DOI:
10.1039/C6RA10042B
(Paper)
RSC Adv., 2016,
6, 69836-69844
Tribological properties of oleic acid-modified zinc oxide nanoparticles as the lubricant additive in poly-alpha olefin and diisooctyl sebacate base oils†
Received
18th April 2016
, Accepted 14th July 2016
First published on 15th July 2016
Abstract
Oleic acid (OA) modified ZnO nanoparticles with an average size of 4.04 nm were prepared via a facile in situ one-step route. The as-prepared ZnO nanoparticles were characterized by X-ray diffraction, transmission electron microscopy, and Fourier transform infrared spectroscopy. The light-absorbing performance and thermal stability of the as-prepared ZnO nanoparticles were evaluated by ultraviolet-visible light spectrophotometry and thermogravimetric analysis, and their tribological behaviour as the lubricant additive in poly-alpha olefin (PAO) and diisooctyl sebacate (DIOS) base oils was evaluated with a four-ball machine. The surface morphology of the wear scar was observed with a scanning electron microscope and a three-dimensional optical profiler, and the element composition of the wear scar was determined by energy dispersive spectrometry. It was found that the surface-capping of ZnO nanoparticles by OA helps to greatly increase their dispersibility and thermal stability. In the meantime, OA-modified ZnO nanoparticles can effectively improve the antiwear and friction-reducing abilities as well as the load-carrying capacity of the base oils, which is due to the formation of a tribofilm in association with the tribo-sintering and/or adsorption of the additives on the rubbed steel surfaces. Furthermore, the friction-reducing and antiwear performances of the as-prepared ZnO nanoparticles as lubricating oil additives seem to be closely related to the polarity of the base oils. Namely, the OA-modified ZnO additive exhibits better tribological behaviour in apolar PAO than in polar DIOS.
Introduction
In recent years, the use of nanoparticles in tribology has received more and more attention, thanks to their unique antiwear and friction-reducing properties as well as high load-carrying capacity.1–3 Various nanolubricants, including metal nanoparticles,4–6 metallic compound nanoparticles7–15 and nanostructures have been reported. As a representative metallic compound nanolubricant, dialkyldithiophosphate (DDP)-modified copper exhibits good friction-reducing and antiwear abilities.16,17 However, copper is easily oxidized, and DDP contains sulphur and phosphorus which may pollute ecological environments and cause troubles to the exhaust gas-treatment systems of automobiles.18–21 Therefore, many researchers have made great efforts to develop new lubricant additives to replace sulphur- and phosphorus-containing lubricant additives.22–24
Among various nanolubricants, metallic oxides with compact and stable structure as well as good thermal stability may be promising green lubricant additives. Nanoscale ZnO (nano-ZnO) is an example of the so-called nanolubricants, and it is of significance with large surface area, high surface energy, strong adsorption, high diffusion, easy sintering, low melting point, good tribological properties. Particularly, nano-ZnO, free of sulphur and phosphorus, is environment-friendly.25,26 S. M. Alves et al. observed that ZnO nanoparticles exhibit good friction-reducing and antiwear abilities.27 A. Hernandez Battez et al. studied the tribological properties of ZnO (20 nm) nanoparticles as an additive in polyalpha olefin (PAO) base oil and found that ZnO nanoparticles can form tribofilms thereby showing excellent tribological properties.28 Qian et al. reported that ZnO (125 nm) prepared by homogeneous precipitation method in the presence of lauryl sodium sulfate (SDS) as the surfactant can effectively reduce friction and wear under boundary lubrication condition.25
It has been well recognized that the tribological properties of nanoparticles as the lubricant additives are closely related to their size. Usually, nanoparticles with a small size could exhibit better tribological properties, because they are easier to fill up micropits and grooves on worn steel surfaces to form a compact protective layer thereon.6 ZnO nanoparticles with a small size, however, are inherently unstable and tend to agglomerate in the lubricant base oils. To deal with this issue, many researchers made use of surface-modification technique to obtain stable dispersions of nanoparticles in lubricant base oils thereby effectively inhibiting their agglomeration. The resultant surface-capped nanoparticles as lubricant additives could find promising application in industry. This is because the in situ surface-modification with a variety of organic molecules can greatly improve the dispersibility of inorganic nanoparticles in various organic mediums.29–31
Among various lubricant base oils, synthetic base oils such as poly alpha olefin (denoted as PAO) and diisooctyl sebacate (denoted as DIOS) are of special significance, because they exhibit better thermal stability and antioxidant ability than mineral and vegetable oils.32–34 In the present research we focus on the influence of oleic acid (denoted as OA) modified ZnO nanoparticles on the tribological properties of DIOS (a common synthetic lubricant with polar functional group), and we place the emphasis on the comparative investigation of the tribological effects of OA-modified ZnO nanoparticles in non-polar PAO and polar DIOS lubricant base oils. This paper reports the preparation of size-controllable OA-modified ZnO nanoparticles by one-step method and their tribological properties as the additives in PAO and DIOS under boundary lubricating conditions. Moreover, the action mechanisms of OA-modified ZnO nanoparticles are also discussed in relation to the characterization of the tribofilms formed on rubbed metallic surfaces by scanning electron microscopy, energy dispersive spectrometry and three-dimensional surface profilometry.
Experimental
Chemicals
Sodium oleate was purchased from Aladdin Industrial Corporation (Shanghai, China). All other reagents of analytical grade were provided by Tianjin Kemiou Fine Chemical Reagent Company Limited (Tianjin, China). The structures of PAO and DIOS are shown in Fig. S1 and S2,† respectively. All the chemicals were used without further purification, and distilled water was used as the solvent and for washing as well.
Preparation of zinc oleate precursor and OA-modified ZnO nanoparticles
Zinc oleate precursor, Zn[CH3(CH2)7CH = CH(CH2)7COO]2, was prepared by ion exchange reaction between zinc chloride and sodium oleate.35 Briefly, 5.0 mmol zinc chloride and 10.0 mmol sodium oleate were mixed in the solvent consisting of 10 mL ethanol, 17.5 mL n-hexane and 7.5 mL deionized water. The mixture was loaded into a three-neck flask equipped with a condenser and a thermometer and refluxed at 80 °C for 2.5 h to allow the upper organic layer consisting of n-hexane to turn yellowish upon heating. At the end of heating, the mixed solution was naturally cooled to room temperature and stored in a refrigerator at 0 °C for 4 h to allow the upper organic layer consisting of n-hexane to turn white (such a change in the solution colour clearly indicates the formation of zinc oleate). The resultant solution was separated with a separation funnel to afford zinc oleate crude product, and the crude product was repeatedly washed with excess warm distilled water to remove unreacted metal salts, followed by drying for 5 h in a vacuum-freeze dryer to afford zinc oleate powder.
OA-modified ZnO nanoparticles were prepared with reference to the method for directly preparing oxide nanoparticles from organometallic precursor.36–40 Briefly, 0.8 mmol zinc oleate was dissolved in 15.0 mL tetrahydrofuran under magnetic stirring to afford a colourless solution. Then 0.52 mL ammonium hydroxide was added into the mixed solution, and the mixed solution was kept at 50 °C for 12 h to slowly turn into white. At the end of the reaction, the precipitate (i.e., the crude product of ZnO nanoparticles), was collected with rotary steam and fully washed with distilled water and absolute ethanol, followed by drying for 5 h in a vacuum-freeze dryer to afford white powders as the desired final product. The formation of OA-modified ZnO is schematically illustrated in Scheme 1.
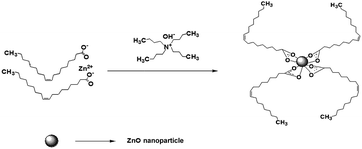 |
| Scheme 1 Representative procedure for the preparation of OA-modified ZnO nanoparticles. | |
Characterization of OA-modified ZnO nanoparticles
The OA-modified ZnO nanoparticles prepared by the simple one-step method were characterized by X-ray diffraction XRD, Philips X′ Pert Pro X-ray diffractometer (Cu-Kα radiation, wavelength = 0.154 nm), Fourier transform infrared spectrometry (FT-IR, AVATAR360FT-IR spectrometer), and transmission electron microscopy (TEM, JEOL JEM-2010 transmission electron microscope; accelerating voltage: 200 kV). Their light-absorbing performance and thermal stability were determined by ultraviolet-visible light (UV-vis) absorption spectrometry and thermogravimetric analysis (TGA, about 5 mg of the to-be-tested samples was heated from 25 °C to 800 °C at a heating rate of 10 °C min−1 in flowing nitrogen), respectively. A drop of the dispersion of OA-modified ZnO nanoparticles in absolute alcohol was dripped onto a copper grid covered by carbon film and then fully dried at ambient temperature to afford the sample for TEM analysis. Moreover, the as-prepared OA-modified ZnO nanoparticles were mixed with KBr powder and pressed into a pellet to provide the samples for FT-IR measurement (background correction was made with blank KBr pellet as the reference).
Friction and wear test as well as scanning electron microscopy and energy dispersive spectrometry analyses of worn steel surfaces
The tribological properties of the as-prepared OA-modified ZnO nanoparticles as the lubricant additives in PAO and DIOS were evaluated with an MSR-10A four-ball apparatus made by Jinan Testing Machine Factory (Jinan, China). As-synthesized OA-modified ZnO nanoparticles were dispersed in the lubricant base oils at pre-selected mass fractions under magnetic stirring and then introduced to the contacting zone of the frictional pair by single dripping. GCr15 bearing steel (SAE-52100) balls with a diameter of 12.7 mm and a hardness of HRC 61–64 were purchased from Shanghai Bearing Factory (Shanghai, China) and used to assemble the frictional pair. Before and after each test, the steel balls were cleaned with petroleum ether and thoroughly dried in air. According to Chinese National Standard GB/T3142-82, the friction and wear tests were conducted at a rotary speed of 1200 rev min−1, an ambient temperature of about 75 °C and a duration of 60 min. The friction and wear tests under each pre-set condition were repeated three times so as to minimize data scattering. The friction coefficient (COF) was automatically recorded by a computer connected to the friction and wear tester, and the wear scar diameter (WSD) on the three lower balls was measured with a digital microscope (resolution: 0.001 mm) at the end of each test. The average friction coefficient and wear scar diameter are calculated and reported in this paper.
Upon completion of the friction and wear tests, a JSM-5600 scanning electron microscope (SEM) equipped with an energy dispersive spectrometer (EDS) attachment and a three-dimensional (3D) optical profiler (Bruker, Contour GT-I 3D) were performed to investigate the surface morphology and composition of the tribofilm formed on the rubbed steel surfaces.
Results and discussion
Structure as well as light-absorbing performance and thermal stability
The size and morphology of OA-modified ZnO nanoparticles were analyzed by TEM. Fig. 1 shows the high resolution TEM (HRTEM) image of OA-modified ZnO nanoparticles. It can be seen that the OA-modified ZnO nanoparticles show no sign of obvious aggregation, and they display distinct lattice fringes with a lattice spacing of 0.32 nm. This, in association with corresponding selected area electron diffraction (SAED) pattern (Fig. 1c), confirms that the as-prepared ZnO nanoparticles possess polycrystalline structure. The XRD patterns shown in Fig. 2 also provide evidences to the above conclusion the main diffraction peaks at 31.77°, 34.42°, 36.25°, 47.53°,56.60°, 62.86°, 66.37°, 67.96° and 69.10° well correspond to the characteristic diffractions of (100), (002), (101), (102), (110), (103), (200), (112) and (201) planes of ZnO (JCPDS card no. 04-003-2106). Besides, the as-prepared ZnO nanoparticles have an average diameter of 4.04 nm. Therefore, we can infer that the surface modification of ZnO nanoparticles by oleate acid helps to inhibit their agglomeration and retain a relatively narrow size distribution. The reason might lie in that OA molecules anchored on the surface of ZnO nanoparticles are able to reduce the surface energy of ZnO nanoparticles thereby preventing them from agglomeration. In the meantime, oleate acid molecules anchored on the surface of ZnO nanoparticles also help to decrease the collision rate of ZnO crystal nucleus thereby retarding the growth of ZnO nanoparticles.
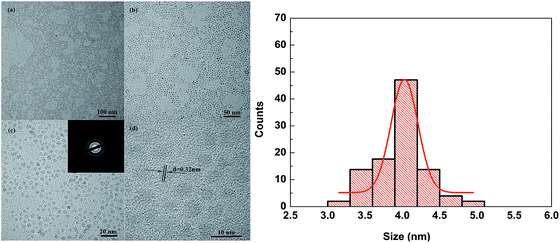 |
| Fig. 1 HRTEM images, SAED pattern and size distribution of as-prepared OA-modified ZnO nanoparticles. | |
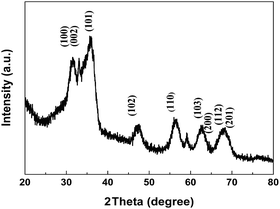 |
| Fig. 2 XRD pattern of OA-modified ZnO nanoparticles. | |
To further examine the interaction between the organic surface-modifier and ZnO nanoparticles, we conducted FTIR and TG analysis of the surface-modified ZnO nanoparticles and pure OA. Fig. 3 shows the FTIR spectra of ZnO nanoparticles, oleic acid and OA-modified ZnO nanoparticles. The C–H stretching vibration bands of –CH3 and –CH2– are located at 2927 cm−1 and 2852 cm−1, and the C–H bending vibration band appears at 1443 cm−1. Interestingly, these absorption bands of C–H are retained in OA-modified ZnO nanoparticles. Besides, oleic acid shows the characteristic peak of νCO around 1710 cm−1 as well as the absorption peak of carboxylate at 1581 cm−1.41,42 The OA-modified ZnO nanoparticles, however, do not show these two peaks, which is possibly attributed to the chemical reactions between OA and ZnO nanoparticles. The above FTIR datas prove that long alkyl chains have been successfully introduced onto the surface of ZnO nanoparticles to afford OA-modified ZnO nanoparticles.
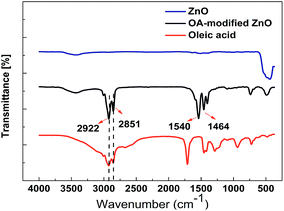 |
| Fig. 3 FT-IR spectra of oleic acid, ZnO nanoparticles and OA-modified ZnO nanoparticles. | |
Fig. S3† shows the TGA curve of as-prepared OA-modified ZnO nanoparticles. It can be seen that as-synthesized ZnO nanoparticles lose about 80% of weight in the temperature range of 25–600 °C. The slow weight loss within 25–250 °C corresponds to the volatilization of a small amount of tetrahydrofuran and oleic acid physically adsorbed on the surface of ZnO nanoparticles. The rapid weight loss around 363.7 °C is due to the decomposition of chemically adsorbed OA molecules; and the weight loss around 410.7 °C is possibly due to the elimination of decomposed residuals.
Fig. S4† shows the UV-vis absorption spectrum of as-prepared ZnO nanoparticles. It is seen that as-prepared ZnO nanoparticles display UV-vis absorption at 355 nm. Usually, the surface plasmon absorption of metal oxide nanoparticles is due to the collective oscillation of the free conduction band electrons which are excited by the incident electromagnetic radiation. This type of resonance is related to the diameter of the particles. The sharp UV-vis peak indicates that the as-prepared OA-modified ZnO nanoparticles have a quite uniform size.
Tribological properties of OA-modified ZnO nanoparticles as the additive in PAO
Fig. 4 illustrates the friction coefficients and wear scar diameters of the steel balls lubricated by PAO containing different concentrations of OA-modified ZnO nanoparticles (load: 392 N; speed: 1200 rev min−1; time: 60 min; temperature: 75 °C). It can be seen that the OA-modified ZnO nanoparticles as the additive in PAO can effectively reduce the friction coefficient and wear scar diameter of the steel–steel pair. Namely, when the OA-modified ZnO nanoparticles are added into PAO at a concentration of 1.2% (mass fraction; the same hereafter), the best antiwear performance and friction-reducing ability are obtained: the friction coefficient is decreased from 0.106 to 0.096 and the wear scar diameter is decreased from 0.850 mm to 0.585 mm (corresponding to a reduction by 9.9% and 31.2%). However, higher concentrations of OA-modified ZnO nanoparticles in PAO are less effective in reducing the friction coefficient and wear scar diameter. It can be inferred that, at a too low additive concentration, the lubricant can hardly form a tribofilm with good coverage to prevent the direct contact of the sliding steel pairs, thereby leading to relatively high friction coefficient. When the additive concentration is too high, the as-prepared OA-modified ZnO nanoparticles would tend to form large aggregates and can hardly fill the valleys between the asperities of the sliding steel pair, thereby also yielding a relatively high friction coefficient in association with enhanced scratching and shearing.
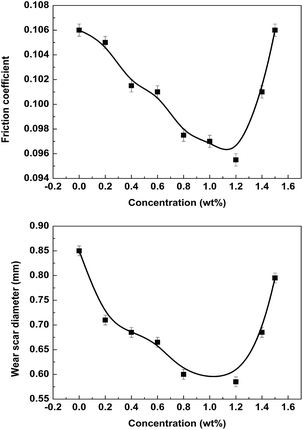 |
| Fig. 4 Variations of wear scar diameter (WSD) and friction coefficient with the concentration of OA-modified ZnO nanoparticles in PAO (load: 392 N; speed: 1200 rev min−1; time: 60 min; temperature: 75 °C). | |
Therefore, it is suggested to keep the concentration of the OA-modified ZnO nanoparticles in PAO as 1.2% in order to effectively reduce the friction and wear of the steel–steel sliding pair.
Fig. 5 shows the variations of the friction coefficient and wear scar diameter with load under the lubrication of PAO alone and PAO containing 1.20% OA-modified ZnO nanoparticles (speed: 1200 rev min−1; time: 60 min; temperature: 75 °C). It is seen that the friction coefficient decreases initially and increases later with rising load, and WSD increases monotonously therewith. On the one hand, when the load is small, the applied force concentrates on a small number of large particles thereby resulting in a higher friction coefficient owing to severe abrasion. On the other hand, when the load increases, large nanoparticles will undergo deformation to allow even distribution of the applied load on deformed particulates thereby reducing friction coefficient owing to enhanced rolling effect. Besides, as-synthesized ZnO nanoparticles can improve the antiwear ability of PAO base oil, possibly because they can be adsorbed on steel sliding surfaces to form boundary lubricating films with good antiwear ability.
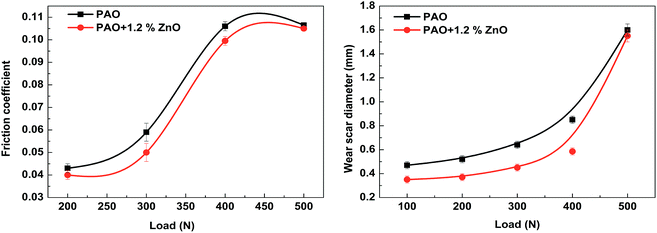 |
| Fig. 5 Variations of wear scar diameter and friction coefficient with load (speed: 1200 rev min−1; time: 60 min; temperature: 75 °C). | |
In order to investigate the wear mechanism, we observed the morphologies of the worn surfaces with SEM and 3D profile. Fig. 6 presents the SEM images of the wear scar of steel balls lubricated by PAO and PAO containing 1.20% OA-modified ZnO nanoparticles (load: 392 N; speed: 1200 rev min−1; time: 60 min; temperature: 75 °C). It can be seen that the worn steel surface lubricated by PAO alone is quite rough and shows wide and deep furrows as well as grooves along the sliding direction. Contrary to the above, the worn steel surface lubricated by PAO containing 1.20% OA-modified ZnO nanoparticles is smooth and shows few furrows and grooves, which well corresponds to the good antiwear ability of the OA-modified ZnO nanoparticles.
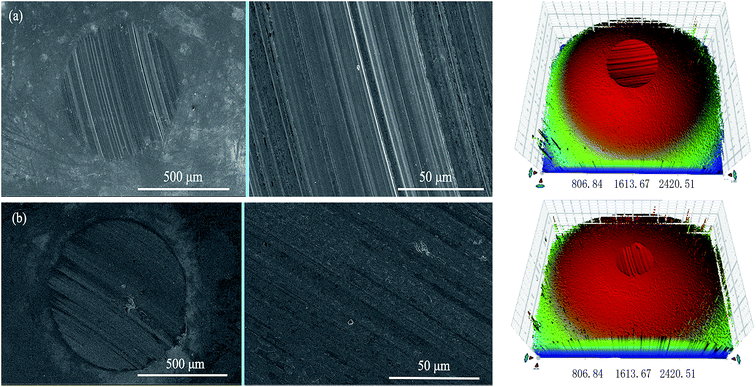 |
| Fig. 6 SEM micrographs, three-dimensional (3D) morphologies of the worn steel surface lubricated by (a) PAO and (b) PAO/OA-modified ZnO nanoparticles (1.20%; load: 392 N; speed: 1200 rev min−1; time: 60 min; temperature: 75 °C). | |
The 3D profiles of the worn steel surfaces lubricated by PAO and PAO containing 1.20% OA-modified ZnO nanoparticles are shown in Fig. 6 (load: 392 N; speed: 1200 rev min−1; time: 60 min; temperature: 75 °C). It can be seen that the wear scar under the lubrication of PAO alone is quite larger than the one under the lubrication of PAO with 1.20% OA-modified ZnO nanoparticles. This well corresponds to the observation that the OA-modified ZnO nanoparticles as the additive can effectively improve the tribological properties of PAO.
Tribological properties of OA-modified ZnO nanoparticles as the additive in DIOS
Fig. 7 illustrates the friction coefficients and wear scar diameters of the steel balls lubricated by DIOS containing different concentrations of as-prepared ZnO nanoparticles. Here the friction and wear tests were run under the same test conditions as that of PAO (load: 392 N; speed: 1200 rev min−1; time: 60 min; temperature: 75 °C). It can be seen that the friction coefficient and wear scar diameter of the steel–steel sliding pair gradually decrease with increasing concentration of as-prepared ZnO nanoparticles in DIOS, and higher concentrations of as-prepared ZnO nanoparticles in DIOS correspond to larger friction coefficient and wear scar diameter. The lowest friction coefficient and wear scar diameter are obtained when 0.80% of OA-modified ZnO nanoparticles is added into DIOS, at which the friction coefficient is decreased from 0.112 to 0.096 and the wear scar diameter is decreased from 0.830 mm to 0.645 mm (corresponding to a reduction by 14.5% and 22.3%). Moreover, PAO as the lubricant base oil seems to be advantageous over DIOS in reducing the friction coefficient and wear scar diameter of the steel–steel sliding pair under boundary lubrication condition (Fig. S5†). This could be because the surface modifier and DIOS compete to be adsorbed on the rubbed steel surface by way of their functional groups, thereby hindering the tribological effect of the lubricant additive. In order to evaluate the antiwear life of the OA-modified ZnO nanoparticles as the additives in PAO and DIOS, we prolonged the friction and wear test duration from 60 min to 780 min. As shown in Fig. S6,† the friction coefficient–time curve of PAO with 1.20% OA-modified ZnO nanoparticles is of less fluctuation than that of DIOS with 0.80% OA-modified ZnO nanoparticles, which well corresponds to the abovementioned observation.
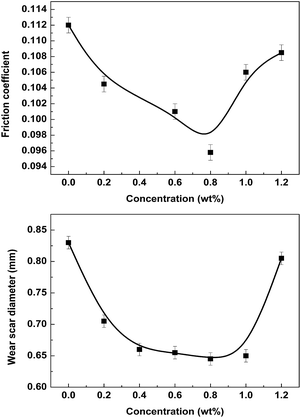 |
| Fig. 7 Variations of friction coefficient and wear scar diameter of the steel–steel sliding pair with the concentration of OA-modified ZnO concentration in DIOS (load: 392 N; speed: 1200 rev min−1; time: 60 min; temperature: 75 °C). | |
The variations in the friction coefficient and wear scar diameter with load under the lubrication of DIOS containing 0.80% OA-modified ZnO nanoparticles are shown in Fig. 8. It is seen that the as-synthesized ZnO nanoparticles can effectively improve the friction-reducing and antiwear abilities of DIOS when the load is below 400 N. This could be because the stable suspension of OA-modified ZnO nanoparticles in DIOS can be readily transferred onto the contact zone of rubbing steel surfaces and deposited thereon to form a surface protective and lubricious layer, resulting in reduced friction coefficient and wear scar diameter. As the load increases to 500 N, however, the wear scar diameter rises significantly. This means that the OA-modified ZnO nanoparticles as the lubricant additive in DIOS are unsuitable at a too high load.
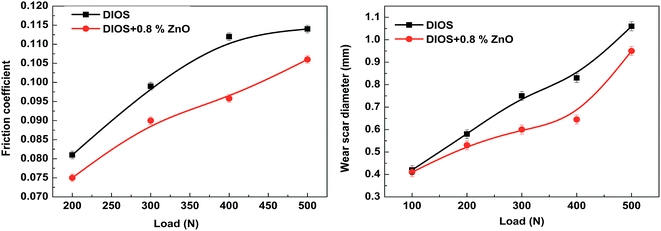 |
| Fig. 8 Variations in the friction coefficient and wear scar diameter of the steel–steel sliding pair with load under the lubrication of DIOS containing 0.80% OA-modified ZnO nanoparticles (speed: 1200 rev min−1; time: 60 min; temperature: 75 °C). | |
Fig. 9 presents the SEM images of the wear scar of steel balls lubricated by DIOS and DIOS containing 0.80% OA-modified ZnO nanoparticles (load: 392 N; speed: 1200 rev min−1; time: 60 min; temperature: 75 °C). The worn steel surface lubricated by DIOS alone is quite rough and shows wide and deep furrows as well as grooves along the sliding direction. These surface damages, however, are obviously reduced when the OA-modified ZnO nanoparticles are introduced into DIOS base oil. Particularly, the worn steel surface lubricated by DIOS containing 0.80% as-synthesized ZnO nanoparticles is quite smooth and shows few furrows and grooves, which well corresponds to good anti-wear ability of the OA-modified ZnO nanoparticles.
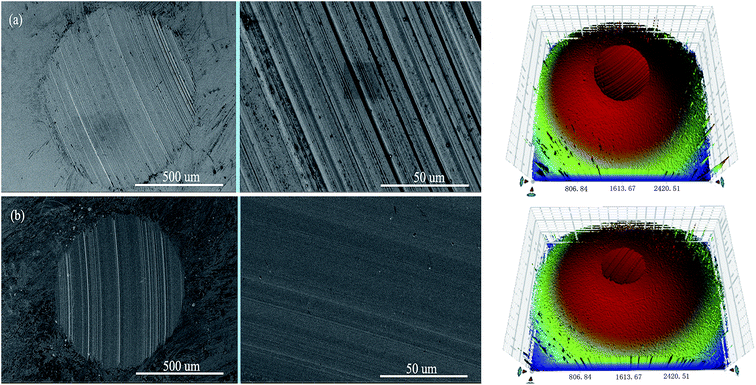 |
| Fig. 9 SEM micrographs and 3D morphologies of the worn steel surface lubricated by (a) DIOS and (b) DIOS/OA-modified ZnO nanoparticles (0.8%; load: 392 N; speed: 1200 rev min−1; time: 60 min; temperature: 75 °C). | |
The 3D profiles of the worn steel surfaces lubricated by DIOS containing 0.80% OA-modified ZnO nanoparticles are shown in Fig. 9. It can be seen that DIOS containing 0.80% OA-modified ZnO nanoparticles always provides a smaller wear scar (referring to smaller wear volume) of the steel–steel sliding pair than the DIOS base oil alone. This well corresponds to the observation that the OA-modified ZnO nanoparticles as the lubricant additive can effectively improve the tribological properties of DIOS.
Tribochemistry of OA-modified ZnO nanoparticles as the lubricant additive
The EDS spectra of the worn steel surfaces lubricated by DIOS and PAO as well as the suspensions of OA-modified ZnO nanoparticles are shown in Fig. S7† (four-ball machine; load: 392 N; speed: 1200 rev min−1; time: 60 min; temperature: 75 °C). It can be seen that, under the lubrication of PAO or DIOS alone, only iron and oxygen are detected by EDS on the rubbed steel surface. Here the former is assigned to the steel substrate, and the latter could be due to the oxide formation on the steel surface. After OA-modified ZnO nanoparticles are added into PAO or DIOS, a strong zinc peak is detected on the rubbed steel surface, which implies that the inorganic nanoparticles have been incorporated into the surface protective and lubricious layer via adsorption or deposition, thereby leading to reduced friction and wear of the steel–steel sliding pair. What should be mentioned is that, the intensity of the Zn peaks with respect to PAO–ZnO additive and DIOS–ZnO additive cannot be directly compared, because the inorganic nanoparticles exhibit different optimal concentration in the two kinds of base oils (1.20% in PAO, but 0.80% in DIOS). Table 1 lists the EDS data of the rubbed steel surfaces lubricated by different lubricants, and they basically well correspond to the EDS spectra shown in Fig. S7.†
Table 1 EDS data of the worn steel surfaces
Lubricant |
Elemental composition (wt%) |
Zn |
C |
Mn |
O |
Cr |
Fe |
Si |
PAO |
0 |
17.48 |
18.67 |
1.6 |
2.01 |
59.83 |
0.41 |
PAO + 1.2% ZnO |
9.54 |
14.00 |
1.99 |
7.91 |
14.95 |
50.75 |
0.87 |
DIOS |
0 |
12.97 |
15.32 |
6.21 |
29.42 |
36.42 |
0.15 |
DIOS + 0.8% ZnO |
3.77 |
31.89 |
15.81 |
5.71 |
24.18 |
18.46 |
0.19 |
Antiwear mechanism of OA-modified ZnO nanoparticles
It is well known that the metallic surfaces are not smooth and contain numerous asperities and valleys. Under the mixed or boundary lubricating conditions, when the lubricant film between the tribo-pairs becomes thinner, the additive may carry a proportion of load and separate the two surfaces to prevent adhesion. The size of OA-modified ZnO nanoparticles is so small that they can easily enter sliding contact and do not perturb the hydrodynamic regime. When OA-modified ZnO nanoparticles are added into the lubricant base oils, they can be easily transferred into the worn area under the compressive stress, thereby forming a self-laminating protective film in solid state to micro-polish and self-mend the friction surface.42,43 This observation is also supported by relevant EDS analysis in the present research. Namely, the existence of ZnO nanoparticles on the rubbed steel ball surfaces is confirmed by EDS analysis (see Fig. S7†), which proves that the OA-modified ZnO nanoparticles added in PAO and DIOS can be adsorbed and/or deposited on sliding steel surfaces, thereby reducing the friction coefficient and wear scar diameter of the steel–steel pair under boundary lubrication condition. The desired tribological properties of the as-prepared inorganic nanoparticles should be closely related to their surface-capping with oleic acid, because it is just such a surface-capping by OA that helps to greatly improve their dispersion and suspension stability in the lubricant base oils.
Conclusions
OA-modified ZnO nanoparticles with an average size of 4.04 nm were in situ synthesized via a simple one-step method in the presence of oleic acid as the surface-capping agent. Findings indicate that the as-prepared OA-modified ZnO nanoparticles can be well dispersed in PAO and DIOS base oils. The OA-modified ZnO nanoparticles as the lubricant additive in PAO and DIOS can effectively reduce the friction coefficient and wear scar diameter of the steel–steel sliding pair under boundary lubrication condition. This is because the OA-modified ZnO nanoparticles are easily adsorbed and/or deposited on rubbed steel surfaces to form a surface protective film thereon. Moreover, the as-prepared OA-modified ZnO nanoparticles exhibit better friction-reducing and antiwear abilities in apolar PAO than in polar DIOS, which could be related to the competitive adsorption of the surface modifier and DIOS on the rubbed steel surfaces by way of their functional groups.
Acknowledgements
The authors acknowledge the financial support provided by the Ministry of Science and Technology of China (Project of “973” plan; grant no. 2013CB632303), National Natural Science Foundation of China (Grant No. 51275154 and 51405132), Plan for Young Scientific Innovation Talent of Henan Province (Grant No. 154100510018), Innovation Scientists and Technicians Troop Construction Projects of Henan Province (Grant No. C20150011) and Natural Science Foundation of Henan Province (Grant No. 14A15006).
References
- Y. Y. Wu, W. C. Tsui and T. C. Liu, Wear, 2007, 262, 819–825 CrossRef CAS
. - M. Goto and F. Honda, Wear, 2004, 256, 1062–1071 CrossRef CAS
. - Q. Chen, S. Zheng, S. Yang, W. Li, X. Song and B. Cao, J. Sol-Gel Sci. Technol., 2012, 61, 501–508 CrossRef CAS
. - G. B. Yang, S. T. Chai, X. J. Xiong, S. M. Zhang, Y. U. Lai-Gui and P. Y. Zhang, Trans. Nonferrous Met. Soc. China, 2012, 22, 366–372 CrossRef CAS
. - G. Yang, J. Zhang, S. Zhang, L. Yu, P. Zhang and B. Zhu, Tribol. Int., 2013, 62, 163–170 CrossRef CAS
. - Y. Chen, Y. Zhang, S. Zhang, L. Yu, P. Zhang and Z. Zhang, Tribol. Lett., 2013, 51, 73–83 CrossRef CAS
. - A. H. Battez, R. González, J. L. Viesca, J. E. Fernández, J. M. D. Fernández, A. Machado, R. Chou and J. Riba, Wear, 2008, 265, 422–428 CrossRef
. - R. Gusain and O. P. Khatri, J. Mater. Chem., 2013, 1, 5612–5619 RSC
. - L. Zhang, L. Chen, H. Wan, J. Chen and H. Zhou, Tribol. Lett., 2011, 41, 409–416 CrossRef CAS
. - A. H. Battez, J. L. Viesca, R. González, D. Blanco, E. Asedegbega and A. Osorio, Wear, 2010, 268, 325–328 CrossRef
. - V. N. Bakunin, A. Y. Suslov, G. N. Kuzmina and O. P. Parenago, Lubr. Sci., 2005, 17, 127–145 CrossRef CAS
. - S. Ingole, A. Charanpahari, A. Kakade, S. S. Umare, D. V. Bhatt and J. Menghani, Wear, 2013, 301, 776–785 CrossRef CAS
. - Z. S. Hu and J. X. Dong, Wear, 1998, 216, 92–96 CrossRef CAS
. - Y. Gao, G. Chen, Y. Oli, Z. Zhang and Q. Xue, Wear, 2002, 252, 454–458 CrossRef CAS
. - Q. Xue, W. Liu and Z. Zhang, Wear, 1997, 213, 29–32 CrossRef CAS
. - J. Zhou, J. Yang, Z. Zhang, W. Liu and Q. Xue, Mater. Res. Bull., 1999, 34, 1361–1367 CrossRef CAS
. - J. Zhou, Z. Wu, Z. Zhang, W. Liu and Q. Xue, Tribol. Lett., 2000, 8, 213–218 CrossRef CAS
. - B. H. Kim, R. Mourhatch and P. B. Aswath, Wear, 2010, 268, 579–591 CrossRef CAS
. - A. M. Barnes, K. D. Bartle and V. R. A. Thibon, Tribol. Int., 2001, 34, 389–395 CrossRef CAS
. - H. Ji, M. A. Nicholls, P. R. Norton, M. Kasrai, T. W. Capehart, T. A. Perry and Y. T. Cheng, Wear, 2005, 258, 789–799 CrossRef CAS
. - H. A. Spikes, Tribol. Lett., 2004, 17, 469–489 CrossRef CAS
. - V. Jaiswal, R. B. Rastogi, R. Kumar, L. Singh and K. D. Mandal, J. Mater. Chem. A, 2014, 2, 375–386 CAS
. - H. Spikes, Lubr. Sci., 2008, 20, 103–136 CrossRef CAS
. - L. Yan, W. Yue, C. Wang, D. Wei and B. Xu, Tribol. Int., 2012, 53, 150–158 CrossRef CAS
. - J. Qian, Z. Yu, L. Wang and J. Xing, China Pet. Process. Petrochem. Technol., 2011, 13, 69–73 CAS
. - L. Gara and Q. Zou, Tribol. Trans., 2013, 52, 236–244 CrossRef
. - S. M. Alves, B. S. Barros, M. F. Trajano, K. S. B. Ribeiro and E. Moura, Tribol. Int., 2013, 65, 28–36 CrossRef CAS
. - A. H. Battez, J. E. F. Rico, A. N. Arias, J. L. V. Rodriguez, R. C. Rodriguez and J. M. D. Fernandez, Wear, 2006, 261, 256–263 CrossRef
. - V. N. Bakunin, A. Y. Suslov, G. N. Kuzmina, O. P. Parenago and A. V. Topchiev, J. Nanopart. Res., 2004, 6, 273–284 CrossRef CAS
. - M. F. Trajano, E. I. F. Moura, K. S. B. Ribeiro and S. M. Alves, Mater. Res., 2014, 17, 1124–1128 CrossRef
. - H. Huang, H. Hu, S. Qiao, L. Bai, M. Han, Y. Liu and Z. Kang, Nanoscale, 2015, 7, 11321–11327 RSC
. - A. Luksa, J. Synth. Lubr., 1990, 7, 187–192 CrossRef CAS
. - M. M. Kukovitskii, R. N. Khairullin, N. I. Sigov and T. A. Ismagilov, Chem. Technol. Fuels Oils, 1990, 26, 64–67 CrossRef
. - A. Pettersson, Tribol. Int., 2003, 36, 815–820 CrossRef CAS
. - W. S. Chiu, P. S. Khiew, D. Isa, M. Cloke, S. Radiman, R. Abd-Shukor, M. H. Abdullah and N. M. Huang, Chem. Eng. J., 2008, 142, 337–343 CrossRef CAS
. - M. L. Kahn, M. Monge, V. Collière, F. Senocq, A. Maisonnat and B. Chaudret, Adv. Funct. Mater., 2005, 15, 458–468 CrossRef CAS
. - C. L. Carnes and K. J. Klabunde, Langmuir, 2000, 16, 3764–3772 CrossRef CAS
. - M. Miguel, M. L. Kahn, M. André and C. Bruno, Angew. Chem., Int. Ed., 2003, 42, 5321–5324 CrossRef PubMed
. - A. Tamar, G. Yinyan, P. Mark, Y. Ming, K. Igor, N. Gertrude and O. Stephen, J. Phys. Chem. B, 2005, 109, 14314–14318 CrossRef PubMed
. - S. Wang, L. Feng and L. Jiang, Adv. Mater., 2006, 18, 767–770 CrossRef CAS
. - L. Wang, Z. Ming, X. Wang and W. Liu, Mater. Res. Bull., 2008, 43, 2220–2227 CrossRef CAS
. - H. Kato and K. Komai, Wear, 2007, 262, 36–41 CrossRef CAS
. - A. Rong, Y. Qiuming, Z. Luzheng, Z. Yudan, G. Xiaojing, F. Shuangqin, L. Licheng, W. Changsong, W. Ximing and L. Chang, Langmuir, 2012, 28, 15270–15277 CrossRef PubMed
.
Footnote |
† Electronic supplementary information (ESI) available. See DOI: 10.1039/c6ra10042b |
|
This journal is © The Royal Society of Chemistry 2016 |
Click here to see how this site uses Cookies. View our privacy policy here.