DOI:
10.1039/C6RA02752K
(Paper)
RSC Adv., 2016,
6, 33554-33560
Preparation and adsorption behaviour of cationic nanoparticles for sugarcane fibre modification
Received
29th January 2016
, Accepted 18th March 2016
First published on 24th March 2016
Abstract
Cationic nanoparticles with a core–shell structure and high zeta potential were prepared by two-step semi-batch emulsion polymerization and pre-emulsification technology using the cationic emulsifier hexadecyl trimethyl ammonium chloride (CTAC). The core–shell structure of the latex particles was confirmed by the TEM image and the change of mean particle size. Various influencing factors related to the adsorption of cationic latex on sugarcane fibres were investigated, including the time of adsorption, the concentration of latex, pH, temperature and ionic strength. The adsorption kinetics and thermodynamics were also studied. The obtained adsorption experimental data fit the Langmuir adsorption model well, and the maximum theoretical adsorption capacity of the nanoparticles on the sugarcane fibres reached 197.6 mg g−1. TGA analysis was used to further quantify the amount of adsorption. The water contact angle of the modified fibre was increased from 0° to 98°, compared with the untreated fibre, which indicates that the sugarcane fibres were rendered hydrophobic by the cationic nanoparticles.
1. Introduction
The polymer composites reinforced with non-green based fibres (e.g., glass, carbon, graphite and synthetic fibres) have been broadly applied in many industrial areas to accommodate the light-weight and high-strength property required for certain applications.1,2 However, with the current growing use of synthetic polymer composites, environmental issues such as waste disposal and waste removal are becoming more serious.3,4 In recent years, some green composites were developed rapidly using some cellulose-based natural fibres as reinforcements for polymeric matrices.5–8 The natural fibres based composite have certain advantages over the traditional composites such as environmental friendly nature, low cost, non-toxic, lower density and high specific strength.9–12 However, there are still concerns regarding the use of natural fibres in reinforced composites, such as poor interfacial bonding between the fibres and the thermoplastic matrix, and poor fibre dispersion within the composites because of the existence of a great number of hydroxyl groups on fibre surface, which renders the fibre highly hydrophilic and is different from the hydrophobic thermoplastic matrix.13
Since the idea of ‘particle design’ was put forward in 1980s,14 the control of micro-phase separated structure of latex particles via controlling the distribution of hetero-functional groups in their internal particles or on their surface has attracted much research interest. Various latex particles with different morphology, such as double or multi-layers structures, were obtained via special molecular design and emulsion polymerization techniques. It was found that the composite latexes also expressed the distinguished physical properties.15 Therefore, the ‘particle design’ could be used in the field of composite science and achieve more significant applications in coatings, adhesives, plastics and biomedicine fields as a novel technology.16–18 The physical properties of latex polymer film closely depend on the molecular structure, molecular weight, molecular internal and intra-chemical crosslinking network structure, size and morphology of the latex particles.19,20 The polyacrylate-based latexes are kinds of latexes being widely used due to their excellent anti-oxidation, hydrophobic property and so on. However, their physical properties, including the toughness, light fullness, water and solvent resistances of film, are relatively weak, which limit their applications. In order to further improve the performance of acrylate-based latexes, various kinds of techniques including pre-emulsification technology and latex particle design with core–shell morphology, have been developed.
Sugarcane, one of the most abundant economic plants in many places, is the main feedstock for the production of sugar as well as ethanol.21 Sugarcane bagasse is a complex and fibrous material of cane stalks left over after the crushing and extraction of the juice from the sugarcane. It is a residue (by-product) of the sugar industry and has been often used by the sugar factories themselves as fuel for the boilers. The sugarcane bagasse consists of cellulose fibre (40–45%), hemicellulose (30–35%), lignin (20–30%).22 In recent years, there has been an increasing trend towards the production of value-added products of agro-industrial residues,23 including sugarcane bagasse. Several processes and products have been reported that utilize sugarcane bagasse as a raw material.24–26 However, most of the thermoplastic polymeric matrices used for composites such as polyethylene (PE), polypropylene (PP), and polyvinyl chloride (PVC) are highly hydrophobic. Therefore, the interfacial compatibility is poor between the fibre reinforcement and matrix phase. Unmodified fibre added into the polymer matrix will make a significant reduction on impact strength of the composites due to the poor compatibility.27 The hydrophobic modification of plant fibre is one of the feasible approaches to improve the interfacial compatibility between the fibre and the non-polar thermoplastic matrix.28 Faruk et al. applied latex-modified nanocellulose for reinforcing rigid polyurethane (PU) foam.29 However, the reports on research related to modifying fibres with latex particles appear to be limited.
In this work, polymer latex having a core–shell structure as “designed particle” was prepared and used for sugarcane fibre modification. Positive-charged poly(styrene/butyl acrylate-co-glycidyl methacrylate) [P(St/BA-co-GMA)] latex with core–shell structure was synthesized in the presence of a cationic surfactant and a cationic initiator. The surface of latex bearing the resultant cationic groups (i.e., quaternary ammonium salt) promotes their strong adsorption on the surfaces of cellulose fibres which are negative-charged. The repulsion between cationic particles themselves also prevents their homocoagulation and drives the particles forming monolayer of discrete particles on sugarcane fibre surfaces. The latex particles will coalesce and form thin rubber-like or elastomeric films (at T > Tg of latex), thus rendering sugarcane fibre hydrophobic, and enhancing the compatibility between modified fibre and non-polar thermoplastic matrix. Moreover, the adsorption behaviour of cationic latex or nanoparticles on sugarcane fibre was investigated thoroughly. The modification of non-wood cellulose fibres via the adsorption of nanosized latex particles (driven by electrostatic association), followed by the filming of functional layer on the surface, has been seldom reported. This approach facilitates the scaling up of the modification and is of great potential to create the value-added non-wood fibre products. The as-modified fibres are promising for the production of biocomposites.
2. Experimental section
2.1 Materials
The bleached sugarcane fibre, obtained from sugarcane bagasse containing 40–50 wt% cellulose fibres after chemical pulping/bleaching processes, was provided by Nanning sugar industrial Corp., China. The fibres were smashed mechanically using a grinder and passed through a 100-mesh sieve after smashing to ensure the fibres with relatively small particle size and high specific area. The treated fibres were washed with deionized water three times prior to use. Styrene (St), butyl acrylate (BA), and glycidyl methacrylate (GMA) were purchased from the Aladdin Reagent Co., Ltd. (Shanghai, China), washed with alkali solution and distilled under reduced pressure before use. The emulsifier, hexadecyl trimethyl ammonium chloride (CTAC) was obtained from Sinopharm chemical reagent Co., Ltd. The initiator 2,2′-azobis(2-methylpropionamidine) dihydrochloride (AIBA) was from Aladdin Reagent Co., Ltd. (Shanghai, China). The crosslinker ethylene glycol dimethacrylate (EGDMA) was from Sigma-Aldrich. AR grade nitric acid (HNO3), potassium hydroxide (KOH), sodium chloride (NaCl) and potassium chloride (KCl) were from Guangdong Guanghua Sci-Tech Co., Ltd. China, and used as received without further purification. Deionized water was used in all the experiments.
2.2 Synthesis of cationic PSt/BA-co-GMA latex with core–shell structure
A two-step semi-batch emulsion polymerization and pre-emulsification technology were employed for constructing core–shell latex. A typical emulsion copolymerization process is described as follows.
Firstly, 30 mL of distilled water, 6 g of St, and 0.724 g of CTAC (6% of the monomer weight) were pre-emulsified for 30 min at 60 °C; followed by adding 0.030 g AIBA of initiator (0.5% of the monomer weight) dissolved in 5 mL deionized water, 0.121 g of EGDMA (1% of the monomer weight) as a cross-linker to prepare core latex. The system was purged with nitrogen for 30 min and maintained at 60 °C. The emulsion polymerization then proceeded under constant stirring at 200 rpm for 2 h in order to achieve a high conversion of the core copolymer.
Secondly, 6.070 g of BA/GMA mixed monomers at molar ratio of 3
:
1, and 0.030 g of initiator (0.5% of the monomer weight) dissolved in 5 mL deionized water were placed in funnels and dropped into the reactor within 1 h for the shell latex preparations. The emulsion polymerization was carried out at 80 °C for another 2 h after the shell monomers and initiator were dropped completely.
2.3 Testing methods
The zeta potential, mean particle size and size distribution of the latex particles were determined using NanoBrook Omni Particle Sizer and Zeta Potential Analyzer (BrookHaven, American) in 0.01 mM KCl aqueous solution. Three repeats were conduct to get an average value for each sample. The morphology of latex particle was observed using a Transmission Electron Microscope (TEM, Tecnai G2 F30 S-Twin, FEI, American) operated at 300 KV. The samples were diluted and stained with 2% phosphotungstic acid, mounted on 400-mesh carbon coated copper grids and then dried prior to observation. TEM images were recorded using Gatan 4k × 4k digital camera. The fracture surfaces of the fibre specimens, coated with gold, were observed using a Scanning Electron Microscope (SEM, S-3400N, Hitachi, Japan). Thermogravimetric analyses (TGA) were collected with a Thermoanalyzer (TGA, STA 449F3, NETZSCH, Germany). Measurements were taken under nitrogen atmosphere and using a ramping temperature profile of 10 °C min−1, within a temperature range of 25–700 °C. The hydrophobic property of modified cellulose was characterized by the contact-angle measurement (JC2000P, Shanghai power each digital technology equipment Co. Ltd., China).
2.4 Adsorption of latex on sugarcane fibre
Adsorption studies were carried out in 100 mL of fibre (10 g L−1) suspension; and proceeded with shaking at 130 rpm using a temperature-controlled shaker (SHZ-88, Shanghai Yiheng Corporation, China). Various influencing factors, including the time of adsorption, the concentration of latex, pH, temperature, and ionic strength were investigated. The concentration of the latex after filtration was measured with UV (TU-1900, Beijing Puxi Corporation) at 211 nm.30 The liner relationship between the concentration of diluted latex and the absorbance, was used as a calibration curve. And the adsorption capacity (Q) was calculated as follows: |
 | (1) |
where Q is the adsorption of the latex (mg g−1), C0 (mg L−1) is the initial concentration of latex, Ce (mg L−1) is the equilibrium concentration of latex, m is the mass of absorbent (g), and V (L) is the volume of latex solution, respectively.
3. Results and discussion
3.1 Characteristics of as-synthesized latex
Table 1 shows the relevant parameters of latex, including stability, mean particle size, polydispersity, and zeta potential. As can be seen, the latex was stable, and the mean particle size increased after the shell monomer was added, confirming that the particles of latex possess core–shell structure, in which cores formed first, followed by the formation of the shell layer. In addition, the core and core–shell particles have narrow distribution or the latex tends to be monodispersed with the introduction of BA and GMA, according to polydispersity analysis (PDI = 0.051). The zeta potential became higher after the shell monomer was added since the cationic emulsifier concentration was increased accordingly (the amount of emulsifier was maintained at 6.0 wt% relative to the total amount of monomers).
Table 1 Relevant parameters of latex
St(core) : BA : GMA(shell) (mol : mol) |
Mean particle size (nm) |
PDI |
Zeta potential (mV) |
5 : 0 : 0(core only) |
48.9 |
0.073 |
32.2 |
5 : 3 : 1 |
57.2 |
0.051 |
47.6 |
The morphology of latex, revealed by TEM, is presented in Fig. 1. Clearly, the image indeed demonstrated the core–shell structure of latex with the dark edges for shell. The particles distribution in TEM appears to be uniform. The soft shell has low glass transition temperature (Tg) and promotes the filming of the latex on fibre after adsorption and drying processes.
 |
| Fig. 1 TEM image corresponding to core–shell particles. | |
3.2 Effect of pH and ionic strength on latex property and adsorption on fibre
As can be seen from Table 2, the size of latex particle was increased significantly at pH 10 or above, indication the aggregation of particles or instability of the emulsion, due to the lowering of the zeta potential of latex (see Table 2). The effect of pH on the adsorption of latex on sugarcane fibre surface was investigated in the pH range of 2.0–12.0. As seen in Table 2, the adsorption capacity considered in this study remained almost constant in the pH range from 2.0 to 8.0 (the pH of fibre suspension alone without additives was 6.53). At pH 12.0, the adsorption capacity was very lowered due to the agglomeration of latex itself and the weak electrostatic interactions between latex and fibre.
Table 2 Effect of pH on latex particle size, zeta potential and the adsorption of latex on fibre
pH |
Mean particle size (nm) |
Zeta potential (mV) |
Adsorption amount of latex on fibre (mg g−1) |
2 |
52.9 |
45.1 |
154.1 |
4 |
53.9 |
46.7 |
163.9 |
6 |
54.7 |
47.8 |
170.1 |
6.5 |
57.2 |
47.6 |
170.2 |
8 |
54.8 |
32.4 |
169.0 |
10 |
90.2 |
20.8 |
112.3 |
12 |
181.0 |
2.5 |
12.3 |
Table 3 shows the influence of NaCl concentration (or ionic strength) on the adsorption of latex on sugarcane fibre surface. Clearly, NaCl decreased adsorption capacity of latex on sugarcane fibre surface at 0.1 M or above. At such concentrations, the stability of latex particles was also destroyed or the emulsion was broken. When the ionic strength was increased, the electrical double layer surrounding latex particle surface was compressed. The lowering of latex zeta-potential tends to induce the aggregation of latex particles, thus decreasing the adsorption. Meanwhile, the reduction in the effective charge of polyelectrolyte with increasing ionic strength results from an enhanced degree of counter ions binding to the surface of fibres. Therefore, the remaining experiments were carried out without pH and ionic strength adjustment.
Table 3 Effect of ionic strength on latex particle size, zeta potential and the adsorption of latex on fibre (pH 6.5)
Concentration of NaCl (mol L−1) |
Mean particle size (nm) |
Zeta potential (mV) |
Adsorption amount of latex on fibre (mg g−1) |
0 |
57.2 |
47.6 |
170.2 |
1 × 10−4 |
56.3 |
48.3 |
167.6 |
1 × 10−3 |
58.5 |
49.9 |
166.0 |
0.01 |
54.6 |
47.6 |
168.9 |
0.1 |
136.8 |
38.8 |
124.5 |
0.5 |
534.7 |
−3.6 |
21.4 |
3.3 Adsorption rate and adsorption kinetics
The adsorption rate was determined to further investigate the dynamic adsorption process. The results in Fig. 2 indicated that the adsorption proceed rapidly in the first 6 min and reached the adsorption equilibrium afterwards. This phenomenon also further confirmed that the strong electrostatic attraction between the positively charged nanoparticles and the negatively charged sugarcane fibre surfaces.
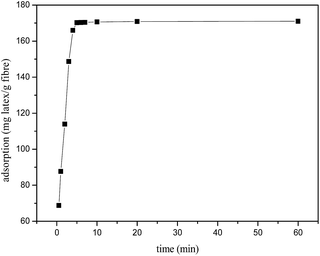 |
| Fig. 2 The adsorption rate curve of latex particles on the surface of sugarcane fibres. T = 25 °C, pH 6.53, [latex] = 2000 mg L−1, [fibre] = 10.0 g L−1. | |
There are three well-known kinetic models for the adsorption kinetics: pseudo-first-order kinetics, pseudo-second-order kinetics, and intra-particle diffusion. Linear forms are presented in eqn (2), (3) and (4), respectively.31
|
ln(qe − qt) = ln qe − k1t
| (2) |
|
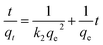 | (3) |
where
qt and
qe are the amounts of the latex adsorbed at any time
t and at equilibrium (mg g
−1), respectively.
k1,
k2 and
kp is the constant rate for the adsorption (g mg
−1 min
−1). The value of
R2 is carried out by the linear form equations. The results of adsorption kinetics, calculated from
Fig. 2 and fitted with all three models, are presented in
Table 4 and
Fig. 3.
Table 4 Adsorption kinetics of latex
Kinetics model |
qe (mg g−1) |
k1 (g mg−1 min−1) |
k2 (g mg−1 min−1) |
kp (g mg−1 min−1) |
R2 |
Pseudo-first-order |
9.60 |
0.14 |
— |
— |
0.6052 |
Pseudo-second-order |
172.71 |
— |
1.38 × 10−2 |
— |
0.9995 |
Intra-particle diffusion |
— |
— |
— |
11.29 |
0.3448 |
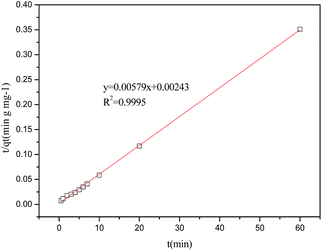 |
| Fig. 3 Pseudo-second-order adsorption kinetics on fibre. | |
As can be seen from Table 4, the adsorption of latex on fibres is better described by pseudo-second-model, where the R2 is 0.9995. The fitting results suggested that the adsorption rate was dominated by chemical adsorption, which involved the electron sharing or electron transfer between the adsorbent and the adsorbate.
3.4 Adsorption isotherms
Fig. 4 presents the adsorption isotherms of latex on sugarcane fibre surface. The latex adsorbed onto the sugarcane fibre surfaces completely in the range of latex addition (0.125–1.5 g L−1 or 1.25 to 15 wt% on fibre). Further increase in latex concentration did not further increase the amount of adsorption due to the saturation reached.
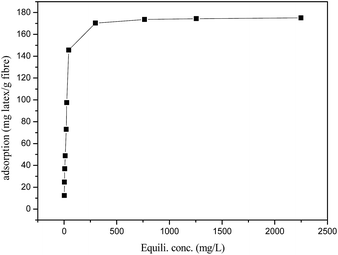 |
| Fig. 4 Adsorption isotherm of latex on sugarcane fibre surface. T = 25 °C, pH 6.53, [fibre] = 10.0 g L−1, t = 10 min. | |
The adsorption isotherm can be described as the equilibrium relationship between the adsorbate concentration in the liquid phase and on the adsorbent surface under specific conditions. There are several models describing the adsorption isotherms. In this study, Langmuir, Freundlich, and Temkin isotherm models32,33 were chosen to fit the equilibrium data.
|
 | (5) |
|
 | (6) |
|
 | (7) |
where
Qmax (mg g
−1) and
a (L mg
−1) are isotherm constants.
Ce (mg L
−1) and
qe (mg g
−1) are the concentration and adsorption capacity at the equilibrium, respectively.
Kf is roughly an indicator of adsorption capacity and
n is adsorption intensity.
A (L mg
−1) and
bT (J mol
−1) are the Temkin constants,
T is the absolute temperature, and
R is the universal gas constant 8.314 J mol
−1 K
−1.
The results of adsorption isotherm obtained from three models are shown in Table 5 and Fig. 5.
Table 5 The isotherm models for adsorption
Isotherm models |
Qmax (mg g−1) |
a (L g−1) |
Kf |
n |
A |
bT |
R2 |
Langmuir |
197.6 |
0.0361 |
— |
— |
— |
— |
0.9912 |
Freundlich |
— |
— |
1.3943 |
0.3300 |
— |
— |
0.8006 |
Temkin |
— |
— |
— |
— |
0.0586 |
36.06 |
0.9088 |
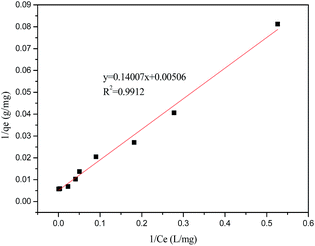 |
| Fig. 5 Linear plots of Langmuir isotherm for adsorption on sugarcane fibre at 25 °C. | |
As can be seen from Table 5, the adsorption of latex onto fibres was better described by the Langmuir isotherm, and the corresponding R2 reached 0.9912. The definition of Langmuir isotherm is monolayer sorption where all of the adsorption sites are the same and the absorbed particles are totally independent; therefore, no further sorption can take place after the saturation is reached.34 When a > 0, the sorption system is favourable. In this study, the value of a for latex is 0.0361 L mg−1. The maximum monolayer capacity (Qmax) for latex reached 197.6 mg g−1, close to the experimental data.
3.5 Effect of temperature on the adsorption efficiency and thermodynamic parameters
Fig. 6 presents the effect of temperature on the adsorption, and the adsorption capacity was enhanced while the temperature was raised. In order to further elucidate the temperature effect, thermodynamic parameters such as standard free energy change (ΔG0), standard enthalpy change (ΔH0) and standard entropy change (ΔS0) were also obtained for latex adsorption onto fibre. The Gibbs free energy change of adsorption process was calculated in terms of the following equations: |
ΔG0 = −RT ln Kd
| (8) |
|
 | (9) |
where Kd is the distribution coefficient, T is the solution temperature.
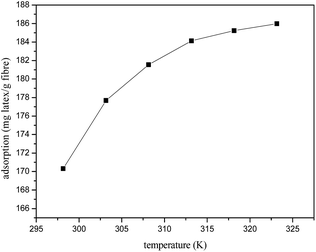 |
| Fig. 6 Effect of temperature on the adsorption of latex on fibre surface. [latex] = 2000 mg L−1, pH 6.53, [fibre] = 10.0 g L−1, t = 10 min. | |
The standard enthalpy and entropy change values of adsorption can be calculated from van't Hoff equation given as below
|
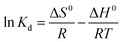 | (10) |
The results are shown in Table 6.
Table 6 Thermodynamic parameters for the adsorption
Temperature (K) |
Kd |
ΔG (kJ mol−1) |
ΔH (kJ mol−1) |
ΔS (J mol−1 K−1) |
298 |
5.72 |
−4.61 |
26.35 |
103.8 |
303 |
7.96 |
−5.13 |
308 |
9.85 |
−5.65 |
313 |
11.59 |
−6.17 |
318 |
12.54 |
−6.68 |
323 |
13.27 |
−7.20 |
As can be seen from the Table 6, the adsorption process of latex on fibres was endothermic, and ΔH0 was 26.35 kJ mol−1. The negative ΔG0 values at different temperatures indicate the spontaneous nature of the adsorption latex onto the sugarcane fibres adsorbent. In addition, the positive value of ΔS0 (103.8 J mol−1 K−1) is an indication of the strong affinity of latexes toward the sugarcane fibres adsorbent, thus verifying the strong adsorption of latex on fibre from a thermodynamic point of view.
3.6 Characterization of modified fibre
3.6.1 Thermal analysis of modified fibres. The adsorption of cationic latex onto surfaces of fibre can also be confirmed by thermal analysis. As shown in Fig. 7a and b, there is only one decomposed temperature for the latex and untreated fibre, 406.1 °C and 347.2 °C respectively. However, there are two peaks for the modified fibres (Fig. 7c), Fig. 7c shows two peaks for the modified fibres, one corresponding to the fibres at 349.3 °C, and another to the polymer film formed on the surfaces of fibres at 412.1 °C. The thermostability of modified fibres was slightly improved, compared with untreated fibres. Based on the weight loss shown in Fig. 7c, the amount of latex adsorbed on fibre is estimated at approximately 16.2% (wt), which is close to the saturated adsorption amount (175 mg g−1 fibre or 14.9% wt) identified from the adsorption isotherm (see Fig. 4). Such an amount of latex is sufficient to ensure the film formation of latex on fibre surface and create hydrophobic layer.
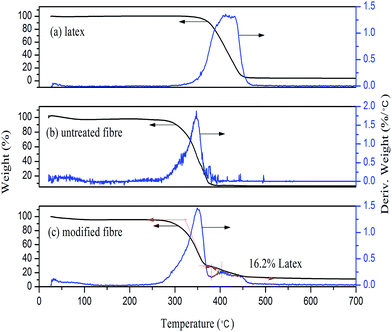 |
| Fig. 7 Thermal analysis of (a) latex (treated with alcohol), (b) untreated fibre and (c) latex modified fibre. | |
3.6.2 Contact angle test with water on modified fibre and untreated fibre. It is well known that the contact angle measurement is one of the most sensitive methods for providing information on the outer few angstroms of polymer surfaces to study the effect of latex thin films on fibre surface. The results, shown in Fig. 8, indicated that the contact angles of water on the surface of the fibres treated with latex increased dramatically, above 93° even at 5 wt% of latex addition. The high contact angle suggested that a stable hydrophobic surface of the fibres was created in the presence of the latex with core–shell structure.
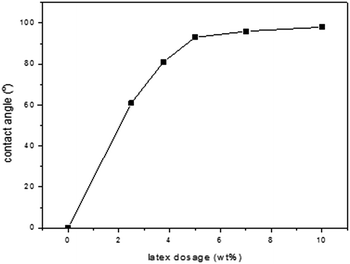 |
| Fig. 8 Contact angle of sugarcane fibres modified with latex. | |
3.6.3 Surface morphology of modified fibres. The morphology of fibres, revealed by SEM observation (Fig. 9), indicates that the layer of latex covers the fibre surface which appears to be smoother. No individual latex particles are visible on the surface, which implies the filming of the latex due to its rather low Tg. It should be addressed that the latex film could be formed either during the sample preparation for SEM observation or the drying of fibre by heating.
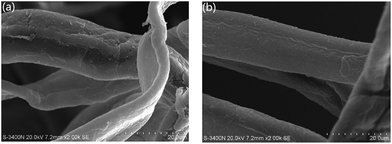 |
| Fig. 9 SEM images of surface of (a) untreated fibre and (b) latex modified fibre. | |
4. Conclusions
In this work, cationic nanosized latex with core–shell structure, prepared via an emulsion copolymerization of St/BA-co-GMA using CTAC as surfactant, was used for hydrophobic modification of sugarcane fibre. The core–shell structure of the latex particles was revealed by TEM. Adsorption of latex on sugarcane fibre surface was highly efficient due to the strong electrostatic attractive force between latex and fibre, leading to the film formation confirmed by SEM observation. The obtained adsorption experimental data were well fitted to the Langmuir adsorption model for monolayer adsorption; and the pseudo-second-model kinetics for chem-adsorption. The TGA analysis was used to further confirm the adsorption of latex on sugarcane fibre surface. The water contact angle of the modified fibre was increased significantly, indicating that the modified sugarcane fibres were successfully rendered hydrophobic.
Acknowledgements
The authors are grateful to National Natural Science Foundation of China (No. 21306027 and No. 51379077), Guangxi Natural Science Foundation (2013GXNSFCA019004); the Dean Project of Guangxi Key Laboratory of Petrochemical Resource Processing and Process Intensification Technology (2014Z003) for funding.
Notes and references
- R. Sengupta, M. Bhattacharya, S. Bandyopadhyay and A. K. Bhowmick, Prog. Polym. Sci., 2011, 36, 638–670 CrossRef CAS.
- H. T. Chu, Z. C. Zhang, Y. J. Liu and J. S. Leng, Carbon, 2016, 98, 557–566 CrossRef CAS.
- A. K. Bledzki and J. Gassan, Prog. Polym. Sci., 1999, 24, 221–274 CrossRef CAS.
- A. Hadjadj, O. Jbara, A. Tara, M. Gilliot, F. Malek, E. M. Maafi and L. Tighzert, Compos. Struct., 2016, 135, 217–223 CrossRef.
- S. H. Park, K. W. Oh and S. H. Kim, Compos. Sci. Technol., 2013, 86, 82–88 CrossRef CAS.
- H. Liu, Q. Wu and Q. Zhang, Bioresour. Technol., 2009, 100, 6088–6097 CrossRef CAS PubMed.
- S. Spoljaric, A. Salminen, N. D. Luong and J. Seppala, RSC Adv., 2015, 5, 107992–108001 RSC.
- M. Mariano, N. El Kissi and A. Dufresne, Carbohydr. Polym., 2016, 137, 174–183 CrossRef CAS PubMed.
- P. Dhar, D. Tarafder, A. Kumar and V. Katiyar, RSC Adv., 2015, 5, 60426–60440 RSC.
- J. Jayaramudu, B. R. Guduri and A. Varada Rajulu, Mater. Lett., 2009, 63, 812–814 CrossRef CAS.
- A. Lavoratti, L. C. Scienza and A. J. Zattera, Carbohydr. Polym., 2016, 136, 955–963 CrossRef CAS PubMed.
- F. W. Xie, E. Pollet, P. J. Halley and L. Averous, Prog. Polym. Sci., 2013, 38, 1590–1628 CrossRef CAS.
- S. Li, M. Xiao, A. Zheng and H. Xiao, Biomacromolecules, 2011, 12, 3305–3312 CrossRef CAS PubMed.
- M. Okubo, S. Yamaguchi and T. Matsumoto, J. Appl. Polym. Sci., 1986, 31, 1075–1082 CrossRef CAS.
- C. Xu, T. Qiu, J. Deng, Y. Meng, L. He and X. Li, Prog. Org. Coat., 2012, 74, 233–239 CrossRef CAS.
- J. Z. Ma, Y. H. Liu, Y. Bao, J. L. Liu and J. Zhang, Adv. Colloid Interface Sci., 2013, 197, 118–131 CrossRef PubMed.
- B. Foster, P. A. Lovell and M. A. Rabjohns, Polymer, 2009, 50, 1654–1670 CrossRef.
- L. Yichen, C. H. Li and D. R. Talham, Nanoscale, 2015, 7, 5209–5216 RSC.
- D. I. Lee, Polymer, 2005, 46, 1287–1293 CrossRef CAS.
- N. Fu, G. Li, Y. Yao, N. Wang, M. E. Grami, Q. Zhang and X. Qu, Mater. Des., 2015, 87, 495–500 CrossRef CAS.
- F. C. U. Santos, L. L. Paim, J. L. da Silva and N. R. Stradiottoa, Fuel, 2016, 163, 112–121 CrossRef CAS.
- P. K. Rai, S. P. Singh, R. K. Asthana and S. Singh, Bioresour. Technol., 2014, 152, 140–146 CrossRef CAS PubMed.
- F. D. Mele, A. M. Kostin, G. Guillén-Gosálbez and L. Jiménez, Ind. Eng. Chem. Res., 2011, 50, 4939–4958 CrossRef CAS.
- H. B. Feng, H. Hu, H. W. Dong, Y. Xiao, Y. J. Cai, B. F. Lei, Y. L. Liu and M. T. Zheng, J. Power Sources, 2016, 302, 164–173 CrossRef CAS.
- A. Pandey, C. R. Soccol, P. Nigam and V. T. Soccol, Bioresour. Technol., 2000, 74, 69–80 CrossRef CAS.
- A. Pereira, J. L. Akasaki, J. L. P. Melges, M. M. Tashima, L. Soriano, M. V. Borrachero, J. Monzó and J. Payá, Ceram. Int., 2015, 41, 13012–13024 CrossRef CAS.
- J. Park, S. T. Quang, B. Hwang and K. L. DeVries, Compos. Sci. Technol., 2006, 66, 2686–2699 CrossRef CAS.
- D. Lu, L. S. Dong, Z. L. Feng, H. X. Zhang, X. H. Wang and L. Q. Wang, Macromol. Chem. Phys., 1998, 199, 1709–1714 CrossRef CAS.
- O. Faruk, M. Sain, R. Franood, Y. Pan and H. Xiao, J. Polym. Environ., 2014, 22, 279–288 CrossRef CAS.
- G. Bayramoglu, B. Altintas and M. Y. Arica, Chem. Eng. J., 2009, 152, 339–346 CrossRef CAS.
- M. S. Chiou and H. Y. Li, Chemosphere, 2003, 50, 1095–1105 CrossRef CAS PubMed.
- I. Kavianinia, P. G. Plieger, N. G. Kandile and D. R. K. Harding, Carbohydr. Polym., 2012, 87, 881–893 CrossRef CAS.
- Z. Chen, W. Ma and M. Han, J. Hazard. Mater., 2008, 155, 327–333 CrossRef CAS PubMed.
- E. Errais, J. Duplay, F. Darragi, I. M'Rabet, A. Aubert, F. Huber and G. Morvan, Desalination, 2011, 275, 74–81 CrossRef CAS.
|
This journal is © The Royal Society of Chemistry 2016 |
Click here to see how this site uses Cookies. View our privacy policy here.