DOI:
10.1039/C5NJ02509E
(Paper)
New J. Chem., 2016,
40, 589-595
Preparation of porous alumina microspheres via an oil-in-water emulsion method accompanied by a sol–gel process
Received
(in Montpellier, France)
17th September 2015
, Accepted 3rd November 2015
First published on 10th November 2015
Abstract
Porous alumina (Al2O3) microspheres with incontinuous multicavities have been successfully prepared via an oil-in-water (O/W) emulsion method accompanied by a sol–gel process in the presence of polyvinylpyrrolidone (PVP), sorbitan monooleate (Span 80) and ethyl acetoacetate (EAA). The introduction of PVP as a phase separation inducer into the oil phase of the O/W emulsion leads to the formation of incontinuous multicavities inside the microspheres, and the size of the cavities enlarges with the increase of the amount of PVP, while has no significant influence on the surface morphology and particle size distribution of the microspheres. EAA works as a chelating agent to ensure a spherical shape, and Span 80 acts as a stabilizer to preserve a smooth surface. An appropriate amount of PVP, EAA and Span 80 allow the formation of porous alumina microspheres with incontinuous multicavities. A preliminary mechanism based on phase separation for the structural evolution of alumina porous microspheres with multicavities is suggested. The spheres after heat treatment experience a phase transformation process in the following sequence: amorphous → γ-Al2O3 → α-Al2O3.
1 Introduction
Porous microspheres have recently attracted much attention owing to their low density, high specific surface area, low thermal conductivity, good flow ability and attractive optical properties, which contributing to their extensive application in the areas such as catalysis, drug delivery, chromatography separation, chemical reactors, and controlled release of various substances.1–5 To date, numerous synthetic approaches, such as emulsion routes,6–8 layer-by-layer, self-assembly techniques,9 templating methods10,11 and solvothermal reactions,12 have been developed for the fabrication various fascinating porous microspheres with unique characteristics. Wherein, porous microspheres with multicavities as an important class of porous microspheres have gained more and more attention due to their potential applications such as heat insulation and separation.13,14
Porous alumina microspheres are widely used as absorbents, composite materials, ceramics and a catalyst support due to their instinct porous structures, large surface areas, high stability and various acid/basic sites.15–17 In most of previous reports on alumina microspheres, soft or hard templating methods,18,19 and spray drying or pyrolysis approaches20,21 were employed. However, templating methods are time-consuming, laborious and expensive. Spherical particles prepared by traditional spray drying or pyrolysis methods have thick shells, broad size distributions and significant aggregations. Therefore, detecting an effective template-free approach for the preparation of alumina porous microspheres is of great importance. Meanwhile, we notice that the preparation of porous alumina microspheres with multicativies has not been reported in the open literature.
In the present work, we demonstrate a facile template-free synthesis of alumina porous microspheres with incontinuous multicavities via an oil-in-water (O/W) emulsion method accompanied by a sol–gel process. It is found that polyvinylpyrrolidone (PVP) used as a phase separation inducer plays an important role in forming porous structures of alumina microspheres, while ethyl acetoacetate (EAA) added as a chelating agent and sorbitan monooleate (Span 80) a stabilizer have great effects on preserving spherical structure and smooth surface of microspheres, respectively. In addition, the influence of heat-treatment conditions on the crystalline phase and the porous structure is also investigated. Upon further investigation, this porous material has potential applications in liquid chromatography and heat insulation.
2 Material and methods
2.1 Raw materials
Aluminum sec-butoxide (ASB, C12H27AlO3: Aladdin Co., China, 97%, AR) was utilized as an aluminum source. 1-octanol (C8H18O: Aladdin Co., China, AR) was used as a solvent. Polyvinylpyrrolidone (PVP-K30: Sinopharm Chemical Reagent Co. Ltd, China, CP) was used as a phase separation inducer. Ethyl acetoacetate (EAA: Aladdin Co., China, AR) was added as a chelating agent. Sorbitan monooleate (Span 80: Aladdin Co., China, AR), sodium dodecylsulfate and alkylphenolethoxylates (SDS and OP-10: Sinopharm Chemical Reagent Co. Ltd, China, CP) were added as surfactants. All reagents were used as received.
2.2 Synthesis of alumina porous microspheres
The starting compositions are listed in Table 1. In a typical synthesis, at first, 4.0 g of SDS and 8.0 g of OP-10 were dissolved in 300 ml of deionized water, acting as an external water phase. Then, 2.377 g of EAA and 4.545 g of ASB (EAA/ASB = 1 in molar ratio) were added into 10.450 g 1-octanol under constant stirring for 1 h to form the oil phase. Subsequently, WPVP g of PVP and 0.571 g of Span 80 were added slowly (about 0.5 g min−1) into the oil phase by vigorous stirring. After mixing for 30 min, the obtained homogeneous solution was added into the water phase once under strong stirring at 1000 rpm. After stirring for 24 h at room temperature, the products were collected after centrifugation and being washed with ethanol three times. Afterwards, the obtained powders were dried at 40 °C for 24 h. Some of the resultant gel microspheres were subsequently heat-treated at various temperatures up to 1300 °C for 2 h with a heating rate of 5 °C min−1.
Table 1 Starting compositions of the reaction mixtures in this study
Materialsa |
PVP (g) |
EAA/ASBb |
Span 80 (g) |
4.0 g SDS, 8.0 g OP-10, 4.545 g ASB, 10.450 g 1-octanol and 300 ml H2O were used in each reaction mixture.
EAA/ASB = 0–2 in molar ratio.
|
AM1 |
0 |
1 |
0.571 |
AM2 |
0.286 |
1 |
0.571 |
AM3 |
0.571 |
1 |
0.571 |
AM4 |
1.142 |
1 |
0.571 |
AM5 |
1.713 |
1 |
0.571 |
AM6 |
0 |
0 |
0.571 |
AM7 |
0 |
2 |
0.571 |
AM8 |
1.142 |
1 |
0 |
2.3 Characterization methods
Morphologies of dried and heat-treated microspheres were observed using a field-emission scanning electron microscope (FESEM: S-4800, Hitachi, Japan). The crystal structure was confirmed by powder X-ray diffraction (XRD: Empyrean 200895, PANalytical B.V., Holland), employing Cu Kα radiation in the range of 2θ = 10–80°. Chemical bonding information on the dried microspheres was obtained by Fourier transform infrared spectroscopy (FT-IR: Nicolet 5700, ThermoFisher Co., USA). Thermal analysis for the Al2O3 gel microspheres was carried out using a TG-DTA analyzer (STA449C, Netzsch Co., German) at a heating rate of 10 °C min−1. Particle size analysis was performed on a laser particle size analyzer (LS 230, BeckmanCoulter, US), using ethanol as the dispersing agent.
3. Results and discussion
3.1 Formation Mechanism of the microspheres
The formation mechanism of alumina microspheres with and without multicavities through the oil-in-water emulsion system is schematically shown in Fig. 1. In the case of solid alumina microspheres, when 1-octanol solution containing aluminum sec-butoxide (the oil phase) is mixed sufficiently with the water phase and cut into small spherical droplets by high-speed shearing, water molecules around the oil droplets diffuse through the oil–water interface and react with ASB to initiate the sol–gel process, consisting of hydrolysis and polycondensation. As the reaction proceeds, the viscosity of oil droplets keeps increasing until the sol–gel transition occurs, which leads to the transformation of the droplets into gel spheres. As a result, the solid alumina microspheres can be obtained.
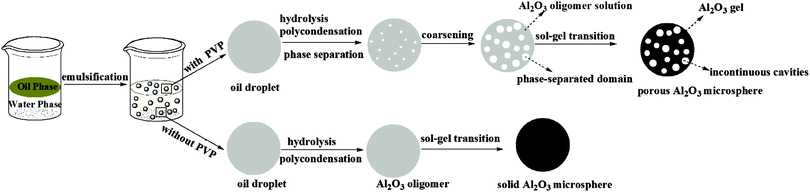 |
| Fig. 1 Schematic illustration of the formation of solid and porous alumina microspheres. | |
Unlike solid alumina microspheres, the mechanism for the formation of the porous alumina microspheres with multicavities can be explained on the basis of a nucleation-growth phase-separation model. As described by Nakanishi,22 the polymerization and gel forming reactions causing a phase separation are thermodynamically analogous to the continuous cooling of a glass-forming liquid into a miscibility gap,23 which can be described as “chemical cooling24”. In the sol–gel system described in this work, the polymerization degree of alumina keeps increasing with the hydrolysis and polymerization of ASB, resulting in a gradual decline in the compatibility of the whole system, inducing the phase separation. The Gibbs free energy change of mixing for a polymer solution system can be expressed as the following formula:25
| 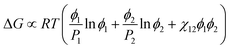 | (1) |
Here,
ϕi and
Pi (
i = 1, 2) denote the volume fraction and the degree of polymerization of each component, respectively,
χ12 is the interaction parameter. The former two terms in the bracket express the entropic contribution, and the last term expresses the enthalpic contribution. According to the following results of FTIR (
Fig. 8), the interaction between PVP and aluminum oxide polymers is weak. This suggests that phase separation is actually driven by entropy changes. As the polymerization degree of aluminum oxide increases, the value of
Pi increases, resulting in the increase of free energy of mixing in this system, thus leading to the onset of phase separation.
Subsequently, under the impulse of the interfacial energy, phase-separated domains go through a coarsening process.26 According to the nucleation-growth phase-separation theory, the coarsening process of phase-separated domains is under the control of diffusion, that is to say, the coarsening process must be accompanied by the composition migration inside the oil phase system. Actually, at the initiation of the phase separation process, PVP precipitates inside the oil phase and acts as the nucleation center. The chelating agent EAA releases under the nucleophilic attack of water molecules to aluminum atoms and diffuses toward the center, inducing the coarsening of phase-separated domains.
Eventually, the sol–gel transition freezes the phase separation structures to prevent further coarsening. At the same time, the porous microspheres are obtained.
3.2 Morphology and pore structure of porous microspheres
Fig. 2 shows the SEM images of alumina solid microspheres fabricated with different amounts of EAA. As observed, the dosage of EAA has a significant influence on the morphology of final products. As the molar ratio of EAA and aluminum sec-butoxide varies from 0 to 2.0, the morphology of the obtained particles changes from the irregular structure to the spherical structure. In this study, EAA is used as a chelating agent, its chelating groups can coordinate with aluminum atoms to form a shield effect,27 which hinders the nucleophilic substitution of water molecules. Besides, the stereo-hindrance effect of EAA is significant. In other words, the synergetic effect of the above two greatly delays the hydrolysis and polycondensation rate of ASB, which can guarantee the thorough emulsification of the oil phase before gelation and contribute to an excellent spherical shape. The chelate mechanism of EAA is exhibited in Fig. 3. Once the oil phase free of EAA is added to the water phase, ASB hydrolyzes rapidly before the oil phase solution is fully emulsified, accordingly obtaining irregular products.
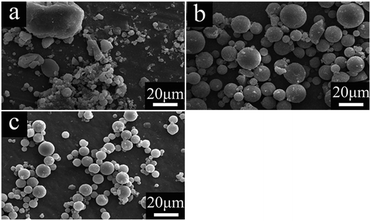 |
| Fig. 2 SEM images of Al2O3 gel particles prepared with various molar ratios of EAA/ASB: (a) 0 (AM6), (b) 1.0 (AM1) and (c) 2.0 (AM7). | |
 |
| Fig. 3 The chelate mechanism of ethyl acetoacetate. | |
In addition, the Span 80 additive also plays an important role in the microstructure of microspheres. The hydroxyl groups of Span 80 have hydrogen-bond interaction with amide groups in PVP (Fig. 4c), so it is expected that Span 80 molecules can locate on the interface of the separated domains to act as a stabilizer in order that the separated domains could experience less deformation during the coarsening process.28 As shown in Fig. 4a and b, the absence of Span 80 will result in a coarse surface and irregular inner cavities.
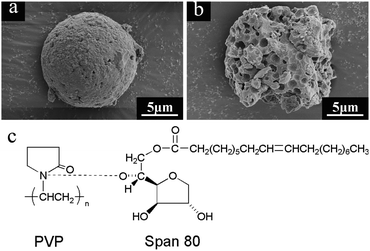 |
| Fig. 4 SEM images of Al2O3 microspheres (AM8) fabricated in the absence of Span 80 (a and b) and hydrogen-bond interaction between Span 80 and PVP (c). | |
The SEM images of dried alumina microspheres prepared with varied WPVP values are shown in Fig. 5. All of the four samples are spherical structures with relatively smooth surfaces (Fig. 5a, c, e and g), which suggests that the addition of PVP makes no difference to the surface morphology of microspheres. On the other hand, almost no phase separation takes place and the solid spheres are obtained in the absence of PVP (AM1, Fig. 5b), while the addition of PVP results in porous structures with incontinuous multicavities (Fig. 5d, f, and h). The average cavity diameters calculated as shown in Fig. 5d, f, and h are ∼580 nm, ∼810 nm and ∼1.0 μm, respectively. In addition, the microspheres obtained with 1.713 g of PVP (AM5) possess generally broken structures (Fig. 5i). It can be deduced that the increase of PVP improves the phase-separation tendency, which can lead to an early onset of phase separation compared to the sol–gel transition,29 and results in a relatively long time for the coarsening process to build an enlarged pore size. However, when the pore size increases to a certain degree, the decrease in wall thickness of cavities together with this may cause the fragility of microspheres. As shown in Fig. 6, the cavity size distributions calculated from SEM images also become wider with the amount of the PVP content increases gradually.
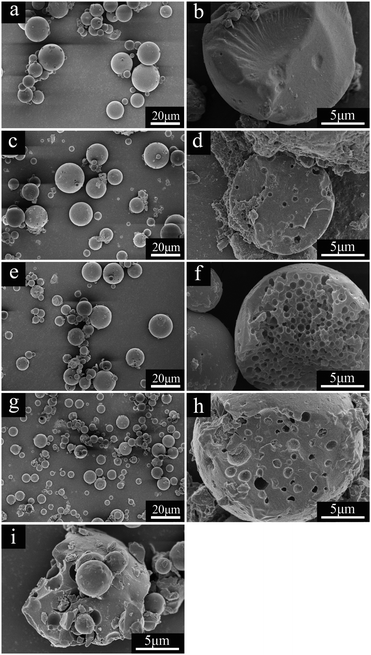 |
| Fig. 5 SEM images of dried alumina microspheres synthesized with various WPVP values: (a and b) AM1, (c and d) AM2, (e and f) AM3, (g and h) AM4 and (i) AM5. | |
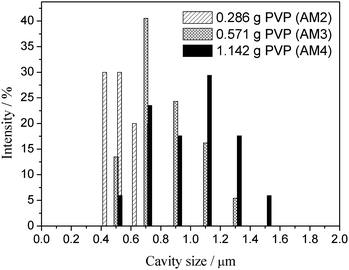 |
| Fig. 6 Evolution of cavity sizes of the alumina microspheres prepared using various WPVP values. | |
3.3 Particle size distribution
The addition of PVP to the oil phase will increase the viscosity of the oil phase, which may make a difference to the particle sizes of the obtained microspheres.30 The particle size distribution curves of the microspheres fabricated with various WPVP values are shown in Fig. 7. It is clear that the presence of PVP has no significant influence on the particle size distribution of Al2O3 microspheres, in spite of its effect on the viscosity of the oil phase (Fig. 7). For the selected four samples (AM1, AM2, AM3 and AM4), the particle sizes show a unimodal distribution and are subject to almost the identical range.
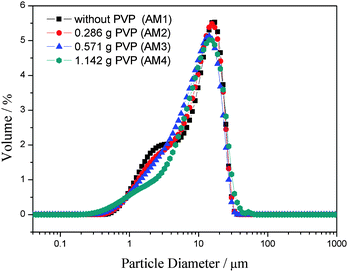 |
| Fig. 7 Particle size distribution of porous alumina microspheres prepared with various WPVP values. | |
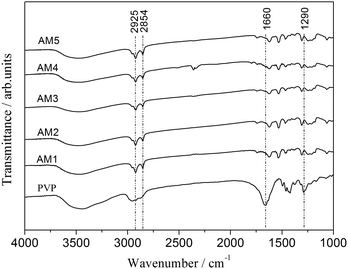 |
| Fig. 8 FTIR spectra of Al2O3 microspheres prepared with various WPVP values (AM1: without PVP, AM2: 0.286 g PVP, AM3: 0.571 g PVP, AM4: 1.142 g PVP, AM5: 1.713 g PVP). | |
3.4 FT-IR spectra
To clarify the role of PVP, chemical bonding analysis and thermal analysis were carried out to determine the distribution of PVP between the alumina oligomers rich phase and the liquid phase. The Fourier transform infrared spectra of the microspheres synthesized with different PVP contents (AM1, AM2, AM3, AM4 and AM5) and pure PVP are depicted in Fig. 8. All of the five samples have almost identical FTIR spectra. Typically, the two absorption bands at approximately 2854 and 2925 cm−1 are associated with the C–H symmetrical stretching vibration and the C–H asymmetric stretching vibration, respectively,31 which result from residual organic components in the microspheres. Besides, the FTIR spectra of PVP shows two characteristic bands at 1660 and 1290 cm−1, assigned to the C
O stretching vibration and the C–N stretching vibration,32 which are absent in the FTIR spectra of the five samples.
The measurement contributes to a conclusion that PVP prefers to diffuse into the water phase, rather than the alumina oligomers rich phase. Meanwhile, it suggests that the affinity between PVP and Al2O3 oligomers in the oil phase is very low. However, according to an earlier research,33 PVP chains can be adsorbed onto the alumina colloidal particles through strong hydrogen bonding, since there are a large number of polar amide and C
O groups in the PVP molecular chains while there are numerous polar surface OH–Al– groups of alumina colloidal particles. In this work, the low affinity may be attributed to the decrease in the polarity of alumina precursors during the polymerization process and the increase of steric hindrance resulted from the improving Al2O3 gel network.34
3.5 Heat-treatment of microspheres
TG-DTA curves for the dried alumina microspheres prepared without PVP (AM1) and with PVP (AM4) are depicted in Fig. 9b. This result shows that the TG-DTA curves for the above two samples are similar. The broad endothermic peak at around 100 °C with a big weight loss is attributed to the evaporation of residual solvent components. The exothermic peak at around 300 °C is related to the pyrolysis of 1-octanol and other organics. The exothermic peak around 400 °C is accompanied by a weight loss around 20%, which is probably due to the combustion of the gel. The decomposition of butoxy and residual 1-octanol can produce a lot of oxygen, which accelerates the combustion process.35 A small exothermic peak at 870 °C is ascribed to the crystallization of γ-Al2O3. The difference in the exotherm possibly results from the porous nature. Besides, there is no evidence of the two large exothermic peaks around 300–400 and 500–700 °C in both samples, which result from the decomposition of PVP (Fig. 9a). This indicates that PVP is preferentially distributed into the water phase, as the same conclusion as the FTIR measurement.
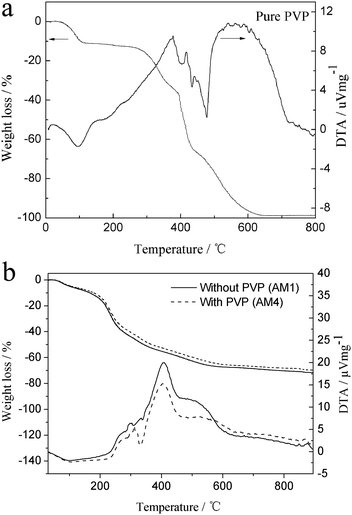 |
| Fig. 9 (a) TG-DTA curves of pure PVP. (b) TG-DTA curves of dried alumina microspheres prepared with PVP (AM4) and without PVP (AM1) | |
According to the TG-DTA curves of microspheres (Fig. 9b), heat treatment was carried out for the AM4 sample at different temperatures between 700 and 1300 °C (every 100 °C, except 1200 °C) with a heating rate of 5 °C min−1. The effect of heat treatment on the crystalline phase is studied below.
Variation of XRD patterns with heat-treatment temperature in air is depicted in Fig. 10. No specific peaks attributed to the as-dried spheres and the samples heat-treated below 700 °C are observed, indicating the amorphous phase. While the diffraction peaks ascribed to γ-Al2O3 appear after heat-treated at 800 and 900 °C. The diffraction peaks are broad and diffuse, indicating that the crystallites are very small and imperfect.36 The diffraction peaks ascribed to α-Al2O3 emerge after heat-treated at 1000 °C, indicating the transformation of γ-Al2O3 into α-Al2O3. When the heat-treatment temperature increases to 1100 °C, the γ-Al2O3 phase vanishes completely, and instead, the pure α-Al2O3 phase is exhibited, proving the absolute transformation into α-Al2O3. The intensity of diffraction peaks for the α-Al2O3 phase increases with further increase of heat-treatment temperature.
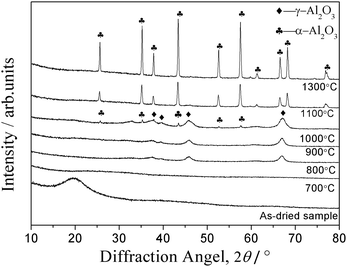 |
| Fig. 10 XRD patterns of alumina microspheres fabricated with 1.142 g PVP (AM4) as-dried and heat-treated at different temperatures in air. | |
As shown in Fig. 10, the diffraction peaks at 1300 °C is sharp, suggesting a good crystallinity. The sequence of the development of phases could be summarized as follows: amorphous → γ-Al2O3 → α-Al2O3. A similar phenomenon of development of the crystalline phase via a sol–gel process was reported by Jiang Li.37 However, as reported by L. A. O'Dell,38 in a pure sol–gel process of ASB, the hydrolyzed product of ASB is γ-AlOOH (boehmite). The phase transformation occurs in the following sequence: boehmite → γ-Al2O3 → δ→θ→corundum. In this study, no discernible peaks are detected from the as-dried sample, proving residual organics may make a great difference to the structure of Al2O3 gel. The same reason also brings out the sluggish of the formation of the γ-Al2O3 phase (usually occurs around 500 °C). Besides, the transition temperature range between the transition aluminas is very sharp, and the transformation strongly depends on the precursors and the thermal treatment, resulting in the absence of the δ-Al2O3 and θ-Al2O3 phases.
In order to make out the effect of heat-treatment temperature on the morphology and interior structures of the as-synthesized microspheres, the SEM images of the AM4 sample heat-treated at 900 and 1300 °C were obtained respectively. As shown in Fig. 11a and b, the sample heat-treated at 900 °C retains the smooth spherical morphology and internal porous structure as with the as-dried sample. The average cavity diameter of the heat-treated microspheres calculated from SEM images is about 1 μm, which presents no obvious difference compared with the as-dried sample. It indicates that the microspheres have excellent thermal stability. After heat-treatment at 1300 °C, the multicavities collapse gradually and a three-dimensional interconnection occurs, which is a typically crystal structure for α-Al2O3.39
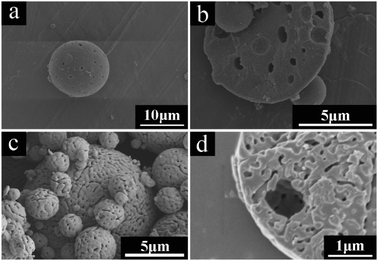 |
| Fig. 11 SEM images of Al2O3 microspheres fabricated with 1.142 g PVP (AM4) heat-treated in air at 900 °C (a and b) and 1300 °C (c and d). | |
4 Conclusion
Alumina porous microspheres with incontinuous multicavities have been successfully synthesized via a facile template-free approach involving an oil-in-water emulsion method and a sol–gel process. The appropriate choice of the amount of polyvinylpyrrolidone (PVP) as a phase separation inducer, ethyl acetoacetate (EAA) as a chelating agent and sorbitan monooleate (Span 80) a stabilizer allows the formation of excellent spherical shape, smooth surface and internal incontinuous porous structure of the microspheres. The as-dried microspheres are amorphous and transform into γ-Al2O3 and then α-Al2O3 after careful heat-treatment. Specially, the porous microspheres heat-treated at 1300 °C possess a three-dimensional interconnected structure.
It is expected that further improvements to particle size distribution and porous structures will be achieved by optimization of the starting compositions and preparation procedures in the future. Furthermore, the obtained porous microspheres can find various applications in liquid chromatography and heat insulation through further treatment.
Acknowledgements
This work was supported by the High Science & Technique Brainstorm Project of Zhejiang Province of China (Grant no. 2014C01025).
References
- B. Celebi, A. Gokaltun, E. Arman, O. A. Evirgen and A. Tuncel, Colloids Surf., A, 2014, 441, 629–637 CrossRef CAS.
- T. F. Fan, J. G. Feng, C. Ma, C. Yu, J. Li and X. M. Wu, J. Porous Mater., 2014, 21, 113–119 CrossRef CAS.
- Y. H. Deng, Y. Cai, Z. K. Sun, J. Liu, C. Liu, J. Wei, W. Li, C. Liu, Y. Wang and D. Y. Zhao, J. Am. Chem. Soc., 2010, 132, 8466–8473 CrossRef CAS PubMed.
- K. Yan, G. S. Wu, C. Jarvis, J. L. Wen and A. C. Chen, Appl. Catal., B, 2014, 148, 281–287 CrossRef.
- J. X. Xu, G. J. Chen, R. Yan, D. Wang, M. C. Zhang, W. Q. Zhang and P. C. Sun, Macromolecules, 2011, 44, 3730–3738 CrossRef CAS.
- C. Takai, T. Hotta, S. Shiozaki, S. Matsumoto and T. Fukui, Colloids Surf., A, 2011, 373, 152–157 CrossRef CAS.
- J. Lee, Y. J. Oh, S. K. Lee and K. Y. Lee, J. Controlled Release, 2010, 146, 61–67 CrossRef CAS PubMed.
- S. Giovagnoli, P. Blasi, A. Schoubben, C. Rossi and M. Ricci, Int. J. Pharm., 2007, 333, 103–111 CrossRef CAS PubMed.
- Y. L. Xie, M. J. Wang and S. J. Yao, Langmuir, 2009, 25, 8999–9005 CrossRef CAS PubMed.
- M. Behra, S. Schmidt, J. Hartmann, D. V. Volodkin and L. Hartmann, Macromol. Rapid Commun., 2012, 33, 1049–1054 CrossRef CAS PubMed.
- G. J. Ding, Y. J. Zhu, C. Qi, B. Q. Lu, J. Wu and F. Chen, J. Colloid Interface Sci., 2015, 443, 72–79 CrossRef CAS PubMed.
- J. Zou, J. N. Ma, J. Z. Jiang, Y. X. Zhang, L. Li and Q. J. Wan, Micro Nano Lett., 2013, 8, 197–200 CAS.
- S. L. Yang, H. B. Yao, M. R. Gao and S. H. Yu, CrystEngComm, 2009, 11, 1383–1390 RSC.
- J. J. Kirkland, F. A. Truszkowski, C. H. Dilks and G. S. Engel, J. Chromatogr. A, 2000, 890, 3–13 CrossRef CAS PubMed.
- Y. Piao, H. Lim, J. Y. Chang, W. Y. Lee and H. Kim, Electrochim. Acta, 2005, 50, 2997–3013 CrossRef CAS.
- Y. Lv, S. C. Zhang, G. H. Liu, M. W. Huang and X. R. Zhang, Anal. Chem., 2005, 77, 1518–1525 CrossRef PubMed.
- B. H. Yoon, W. Y. Choi, H. E. Kim, J. H. Kim and Y. H. Koh, Scr. Mater., 2008, 58, 537–540 CrossRef CAS.
- T. Kato, H. Ushijima, M. Katsumata, T. Hyodo, Y. Shimizu and M. Egashira, J. Mater. Sci., 2002, 37, 2317–2321 CrossRef CAS.
- J. Lu, S. S. Liu and C. H. Deng, Chem. Commun., 2011, 47, 5334–5336 RSC.
- M. Y. Li, Z. C. Si, X. D. Wu, D. Weng and F. Y. Kang, J. Colloid Interface Sci., 2014, 417, 369–378 CrossRef CAS PubMed.
- Y. J. Hu, H. Q. Ding and C. Z. Li, Particuology, 2011, 9, 528–532 CrossRef CAS.
- K. Nakanishi, J. Porous Mater., 1997, 4, 67–112 CrossRef CAS.
- J. W. Cahn and R. J. Charles, Phys. Chem. Glasses, 1965, 6, 181–191 CAS.
- K. Nakanishi and N. Soga, J. Non-Cryst. Solids, 1992, 139, 14–24 CrossRef CAS.
- P. I. Flory, J. Chem. Phys., 1942, 10, 51–61 CrossRef CAS.
- K. Nakanishi and N. Soga, J. Am. Ceram. Soc., 1991, 74, 2518–2530 CrossRef CAS.
- Q. F. Gao, C. R. Zhang, J. Feng, W. Wu, J. Z. Feng and Y. G. Jiang, Chin. J. Org. Chem., 2008, 24, 1456–1460 CAS.
- W. W. Cai, H. Yang and X. Z. Guo, Chin. Chem. Lett., 2014, 25, 441–446 CrossRef CAS.
- K. Nakanishi and N. Tanaka, Acc. Chem. Res., 2007, 40, 863–873 CrossRef CAS PubMed.
- J. H. Park, C. Oh, S. I. Shin, S. K. Moon and S. G. Oh, J. Colloid Interface Sci., 2003, 266, 107–114 CrossRef CAS PubMed.
- F. BoCcuzzi, A. Chiorino, M. Manzoli, P. Lu, T. Akita, S. Ichikawa and M. Haruta, J. Catal., 2001, 202, 256–267 CrossRef CAS.
- T. R. Zhang, R. Lu, X. L. Liu, Y. Y. Zhao, T. J. Li and J. N. Yao, J. Solid State Chem., 2003, 172, 458–463 CrossRef CAS.
- C. B. Jing, X. G. Xu and J. X. Hou, J. Sol-Gel Sci. Technol., 2007, 43, 321–327 CrossRef CAS.
- Y. Frere and P. Gramain, Macromolecules, 1992, 25, 3184–3189 CrossRef CAS.
- Q. L. Zhang, F. Wu, H. Yang and D. Zou, J. Mater. Chem., 2008, 18, 5339–5343 RSC.
- J. A. Wang, X. Bokhimi, A. Morales, O. Novaro, T. Lopez and R. Gomez, J. Phys. Chem. B, 1999, 103, 299–303 CrossRef CAS.
- J. Li, Y. B. Pan, C. S. Xiang, Q. M. Ge and J. K. Guo, Ceram. Int., 2006, 32, 587–591 CrossRef CAS.
- L. A. O'Dell, S. L. P. Savin, A. V. Chadwick and M. E. Smith, Solid State Nucl. Magn. Reson., 2007, 31, 169–173 CrossRef PubMed.
- F. S. Yen, P. L. Cheng, H. Y. Huang and T. C. Lin, J. Am. Ceram. Soc., 2009, 92, 2089–2092 CrossRef CAS.
|
This journal is © The Royal Society of Chemistry and the Centre National de la Recherche Scientifique 2016 |
Click here to see how this site uses Cookies. View our privacy policy here.