DOI:
10.1039/C5RA23222H
(Paper)
RSC Adv., 2016,
6, 1129-1135
Cobalt oxide nanoparticle embedded N-CNTs: lithium ion battery applications†
Received
4th November 2015
, Accepted 11th December 2015
First published on 15th December 2015
Abstract
Cobalt oxide embedded nitrogen-doped carbon nanotubes (CoO/N-CNT) are synthesized by the direct carbonization of a cobalt–benzimidazole framework (ZIF-12) at 950 °C under an inert atmosphere. X-ray photoelectron spectroscopy indicates the conducting graphitic networks of the CNT contain edge and aromatic substituted pyridinic-nitrogen. Microscopy reveals the extensive formation of multi-walled CNT encasing CoO nanoparticles. This trapping of CoO nanoparticles within the nitrogen doped CNT network is discussed as the key basis of improving the material's contact resistance and conductivity to achieve high power outputs, together with the high specific surface area (365 m2 g−1) and structural robustness of the novel composite material. The material shows an excellent lithium charge/discharge and storage, retaining ∼95% capacity after 50 cycles and a reversible capacity of ∼1100 mA h g−1 at a current density of 0.1 A g−1, which far exceeds the performance of conventional lithium ion battery anode materials under similar conditions.
Introduction
Research into energy conversion and storage systems is important due to the widespread societal dependence on mobile and portable electronic devices. Hence, much attention continues to be focused on developing battery component materials with high specific capacities to store and release electrical energy.1–3 Despite the rapid progress to date, the major challenge to improve battery performance requires new materials capable of high electron transport at high charge–discharge rates. The poor cycle performance has limited the application of lithium ion batteries (LIBs) in industrial scale technologies.4,5 Traditionally, graphite and various natural and synthetic carbon based materials, have been used as anode for LIBs due to their robustness and enhanced specific capacities.6–8 Amongst various reported carbon materials, carbon nanotubes (CNTs) present a unique combination of properties useful for anodic materials in LIBs including outstanding electrical properties, strong mechanical strength, chemical stability, superior aspect ratios, and high surface areas.9,10 Fundamentally however, lithium ion (Li+) storage in CNTs differs from conventional graphite and other carbon anodes because the CNTs have stable sites located inside individual nanotubes through endcap or sidewall openings with the curved multi-layers facilitating Li+ diffusion.3
Nitrogen substitution within graphitic nanotube networks has been shown to enhance their electron-conducting properties due to the presence of additional lone pairs of electrons that act as donors with respect to the delocalized π-system of the hexagonal framework.11 Transition metals/metal oxides decorated nitrogen/oxygen-doped graphitic carbon materials have also been reported for various energy conversion processes like oxygen reduction reactions,12,13 solar energy conversion14,15 and hydrogen evolution reaction.16 Different strategies have been adopted to obtain nitrogen-doped CNTs including chemical vapour deposition (CVD) in the presence of nitrogen sources,17 direct pyrolysis of organo–metallic precursors,15 and the controlled conversion of metal–organic frameworks (MOFs).18–25
However, facile single-step conversion of MOFs into metal oxide decorated CNTs remains a considerable challenge, and hence new methods are required. In the present work, we use ZIF-12 for the synthesis of cobalt oxide embedded nitrogen-doped carbon nanotubes (CoO/N-CNT). We attribute the formation of the carbon nanotubes to a mechanism involving the high temperature decomposition of the 1-dimensional benzimidazole containing channels of ZIF-12 and carbon nucleation and growth catalysed by cobalt oxide nanoparticles (Scheme 1). During carbonization at 950 °C the CNTs form by a cobalt oxide catalysed growth, that embeds the nanoparticles within the multi-walled CNTs; while at these high temperatures nitrogen substitutes with carbon in the CNTs sp2 hybridised conjugated network. This chemical and electronic alteration of the carbon nanotubes results in a high reversible capacity of 1100 mA h g−1 at current density of 0.1 A g−1 whilst maintaining a good capacity retention of more than 95%, even over 50 cycles when used as an anode in LIB application.
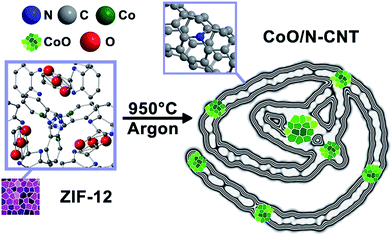 |
| Scheme 1 ZIF-12 converted into CoO/N-CNT at 950 °C under argon atmosphere. | |
Materials & methods
Synthesis of ZIF-12
For the synthesis of ZIF-12; Co(NO3)3·6H2O (1.4 mmol; 0.41 g) and benzimidazole (6.1 mmol; 0.72 g) were dissolved each separately in 7 mL of dimethylformamide (DMF) solvent. Both the solutions were mixed together, stirred thoroughly and transferred to a Teflon-lined stainless steel autoclave and kept at 150 °C for 48 h.26 After completion of the reaction and cooling to room temperature, purple coloured crystals were collected, and washed with excess DMF and ethanol to remove the unreacted materials. The sample was analysed by powder X-ray diffraction (PXRD) and the pattern of as-synthesised product was found to match well with the reported single crystal data.
Carbonization of ZIF-12
The synthesized and vacuum evacuated ZIF-12 (300 mg) was transferred into a ceramic boat which was placed in a quartz tube fixed in a tube furnace (Nabertherm B 180). Initially air was flushed away by continuous flow of Argon for 30 min followed by heating at 950 °C for 6 h to obtain the cobalt oxide embedded nitrogen-doped carbon nanotubes (CoO/N-CNT) material; yield ca. 83% (250 mg).
Characterisation
Thermogravimetric analysis was carried out using a TGA/SDT 851e (Mettler Toledo, Switzerland) thermobalance under N2 flow with temperature ramp of 10 °C min−1 from room temperature to 680 °C. Weight loss versus temperature was continuously recorded during the experiment.
PXRD data was collected on a PANalytical X'Pert Pro diffractometer fitted with a solid state PIXcel detector (40 kV, 30 mA) using Cu-Kα (λ = 1.5406 Å) radiation and 1/2° divergence and 1° anti-scatter slits, over the 5° to 60° 2θ range with a 0.016413° step size and 0.001087° s−1 scan rate (total scan time ∼ 15 h). No mathematical manipulation was performed on the presented data.
X-ray photoelectron spectroscopy (XPS) measurements were conducted with ESCALAB250Xi (Thermo Scientific, UK) instrument having background vacuum less than 2 × 10−9 mbar. Monochromated Al Kα (energy hν = 1486.68 eV) as the radiation source and power of 164 W (10.8 mA and 15.2 kV) with a spot size of 500 μm were used during analysis. Curve fitting was performed using the Scienta ESCA300 data-system software.
N2 adsorption/desorption measurements were carried out using the Accelerated Surface Area & Porosimetry System 2020 supplied by Micromeritics Instruments Inc. Approximately 147 mg of sample was loaded into a glass analysis tube and outgassed for 3 h under vacuum at 200 °C prior to measurement. The isotherm was measured at 77 K and data was analysed using Bruner–Emmett–Teller (BET) model to determine the surface area.27
Scanning electron microscopy (SEM) was performed using JEOL-JSM-6610LV. Transmission electron microscopy (TEM) and select area electron diffraction (SAED) analysis were conducted on a JEOL2100 operated at an accelerating voltage of 200 kV.
Electrochemical studies
The electrochemical performance of CoO/N-CNT was evaluated by galvanostatic charge–discharge testing against lithium as counter electrode. The working electrodes were made by a slurry coating procedure. The slurry was prepared by sonicating 80 weight percent (wt%) of CoO/N-CNT material, 10 wt% of acetylene black and 10 wt% of PVDF (polyvinylidene difluoride) binder in N-methylpyrrolidinone solvent. This slurry was uniformly coated on copper foil current collector. The electrodes were dried in vacuum oven at 100 °C for 12 h. A 2025 type coin cell was fabricated in argon filled glove box using polyethylene as separator and 1 mol L−1 LiPF6 in ethylene carbonate/dimethyl carbonate (1
:
1) as electrolyte. The electrochemical charge/discharge tests of the sample was performed at voltage limits of 0.01–3.0 V versus Li/Li+ and the mass loading of material was ca. 1 mg cm−2.
Results and discussion
Characterization
The thermogravimetric weight loss curve of ZIF-12 in the temperature range of 25–680 °C in air showed a two-step weight loss with increasing temperature (ESI Fig. S1a†). The first weight loss of up to 13 weight percent (wt%) in the temperature range of 160–270 °C is due to the removal of entrapped solvent molecules in the network and no weight loss is observed until 500 °C, showing a very high thermal stability of the ZIF-12 network. Beyond 500 °C, the network decomposes, resulting in small weight loss steps. The overall weight loss of ca. 70 wt% was observed up to 680 °C, after which a residue remained consisting of Co-oxide and carbon.
SEM was performed to determine the size and morphology of the synthesized ZIF-12 and the acquired image is shown in Fig. S1b of ESI.† From the SEM image the morphology of ZIF-12 particles can be seen as 1 μm to 3.5 μm prismatic crystals.
TEM images show that the material consists entirely of tangled mats of carbon nanotubes extending over micron length scales, Fig. 1a and b. The nanotubes vary in tube diameter although observations of tube diameters up to 50 nm were made. Nanoparticles were also present throughout the material. The nanoparticles appeared as irregular in size and rounded; the nanoparticles were as large as 50 nm in size in one lateral dimension, Fig. 1c and d. Higher magnification of the nanotubes revealed the encapsulation of the nanoparticles within the nanotubes, Fig. 1e. The red-green-blue contrast image resulting from overlap of the hollow cone dark field TEM image with the bright field image indicated the location of the nanoparticles in the bulk material, Fig. 1f.
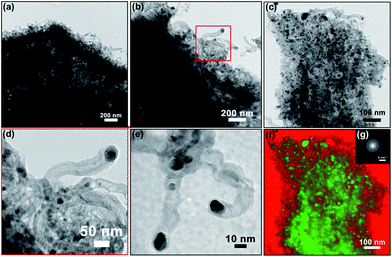 |
| Fig. 1 (a–e) TEM images of the CoO/N-CNT nanocomposite, with nanoparticles visibly encapsulated at the ends of the nanotubes. (f) Red-green-blue contrast TEM image showing nanoparticles in green and the inset (g) shows SAED pattern with 5 nm−1 scale bar. | |
The PXRD pattern of CoO/N-CNT is shown in Fig. 2a, with peaks corresponding to (002), (101), and (004) reflections of lattice planes in graphitic material; the pattern was typical of carbon nanotubes (see ESI Fig. S2†). Peaks corresponding to metal oxides were not detected in PXRD, however TEM images clearly showed nanoparticles were evident (see Fig. 1). SAED taken of a region with encapsulated nanoparticles indicated the presence of polycrystalline cobalt(II) oxide (CoO) and carbon, Fig. 2b. It must be noted that CoO and cobalt(III) nitride (CoN) cannot be distinguished using conventional PXRD and SAED as the respective cubic lattice constants are very close (a = 4.24 Å and a = 4.28 Å respectively), however CoN decomposes completely to cobalt metal at 375 °C,28 which is well below the current 950 °C reaction condition, whereas the CoO is stable above 900 °C and hence more likely the remaining cobalt compound.
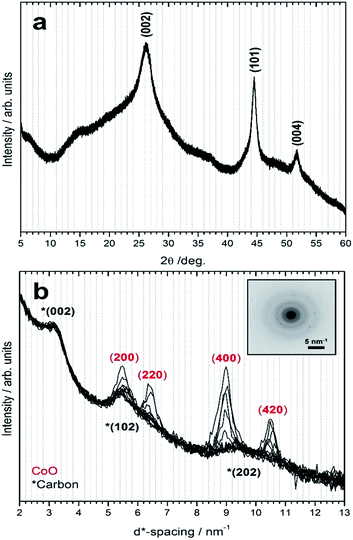 |
| Fig. 2 (a) PXRD pattern of CoO/N-CNT. (b) Line profiles taken from the center bright spot corresponding to the reciprocal d-spacing from the SAED pattern of a region containing CNT encapsulated CoO nanoparticles; inset shows the analysed SAED pattern. | |
XPS analysis indicated that the surface of CoO/N-CNT consists of carbon (90.0 wt%), nitrogen (3.4 wt%), cobalt (2.3 wt%), oxygen (2.8 wt%) and chlorine residues (1.5 wt%) (ESI Table S1†). The Co 2p3/2 peaks within the main Co 2p envelope, Fig. 3a, indicate cobalt in oxides 1.9 wt% and metallic cobalt 0.4 wt%. The C 1s core line shows an asymmetric peak commonly obtained for conductive graphitic materials, Fig. 3b.29,30 The fitted envelope in the XPS spectra for the O 1s core line is a convolution of two very broad peaks (A) and (B), resulting from oxides in cobalt (A) at 531.3 eV and also that bound to carbon (O
C) at the higher binding energy side (B) at 533.3 eV, Fig. 3c.31–33 The atomic ratio of cobalt in oxides to oxygen (A) was ∼1
:
1 (i.e. CoO). A convolution of two broad peaks was also found in the N 1s core line corresponding to graphite substituted nitrogen (2.0 wt%), i.e. bound within the graphene lattice of the carbon material at 400.9 eV, and the remaining as organic residue in the form of pyridinic-nitrogen (1.4 wt%) at 398.6 eV,34 Fig. 3d. Chlorine residues were also found in the sample (1.5 wt%) which comprised both organic (197.5 eV, 0.8 wt%) and inorganic material on the surface (200.2 eV, 0.7 wt%).35 The bulk concentration of total cobalt was also verified by atomic absorption spectroscopy (2.2 wt%) which was found to agree with that obtained by XPS analysis.
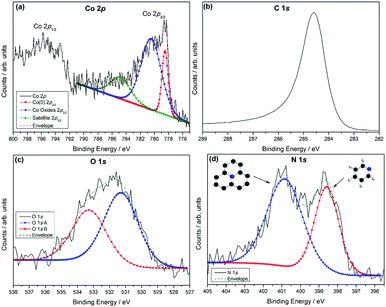 |
| Fig. 3 XPS spectra of (a) Co 2p core lines, (b) C 1s core line, (c) O 1s core lines, and (d) N 1s core lines (d) in the analysed CoO/N-CNT nanocomposite. In the molecular models in (d) show atoms of nitrogen (blue), carbon (black), and hydrogen (white). | |
A type-IV isotherm was observed for CoO/N-CNTs during N2 sorption experiments, Fig. 4a. This can be explained on the basis of a possibility that N2 gas condenses in the microporous and mesoporous capillaries of the CoO/N-CNT at pressures below the saturation pressure of the N2 gas. The BET surface area of CoO/N-CNT was 365 m2 g−1 and pore size distribution ranging from 1.5 nm to 7.6 nm, Fig. 4b. The high BET surface area and wide range of porosity provides a higher degree of active sites and pores for Li+ diffusion during charge and discharge.
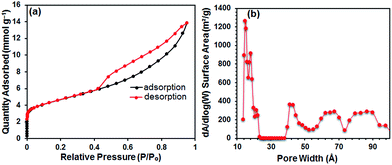 |
| Fig. 4 (a) N2 adsorption/desorption isotherm and (b) pore size distribution plot of CoO/N-CNT. | |
CoO/N-CNT growth mechanism
Curved growth lines are prominent within the nanotubes which form in semi-circular layers following from the surface of the nanoparticles and they are not concentric. This growth pattern is a common signature for nanoparticle catalyzed carbon growth and nucleation.36–38 During the elongation of a nanotube, the continual incorporation of carbon atoms into the tube wall consists of three relatively independent steps:39–42 (i) catalytic decomposition of precursor molecules on the catalyst surface; (ii) surface diffusion of the decomposed carbon to the CNT–catalyst interface and (iii) incorporation of the carbon (and other) atoms into the growing CNT.
The elongation of the nanotube sidewall dominates the growth kinetics once a CNT cap is formed on the catalyst surface. In this regard a crucial aspect of the growth mechanism is the formation and healing of defects during carbon incorporation, which control the structural quality of the CNT. In most cases of CNT growth, a large number of chemical and structural defects are present due to the emergence of multiple nucleation sites and the incorporation of dopant atoms during the elongation of the CNT (e.g. nitrogen and oxygen).
We observe CNTs encapsulating the nanoparticles in the CoO/N-CNT composite with diameters equal or slightly greater than that of the catalyst particle. This indicates that the CNT–catalyst interaction is substantially stronger than the energy associated with CNT cap closure,40 and hence carbon–catalyst binding is energetically preferred and maximised during the CNT growth. Furthermore, CNT nucleation and carbon–catalyst adhesion is strongly correlated to more structurally and chemically modified CNTs.43
From this we propose that the CoO nanoparticles form prior to the CNTs. However, in the absence of CoO nanoparticles (i.e. prior to CoO formation) the condensation of carbon may not necessarily result in CNT formation. Examining the PXRD of the CoO/N-CNT in the region of (002) graphitic reflections (see ESI Fig. S3†), we can resolve two discrete interplanar d-spacings (0.34 nm and 0.33 nm). The presence of these discrete graphitic d-spacings implies that (at least) two structurally different crystalline regions (along the interplanar c-axis) of the carbon material may be present. From our microscopy studies (Fig. 1) we only observe the extensive formation of irregular CNT morphologies with highly disordered side-walls, hence the variation in d-spacing may be (i) intrinsic, or (ii) due to a very small amount of another carbon morphology. A combination of both is likely, and both are linked to an indiscriminate condensation of carbon during pyrolysis.
Lithium ion battery testing
The typical charge–discharge curves of the CoO/N-CNT at a current density of 0.1 A g−1 for the first, second and fifth cycles are shown in Fig. 5a. The CoO/N-CNT delivers a high first cycle capacity up to 1250 mA h g−1. This value is three times greater than that reported for graphite (372 mA h g−1) as electrode materials in Li-ion batteries. The excellent capacity of the CoO/N-CNT is due to the combination of high porosity, high surface area, the presence of cobalt oxide nano-particles and dopant nitrogen atoms in the graphitic network of the CNTs. The extensive SEI film formation and electrolyte decomposition contribute to the non-reversible capacity of the first cycle. The non-reversible reduction of cobalt oxide and formation of lithium oxide (Li2O) also contribute in this higher capacity.
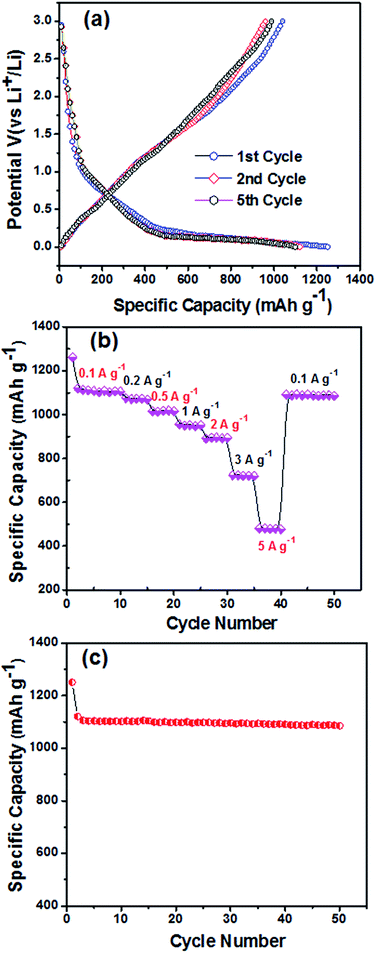 |
| Fig. 5 (a) Charge/discharge curve, (b) rate capability performance at different current densities, and (c) cycling stability of the CoO/N-CNT electrode material. | |
Generally, cobalt-oxide-only electrodes show a plateau at about 1 V during discharge, however in our study a weak plateau is observed in first cycle (ESI Fig. S4†) due to the small amount of the cobalt oxide present. The charge–discharge profile of 5th cycle is provided in Fig. 5a while the columbic efficiency data up to the 50th cycle is given in Table S2 of ESI.† The lower columbic efficiency of the first cycle (Table S2†) can be attributed to the reduction of CoOx, formation of Li2O and formation of the solid electrolyte interphase (SEI) film due to the high surface area of the electrode material. The 2nd cycle columbic efficiency slightly increases (Table S2†) as the discharged capacity is lowered due to irreversible losses of first cycle capacity. Furthermore, the columbic efficiency increases due to decrease in SEI formation and irreversible losses. The columbic efficiency at 50th cycle (Table S2†) is high – although the discharge capacity is decreased with an increase in stability.
The higher capacity achieved by the CoO/N-CNT nanocomposite material is attributed to the conversion reaction between lithium and cobalt oxide nanoparticles. This results in the formation of Li2O and cobalt nanoparticles in the first cycle, which consequently results in the loss of first cycle capacity. From the 2nd cycle onward the capacity values are stabilized and lithium presents reversible conversion reaction with cobalt, which contributes to a higher charge–discharge capacity. The reversible specific capacity for CoO/N-CNT is much higher than that reported for bulk Co3O4, porous carbon, N-doped porous carbon, N-doped CNTs, Co3O4/CNT, Co3O4/graphene nanocomposite, other MOFs, amongst other derived electrode materials44–61 as shown in Table 1.
Table 1 Comparison of different anode materials and their LIBs performance
Electrode materials |
1st cycle discharge (mA h g−1) |
Columbic efficiency (%) |
Reversible capacity (cycle) (mA h g−1) |
Current density (mA g−1) |
Ref. |
High concentration of nitrogen doped CNTs (HN-CNTs: 16.4 wt% nitrogen content). |
Porous carbon spheres |
1213 |
— |
506 (50) |
100 |
44 |
HN-CNTsa |
730 |
68 |
494 (100) |
100 |
47 |
N-doped graphene/Fe–Fe3C nanocomposite |
904 |
24.6 |
1098 (48) |
100 |
48 |
Co-doped ZnO coated with carbon |
1663 |
— |
725 (50) |
100 |
49 |
Co3ZnC/N-doped carbon hybrid nanospheres |
1570 |
58.1 |
— (60) |
100 |
50 |
Co3O4/CNT |
1478 |
81.0 |
873 (50) |
100 |
51 |
Co3O4/graphene nanocomposite |
1433 |
49.1 |
631 (50) |
55 |
52 |
Co3O4/C composite |
1170 |
76.0 |
900 (30) |
100 |
53 |
Co3O4 arrays |
1200 |
80.0 |
600 (100) |
400 |
54 |
Co3O4 nanoneedles |
1542 |
71.3 |
813 (20) |
0.5C |
55 |
Co3O4/TiO2 |
632.5 |
— |
602.8 (480) |
200 |
56 |
Doped hollow porous graphene (DHPG) |
2300 |
— |
900 (100) |
100 |
57 |
β-Co(OH)2/graphene hybrid |
944 |
97 |
640 (150) |
100 |
58 |
GC–Co(OH)2 |
1146 |
— |
706 (50) |
58 |
59 |
NiO/GNS |
1398 |
— |
982 (50) |
100 |
60 |
Co(OH)2/Co3O4 hybrid |
1452 |
73.42 |
1160 (40) |
58 |
61 |
Quadrate tubular Co3O4 nanoboxes |
1447 |
— |
1240 (50) |
200 |
62 |
ZnO@C/CNT |
1551 |
— |
758 (100) |
100 |
63 |
CNT@Co3O4 |
850 |
— |
— |
— |
64 |
CoO/N-CNTs |
1250 |
83 |
1100 (50) |
100 |
This work |
The rate capability of CoO/N-CNT is shown in Fig. 5b. The cell was cycled at a rate of 0.1 A g−1 for 5 cycles, and then the current densities were increased stepwise to 5 A g−1. With increasing the discharge–charge rates to 0.2, 0.5, 1, 2, 3 and 5 A g−1, and the delivered capacities were 1070, 1000, 950, 890, 700 and 470 mA h g−1, respectively. When the rate is tuned back to 0.1 A g−1 after cycling at different rates, the specific capacity is recovered back to ∼1100 mA h g−1, indicating the excellent stable cycling performance of the CoO/N-CNT. It is evident from Fig. 5b that the material is capable of very high discharge current, up to 5 A g−1. The material retains its stability and delivers high specific capacity after discharging at high current density. The cycling performance of the CoO/N-CNT at a current density of 0.1 A g−1 is shown in Fig. 5c. The CoO/N-CNT shows excellent cycling stability up to 50 cycles, retaining ∼95% capacity of the second cycle.
Conclusions
The synthesis of cobalt oxide embedded nitrogen-doped CNTs was achieved by a simple one-step method that can be summarized as the pyrolysis of ZIF-12 at 950 °C under inert atmosphere. The material was a suitable anode material for LIBs testing. A first-cycle discharge capacity of up to 1250 mA h g−1 was obtained at 0.1 A g−1 which is amongst the highest reported for any anodic material of comparable chemical composition. Upon rate cycling the specific capacity was recovered back to ∼1100 mA h g−1 at 0.1 A g−1, indicating a stable cycling performance. The hybrid nanocomposite retained 95% of its initial capacity even after 50 cycles at a current density of 0.1 A g−1. Practically, modern electronic devices like cell phones require such compact high energy batteries with high rate capability. The unique electrochemical behaviour of this material is attributed to the nitrogen doping of the CNTs framework and the strong interaction between the encapsulated cobalt oxide nanoparticles and CNT walls. Nitrogen substituents act as dopants to enhance the electrically conductivity of the CNTs while the cobalt oxide nanoparticles strongly interact with the CNT walls to facilitate the reaction with lithium. This chemical modification improves the ionic and electronic conductivity of the electrode by altering the contact resistance so that high power can be obtained. Conventional factors that influence cycle stability and charge capacities like porosity and surface area were also critical, which assisted in the soaking of the electrolyte and resulted in greater ion diffusion. The facile production method, and superior redox kinetics and high current capability, present a promising avenue for the development of rechargeable LIBs for industrial technologies.
Acknowledgements
The work was financially supported by Higher Education Commission (HEC) of Pakistan (No. 20-1638/R&D/09/2900) and (No. 20-2704/NRPU/R&D/HEC/12). M. C. acknowledges financial support from University of Sydney and technical assistance from Australian Centre for Microscopy and Microanalysis, and Mark Wainwright Analytical Centre.
Notes and references
- Y. S. Hu, R. D. Cakan, M. M. Titirici, J. O. Muller, R. Schlogl, M. Antonietti and J. Maier, Angew. Chem., Int. Ed., 2008, 47, 1645–1649 CrossRef CAS PubMed.
- D. Derrien, J. Hassoun, S. Panero and B. Scrosati, Adv. Mater., 2007, 19, 2336–2340 CrossRef.
- B. J. Landi, M. J. Ganter, C. D. Cress, R. A. DiLeo and R. P. Raffaelle, Energy Environ. Sci., 2009, 2, 638–654 CAS.
- L. F. Cui, R. Ruffo, C. K. Chan, H. L. Peng and Y. Cui, Nano Lett., 2009, 9, 491–495 CrossRef CAS PubMed.
- Y. Yu, L. Gu, C. B. Zhu, P. A. Aken and J. Maier, J. Am. Chem. Soc., 2009, 131, 15984–15985 CrossRef CAS PubMed.
- J. Hu, H. Li and X. J. Huang, Solid State Ionics, 2007, 178, 265–271 CrossRef CAS.
- E. J. Yoo, J. Kim, E. Hosono, H. S. Zhou, T. Kudo and I. Honma, Nano Lett., 2008, 8, 2277–2282 CrossRef CAS PubMed.
- V. Subramanian, H. W. Zhu and B. Q. Wei, J. Phys. Chem. B, 2006, 110, 7178–7183 CrossRef CAS PubMed.
- D. S. Su and R. Schlogl, ChemSusChem, 2010, 3, 136–168 CrossRef CAS PubMed.
- K. P. Gong, F. Du, Z. H. Xia, M. Durstock and L. M. Dai, Science, 2009, 323, 760–764 CrossRef CAS PubMed.
- M. Terrones, P. H. Redlich, N. Crobert, S. Trazobares, W. K. Hsu, H. Terrones, Y. Q. Zhu, J. P. Hare, C. L. Reeves, A. K. Cheetham, M. Rühle, H. W. Kroto and D. R. M. Walton, Adv. Mater., 1999, 11, 655–658 CrossRef CAS.
- J. Duan, Y. Zheng, S. Chen, Y. Tang, M. Jaroniec and S. Qiao, Chem. Commun., 2013, 49, 7705–7707 RSC.
- H. Peng, Z. Mo, S. Liao, H. Liang, L. Yang, F. Luo, H. Song, Y. Zhong and B. Zhang, Sci. Rep., 2013, 1765, 1–7 Search PubMed.
- S. Ameen, M. S. Akhtar, M. Song and H. S. Shin, ACS Appl. Mater. Interfaces, 2012, 4, 4405–4412 CAS.
- X. Zheng, J. Deng, N. Wang, D. Deng, W.-H. Zhang, X. Bao and C. Li, Angew. Chem., Int. Ed., 2014, 53, 7023–7027 CrossRef CAS PubMed.
- X. Zou, X. Huang, A. Goswami, R. Silva, B. R. Sathe, E. Mikmeková and T. Asefa, Angew. Chem., Int. Ed., 2014, 126, 4461–4465 CrossRef.
- E. Munoz-Sandoval, N. Perea-Lopez, R. Lima-Juarez, G. J. Labrada-Delgado, B. A. Rivera-Escoto, A. Zamudio, H. G. Silva-Pereyra, E. Robles-Avila and M. Terrones, Carbon, 2014, 77, 722–737 CrossRef CAS.
- L. Lux, K. Williams and S. Ma, CrystEngComm, 2015, 17, 10–22 RSC.
- B. Liu, H. Shioyama, T. Akita and Q. Xu, J. Am. Chem. Soc., 2008, 130, 5390–5391 CrossRef CAS PubMed.
- S. J. Yang, T. Kim, J. H. Im, Y. S. Kim, K. Lee, H. Jung and C. R. Park, Chem. Mater., 2012, 24, 464–470 CrossRef CAS.
- H. L. Jiang, B. Liu, Y. Q. Lan, K. Kuratani, T. Akita, H. Shioyama, F. Zong and Q. Xu, J. Am. Chem. Soc., 2011, 133, 11854–11857 CrossRef CAS PubMed.
- R. Das, P. Pachfule, R. Banerjee and P. Poddar, Nanoscale, 2012, 4, 591–599 RSC.
- T. K. Kim, K. J. Lee, J. Y. Cheon, J. H. Lee, S. H. Joo and H. R. Moon, J. Am. Chem. Soc., 2013, 135, 8940–8946 CrossRef CAS PubMed.
- S. J. Yang, S. Nam, T. Kim, J. H. Im, H. Jung, J. H. Kang, S. Wi, B. Park and C. R. Park, J. Am. Chem. Soc., 2013, 135, 7394–7397 CrossRef CAS PubMed.
- I. A. Khan, A. Badshah, M. A. Nadeem, N. Haider and M. A. Nadeem, Int. J. Hydrogen Energy, 2014, 39, 19609–19620 CrossRef CAS.
- K. S. Park, Z. Ni, A. P. Côté, J. Y. Choi, R. Huang, F. J. Uribe-Romo, H. K. Chae, M. O'Keeffe and O. M. Yaghi, Proc. Natl. Acad. Sci. U. S. A., 2006, 103, 10186–10191 CrossRef CAS PubMed.
- S. Brunauer, P. H. Emmett and E. Teller, J. Am. Chem. Soc., 1938, 60, 309–319 CrossRef CAS.
- Y. Shi, Y. Wan, R. Zhang and D. Zhao, Adv. Funct. Mater., 2008, 18, 2436–2443 CrossRef CAS.
- H. Estrade-Szwarckopf and B. Rousseau, J. Phys. Chem. Solids, 1992, 53(3), 419–436 CrossRef CAS.
- K. L. Smith and K. M. Black, J. Vac. Sci. Technol., A, 1984, 2, 744–747 CAS.
- B. Li, Y. Xie, C. Wu, Z. Li and J. Zhang, Mater. Chem. Phys., 2006, 99, 479–486 CrossRef CAS.
- H.-P. Cong and S.-H. Yu, Cryst. Growth Des., 2009, 9, 210–217 CAS.
- S. Abouali, M. A. Garakani, B. Zhang, H. Luo, Z.-L. Xu, J.-Q. Huang, J. Huang and J.-K. Kim, J. Mater. Chem. A, 2014, 2, 16939–16944 CAS.
- H. Peng, Z. Mo, S. Liao, H. Liang, L. Yang, F. Luo, H. Song, Y. Zhong and B. Zhang, Sci. Rep., 2013, 3, 1765 Search PubMed.
- NIST X-ray Photoelectron Spectroscopy Database, Version 4.1, National Institute of Standards and Technology, Gaithersburg, 2012, http://srdata.nist.gov/xps/ Search PubMed.
- H.-B. Li, A. J. Page, Y. Wang, S. Irle and K. Morokuma, Chem. Commun., 2012, 48, 7937–7939 RSC.
- A. J. Page, K. R. S. Chandrakumar, S. Irle and K. Morokuma, J. Am. Chem. Soc., 2011, 133, 621–628 CrossRef CAS PubMed.
- A. J. Page, F. Ding, S. Irle and K. Morokuma, Rep. Prog. Phys., 2015, 78, 036501 CrossRef CAS PubMed.
- F. Ding, K. Bolton and A. Rosén, J. Phys. Chem. B, 2004, 108, 17369–17377 CrossRef CAS.
- E. Mora, J. M. Pigos, F. Ding, B. I. Yakobson and A. R. Harutyunyan, J. Am. Chem. Soc., 2008, 130, 11840–11841 CrossRef CAS PubMed.
- F. Abild-Pedersen, J. K. Nørskov, J. R. Rostrup-Nielsen, J. Sehested and S. Helveg, Phys. Rev. B: Condens. Matter Mater. Phys., 2006, 73, 115419 CrossRef.
- S. Hofmann, G. Csányi, A. C. Ferrari, M. C. Payne and J. Robertson, Phys. Rev. Lett., 2005, 95, 036101 CrossRef CAS PubMed.
- Y. Shibuta and S. Maruyama, Chem. Phys. Lett., 2007, 437, 218–223 CrossRef CAS.
- W.-Q. Tian, X.-Y. Wu, K.-X. Wang, Y.-M. Jiang, J.-F. Wang and J.-S. Chen, RSC Adv., 2013, 3, 10823–10827 RSC.
- G. X. Wang, Y. Chen, K. Konstantinov, J. Yao, J.-h. Ahn, H. K. Liu and S. X. Dou, J. Alloys Compd., 2002, 340, L5–L10 CrossRef CAS.
- T. Chen, L. Pan, T. A. J. Loh, D. H. C. Chua, Y. Yao, Q. Chen, D. Li, W. Qin and Z. Sun, Dalton Trans., 2014, 40, 14931–14935 RSC.
- X. Li, J. Liu, Y. Zhang, Y. Li, H. Liu, X. Meng, J. Yang, D. Geng, D. Wang, R. Li and X. Sun, J. Power Sources, 2012, 197, 238–245 CrossRef CAS.
- Y. Tan, K. Zhu, D. Li, F. Bai, Y. Wei and P. Zhang, Chem. Eng. J., 2014, 258, 93–100 CrossRef CAS.
- H. Yue, Z. Shi, Q. Wang, Z. Cao, H. Dong, Y. Qiao, Y. Yin and S. Yang, ACS Appl. Mater. Interfaces, 2014, 6, 17067–17074 CAS.
- Y. Xiao, P. Sun and M. Cao, ACS Nano, 2014, 8, 7846–7857 CrossRef CAS PubMed.
- S. M. Abbas, S. T. Hussain, S. Ali, N. Ahmad, N. Ali and K. S. Munawar, Electrochim. Acta, 2013, 105, 481–488 CrossRef CAS.
- B. Wang, Y. Wang, J. Park, H. Ahn and G. Wang, J. Alloys Compd., 2011, 509, 7778–7783 CrossRef CAS.
- B. C. Yu, J. O. Lee, J. H. Song, C. M. Park, C. K. Lee and H. J. Sohn, J. Solid State Electrochem., 2012, 16, 2631–2638 CrossRef CAS.
- J. Wang, B. Niu, G. Du, R. Zeng, Z. Chen, Z. Guo and S. Dou, Mater. Chem. Phys., 2011, 126, 747–754 CrossRef CAS.
- X. Y. Xue, S. Yuan, L. L. Xing, Z. H. Chen, B. He and Y. J. Chen, Chem. Commun., 2011, 47, 4718–4720 RSC.
- H. Wang, D. Ma, X. Huang, Y. Huang and X. Zhang, Sci. Rep., 2012, 2, 701 Search PubMed.
- Z.-L. Wang, D. Xu, H.-G. Wang, Z. Wu and X.-B. Zhang, ACS Nano, 2013, 7, 2422–2430 CrossRef CAS PubMed.
- X.-l. Huang, R.-z. Wang, D. Xu, Z.-l. Wang, H.-g. Wang, J.-j. Xu, Z. Wu, Q.-c. Liu, Y. Zhang and X.-b. Zhang, Adv. Funct. Mater., 2013, 23, 4345–4353 CrossRef CAS.
- X.-l. Huang, J. Chai, T. Jiang, Y.-J. Wei, G. Chen, W.-q. Liu, D. Han, L. Niu, L. Wang and X.-b. Zhang, J. Mater. Chem., 2012, 22, 3404–3410 RSC.
- Y. Huang, X.-l. Huang, J.-s. Lian, D. Xu, L.-m. Wang and X.-b. Zhang, J. Mater. Chem., 2012, 22, 2844–2847 RSC.
- X.-l. Huang, X. Zhao, Z.-l. Wang, L.-m. Wang and X.-b. Zhang, J. Mater. Chem., 2012, 22, 3764–3769 RSC.
- H. Song, L. Shen and C. Wang, J. Mater. Chem. A, 2014, 2, 20597–20604 CAS.
- H. Yue, Z. Shi, Q. Wang, T. du, Y. Ding, J. Zhang, N. Huo and S. Yang, RSC Adv., 2015, 5, 75653–75658 RSC.
- K. Wenelska, C. Neef, L. Schlestein, R. Klingeler, R. J. Kalenczuk and E. Mijowska, Chem. Phys. Lett., 2015, 635, 185–189 CrossRef CAS.
Footnote |
† Electronic supplementary information (ESI) available. See DOI: 10.1039/c5ra23222h |
|
This journal is © The Royal Society of Chemistry 2016 |
Click here to see how this site uses Cookies. View our privacy policy here.