DOI:
10.1039/C6RA11095A
(Paper)
RSC Adv., 2016,
6, 52556-52563
Enhanced power generation using nano cobalt oxide anchored nitrogen-decorated reduced graphene oxide as a high-performance air-cathode electrocatalyst in biofuel cells†
Received
29th April 2016
, Accepted 26th May 2016
First published on 27th May 2016
Abstract
So far, the effect of the carbon matrix on ORR catalytic efficiency over carbon/cobalt oxide nanohybrids in biofuel cells has not been investigated, which is vital to guiding the scientific research on ORR catalysts. Moreover, although cobalt oxide crystals have been reported with electrocatalytic activity, studies on square-like nano cobalt oxide are very few, and it has not been reported as an oxygen reduction reaction (ORR) catalyst, let alone used in biofuel cells. Thus, herein, square-like nano cobalt oxide anchored on nitrogen-doped graphene (NG/Co-NS), carbon nanotube (CNT/Co-NS) and carbon black (CB/Co-NS) were prepared by a one-pot hydrothermal method for the application as an ORR catalyst in microbial fuel cells (MFC). The results indicated that NG/Co-NS exhibited outstanding ORR activity with a more positive on-set potential (−0.05 V vs. Ag/AgCl) and higher limiting diffusion current (5.8 mA cm−2 at −0.8 V) than CB/Co-NS and CNT/Co-NS, attributed to the synergistic catalytic effect of NG and Co-NS. Besides, in MFC tests, the maximum power density of NG/Co-NS was improved significantly to 713.6 mW m−2, which was 24.9% higher than Pt/C (571.3 mW m−2, 0.2 mg Pt cm−2). In addition, the internal resistance of MFCs with NG/Co-NS was lower than CB/Co-NS and CNT/Co-NS, which favored the electricity generation performance. Thus, NG/Co-NS was promising material for an alternative oxygen reduction reaction electrocatalyst of Pt/C in MFCs.
1. Introduction
Microbial fuel cells (MFCs), which directly convert chemical energy within an organic substrate into electricity with the aid of microbes, is one kind of eco-friendly water treatment technology as well as new energy technology.1,2 Up to now, various types of MFCs have been developed and attempted for performance optimization and cost reduction.3–6 Among them, air-cathode MFCs are the most promising ones to be scaled up for commercial application, due to their advantages of high output power density, low internal resistance, easy-operation, and non-toxicity.7–9 However, the scarcity, high-cost, and poor durability of noble Pt that widely used as oxygen reduction catalyst in air-cathode MFCs had became the greatest obstacle for MFCs' further development,10,11 since large-scale MFCs have a great demand on electrocatalysts.12,13 Therefore, it is difficult but desirable to develop alternative ORR catalysts that cost-effective, efficient and can be easily prepared for air-cathode MFCs.
Recently, an increasing attention has been paid on the development of diversiform new ORR catalysts, including (1) elements doped carbon materials, such as X-doped (X= N, P, S, B, F, Fe, Co, Mn) graphene,14–16 carbon nanotubes,17–19 activated carbon,20,21 carbon black22,23 and some other carbon derived from different precursors;24–29 (2) metal nano particles and carbon composites, such as silver nano particles or nanowires anchored graphene;30–32 (3) metal compounds (such as MnO2, Fe3O4, NixP and Co3O4) and carbon nanohybrids.33–38 So far, the effect of carbon matrix on ORR catalytic efficiency over carbon/cobalt oxide hybrids in biofuel cells has not been investigated, which is vital to guiding the scientific researches on ORR catalysts. Besides, although cobalt oxide crystal had been reported with electrocatalytic activity,39 the study on square-like nano cobalt oxide is very few,40–42 and have not been reported as oxygen reduction reaction (ORR) catalysts, let alone used in biofuel cells. Naturally, graphene, carbon nanotubes and carbon black would be chose as carbon matrix for fabrication carbon/Co3O4 hybrids, due to their better electroconductivity as well as synergistic catalytic activity. Besides, heteroatom-doping method was also attempted to achieve heteroatom-doped carbon matrix, which can absolutely favour the ORR activity.
Thus, in this work, square-like nano cobalt oxide anchored several carbon support materials including nitrogen-doped reduced graphene oxide (NG), multi-walled carbon nanotubes (CNT) and carbon black (CB) were prepared by one-pot hydrothermal method, followed by the physical characterization and electrochemical tests. And then the as-prepared materials were employed as oxygen reduction reaction catalysts in air-cathode MFCs. The results indicated that NG/Co-NS exhibited better ORR catalytic activity than CB/Co-NS and CNT/Co-NS. Subsequently, the effect of mass ratio of NG and Co-NS had been studied and optimized to enhance the output power density and voltage in air-cathode MFCs. The optimal NG/Co-NS composite proved to be a promising ORR catalyst, whose power generation performance was comparable to Pt/C catalyst (0.2 mg Pt cm−2).
2. Experimental
2.1. Materials
Graphene oxide (GO) was prepared by a modified Hummers' method.43 Briefly, 2 g of graphite powder (30 μm) and 1.5 g of sodium nitrate (NaNO3) were mixed with 70 mL of sulfuric acid (H2SO4, 98%) and stirred at 0 °C for 0.5 h, followed by slowly adding 7 g of potassium permanganate (KMnO4) under vigorous stirring within 2 h in ice bath. And then, rose temperature to 35 °C with continuously stirring for 2 h. Subsequently, 90 mL of water was added into the solution drop by drop, and the temperature was transferred to 90 °C in oil bath (silicon oil) for 1 h with stirring. Finally, 50 mL mixture solution of water (35 mL) and hydrogen peroxide (15 mL, H2O2, 30%) was added into the mixture. GO were collected by centrifugation and washing with HCl (3 wt%, 45 °C) and distilled water several times. The suspension of GO was obtained by dispersing GO in water with the assistance of ultrasonic.
Carbon black (CB, F24X016), multi-walled carbon nanotubes (CNT) and graphite powder (30 μm) were purchased from Alfa Aesar. Carbon cloth (HCP331N) and Pt/C catalyst (JM 40%) were purchased from Shanghai HeShen Company. Polyvinyl fluoride (PTFE, 60%) and whole fluorine sulfonic acid polyvinyl fluoride (Nafion, 5%) were purchased from Shandong DongYue company. All other chemicals were purchased from Beijing chemical works and used directly without further purification.
2.2. Preparation for catalysts
Nitrogen-doped reduced graphene oxide and square-like nano cobalt oxide (NG/Co-NS) hybrid was synthesized using a modified one-pot hydrothermal method (Fig. 1). In a typical synthesis, 45 mg hydrated cobalt chloride (CoCl2·6H2O) and 30 mg urea were dissolved in 60 mL graphene oxide suspension (1.5 mg mL−1). The mixture solution was poured into 100 mL PTFE pressure vessel and reacted at 150 °C for 15 h. The product was collected by filtration and washing with distilled water, followed by freeze-drying. The mass ratio of NG and Co-NS in NG/Co-NS was altered by changing the dosages of precursors (GO and CoCl2·6H2O). CNT/Co-NS and CB/Co-NS were prepared using the similar method as described above and just replaced the GO by CNT or CB. Note that CB and CNT were treated with a mixture of concentrated nitric and sulphuric acids prior to using. Bare cobalt oxide (Co-NS) was also synthesized by the similar hydrothermal method without adding carbon materials, and NG was prepared without adding hydrated cobalt chloride.
 |
| Fig. 1 The synthetic route of NG/Co-NS hybrids. | |
2.3. Physical characterization
Transmission electron microscopy (TEM) was carried out on a Hitachi H-800 transmission electron microscope at an acceleration voltage of 100 kV. The specimens for TEM were prepared by dropping a small drop of the suspension of samples on the copper grid and air drying. X-ray photoelectron spectroscopy (XPS) was performed on the Thermo Scientific ESCALab 250Xi using 200 W monochromater Al Kα radiation. The 500 μm X-ray spot was used for XPS analysis. The base pressure in the analysis chamber was about 3 × 10−10 mbar. Typically the hydrocarbon C 1s line at 284.8 eV from adventitious carbon is used for energy referencing. X-ray diffraction (XRD) were investigated by X-ray powder diffractometer with Cu Kα radiation as the X-ray source for excitation operating at 40.0 kV and 40.0 mA within the 2θ ranged from 5° to 70°.
2.4. Electrochemistry tests
Electrochemistry measurements was recorded by electrochemical workstation (CHI 750D, ChengHua Co. Shanghai) with three-electrode system (100 mL, 100 mM PBS) using the Ag/AgCl (saturated KCl) as the reference electrode, platinum wire (0.5 mm in diameter and 37 mm in length) as the counter electrode and catalysts modified glassy carbon (3 mm in diameter) as the working electrode, respectively. The distance between the working and counter electrode is 2 cm. And in this paper, all of potentials are versus reference electrode of Ag/AgCl (saturated KCl) unless noted otherwise. The scan rate was 10 mV s−1 and sweep range from 0.3 V to −0.8 V.
Prior to cyclic voltammetry (CV) measurements, N2 and O2 were bubbled into 0.1 M phosphate buffer solution (PBS, pH = 7) for 30 min, respectively, to achieve O2-free and O2-saturated solution. Linear sweep voltammetry (LSV) was investigated on rotating disk electrode (RDE, ATA-1B, JiangFen Co, Jiangsu) with three-electrode system as described above in O2-saturated PBS solution, and the rotating speed ranged from 250 to 2500 rpm. To prepare the ink of catalysts, 10 mg sample was dispersed into 1 mL mixture solution (0.75 mL water, 0.25 mL ethanol) with the assistance of ultrasonic for 30 min, followed by adding 50 μL of 5 wt% Nafion (DuPont) in the system, and the resultant ink was ultrasonicated for 10 min. 10 μL of ink was dropped on glassy carbon electrode (3 mm in diameter, 14 μg mm−2) and dried in the air. The glassy carbon electrode was polished with 0.5 μm aluminum oxide and cleaned ultrasonically for 30 min, prior to modifying.
2.5. MFCs configuration and operation
The air-cathode was prepared by traditional brushing method. Typically, 40 mg of as-prepared catalysts were dispersed in the mixture solution of water (0.83 μL mg−1), Nafion (5%, 6.67 μL mg−1) and isopropanol (3.33 μL mg−1), followed by ultrasonication for 20 min. And then the mixtures were uniformly coated on the surface of carbon cloth by brushing, and dried at 35 °C for 12 h.
The configuration of MFCs was the standard single-chamber cubic air-cathode (5 cm in width, 6.5 cm in length and 5 cm in height), and the available capacity was 27 cm3 with a 7 cm2 air-cathode.29 Prior to serving as anodes, graphite felts (2 cm in length, 2 cm in width and 0.5 cm in thickness) were immersed in acetone for 12 h and heat-treated at 450 °C for 30 min. All MFCs were inoculated from other MFCs which were inoculated with strain from our previous fermenting bacteria and had been running for more than 2 years.44 Each MFC was operated at 35 °C and fed with the culture medium containing sucrose (1 g L−1), vitamin solution (12.5 mL L−1), trace elements solution (12.5 mL L−1) in 50 mM phosphate buffer solution. The culture medium was refreshed when the voltage dropped below 100 mV.
A 1 kΩ resistor was loaded between the anode and air-cathode at initial period for measuring the curves of voltage versus time (V–t), using a data acquisition system (HIOKI LR8431-30) at 1 min interval. Power density and electrode polarization curves were investigated by varying the external resistor from 5 kΩ to 30 Ω. All the electrode potentials were tested versus the Ag/AgCl (saturated KCl) reference electrode. Both of the current density and power density results were reported normalized to the projected area of the air-cathode (7 cm2). The power density was calculated based on the cathode area as follows, eqn (1):
|
P = Ecell2/(RextAcat)
| (1) |
where,
Ecell is the external voltage,
Rext represents the external resistance, and
Acat is the projected area of cathode.
3. Results and discussion
3.1. Physical characterization of catalysts
Square-like nano cobalt oxide composited with different carbon support materials were prepared by one-pot hydrothermal method, followed by physical characterization. Fig. 2 showed the TEM images of different catalysts, indicating that both bare square-like nano cobalt oxide and square-like nano cobalt oxide/carbon materials hybrids were successfully achieved. From Fig. 2(c–f), a square-like morphology of cobalt oxide with size ranging from 100–200 nm was uniformly dispersed in carbon materials. In detail, as shown in Fig. 2(e), it is clearly that square-like nano cobalt oxide were wrapped by multilayer reduced graphene oxide, due to layer-by-layer self-assembly of cobalt oxide with NG, which was critical factor for enhancement of ORR activity.39 And bare monolayer NG was showed in Fig. 2(b) for comparing with NG/Co-NS. Moreover, it was not so angular for square-like cobalt oxide in Fig. 2(f) compared to Fig. 2(a), resulting from interaction between GO and Co2+ during the growth of crystal.
 |
| Fig. 2 TEM images of (a) Co-NS, (b) NG, (c) CB/Co-NS, (d) CNT/Co-NS, (e) and (f) NG/Co-NS. | |
XRD technique was first used to character the chemical composition of the as-prepared catalysts. Fig. 3(b) showed a characteristic peak at 12.2° that was ascribed to the (001) reflection plane of GO, revealing the GO was achieved from graphite carbon by modified Hummers' method. NG (Fig. 3(c)) and NG/Co-NS (Fig. 3(d)) exhibited the characteristic reflection plane at 25.2° and 44.6°, which were indexed to the (002) and (100) planes of graphitic carbon, respectively, demonstrating NG was achieved from GO. The significant diffraction peaks at 19.2°, 31.1° 36.5°, 37.4°, 44.7°, 55.7°, 59.2° and 65.1° emerged in XRD pattern of square-like nano cobalt oxide (Fig. 3(a)), which were corresponding to the (111), (220), (311), (222), (400), (422), (511) and (440) reflection planes of FCC structure,40 respectively, and were exactly consistent with the standard XRD patterns of Co3O4. Moreover, the characteristic peaks of Co3O4 also obviously appeared in CB/Co-NS (Fig. 3(e)), CNT/Co-NS (Fig. 3(f)) and NG/Co-NS (Fig. 3(d)), indicating Co3O4 was successfully composited with carbon materials.
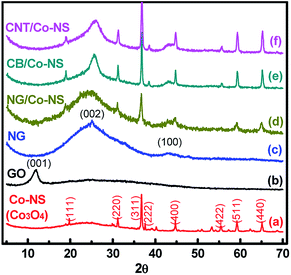 |
| Fig. 3 XRD patterns of (a) Co-NS, (b) GO, (c) NG, (d) NG/Co-NS, (e) CB/Co-NS, (f) CNT/Co-NS. | |
The chemical components of Co-NS, CB/Co-NS, CNT/Co-NS and NG/Co-NS were then characterized by XPS. The whole XPS surveys depicted in Fig. 4(a) revealed that all of hybrid materials were composed of element C, O and Co. And element N barely appeared in NG/Co-NS and NG, indicating successful N-doping on graphene by hydrothermal method. The details of atom ratio of different catalysts were listed in Table 1, and the Co/O ratios were lower than the stoichiometric value of Co3O4 (0.75), especially in NG/Co-NS, which might be due to the adsorption of water and oxygen on catalysts, and residual oxygen-containing groups on the NG.
 |
| Fig. 4 (a) XPS survey spectrums of different catalysts and high-resolution scan of (b) Co 2p, (c) C 1s of, NG/Co-NS and NG, (d) N 1s of, NG/Co-NS and NG. | |
Table 1 The atom ratio of different catalysts calculated by XPS
Catalysts |
C 1sa |
O 1sb |
Coc |
Co/O |
Pyridinic-Nd |
Pyrrolic-Ne |
Carbon content (at%). Oxygen content (at%). Cobalt content (at%) calculated from XPS measurement. Fraction (at%) of pyridinic-N calculated from deconvoluted high-resolution N 1s spectra. Fraction (at%) of pyrrolic-N calculated from deconvoluted high-resolution N 1s spectra. ‘Non’ indicates ‘not detectable’. |
Co-NS |
Non |
56.66 |
40.4 |
0.71 |
Non |
Non |
NG |
80.05 |
15.93 |
Non |
Non |
1.53 |
2.49 |
CB/Co-NS |
97.16 |
1.46 |
0.84 |
0.58 |
Non |
Non |
CNT/Co-NS |
96.64 |
2.14 |
1.22 |
0.57 |
Non |
Non |
NG/Co-NS |
80.38 |
15.18 |
1.55 |
0.10 |
1.17 |
1.56 |
The high resolution Co 2p spectrums (Fig. 4(b)) of catalysts exhibited two main characteristic peaks located at 781 ± 0.5 eV and 796.5 ± 0.5 eV, corresponding to the Co 2p3/2 and Co 2p1/2 spin-orbital peaks of Co3O4, respectively, which demonstrated the formation of Co3O4 in Co-NS, CB/Co-NS, CNT/Co-NS and NG/Co-NS. And this result was in agreement with XRD characterization.
The high resolution C 1s of NG/Co-NS and NG were deconvoluted into three different components as illustrated in Fig. 4(c). And the peaks located at 284.8 eV, 286.1 eV and 288.8 eV were corresponding to C–C bonds in graphitic carbon, C
N and C–O bonds, C–N and C
O bonds, respectively. The C
N bonds or C–N bonds might originate from N-doping into the defective sites of NG. Moreover, the small integral area of last two peaks stated clearly that most of the oxygen-containing groups on GO sheets had been reduced by hydrothermal method, which was favourable for improvement of the catalysts' conductivity. The high resolution N 1s spectrum of NG/Co-NS and NG was showed in Fig. 4(d), and the N 1s peaks can be deconvoluted into two types of doping-N that pyridinic N (399.5 eV), pyrrolic N (401.1 eV), revealing nitrogen atoms had been doped into either the defective sites at the edges or the in-plane sp2 hybridized carbon framework of graphene sheets. Noted that pyridinic N including doped in graphene as well as other carbon materials, had been reported with oxygen reduction catalytic activity.19,27 Additionally, the synergetic effect of pyridinic N and Co3O4 would significantly improve the ORR activity of NG/Co-NS.27,39
3.2. Electrochemical performance of catalysts
The electrocatalytic activity for oxygen reduction reaction of different catalysts was investigated by CV and LSV measurements. As depicted in Fig. 5(a), for all catalysts, the oxygen reduction current dramatically appeared in negative scan in O2-saturated (solid lines) PBS solution compared to N2-saturated ones (dash lines), suggesting all of them possessed ORR activity. Moreover, the peaks of oxygen reduction current varied between different catalysts: −0.12 V, −0.25 V, −0.29 V and −0.52 V for CNT/Co-NS, NG/Co-NS, CB/Co-NS and Co-NS, respectively, revealing a lower over-potential of catalytic activity with CNT/Co-NS and NG/Co-NS than others. However, it should be noted that CNT/Co-NS almost existed a rectangular CV curves which meant it had a capacitive property, the ORR activity was probably weakened by the high charge transfer resistance of oxygen reduction reaction on the surface of CNT/Co-NS due to electric double layer.45 From Fig. 5(b), it can be seen clearly that the on-set potential (−0.05 V) and half-wave potential of NG/Co-NS were more positive than those of other catalysts. Additionally, the limiting diffusion current of NG/Co-NS significantly increased to 5.8 mA cm−2 at −0.8 V, which was bigger than CNT/Co-NS (4.3 mA cm−2), CB/Co-NS (4.9 mA cm−2) and Co-NS (0.7 mA cm−2). Fig. S1† showed that the limiting diffusion current continuously increasing along with the rotation speed increased from 500 up to 2500 rpm. These results exactly demonstrated a better oxygen reduction catalytic activity of NG/Co-NS in PBS solution, and it was interesting for us to evaluate its electrocatalytic activity in real MFCs.
 |
| Fig. 5 (a) CV curves of different catalysts in N2-saturated (dash lines) or O2-saturated (solid lines) PBS solution, (b) LSV curves of different catalysts with rotation speed of 1600 rpm. | |
3.3. MFCs performance
To check and compare the practical electrocatalytic activity of catalysts as mentioned above, air-cathodes coated with different catalysts were prepared and installed in singer-chamber microbial fuel cells, and carried out for nearly one week. From Fig. 6(a), for all MFCs, distinct voltage plateaus emerged as soon as PBS solution was refreshed, and the stable voltages were 230.6 mV, 293.5 mV, 407.1 mV, 486.4 mV and 471.5 mV for Co-NS, CB/Co-NS, CNT/Co-NS, NG/Co-NS and Pt/C, respectively. It is mentionable that voltage plateaus were on the decline and dropped about 10 percent for most catalysts including Pt/C in a week, but not NG/Co-NS, which still generated a steady voltage plateaus after 7 cycles.
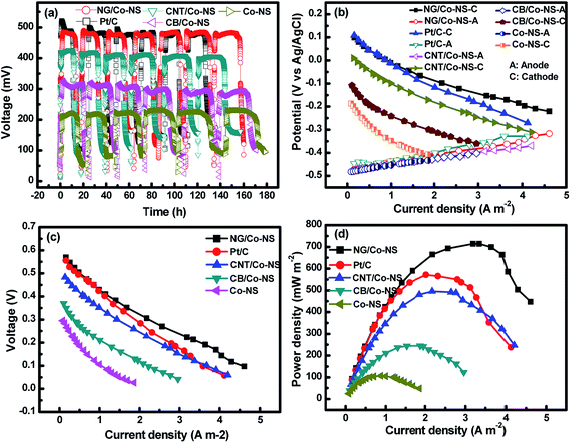 |
| Fig. 6 (a) The voltages versus time curves (V–t) of various catalysts modified air-cathodes MFCs, (b) the polarization of anodic and cathodic electrode potentials, (c) the voltages versus current density curves and (d) the output power density curves of MFCs based on the air-cathodes with different catalysts. | |
For further evaluation, output power, always a key parameter of fuel cells, was measured by varying external resistance. Meanwhile, polarization curves of anode and cathode of MFCs were achieved to assess the polarization of electrodes. From Fig. 6(b) and (c), nearly identical anode potential of different catalysts modified MFCs almost changed unanimously. However, both cathode potential and voltage of air-cathode MFC with NG/Co-NS were relatively higher than other carbon materials supported square-like nano Co3O4, and even higher than Pt/C, which definitely demonstrated a feeblish cathode polarization with NG/Co-NS.
Fig. 6(d) showed that output power density increased along with current density increasing until reached maximum power density, and then fell down. In detail, the maximum power density of 713.6 mW m−2 was achieved for NG/Co-NS, which was much higher than Co-NS (107.2 mW m−2), CB/Co-NS (245.5 mW m−2), CNT/Co-NS (496.0 mW m−2), and Pt/C (571.3 mW m−2). Therefore, we believed that NG/Co-NS had more efficient and durable electrocatalytic activity in MFCs than the rest.
However, it is interesting that NG/Co-NS excelled in electricity generation in MFCs, yet exhibiting obvious weaker ORR activity compared to Pt/C catalyst in LSV measurements on rotating disk electrode. To make this phenomenon clear, LSV measurements were directly conducted on real MFCs, in which catalysts modified air-cathode as work electrode and bio-anode as counter electrode. This was very different from measured on RDE, such as work electrode, catalysts loading mass or counter electrode. Fig. S2† showed that the polarization current density of air-cathode with NG/Co-NS rose rapidly, significantly exceeded that of other catalyst and even overmatched Pt/C. Therefore, we had faith in that both catalysts loading mass and bio-anode will affect catalytic activity in real MFCs, and NG/Co-NS was a promising ORR catalyst used in MFCs.
3.4. Impedance analysis
Indeed, under our experiment condition, the performance of MFCs, such as maximum power density and output voltage, was mainly affected by catalytic activity of air-cathode and internal resistance of cells. The higher maximum power density meant a better ORR activity of catalyst and a lower internal resistance as well. Thus, it is essential for us to measure total internal resistance of MFCs with various catalysts, and analyzed where resistance was rooted in and how it influenced cell's performance.
The total resistance and resistance distribution property of MFCs were studied by use of AC impedance technique (frequency: 0.1–1.0 × 106 Hz, initial potential: −0.1 V). Through explanation and analyzing the Nyquist graph (Fig. 7), the characteristic equivalent electrocircuit was provided (insert picture in Fig. S3, ESI Materials†). And Fig. S3† illustrated that total resistance was made up of ohmic resistance (Rs), diffusion resistance (Rd) and electron transfer resistance (Rct). In detail, total resistance of NG/Co-NS was 135.5 Ω, which was bigger than Pt/C, but fewer than other catalysts. All ohmic resistances did not vary much according to similar fundamental construction and electrolyte. And electron transfer resistances were almost the least proportion except for CNT/Co-NS, due to its capacitive character as we mentioned above which would block electron transfer.45 Moreover, regardless of CNT/Co-NS, diffusion resistances were nearly the largest proportion, which mostly hindered ORR process.
 |
| Fig. 7 Nyquist graph of different catalysts modified air-cathode MFCs. | |
3.5. Effect of mass ratio of NG and Co-NS
Since NG/Co-NS had delivered better ORR activity and electricity generation performance in MFCs as mentioned above due to synergetic effect of NG and Co-NS, then the effect of components proportion of NG/Co-NS on MFCs' performance needed to be discussed more deeply. Therefore, NG/Co-NS with different proportions of two components were prepared by changing feeding ratio, and the feeding mass ratios of GO to CoCl2·6H2O for preparation of NG/Co-NS-0.25, NG/Co-NS-0.5 (equal to NG/Co-NS that mentioned above), NG/Co-NS-1.0 and NG/Co-NS-2.0 were 4
:
1, 2
:
1, 1
:
1 and 1
:
2, respectively. The TEM images of as-prepared catalysts were showed in Fig. 9. The number of Co3O4 nano particles were increasing obviously with the increasing amount of feeding CoCl2·6H2O. However, compared to NG/Co-NS-0.5 (Fig. 2(e)), Co3O4 nano particles were not well-distributed on N-doped reduced graphene oxide in NG/Co-NS-0.25, NG/Co-NS-1.0 and NG/Co-NS-2.0, which can absolutely affect the ORR activity.
The electricity generation performance of above catalysts was then investigated in real MFCs. From Fig. 8(a), the stable voltage platforms of catalysts emerged at 338.6 ± 13 mV, 435.6 ± 11 mV, 483.8 ± 6 mV, 418.2 ± 15 mV and 400.2 ± 27 mV for NG, NG/Co-NS-0.25, NG/Co-NS-0.5, NG/Co-NS-1.0 and NG/Co-NS-2.0, respectively. Moreover, the corresponding output power density was depicted in Fig. 8(b). The maximum output power density of 713.6 mW m−2, distinctly higher than others, was generated by NG/Co-NS-0.5, indicating 2
:
1 of mass proportion of GO and cobalt chloride hexahydrate was optimal for catalyst preparation and application in MFCs. This may because the high-loading of Co3O4 on reduced graphene oxide could lower the conductivity of hybrids, so that weakened its ORR activity, even though nano Co3O4 has the ORR activity.
 |
| Fig. 8 (a) The voltages versus time curves (V–t) of various catalysts modified air-cathodes MFCs and (b) the output power density curves of MFCs based on the air-cathodes with different catalysts. | |
 |
| Fig. 9 The TEM images of NG/Co-NS-0.25 (a), NG/Co-NS-1.0 (b) and NG/Co-NS-2.0 (c). | |
4. Conclusions
In this study, square-like nano cobalt oxide anchored different carbon matrix including nitrogen-doped reduced graphene oxide (NG/Co-NS), carbon nanotube (CNT/Co-NS) and carbon black (CB/Co-NS) nanohybrids were synthesized by one-pot hydrothermal method. And then they were employed as oxygen reduction reaction (ORR) catalyst in air-cathode microbial fuel cells to study the effect of carbon matrix on oxygen reduction catalytic efficiency over carbon/square-like cobalt oxide hybrids. It is exciting that NG/Co-NS exhibited better ORR activity both in electrochemical measurement and MFCs test, due to the lower internal resistance of MFC and synergistic catalytic effect of NG and Co-NS. Since the facile synthesis and relatively low cost of NG/Co-NS, it is a promising ORR catalyst for application in MFCs, which improving the power generation and meeting the requirements of MFCs' development.
Acknowledgements
This work was financially supported by the National Natural Science Foundation of China (No. 21403251).
References
- B. E. Logan, B. Hamelers, R. Rozendal, U. Schröder, J. Keller, S. Freguia, P. Aelterman, W. Verstraete and K. Rabaey, Environ. Sci. Technol., 2006, 40, 5181–5192 CrossRef CAS PubMed.
- K. Rabaey and W. Verstraete, Trends Biotechnol., 2005, 23, 291–298 CrossRef CAS PubMed.
- Y. Fan, H. Hu and H. Liu, J. Power Sources, 2007, 171, 348–354 CrossRef CAS.
- S. Freguia, K. Rabaey, Z. Yuan and J. Keller, Water Res., 2008, 42, 1387–1396 CrossRef CAS PubMed.
- H. Liu, S. Cheng and B. E. Logan, Environ. Sci. Technol., 2005, 39, 5488–5493 CrossRef CAS PubMed.
- B. E. Logan, M. J. Wallack, K.-Y. Kim, W. He, Y. Feng and P. E. Saikaly, Environ. Sci. Technol. Lett., 2015, 2, 206–214 CrossRef CAS.
- Y. Feng, Q. Yang, X. Wang and B. E. Logan, J. Power Sources, 2010, 195, 1841–1844 CrossRef CAS.
- H. Liu and B. E. Logan, Environ. Sci. Technol., 2004, 38, 4040–4046 CrossRef CAS PubMed.
- B. Logan, S. Cheng, V. Watson and G. Estadt, Environ. Sci. Technol., 2007, 41, 3341–3346 CrossRef CAS PubMed.
- L. Li, M. Wang, N. Cui, Y. Ding, Q. Feng, W. Zhang and X. Li, RSC Adv., 2016, 6, 25877–25881 RSC.
- O. Lefebvre, W. K. Ooi, Z. Tang, M. Abdullah-Al-Mamun, D. H. C. Chua and H. Y. Ng, Bioresour. Technol., 2009, 100, 4907–4910 CrossRef CAS PubMed.
- H. Dong, H. Yu, X. Wang, Q. Zhou and J. Feng, Water Res., 2012, 46, 5777–5787 CrossRef CAS PubMed.
- X. Quan, Y. Mei, H. Xu, B. Sun and X. Zhang, Electrochim. Acta, 2015, 165, 72–77 CrossRef CAS.
- X. Wang, G. Sun, P. Routh, D.-H. Kim, W. Huang and P. Chen, Chem. Soc. Rev., 2014, 43, 7067–7098 RSC.
- Q. Wen, S. Wang, J. Yan, L. Cong, Y. Chen and H. Xi, Bioelectrochemistry, 2014, 95, 23–28 CrossRef CAS PubMed.
- S. Yang, L. Zhi, K. Tang, X. Feng, J. Maier and K. Müllen, Adv. Funct. Mater., 2012, 22, 3634–3640 CrossRef CAS.
- K. Chen, X. Huang, C. Wan and H. Liu, Chem. Commun., 2015, 51, 7891–7894 RSC.
- Y. J. Sa, C. Park, H. Y. Jeong, S.-H. Park, Z. Lee, K. T. Kim, G.-G. Park and S. H. Joo, Angew. Chem., Int. Ed., 2014, 53, 4102–4106 CrossRef CAS PubMed.
- K. Gong, F. Du, Z. Xia, M. Durstock and L. Dai, Science, 2009, 323, 760–764 CrossRef CAS PubMed.
- X. Sheng, N. Daems, B. Geboes, M. Kurttepeli, S. Bals, T. Breugelmans, A. Hubin, I. F. J. Vankelecom and P. P. Pescarmona, Appl. Catal., B, 2015, 176–177, 212–224 CrossRef CAS.
- B. Wu, S. Zhang, F. Yao, R. Huo, F. Zhang and S. Xu, J. Colloid Interface Sci., 2016, 462, 183–190 CrossRef CAS PubMed.
- J. Chang, X. Sun, L. Feng, W. Xing, X. Qin and G. Shao, J. Power Sources, 2013, 239, 94–102 CrossRef CAS.
- R. K. Shervedani and A. Amini, Carbon, 2015, 93, 762–773 CrossRef CAS.
- X. Tang, H. Li, Z. Du and H. Y. Ng, RSC Adv., 2015, 5, 79348–79354 RSC.
- X. Tang, H. Li, W. Wang, Z. Du and H. Y. Ng, RSC Adv., 2014, 4, 12789–12794 RSC.
- Q. Liu, Y. Zhou, S. Chen, Z. Wang, H. Hou and F. Zhao, J. Power Sources, 2015, 273, 1189–1193 CrossRef CAS.
- K. Zhou, W. Zhou, X. Liu, Y. Wang, J. Wan and S. Chen, ACS Appl. Mater. Interfaces, 2014, 6, 14911–14918 CAS.
- L. Liu, Q. Xiong, C. Li, Y. Feng and S. Chen, RSC Adv., 2015, 5, 89771–89776 RSC.
- C. Cao, L. Wei, M. Su, G. Wang and J. Shen, Bioresour. Technol., 2016, 214, 348–354 CrossRef CAS PubMed.
- D. J. Davis, A.-R. O. Raji, T. N. Lambert, J. A. Vigil, L. Li, K. Nan and J. M. Tour, Electroanalysis, 2014, 26, 164–170 CrossRef CAS.
- R. Liu, X. Yu, G. Zhang, S. Zhang, H. Cao, A. Dolbecq, P. Mialane, B. Keita and L. Zhi, J. Mater. Chem. A, 2013, 1, 11961–11969 CAS.
- X. Lou, H. Pan, S. Zhu, C. Zhu, Y. Liao, Y. Li, D. Zhang and Z. Chen, Catal. Commun., 2015, 69, 43–47 CrossRef CAS.
- J. Ahmed, H. J. Kim and S. Kim, RSC Adv., 2014, 4, 44065–44072 RSC.
- Y. Cao, M.-S. Zheng, S. Cai, X. Lin, C. Yang, W. Hu and Q.-F. Dong, J. Mater. Chem. A, 2014, 2, 18736–18741 CAS.
- S. Li, Y. Hu, Q. Xu, J. Sun, B. Hou and Y. Zhang, J. Power Sources, 2012, 213, 265–269 CrossRef CAS.
- Y. Lu, X. Wang, Y. Mai, J. Xiang, H. Zhang, L. Li, C. Gu, J. Tu and S. X. Mao, J. Phys. Chem. C, 2012, 116, 22217–22225 CAS.
- Q. Wen, S. Wang, J. Yan, L. Cong, Z. Pan, Y. Ren and Z. Fan, J. Power Sources, 2012, 216, 187–191 CrossRef CAS.
- N. A. Zubir, C. Yacou, J. Motuzas, X. Zhang, X. S. Zhao and J. C. Diniz da Costa, Chem. Commun., 2015, 51, 9291–9293 RSC.
- Y. Liang, Y. Li, H. Wang, J. Zhou, J. Wang, T. Regier and H. Dai, Nat. Mater., 2011, 10, 780–786 CrossRef CAS PubMed.
- G. Gnana kumar, M. Christy, H. Jang and K. S. Nahm, J. Power Sources, 2015, 288, 451–460 CrossRef CAS.
- F. Roncaroli, E. S. Dal Molin, F. A. Viva, M. M. Bruno and E. B. Halac, Electrochim. Acta, 2015, 174, 66–77 CrossRef CAS.
- M. Zhang, R. Li, X. Chang, C. Xue and X. Gou, J. Power Sources, 2015, 290, 25–34 CrossRef CAS.
- D. R. Dreyer, S. Park, C. W. Bielawski and R. S. Ruoff, Chem. Soc. Rev., 2010, 39, 228–240 RSC.
- L. Wei, H. Han and J. Shen, Int. J. Hydrogen Energy, 2013, 38, 11110–11116 CrossRef CAS.
- E. Frackowiak, K. Metenier, V. Bertagna and F. Beguin, Appl. Phys. Lett., 2000, 77, 2421–2423 CrossRef CAS.
Footnote |
† Electronic supplementary information (ESI) available. See DOI: 10.1039/c6ra11095a |
|
This journal is © The Royal Society of Chemistry 2016 |
Click here to see how this site uses Cookies. View our privacy policy here.