DOI:
10.1039/C6RA09077J
(Paper)
RSC Adv., 2016,
6, 52549-52555
Bio-based epoxy-anhydride thermosets from six-armed linoleic acid-derived epoxy resin†
Received
8th April 2016
, Accepted 24th May 2016
First published on 26th May 2016
Abstract
Six-armed linoleic acid-derived epoxy resin with a rigid triazine core (EHL) was prepared through the esterification reaction between linoleic acid and hexamethylol melamine, followed by epoxidation of unsaturated fatty acid chains by using hydrogen peroxide. Bio-based epoxy-anhydrides thermosets were then produced from this resin by using 4-methyl hexahydrophthalic anhydride as the hardener and 1,8-diazabicyclo[5.4.0]undec-7-ene as the catalyst; the properties of these thermosets were then systematically investigated. The epoxy oligomer was fully characterized and confirmed through Fourier-transform infrared spectroscopy, nuclear magnetic resonance, and matrix-assisted laser desorption and ionization time-of-flight mass spectrometry. The physical properties of this oligomer were also studied according to its bulk viscosity, epoxy equivalent weight, and density. The curing extent of the bio-based epoxy-anhydride thermosets were measured through differential scanning calorimetry and gel content testing. The properties of these thermosets were characterized through tensile testing, dynamic mechanical thermal analysis, and thermogravimetric analysis. Compared with thermosets based on benchmark bio-based epoxy resins, such as epoxidized soybean oil and epoxidized sucrose soyate, EHL-based thermosets showed higher glass transition temperatures, and enhanced tensile strength and modulus for a given cross-link density. These enhancements can be rationalized according to the rigidity of the triazine core, and the cohesive energy stemmed from the inter-molecular interaction of highly polarized heterocycle.
1. Introduction
Epoxides are a class of thermosetting resins that can produce thermosets with the combined properties of excellent adhesion to substrates, favorable chemical resistance, and high mechanical properties at ambient and elevated temperatures. Thus, epoxy polymers have been widely used for various applications including surface coatings, adhesives, matrices for fiber-reinforced composites, and electrical and electronic laminates. Bisphenol A (BPA) diglycidyl ether (DGEBA) and its condensed form are the most widely used epoxy resins, accounting for approximately 90% of total epoxy consumption worldwide.1,2 However, the major reactant for epoxy resins, BPA, was classified as an endocrine-disrupting chemical (EDC). Because of its negative effects on human health and the environment, some countries have banned the use of BPA in food contact materials.3–5 Therefore, considerable research efforts have been aimed at developing BPA-free epoxy resins and thermosets.6
The development of epoxy polymers from bio-renewable feedstocks is of academic and practical importance because of uncertainty regarding the price and foreseeable limit of petroleum, as well as a global tendency toward sustainable development. Various bio-based raw materials have been used for producing epoxy monomers and hardeners such as vegetable oils, natural rubbers, cardanol, polysaccharides, lignins, tannins, and their derivatives.7–13 Among these bio-sourced chemicals, vegetable oils are attractive and feasible raw materials for epoxy resins because of their high annual production, high availability, relatively low cost, structural diversity, and high potential for further modification. Epoxy functionality can be readily introduced into vegetable oils through the catalyzed epoxidation of unsaturated fatty acid chains by using peracids as oxidative reagents. Several epoxidized vegetable oils (EVOs), such as epoxidzed soybean oil (ESO), and epoxidized linseed oil (ELO), are produced on an industrial scale by Arkema under the brand name Vikoflex®. EVOs are generally used as stabilizers or plasticizers for polyvinylchloride (PVC), as well as reactive diluents and toughening additives for DGEBA-based formulations. Moreover, through the ring-opening reactions of oxiranes, EVOs can be into polyols for polyurethane synthesis, and (meth) acrylates for UV-curable coatings.13–17
Despite their obvious advantages and application potential, EVOs remain associated with several drawbacks including the flexibility of fatty acid chains and low reactivity of internal epoxy groups. These drawbacks often lead to low glass transition temperatures (Tg) and inferior mechanical properties in EVO-based thermosets, which renders them less competitive compared with petroleum-based epoxy resins in structural applications. Therefore, various synthetic approaches have been explored to enhance the thermal and mechanical properties of EVO-based epoxy polymers. Three strategies are generally employed: introduction of rigid aliphatic or aromatic segments, incorporation of terminal epoxide groups, and increase in functionality.13–17 Webster et al. reported a series of epoxidized sucrose esters of fatty acids (ESEFAs) that possessed a rigid sucrose core and an average of 7.7 fatty acid chains per molecule. Compared with ESO, thermosets based on ESEFAs and anhydrides exhibited a considerably higher Tg and improved mechanical properties at room temperature.18–22 Epoxy functionality was further increased by Chisholm et al. through the cationic polymerization of vinyl ether of soybean oil fatty acids, followed by the epoxidation of the unsaturation of the fatty acids. These epoxides exhibited considerably faster curing kinetics and higher thermal and mechanical properties compared with ESO.23,24 Wang and Schuman developed a range of glicidyl esters of epoxidized fatty acids (EGSs) through transesterification and epoxidation reactions. The higher oxirane contents and more reactive terminal epoxides of EGSs gave rise to thermosets with markedly higher Tg values.25,26 Cadiz et al. described the preparation of an array of bio-based epoxides derived from undecylenic acid, which is a non-natural fatty acid produced by the pyrolytic cracking of castor oil under pressure. The resulting thermosets displayed a moderate Tg and favorable thermal stability.27 Zhang et al. synthesized bio-based resins with two or three terminal epoxy groups by using tung oil fatty acid as a major raw material. Thermosets derived from these epoxies and nadic methyl anhydride exhibited thermal and mechanical properties comparable to DGEBA-based ones.28
In this paper, we report the synthesis and characterization of a novel six-armed epoxy resin, epoxidized hexa (linoleoyl hydroxymethyl) melamine (EHL). This oligomer exhibits a rigid triazine core and high epoxy functionality stemmed from its six fatty acid chains. This oligomer was then formulated into epoxy-anhydride thermosets, and the curing extent and material properties were comprehensively investigated. The results revealed that EHL-based thermosets possessed improved thermal and mechanical properties compared with those derived from benchmark bio-based epoxides, ESO, and epoxidized sucrose soyate (ESS).
2. Experimental
2.1. Materials
Hexamethylol melamine (HMM) was supplied by Jianfeng Haokang Chemical Co. (Chongqing, China). Epoxidized soybean oil (ESO) was purchased from Sanmu Group (Wuxi, China). Sucrose soyate (Sefose 1618U) was provided by Procter and Gamble Chemicals (Cincinnati, OH). All the other chemicals were purchased from J&K Chemicals (Shanghai, China). All the reagents were used as received unless specified otherwise. ESS was prepared according to a previous study.22
2.2. Synthesis of epoxidized hexa (linoleoyl hydroxymethyl) melamine
2.2.1. Synthesis of hexa (linoleoyl hydroxymethyl) melamine. HMM (3.06 g, 0.01 mol), linoleic acid (25.24 g, 0.09 mol), N,N′-dicyclohexylcarbodiimide (DCC) (18.56 g, 0.09 mol), 4-dimethylaminopyridine (DMAP) (1.09 g, 9 mmol), and dichloromethane (150 mL) were charged into a three-necked, round-bottomed, 250 mL flask equipped with an overhead stirrer, a condenser, and nitrogen inlet and outlet. The mixture was stirred at room temperature for 24 hours under a nitrogen atmosphere, and then refluxed for another 24 hours. When the mixture cooled to room temperature, the by-product, dicyclohexylurea, was removed through filtration. Dichloromethane was removed by rotary evaporation. The residue was washed with ethanol (100 mL, four washes) to afford hexa (linoleoyl hydroxymethyl) melamine (HL) as a yellow liquid (17.87 g, 95%). FT-IR (cm−1): 3010 (C–H stretching for double bond), 2960 (C–H stretching for –CH3), 2920 and 2860 (C–H stretching for –CH2–), 1750 (C
O stretching for ester), 1570 (C
N stretching for triazine). 1H NMR (CDCl3, δ ppm): 0.91 (t, J = 6.8 Hz, 3H), 1.27–1.39 (m, 14H), 1.60–1.64 (m, 2H), 2.04–2.09 (m, 4H), 2.29 (t, J = 7.6 Hz, 2H), 2.79 (t, J = 7.6 Hz, 2H), 5.31–5.44 (m, 4H), 5.80 (s, 2H); 13C NMR, (CDCl3, δ ppm): 14.04, 18.40, 22.56, 24.73, 25.62, 27.19, 29.15, 29.23, 29.33, 29.61, 31.51, 34.17, 58.35, 71.35, 127.87, 128.07, 129.93, 130.19, 166.03, 173.26. MALDI-TOF MS: calculated for C117H198N6O12: 1880.86, found m/z: 1904.46 [M + Na+].
2.2.2. Epoxidation of hexa (linoleoyl hydroxymethyl) melamine. HL (12.54 g, 6.7 mmol), acetic acid (2.41 g, 0.04 mol), Amberlite 120H (2.51 g, 20 weight percent of HL), and toluene (100 mL) were placed into to a four-necked, round-bottomed, 250 mL flask equipped with a condenser, overhead stirrer, pressure-equalized dropping funnel, and nitrogen inlet and outlet. The mixture was heated to 60 °C with stirring under a nitrogen atmosphere. Then hydrogen peroxide (50 wt% aqueous solution) (10.93 g, 0.16 mol) was added dropwise while the reaction temperature was controlled in the range of 60–70 °C. After the completion of hydrogen peroxide addition, the reaction was stirred at 60 °C for another 12 hours. After the mixture cooled to room temperature, Amberite 120H was removed through filtration. The filtrate was thoroughly washed with DI water until the pH value was neutral. The organic layer was collected, dried over anhydrous magnesium sulfate, evaporated under reduced pressure, and dried in vacuum at 35 °C for 12 hours to obtain EHL as a yellow wax (12.78 g, 92%). FT-IR (cm−1): 2970 (C–H stretching for –CH3), 2930 and 2850 (C–H stretching for –CH2–), 1730 (C
O stretching for ester), 1580 (C
N stretching for triazine), 830 (C–O stretching for oxirane). 1H NMR, (CDCl3 δ ppm): 0.92 (t, J = 6.0 Hz, 3H), 1.34–1.36 (m, 10H), 1.48–1.55 (m, 8H), 1.60–1.64 (m, 2H), 1.73–1.79 (m, 2H), 2.29 (t, J = 7.6 Hz, 2H), 2.97–3.00 (m, 2H), 3.07–3.15 (m, 2H), 5.79 (s, 2H); 13C NMR, (CDCl3 δ ppm): 13.95, 22.54, 24.68, 26.13, 26.23, 26.49, 26.60, 26.94, 27.24, 27.87, 29.25, 31.65, 34.12, 54.15, 54.30, 54.32, 56.62, 56.71, 56.90, 56.98, 71.33, 166.04, 173.23. MALDI-TOF MS: calculated for C117H198N6O24: 2072.85, found m/z: 2095.38 [M + Na+].
2.3. Epoxy-anhydride thermoset formulation
Bio-based thermosets were formulated using 4-methyl hexahydrophthalic anhydride (MHHPA) as the hardener and 1,8-diazabicyclo[5.4.0]undec-7-ene (DBU) as the catalyst. The equivalent ratio of epoxide to anhydride was 1.0
:
0.4, 1.0
:
0.5 and 1.0
:
0.6. DBU was used with 1.5 wt% of the total resin weight. A representative procedure for thermoset formulation is as follows. EHL (4.08 g, containing 0.02 mol epoxide), MHHPA (1.68 g, 0.01 mol), and DBU (0.86 g) were mixed thoroughly in a glass vial and cast onto a glass panel with a drawdown bar to form a thin film. Curing was performed at 95 °C for 48 hours. The cured films were peeled from the substrate and conditioned for 24 hours at room temperature prior to characterization.
2.4. Characterization
Fourier transformed infrared spectroscopy (FT-IR) was conducted with a Bomem FTLA 2000-104 FT-IR spectrometer. Proton and carbon nuclear magnetic resonance (1H and 13C NMR) spectra were recorded on an AVANCE III 400 MHz Digital NMR spectrometer with CDCl3 used as the solvent. Epoxy equivalent weights (EEWs) were obtained through epoxy titration by using a Mettler Toledo T50 potentiometric titrator, according to ASTM D 1652. Crystal violet and a solution of 0.1 N HBr in glacial acetic acid were used as the indicator and titrant, respectively. Iodine values were determined according to GB/T5532-2008. The viscosity of the oligomers was measured using a DHR-2 Rheometer (TA Instruments) operating from 0.001 to 400 rad s−1 with an optimal strain of 1%. Iodine values were determined according to ASTM 5768-02. The densities of the oligomers were measured by using a densimeter (MH-300S) at 25 °C. Matrix-assisted laser desorption and ionization time-of-flight (MALDI-TOF) mass spectra were recorded on a Bruker autoflex III spectrometer (Bruker, Germany) equipped with a smart beam laser with a wavelength of 355 nm. All mass spectra were obtained in the positive ion and linear/reflective mode. Samples were dissolved in tetrahydrofuran (THF) (1 mg mL−1), and 2,5-dihydroxybenzoic acid (10 mg mL−1 in THF) was used as the matrix. Differential scanning calorimetry (DSC) was measured using a Mettler Toledo DSC 822e instrument (Mettler-Toledo, Switzerland) with a heating rate of 20 °C min−1. The extent of curing was calculated according to the following equation: αt = ΔH0 − ΔH1/ΔH0, where ΔH0 and ΔH1 are the total reaction heat and the residue heat after curing at 95 °C for 48 hours, respectively. Dynamic mechanical thermal analysis (DMTA) was conducted using a Q800 DMTA (TA Instruments) operating at 1 Hz and a heating rate of 3 °C min−1 from −40 °C to 150 °C (tensile mode). The dimensions of the samples for DMTA tests were 40 mm × 5 mm × 90 ± 10 μm. Cross-link density was calculated according to the following equation: E′ = 3veRT, where E′ is the storage modulus at the temperature of (Tg + 50 °C); and R and T are gas constant and absolute temperature, respectively. Thermogravimetric analysis (TGA) was performed using a Mettler Toledo STAR thermogravimetric analyzer under a continuous nitrogen flow, with a heating rate of 15 °C min−1 from 30 °C to 600 °C. Gel contents of the thermosets were determined through Soxhlet extraction by using dichloromethane. Mechanical properties of cured films (4 cm × 0.5 cm × 90 ± 10 μm) were measured using an Instron material testing system (Model 5982, Instron) under a constant displacement rate of 5.0 mm min−1. Five samples were measured for each thermoset, from which the averages were reported.
3. Results and discussion
3.1. Oligomer synthesis
Six-armed bio-based epoxy resin was prepared through a two-step route by using linoleic acid and HMM as the starting materials. As depicted in Scheme 1, the six-armed unsaturated oligomer, HL, was constructed through an esterification reaction between linoleic acid and HMM in the presence of DCC and DMAP. The acid to hydroxyl ratio was set at 1.5
:
1.0 to avoid the formation of partially esterified products. The excess linoleic acid was easily removed through washing with ethanol. Successful esterification reaction was evidenced by a new peak near 5.8 ppm in the 1H NMR spectrum of HL (Fig. 1), which was attributed to the protons on the methylene carbons beside the amino nitrogen atoms. The protons on the methylene carbons adjacent to the carbonyl groups also shifted from 2.39 (for linoleic acid) to 2.27 ppm (for HL). In the 13C NMR spectrum (Fig. S2†), the peaks near 173 and 166 ppm were attributed to the linoleoyl carbons and the carbons of triazine segments, respectively. The peaks near 127–130 ppm corresponded to the double bond carbons. Furthermore, the molecular mass of HL (m/z 1904 [M + Na+]), measured through MALDI-TOF MS, matched the theoretical value, further confirming the complete esterification of the hydroxyl groups.
 |
| Scheme 1 Synthetic route to epoxidized hexa (linoleoyl hydroxymethyl) melamine and the structures of bio-based epoxy resins in this work. | |
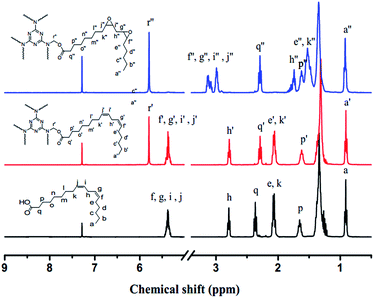 |
| Fig. 1 1H NMR of bio-based epoxy resin and its intermediates. | |
The unsaturated oligomer was then epoxidized with H2O2 in the presence of acetic acid and a strong acid ion exchanger resin. In the 1H NMR spectrum, peaks near 5.2–5.5 ppm, which were related to the unsaturated protons, disappeared after epoxidation. New peaks appeared near 2.9–3.2 ppm, indicating of epoxy functionality. In the 13C NMR spectrum, new peaks appeared at 54–57 ppm, which were attributed to epoxy carbons. Successful epoxidation was also evidence by the disappearance of the peaks near 3010 cm−1 (C
C–H function), as well as the new bands near 830 cm−1 (epoxy groups) in FT-IR spectra (Fig. 2). Furthermore, the MALDI-TOF MS results indicated that the molecular mass for EHL was m/z 2095 [M + Na+], which was in good agreement with the calculated value.
 |
| Fig. 2 FT-IR spectra of unsaturated resin, epoxy resin and representative thermosets. | |
The physical and chemical properties of HL and EHL, including IV, EEW, bio-based content, viscosity, and density, were characterized. The results were presented with ESO and ESS in Table 1 for comparison. The bio-based contents for HL and EHL were 92.3%, which was slightly lower than those of ESO and ESS. The IVs of EHL and ESS were lower than 5 after epoxidation reactions, which was indicative of the completion of epoxidation. Based on IVs before and after epoxidation, the double bond to epoxide conversion was nearly 97% for EHL. As evidenced by its lower EEW value, the epoxy content of EHL was higher than those of ESO and ESS because of its higher degree of unsaturation. However, EHL and ESS had similar epoxy functionality because EHL contained fewer fatty acid chains per molecule than ESS (6 versus 7.7). The density of EHL was also higher than those of ESO and ESS, which can be explained by the higher density of HMM (1.82 g cm−3) compared with glycerol (1.30 g cm−3) or sucrose (1.59 g cm−3). EHL was a waxy solid at room temperature, and more viscous than ESS and ESO, which can be attributed to its symmetric architecture, and its aromatic triazine core. EHL was compatible with the hardener, MHHPA, and the epoxy-anhydride formulation was a liquid at room temperature.
Table 1 Properties of bio-based unsaturated and epoxy resins
Oligomer |
Bio-based contenta (%) |
EEWb (g eq.−1) |
Iodine valuec |
Viscosityd (mPa s) |
Densitye (g cm−3) |
Calculated according to a method in the literature.21 Epoxy equivalent weight, determined according to ASTM D 1652. Measured according to GB/T5532-2008. Measured using a rheometer at 25 °C. Measured at 25 °C. Measured at 50 °C since EHL is a waxy solid at room temperature. |
HL |
92.3 |
|
143 |
700 |
0.974 |
EHL |
92.3 |
204 |
4.7 |
1190f |
1.042 |
SS |
100 |
|
127 |
316 |
0.942 |
ESS |
100 |
248 |
1.3 |
1110 |
1.005 |
ESO |
100 |
238 |
|
254 |
0.983 |
3.2. Curing of epoxy-anhydride thermosets
The epoxy-anhydride thermosets were cured at 95 °C in the presence of DBU. The curing extent was characterized through DSC and gel content measurements. The representative DSC cures for the uncured resin EHL_MHHPA_0.6 and resins cured at 95 °C for 12 and 48 hours are displayed in Fig. 3. The peak temperatures of exotherm (Tp) ranged from 165 °C to 178 °C. The Tp values of EHL were slightly lower than those of ESS and ESO, which can be contributed to the higher epoxide content of EHL. The total reaction heat for curing (ΔH0) and the residue heat after curing at 95 °C for 48 hours (ΔH1) were calculated according to the integral of the exothermic peaks in the DSC curves, the results of which are summarized in Table 2. As expected, the ΔH0 values increased with the epoxide content and epoxy-anhydride ratios. The curing extent (αt) values were approximately 80% after curing for 12 hours (Fig. 3). With 48 hours of curing, these thermosets achieved 97.5–99.4% (Table 2).
 |
| Fig. 3 Representative DSC curves of uncured bio-based epoxy-anhydride thermosets and thermosets cured at 95 °C for 12 and 48 hours. | |
Table 2 Curing of bio-based epoxy-anhydride thermosets
Formulation |
Tpa (°C) |
ΔH0b (J g−1) |
ΔH1c (J g−1) |
Degree of cured (%) |
Gel contente (%) |
Peak temperature of first scan in DSC curves of uncured formulation. Total heat of reaction determined by DSC. Residue heat after cured at 95 °C for 48 hours. Conversion after cured at 95 °C for 48 hours, calculated by ratios between total heat of reaction and residue heat. Gel contents after cured at 95 °C for 48 hours. |
ESO_MHHPA_0.4 |
178 |
121.6 |
0.9 |
99.3 |
95.2 |
ESS_MHHPA_0.4 |
177 |
116.0 |
1.1 |
99.1 |
97.7 |
EHL_MHHPA_0.4 |
167 |
182.4 |
4.6 |
97.5 |
98.7 |
EHL_MHHPA_0.5 |
172 |
214.5 |
2.9 |
98.7 |
96.6 |
EHL_MHHPA_0.6 |
165 |
317.5 |
1.8 |
99.4 |
97.4 |
The gel contents of these thermosets were higher than 95% after curing at 95 °C for 48 hours, indicating the completion of curing reactions. The curing of the epoxy resins was also evidenced by the FTIR results (Fig. 2). The characteristic peaks near 1860 and 1790 cm−1, corresponding to the stretching of carbonyl groups in MHHPA, completely disappeared from the FTIR spectrum of the thermoset (Fig. S3†).
3.3. Properties of epoxy-anhydride thermosets
3.3.1. Bio-based content. The bio-based content was defined as the percentage of bio-based carbons in the total organic carbons of the materials. In epoxy-anhydride formulations, linoleic acid was bio-based chemicals, while MHHPA and HMM were petroleum-based ones. The bio-based contents of these thermosets were estimated according to a previous study,21 the results of which are listed in Table 3. The bio-based contents of these thermosets were up to 70%, which is considerably higher than the minimum requirement for bio-based materials (25%).
Table 3 Bio-based contents, cross-link densities, and thermal properties of bio-based epoxy-anhydride thermosets
Formulations |
Bio-based contenta (%) |
Tgb (°C) |
T5%c (°C) |
ve (10−3 mol mm−3) |
Calculated according to a method in the literature.21 Determined by DMTA with a heating rate of 3 °C min−1. Determined by TGA in air with a heating rate of 15 °C min−1. |
ESO_MHHPA_0.4 |
80.2 |
4.6 |
351 |
0.25 |
ESS_MHHPA_0.4 |
80.2 |
50.4 |
336 |
1.01 |
EHL_MHHPA_0.4 |
70.3 |
77.8 |
316 |
0.99 |
EHL_MHHPA 0.5 |
66.4 |
81.7 |
259 |
1.11 |
EHL_MHHPA_0.6 |
62.8 |
91.6 |
246 |
1.74 |
3.3.2. DMTA. The glass transition temperature (Tg) and crosslinking density (ve) were characterized through DMTA, the results of which are summarized in Table 3. Fig. 4 shows the temperature dependence of the storage modulus and tan
δ for the bio-based epoxy-anhydride thermosets. The ranges of the glass transitions for these thermosets were very broad, indicating a large distribution of relaxation times. This can be explained by the heterogeneity of the thermosets stemmed from the structural complexity of fatty acids. The Tg values of these thermosets were in the order of EHL_MHHPA_0.6 > EHL_MHHPA_0.5 > EHL_MHHPA_0.4 > ESS_MHHPA_0.4 > ESO_MHHPA_0.4, ranging from 4.6 °C to 91.7 °C. EHL_MHHPA_0.6 showed the highest Tg value (91.7 °C), which is considerably high for epoxy-anhydride thermosets derived from vegetable oils. The cross-link densities of EHL_MHHPA_0.4 and ESS_MHHPA_0.4 were very similar to each other because of their similar functionalities. However, EHL_MHHPA_0.4 showed markedly higher Tg value compared with ESS_MHHPA_0.4, which can be attributed to the rigidity of the aromatic core and the high cohesive energy stemmed from the inter-molecular interactions of the highly polarized triazine ring. As expected, the cross-link density values for the EHL-based thermosets increased with the equivalent of the anhydride hardener. The higher cross-link density gave rise to higher Tg values of thermosetting formulations with the increase in anhydride hardener content.
 |
| Fig. 4 DMTA curves of bio-based epoxy-anhydride thermosets. | |
3.3.3. Thermal stability. The thermal stability of the bio-based epoxy-anhydride thermosets was evaluated through TGA in air. All the polymers displayed a one-step degradation profile, with 5% weight loss temperatures of 246 °C to 351 °C. As illustrated in Fig. 5, the thermal stability of EHL-based thermosets decreased as the anhydride equivalents increased. Ester bonds were more susceptible to thermal decomposition, which accounted for the poorer stability of the thermosets with high ester concentration resulting from the higher anhydride hardener content.29,30 For a given anhydride equivalent, the EHL-based thermosets exhibited inferior thermal stability compared with the ESO- and ESS-based ones, which might be explained by the HMM core being more sensitive to thermal degradation in comparison with sucrose or glycerol cores.
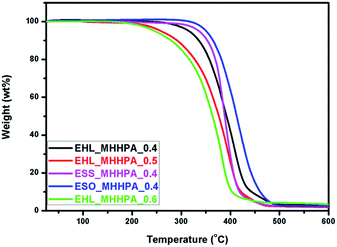 |
| Fig. 5 TGA traces of bio-based epoxy-anhydride thermosets. | |
3.3.4. Tensile properties. The mechanical properties of the bio-based epoxy-anhydride thermosets were examined through tensile testing, the results of which are summarized in Table 4. As shown in Fig. 6, the EHL-based thermosets were very brittle with very low elongation at break values (<5%). Their tensile strength and modulus values of the EHL-based thermosets were 38.5–46.7 MPa and 1570–1790 MPa, respectively. In general, their tensile strength and modulus increased with the anhydride equivalent and cross-link densities. By the contrast, the ESO- and ESS-based thermosets were more flexible, with relatively low tensile strength and modulus, but markedly higher elongation at break values (>30%). Because the EHL_MHHPA_0.4 and ESS_MHHPA_0.4 had a similar cross-link density, we concluded that the HMM core played a critical role in the mechanical properties of the resulting polymers. The rigidity and cohesive energy of HMM core, which were caused by the inter-molecular interactions of the heterocycle, were responsible for the high tensile strength and modulus of the EHL-based thermosets.
Table 4 Mechanical properties of bio-based epoxy-anhydride thermosets
Formulations |
Modulus (MPa) |
Tensile strength (MPa) |
Elongation at break (%) |
ESO_MHHPA_0.4 |
1.3 ± 0.1 |
1.2 ± 0.2 |
50.2 ± 10.3 |
ESS_MHHPA_0.4 |
90 ± 10.5 |
8.6 ± 0.5 |
39.3 ± 9.3 |
EHL_MHHPA_0.4 |
1570 ± 39.3 |
38.5 ± 2.2 |
3.3 ± 0.5 |
EHL_MHHPA_0.5 |
1700 ± 22.5 |
46.5 ± 4.8 |
4.2 ± 1.8 |
EHL_MHHPA_0.6 |
1790 ± 50.3 |
46.7 ± 5.2 |
3.1 ± 0.9 |
 |
| Fig. 6 Representative stress–strain curves of bio-based epoxy-anhydride thermosets. | |
4. Conclusion
In this study, a novel bio-based six-armed epoxy resin (EHL) was developed through a two-step procedure by using linoleic acid and HMM as the raw materials. The double bond to epoxide conversion was approximately 97% for EHL, as indicated by the IV titrations. Bio-based epoxy-anhydride thermosets were then produced using EHL and MHHPA in the presence of DBU; the thermosets were systematically evaluated according to their curing extent, and thermal and mechanical properties. Compared with ESO- and ESS-based counterparts, the thermal and mechanical properties of the EHL-based thermosets were markedly improved because of the rigidity and cohesive energy stemmed from inter-molecular interactions of the triazine ring. EHL-based thermosets possessed bio-based content of 62.8–70.3%, Tg values of 77.8–91.6 °C, tensile strength of 38.5–46.7 MPa, modulus of 1.57–1.79 GPa, and elongation at break values of 3.1–4.2%. Because of a combination of remarkable overall properties and reasonably high bio-based content, the EHL and its thermosets show considerably potential as the matrix for fiber-reinforced composites, replacing petroleum-based epoxy resins and thermosets. This study provides new insights on how to achieve high performance bio-based thermosets without comprising their bio-based contents.
Acknowledgements
The authors thank the National Science Foundation of China (No. 21304093) and MOE & SAFEA for the 111 Project (B13025) for their financial supports.
References
- E. M. Petrie, Epoxy Adhesive Formulations, McGraw-Hill, New York, 2006 Search PubMed
. - J. P. Pascault and R. J. J. Williams, Epoxy Polymers: New materials and Innovations, Wiley-VCH, Weinheim, Germany, 2010 Search PubMed
. - J. C. O'Connor and R. E. Chapin, Pure Appl. Chem., 2003, 75, 2099–2123 CrossRef
. - H. Okada, T. Tokunaga, X. Liu, S. Takayanagi, A. Matsushima and Y. Shimohigashi, Environ. Health Perspect., 2008, 116, 32–38 CrossRef CAS PubMed
. - F. S. vom Saal and C. Hughes, Environ. Health Perspect., 2005, 113, 926–933 CrossRef CAS PubMed
. - A. M. Nelson and T. E. Long, Polym. Int., 2012, 61, 1485–1491 CrossRef CAS
. - R. Auvergne, S. Caillol, G. David, B. Boutevin and J. Pascault, Chem. Rev., 2014, 114, 1082–1115 CrossRef CAS PubMed
. - J. M. Raquez, M. Deleglise, M. F. Lacrampe and P. Krawczak, Prog. Polym. Sci., 2010, 35, 487–509 CrossRef CAS
. - M. N. Belgacem and A. Gandini, Monomers, Polymers and Composites from Renewable Resources, Elsevier Science Publisher, Amsterdam, 2008 Search PubMed
. - J. A. Galbis, M. G. García-Martín, M. V. de Paz and E. Galbis, Chem. Rev., 2016, 116, 1600–1636 CrossRef CAS PubMed
. - I. Delidovich, P. J. C. Hausoul, L. Deng, R. Pfützenreuter, M. Rose and R. Palkovits, Chem. Rev., 2016, 116, 1540–1599 CrossRef CAS PubMed
. - B. M. Upton and A. M. Kasko, Chem. Rev., 2016, 116, 2275–2306 CrossRef CAS PubMed
. - A. Gandini, T. M. Lacerda, A. J. F. Carvalho and E. Trovatti, Chem. Rev., 2016, 116, 1637–1669 CrossRef CAS PubMed
. - M. A. R. Meier, J. O. Metzger and U. S. Schubert, Chem. Soc. Rev., 2007, 36, 1788–1802 RSC
. - Y. Xia and R. C. Larock, Green Chem., 2010, 12, 1893–1909 RSC
. - R. Wang and T. Schuman, in Green Materials from Plant oils, ed. Z. Liu and G. Kraus, The Royal Society of Chemistry, Cambridge UK, 2015, ch. 9, pp. 202–241 Search PubMed
. - J. Xin, P. Zhang, K. Huang and J. Zhang, in Soy-based Chemicals and Materials, ed. R. P. Brentin, American Chemical Society, Washington D. C, 2014, ch. 13, pp. 304–313 Search PubMed
. - S. Ma and D. C. Webster, Macromolecules, 2015, 48, 7127–7137 CrossRef CAS
. - C. Kovash, E. Pavlacky, S. Selvakumar, M. P. Sibi and D. C. Webster, ChemSusChem, 2014, 7, 2289–2294 CrossRef CAS PubMed
. - X. Pan and D. C. Webster, Macromol. Rapid Commun., 2011, 32, 1324–1330 CrossRef CAS PubMed
. - X. Pan, P. Sengupta and D. C. Webster, Biomacromolecules, 2011, 12, 2416–2428 CrossRef CAS PubMed
. - X. Pan, P. Sengupta and D. C. Webster, Green Chem., 2011, 13, 965–975 RSC
. - S. Alam, H. Kalita, A. Jayasooriya, S. Samanta, J. Bahr, A. Chernykh, M. Weisz and B. J. Chisholm, Eur. J. Lipid Sci. Technol., 2014, 116, 2–15 CrossRef CAS
. - S. Alam and B. Chisholm, J. Coat. Technol. Res., 2011, 8, 671–683 CrossRef CAS
. - R. Wang and T. Schuman, eXPRESS Polym. Lett., 2013, 7, 272–292 CrossRef CAS
. - R. Wang, T. Schuman, R. R. Vuppalapati and K. Chandrashekhara, Green Chem., 2014, 16, 1871–1882 RSC
. - G. Lligadas, J. C. Ronda, M. Galia and V. Cadiz, J. Polym. Sci., Part A: Polym. Chem., 2006, 44, 6717–6727 CrossRef CAS
. - K. Huang, P. Zhang, J. Zhang, S. Li, M. Li, J. Xia and Y. Zhou, Green Chem., 2013, 15, 2466–2475 RSC
. - H. A. Pohl, J. Am. Chem. Soc., 1951, 73, 5660–5661 CrossRef CAS
. - A. P. Gupta, S. Ahmad and A. Dev, Polym.-Plast. Technol. Eng., 2010, 49, 657–661 CrossRef CAS
.
Footnote |
† Electronic supplementary information (ESI) available. See DOI: 10.1039/c6ra09077j |
|
This journal is © The Royal Society of Chemistry 2016 |
Click here to see how this site uses Cookies. View our privacy policy here.