DOI:
10.1039/C5RA25701H
(Paper)
RSC Adv., 2016,
6, 12525-12529
High-performance supercapacitors based on graphene/MnO2/activated carbon fiber felt composite electrodes in different neutral electrolytes
Received
2nd December 2015
, Accepted 20th January 2016
First published on 25th January 2016
Abstract
Graphene/MnO2 composites are introduced into activated carbon fiber felt (ACFF) to fabricate composite textile electrodes. Their micro-structure, electrical properties and electrochemical performance for supercapacitor applications in different neutral electrolytes (1 M NaNO3 and Ca(NO3)2 aqueous solutions) have been studied. The composite electrodes have similar pore features to original ACFF textiles, but show notably enhanced electrical and electrochemical performance. The composite textile electrodes show low electrical resistance, high specific capacitance (up to 1516 mF cm−2 in neutral electrolytes) and excellent cycling stability (no capacitance decay after 5000 charge–discharge cycles). Besides, electrochemical capacitance of composite textile electrodes in Ca(NO3)2 electrolyte is higher than that in NaNO3 electrolyte at low scan rates (1–5 mV s−1), but the situation is reversed when scan rates are higher than 10 mV s−1. Above all, the results show that our low-cost composite textile electrodes are high-performance in neutral electrolytes, which is helpful for developing large-scale energy storage devices.
1. Introduction
Supercapacitors, also known as electrochemical capacitors, have a fast charge–discharge rate, high power capability and long cycle lifetime.1–6 Supercapacitors have been used in a wide range of applications such as portable electric devices, hybrid cars, intelligent wireless sensors and memory backup systems.7–11 However, limited energy density, usually lower than batteries by an order of magnitude, hinders broader applications of supercapacitors.7 During the past years, a significant amount of effort has been devoted to improving the energy density of supercapacitors.12–16 MnO2 is one type of transition-metal oxide and has high specific pseudocapacitance due to reversible redox reactions near the surface.17–21 However, because of its poor electrical conductivity, MnO2 has low rate capability and stability, and broader applications of MnO2 are still a great challenge.18,22 Graphene (GN), a two-dimensional carbon material, has advantages of good electronic conductivity, high specific surface area and high chemical stability.23–26 Due to expectation to combine their merits together, various GN/MnO2 composites have been synthesized and explored.22,27–31 We put forward a self-reacting micro-emulsion method to prepare ultrathin amorphous MnO2 nanosheets with high capacitance of over 500 F g−1 in Na2SO4 electrolyte.32,33 This method can be utilized to prepare GN/MnO2 composites.
In our previous work, activated carbon fiber felt (ACFF) was used to prepare multiscale carbon composite textiles and all-carbon compressible supercapacitors.34 However, the high-performance supercapacitors were achieved in a strong alkaline electrolyte (6 M KOH aqueous solution), this may increase risk of environmental issues.
In this work, GN/MnO2 composites prepared through self-reacting micro-emulsion method were introduced into ACFF to fabricate GN/MnO2/ACFF composite textile electrodes. Micro-structure, electrical property and electrochemical performance of the prepared GN/MnO2/ACFF composite electrodes in different neutral electrolytes were studied. The composite electrodes have similar pore features to original ACFF but better electrochemical performance. The neutral electrolytes also eliminate the risks and environmental issues of strong alkaline electrolytes. As a whole, our results show that the cheap ACFF, modified by GN/MnO2 composites, is capable to be used as supercapacitor electrodes in neutral electrolytes, which is helpful for developing supercapacitors with high performance and low cost.
2. Experimental
2.1 Materials
ACFF textiles, with thickness of ∼3.0 mm, were purchased from Shenzhou Carbon Fiber Co., Ltd, China. Water-based GN paste (Model: Pas2002, 5.49 wt%) was obtained from SuperC (Dongguan) Technology Co., Ltd, China. The AR grade potassium permanganate (KMnO4), sodium bis (2-ethylhexyl) sulfosuccinate (Aerosol-OT, AOT), isooctane, sodium nitrate (NaNO3) and calcium nitrate (Ca(NO3)2) were purchased from Sinopharm Chemical Reagent Co., Ltd.
2.2 Synthesis of GN/MnO2/ACFF composite textiles
Firstly, GN/MnO2 composites were synthesized through self-reacting micro-emulsion method. AOT was excessive and all added KMnO4 was reduced to MnO2 in this method, so the weight of MnO2 could be calculated. 17.11 g (or 1.07 g) GN paste was added into 500 ml 0.1 M AOT/isooctane solution followed by 30 minute ultrasound. 27 ml 0.1 M KMnO4 aqueous solution was added into the suspension followed by an-hour ultrasound. The product (dark brown precipitate) was separated, washed with ethanol and deionized water and dried at 80 °C for 12 h. The product was denoted as 80GM (or 20GM) (the weight ratio of GN to MnO2 was 80
:
20 (or 20
:
80)). Then 0.25 g 80GM (or 20GM) was dispersed in 50 ml deionized water by sonifier cell disrupting for 2 h. A wafer-shaped piece of ACFF, with diameter of 15 mm, was immersed in the 80GM (or 20GM) suspension and then freeze-dried. The obtained GN/MnO2/ACFF composite textile electrodes were denoted as 80GMC (or 20GMC). Weight of ACFF, 20GMC and 80GMC is 21.2 mg, 21.5 mg and 21.7 mg respectively.
2.3 Characterization
Weight of all textile electrodes was measured on an electronic balance. Their micro-structures were observed through scanning electron microscopy (SEM. Model: Hitachi, S-5200). Electrical conductivity was measured on a four-point probe instrument. The specific surface area and pore size distribution were measured on Micromeritics ASAP2020 analyzer. Specific surface area (SBET) and total pore volume (Vp) were determined by BET method and single point adsorption, respectively.
2.4 Electrochemical measurement
To measure the electrochemical performances of our composite textile electrodes, full-cell symmetric supercapacitors were assembled. 1 M NaNO3 or Ca(NO3)2 aqueous solution was used as the electrolyte. Supercapacitors in which the electrolyte is NaNO3 and the electrode is ACFF, 20GMC and 80GMC were denoted as ANa, 20Na and 80Na, respectively. Similarly, those in Ca(NO3)2 electrolyte were denoted as ACa, 20Ca and 80Ca, respectively. Electrochemical tests of cyclic voltammetry (CV) and galvanostatic charge–discharge (GCD) were performed on an Im6e (Zahner) electrochemical station. The specific capacitance of a single electrode was calculated on the area of one electrode (1.767 cm2).
3. Results and discussion
The micro-structure of prepared GN/MnO2 composite powder is first observed. The SEM images of 20GM and 80GM, as shown in Fig. 1, indicate that the GN/MnO2 composites with different GN contents are successfully synthesized and MnO2 is loaded on the GN sheets. What's more, the GN sheets in SEM images are not thin or transparent, which proves that the GN we use, is composed by several layers instead of single layer GN sheets. The product information provided by the manufacturer also confirms this.
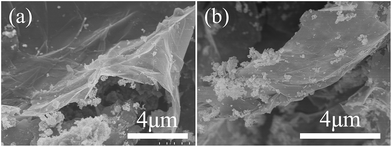 |
| Fig. 1 SEM images of (a) 20GM, (b) 80GM. | |
The micro-morphology of the obtained GN/MnO2/ACFF composite textiles is displayed in Fig. 2. Fig. 2a and b show the SEM images of ACFF textiles. The images indicate that the original ACFF is fabricated by intertwining and overlapping carbon fibers, giving rise to a great quantity of holes in different sizes in the textiles. The abundance of holes makes ACFF textiles have high specific surface area and other excellent features of foams, such as bendability and compressibility. As observed in our experiments, ACFF textiles have ultrahigh water absorbability, which makes the impregnation process much simpler and quicker than other carbon materials.35 As shown in Fig. 2c–f, the GN/MnO2 composites are successfully introduced into ACFF. As can be seen, GN/MnO2 composites with different weight ratio of GN to MnO2 are attached on the surface of activated carbon fibers. However, when GN content increases, one distinct difference is that volume of nanofillers in 80GMC becomes much more than that in 20GMC. This volume increase makes GN aggregation more serious.
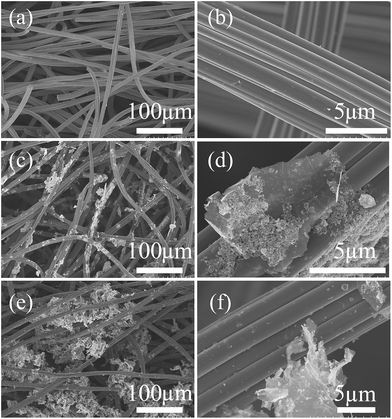 |
| Fig. 2 SEM images of (a and b) ACFF, (c and d) 20GMC and (e and f) 80GMC. | |
It should be noted that in the assembled full-cell supercapacitors, the electrodes are highly compressed. In this case, GN/MnO2 particles are pinned in local spaces encircled by carbon fibers, thus will not easily fall off the composite electrodes in supercapacitors.
Fig. 3a displays the electrical conductivity of textiles. As can be seen, conductivity is improved after introducing GN/MnO2 composites. The electrical conductivity of 20GMC and 80GMC is 35% and 114% higher than that of ACFF, respectively. Due to the short carbon fibers used in manufacturing ACFF, as well as its porous feature, the electrical conductivity of ACFF is not as high as other carbon fabrics.36,37 The added GN sheets could increase the channels for electron transport. For further consideration of the compressed state of electrodes in full-cell supercapacitors, we also measured the conductivity when the textile samples are manually pressed. It is obvious that the conductivity is higher than that at fluffy state. Although the pressure on the samples cannot be measured precisely, the data does indicate that those composite textiles can achieve higher conductivity when they are used as electrodes in full-cell supercapacitors.
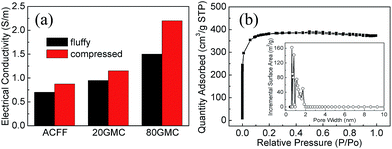 |
| Fig. 3 (a) Electrical conductivity of textiles at different states; (b) N2 adsorption/desorption isotherms of 80GMC at 77 K (the inset of (b) exhibits the pore size distribution). | |
In previous work,34 the SBET, Vp and d of ACFF were measured to be 1528 m2 g−1, 0.65 cm3 g−1 and 1.73 nm respectively. Fig. 3b shows N2 adsorption/desorption isotherms of 80GMC. The type I isotherms indicate the micropore structure of 80GMC.38 The SBET, Vp and d of 80GMC are 1465 m2 g−1, 0.58 cm3 g−1 and 1.57 nm respectively. All of these figures are lower than their counterparts of original ACFF. Because the few-layered GN in our experiments has lower specific surface area than ACFF and the GN sheets can cover some pores of ACFF body materials. As shown in the inset of Fig. 3b, most pore sizes distribute under 2 nm, this reflects the micropore feature of 80GMC again.
Fig. 4a–f show CV curves of supercapacitors at scan rates of 1–20 mV s−1. For ANa and ACa, the quasi-rectangular shape of CV curves only exists at low scan rates (1–2 mV s−1), the deformation of CV curves becomes serious at high scan rates. This reflects the poor electrochemical performance of original ACFF. For 20Na and 20Ca, although the deformation of CV curves is not as serious as ACFF, the narrow areas of CV curves still indicate low capacitance of 20GMC. For 80Na and 80Ca, the rate performance is much better. When the scan rate increases, the CV curves of 80Na and 80Ca maintain rectangular well.
 |
| Fig. 4 CV curves at different scan rates of (a) ANa, (b) ACa, (c) 20Na, (d) 20Ca, (e) 80Na, (f) 80Ca; (g) areal capacitance of each sample calculated from CV curves. | |
Fig. 4g displays areal capacitance of the single electrode at scan rates of 1–20 mV s−1. Compared with ACFF, the capacitance of 80GMC is largely enhanced while that of 20GMC is slightly improved. For example, the specific capacitance (Cs) of ACa, 20Ca and 80Ca at 2 mV s−1 is 763 mF cm−2, 918 mF cm−2 and 1516 mF cm−2 respectively. Besides, after introducing GN/MnO2 composites, the capacitance retention of textile electrodes is improved. The rate performance of 80GMC is much better than ACFF, while the improvement of 20GMC is negligible. For example, when the scan rate increases from 1 mV s−1 to 20 mV s−1, about 13.7%, 17.0% and 54.6% of Cs retains for ANa, 20Na and 80Na respectively.
Different electrolytes have different influence on each textiles. For ACFF and 20GMC, the Cs and Cs retention rate between NaNO3 and Ca(NO3)2 electrolytes do not show large distinction. Unlike ACFF and 20GMC, different electrolytes lead to distinguishing electrochemical performance of 80GMC. At low scan rates (1–5 mV s−1), 80Ca possesses higher Cs than 80Na, while at high scan rates (10–20 mV s−1), 80Ca possesses lower Cs than 80Na. Thus when the scan rate increases from 1 mV s−1 to 20 mV s−1, the Cs retention rate of 80Ca is 9.1% lower than that of 80Na. This variation mainly results from the different capacitance of MnO2 in NaNO3 and Ca(NO3)2 electrolytes. The capacitance of MnO2 in Ca(NO3)2 electrolyte is much higher than that in NaNO3 electrolyte at 2 mV s−1.39–41 Due to this reason, the capacitance of 80Ca is higher than that of 80Na at low scan rates (1–5 mV s−1). However, at high scan rates (10–20 mV s−1), the cation diffusion in electrolytes has a significant impact on the electrode capacitance: compared with Na+, Ca2+ has a lower diffusion coefficient and mobility, thus leading to a smaller capacitance of MnO2. Therefore, capacitance of 80GMC electrode in Ca(NO3)2 electrolyte is lower than that in NaNO3 electrolyte at high scan rates.
As shown in Fig. 5a–f, after introducing GN/MnO2 composites, more symmetric GCD curves, longer discharging time and smaller IR drops are achieved, especially for 80GMC. The IR drop reflects internal resistance of supercapacitors. For clear comparison between different textiles, the equivalent series resistance (ESR) is used and can be calculated according to equation:
IR (V) is the IR drop during discharge process,
I (mA cm
−2) is the current density. ESR values of ANa, ACa, 20Na, 20Ca, 80Na and 80Ca are about 149, 150, 118, 120, 16 and 14 Ω cm
2 respectively at
I = 2 mA cm
−2. As can be seen, after introducing GN/MnO
2 composites, the electrical resistance of textiles decreases, while the influence of different electrolytes is negligible.
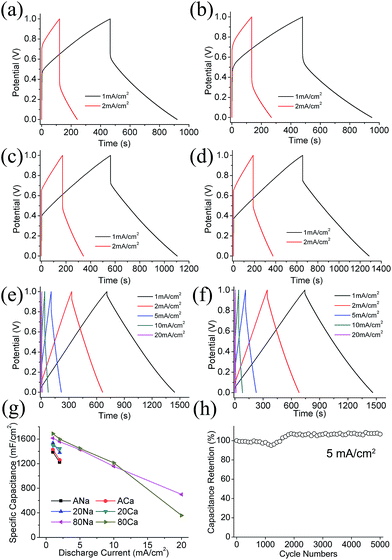 |
| Fig. 5 GCD curves of (a) ANa, (b) ANa, (c) 20Na, (d) 20Ca, (e) 80Na, (f) 80Ca at different current densities (1–20 mA cm−2); (g) areal capacitance of each sample calculated from GCD curves; (h) cycling stability of 80Ca tested at the current density of 5 mA cm−2. | |
Because the high resistance of ACFF and 20GMC makes their IR drops theoretically larger than 1 V at the scan rate of more than 2 mA cm−2, the charge–discharge process of them lasts less than 1 second and the Cs cannot be calculated from GCD curves. Therefore Fig. 5 only contains GCD curves and Cs of ACFF and 20GMC at 1–2 mA cm−2. As shown in Fig. 5g, Cs has been improved after introducing GN/MnO2 composites, and Cs of 80GMC is higher than that of 20GMC. Different electrolytes do not have much impact on the Cs of ACFF and 20GMC, but influence the electrochemical performance of 80GMC. The Cs of 80Ca is higher than that of 80Na at low current density, and decreases faster when the current density increases. So when the current density increases from 1 mA cm−2 to 20 mA cm−2, Cs of 80Na is retained about 43%, while that of 80Ca is retained about 23%. 80Na can achieve 25.4 μW h cm−2 of energy density with 895.2 μW cm−2 of power density at current density of 5 mA cm−2. This variation of Cs calculated from GCD curves is as same as that calculated from CV curves. Long-term cycling performance of 80Ca was also evaluated. As presented in Fig. 5h, there is no capacitance decay after 5000 charge–discharge cycles, demonstrating its excellent cycling stability.
4. Conclusions
In this work, GN/MnO2/ACFF composite electrodes are prepared by introducing GN/MnO2 composites into ACFF textiles. The electrochemical performances of as-prepared composite textile electrodes in neutral electrolytes (1 M NaNO3 and Ca(NO3)2 aqueous solutions) are studied. After introducing GN/MnO2 composites, lower electrical resistance and better electrochemical performances of the electrodes are observed. Besides, capacitance of composite textile electrodes in Ca(NO3)2 electrolyte is higher than that in NaNO3 electrolyte at low scan rates (1–5 mV s−1), but the situation is reversed when the scan rate is higher than 10 mV s−1. Our results show that the low-cost composite textile electrodes are high-performance in neutral electrolytes, which is helpful for developing large-scale energy storage devices.
Acknowledgements
We would like to thank NSFC (No. 51102139 and 51232005) and Shenzhen Technical Plan Projects (No. JC201105201100A and JCYJ20130402145002425) for financial support. We also appreciate the financial support from Guangdong Province Innovation R&D Team Plan (2009010025).
Notes and references
- A. Burke, J. Power Sources, 2000, 91, 37–50 CrossRef CAS.
- Y. Huang, J. Liang and Y. Chen, Small, 2012, 8, 1805–1834 CrossRef CAS PubMed.
- A. Burke, Electrochim. Acta, 2007, 53, 1083–1091 CrossRef CAS.
- R. Kötz and M. Carlen, Electrochim. Acta, 2000, 45, 2483–2498 CrossRef.
- B. E. Conway, Electrochemical supercapacitors: scientific fundamentals and technological applications, Springer Science & Business Media, 2013 Search PubMed.
- X. Zhang, H. Zhang, C. Li, K. Wang, X. Sun and Y. Ma, RSC Adv., 2014, 4, 45862–45884 RSC.
- P. Simon and Y. Gogotsi, Nat. Mater., 2008, 7, 845–854 CrossRef CAS PubMed.
- J. R. Miller and P. Simon, Science, 2008, 321, 651–652 CrossRef CAS PubMed.
- P. J. Hall and E. J. Bain, Energy Policy, 2008, 36, 4352–4355 CrossRef.
- L. G. H. Staaf, P. Lundgren and P. Enoksson, Nano Energy, 2014, 9, 128–141 CrossRef CAS.
- L. Dong, Z. Chen, D. Yang and H. Lu, RSC Adv., 2013, 3, 21183 RSC.
- J. Yan, Q. Wang, T. Wei and Z. Fan, Adv. Energy Mater., 2014, 4, 1300816 Search PubMed.
- J. Yan, Z. Fan, W. Sun, G. Ning, T. Wei, Q. Zhang, R. Zhang, L. Zhi and F. Wei, Adv. Funct. Mater., 2012, 22, 2632–2641 CrossRef CAS.
- A. Izadi-Najafabadi, S. Yasuda, K. Kobashi, T. Yamada, D. N. Futaba, H. Hatori, M. Yumura, S. Iijima and K. Hata, Adv. Mater., 2010, 22, E235–E241 CrossRef CAS PubMed.
- Z. Tang, C. H. Tang and H. Gong, Adv. Funct. Mater., 2012, 22, 1272–1278 CrossRef CAS.
- W. Deng, X. Ji, Q. Chen and C. E. Banks, RSC Adv., 2011, 1, 1171 RSC.
- M.-W. Xu, D.-D. Zhao, S.-J. Bao and H.-L. Li, J. Solid State Electrochem., 2007, 11, 1101–1107 CrossRef CAS.
- T. Brousse, M. Toupin, R. Dugas, L. Athouël, O. Crosnier and D. Bélanger, J. Electrochem. Soc., 2006, 153, A2171–A2180 CrossRef CAS.
- H. Xia, J. Feng, H. Wang, M. O. Lai and L. Lu, J. Power Sources, 2010, 195, 4410–4413 CrossRef CAS.
- S. Chen, J. Zhu, X. Wu, Q. Han and X. Wang, ACS Nano, 2010, 4, 2822–2830 CrossRef CAS PubMed.
- F. Wang, S. Xiao, Y. Hou, C. Hu, L. Liu and Y. Wu, RSC Adv., 2013, 3, 13059 RSC.
- G. Yu, L. Hu, N. Liu, H. Wang, M. Vosgueritchian, Y. Yang, Y. Cui and Z. Bao, Nano Lett., 2011, 11, 4438–4442 CrossRef CAS PubMed.
- C. Liu, Z. Yu, D. Neff, A. Zhamu and B. Z. Jang, Nano Lett., 2010, 10, 4863–4868 CrossRef CAS PubMed.
- Y. Wang, Z. Shi, Y. Huang, Y. Ma, C. Wang, M. Chen and Y. Chen, J. Phys. Chem. C, 2009, 113, 13103–13107 CAS.
- B. G. Choi, M. Yang, W. H. Hong, J. W. Choi and Y. S. Huh, ACS Nano, 2012, 6, 4020–4028 CrossRef CAS PubMed.
- L. Dong, C. Xu, Y. Li, C. Wu, B. Jiang, Q. Yang, E. Zhou, F. Kang and Q. H. Yang, Adv. Mater., 2015 DOI:10.1002/adma.201504747.
- Z. Zhang, F. Xiao, L. Qian, J. Xiao, S. Wang and Y. Liu, Adv. Energy Mater., 2014, 4, 1400064 Search PubMed.
- B. Wei, L. Wang, Q. Miao, Y. Yuan, P. Dong, R. Vajtai and W. Fei, Carbon, 2015, 85, 249–260 CrossRef CAS.
- Y. He, W. Chen, X. Li, Z. Zhang, J. Fu, C. Zhao and E. Xie, ACS Nano, 2013, 7, 174–182 CrossRef CAS PubMed.
- Z. Fan, J. Yan, T. Wei, L. Zhi, G. Ning, T. Li and F. Wei, Adv. Funct. Mater., 2011, 21, 2366–2375 CrossRef CAS.
- Y. Zhao, W. Ran, J. He, Y. Huang, Z. Liu, W. Liu, Y. Tang, L. Zhang, D. Gao and F. Gao, Small, 2015, 11, 1310–1319 CrossRef CAS PubMed.
- C. Xu, B. Li, H. Du, F. Kang and Y. Zeng, J. Power Sources, 2008, 180, 664–670 CrossRef CAS.
- S. Shi, C. Xu, C. Yang, Y. Chen, J. Liu and F. Kang, Sci. Rep., 2013, 3, 2598 Search PubMed.
- L. Dong, C. Xu, Q. Yang, J. Fang, Y. Li and F. Kang, J. Mater. Chem. A, 2015, 3, 4729–4737 CAS.
- L. Dong, F. Hou, Y. Li, L. Wang, H. Gao and Y. Tang, Composites, Part A, 2014, 56, 248–255 CrossRef CAS.
- L. Dong, Y. Li, L. Wang, F. Hou and J. Liu, Mater. Lett., 2014, 130, 292–295 CrossRef CAS.
- G.-Y. Heo, Y.-J. Yoo and S.-J. Park, J. Ind. Eng. Chem., 2013, 19, 1040–1043 CrossRef CAS.
- S. Storck, H. Bretinger and W. F. Maier, Appl. Catal., A, 1998, 174, 137–146 CrossRef CAS.
- C. Xu, B. Li, H. Du, F. Kang and Y. Zeng, J. Power Sources, 2008, 184, 691–694 CrossRef CAS.
- C. Xu, H. Du, B. Li, F. Kang and Y. Zeng, J. Electrochem. Soc., 2009, 156, A73 CrossRef CAS.
- C. Xu, C. Wei, B. Li, F. Kang and Z. Guan, J. Power Sources, 2011, 196, 7854–7859 CrossRef CAS.
|
This journal is © The Royal Society of Chemistry 2016 |
Click here to see how this site uses Cookies. View our privacy policy here.