DOI:
10.1039/C6RA14342C
(Paper)
RSC Adv., 2016,
6, 77636-77643
Fast response ammonia sensors based on TiO2 and NiO nanostructured bilayer thin films†
Received
2nd June 2016
, Accepted 9th August 2016
First published on 9th August 2016
Abstract
In the present work, we have synthesized TiO2 and NiO based bilayer nanostructured thin films on glass substrates via DC magnetron sputtering at room temperature. The structural and morphological properties of the bilayer samples were systematically studied using numerous analytical techniques, including X-ray diffraction (XRD), Raman spectroscopy, atomic force microscopy (AFM), field-emission scanning electron microscopy (FESEM) and transmission electron microscopy (TEM). The ammonia (NH3) gas sensing properties of both bilayer sensors towards a low detection range (5–500 ppm) within a low operating temperature regime (30–300 °C) have been extensively discussed in detail. The TiO2/NiO and NiO/TiO2 sensors exhibited high sensing responses (Rg/Ra ∼ 7.6) and (Ra/Rg ∼ 5.0) with very fast response times (∼24 s) and (∼30 s) towards 100 ppm NH3 at 280 °C and 200 °C, respectively. Furthermore, the working principle attributed behind their good gas sensing properties was also investigated via formation of p–n and n–p heterojunctions at the interface.
1 Introduction
With an increasing demand for environmental monitoring, chemical and process control industries have attracted the great attention of researchers towards the monitoring of highly toxic species (e.g. NH3, CO2, CO, NOx, and H2S) in our environment.1–3 Among all the pollutants, ammonia is a common reagent and colorless toxic ingredient with a pungent odour. Recently, numerous efforts have been carried out to assess the ammonia (NH3) released in human breath and to measure its importance as a potential disease biomarker for physical disorders like renal insufficiency, hepatic dysfunction or halitosis.4,5 Ammonia can be produced in our environment through animal manure, agricultural sources, industrial refrigeration, refining, nitrogenous fertilizers and automobile emissions.6–8 Human beings can detect ammonia only if its concentration exceeds 50 ppm in our environment.9 However, when the ammonia concentration exceeds the exposure limit of 25 ppm in air for a period of 8 h and 35 ppm for a period of even 15 minutes, it causes serious human health threats such as irritation to the eyes, skin, lungs and respiratory system.10 Over the past few decades, a huge number of materials have been widely investigated as promising sensing materials to this end. Therefore, for human demand, tremendous efforts have been concerned toward the development of an inexpensive, reliable, extremely sensitive and selective gas sensor devices to detect the ammonia under ambient conditions even at very low (ppm) concentration levels in the environment.11 Among various types of gas sensors, transition metal oxides (TMOs) based thin film chemiresistive gas sensors offer low cost, high sensitivity and selectivity, environmental benignity and portable device configurations for long range of operations.12–15 The sensing mechanism for chemiresistive gas sensors predominantly depends on the change in the electrical resistance of material with effective diffusion and strong adsorption during exposure to analyte gas molecules at the surface of nanostructured materials.16–19
Among all the TMOs, TiO2 and NiO nanostructured materials have been increasingly recognized as promising materials for ammonia gas sensors due to their high chemical stability and low cost. Unfortunately, gas sensors based on TiO2 and NiO nanostructured thin films generally work at a high temperature regime (≥350 °C) due to high activation energy of reaction with target gas molecules. The high operating temperature is unfavorable for the purpose of power saving and device integration. Thereafter, improving the sensitivity towards ammonia at relatively low temperature regime has become a great challenge for the researchers. Moreover, excellent attempts have been employed to reduce the operating temperatures for TiO2 and NiO thin film based sensors and enhancing the sensor response characteristics by improving the adsorption and desorption rate of analyte gas molecules via formation of p–n heterojunction at the interface. Thus, the existence of opposite type of semi-conductive material with the parent material is more likely to facilitate the formation of the p–n junction which have been significantly attributed to enhance the sensing properties for detecting the trace amount of analyte gas at relatively low operating temperatures.20,21 Therefore, p–n or n–p type bilayer nanostructured thin films demonstrated as the encouraging sensing material for metal oxide based gas sensors.22,23 Based on these investigations, nanostructured TiO2/NiO and NiO/TiO2 bilayer thin film sensors have been established with outstanding capability for the detection of low ammonia concentration (ppm level) at relatively lower operating temperatures compared to their single layer counterpart.24
Although many fabrication techniques such as electron beam evaporation, electro-spinning, atomic layer deposition, dip-coating, sol gel, hydrothermal, chemical vapour deposition and physical vapour deposition have been employed to fabricate the different p–n heterojunction sensors.12,25–28 Meanwhile, sputtering technique have been employed as an effective and straightforward way to fabricate high phase purity, particle homogeneity, excellent reproducibility and contamination free heterojunction thin films which provide large surface area to volume ratio.
In the present work, we have synthesized the TiO2/NiO and NiO/TiO2 bilayer thin films on glass substrates by DC magnetron sputtering at room temperature. There microstructure, morphological and ammonia gas sensing properties under low detection limit (5–500 ppm) were investigated in detail. Furthermore, we have also studied the variation in sensing response under humidity conditions. The sensitivity, selectivity and reproducibility during sensing mechanism were also discussed.
2 Experimental details
2.1 Materials and chemicals
Titanium and nickel targets (2′′ dia.) with 99.99% purity were purchased from Testbourne Ltd. UK. Argon, oxygen, synthetic air and ammonia gas cylinders were purchased from Sigma Gasses, India.
2.2 Fabrication of sensor
The nanostructured bilayer sensors were fabricated on glass substrate using Ti and Ni targets by DC magnetron sputtering at room temperature. Initially, we have fixed the bottom NiO film layer to 200 nm and varying the top TiO2 film layer thickness from 160 to 580 nm. During the sensing measurements, we have found that TiO2/NiO sensor with 400 nm TiO2 layer (at top) and 200 nm NiO layer (at bottom) exhibited the best sensing response towards ammonia at 280 °C (ESI Fig. S4†). Thereafter, the sequence was altered and 200 nm NiO thin film was deposited on the top of the 400 nm TiO2 thin film. The key difference between the bilayers is in the sequence of the top two functional layers. Here we found that the NiO/TiO2 sensor also shows the reasonable good sensing response towards 100 ppm ammonia relatively at low temperature 200 °C. Therefore, in the present work the optimized TiO2 (400 nm)/NiO (200 nm) and NiO (200 nm)/TiO2 (400 nm) nanostructured bilayer sensors were investigated in detailed. During each deposition, glass substrates were cleaned by rinsing in an ultrasonic bath of acetone and ethanol for 15 min each and washed in DI water. Thereafter, evaporate on the hot plate at 100 °C for 10 minutes and kept in sputtering chamber at a distance of 6 cm from sputtering source. For electrical measurements, the bottom contact layer and top dots of platinum (Pt) of 25 nm thickness were deposited using metal shadow mask on glass substrates via DC sputtering technique. The diameter of Pt dot is 0.5 mm and space between the two dots is 2 mm, approximately. Prior to the deposition, the sputtering chamber was evacuated to high vacuum (∼2.5 × 10−6 Torr) by turbo molecular pump backed by rotary pump. The working pressure of chamber was kept constant at 10 mTorr by constant flow of Ar
:
O2 (40
:
10) using mass flow controller (MKS). Thereafter, the bilayer thin films were directly deposited on glass substrates by sputtering the Ti and Ni targets sequentially at room temperature for a period of 60 min and 10 min by applying sputtering power of 80 W and 50 W, respectively.
2.3 Characterization
The XRD patterns of as deposited TiO2/NiO and NiO/TiO2 bilayer thin films were characterized using X-ray diffractometer (Bruker AXS, D8 advance) with CuKα radiation (λ = 1.5418 Å). For phase identification the SAED pattern of TiO2/NiO bilayer thin film was investigated by using TEM (FEI, TECNAI G2). The surface microstructures and cross section of bilayers were investigated using FE-SEM (Carl ZEISS, Ultra-Plus). The elemental composition analysis and mapping of these films were carried out using an energy dispersive spectroscopy analysis (EDS, Oxford Instruments). The surface morphologies and root mean square (rms) surface roughness of as deposited samples were analysed using AFM (NT-MDT, Ntegra). The Raman spectra of the bilayers were recorded via Raman spectrophotometer (Renishaw, UK) using 514 nm laser as an excitation wavelength. The gas sensing characteristics of bilayers were measured in situ with the help of two-probe technique using a nanovoltmeter (Keithley 2182 A) and source meter (Keithley 2400). Here we used the custom designed sensing chamber with the volume of 300 cm3 equipped with PID controlled electric heater. Prior to sensing measurements, mechanical rotary vacuum pump was used to create necessary vacuum (4 × 10−2 Torr) inside the sensing chamber. Thereafter, the mixed ratio of ammonia and synthetic air with controlled flow rate of 50 cm3 min−1 was introduced into the sensing chamber using mass flow controller (MKS, USA). Sensor response (Ra/Rg) for TiO2/NiO bilayer is defined as the ratio of electrical resistances in air (Ra) to that of target gases (Rg), and sensor response (Rg/Ra) for NiO/TiO2 bilayer is defined as the ratio of electrical resistances in target gases (Rg) to that of air (Ra). Response and recovery times were defined as the time required to reach the signal up to 90% of the total steady change in resistance during adsorption and the desorption process, respectively.29 The ammonia sensing measurements were repeated four times for both the bilayer sensors and a variation of 3% was detected. The particulars of the gas sensing setup are described elsewhere.12
3 Results and discussion
3.1 Structural properties
Fig. 1a depicts the XRD patterns of TiO2/NiO and NiO/TiO2 bilayer sensing film consists of tetragonal phase of TiO2 corresponding to (101), (200), (211) and (200) planes at 25.34°, 48.10°, 55.12°, and 70.50° (JCPDS ICDD no. 00-002-0387) along with rhombohedral phase of NiTiO3 corresponding to (221) and (231) planes at 38.60° and 54.06° (JCPDS no. 01-077-0152). Both bilayer sensing films also consists of cubic phase of NiO corresponding to (111), (200), (220), (311) and (222) planes at 37.26°, 43.22°, 62.72°, 75.25° and 79.17° (JCPDS ICDD no. 01-071-1179). The average crystallite size of TiO2 and NiO was found to be 20 nm and 25 nm, respectively. In addition, Fig. 1b depicts the Raman spectra of both bilayer thin films. The Raman peaks located at 144, 514 and 637 cm−1 correspond to the anatase phase of TiO2. The strong peaks observed at 144, and 634 cm−1 assigned to Raman active Eg mode caused by symmetric stretching vibrations of O–Ti–O. The band appeared at 514 cm−1 corroborated to Raman active A1g mode with symmetric bending vibration of O–Ti–O.30 Moreover, for both bilayer samples, the broad peak observed at 401 cm−1 assigned to first order vibrational transverse optical phonon mode corresponds to cubic NiO.31
 |
| Fig. 1 (a) XRD patterns, and (b) Raman spectra of TiO2/NiO and NiO/TiO2 bilayers. | |
3.2 Surface morphology
Fig. 2a–d depicts the FE-SEM microstructure and their corresponding cross-sectional micrographs of TiO2/NiO and NiO/TiO2 bilayer sensing films. Here, the uniformly distributed nano-crystallites of as-deposited thin films indicate the presence of significantly compact and dense packed structures. The thickness of TiO2 and NiO thin films were found to be nearly 400 nm and 200 nm respectively. As shown in Fig. 3a, b and S3,† the elemental mapping and EDS spectrum of both bilayers indicate the uniform element distribution of titanium, oxygen and nickel elements. The red region of O, green region of Ti and yellow regions of Ni are typically overlapped. Fig. 4a and b depicts the SAED pattern and HR-TEM images of the TiO2/NiO heterostructure, respectively. The SAED pattern demonstrated the (101), (200) and (211) planes correspond to anatase phase of TiO2 and (111), (200), (220) and (311) planes correspond to cubic phase of NiO. The HR-TEM image clearly reveals the coexistence of the nanocrystalline TiO2 and NiO crystal lattice in the TiO2/NiO bilayer thin film. The interplanar spacing of 0.352 nm and 0.189 nm are very close to the lattice spacing of the (101) and the (200) planes of the anatase TiO2. Furthermore, the interplanar distance of 0.242 nm is in a good agreement with the lattice spacing of the (111) planes of the cubic NiO. Therefore, we can conclude that the SAED pattern and HRTEM observations are consistent with the XRD results.
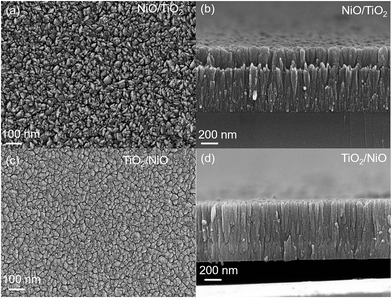 |
| Fig. 2 (a) FE-SEM image, and (b) cross-section image of NiO/TiO2 bilayer thin film. (c) FE-SEM image, and (d) cross-section image of TiO2/NiO bilayer thin film. | |
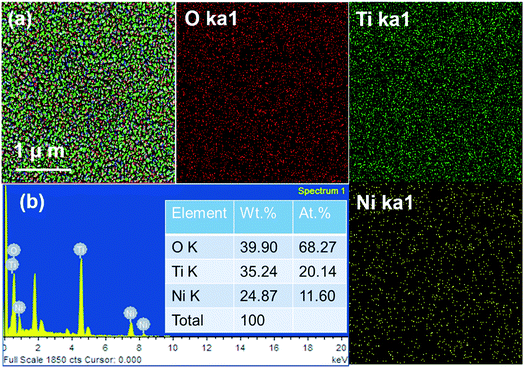 |
| Fig. 3 (a) Elemental mapping, and (b) EDS spectra of TiO2/NiO bilayer thin film. | |
 |
| Fig. 4 (a) HR-TEM image, and (b) SAED pattern of TiO2/NiO bilayer thin film. | |
Fig. 5a and b shows the 2D AFM micrographs of as deposited nanostructured bilayer thin films. The AFM topography reveals the rough, homogeneous and compact surface of both investigated bilayer thin films. From the figures, we can also observed that the film surface with nanocrystalline nature is composed of dense nano grains. As shown in Fig. 5a, the rms surface roughness was found to be 7 nm for TiO2 at top, which is greater than the rms value of 4 nm for NiO at top (Fig. 5b). These nano-level grains could enhanced the surface-to-volume ratio of the bilayer thin films and improved the adsorption of target gas molecules on the surface.
 |
| Fig. 5 2-D AFM images of (a) NiO/TiO2, and (b) TiO2/NiO bilayer thin films. | |
3.3 Sensing performance
The sensing characteristics behaviour of the resistive type gas sensors is based on the change in the electric resistance upon exposure to the analyte gas species on the oxide surface/interface. To further explore the resistive characteristics of the bilayer coatings, we have measured I–V plots of both bilayer thin films (Fig. 6a). The results show the rectifying behaviour of the samples. The resistance variation usually depends on the working temperature and target gas concentration exposed to the sensing materials.23,32 Therefore, parallel sensing measurements were carried out in the range of 30–320 °C to optimize the working temperature for fabricated bilayer sensors. Fig. 6b depicts the sensing response as a function of temperature for TiO2/NiO and NiO/TiO2 bilayer thin films gas sensors exposed to 100 ppm NH3 in dry air. The results indicate that the bilayer gas sensors exhibit noticeable increase in response with rising the temperature up to optimum value. Thereafter, the sensing response of TiO2/NiO and NiO/TiO2 bilayer sensors regularly decreases as the temperature further increases. At low temperature, slow chemical activation between film surface and adsorbed gas molecules reveals the lower sensing response but at too high operating temperature the improvement of desorption rate reduces the quantity of the adsorbed gas molecules and these molecules may escape from the oxide surface before reactions take place, resulting in decreased sensing response.33–35 The TiO2/NiO and NiO/TiO2 bilayer thin film sensors exhibit maximum response value of 7.6 and 5.0 towards 100 ppm NH3 at optimum temperature of 280 °C and 200 °C, respectively. There are two proposed phenomena which can justify the sensing performance of bilayer sensors. According to the Kosc et al. 2014,36 the difference between the sensing performances of bilayer sensors could be attributed to the amount of NiOx content present in the surface and near subsurface area. Furthermore Sakai et al. 2001,35 proposed that the sensitivity may be depends on the reactivity and diffusion of the target gas molecules with the particular sensing layer. The effect of film thickness on sensing response was observed with the parallel investigation. During the sensing measurements, we found that the sensor response increases as the TiO2 layer thickness increases from 160 nm to 400 nm but it decreases when the TiO2 thickness further increases to 580 nm (ESI Fig. S4†). The decrease in sensor response with increasing film thickness may be due to the microstructural defects exist in the sensing bilayer thin film.37,38 On the other hand, the sensing response of the gas sensors could co-relate with the diffusivity of reactive gas molecules present inside the sensing layer. Therefore, high thickness of the thin film results in a decrease in the sensing response due to the increase of the diffusion length of gas molecules.35
 |
| Fig. 6 (a) I–V characteristics at 280 and 200 °C for TiO2/NiO and NiO/TiO2 bilayer thin films in air, respectively. (b) Response vs. temperature curve at 280 and 200 °C in 100 ppm NH3 for TiO2/NiO and NiO/TiO2 bilayer thin films, respectively. (c) Response vs. concentration curve at 280 and 200 °C for TiO2/NiO and NiO/TiO2 bilayer thin films, respectively. (d) Response and recovery time vs. concentration curve at 280 °C for TiO2/NiO bilayer sensor. (e) Response and recovery time vs. concentration curve at 200 °C for NiO/TiO2 bilayer sensor. | |
Fig. 6c shows the response curves of TiO2/NiO and NiO/TiO2 bilayer gas sensors exposed to different ammonia concentration in the range of 5–500 ppm at optimized temperature of 280 °C and 200 °C, respectively. These results demonstrated that the TiO2/NiO and NiO/TiO2 bilayer gas sensors are able to detect the ammonia concentration down to 5 ppm and exhibits improved response in the wide detection range (5–500 ppm) for ammonia. This may be due to uniformly distributed grains with the large surface to volume ratio of the nanostructured bilayer thin films. The formation of heterostructures between the two dissimilar n-type and p-type materials play a vital role in remarkable improvement of the sensing response for bilayer sensors. Therefore, the main cause of high response of bilayer sensors towards NH3 at relatively low temperature is due to increase in the number of charge carriers in depletion region at the heterojunction.39,40 Fig. 6d and e shows the response and recovery time characteristics for TiO2/NiO and NiO/TiO2 bilayer sensors at different NH3 gas concentrations, respectively. A very fast response time within 24 and 30 s was achieved with the recovery time of 45 and 52 s at 100 ppm of NH3 at 280 °C and 200 °C for both TiO2/NiO and NiO/TiO2 bilayer sensors, respectively. For both bilayer systems the selectivity of ammonia gas with respect to other potentially hazardous gases such as CO and ethanol (C2H5OH) at 100 ppm level was studied (Fig. 7a). The TiO2/NiO and NiO/TiO2 bilayer sensor exhibited high ammonia response (Ra/Rg ∼ 7.6 ± 0.3) and (Ra/Rg ∼ 5.0 ± 0.3), with respect to weak response (Ra/Rg < 3.2 ± 0.2) towards the other gases at 100 ppm level, confirming the high ammonia selectivity for this sensor. However, the long term stability of the sensor response is also an important requirement for developing the stable performance for several months. We carried out the stability characteristics of TiO2/NiO and NiO/TiO2 bilayer sensors accomplished at 280 °C and 200 °C towards 100 ppm NH3 concentration for 90 days (ESI Fig. S5†). During the measurements, the TiO2/NiO and NiO/TiO2 bilayer sensors exhibits nearly constant response signal (∼10% changes) and (∼12% changes) respectively, indicating the significant long term stability of the sensor. Therefore, we concluded that the above-mentioned stability test will contributes to establish both the bilayer sensors as potential candidate for NH3 gas sensing application. Thereafter, at low temperature, relative humidity (RH) is one of the important factor which affect the sensing characteristics. The sensing response of both the bilayer thin films at different humidity conditions (0–60%) towards 100 ppm ammonia in air were investigated (Fig. 7b). The change in the sensor response for TiO2/NiO and NiO/TiO2 bilayer sensors under the high humidity (60% RH) conditions was observed to be around 12% and 5%, respectively. The improved response is mostly recognized to the water molecules present in humid air, which react as reducing agent for bilayer films.33,41 This trend was also observed due to chemisorption of water molecules on the oxygen vacancy sites and hence charge conduction follows the hopping mechanism.42
 |
| Fig. 7 (a) Cross sensitivity curve at 100 ppm of various gases, and (b) response vs. humidity curve at 100 ppm of NH3 for TiO2/NiO and NiO/TiO2 bilayer thin films. | |
3.4 Sensing mechanism
The reaction mechanism for TiO2/NiO and NiO/TiO2 bilayer sensors is different than the single layer sensor due to the formation of n–p and p–n heterojunctions. For bilayer sensors when n-TiO2 and p-NiO semiconducting materials have an electrical connection, the electrons transfer across the interface will takes place from higher energy states to unoccupied lower-energy states until the Fermi levels have equilibrated. Thus, the electron–hole recombination leads to the formation of depletion region at the p–n junction interface. Furthermore, a potential energy barrier develops at the junction interface due to the band bending caused by the difference in Fermi levels of the materials.43 At n–p heterostructure interface the depletion region extended towards n-TiO2 layer, as a result decreasing the width for charge conduction channel which leads to enhance the initial resistance.11 Hence, the observed enhancement of sensing response for TiO2/NiO towards NH3 gas could be attributed to the formation of n–p junction between n-type TiO2 and p-type NiO nanostructure materials.
Furthermore, at the n–p heterojunction the two contributing mechanisms are explained as follows: when the TiO2/NiO heterojunction sensor is exposed to ammonia gas, the adsorbed oxygen ions (O−, O2−) react with ammonia gas molecules and release the electrons back to TiO2/NiO bilayer causes a decrease in hole concentration in valance band of NiO and increasing electron concentration in conduction band of TiO2, as a result overall decrease in sensor resistance.44 Hence both the factors contribute to large decrease in sensor resistance causes to enhance the sensing response. During recovery process, in absence of NH3 gas the electron concentration reduces which results to recover the original resistance of the sensor.32 When NiO/TiO2 heterojunction sensor is exposed to ammonia, the adsorbed negatively charged oxygen species interact with the target gas molecules and then transfer the electrons back to NiO/TiO2 bilayer. As a consequence, increases the electron concentration in valance band of TiO2 and reducing the hole concentration in conduction band of NiO, causes the thickness of hole-accumulation layer reduced and thus the sensor resistance enhanced (and hence the overall sensor resistance enhanced).29
When the bilayer sensor is exposed to humid air then two promising mechanisms may occur. Firstly, the water molecules in hydroxyl or molecular form may adsorbed on the film surface and provide the electrons to the sensor surface. Secondly, water molecules may exchange with the formerly adsorbed oxygen ions and then release the electrons from the ionized oxygen atoms.45 Both mechanisms contribute to enhance the electron concentration, leading to change the electrical resistance of bilayer sensors. Therefore, the intimate contact between TiO2 and NiO will contribute to the remarkable improvement in the sensor performance. Furthermore, the formation of n–p and p–n heterojunctions can be attributed for fast response, good selectivity, stability, reproducibility and low operating temperature which make these sensors as promising potential candidate compared to the bare TiO2 and NiO sensors reported in the literature.
4 Conclusion
In summary, we have successfully synthesized a highly sensitive and selective TiO2/NiO and NiO/TiO2 bilayer thin film sensors by DC magnetron sputtering for detecting trace amount of NH3 gas. For 100 ppm concentration of NH3, the TiO2/NiO bilayer thin film sensor exhibited high response value of 7.6 with fast response–recovery time of 24 s and 45 s at 280 °C. However, minimum response–recovery time of NiO/TiO2 thin film sensor for same ammonia concentration were found to be 30 s and 52 s with response value of 5.0 at 200 °C. The TiO2/NiO and NiO/TiO2 bilayer sensors show a stable change in response about 12% and 5% under the high humidity (60% RH) conditions for 100 ppm NH3, respectively. Thus, the investigated bilayer thin films can be expected to facilitate the potential candidate material for trace amount of NH3 detection in our environment. Therefore, this work provides a promising approach for design and development of low-power consumption and high-performance gas sensor.
Conflict of interest
The authors declare no competing financial interests.
Acknowledgements
The authors would like to acknowledge the financial support from the University Grant Commission, India (Grant No. 7412-32-044).
References
- J.-W. Yoon, Y. J. Hong, Y. Chan Kang and J.-H. Lee, RSC Adv., 2014, 4, 16067–16074 RSC.
- S. Tian, X. Ding, D. Zeng, J. Wu, S. Zhang and C. Xie, RSC Adv., 2013, 3, 11823–11831 RSC.
- K.-P. Yoo, K.-H. Kwon, N.-K. Min, M. J. Lee and C. J. Lee, Sens. Actuators, B, 2009, 143, 333–340 CrossRef.
- A. Tizianello, G. De Ferrari, G. Garibotto, G. Gurreri and C. Robaudo, J. Clin. Invest., 1980, 65, 1162–1173 CrossRef CAS PubMed.
- A. M. W. T. van den Broek, L. Feenstra and C. de Baat, J. Dent., 2007, 35, 627–635 CrossRef PubMed.
- B. Timmer, W. Olthuis and A. v. d. Berg, Sens. Actuators, B, 2005, 107, 666–677 CrossRef CAS.
- P. Karthick Kannan and R. Saraswathi, J. Mater. Chem. A, 2014, 2, 394–401 CAS.
- P. M. Ashraf, K. V. Lalitha and L. Edwin, Sens. Actuators, B, 2015, 208, 369–378 CrossRef CAS.
- R. Ghosh, A. K. Nayak, S. Santra, D. Pradhan and P. K. Guha, RSC Adv., 2015, 5, 50165–50173 RSC.
- Y. Zhou, K. Zheng, J.-D. Grunwaldt, T. Fox, L. Gu, X. Mo, G. Chen and G. R. Patzke, J. Phys. Chem. C, 2011, 115, 1134–1142 CAS.
- T. Li, W. Zeng and Z. Wang, Sens. Actuators, B, 2015, 221, 1570–1585 CrossRef CAS.
- A. Sanger, A. Kumar, A. Kumar and R. Chandra, Sens. Actuators, B, 2016, 234, 8–14 CrossRef CAS.
- C. Wang, L. Yin, L. Zhang, D. Xiang and R. Gao, Sensors, 2010, 10, 2088 CrossRef CAS PubMed.
- G. F. Fine, L. M. Cavanagh, A. Afonja and R. Binions, Sensors, 2010, 10, 5469 CrossRef CAS PubMed.
- S. J. Patil, A. V. Patil, C. G. Dighavkar, K. S. Thakare, R. Y. Borase, S. J. Nandre, N. G. Deshpande and R. R. Ahire, Front. Mater. Sci., 2015, 9, 14–37 CrossRef.
- V. Srivastava and K. Jain, RSC Adv., 2015, 5, 56993–56997 RSC.
- C. Dong, X. Xiao, G. Chen, H. Guan, Y. Wang and I. Djerdj, RSC Adv., 2015, 5, 4880–4885 RSC.
- L. Zhen, Z. Lin, P. Selcuk and Z. Xinyu, Curr. Org. Chem., 2013, 17, 2256–2267 CrossRef.
- Z. Ai, K. Deng, Q. Wan, L. Zhang and S. Lee, J. Phys. Chem. C, 2010, 114, 6237–6242 CAS.
- A. Kumar, A. Sanger, A. Kumar and R. Chandra, RSC Adv., 2016, 6, 47178–47184 RSC.
- S.-W. Choi, A. Katoch, G.-J. Sun, J.-H. Kim, S.-H. Kim and S. S. Kim, ACS Appl. Mater. Interfaces, 2014, 6, 8281–8287 CAS.
- L. Wang, H. Huang, S. Xiao, D. Cai, Y. Liu, B. Liu, D. Wang, C. Wang, H. Li, Y. Wang, Q. Li and T. Wang, ACS Appl. Mater. Interfaces, 2014, 6, 14131–14140 CAS.
- W. Guo, L. Mei, J. Wen and J. Ma, RSC Adv., 2016, 6, 15048–15053 RSC.
- X. Li, N. Chen, S. Lin, J. Wang and J. Zhang, Sens. Actuators, B, 2015, 209, 729–734 CrossRef CAS.
- A. Kar and A. Patra, J. Mater. Chem. C, 2014, 2, 6706–6722 RSC.
- S. H. Park, S. H. Kim, S. Y. Park and C. Lee, RSC Adv., 2014, 4, 63402–63407 RSC.
- A. Sanger, A. Kumar, A. Kumar, J. Jaiswal and R. Chandra, Sens. Actuators, B, 2016, 236, 16–26 CrossRef CAS.
- G. Martínez-Criado, J. Segura-Ruiz, M.-H. Chu, R. Tucoulou, I. López, E. Nogales, B. Mendez and J. Piqueras, Nano Lett., 2014, 14, 5479–5487 CrossRef PubMed.
- P.-P. Zhang, H. Zhang and X.-H. Sun, Nanoscale, 2016, 8, 1430–1436 RSC.
- F. Tian, Y. Zhang, J. Zhang and C. Pan, J. Phys. Chem. C, 2012, 116, 7515–7519 CAS.
- D. C. Joshi, S. Nayak, A. Kumar, A. Mohanta, D. Pamu and S. Thota, J. Appl. Phys., 2016, 119, 074303 CrossRef.
- D. Ju, H. Xu, Q. Xu, H. Gong, Z. Qiu, J. Guo, J. Zhang and B. Cao, Sens. Actuators, B, 2015, 215, 39–44 CrossRef CAS.
- L. Liu, S. Li, J. Zhuang, L. Wang, J. Zhang, H. Li, Z. Liu, Y. Han, X. Jiang and P. Zhang, Sens. Actuators, B, 2011, 155, 782–788 CrossRef CAS.
- C. Fang, S. Wang, Q. Wang, J. Liu and B. Geng, Mater. Chem. Phys., 2010, 122, 30–34 CrossRef CAS.
- G. Sakai, N. Matsunaga, K. Shimanoe and N. Yamazoe, Sens. Actuators, B, 2001, 80, 125–131 CrossRef CAS.
- I. Kosc, I. Hotovy, T. Roch, T. Plecenik, M. Gregor, M. Predanocy, M. Cehlarova, P. Kus and A. Plecenik, Appl. Surf. Sci., 2014, 312, 120–125 CrossRef CAS.
- N. Van Hieu, L. T. B. Thuy and N. D. Chien, Sens. Actuators, B, 2008, 129, 888–895 CrossRef CAS.
- F. Hossein-Babaei and M. Orvatinia, Sens. Actuators, B, 2003, 89, 256–261 CrossRef CAS.
- J. Deng, L. Wang, Z. Lou and T. Zhang, J. Mater. Chem. A, 2014, 2, 9030–9034 CAS.
- G. Zhang, X. Han, W. Bian, J. Zhan and X. Ma, RSC Adv., 2016, 6, 3919–3926 RSC.
- Y.-C. Liang, W.-K. Liao and S.-L. Liu, RSC Adv., 2014, 4, 50866–50872 RSC.
- Z. Chen and C. Lu, Sens. Lett., 2005, 3, 274–295 CrossRef CAS.
- Y.-B. Zhang, J. Yin, L. Li, L.-X. Zhang and L.-J. Bie, Sens. Actuators, B, 2014, 202, 500–507 CrossRef CAS.
- J. Zhang, D. Zeng, Q. Zhu, J. Wu, Q. Huang, W. Zhang and C. Xie, Phys. Chem. Chem. Phys., 2016, 18, 5386–5396 RSC.
- R. Pandeeswari and B. G. Jeyaprakash, Sens. Actuators, B, 2014, 195, 206–214 CrossRef CAS.
Footnotes |
† Electronic supplementary information (ESI) available: Included the FE-SEM cross-section micrographs of TiO2/NiO bilayer and pure TiO2 and NiO thin films, EDS mapping and elemental analysis of NiO/TiO2 bilayer thin film, the variation in the response with the thickness of top TiO2 layer and the stability analysis of TiO2/NiO and NiO/TiO2 bilayer sensors. See DOI: 10.1039/c6ra14342c |
‡ A. K. and A. S. have equal contribution in the manuscript. |
|
This journal is © The Royal Society of Chemistry 2016 |
Click here to see how this site uses Cookies. View our privacy policy here.