of PANI/PET composite conductive fabric, J. Text. Inst., 2014, 106(3), 253–259 CrossRef.
- J. Molina, et al., Conducting fabrics of polyester coated with polypyrrole and doped with graphene oxide, Synth. Met., 2015, 204, 110–121 CrossRef CAS.
- C. Y. Lee, et al., Conductivity and EMI shielding efficiency of polypyrrole and metal compounds coated on (non) woven fabrics, Synth. Met., 2001, 119(1–3), 429–430 CrossRef CAS.
- P. Tang, et al., Synergetic effects of carbon nanotubes and carbon fibers on electrical and self-heating properties of high-density polyethylene composites, J. Mater. Sci., 2015, 50(4), 1565–1574 CrossRef CAS.
- X. Liu, et al., Fabricating conductive poly(ethylene terephthalate) nonwoven fabrics using an aqueous dispersion of reduced graphene oxide as a sheet dyestuff, RSC Adv., 2014, 4(45), 23869–23875 RSC.
- C. Croitoru, C. Croitoru, S. Patachia, A. Papancea, L. Baltes and M. Tierean, Glass fibres reinforced polyester composites degradation monitoring by surface analysis, Appl. Surf. Sci., 2015, 358, 518–524 CrossRef CAS.
- W. Liu, et al., Oxygen plasma treatment of bamboo fibers (BF) and its effects on the static and dynamic mechanical properties of BF-unsaturated polyester composites, Holzforschung, 2015, 69(4), 449–455 CrossRef CAS.
- N. M. Abdullah and I. Ahmad, Potential of using polyester reinforced coconut fiber composites derived from recycling polyethylene terephthalate (PET) waste, Fibers Polym., 2013, 14(4), 584–590 CrossRef CAS.
- M. Goto, M. Matsuki and S. Nishimura, US Pat., US3802817 A, Apparatus for producing non-woven fleeces, 1974.
- L. Hartmann., Process of producing non-woven fabric fleece, US Pat., 3502763, 1970.
- M. Ring, M. P. Godsay, R. S. Swenson and J. N. Kent, Method for forming wet-laid non-woven webs, US Pat., 4007083, 1977.
- R. Butin, J. Harding and J. Keller, Non-woven mats by melt blowing, US Pat., 3849241, 1974.
- P. E. Stevenson and J. King, Non-woven needle-punched filter fabric, US Pat., 5877096, 1999.
- G. K. Buerger, et al., Nonwoven composite material and method for making same, 1997, available from: https://www.google.com/patents/US5652041.
- A. T. Purdy, Developments in non-woven fabrics, Text. Prog., 1983, 12(4), 1–86 CrossRef.
- R. K. Dharmadhikary, et al., Thermal bonding of nonwoven fabrics, Text. Prog., 1995, 26(2), 1–37 CrossRef.
- K. Thangadurai, G. Thilagavathi and A. Bhattacharyya, Characterization of needle-punched nonwoven fabrics for industrial air filter application, J. Text. Inst., 2014, 105(12), 1319–1326 CrossRef CAS.
- S. I. Abou-Elela, et al., Application of Nanometal Oxides in situ in Nonwoven Polyester Fabric for the Removal of Bacterial Indicators of Pollution from Wastewater, Sci. World J., 2014, 2014, 950348 Search PubMed.
- A. Bouazza, A simple method to assess the wettability of nonwoven geotextiles, Geotextiles and Geomembranes, 2014, 42(4), 417–419 CrossRef.
- S. Debnath and M. Madhusoothanan, Thermal insulation, compression and air permeability of polyester needle-punched nonwoven, Indian J. Fibre Text. Res., 2010, 35, 38–44 CAS.
- R. F. Tietz, Novel polyesters and their use in compostable products such as disposable diapers, US Pat., 5171308, 1991.
- M. K. Iqbal, The applications of nonwovens in technical textiles, PTJ, December, 2009 Search PubMed.
- J. H. Warner, et al., Chapter 6-Applications of Graphene, in Graphene, ed. J. H. W. S. B. H. Rümmeli, Elsevier, 2013, pp. 333–437 Search PubMed.
- V. Georgakilas, Functionalization of graphene, Wiley-VCH, Weinheim an der Bergstrasse, Germany, 2014 Search PubMed.
- Y. Zhong, D. L. Nika and A. A. Balandin, Thermal properties of graphene and few-layer graphene: applications in electronics, IET Circuits, Devices and Systems, 2015, 9(1), 4–12 CrossRef.
- G. Khurana, P. Misra and R. S. Katiyar, Forming free resistive switching in graphene oxide thin film for thermally stable nonvolatile memory applications, J. Appl. Phys., 2013, 114(12), 124508 CrossRef.
- P. Ray, S. Pandey and V. R. Rao, Development of graphene nanoplatelet embedded polymer microcanti lever for vapour phase explosive detection applications, J. Appl. Phys., 2014, 116(12), 1–5 CrossRef.
- J. Foroughi, D. Antiohos and G. G. Wallace, Effect of post-spinning on the electrical and electrochemical properties of wet spun graphene fibre, RSC Adv., 2016, 6(52), 46427–46432 RSC.
- R. Jalili, Organic solvent-based graphene oxide liquid crystals: A facile route toward the next generation of self-assembled layer-by-layer multifunctional 3D architectures, 2013 Search PubMed.
- L. Dan, et al., Processable aqueous dispersions of graphene nanosheets, Nat. Nanotechnol., 2008, 3(2), 101–105 CrossRef PubMed.
- S. Gambhir, et al., Chemically converted graphene: scalable chemistries to enable processing and fabrication, NPG Asia Mater., 2015, 7(6), e186 CrossRef CAS.
- S. Gambhir, et al., Anhydrous organic dispersions of highly reduced chemically converted graphene, Carbon, 2014, 76, 368–377 CrossRef CAS.
- M. Bastiurea, et al., Thermal and mechanical properties of polyester composites with graphene oxide and graphite, Digest Journal of Nanomaterials and Biostructures, 2015, 10(2), 521–533 Search PubMed.
|
This journal is © The Royal Society of Chemistry 2016 |
Click here to see how this site uses Cookies. View our privacy policy here.