DOI:
10.1039/C5RA22111K
(Paper)
RSC Adv., 2016,
6, 21802-21807
Metallic glass formation in Cu–Ni–Ti (Zr, Hf) systems studied by thermodynamic calculations
Received
22nd October 2015
, Accepted 3rd February 2016
First published on 4th February 2016
Abstract
For the family of Cu–Ni–Ti (Zr, Hf) systems, which are promising for obtaining bulk metallic glasses, glass formation regions were calculated based on the extended Miedema’s model and Alonso’s method. It is found that the calculated glass formation regions of the Cu–Ni–Zr and Cu–Ni–Hf systems agree well with experimental results, whereas it does not for the Cu–Ni–Ti system. The composition dependence of the glass forming ability in the Cu–Ni–Ti (Zr, Hf) systems were then predicted, and it turns out that the glass forming ability of the Cu–Ni–Ti system largely deviates from the experimental results, from which it is assumed that kinetic factors (low liquidus temperature) instead of thermodynamic factors cause the Cu-rich composition to easily form glass in the Cu–Ni–Ti system. Meanwhile, the effect of Ti (Zr, Hf) on the glass forming ability was discussed in terms of the mixing enthalpy and atomic size effect.
1. Introduction
Since the first amorphous alloy was obtained by Klement et al. via liquid melt quenching (LMQ) in the Au–Si system in 1960,1 a large number of metallic glasses have been developed in Cu-, Ni-, Zr-, and Hf-based systems, exhibiting inviting properties such as high mechanical strength and good corrosion resistance.2 Over the past few decades, bulk metallic glasses (BMGs) have attracted extensive interest due to their unique properties, and BMGs have emerged as a new class of materials with near theoretical strength and large elastic strain. In order to produce bulk metallic glasses (BMGs), one of the fundamental issues is to develop a method/model capable of predicting the quantitative glass formation range (GFR) of a metallic system, e.g. a composition range for a binary metallic system, or a composition region for a ternary metallic system, within which the formation of metallic glass is energetically favored. Concerning this issue, several empirical criteria and models have been proposed in the past few decades to predict the GFR of a metal system. For instance, Turnbull proposed a ratio of the glass transition temperature Tg to the melting point Tm, referred to as the reduced glass transition temperature Trg = Tg/Tm, used as a criterion to determine the glass forming ability (GFA) of an alloy.3 In the early 1980s, Egami and Waseda suggested an empirical formula to predict the GFR based on the atomic size effect, which correlates with the instability of the solid solution when the solute concentration reaches a critical value.4 Although these empirical criteria or rules have served as guidelines for synthesizing metallic glasses for decades, they still belong to the empirical models and some essential experimental parameters cannot be predicted a priori. From a thermodynamic point of view, Miedema’s model and Alonso’s method have been proposed as effective semi-empirical approaches to predict metallic glass formation a priori and they have been used to explain some fundamental issues of metallic glass formation.5,6
In the present study, we focus our attention on the metallic glass formation of the ternary Cu–Ni–Ti (Zr, Hf) systems which have been revealed to be quite promising for obtaining BMGs. For example, the Cu–Ni–Ti bulk metallic glass composite has good shape memory properties,7 and the Cu–Ni–Zr system has excellent mechanic properties.8 The Cu–Ti (Zr, Hf) and Ni–Ti (Zr, Hf) systems are miscible while the Cu–Ni system is immiscible. Therefore the Ti (Zr, Hf) content is the dominating factor for metallic glass formation. Meanwhile, the difference in atomic sizes between Cu–Ti (Zr, Hf) and Ni–Ti (Zr, Hf) are relatively large, with a maximal difference of more than 17%, which facilitates the formation of amorphous alloys. In the present study, thermodynamic calculations based on the extended Miedema’s model and Alonso’s method were employed to predict the GFR and GFA of the intriguing Cu–Ni–Ti (Zr, Hf) systems.
2. Thermodynamic calculations
Miedema’s model and Alonso’s method have been proposed as thermodynamic approaches to predict the glass formation range of a binary system, by comparing the enthalpy of formation of the solid solution and amorphous phase. Generally, the Gibbs free energy of an alloy phase could be calculated using ΔG = ΔH − TΔS, where ΔH and ΔS are the enthalpy and entropy terms, respectively. As a first approximation, the entropy term ΔS for a concentrated solid solution or an amorphous phase is simply taken as that of an ideal solution. For a ternary alloy system with constituents A, B and C, ΔS could be calculated as |
ΔS = −R[cA ln cA + cB ln cB + cC ln cC]
| (1) |
where R is the gas constant and cA, cB and cC are the atomic concentrations of metals A, B and C, respectively.
According to the work by Gallego et al.,9 the enthalpy of formation of a ternary solid solution of transition metals A, B and C is given by
|
ΔHssABC = ΔHcABC + ΔHeABC + ΔHsABC
| (2) |
where Δ
HcABC, ΔH
eABC and Δ
HsABC are the chemical, elastic and structural contributions, respectively. The chemical term Δ
HcABC which is related to the electron redistribution can be divided into contributions of three binary subsystems as
|
ΔHcABC = ΔHcAB + ΔHcAC + ΔHcBC
| (3) |
where Δ
HcAB, Δ
HcAC and Δ
HcBC are the chemical terms of the three binary subsystems. For the binary subsystem, the chemical term Δ
HcAB is given by
|
ΔHcAB = cAcB[cBΔ interA in B + cAΔ interB in A]
| (4) |
where
cA,
cB and
cC are the atomic concentrations of metals A and B, Δ
interA in B and Δ
interB in A are the electron redistribution contributions to the enthalpies of A dissolved in B and that of B dissolved in A. Further considering the chemical short-range order (CSRO) of the alloy phases, the right-hand side of
eqn (3) should be multiplied by a factor
where
csA and
csB are the cell surface concentrations, which can be calculated using
|
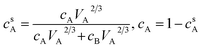 | (6) |
The γ is an empirical constant which is used to describe the degree of chemical short-range order in different alloys. For the statistically disordered solid solution, there is hardly any degree of chemical short-range order and the parameter γ should be taken as 0.10 For ordered alloys (compounds in particular), the short-range order around each type of atom is entirely fixed and the γ was equal to 8, indicating the highest degree of chemical order.10,11 For the amorphous phase, it has been revealed through atomistic simulations as well as several experimental studies that CSRO indeed exists in Cu–Ni–(Ti, Zr, Hf)-related metallic glasses,12,13 and γ was taken to be 5 for the amorphous phase and this setting was found to be in reasonable agreement with the actual situation.10,14
The elastic term ΔHeABC is an atomic size mismatch contribution and could also be divided into three binary subsystem terms,
|
ΔHeABC = ΔHeAB + ΔHeAC + ΔHeBC
| (7) |
For the binary subsystem consisting of A and B, the chemical term ΔHeAB is given by
|
ΔHeAB = cAcB[cBΔ elasticA in B+ cAΔ elasticB in A
| (8) |
where
cA and
cB are the atomic concentrations of metals A and B, while Δ
elasticA in B and Δ
elasticB in A are the elastic contributions to the enthalpies of A dissolved in B and that of B dissolved in A.
The structural contribution ΔHsABC reflects the correlation between the number of valence electrons and the crystal structure of the transition metals. It can be deduced from the lattice stability Eσ(Z) of each crystal structure σ (σ = bcc, fcc or hcp) as a function of the number of valence electrons Z of the metal,
|
ΔHsABC = Eσ( ) − [cAEσ(ZA) + cBEσ(ZB) + cCEσ(ZC)]
| (9) |
where
cA,
cB and
cC are the atomic concentrations of metals A, B and C,
![[Z with combining macron]](https://www.rsc.org/images/entities/i_char_005a_0304.gif)
,
ZA,
ZB and
ZC are the numbers of mean valence electrons of the alloy phase and valence electrons of the pure metals A, B and C, while
Eσ(
![[Z with combining macron]](https://www.rsc.org/images/entities/i_char_005a_0304.gif)
),
Eσ(
ZA),
Eσ(
ZB) and
Eσ(
ZC) are the lattice stability parameters of the alloy phase and the pure metals A, B and C, respectively.
For the amorphous phase, both the elastic term ΔHeABC and the structural term ΔHsABC are absent,5,6 but the enthalpy difference between the amorphous and crystalline states of pure metals ΔHtopologicalABC should be considered. The formation enthalpy ΔHamABC of the amorphous phase can thus be written as
|
ΔHamABC = ΔHcABC + cAΔHa-sA + cBΔHa-sB + cCΔHa-sC
| (10) |
where
cA,
cB and
cC are the atomic concentrations of metals A, B and C, respectively, while Δ
Ha-sA, Δ
Ha-sB and Δ
Ha-sC are the enthalpy differences between the amorphous and crystalline states. This quantity is given by
where
α = 3.5 J mol
−1 K
−1 and
Tm,i is the melting temperature of component
i.
By comparing the Gibbs free energies of the solid solution and the amorphous phase, an estimate of the GFA of a ternary transition metal alloy system can be obtained. Since the entropy terms for concentrated solid solutions and amorphous phases are both taken as ideal solutions, comparison of the enthalpies of them is enough. Accordingly, the GFA of a ternary alloy consisting of metals A, B and C can be evaluated as15
|
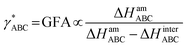 | (12) |
The lager the value of γ*ABC, the better the GFA of the corresponding composition in the alloy system.
3. Results and discussion
The thermodynamic calculation results for the Cu–Ni–Ti (Zr, Hf) systems are presented here. The complicated phase could not nucleate and grow due to the extremely restricted kinetic conditions during the process of producing metallic glasses. It follows that the competing amorphous phase is the terminal solid solution phase, whose structure is relatively simple. Accordingly, the issue of predicting the favored glass formation compositions could be converted into an issue of comparing the stability of the amorphous phase versus the solid solution phase. Therefore, by comparing the relative energy status of the amorphous phase versus the solid solution phase, the compositions which are energetically favored for metallic glass formation can thus be located.
Table 1 shows the atomic radius, electronic structure, crystal structure and atomic size difference of these elements. According to Miedema’s model, the heats of formation (ΔHf) of the Cu–Ni, Cu–Ti, Cu–Zr, Cu–Hf, Ni–Ti, Ni–Zr, and Ni–Hf systems are +5 kJ mol−1, −23 kJ mol−1, −14 kJ mol−1, −19 kJ mol−1, −35 kJ mol−1, −49 kJ mol−1, −42 kJ mol−1, respectively.6 The parameters used in the thermodynamic calculations of the Cu–Ni–Ti (Zr, Hf) systems are listed in Table 2. For the Cu–Ni system, they are immiscible and the Gibbs free energy is always positive, however, the appropriate addition of Ti (Zr, Hf) can significantly change the difference in atomic sizes as well as the electron redistribution, which are both highly related with the GFR of the system. According to Miedema’s model and Alonso’s method, an estimate of the GFR of a ternary transition metal alloy system can be obtained through comparing the Gibbs free energies of the solid solution and the amorphous phase, if the Gibbs free energy of the amorphous phase is lower than that of the solid solution, the amorphous could be obtained for the corresponding composition of the alloy system. Then we projected the predicted glass formation region onto a composition triangle which reflects the thermodynamic characteristics of each ternary system in Fig. 1. If an alloy composition is located inside the defined green dot region the amorphous phase is energetically favored, while when it is located outside, the crystalline solid solution is favored. To validate the amorphous region i.e., the glass formation region (GFR) in Fig. 1, the related experimental results were collected and are shown as red dots.7,16–34 From Fig. 1, one can see that these experimentally measured glass formation compositions mostly fall within the predicted GFR for the Cu–Ni–Zr (Hf) systems, suggesting that the results predicted by Miedema’s model and Alonso’s method are acceptable in determining the glass formation region of the Cu–Ni–Zr (Hf) ternary systems. While for the Cu–Ni–Ti system, the thermodynamic calculations deviated from the experimental results, we speculate that the main factor for metallic glass formation in this system could be kinetic instead of thermodynamic.
Table 1 Atomic radius, atomic size difference, electronic structure and crystal structure of the elements in the Cu–Ni–Ti (Zr, Hf) systems
Elements |
Atomic radius (Å) |
Electronic structure |
Crystal structure |
|ri − rCu|/rCu |
|ri − rNi|/rNi |
Cu |
1.28 |
3d104s1 |
fcc |
0 |
2.4% |
Ni |
1.25 |
3d84s2 |
fcc |
2.4% |
0 |
Ti |
1.47 |
3d24s2 |
hcp |
14.8% |
17.6% |
Zr |
1.60 |
4d25s2 |
hcp |
25.6% |
28.0% |
Hf |
1.62 |
4f145d26s2 |
hcp |
26.6% |
29.6% |
Table 2 The parameters used in the thermodynamic calculations on the Cu–Ni–Ti (Zr, Hf) system (ref. 6). Δ
interA in B, Δ
interB in A, Δ
elasticA in B, Δ
elasticB in A and Eσ(ZA) are expressed in kJ mol−1, while Tm,i is expressed in K
|
Eσ(ZA) |
Tm,i |
Δ interA in B |
Δ interB in A |
Δ elasticA in B |
Δ elasticB in A |
Cu |
1.5 |
1357.6 |
|
|
|
|
Ni |
−2.0 |
1726.0 |
|
|
|
|
Ti |
−2.5 |
1943.0 |
|
|
|
|
Zr |
−2.5 |
2125.0 |
|
|
|
|
Hf |
−2.5 |
2500.0 |
|
|
|
|
Cu–Ni |
|
|
+14 |
+14 |
+0.09 |
+2.58 |
Cu–Ti |
|
|
−33 |
−40 |
+20.41 |
+32.81 |
Cu–Zr |
|
|
−78 |
−110 |
+61.33 |
+94.57 |
Cu–Hf |
|
|
−58 |
−81 |
+74.99 |
+97.04 |
Ni–Ti |
|
|
−126 |
−154 |
+38.38 |
+40.31 |
Ni–Zr |
|
|
−165 |
−237 |
+93.09 |
+95.49 |
Ni–Hf |
|
|
−145 |
−204 |
+116.68 |
+107.26 |
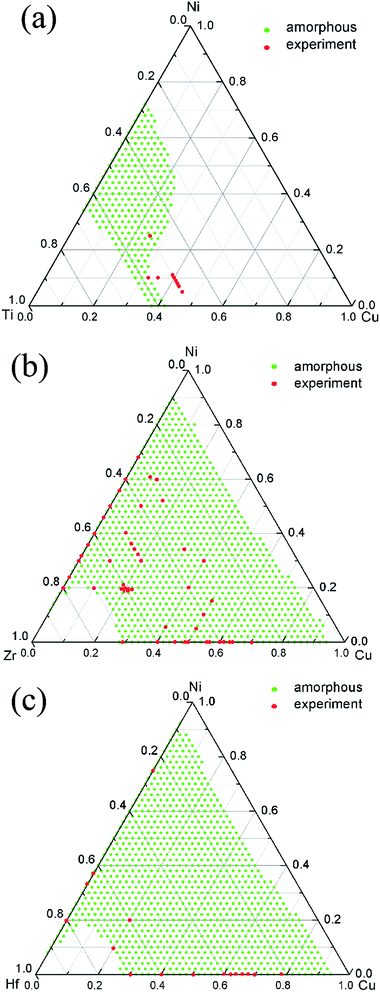 |
| Fig. 1 Glass formation compositions of the (a) Cu–Ni–Ti, (b) Cu–Ni–Zr and (c) Cu–Ni–Hf alloy systems predicted using thermodynamic calculations. | |
Furthermore, we pinpointed the compositions with large GFA inside the determined glass formation region. To evaluate the composition dependence of GFA and locate the compositions with relatively large GFA, the parameter γ* was further calculated over the entire predicted GFR. Meanwhile, one can see from Fig. 2 that the best of the Cu–Ni–Ti (Zr, Hf) systems at glass forming, calculated based on Miedema’s model, Alonso’s method and Xia’s theory,5,6,15 are the compositions Cu1Ni56Ti43, Cu19Ni27Zr54 and Cu10Ni56Hf34 indicated by the black pentagrams. Experimentally, Gargarella et al.7 considered the Cu43Ni7Ti50 alloy to have the best GFA in their report, while Yang et al.19 have obtained a series of Cu–Ni–Zr glassy rods, finding the alloy Cu20Ni18Zr62 to have the largest reduced glass-transition temperature and Cui et al.35 have reported that Cu10Ni45Hf45 has the largest glass formation driving force calculated from an atomistic simulation. As indicated above, the experimental results are in good agreement with the present predictions for Cu–Ni–Zr (Hf) systems, despite some minor deviation. The minor deviation may mainly result from Miedema’s model and Alonso’s method being empirical approaches and the model being strictly only valid at low temperature.
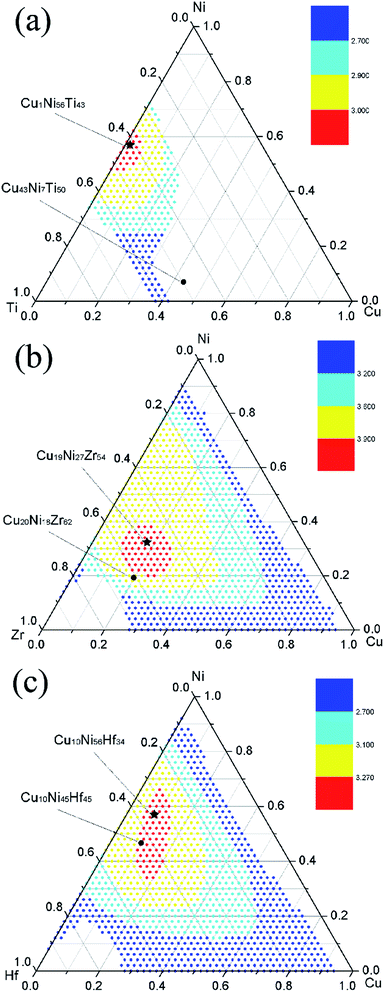 |
| Fig. 2 Calculated γ*ABC in the GFRs of the (a) Cu–Ni–Ti, (b) Cu–Ni–Zr and (c) Cu–Ni–Hf alloy systems. The red regions are the compositions which have the largest γ*ABC, i.e., the best GFA as well as vicinity compositions. | |
From the above analyses, one can see that the glass formation regions of the Cu–Ni–Zr and Cu–Ni-Hf systems are similar, while the GFR and GFA/best at glass forming of the Cu–Ni–Ti alloy system are different from that for Cu–Ni–Zr (Hf). Meanwhile, it was found that the best glass forming composition of the Cu–Ni–Ti system calculated using thermodynamic calculations largely deviates from the experiment results. Specifically, early studies have shown that the GFA for the ternary Cu–Ni–Ti alloy system is good for Cu-rich compositions and poor for Ni-rich compositions,36 which is contrary to the result of thermodynamic calculations in Fig. 2(a). From the Cu–Ni–Ti phase diagram,37 one can see that the liquidus temperature of the Cu-rich composition is lower than that of the Ni-rich composition, and Gupta et al.38 have found that the liquidus temperature increases with increasing Ni content of the Cu–Ni–Ti alloy system. Then we speculated that the kinetic factors instead of thermodynamic factors have a much more important role in the glass formation of the Cu–Ni–Ti alloy system. Generally, the glass formation process can be influenced by thermodynamic factors as well as kinetic factors, such as cooling rate and overheating during producing etc, and we consider the thermodynamic factors as intrinsic ones. However, for certain alloy systems, the kinetic factors may play a much more important role during the glass formation process. Consequently, the predicted GFR and the so-called GFA could exhibit some deviation from the practically observed characteristics. For the Cu–Ni–Ti alloy system, the main kinetic factors that exert effect on glass formation are the glass transition temperature (Tg) and cooling rate etc. It is in general accepted that the glass transition temperature (Tg) is not a strong function of composition and the liquid should be undercooled to below Tg for glass formation. As a result, if for a given alloy with higher liquidus temperature, the cooling time would be longer and is in favor of nucleation instead of glass formation, while for an alloy with lower liquidus temperature, the cooling time would be shorter at the same cooling rate and nucleation is restrained, then metallic glass would be obtained. Accordingly, the kinetic consideration of a low liquidus temperature causes the Cu-rich composition to easily form glass, while the higher liquidus temperature of the Ni-rich composition results in it having poor glass forming ability with larger possibility to obtain crystalline phases such as CuTi, NiTi, etc. Thereby, for the Cu–Ni–Ti ternary alloy system in which the kinetic factor plays a principle role in glass formation, thermodynamic calculations based on Miedema’s model and Alonso’s method may not quite be accurate.
4. Conclusion
Based on Miedema’s model and Alonso’s method, the GFR and GFA of the Cu–Ni–Ti (Zr, Hf) ternary alloy systems have been predicted. It was found that thermodynamic calculations of GFR and GFA are in good agreement with the experimental results for the Cu–Ni–Zr (Hf) systems, while for the Cu–Ni–Ti alloy system, the calculated results largely deviated from experimental results in terms of the Cu and Ni content, and it is assumed that kinetic factors instead of thermodynamic factors have a much more important role in glass formation for the Cu–Ni–Ti alloy system. Specifically, kinetic consideration shows that low liquidus temperature reduces the cooling time causing less nucleation, resulting in the Cu-rich composition easily forming a glass, while the higher liquidus temperature of the Ni-rich composition results in a longer cooling time and stimulates nucleation with larger possibility for obtaining crystalline phases such as CuTi, NiTi, etc., and the Ni-rich composition would have poor glass forming ability.
Acknowledgements
The authors are grateful for the financial support from the National Natural Science Foundation of China (51131003, 51571129), the Ministry of Science and Technology of China (973 Program 2012CB825700), and the Administration of Tsinghua University.
References
- W. Klement, R. H. Willens and P. Duwez, Nature, 1960, 187, 869–870 CrossRef CAS.
- J. S. C. Jang, K. C. Wu, S. R. Jian, P. J. Hsieh, J. C. Huang and C. T. Liu, J. Alloys Compd., 2011, 5091, S109–S114 CrossRef.
- D. Turnbull, Trans. Metall. Soc. AIME, 1961, 221, 422–439 CAS.
- T. Egami and Y. Waseda, J. Non-Cryst. Solids, 1984, 64, 113–134 CrossRef CAS.
- J. A. Alonso, L. J. Gallego and J. A. Somoza, Nuovo Cimento, 1990, 12, 587–595 CrossRef.
- F. R. de Boer, R. Boom, W. C. M. Mattens, A. R. Miedema and A. K. Niessen, Cohesion in Metals: Transition Metal Alloys, Elsevier Science Publishers B. V, Amsterdam, 1988 Search PubMed.
- P. Gargarella, S. Pauly, K. K. Song, J. Hu, N. S. Barekar, M. S. Khoshkhoo, A. Teresiak, H. Wendrock, U. Kuehn, C. Ruffing, E. Kerscher and J. Eckert, Acta Mater., 2013, 61, 151–162 CrossRef CAS.
- W. H. Wang, C. Dong and C. H. Shek, Mater. Sci. Eng., R, 2004, 44, 45–89 CrossRef.
- L. J. Gallego, J. A. Somoza and J. A. Alonso, J. Phys.: Condens. Matter, 1990, 2, 6245–6250 CrossRef CAS.
- R. H. de Tendler, M. R. Soriano, M. E. Pepe, J. A. Kovacs, E. E. Vicente and J. A. Alonso, Intermetallics, 2006, 14, 297–307 CrossRef.
- A. R. Miedema, J. Less-Common Met., 1973, 32, 117–136 CrossRef CAS.
- I. Kaban, P. Jovari, V. Kokotin, O. Shuleshova, B. Beuneu, K. Saksl, N. Mattern, J. Eckert and A. L. Greer, Acta Mater., 2013, 61, 2509–2520 CrossRef CAS.
- I. Bakonyi, J. Non-Cryst. Solids, 1995, 180, 131–150 CrossRef CAS.
- T. L. Wang and B. X. Liu, J. Alloys Compd., 2009, 481, 156–160 CrossRef CAS.
- L. Xia, S. S. Fang, Q. Wang, Y. D. Dong and C. T. Liu, Appl. Phys. Lett., 2006, 88, 171905 CrossRef.
- P. Gargarella, S. Pauly, M. Stoica, G. Vaughan, C. R. M. Afonso, U. Kuehn and J. Eckert, APL Mater., 2015, 3, 016101 CrossRef.
- X. F. Wu, Z. Y. Suo, Y. Si, L. K. Meng and K. Q. Qiu, J. Alloys Compd., 2008, 452, 268–272 CrossRef CAS.
- R. Ristic, M. Stubicar and E. Babic, Philos. Mag., 2007, 87, 5629–5637 CrossRef CAS.
- H. Yang, J. Q. Wang and Y. Li, J. Non-Cryst. Solids, 2006, 352, 832–836 CrossRef CAS.
- G. Duan, D. H. Xu and W. L. Johnson, Metall. Mater. Trans. A, 2005, 36A, 455–458 CrossRef CAS.
- D. H. Xu, B. Lohwongwatana, G. Duan, W. L. Johnson and C. Garland, Acta Mater., 2004, 52, 2621–2624 CrossRef CAS.
- A. Inoue and W. Zhang, Mater. Trans., 2004, 45, 584–587 CrossRef CAS.
- H. R. Wang, Y. L. Gao, X. D. Hui, G. H. Min, Y. Chen and Y. F. Ye, J. Alloys Compd., 2003, 349, 129–133 CrossRef CAS.
- C. J. Hu and P. Y. Lee, Mater. Chem. Phys., 2002, 74, 13–18 CrossRef CAS.
- C. F. Li, L. M. Wang and A. Inoue, Mater. Lett., 2001, 51, 203–207 CrossRef CAS.
- J. Garaguly, A. Lovas, K. Tompa and J. Takacs, J. Alloys Compd., 1997, 253, 114–117 CrossRef.
- L. Stojanova and K. Russew, Materials Science & Engineering, A: Structural Materials: Properties, Microstructure and Processing, 1997, 226, 483–486 Search PubMed.
- M. Ming and Z. Altounian, J. Non-Cryst. Solids, 1996, 205–207, 633–636 Search PubMed.
- G. Peto, I. Bakonyi, K. Tompa and L. Guczi, Phys. Rev. B: Condens. Matter Mater. Phys., 1995, 52, 7151–7158 CrossRef CAS.
- O. Haruyama, I. Kanazawa, N. Asahi, M. Ito and T. Iwashita, J. Non-Cryst. Solids, 1995, 192–193, 451–455 CrossRef.
- T. Zhang, A. Inoue and T. Masumoto, Mater. Sci. Eng., A, 1994, 181, 1423–1426 CrossRef CAS.
- M. Vanrossum, M. A. Nicolet and W. L. Johnson, Phys. Rev. B: Condens. Matter Mater. Phys., 1984, 29, 5498–5503 CrossRef CAS.
- Z. Altounian and J. O. Stromolsen, Phys. Rev. B: Condens. Matter Mater. Phys., 1983, 27, 4149–4156 CrossRef CAS.
- K. Buschow, J. Appl. Phys., 1981, 52, 3319–3323 CrossRef CAS.
- Y. Y. Cui, X. Bai, S. Y. Luo, Q. Wang, J. H. Li and B. X. Liu, J. Alloys Compd., 2013, 552, 55–59 CrossRef CAS.
- B. S. Murty, M. M. Rao and S. Ranganathan, Mater. Sci. Eng., A, 1995, 196, 237–241 CrossRef.
- Q. Y. Zhang and H. S. Zhuang, San Yuan He Jin Xiang Tu Shou Ce, China Machine PRESS, 2011 Search PubMed.
- P. G. Gupta, Phase Diagrams of Ternary Ni Alloys, Indian Institute of Metals, Calcutta, 1990 Search PubMed.
|
This journal is © The Royal Society of Chemistry 2016 |
Click here to see how this site uses Cookies. View our privacy policy here.